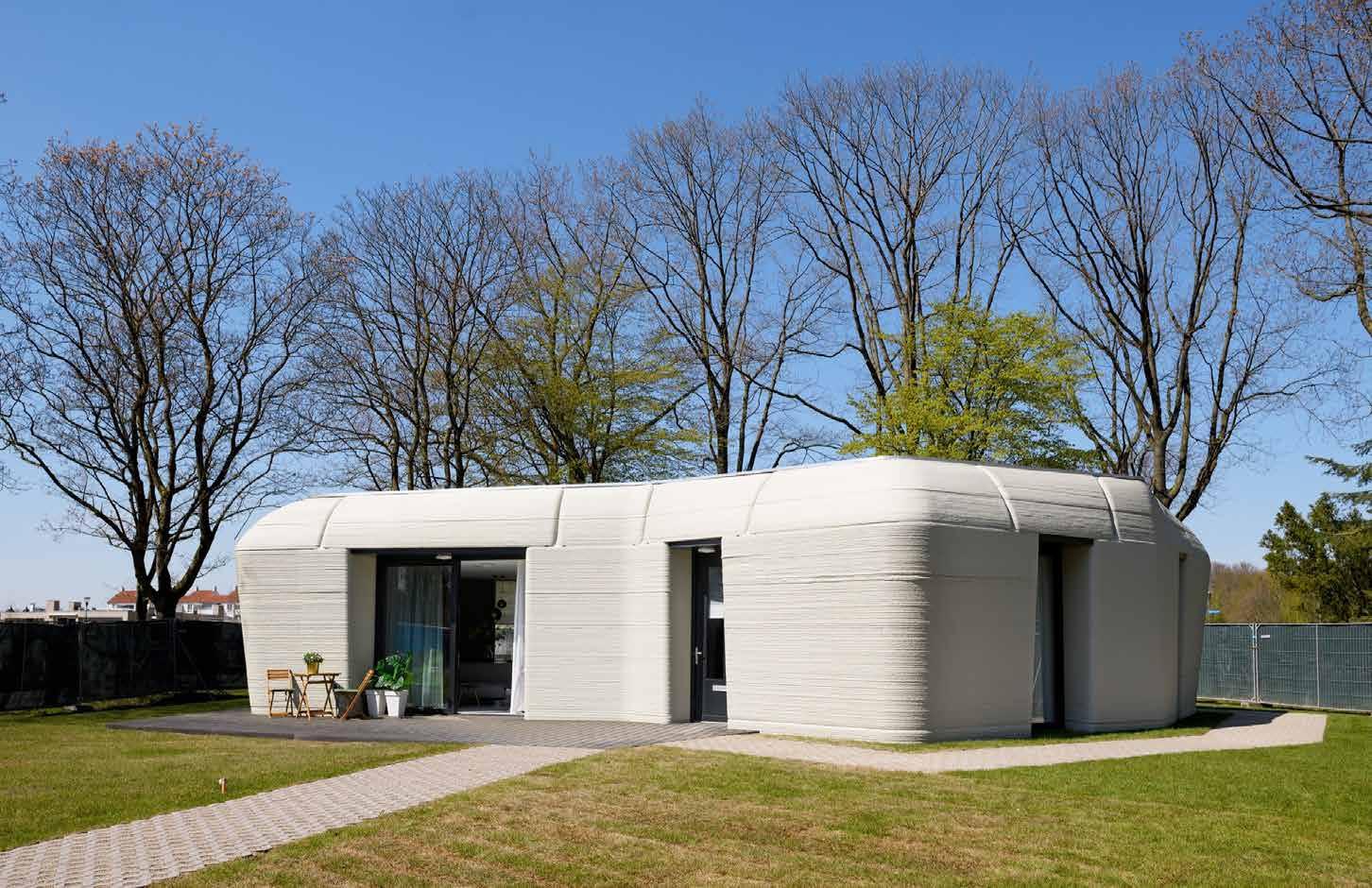
8 minute read
First 3D printed Milestone house
from IM20213EN
Photographie: Milestone/Houben/Van Mierlo architecten (A.I: YuconVR)
April 30, the first tenant of the first ever Dutch 3D-printed concrete home has received the key. The 3D printed house in Eindhoven - the first of five within ‘Project Milestone’ - fully complies with all of the strict building requirements of The Netherlands. Project Milestone is a joint construction and innovation project of Eindhoven University of Technology, Van Wijnen, Saint-Gobain Weber Beamix, Vesteda, the Municipality of Eindhoven and Witteveen+Bos. The group of TU/e professor Theo Salet is one of the driving forces of the project.
