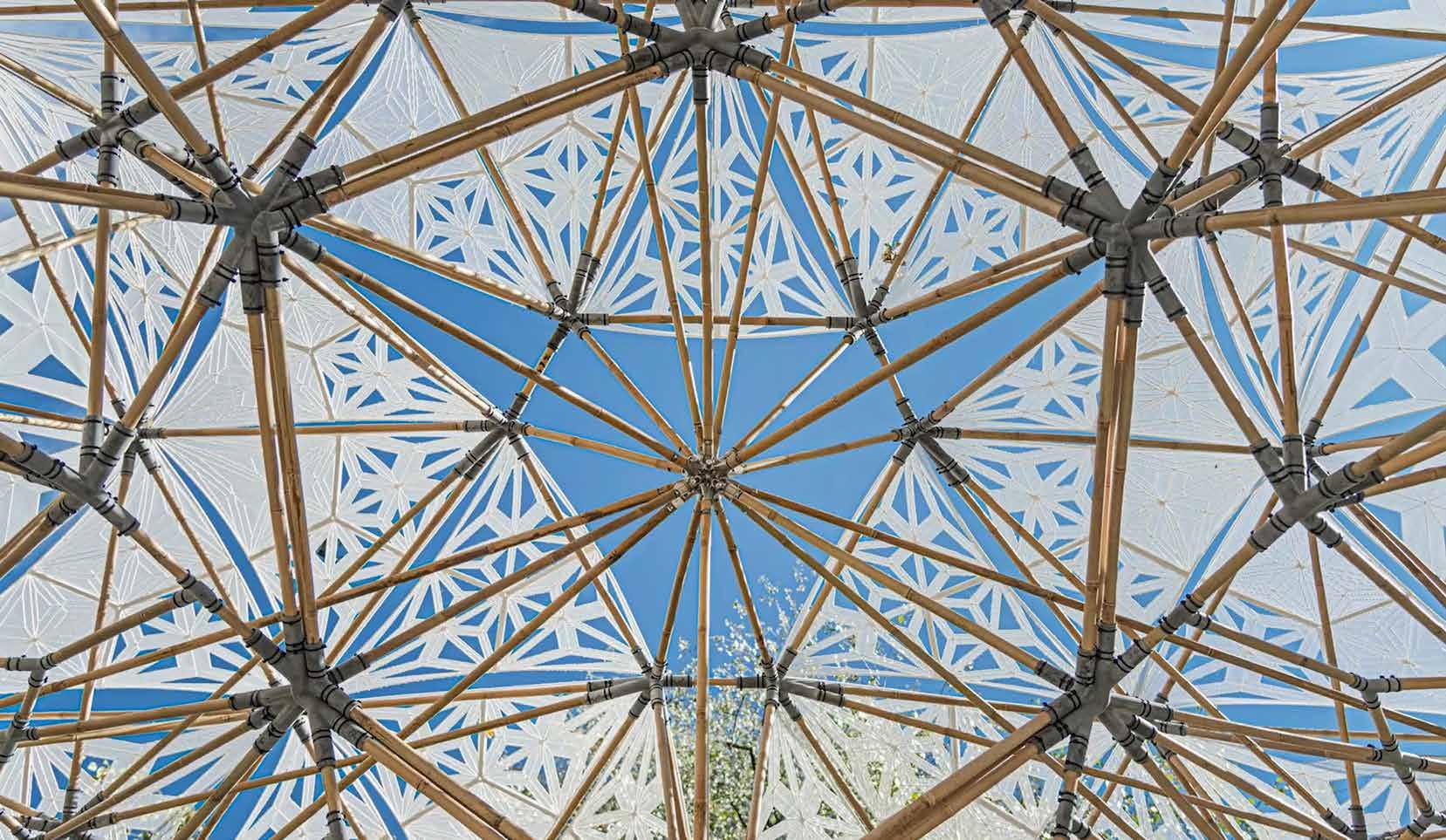
22 minute read
Digital Bamboo Pavilion
from IM20213EN
Students at ETH Zurich developed an extremely lightweight and filigree pavilion from bamboo, using innovative digital fabrication technology. The Digital Bamboo Pavilion explores the innovative combination of a naturally grown material with digital fabrication. Bamboo is an excellent sustainable building material, because of its rapid growth and very low weight-to-strength ratio. Customized computational tools were developed to design the ultra-lightweight structure, whose bespoke connections were manufactured using 3D printing technology. The structure covers more than 40 sqm with a total weight of only 200 kgs.
The pavilion’s solar shading panels are designed with a specially developed computer process and manufactured from a 3D-printed recyclable, UV-re-
Advertisement
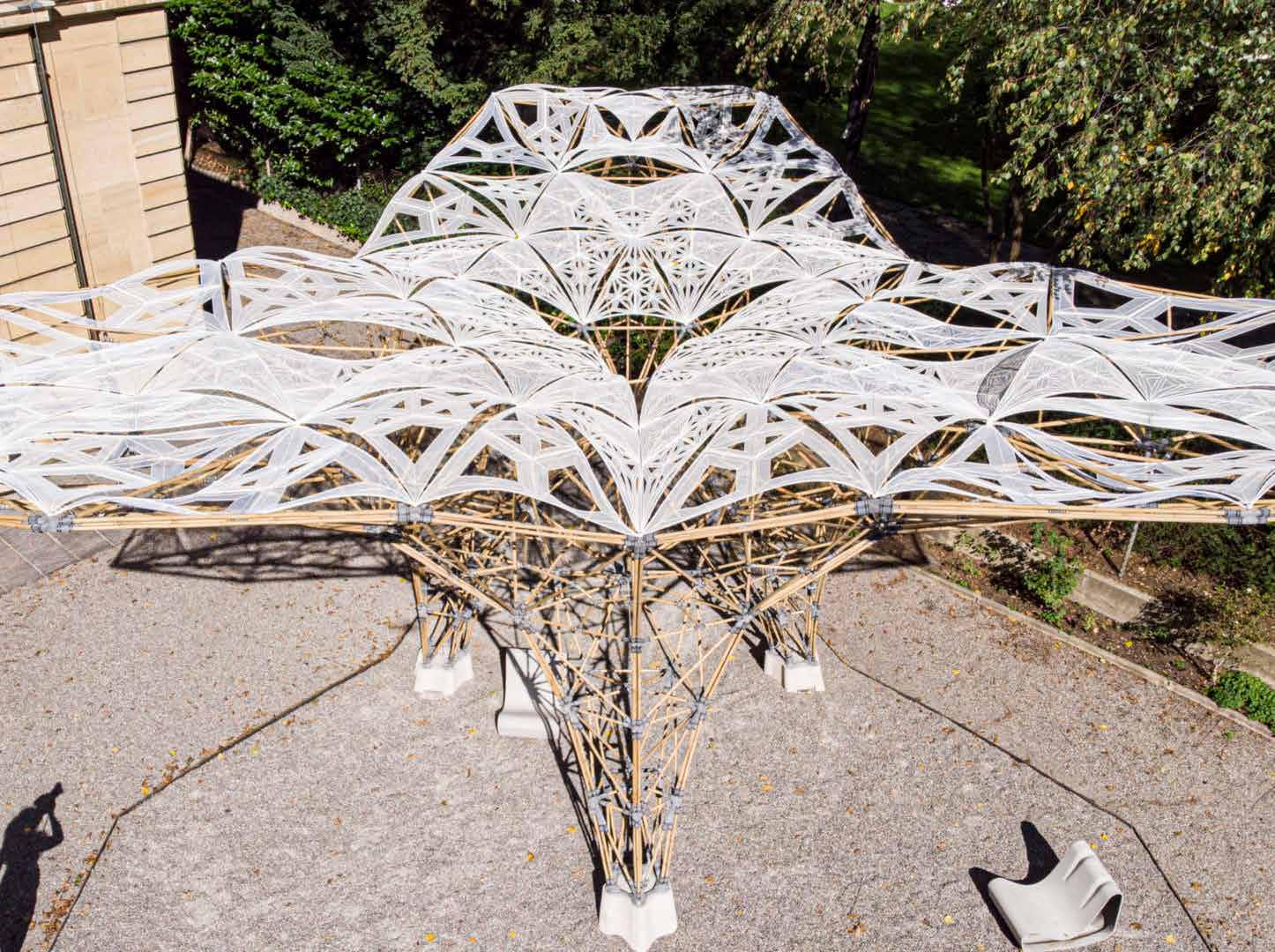

The connection at the center of the pavilion has a unique connecting system and is fabricated in stainless steel to meet the necessary mechanical requirements (Dinorah Martinez Schulte, dbt)
sistant thermoplastic on a lightweight Lycra textile. 3D printing strengthens and shapes the fabric into flexible custom panels. The composite elements are locally reinforced, so that less material is needed. The final construction is five meters high and made from more than 900 bamboo poles connected via digitally designed connections and manufactured in nylon and stainless steel to an accuracy of less than a millimetre. A total of 379 connections and a large number of small parts were used. The construction system developed for the Digital Bamboo Pavilion aims to reduce construction logistics efforts while harnessing the benefits of digital fabrication for a more sustainable building culture. Under the principle of distributed prefabrication, the complexity of