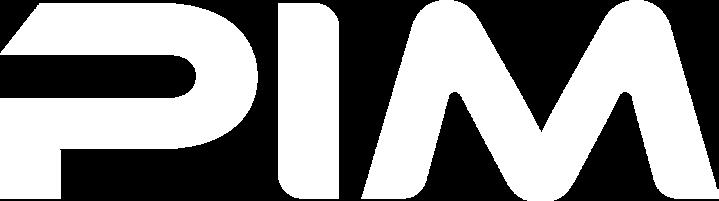
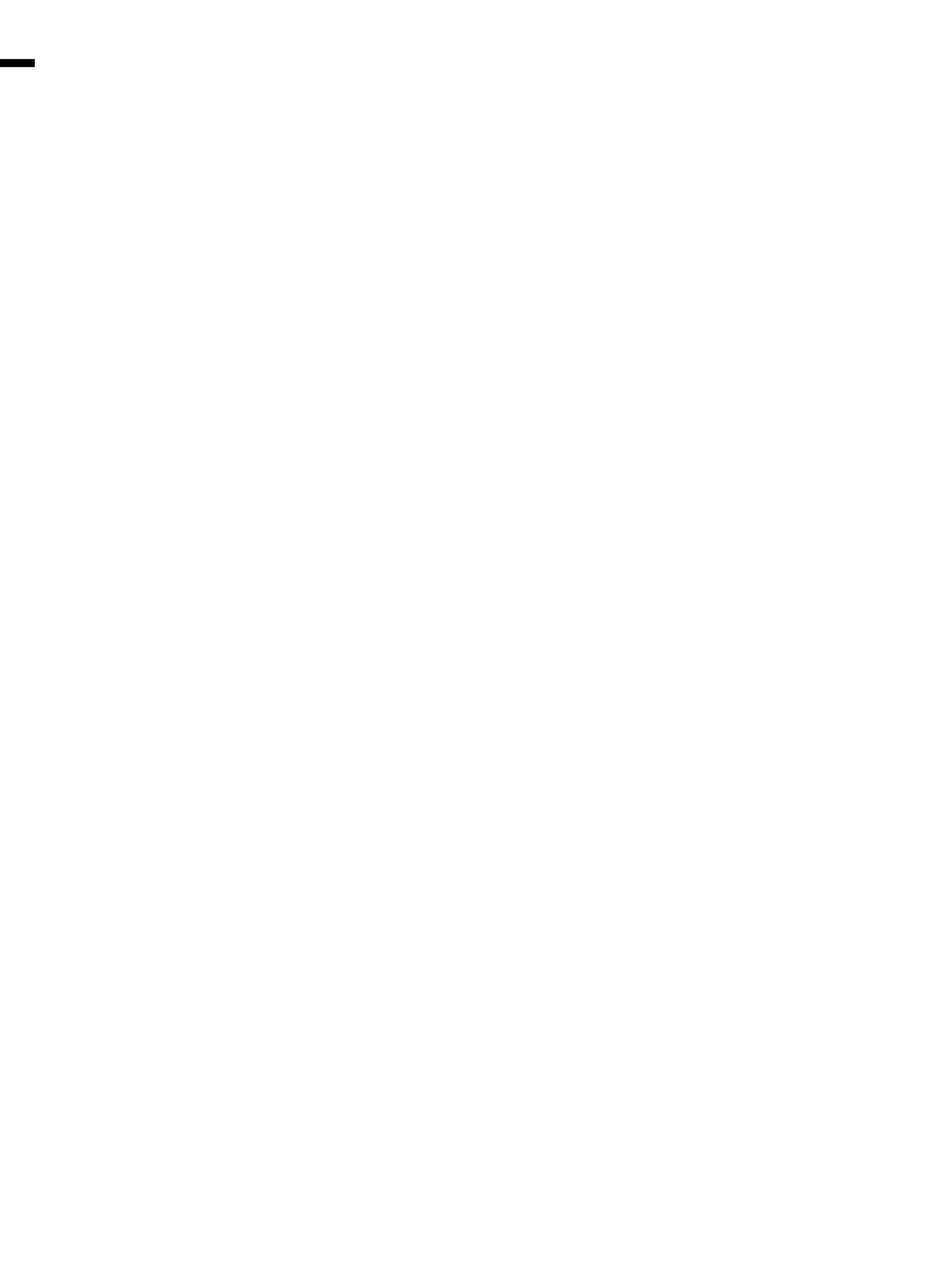
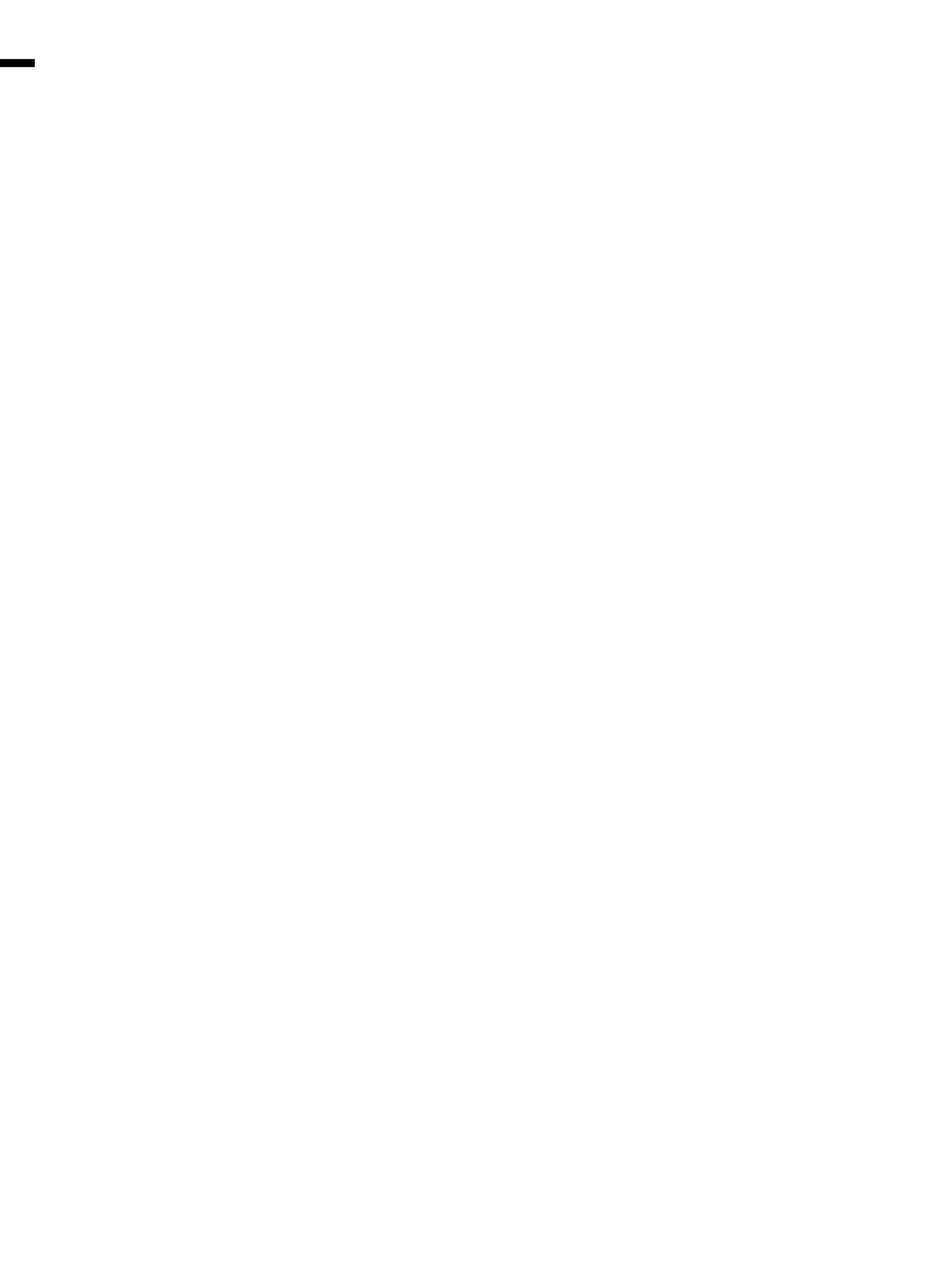
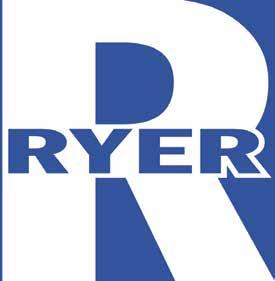
• At RYER, all our feedstocks are manufactured to the highest level of quality, with excellent batch-to-batch repeatability.
• RYER is the ONLY commercially available feedstock manufacturer to offer all five debind methods.
• RYER offers the largest material selections of any commercially available feedstock manufacturer.
• RYER offers technical support for feedstock selection, injection molding, debinding and sintering.
• A direct replacement for all current commercially available catalytic debind feedstocks
• Improved flow
• Stronger green and brown parts
• More materials available and better surface finish
• Custom scale-up factors available
• Faster cycle times
• 65°C / 150°F mold temperature
• Water Debind
• Custom scale-up factors available
• Large selection of available materials
• Solvent, Super Critical Fluid Extraction (SFE) or Thermal Debind methods
• Hundreds of materials available
• Custom scale-up factors available
Publisher & Editorial Offices
Inovar Communications Ltd
11 Park Plaza
Battlefield Enterprise Park
Shrewsbury SY1 3AF
United Kingdom
Tel: +44 (0)1743 469909 www.pim-international.com
Managing Director & Editor
Nick Williams, nick@inovar-communications.com
Group News Editor & Director
Paul Whittaker, paul@inovar-communications.com
Advertising Sales Director
Jon Craxford
Tel: +44 (0)207 1939 749 jon@inovar-communications.com
Assistant Editors
Amelia Gregory, amelia@inovar-communications.com Emma Lawn, emma@inovar-communications.com
Assistant News Editor
Charlie Hopson-VandenBos charlie@inovar-communications.com
Digital Marketer
Mulltisa Moung, mulltisa@inovar-communications.com
Production Manager
Hugo Ribeiro, hugo@inovar-communications.com
Operations & Partnerships Manager
Merryl Le Roux, merryl@inovar-communications.com
Office & Accounts Manager
Jo Sheffield, jo@inovar-communications.com
Technical Consultant
Dr Martin McMahon
Consulting Editors
Prof Randall M German
Former Professor of Mechanical Engineering, San Diego State University, USA
Dr Yoshiyuki Kato
Kato Professional Engineer Office, Yokohama, Japan
Professor Dr Frank Petzoldt
Ingenieurbüro Dr. Petzoldt, Geestland, Germany
Dr David Whittaker
DWA Consulting, Wolverhampton, UK
Bernard Williams
Consultant, Shrewsbury, UK
Subscriptions
PIM International is published on a quarterly basis as either a free digital publication or via a paid print subscription. The annual print subscription charge for four issues is £150 including shipping.
Accuracy of contents
Whilst every effort has been made to ensure the accuracy of the information in this publication, the publisher accepts no responsibility for errors or omissions or for any consequences arising there from. Inovar Communications Ltd cannot be held responsible for views or claims expressed by contributors or advertisers, which are not necessarily those of the publisher.
Advertisements
Although all advertising material is expected to conform to ethical standards, inclusion in this publication does not constitute a guarantee or endorsement of the quality or value of such product or of the claims made by its manufacturer.
Reproduction, storage and usage
Single photocopies of articles may be made for personal use in accordance with national copyright laws. All rights reserved. Except as outlined above, no part of this publication may be reproduced or transmitted in any form or by any means, electronic, photocopying or otherwise, without prior permission of the publisher and copyright owner.
Design and production
Inovar Communications Ltd.
ISSN: 1753-1497 (PRINT)
ISSN: 2055-6667 (ONLINE)
© 2025 Inovar Communications Ltd.
Powder Injection Moulding’s transformation from a niche process into a global manufacturing technology has occurred not through sudden disruption but through nearly five decades of incremental refinement and improvement.
Two articles in this issue of PIM International reflect that progress: the continued expansion of INDO-MIM – in particular its North American operation – and the growing importance of Metal Injection Moulding in the production of hinge components for consumer electronics.
Yet behind these success stories lies something less headline-grabbing, but no less essential: the foundational knowledge that underpins the development of the Metal Injection Moulding industry.
Few have contributed more to this foundation than Randall German, whose legacy was recognised at this year’s MIM2025 conference. As highlighted in our in-depth report, his work – from pioneering research on sintering to the education and training of a skilled MIM workforce – has been instrumental in enabling MIM to achieve commercial success globally.
As the industry explores new frontiers in sinter-based Additive Manufacturing and faces fresh challenges in scale, cost, and performance, the value of this accumulated knowledge and experience only grows. As in most areas of engineering, progress in MIM relies not just on innovation, but on the disciplined application of sound fundamentals.
Nick Williams Managing Editor
Cover image
HP Metal Jet Binder Jetting machines at INDO-MIM (Courtesy INDO-MIM)
As the industry leader in debind & sinter batch furnaces and equipment, Elnik Systems is known for precision, performance, and reliability. Our hand crafted furnaces are the gold standard for the MIM and Metal AM industries, delivering superior results for your production needs. When you think Debind & Sinter - Think Elnik. More than a furnace company.
12004 Carolina Logistics Drive, Ste A, Pineville, NC
elnik.com
for expert process engineering and toll services
Remote or In-person process, engineering, metallurgy support
Debind and Sinter Services
You Print It, You Mold It - We Debind & Sinter It”
In person facility walk through, process evaluation, and educational programs
For 25 years, DSH has been the best source for Metal Powder part making process support, Debind and Sinter Services and educational resources.
Our mission is to empower you with the knowledge and expertise to master part processing and unlock your path to success
53 INDO -MIM in North America: Scaling MIM and developing Binder Jetting to meet evolving market needs
With a portfolio of 12,000 MIM components and annual sales exceeding $350 million, INDO-MIM is among the most widely recognised names in the global Metal Injection Moulding industry. Founded in Bangalore in 1997, the company now supplies customers across five continents.
In 2017, it established a major facility in San Antonio, Texas, to meet rising demand and strengthen supply chain resilience. Bernard North visited the site for PIM International and reports on its development, strategic significance, and INDO-MIM’s increasing investment in Binder Jetting Additive Manufacturing. >>>
75 Redefining device design: The role of MIM in consumer electronics hinge mechanisms
The capabilities of Metal Injection Moulding have transformed the design of hinges, unlocking new possibilities in consumer electronics and beyond. By enabling the production of compact, durable, and highly complex components, the technology has allowed engineers to rethink functionality and aesthetics, especially in devices such as foldable smartphones, laptops, and wearables.
In this comprehensive review, Dr Chiou Yau Hung (Dr Q) explores how MIM’s unique advantages have influenced hinge innovation, reshaped product design, and opened new frontiers for mechanical systems. >>>
Experience significantly improved printability with Osprey® HWTS 50. This new lean hot-work tool steel powder reduces many of the challenges customers face in hot-work applications. Characterized by lower carbon content it offers higher thermal conductivity together with optimized resistance to tempering and thermal fatigue. With its alloy design philosophy, Sandvik contributes to the shift towards a more sustainable future in several ways.
Learn more and explore how Osprey® HWTS 50 creates opportunities for your business.
85 Binder Jetting at a crossroads: Dan Brunermer on scale, strategy and the technology’s future
In this wide-ranging interview, Nick Williams speaks with Dan Brunermer, founder of B-jetting LLC and veteran of the metal Binder Jetting (BJT) industry.
Drawing on decades of experience, Brunermer reflects on what past successes reveal about the future of Additive Manufacturing – from the growing demand for custom machines and integrated automation to the economic realities shaping adoption.
This is a candid and insightful exploration of where Binder Jetting stands today – and the challenges and opportunities that lie ahead. >>>
97 Prof Randall M German: Shaping the field of Powder Injection Moulding – a MIM2025 tribute
Held in Costa Mesa, California, the MIM2025 conference marked a significant moment for the Powder Injection Moulding community – not only for its technical programme and strong industry participation, but for a special symposium dedicated to honouring Prof Randall M German’s six-decade career. The tribute brought together former students, collaborators, and leading global experts to reflect on his scientific legacy and personal influence.
Dr Animesh Bose reports from the event, highlighting Prof German’s unparalleled role in the rise of PIM. >>>
09 Industry news
131 Advertisers’ index & buyer’s guide
Discover the leading suppliers of materials and equipment for MIM, CIM and sinterbased AM, as well as part manufacturing and more. >>>
137 Events guide
View a list of upcoming events for the MIM, CIM & sinter-based AM industries. >>>
The PIM International newsletter is sent to several thousand industry professionals worldwide. Register today to ensure you benefit from reading the latest industry news and advances in Metal Injection Moulding, Ceramic Injection Moulding and sinter-based AM technologies.
www.pim-international.com/e-newsletter
Iwaki Die-Casting Co Ltd, headquartered in Yamamoto, Japan, has completed construction and commenced operations at its second Metal Injection Moulding production facility in Kodaira, near Yamamoto.
The company was established as a die casting business in 1968, later adding MIM production in 1988. In addition to manufacturing components, it developed its own in-house MIM feedstock. In 2016, Iwaki Die-Casting consolidated its MIM production facilities in Kodaira.
“Thanks to continuous technological development and investments, we reached the limits of the existing site, prompting the construction of Kodaira Plant No 2 to further enhance our capacity and automation,” stated Akimasa Saito, Iwaki Die-Casting’s Representative Director and president.
“This plant introduces advanced automated systems, including unmanned sintering lines and integrated process control. We aim to build a stable, high-quality production system that can flexibly respond to customer needs and volume changes,” added Saito. www.iwakidc.co.jp
Epson Atmix Corporation, a group company of Seiko Epson Corporation based in Aomori, Japan, has completed construction of a new $38 million metal recycling facility at Kita-Inter Plant No 2. The new centre will recycle used metals from the Epson Group’s operations and the local community to produce raw materials for Atmix’s metal powder products. The recycling facility was first announced in 2022, with construction beginning in 2023.
Atmix will recycle out-of-specification metal powders, metal scraps from its own production processes, and used moulds and metal offcuts from Epson Group operations. These materials will be refined into high-quality raw materials, which will then be used at Atmix’s headquarters and Kita-Inter Plant to
produce metal powders suitable for Metal Injection Moulding.
Epson stated that it is committed to developing environmental technologies that support resource circulation and carbon reduction, particularly through materials innovation. Its Environmental Vision 2050 outlines its goal of becoming carbon negative and underground resourcefree by 2050. Kita-Inter Plant No 2 is expected to play a key role in advancing this goal.
Atmix produces a range of metal powders for a variety of manufacturing processes, including Metal Injection Moulding and Additive Manufacturing. The company also produces magnetic powders for use in power supply circuits, as coils for IT equipment, and for components in hybrid and electric vehicles.
www.atmix.co.jp
At Kymera International, we engineer high-performance metal powders, pastes, granules, and master alloys to power innovation across industries. From additive manufacturing and aerospace to medical, electronics, and beyond—our advanced materials enable breakthrough solutions. With a legacy of metallurgical expertise and a commitment to quality, sustainability, and customer collaboration, we provide tailored material solutions designed to meet the most demanding applications.
PARTNER WITH US AND UNLOCK NEW POSSIBILITIES. Learn more at kymerainternational.com
The MIM division of Japan’s Teibow Corporation has now been formally established as Hamamatsu Metal Works Corporation. The transition was completed on April 1 and follows the announcement from parent company Noritsu Koki Co, Ltd, to separate the two core businesses of its subsidiary Teibow Co Ltd. Hamamatsu Metal Works, and the remaining pen nib business (Teibow Co Ltd.), will operate under the umbrella of Teibow Holdings Co, Ltd.
In recent years, Teibow has identified strong growth potential in its MIM operations, with investments in management resources and the establishment of a new factory for mass-producing MIM components.
Based in Shizuoka Prefecture, Japan, the new president and CEO of Hamamatsu Metal Works Corporation
is Hiroshi Suzuki. “We have been able to reach this important milestone thanks to the customers who have been with us since the days of Teibow Co, Ltd, before the company was spun off, and we would like to express our sincere gratitude to them,” he stated.
www.h-metalworks.co.jp
Nano Dimension ‘exits’ Formatec and Admatec, highlights Desktop Metal’s ‘significant
Nano Dimension, headquartered in Waltham, Massachusetts, USA, has announced it is ‘discontinuing’ its Formatec and Admatec product lines. Reported in its 2024 financial results, and discussed in the accompanying investor call, it was also stated that the recently acquired Desktop Metal business is undergoing a strategic review as a result of its limited liquidity and significant liabilities.
Formatec and Admatec
Formatec was established as a Ceramic Injection Moulding company in Holland in 1996. Through its research into ceramic Additive Manufacturing and a partnership with Energy Center Netherlands, it established Admatec Europe in 2013. Admatec developed its Admaflex Technology, a stereolithography-
based AM process, and launched the Admaflex 130 AM machine in 2016. This machine can process both ceramic and metal.
After some years of small-scale Metal Injection Moulding production of refractory metals such as tungsten, Formatec added a full MIM production line to its portfolio in 2020. Nano Dimension acquired Formatec and Admatec in 2022.
Asked during the conference call about the future of these businesses, Julian Lederman, Chief Business Officer at Nano, stated, “We did look at divestment opportunities on all of them. That is our responsibility and our interest to shareholders to do so. After running processes there, we found that there wasn’t an opportunity to do so, and we ultimately had to make a decision on what is best
for our shareholders. And I think we were very convinced that the best thing to do was discontinue as soon as possible after running that process.”
Discussing the management’s recent assessment and strategic outlook for the company, Ofir Baharav, Nano Dimension’s CEO, stated, “The outcome was a focused commitment to two core product groups: Additively Manufactured Electronics (AME) and surface-mount technology (SMT). At the same time, we made the decision to discontinue non-core product groups, including Admatec, DeepCube, Fabrica, and Formatec.”
These moves, along with broader organisational efficiencies, were said to have enabled Nano to reduce the annualised operating expenses of its core business by over $20 million and increase revenue per employee from $147,000 to 223,000, a 52% gain. “This was disciplined, decisive action – and it delivered results,” Baharav added. www.nano-di.com
Gevorkyan a.s., headquartered in Vlkanová, Slovakia, has reported a successful start to 2025, with Q1 revenues of €20.88 million and statutory EBITDA of €8.35 million, resulting in an EBITDA margin of almost 40%. This represents an increase in revenues of 11.2% and an increase in EBITDA of 14.35% compared to the same period of the previous year. The company reported an operating EBIT of €4.21 million, an increase of 7.15% compared to the same period last year. The profit after tax (EAT) was reported at €2.98 million, representing a 26.32% increase compared to the same period last year.
“Our strong performance in an uncertain economic environment underlines our resilience and ability to use global uncertainties to our advantage,” stated Artur Gevorkyan, Chairman of the Board “We are optimistic about our plans and will combine organic growth with selective and value enhancing acquisitions.”
In the announcement, the company reported that it has won nine new long-term projects in the arms industry for the European and American markets. Following the success at a recent international trade fair, an agreement was signed to develop components for sporting arms in the USA.
Tekna Holding ASA, Sherbrooke, Quebec, Canada, has announced it has received three orders, valued at a total of CA$5.2 million, for titanium powder used in Metal Injection Moulding. The orders are scheduled for delivery in 2025 and 2026.
“These sales have historically been strong contributors to our cash flow, and it is reassuring to now have multiple customers for this material,
signalling an increase in demand and potential for margin improvement,” said Luc Dionne, CEO of Tekna.
The three customers are reported to be Tier 1 component manufacturers based in Asia. They plan to use the titanium powder to mass-produce sub-components such as digital watch cases, hinges, and buttons. Rémy Pontone, VP Sales and Marketing, added, “These orders
At the same time, mass production of components for a $30 million project that the company won in a 2024 tender, has now started.
The first phase of a project for a European manufacturer of optoelectronic devices using night vision, thermal imaging, and laser technology has been successfully completed. In the next phases, development and mass production for new applications in armaments and aerospace will continue.
In the automotive segment, new projects for autonomous robotic taxis have been acquired in the US and Europe. Additionally, after several years of technical and commercial negotiations, the company won a project for the petrol station and oil industry in the USA.
The company reports that it has also received orders from Europeanbased customers, notably one to supply a European plant wholly owned by a renowned Asian brand. Following the rapid and successful completion of development based on specific customer requirements, series production is scheduled to ramp up soon.
As part of investments in new premises, automation and robotisation, Gevorkyan reported that a warehouse and production area were expanded by approximately 1,000 m². In Q1 2025, a project to robotise two calibration presses was also completed, helping further reduce operational costs.
www.gevorkyan.sk
are for material consisting of smaller particles from our existing powder production, which is partly available in our inventory and partly from ongoing production. It plays a key role in our strategy to maximise sales from Tekna’s entire production yield. Through collaboration with our customers, we have successfully qualified this smaller cut size for MIM, improving resource efficiency, increasing sales yield, and significantly expanding our market share within the consumer electronics components industry.” www.tekna.com
Ceramic Additive Manufacturing (AM) offers a revolutionary step change in design and manufacture for ceramics
The possibilities include the ability to rapidly prototype designs, minimise material wastage and tooling costs, shorten lead times, and produce complex, near-net shape geometries that could not otherwise be obtained through conventional forming methods
From commercially available vat polymerisation techniques to novel AM processes, Lucideon can optimise printing and process parameters as well as develop novel formulations for your applications
Contact us for more information on Ceramic AM development
www.lucideon.com/ceramicam
query@lucideon.com
www.lucideon.com/company/lucideon
Phoenix DeVentures Inc, Dana Point, California, USA, a provider of product development and turnkey manufacturing services in the MedTech sector, has been acquired by INDO-MIM, Bengaluru, India. Following the acquisition, Phoenix DeVentures will continue operations as PDV MedTech, a wholly-owned INDO-MIM subsidiary.
The acquisition is expected to enable the companies to take on a greater variety of projects,
providing customers with more tailored solutions. As part of INDO-MIM, PDV MedTech will also have access to a broader global network, expanding its market presence and allowing customers to benefit from a wider range of resources and expertise.
“The acquisition of PDV MedTech allows us to provide a greater range of services that will increase speed to market, simplify supply chains and provide greater overall value to our customers,”
Phoenix DeVentures Inc, now PDV MedTech, offers a range of turnkey manufacturing services (Courtesy INDO-MIM/PDV MedTech)
Sandvik AB, headquartered in Stockholm, Sweden, has announced the appointment of David Goulbourne as the new President of the Powder Solutions division, effective May 1, 2025. The Powder Solutions division belongs to business area Sandvik Manufacturing and Machining Solutions, part of the Sandvik Group. The division includes the Osprey line of products as well as the Wolfram and
Buffalo Tungsten brands. Goulbourne will also be the President of Wolfram Bergbau und Hütten AG.
Goulbourne brings nearly twenty-five years of experience in the manufacturing industry and an entrepreneurial mindset. Before taking this role, Goulbourne held the position as Vice President Business Unit Solid Round Tools at Sandvik Coromant.
“I am thrilled to join the Powder Solutions division and contribute to
stated Krishna Chivukula Jr, CEO of INDO-MIM. “We share a common goal of helping innovative companies bring new products to market and manufacturing the highest quality medical devices.”
Jeffrey Christian, founder of Phoenix DeVentures, added, “INDOMIM’s and our shared vision of supporting entrepreneurs in Med Tech and their proven capabilities for scale and quality will be an enormous asset to our customers and enable further expansion in this space.”
“This partnership with INDO-MIM brings unparalleled scale and automation, extending our reach from innovative startups to large enterprises,” said Bryant Grigsby, CEO of Phoenix DeVentures.
Combining Phoenix DeVentures’ twenty-four years of experience transforming napkin sketches into commercialised products with INDO-MIM’s state-of-the-art capabilities is expected to drive groundbreaking advancements in the MedTech industry.
The announcement was made during LSI Dana Point, an event that offers industry executives from emerging companies, venture capital and other capital firms, strategics, and service providers an opportunity to meet.
www.indo-mim.com
www.pdvmedtech.com
strengthening and expanding our leadership in the powder manufacturing industry. My focus will be on ensuring that customer value remains our top priority, by continuously developing more sustainable processes and high-quality powder solutions,” said Goulbourne.
