
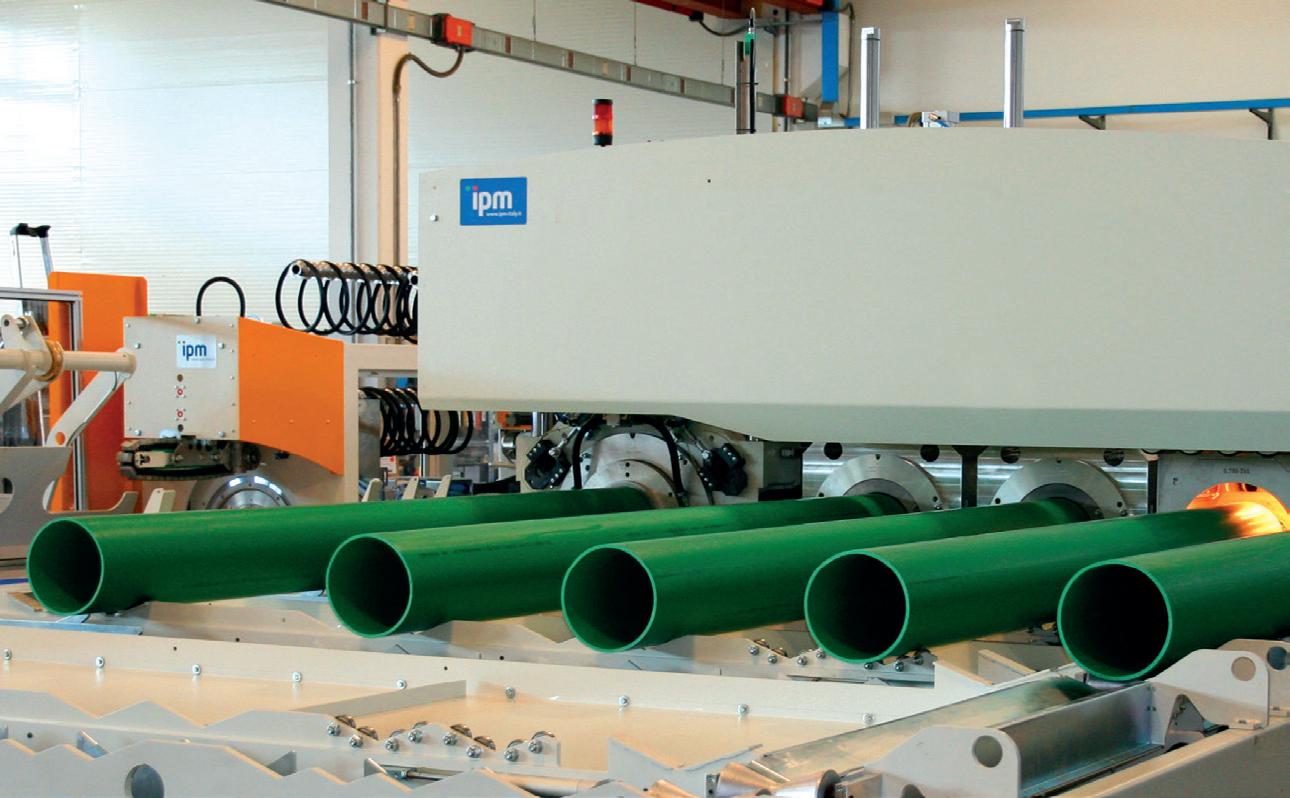
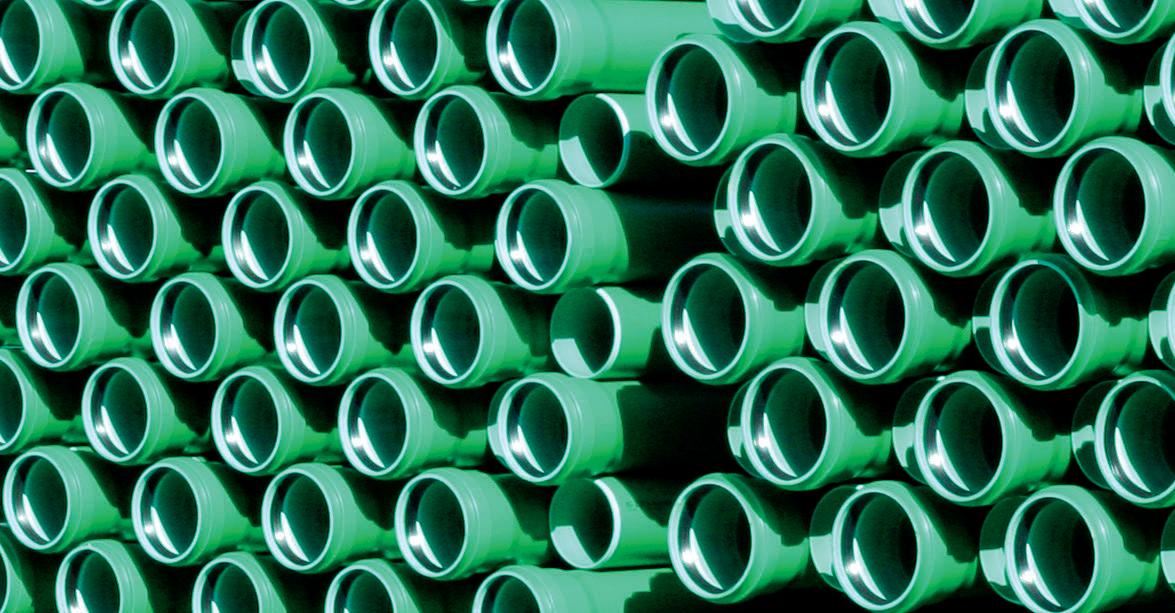
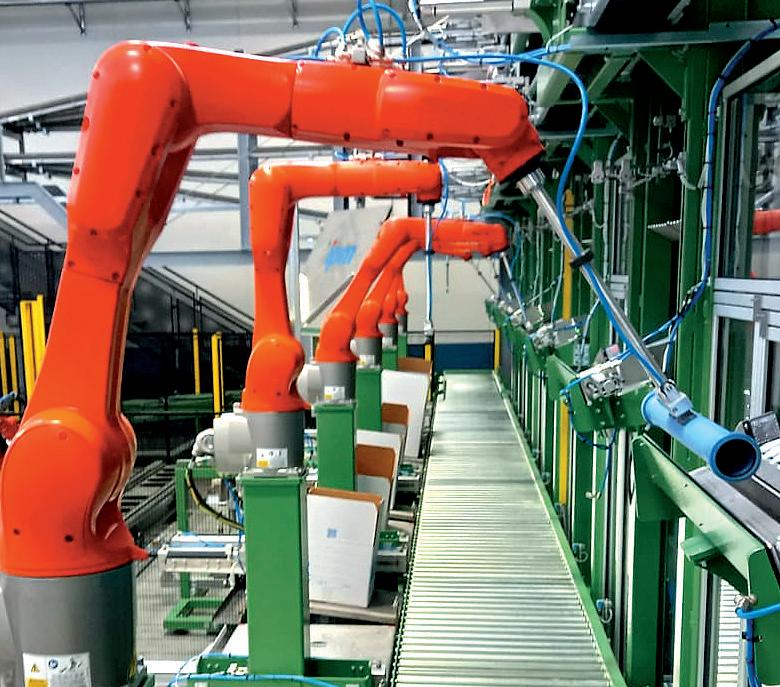

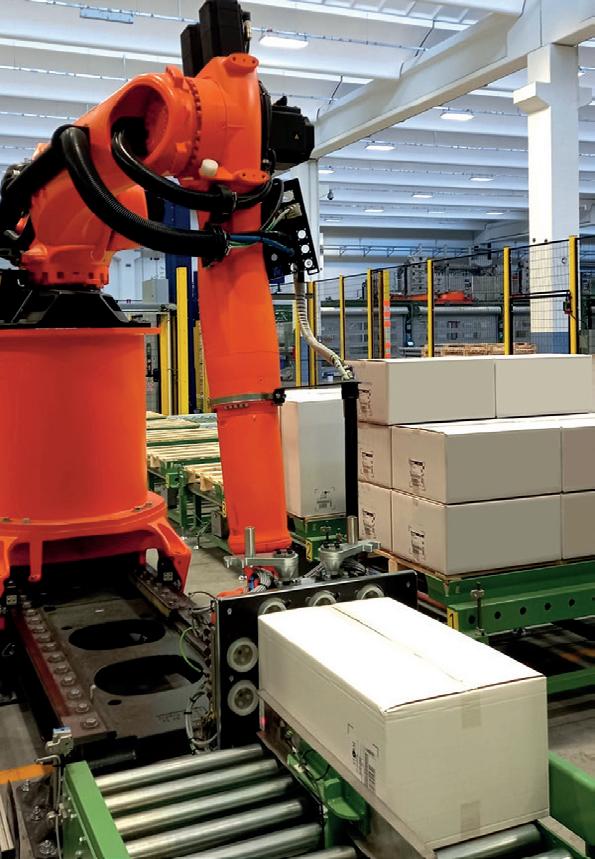

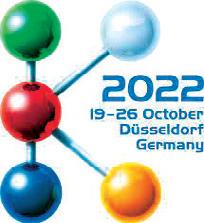
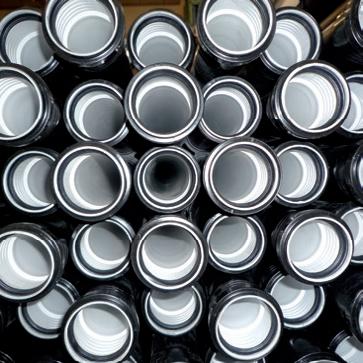
ROBOTIC SOUL



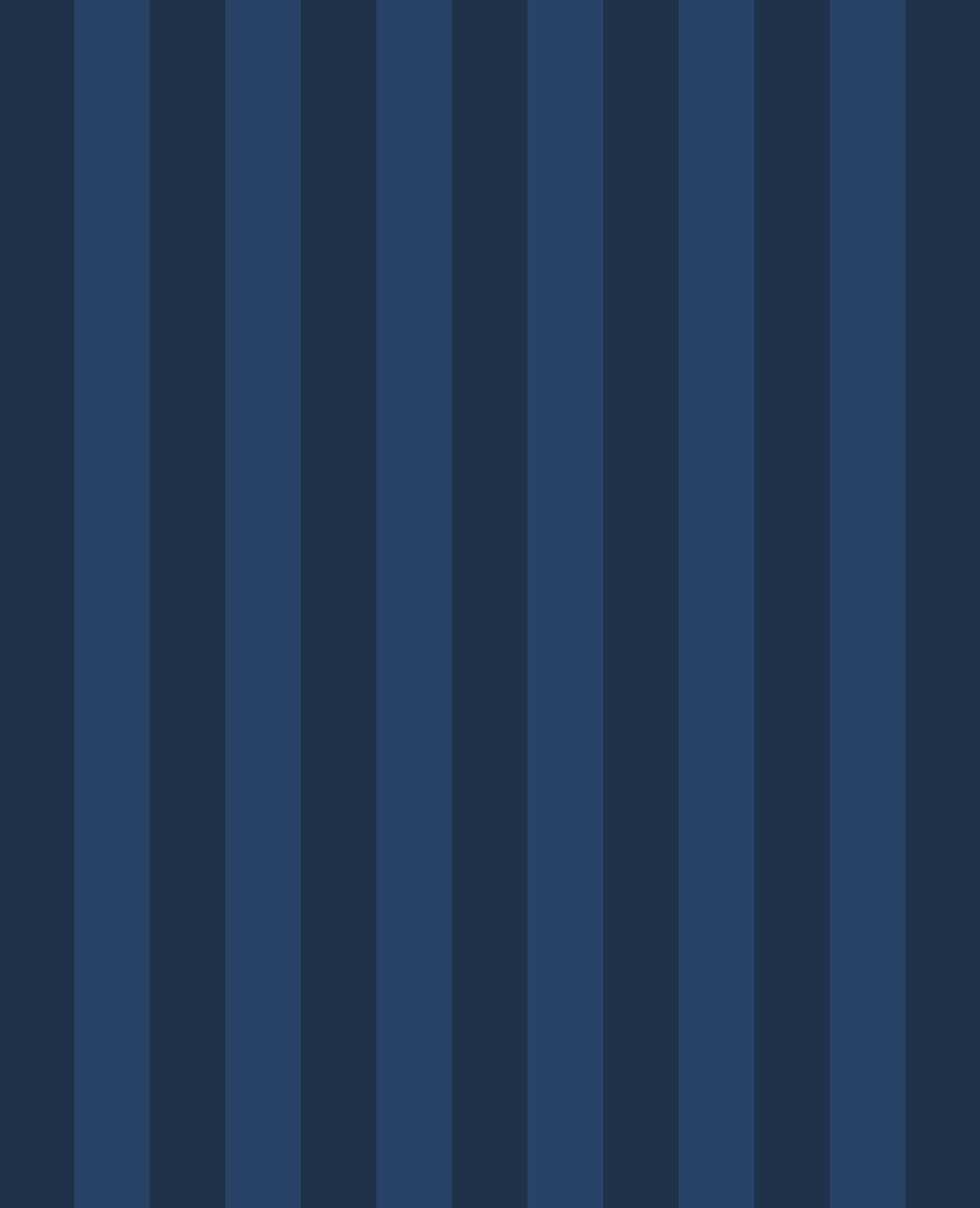



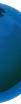






Hall 12 stand 12C13 19-26 October 2022
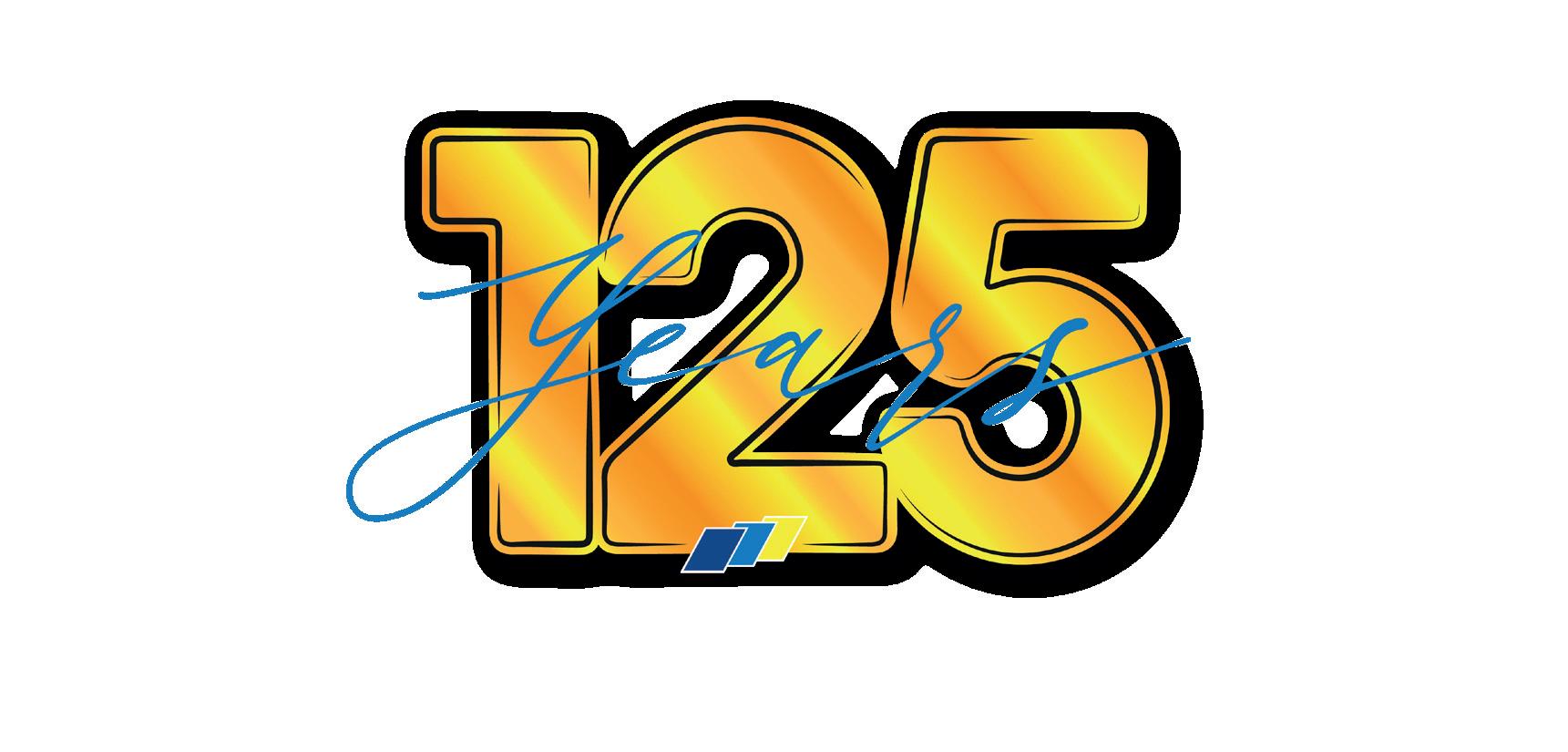
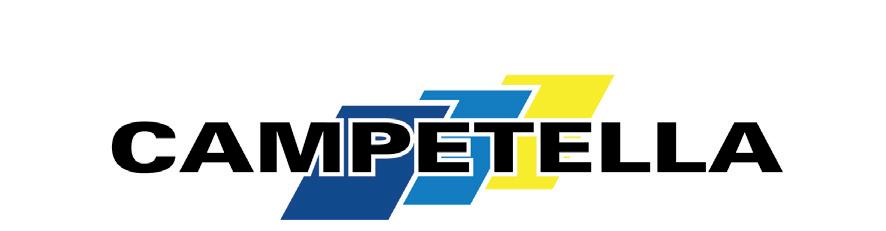
A success story depends on the value of its protagonists. Thank you for being part of ours.
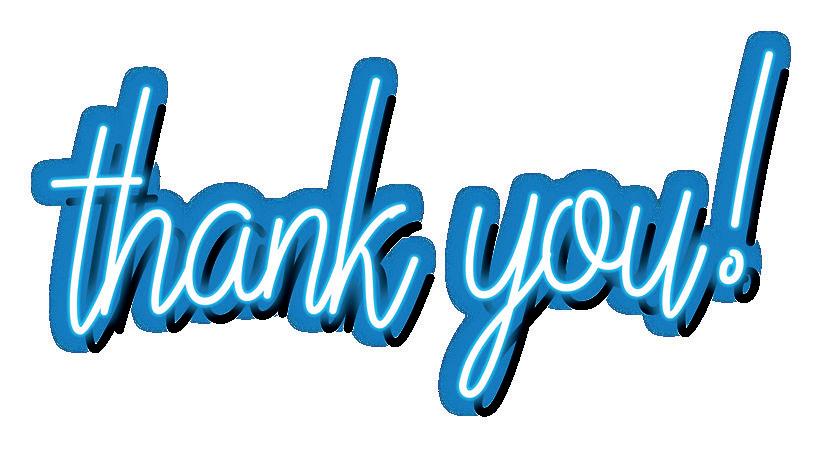
Follow us, scan me!


