
6 minute read
Leggeri, riciclati e bio: i polimeri di RadiciGroup per la mobilità del futuro
La transizione ecologica è al centro della strategia del Gruppo. L’area di business High Performance Polymers punta in particolare allo sviluppo di materiali innovativi e green anche per l’e-mobility, un mercato in accelerazione e con enormi prospettive di crescita.
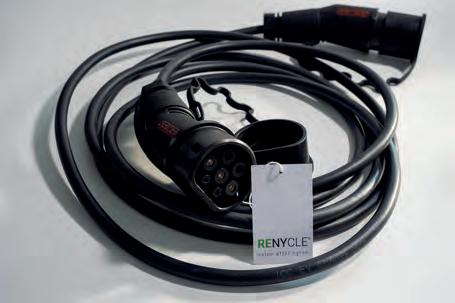
Advertisement
di Alessandro Bignami
La sostenibilità ambientale in senso ampio e la sua declinazione nell’ambito della mobilità elettrica sono i principali trend che stanno impegnando l’area di business High Performance Polymers di RadiciGroup e che ispireranno in larga parte la sua partecipazione alle imminenti fiere Plast (a Milano dal 5 all’8 settembre) e Fakuma (dal 17 al 21 ottobre a Friedrichshafen). Da alcuni anni la strategia del Gruppo è fortemente orientata verso questi temi, che d’altronde coinvolgono profondamente la produzione e lo sviluppo di materiali innovativi. “È una transizione che ha cambiato radicalmente anche il nostro sguardo verso il futuro”, spiega a La Plastica Oggi e Domani Erico Spini, Global Marketing Director di RadiciGroup High Performance Polymers. “Siamo molto concentrati sul metal replacement, ovvero sullo sviluppo di tecnopolimeri con prestazioni tali da poter sostituire i metalli in tantissime applicazioni, anche molto critiche. Per molte applicazioni, RadiciGroup ha proposto tecnopolimeri che possono sostituire, in molti casi, sia le leghe leggere sia l’acciaio, con costi spesso decisamente più competitivi. Ma oggi alle performance tecniche ed eco- nomiche dobbiamo aggiungere un terzo fattore che sta acquisendo importanza crescente: quello della sostenibilità ambientale. Considerare aspetti quali il minor impatto ambientale, l’eco-design e l’economia circolare sono ormai la norma nello sviluppo di nuovi progetti”.
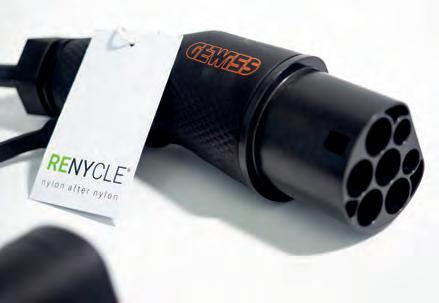
Ingegner Spini, quali sono i cardini attorno a cui ruota la vostra produzione di polimeri ecosostenibili?
“Siamo impegnati principalmente su tre fronti: materiali con caratteristiche elevate per la sostituzione dei metalli e l’alleggerimento dei componenti; il riciclo meccanico da fonte pre e post consumer; materie prime biobased”.
Cominciando dal primo, perché resta fondamentale la riduzione del peso?
“L’alleggerimento è un obiettivo che oggi appare ancora più importante di un tempo, ma che noi abbiamo sempre perseguito ot- tenendo importanti risultati. Diminuire il peso dei materiali ha effetti immediati sul contenimento dell’impatto ambientale, permettendo in particolare di abbassare le emissioni dei veicoli, in modo facilmente misurabile e certificabile da enti terzi, come oggi il mercato richiede”.