He will succeed Alex Nieuwpoort, who has decided to retire after twenty-eight years of dedicated service and significant contribution to Sandvik’s growth and business development. Nieuwpoort will remain with Sandvik until the end of June.
www.metalpowder.sandvik
These two binder systems have excellent characteristics during the production process and combine attractive prices with worldwide availability
High performance as well for the 3D-Printing process based on the water soluble binder system
The Metal Powder Industries Federation (MPIF) has released the 2025 edition of MPIF Standard 35-MIM Materials Standards for Metal Injection Molded Parts. The standard provides design and materials engineers with the latest property data and information to specify materials for components made by the MIM process.
Developed by the MIM commercial parts manufacturing industry, each section of the standard is clearly distinguished by easy-to-read data tables (inch-pound and SI units) and
explanatory information for materials listed.
This edition includes new material standards for:
• MIM-CpTi – Titanium
• MIM-Ti-6Al-4V – Titanium MIM-420 HIPed & HT – Stainless Steel
And updates for:
• MIM-17-4 PH – Stainless Steel Corrosion Resistance
The new standard replaces previous editions and is available to order in both digital and print. www.mpif.org
Nabertherm adds LH..DB furnace line for thermal post-processing and debinding
Nabertherm GmbH, headquartered in Lilienthal, Germany, has introduced its LH..DB furnace range, tailored for thermal post-processing of metal additively manufactured components, as well as the debinding and sintering of ceramic parts.
The furnace series is available in two different sizes, with oven volumes of 120 and 216 litres. This is said to allow heat treatment of all platform sizes of the current binderbased Additive Manufacturing machines. The LH..DB furnace is compact, with the controller, control elements, automatic gassing system, and switchgear integrated directly into the furnace housing. Once connected to the power supply, the furnace is immediately ready for use.
The LH..DB series is not limited to debinding and sintering processes in air: as a hybrid solution, processes under nonflammable process gases can be performed with the optional protective gas box. This allows debinding
of additively manufactured components made of metal or other materials requiring an inert atmosphere up to 600°C. Subsequent heat treatment under inert gas is possible up to 1,100°C.
During processes in air, preheated fresh air dilutes the escaping binder gases so that no ignitable atmosphere is created.
The 2025 edition of MPIF Standard 35-MIM Materials Standards for Metal Injection Molded Parts replaces all previous editions (Courtesy MPIF)
During inert debinding, the safety package monitors the gas flow of the gassing system and ensures reliable purging of the protective gas box.
In addition, the furnace chamber is purged with preheated fresh air independently of the process, improving the heat transfer into the charge and ensuring uniform debinding.
Specifications on each model in the new LH..DB series are available on the company website. www.nabertherm.com
Nabertherm has launched its LH..DB range of furnaces designed for thermal post-processing and debinding in Additive Manufacturing and ceramics (Courtesy Nabertherm)
Tekna Holding ASA, Sherbrooke, Quebec, Canada, has released its 2024 Annual Report, including the company’s 2024 Sustainability Report.
“As we conclude the year, Tekna has made significant progress despite a challenging market, driven by resilience and adaptability,” stated Luc Dionne, CEO. “Key achievements include improving cash flow from operations through effective management of working capital and a favourable litigation settlement.
“We focused on continuous improvement, executing cost-reduction initiatives, and restructuring the management team to boost transparency and performance. Our Systems product line maintained strong
efficiency and margins despite a revenue drop, while Materials saw growth in medical, aerospace, and consumer electronics. We entered the new year with confidence, healthy and with an improving backlog for Materials and good prospects for Systems.”
The cash balance was noted as having improved by CAD 4.8 million compared to the last quarter; net working capital improved by CAD 5.1 million year on year and CAD 2.7 million compared to the last quarter.
Low machine revenues had EBITDA effect of negative CAD 1.6 million in the quarter, compared to
Stratasys Ltd has acquired the key assets and operations of Forward AM Technologies GmbH, based in Rheinmünster, Germany. While continuing to operate under the Forward AM brand, the business will now function as a standalone company within Stratasys, named
Mass Additive Manufacturing GmbH.
Forward AM, the former Additive Manufacturing business of BASF, entered insolvency proceedings in November 2024, having undergone a management buyout in July 2024. The company
Forward AM offers a range of Ultrafuse filaments, including 17-4 PH and 316L stainless steels, for making metal parts (Courtesy Forward AM)
the same quarter last year. In 2024, the EBITDA effect of lower machine revenues was negative CAD 2.9 million compared to 2023.
“At Tekna, we remain committed to sustainability and are proud to share that our energy intensity per kilogram produced has improved to 12.1 kWh/kg (12.4), down from 16.3 kWh/kg in the 2019 baseline,”
Dionne explained. “For the first time, we have completed a comprehensive greenhouse gas assessment, which includes all material scope 3 emissions. This assessment provides us with valuable insights to prioritise our reduction efforts moving forward. Our goal to reduce scope 1 and 2 emissions by 50% by 2030 remains firmly in place. Our vision is to advance the world with sustainable material solutions, one particle at a time.”
www.tekna.com
offers a range of Ultrafuse metal filaments, including 17-4 PH and 316L stainless steels, for the Material Extrusion (MEX)-based Additive Manufacturing process Fused Filament Fabrication (FFF).
Operating as an independent materials business, Forward AM stated that its portfolio will remain open to all partners and platforms, allowing it to provide materials, technical support, and collaboration, regardless of the hardware used.
“With the backing of Stratasys, we now have greater resources and reach to drive innovation, expand our offering, and better serve your needs. This partnership empowers us to do more of what we do best: helping you succeed in Additive Manufacturing,” Forward AM stated in its press release.
“To our customers, partners, and friends: thank you for standing with us. We’re back, and we’re just getting started,” the company added.
www.forward-am.com www.stratasys.com
● GAS AND ULTRASONIC ATOMIZERS FOR SPHERICAL POWDERS WITHOUT ANY SATELLITES for LPBF, MIM, Binder Jetting and other Additive Manufacturing applications. High purity, sphericity and wide range of reproducible particle size distribution.
● WATER ATOMIZERS FOR MORE IRREGULAR POWDERS ideal for recycling/refining process, press & sinter process and others.
● AIR CLASSIFIERS FOR THE PRECISE SEPARATION OF METAL POWDERS into fine and coarse powder fractions especially in the range < 25 µm
IperionX, based in Charlotte, North Carolina, USA, announced that the Board of Directors of the ExportImport Bank of the United States (EXIM Bank) has approved an equipment finance loan of $11 million. Subject to the completion and execution of definitive documentation, this loan will support the significant expansion of IperionX’s advanced titanium manufacturing capabilities.
The EXIM Loan will finance the acquisition of state-of-the-art manufacturing equipment, including advanced Additive Manufacturing systems and precision machining tools. These manufacturing assets will enhance IperionX’s capabilities to produce a broad array of highperformance titanium components, leveraging proprietary and patented technologies at its Advanced Manufacturing Center in Virginia, USA.
This financing initiative is directly aligned with EXIM Bank’s strategic objectives, notably the ‘Make More in America Initiative’ and the China and Transformational Exports Program, which aim to strengthen US manufacturability capabilities, mitigate foreign supply chain vulnerabilities, and bolster economic resilience and national security.
The EXIM Loan provides IperionX with a low-cost, non-dilutive funding pathway to further scale its advanced materials and Additive Manufacturing
capabilities, and underpin a fully integrated, end-to-end titanium supply chain within the United States. Titanium is prized for its superior strength-to-weight ratio, exceptional corrosion resistance, and outstanding performance under extreme conditions, making it critical for advanced industries such as aerospace, defence, automotive, and healthcare. Currently, the US is overwhelmingly reliant on foreign sources for primary titanium (sponge) and titanium minerals, creating significant economic and national security vulnerabilities.
Through its Advanced Manufacturing Center, IperionX is utilising its patented technologies to produce high-value titanium products in Virginia, creating highly skilled American manufacturing jobs and addressing critical supply chain gaps. IperionX’s technology portfolio enables the production of low cost and high-performance near net shape products, semi-finished titanium products, spherical titanium powder for AM and MIM, and angular titanium powder for a wide range of advanced manufacturing applications.
The EXIM Loan directly supports IperionX’s mission to re-shore a lowcost, uninterruptable ‘all-American’ titanium supply chain, essential for both national security and sustained economic growth.
www.iperionx.com
Yuean New Materials, a leading supplier of MIM powders, feedstock, soft magnetic materials and carbonyl iron powders, based in China’s Jiangxi Province, has released its end-of-year results for 2024.
The company achieved revenue of 418 million yuan (approx $58 million), a year-on-year increase of 13.4%. Net profit for the year was 70.29 million yuan (approx $9.8 million), a year-on-year decrease of 12%, with net profit after deducting non-recurring items being 66.53 million yuan, a year-onyear decrease of 8.95%.
The company stated that the main reason for its revenue growth was the increased use of Metal Injection Moulding technology in
sectors such as consumer electronics and automobiles, replacing some traditional forging, casting, and similar processes to produce precision parts. This was said to have driven the company’s related powder product revenue growth and the increase in demand for downstream application products in electronic components.
Revenue from the company’s soft magnetic powder product line was 153 million yuan (approx $21.3 million), an increase of 19.1% year over year. Gross profit margin was 42%, a decrease of 5.4 percentage points year-over-year. The company said the main reason was that the fundraising and investment projects were converted into fixed assets, while production
capacity was still growing, and the operating costs, such as depreciation, increased.
The revenue of the carbonyl iron powder product line was 122 million yuan (approx $17 million), up 6.4% year-on-year, and the gross profit margin was 44.8%, down 4.9 percentage points year-on-year. The decline in gross profit margin was mainly due to the increase in raw material prices and production costs.
Regarding the total volume and development trend of the carbonyl iron powder industry, Yuean New Materials said in an interview with institutional investors in April this year that the global annual demand for carbonyl iron powder is about 30,000 tons, with a compound growth rate of about 20% in the past five years. If the price remains relatively stable, the annual increase in the existing market is expected to be about 10-15%.
www.yueanmetal.com
Tel.: +49 (0) 96 45 - 88 300 kerafol.com/technische-keramik/ cts@kerafol.com
Printy, based in Lučenec, Slovakia, has announced that it is now offering Metal Injection Moulding services for high-precision metal parts, paired with advanced Cerakote ceramic coatings said to result in exceptional performance and durability.
Building on its established Binder Jetting services, Printy’s move into MIM is geared towards offering its customers even higher volume part production.
Combining MIM with Cerakote’s ceramic coatings is reported to provide superior wear and corrosion resistance, thermal stability and chemical protection, as well as enabling lightweight, durable solutions. This is seen as ideal for defence, aerospace, and highperformance applications where both precision and endurance are critical.
www.printy.me
Epson Atmix Corporation, a group company of Seiko Epson Corporation based in Aomori, Japan, has partnered with Epson Europe Electronics GmbH to establish a sales office in Munich, Germany. The new office, which opened on April 1, 2025, is expected to strengthen and expand the group’s metal powder business in Europe.
Epson Atmix is a leading producer of high-quality water-atomised spherical metal powders, suited to both Metal Injection Moulding and
metal Additive Manufacturing. The company’s range includes iron-, nickel- and cobalt-based alloy powders.
Prior to the new sales office, Epson Atmix had been serving the European market directly from Japan. The Munich office will focus on enhancing the sales and service functions, enabling quicker response times to enquiries from across Europe.
www.atmix.co.jp
www.epson-electronics.de
Atomising Systems Ltd (ASL), headquartered in Sheffield, UK, has announced that the seventeenth edition of its two-day course, Atomisation for Metal Powders, will take place in Glasgow, UK, September 18-19, 2025.
The popular short course has been developed for engineers working in both powder production and research and development. It combines up-to-date practical information with theory and will cover
all current atomiser types for most metals, powder types and usages, along with plant design, operation and economics.
Building on previous events, the course will expand its coverage of powder production, testing, and properties for Additive Manufacturing.
ASL’s Tom Williamson, General Manager, and Dirk Aderhold, Technical Director, will present the course.
www.atomising.co.uk
Schunk Sintermetalltechnik GmbH
Discover the future of power electronics with our cutting-edge heat sinks, crafted using advanced Metal Injection Moulding (MIM) technology. These innovative heat sinks offer unparalleled thermal management, ensuring optimal performance and longevity for your electronic devices.
MIM allows for complex geometries and superior material properties, resulting in highly efficient heat dissipation. Perfect for high-power applications, our MIM heat sinks are lightweight, durable, and cost-effective. Upgrade your power electronics with our state-of-the-art MIM heat sinks and experience the difference in performance and reliability. Embrace the next generation of thermal solutions today!
� Roßtrappenstraße 62 06502 Thale, Germany
� +49 3947 7 1560 At thorsten.klein@schunk-group.com � schunk-mobility.com
Nanoe, based in Ballainvilliers, France, has announced the acquisition of the Upryze-Shock line of ceramic powder from Saint-Gobain ZirPro, based in Le Pontet, France. The deal includes technology transfer, a portfolio of existing customers, and an exclusive licence on the associated patent and trademark.
Upryze-Shock is a line of ultrahigh-toughness zirconia-based material developed by Saint-Gobain Research Provence R&D centre. It has applications in industrial tooling, especially shock- and wearresistant tooling such as welding location pins, cutting tools, and other high-wear and shock applications. Other possible applications include medical devices and watch components.
Upryze-Shock material is based on a ceria and yttria co-stabilised zirconia, reinforced with alumina in the form of platelets. It allows for a very high toughness compared to traditional yttria stabilised zirconia, with fracture toughness of 14 MPa. m 1/2 compared to a usual value around 6 MPa.m 1/2, while retaining good bending strength (1,000 MPa 4-point bending strength) and hardness (12.5 GPa Vickers hardness), which was traditionally the drawback of ceria-doped zirconia. Guillaume de Calan, CEO of Nanoe, shared, “We’re very happy to be able to add Upryze-Shock material to our already extensive portfolio of high-performance alumina/ zirconia composite powders. It will nicely complement our portfolio, and fits with our strategy of speciality
ceramic raw materials, with high-end, application-specific materials at the heart of this strategy. This transition allows us to keep serving the already existing customer base of SaintGobain, and offer this new material to our customer base as well.”
Frederic Wiss, commercial director EMEA of Saint-Gobain ZirPro, explained, “While Upryze-Shock is technically a great product, it remains a niche material for very specific industries, and did not fit ZirPro strategy anymore. We therefore wanted to find a solution for our customers to avoid supply interruption, and are very happy to partner with Nanoe to avoid such interruption.”
The transition of production from Saint-Gobain facilities to Nanoe was completed in 2024. From 2025 onwards, Upryze-Shock materials can be purchased directly from Nanoe. www.nanoe.com www.zirpro.com
Reliable Vacuum Furnaces for better end-to-end production. From prototyping to high-volume production, Ipsen offers vacuum furnaces in a variety of sizes that accommodate common heat-treatment processes used for AM, such as debinding, sintering, stress relieving and annealing.
Atomik AM, a UK-based advanced manufacturing start-up, has secured a £600,000 investment from the UK’s Northern Powerhouse Investment Fund II, managed by Praetura Ventures, to scale its sustainable materials technologies.
Founded by Professor Kate Black (FREng) in 2022, Atomik AM creates sustainable materials and patented technologies to support scalable
and efficient advanced manufacturing. The company is working with companies including Unilever and Ricoh to transform manufacturing, as well as developing and patenting its own intellectual property.
With the funding, Atomik AM is expected to grow its team by 40% and explore larger premises, as it scales its operations.
Over 6,500 production and laboratory furnaces manufactured since 1954
• Metal or graphite hot zones
• Processes all binders and feedstocks
• Sizes from 8.5 to 340 liters (0.3–12 cu ft.)
• Pressures from 10-6 torr to 750 torr
• Vacuum, Ar, N2 and H2
• Max possible temperature 3,500°C (6,332°F)
• Worldwide field service, rebuilds and parts for all makes
“At Atomik AM, we believe that true innovation starts with putting materials and sustainability first,” explained Professor Black. “This investment will allow us to grow our team and scale our patented technologies, accelerating our ability to deliver cleaner, more efficient manufacturing solutions. From our base in Liverpool, we’re proud to lead this transformation and work with global partners to set a new benchmark for sustainable, materials-led innovation in advanced manufacturing.”
The company also produces inks for 2D sensor printing and specialist pastes used in electronic coatings. It has delivered solutions to help companies remove unnecessary resources, such as water, from their manufacturing processes. Atomik AM has also developed a sustainable process for turning aluminium metal waste into more durable products, with the excess waste from this process then recycled into energy, representing a more endto-end approach to sustainability.
Atomik AM is currently in the process of patenting a series of new and innovative manufacturing products, including a universal binder for Binder Jetting metal Additive Manufacturing. Its universal binder is designed to work across multiple material systems, removing the need for unique formulations for different metal powders. This development could have major implications for manufacturers, particularly those working with a range of materials or looking to switch between materials without overhauling their entire process.
This latest funding also follows a £125,000 investment from Liverpool City Region Combined Authority-backed LYVA Labs, who invested in Atomik AM earlier this year. Akshay Bhatnagar, Head of Investment, LYVA Labs, added, “We are delighted that Atomik has secured investment from NPIF II and Praetura. This is great news for the Liverpool City Region. We are excited to be working with Praetura to support Kate and the team to accelerate the Additive Manufacturing revolution which is underway.”
www.atomik-am.com
Regardless of the complexity of your custom application and formulation, it remains standard for us with our quality systems, technical support, and two proprietary binding systems.
We ensure 100% batch-to-batch consistency, a wide range of alloys, and 36 years of supplying MIM feedstocks for mission-critical parts.
Advanced Metalworking Practices (AMP) manufactures and supplies a wide range of both standard and custom-configured MIM feedstocks for your application. Contact Chris Chapman at cchapman@ampmim.com or 724-396-3663.
Scan the QR code or click here to view our current list of alloys www.ampmim.com/resources
Electronic audio equipment manufacturer Ortofon, based in Nakskov, Denmark, has released its new MC X range of phono cartridges, using Metal Injection Moulding to produce the frame structure.
A phono cartridge is the small, stylus-containing device mounted at the end of a turntable’s tonearm. Its main function is to convert the mechanical vibrations from a record’s grooves into an electrical signal that can be amplified and played through speakers.
Traditionally, Ortofon used an extruded aluminium core followed
by machining. With the MC X series, however, the company has turned to Metal Injection Moulding to improve precision and design flexibility.
The new MC X series features honeycomb-structured stainless steel fabricated via MIM. According to the company, this refined structure ensures superior mechanical stability, providing the basis for precise and accurate sound reproduction.
After the moulding and sintering processes, the cartridges are surface treated by Physical Vapour
Each of the cartridges in the MC X range features a different stylus material and/or shape (Courtesy Ortofon)
Deposition (PVD) to enhance appearance and extend material integrity.
“With this production method, new shapes and ways of designing the structure open up the possibilities,” Peter Wieth Hjordt, Ortofon Product Director, told What Hi-Fi?
The cartridges also include coils wound with silver wire and a newly developed system that integrates a pole cylinder into the rear magnet yoke. These enhancements are designed to optimise the signal path and improve clarity.
The MC X range consists of four cartridges, each offering a different stylus and price point. The cartridges are designed to be compatible with a large number of tonearms and turntables.
www.ortofon.com
Ortofon’s new phono cartridge series is distinguished by its MIM honeycomb pattern (Courtesy Ortofon)
Seco Tools, headquartered in Fagersta, Sweden, has introduced a new self-service carbide tool recycling system in an effort to make the recycling process simple, more transparent and efficient. The digitalised buy-back programme, available in a number of its markets, enables customers to easily return used carbide tools and contribute to a circular economy.
The new web-based service, accessible through customers’ My Pages accounts, offers a streamlined approach where users can request price quotes for their used carbide tools, order free recycling containers, book shipments, track orders, monitor CO 2 savings, and receive a sustainability certificate. By recycling used carbide tools, Seco helps reduce reliance on virgin raw materials such as tungsten,
cobalt, and tantalum. This approach is said to lower energy consumption by 70% and cut CO 2 emissions by 64%.
“We are committed to making carbide recycling easier and more accessible for our customers. This digital transformation enhances efficiency while ensuring we meet our ambitious sustainability goals,” stated Malvina Roci, Circularity Manager at Seco.
This service is already available in several markets, with ongoing expansion planned across Europe, the Americas, and Asia Pacific.
www.secotools.com
Granutools, based in Awans, Belgium, has introduced its GranuCharge At Line (AL), an instrument designed to measure electrostatic charges in powders during flow in real time and directly on the production line.
The new GranuCharge AL is designed to measure electrostatic charges in powders (Courtesy Granutools)
Electrostatic charging is a common challenge in powder processing industries such as Additive Manufacturing, and metal powder handling. This phenomenon affects powder flowability, causes handling difficulties, and can even present safety risks.
Unlike traditional lab-based methods, the GranuCharge AL provides instant access to the charge per mass measurement through an integrated load cell combined with a Faraday cup connected to a highly sensitive electrometer. As powder flows through the process and into the device, the GranuCharge AL automatically captures the accumulated electrostatic charge, delivering high-precision results with minimal setup, all without stopping production.
GranuCharge AL allows users to assess how equipment such as hoppers, feeders, and blenders influence electrostatic charge accumulation to optimise material handling and process design. It also enables users to monitor charge effects on powder spreadability in Powder Bed Fusion machines or during nozzle flow in Directed Energy Deposition (DED), helping to improve powder bed quality and process reliability. Additionally, the GranuCharge AL identifies charge build-up hotspots on production lines in real time, enabling swift corrective actions without interrupting operations.
GranuCharge AL is reportedly the only compact instrument capable of real-time electrostatic charge measurement under true process conditions. This innovation helps industries reduce downtime, optimise materials, and enhance process reliability by providing critical data precisely where it is needed.
www.granutools.com
William Rowland, headquartered in Barnsley, UK, has announced it is celebrating its 195 th anniversary this year, marking almost two centuries in the metals industry. Founded in 1830 by Jonathan Rowland, the company has evolved into a global supplier of metals and alloys, serving a diverse range of sectors including civil aerospace, defence, automotive and EV, energy, Additive Manufacturing, petrochemicals, and electronics.
In addition to its revert alloy and refined metals businesses, William Rowland is an established supplier of metal powders in different particle sizes, shapes and alloys. The company offers gas-atomised metal powders specifically designed for Additive Manufacturing, including Inconel 625, 713 and 718 nickel-based powders possessing high strength properties and resistance to elevated tempera -
tures. It also offers Hastelloy X, a nickel-based alloy that has exceptional strength and oxidation properties, and F75, a cobalt chrome alloy.
With the support of its parent company, AMC Group, William Rowland recently invested in a state-of-the-art headquarters and recycling centre in Tankersley, which has enabled it to expand and diversify its offerings even further.
Recent investments in key plant room equipment are said to have reinforced the company’s commitment to precision, efficiency, and minimising waste. The company is also placing a greater focus on scrap and recycling supply chains, reducing its carbon footprint while recirculating valuable metals back into the industry.
www.william-rowland.com
CeramTec GmbH, headquartered in Plochingen, Germany, has announced that Dr Carla Kriwet will become the group’s new CEO and President Medical, by the end of 2025 at the latest. It was also confirmed that Dr Hadi Saleh, the current CEO, will transition to a new role as nonexecutive director of the company’s Supervisory Board.
Dr Kriwet, who will join CeramTec in July 2025, is reported to bring experience from leading a number of successful global businesses, including serving as CEO of BSH Hausgeräte GmbH, CEO of Fresenius Medical Care AG and CEO of the Connected Care division at Philips NV.
Dr Saleh and Dr Kriwet will work closely together in an effort to ensure a smooth and effective transition for CeramTec.
“CeramTec would like to thank Dr Hadi Saleh for his successful leader -
ship, passion and commitment over the past decade,” the company stated. “We look forward to his continued contributions as a member of our supervisory board.”
www.ceramtec-group.com
Dr Carla Kriwet will take over the roles of CEO and President Medical of CeramTec by the end of 2025 (Courtesy CeramTec)
first long-term study shows 92% success rate for additively manufactured bioceramic implants in mandibular surgery
Lithoz, based in Vienna, Austria, has shared its first scientific long-term study on additively manufactured bioceramic patient-specific implants (PSI), which showed a total success rate of over 92% achieved with Lithoz’s LithaBone TCP 300 tricalcium phosphate material.
Processed on a Lithoz CeraFab machine, these implants display the high medical standards of Lithoz technology, which, as of recently, have been produced under an ISO 13485 certified quality management system.
This study, which evaluates the healing success of LCM-manufactured ceramic implants in human bodies over a follow-up period of five years, is expected to support the expanded use of ceramic Additive Manufacturing in surgery.
Complex/miniature medical device components
High temperature stainless steel/superalloy automotive parts
Advanced ceramics with high density, high wear and tear resistance, and high precision.
Micro MIM/CIM
Materials customization and RnD.
Lithoz’s first scientific long-term study on additively manufactured bioceramic patient-specific implants showed a total success rate of over 92%, achieved with Lithoz’s LithaBone TCP 300 tricalcium phosphate material (Courtesy Lithoz)
In a minimally invasive approach, fourteen patients between seventeen and fifty-seven years of age suffering from dysgnathia were treated with patientspecific implants produced on a Lithoz CeraFab machine to prevent antegonial notching. Delivering ideal osteoconductivity and osteoinductivity, the study clearly confirmed the implants’ potential to reconstruct and bridge healing gaps occurring after surgical bone-cutting intervention (‘osteotomy gap’) due to their interconnected pores. The study also found that the rapid growth of new bone tissue in the beta-TCP implant was promoted.
Prior to this study, surgeons had yet to find an ideal solution to the postoperative development of mandibular lower border defects and irregularities following bilaterial sagittal osteotomy (BSSO).
Dr Johannes Homa, Lithoz CEO, shared, “This first-ever long-term clinical follow-up study marks a historic moment for the entire Additive Manufacturing industry! These results are not only about celebrating a great achievement for our Lithoz LCM technology. By clinically proving a success rate of over 92%, we’ve set a game-changing milestone in the history of surgery to establish the 3D printing of patient-specific bioceramic implants as a fullyfledged alternative alongside traditional surgical interventions.”
The clinical paper’s conclusion states “the feasibility and potential of the ß-TCP gap PSI concept as an innovative and promising approach to prevent antegonial notching after BSSO at primary surgery and in the long-term.”
www.lithoz.com
The European Powder Metallurgy Association (EPMA) has appointed Adeline Riou as its new president. Riou, who serves as Market Development Director – Metal Powders at Aubert & Duval, France, succeeds Ralf Carlström of Höganäs AB, Sweden, who is stepping down after six years as the association’s president. The EPMA also announced Steven Moseley, Chief Scientist Hard Materials & Key Expert at Hilti, as its new Treasurer.
The appointments were confirmed during the association’s General Assembly. Every three years, the EPMA Statutes require members to elect a new president and treasurer, both subject to a maximum of two terms.
“I’m very pleased that Adeline accepted the appointment as President of EPMA,” stated
Carlström. “Her long experience within the Powder Metallurgy field, combined with her dedication, will be a very valuable asset for EPMA in the future.”
Riou has worked in the field of metal powders for close to thirty years, having been at Aubert & Duval since 2018 and at Erasteel for twenty-two years. Over that time, she has been very active within EPMA, where she initiated the EuroHIP sectoral group in 2009 and the EuroAM sectoral group in 2013 before joining EPMA Board and Council in 2023.
president, succeeding Ralf Carlström (right) (Courtesy EPMA)
She served as co-chair at the WorldPM2022 Congress and received the EPMA Distinguished Service Award in 2023. Riou is also the co-author of the EPMA’s Introduction to HIP technology and Introduction to AM technology publications.
“I am very happy and deeply honoured to have been elected as EPMA’s new president and even more so as the first woman to hold this position,” added Riou. “Many thanks to Ralf Carlström for the opportunity and for the excellent work and new ideas implemented in the last six years to strengthen the EPMA, in particular to recover from the challenging Covid crisis.”
www.epma.com
Our experienced team is ready to solve your toughest thermal processing challenges and will design, manufacture, install and maintain
Furnace you’ll ever own.