the structure is encapsulated in small parts that can be made all over the world with a 3D printer. These custom parts can be used to build high quality structures together with local materials. Thanks to the modular design, the construction can be quickly assembled and disassembled. The premounted parts of the pavilion were assembled on site in just 48 hours. According to the developers of Digital Bamboo, the project is a good example of how digital fabrication can lead to a sustainable future in construction. New architectural concepts could be developed by combining locally produced materials with 3D printed parts.
The Digital Bamboo Pavilion is designed by students of the Master in Advanced Studies in Architecture and Digital Fabrication 2019-2020 at the ETH Zurich and is based on research at the chair of Digital Building Technologies.
ETHZ>
Photography: ETH Zürich
video
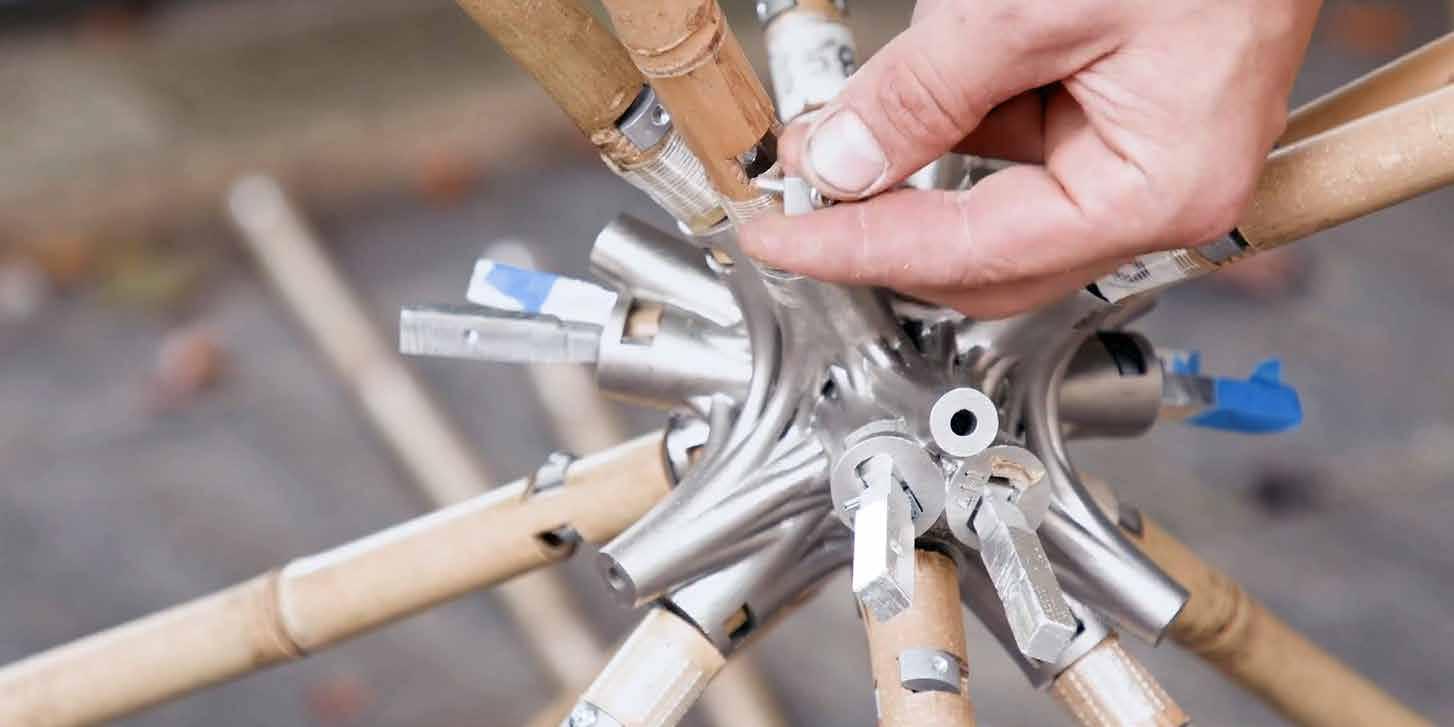
Liquid metal reactor walls
Extreme conditions exist in a fusion reactor and the reactor vessel wall must be able to withstand extreme heat. Many promising wall materials have been tested already and found to be inadequate. A wall made of liquid metals now seems to be the solution. DIFFER and Eindhoven University of Technology (TU/e) have received a NWO Investment Grant Large of 2,5 million euros to build a laboratory where the new technology can be investigated: the LiMeS lab.
In the future, nuclear fusion could be a sustainable and safe source of energy, but before we reach that stage, we still need to overcome several obstacles. Inside a fusion reactor, an immense amount of energy is generated in the form of heat. Ultimately, that energy needs to leave by passing through the wall. Tungsten is a heat-resistant metal that often serves as the wall material. However, even that material is not good enough despite a melting point of 3422 °C.