Advertisement
Eindhoven University of Technology started the 3D Concrete Printing (3DCP) research program in 2015. The goal of the program was to establish concrete printing as a viable new method to manufacture concrete elements and buildings, and to fundamentally understand its processes. The research group operates and develops its own 3D Concrete Printer at the Department of the Built Environment. The printer consists of a four axis gantry robot with a print bed of approximately 9.0x4.5x3 m3, coupled with a concrete mixing pump, both controlled by a numerical controller. The TU/e has found a group of contractors, building materials suppliers and engineering firms to finance and support the 3DCP program. However, he ambitions turned out to be higher. Fundamental research and
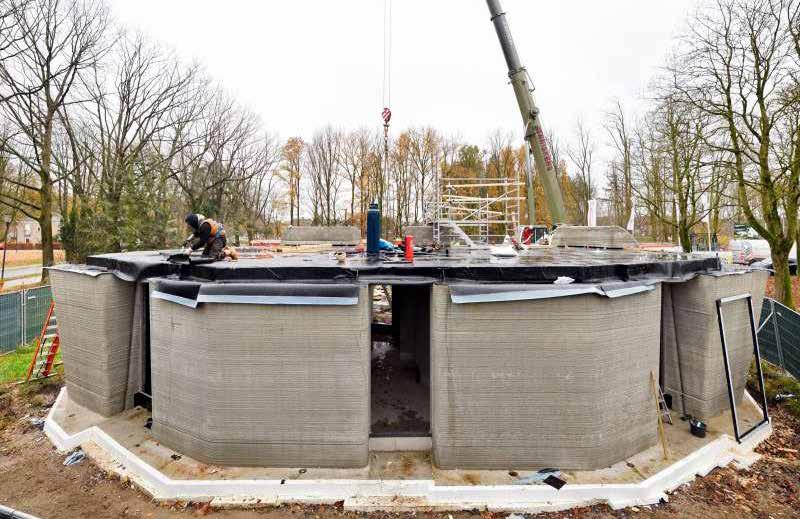
experimentation must lead to predictability of the behaviour of materials and equipment, in changing circumstances. With the ultimate goal that constructive elements and constructions are made in a responsible manner. This eventually led to the Milestone project, which will be used to build five 3D-printed concrete houses in the city of Eindhoven.
No experiment
Project Milestone can rightly be seen as a milestone for many reasons. Not only when it comes to the technology and the builders, but also with respect to design, the municipality, the future occupant and the landlord. Ultimately, the project will complete five houses, with both printing technology and home design becoming increasingly complex, as one is build after the other. If the ground floor is still being printed off-site, the two-storey fifth home will be manufactured entirely on-site. The development of the 3D concrete printing technique will therefore be beautifully visible. The project partners don’t consider it as an experiment, but as an extensive innovation that can be essential for the (residential) construction sector. After all, concrete is the most widely used building material in the world.