FEATURES
• Metal or Graphite Hot Zones
• Metal and Graphite Retorts
• Debinding & Sintering
• Trapping Systems to Suit The Best Thermal Processing Solution for the Powder Industry
APPLICATIONS
• Additive Manufacturing
• Metal Injection Moulding
• Ceramic Injection Moulding
• Powder Metallurgy
Yoshio Uetsuki, Executive Director of Japan Powder Metallurgy Association (JPMA), has announced his retirement, effective May 23, 2025. Tetsuya Sawayama, formally of Kobe Steel and a JPMA board member, was announced as the new JPMA Executive Director.
“I would like to express my deepest gratitude for the exceptional support received during my term in office,” Uetsuki stated. “I will treasure all the happy memories I shared with you all.” www.jpma.gr.jp
The Verder Group, headquartered in Haan, Germany, has announced the establishment of Verder Scientific Iberia, the company’s thirteenth sales facility. Located in the city of Eibar in the Basque Country, with sales and service representatives across Spain, the new facility will be the central hub for all operations in Spain and Portugal. Verder Scientific Iberia is a joint venture with Neurtek, the company’s distributor.
With the partnership, Verder is also integrating the Retsch brand into the new organisation, which was previously managed by Biometa.
Verder Scientific Iberia will be equipped with a modern demonstration laboratory and service centre, ensuring hands-on technical support and training opportunities for its customers.
This strategic decision is said to reinforce Verder’s commitment to market expansion and closer customer engagement. It allows the company to enhance its market presence, improve support, and achieve synergies across its product lines. www.verder.com
The EROWA PM Tooling System is the standard interface of the press tools between the toolshop and the powder press machine. Its unrivalled resetting time also enables you to produce small series profitably.
www.erowa.com
Japan’s MIM industry serves customers around the world with innovative, high-performance engineered components. These are used in a wide range of applications, from industrial machinery to automotive, medical and more. Contact us to discover how we can support your MIM applications.
CASTEM Co.,Ltd. www.castem.co.jp/en
IWAKI Diecast Co.,Ltd. www.iwakidc.co.jp
JUKI Aizu Corporation www.jukiaizu.co.jp
Nakahara Precision Co.,Ltd. www.nprec.com
Nippon Piston Ring Co.,Ltd. www.npr.co.jp
Oriental Chain Mfg.Co.,Ltd. www.ocm.co.jp
OSAKA Titanium technologies Co.,Ltd. www.osaka-ti.co.jp
Osaka Yakin Kogyo Co.,Ltd. www.osakayakin.co.jp
Pacific Sowa Corporation www.pacificsowa.co.jp
Repton Co., Ltd. www.repton.co.jp
Taisei Kogyo Co., Ltd. www.taisei-kogyo.com
Teibow Co., Ltd. www.teibow.co.jp
TAV Vacuum Furnaces, based in Caravaggio, Italy, highlighted the work of its Performance Lab, a key strategic resource within the company’s R&D department, in a recent blog post.
The laboratory is equipped with a range of highly specialised furnaces designed to support R&D activities focused on refining heat treatment processes. Through its range of technical features, the company can perform numerous fundamental tests on metals and ceramics, including common heat treatments, sintering, brazing and thermochemical treatments.
In addition to research and development activities, the TAV Performance Lab also serves as a technology transfer platform, allowing the company’s customers to save money on their R&D activities and become operational with tested
and qualified processes directly after the furnace installation phase.
“Our commitment to research and development offers a concrete response to the most advanced industrial challenges and needs,
ensuring our customers always have cutting-edge products and processes,” the company explained. “We offer the opportunity to carry out dedicated test runs and this collaborative approach allows us to develop tailor-made solutions that perfectly meet specific needs, ensuring toplevel performance.”
www.tav-vacuumfurnaces.com
Bodycote plc, headquartered in Macclesfield, Cheshire, UK, has announced that the Science Based Targets initiative (SBTi) has officially validated its upgraded science-based carbon reduction target. This milestone is said to highlight Bodycote’s commitment to taking decisive action against climate change and driving efficiency across its global operations.
In 2022, the company became the first major heat treatment company to set a science-based carbon reduction target. The upgraded target builds on Bodycote’s earlier success in reducing its energy use and carbon emissions, committing to a 46% reduction in Scope 1 and 2 emissions by 2030 compared to a 2019 baseline. This new goal marks a major step forward from the previous target of
a 28% reduction by 2030, which was achieved six years early in 2024.
Bodycote provides advanced material solutions that address complex challenges, supporting customers in cutting emissions and achieving their decarbonisation targets. For instance, outsourcing heat treatment to Bodycote using a low-carbon thermal processing technology enabled a customer to lower carbon emissions by up to 90% per part, while also enhancing product performance.
Lily Heinemann, Chief Sustainability Officer at Bodycote, remarked, “Achieving SBTi validation for our enhanced target reflects our enduring commitment to sustainability and the measurable progress we’ve made. By exceeding our previous goal ahead of schedule
and setting ourselves this higher bar, we’re demonstrating that bold climate action is both achievable and essential. We are excited to continue leading efforts to make a meaningful impact on the global climate challenge and support our customers to achieve their goals.”
Over the past three years, Bodycote has achieved a 29% reduction in Scope 1 and 2 emissions, positioning itself strongly to meet the ambitious 46.2% reduction goal by 2030. In 2024, Bodycote launched a new integrated strategy that aligns its business objectives with longterm sustainability commitments. With clear objectives extending to 2030 and beyond, the group is delivering measurable environmental and social impact across all stakeholders. This commitment is further reflected in its strong performance in key ESG ratings, including an A-leadership rating for CDP Climate in 2024 and an AA rating from MSCI. www.sciencebasedtargets.org www.bodycote.com
TekSiC, based in Linköping, Sweden, has announced its new Xforge HT, a modular high-temperature induction heating furnace. The Xforge HT is designed for various high-temperature heat treatment applications, such as post processing of additively manufactured components, sintering, various diffusion treatments, material testing etc.
offering a modular solution that can be customised to each customer’s unique requirements.”
• Metal or Graphite Hot Zones
• Metal and Graphite Retorts • Debinding & Sintering
APPLICATIONS
“The Xforge HT represents the next step in our evolution as a company,” stated Joachim Tollstoy, CEO of TekSiC. “This product is a result of our dedication to innovation, designed with the flexibility to meet the specific needs of processes in high temperatures, low pressures, and introduction of process gases. We engineered it to provide the highest performance in the most demanding environments while
Our experienced team is ready to solve your toughest thermal processing challenges and will design, manufacture, install and maintain the Best Sintering Furnace you’ll ever own.
The Xforge HT is designed for high-temperature performance, reportedly able to stably exceed 2,500°C. Its pressure and gas management system is said to enable the precise regulation of the processing environment, allowing optimal conditions for complex heat treatment applications. The machine’s design is also focused on versatility, enabling the next generation of high-vacuum environments while allowing the controlled introduction of multiple gases, including hydrogen. Its advanced control algorithms enable precise thermal management, even making it possible for processing refractory metals such as tungsten, niobium, and tantalum.
• Additive Manufacturing
• Metal Injection Moulding
• Ceramic Injection Moulding • Powder Metallurgy
Throughout its development, Xforge HT underwent industrial reliability testing at customer sites over several years, demonstrating its ability to function during extreme high-temperature applications. Additionally, Xforge HT is CE-marked, certifying compliance with EU health, safety, and environmental standards. www.teksic.com
Our experienced team is ready to solve your toughest thermal processing challenges and will design, manufacture, install and maintain the Best Sintering Furnace you’ll ever own. APPLICATIONS
• Additive Manufacturing
• Metal Injection Moulding
• Ceramic Injection Moulding • Powder Metallurgy
Main Street, Adamsville, PA
Waygate Technologies, a Baker Hughes business based in Hürth, Germany, has introduced its Phoenix Nanotom HR (High Resolution) computed tomography (CT) system. The new system is designed to make advanced X-ray imaging technology accessible to a broader range of users and is reported to be ideal for applica -
tions across numerous fields, including Additive Manufacturing, material science, semiconductor and electronics inspection, battery technology research, geoscience, life sciences, and cultural heritage preservation.
As part of the new product introduction, Waygate also announced a technology collaboration with
X-ray equipment supplier Excillum, Kista, Sweden. Through this collaboration, Phoenix Nanotom HR will use a new high-resolution nanofocus X-ray tube supplied by Excillum for high imaging resolution and contrast across the full voltage range (40-160 kV).
“We are excited to present our Phoenix Nanotom HR here at Control 2025 and announce our strategic collaboration with Excillum,” said Ludovic Milosevic, General Manager Radiography Systems at Waygate Technologies. “Leveraging Excillum’s nanofocus source, the new HR version delivers up to five times better resolution than our existing stateof-the-art Nanotom M. That puts it on par with advanced optical magnification scanners – but with a simpler system, faster learning curve, greater flexibility, and at a better price point than comparable solutions.”
With its 300 nm focal spot technology, the Phoenix Nanotom HR is said to enable high geometric sharpness and detail detectability down to 50 nanometres (0.05 microns). It also allows for high contrast in high- and low-absorbing materials within a single image. The company states that high resolutions can be achieved 3-5x faster than with the Nanotom M or optical solutions, thus reducing scan times for samples requiring 120 minutes for 0.5 µm resolution to as little as forty minutes, or from one hour to ten minutes.
The Phoenix Nanotom’s user interface, featuring automated focal spot selection, is designed to increase ease of use. It allows users to explore sub-micron particles, design deviations, manufacturing issues, material flaws, and geometric structures.
In addition, the system is capable of 24/7 operation with a reportedly excellent stability, effectively reducing the need for maintenance work to a quarter of standard industry levels.
www.waygate-tech.com
The Manufacturing Intelligence division of Hexagon AB has launched MAESTRO, a new coordinate measuring machine (CMM) engineered to meet the rising productivity demands of modern manufacturing and the increasing quality requirements. The CMM’s digital-first architecture offers rapid measurement routines, an intuitive user experience and seamless data integration. With modular software and hardware, it is designed to scale with evolving production needs, making it ideal for aerospace, automotive, and high-precision manufacturing environments where there is a high demand for accuracy.
MAESTRO features a newly developed digital architecture, incorporating digital sensors, a single cable system, and a completely new controller and firmware. Together, these new capabilities increase
throughput, streamline the complete measurement operation, and ensure future-ready connectivity for modern production environments.
“Manufacturers told us they needed a next-generation system that tackles rising quality demands and skills shortages,” stated Jörg Deller, General Manager Stationary Metrology.“By rethinking our hardware and software from the ground up, rather than iterating on existing systems, we’ve had the freedom to create a high-accuracy inspection solution that is so intuitive that anyone from expert to new hires become significantly more productive. Meeting the needs of industry headon, MAESTRO’s digital backbone also makes it straightforward to integrate into modern connected factories, so stakeholders can improve quality quickly and definitively.”
Pilot users report dramatic productivity gains and reduced inspection lead times, helping to avoid production bottlenecks and to keep apace with fast-changing customer requirements. Customers have tested various sensors, ranging from high-speed laser scanning to tactile probes, with consistently strong results in both R&D and production applications.
Hexagon’s software tools and services, such as PC-DMIS and the Metrology Mentor, Metrology Asset Manager, and Metrology Reporting Nexus Apps, were developed in tandem with MAESTRO to create an integrated system that significantly boosts productivity from part loading to analysis, compared to isolated component solutions. The end goal is to deliver ease-of-use and fast workflows, from programming, execution, and usage to reporting and collaboration with colleagues in design and manufacturing.
www.hexagon.com
more? Engineered for precision, surface quality and easy machine handling –ideal for prototypes and small series.
Material Options (Metal)
Material Options (Ceramics)
Build Envelope
Quantity
Tolerance capability
CONTACT FOR MORE DETAILS
17-4PH, SS 316, Tool Steel M2 & S-7, Inconel 625, 4140
Alumina 99.5%, Zirconia
~ 300 grams max, Footprint equivalent of baseball size or less, 0.02” (0.50 mm) wall thickness minimum
10~50 samples based on footprint. Larger quantities up to 1,000 pcs welcome depending on the part size.
Within 2% of the feature size, 2~3 Ra Surface finish, Option of finishing to closer tolerances available.
NORTH AMERICA Email: Mukund.N@indo-mim.com Ph: +1 (210) 557-1594
EUROPE Email: InfoEU@indo-mim.com Ph: +49 1732656067
ASIA Email: InfoHQ@indo-mim.com Ph: +9198459 47783 / +91 98450 75320
ISO 9001:2015 / IATF 16949:2016 / AS
OptiMIM, a Form Technologies company with headquarters in Portland, Oregon, USA, has announced a strategic joint venture with Vasantha Tool Crafts Pvt Ltd, a division of the Vasantha Group based in Hyderabad, India. Together, the companies have established OptiMIM Global, a new entity to enhance manufacturing capabilities, expand market presence, and deliver advanced MIM solutions to industries worldwide.
“Partnering with Vasantha Tool Crafts Pvt Ltd aligns with OptiMIM’s mission to deliver world-class precision metal components with superior performance,” stated Marc Riquelme, President of OptiMIM & Signicast.
“This joint venture enables us to leverage Vasantha’s deep expertise in mould design and manufacturing to further enhance our offerings and
provide even greater value to our customers worldwide.”
By combining OptiMIM’s MIM technology with Vasantha’s expertise in precision mould design and high-accuracy manufacturing, the collaboration is expected to expand the market for complex metal components across the automotive, medical device, consumer electronics, industrial, defence, and aerospace sectors.
Dayanand Reddy, Managing Director, Vasantha Tool Crafts, added, “We are excited to join forces with OptiMIM to push the boundaries of MIM technology. Our complementary strengths in high-precision manufacturing and innovative design will drive new possibilities for our customers across various industries.”
In addition to OptiMIM’s strong presence in North America, Vasantha has established operations in India,
The newly formed OptiMIM Global will serve a wide range of industries (Courtesy OptiMIM)
Europe, and the USA. The partnership will bring together a large team of highly skilled and experienced professionals to create a robust infrastructure and streamlined operations. Combining research and development efforts is also expected to accelerate advancements in materials and MIM technology. www.optimim.com www.vasantha.com
CMG Technologies, Woodbridge, UK, recently celebrated fifty years in business. Established in 1975 as a fibre optic specialist, the company began its Metal Injection Moulding journey in the early 2000s, trading under the names Europlus and Egide UK, before becoming CMG Technologies after its 2013 management buyout. In 2023, CMG became part of the INDO-MIM group.
“Today is both a proud moment and significant achievement for our business and everyone who has been involved in its journey over the years,” stated Rachel Garrett, Managing Director. “Like with every business, we have been on a rollercoaster through the years, but have always been lucky to have an
The CMG Technologies team celebrates 50 years in business (Courtesy CMG Technologies)
incredible team that provides us both stability and innovation to move forward.”
Throughout its history, CMG has provided MIM and Additive Manufacturing solutions for numerous high-profile clients and made headlines during the COVID-19 pandemic for its work producing parts for ventilators.
Under Garrett’s leadership, the company has received national attention for its adoption of a four-day working week and its support of a healthy work/life balance.
Garrett added, “One thing that has never changed over the years is our company culture, which is hugely important to us. We’re a close-knit team that supports one another. We have shared so many highs and lows together, including the loss of my father [founder Chris Conway] in 2018, and are proud to keep his legacy alive through everything we do.”
“CMG Technologies are continuing to advance and we look forward to plenty more years of innovation and teamwork,” she concluded.
www.cmgtechnologies.co.uk
Emery Oleochemicals, headquartered in Cincinnati, Ohio, USA, has achieved ISO 50001: Energy Management Systems certification at its manufacturing facility in Cincinnati. In May 2025, the Ohio Chemistry Technology Council (OCTC) recognised this certification, honouring the company with an Award for Excellence in Environmental Performance.
In 2024, Emery launched a comprehensive Energy Management System (EnMS), including initiatives such as steam trap testing and repair, ozonator efficiency studies, steam boiler tuning, and employee training focused on eliminating wasteful energy practices. These actions are said to have already delivered results – most notably, per the company, a 25% reduction in nitrogen oxide (NOx)
emissions, or 16 tons annually, due to improved boiler performance.
Emery’s Energy Committee is now focused on setting new targets and identifying additional energy-saving opportunities for 2025 and beyond.
Emery Olechemicals provides a wide range of sustainable polymer additives, including binders for Metal Injection Moulding, Ceramic Injection Moulding and sinter-based Additive Manufacturing feedstock.
The company’s polyamide-based binder system is supplied as a readyto-use solution to be compounded with the powder to make a feedstock. It also supplies single ingredients for customers who want to tailor the binder composition to their specific requirements.
Our vacuum furnaces solutions for INDUSTRY and R&D LAB: - High Temperature Vacuum Sintering - Debinding & Sintering - Debinding/Pre-Sintering - High Pressure Sinter-HIP Vacuum thermal technologies: MIM, CIM, Hard Metal
www.emeryoleo.com
The Metal Powder Industries Federation’s (MPIF) Industry Development Board has launched a new University Outreach Program to promote metal powder technologies to future engineers.
Over the past eight years, hundreds of students have attended the annual PowderMet and AMPM conferences with grants from the National Science Foundation, Center for Powder Metallurgy Technology, and MPIF reserves. However, while student grant recipients had a good understanding of metal AM, they had limited knowledge of other metal powder technologies, such as press and sinter, MIM, and HIP.
The new Outreach Program will provide an opportunity to engage with students in their local educational environment and teach them that there are many ways to consolidate metal powders. To begin, the MPIF plans to take the Outreach Program to four universities during the autumn 2025 term. www.mpif.org
Lithoz, based in Vienna, Austria, has announced that its quality management system is now certified to ISO 13485 standards. This is said to mark a significant milestone in the company’s commitment to providing high-performance Additive Manufacturing solutions for the medical devices and dental sectors.
The ISO 13485 certification is internationally recognised as the gold standard for quality management in medical device manufacturing. This achievement builds on Lithoz’s existing ISO 9001 certification and enables compliance with the FDA’s QSR, positioning the company to meet
the industry’s growing demand for reliable, production-ready medical and dental applications.
“This certification reinforces our leading role as a trusted technology partner to medical innovators,” said Dr Daniel Bomze, Director of Medical Solutions at Lithoz. “It enables us to provide a reliable and low-risk entry point into LCM ceramic 3D printing to the many pioneers in healthcare and dental industry, accelerating the development of next-generation medical devices, applications and materials from initial prototype to serial production. The presence of these standards has removed a major hurdle on our technology’s path of adoption of our technology.”
ISO 13485 certification formally recognises Lithoz’s established position in regulated markets, ensuring that its Lithography-based Ceramic Manufacturing (LCM) technology meets the high standards required by medical device manufacturers.
Dominic Weiss, MD of the Vienna Business Agency stated, “Lithoz is a beacon of Additive Manufacturing in Vienna and proof of the city’s excellent innovation ecosystem.
The founders Johannes Homa and Johannes Benedikt established Lithoz thirteen years ago as students at the Vienna University of Technology and have built it up to become the global market leader in its field.”
“We congratulate Lithoz on this achievement, it opens the door to fundamentally change the medical sector – and to further strengthen Vienna as a hub for life sciences in Europe,” he concluded. www.lithoz.com
Sony has announced the latest iteration of its 1000X noise-cancelling headphone series. The wireless
WH-1000XM6 features a seamless folding mechanism that was produced via Metal Injection Moulding.
Sony’s new noise-cancelling headphones feature a MIM hinge (Courtesy Sony)
After several years of collaboration, Nanoval, headquartered in Berlin, Germany and Ingpuls, located in Bochum, Germany, have entered into strategic cooperation to produce nickel-titanium (NiTi) shape memory alloys. The companies have decided to deepen their partnership to boost production capacities and reduce delivery times for customers.
“For years, we have been impressed by Ingpuls’s ability to produce rods of difficult alloys for us,” Christian Gerking, Managing Partner of Nanoval GmbH, stated. “During recent mutual visits, we were also able to get to know the way of
working, the career and the teams of both companies. In the exchange on site in Bochum, we were fascinated by the consistent and thorough approach of the Ingpuls team during the founding and development phase of the company, as well as the extraordinary dynamics of the company’s development in recent years, which can be traced back to an incredibly sustainable and farsighted commitment of the Ingpuls founders.”
Dr Christian Grossman, member of the Ingpuls management board, added, “What is very exciting and strategically valuable is that demand
The folding mechanism is designed to help the headphones slip seamlessly into bags and aeroplane pockets.
The use of Metal Injection Moulding for hinges in consumer electronics has grown rapidly due to its ability to produce complex, miniaturised components with high strength, precision, and excellent surface finish. This growth is driven by rising demand for durable and compact hinge mechanisms in foldable smartphones, tablets, wireless earbuds, and wearable devices, where conventional machining or casting methods fall short in cost-efficiency and design flexibility.
MIM also supports high-volume production with consistent quality, making it ideal for the fast-paced consumer electronics sector.
www.sony.com
from aerospace, medical technology, nuclear technology and research is very diversified. After the cooperation with Nanoval has grown over the years, we were able to define processes and production procedures in a strategic exchange, through which we are now able to significantly reduce delivery times.”
Grossman continued, “This is very important for our customers, as it helps them to accelerate their development projects. Time to market is drastically shortened and everyone benefits.”
Ingpuls lists Metal Injection Moulding, Laser Beam Powder Bed Fusion (PBF-LB) and Electron Beam Powder Bed Fusion (PBF-EB) as potential processing methods for its shape memory alloys.
www.ingpuls.de
www.nanoval.de
Secure your spot as an exhibitor now! 18
Formnext 2025 offers the ideal platform for presenting your solutions all along the AM process chain to an international audience. Not only is Additive Manufacturing an essential component of the industry that facilitates tailored products, shorter development times, and sustainable processes; entire supply chains are changing due to the way in which it enables local production.
Join us in celebrating 10 years of Formnext and position yourself as an industry pioneer as you gather valuable business contacts and take an active role in shaping the future.
formnext.com/ exhibitors
With a portfolio of 12,000 MIM components and annual sales exceeding $350 million, INDO-MIM is among the most widely recognised names in the global Metal Injection Moulding industry. Founded in Bangalore in 1997, the company now supplies customers across five continents. In 2017, it established a major facility in San Antonio, Texas, to meet rising demand and strengthen supply chain resilience. Bernard North visited the site for PIM International and reports on its development, strategic significance, and INDO-MIM’s increasing investment in Binder Jetting Additive Manufacturing.
With more than 500 million parts shipped over the past twenty-eight years, some 12,000 MIM part variants in its portfolio, and annual sales of more than $350 million, INDO -MIM has become one of the most prolific and widely recognised companies in the global Metal Injection Moulding industry. Since PIM International last covered the company’s Indian operations in 2011 [1] and 2016 [2], that growth has only continued.
Founded in Bangalore in 1997, INDO -MIM now supplies customers across five continents, employs over 3,000 people, and operates two Indian MIM facilities spanning a combined 81,000 m². The company remains around 95% family-owned, with the rest of the shares held by longstanding employees and retirees.
In 2017, INDO -MIM signalled its global ambitions with the opening of a manufacturing facility in San Antonio, Texas. In April 2025, the author visited the operation on behalf of PIM International to learn firsthand how the company is meeting the challenges of global production and rising demand. After a detailed plant
tour and conversations with Jag Holla (Senior Vice President – Marketing), Sreenivasulu ‘Seenu’ Suri (General Manager – Operations), and Mahesh Mantrodi (Senior Manager – Primary Processing), it became clear that INDO -MIM’s US site is far more than a satellite facility. It plays a central role
in the company’s global production strategy. That impression was reinforced in a follow-up conversation with Krishna Chivukula Jr, CEO of INDO -MIM, who shared the long-term vision behind the company’s ongoing investment in people, technology, and production capacity.
1997: Joint venture founded
INDO-US MIM Tec (P) Ltd was established as a joint venture between INDO -MIM Private Ltd (51%) and the Advanced Forming Technologies (AFT) division of US-based Precision Parts Corporation (49%). AFT brought a decade of experience in MIM, and the core technologies introduced then – feedstock blending, injection moulding, debinding, and sintering – are still in use today.
1997: First plant opens
INDO -MIM’s first plant opened in Hoskote, a town near Bangalore in the Bangalore Rural District of Karnataka, India.
2001: Joint venture to single ownership
Dr Krishna Chivukula Sr led INDO -MIM Private Ltd’s purchase of AFT’s share, making INDO -MIM fully Indian-owned. Following this, the company experienced rapid growth, with a significant proportion of sales directed towards the North American market.
2002 North American sales office
North American sales operations – initially based in Ann Arbor, Michigan – were relocated in 2021 to Princeton, New Jersey. Currently, the facility is in Yardley, Pennsylvania.
2007: Second plant opens
A larger plant was opened in Doddaballapur, Bangalore.
2008: Investment casting facility established
Gowri Ventures, a precision investment castings plant, was established in Tirupati, Andhra Pradesh, India.
2017: Manufacturing in North America
Due to the high volume of business from the North American market, INDO -MIM leased a 36,000 m² manufacturing facility in San Antonio, Texas. This became the manufacturing plant for its wholly owned subsidiary, INDO -MIM Inc.
2020: Acquisition of Triax Industries
The company acquired a specialised investment castings plant (Triax Industries) in Chandler, Arizona. The company also operates a 3,000 m² finishing facility in Mexico, where it holds a 49% ownership stake. This facility supports post-manufacturing secondary processes for components produced at the Arizona and Texas plants.
2023: UK acquisition and new Chennai facility announced INDO -MIM acquired CMG Technologies, a MIM and Additive Manufacturing (AM) specialist based in Woodbridge, Suffolk, UK. A new 35,000 m² facility is under construction near Chennai, Tamil Nadu, targeted for completion in 2026.
2025: Acquisition of Phoenix DeVentures (now PDV MedTech) Phoenix DeVentures Inc, Dana Point, California, USA, is a provider of product development and turnkey manufacturing services in the MedTech sector.
Thanks to a combination of INDOMIM’s beginnings as a joint venture with an established US-based MIM company (see inset box, left) and the large North American market, a very high percentage of its business has, from the outset, focused on the US market. Jag Holla explained, “Many of our customers were, and are, single-sourced on us, and some of them were concerned about the supply chain risk and geographic distances, while other potential customers would only buy US-manufactured products.” Further, the increasing use of automation has reduced the cost differential between Indian and US manufacturing, prompting the decision to open a manufacturing facility in the US.
When asked, ‘Why San Antonio?’, Sreenu Suri explained, “The reasons were a favourable business climate in Texas, and a fairly short distance to the site in Mexico that conducts some finishing operations. The presence of a major Toyota facility in the city had also helped develop a high-quality manufacturing culture.” The selected site was a modern 36,000 m² facility located adjacent to the former Kelly Field US Air Force base, previously used as a maintenance and repair centre.
A ‘right of first refusal’ lease deal has allowed the operation to incrementally increase its occupied space as capacity has increased, as shown in Table 1, in response to rapidly growing business levels. The company retains the option to purchase, rather than lease, the facility if it chooses to do so. According to Krishna Jr, establishing production in the US “was a very, very big deal for us at the time. We were used to operating in India, so setting up in the US presented very different operational challenges. There was a lot to it for us, but we have clearly demonstrated that there is a market here. It has grown very quickly – we’ve just finished our third expansion.” Currently,
approximately half of the building is occupied and, depending on the rate of business growth, the company anticipates utilising the remainder over the next five years. Staffing has expanded rapidly and now stands at around 300 people.
While sales of products manufactured at the San Antonio site have grown rapidly, much of INDO - MIM’s production for the US market is still exported from India. At the time of the author’s visit, in late April 2025, the US administration had announced a tariff of 26% on imports from India. This tariff, like those imposed on most other countries, had been reduced to 10% for a three-month period during which negotiations on bilateral trade deals will take place.
Jag Holla noted that, while the cost differential has narrowed over time, manufacturing in India remains less expensive than in the US. However, the imposition of tariffs could erode – or even eliminate –this margin advantage. INDO -MIM therefore expects to shift further
“Jag Holla noted that, while the cost differential has narrowed over time, manufacturing in India remains less expensive than in the US. However, the imposition of tariffs could erode – or even eliminate – this margin advantage.”