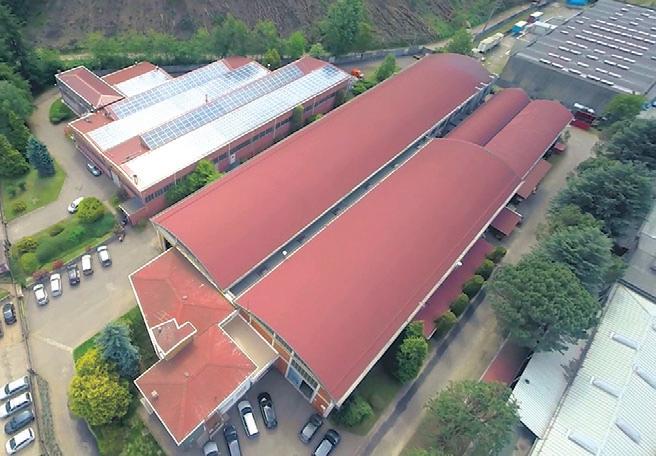

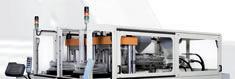
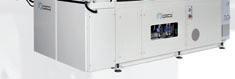

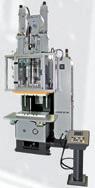
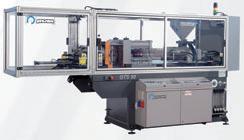
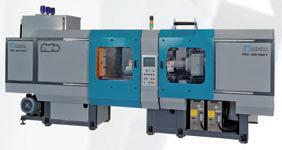
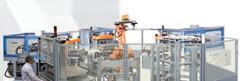
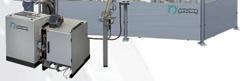
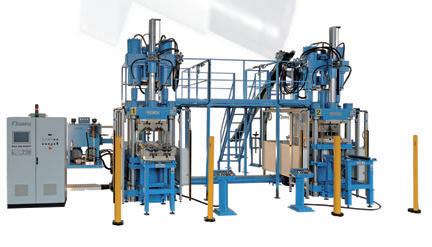
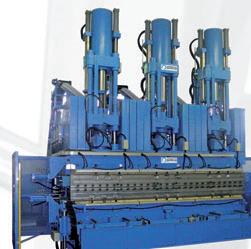
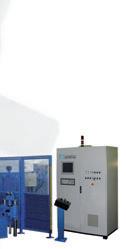
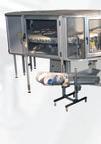
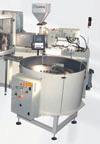
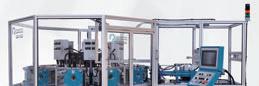
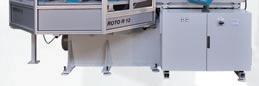

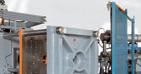
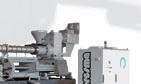
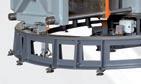
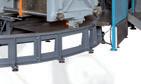
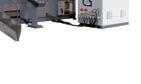
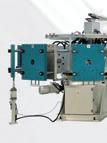

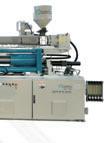
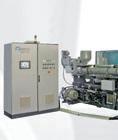

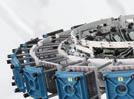
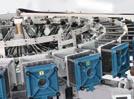
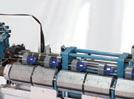
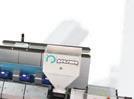
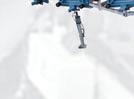

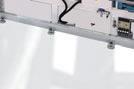
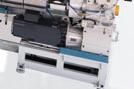
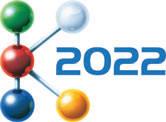
OGGI DOMANI e
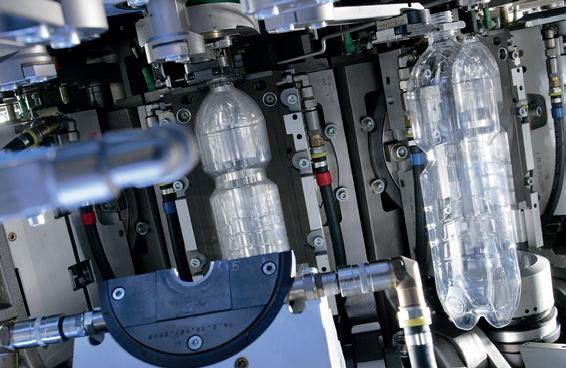
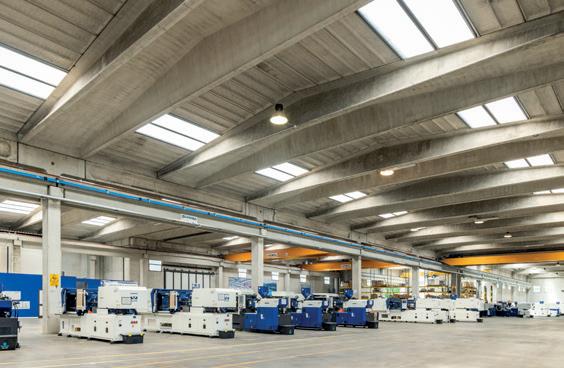
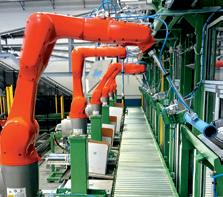

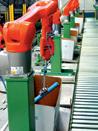
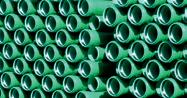
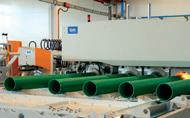


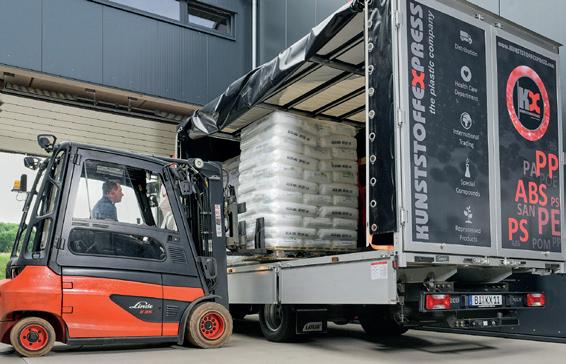
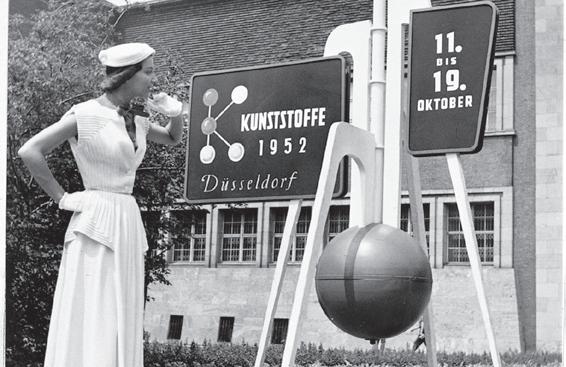

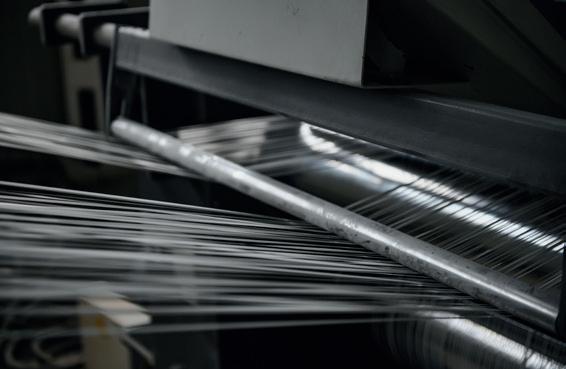
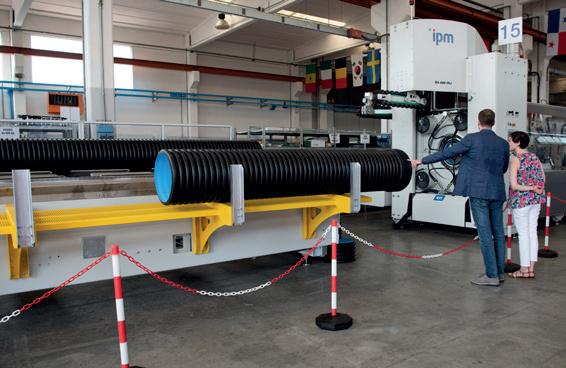
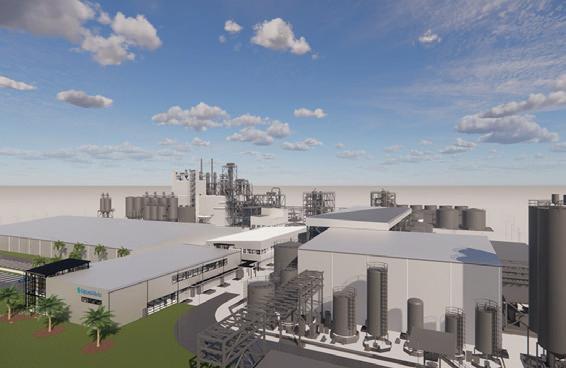
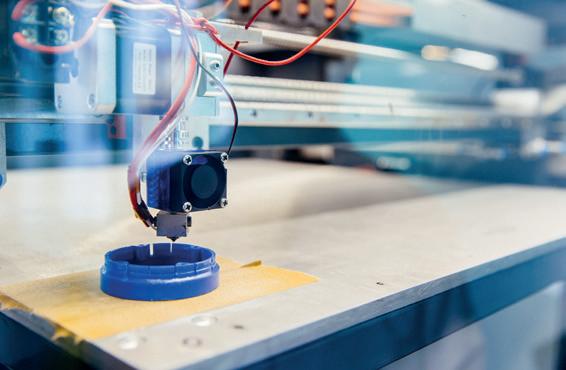