Advantages
According to the initiators, the advantages of 3D-printed houses are evident. For instance, the concrete printer has the option of laying concrete only where it is structurally needed. Traditional poured concrete is solid and contains much more concrete than is necessary structurally. More is used, which is bad for CO2 emissions, because a lot of this
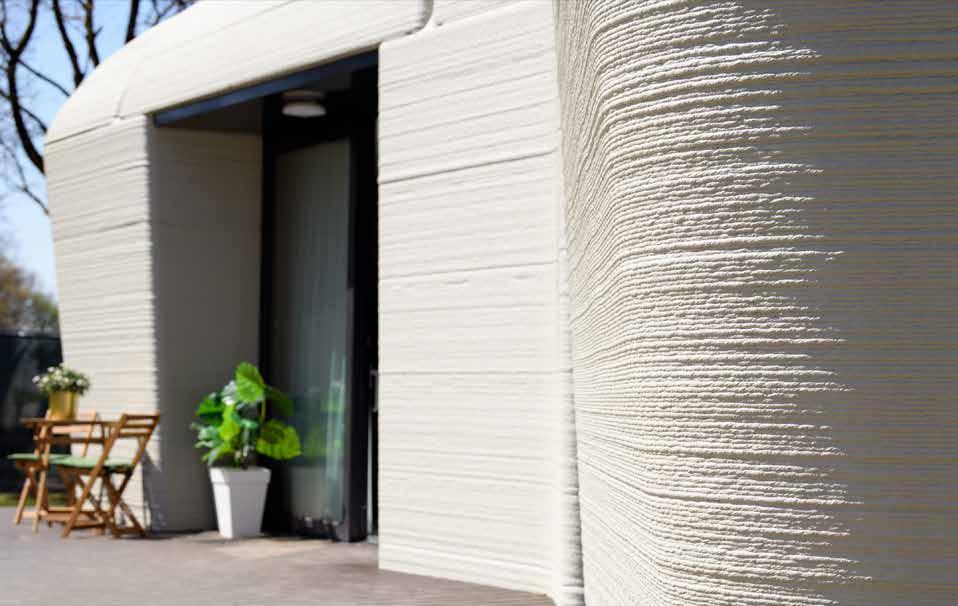
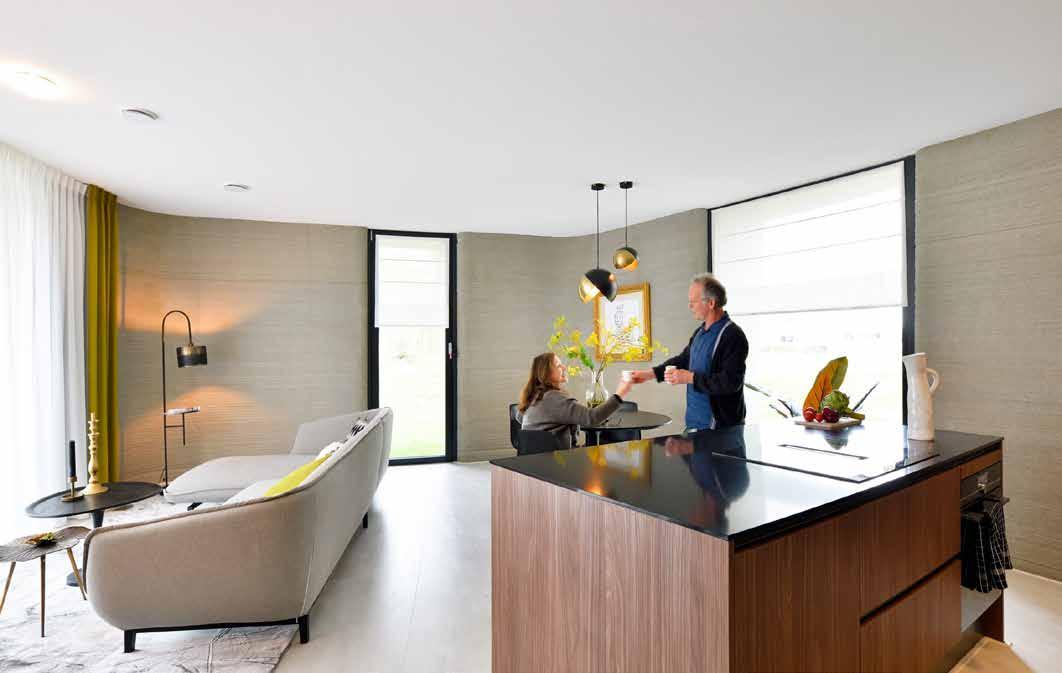
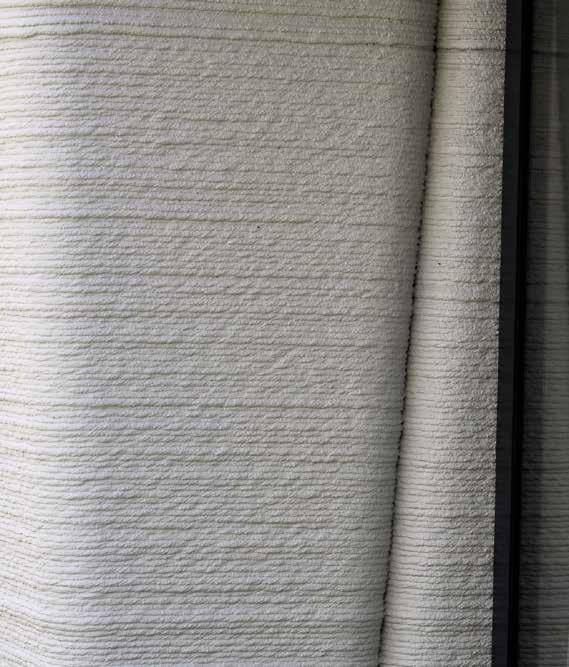
greenhouse gas is released during the production of cement. Furthermore, an important advantage is the freedom of design. Very detailed concrete constructions are possible with 3D concrete printing. In the traditional pouring of concrete, the formwork determines the shape of concrete. With concrete prints, builders will soon be able to make concrete details as small as a pea and round, concave or convex shapes. This makes concrete buildings and constructions with completely new shapes possible. A new option is the printing of different types, qualities and colours of concrete, all in one integrated product. This means that a complete wall can be printed with all the necessary functionalities. Such a wall must be reinforced with insulating wire fibres and kept dirt-repellent on the outside, and a layer on the inside that ensures pleasant acoustics. Additionally, it includes the required recesses and internal drainage pipes made of waterproof concrete. That makes the construction process much faster.
