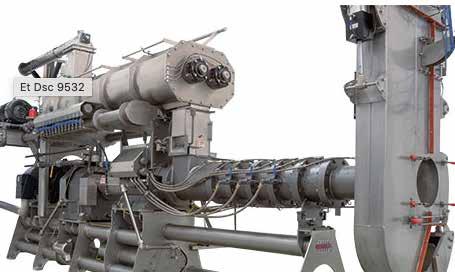
4 minute read
Troubleshooting
Meat Inclusion in Extrusion
An interesting topic and one deserving some attention. The “meat” typically Stored in frozen blocks is thawed to temperature just above freezing which grinded easier usually metal checked and ground into a pumpable slurry. Equalising the moisture content to a standard the meat is now ready to send to the process. It can go to the extruder directly but usually a counter flow heat exchanger is used to elevate the meat temperature. Higher capacities are possible in the extruder if it does not have to heat the meat. A special pump for viscous materials is used to meter the meat into the conditioning cylinder. Levels pumped in will depend on the design and ability of the cylinder to handle meats.
Advertisement
Now for the extrusion aspect of dealing with meat. Most extrusion designs have a limit on water usage and still make an acceptable kibble shape. Earlier mentioning the equalisation of moisture in the meat is generally done so that the extrusion process is stable. If the moisture in the meat pumped in varies then the kibble density, appearance and moisture will vary out of the extruder over time. The limit of meat used depends on the moisture in the meat. Meat usually has somewhere in the area of 65 to 75 percent water. Typical moisture contents during extrusion vary but are in the area of let’s say 20 to 35 percent moisture. Typical dry formulas would have a moisture content of 10 to 12 percent which means you can add approximately 25 percent meat in a single screw and 30 percent in a twin screw which is 66.7 percent moisture which would yield respectively 10.9 to 13.7 percent meat in the final kibble. As you can see on a standard basis a twin can handle a bit more meat than a single screw but in both of these cases these are very traditional standard extruders.
There were some limitations with this above process as it was used for years but the desire for higher meat products pushed continued research. The development of advanced preconditioning where high levels of meat added did not clump or ball up assisted greatly. The changes allowed for high meat inclusion and a free-flowing powder like material out of the conditioner to the extruder. Extruders then reared up and said no you can’t do that; you are not going to send me a high moisture very slippery formula and expect me to generate friction to cook this product when meat levels were pushed! So, some changes occurred, more flow disruption with various screw and kneading lobe in the barrel allowed for handling a slightly higher level of meat in the formula.
In conclusion, systems exist which cook a wide range of meat inclusion petfoods. Development of thermal energy extrusion processes are allowing meat levels to be pushed to unheard levels which are getting close to 65 to 75 percent meat formulations. See March issue 2022 for an article on a demo on 110 percent (% of dry feed) meat inclusion.
Previously on Troubleshooting...
1. Density
An examination of product density and its relationship with moisture levels, heating, cooling feeder screw rate and automation.
2. Non-uniform and rough appearance
A guide to understanding the science involved in improving the art of making products of all the same size.
3. Extrusion dies
This article takes a look at aspects of the process including high, medium and low shear as well the adjustments required when producing feed for small mammals.
4. Dryers
The dryer is without a doubt one of the machines in the system which greatly impacts the bottom line.
5. The Extruder Barrel - Part 1
Forming extruders are used for some select products – thus this part of the discussion centres on single and twin designs.
6. Cook in the Extruder Barrel – part 2
As discussed last month, the extruder barrel has a number of functions, but the main goal is to finalise the cook, yield the desired shape with the density target.
7. Coating
The coating process has a few areas of importance, with this edition of ‘Troubleshooting’ exploring the most important of these.
8. Expanded cat food
Dry expanded cat food production is similar to dog food production, but there are some differences, with this edition exploring a choice selection of these.
9.
Extrusion during operation
This month we discuss steam input into the conditioner. During the water addition process, the steam is usually in the two-bar range.
Innovations this month April 2023
This month’s Production Showcase section features equipment and ingredients that will help in the production of petfood, taking you right from the recipe book, right up until until your product is ready to leave your factory door.
If you would like your product or service to appear on this page in a future edition of International Petfood magazine, then please contact us at editorial@perendale.co.uk
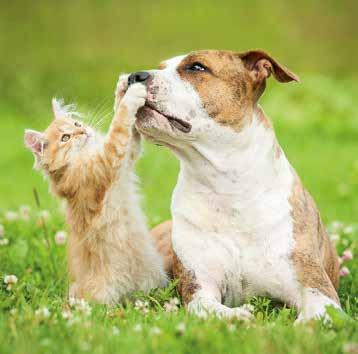
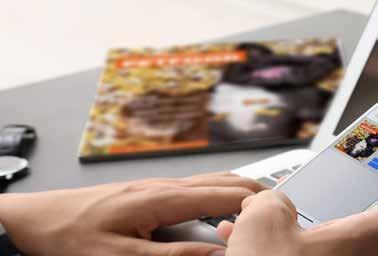
Extruder Barrels by Extru-tech
Extru-tech extruder barrels are already designed for broad production capabilities with maximum efficiency and minimal metal-to-metal wear. However, to further eliminate pathogens in the extruder barrel, extrutech advanced feature extruders utilize a modified barrel profile and increased steam injection into the barrel. Each extruder model can be equipped with multiple barrel length packages, each designed for the production of specific product types. Naturally, all extruder screws and liners continue to be constructed of high quality, wear-resistant stainless steel alloys that are subsequently polished, heattreated to required hardness specifications and then parallel ground to ensure proper fit between barrel components.
From unprecedented production capacities to exacting finished product quality, Extru-Tech Extrusion Cooking Systems have established the industry standards for performance and value. Extru-Tech’s Advanced Feature Extrusion systems were designed with two important criteria. The unit needed to be quick and easy to clean, and it needed to allow customers to control, reduce or eliminate contaminants in the system. http://extru-techinc.com/products/extruders/system--5