Table 1 Past and projected future of capacity expansion at INDO -MIM’s San Antonio Facility
production onshore: “Many customers insist on US production, while others are increasingly moving towards it due to supply chain concerns and worries about future tariffs, even if a negotiated agreement between governments resolves the current ones.”
It is clear that INDO -MIM got ‘ahead of the game’ by establishing its US manufacturing operation eight years ago, recognising early on the benefits of manufacturing close to its customers. The company appears committed to significantly expanding
its US manufacturing presence. While tariffs may accelerate this shift, the path is already well established.
It is interesting to explore the typical sequence of tool design, prototype development and part production at INDO -MIM, as this workflow is a critical aspect of commercially successful MIM part development. Once a customer has expressed a
strong interest in obtaining a specific component through MIM, the tool design team in Bangalore creates a simplified single cavity ‘soft tool’ (i.e. one where the tool steel is not hardened). This will not include the complex conformal cooling channels used in production moulds and, in some instances, will omit some intricate features.
In parallel, ceramic setter prototypes are produced to allow for design optimisation early in the product cycle. Once finished, the mould is run on a production machine at one of the Bangalore facilities to manufacture a limited number of parts, which are subsequently debound and sintered on the various setter variants, followed by additional finishing steps.
These prototypes are then presented to the customer, typically after around four weeks, along with comprehensive Design for Manufacture (DfM) documentation, a final product drawing including tolerances, and a detailed quotation. If approved, a full production tool with hardened steel segments – and, in many cases, multiple cavities – is manufactured, purchased by the customer, and supplied to a production plant in India or San Antonio, along with optimised ceramic setters; the lead time for this part of the process averages approximately eight weeks.
Once the plant has a tool, the response time to a new production order is typically about three weeks; however, most customer contracts stipulate that the plant maintains up to eight weeks of ‘safety stock’, generally divided between semifinished (sintered) and finished goods, which enables very short delivery times when required.
Tool maintenance is free of charge to the customer. However, if a tool requires full replacement (typically after around half a million shots per cavity), customers will need to purchase replacement tooling. If or when a part is discontinued, the customer will take delivery of the safety stock and, since they own the tooling, has the option of either
retaining it, instructing INDO -MIM to scrap it, or contracting INDO -MIM to store it in case it is needed again.
One of INDO -MIM’s greatest strengths lies in its extensive tool design and manufacturing operation at the Doddaballapur facility. To date, the operation has produced tools for about 12,000 different MIM parts, highlighting its high levels of experience and expertise. Capacity is in place for approximately ninety new or duplicate tools per month, with actual production averaging around thirty new designs, along with some replacements. Each features between one and thirty-two cavities.
At present, nearly all of the mould tooling for the San Antonio plant is designed, manufactured, and qualified for production on identical injection moulding units in Bangalore before being dispatched to the San
Antonio facility. To support this transition, a dedicated part of the mould design and manufacturing capacity, along with staff, is assigned to assist the US plant’s operations.
The mould operation in San Antonio is, compared to the Indian facilities, modest in size, but its scope is expanding. It is used for preventive maintenance such as cleaning, and, when necessary, repair. This includes the replacement of worn or damaged core pins or mould segments.
Installed equipment includes high-speed milling for electrode making, wire Electrical Discharge Machining (EDM) and plunge EDM, also known as ‘sinking’. A recent addition is a multi-tank automated cleaning system. “New tooling is now being designed with special channels to facilitate automatic cleaning,” Sreenu Suri explained.
“The San Antonio tool shop has the capacity to manufacture four tooling sets per month, and is currently
“To date, the operation has produced tools for about 12,000 different MIM parts [...] Capacity is in place for approximately ninety new or duplicate tools per month, with actual production averaging around thirty new designs, along with some replacements.”
making one per month, and we plan to increase capacity to ten sets per month by 2027.”
The San Antonio facility uses powder produced by INDO -MIM in India as well as powders sourced from established suppliers in Japan and Europe. Powder batches are approved with
the aid of the on-site quality assurance laboratory.
INDO -MIM started manufacturing metal powder in-house in 2018.
Currently, INDO-MIM has three atomisers in production and three more on order, all in or planned for the Doddaballapur facility. The main driver was, and remains, concern about supply chain security for in-house MIM. As capacity has grown, however, the company also sells powder externally to customers using
“Currently, INDO-MIM has three atomisers in production and three more on order, all in or planned for the Doddaballapur facility. The main driver was, and remains, concern about supply chain security for in-house MIM.”
Laser Beam Powder Bed Fusion (PBF-LB) Additive Manufacturing, although the finer particle size ranges needed for MIM and Binder Jetting (BJT) are still used internally.
INDO -MIM keeps a minimum of three months’ inventory of metal powders and organic binders to guard against potential supply chain disruptions.
The San Antonio plant can produce approximately forty tonnes of MIM feedstock each month. The binder technology, along with the mixing and granulation steps, originates from processes introduced by AFT during the joint venture.
In line with INDO -MIM’s standardisation strategy, the feedstock production processes at the San Antonio facility are identical to those in Bangalore. A weighing room contains the balances and drums of metal powder, as well as both the wax and polymer binders used in MIM. During the plant tour, the author witnessed an impressive aspect of the company’s Enterprise Resource Planning (ERP) quality management system for the first time. This involved the use of live instructions with operator prompts, displayed on large digital screens, along with images of equipment and process steps, checklists, and the required amounts of binder ingredients for the operator to weigh. Data from the balances were clearly displayed, accompanied by feedback indicating whether more of a constituent was required or if some needed to be removed. Labels displaying the batch number, alloy type, and a barcode are printed to identify the batch throughout subsequent processes. The status of different work orders was also displayed; this highly visible system was present in multiple areas of the plant.
The US facility has one feedstock line set up for small 35 kg MIM batches, consisting of a Turbula mixer to thoroughly blend the constituents, followed by a high shear Ross
planetary mixer. Additionally, there are two lines for 200 kg batches, each comprising a V blender with an intensifier bar and a Winkworth sigma blade mixer. In each case, the second step is conducted at a sufficiently high temperature to melt the wax and polymer constituents, which, combined with the high shear, produces an optimal feedstock.
In either case, rework material (sprues, runners, and scrap mouldings of the same grade) is blended with virgin material during these process steps at an approximate 60/40 virgin/rework ratio. The output of either process is then cut by hand tooling into ‘chunks’ that are fed into granulators, which produce pellets that flow well when feeding the injection moulding machines. Equipment is cleaned between batches, but, where practicable, is also dedicated by alloy grade family.
The ERP system contains unique information for each batch and specifies which injection moulding machine(s) the batch should run on,
“The plant has twenty-eight Battenfeld injection moulders (twenty-six 110 models and two larger 180 models); currently, twenty-one are operational, though the other seven are fully equipped and qualified.”
along with the specific part order(s) it is assigned to. Prior to releasing any given powder batch for moulding parts, an X-ray fluorescence (XRF) chemical analysis test is conducted.
At full capacity, the San Antonio plant could currently produce approximately 150 million MIM parts per year. The plant has twenty-eight Battenfeld injection moulders (twenty-six 110 models and two
larger 180 models); currently, twenty-one are operational, though the other seven are fully equipped and qualified. Mantrodi informed the author of the company’s practice of not operating at more than approximately 75% capacity as part of its policies to ensure short lead times, given a variable and somewhat unpredictable product mix, and the need to be ready for business growth.
Each machine is equipped with two robots. The first robot picks the moulded parts from the tool when
opened, and places them on a holding table (or, if the parts come from a ‘shot’ where one or more designated parameters are outside the acceptable range, drops them into a labelled rework container). Then, a second robot picks the mouldings off the holding table and places them on ceramic setters, which are themselves on stainless steel transport trays.
Sprues and runners are automatically ejected when the mould opens and fall into a second rework container, which is also labelled with key information from the ERP system. The automation enables the machines to operate with an average of six machines per operator.
This method avoids potential damage from handling and provides accurate part placement on setters. Granulated feedstock is supplied to the feed screw hopper from covered, wheeled containers located alongside each moulder, with feedstock depth sensors in the hopper controlling when granulate is pneumatically transferred to the hopper or, if overfilled, returned pneumatically to the container. Stainless steel trays holding ceramic setters with moulded parts are stacked in steel frames, ready for the solvent debinding step.
Tool changes are carried out swiftly – in fifteen to twenty minutes – with the aid of standardised, wheeled carts equipped with rollers to move tools on and off machines and around the manufacturing areas. If a new powder grade is necessary for the subsequent order, a further ten minutes is required to empty the hopper and purge the material already in the injector screw. However, most of the moulding machines are dedicated to a particular material type. Moulds differ in terms of interior shape, size, and the number of cavities. In the San Antonio plant, the highest number of cavities in a mould run to date is sixteen, whereas thirty-two cavity moulds are used in Bangalore.
As with the feedstock preparation areas, the moulding area has large screens with detailed information on work orders and other informa -
tion. The machine controllers are configured to reject any parts for which primary or derivative operating parameters fall outside ranges established by Statistical Process Control (SPC). Parameter adjustments can only be made by personnel with the appropriate access permissions. At the time of the tour, a dedicated ‘white room’ was being set up for medical parts production, with four of the currently unused Battenfeld 110 moulding machines in place.
INDO -MIM uses a two-component organic binder for MIM. The first component is a wax that, after moulding, is removed from the ‘green’ parts by solvent debinding. This process opens up a connected porosity network in the ‘brown’ parts, thus facilitating the removal of the second polymeric component during the early debinding stage of the sintering cycle.
The San Antonio plant has two large tandem debinding units in which racks of green parts are placed before the chambers are filled with a circulating, heated organic solvent, which dissolves most of the wax component of the binder. Another portion of the system evaporates the solvent to leave behind the dissolved wax; the condensed solvent is then reused. Test pieces are weighed before and after the process to ensure that at least 95% of the wax is removed from the green parts.
On their respective setters, the brown parts are then slid off the stainless steel carrier trays onto sintering trays. These are mostly graphite, although some alloys, such as those based on nickel and titanium, use molybdenum trays. The loaded graphite trays are placed into slotted graphite frames, which are then inserted into one of five large sintering furnaces, each equipped with seven graphite heating zones and featuring a hot zone length of 2.2 m. The molybdenum tray
“The machine controllers are configured to reject any parts for which primary or derivative operating parameters fall outside ranges established by Statistical Process Control (SPC).”
“...the use of such large graphite hot zone furnaces is unusual in the industry, but when correctly applied, they work well for the sintering of ferrous materials and provide a cost advantage.”
assemblies are sintered in a smaller molybdenum element furnace.
As in previous areas, prompted interactive operating instructions were evident. During the early stages of the sintering cycle, an inert gas flow evaporates the remaining binder, which is then collected downstream in cold traps. Once all binder has been removed, the temperature is ramped up to facilitate sintering to full density.
Jag Holla stated that the use of such large graphite hot zone furnaces is unusual in the industry, but when correctly applied, they work well for the sintering of ferrous materials and provide a cost advantage in capital and replacement parts, which in turn translates to lower sintering costs per part.
While the Bangalore operation also uses some continuous sintering furnaces – the norm in conventional ‘press and sinter’ Powder Metallurgy operations – Sreenu Suri stated that there were no plans for such capacity in San Antonio, as continuous furnaces are best suited to very high volume components (commonly automotive and consumer electronics) that do not require frequent changes to sintering conditions.
Sreenu Suri and Jag Holla stressed the critical importance of ceramic setter expertise and capability, something that is perhaps underestimated by some in the MIM and AM fields, to maximise the dimensional accuracy of MIM and sinter-based AM parts, thereby reducing the need for finishing operations. Usefully, the same ceramic setters can be used for a given part, whether it is produced by MIM or AM.
The San Antonio facility receives all its setters from one of the Bangalore facilities, which has a separate area and staffing dedicated to optimising setter geometries for each part and then producing setters for production orders. Slip casting, uniaxial die pressing, and Ceramic Injection Moulding are all employed for setter prototyping and/or production, and rapid optimisation of setter geometry – greatly aided by the experience of the staff – is a critical aspect of overall short lead times.
Sreenu Suri stated, “When the San Antonio plant receives a new part mould from Bangalore, the initial production requirement of setters accompanies the mould.”
The Bangalore team has developed in-house sintering simulation software to aid ceramic setter design, reducing the number of iterations needed to optimise their geometry.
According to Jag Holla, the San Antonio facility and its subsidiary in Mexico can handle 90% of postsintering operations in-house. These include a wide variety of machining processes such as turning, milling, boring, reaming, and tapping, as well as coining, a diverse range of heat treatments, carburising, induction hardening, bead blasting, magnetic deburring, vibro finishing, passivation, grinding, polishing, plastic
“According to Jag Holla, the San Antonio facility and its subsidiary in Mexico can handle 90% of postsintering operations in-house.”
overcoating, and laser serialisation markings – the latter being widely used for firearm components.
Some specialised processes, including black oxide and nitride coatings, electroless nickel coating, Hot Isostatic Pressing (HIP), centreless grinding, and double disc grinding, are outsourced. During the plant tour, Mantrodi pointed out many of the internal post-sinter processes to the author. The most impressive of these was a large multi-chamber ECM vacuum heat
treatment furnace with internal handling mechanisms to transfer the load from one chamber to another for different treatments.
“99% of our products are heattreated,” Mantrodi explained.
The San Antonio plant is ISO 9001-2015 and ISO 13485 (medical devices) certified and compliant with ITAR (International Traffic in Arms Regulations). Materials science QA tests include carbon levels, XRF elemental analysis, hardness testing, microstructural
Characteristic
Table 2 Comparison of AM vs MIM, adapted from Jag Holla’s 2022 article [3] and 2025 interview. Specific numbers are highly case-dependent, but comparisons are qualitatively valid
analysis, microhardness testing, rheology testing, mechanical strength, and density measurements using the tap, pycnometer, and Archimedes methods. Dimensional measurements, conducted either on the machine or in the metrology lab, include hard gauging, Coordinate Measuring Machine (CMM), and Video Measurement System (VMS), with most orders receiving 100% inspection on at least one dimension. All data are linked to the ERP system.
Since 2020, INDO -MIM has developed significant Additive Manufacturing capabilities at its Bangalore and San Antonio facilities. As with its MIM operations, the two sites coordinate and communicate closely. The primary technology in use is Binder Jetting, which readers of PIM International will recognise as sharing several technical and market synergies with Metal Injection Moulding. Both facilities also have Laser Beam Powder Bed Fusion (PBF-LB) capabilities, and the Bangalore site operates a metal Vat Photopolymerisation (VPP) process.
In San Antonio, a 1,500 m² room is dedicated to AM. A small portion of this space houses a Nikon SLM Solutions SLM 500 PBF-LB machine, used primarily for processing nickel-based alloys for both part development and series production, as well as for demonstrating capabilities to relevant powder customers.
A range of BJT machines are currently in operation and used for processing stainless steels, including 304, 316L, and 17-4PH. Desktop Metal P1 and Shop Pro machines are installed, along with two Desktop Metal debinding and sintering furnaces. However, the most recent additions are three HP S100 machines, and infrastructure is already in place to support up to ten additional machines.
Initial depowdering is currently a manual operation, but an HP auto -
mated depowdering machine has been installed; final ‘fine’ depowdering, however, is expected to remain a semi-manual process done by skilled operators. Removed powder is conditioned in drying ovens before being blended with virgin metal powder.
INDO -MIM designs its process to achieve similar linear shrinkages (17-20%) for a given alloy (the most common material, 17-4PH, is 18%) for both MIM and AM. While sintering shrinkage in MIM is isotropic, Additive Manufacturing components experience different shrinkage in the z, or vertical, axis compared to the lateral x and y axes. However, this shrinkage is predictable and does not pose any problems in practice.
While small compared to the company’s MIM operations, with current output around 1,000 parts per month, the company’s Additive Manufacturing activity is growing steadily. Applications include
“While small compared to the company’s MIM operations, with current output around 1,000 parts per month, the company’s AM activity is growing steadily.”
prototyping for MIM parts – beginning to replace the traditional ‘soft tool’ stage – as well as low-volume components for which the cost of MIM tooling could not be justified. AM is also used to produce large or thick-section parts, internally required jigs, fixtures, and mould components, and it supports a dedicated programme for marine spare parts.
In 2022, Jag Holla [3] gave a very good comparison of the pros and cons of AM versus MIM; Table 2 summarises the information in that article and adds information gained during the April 2025 communications with Jag Holla and Krishna Jr.
INDO -MIM’s entry into AM reflects both interest in the technology’s potential and a clear understanding of its current limitations. As Jag Holla explained, “The current issues with AM growth are high costs and low productivity compared to conventional MIM or PM, as well as limited materials options.” He also noted that tolerance control is a key challenge – “the tolerance capability of the AM process is much poorer compared to MIM” – which often leads to discussions with customers about possible tolerance relaxations.
In 2024, INDO -MIM revealed that it was using Binder Jetting to produce M2-grade tool inserts for its Metal Injection Moulding operations.
Tool inserts had been additively manufactured using laser-based Powder Bed Fusion (PBF-LB) for over a decade, stated Jag Holla at the time. However, he noted that the process was relatively slow and limited to the use of maraging steel for tool insert applications. “This material can, at best, reach 55 HRC after heat treatment,” explained Jag Holla, “making it unfavourable for many tooling applications.”
“Given our material development and sintering expertise, fine-tuned over twenty-five plus years, our
M2-grade material offers 50-80% increase in wear resistance, 40% better machinability compared to conventional wrought M2 material. These are accomplished through finer grain microstructure and 99% minimum density postsintering. Our M2 material can guarantee 63-66 HRC hardness consistently.”
INDO -MIM can use BJT to build tool inserts weighing between 300 g and 8 kg, all to near-net shape and including complex conformal cooling channels. As well as producing these for in-house use, the company also offers the production of tool inserts as a service to customers.
a decade, though timelines remain uncertain.
Krishna Jr also highlighted the value of the company’s involvement with HP: “The engagement with HP has been pretty incredible – their Digital Manufacturing Network is bringing in customers who have applications already in mind.” He acknowledged that, while some parts made with Additive Manufacturing could also be produced using MIM, others simply cannot. This creates a valuable overlap. “People love printing samples with AM – it’s been very, very helpful to us.”
Beyond prototyping, AM has therefore had practical benefits for customer engagement. “It was certainly good to get systems like this and immediately have an economic use in terms of sales and marketing,” said Krishna Jr. “Customers are getting a Powder Metallurgy component with their geometry – they’re able to try it and test the functionality without investing in tooling.” This has helped convert interest into MIM programmes and build confidence in the technology. While some AM machine vendors are ‘still maturing’, Krishna Jr noted that customer demand has not been affected: “The customers do not care. [...] I think this is normal when an industry is growing like this.”
Krishna Jr went on to explain that AM “is a more expensive process, and customer expectations must be reasonable.” That said, AM offers advantages where design flexibility is critical. “Design changes by the customer are not limited because the AM process offers 360° design flexibility,” Jag Holla stated. INDO - MIM has focused its AM efforts on parts that are physically larger or have geometries that are difficult or impossible to produce through MIM. Looking ahead, Jag Holla believes sinter-based AM could start to overlap with traditional MIM applications as the technology matures. INDO -MIM made a deliberate decision
to enter early to build experience and capability: “We wanted to be an early adopter so that we could be the dominant player as the technology matures.” While other MIM firms are exploring the space, many face financial constraints. “Most of them are small and do not have enough CapEx capability, as the equipment is expensive,” Krishna Jr stated, suggesting that “equipment costs are far too high – $1.2 million for what is basically a three-axis machine with low productivity.” Despite the cost, real market potential is seen and it was suggested that AM volumes could reach parity with MIM within
While acknowledging that AM is not the right fit for every part, there are applications where it clearly adds value, such as managing aftermarket parts catalogues and producing midsized components in the 5-7 kg range. “There’s a niche for it, and I think that niche is going to grow.”
MIM accounts for 98% of production in San Antonio, with the balance being AM production. Jag Holla stated that, while MIM growth in North America has slowed, it still stands at approximately 7% per annum. AM is growing at around 50%
per annum, albeit from a low base. In terms of geographic distribution, 98% of San Antonio’s business is in the Americas.
Approximately 75% of output serves the defence sector and 25%, the medical sector. The Bangalore operation has a more diverse mix, including automotive. Looking ahead, the San Antonio plant anticipates growth in aerospace.
Business is evenly split between repeat and new orders, with repeat demand typically occurring on a quarterly or annual cycle. Annual demand per MIM component ranges from 2,000 to 5 million parts, with batch sizes typically between 500-50,000 parts.
INDO-MIM primarily uses stainless steels (17-4 PH, 316), S7-grade tool steels, and some low-carbon steels. Titanium is expected to be introduced to the plant in 2025. MIM parts range in weight from 0.2 to 250 g, and in size from a US cent coin to approximately 25 × 15 cm.
While the growth of Metal Injection Moulding in the North American market has slowed in recent years, INDO -MIM continues to see strong potential. Whilst Jag Holla estimated annual growth to be around 7%, he stated that reshoring trends in the US could help double output at the company’s San Antonio plant within the next two years, building on strong momentum since its launch in 2017.
The establishment of the San Antonio plant marked a pivotal shift for INDO -MIM. Krishna Jr described the move as a strategic leap designed to bring the company closer to its key markets. “We believed there was an aspect of the US market we would be better able to access if we were on site,” he stated. Six to seven years on, he said this belief has been validated, with the facility even demonstrating operational resilience during the challenges of the COVID-19 pandemic.
Krishna Jr also emphasised that INDO -MIM’s growth strategy has not relied on taking market share from competitors. Instead, it has focused on expanding the overall adoption of MIM. “We were growing the market rather than taking from it,” he explained, highlighting the company’s success in converting components traditionally produced by casting or forging, plus machining to MIM. These conversion opportunities, he noted, are particularly evident in San Antonio, where the company has experienced strong customer interest.
Regardless of expansion opportunities, market penetration challenges remain. Many mid-sized firearms manufacturers in North America are still failing to leverage the commercial benefits that MIM offers. Some
“While resistance to MIM has been a barrier in the firearms industry, Krishna Jr sees this changing: ‘I would say that it’s still there, but it’s much rarer. Especially when you’re at scale in the firearms industry, adopting MIM can produce very, very significant cost savings...’”
maintain a sceptical view of the technology, while others have been hesitant to source parts from overseas. “ITAR is part of it,” Krishna Jr explained, “but even just managing payments to a foreign supplier, and things like that, can be a challenge to small companies.”
One area that has helped INDO - MIM bridge this gap is its use of Binder Jetting technology to support MIM firearms sales. “When we were in San Antonio, we definitely found a lot of firearm customers who wanted to try MIM but hadn’t been doing it
before,” Krishna Jr stated. “From an early stage of the operation, we had Binder Jet there. Within a short period of time, we were able to print samples for our customers in San Antonio, and honestly, for the smaller firearm companies we were trying to do business with, it was amazing.”
“We would print a sample; they would get it, do whatever little machining they had to do on it, and then they would figure out if they really wanted a MIM part. We had a huge number of programmes
converted via that mechanism. And I’m not talking five or six; I’m talking twenty, thirty, and forty – very significant programmes, some still developing.”
While resistance to MIM has been a barrier in the firearms industry, Krishna Jr sees this changing: “I would say that it’s still there, but it’s much rarer. Especially when you’re at scale in the firearms industry, adopting MIM can produce very, very significant cost savings,” he stated. “The awareness of us in the US market is much different than it was fifteen years ago. And now we’re onshore, and that also changed a lot of perceptions.”
The technical advantages of MIM also help drive adoption. With near-net shape capabilities, the process allows for a high degree of material flexibility. “Because of the ability to get near-net shape, you have a level of material flexibility, which can be advantageous,” Krishna Jr noted. “The classic example is firing hammers in S7. After 20,000
rounds, you look at it, and you can’t even see a dimple on the firing pin on the MIM S7 compared to a hammer that’s been forged or cast and then machined.”
INDO -MIM is also pushing the boundaries of MIM component size. “We’re producing larger parts in the 80, 100, 150, and 250 gram range,” he confirmed. “We are accomplishing this in San Antonio.”
There is no single factor behind INDO -MIM’s success in North America or globally. Instead, what emerged during conversations with senior staff and the detailed tour of the company’s San Antonio plant was a web of interlocking strengths: technical capabilities, operational discipline, and strategic vision. These advantages are not isolated but function as a system – one that consistently delivers value to customers, employees, and stakeholders across continents.
Integrated supply chain and scale
INDO -MIM maintains a diversified network of powder suppliers –including in-house atomising capabilities – and ensures resilience through a minimum of three months’ safety stock of powders and other raw materials. Its global footprint includes multiple manufacturing sites in India, the US, and the UK. For North American customers, the presence of a US-based facility – and, crucially for firearms components, one that is ITAR-certified – is not only highly desirable but, in some cases, essential. As Jag Holla remarked, “I can readily think of at least twelve customers we only have because of the San Antonio facility. It will be very helpful for growing the aerospace business.”
INDO -MIM also employs dual sourcing for certain high-volume components, using duplicate tools in Bangalore and San Antonio to ensure continuity and flexibility. Several weeks’ safety stock is
Fig. 17 A stainless steel curved jaw, part of an advanced bipolar device designed for use in open or laparoscopic tissue sealing surgical procedures. The part won an MPIF Grand Prize (Courtesy MPIF)
typically held on-site, further enhancing responsiveness. This supply chain integration, combined with vertical integration that reduces transportation times and dependence on third parties, supports both reliability and agility in global operations.
INDO -MIM’s tool design and production capacity in India – now increasingly mirrored at its San Antonio facility – directly addresses
the persistent shortage of mould design and manufacturing expertise in North America and Europe. This capability enables the company to handle complex, large-scale projects at speed. Jag Holla cited a notable example involving a major firearms manufacturer that required twenty-seven new components within the same timeframe – a programme INDO -MIM completed from initial enquiry to shipment of finished parts in under four months. “No other MIM company could have done that,” he stated.
“As Jag Holla highlighted, customer contracts are structured with complete transparency and carry ‘no hidden charges,’ supporting INDO-MIM’s commitment to offering ‘Lowest Total Cost.’”
The company’s production capacity also features a large number of injection moulding machines and a very large sintering capacity, comprised mainly of large graphite hot zone furnaces. A very high volume of products shares capital, labour, consumables, maintenance, and overhead costs.
A combination of geographic advantage, process control, and strategic integration drives INDO - MIM’s emphasis on cost reduction. Operations in India benefit from comparatively low labour costs – a factor that continues to underpin competitive pricing even for customers based in the US. Notably, the cost of MIM tool design and manufacture remains low, regardless of the customer’s location. Growing automation – most visibly in injection moulding but increasingly across other production areas – not only reduces labour costs but also enhances quality and consistency. As Jag Holla highlighted, customer contracts are structured with complete transparency and carry “no hidden charges,” supporting INDO - MIM’s commitment to offering ‘Lowest Total Cost.’
The company’s expertise, coupled with tightly standardised processes, enables excellent dimensional and surface finish control, significantly reducing the need for secondary post-sintering operations. Vertical integration, with the majority of manufacturing steps kept in-house, further supports this, reinforcing cost control while maintaining quality and delivery performance.
INDO -MIM achieves industry-leading short lead times by maintaining capacity utilisation below 75%, allowing flexibility to manage variable volumes and shifting product mixes. The company holds safety stock of finished and semi-finished parts to meet urgent demands swiftly. A highly skilled team, supported by proprietary expert
systems, enables rapid optimisation of mould geometry and ceramic setter design. Their in-house ceramic setter manufacturing runs parallel to tool production, speeding up the process further.
Vertical integration is extensive – around 90% of post-sintering processes are handled internally – minimising transport delays and reliance on third parties with potential lead time issues. This operational approach delivers a 97% on-time delivery rate, with most delays attributable to the company’s willingness to say ‘yes’ to challenging requests.
discipline, quality control and ERP integration
INDO -MIM’s integrated ERP system plays a key role in minimising process errors through the use of highly visible, interactive operating instructions. Labelling and barcodes are fully incorporated into the system to ensure accuracy and traceability. Each work area at the San Antonio facility is overseen
“INDO-MIM achieves industry-leading short lead times by maintaining capacity utilisation below 75%, allowing flexibility to manage variable volumes and shifting product mixes. The company holds safety stock of finished and semi-finished parts to meet urgent demands swiftly.”
by experienced staff seconded from the home operations in Bangalore, working alongside locally hired colleagues. Automated materials handling, calibrated to statistically derived injection moulding parameters, reduces handling damage, improves part placement consistency, and automatically rejects parts that fall outside predetermined ranges.