The 3D printing of concrete makes it possible to place sensors directly in the right place of the construction. Examples include wireless sensors that measure temperature, sensor-controlled lighting or those used for security. These can be processed directly in the printing process, instead of afterwards, which saves time and money.
Finally, concrete printing also has important advantages in terms of working conditions. Traditional concrete processing is heavy and demanding work. The vibrations of poured concrete and the braiding of the steel reinforcement meshes are heavy. These activities are not required with 3D-printed concrete.
TU Eindhoven/Milestone project>
Photography: Milestone/Houben/Van Mierlo architecten (A.I: YuconVR)
Video:
3DPC
3D Concrete Printing (3DCP) provides the potential to increase the productivity and reduce the environmental impact of the Architecture, Engineering and Construction (AEC) industry. The 3DCP research group adresses the scientific challenges to develop the technology towards structural applications of 3D printed concrete. The program is run by the chair of Concrete Structures of the Unit Structural Design, in close collaboration with the chair of Innovative Structural Design and chair of Architectural Design and Engineering. Within the 3DCP program, numerous PhD, MSc and other research projects is being conducted. The research activities are supported by industrial partners, a number private enterprises covering the whole production chain of concrete for construction. Their contribution and involvement is gratefully acknowledged: Ballast Nedam, BAM, Bekaert, Concrete Valley, CRH, CyBe, M-Tec, SGS Intron, Siemens, Verhoeven Timmerfabriek Nederland, Weber Beamix, Van Wijnen, Witteveen+Bos and stichting SKKB.