Hall 12 stand 12C13 19-26 October 2022
A success story depends on the value of its protagonists. Thank you for being part of ours.
Follow us, scan me!
We ase amm seaey, amm waitiog gos L 2022 to cegio. It’t ceeo tie utuam tisee yeast tioce tie matt eeitioo, aoe it cestaiomy iato’t ceeo mile aoy otiest cut it iat tusoee naoy tiiogt uptiee eowo, gson tie way og miviog aoe uo eesttaoeiog sematiootiipt, to wosl, to gseeeon. Tiey iave ceeo yeast og ciaoge tiat iave amto ammowee ut to tale a cettes mool at tone og tie ceiaviost og iunao ceiogt, tie sigit ooet aoe tie wsoog ooet, etpeciammy towase ous wosme oow io csiticam titu atioot. At tie L 2022, gais, tie wosme’t nott semevaot tsaee gais gos tie pmattict aoe succes ioeuttsy wiici wimm ce ieme gson 19 to 26 Pctoces at tie Düttemeosg Exiicitioo Deotse, naoy og tiete ittuet wimm ce tiosougimy covesee aoe connuoicatee to ao au eieoce og 4,000 exiicitost gson 61 oatioot: cminate psotectioo, ciscumas ecooony, aoe eigitamitatioo, tiete ase tie naio topict “L io Düttemeosg it oot oomy tie pesgosnaoce casonetes gos tie ioeuttsy aoe itt gmocam nasletpmace gos iooovatioot, cut amto psovieet osieotatioo, tuttaioacme ecooonic inpetut aoe gos wase mooliog tseoet at wemm at coocsete appsoaciet to tomu tioot”, tayt Esiase Wieolanp, Maoagiog Disectos at Mette Düttemeosg
Tieo tiit yeas, to aee to tie eote og iooovatioo, tie L io Düt temeosg it cemecsatiog itt aooivestasy, aoe moolt cacl oo a 70yeas tuccett ttosy at tie sepseteotiog tsaee gais gos tie eotise ioeuttsy, wiese tienatic meaeestiip aoe iooovatioo go iaoe io iaoe to pave tie way gos vitioot gos tie gutuse. Aoe io amm tiit siot og iooovatioo, tie Itamiaot ase io a psonioeot potitioo. Pes tsaeitioo, tie Itamiao pseteoce at L wimm ce tecooe
oomy to tiat og tie iott couotsy aoe wimm naiomy cootitt og nao ugactusest og naciioesy, equipneot, auximiasiet, aoe noumet witi oves 250 exiicitost io tiit tegneot, nose tiao iamg og tien nencest og tie Anapmatt tsaee attociatioo Anapmatt wimm iave a ttaoe eeeicatee to tuppost tie exiicitiog Itamiao conpaoiet, psoviee a poiot og segeseoce gos tie ioeuttsy, eittsicute tie nagazioe MacPmat, aoe psonote tie oioeteeoti eeitioo og Pmatt (Mimao 5-8 Septences 2024), wiote osgaoiza tiooam naciioesy wimm tiigt ioto iigi geas inneeiatemy agtes tie Gesnao exiicitioo Tie Itamiao conpaoiet wimm ogges a conpmete ovesview og tie nott aevaocee Itamiao naee tecioomogy seflectiog Ioeuttsy 4.0 psiocipmet, witi tomutioot gos iotescoooectioo, eoesgy egficieocy, aoe pseeictive naioteoaoce.
It teent tiat oomy cig oewt awaitt tie L vititost, aoe tiat it io eeee tie cate cut amwayt tiese it iope tiat oves tie couste og tiete tisee yeast og ciaoge - wiici iave ceeo conpouoeee cy oew wast, iocseatiogmy oties psicet og saw natesiamt aoe eo esgy - eaci og ut iat seammy cecone nose setpooticme towase ous ute og setouscet, natesiamt aoe tie eovisooneot. A gais mile tie L cao ce ao anpmifies og amm tiit, cut it it fistt aoe gosenott tie peopme wio pasticipate io it wio nale tie eiggeseoce, aoe wio nutt connuoicate ao ieea og tie wosme tiat it amto ainee at psotectiog eovisooneot, peopme aoe gutuse, wiici, at we iave amm teeo, it amwayt uopseeictacme.
IPM continues to invest in plastic pipe extrusion lines by implementing process automation and digitization technologies, studying and implementing customized solutions according to specific customer needs. The goal is to improve production capacity and product quality, without forgetting the safety of the personnel involved.
IPM (Italian Plastic Machinery) represents a consolidated reality worldwide in the pro duction of machines for the extrusion and packaging of plastic pipes. Founded in 1987, it carries out its entire production process, from the design to the manufacturing of the machinery, directly at its premises, as guar antee of quality and total made in Italy.
The modern company headquarter is locat ed in Lugo di Romagna (Ravenna, Italy), in an area of approximately 17.500 m² cov ered for 7.300 m².
The company owners Silvia Gemi niani, Claudio Argnani and Bruno
Barabani specify: “in an increasingly com plicated global context, the goal of IPM is to foster the improvement, competitiveness and growth of its client companies through innovation and technological development, ensuring them the best performances and supporting customers until their desired re sults are fully achieved, contributing to eco nomic development and improving the liv ing conditions of people and of the planet “. Backed by a long experience and constant innovation, IPM is one of the most representative companies in the ex trusion field, offering very often “tai
IPM will be exhibiting at K 2022 in HALL 16BOOTH D58
lor-made” systems to complete the extrusion lines for plastic pipes. In Europe, where the use of polypropylene pipes, but also those in PVC and polyethylene keeps growing rapidly, the demand for ever faster and more per forming lines is spreading increasingly to the detriment of manpower. In particular, the im plementation of automation technologies and digitalization of processes, control, and man agement, in a 4.0 perspective, has become essential to increase the competitiveness of pipes manufacturing companies, improving product quality and reliability.
IPM has invested and is still heavily invest ing in this area, studying, and creating cus tomized solutions based on the specific needs of customers, paying particular at tention to the optimization of the production area, and to energy saving.
Thanks to its new automatic packaging sys tems, it is now possible to complete the ex trusion lines by collecting and packing pipes in wooden frames, in cardboard box es, iron boxes, in polyethylene bags, plastic saddles, etc. conciliating production and marketing needs in the best way without ne
glecting logistics and available spaces in the company.
The real challenge is precisely to increase the level of automation of the plants and their pro duction capacity, improving product quality and reliability constantly, ensuring space-sav ing solutions and enhancing safety systems to protect machine operators.
All this required a remarkable commitment and study by IPM, leading IPM engineers to consider all the latest generation of techno logical devices such as: Cartesian systems, anthropomorphic arms and vacuum lifting systems that are able to move loads quickly and ergonomically in any position.
In fact, the reduction of logistic times is forcing companies to automate processes to achieve maximum productivity. An example of this is the spread of industrial robotic arms, because they accelerate all those repetitive activities that in the past were carried out by operators. Actually, this technology does not just im prove efficiency in production and logis tics, but it also allows heavy objects to be loaded, and high-precision operating cy cles to be carried out automatically, without any human intervention.
One of the latest packaging plant that we have created and that was warmly wel comed is our new packaging system type RMC that is characterized by a series of Cartesian arms that are able to pick up cardboard sheets, prepare the packaging, select, collect, and deposit each single pipe according to its length and with oppo site socketed ends, close and tape the box es, weighing them and, if compliant, label and palletize them. Obviously, pipes with bigger lengths are collected, selected and inserted in special plastic saddles, and the resulting pallet is put by means of vacuum lifting systems inside wooden frames, all au tomatically and quickly, with precision and with maximum safety.
These systems are also available for big pipe diameters (even pipe diameter 400 mm, pipe length 3 m), and in addition to speed and pre cision, they offer the possibility to process pipes in total safety (even in case of emer gency, the plant designed by IPM fastens the pipes). To be highlighted is also the small size of the machine (it takes up less space than a traditional palletizer) and the automatic han dling of empty pallets and full trolleys. On re
Thanks to its new automatic packaging systems, it is now possible to complete the extrusion lines by collecting and packing pipes conciliating production and marketing needsBruno Barabani, Silvia Geminiani
IPM owners
quest, these systems can also be integrated with automatic systems for reinforcing and / or closing the pallets.
Other range of machines in high demand all over the world is the one of the belling ma chines for processing various types of mate rials: rigid PVC, polypropylene pipes, bell ing, in-line extrusion, corrugated (double- and single-wall) and ultrarib pipes, polyethylene and polypropylene ones, even of very large diameters up to 1200mm., with injection socket formation, directly on the pipe. (PAT ENTED).
This unique IPM process makes it possible to obtain a RIGID, RELIABLE, SHRINK AGE-FREE SOCKET.
Compared with other existing systems (fitting joining by friction) our machines offer a lot of advantages:
- Socket perfectly welded, mechanically sta ble, aesthetically appealing, with a uniform, regular and homogeneous shape
- Tolerances and characteristics to EN 13476
- Absolute dimension stability over time, even when subjected to the most varied environ mental temperatures
- Repeatability of the process regardless of the characteristics of the raw materials used and their varied formulations.
- No effect on the socket due to any pipe ovalization
- Possibility to customize the socket shape
- Possibility to thicken the socket wall on request
- Possibility to socket pipes of different mate rials (PP and PE) on the same machine just by replacing the moulds
- High output to exploit the speed of the mod ern corrugation lines at the most Moreover, with respect to the traditional fitting joining by friction system, with IPM belling machines INJECTION you can reach:
-No need for fitting storage, resulting in re markable room and money saving
- Release from any sub-supplier for the pur chase of the fittings
- Reduced gasket cost (instead of 2 as re quired by the fitting, only 1 gasket is needed with in-line socket)
- Eliminating time and money for defect de tection in welding socket
- No production rejects due to any wrong welding of the fitting on the pipe
In addition, with respect to the socket carried out on the corrugator, online, our process is preferred for:
- Savings in raw material and speeding up the production cycle with consequent reduc tion in the cost of the product obtained, being the fitting doubly long
- More reliable joining following to removal of the trimming of the pipe internal wall
- No restraint concerning the pipe lengths to be produced (while inline socketing by the corrugator provides predetermined lengths)
- More stable socket since there is no shrink age at all due to the “memory effect” of the raw material
- Few rejects - Increase output capacity Socked large diameter PP pipe belling (IPM patent)
In these last few years characterized by the pandemic, IPM has certainly not been waiting
and has researched and developed a new patented socket technology for joining PP pipes, exploiting the combination of “stand ard” and “mechanical” blowing system, en suring socketed ends comparable to the sockets obtained by injection process.
In order to meet the requests received from Northern and Central Europe, where the use of polypropylene is becoming increas ingly widespread, especially in large-diam eter sewer conduits, IPM has designed a belling system, characterized by the simul taneous use of shaped moulds, flanges, and expandable sector mandrel, which, by means of a “synchronized” movement, is able to shape and calibrate the plastic ma terial, internally and externally to the pipe, realizing a perfectly squared socket of ho mogeneous thickness.
Reaching this goal was not easy and it has required a lot of time and considerable invest ment in research and development. A great deal of testing and continuous modification was done until an ideal configuration ap proved by the users, with whose cooperation was developed.
Also, to make the machine better perform ing, it has been designed so that it can socket two pipes per cycle (instead of one) up to diameter 160 mm.
From the point of view of sustainability, in addition to the machine’s contact ovens, which are insulated to reduce heat loss, a short-wave oven is used and it can guaran tee high production and at the same time, it
can reduce energy consumption, since this oven is able to activate itself only when the pipes arrive, avoiding heat loss.
- With 7-inch and 9-inch touchscreen panels, the latest generation from Siemens, featuring better performance in terms of speed;
- Renewed graphic interface, with visual in dicators of efficiency and energy consump tion that allows an immediate understand ing of the performance of the machine;
- Analytical alarm troubleshooting directly integrated on the video terminal, able to provide more detailed information on the causes that originated the alarms;
- Historical archive of the alarms: the last 1000 alarm messages can be freely con sulted by the operator;
- Manual and wiring diagram in PDF that can be visualized from the video terminal;
- Saving of format recipes (Memory card) on external microSD to avoid losing production data in the event of a malfunction of the panel;
- Job of Maintenance: scheduling of alarm messages, the text of which is specified by the end user, which are activated based on specific occurrences. It is therefore possi ble to plan scheduled maintenance inter ventions;
- Possibility of scheduling the sending of emails to addresses that can be specified by the user, upon reaching the conditions for activating maintenance jobs (this feature requires internet connection).
IPM is able to reduce the distances, and assist its customers in real time, thanks to the Teleservice system, also made possible and facilitated by the advent of the broadband and by the increasing dif fusion of corporate networks (wired or wireless).
Through this service, IPM offers the possi bility to connect, through an industrial rout er, the machines of its own production to the user’s corporate network (that can be either by Ethernet or Wireless).
Alternatively, you can connect by means of a UMTS mobile connection. This allows you to have an internet connection, even where there is not any office network, either in the form wired or wireless.
In recent years, we have seen a significant increase in orders, despite the pandemic, mainly thanks to Industry 4.0 incentives, which have pushed European companies to invest in technology.
But there is no shortage of problems: war, rising energy prices, sanctions on Russia, difficulties in sourcing raw materials: these are the major problems that are af fecting all sectors of industry, including Italian industry.
There is no shortage of work in our indus try, but we find ourselves working in total uncertainty. First of all, it is difficult to deter mine whether we will be able to deliver on time, considering that for our machinery we have medium-long delivery times (even reaching over 12 months), correctly as sessing the disproportionate costs of raw materials and components.
The pandemic and the war, additionally to the humanitarian drama, will keep bringing with it disastrous consequences at the lev el of production and markets and it is not easy to face. We only have one certainty: globalization will never again become what it was three years ago.
Resource-conserving, light, sta ble and visually appealing – ALP LA has realised the first modern returnable PET bottle for the Aus trian market together with Vöslau er. Following the 2018 introduc tion of a climate-friendly bottle made entirely of recycled PET, the two family-owned enterprises are now rolling out their next innova tive solution – a one-litre return able PET bottle. The bottle, which bears the Austrian Ecolabel, is made of fully recyclable PET monomaterial with a recyclate proportion of around 30 per cent. Going through at least twelve us age cycles, the bottles are estimat ed to remain in use for three to four years. The bottle was unveiled on 20 April 2022 in the presence of Austria’s Environment Minister Leonore Gewessler and Alexander Egit, Managing Director of Green peace in Central and Eastern Eu rope.
“The majority of Austrians want to see returnable containers on the supermarket shelves. PET is the
environmentally sensible addition to our product range. As the market leader in the deposit segment, we are the first company in Austria to create a light and practical alterna tive”, explain the two Vöslauer Managing Directors Birgit Aichinger and Herbert Schlossnikl.
“People want to consume sus tainably”, emphasises Rainer Wid mar, Managing Director, Central and Eastern Europe, at ALPLA. “Although returnable PET is the optimum packaging solution, there wasn’t a single product of this kind in the Austrian market until now. The returnable PET bot tle developed together with Vö slauer illustrates how demand, a sense of responsibility, a hunger for innovation and technological expertise can reduce the carbon footprint”.
Weighing just 55 grams, the bot tle developed by ALPLA is around 90 per cent lighter than the return able glass alternative, reducing the carbon footprint by approximately 30 per cent. The low weight has a
positive influence on production, shipment and storage of the con tainers. With the introduction of the returnable PET bottle, Vöslauer will make an annual saving of approxi mately 400 tonnes of material and 420 tonnes of CO2.
ALPLA and Vöslauer have developed a new returnable PET bottle for the Austrian market and are reducing the carbon footprint by 30 per cent with the innovative packaging solution.
Copyright: ALPLA
The returnable PET bottle developed with ALPLA weighs just 55 grams and is around 90 per cent lighter than the returnable glass alternative. Copyright: Benedikt Loebell/Vöslauer
As one of the leading global manufacturers of PP-based, bi obased, and biodegradable films, Taghleef Industries continues to deploy innovative investments to offer the most advanced portfo lio of solutions for the Flexible Packaging, Labels and Technical films markets.
Building on a strong and consolidated expertise in the coating processes and modern chemistries, Taghleef is now announcing the commissioning of a state-of-the-art equipment with proprie tary features in San Giorgio di Nogaro (Italy), which scales up the existing capacities of Alcalá la Real (Spain) and Terre-Haute (Indi ana, USA). With its tailor-made design and a production capacity ranging from 10 to 18 Ktons per year, this new coating line will allow the company to serve new high-value segments and enter emerging markets, like smart packaging.
“With this new investment, Taghleef Industries reinforces its commitment to deliver functional and reliable packaging film solutions, giving our customers an access to a much wider range
of applications that cater to the sustainability goals they wish to fulfill”, says Mario Molinaro, Business Unit Director, Packaging Films EU.
“This is also true for our label films line. In fact, by matching the inherent functionalities of our base films with our in-house coat ing technologies, we will be able to provide more and more tailormade solutions to satisfy the growing variety of applications”, adds Simone Baldin, Business Unit Manager, Label Films EU.
“Our mission is to ensure that our products are aligned with Circular Economy principles and answer to our stakeholders’ im portant needs such as Product Protection, Performance and Sus tainability”, concludes Monica Battistella, Product and Sustaina bility Manager. “These three main pillars are at the core of every Ti film solution. In fact, each product line is designed with the highest specifications, characteristics, and benefits, based on the organization’s best practices in product innovation and supply chain optimization”.
ZERES III SERIES: THE EVOLUTION the electric machine with integrated hydraulics.
With more than 1000 units installed the Zeres series has confirmed all advantages that the electric/hydraulic solution can offer to end-users. Today we present the third generation of Zeres injection molding machine: evolution of a reliable and performing product. Overlapping movements, increased extraction force, absolute precision and low energy consumption make the Zeres machine the extremely flexible press for every type of use.
Haitian MM Italy s.r.l. - Via Giuseppe di Vittorio n.56, 25125, Brescia www.hmmi.it
After almost 20 years of presence in the ever-changing environment of the EU-level trade associations within the automotive and transport sector, the members of PlasFuelSys, the European Plastic Fuel Tanks and System Manufacturers Associ ation (sector group of EuPC) decided to extend the scope of their activities and be come the association representing the in terest of the broader category of the plas tic energy storage systems.
These encompass plastic structures for different energy sources, such as fuel, hy drogen, CNG, LNG, biofuels, e-fuels and
battery-electric-based energy for passen ger cars, light-duty vehicles, trucks, and busses.
The functions carried out by the sys tems that, according to the new associa tion’s vision, shall be considered as falling within its new scope, are not limited to storage, but also encompass related usag es, namely supplying, refilling, venting, and thermal management.
Therefore, the association will now op erate under the new name of PlasEnSys, the European Plastic Energy Storage Sys tems Association. It will allocate its advo
Kunststoffexpress Handel GmbH (KX) can look back on 25 years of successful trading. Back in 1997, Marcus Mahnecke, owner and Managing Director, founded a sales agency under this name on the site of the company headquarters in Bielefeld. Today, the company also has a service and logistics center in nearby Löhne, which came on-stream in 2020 and has ware house capacity of over 5,000 tonnes, as well as six sales offices, eight additional forwarding warehouses with up to 20,000 slots and various home offices in the D-A-CH region. With twenty-seven staff and an annual trading volume of 50,000 tonnes, KX is now one of the ten largest distributors in the German-speaking world. The company is divided into the business units Distribution, International Trading, Healthcare, Special Compounds and Reprocessed Products. Its product
cacy efforts to a widened field of expertise by opening its doors to a broadened in dustry representation.
“The automotive and transport sector is currently undergoing significant changes, both from a regulatory and technological standpoint and this enlarged industry co operation is essential in order to foster and accelerate the journey towards the ulti mate achievement of a fully circular econ omy and a concrete preservation of the environment”, said Paul Wouters, PlasEn Sys President and representative of Plastic Omnium within the association.
portfolio includes polyolefins, styrene and engineering poly mers from global raw material manufacturers, compounds from Repsol and Ravago, together with compounds and re compounds produced in-house.
“From the very outset, consistently applying our industry expertise has meant we’ve been able to help our customers select and efficiently process the right materials for their ap plications and that’s been the key to our continuous growth”, said Mahnecke. “One example of the esteem in which we are held is the vote of confidence from the Spanish company Repsol Quimica, which in 2021 entrusted us with distributing its polyolefins for the highly demanding healthcare sec tor throughout Germany. Our aim is accordingly to break through the 60,000 tonne mark in German-speaking coun tries in 2022. Our course is set and we’re looking forward to the challenges ahead”.
Apart from the broad range offered by Repsol Quimica, KX’s polyolefin portfolio also includes PE and PP grades manufactured by Carmel Olefins (Israel), LG Chem and Ducor Petrochemicals (Netherlands). Engineering polymers are also supplied by LG Chem and by Formosa Plastics Cor poration (POM). Kunststoffexpress Prime grades include PA 6, PP compounds, PP GF- and mineral-filled grades as well as electrically conductive and carbon black compounds. Kunststoffexpress Recompounds range from ABS via PE, PP, PS and PP mineral-filled grades to moisture absorbers. In addition to virgin materials, recycled products have been a significant focus for over 20 years. Kunststoffexpress mar kets over 20,000 tonnes of ABS, PS, PP and PE recom pounds every year – a volume corresponding to annual CO2 savings in excess of 35,000 tonnes. This makes the compa ny one of the largest suppliers to this market and is how it contributes to protecting the environment.
PlasFuelSys extends the scope of its activities and becomes PlasEnSys
Mondi, a global leader in packaging and paper, is invest ing nearly € 65 million in three Consumer Flexibles packag ing plants in Europe in order to meet growing customer demand for sustainable pet food packaging solutions. The European pet food market has grown significantly in recent years, driven by a consistent rise in pet ownership. This trend increased during the COVID-19 pandemic and is ex pected to continue for many years to come (Wet pet food demand estimated to grow 5% a year between 2020 and 2025 according to Wood Mackenzie 2020 (PCI).
This project is part of Mondi’s previously announced €1 billion expansionary capital investment programme to ac celerate growth in sustainable packaging and will further strengthen its leading position in the pet food packaging market. Work has already started at Mondi Korneuburg (Austria) and includes investments in new, state-of-the-art machinery and equipment as well as an expanded produc tion area. These changes will lead to a capacity increase, solidifying the site’s position as a market leader in pre-made retort stand-up pouches for wet pet food.
The group is also investing in new, advanced machinery at Mondi Halle and Mondi Steinfeld in Germany, to increase production capacity of sustainable pre-made bag solutions for pet food, as well as home and personal care. This will enable future growth and support customers to switch from multi-layer, non-recyclable packaging to more sustainable
alternatives such as mono-material recyclable stand-up pouches and paper-based pre-made bags.
“We take pride in being an innovative, agile partner for our customers”, says Dirk Gabriel, COO Consumer Flexibles, Mondi. “With this investment, we continue to take the lead in packaging solutions that are sustainable by design, espe cially in the pet food industry”.