What is the point of a fusion reactor if the wall regularly fails? So, for several years, fusion research has been working on a new category of heat shield for the wall combining tungsten with liquid metal. After all, you cannot make a dent in a liquid, and neither can you fracture, break, or rupture it. Liquid wall materials are therefore seen as a solution to the ‘wall problem’. The reactor’s wall would then consist of a sponge-like structure made from tungsten containing the liquid metal.
DIFFER and TU/e have worked together for several years on this research, and they lead the way in this field. They are jointly developing a plan to construct a laboratory for this research in which materials and designs can be developed and tested: the LiMeS-Lab. This plan has now received financial support from NWO. The laboratory consists of two main components. A 3D printer will be constructed for the printing of tungsten and other materials. This a highly promising production method for the sponge-like structures required. It is a new technology. In addition, a large plasma setup will be constructed in which a prototype can be tested. Plasma will be fired at the prototype, and it will experience almost the same conditions as it would in an actual fusion reactor. Meanwhile, researchers will be able to observe how the components withstand the test. The 3D printer will be located in the Additive Manufacturing Lab of TU/e, and the plasma setup will be constructed at DIFFER. The equipment can also be used for other disciplines in which high temperatures play a role, such as for other energy sources, EUV lithography, and neutron sources.
The construction of the LiMeS laboratory is expected to be completed in 2024. The project will strengthen the intensive collaboration between TU/e and DIFFER in the area of fusion research.
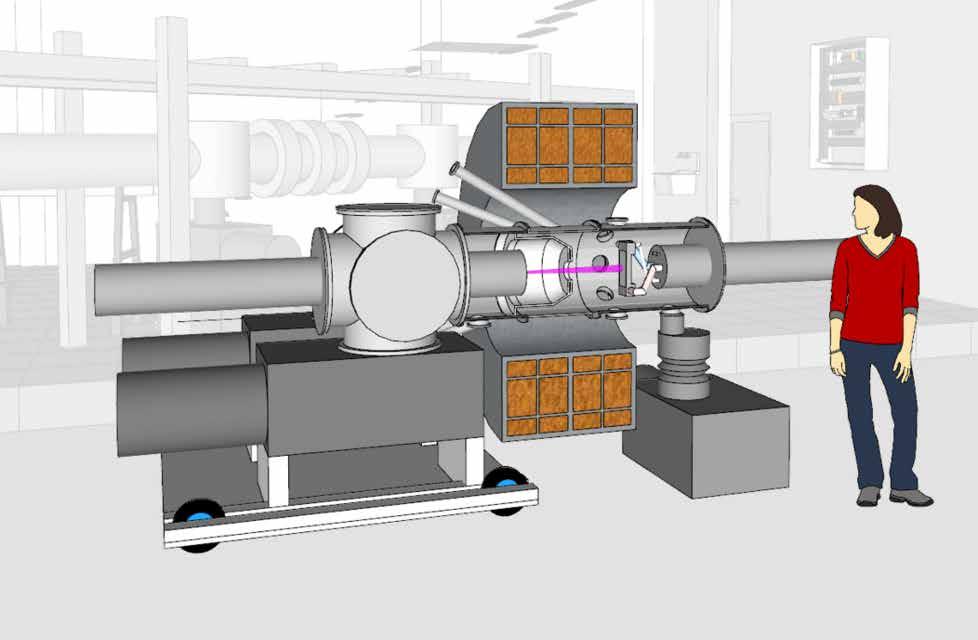

TU/e researcher Peter Rindt. Foto: Bart van Overbeeke
Text: TU/e>
Technieken voor o.a.:
- Ontstoffing van productieruimtes (MAC) - Reduceren van geuremissies (NER) - Reduceren van stofemissies (NER)
Componenten die wij o.a. kunnen leveren:
- Natfilters & Droogfilters - Cyclonen - Gaswassers - Topsteen- / Frogreinigers - Naverbranders

Projecten kunnen turn-key worden uitgevoerd Wij garanderen de emissie & grenswaarden Engineering, bouw en onderhoud in eigen beheer
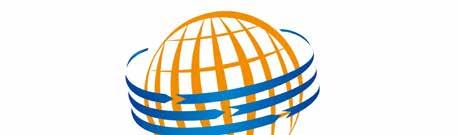
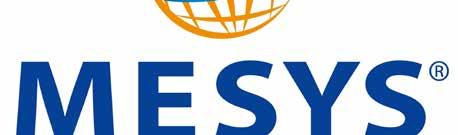

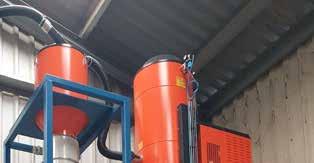
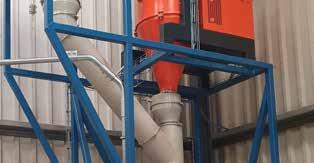


Hoog vacuüm stofzuiginstallatie Natfilter met slibtransporteur
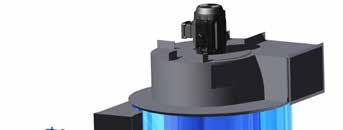
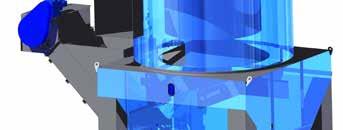
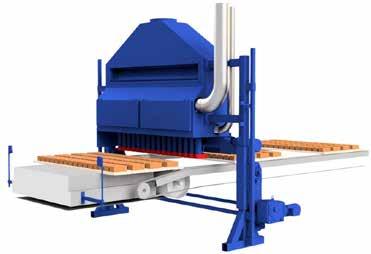
Frogreiniger
Mesys Industrial Air Systems BV Molenstraat 27, 6914AC Herwen www.mesys.nl +31 (0) 316 248744 Info@mesys.nl
Integer, onafhankelijk, objectief onderzoek en advies. ISO 17025 geaccrediteerd.