World first rechargeable cement-based batteries
Suppose the construction of an entire building could be used to store electricity. Researchers from the Department of Architecture and Civil Engineering, from Chalmers University of Technology, Sweden, recently published an article outlining a new concept for rechargeable batteries, made of cement. The concept involves first a cement-based mixture, with small amounts of short carbon fibres added to increase the conductivity and flexural toughness. Then, embedded within the mixture is a metal-coated carbon fibre mesh - iron for the anode, and nickel for the cathode.
Based on this concept, the researchers built a rechargeable cement-based battery with an average energy density of 7 Watthours per square metre (or 0.8 Watthours per litre). The energy density is low in comparison to commercial batteries, but this limitation could be overcome thanks to the huge volume at which the battery could be constructed when used in buildings.
The researchers tested several combinations for the electrodes, and found that an iron anode, and a nickel-based oxide cathode yielded the best results. The conductivity of the cement mixture was increased by adding short carbon fibers. Experiments showed that 0.5 percent carbon was optimal.
The possibilities seem to be limitless. The researchers see applications that could range from powering LEDs, providing 4G connections in remote areas, or cathodic protection against corrosion in concrete infrastructure. The system could also be used to supply electricity to monitoring systems on highways or bridges, where sensors operated by a concrete battery could detect cracking or corrosion. However, the idea of the cement battery is still at an early stage. Important technical issues need to be solved, such as extending battery life and developing recycling techniques. Since concrete infrastructure is usually built to last fifty or even a hundred years, the batteries would need to be refined to match this, or to be easier to exchange and recycle when their service life is over. For now, this offers a major challenge from a technical point of view.
More at Chalmers>
This work was done by Doctor Emma Zhang and professor Luping Tang, Chalmers University of Technology, Sweden. The results were published earlier this year in ‘Buildings’ titled ‘Rechargeable Concrete Battery’>
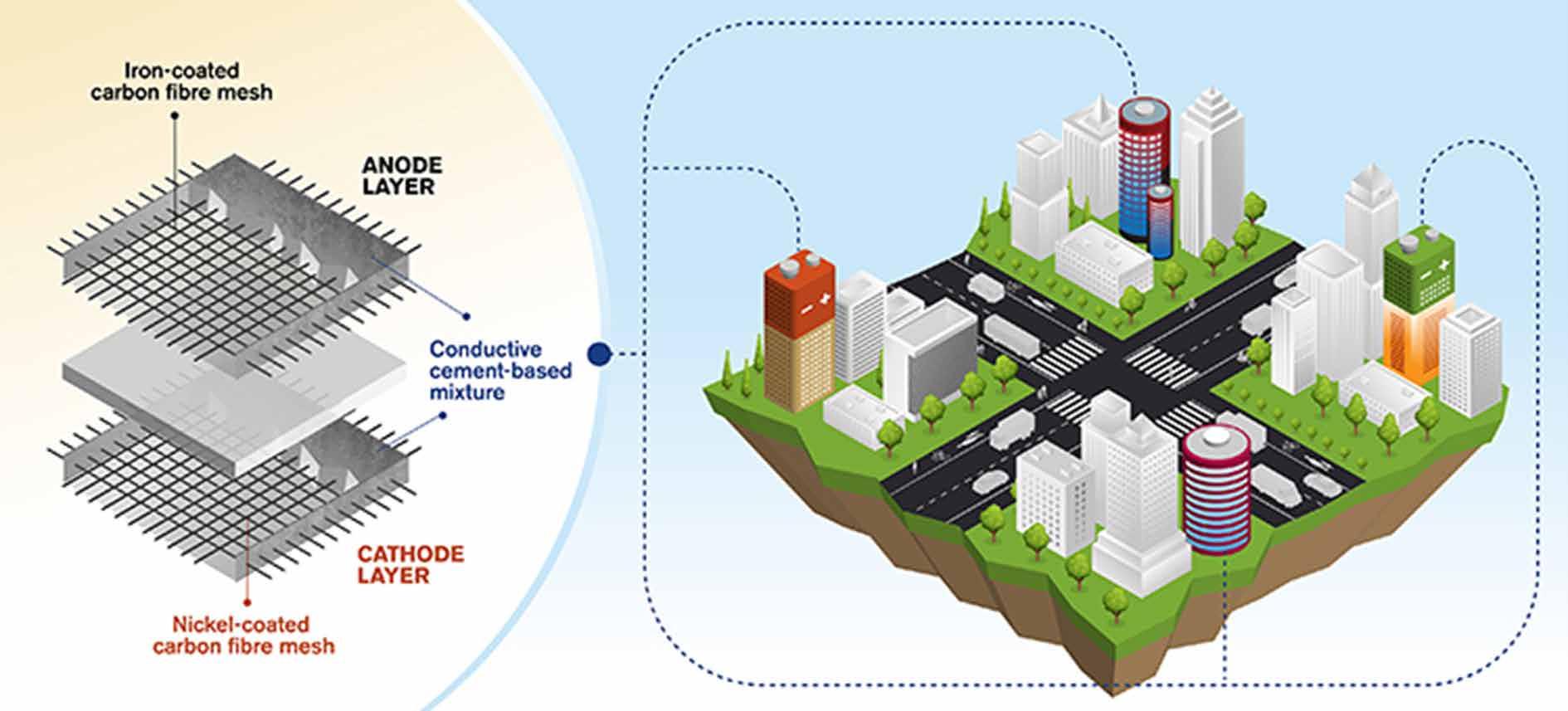
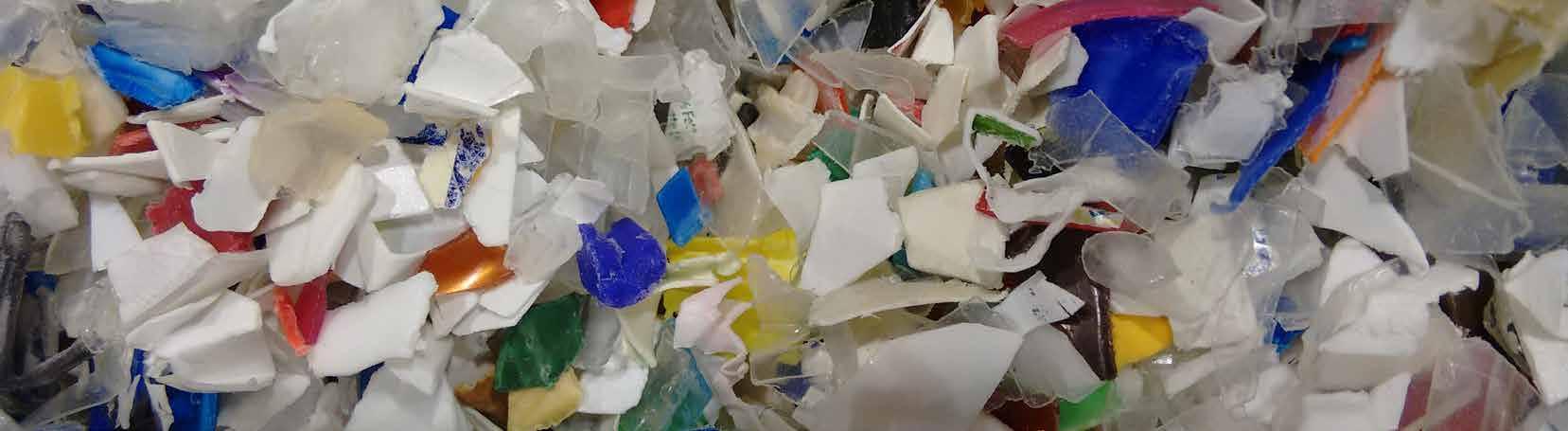
Recycled plastic in concrete
Plastic waste is a global problem. In a recent study, researchers in MSU’s Norm Asbjornson College of Engineering found that plastic treated with bacteria could be added to concrete in significant quantities without compromising the structural material’s strength. The study was published in the journal Materials in April.