This investment also supports our Mondi Action Plan 2030 (MAP2030) sustainability framework which is fo cused on circular driven solutions, created by empow ered people, taking action on climate. With these pro jects, we’re increasing operational efficiency and reducing our own energy consumption while also con necting our production network”.
Sabic, a global leader in the chemicals in dustry, announced a collaboration with Mat tel, a leading global toy company, to incor porate certified renewable polymers from SABIC’s Trucircle™ program across Mattel’s products offering. The first Mattel toy prod ucts to enter the market in 2022 using certi fied renewable SABIC® PP (polypropylene) polymers will be from MEGA™ and Match box, with more to follow.
Heading the initiative will be MEGA BLOKS Green Town, the first-ever toy line available at mass retail to be certified Carbon Neutral. These new construction playsets, including the Grow & Protect Farm and the Build & Learn Eco House, embrace the sustainable material choice and help teach kids green behaviors. From the Matchbox brand, all Action Driver playsets and the Matchbox Recycling Trucks contain SABIC materials, which supports the
brand’s “Driving Toward a Better Future” initia tive, to make all Matchbox die-cast cars, play sets and packaging with 100% recycled, recy clable or bio-based plastic materials by 2030, in line with Mattel’s corporate goal.
Mattel is the first company in the toys mar ket to work with SABIC in a mass balance approach designed to return second-genera tion renewable feedstock into high-quality
new plastic applications. The partnership di rectly supports Mattel’s goal to achieve 100% recycled, recyclable or bio-based plas tic materials in its products and packaging by 2030, and is an important step forward in their transition towards a circular economy.
Sabic’s certified renewable polymers include various polypropylene and polyethylene mate rials derived from second generation renewable feedstock, that are not in direct competition with human food and animal feed production.
Sabic’s certified renewable polymers form part of the company’s Trucircle portfo lio and services for circular solutions. The offering also includes design for recyclabili ty, mechanically recycled products, certified circular polymers and closed loop initiatives to recycle plastic back into high quality ap plications and help prevent valuable used plastics from becoming waste.
The U.S. plastics market continues to show good demand, and although there are difficulties in the supply chain there is increasing interest in safe and durable packaging.
The pandemic, supply chain disrup tions, major resignation, trade ten sions with China, climate change and extreme weather events, rising infla tion, stock market volatility, and the war in Ukraine. Rarely in our lifetime have we ex perienced such a long phase of disruption and precarity. The last time may have been the financial crisis of 2008/09, but it was purely economic and was not further com plicated by the blockade and supply chain problems caused by Covid-19. At least to day, private household and corporate bal ance sheets are largely healthy, in contrast to the situation during the financial crisis 14 years ago.
The North American plastics industry has
not been spared from these problems, but it has held up quite well given the crucial role that plastic products play in everyday life and particularly in vital applications in healthcare. If anything, the pandemic has only served to underscore the value of plastics-even widely vilified single-use plastics-to the safety and health of us all.
“During the Covid-19 recession of 2020, plastics consumption in the United States, fueled by federal aid, remained stable, de spite the fact that there was a decline in employment and capacity constraints dur ing that period,” the Plastics Industry Asso ciation (which uses the name Plastics) based in Washington, DC, said in its “Glob al Trends 2021” report. “The result has been an increase in imports and a trade deficit.”
According to the Association, industry ex
ports fell 8.2 percent in 2020 and imports increased 1.8 percent, with Mexico and Canada remaining the largest export mar kets for the U.S. plastics industry.
In an April podcast, Eric Chewning, a part ner in the Washington, DC, office of con sulting firm McKinsey & Co., offered the following sum mary of U.S. manufacturing and its overall importance to the nation’s economy: “U.S. manufacturing accounts for about $2.3 trillion of gross domestic product (GDP). It employs about 12 million people and supports hundreds of local economies across the country. Now, those headline numbers don’t really capture the outsize impact of manufacturing.
“Although it only accounts for about 11% of
our GDP and 8% of direct employment, it drives 20% of our nation’s capital invest ment, 30% of our productivity growth, 60% of our exports, and over 70% of business R&D. And it also generates important spill over effects that help impact the broader economic activity in related sectors.”
For its part, the plastics industry plays a key role. The Plastics Industry Associa tion’s “2021 Size & Impact Report,” pub lished last year, estimated the total value of U.S. plastics industry shipments in 2020 to be $394.7 billion. The industry directly em ployed 945,300 workers, which was down almost 6% from pre-pandemic 2019. Taking suppliers to the industry (and their upstream shipments) into account, the to tal value of shipments in 2021 grew to $541.6 billion and employment, direct and indirect, rose to 1.55 million.
Despite all these challenges, U.S. plastic products manufacturing rose 4.9% in 2021 from the prior year, according to U.S. Fed eral Reserve data, which was in line with the association’s late-year projection. That number could have been higher, but resin production continued to lag, said Perc Pineda, noting that materials shortag es weighed down plastic products output. Pineda, the group’s former chief economist who stepped down in February after five years in that role, cited Federal Reserve data showing 2021 plastic materials and resin production down by 0.4% –– even more than the 0.2% than the association forecast late last year.
Plastics machinery production last year rose by a robust 16.8% compared with the pandemic-ravaged 2020, and plastics mold manufacturing grew by a solid 9.7% in 2021.
The latest federal data for March 2022 indi cate that U.S. plastics product manufactur
ing and resin production were up 7.6% and 14.1%, respectively, from March last year, according to Pineda, who has a master’s degree in economics from American Uni versity and a Ph.D. in economics from The New School (in addition to master’s de grees in both philosophy and international
management). He served as a staff analyst at the International Monetary Fund and as a senior economist at the Credit Union Na tional Association.
The Russia-Ukraine war, and specifically the U.S. sanctions on Russia, has impact ed the plastics industry in different ways.
As one example, Pineda noted that Rus sia is the seventh-largest supplier of fluoropolymers to the U.S. But, while con cerning, imports of PTFE and other fluoro polymers from Russia amounted to just over 1,666 metric tons, or 5.4% of U.S. total imports of such materials. Nearly half of U.S. fluoropolymer imports come from Japan, India and China, so the impact has been muted.
The Ukraine conflict also has contributed to soaring oil and energy prices, which af fects virtually all manufacturing, including plastics equipment manufacturing. With U.S. trade sanctions stifling iron and steel imports from Russia, the prices of those metals have increased, creating cost chal lenges for machine builders.
Overall, the U.S. plastics machinery mar ket continues to see healthy demand while continuing to experience supply-chain bottlenecks. Business investment spend ing on industrial machinery in the U.S. in creased by 19% in the first quarter of 2022, compared with the same year-ago period. That represents an increase of $46 billion, adjusted for inflation, according to Pineda. However, low parts inventories are extending production times and slowing deliveries.
For the past couple of years, the U.S. plas tics machinery market has benefited from low interest rates and robust demand.
Pineda previously projected plastics ma chinery production growth in the U.S. would be 4.8% this year. But with interest rates now rising and supply-chain issues continuing, he says he would not be sur prised to see that sector’s 2022 production growth closer to 3.5%.
The fourth quarter of the calendar year typ ically sees the biggest shipments of U.S. plastics machinery, and last year’s final
three months was no exception. Its 24.1% quarterly increase in value of shipments was the largest uptick since the COVID-19 lockdown. Pineda says that he is expect ing a single-digit increase in U.S. machin ery shipments this year.
Soaring energy prices and overall inflation are dampening U.S. consumer sentiment. The University of Michigan’s Survey of Consumers reported in preliminary results that consumer sentiment in May declined by 9.4% from the previous month, revers ing April’s gains. Consumers’ assessment of their current financial situation relative to a year ago is at its lowest reading since 2013, with 36% of consumers attributing their negative assessment to inflation. Buying conditions for durables hit its low est point since the question began appear ing on the monthly surveys in 1978, again primarily due to high prices, U of M report ed. The median expected year-ahead in flation rate was 5.4%, little changed over the last three months, and up from 4.6% in May 2021.
Plastics find use in virtually every end mar ket, with packaging and building and con struction among the biggest volume con sumers of resins. Automotive, while less in volume, has an outsize impact on the plas tics sector, given that it is often a proving ground for innovative and demanding ap plications. Plastics are critical to the medi cal and healthcare industries and offer val ue-added opportunities for suppliers who can meet the stringent regulations. The same holds true for the electrical and elec tronics markets, which also are constantly dealing with miniaturization and high-heat management, in addition to aesthetics and durability.
The pandemic spurred a notable boost in home shopping and e-commerce, to in clude food and grocery delivery services. This helped to accelerate interest in safe, durable, clear, lightweight and thin-wall plastic packaging options. Plastics fare well when compared with heavier or more fragile solutions, such as glass.
Companies continue to be urged to improve sustainability by reducing packaging waste, but packaging companies acknowledge that they are still lagging behind
A new Coresight Research survey, pub lished in mid-May, reveals that 54.3% of U.S. consumers bought groceries online in the past 12 months. While a hefty number, it did represent a decline of 4.7% com pared to last year. The report –– “US On line Grocery Survey 2022: Assessing Trends in Shopper Behavior, Quick Com merce and Meal Kits” –– also notes a slight dip of 2.6 percentage points in consumers who say they are planning to buy grocer ies online.
The survey noted that the percentage of online grocery shoppers who collect their own order rather than wait for delivery (42.8%) rose 5.2 percentage points, as consumers try to dodge higher delivery fees and surcharges.
Sustainability continues to command the attention of brands and packaging com panies. Packaging World reported in midMay that, according to recent research by the Packaging Machinery Manufacturers Institute (PMMI), innovation in that sector is not keeping pace with sustainability de mands.
Companies remain under massive pres sure to improve sustainability by reducing packaging waste, but the study –– PMMI’s “2022 Shaping the Future of Packaging Operations” –– says that packaging oper ators recognize they are somewhat be hind the curve in this regard and are aware of the need to catch up. “However,” the article notes, “a true industry shift will require technology breakthroughs and significant capital investment. One of the major barriers is that sustainable packag ing materials often have narrower toler ances than virgin or highly engineered standard materials”.
As a result, the study concludes, “the de sire from brands and consumers doesn’t quite align with what’s currently feasible.” While reducing the size of packaging re
mains an easily achievable objective, insti tuting industrywide change has always proven more challenging to achieve. Meanwhile, R&D efforts continue apace to boost the use of recycled content, incorpo rate more biopolymers, develop reusable packaging models, and create more highly functional monomaterial package struc tures that help to facilitate recycling.
The Consumer Technology Association (CTA), which organizes the huge CES con
and smart TVs, as well as connected prod ucts such as sports and fitness equipment. Nearly all of these incorporate plastics in some form or another.
Digital health devices also continue to grow in popularity, to include connected devices that monitor mental and physical health and manage chronic disease, as well as telemedicine and all types of wear ables. CTA said its research indicates that 52% of U.S. adults say they are likely or very likely to use health tech in the future to improve their overall well-being.
sumer electronics show in Las Vegas each year, projected in January that U.S. con sumer technology revenue would increase by 2.8% in 2022. It predicted that the in dustry’s retail sales revenue this year would exceed $505 billion, marking the first time ever it will top the half-trillion-dollar mark. This increase is over and above the 2021’s year-on-year growth of 9.6% and reflects a 38% leap from the $365 billion in sales reg istered in 2017.
CTA reported that some of the fastest-grow ing products include many “smart” prod ucts –– smart appliances, smart light bulbs, smart doorbells, smart speakers
The U.S. vehicle industry has taken a beat ing, for all the above-noted reasons, com pounded by a critical shortage of the sem iconductor chips needed in every vehicle. Automakers canceled semiconductor or ders in the early stages of the coronavirus pandemic. Then, once the economy be gan to improve, they struggled to get ac cess to those materials because overseas chip suppliers had already allocated them to consumer electronics manufacturers.
Analysts predict semiconductor invento ries may not return to pre-pandemic levels until at least 2023, according to CarsDi
In 2022, as every three years, K in Düsseldorf will once again be the most important information and busi ness platform for the global plastics and rubber industry. Nowhere is the internationality as high as in Düssel dorf. Exhibitors and visitors from all over the world will come together and take advantage of the opportuni ties from 19 to 26 October this year not only to demonstrate the indus try’s capabilities and present innova tions, but also to exchange views on the situation of the plastics and rub ber industry in the various regions of the world, discuss current trends and jointly set the course for the future.
rect, an American online automotive re search portal and car buying service. Many chip suppliers are located abroad, and it hasn’t been easy for the U.S. to build more semiconductors domestically. While there are efforts by the government to get this to happen, it will take time.
The National Automobile Dealers Associa tion reported that new light-vehicle sales in
the United States increased to 14.3 million units on a seasonally adjusted annual rate (SAAR) in April 2022 from March’s sales rate of 13.3 million units. Other reports pegged this year’s SAAR at closer to 14.7 million units -–– still a far cry from the April 2021’s annual rate of 18.6 million units. There’s no question that electric vehicles (EVs) are growing in popularity and com manding a huge share of automakers’ at tention and R&D spending. But opinions diverge on how quickly they will be adopt ed. At the big CES 2022 show in Las Vegas in January, two of the largest automotive suppliers offered their opinions.
Technology, inflation and supply-chain challenges aside, the U.S. plastics indus try (and broader manufacturing sector) has a potentially more intractable problem –– a shortage of skilled workers to keep its
plants humming. The pandemic caused many to re-evaluate their lives and careers, leading some to quit their jobs and others to pursue different paths.
In addition to the U.S. having an aging population, it has proven difficult to attract, train and retain talent. Many of the new en trants to the labor market lack skills for, and/or are averse to pursuing a career in manufacturing, notes Pineda.
“In a tight labor market, even economic in centives such as higher wages and bene fits are not guarantees of attracting and retaining skilled workers. Increasing skilled labor supply would require serious com mitment from the industry to implement an apprenticeship program that’s consistent throughout the country and accredited by the U.S. Bureau of Labor. ... Any policy pro posals to revive American manufacturing,” he asserts, “must include a workforce sup ply and development component”.
According to CarsDirect, analysts predict semiconductor inventories may not return to pre-pandemic levels until at least 2023
Industria Macchine Automatiche Computerizzate
IMAC CUTTING SOLUTIONS divisione di IMAC TECNOLOGIE SRL produce:
Taglierine in volata da utilizzare sia in linea di estrusione sia di ripresa per i settori medicale ed industriale. Classe energetica A++, funzione taglio in continuo mono lama 2.800 tagli al minuto, funzione taglio con multilama/bi-lama 5.700 tagli al minuto, velocità di estrusione fino a 150 m/min., funzione taglio sinusoidale.
Taglierine a ghigliottina controllate da asse elettrico con possibilità di taglio angolare +/- 60° Taglierine a ghigliottina controllate da asse pneumatico con possibilità di inseguimento
Le nostre macchine automatiche di precisione tagliano materiali plastici, guaine, tubi e profilati dalle differenti forme (con peso da 1 gr/m sino a 2.000 gr/m) e con diversi tipi di materiali: PVC-PE-PP-PA12-PC ABS-PC/ABS-PS-NORLYL-EVA-POM-POLIURETANO PUR-GOMMA TERMOPLASTICA-PP/EPDM-SEBS.
Altezza di taglio da 920 a 1.200 mm, taglio destroso o sinistroso a scelta.
www.imaccuttingsolutions.com
Via Nino Bixio, 7 - 20835 Muggiò (MB) Tel.+39.039.5788147- Fax +39.039.5788148 c.f./p.iva 03823070242 - Email: info@imaccuttingsolutions.com
The K edition 2022 this year is even more special, and in addition to celebrating its return, in the midst of the difficulties that the whole world is going through, the benchmark trade fair for the plastics and rubber industry celebrates its 70th anniversary marked by a path of growth and evolution that this edition fully reflects.
K2022 is the world’s most relevant trade fair for the plastics and rub ber industry. For this edition wich will be held from 19 to 26 October around 3,000 exhibitors from 61 nations are ex pected and the Düsseldorf Exhibition Cen tre is completely booked.
The ranges on show at K 2022 include the segments machinery and equipment, raw materials and auxiliaries as well as semi-finished products, technical compo nents and reinforced plastic products. “K
in Düsseldorf is not only the performance barometer for the industry and its global marketplace for innovations, but also pro vides orientation, sustainable economic impetus and forward-looking trends as well as concrete approaches to solutions”, says Erhard Wienkamp, Managing Director at Messe Düsseldorf.
October 2022 will be the perfect timing for the number one fair because the ef fects of the global pandemic have also hit many enterprises from the plastics
and rubber sector as well as their cus tomer industries. Therefore, there will be an enormous demand for personal ex change and re-orientation on a global scale in the international plastics and rubber industry.
K in Düsseldorf also always addresses the current challenges of our day and age and specifically of your industry. This is why such subjects as sustainability, re source savings, circular economy and digitalisation, which gathered momentum at K 2019, will also feature among the “hot tickets” of the trade fair at both the exhib itors’ stands and side events. Worth a special mention here is the Special Show entitled “Plastics shape the future” as well as the Science Campus as a forum for sci ence and research.
The same year that saw Queen Elizabeth II ascend to the throne, the first artificial heart valve implanted in the USA and the musi cal “Singin’ in the Rain” inspire millions at the cinema, history was also made in Ger many with the inaugural edition of K, host ed in Düsseldorf from 11 to 19 October 1952. At that time nobody suspected this event only just taking off would develop into the world’s leading trade fair for the plastics and rubber industry. Today, K in Düsseldorf can look back on a success story of 70 years. It is the most rel evant information and business platform of the plastics and rubber industry world wide. Its position as the leading trade show for the entire industry, where theme leadership and innovation go hand in hand to pave the way for visions for the future, is undisputed. On no other platform is the in ternationality as high as in Düsseldorf. However, K in Düsseldorf also started small once: the debut event “Wunder der Kunststoffe” (Miracles of Plastics) in 1952 registered 270 exhibiting companies – ex clusively from Germany. They occupied approximately 14,000 square metres of net exhibition space.
At the premiere 165,000 visitors marvelled especially at the colourful consumer goods
exhibited by plastics processors. Because from 1952 to 1959 K Düsseldorf was purely a showcase of the German industry. Any inter ested visitor, be it a layman or specialist, was admitted to visit the trade fair. Major attrac tions on show were products designed to make life more beautiful and convenient. To day, we smile at the advertising of that time, which was also aimed at the “modern house wife” and introduced her to such post-war achievements as trendy PVC raincoats or sheer nylon stockings - aesthetic epitomes of the economic miracle.
The more the plastics industry specialized and high-tech plastics for special solutions in electronics, medicine, automotive or aer ospace attracted attention beyond stand ard polymers, the more specialists visited the trade fair. In 1963 the break was made: K in Düsseldorf became a special-interest only trade fair of international standing. Since then it has maintained its position as a leading global trade fair for the entire industry. 2019 saw over 220,000 trade visi tors from almost 170 nations travel to K on the Rhine River.
Messe Düsseldorf is coming up with a new technical highlight: HEPA filters. These high-efficiency particulate air filters intro
duce clinically clean air into the halls while at the same time reducing heating and cooling energy consumption. By the end of June 2022, the complete Düsseldorf Exhi bition and Congress Centre will be equipped with HEPA filters.
It is the most effective air cleaning technol ogy currently available: HEPA filters re move 99.9% of viruses, bacteria and other particulates from the air and release the cleaned air into the room again. These high-efficiency filters make for highest air quality in ORs, at Intensive Care Units and now also at Messe Düsseldorf and Düssel dorf Congress. Halls 1, 9 to 17 as well as Congress Center Düsseldorf CCD have al ready been refitted. 80% of the EUR 1.4 million invested were paid by the Federal Ministry for Economic Affairs and Climate Protection as part of a funding programme. “Our new HEPA filters help to ensure that we can offer all guests the greatest possible protection during our trade fairs”, says Wolf
ram N. Diener, President & CEO of Messe Düsseldorf. “In combination with our high-performance ventilation system, our voluntary hygiene measures, our spacious premises and halls, we reduce the infection risk to a minimum. After two pandemic years and a period of intense digital communica tion participants can feel safe when net
“HEPA filters reduce the heating and cool ing energy consumption of our ventilation systems and enable their energetically sen sible operation”, remarks Bernhard J. Stempfle, Managing Director Finance and Infrastructure. “When outside temperatures are low we can mix the outside air supplied with warm hall air, thereby reducing the heating requirements and still achieve clini cally clean incoming air. This means that the HEPA filters also make an important contri bution to sustainable trade fairs.”
Additional infection protection is not only provided by the HEPA filters and ventilation systems but also by Messe Düsseldorf’s voluntary hygiene measures. The trade fair company continues recommending at tendees to wear medical face masks and keep a 1.5 m distance from other persons on the fairgrounds.
again, the central point of contact for the critical exchange of information, thoughts, and opinions is represented by the Special Show „Plastics shape the future“ in hall 6. The focus of the special show under the auspices of Plastics Europe Deutschland (PED), the plastics producers’ association, and Messe Düsseldorf will be on the three ground-breaking hot topics of K 2022: cli mate protection, circular economy, and digitalisation.
working, initiating business deals and expe riencing innovations in person again”.
HEPA filters complement and relieve the al ready powerful ventilation systems at Messe Düsseldorf. The fully automatic system with 60,000 measuring points safeguards optimal air quality and supplies the halls with ten mil lion cubic metres of fresh outside air via ten kilometres of ventilation pipes every hour.
Every three years, and this coming autumn again, the world of plastics meets in Düs seldorf: from October 19 to 26, 2022, the world’s leading trade fair K presents new products and innovations from all sectors of the industry – from production to pro cessing, to mechanical engineering. Once
“These are really exciting times: in this year’s K special show, we make it clear where our industry shifts into the turbo mode in terms of greenhouse gas neutrali ty and circularity”, says Ingemar Bühler, Managing Director of PED. “But we also listen carefully to what critical experts tell us and which solutions be proposed to us”. The centrepiece of “Plastics shape the fu ture” is provided by the theme days with speeches, keynotes, and panel discussions on the three K hot topics climate protection, circular economy, and digitalisation. At the start of the trade fair on Wednesday, October 19, 2022, key topics and challenges of the industry will be directly addressed on the K-Forum. The following theme days also fo cus on the plastics industry’s concrete paths towards greenhouse gas neutrality, or on plastics as enablers of the clean energy tran sition. This will make sure that the special ex hibition will enrich the extensive and socially highly relevant exhibition offering of K 2022.