Wij helpen u graag verder met onderzoek en analyse van uw innovatieve materialen. Bel ons op 026 3845600 of mail info@tcki.nl www.tcki.nl
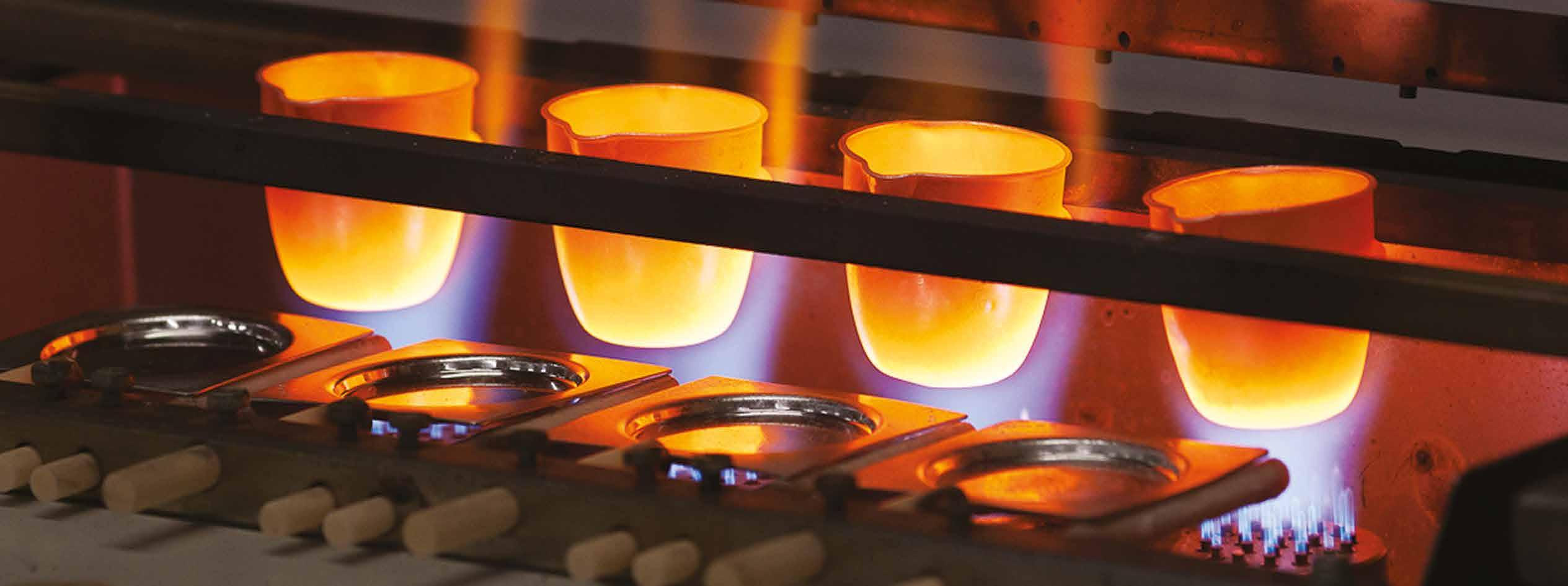
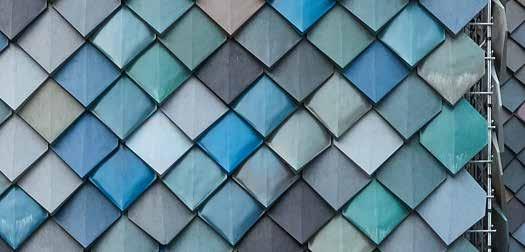
Overtreders-W
Exhibition Kunst & Kunststof Designing for a better world
Plastic is a rewarding subject for artists to criticize our consumer society. More and more artists and designers are showing that plastic should not be thrown away as a useless material. On the contrary, it should be used sparingly, reusing it, and making beautiful things out of it. At the same time, creative designers are looking for sustainable alternatives to plastic, such as materials based on natural raw materials, plants or micro-organisms. The Kunst & Kunststof exhibition (art & plastic) allows visitors to look at plastic differently, the material that is in the genes of Zuid Limburg and certainly also of Sittard-Geleen. The exhibition can be visited in Museum Contemporary Art De Domijnen in Sittard until September 19, 2021.
The exhibition shows that young designers are increasingly looking for alternative materials. Like Polina Baikina, who made a set of household items from nettles. The Swiss Sarah Harbarth developed a biodegradable material
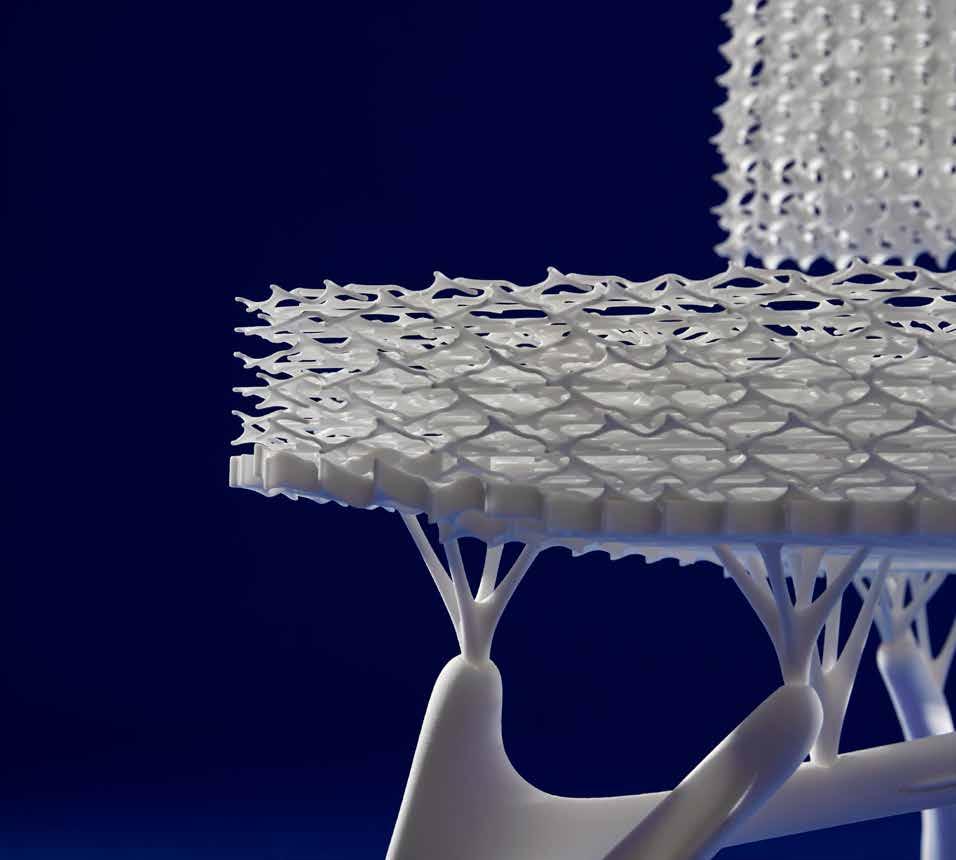
from banana peels. Mona Abusamra, industrial design student in Vienna and Belgrade, used bacteria and fermented liquids to arrive at the new plastic-like material New Culture. The Dutch Emma van der Leest is on the same track with a kind of bio leather made by bacteria. Together with Radboudumc in Nijmegen, she is developing a coating based on fungi to make this bio-leather water-repellent and to provide it with scent and colour. She already has a brand name for it: Fungkee. In addition to these experimental projects, Kunst & Kunststof shows examples of sustainable products from the Dutch plastics industry. Projects will be shown from the Chill LAB, the learning, working and research environment on the Brightlands Chemelot Campus in Geleen, where companies and institutions work together on innovations. Some of these presentations are interactive.