Nell’ambito del riciclo si sta affermando la vostra gamma Renycle…
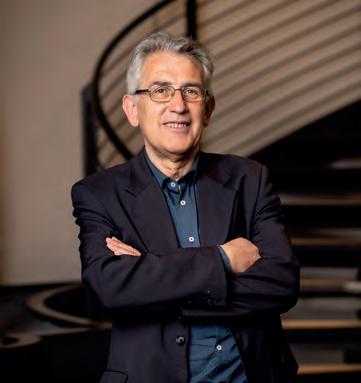
“Si tratta di una famiglia di prodotti a base di filo di poliammide PA6/66 riciclata. Vengono recuperati materiali provenienti dal riciclo meccanico di scarti sia post-industrial, inclusi quelli che provengono dalle divisioni di RadiciGroup, sia post-consumer, cioè ricavati da prodotti a fine vita. Nella lavorazione di post-industrial abbiamo un’esperienza ultradecennale, trattando da molto tempo gli scarti della nostra area di business dedicata alle fibre sintetiche. Accanto a questi materiali, ci stiamo dedicando sempre di più al recupero dei post-consumer, che chiaramente presuppone sfide più complesse. Spesso per la produzione di componenti con i tecnopolimeri si utilizzano vari materiali tra loro diversi e non semplici da separare nella fase di smantellamento di oggetti che hanno terminato il primo ciclo di vita. Comunque, quando possibile, si procede per diverse fasi di lavorazione, dal lavaggio fino alla separazione e alla trasformazione degli scarti in polimeri di nuova generazione utilizzabili in molteplici applicazioni. Oggi la gamma Renycle® conta oltre 40 prodotti che consentono un impatto ambientale minore rispetto agli analoghi prodotti ‘prime’, che derivano dalla polimerizzazione di monomeri di origine fossile. I Renycle possono essere composti da percentuali diverse fra materie prime post industrial, post-consumer e vergini, a seconda delle esigenze applicative. La quota di materiale riciclato può andare da un minimo di solito del 20% fino al 100%. Le prestazioni meccaniche sono un po’ inferiori rispetto alle soluzioni con materiali ‘prime’, ma il loro LCA è di gran lunga più ecosostenibile, come è possibile dimostrare attraverso misurazioni oggettive. Questi prodotti sono sempre più richiesti anche dai nostri clienti storici, che vogliono mostrare al mercato i progressi concreti e verificabili che stanno compiendo sulla strada della transizione ecologica”.
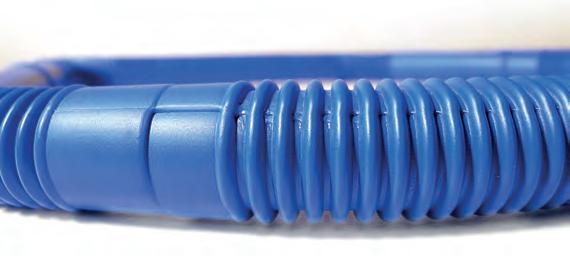
Diceva che il terzo pilastro della vostra produzione sostenibile è rappresentato dai materiali biobased…
“Abbiamo una serie di prodotti che contengono materie prime di origine biologica. Mi riferisco in particolare alla gamma Radilon® D, basata sulla poliammide 6.10, realizzata per il 64% a partire da acido sebacico, che si ricava dai semi dell’olio di ricino. È un prodotto che abbiamo lanciato oltre 10 anni fa e che offre ottime caratteristiche: rispetto alle poliammidi 6 e 6.6, per esempio, presenta maggiori resistenza chimica e stabilità dimensionale, oltre a una notevole resistenza ai sali stradali in caso di impiego nell’automotive. È in grado di sostituire la poliammide 12 di origine fossile e ha una forte valenza green, considerando che la pianta dell’olio di ricino consuma anidride carbonica nel corso della sua crescita. Inoltre la coltivazione di questa pianta non interferisce in maniera significativa con l’uso di terreni dedicati alla produzione di prodotti per l’alimentazione umana”.
Le vostre soluzioni con materiali di origine biologica trovano applicazione anche nella mobilità elettrica? Per quali componenti soprattutto?
“Per noi produttori di poliammidi uno dei campi di applicazione più interessanti nell’e-mobility riguarda la gestione termica dell’intero veicolo: dal motore elettrico al sistema batteria, dalle apparecchiature di potenza fino allo stesso abitacolo. Si tratta di una sfida tecnologica più complessa rispet- to al thermal management di un veicolo a motore endotermico, la cui inefficienza energetica consente di avere molta energia a disposizione per la regolazione della temperatura. Nel caso della vettura elettrica si tratta invece di recuperare energia senza compromettere l’autonomia chilometrica del motore. È un sistema dunque più articolato, formato da circa il doppio dei componenti rispetto alla gestione termica di un’auto tradizionale. Tra questi componenti sono molto importanti i condotti per i liquidi di raffreddamento, che devono superare test specifici, come quello della resistenza al contatto con i sali stradali. Per la realizzazione di questi condotti risultano particolarmente adatti i materiali di origine parzialmente biologica, come la poliammide 6.10 della gamma Radilon D. I nostri prodotti biobased possono essere utilizzati anche per molti altri componenti dell’auto elettrica, in segmenti diversi: powertrain, interni veicolo, chassis e altro ancora”.