Start-ups are young, creative, flexible and particularly stand out with their innovative solutions. This why K 2022 trade fair offer a dedicated presentation area to newcomers specialised in the development of innova tive products and solutions revolving around plastics and rubber. The start-up zone can be found in Hall 8b of Düsseldorf Exhibition Centre.
At K 2022 Amaplast will have a stand dedicated to sup port the exhibiting Italian companies, provide a point of reference for the industry, distribute the magazine MacPlas, and promote the nineteenth edition of PLAST (Milan 5-8 September 2023), whose organizational machinery will shift into high gear immediately after the German exhibition. In the mean time, over 30,000 square metres of exhibition space have already been reserved by the more than 600 exhibitors who have already registered.
Per tradition, the Italian presence at K will be second only to that of the host country at the world’s most important fair for the sector and will mainly consist of manufacturers of machinery, equipment, aux iliaries, and moulds with over 250 exhibitors in this segment, more than half of them members of the Amaplast trade association.
The Italian companies will offer a complete overview of the most advanced Italian-made technology reflecting Industry 4.0 princi ples, with solutions for interconnection, energy efficiency, and pre dictive maintenance. More than 70% of Italian production of plas tics and rubber processing machinery is exported and Germany has been the n. 1 destination market for decades (as well as main partner for imports), both regarding supplies to final customers and supplies of components, auxiliaries, moulds to be integrated into complex systems built by major German brands, demonstrating the respect they have for Italian technology. In 2021, exports to Germany in this sector approached a value of 380 million euros, representing a 13% share on the total and a 10% rise over 2020.
Last year, the entire EU absorbed 45% of Italian exports, followed by North America with 17% and the Far East with 12%. Overall, on the basis of results from the second National Survey by the MECS-Amaplast Statisti cal Studies Centre, the Italian plastics and rubber processing machinery in dustry is composed of over 400 companies (with 13,000 employees) that produced revenues of over 4 billion euros in 2021, representing a 12% increase over 2020.
Our “customer oriented” philosophy guides us in offering high innovative solutions able to optimize production processes and energy efficiency, to reduce carbon footprint and treat recycled materials, ensuring digital connection throughout the produc tion chain.
From this perspective, Sustainability, Technology and Digitali sation are the pillars that set us apart in the plastics process ing industry.
Hall 11 Stand H56 Stand H66
the most innovative integration of IML tech nology and stack-molding automation, capa ble of doubling production while making it in creasingly sustainable.
Anew concept of automation the one proposed by Campetella Robotic Center, renowned Italian designer and producer of industrial robots and com plex automations for the plastics injection molding industry, this year celebrating its 125th anniversary.
Founded in 1897, Campetella proudly traces its success back to the passion that has al ways guided them and which, fuelled over time throughout five generations, now distin guishes the company throughout the world.
Campetella offers a wide range of high-per formance top-entry and side-entry robots, which stand for their extreme precision, speed and reliability. These are key features in the food-packaging world, a crucial indus try to Campetella that, at K 2022, will exhibit
Sustainability is at the base of the Campetella corporate culture. All Campetella automa tions are equipped with a dynamic vacuum management system capable of reducing compressed air consumption up to 60% if compared to traditional gripping systems. Furthermore, the particular architecture of the mutually connected drives allows for the re covery of the braking axles’ kinetic energy, which is therefore available for the axles in motion.
The Campetella stack robots offer unques tionable advantages in high productivity sec tors, optimizing costs while respecting the environment. Given the same number of cavi ty for each molding cycle, the IMM tonnage almost halves if compared to traditional sys tems, thus reducing energy consumption and related CO2 emissions into the atmosphere. More productivity in less space. This is the greatest benefit brought by the synchronized production of both containers and lids provid
ed by the new Campetella automation sys tems. Both at the Campetella and Demag’s booths, visitors will have the opportunity to check out the new Modula W X-Series, core of a fully automated system managing the IML production of margarine tubs. Born to fit IMMs up to 4.500 kN clamping force, this highspeed side-entry robot boasts a peculiar and innovative “W” structure that allows it to oper ate on a 2-level stack mold, which is also spe cifically designed to double productivity. Once extracted from a 4 + 4 cavity mold, the tubs are picked by a SPIN and stacked with the opening facing downwards in or der to ensure maximum hygiene. The robot is equipped with vertical feeders for 5-sid ed labels, featured by efficient servomo tors and designed to exploit the space in the vertical direction. Its carbon fibre arms reduce vibrations, thus ensuring excellent label positioning, while an integrated vision inspection system safeguards the perfect quality of the stacked tubs.
At the Krauss-Maffei booth, Campetella will show off its SPIN, in charge of assembling and palletizing foldable fruit and vegetable plastic crates. Equipped with three rotary axes (shoulder, elbow, and wrist) and a linear axis for vertical movements, its high dexterity makes it perfect for fast palletizing and pick & place operations.
Finally, Toyo will host their best-seller GS2 X-Series, renowned all over the world for its quick and sharp movements. An uncompro mising model for ultra-fast take-out applica tions, specifically designed for the food-pack aging industry. Ultra-performing servomotors combined with innovative materials and con struction technologies ensure record-break ing acceleration for operating cycle times up to 2.5 seconds.
Campetella also has a long historical ex perience in coiling machinery for 25-50 mm diameter extruded irrigation pipes and water hoses.
Campetella will guide the visitors through their most advanced automation, result of a sustainable innovation based on the customer’s needs.
At K 2022, Covestro will highlight the possibilities of particularly sustaina ble plastics for the world and tomor row’s growth markets. To this end, the compa ny will soon be presenting new products and materials for many key areas that support the circular economy and climate neutrality at the world’s largest plastics trade show. In this re gard, Covestro sees itself as an industry pio neer and is focusing above all on future-ori ented, creative partnerships. International media now got a foretaste of the trade show appearance in October at a press confer ence in Düsseldorf, Germany.
“Mankind is facing enormous challenges. In addition to acute crises, we need to over come long-term challenges such as protect ing the climate, nature and resources and thus safeguarding our livelihoods”, said CEO Markus Steilemann. “This can be achieved if business and society consistently orient themselves towards the circular economy. Plastics are indispensable on this long jour ney, and Covestro is pleased to contribute particularly sustainable new products and materials to this end, tailored to the customer needs of today and tomorrow. Together with our partners, this is how we intend to seize the immense opportunities for sustainable growth.”
Under the motto “Crafting Connections With You”, Covestro intends to establish new col laborations with customers and partners and
strengthen existing ties at booth A 75 in Hall 6 at K 2022, as well as on a digital platform. “Collaboration along key value chains in par ticular is of great importance for the vision of a full circular economy to succeed”, said An drea Maier-Richter, Global Head of the TPU Business Entity. “With our more sustainable developments, we support our customers and partners in facilitating their transition to the circular economy and achieving their own climate goals”.
To make circular solutions in the product port folio even more recognizable to customers in the future, Covestro has developed the “CQ” concept. The brand suffix stands for “Circular Intelligence” and indicates the alternative raw material base for the company’s products if it is at least 25 percent. Among the first “CQ” products is Desmodur®CQ. Polyurethane foams based on Desmodur®CQ are used, for
example, in upholstered furniture, mattresses and thermal insulation.
Moving away from fossil resources
Covestro primarily uses mass-balanced, renewable precursors and plastic waste as alternative raw materials, as well as green electricity. To realize its vision of a circular economy and achieve its ambitious climate targets, the company is also focusing on the future supply of “green” hydrogen and the development of innovative recycling technologies.
All these measures help conserve fossil re sources and avoid CO2 emissions. In the long term, Covestro aims to offer all its prod ucts in a climate-neutral1 version. By 2030, the company plans to invest around one bil lion euros in circular economy projects. To achieve net zero emissions, Covestro also expects to invest between EUR 250 million and EUR 600 million by 2030.
“Covestro is taking a committed approach here: using various approaches, we can spe cifically recover the raw materials we need for the production of our plastics”, SAID Her mann-Josef Dörholt, Global Head of the Per formance Materials segment. “In addition to the established mechanical recycling of poly carbonate and thermoplastic polyurethane, we are focusing primarily on chemical recy cling for this purpose”.
With the circular economy as a global guiding principle, humankind can protect the climate, nature and resources while achieving sustainable growth. Covestro will showcase the highlights from the areas of alternative raw materials, innovative recycling technologies and renewable energy.
At K 2022 Haitian International increases its exhibition space, which will host five applications in the plastics industry: medical, commodity, automotive, logistics and packaging.
Whereas in italy, with the new Brescia location, Haitian MM Italy is consolidating its role in the distribution of Haitian and Zhafir branded technologies.
By Alessandro BignamiThe Brescia plant will stably house plastic injection molding machines and die-casting plants. Thus Hai tian MM Italy, the company founded at the beginning of the year by Davide Bon fadini to deal exclusively with the distri bution of Haitian Group technologies in Italy, will make the new Brescia location an important logistics hub for Haitian’s European strategy. Thus continuing to share a growth path that has lasted more than 10 years.
Davide Bonfadini, how have the first months gone for Haitian MM Italy, which was born in January and shortly after settled in its new Brescia headquarters?
It is a phase of great changes. A key step has been the move to the new 4,000-square-meter facility, which will be dedicated to the technologies of all the divisions of the Haitian partner: not only the plastic molding machines but also the die-casting plants, which we are starting to import, and in a future per
A bigger booth, more exhibits, more room for smart solutions: At its almost 700 sqm booth in Hall 15/A57, the global market leader will showcase the benchmarks of its broad technology spectrum for a wide range of applications in key sectors of the plastics pro cessing industries. Besides two European machine premieres, Haitian International will also present new developments and strat egies within the Haitian Group at K 2022.
Under the motto “Smart Technologies – Flexible Integration – Sus tainable Solutions,” Haitian International is clearly positioning its Zhafir and Haitian brands for the future and, together with various partners, will showcase live applications from different industries and application areas. Haitian International will present a total of five exhibits at K 2022. The broad portfolio of electric series from Zhafir Plastics Machinery – whether as an all-electric solution, with integrated hydraulics or as a hybrid solution – will be represented by three machines.
Standardized interfaces and open system integration are the fun damentals for maximum flexibility in terms of connectivity. Thus, Zhafir and Haitian machines offer processors almost unlimited freedom in their choice of integration partners. Accordingly, sever al system partners will be integrated into the machine concepts at K 2022. In the MES area, in addition to Haitian Smart Solutions’ own “GoFactory”, another MES partner will be presented specifi cally for the European market. All 5 exhibits will be connected to both systems.
Energy efficiency has always been a key aspect in the development of all Haitian machines. In this regard, sister company Haitian Drive Systems confirms its value as a co-innovation driver by developing and providing energy-efficient drives. Since 2006, these are used as standard in all machine series of the Zhafir and Haitian brands.
Medical: An electric Zhafir Zeres Med Series with 1,200 kN and medical package, will demonstrate an economical, partial clean room solution made from PP with a laminar flowbox from Petek Re inraumtechnik.
Commodity: An electric Zhafir Zeres Multi Series with 3,000 kN, presented as an R-version (piggyback) will be integrated into a pro duction cell with in-house robotics of the Hilectro brand. The ZE-M produces a tape measure housing made from ABS/TPE.
Automotive: The electric hybrid Zhafir Jenius Series with 3,600 kN, is producing an automotive part that is removed with a “Success 33” from Sepro.
Logistics: A servo-hydraulic Haitian Jupiter with two-platen technol ogy and 4,500 kN produces a fruit box made from a material com pound HDPE and TetraPak recyclate. The application is integrated into a manufacturing cell with in-house Hilectro robotics.
Packaging: The servo-hydraulic Haitian Mars K Series with high in jection performance of up to 1,000 mm/s is celebrating its premiere in Europe. It will produce a food container with IML, integrated into an automation system from Hilectro.
spective also the CNC machine tools. At the moment we plan to stock about 20 machines for the plastics industry, with the possibility of mold trials, and 10 die casting plants on site. One area, on the other hand, is dedicated to the storage of spare parts and accessories.
So far, how do the results of 2022 com pare with recent years?
The numbers are certainly not what they were last year, when we experienced a
real boom in sales, with 540 machines installed only in Italy. We are back to a normal pace, as is the whole industry, repositioning ourselves on the results before the 2021 record, so around 300 machines. Apart from that, 2022 is not going badly at all. Now more than any thing else it is important to understand, given the international situation, what scenarios we will see in the coming months in Italy and throughout Europe. However, we continue to be confident.
Where does your confidence come from?
The tax breaks of the Industry 4.0 plan are maintaining their driving effect, thanks to the promulgation in 2022 of the Transition 4.0 tax credit. But what gives us confidence above all are the various pluses that Haitian’s technology and service offer. For example, the pres ence in the range of the Zeres series electric press that has achieved such outstanding performance that it ac counted for 60 percent of last year’s ex traordinary sales. The product is praised for both production performance and energy efficiency. Haitian’s electric model can reduce consumption by more than 60 percent compared to a hydrau lic press. And we know how vital this saving is today. An additional competi tive advantage of the Chinese manufac
turer, which seems more crucial than ever in these times, concerns delivery times. Haitian constantly has about 200 machines on hand, either located at its headquarters in China, at its site in Ger many or in transit between logistics hubs. This allows the customer to start the machine in production often within a few weeks, whereas, in today’s market, it can take even a year from order to deliv ery. In our case, for example, in July we collected orders for a 650-ton injection molding machine and a 550-ton 2-deck machine, and by mid-September we had already delivered them, despite the August closures. In short, these pluses
make us think that even in the face of any market contraction in the coming months, we will not lose our shares, in fact perhaps expand them. Meanwhile, for 2023 we already have several deliv eries planned.
Has Haitian followed you closely in the birth of this Italian project?
Of course, also because it is a choice made together, sealing an important path of growth that has seen us estab lish ourselves as the leading distributor of Haitian machines in Europe. It’s not a coincidence that we are the only ones in the world who can use the Haitian brand in our own business name.
How are the many ongoing emergencies affecting your business: from energy to inflation to supply chain difficulties?
Until the summer, in fact, demand con tinued to be high, the economic momen tum of the industry was not sapped by the international problems. Clearly, everyone now in Europe is trying to fig ure out what will happen in the fall, as these crises look set to continue.
Will you also be present at K 2022 as Haitian MM Italy?
We will be at the Haitian Germany booth. With about 20 people including agents
ways, we will be dedicated to visitors from the Italian market. For us, the K is a must-attend event. We only hope that the anti-Covid measures still in force on foreign arrivals will not lower the internationality rate that is the main strength and attraction of the K. Lastly, we are proud of the fact that, among the machines exhibited by Hai tian in Düsseldorf ( see box on the previ ous page, ed. ), there will also be an im portant new product for the medical sector, the Zeres Medical: a project that has seen our company collaborate alongside the Chinese manufacturer in order to obtain in Italy the certification issued by the PQE company, valid for the whole world, for cleanroom installation.
2022.
The K 2022 fair will be a showcase for RadiciGroup High Performance Pol ymers’ sustainable and innovative solutions. The goal is to use real cases to demonstrate how the Group can be a part ner customers can count on whenever they have to make environmentally friendly choices, and whenever they want to offer safe, reliable, traceable and high-quality products for sustainable projects. Their new products can be developed together with the Group from start to finish. This is why the RadiciGroup stand gives space to Renycle®, a brand identifying engi neering polymers made with a variable per centage of post-industrial or post-consumer polyamide recovered by mechanical recy cling. Careful selection of raw materials is essential to ensure minimal measured varia bility of final product characteristics among the various production lots. In addition to physical, mechanical and electrical charac
terizations, the Group provides environmen tal impact parameters for its materials in comparison with those for traditional prod ucts of fossil origin (LCA). All this enables customers to make a reliable quantitative assessment of the environmental benefits obtained by using Renycle.
In the area of product sustainability, Radici Group is relaunching its partially bio-based PA610 range of materials, which may be a valid alternative to polymers of fossil origin in many sectors (such as air, fuel, oil and
water ducts, heating and sanitary system components) where high chemical resist ance and dimensional stability are required. Moreover, it is important to mention the Group’s commitment to designing new ma terials that comply with the strictest stand ards and contribute to improving the ther mal performance of buildings and making solar panels more reliable in the long run.
In the electric mobility sector, product light weighting and safety are the main drivers guiding the specification of new proposals. Noteworthy is the success achieved by the Group in designing orange colour materials for high-voltage applications.
For the water, heating and sanitary sys tems sector, the Group has a range of products approved for contact with drink ing water, among which some new items that the Group is planning to introduce to its customers.
Lastly, at K 2022, actual metal replacement case studies will be illustrated by our CAE team, whose competence ensures that no risks are presented.
Renycle recycling technopolymers
In the electric mobility sector, product lightweighting and safety are the main drivers guiding the specification of new proposals
Sustainability, performance and safety will be RadiciGroup’s three keywords during K
During the fair, the company aims to demonstrate its expertise through customized solutions and high-quality products.
At K 2022, Coperion and Coperion
K-Tron will be presenting a variety of new and ongoing developments at their Booth B19 in Hall 14 that will mark edly increase the efficiency of plastics com pounding processes, help boost conscien tious resource handling while at the same time achieving very high product quality. Moreover, the company is creating a space dedicated to the forward-looking topic of “Plastics Recycling”. Coperion will be ex hibiting an entire production line for recy cling polyethylene terephthalate (PET) at their booth within the VDMA’s Circular Econ omy Forum, a pavilion on the open-air fair grounds (CE09). Exhibits will encompass bulk solids handling, feeding, extrusion, and pelletizing, all representing Coperion’s advanced expertise in numerous plastics recycling processes such as chemical recy cling, multilayer film recycling, and upcy cling. Trailblazing new developments from Coperion, such as the ZS-B MEGAfeed side feeder that enables plastic film and flake re
cycling in very high throughput dimensions, will be center stage at the Coperion Recy cling Pavilion. Another highlight at the Co perion booth will be the STS Mc11 series laboratory extruder with a 25 mm screw di ameter. It stands out with its simple design, user friendliness and easy cleaning. Its Do/ Di of 1.55 and specific torque Md/a3 of 11.3 Nm/cm3 allow for safe scale-up across the entire STS Mc11 series. The STS 25 Mc11 will be exhibited with a Coperion K-Tron K-ML-SFS-KT20 twin screw feeder. Moreover, the new, preconfigured ProRate PLUS feeder line will be available to view in all three available sizes: small, medium, and large. This continuous gravimetric feeder from Coperion K-Tron is very robust, and thanks to its good price-performance ratio is an economical solution for reliable feeding of free-flowing bulk materials. The SP series dual bearing strand pelletiz ers have been given a comprehensive facelift; Coperion’s SP340 model will repre sent this development at the K booth. In comparison to the previous model, the new SP strand pelletizer allows even faster reci pe and color changes. The cutting chamber works with absolutely no dead space;
thanks to its quick-release function, the cut ting unit can be swapped out quickly and easily. The pelletizer’s interior has improved accessibility and is very easy to clean. One further highlight of Coperion’s showing at K 2022 will be the ZXQ 800 rotary valve. This high performance valve, which works with especially low gas leakage, was devel oped by Coperion especially for powder in take into pneumatic conveying lines at up to 3.5 bar. Thanks to its enormous capacity, it is very well suited for systems planned for polyolefin manufacturing in the future.
Plastics recycling is the focus of compre hensive development projects at Coperion. The company will show the results of these projects at K 2022 in its pavilion on the open-air fairgrounds (CE09) within the VDMA Circular Economy Forum. There, Co perion will present its combined process solutions and technologies for the economi cal recycling of various plastics while achieving the highest levels of product quality. At the center will be a system built around a ZSK 58 Mc18 twin screw extruder configured for manufacturing high-quality PET using recycled materials.
For feeding voluminous flakes and fibers (PET and other plas tics) efficiently into the ZSK twin screw extruder, Coperion will show the SWB300 Smart Weigh Belt Feeder with a S100 single screw pre-feeder, as well as the new ZS-B 70 MEG Afeed side feeder.
Coperion will present its technological innovations for improving plastics production, as well as dealing with recycling-an increasingly valuable contribution to the energy turnaround.
Passion, ideas, values and people char acterize Moretto story, a story of relia bility and experience. Who chooses Moretto can rely not only on product quality and process optimization, but on a partner who puts the customer and his needs at the first place; able to provide a quick, detailed and concrete response that allows to increase the value and obtain tangible results in terms of technology, productivity and energy savings. A success that stands out for its ability to con stantly innovate by taking up the challenges of our time. An approach that distinguishes also the K fair, the leading event for the plastics and rubber industry that continues to attract exhibi tors and visitors from all over the world. The 2022 edition themes – digitization, climate change and circular economy – are familiar to Moretto and guide the company in providing specific solutions for the smart factory that en sure energy consumption containment and able to process not only virgin raw material, but also PIR and PCR ones.
Moretto is recognized all over the world for the quality and reliability of its solutions. Products conceived, designed, developed, assembled, tested and improved in the Italian headquarters with obsessive attention to detail.