Staff expertise and collaborative management
Williams [1] and Schlieper [2] noted the strong work ethic, enthusiasm, and experience of the teams in both the Bangalore facilities, and these qualities were clearly evident at the San Antonio facility. Each functional area at the San Antonio facility is led by Bangalore-trained staff,
supported by a ‘shadow team’ in Bangalore that regularly collaborates with the US plant, including twice-yearly visits. Production staff handle customer interactions for replenishment orders, which brings the ‘Voice of the Customer’ into manufacturing. This also allows
sales teams to focus on new business development through trade shows, digital marketing, referrals, and cold calls. This structure helps maintain clear communication between manufacturing and customers while supporting business growth.
Investment casting is not, of course, a PM process, but it shares several similarities: it produces net or near-net shape metallic parts, often using the same alloys. The same finishing processes (machining, polishing, etc.) can be applied to investment casting, MIM, or AM components, and the customer bases may also overlap.
The PCC-AFT JV origins of INDO-MIM exemplified this synergy; notably, INDO -MIM’s 2008 Tirupathi
investment casting plant capability has, in a sense, been replicated by the company’s 2020 acquisition of Triax Industries. Currently, INDO -MIM’s facility in Mexico primarily focuses on finishing operations for Triax Industries’ products. PIM International readers may also be aware of another company that combines investment casting, MIM, and AM – namely Tritech Titanium Products [4].
INDO -MIM has recently introduced Additive Manufacturing to expand its product range to larger and/ or thicker-section components that are otherwise challenging or even impossible to produce. This capability also facilitates low-volume production runs that would not warrant the expense of traditional MIM tooling. Additive Manufacturing is being employed to replace ‘soft tooling’ in the customer acceptance process via rapid, tool-free prototyping and for internal applications such as jigs, fixtures, and tooling parts. The company’s robust vertical integration, including raw metal powders, ceramic setters, sintering furnaces, and finishing, effectively complements these new capabilities. Although not a specialist in MIM, the author has extensive experience in related manufacturing sectors and aims to provide an objective outsider’s perspective. While many MIM companies may share some of INDO-MIM’s qualities,
few possess such a broad combination of strengths. This unique mix is believed to be a major factor behind INDO - MIM’s success.
With ongoing investment in technology, a high degree of vertical integration, and a focus on local manufacturing in key markets, INDO - MIM is well-placed to lead the next phase of growth in precision manufacturing. As reshoring accelerates in North America and Additive Manufacturing continues to evolve, the company’s dual-track strategy – combining scale with agility – positions it as a strong model for global industrial competitiveness.
Reflecting on INDO -MIM’s journey, Krishna Jr noted, “So maybe some ideas have worked out a little better than even I thought over time. It’s
pretty amazing where we’ve gone in the past fifteen years, when you look back on it.”
Author
Bernard North North Technical Management, LLC Greater Pittsburgh area Pennsylvania, USA brnrdnorth@gmail.com
INDO-MIM infous@indo-mim.com www.indo -mim.com
[1] INDO -MIM: The world’s largest capacity MIM producer sees no limits to the industry’s expan -
sion. N Williams, Powder Injection Moulding International Vol. 5, No. 3 September 2011 pp 39-43
[2] INDO -MIM: A giant in Metal Injection Molding expands to build on strong international growth. G Schlieper, Powder Injection Moulding International Vol. 10, No. 1 March 2016 pp 47-55
[3] INDO -MIM: Exploring the dividing line between Metal Injection Molding and Binder Jetting. J Holla, Powder Injection Moulding International , Vol. 16, No. 1 March 2022 pp 61-68
[4] The future is titanium: TriTech Titanium Parts targets the opportunities for MIM, Binder Jetting and Investment Casting. B North, Powder Injection Moulding International , Vol. 17, No.3 Autumn 2023 pp 81-89
The PIM International newsletter is sent to several thousand industry professionals worldwide. Register today to ensure you benefit from reading the latest industry news and advances in Metal Injection Moulding, Ceramic Injection Moulding and sinter-based AM technologies.
The capabilities of Metal Injection Moulding have transformed the design of hinges, unlocking new possibilities in consumer electronics and beyond. By enabling the production of compact, durable, and highly complex components, the technology has allowed engineers to rethink functionality and aesthetics, especially in devices such as foldable smartphones, laptops, and wearables. In this comprehensive review, Dr Chiou Yau Hung (Dr Q) explores how MIM’s unique advantages have influenced hinge innovation, reshaped product design, and opened new frontiers for mechanical systems.
The growth of the Metal Injection Moulding industry in the Greater China region owes much to the production of hinge components and assemblies. As demand for compact, high-performance electronics grows, hinges offer a compelling case study of how MIM continues to meet the evolving needs of modern manufacturing. These mechanisms have significantly expanded MIM’s presence across the 3C (computer, communication, and consumer electronics) sector and beyond, demonstrating the technology’s ability to deliver miniature, high-strength components in high volumes.
Hinges remain a key driver of demand for MIM technology, particularly in the 3C sector. Their use is being fuelled by growing demand for compact, durable mechanisms in foldable smartphones, tablets, wireless earbuds, and wearable devices – applications where conventional machining or casting often fall short in terms of design flexibility and cost-efficiency.
Though MIM is a decades-old process, it continues to be associ -
ated with innovation. Consumer electronics OEMs frequently highlight their use of MIM in marketing campaigns; Sony’s latest noisecancelling headphones, shown in Fig. 1, are just one recent example.
Examples such as these illustrate not just the innovation enabled by MIM, but also its commercial importance. This is reflected in the growth trends seen across the global MIM market.
Fig. 2 An estimation of the evolution of global MIM part sales (Courtesy Dr Q)
According to global market data, the MIM industry was projected to reach a value of $2.65–3.05 billion by the end of 2024, with the Greater China region – consisting of mainland China, Hong Kong, Macau and Taiwan – accounting for approximately $1.83 billion, or 60–69% of the total.
Although many other data sources suggest a higher market value, I
believe that the trends shown in Fig. 2 are highly valuable as a reference. Despite the disruption caused by COVID-19, the MIM industry has shown notable resilience. As illustrated by the global market trends in Fig. 2, MIM’s development can be categorised into four distinct stages:
The first stage saw innovation and the promotion of MIM, however, it did
“...advancements and greater engagement from material and equipment suppliers helped sustain steady sales. As the industry matured, MIM began to challenge established manufacturing methods such as investment casting, die-casting, and machining.”
not achieve significant sales volume. At the time many engineers were still in the early stages of adopting the technology. Additionally, materials and equipment were unstable, resulting in MIM having a relatively low status among metal processing technologies.
This period saw explosive growth driven by the widespread adoption of MIM in 3C products such as laptops, mobile phones, and tablets. Engineers in the 3C sector began to recognise the unique advantages of MIM and incorporated large volumes of MIM parts into their designs. This led to a significant increase in sales.
Growth continued, though at a slower pace. Profits from the previous stage attracted more manufacturing companies to enter the MIM market, intensifying price competition and pushing costs down. Meanwhile, advancements and greater engage
ment from material and equipment suppliers helped sustain steady sales. As the industry matured, MIM began to challenge established manufacturing processes such as investment casting, die-casting, and machining.
Following the intensified price competition of the previous stage, the MIM industry from 2020 to 2024 entered a plateau. This period is characterised by ongoing price bargaining between product manufacturers and MIM suppliers, leading to a more mature and polarised market.
Engineers designing 3C products became adept at using smaller, more precise MIM parts. Facing mounting pressure to deliver results, some MIM manufacturers integrated conventional metalworking methods to broaden their capabilities and meet diverse customer demands, further contributing to market polarisation. For example, precision folding-screen mobile phone hinges can incorporate between thirty and fifty MIM parts weighing less than 1 g each, while traditional hardware fixtures may rely on single MIM parts weighing over 300 g – sometimes up to 1,000 g. After decades of development, MIM has become indispensable for producing small metal parts.
Notably, 2024 saw a marked increase in MIM equipment sales in China; feedstock production systems, injection moulding machines, and debinding and sintering furnaces manufacturers reported figures nearly double those of 2023. However, signs of the market plateauing remain. Against this backdrop, it is timely to review the current landscape and key trends shaping the industry.
Visits to leading MIM suppliers and manufacturers in 2025 revealed several insights. Firstly, powder prices have reached a low point,
“Notably, 2024 saw a marked increase in MIM equipment sales in China; feedstock production systems, injection moulding machines, and debinding and sintering furnaces manufacturers reported figures nearly double those of 2023.”
thanks to ongoing investments in Additive Manufacturing powder production, resulting in more MIM-grade powder availability. Production sites reported that the strong demand from 2024 has continued unabated.
While larger MIM parts still support traditional hardware applications, it is the 3C sector that drives the most significant growth. Once again, hinge components stand out as a key factor in the ongoing expansion of the MIM industry.
The impact of hinges on the MIM industry
Over the past decade, I have provided guidance to more than 100 MIM-related enterprises, including those involved in metal powder and raw materials, feedstock, equipment manufacturing, and MIM parts processing factories. In my experience, a significant portion of MIM products are being designed for use as hinges, with over 50% of parts featuring holes to accommodate shaft components.
Support Supports other components of the mechanism, such as the display screen or the working pallet
Adjustment Controls the movement of the mechanism necessary to its function, such as in projection or lighting lamps and industrial fans. The range of movement and rotation angle depend on the mechanism’s design
Loading bearing In addition to vertical tension and compression stresses, this module must also withstand operational bending and torque
Transmission Transmits torsional power and must endure a certain frequency of repetitive or random rotational friction
Damping Provides damping to ensure the safety of users, particularly in heavy systems
Weight Must meet the weight limitations of the overall assembly, balancing the need for high mechanical performance with minimal weight
One of the earliest MIM applications is the metal watchband (Fig. 3), which features a shaft passing through two MIM components with matching holes. This allows the two parts to rotate freely and thus demonstrate an early hinge module process.
Today, the use of hinge modules has expanded across major consumer product categories, and MIM has become one of the key manufacturing processes for the structural components used. Core functions are outlined in Table 1. A look at the early implementation of MIM in hinge modules reveals how the technology first gained traction in high-performance applications.
During 2004-2005, Sony became the first company to utilise Metal Injection Moulding to produce the hinge module for the X505 model in its VAIO laptop series (Fig. 4). The launch of X505 marked the first time an innovative manufacturing process such as MIM was applied to hinge modules. Through its lightweight and durable design, users were able to experience first-hand the benefits of MIM technology. It should be noted that while a Taiwanese individual filed the first patent for an MIM laptop hinge in the United States during that time, it was not produced. Early foldable smartphones such as the Motorola V688 and Razr V3 series (Fig. 5) also featured fully functional MIM hinges, marking a significant milestone in the use of the technology in consumer electronics. These multi-joint hinge assemblies require precise MIM components, highlighting the technology’s vital role in enabling more complex and durable device designs.
Hinge modules are formed by assembling MIM hinge parts with traditionally processed components, including sheet metal stamping, turning, milling composites, diecast, and liquid metal (LQMT) formed parts. This combination has driven a renewed surge in order volume for MIM manufacturing plants. Over fifty
MIM manufacturers now produce complete hinge modules, while more than 100 specialise in individual parts.
The modern evolution of hinge components therefore began with the introduction of MIM. Fig. 7 shows key hinge products from 2002–2012. Initially, MIM manufacturing producers only supplied individual components such as cams, hinge plates, and fastening pieces to higher-level factories, which assembled these parts into complete hinge modules for use in various 3C products.
Since 2012, with the rise of tablet computers and wearable devices such as earphones, hinges have become a more prominent feature in product design. They are no longer just functional components but are now considered part of the products’ overall aesthetics. This shift has led to the use of more complex, multi-piece hinge designs. As demand for advanced hinge modules has grown, MIM manufacturers have expanded and improved their assembly capabilities to keep pace. This shift has created new business opportunities (Fig. 8) and enabled the development of a new generation of hinge designs that require greater mechanical complexity.
Since around 2018, influenced notably by companies such as Apple, many electronic product brands with skilled industrial designers have introduced increasingly complex and sophisticated hinge mechanisms. These hinge modules incorporate a large number of gears to enable the smooth rotation of the hinge, as well as more mechanisms resembling crab structures. Due to factors such as an excessive number of mechanical parts, inability to polish certain materials, and user safety issues, these hinge modules must be hidden and are unsuitable for exposure. During this
Fig. 7 (A) and (B) show the earliest designs of the hinge. The cam lobes, shaft components, and fastening pieces produced with MIM were sent to the upperlevel assembly factory for assembly. In (C), the fastening pieces with complex geometric shapes were made using MIM, and an appearance requirement was imposed. In (D), the fastening pieces were even integrally formed with the shaft components (Courtesy Dr Q)
Fig. 8 (A) the hinge of the support backplate on the first-generation Microsoft Surface tablet; (B) the hinge of the support backplate on the updated Microsoft Surface tablet; (C) a delicate MIM hinge on the storage case of wireless Bluetooth earphones (Courtesy Dr Q)
Fig. 9 (A) and (B) show hinge modules that incorporate bevel gears and spur gears to enhance the smoothness of rotation. (C) is a multi-joint hinge with an appearance similar to a watch band. A cover plate conceals the complex mechanism and prevents the leakage of hinge lubricating oil. (D) shows an exposed multi-section hinge that is prone to dust accumulation and may also scratch the user. Both (E) and (F) are designs of hinge decorative covers used on 3C products such as laptops and mobile phones (Courtesy Dr Q)
“In the case of a three-screen phone, the use of two hinge modules can involve upwards of sixty MIM parts. Such demand has greatly increased the requirements for MIM production capacity and manufacturing process capabilities.”
period, decorative panels to manage the appearance of hinges began to be introduced. In other words, this added one more design requirement to the hinges (Fig. 9).
Finally, following the increasing adoption of foldable smartphones after 2020, a two-screen foldable smartphone now typically requires more than 100 parts, with over thirty of these being MIM components. In the case of a three-screen phone, the use of two hinge modules can involve upwards of sixty MIM parts. Such demand has greatly increased the requirements for MIM production capacity and manufacturing process capabilities. Furthermore, MIM parts have begun to be embedded into assemblies formed using other metal forming processes such as die-casting techniques, sheet metal processing and, more recently, liquid metal and bulk metal glass (BMG) technologies.
This surge in demand has created a new wave of business for MIM producers, significantly increasing the need for MIM production capacity and process capabilities. This uptick has gone a long way to compensate for the decline in Apple’s demand for
Fig. 11 In addition to the progress made by BASF SE in MIM hinge materials, engineers have gradually figured out the properties of MIM materials suitable for use in hinges (This diagram is based on the BASF website and modified by the author)
MIM parts. As shown in Fig. 10, the evolution of foldable screen hinges reflects a growing use of MIM parts.
Although MIM has been in development for over fifty years, new materials continue to emerge to meet the evolving needs of products. This is one of the most fascinating aspects of MIM: the ability to design material formulations that allow for the production of hinge components from various materials using the same set of moulds. Additionally, the size of the hinge products can be adjusted by altering the powder loading. Once a verification process is completed, mass production can begin swiftly.
Here, I would like to acknowledge the significant contributions of BASF SE, a German company, in advancing MIM feedstock development. The company’s dedication to promoting the progress of the entire MIM industry and its willingness to share technical resources with numerous MIM professionals is greatly appreciated.
“This is one of the most fascinating aspects of MIM: the ability to design material formulations that allow for the production of hinge components from various materials using the same set of moulds. Additionally, the size of the hinge products can be adjusted by altering the powder loading.”
The materials within the green dotted line in Fig. 11 are all suitable for manufacturing MIM hinge parts, particularly low-alloy steels and hardenable stainless steels. With the exception of non-ferrous alloys, tungsten alloys, and some ASP series tool steels, materials that are too hard cannot withstand drop tests. This emphasises that the most suitable material is the best choice; it’s important not to focus solely on achieving high yield strength. Generally, a yield strength of less than 2,000 MPa is considered excellent. The Advanced High Strength Steel
(AHSS) developed by Chinese powder manufacturers is also included. The current phase of material evolution still centres on iron-based alloys, with cost being the primary factor, followed by familiarity with these materials.
While material innovations continue to expand design flexibility, many in the industry are now looking ahead to future applications – especially
“...hinge modules featuring MIM parts will play a crucial role in human-like robot development, and the demand for these components could soon surpass that of foldable smartphones.”
as emerging technologies demand ever more compact and precise mechanisms.
You may be curious about how close we are to achieving robots with human-like limb movements becoming part of everyday life. The film Bicentennial Man, directed by Chris Columbus and starring Robin Williams, remains a notable depiction of realistic robot–human interaction.
While we may not yet be on the verge of AI robots serving humanity as portrayed in the film, robots with embodied intelligence are already becoming a reality. Although they do not yet possess the full flexibility seen on screen,
hinge modules featuring MIM parts will play a crucial role in humanlike robot development, and the demand for these components could soon surpass that of foldable smartphones. With MIM at the heart of so many precision assemblies, the future of robotics – and countless other applications – will depend on the continued refinement of this versatile manufacturing technology.
Achieving a standardised component that can be produced reliably and consistently over a long time is a key
aspiration for every expert in metal product technologies. For instance, stamping processes are commonly used for gaskets and metal brackets, while powder pressing is employed to produce precision gears. Additionally, specialised production methods are used for various screws and nuts.
Following over twenty years of development, the hinge module industry has begun to show significant promise. The unique characteristics of MIM enable hinge design engineers to create optimised, compact, and durable components. Beyond the aforementioned benefits, the use of increasingly precise hinge modules is also improving the accuracy of mechanical watches –devices that continue to serve daily functionality.
Prof Randall M German, a veteran in the MIM field, told us, “MIM manufacturing companies need both long-term orders and fashion orders.” Long-term orders may consist of small-volume batches, but they enable planned mass production. Trend orders, on the other hand, bring the thrill of rapid growth and greatly enhance MIM’s market visibility. The more people understand MIM technology, the deeper it can integrate into society and serve its people.
In the process of exploring the cutting-edge field of powder moulding technology, I have received a great deal of help and support from many people. Here, I would like to express my most sincere gratitude to them. Of course, I also want to thank readers around the world who support the MIM industry. Whether you are in Europe, Asia, Oceania, the Americas, or Africa, thank you all for your continuous attention to the MIM industry.
Author
Dr Chiou Yau Hung (Dr Q) You neeD Technical Office chiou_yh@yahoo.com.tw chiou55631966@163.com
find
In this wide-ranging interview, Nick Williams speaks with Dan Brunermer, founder of B-jetting LLC and veteran of the metal Binder Jetting (BJT) industry. Drawing on decades of experience, Brunermer reflects on what past successes reveal about the future of Additive Manufacturing – from the growing demand for custom machines and integrated automation to the economic realities shaping adoption. This is a candid and insightful exploration of where Binder Jetting stands today – and the challenges and opportunities that lie ahead.
Dan Brunermer lives and breathes Binder Jetting. Over a career that has included more than twenty years at ExOne, where he played a pivotal role in the development and commercialisation of the technology for sand, metal, and ceramic applications, he significantly influenced the evolution of Binder Jetting into a mainstream manufacturing process. In 2021, Dan left his role as Technical Fellow at ExOne to co-found B-jetting LLC, based in Vandergrift, Pennsylvania. The company’s mission is to support those seeking success in Binder Jetting – whether they are machine builders, materials developers, or application engineers. In addition to offering consultancy services and supporting the maintenance, repair, and optimisation of machines in the field, the company has developed two R&D-focused BJT machines of its own: the Educator and the Researcher.
For several years, Dan and I have found ourselves in deep conversation on the sidelines of the AMUG conference, discussing
the latest industry developments and, as the saying goes, putting the world to rights. This interview was inspired by those exchanges, offering insights into the state of Binder Jetting from someone with an unusually clear view of the landscape.
The current state of Binder Jetting, bruised by financial turmoil and past overpromises, is probably different to what many of us imagined ten years ago. I asked Brunermer about
Fig. 2 Binder Jetting successes are rarely shared, so the work of contract manufacturers, when it can be publicised, provides rare insight. This 316L fluid matter exchanger won a Grand Prize for Azoth in the MPIF’s 2023 Design Excellence awards (Courtesy MPIF/Azoth)
this and whether there’s more to the industry than meets the eye. He explained, “I think, Nick, one of the things we learned – though it was a bit painful at the time – is that some of the most successful Binder Jetting applications are ones you’ve never heard of. People often get into Binder Jetting for highly strategic reasons.
“Some of the best use cases are within vertically integrated companies, and they don’t talk about it. They don’t want their competitors to know they’ve made the leap. But I know that they are doing it, and
continue to do it, because in many cases, I rebuild their printheads. They have cracked the materials and cracked the automated depowdering. Everything about it is tailored. The reality is that there aren’t many doing Binder Jetting publicly –FreeFORM Technologies, Azoth, maybe one or two others doing contract work – but otherwise, it’s mostly silent.”
Brunermer explained that this secrecy has held back the adoption of the technology. “I think that’s hurt the industry a little. There are
some really great applications out there that are simply unknown. Because of NDAs, IP concerns, and all that, people just don’t talk about them. It’s funny – you read all these case studies on machine vendor websites, but the question is often ‘are any of these actually in production?’ The chances are, if it’s in a public case study, it’s probably not in production.”
So in answer to our questions – ‘Is this industry actually going anywhere? Can it do anything? Are we being sold a myth?’ – Brunermer stated, “That’s a fair question: have we been sold a bad bag of goods? I’d say no. I’ve seen enough real success to know that Binder Jetting is viable. But it often gets paired with the wrong applications – or, maybe more accurately, the wrong customers. There’s not always a good enough match between the technology and the part.
“And there’s a fundamental reality: it’s still a near-net process. You see all these flashy images, like watch cases rolling off the line. There was a time when everyone was pushing that message, especially from some of the Chinese companies. I worked on a watch case project back in 2019, and honestly, at that time, it was a terrible application for Binder Jetting. That’s not to say that it can’t work now, but mounting a precision piece of glass, housing miniature electronics, and ensuring a reliable bond to the metal requires a level of accuracy that Binder Jetting just didn’t offer at the time.
“I feel like the best applications are actually going to be even smaller parts. I mean, maybe the size of a five-cent coin or so. It is often the case that the smaller the part, the higher the chance of success.”
This naturally brings us to the MIM industry, where parts of this size have proved to be the sweet spot, decade after decade. The MIM industry, of course, has
paved the way for the adoption of Binder Jetting – think Indo-MIM, Parmatech, GKN Powder Metallurgy, to name just a few. “Right,” said Brunermer, “and every MIM guy who knows anything about Metal Injection Moulding and anything about Binder Jetting will tell you how similar they are.
“And so a lot of these companies use their Binder Jetting systems to support their MIM operations. You do all your prototyping on Binder Jetting because the parts behave very similarly in terms of density, geometry, and shape. The surface finish won’t be quite as smooth as a true MIM part, but you get all your material properties. So it’s a great bridge tool. Maybe while you’re waiting for tooling to be completed, or whatever it is, Binder Jetting fills that gap. And that’s the thing: the MIM industry is good for what, five, ten, fifteen million parts a year? That’s real scale.”
Brunermer stated, “Let’s start from what I think the future is: more bespoke machines. I think this is not only the future for high volume Binder Jetting, but I also believe it could be the broader future for high volume Additive Manufacturing. When you look at some of the more successful applications of Binder Jetting, or some of the big head -
lines over the past ten years, you might see some of the commercially available machines. However, if you look at some of the other headlines, like VoxelJet getting a multi-million dollar commission from GE Power in Germany to build that special, super-huge machine, there’s a trend. Even some of the things that ExOne turned into products, like the Exerial, were really speciality, purpose-built machines for BMW.”
“Let’s start from what I think the future is: more bespoke machines. I think this is not only the future for high volume Binder Jetting, but I also believe it could be the broader future for high volume Additive Manufacturing.”
The PIM International newsletter is sent to several thousand industry professionals worldwide. Register today to ensure you benefit from reading the latest industry news and advances in the MIM, CIM, and sinter-based Additive Manufacturing industries.
Newsletter subscribers also benefit from a free digital subscription to PIM International magazine. As soon as each new issue is available we’ll send you an email containing a direct link to our digital edition.
www.pim-international.com/e-newsletterand-free-digital-subscription/
Binder Jetting
The building step
Raster recoater (triple ACT)
Compactor
Powder
Energy
Cross-section images
Binder
Binder droplets
Powder layers
Inline recoater (SPJ)
Compactor
Powder
Energy
Desired object
Fig. 2 A step-by-step view of the building step during Binder Jetting
While the entire process of Binder Jetting for a fully dense metal part is much more complex than the picture shows, the actual building step is very straightforward:
1. Spread a layer of powder
2. Jet the object cross-section in binder
3. Add energy to partially dry the layer
4. Repeat
Fig. 4 Brunermer, a passionate educator and advocate for Binder Jetting, created this sketch of the process, published in the June 2022 issue of PIM International in the article ‘Saturation in metal Binder Jetting: Simple in principle, complicated in practice?’, Vol. 16 No. 2, June 2022, (Courtesy Dan Brunermer)
As illustrated in Fig. 2, three basic operations are repeated inside a typical Binder Jetting machine during manufacturing:
Whilst Binder Jetting is often used for low-volume or prototype production, particularly by the MIM community, there are clear ambitions for it to be used for high volume part production. As we explored this topic, Brunermer explained, “Whenever I think about productivity – let’s start from this point, Nick: there are roughly 31 million seconds in a year, so if you want to make three million parts a year, that means you’ve got to be making one part every ten seconds, every day, twenty-four hours a day. And I just don’t think you’re going to figure out that balance.
• Spread a uniform layer of powder
• Additively manufacture an image in binder that represents the cross-section of the part at that layer height
• Add some amount of energy, usually heat, to slightly dry the surface
Saturation defined
it’ll be productive enough. That’s one way to scale. Or, you could pick a machine size and say, ‘Okay, I’m going to get ten of these machines,’ because, combined, you’ll get the productivity you need. Those are really the only two approaches to scale at the moment.”
Let us get the easy part out of the way and start with the basic definition of saturation and its underlying assumptions. Of the latter, the most important is that the powder we are binding is made of whole granules and that these are insoluble in the binder being jetted as the glue. This is true for 99% of metal BJT, as the binder is not normally mixed into the powder, but it is not true for several other forms of BJT, nor when binding some agglomerates. This discussion will only lightly describe variablesized drops, as they are an emerging laydown strategy.
We can introduce the term 'Packing Rate', PR, to express the ratio of the measured powder density to the material's solid density, and rewrite.
We can introduce the term "Packing Rate", �� , to express the ratio of the measured powder density to the material's solid density, and rewrite.
mation experts to design something completely bespoke. It will have the exact productivity required for that exact task.
We can introduce the term "Packing Rate", �� , to express the ratio of the measured powder density to the material's solid density, and rewrite.
If we fill ���� with some volume of binder, ������� , we can define saturation,
“But another way to scale would be to have someone whose entire job is thinking about systems automation – thinking not just about your machine, but how the whole system integrates. Because maybe that’s the only way you are going to hit equivalency with other technologies.
If we fill ���� with some volume of binder,
These three activities happen repeatedly, from the bottom to the top. The engineering complexity of any Binder Jetting machine is much larger than what I have described, but this is the essence. The rest of this paper is meant to describe how the machine decides where to place the binder droplets and how much gets used in the build.