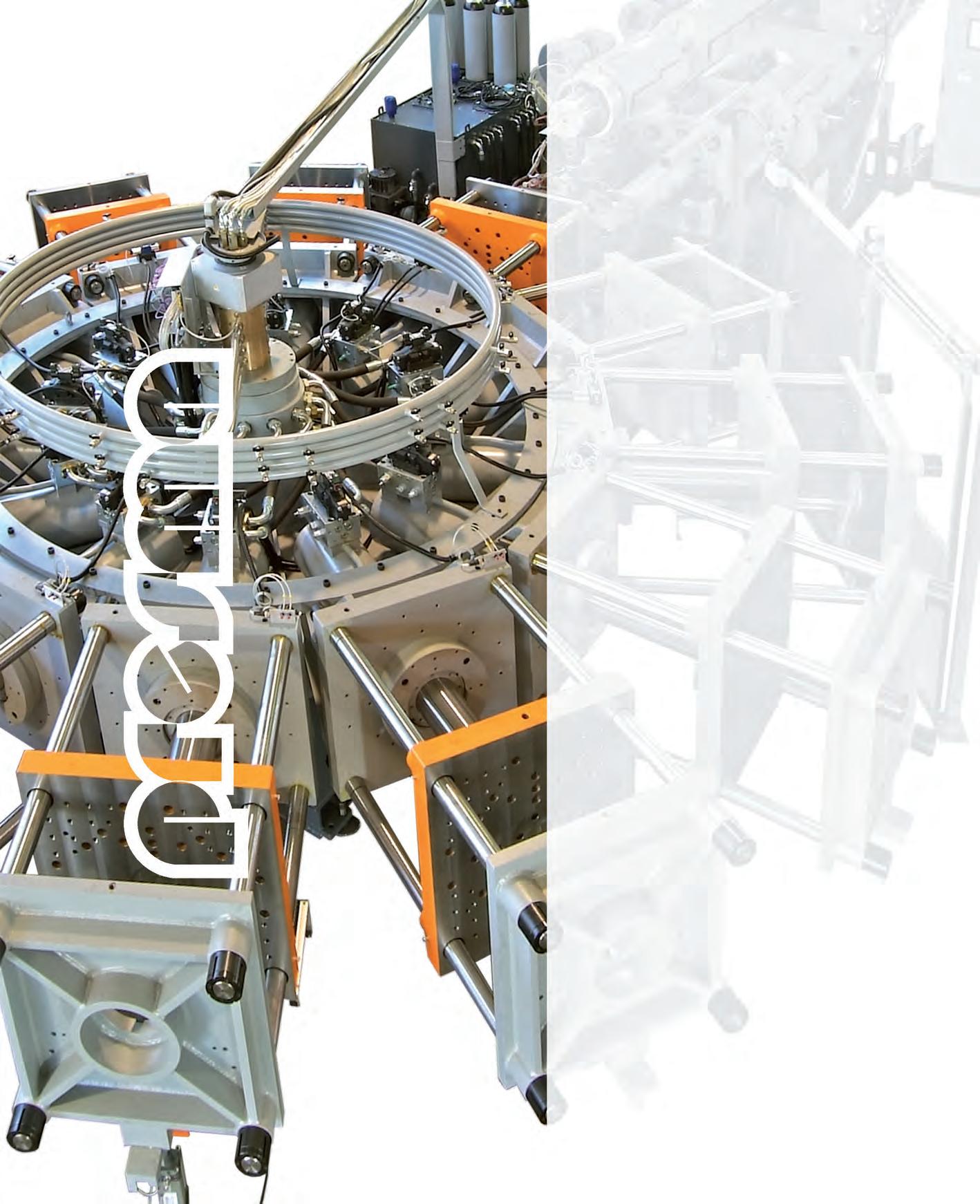
L’evoluzione dell’e-mobility è incalzante e richiede grandi investimenti per rispondere alle sue esigenze…
“Certamente bisogna essere reattivi e rapidi nell’assecondare questa evoluzione. Faccio notare che lo sviluppo di nuovi materiali è uno degli aspetti chiave su cui si sta concentrando la ricerca del settore. Per quanto ci riguarda, noi siamo avvantaggiati dalla lunga esperienza nella realizzazione di materiali destinati al settore elettrico ed elettronico, sia in ambito industriale sia civile. Molti di questi materiali, pur modificati dove necessario, sono già utilizzati nell’e-mobility”.