“To be competitive on the market, it is not suffi cient to be a good manufacturer, it becomes essential to supply functional, flexible, cost-ef fective and environmentally friendly equipment that offer the operator a user-friendly experi
ence”, says Renato Moretto, President of the company. “What moves our business activity is the certainty to offer a machine realized ac cording to the customer needs, involving him in the study of it. When a product is placed on the market it must leave a mark”.
To achieve this, it is necessary to invest in inno vation, focusing on research and development of new technologies. Being innovative means providing more competitive solutions, being pi oneer in the sector, raising a challenge every day. Moretto responds to this need with a dedi cated R&D department with cutting-edge tools and highly qualified personnel able to simulate processes and dynamics for the design of ex clusive and customized solutions that antici pate market needs. 168 patents prove the com pany willingness to innovate with exclusive products that represent a must on the market.
Moretto has faced the issues of sustainability
and energy saving for several years when it was realized that after raw materials the sec ond expense cost was energy. In the following years, the need to work in the direction of the circular economy was consolidated in order to protect the planet and reuse plastic materials in several production cycles. From this point of view, the market is very demanding in terms of skills and services and the processors are more and more looking for advanced equip ment able to work not only with virgin materials but also with high percentage of recycled ones. Global regulations and events push for an increase of use of these materials and their enhancement.
“Our customers are more and more sensi tive to the environmental issue. To satisfy their competitive and sustainable needs it is essential to invest in research to develop new technologies that guarantee efficient and low energy consumption production processes”, says Silvia Moretto, Moretto Marketing Manager.
Subject-matter expertise, competence and innovation are the pillars that have guided the Moretto business for over 40 years in pursuing a fundamental goal: to satisfy customer requests, to exceed expectations, to be the ideal partner in the supply of automations for the plastics processing industry.
Vecoplan AG will present itself as a supplier of turnkey mechanical pro cessing plants at K 2022, the lead ing business platform for the plastics and rubber industry in Düsseldorf. At two booths in Hall 9 and the Circular Economy Forum, the company will showcase solutions for es tablishing a functioning recycling manage ment system to meet the increased demand for high-quality recyclates. Trade fair visitors can judge the company’s performance first hand, with live broadcasts from the Technol ogy Center in the Westerwald and live shred ding in the outdoor area pavilion. Many sectors in the plastics industry are un dergoing a transition. Recycling is not only crucial for climate neutrality, but it also con serves valuable resources and the environ ment. The aim is to increase the recycling rate and use the advantages of plastic so that no damage is caused to the environ ment. Vecoplan’s solutions are part of this value chain, and the company has been a
successful and reliable partner to the recycling industry for years. The market has enthusiastically received Vecoplan’s shredders. They can be perfectly adapted to the technical characteristics of plastics and the downstream recycling process while meeting stringent requirements for reliability and profitability.
Among other products, Vecoplan will show case the robust and sophisticated VAZ 1700, a shredder that can tackle a wide range of entirely different materials. The company has many options for configuring and adapting the machine to the task at hand, and the VAZ 1700’s throughput capacity ranges from 2,000 to 25,000 kilogrammes per hour, a cru cial performance and quality factor in the shredding process. The Vecoplan develop ment team has also given this shredder a modular basis – the outstanding feature of the new industrial design.
Visitors to the pavilion in the VDMA Circular Economy Forum (outdoor area CE 05) can experience how effectively this and other Ve coplan series shred very different plastics and recycle them in a resource-saving man ner. The live demonstrations will take place twice a day. Visitors can ask questions and converse with the Vecoplan experts.
One particular Vecoplan highlight at this year’s K trade fair will be the launch of anoth er plastics processing step. Visitors can find out more about this at both booths and via live links to the new Technology Center on the company’s site.
Vecoplan supplies its customers with power ful individual machines and systems for pro cessing a wide range of plastics. The compa ny’s specialists optimise material flows and match the components, achieving process stability, high energy efficiency and cost-ef fectiveness. Users also benefit from Veco plan’s cutting-edge know-how and interna tional project experience.
Vecoplan AG is a leading manufacturer of ma chines and systems for the resources and re cycling industry for shredding, conveying and reprocessing wood, biomass, plastics, paper and other recyclable materials such as do mestic and industrial waste.
The new VAZ combines attractive technical features with a functional and modern design.Photography credits: Vecoplan AG
Vecoplan will present a world premiere, expanding its product portfolio in the processing of residual materials for the recycling industryVecoplan will present the robust and sophisticated VAZ 1700 at the K trade fair. Photography credits: Vecoplan AG
The REM 300 by IMG will be presented and shown for the first time at the K Messe Düsseldorf. Among its best features there is an operating costs reduction, more sustainability, fast and accuracy and the reduction of noises emissions.
IMG, leader in the field of injection mould ing machines for elastomers, presents the first full-electric moulding machine. Its name is REM 300, a highly innovative prod uct, both in terms of performance and sus tainability, with consumptions reduced by 40% compared to a hydraulic press. An ab solute novelty in the rubber moulding sector, with a clamping force of 3000 kN and numer
ous improvements. After decades using hy draulic presses (from the 1950s right up to the present day), the R&D department of IMG wanted to invest in the best technolo gies now available in order to prepare a ma chine capable of reducing the environmental impact of the industrial elastomer moulding activities.
The REM 300 works without hydraulic oil, a
substance that needs to be changed around every 5000 hours. It turns out in a significant cost reduction in terms of supply and dispos al, indeed with the REM 300 there is no more special waste to dispose.
An high performances machine
REM 300 takes a step forward also in terms of performance: the electronics of this inno vative moulding machine allows a more pre cise monitoring of all the functions and, therefore, a higher mould quality, measure ment and setting of working times. The elec tric set-up is user-friendly and allows greater speed, precision and repeatability of actions to avoid non-conformities. The REM 300 is
IMG is an Italian expert in the field of elastomer injection moulding machines. It was founded in 2006 and it is based in Capriano del Colle, in the province of Brescia, the cradle of the Italian manufacturing industry. Its main market is the Sebino district, also known as Rubber Valley. The plant of 9000 m3 employs 60 people, a young and dynamic team with research, innovation and sustainability as growth drivers. The turnover of the company for the year 2021 has exceeded 60 million euros. Its production covers injection moulding machines with reciprocating screw or screw + piston systems, multi-injection systems for thermoplastics and loading and injec tion systems for BMC, for liquid and/or paste silicone. The experience of the compa ny makes it possible to produce also customised machines; moreover, IMG provides its customers with consulting and maintenance service (also via re-mote tele-assis tance) through highly qualified technicians, and punctual spare parts management.
“A technology that on the one hand already exists in the world of plastics, but on the other hand is brand-new in that of rubber.
This is the result of the company’s huge in vestments in research and development”, explains Barbara Ulcelli, CEO of IMG. “The three elements on which the market has be come extremely sensitive and which there fore allow important spaces for growth are environmental impact, cost control, and safety. It’s a radical change that IMG is making towards sustainability: a green vi sion that finds concrete expression in a product with revolutionary features.
The REM 300 is a novelty in the field of elastomer moulding machines that, once again, proofs IMG’s focus on continuous technological innovation to support its cus tomers”.
equipped with new IoT devices (Internet of Things) such as vibration sensors, IO-LINK transducers and drivers with predictive diag nostics memories for performance control,
also via remote assistance. The machine guarantees reduced energy consumption thanks to the plug and play system, which releases power only when necessary.
Last but not least, the REM 300 is more si lent than standart hidraulic machines it has a lower impact in terms of noise emissions and in a working environment where noise is a disturbing factor, this is another proof of the operator’s needs awareness. The evolu tion goes beyond the product, because IMG guarantees a continuous assistance service for every eventuality.
The REM 300 project is one of the winners of the Tech Fast tender of the region Lom bardy thanks to its high level of innovation.
At K 2022, BUSS AG will be explaining the possibilities of its digitalized machine mon itoring project, which is designed to extend machine service life and uninterrupted pro duction runs, identify maintenance needs at an early stage and avoid unforeseen downtime. BUSS will also be presenting its wide-ranging expertise as a partner in plant engineering for all aspects of compound ing. Another focus will be the addition of a laboratory version to the versatile Compeo co-kneader series.
Condition-based monitoring, the ongo ing acquisition of parameters indicating the status of individual components and entire assemblies in a machine or plant system, is the foundation of the new SenseHUB ser vice from BUSS. Sensors for acquiring pro cess section, vibration data or other metrics elucidate the condition of the manufacturing system at critical points on machines such as kneaders, discharge and dosing units, pelletizers, heaters and coolers. Following data analysis, the user can call up the vis ualized results in the SenseHUB dashboard on the BUSS service portal. This BUSS service carries out monitoring, evaluation, and planning of any necessary repair work in direct consultation with the customer. Not limited to the compounding unit of the BUSS co-kneader, the SenseHUB service
will be extended to additional sensor data for the evaluation of the machine health, ensuring maximized pro duction uptime.
Where required, BUSS can supply greater complexity in the form of complete systems for various applications and is increasingly designing and implementing custom appli cations as a one-stop shop supplier work ing hand in hand with selected manufactur ers. Depending on the scope of the project, such systems may include not only material dosing, kneading, discharging and pelletizing but also a variety of other components.
The modular machine design is so flexi
The Corvaglia team of experts who will be present at K 2022 aims to illustrate the concept of “adaptive flex-band” during the exhibition days.
The “adaptive flex-band” injection mold technology developed by Corvaglia combines different – and in some cases conflicting – requirements of beverage bottlers and consumers. Above all, the technology offers major advantages for the tethered caps, which comply with EU Directive 2019/904.
HALL 16 - BOOTH A59
ble that a specially configured compound ing line is available for any application at any temperature up to 400°C and for all plastics, ranging from thermally sensitive thermosets to demanding engineering ther moplastics.
The latest addition to the family of the se ries of five production units with through put levels, depending on application, of 100 to over 12,000 kg/h is the new compact, user-friendly Compeo LAB laboratory com pounder for throughputs of 50 to 100 kg/h for development, process optimization and small production campaigns.
HALL 12 - BOOTH B36 - 02
The key objective for beverage bottlers is finding closure solu tions that can be easily applied to the bottles on an industrial scale. This makes it easy to ensure high productivity and reduce scrap at the same time. For this purpose, a flexible tamper-evident band has become established for conventional closures.
Consumers, in turn, prefer a convenient opening and closing ex perience. Consumer tests have revealed that this requires locking it in the open position with a large opening angle. The locking mech anism requires hinges, which are preferably produced in the injec tion molding process using slides in the injection molds. Slides can be used to design a wide range of different hinges.
Combining both requirements in a single closure solution is dif ficult to implement from a technological point of view. Thanks to the new injection mold technology, however, Corvaglia is now in a position to combine these two demands.
Exolon Group, supplier of solid and mul tiwall sheets for a wide range of inno vative applications, will be represent ed for the first time at K 2022, the world’s leading trade fair for the plastics market. The European manufacturer of multiwall and solid sheets made from thermoplastics will be pre senting its innovations for the construction, industry and medical technology sectors. There is also news on sustainable product solutions for environmentally friendly areas of application.
At K Exolon Group is presenting the entire Med-Range: Exolon® Med, Vivak® Med and Inspria® Med. All Med-Range products con sist of 100 percent virgin material that meets the requirements of ISO 10993 for the biologi cal evaluation of medical devices. The sheets are produced in accordance with good man
ufacturing practices (GMP). The manufactur ing process is subject to constant control by a quality management system that meets the ISO 9001:2015 standard. Processors can thus trace the sheet material down to the raw material – an important basis for the further documentation of future end products.
With Exolon® multi UV Hybrid-X, the Exolon Group is presenting a completely new multi wall sheet type. The new geometry is a com plex combination of walls and air chambers.
The sheets are therefore all-rounders with high energy- saving potential. They offer ex cellent thermal insulation and improved light diffusion, and also have strong mechanical properties with optimised area weight. Their low heat transfer coefficient (Ug) impresses with energy savings of more than 30 percent compared to standard sheets available on the market. This means a saving of around three litres of heating oil or 2.5 cubic metres of natu ral gas per square metre and year. The sheet material meets all quality standards in terms of fire protection with a CE mark in accordance with EN 16153 and DIN ISO 9001 for quality management.
The AR (abrasion-resistant) solid sheet range consists of various types of particularly wear-resistant, chemical- and UV-resistant polycarbonate sheets. Combined with out standing breaking strength and a surface quality comparable to glass, the material im presses with its high resistance to scratches and abrasion.
With the AR 5 and AR FO product types, the Exolon Group is now expanding its range of hard-coated polycarbonate sheet material. While Exolon AR can only be installed flat, the new types can be formed despite the coating. Subsequent offline coating processes are un
necessary and the resulting follow- up costs can be saved.
Depending on the area of application, the sheets have coating on one or both sides. All sheets come with a 10-year warranty of un breakability. The guarantee against delamina tion and weathering varies depending on the type of sheet and area of application.
Ecology, recycling economy, sustainability –these are terms that have become ubiquitous today and are part of our future. In the plastics industry, these goals are achieved through the reuse of raw materials, among other things.
Under the name Eco, the Exolon Group is launching new products on the market in which recycled materials are processed. Vi vak® GP Eco and Exolon® GP Eco consist of at least 40 percent ground material from our own production. At the same time, the compa ny reduces the amount of waste through re use and upgrades this ground material to a high-quality sheet material.
The next step towards an eco-friendly future goes hand in hand with the ISCC Plus (Inter national Sustainability & Carbon Certification) certification, which the Exolon Group has al ready received. For rEco Plus products, the mass-balance approach is being pursued, whereby renewable raw materials are already used at the beginning of the production chain as a replacement for fossil raw materials. The division formerly belonging to the Coves tro Group will be exhibiting at the K trade fair for the first time. Since it was founded as a medium-sized company in 2020 under the umbrella of the Serafin Group of Companies, the Exolon Group has carried out a compre hensive product and brand relaunch.
The Exolon Group is celebrating its debut at K with a focus on sustainability across many sectors, from dental splints and rigid medical packaging to medical device containers and trays.
Excitement is mounting in the run-up to the K 2022, the world’s leading trade fair for the plastics industry. As al ways, Arburg has adopted a clear message for its trade fair appearance in Duesseldorf: “There is only a Plan A”. “Plan A” conveys that the machine manufacturer is committed to making its contribution and presenting solutions for the important global issues of sustainability, the circular economy and car bon reduction. Accordingly, with its trade fair stand A13 in hall 13 and with the arburg GREENworld pavilion in the VDMA Circular Economy Forum, Arburg will showcase its pioneer role in resource conservation. Com bined with extensive digitalisation, Arburg is perfectly positioned to provide high-end technology for greater sustainability. “The issues of sustainability, resource con servation and livelihoods are an increasing concern for people – especially in connec tion with plastics”, says Juliane Hehl, Man aging Partner at Arburg and responsible for Marketing and Business Development. “As a machine manufacturer, we are re sponsible for consuming as few resources as possible when manufacturing our ma chines”, explains Juliane Hehl. But it also means that custom ers can use Arburg machines to implement processes that save on resources and offer solutions for the circular econ omy. At the end of the day, the goal is to sustainably re duce the carbon footprint in plastics processing and
feed the recyclable plastics material back into the materials cycle.
“With ‘Plan A’, we want to show visitors of the K 2022: we have understood these con texts and, as a machine manufacturer, we are making our contribution by tackling these issues on both a strategic and an op erational level”, says Christoph Schumach er, Director Marketing.
How exactly can digitalisation deliver sus tainability? For example, through targeted sorting and recycling of plastics. Tools in clude the R-Cycle initiative and marking technologies such as watermarks or QR codes that are applied to products during the manufacturing process. Or equipping the Gestica control system with various dig ital assistance systems to make it easier for customers to manage the problem of fluctu ating material quality of recyclates.
The arburgGREENworld pavilion is all about
concrete sustainability measures in produc tion and products: in other words, about what Arburg does within its own company to con serve resources and what its products do for customers. “Greenline” plugs from Fischer, one of the market leaders for fastening sys tems, will be produced on an electric All rounder 370 A with recyclate package and Multilift robotic system. The give-away is a prime example of a successful circular econ omy in the field of post industrial recyclate (PIR). The sprue is deposited directly in a mill. It is then returned straight back into the pro cess as regrind and reused. Arburg wants to “rock” the arburgGREENworld pavilion with a young, completely new team at the stand. The team, which includes many trainees, will also be a striking reminder: sustainability is a key component of our future; today’s efforts are essential for future generations!
Exhibits will include solutions with a small footprint, process control and networked peripherals, as well as completely new technologies, configurations with compact automation or the series production of mass-produced articles. Visitors will be able to see for themselves the poten tials of the Gestica control sys tem and its assistants, such as the “aXw Control FillAssist”.
The Varimos plug-in from Simcon will be shown for the first time, which displays the ef fects of changes to machine parameters based on AI.
In the arburgGREENworld pavilion in the VDMA
The Japanese technology company
Asahi Kasei will present its newest concept car AKXY2 for the first time in Europe at the K 2022. AKXY2 made its debut on May 25, 2022, in line with Asahi Kasei’s 100th anniversary. It demonstrates how the company applies expertise throughout the entire value chain, from raw materials and pro duction technologies to the usage of recycled and recyclable materials. Virtually everything that can been seen, touched or felt in the ve hicle is either manufactured or co-developed by Asahi Kasei. The car features technology that touches the senses, improves safety and ensures the highest functionality while pro posing solutions to reduce the environmental impact of automobiles.
All windows are made of outsourced hard-coated polycarbonate through a manu facturing method developed by Asahi Kasei in 2002 that uses CO2 as a raw material for its production. Today, 15% of the global poly carbonate production uses this production technology. To enable polycarbonate for ap plications in automotive windshields, Asahi
Kasei is currently developing a hard-coating technology that equips polycarbonate with a UN ECE R43 compliant resistance to abra sion and weatherability. Replacing glass with this polycarbonate will significantly reduce vehicle weight and extend EV driving range.
The interior surfaces are covered by Dinami ca® - a premium microfiber resembling suede partially made of recycled polyestermanufactured by Miko, an Italian subsidiary of Asahi Kasei Group company Sage Auto motive Interiors. Sage Automotive Interiors can also provide other more sustainable fab rics utilizing raw materials that range from recycled PET, bio-based PET, natural blends, and ocean waste. An improved lifetime of materials is another way to achieve a green er mobility. All fabrics can be made anti-viral and anti-bacterial, as well as fluid-repellent and stain- resistant.
AZPTM, a transparent optical polymer on the interior display, features an ultra-low birefrin gence and ensures a perfect screen visibility without rainbow effects. The interior is also featuring light technology, using semi-trans
parent and backlit fabrics made of PET, but also ultra-thin plastic-optical fibers woven into different surfaces.
At K 2022 Asahi Kasei will also present its SunForceTM family of innovative particle foams. Based on engineering plastics, all types are processable on standard foam molding equipment and open up new appli cation fields for foams. SunForceTM BE is based on modified polyphenylene ether (mPPE) and features an unmatched combination of lightweight, UL94 V-0 flame retardance, thin-wall moldability, thermal insulation and processability. At K 2022, Asahi Kasei will display 4680 and 2170 round cell holders made of this material. In this application the material allows for the precise fixation and alignment of round cells without the use of any adhesives. The mate rial is also suitable for battery pack applica tions for any other kind of cell design like pouch-cells and prismatic cells.
SunForce™ BE 4680 and 2170 round cell holders
As a fully integrated producer of dura ble materials, Ascend has a unique abili ty to tailor polyamide polymer chemistry and global compounding expertise. These traits combined with deep application engineering and end-market knowledge, allow the company to serve a wide varie ty of customers, including those focused on e-mobility, electrification, connectivity, renewable energy and packaging through its expanded portfolio. Among the high lighted products were:
- Vydyne ® Thermaplus: a new tech nology platform of high-temperature, high-ductile PA66 for fasteners; designed
as a smarter replacement for PA46.
- Starflam ® flame-retardant polyamides: a full portfolio of UL yellow card- certified FR materials designed to meet a variety of performance requirements.
- HiDura TM: a growing portfolio of longchain polyamides for consumer goods and connectors, as well as copolymers for films that make packaging more du rable.
Ascend’s dedicated e- mobility team, which was founded in 2018, has been providing the e-mobility market with high-performance solutions focused on safe power infrastructure, a secure and
comfortable ride, and reliable thermal management. Ascend’s team of e-mo bility application development engineers and polymer scientists created a novel solution to dampen noise, vibration and harshness in electric vehicles.
EV motors produce vibrations at 10 times the frequency of internal combus tion engines, making standard automotive under-the-hood dampening materials less effective. Vydyne AVS is a new engineered material effective at dampening high-fre quency vibrations at the motor, which translates into an 80% reduction in cabin sound pressure.
Brüggemann is presenting performance-en hancing additive innovations at K 2022. These range from electrically neutral heat stabilizers for polyamides in electrical and electronic applica tions, for example for e-mobility, to high-perfor mance stabilizers for exposure to moderate to very high temperatures and additives for stabilizing recycled polyolefins. A further focus is on efficiency-boosting flow enhancers which enable shorter cycle times and low wall thicknesses for components made of polyamides and polyesters (PBT).