Kunst & Kunststof was composed by Leonne Cuppen (Yksi Connect) in collaboration with Marcel Sloots, Marlon van Schellebeek and Walter van Hulst.
www.yksi.nl>
Video Kodai Iwamoto: plasticblowing
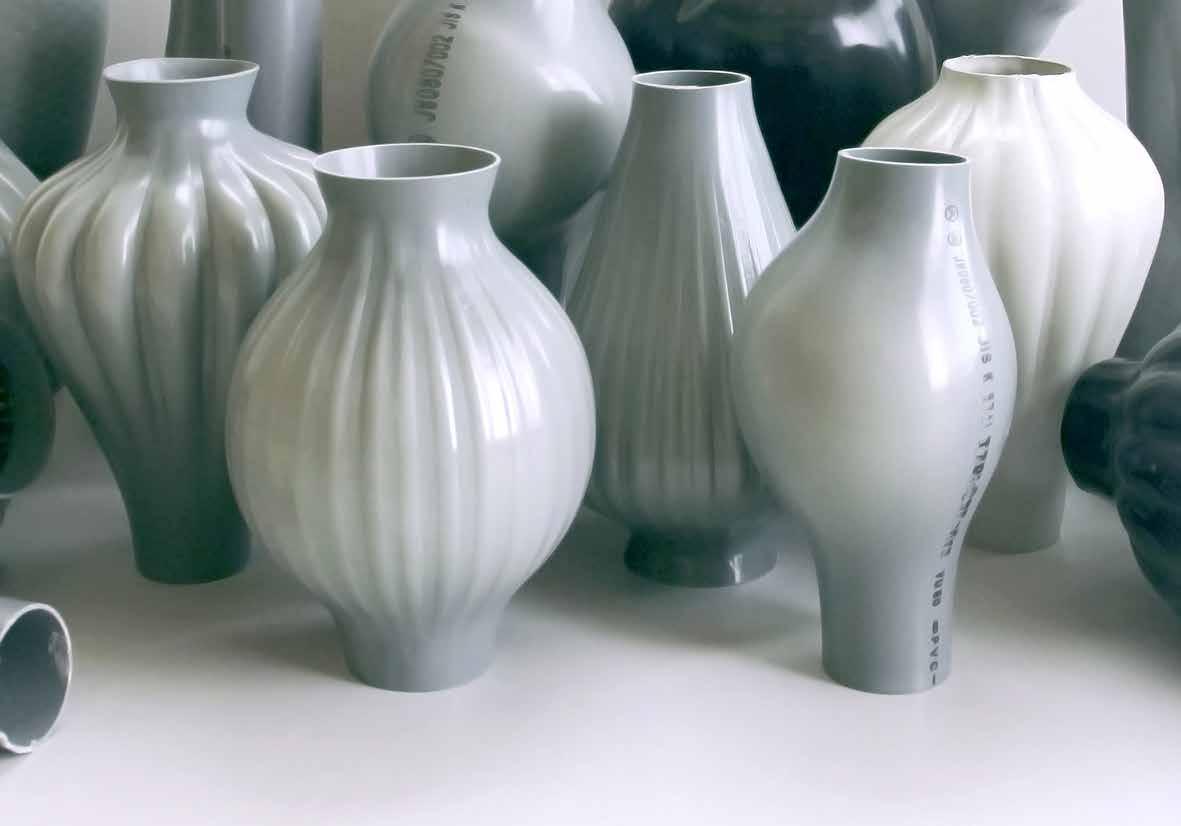
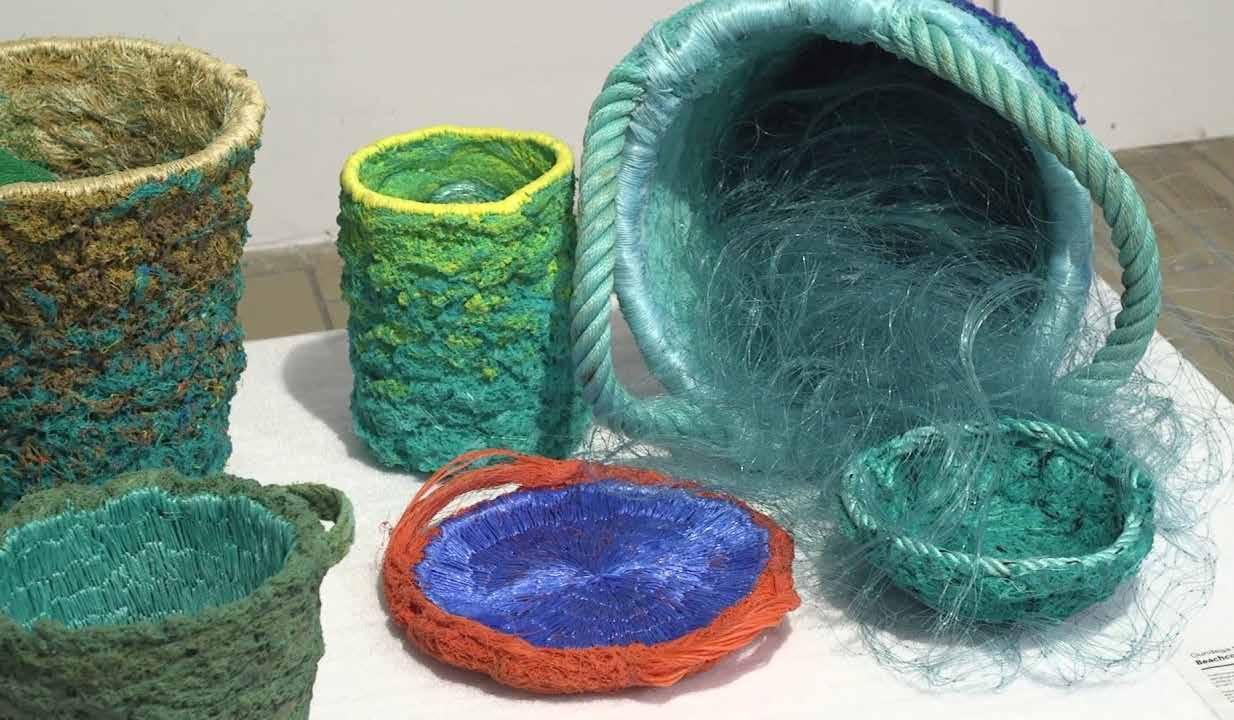
Gundega Strauberga
Waar ren jij mee? Ga naar rentegenkanker.nl
Hybrid sandwich element

Earlier this year, the Finnish company Metsä Wood presented a hybrid sandwich wall element, specially designed for prefab construction. According to Metsä Wood, the material - a combination of concrete and Kerto LVL (laminated veneer lumber) - is an easy way to replace standard concrete sandwich elements. According to Metsä, there is an urgent need for such more sustainable solutions, because the construction sector is responsible for 30 % of all CO2 emissions. The hybrid sandwich wall element combines innovation and guarantees an efficient construction. Metsä Wood collaborated with Finnish building and construction companies to design the optimal hybrid sandwich wall element, including precast element manufacturer Lipa-Betoni.