In termini di volumi di vendita, la mobilità elettrica vi sta dando risultati soddisfacenti?
“I riscontri sono interessanti, sia per la poliammide 6.10 biobased sia per i materiali di prima scelta ritardanti alla fiamma Radiflam ®, sviluppati per le specifi - che esigenze dell’e-mobility.
I volumi sono in crescita, ma è nei prossimi anni che ci aspettiamo una grande accelerazione. Gli investimenti delle case automobilistiche sono ormai quasi esclusivamente orientati all’elettrico, essendo stata pressoché abbondonata la ricerca e sviluppo nell’endotermico. Se le prospettive per un vicino futuro sono buone, al momento dobbiamo comunque considerare che il mercato dell’auto elettrica non supera il 14% del dato globale. Per i grandi numeri, occorrerà aspettare una decina di anni, entro i quali si prevede che il settore raggiungerà il 50% del mercato auto. E c’è da crederci. Non solo per il limite fis- bali nella mobilità elettrica, sia per la produzione di vetture, sia per la fornitura di componenti e apparecchiature. Siamo attenti al contempo alle opportunità del mercato indiano, dove abbiamo completato l’acquisizione del ramo tecnopolimeri della società Ester Industries Ltd”.
Proprio in Cina, a Suzhou, avete inaugurato quest’anno un nuovo stabilimento all’avanguardia.
Il nuovo stabilimento di RadiciGroup in Cina si estende su un’area di oltre 36mila metri quadrati ed è all’avanguardia per standard ambientali, sicurezza e tecnologie produttive sato dalla UE al 2035 per la vendita di vetture alimentate a benzina e diesel, ma anche perché l’e-mobility in questi ultimi anni ha corso più velocemente di quanto previsto dai più autorevoli studi. Le potenzialità sono dunque interessanti. E in Cina più ancora che altrove, visto che oggi il gigante asiatico è alla testa di questa evoluzione e presenta i principali player glo-
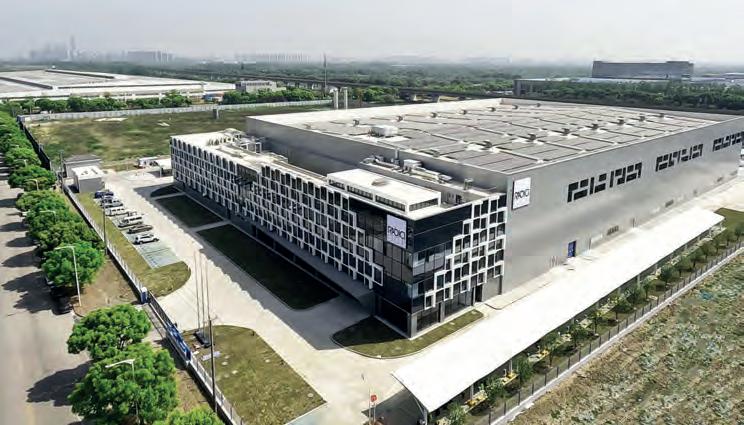
“È il frutto di un investimento di 35 milioni di euro, un fiore all’occhiello non solo per tecnologie produttive e standard ambientali, ma anche per la sicurezza e il benessere garantiti agli operatori. Ne siamo tutti orgogliosi. Si sviluppa su un’area complessiva di 36mila metri quadrati di cui circa la metà dedicati alla produzione e alla ricerca e sviluppo. Il resto è costituito da uffici, sale riunioni, spazi comuni, aree verdi e parcheggi. Ho avuto il piacere di visitarlo e posso dire che, nella mia non breve carriera nell’industria dei tecnopolimeri, non avevo mai visto nulla di simile”.