“Right now, in Additive Manufacturing, we have two ways to scale. In Binder Jetting, you’ve seen it for twenty years: just keep making the machine bigger. Someday
Given a contained volume of powder VC with dimensions X,Y,Z, we can say the container is filled with solid granules and air. That is,
“If someone wants to be equivalent to Ford or BMW, well, they build a special-purpose assembly line that makes exactly one thing. They bring in their most trusted teams of auto -
If we fill Vair with some volume of binder, Vbinder, we can define saturation, S
, we can define
This bulk property of saturation is true all the way down to the base unit level: the Voxel – I love this word, I have to say. It means Volumetric Picture Element. This is the most accurate and descriptive word that has been coined in a long
“So, for Binder Jetting very high volumes of a part, I just don’t think companies are going to go out and buy ten ExOne 25Pros at $2 million each. I mean, you can, but in my experience, this isn’t how these companies operate. Early in my career, I did some automation work in the automotive industry. We were making airbag inflators. We were building an assembly line in 1997 to make airbags for a model launching in 2000. We had to be producing one airbag inflator every four seconds by 1998 to fill the first order. That’s the kind of scale, size, and timeframe these companies work with. They’re huge.
We can introduce the term "Packing Rate", �� , to express the ratio of the measured powder density to the material's solid density, and rewrite.
“Ford doesn’t take lightly the decision to rehab an assembly plant and invest $4 billion to make the new Maverick and F-150 on the same line. Once they’ve made that decision, they spend that money incredibly strategically to get the exact productivity they need. I think that world – that super high-productivity world –revolves around bespoke equipment.”
During numerous conversations over the past few months regarding the barriers to the much wider industrial adoption of Additive Manufacturing, the issue of machine costs has come up. Brunermer explained, “Theoretically, they’re quite simple machines, yet compared to a CNC machine, they’re very, very expensive. And that plays into the wider discussion, because if you have a bespoke machine for the right application, then, theoretically, rather than needing twenty off-the-shelf machines, you’re doing something a little bit different.
“When companies go ahead with Binder Jetting at scale, it’s going to be a whole package. They’re going to select a powder supplier and get them into a long-term five- or sevenyear agreement where prices are capped. There’s probably going to be a special binder involved, and they’re going to aim for exact productivity. They’ll look at every step – printing, curing, depowdering, sintering – and say, ‘What’s on the market isn’t good enough. This has to be better.’ So there’s going to be a powder. There’s going to be a binder. There’s going to be a specific platform size and productivity target. You can’t make three million parts a year depowdering by hand. That all has to be automated.
“And that’s why I say they’re going to find one part, just one part, where if they could make five hundred thousand of them, not only would it be equivalent, it might actually be cheaper. Of course, we all know it’s never going to be the exact same
“I argue that equivalency alone is not going to be enough to displace the status quo. If you’re equivalent, then you’re just another option. Is that enough? I don’t think so. It has to be specialised. They’ll find that one part or small assembly where Binder Jetting isn’t just equivalent – it’s better and cheaper.”
part. It’ll need a bit of creativity and imagination. Some engineer deep inside Ford has to be looking at two or three parts that are welded together, or joined somehow and think, ‘You know what? Maybe those could be combined and turned into a Binder Jetting part.’
“And that’s the thing. I argue that equivalency alone is not going to be enough to displace the status quo. If you’re equivalent, then you’re just another option. Is that enough? I don’t think so. It has to be specialised. They’ll find that one part or small assembly where Binder Jetting isn’t just equivalent – it’s better and cheaper.
“And that’s one thing I swear people overlook: cost matters in this industry. It’s like they think just because it’s Additive Manufacturing, it’s going to be cool, and that ‘cool’ is worth something. I haven’t found ‘cool’ to be worth a penny. I’ve never met anyone who says, ‘I’m not buying that part if you made it with CNC.’ It’s a ridiculous mindset. I think it’s going to take that one application to break through. And I think it almost has to go that way.”
The past year has seen some AM machine OEMs step in to sell parts, a topic that at once highlights the challenges faced by these companies in
a tough period for the industry and those faced by application developers in producing and scaling their applications.
“Let’s step back. A few years ago, Alcoa split and created a separate parts division from the main aluminium business. I don’t think it lasted long. But what they realised was that the part producers were making far more money from their aluminium than they were making selling the material. So they wanted to get into that parts business, because it’s higher value.
“And that’s the thing in AM: the parts you make have to be more valuable than the machine you’re making them on, otherwise you’re not going to buy the machine.
When you look at a typical Additive Manufacturing person selling machines – including myself – we run on much better margins than Haas, Makino, etc. The real world of manufacturing is a cutthroat, low-margin industry. But a mature manufacturing market is a highly competitive market. Everyone is competing, whether on equipment, on tools, or on materials. You can draw direct parallels: genuine powders, binders, printheads, platforms. But, in the end, the customers have to be more valuable than the OEMs.
“And yet look at the recent headlines. I feel like most OEMs have gone back to operating their own parts businesses. But when you do that, when you try to sneak
Fig. 5 The Educator is designed as a Binder Jetting starting point, yet offers best-in-class technical and application support. It features a 125 mm wide build box, ideal for producing stress test dog bones or sampling new materials. The Educator, along with its highly customisable counterpart, The Researcher, can both be operated within inert environments, enabling the safe use of reactive powders such as aluminium and titanium. A range of accessories is also available, including customised hoppers, recoaters, and a drop watcher (Courtesy B-jetting LLC)
like Ford. Because they’d have the experience, the right people, and the cross-knowledge you need for something of that scale.
“The Educator came out of that idea. James and I were just doing consulting work at first. We had customers asking, ‘Is there a small Binder Jetting machine suitable for testing?’ After hearing that question enough times, we said, ‘Alright, we’ll build one.’
“So now, when OEM clients come to us, we say, ‘If you want to figure this out, buy one of these small machines. Learn how Binder Jetting works. Get your feet wet. Then work on scaling up your own machine.’
Of machines being used in research, Brunermer commented, “We currently have three machines in the field. We’re delivering another one in about a month. Like I say, I’m a bespoke person. People don’t come to me for standard machines – they come when they want something special.
in on the parts money as an OEM, you’re taking revenue from your best customers.
“When people ask me to make parts, I always say, ‘I don’t make parts. I make machines. If you want parts, talk to my customers.’ I’d much rather refer someone to a customer, because that customer is going to keep me in business. I don’t want to fight for the parts business. But OEMs are desperate for revenue, so they’re making parts and competing directly with their customers and the service bureaux.
“OEMs need to recognise that their machine isn’t worth what they think it is. A machine can’t be worth more than the parts it makes. You can’t have the attitude that the people making money from parts are somehow taking your money. That’s their money. Your money is for the machine and equipment. I feel like there are some misplaced ambitions around.”
“My ambition is to spread the word about Binder Jetting. I’m trying to promote and foster a market where people say, ‘Maybe this Binder Jetting thing is worth getting into at a reasonable level, at a reasonable price, to learn about it.’ When I created the Educator, my first thought wasn’t to educate the general public, though. I wanted to educate others – toolmakers, people who want to make Binder Jetting machines. That was who I had in mind.
“People who should be using my machines are those who want to become experts in Binder Jetting, understand all the nuances, and eventually be in a position to sell a $50 million solution to someone
“The first machine we shipped went to Vitriform3D, which was part of Oak Ridge National Labs’ Crossroads Program. They were a graduate of that programme, and we supplied them with a special Binder Jetting machine. It was designed to handle crushed, recycled glass frit, glued together using a UV-curable binder.
“We helped them develop the chemistry and process, and we’ll be supporting them as they scale. Their goal is to print large-scale objects, architectural pieces – big things. There’s plenty of glass frit available. They eventually want to scale up to something like an S-Max size. For now, they’re using the Researcher we built to develop materials.
“The second machine went to the National Research Council in Canada, at their Montréal facility, where they work closely with automotive OEMs. We supplied them with a Researcher which had a few interesting configurations. They were the first to ask for heated build boxes – important for stable metal printing. So we added heat and offered different build sizes. We made them a big box and a really small box because they wanted to use small amounts of material. Some of
their aluminium was a bit hard to get. They also bought a glovebox unit. The whole machine, the way I designed it, fits entirely inside a standard inert gas box. So they picked one up to allow them to do reactive work. They also got a drop watcher [a diagnostic system used to monitor and analyse the performance of printheads] so they could develop their own binders and tune waveforms and things like that. That was machine number two.
“Machine three is at the University of Tennessee in Knoxville. What made that one special was they wanted to use two binder systems. So, for example, they might print one regular binder, and in another area of the part, a binder with a special additive or enhancer. They wanted to print different binders in different locations to enable multi-material applications. So we built a special machine for handling two binders, including software for slicing two image sets – that was a completely custom machine.”
Brunermer has also built prototypes for in-house development. Three beta machines are shipping now, and three more are in production.
“The first of the new batch is a special one: our new beta for 2025. For the University of Pittsburgh, we built a special two-box unit. If you think about spreading powders in Additive Manufacturing, you can either recoat from the top or push powder from one box to another. They wanted a box-to-box feeding system, so I made design changes to the machine, extended it slightly, updated the software, and they’re getting our first box-to-box unit.”
Despite the number of papers published on Binder Jetting in the past five years, Brunermer believes that a lot of the fundamental science is barely understood.
“Take the interaction between binders and powders, for instance. If you look at the commercial binders available, there have only ever really
“Take the interaction between binders and powders, for instance. If you look at the commercial binders available, there have only ever really been three. And even though many companies would like to get into that space, it’s difficult. But that’s one of the areas I hope researchers will explore.”
been three. And even though many companies would like to get into that space, it’s difficult. But that’s one of the areas I hope researchers will explore.
“What happens when a droplet hits the powder? What’s the usable range of chemistries? What viscosities work? Can we eliminate steps in the process? That’s what I hope our Researcher machine will be used for: to help answer those fundamental questions.
“This work just hasn’t been done – or not to the extent it should. I feel like the world knows far more about Laser and Electron Beam Powder Bed Fusion than it does about Binder Jetting on a scientific level. In Binder Jetting, the material systems are still very OEM-dominated. Each company has its own preferences. They sell you the binder; they want to sell you the powder. It is what it is.”
This scenario brings back memories of powder supply management in the early days of Powder Bed Fusion. With Binder Jetting now, perhaps this cycle will break, possibly because some companies may no longer exist. How might that influence the availability of specific binders? If you are a company operating multiple Desktop Metal machines, should you be worried about supply security? Do you have alternatives?
Brunermer responded, “That’s a great question. Well, of course, people have options – they come to me! But seriously, should customers be nervous? I don’t know. But I’ll say this: they are nervous. There are a lot of us deeply involved in Binder Jetting who are having serious conversations about what we’re going to do. And maybe this is just part of the industry maturing.
“The British company, Atomic, has just announced a new ‘universal’ binder; I assume it’ll work on quite a few machines, and that’s a positive sign. Someone else is also stepping in on the sand side of Binder Jetting, and that market is even more exposed. It’s not exactly Powder Metallurgy, but it’s relevant. If you’ve got a dozen S-Max machines, you’ve invested somewhere between $18-24 million. The last thing you want is for your binder to become unavailable.
“At that scale, users are inevitably taking matters into their own hands. Some machine OEMs never made their own binders – they were simply private-labelled. Now, users are inevitably having conversations with binder producers directly about what would happen should anything go wrong.
“I’ve got to think that Nano Dimension, as part of its strategic review, is going to be looking at where ExOne makes money and
where it doesn’t. I reckon they make money on binder and service. But I doubt they make much money on the machines themselves.
“So binder, as a product, can sustain itself in a maturing market. And I’m bullish about services for one reason: our service business did more work in the first quarter of 2025 than we’ve done since we founded the company. Whether it’s on-site machine repairs, printhead rebuilds, or helping people solve technical problems, there’s a lot of concern out there, and people are looking for Plan B – and that’s because the successful applications are truly successful. These parts makers don’t make the machines; they make the valuable parts. So for them, it’s a big deal to think, ‘What if I can’t get my printer rebuilt anymore?’ These people are finding us, and we’re building a network. I know plenty of ExOne service techs, people who’ve been laid off over the past four years, so we’re bracing for it, but we’re ready.”
With the future of Desktop Metal looking uncertain, Nano Dimension’s strategy for Markforged unclear, and little news on the BJT developments at Colibrium Additive, I asked Brunermer if we were in a one-horse race with HP Additive Manufacturing.
“As we spoke about at RAPID and AMUG, HP is clearly making some headway. INDO-MIM just bought five of their systems. I’ve heard from people that there are some shops where ExOne machines are sitting idle, while the HP machines are just plugging away. So yes, you could argue it’s looking like a one-horse race – at least in terms of who feels confident enough to move forward.
“If you’re hyper-aware of the market, would you buy a Desktop Metal machine today, with so much uncertainty? I’d be surprised if anyone had bought one in the last six months.
“Until the big questions are answered and put to rest, they haven’t got a chance. And once it’s clear, I think you’ll see the pieces sold off. Either they get bought out of bankruptcy or someone will pick up the valuable assets.
“The sand business, for instance, is too valuable to just shut down. Someone’s going to move in on that. And Desktop Metal had a lot of interesting things – not just machines, but software too. They’ve got Live Sinter and a part-management app. So there are a lot of useful bits for which there’s definitely a buyer out there.”
As previously mentioned, a growing part of Brunermer’s business is BJT machine maintenance. Whilst many readers will be more familiar with the maintenance procedures and uptime expectations of PBF machines, for which there is a much larger installed base, I asked about the specific requirements and challenges around BJT machines.
“Printhead life can range from three months to three years. It all depends on how aggressive your materials are and how well your machine is designed. Mechanical subtleties – like how your wiping system interacts with the printhead – really matter. Miss those, and printhead life drops dramatically.”
“It really depends on the type of binder and what you’re printing on,” stated Brunermer. “Take sand printing, for example. You’re spraying binder onto sand. Some of that binder ends up on the wipers, and over time, if you take a printhead apart, the nozzle plate can look like it’s been hit with sandpaper. That’s real physical degradation.
“In metal Binder Jetting, I’ve found it mostly comes down to how you design your wiper systems and how they interact with the printhead modules. With my customers, I’d say 85–90% of failures aren’t from clogged nozzles – they’re from someone mishandling the nozzle plate. Maybe the wipers are adjusted too high and are hitting the nozzles too hard. Or maybe the wipers aren’t being kept clean enough. Most issues boil down to nozzle plate delamination or other common printing problems.
“The binders themselves can be harsh. Some chemistries are pretty aggressive. But if the parts are worth it, for example, if you’re making silicon carbide mirrors for satellites, and you have to replace the printhead every three months, then that’s just the cost of doing business. Printhead life can range from three months to three years. It all depends on how aggressive your materials are and how well your machine is designed. Mechanical subtleties – like how your wiping
system interacts with the printhead – really matter. Miss those, and printhead life drops dramatically.”
Brunermer stated that on his Researcher machine, a soft cloth wiper with zero deflection is used, so the wipe is very gentle, helping to preserve the printhead. “But yes, it gets expensive if you’re rebuilding your printhead every six months. To talk numbers: a typical printhead rebuild for an M-Flex costs around $10,000. Most of our customers come to us every six to nine months. So you’re spending about $1,000 to $1,500 a month on printhead maintenance.”
A common refrain from those getting into Additive Manufacturing – and especially those in machine development – is that the process turns out to be much more difficult than they initially imagined. Yet, Brunermer has often spoken about the idea of having fun with Binder Jetting. So I asked him – is it rocket science, or something a little more accessible?
“People assume it’s going to be easy – because you’ve got a printer at home, you print documents every day, you’ve seen 3D printers work, so how hard can it be? But what you learn over time is that Binder Jetting is a mate -
“ ...people always do it backwards. They think a technical feasibility study will be free and easy. It isn’t. I don’t know if this is unique to Binder Jetting, but it feels like it might be. Everyone asks first, ‘Can the technology do it?’ when what they should ask is, ‘Does this make business sense?’ Because if it does, then we can make the technology work.”
rials handling challenge. You’ve got to spread super-fine powder in a super-fine layer, and you’ve got to deposit a very specific liquid in very specific places. Sure, everyone’s seen powders – we put sugar in our coffee, right? So we underestimate it far too easily.
“My personal contribution to Binder Jetting is the tool. I’m not a sintering expert. I’m not a metallurgist. And in fact, I’d say the really hard part of Binder Jetting has almost nothing to do with the machine itself. You can build a machine. The hard part is the sintering side – what happens after the print. That’s where the real work starts. There are tools like Live Sinter, and Hexagon released a BJT sintering simulator recently as well. But yes, that’s where most of the complexity lies.”
This doesn’t mean that when a project fails, or when a grand idea doesn’t come together, the problem is always the sintering step. Brunermer explained: “It takes time and money to get it right. And yes, sintering is often where it breaks down. But here’s my issue with the typical approach to these projects – and it’s a broader problem in technical work: things often go backwards. Company leadership will say, ‘We have an opportunity. If you can make this work, we’ll talk about the business later.’ That’s ridiculous. My job is to make the technology work. Your job is to
make the business work. You go figure out if there’s a business case. Then I’ll figure out if the technology can meet it.
“But people always do it backwards. They think a technical feasibility study will be free and easy. It isn’t. I don’t know if this is unique to Binder Jetting, but it feels like it might be. Everyone asks first, ‘Can the technology do it?’ when what they should ask is, ‘Does this make business sense?’ Because if it does, then we can make the technology work.
“I always feel like that’s where we go wrong: people start with the tech and only later ask whether it was worth it. But if business leaders came together first and agreed on a direction, we engineers could work to make the technological barriers disappear. Just give us the environment and clarity to work in.”
Today, one can’t consider the Additive Manufacturing landscape without considering China’s place in it. With the pace and scale of developments there, it can look like China is running while Western companies are still talking.
“Yeah, absolutely,” Brunermer agreed. “Take EasyMFG. They’ve got ten different Binder Jetting systems, all aimed at different
materials. I didn’t go to Formnext last year, but I know they were there showing their machine. We’re definitely seeing good international progress. And yes, the Chinese are already pushing forward. What’s keeping them out, for now, is local support and service. But if they ever find the right importer – someone who can stand behind the machines – it could be painful. And I don’t just mean Binder Jetting. I mean the larger laser systems too. If they find the right partner, things could shift quickly. Let’s be honest, if someone can make a machine that’s every bit as productive as a 25Pro for a tenth of the cost – why wouldn’t you?
“So yes, it bothers me. But I try not to think about it too much. My ideal customer is someone who already has a 25Pro but wants to run small jobs on the side, or experiment and develop without tying up their production machine. My machine is perfect to sit next to your production line, if you’re already into Binder Jetting.”
Dan Brunermer’s insights offer a grounded view into the evolution of metal Binder Jetting, from its hidden successes to the growing need for specialisation, automation, and business realism. As the industry navigates economic pressures and supply chain uncertainties, it’s clear that future growth will not be driven by hype but by fit-for-purpose machines, strong partnerships, and a pragmatic understanding of what the process does well. It remains a technology with real promise but, as Brunermer reminds us, it has to earn its place, part by part.
Contact James Gill B-jetting LLC
james@b-jetting.com www.b-jetting.com
AND MANUFACTURING INNOVATIONS:
• Part Design • Metals & Alloys
• Tooling
• Molding
• Debinding
• Sintering
• Part Inspection
• Secondary Operations
• Process Simulation
• Competing Technologies
TARGETED AUDIENCE:
• Product Designers
• End Users
Ceramics
• Hardmaterials
• Binder Technologies
• Mixing
• Mechanical Properties
• Standards
• Coatings
Engineers
Manufacturers • Researchers
Students
Educators
Business Development
Held in Costa Mesa, California, the MIM2025 conference marked a significant moment for the Powder Injection Moulding community – not only for its technical programme and strong industry participation, but for a special symposium dedicated to honouring Prof Randall M German’s six-decade career. The tribute brought together former students, collaborators, and leading global experts to reflect on his scientific legacy and personal influence. Dr Animesh Bose reports from the event, highlighting Prof German’s unparalleled role in the rise of PIM.
Every year, the Metal Powder Industries Federation (MPIF) organises the International Conference on Injection Molding of Metals, Ceramics and Carbides. This year, the conference, referred to as MIM2025, was held from February 23-27 in Costa Mesa, California, USA. The conference featured a special group of presentations – each notated with a special icon in the programme –that had been inspired by Professor Randall M German (known to friends and colleagues as Rand), forming a symposium to honour and celebrate his exceptional six-decade career.
The organisers had issued personal invitations to many of Prof German’s former students and colleagues and these experts – coming from as far afield as Japan, Taiwan, India, and Spain –also shared some of their personal stories about their interactions with him. It was gratifying to see several of them accept the invitation to come and give a presentation.
All three co-organisers of this special segment of MIM2025 – Dr John Johnson, Prof Sundar Atre,
and I – have shared a close association with Prof German spanning many decades. Dr Johnson and Prof Atre completed their PhDs under the guidance of Prof German, whilst my own association with Prof German began in 1985, when he invited me to join his group as a visiting scientist at the Materials Research Center
at Rensselaer Polytechnic Institute (RPI) in Troy, New York, where he was then an Assistant Professor. This collection of invited papers honouring Prof German’s legacy was delivered by global experts and reflected his extraordinary impact on the PM and PIM industries over a career spanning six decades.
Chris Chapman, Advanced Metalworking Practices LLC, and Bill Thorne from BASF co-chaired MIM2025. As in previous conferences, this year’s event touched on the advances in injection moulding of metals, ceramics and carbides; looked at the developments that contribute to the growth of Powder Injection Moulding; and, through the short presentations given by various companies on their products and developments, kept the MIM community apprised of their unique offerings.
This year’s tabletop exhibit featured approximately twenty exhibitors, with experts from leading MIM companies available at the booth to address any questions from interested attendees. Companies ranged from powders, production equipment, process technologies, testing, and quality control. The tabletop exhibit –always well attended and well received – serves as a valuable platform to engage with current and potential suppliers, receive assistance with production and materials enquiries, and discuss technical questions and the latest trends in real time.
The two books co-authored by Rand and Animesh, highlighting their ongoing collaboration: The Injection Molding of Metals and Ceramics, published by MPIF in 1997, and Binder and Polymer Assisted Powder Processing, published by ASM International in 2020 [1]
The complete MIM2025 programme included a PIM tutorial presented by former MIMA President Matthew Bulger, the MIMA Standards Committee Meeting, the MIMA Board of Directors Meetings, the MIMA Membership Meeting, a welcome reception hosted by Arburg, technical sessions, process and product innovation discussions, as well as the aforementioned tabletop exhibition.
The MPIF honoured me by inviting me to deliver the first presentation in this special track. Alongside my paper, ‘Low-Pressure Powder Injection Moulding (LP-PIM) of Metals and Ceramics’, I shared my history with Prof German.
Our collaboration began in 1985, when he invited me to join his group at RPI as a visiting scientist. Fig. 2 shows one of our earliest photos together, alongside the then-new PIMFlow software. Judging by my full head of hair, I estimated the photo dates back to around 1986-87. Our collaboration continued even after I left RPI, culminating in two joint textbooks (Fig. 3).
I briefly outlined my journey from Rand’s lab at RPI to my current role consulting for the PM industry in both advanced processes and novel materials including PIM, sinterbased AM, refractory metals, hard materials, ultra-high temperature materials, metal and ceramic matrix composites. I described several applications for LP-PIM across ceramics and hardmetals, including cutting inserts, wire drawing dies, knives and blades for diverse industries, nozzles, drills, wear parts, sensor housings for space, and gun barrels.
Many carbide and ceramic components require complex shapes, traditionally fabricated by green machining or hard machining after consolidation. LP-PIM offers an alternative route for producing such complex parts.
For example, Fig. 4 shows a 47 g hardmetal part with intricate internal features, produced via LP-PIM.
LP-PIM is capable of fabricating both small and relatively large parts compared to conventional MIM. Fig. 5 illustrates a hardmetal LP-PIM twist blade nearly 20 cm long, used in nuclear steel cutting. The process has also produced blades over 30 cm for cutting diapers and silicon nitride gun barrels with internal twists of similar length. Additionally, LP-PIM can fabricate alumina parts, such as the textile industry spinneret shown in Fig. 6.
Advantages of low-pressure Powder Injection Moulding
Some of the key advantages of low-pressure Powder Injection Moulding (LP-PIM) over conventional PIM include the relatively low cost of tooling, which can be amortised over a much smaller number of parts, especially in the case of hard, wear-resistant components. In some instances, it has been possible to amortise tooling over as few as 100 parts per year, although a more typical figure is around 1,000.
LP-PIM also accommodates a wide range of part sizes, from very small components (less than 1 g) to parts exceeding 1 kg. Because the process operates at low pressure (around 100 psi), the tooling can be made from softer, more affordable materials such as aluminium or brass. The moulding temperature is also relatively low, typically around 100°C.
Furthermore, the same powder used in LP-PIM can often support a solid loading that is approximately 6–10% vol.% higher than in conventional PIM. This results in lower shrinkage of the final consolidated part, strengthening the case for LP-PIM in applications that benefit from its cost-effective tooling and enhanced material performance.
I concluded my presentation by noting that Prof German was not only a mentor to his students and fellow research collaborators but also interacted with them at a family level. As shown in Fig. 7, Prof German is pictured with his wife, Carol German, and me. Fig. 8 captures a moment with Prof German and Prarthana Bose, my wife. In Fig. 9, Prof German and I share a light moment together during a conference.
The next presentation in the series, ‘Synergising Metal Injection Molding and Materials Extrusion: Enhancing Manufacturing Flexibility and Performance,’ was delivered by Prof José M Torralba from the Department of Materials Science and Engineering at Universidad Carlos III de Madrid (UC3M), Spain. The presentation included several co-authors: Alberto
Meza, Andrea Alonso, Angel Martín, Adrián Barbosa, Lucía García de la Cruz, Paula Alvaredo, and Monica Campos.
In his presentation, Prof Torralba outlined Prof German’s illustrious career and provided insights into their close interactions, including his receipt of an honorary doctorate from the UC3M. In addition, Prof German is a Fellow of the American Society for Metals, American Powder Metallurgy Institute, and American Ceramic Society. His awards include the Tesla Medal, Nanyang Professorship, Japan Institute for Materials Research Lectureship, Penn State Engineering Society Outstanding Research Award and Premiere Research Award, Distinguished Research Award from the Japan Society for Powder Metallurgy, University of California at Davis Distinguished Engineering Alumni Award, The Ohio State University Distinguished Engineering Alumnus Award, San Jose State University Award of Distinction, Technical Development Award from the Japan Institute of Metals, Honorary Member of Alpha Sigma Mu, Society of Automotive Engineers Teetor Award, Honorary Professorship at Northeast University of Technology, RPI Early Career Award, Geisler Young Metallurgist Award, Kuczynski Prize, and Samsonov Prize.
“Prof Torralba also spoke about Prof German’s 2004 UC3M investiture speech in which he focused on the importance of engineering education and the need to improve engineering studies at universities.”
Prof Torralba adopted the theme of ‘on the shoulder of giants’, naming several of the stalwarts of the PM industry. The list of these names included Boettger, Wollaston, Acheson, Ostwald, Moissan, Coolidge, Frenkel, Lenel, Kuczynski, Kingeri, Coble, Johnson, Ashby, and, of course, German. Prof Torralba also spoke about Prof German’s 2004 investiture speech in which he focused on the importance of engineering education and the need to improve engineering studies at universities.
Combining high-entropy alloys and material extrusion
Prof Torralba proceeded with his technical presentation, which discussed a method for fabricating parts using lower-cost high entropy alloys (HEA) and a Material Extrusion-based AM process. Mixing existing PM alloys to achieve the HEA composition is an interesting approach that may provide a novel way of fabricating this class of material into useful complex shapes.
The overall processing steps are depicted in Fig. 11, while Fig. 12 illustrates a comparison of the extrusion-based process, referred to as Composite Extrusion Modelling (CEM), with Metal
Fig. 14 Schematic diagram of the extrusion Additive Manufacturing machine [2]
Injection Moulding and Additive Laser Manufacturing (ALM), also know as Laser Beam Powder Bed Fusion (PBF-LB). Fig. 13 presents details of the characteristics of the HEA powder used in this investigation, including the composition and the X-ray analysis of the bcc powder. The feedstock was produced using paraffin wax (PW) and high-density polyethylene (HDPE) at a mixing temperature of 170ºC and a shear rate of 40 rpm. A schematic of the extrusion-based AM process employed is shown in Fig. 14.
The presentation discussed the impact of processing parameters, with Fig. 15 highlighting how variations in layer thickness can result in voids within the build structure.