According to Metsä Wood, almost one million square meters of concrete wall elements are produced in Finland every year, resulting in 45,000 tons of CO2 emissions. If all concrete walls were replaced by hybrid sandwich wall elements, CO2 emissions would decrease by 30,000 tons per year and 95,000 tons of carbon would be stored. Metsä Fiber’s new sawmill in Rauma is the first construction project to apply the hybrid sandwich wall elements. The elements are produced at the Lipa-
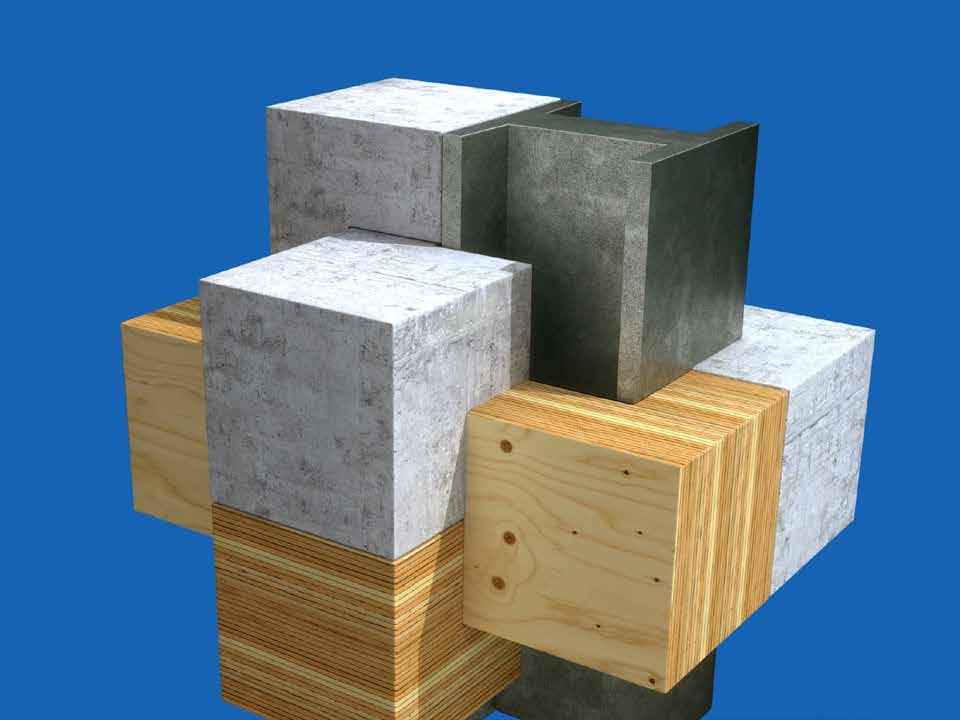

Left to right: concrete, insulation, Kerto
Video: the hybrid city
Betoni factory in Pieksämäki, Finland and were installed in June.
Starting point for the new element design was a common residential sevenstorey building with a concrete structure including hollow-core slabs and party walls made from concrete as well. In the hybrid sandwich wall panel, the load-bearing internal panel is replaced with a Kerto LVL Q-panel. Otherwise, the structure of the element remains the same; the façade is made from concrete and the element has an insulation layer. As a material, Kerto LVL is very comparable with concrete. The compressive strength of the Kerto LVL panel is as high as that of C25 concrete, 26 MPa. Also, the tensile strength of the panel is at the same level, whereas in concrete it is 10 % of the compressive strength without steel reinforcement. In a hybrid sandwich element, the reinforcement is needed only in the façade.
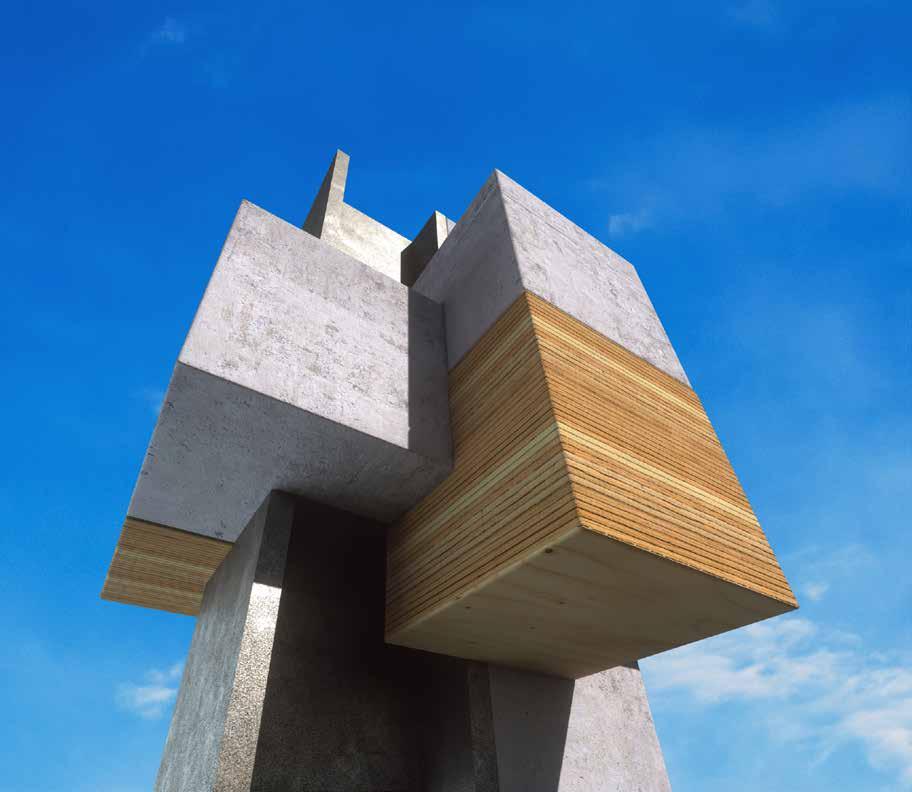
www.metsawood.com
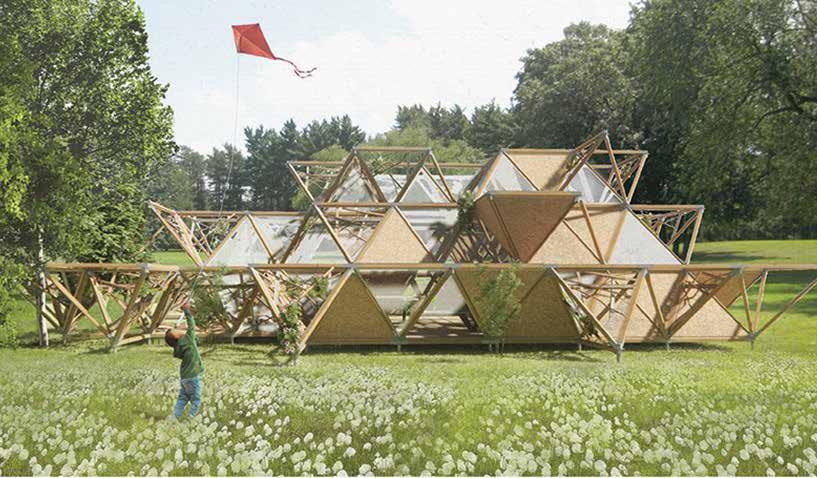
‘Incremental Equilibrium’, Team: Raluca Bratfae-Igna, Ingo Aelbers, Lucas Mézière, Adrian Beijaard, Teacher: Henri van Bennekom (Bron: TUDelft)
Students design pavilion for Soestdijk Palace
Complex Projects students have submitted eleven different designs for sustainable, circular and modular pavilions to the design contest set out by Soestdijk Palace. The winning design will be developed, built and installed at the estate when ‘Soestdijk Palace | Made by Holland’ opens.