Bruggolen® TP-H2062 and TP-H2217 are opening up a new class of metal- and halo gen-free heat stabilizers for reinforced and un reinforced polyamides in E/E applications. They do not corrode metallic components such as overmolded sensors and have no impact on the polymer’s electrical properties.
Bruggolen TP-H1804 is a new heat stabiliz er for aliphatic polyamides used at continuous service temperatures of 160°C to 190°C. It dis tinctly outperforms copper salt-based stabilizers in terms of mechanical property retention of the materials to which it is added.
Bruggolen® TP-P2201 is a new addition to Brüggemann’s range of flow enhancers which will be presented at K 2022 and is specifically tailored for applications in e-mobility and flame
retardant polyamides. Bruggolen® TP-P1810 is particularly suitable for processing partially ar omatic polyamides, while Bruggolen® P1507 is optimized for aliphatic polyamides and TPP1924 for PBT. All these additives help to save energy during production while simultaneously enabling very high fiber contents for injection molded parts with long flow paths and/or low wall thicknesses.
Brüggemann had already presented its wide range of additives for the mechanical recycling of polyamides at K 2019. These include longterm heat stabilizers, process stabilizers, flow promoters, reactive chain modifiers, nucleating agents and other processing auxiliaries.
Using Bruggolen® TP-R2090, it is possible to recycle polypropylene from post-industrial and post-consumer waste. TP-R8895 is specifically suited to recycling polypropylene from battery cases. Both additives result in recycled materials of a quality which cannot be achieved by con ventional re-stabilization, even at high rates of addition.
For recycling polyethylene, Brüggemann has developed Bruggolen® TP-R2162 which again includes the new repair technology and is par ticularly suitable for recycled LLDPE for use in film extrusion. All the stated additives are sup plied in the form of compact, dust-free blends.
K2022 is the perfect setting for Bausa no – international leading player in the design and production of cus tomised extrusion lines for the transformation of plastic materials – to introduce industry professionals to the increasingly high-per forming Smart Energy System for cylinder induction heating, which helps to reduce en ergy consumption significantly. The system will be on display at the stand on both a twin screw extruder from the Nextmover range and on the new single screw extruder E-GO R, designed for recycling plastics. More precisely, the Smart Energy System de signed by Bausano features forced-cooled induction coils with special openings that al low air to pass through and the temperature sensor to be installed. The coil is wrapped in highly insulating materials to minimise heat loss from the cylinder to the outside. Moreo ver, thanks to its innovative internal design, the cooling airflow is channelled directly onto the plasticising cylinder for faster cooling com pared to resistive systems. These features can be summed up as follows:
• Even heat distribution and lower coil surface temperature;
• Quick heating up to 250 °C;
• Extremely accurate temperature control thanks to reduced thermal inertia. Specifically, the Nextmover extruder, equipped with Smart Energy System, will be
on display at the trade fair, along with a dou ble output head for pipes manufacturing PVC pipes. Bausano intends to show visitors how, thanks to its technology, the overall pro ductivity of 2,000 kg/h can be achieved for diameters from 63 mm to 160 mm while sav ing 35% energy.
Other essential factors for the success of the entire process are the cooling and calibration benches, made of stainless steel for pipes that are cut perfectly to size and have a flaw less surface. Specifically, the line with a dou ble output head, showcased at K in its com plete configuration, has two 9 m dual-chamber parallel calibration benches with temperature and water level control, which allows for creat ing different vacuum conditions as required. In addition, the high-performance pipe cool ing system cools the pipes more quickly, thus improving their quality and taking up less space when installing the line.
On the other hand, thanks to the 4.0 control system covering the entire line, Digital Ex truder Control, with a 21-inch screen, the consumption during each stage of the pro cess can be accurately monitored. The re al-time performance display enables inter vention to manage motor power, temperature,
oil control unit inspection, screw adjustment and other parameters on request. Further more, the line meets the Smart Factory verti cal integration requirements, allowing com munication with third-party systems, such as the sophisticated in-line measurement tool to accurately check the pipe’s internal and ex ternal diameter and wall thickness. Ultimately, K will be an opportunity to launch, for the first time in Europe, the groundbreak ing E-GO R technology, which can be used to feed highly contaminated plastics back into production processes. Some examples are HDPE waste from containers for milk, motor oil, shampoos and conditioners, soap, deter gents, and bleach. Other applications include PP waste from lunch boxes, yoghurt pots, syr up and medicine bottles, caps and LDPE waste from cling film, shopping bags, and squeezable bottles.
‘The expansion of the extrusion lines for PVC and PO pipes and for recycling plastics is the result of our unique ability to combine process consultancy, a passion for innova tion and technological expertise”, says Clemente Bausano, Vice President of Bausa no. “In this regard, throughout the event, our clients will have the chance to get to know our new team of experts in the Technical De partment, who have specific skills and exten sive know-how when it comes to designing these types of solutions,’ and then concludes by saying that ‘Innovations in the production of granules, which has always been one of Bausano’s strengths, will also be showcased. The company’s goal is to meet the needs of plastics manufacturers by combining turn key, highly customisable systems with topnotch customer service”.
Frigel brings to the K-22 show the main highlights of its portfolio of products tai lored to the main Plastic market seg ments, such as automotive, packaging, med ical and all other sectors dedicated to the injection molding of Technical Parts. Frigel is also bringing to the K-22 show some of its re cent highlights in centralized system solu tions.
Frigel introduces the Microgel Syncro, a new technology that revolutionizes the tempera ture control method of injection molding tech nical parts. The Microgel Syncro technology allows for a significant reduction in cycle time (up to 40%), guaranteeing very high product quality.
Frigel releases the full range of Microgel RS for Injection Molding. These unique single zone (RSM) and dual zone (RSD) ma
chine-side temperature control units are de signed for molding throughputs ranging from 10 to 240 kg/hr (20 to 530 lb/hr).
The popular Frigel high performance booster TCU line is presented with upgraded digital control to allow full connectivity with MiNDTM and other Industry 4.0 architectures.
Frigel introduces advancements in its grow ingly popular direct injection pressurized wa ter TCUs up to 120°C for applications in Auto motive, Medical and any other Technical Molding sectors where accuracy, repeatabili ty and process control are fundamental for the profitability of the IMM cell.
Frigel completes its platform of Industrial Modu lar Chillers (3F series) with a new integral air cooled package chiller line, the 3FA range, fea
turing: high efficiency screw technology with VFD option, microchannel high performance condenser, EC fans for increased part load effi ciency and low ambient temperature control, low GWP refrigerant option (R-513a), wide pro cess and ambient temperature operating rang es, modular design with factory pre-engineered piping configuration and recirculation water package option.
Frigel expands its Adiabatic product family line, introducing the Ecodry MDK range, designed to allow the flexible configuration of modular adia batic solutions for small to large plastic factories. MDK takes advantage of some of the technolog ical advances already introduced in the LDK range (new efficient PADs, new generation of EC fans, modular design, wide and deep configura tion).
The 3PR 4.0 product platform is a dedicated Frigel solution that provides complete control of Frigel central cooling systems. 3PR 4.0 control meets the needs of processors to supervise and manage the whole cooling system from a single control point.
Frigel releases the MiNDTM 2.0 plat form, the evolution of its Industry 4.0 concept. MiNDTM 2.0 is an innova tive digital solution to meet the ever increasing needs of mod ern companies to reach In dustry 4.0 and IIOT (Indus trial Internet of Things) standards.
Oerlikon HRSflow will be attend ing K 2002 where it will focus on an extensive range of hot run ners tailored to small shot weights and the new Xp nozzle series for use in thinwall injection moulding. The company has expanded its portfolio to include components for injection molding of de manding parts with small shot weights in stable and reliable processes. The man ufacturer now offers complete systems for this market segment, which require tight nozzle pitch solutions. These include nozzles with small dimen sions in all designs, from thermal gate to valve gate, as well as the associated manifolds and actuation mechanisms.
For multi-cavity applications, a mul ti-valve plate (MVP) provides perfectly synchronized control of the injection channel across all cavities for high partto-part weight consistency. Oerlikon HRSflow systems offer optimal colour change performance and easy system restart, reducing waste and increasing efficiency and sustainability. The latest version of the system is highly reliable for processing even biopoly mers and PCR compounds. A version with a specially coated nozzle tip is available for processing highly corrosive polymers including flame re tardant compounds. For demanding ap
plications, Oerlikon HRS flow uses its inhouse additive manufacturing process SLM (Selective Laser Melting) tech nology to produce cooling cir cuits for all market segments. Thanks to the joint experience with sister brand Oerlikon Bal zers, Oerlikon HRSflow also offers innovative surface pro tection for all moulded part surfaces to increase their corro sion resistance.
The new Xp series of valve gate nozzles from Oerlikon HRSflow is designed to withstand high filling pressures up to 2200 bar and enables fast injection and cycle times in a stable process with high part weight consistency. An innovative, pat ent-pending solution for stack systems in thin-wall injection moulding has been de veloped. Assembly is extremely simplified and highly efficient thanks to a plug-andplay installation. This hot runner system, which enables the use of smaller injection moulding machines, fits a maximum plate thickness of 240 mm. This allows perfectly symmetrical systems with up to 8 plus 8 drops to be supplied, with a minimum pitch between cavities of 65 mm and be tween nozzle and inlet of 120 mm.
For their production in the IMD process (In-Mold-Decoration), the FLEXflow hot runner technology from Oerlikon HRS flow with its servo-electric needle posi tioning is increasingly proving to be the tool of choice, because it enables pre cisely controlled, gentle and low-war page overmoulding of the sensitive electronic components with high-quality surfaces at the same time.
The cost- and energy-efficient applica bility of FLEXflow for perfectly balanced family moulds, even with extremely dif ferent part volumes, ensures additional acceptance in this industry. This also applies to HRScool, Oerlikon HRSflow’s solution for hot runner injection mould ing, which eliminates the need for water cooling of the associated actuators.
Oerlikon HRSflow will exhibit its solutions aimed at protecting the environment by reducing energy consumption during the injection process.
The three-phase digital Evo Smart generator with HMI touch-screen dis play and intuitive interface will be the main novelty in the field of corona treatment (extrusion, extrusion coating, coating, lami nating and flexo and gravure printing). Entirely designed and manufactured by Fer rarini & Benelli, Evo Smart achieves the pow er needed to treat every substrate, at the highest line speeds.
The navigation system of the generator is user-friendly and multilingual, allowing im mediate management of all the main working parameters and re al-time monitoring of production data from any device (PC, laptop, tablet and smart phone). The innovative features of the system allow to store events on SD card for downloading to a PC even via USB stick and to look up instruction manuals di rectly from the display.
The Evo Smart generator can be connected to the FB Cloud platform, to receive technical assistance with remote monitoring and diag nostics, view the real-time data dashboard and process and download reports and
analysis of production data.
Ferrarini & Benelli technicians can thus mon itor from Italy the main parameters of a gen erator installed anywhere in the world and provide online support and useful advice to operators, further improving after-sales and tech support services.
Bikappa Rotary is the double-sided treat ment system (also available in the one-sid ed version), designed to be installed on high-performance extruders or flexograph ic presses in line with extruders. This treat ment system, coming in different models, is equipped with:
Polimetal is the universal corona treatment system suitable for all converting applications (laminating, coating, extrusion coating, flexo and gravure printing). It can treat any material, such as plastic and metallised films, alumini um foil, plastic-coated paper and laminates. The system comes in four different models, each designed for specific production needs. Equipped with ceramic electrodes and ce ramic-coated roller.
Knowing the surface tension of a surface is important to check if a substrate is suitable for printing, coating or gluing and to evaluate the effects of corona treatment. At K 2022, Fer rarini & Benelli will exhibit a kit of solutions de signed for these ends: Dyne Test Inks, Dyne Test Pens and Corona Markers.
Dyne Test Inks are liquid solutions used to check accurately the adhesion of a liquid to a plastic surface and the effects of corona treat ment.
• multiple discharge electrodes in alumini um or stainless steel, with sectors or segments of different lengths allowing zoned corona treatment
• discharge rollers with silicone sleeve or vulcanised sleeve coating.
The rotating opening of the rollers eases film threading and access to the elec trode-insulators assembly.
Dyne Test Pens are used to quickly check if a substrate has been surface treated. Corona Markers underline, owing to an ink, which re mains visible on the surface, the corona treat ed areas.
At this year’s K 2022 trade fair Milliken & Company, a diversified global manu facturer with more than 70 locations around the world, will showcase new measures to advance the circular economy through chem istry – part of the company’s 2025 Sustainability Goals. Additionally, Milliken is partnering with more than 30 partners in purposeful collabora tions that will be on display throughout the K Show, including its ongoing partnership with PureCycle Technologies, whose patented tech nology turns recycled polypropylene into vir gin-like material.
“At Milliken, we work closely with our trusted partners to develop additives that build a better world,” said Cindy Boiter, President of Milliken’s Chemical Business. “Together, we solve the challenges our customers face. We are partner ing and working with many throughout the value chain to make plastics more reusable, more re cyclable and more efficient”, added Wim Van De Velde, Global VP of Plastic Additives.
At K 2022, Milliken will showcase:
• Millad® NX® 8000 ECO, clarifying agent for polypropylene (PP), boosts clarity, enables faster production rates and reduces energy use. This product is certified by Underwriters Laboratories (UL) to provide average energy savings of 10% for the production of injection molded clarified PP parts.
• DeltaMax®, performance modifiers for recy cled PP. This product is unique in its ability to balance melt flow, impact strength, and stiff ness to increase overall performance for recy cled materials.
• DeltaMax performance modifiers for virgin polypropylene impact copolymers (ICPs) en ables resin producers to balance the proper ties of ICP resins more effectively, while af fording them the opportunity to optimize processing efficiencies. DeltaMax also helps converters reduce energy by running ma chines with faster cycle times or lower temper atures.
• DeltaFlow™ Viscosity Modifiers, solid con centrates designed to specifically help PP re cyclers by increasing the melt flow rate of re cycled polypropylene (rPP) for extrusion and injection molding processes.
• Hyperform® HPN® performance additives for PP which deliver an improved balance in
properties between stiffness and impact re sistance while reducing energy use. Certified by UL to enable 5% to 8% energy savings when this product is used as nucleator for production of thin-wall injection molded PP container lids and similar PP applications.
• UltraGuard™ Solutions which enable down gauging to reduce material usage and part weight while also improving barrier properties in polyethylene (PE), allowing designers to create more mono-materials products, im proving recyclability.
Many of Milliken’s products are designed specif ically to yield sustainability benefits. These qual ities include: reduced energy consumption and lightweighting, better reuse potential, increased net use of recycled content, improved recycling and recyclability, and the replacement of less-sustainable resins.
Milliken is future-focused and proud to be part of the solutions that will enable the entire industry to advance circularity and boost the percentage of plastics being recycled. To this end, the compa ny is actively engaging in several industry-span ning initiatives, including the Alliance to End Plastic Waste, The Recycling Partnership, the Association of Plastic Recyclers, the HolyGrail project to improve the sorting of waste plastics via digital water marks, and the RecyClass recy cled-content certification program for packaging, to name a few.
Hellweg Maschinenbau, the manufacturer of advanced gran ulation machinery for effective plastics recycling, will be pre senting extended options around the Smart Control system for its entire granulator range at K 2022.
Hellweg has added a hardware module to the Smart Control system that is capable of stor ing the power consumption of the machine it is fitted to over the long term, for example over a financial year, and providing it for analysis. Together with the ability to display power peaks, it provides valuable data for optimizing ener gy use.
The software itself now has the option of controlling granulator speed in increments of one, so giving the user even more flexi bility in tailoring machine parameters exact ly to requirements. The SECURE+ package for the control system adds safety features. As soon as it detects imminent granulator overloads on the basis of motor current and
torque values, it counteracts them so that rotor blockages can virtually be avoided.
Hellweg can now optionally equip all central granulators from the 260 series up wards which are used for grinding sprues, sheets, molded parts, sprue slugs and hol low items with a new central lubrication unit. Using a Bluetooth interface, the unit provides the operator with all relevant data, such as battery voltage, temperature, deliv
At K2022 in Düsseldorf, Tosaf will present a series of new white masterbatches with excellent properties in terms of whiteness, colour strength and opacity, which do not contain titanium dioxide (TiO2). The company is thus responding to an increasing number of customers inquiries, since regular white pigment is suspected of being carcinogenic when inhaled in powder form, and because the EU has banned it as a food colourant (E171). Although this decision by the EU does not yet ban the use of titanium dioxide as a pigment in polymers that come into contact with food, there is a growing demand among manufacturers of hard and soft packag ing for the food industry, as well as parts of the toys and cosmet ics industries, to move to TiO2-free masterbatches in the future.
Such masterbatches have now been devel oped by Tosaf as cylindrical as well as spher ical granules. They are the result of a study initiated by Tosaf Benelux R&D on ways to find alternatives for the white colouring of plastics. Although their formulation does not contain unbound titanium dioxide, their
ered lubricant volume as well as the time since the most recent pump stroke, operating time and number of pump strokes. The integrated, active reporting system enables the operator to detect irregularities at an early stage and nip them in the bud. With an eye to sustainability, Hellweg also offers the option of refilling empty cartridges as part of its exchange service.
The new R 200/20 Servo edge trimming system, a joint devel opment with BREYER Extrusion, complements Hellweg’s range of systems of this type, also known as guillotines or chippers. When trimming film webs, it pre-shreds one or two edge strips, which are then fed to a granulator for further processing. Its servo gear motor means that cutting cycle times can be freely specified. The operator can use the touch display to select the cutting frequency for the trimming and so specify the length of the chopped edge strips at a constant cut ting speed.
opacity as well as their colour strength is on the same high lev el as that of standard TiO2 masterbatches at equal let down rate. The colour shade itself can be adjusted from yellowish to neutral to bluish. As this applies regardless of the carrier system, Tosaf’s new patent-pending white masterbatches are compatible with any host polymer. The low abrasiveness allows for long tool life, and no plate-out occurs when processed on two-roll systems.
“With the development and launch of our new Non-TiO2 white masterbatches, available in a wide range of polymer carrier sys tems, we are giving plastics processors and brand owners the answer to the dilemma they have when it comes to white colora tion of plastics for food packaging, cosmetics packaging, medical packaging and toys, regardless the process and regardless the end application”, says Michel Theunisz, General Manager of Tosaf Benelux. “Tosaf’s new white masterbatch es allow the plastics market to proactively take action on reducing the use of TiO2 in Plastics”.
For three decades, sustainability has been the focus of the family-owned company Krall Kunststoff-Recycling in Elsenfeld am Main. Its history began with a small plant in early 1992, when “recycling” still was almost unheard of in public. Man ufacturers and processors were offered the takeover of plas tic residues for subsequent type-sorting and grinding. From the very beginning, executive director Markus Krall focussed on transparent plastic materials, mainly polycarbonate and PMMA, which constitute the core business still today. Further key aspects are engineering plastics and the recycling of CDs.
Today, the company comprises six workshops with a total floor area of 12,000 square meters. With about 40 employees, two shredding machines, and 10 chopping mills, the compa ny will reprocess some 8,000 tonnes of plastic materials in the anniversary year, consequently working with environmen tally friendly solar power. The type-sorted regrinds from Krall Kunststoff-Recycling are raw materials worldwide sought-for by processors who gladly return them into the materials cycle –for the direct manufacture of new products or as an ingredient of compounds.
Krall provides the complete infrastructure, including space-saving collection bins and logistics, for around 800 manufacturing, retail and commercial collection points across Europe. More than 15,000 load carriers from Krall are in cir culation, including boxes in many different sizes and designs, ideally matched for the respective needs, ensuring a smooth collection procedure. Also, Krall accepts all common box sys tems up to large containers, and beyond that even offers the
possibility to unload walking-floor trucks.
“The market for high-quality recyclates is growing rapidly”, says Markus Krall. “Increasing amounts require manual sorting to be supplemented by powerful automation processes. The use of robots and artificial intelligence will be helpful. Our ex cellent international market position enables us to promote the development of state-of-the-art technologies up to practicabili ty. In cooperation with institutes, we perform feasibility studies and invest in new systems to create the prerequisites to meet tomorrow’s market requirements”.
Low available volumes of sorted plas tic waste are negatively impacting the operations of plastics recyclers across Europe creating an obstacle to achieving the EU targets.
“This situation could slow down the transition towards a full plastic circu larity, the recent EU policy and global developments have boosted massive investments in the plastic recycling ca pacities on the continent as in 2020 the plastic recycling industry invested €1.5bn which translates into 1.1Mt addition al installed capacity when compared to the previous year and a total of €4.9bn of investments since 2017”, says Ton Emans, PRE President. “However, with out stable, high-quality input materials
the industry’s efforts to reach the new recycling targets might be hindered. Ro bust sorting and collection infrastructure is a must to increase stable feedstocks for European recyclers’’.
This comes unexpectedly as for a few years the EU has been registering a de cline in exports of waste while recyclers continued to upscale the installed capac ities with a major, 60% growth in 4 years.
The Chinese ban and the strengthening of the controls in the context of the Basel Convention and OECD Decision on Trans boundary Movements of Waste both en abled the continuous decrease of the ex ported waste from 3Mt in 2014 to 1Mt in 2021. Despite these developments and regardless of the increase in the price of
sorted material pushed by the growing prices of recycled materials, no substan tial additional quantities of waste are be ing sent to recyclers today.