Matrix: Fe-Cr rich
Precipitates: Ni-Al rich
Formation of two BCC phases:
• disorder BCC (matrix)
The built parts were subjected to solvent debinding using Heptane at 60°C for 3 h, followed by thermal debinding. Sintering was carried out in high vacuum using a constant heating rate of 5°C/min to a sintering temperature of 1,360°C and held there for 2 h and cooled using a cooling rate of 5°C/min.
Fig. 16 shows the SEM photomicrograph of the consolidated HEA material and the composition of two select areas within the microstructure, shown as Area 1 and Area 2.
Fig. 17 shows a higher magnification SEM photomicrograph where the composition of the matrix area is shown in Area 1 (shown in Fig. 16) and the composition of the Ni-Al rich precipitate is shown in Area 2 (shown in Fig. 16). The overall grain size is around 60 +/23 µ m, and the precipitates are around 1.2 +/- 0.2 µ m.
This material was used to create feedstocks that were also processed by MIM. In this case, three powder loadings of 58, 60, and 62% v/v were used. The binder used was the same PW and HDPE that were mixed in the ratio of 1:1, as mentioned above. The parts were injection moulded at a temperature of 180°C, and a pressure of 6 bar to form small tensile test samples. The green parts were solvent debound and thermal debound,
• Ordered B2 coherent precipitates are responsible for the mechanical properties of the alloy
Matrix: Fe-Cr rich
Precipitates: Ni-Al rich
Fig. 17 Shows a higher magnification SEM photomicrograph where the composition of the matrix area is shown as Area 1 (shown in Fig. 17) and the composition of the Ni-Al rich precipitate as shown in Area 2 (also shown in Fig. 16) [2]
“The presentation discussed the impact of processing parameters, with Fig. 15 highlighting how variations in layer thickness can result in voids within the build structure.”
Strain [-]
• Hardness-meter Vickers NEXUS 4303 (Innovatest). 1 kgf, 25s
• PIP 8 kN Benchtop Plastometer (Dynisco).
Shows the density, hardness, and tensile properties (based on Plastometer testing) of a HEA alloy processed using MIM, as a function of powder loading in the feedstock [2]
followed by final sintering that was carried out in a high vacuum of 10 -5 Pa.
Two different peak temperatures and hold times were employed in the investigation (1,200°C for 6 h and 1,375°C for 3 h). A microstructural evaluation was conducted, and various mechanical properties of the material were assessed. The
mechanical properties of the injection moulded HEA alloys are shown in Fig. 18. The tensile properties presented are not based on direct measurements of tensile properties but are, instead, extrapolated from a plastometer that uses hardness measurements to provide fairly accurate tensile properties.
On a personal note, Prof Torralba expressed deep admiration for Prof German, describing him as a trailblazer who has shaped his own career and inspired many others, including his students. Their close association with Prof German is reflected in Figs. 19 and 20. Prof Torralba concluded his presen -
tation with a simple slide reading, “Thanks a lot, Rand!” – a sentiment shared by many in the PM and PIM community.
Matthew Bulger delivered the next paper in the series, titled ‘Particle Size Effects in MIM’. A former Master’s student under Prof German at RPI, Bulger is now a consultant and continues to share his expertise through the MPIF’s PIM tutorial, typically held at the start of the MIM conference.
Bulger began with a slide that read, “Welcome Back to the Fabulous 80s for MIM!” He outlined the early players in PIM, which, as he stated, was a brand-new way of making metal components. Among the key players mentioned was Parmatech Corporation, founded in 1973 and often referred to as MIM’s ‘ground zero’. The company played a pivotal role in the early dissemination of MIM, licensing it to numerous companies worldwide. One of Parmatech’s original co-founders, Ray Weich, left the company and ‘became the Pied Piper of MIM’.
Beyond Parmatech, several other early pioneers in MIM have also endured and continued to contribute to the industry’s growth. These include Brunswick (now FloMet – Cadence), Advanced Forming Technologies (ARC Colorado), Omark (now OptiMIM), 3M (Unitek), SSI (now DSB Technologies), Rocky Mountain Ortho, and Remington Arms.
Bulger noted that there was little academic support for PIM until 1986, when Prof German, along with two other professors at RPI, spearheaded a PIM consortium named Advanced Powder Processing (APP). With many early MIM companies working with ‘black box’ licensed technologies, twenty interested companies signed on to see basic R&D results. Prof German concentrated on powder characteristics that affected sintering, packing/solids loading, mixing, and shrinkage from moulded
Fig. 21 Results of green and sintered density using large and small iron powders [3]
part to sintered parts and their final microstructure and properties.
The milestones that were outlined for the powders were that they pack well, sinter to high density, are compatible with the organic binder used, minimise cost, and show a consistent process response.
Bulger pointed out that fine powder sources were limited in the 1980s, with elemental powders dominating. Carbonyl iron powder was the workhorse, though elemental nickel, molybdenum, tungsten, and copper powders were also available. For stainless steel production, ferrochrome powder was used in conjunction with available elemental powders to achieve the desired composition.
Pre-alloyed stainless steel powders came later, with gas atomised 316 available through Anval (now Sandvik) and water-atomised powder coming from Ametek. Ultrafine Powder (now part of Novamet) started its powder production around 1988, and Sandvik/ Osprey began its operations in the early 1990s.
On the particle packing front, it was determined that size makes a difference in how powders pack, with larger powders packing more
easily than smaller ones. The distribution of the powder also influences packing, as wide particle size distributions allow smaller powders to fit into the void spaces between larger particles, resulting in reduced distortion after sintering. The way Bulger put it: “The more parts shrink, the more they stink.” Monosize spheres with minimal interparticle friction are expected to have a packing of ~ 63%, while adding a small amount of powder that is around 10x smaller in size can lead to a packing of ~ 82%.
The 1988 APP study that Bulger spearheaded included the use of carbonyl Fe and gas-atomised Fe powders. The carbonyl Fe had an average particle size of 4.5 µ m and a 4.3 g/cm 3 tap density, while the gasatomised Fe had an average particle size of 66 µ m and a 5.0 g/cm 3 tap density. The investigation looked at packing and sintering results at different small particle additions.
The results are graphically shown in Fig. 21. The results showed that the highest sintered density was obtained with 100% fine carbonyl powder. The highest packing was achieved using a 70% large and 30% small powder. The sintered density was found to be equal to packing density for the large monosize powders. Results showed that small powders tend to agglomerate and instead of being uniformly distrib -
uted and occupying spaces between the large particles, they agglomerate, resulting in large porosity and cracks as depicted in Fig. 22.
Another result outlined showed that a wide powder particle size distribution benefited the powder packing (shown in Table 1). Another conclusion from this investigation was that fine ‘monosize’ particle size (carbonyl Fe) feedstock is harder to mould than feedstock made with a wide particle size distribution of a gas atomised powder (17-4PH) for
similar solids loading. The work also demonstrated that fine particle sizes reduce distortion during sintering, with the distortion measured by the deflection of unsupported tensile bars, all at the same solids loading. Bulger concluded his presentation by asserting that the fundamentals of particle size and particle size distribution significantly influence the reliability of MIM as a production process. The work and publications of Prof German on these issues spanned five decades and established the
“The work and publications of Prof German on these issues spanned five decades and established the foundational scientific principles for process basics that are now often taken for granted.”
foundational scientific principles for process basics that are now often taken for granted.
The next presentation came from Dr Gemma Herranz, from Universidad de Castilla-La Mancha (DYPAM) and CEO of Blesol Tech, Ciudad Real, Spain. She combined her personal journey, in which Prof German played a significant role, with a technical presentation discussing trends in R&D and exploring synergies between PIM and AM.
Her journey in the PIM sector is something of a testament to Prof Germans’ global influence, with Dr Herranz receiving the first PIM-focused PhD in Spain, developed within a project led by Prof Torralba. This has led to another groundbreaking role in Spain, with Blesol Tech the first Spanish company producing injectable and buildable feedstocks and offering specialised services for sectors such as energy, automotive, and aerospace.
The synergy between PIM and AM outlined by Dr Herranz can allow the expansion into new markets and progressive scaling of applications. Fig. 23 shows some of the R&D areas that are of interest, with Fig. 24 showing some of the broad focus areas of R&D from DYPAM. The energy sector R&D was focused on the development of solid oxide fuel or electrolysis cells (SOFC and SOEC, respectively), paying attention to durability, cost, and scalability. The two main areas of interest were interconnects and anodes.
For interconnects, the feedstock and filaments were not commercially available. Feedstocks and filaments were developed, and critical design improvements were made to maximise PIM capabilities. In the case of the anodes, the R&D focused on the development of two ceramic feedstocks and the tailoring of porosity to maximise performance.
The typical pathway involves prototyping using the AM process and developing mass production
Test results of electrochemical characterisation [4] (Source: DOI: 10.1016/j.ijhydene.2021.02.097)
at a reduced cost. These developments, which include electrochemical performance testing and component design, are conducted in close collaboration with the National Hydrogen Centre (CNH 2) in Spain, where the electrochemical characterisation of the produced materials takes place. Fig. 25 shows some of the test results from the electrochemical characterisation.
In aerospace, tailoring the composition and control of the Ceramic Injection Moulding parameters enables the regulation of the existing
phases, thus influencing the dielectric and thermal properties of the ceramics. Research into materials explores the potential of incorporating graphene into cordierite composites using CIM, contributing to the development of advanced materials for aerospace applications. CIM samples demonstrate a greater mullite phase content, a more homogeneous microstructure, and reduced porosity. This work is being conducted in collaboration with INTA (the Spanish National Institute for Aerospace Technology)
as part of a dedicated research project. Fig. 26 shows a lens holder as an example of the applications developed in the aerospace sector using graphene-reinforced cordierite.
Some of the most promising areas of development in aerospace include the efforts focused on modelling, processing, and validating metal alloys with 2D reinforcements, achieving significant modifications in mechanical and functional properties. The modelling encompasses meta-, micro-,
Fig. 27 The steps used for biomaterial development [4] (Source: DOI:10.1016/j.jmrt.2024.02.057)
and meso-scale structures, while processing involves designing experiments for Fused Filament Fabrication (FFF) and other Additive Manufacturing technologies. These developments target applications demanding unusual combinations of properties, achievable through the design of metamaterials with tailored architectures. These developments create opportunities for tailoring materials to meet the demanding combinations of properties required in aerospace, automotive, and energy applications.
Biomaterials and functional materials development
Another significant focus of Dr Herranz’s lab is biomaterials and their processing. One material in development is a nano-sized 3-YSZ (Yttria Stabilised Zirconia) powder, intended for producing YSZ scaffolds for bone tissue engineering via FFF.
The steps for biomaterial development included designing the filament formulation, mechanically evaluating the filaments, characterising the built parts, and assessing mechanical properties and the tendency for infec -
“Another significant focus of Dr Herranz’s lab is biomaterials and their processing. One material in development is a nano-sized 3-YSZ (Yttria Stabilised Zirconia) powder, intended for producing YSZ scaffolds for bone tissue engineering via FFF.”
tions (illustrated in Fig. 27). In the future, biomaterial development will incorporate 2D materials to enhance bioactivity, as well as in vitro and in vivo testing.
The other areas of focus included rheology studies for filament development and the creation of functional materials. Here, significant results have been achieved, such as a notable enhancement of the luminescent properties of the developed materials (Fig. 28), which demonstrates the ability to finetune these properties by carefully controlling the processing parameters. This opens up new possibilities for tailoring functional responses through advanced manufacturing routes.
Collaborations and future directions
During the presentation, Dr Herranz also highlighted important collaborations that have enabled specialisation in diverse sectors, including the National Hydrogen Center (CNH 2), Ciudad Real Hospital, and the National Institute of Aeronautical Technologies (INTA),
among others. She also discussed Blesol Tech, which took her on the journey from research to industry.
According to Dr Herranz, PIM technology shows enormous potential across various sectors, and her work is pushing the boundaries of innovation through advanced materials and customised solutions.
She concluded by stating that we are celebrating Prof German’s legacy, whose inspiring work continues to guide and transform our journey.
Fig. 29 shows Dr Herranz with Prof German, while Fig. 30 also features Prof Torralba and illustrates his close connections with the Spanish PM community.
The next presentation in the series was delivered by Dr Pavan Suri from HP, in collaboration with his co-authors Ravi Mayavaram and Narendra Singh from Altair. Their work, titled ’Automatic Shape Compensation for Shrinkage During Binder Jet Sintering Process,’ was jointly presented by Drs Suri and Singh.
Fig. 28 Application areas of functional materials [4] (Source: DOI: 10.1016/j. ceramint.2019.12.190)
Slightly oversized to account for shrinkage during sintering
Removal of binding agent using solvent, catalyst or thermal • Heat treatment in a furnace Densification and increase in strength
Dr Suri, who completed his PhD under the guidance of Prof German, introduced the motivation behind the study, highlighting the growing significance of Binder Jetting as a key Additive Manufacturing process. This method avoids melting, reduces energy consumption, and enables the production of large, complexshaped components. For BJT to be effective, accurate shrinkage prediction and compensation are essential. Singh, Programme Manager for Manufacturing Solvers at Altair, elaborated on the computational
theory and simulation methodologies underpinning the work. Fig. 31 shows the general steps associated with BJT.
For sintering analysis, the input data included initial geometry of green powder compact, initial average particle size, initial density field, sintering constitutive law and its parameters, grain growth law and its parameters, sintering temperature curve, friction and support conditions. The Simulation Output provides a timeline of the following: part shape
and dimensions, density, stress field, strain field, grain size, and strength properties.
Several parts (Fig. 32) were chosen for validation examples. The simulation carried out on 316L requires several material characteristic inputs, such as the thermomechanical and viscosity data shown in Table 2. The sintered prediction analysis of the part designated as the bracket is shown in Fig. 33, and an actual sintered versus a simulated bracket is shown in Fig. 34.
Thermomechanical Data Viscosity Data
General Model
Density
8.0e-6 kg/mm 3 Constitutive model
Specific heat 900.0 J/(kg*K) Universal gas constant
Condutivity
0.015 W/(mm*K) Activation energy
Coeff of thermal expansion 1.12e-05 1/K Shear modulus
Volumetric heat source 0.0W/m 3
Liquidus temperature
Solidus temperature
Densification start temperature
Densification maximum temperature
Strain rate offset
K Initial grain size
K Surface energy X
K Surface energy Y
K Surface energy Z
Table 2 Thermomechanical data and viscosity data for 316L used in the simulation [5] Some fields are left blank where input data was either not available or not required by the simulation model
“For repeatability studies, as not all parts are the same, there is variation due to the processes, material and limitations due to the model assumption and process repeatability. Bridging the gap between simulations, compensation, and actionable outcomes is an ongoing focus.”
These simulations are used for hot spot analysis to evaluate part survivability during debinding, enhance design robustness, and detect, avoid, and compensate for deformation during sintering. Use of tools such as Physics AI further enables rapid design iterations to check for green part robustness prior to the build. For repeatability studies, as not all parts are the same, there is variation due to the processes, material and limitations due to the model assumption and process repeatability. Bridging the gap between simulations, compensation, and actionable outcomes is an ongoing focus.
• Gravitational force (mg)
• Frictional force ( µ mg/2)
• Sintering force (?)
Direction of sintering
Frictional forces always oppose shrinkage, gravitational forces can either oppose or aid shrinkage, and sintering forces always aid shrinkage
Sintering studies inspired Prof German
TS (‘Shiv’) Shivashankar gave the following presentation in this series from Indo-MIM, entitled ‘Sintering Studies Inspired by RMG.’ The paper had two co-authors: Ramana Reddy and Sridhar Dharshan. Dr Shivashankar did his PhD with Prof German as his supervisor (Fig. 35), before eventually settling back in India, where he is now VP at Indo-MIM, one of the largest MIM companies.
He gave a fascinating presentation and introduced the concept of the ‘centre of sintering.’ The inspiration came from Prof German’s lab and Dr Shivashankar pointed out that sintering simulations in the past have been more on the particulate rather than the component level. Particle size, shape, PSD, and solids fraction are all fixed, and it’s the components that change. Models that can predict distortions and suggest alternate ‘setting methods’ are going to be highly beneficial.
Fig. 36 shows a schematic of the forces exerted on green parts during sintering (FBD). It is interesting to note that gravity can
“Dr Shivashankar pointed out that sintering simulations in the past have been more on the particulate rather than the component level. Particle size, shape, PSD, and solids fraction are all fixed, and it’s the components that change. Models that can predict distortions and suggest alternate ‘setting methods’ are going to be highly beneficial.”
aid and oppose sintering at the same time; Fig. 37 shows the schematic of the sintering pull force toward the centre of gravity. An important conclusion from this approach is that it is not the magnitude of the friction force, but the position on the part where it influences that determines the distortion from the nominal.
The centre of sintering experiments were run by the use of tensile bars with equal external weights on the two ends, a bar with no weights, and a bar with the external weight placed only on one side (that shifts the centre of gravity toward the side where the external weight was placed).
Schematically, Shivashankar illustrated the difference between the
• What maximum frictional force will cause distortion to occur?
Sintering force
Sintering force
• Can we increase frictional force to estimate the maximum sintering force?
• Center of Sintering is a point in the green part that does not move during sintering
Shrinkage towards CS
No external weight Center of sintering coincides with center of gravity
Equal external weight on both sides Center of sintering coincides with center of gravity
External weight on one side
Center of sintering moves towards the side that is heavy/constrained
Shrinkage towards CS
Shrinkage towards CS
Plane of Sintering is the plane where TUG of WAR takes place between Sintering forces and Frictional forces during sintering
Fig. 38 A schematic of the concept of centre of sintering [6]
Center of Gravity (CG)
@ CG point
• Center of gravity is the point where torque due to weight from both sides are equal
Center of Sintering (CS)
CS point ‘t’ is where,
• Center of Sintering is the point where forces opposing shrinkage (sintering) are equal
Fig. 39 A schematic showing the difference between centre of sintering and centre of gravity [6]
centre of sintering (CS) shown in Fig. 38 and the centre of gravity (CG) in Fig. 39.
He went on to state that the double weight experiments suggested here could assist in developing stress-strain curves for each material. The concept of the centre of sintering was introduced as a pivot point for sintering, and manipulating the CS to a plane that is wider or thicker will help achieve consistent
first-pass yields. Finally, Dr Shivashankar promoted the use of simulation software to analyse various ceramic ‘setting or staging’ options. According to him, manipulating the inter-particle spacing is key to improving the strength of green parts during sintering. This parameter combines the effect of mean particle size, size distribution, and powder volume fraction.
The next paper in the invited talk series was presented by Dr John L Johnson, COO of Novamet / Ultrafine Powders, who completed his PhD under the supervision of Prof German. His presentation was entitled ‘Powder Injection Moulding of Thermal Management Materials,’ began with an overview of key
application areas. These included semiconductor chips (10–100 W/cm²), high-brightness LEDs (10–100 W/ cm²), lithium-ion batteries under high discharge conditions (5–100 W/cm²), phased array antennas (1–50 W/cm²), RF power devices (500–800 W/cm²), and plasma-facing components in fusion reactors (700–2,000 W/cm²).
He also discussed current thermal management solutions, which fall into three broad categories: air cooling, liquid cooling, and immersion. Air cooling typically involves the use of heat sinks and fans. Liquid cooling can be implemented in several ways, each offering varying levels of heat dissipation: direct-tochip microchannels (up to 790 W/ cm²), sprays (up to 1,200 W/cm²), jet impingement (up to 2,000 W/ cm²), and heat pipes (ranging from 10,000 to 20,000 W/m²). Dr Johnson also pointed out that the thermal performance of the current heat sinks is not optimised.
MIM enables the production of complex designs that enhance thermal performance.Copper heat sinks produced via MIM, using –25 µ m powders with a solids loading of 52–68 vol.% and sintered in hydrogen at 1,000–1,075°C, can achieve final densities of 93–94% of theoretical, with shrinkage ranging from 9–19%, depending on the initial loading and final density. However,
Dr Johnson noted that improper processing conditions can lead to oxide reduction, which may result in part swelling.
Fig. 40 shows a MIM copper heat sink; Fig. 41 shows two crosssectional microstructures of copper when sintered using a high heating rate and a slow heating rate. The microstructure of the part produced using a high heating rate was quite porous, with large pockets, compared to the microstructure of the part that was heated slowly
to the sintering temperature. The high porosity of the parts sintered at high heating rates is due to the entrapment of the gases evolving during the heating-up phase. Dr Johnson also pointed out the negative effect of iron impurities in copper-based material on the thermal conductivity.
Dr Johnson went on to present the fascinating concept of two-material injection moulding of a 13 µ m Cu powder and a -150/+325 mesh Cu powder that were co-sintered
• Wick sintering density of 64%
• 22 µm average pore size
• Calculated permeability of 10 -7 cm 2
Suitable for heat fluxes above 100 W/cm 2
Fig. 42 Two-material injection moulded copper part (left) with sintered density of 64% in the coarse powder section and average porosity of 22 μm. The middle image shows the interface between areas formed with coarse and fine copper powders, while the right image is an SEM photomicrograph of the coarse powder region [7]
at 1,050°C. Fig. 42 shows a twomaterial injection moulded copper part (left), with the section produced using coarse powders reaching a sintered density of 64% and an average porosity of 22 µ m. The middle image displays the microstructure of both regions of the part, made from coarse and fine powders. The right-hand image presents an SEM photomicrograph of the coarse powder region, showing the porosity and neck formation between the copper particles.
Additive Manufacturing and alternative heat spreaders
His presentation also briefly covered the area of additively manufactured copper thermal management parts. He showed examples of copper heat sinks based on Material Extrusion and BJT. Both processes were based on using polymer-assisted AM followed by removal of the binder and sintering, with the MEX process having a closer resemblance to the MIM process.
• Enables more complex parts than MIM
• Sinter-based metal AM uses similar Cu powder and sintering profiles as MIM
Cu heat sinks (images courtesy of Univ. of Louisville)
Fig. 43 shows pictures of heat sinks that have been fabricated from copper using the MEX process and 3DEO’s variant of the Binder Jetting processes.
Dr Johnson also covered W-Cu-based heat spreaders fabricated with tungsten content between 80 and 90 wt.% and using sub-micron W-Cu powder, a solid loading of 52 vol.%, and liquid phase sintering at ~1,300°C in a pure hydrogen atmosphere.
Pure Cu heat sink produced by the 3DEO’s sinter-based AM technology
Heat sinks fabricated from copper using MEX, alongside a pure copper heat sink produced by 3DEO’s sinterbased Additive Manufacturing technology [7]
Fig. 44 shows the pictures of several heat spreaders made from W-Cu; the presentation also showed some examples of heat sinks made from Mo-Cu composites. Dr Johnson also covered some ceramic-based heat spreaders made from AlN with 2-6 wt.% Y 2O 3 made by PIM. The powder used was for 1.5 µ m, using a solids loading of 60 vol.%. The material was liquid phase sintered at 1,850°C using a nitrogen atmosphere, where the Y 2O 3 forms an eutectic liquid with Y 2O 3. Fig. 45 shows PIM heat spreaders made from AlN–Y 2O 3
In summary, Dr Johnson stated that thermal management remains an ongoing challenge. However, MIM and metal AM can provide new design solutions from many high thermal conductivity materials used as heat sinks, heat pipes, and heat spreaders. The materials discussed were Cu, Al, W-Cu, Mo-Cu, and AlN-Y 2O 3. Some of the key factors in making desirable high thermal conductivity parts include the effects of impurities, microstructures, and cost.
The next speaker, Prof Emeritus Hideshi Miura of Kyushu University, travelled all the way from Japan to attend this conference and participate in the celebration of Prof German’s career. He previously worked with Prof German in his lab in the USA.
In ‘Development of Innovative Ti Alloy Compacts Through MIM Process,’ Prof Miura focused on the effect of microstructural refinement on the mechanical properties of injection moulded Ti-6Al-4V alloys. His study concentrated on the impact of using fine powder, the effect of α + β
region sintering, and the effect of hydrogenation and dehydrogenation treatment. He also discussed the influence of pore size and grain size on the high-cycle fatigue strength.
Titanium alloys have excellent property combinations, including high specific strength, good corrosion and thermal resistance, and excellent biocompatibility. These attributes make Ti alloys especially suitable for applications in the aerospace, automotive and medical sectors.
Among the Ti-alloys, Ti-6Al-4V has a good balance of strength, ductility, and toughness, but has poor workability and high forming cost. It is expected that MIM will be a suitable technique for fabricating
more complex-shaped parts with mass production capability (this by reducing the forming cost).
In his earlier studies, Prof Miura determined that the tensile properties of MIM Ti-6Al-4V alloy compacts are dictated primarily by relative density and oxygen content after sintering rather than the raw material powders and process conditions. The tensile strength (880 MPa) increases significantly with increasing density and oxygen content up to 0.5 mass%. The equation that connects the strength with the oxygen content is given below:
σ [MPa]=700*Oxygen [mass%] + 10 ρ [%] – 315 [Oxygen < 0.5% and density > 94.5%].
“In his earlier studies, Prof Miura determined that the tensile properties of MIM Ti-6Al-4V alloy compacts are dictated primarily by relative density and oxygen content after sintering rather than the raw material powders and process conditions.”
Table 3 Tensile properties, density, and sintering conditions [8]
4
Prof Miura also observed that ductility is excellent with oxygen content of less than 0.35 mass% (>10%). In this investigation, the MIM process was applied to strengthen Ti-6Al-4V alloy compacts through the addition of fine Fe, Cr, and Mo powders. The effects of third additive elements and sintering conditions on the mechanical properties and microstructures of the injection moulded compacts were primarily investigated. The Fe, Cr, and Mo are β -phase stabilising elements that strengthen the alloy. A term designated as Mo equivalent, based on the mass percentage of several elemental additives, was determined, and the equation is shown below:
[Mo] eq = [Mo] + [Ta]/5 + [Nb]/3.6 + [W]/2.5 + [V]/1.5 + 1.25[Cr] + 1.25[Ni] + 1.7[Mn] + 1.7[Co] + 2.5[Fe]
One of the compositions he investigated was Ti-6Al-4V-4Mo, which, based on the equation above, had a [Mo]eq of 6.7 and sufficient ductility of over 10%. The additions of Fe or Cr were based on the [Mo]eq, which provides a phase-stability classification. When injection moulding these alloys, the relative density was relatively high, exceeding 97% due to the enhancements of elemental diffusion and densification by additional fine particles of Al-40V, Mo, Fe and Cr powders. The strengthening of
Microstructure of Wrought Ti-6Al-4V
Ti-6Al-4V alloy compacts with added Mo, Fe, or Cr powder was attributed not only to fine microstructural modification but also to solid solution strengthening due to the increased β phase content.
Table 3 shows the properties of the modified Ti-6Al-4Al alloys with the additions of Mo, Fe, or Cr. All three new alloys show an increase in strength while the elongation remains almost the same.
One problem with injectionmoulded Ti-6Al-4V alloy compacts is their low fatigue strength, as shown in Table 4. The problem has its roots in the difference in the microstructures between the wrought and MIM samples. The wrought microstructure is much finer than the MIM Ti-6Al-4V microstructure (Fig. 46). One method being tried is the use of TiB 2
At high temperatures – and thus during sintering – TiB 2 particles change to many TiB particles and work as pinning particles against the grain growth of the
Microstructure of MIM Ti-6Al-4V
β lamellar and large prior β grains [8]
prior β phase. Fig. 47 shows the EBSD (electron backscatter diffraction) microstructure showing grain refinement with increasing boron content.
Fatigue testing was carried out on several Ti-based alloys, beginning with a baseline Ti-6Al-4V alloy in both sintered and HIPed conditions. Modified versions incorporating 0.4B were tested with and without HIP, showing improved fatigue performance. The standard fatigue strength for wrought Ti-6Al-4V was 510 MPa; this served as a benchmark. Building on this, Prof Miura further investigated a dual-modified alloy incorporating 4Mo and 0.4B. These samples were sintered for 4 or 8 h, with some also HIPed. The fatigue properties of the baseline, 0.4B-only, and 4Mo-0.4B alloys – in both HIPed and non-HIPed conditions – were compared, with results shown in Fig. 48.