The assignment was to design a pavilion to house exhibitions and presentations on innovations concerning nature, health and a sustainable future. As well as sustainable and circular, the pavilion had to be modular so that it could be installed at various locations. The assignment was based on the AREA Framework, an analysis and design tool developed in a Complex Projects graduation studio. This tool is used to approach sustainable design in a holistic and integrated way. It takes account of social and economic aspects as well as energy, the environment and raw materials. The AREA Framework takes a holistic approach, as a range of social and ecological issues require urgent action. Billions of people across the globe lack decent housing, have no access to healthcare and live below the poverty line. At the same time, our planet faces environmental threats, dwindling resources and climate change. To address these problems effectively, the UN has identified a number of Sustainable Development Goals (UNSDGs). In addition, more and more quality marks are being introduced to promote sustainability. However, current design and certification methods often lack an integrated approach. Purportedly sustainable designs do not always have a truly sustainable impact, for instance, because they fail to contribute sufficiently to the overall achievement of the UNSDGs. Using the AREA Framework ensures that these aspects are approached in an integral manner.
Forty-eight students signed up for the Complex Projects studio. They were divided into 11 groups that worked on the
assignment for 10 weeks, the first three of which were devoted to research into the AREA Framework. This provided the basis for the integrated and comprehensive programme of requirements.
The jury was impressed by the quality of all 11 of the designs presented. After a lengthy appraisal, the decision was taken to nominate two finalists: ‘Incremental Equilibrium’ and ‘Routes over Roots’. Both projects will require additional research and refinement of the design. In the coming months, the management of ‘Soestdijk Palace | Made by Holland’ will discuss how to take the process further.
For more information, visit www.paleissoestdijk.nl (Dutch)>
Text: TU Delft Bouwkunde>
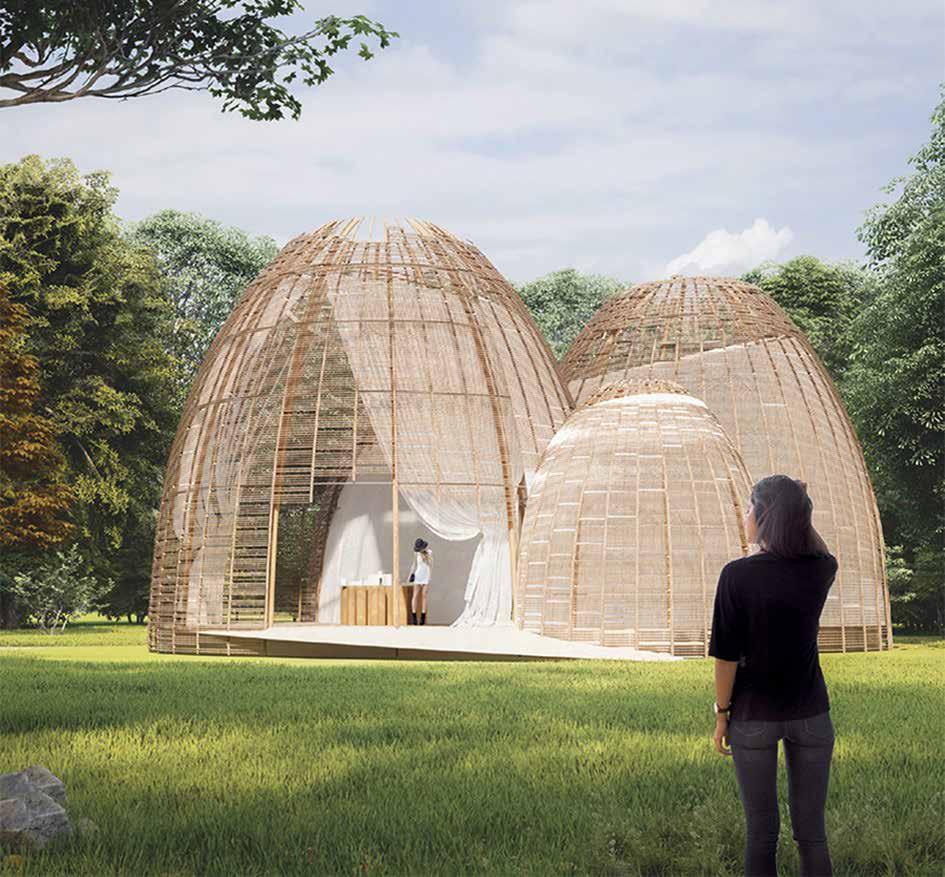
‘Routes over Roots’. Team: Jelmer Eising, Jaap Koopman, Agata Mila, Dino Vojvodic; Teacher: Aleksander Staničić
De Bond voor Materialenkennis (BvM) is een netwerk van experts op het gebied van materiaaltechnologie. Leden zijn onderzoekers en technici bij universiteiten, hogescholen, onderzoeksinstituten en de industrie. Het doel van de BvM is om kennis van de verwerking en toepassing van materialen te verspreiden, binnen en buiten het materialenveld.
De BvM initieert symposia, cursussen, technisch-wetenschappelijke publicaties, onderzoeksactiviteiten en bevordert de educatie in materialen. De totale aangeboden technologische kennis van ieder deelgebied metalen, kunststoffen, keramiek, biogebaseerde materialen, lasertechnologie, verbindingen, verftechnologie, reologie, tribologie, corrosie, warmtebehandelingstechniek, duurzaamheid en betrouwbaarheid - maakt de BvM een krachtige beroepsorganisatie in Nederland en België.