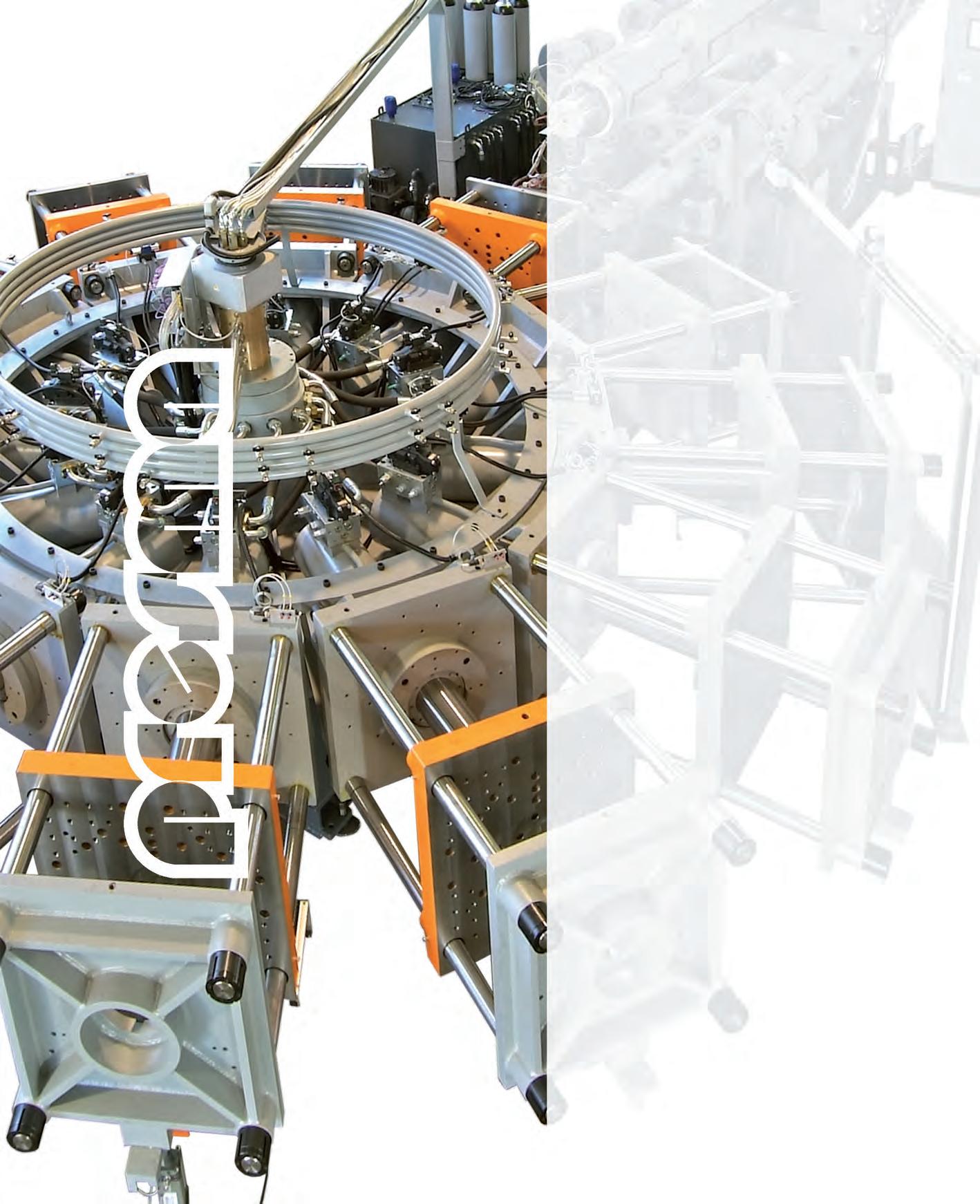
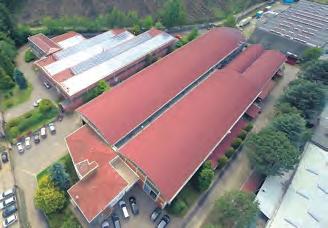