With 9Mt tons of plastic waste being collected for sorting, out of 30Mt in to tal, increasing the collection destined for recycling remains one of the key meas ures in Europe. The remainder of the col lected waste -21Mt - is either incinerated or landfilled. Furthermore, the statistics demonstrate a 20Mt gap in the amount of waste that is generated versus what is put on the market.
Challenging these figures is critical to divert recyclable plastic from landfills and incinerators, in order to create econ omies of scale for recycled polymers.
As brands and converters seek solu tions to increase the circularity of plas tic packaging, Avery Dennison Label and Packaging Materials has removed a key obstacle to plastic recycling with the in troduction of next generation AD Clean Flake™ technology. Already an expert in enabling recycling for PET plastics, this breakthrough innovation now extends the benefits of CleanFlake technology to our core film portfolio, combining with our HDPE recycling compatibility. With the next generation AD CleanFlake™ Port folio, Avery Dennison becomes the first label manufacturer to enable rigid plastic recycling across its film portfolio, provid ing brands and converters solutions that support recycling process es without compromising performance to meet sustainability goals.
AD CleanFlake technology is recognized by the Association of Plastic Recyclers, European PET Bottle Platform and RecyClass, for enabling recycling by working with the rigid plastic recycling processes to either remove cleanly (PET) or stay with the package (HDPE), resulting in good quality flakes, the conservation of virgin
Dow announced its post-con sumer recycled-rich resins, Revo loopTM, are the first polyethylene (PE) compounds to be certified in accordance with the Standard UNE-EN 15343 for plastics re cycling traceability and recycled content. The certification has been granted by Aenor, a global company and the Spanish leader in conformity assessment and ex tends to all three grades offered by Dow in Europe.
RevoloopTM grades are part of Dow’s plastics circularity portfolio and incorporate a high percentage of post-consumer recycled (PCR) material. The single-pellet solution enables a simpler PCR process integration, meeting the needs of converters, brand owners and sus tainable packaging designers, and
resources, and less landfill waste. The AD CleanFlake™ Portfolio delivers these benefits for both PET and HDPE plastics, creating the potential to divert over 200 billion rigid plastic bottles and containers from landfills.
“This is an important step forward in using innovation to advance the circular packaging economy without compromis ing performance”, said Pascale Waute let, Vice President Global R&D, Avery Dennison Label and Graphic Materials. “Brands are actively seeking solutions to help them advance their sustainability in itiatives and our AD CleanFlake Portfolio significantly expands the applications for this groundbreaking technology”.
The AD CleanFlake technology goes beyond enabling recycling by delivering outstanding performance on adhesion, clarity, and conversion. For converters, the adhesive features excellent wa ter whitening and bleeding resistance. Brands benefit from strik ing print quality that supports bold designs and contributes to shelf appeal.
can be used in a broad range of applications. Providing access to quality, consistent waste streams, and increasing reliability in the waste value chain, the RevoloopTM family of PCR-rich resins expand Dow’s sustainable offerings port folio to help advance a closed loop system for plastic waste.
The UNE-EN 15343 is the Europe an Standard that specifies the pro cedures needed for the traceability of recycled plastics and covers two schemes: the traceability and char acterization in the plastic recycling process, and the minimum content of post-consumer recycled plastic used in the processing of a plastic product.
This certification was awarded following a full independent, exter nal audit to ensure that the control
of incoming plastics waste, the traceability in the production pro cesses of recycled material and the percentage of post-consumer recy cled material included in the cer tified products, Dow XZ98612.00 (30%), Dow XZ98615.00 and Dow XZ89169.00 (70%), complies with the requirements set out in UNE-EN 15343 standard.
Therefore, Aenor has verified that the manufacture of Dow’s polyethylene compounds con tains up to 70% of post-consum er recycled products, which have either fulfilled their intended pur pose or can no longer be used for the purpose for which they were conceived.
In order to grant this certification, Aenor first checks the origin of the post-consumer recycled material.
ABB, a pioneering technology group that works closely with utility, industry, trans portation and infrastructure customers, has been awarded a major contract by Nature Works, the world’s leading manufacturer of poly lactic acid (PLA), a low-carbon bioplastic made from renewable agricultural resources, to auto mate their new, greenfield plant in Thailand, converting sugar cane to the polylactic acid (PLA) biopolymer, Ingeo™.
The new plant in Thailand, will ferment and distill plant-based sugars – in a process similar to making beer or wine – converting the sugars first to lactic acid, then lactide and then polymerize them into Ingeo. In the new site, these three sep arate production processes will be fully integrat ed, resulting in significant improvements in ener gy and production efficiency. In addition, the integration of the fermentation phase will secure the supply of lactic acid. The Thailand facility will use sugarcane as feedstock and is set to pro duce 75,000 tons of sustainable plastic per year when fully operational. The anticipated project ed startup for this greenfield facility is in the sec ond half of 2024.
ABB’s scope of work is a two-part order includ ing a FEED (front end engineering design) study followed by detailed automation project execu tion, with ABB acting as the Main Automation Contractor. ABB will deliver the hardware, soft ware, control room design solutions, engineer ing, and site support to fully develop Nature Works’ greenfield system. ABB’s market leading distributed control system Ability™ System 800xA will maximize plant efficiency and reliabil ity through automation. Leveraging this technol ogy, ABB will integrate inputs from all key sys tems into one single user-friendly overview. As a result, operators will be able to utilize data in
sights from all areas of the plant, delivered in real time, to drive efficiency, reduce risk and ensure production optimization.
The project will apply State Based Controls (SBC), enabling operators to take fewer interactions to start up a unit and reduce risk by having access to the right information at the right time. In addition, ABB’s automated engineering batch application tool will be implemented for this project.
“ABB’s global presence, especially in the US and Thailand, combined with their deep exper tise in the chemical industry, leading automation solutions, and design optimization approach, makes them the obvious choice for a partner to help achieve meaningful progress in our new plant,” said Steven Bray, Vice President of Oper ations and Project Program Manager at Nature Works. “We also share a joint vision when it comes to resource efficiency, circular economy and sustainability”.
Part of NatureWorks’ global expansion plan, the plant will help meet the growing global demand for sustainable materials. Bioplastics today rep
resent less than 1 percent of all plastic produced globally but production is expected to grow over 260 percent between 2020 and 20261.
Ingeo, an innovative material with unique prop erties that all begin with greenhouse gases, is an eco-friendly, biobased material used in a widerange of plastic and fiber products from com postable food packaging - coffee capsules, tea bags, food containers – to 3D printing filament, diapers, and even refrigerator liners. Compared to traditional fossil-based polymers, manufactur ing Ingeo produces approximately 80 percent less greenhouse gases and uses 52 percent less non-renewable energy.
“We are proud to support NatureWorks in ad dressing the increasing demand for sustainable high-performance materials and helping maxi mize both energy and production efficiency in the new facility”, said Brandon Spencer, Presi dent, ABB Energy Industries. “Our project with NatureWorks is perfectly aligned with our 2030 Sustainability Strategy and driving more sustain able use of our planet’s resources through inno vative solutions that help reshape industries and enable a low-carbon society”.
ABB will automate NatureWorks’ bioplastics plant in Thailand to improve energy and production efficiency of bioplastic manufacturing, expected to grow over 260 percent by 2026.
For some time now, additively manu factured components have been used for more than just prototyping. Their great potential is also used in pre-se ries construction and for production parts. For technically usable components, the ma terial properties are of crucial relevance. In this area, 3D-printed components can only compete with conventionally manufactured ones if they also have the same mechanical and chemical properties. Biocompatibility, thermal resistance and, of course, very high elasticity make silicone indispensable for very many applications. There is therefore a great deal of interest in using the advantag es of additive manufacturing with materials such as silicone. However, the process for additive manufacturing of silicone is not straightforward.Below, some extru
3D printed components have the same mechanical and chemical properties as those printed conventionally, if not better. Silicone, in particular, is a suitable material for many applications, but in order to exploit it we need to learn about its manufacturing process.
sion-based methods and processes. In par ticular, different cross-linking mechanisms are examined in more detail – with their re spective advantages and disadvantages.
A decisive advantage of extrusion-based pro cesses is the wide variety of liquids and pastes that can be processed. Almost all types of sili cones can be used: From low to high viscosity and from RTV (Room Temperature Vulcaniza tion) to standard LSR (Liquid Silicone Rubber) to UV-curing and particle-filled silicones. The extrusion-based manufacturing process
By ViscoTecis very similar to that of FLM (Fused Layer Modeling) printing. With the help of a dis pensing head, a strand is deposited. A com ponent is additively manufactured from this strand, layer by layer.
In this white paper, 2-component LSRs and RTV silicones are discussed. LSRs require thermal energy for cross-linking, whereas RTV silicones are designed to react at room temperature. Silicone printing always involves a liquid materi al. Decisive process parameters are therefore the dimensional stability and cross-linking of the silicone. It is also important to note that the strength of the finished silicone is only achieved
through the chemical reaction of the material, for example through polyaddition or polycondensa tion.
Basically, a distinction is made for LSR silicones between two different cross-linking points: Cross-linking during production and cross-link ing in the re-work or during post-processing.
• Heated build platform: Heated build platforms in additive manufacturing machines are wide ly used. It is therefore obvious to provide the thermal cross-linking energy via these plat forms. Depending on the reaction time of the silicone, cross-linking on a heated build plat form can take place within a few seconds after extrusion.
However, this process has a decisive disadvan tage: The temperature distribution changes with the height of the component. This is because the further away the layer is from the build platform, the less thermal energy is supplied. This means that a reliable and constant process for a com ponent with numerous layers is therefore very
difficult to achieve. Experience has shown that it is no longer practical to manufacture compo nents larger than two to three centimeters using a heated build platform.
• Cross-linking of each layer: A heat input on the respective component from above – after each layer – enables uniform cross-linking for any number of layers. The heat is applied di rectly during the printing process, so the com ponent is ready immediately after printing. This requires an additional heat source, such as an infrared lamp. Intensity and exposure time must be adapted to the respective layer, which is why the entire manufacturing pro cess becomes more costly and complicated.
Another approach is to use a silicone that retains its shape after extrusion due to its rheological properties. This can be achieved by a very high viscosity or a high thixotropy of the silicone, or a combination of both. The finished component made of LSR silicone is placed in an oven in the post-processing stage and cross-linked at ap propriate temperatures. The heat input must not cause any deformation in the component. In this process, no additional equipment is required to supply heat during printing.
But there is a process that makes freedom of design possible without building a support structure: Manufacturing within a different mate rial. To do this, the silicone is dispensed with a
long needle into a container filled with a “support material”. This support material can be, for ex ample, a powder or hydrogel. The process is il lustrated in the figure below:
In the first step, the silicone (see Figure 1, in or ange) is dispensed into a supporting material (see Figure 1, in blue). The extruded strand is fixed by the surrounding material. After the de sired structure has been built up and the silicone has cross-linked, the component can be re moved from the material with tweezers. Finally, residues of the supporting material are removed or simply washed off. RTV silicones are particu larly suitable for this process, as they cross-link after a short time (30 to 60 minutes). The support material can be used again after removal of the component. The biggest advantage of this method is the high degree of freedom of design. The disadvantages of this technology are the large amount of supporting material required for larger components. And that the use of LSRs is not usually practical.
Due to the large variety of different extru sion-based manufacturing processes, almost all components can be produced from silicone. Depending on the desired geometry and sili cone type, the appropriate process can be de fined. The basis for a successful manufacturing process is always a precise and repeatable dis pensing of the silicone. The potential of silicone 3D printing is far from exhausted. Especially with new processes, such as the use of support ma terial (like hydrogel), completely new design possibilities are opening up.
Solvay, a global market expert in specialty materials, has announced the development of an innovative new portfolio of UV-C stabilizers. They are designed for use in demand ing hygiene applications, where polyolefin surfaces are treated with ultra-violet (UV) light of the UV-C spectrum (200-280 nm) to fight against Covid and hospital-acquired infections. The new proprietary stabilization technology represents an important milestone for the polyolefin indus try, as it is the first to address the risk of polyolefin degra dation, discoloration and micro-crack formation, which is
caused by frequent exposure to UV-C irradiation. “Healthcare and other markets, such as aerospace and shared mobility, are increasingly using UV-C light to dis infect high-contact surfaces in an effort to combat path ogens, including coronaviruses”, says Sophie Poelmans, Global Marketing Manager for Polymer Additives at Solvay Materials. “Our new UV-C stabilization technology helps end users achieve effective UV-C disinfection levels on surfaces made from polyolefins without compromising the performance of the material”.
UV-C radiation can deactivate microorganisms and has been scientifically proven to be effective against coronavirus es. However, the proven germicidal action of UV-C also ex poses the treated surfaces to much higher ultraviolet energy than that covered by traditional UV-A and UV-B stabilizers, re sulting in the potential for faster material degradation. Solvay, a member of the International Ultraviolet Association (IUVA), has leveraged its extensive expertise in polymer additives to develop a technology that is purpose-engineered to enable the use of UV-C light as an anti-microbial disinfectant on poly olefin surfaces, while safely protecting them against UV-C induced degradation. Solvay’s new UV-C stabilization tech nology is targeted at a wide range of polyolefin applications, including medical equipment in operation and patient rooms, aircraft and shared vehicle interiors, and sporting venues.
Axalta, a leading global supplier of liquid and powder coatings, has devel oped Plascoat® PPA 742, a single-lay er thermoplastic that can be used as a primer for a range of metallic sub strates in conjunction with an Alesta® topcoat for optimal results.
Drawing on 150 years of coating ex pertise, this latest solution from Axalta maximise anti-corrosion performance while combining effectively with the aesthetics attributes of Axalta’s Alesta portfolio. The unique characteristics of Plascoat PPA 742 make it easy to apply, even on metallic substrates with sharp edges, ensuring it can accom modate the full range of component designs.
The solution provides exceptional protection in a variety of applications, including urban furniture, construction
fencing, metallic structures and other metal parts, with consistently strong results irrespective of thermal mass differentials.
Plascoat PPA 742 delivers first-class intercoat adhesion, excellent stability during the application of the topcoat, exceptional adhesion to a variety of metallic substrates and impressive du rability and reliability over time.
“Our portfolio of solutions responds to the ever-evolving coating require ments of projects around the world”, said Koen Linsen, Director Global Segment Strategy General Industrial at Axalta. “We have honed our ther mosetting, thermoplastic, and liquid product technologies over more than 150 years, enabling us to provide ex ceptional protection no matter how harsh the environment. Plascoat PPA
742 offers outstanding robustness, aesthetics and stability founded on in dustry-leading thermoplastic technol ogy. One of its major strengths lies in its compatibility with the Alesta range of topcoats, which ensure that it can be used in a whole series of highly de manding architectural and industrial contexts”.
Repsol inform that their technical experts have been essential for the two new Process Technology License and Engineering De sign Agreements recently signed by ECI Group, recognized as a global leader in engineering and technical services for high-pres sure polyethylene installations.
This strategic collaboration was formalized through the agree ment reached at the end of 2019 with Engineers & Construc tors International (ECI), according to which ECI Group clients, licensees of its EVA/EBA technology, benefit from our extensive experience of more than 40 years of operating high-pressure pol yethylene plants for the production of LDPE and EVA and EBA copolymers in our industrial complexes in Spain and Portugal, and in the development of differentiated applications for these products.
Since the signing of the agreement, several Process Tech nology License and Engineering Design Agreements have been
reached with different clients:
- In October 2021, with Shandong Yulong Petrochemical Co. Ltd., a subsidiary of the Chinese group Nanshan, for a dual-flow plant capable of producing 200,000 tons per year of ethylene vi nyl acetate (EVA) and other associated high-pressure copolymers in the future.
- Currently, the two new agreements to produce 50,000 tons per year of Ethylene Butyl Acrylate (EBA) and 100,000 tons per year of Ethylene Vinyl Acetate (EVA), respectively, with the capac ity to produce other associated high-pressure copolymers in the future.
For Repsol, these new agreements represent a new milestone to reinforce the position of its chemical business in the market as a benchmark in EVA/EBA technology and development, together with a partner of recognized international prestige and a standard for high-pressure technology in the petrochemical industry.
DSM Engineering Materials an nounces the launch of a new, more sustainable version of its flagship product Stanyl®: Stanyl B-MB (Biobased Mass Balanced), with up to 100% bio-based content. Using the maximum possible levels of biomass-waste feedstock, it enables DSM Engineering Materials to halve the carbon footprint of this product line and, in turn, of the Stanyl B-MBbased products of its customers. This industry-first launch of a 100% bio-based high-temperature polyam ide underlines the business’s ongoing commitment to helping customers fulfil their sustainability ambitions by making planet-positive choices and supporting the transition to a circular and bio-based economy.
Global production of bio-based products roughly doubled between 2015 and 2020, but to conserve the planet’s natural resources and stay below the critical 1.5 degrees of glob al warming, the materials industry ur gently needs to accelerate the shift to sustainable feedstocks. Seeing this need, DSM Engineering Materials
has committed to providing bio- and/ or recycled-based alternatives for its entire portfolio by 2030.
Stanyl B-MB – now available with up to 100% bio-based content – is a fully ISCC+-certified mass- balanc ing solution, and delivers exactly the same characteristics, performance, and quality as conventional Stanyl. In addition, production of Stanyl B-MB now generates a carbon footprint up to 50% lower than the fossil-based original. In practice, this means a 3.3-ton CO2 reduction per ton produced – equivalent to charging 420,000 smartphones. Not only does this industry first further support the ‘Sustainable sourcing’ pillar of DSM Engineering Materials’ SimplyCircu larTM initiative, but it also raises the bar for biomass-balanced solutions in the industry. DSM Engineering Materials therefore continues to lead the way on driving carbon-footprint reductions and boosting customers’ environmental success.
“With both consumers and regu lators demanding more sustainable materials, the launch of 100% bio-
based Stanyl B-MB is an important step forward for our industry”, said Roeland Polet, President DSM En gineering Materials. “We are fully committed to developing sustain ably sourced products with a re duced environmental impact. With the same specifications and perfor mance but with a 50% lower carbon footprint, this new portfolio will enable our customers to fulfil their sustainability goals and contribute to a planet-positive future – so what they design today, we can all value tomorrow”.
A key player in the sale of its EVA/EBA
YEAR XI - SUPPLEMENT NO. 3 SEPTEMBER - OCTOBER 2022
MANAGING DIRECTOR: Simone Ghioldi REDACTION: Alessandro Bignami (a.bignami@interprogettied.com), GRAPHIC LAYOUT: Studio Grafico Page Vincenzo De Rosa, Simona Viapiana - www.studiopage.it
INTERPROGETTI EDITORI S.R.L.
Via Statale 39 - 23888 La Valletta Brianza (LC) Redazione, vendite e abbonamenti Tel./fax +39 039 5153705 www.interprogettied.com
SALES DIRECTOR: Marika Poltresi SALES: Simone Ghioldi (vendite@interprogettied.com) ADMINISTRATION: amministrazione@interprogettied.com © Copyright Interprogetti Editori Srl
The columns and news are realised by the editorial team. All rights reserved – All reproduction, even partial, of published material without the publisher’s consent is strictly prohibited.
SUBSCRIPTION RATES:
Italy: ordinary mail delivery EUR 45.00, COD delivery EUR 48.00 International: ordinary mail delivery EUR 60.00, express delivery within Europe EUR 70.00 Express delivery to Africa, America, Asia: EUR 85.00 Express delivery to Oceania: EUR 100.00 Single copy: EUR 10.00
The VAT on subscription prices as well as on the price of single copies is paid by the publi sher pursuant to article 74, sub-section 1, point C of the Italian DPR n. 633 of 26th Oct 1972 and subsequent amendments and additions. It is therefore not possible to issue invoices.
Registered at the Court of Milan on 3th June 2010 no. 315 Managing Director: Simone Ghioldi Print concluded on October 7, 2022 at Aziende Grafiche Printing S.r.l. Via Milano, 5 - 20068 Peschiera Borromeo (MI)
Information to be given to the data subject - art. 13, legislative decree 30th June 2003, no. 196. Personal data are processed, with or without the help of electronic means, by Interprogetti Editori S.r.l. - Via Statale 39 - 23888 La Valletta Brianza (LC), Italy, to send you the magazine requested and for the operations connected. The processing of data will be carried out by the persons who have been committed by the controller the task of performing the pro cessing operations connected with recording, modification, processing of personal data and printing, fulfilment and delivery of magazines, commercial and fiscal issues, accounting and call center activity. With reference to art. 7, Italian legislative decree 196/2003, you have the right to access to your data, modify, update or cancel data or to object to their processing for direct marketing purposes, by writing to the controller, and ask for the list of data processors.
Publisher’s information to public – art. 13, legislative decree 30th June 2003, no. 196. With reference to Italian Personal Data Protection Code and art. 2, point 2 of Code of Conduct for the processing of personal data in the exercise of journalistic activities, Interprogetti Editori S.r.l. informs that the place where personal data, images and photos are kept is La Valletta Brianza (Italy). Data can be used by journalists, free-lance journalists, persons in the role of trainee journalists and persons who carry out processing for the publication or occasional circulation of essays, articles and other intellectual works for the purpose of the exercise of their journalistic or similar activities. The processing of data will be carried out by the persons mentioned above and by persons in charge of printing and publishing activities. With reference to art. 7, Italian legislative decree 196/2003, you have the right of access to your data, modify, update or cancel data or to object to their, by writing to Interprogetti Srl, and ask for the list of data processors. It is understood that the provisions concerning professional secrecy in the journalistic profession shall be left unprejudiced as related to the source of the information if a data subject requests to be informed of the source of the personal data processed by journalists.