Typically, adding plastic or other filler material disrupts the mix of sand, aggregate and cement that gives concrete its ability to bind together and support heavy loads. The MSU team discovered that certain bacteria can create a mineral coating around plastic particles, which makes plastic bond much better to cement. Concrete samples containing up to 5 % of the bacteria-treated plastic had virtually the same strength as traditional concrete, according to the study.
Because concrete is used so widely and in such high volumes, replacing even 5 % of it could result in massive reuse of plastic. And because concrete is so energy-intensive to make, the plastic filler could significantly reduce carbon dioxide emissions. According to U.S. Environmental Protection Agency, concrete production is one of the country’s largest industrial sources of the climate-altering gas.
In MSU’s Center for Biofilm Engineering, the researchers immersed the plastic in a water-based solution containing the harmless bacteria Sporosarcina pasteurii, which grows on surfaces to form what’s called biofilm. The microbes, left in the solution for 24 - 48 hours, consumed added calcium and urea to give the plastic a thin, white coating of calcite, the hard mineral that constitutes limestone. The plastic was then mixed into small concrete cylinders that were crushed with specialized equipment to measure their strength.
Although the researchers started with shredded plastic from disposable bottles, they achieved similar results with a mixture of packaging plastics, which is used in a variety of containers but isn’t accepted at most recycling facilities. The next step is to study the material’s long-term durability as well as how the process could be scaled up.
More at MSU>
The paper ‘Biomineralization of Plastic Waste to Improve the Strength of Plastic-Reinforced Cement Mortar‘ is online>
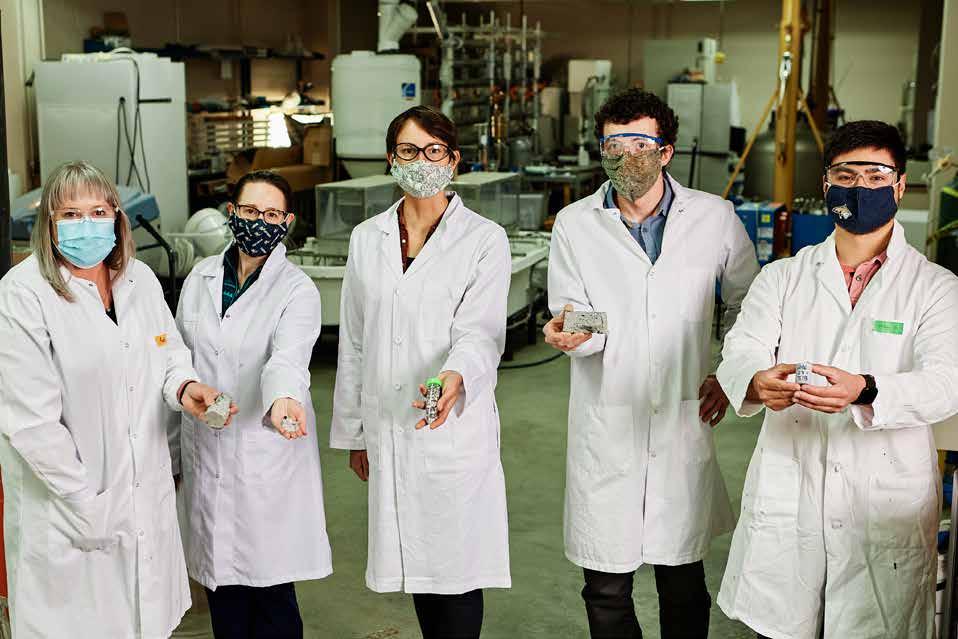