Prof Miura also discussed an alternative method for refining microstructure through hydrogenation and dehydrogenisation (HDH), as well as another sintering technique at lower temperatures, specifically at 980°C (which is just below the β transus of 1,000°C) for periods of 24, 48, and 96 h. Fig. 49 illustrates the fatigue strength of several Ti-6Al-4V alloys and their variations, including those of HDH and HDH-HIP parts. The figure also presents the properties of a typical MIM Ti-6Al-4V alloy alongside those of standard wrought material. Prof Miura concluded his presentation with several key findings
4Mo-0.4B→430 MPa 4Mo-0.4B(HIP)→470 MPa
The fatigue strength of 4Mo-0.4B was almost the same as 0.4B
Fatigue strength of Ti-6Al-4V alloy and its modification using 0.4B and 4Mo-0.4B processed by both sintering and Hot Isostatic Pressing (HIP) [8]
Fig. 49 Fatigue strength of Ti-6Al-4V alloy and its modification using 0.4B and 4Mo-0.4B processed by both sintering and hot isostatic pressing (HIP) [8]
regarding the mechanical properties and microstructural optimisation of MIM Ti-6Al-4V alloys through elemental additions and processing strategies.
The study found that the addition of both molybdenum (Mo) and boron (B) led to a refined microstructure, with fine prior- β grains and a fine lamellar structure. Mo contributed to improved static properties, while B enhanced dynamic performance. Specifically, compacts of Ti-6Al-4V with 4 wt.% Mo and 0.4 wt.% B demonstrated excellent tensile properties, achieving a strength of 1,030 MPa and 13% elongation.
The fatigue strength of these 4Mo-0.4B modified compacts was reported as 430 MPa in the as-sintered condition (8 h) and 470 MPa following HIP treatment. These values were comparable to compacts containing only 0.4 wt.% B.
Tensile strength in MIM Ti-6Al-4V compacts was found to correlate with an experimental equation that incorporates oxygen content (O), density ( ρ ), and grain size (D), demonstrating the complex interplay of these factors in determining mechanical performance.
Notably, excellent static and dynamic mechanical properties were achieved through a combination of techniques aimed at refining the microstructure. These included the addition of third and fourth alloying elements, the use of fine powders, sintering within the α + β phase region, and the application of hydrogenation–dehydrogenation treatment.
A detailed analysis of fatigue behaviour revealed the critical role of pore-to-grain size ratios. When the maximum pore diameter exceeded twice the grain diameter, fatigue fractures initiated from the largest pore in the sintered compacts, with a dramatic decline in fatigue strength observed. Conversely, when the poreto-grain size ratio was below two, fracture initiation shifted to facets within the grains.
Finally, the research emphasised that fatigue strength increases with higher relative density and that the relative size of pores to grain size is a decisive factor in achieving high fatigue performance in all sintered materials.
The next presentation in the series was given by Dr Joseph (‘Joe’) Tunick Strauss from HJE Company, Inc. Strauss also did his PhD under the guidance of Prof German and was one of his early graduate students who completed his PhD thesis in 1991 from Rensselaer Polytechnic Institute.
On a personal note, Joe was one of the three people responsible for my continued stay in the USA. He helped me get my first automobile in the USA (without which living in the US for a long time is extremely difficult) and was an excellent guide who introduced me to US culture.
“As precious metal powders could be processed efficiently using the HJE atomisers, it was hoped that jewellery companies would utilise MIM and require an atomiser. Many HJE atomisers have been sold to produce precious metal powders for MIM and are now also being used for AM-grade powder.”
He had an exceptionally interesting story about how he migrated to MIM, though it had very little to do with his PhD topic.
His presentation was entitled ‘Microstructural Evolution of WC/ Co Alloys with Vanadium Carbide Additions’, though he did mention in his presentation that I had first told him that he could present some of his thesis work. I did, however, encourage him to include a connection to Metal Injection Moulding; he faced the unenviable task of not only presenting his research but also weaving in the story of how he became involved in MIM.
Essentially, in Strauss’ words, after several tedious years attempting to find a mechanism for why VC additions lead to grain refinement in WC-Co-based hardmetals, and failing to identify any existing model that fit, he was compelled to develop his own model to accommodate the microstructural data. Having personally worked in hardmetals, I can somewhat appreciate the tedious nature of the project. Even amidst his struggles to align his results with existing theories, Strauss, in his characteristic manner, managed to find some humour.
Dr Fritz Lenel (1907–2003), a giant in the Powder Metallurgy field, once told Strauss, “I have been working with these LS&W (Lenel, Smith & Wulff) theories for thirty years and they just do not work.” Similarly, M. Barsoum, in his book Fundamentals of Ceramics (McGraw-Hill), observed that “all sintering data can be made to fit all sintering models.” These remarks reflect the longstanding challenges and debates surrounding the theoretical modelling of sintering – a reminder that practical understanding often outpaces the predictive power of existing models.
Strauss had already completed his PhD in carbides, but by that time, he had been captivated by the allure of Powder Injection Moulding. In 1986, Prof German and two other professors established the first PIM consortium at RPI. This consortium was named Advanced Powder Processing (APP), where several
students and postdocs (including yours truly) had their first exposure to MIM. Strauss, who was almost a wizard when it came to equipment, got pulled entirely into this emerging field.
He established his own company, which he named HJE (which is still in operation today). When Strauss first formed his company, he intended to sell small custom atomisers and, to increase sales, developed MIM for precious metals. As precious metal powders could be processed efficiently using the HJE atomisers, it was hoped that jewellery companies would utilise MIM and require an atomiser. Many HJE atomisers have been sold to produce precious metal powders for MIM and are now also being used for AM-grade powder.
His early advertising stated that HJE offered fully integrated mini-MIM services, including prototype mould manufacturing and in-house gas and water atomisation for special alloys. The small atomisers subsequently became a significant part of his business, as illustrated in the advertisement by HJE shown in Fig. 50.
Before long, Strauss was producing some fascinating and innovative PIM parts, especially helping folks in the jewellery area. Some of the parts made by HJE are illustrated in Fig. 51. Shortly thereafter, Strauss began to experiment with some novel ideas, such as developing concepts for hollow jewellery parts (Fig. 52).
Fig. 53 Shows a MIM mould (left), the green bodies after injection (centre) and the finished 50Pt-50Rh watch case after sintering (right) (Courtesy C.HAFNER GmbH + Co. KG; from Laag, T. & Heinrich, J., Advantages and Challenges of Platinum Group Metals Powder Processing, SFS 2018) [10]
He explored two different strategies for hollow jewellery (as shown in Fig. 52): (1) building soluble cores on which he overmoulded the actual PIM part and subsequently washed out the cores and (2) the concept of sinter-bonded MIM. The use of platinum group alloys has also been explored, and Fig. 53 shows a 50Pt–50Rh watch case and its manufacturing process.
Strauss concluded the presentation by stating that MIM research was more enjoyable and rewarding than carbide research. He leveraged his MIM experience to introduce the technology into fresh areas, such as precious metals for dental use, jewellery, and watches, as well as new materials. He noted that MIM is gradually gaining traction in jewellery and watches. He has also applied his precious metal MIM experience to sinter-based AM.
Fig. 54 Variation of mechanical properties with density (Source: Höganäs Handbook 3, 2013) [10]
The presentation ‘Press-and-Sinter Parts Using MIM Powders’ was by one of Prof German’s early PhD graduate students, Prof KuenShyang Hwang (also known as KS) from HPM Labs, alongside co-author Yang-Liang Fan from United Powder Technologies. Prof Hwang travelled all the way from Taiwan to attend the celebration of Prof German’s career.
This was an intriguing presentation in which the researchers used MIM powders to achieve high-performance, high-density press and sintered (HPM) parts. Prof Hwang pointed out that as the sintered density increases, so do all the mechanical properties. Fig. 54 shows a schematic of the changes in mechanical properties with density. Here, there are three distinct zones (1, 2, and 3), represented as follows: Zone 1, Conventional PM; Zone 2, Warm Compaction + High Temp, Sintering; Zone 3, HPM and MIM.
Prof Hwang faced the question of how to improve the density and properties. There are really
three ways to achieve this: high compressibility powders, warm compaction, warm die compaction, and high-temperature sintering. As the sintered density increases, the next question that arises is how the pore size and shape affect the properties, though we know that fine powders tend to perform better.
Fig. 55 shows a schematic of the differences in powder size when using regular press and sinter compared to high-performance/ high-density or MIM, which results in shorter diffusion distances.
Fig. 56 shows the differences in homogeneity between the PM process of Distaloy processed by warm compaction followed by sintering at 1,150°C and HPM/ MIM of modified Fe-6Ni. Prof Hwang’s process takes just two hours, compared to 1.4 years for the conventional press-and-sinter method using powders with a diameter of 95 µ m.
Fig. 55 Differences in powder size when using regular Press and Sinter versus High Performance/High Density or MIM (resulting in shorter diffusion distances) [10]
“Prof Hwang’s process takes just two hours, compared to 1.4 years for the conventional press-andsinter method using powders with a diameter of 95 µm.”
PM (Distaloy® AE/FD-0405 warm compaction +1,150°C sintering
Density = 7.5 g/cm 3
HPM/MIM (modified Fe-6Ni)
Density = 7.5 g/cm 3
How about homogeneity of Ni/Cu/Cr/Mo?
Fig. 56 Differences in homogeneity between the PM process (Distaloy, warm compacted and sintered at 1,150 °C) and HPM/MIM (modified Fe-6Ni). Homogenisation is significantly improved in the HPM/MIM process due to the use of finer powders and a higher sintering temperature [10]
Sintering temp 1,250-1,350°C
HPM using MIM powder
Granulation
D50 = 50~100 µm
(µm)
Raw 316L Powders
Granulated 316L Powders
2015 6 s + 4.1 mm thick
W-4Ni-2Cu
2018~2020 iPhone 10~12
1.3~20.0mm thick
W-2.5Ni-1.5Fe
Spherical RTP powder
(µm)
Fig. 57 illustrates the processing scheme for converting fine MIM powders into large, flowable powders through the spray drying process, making them suitable for HPM. The spray-dried powder has a D50 value ranging from 50-100 µ m. The powder is spherical and flows easily into die cavities, enabling the use of fine powders that would otherwise be non-flowable.
Fig. 58 shows the powder particle size distribution (PSD) before and after spray drying using 17-4 PH and 316L MIM powders (note that the spray-dried powder size becomes coarser and has a narrower distribution). The ready-to-press (RTP) powders are not new; they have been utilised previously to create powders of WC, Mo, ferrites, and W-Ni-Fe and W-Ni-Cu heavy alloy compositions. However, with the availability and reduced cost of fine MIM powders, RTP powders for HPM are becoming a reality.
Fig. 59 shows parts manufactured from W-2.5Ni-1.5Fe material, which is used to produce iPhone components through the RTP powder in the HPM process.
Fig. 60 illustrates a comparison between a part produced using MIM and one made via HPM. It is noteworthy that the HPM process achieves a 30% reduction in cost, an 80% decrease in tooling expenses, and similar daily capacity to MIM.
pusher furnace 1350~1450°C
material for iPhone components, produced using RTP powder in the HPM process [10]
Table 5 compares HPM, MIM, and conventional press and sinter processes. Prof Hwang also highlighted several challenges associated with the HPM process, including dimensional control due to ‘medium’ (~7%) amounts of shrinkage during sintering, uneven green density, compressibility of RTP powders, and 3D shapes.
The last paper in the series of presentations honouring Prof German’s legacy was aptly delivered by Stefan Joens, president and owner of Elnik Systems GmbH, and DSH. Joens
currently serves as president of the Metal Injection Moulding Association (MIMA). His presentation was entitled ‘Advancements in Furnace Technology: Then, Now, and What May the Future Hold.’ For all PM processes, sintering is what allows the process to function. Almost all PIM/MIM and sinter-based AM processes depend on furnaces for the final consolidation step, which is responsible for the densification and attainment of the final part properties.
History and challenges of thermal debinding
Joens began his presentation by discussing the history of debinding. Early developments in Metal Injection Moulding, he stated, were entirely reliant on thermal debinding. Typically, the first stage of debinding was used to remove paraffin wax, while the second stage of debinding was used to remove the polyethylene or polypropylene type of organic polymers. Typical heating rates used were in the range of 1-5°C per minute (especially slow during the first part of debinding. The main goal was to remove the organics and pre-sinter the parts. All thermal debinding processes were relatively simple and had a low set-up cost. However, the process was quite long, often requiring 30-70 h, along with the potential for blistering, cracking, carbon entrapment, and lack of process uniformity due to varying load size. The typical part size was small.
Joens pointed out that pure thermal debinding and pre-sintering took a very long time and resulted in several defects (summarised in Fig. 61). He then moved into the history of solvent debinding, which was initially started by Raymond E Wiech, Jr (one of the original co-founders of Parmatech). He developed the process in the 1970s based on work performed by PO Gibrovsky on the hot casting of ceramics using pressure, with the wax-based binder being removed by solvent.
15.6 x 5.3 x 8.5 mm
Sample submission 21+7 days 14+5 days
Daily capacity 19 k/day 18 k/day
Fig. 60 Comparison of a part produced using the MIM process and the HPM process. The HPM process demonstrates a 30% cost reduction, 80% reduction in tooling cost, and a comparable daily production capacity to MIM [11]
Table 5 Comparison between HPM, MIM, and regular press and sinter processes [11]
30-60 h process time
• Additional furnace need
• Blistering
• Cracking
• Binder build up inside debind/pre-sinter furnace
Fig. 61 Shows a graphical time (hours) – temperature curves for thermal debind and pre-sintering [11]
“By the 1990s, MIM started to be regarded as a reliable technology for part production. The late 1990s and early 2000s saw the introduction of catalytic debinding, spearheaded by BASF with its Catamold process launched in 2002.”
• The CM Penn Stater Vacuum potential
• Hydrogen potential Allowed for better experimentation in MIM part processing
• More equipment functionality
the thermal debinding and sintering operation in the same run.Around 1993–1994, both Prof German on the academic side and I (then working for Parmatech) from industry independently spoke to Claus Joens (Stefan’s father), urging him to build a furnace capable of performing both debinding and sintering in a single run. Claus listened and acted, ultimately manufacturing the current debind-sinter batch furnaces that are now ubiquitous within the MIM and sinter-based AM industries.
• Significantly reduced process time 3 days to 1.5 days
• Gas flow to help debind Binder trap
Fig. 63 Schematic time–temperature graph showing thermal debinding and sintering in the same cycle (light green line). The figure also highlights the advantages of this process and an early furnace capable of performing this cycle [11]
Prior to this, parts had to be thermally debound either with or without solvent, after which the parts needed to be taken out of the furnace, restaged and introduced into a separate sintering furnace. Fig. 63 shows the schematic timetemperature graph that includes the thermal debinding and sintering in the same cycle (shown in the light green line). The figure also outlines the advantages of this process and shows an early furnace capable of carrying out this type of run.
In the 1980s, the solvent debinding process began to be adopted as the method for making MIM parts. By the 1990s, MIM started to be regarded as a reliable technology for part production. The late 1990s and early 2000s saw the introduction of catalytic debinding, spearheaded by BASF with its Catamold process launched in 2002. This process exhibited good green part strength and reduced processing time.
Furnace manufacturers such as CM Furnaces, Elnik Systems, and Cremer Thermoprozessanlagen began to adapt to both the catalytic debinding process along with solvent debinding processes.
At this point, Joens switched to discussions on debinding and sintering. He pointed out that experiments into debinding and sintering were started with the CM Penn Stater (a tube furnace), which had the potential to use vacuum as well as various gases, including hydrogen. This development, led by Prof German, allowed for better experimentation in MIM part processing and more equipment functionality. A picture of the tube furnace by CM is shown in Fig. 62.
However, there were no industrial furnaces that could carry out
Further developments were made based on this concept. Fig. 64 shows the retorts of various debind and sinter furnaces made by different manufacturers, including larger-sized furnaces, smaller box furnaces, and bottom-loading furnaces. As MIM volumes started to grow, there was a need for continuous furnaces in the case of high-volume manufacturing of MIM parts.
Stefan Joens also went on to reflect on the progress made in furnace technology over the past twenty years. He noted a number of key advancements that have helped shape the current state of the industry, including a shift towards automated functionality to enable more lights-out operations and improvements in recipe development systems that allow for greater precision and repeatability. Binder trap designs have been enhanced, and better integration between equipment (e.g. racking systems) has contributed to a more streamlined production flow.
• The benefits of directed gas flow over parts helped to reduce binder removal and improve process control
• Dramatically helped to reduce process debind time
• Adopted philosophy across all mainstream debind and sinter furnaces
He also noted how distribution has been optimised to improve debinding performance and ensure more uniform low-temperature environments, while temperature control, monitoring, and feedback systems have become increasingly sophisticated. Advances in hydrogen safety management have further strengthened the reliability of furnace operations.
Process volumes have grown across both batch and continuous systems, and the choice of process gases has evolved, with argon now preferred over high vacuum for titanium processing. At the same time, materials used in hot zones and retorts have improved, contributing to greater durability and performance. Efforts to simplify maintenance and service have made the systems more user-friendly.
Joens also shared his vision for the future of furnace development, including improvements in temperature uniformity, better power management, and reduced energy consumption. He stressed the ongoing integration of Industry
4.0 technologies, such as smart controls for process deviation bands, enhanced thermocouple design and extended sensor lifespan. He also noted the development of large, allmetal furnaces equipped with robust retorts, underscoring the scale and ambition of today’s MIM and sinterbased AM operations.
Traceability was another primary focus, including for components inside the furnace, the recipe, actual run, and process data. Joens also pointed to the growing role of AI in managing furnace data analytics, helping to create smarter, more adaptive systems.
He noted the need for R&D furnaces designed to support more straightforward scale-up of sintering recipes. Other areas for improvement include user experience (UX), as well as continued development of catalytic and solvent debinding processes and equipment.
In the end, Joens highlighted Prof German’s role and significant influence on the development of MIM and Powder Metallurgy in general. He expressed gratitude to Prof German on behalf of MIMA and MPIF for his contributions to advancing the PM industry.
I would like to extend my gratitude to Prof German not only for his contributions to MIM, PM, and sintering, but also for the influence he has had on my own life. My collaboration with Rand continued even after he left Rand’s Lab in 1989. I spent several years discussing the idea of an event to celebrate his long legacy with Jim Adams, CEO of MPIF. I am pleased that Jim recognised the opportunity and supported the idea, making it possible to bring this programme to life alongside MIM2025.
My heartfelt thanks to everyone who answered the call and travelled from around the world to take part in this celebration. Your enthusiasm and commitment made this gathering possible. In this article, I have briefly summarised the presentations that were directly inspired by Prof German, whether through his research, teaching, or mentorship. I’ve also tried, where appropriate, to reflect the personal relationships many of you have shared with him. I extend a heartfelt thank you to the MPIF team for their exceptional support during the planning and execution of this event. On behalf of
my co-organisers, John Johnson and Sundar Atre, I would especially like to thank Jim Adams, Bill Edwards, Paul Sedor, and Diane Haggerty for their presence and tireless efforts throughout the conference. I am also grateful to all contributing authors for their assistance with the figures and tables included here, and to Nick Williams for the invitation to document this special programme for PIM International
This may also be a good opportunity to share two additional photographs of some of the individuals who participated in and presented at the MIM2025 Conference, which celebrated Prof German’s remarkable career and impact.
At the end of the programme, Rand was invited to say a few words. Understandably emotional, he expressed his sincere thanks to MPIF and to everyone who attended. It was a poignant moment for Rand and for all of us whose lives he has touched
both professionally and personally. We wish him and his family the very best for the years ahead.
Prof German holds an honorary doctorate from the University Carlos III de Madrid and is a Fellow of three professional organisations. Over the course of a distinguished academic career spanning more than four decades, he has received numerous awards and accolades.
Since beginning his career in 1980 at Rensselaer Polytechnic Institute (RPI), Rand has held academic positions at several institutions, including The Pennsylvania State University and San Diego State University. He has secured more than £60 million in research funding, supervised over one hundred doctoral theses and two hundred post-doctoral researchers, and has co-chaired more than thirty conferences.
His scholarly output includes more than one thousand published articles, twenty-five patents, and twenty-one books, several of which are highly cited. With a current h-index of seventy-one and over thirty-six thousand citations, Rand’s contributions to the scientific community are both prolific and influential.
Dr Animesh Bose Shaping Innovations, Inc. Global PM Consultant (PIM, sinter-based AM, novel PM materials and processes) Leesburg, VA, USA animeshbose53@gmail.com
Dr Bose has over forty years of experience in Powder Metallurgy and particulate materials. He holds twenty patents, authored/ co-authored four textbooks, and published over 150 papers. A
Fellow of ASM International and APMI International, he co-organises international conferences and serves on the editorial boards of two prominent journals in Powder Metallurgy and hard materials.
References
[1] Animesh Bose, FAPMI and FASM, ‘Low-Pressure Powder Injection Moulding (LP-PIM) of Metals and Ceramics’, as presented at MIM2025, 25 Feb 2025
[2] José M Torralba, ‘Synergising Metal Injection Molding and Materials Extrusion: Enhancing Manufacturing Flexibility and Performance’, as presented at MIM2025, 25 Feb 2025
[3] Matthew Bulger, ATPM Consulting, ‘Particle Size Effects in MIM’, as presented at MIM2025, 25 Feb 2025
[4] Gemma Herranz Sánchez-Cosgalla, University of Castilla-La Mancha (UCLM), ‘From CISP to DYPAM &
BLESOL TECH: The Journey of MIM from Spain’s First Doctoral Thesis to Industrial Innovation’, as presented at MIM2025, 25 Feb 2025
[5] Pavan Suri, HP, in collaboration with Ravi Mayavaram and Narendra Singh, Altair, ‘Automatic Shape Compensation for Shrinkage During Binder Jet Sintering Process’, jointly presented by Drs Suri and Singh, as presented at MIM2025, 26 Feb 2025
[6] T S Shivashankar, INDO-MIM, ‘Sintering Studies Inspired by RMG’, as presented at MIM2025, 26 Feb 2025
[7] John L Johnson, FAPMI, Novamet/Ultra Fine Speciality Products, ‘Powder Injection Moulding of Thermal Management Materials’, as presented at MIM2025, 26 Feb 2025
[8] Hideshi Miura, FAPMI, Kyushu University, ‘Development of Innovative Ti Alloy through MIM’, as presented at MIM2025, 26 Feb 2025
[9] Joseph Strauss, FAPMI, HJE Company, Inc., ‘Microstructural Evolution of WC/Co Alloys with V Additions’, as presented at MIM2025, 26 Feb 2025
[10] Kuen-Shyang Hwang, National Taiwan University, ‘Pressed-andSintered Parts with MIM Powders’, as presented at MIM2025, 26 Feb 2025
[11] Stefan Joens, Elnik Systems GmbH and DSH, and president of the Metal Injection Moulding Association (MIMA), ‘Advancements in Furnace Technology: Then, Now, and What May the Future Hold’, as presented at MIM2025, 26 Feb 2025
and
Foshan
Qness GmbH - Verder Group 28 www.qatm.com | www.verder-scientific.com ELTRA GmbH - Verder Group 28 www.qatm.com | www.verder-scientific.com
Microtrac Retsch GmbH - Verder Group 28 www.microtrac.com | www.verder-scientific.com
AG
www.erowa.com
Newsletter subscribers also benefit from a free digital subscription to Metal Powder Technology magazine.
PIM International is dedicated to driving awareness and development of the MIM, CIM and sinter-based AM industries and their related technologies. Key to this aim is our support of a range of international partner conferences.
View our complete events listing on: www.pim-international.com
EPMA PM Summer School 2025
June 22–27 - Lund, Sweden summerschool.epma.com
Ceramic AM Summit
June 30 –July 2 - Berlin, Germany www.amsummit.dkg.de
Battery Cells & Systems Expo
July 9–10 - Birmingham, United Kingdom batterysystemsexpo.com
The Advanced Ceramics Show
July 9–10 - Birmingham, United Kingdom www.advancedceramicsshow.com
The Advanced Materials Show
July 9–10 - Birmingham, United Kingdom www.advancedmaterialsshow.com
Formnext Asia Shenzhen
August 26–28 - Shenzhen, China formnext-sz.hk.messefrankfurt.com/shenzhen/ en.html
The Vicenza Symposium for Jewellery Technology & Fashion Makers
September 2–4 - Vicenza, Italy thevicenzasymposium.com
Euro PM2025 Congress & Exhibition
September 14–17 - Glasgow, Scotland www.europm2025.com
T.I.C.’s 66th General Assembly 2025
September 14–17 - Cape Town, South Africa www.mmta.co.uk/ event/t-i-c-s-66th-general-assembly-2025/
The European Additive Manufacturing Congress 2025
September 14–17 - Glasgow, Scotland www.euroam2025.com
Course on Atomisation for Metal Powders
September 18–19 - Glasgow, Scotland www.irp.cdn-website.com/25ba6e5f/files/ uploaded/2025_Press_Release_Website.pdf
Formnext Asia Tokyo Forum 2025
September 25–26 - Tokyo, Japan formnextforum.jp.messefrankfurt.com/tokyo/ en.html
The Advanced Materials Show USA
Sept. 30 – Oct. 1 - Columbus, OH, United States www.advancedmaterialsshowusa.com
Ceramitec USA Pavilion
Sept. 30 – Oct. 1 - Columbus, OH, United States www.ceramitec.com/en/usa/
ICAM25 International Conference on Advanced Manufacturing
October 6–10 - Las Vegas, NV, United States www.amcoe.org/event/icam2025/
Fraunhofer IFAM 6 th Workshop on Sinterbased Additive Manufacturing October 8–9 - Bremen, Germany www.ifam.fraunhofer.de/en/Events/sinterbased-additive-manufacturing-workshop2025.html
If you would like to see your CIM, MIM or sinterbased AM related event listed in this magazine and on our websites, please contact Merryl Le Roux: merryl@inovar-communications.com
EPMA – Use of Powder Metallurgy Technologies in Medical
October 14–15 - Saint-Etienne, France seminars.epma.com/event/use-of-powdermetallurgy-technologies-in-medical/
ASEAN Ceramics
October 15–17 - Bangkok, Thailand www.aseanceramics.com/thailand
APMA 2025 7 th International Conference on Powder Metallurgy in Asia
October 19–22 - Qingdao , China apma2025.scimeeting.cn
AM Ceramics 2025
October 21–22 - Vienna, Austria www.amceramics.cc
Advanced Engineering
October 29–30 - Birmingham, United Kingdom www.advancedengineeringuk.com
Formnext 2025
November 18–21 - Frankfurt, Germany www.formnext.com
MIM2026 – International Conference on Injection Molding of Metals, Ceramics and Carbides
February 23–25 - Jacksonville, FL, United States www.mim2026.org
AMUG 2026
March 15–19 - Reno, NV, United States www.amug.com
Ceramitec 2026
March 24–26 - Munich, Germany www.ceramitec.com
PM China 2026
March 24–26 - Shanghai, China en.pmexchina.com
RAPID + TCT 2026
April 14–16 - Boston, MA, United States www.rapid3devent.com
WorldPM2026
June 25–29 - Montreal, Canada www.worldpm2026.org
If you would like to see your CIM, MIM or sinter-based AM related event listed in this magazine and on our websites, please contact Merryl Le Roux: merryl@inovar-communications.com
As the usage patterns of PIM International magazine’s audience develop and change, we have expanded our social media activities, enabling us to connect with our global audience on multiple levels.
As the only magazine for MIM, CIM, and sinter-based AM, our LinkedIn, Twitter, and Facebook channels serve as indispensable sources for the latest industry news.
www.twitter.com/PIMMagazine
www.linkedin.com/company/piminternationalmagazine/
www.facebook.com/PIMInternationalmag
GLASGOW 14-17 SEPTEMBER 2025
CONGRESS & EXHIBITION
Congress:
Explore the latest advancements in Powder Metallurgy through expert presentations that shape the future of the industry.
Exhibition:
Discover cutting-edge PM solutions, connect with leading suppliers, and stay ahead of industry trends. Meet the EPMA’s European-wide network, as well as the UK Metal Powder industry.
CONSOLIDATION TECHNOLOGIES MATERIALS APPLICATIONS
TOOLS FOR IMPROVING PM POWDERS
Register today as a Delegate or Exhibitor