Voordelen van het lidmaatschap van de BvM:
Gratis studentenlidmaatschap: Vertel het verder! BvM-leden genieten van het FEMS- en het EFC-lidmaatschap van de BvM
FEMS is de Federation of European Materials Societies
EFC is de European Federation of Corrosion Korting op activiteiten van de BvM Toegang tot een groot materialennetwerk
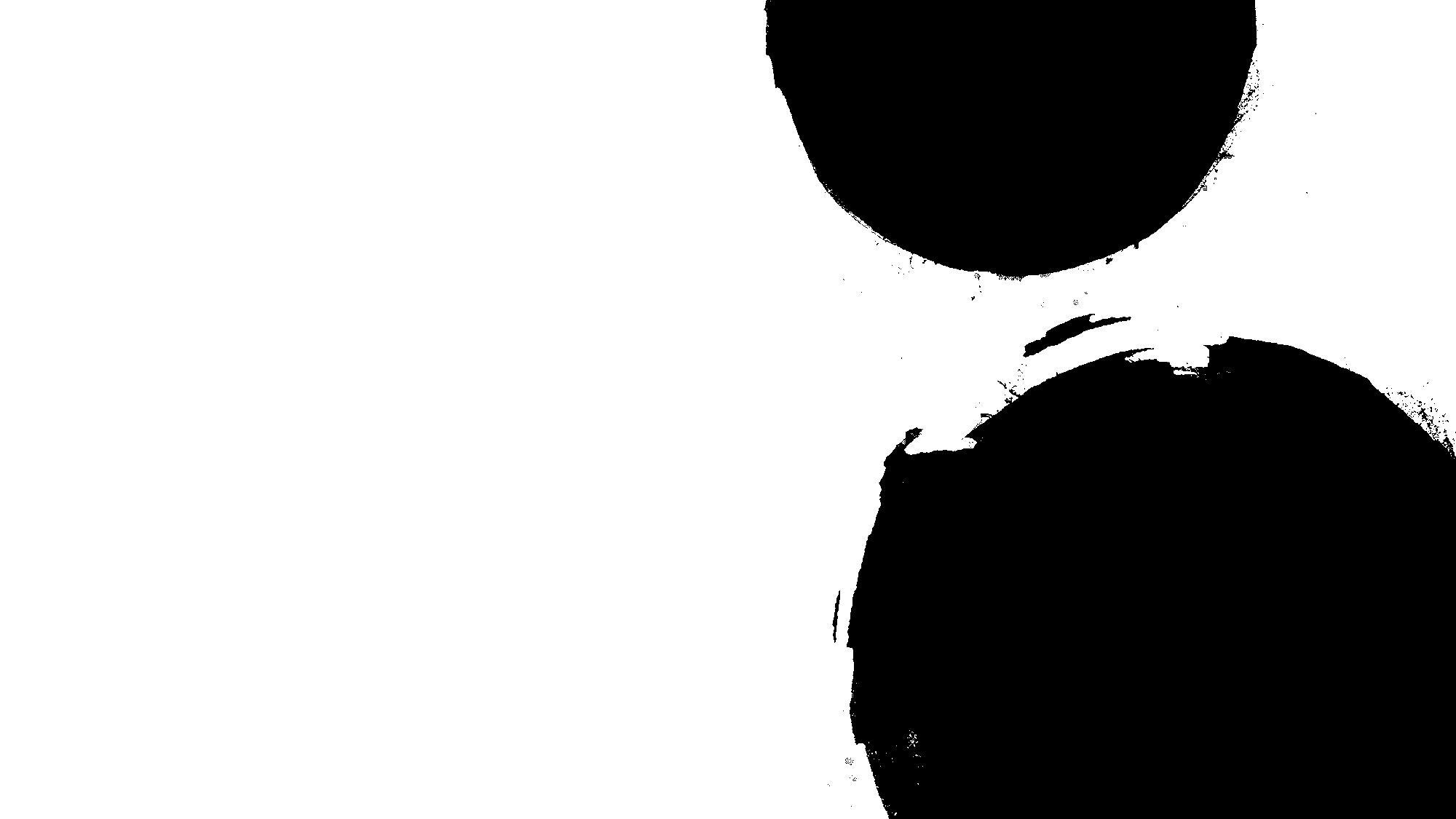
Kijk voor meer informatie en contact op de nieuwe website van de Bond voor Materialenkennis: https://www.bondvoormaterialenkennis.nl/
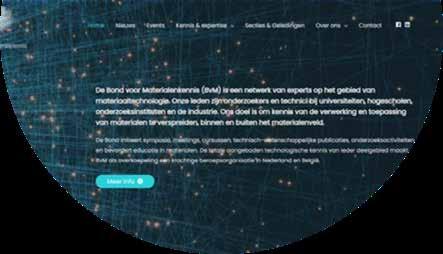
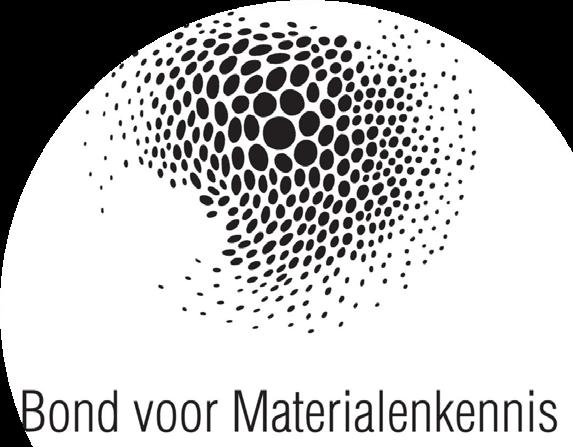
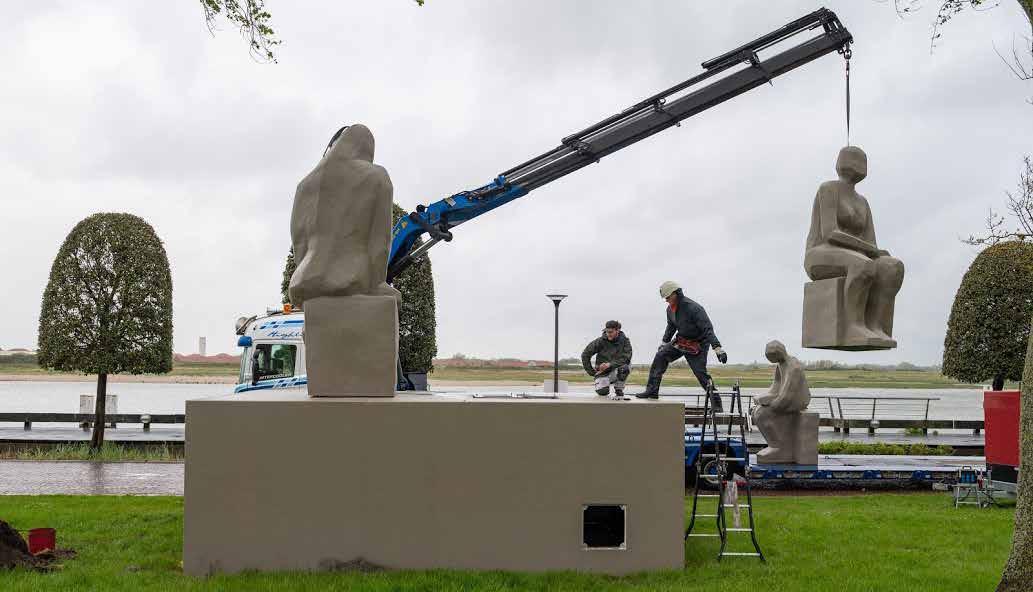
Photo: Poly Products/Gijs Proost Fotografie
Largest plastic 3D printed statues are along the Belgian coast
Poly Products from Werkendam, The Netherlands, has been commissioned by Beaufort to 3D print a special work of art by artist Goshka Macuga. Beaufort is a three-yearly art event that has been taking place since 2003 along the seawalls, beaches and dunes of the entire Belgian coastline. Along this coast you will find thirty special works of art. Together they form the Beaufort Sculpture Park. It is the largest open-air exhibition in Belgium, set against the backdrop of the coast. The artwork, entitled ‘Family Module’, concerns a group of statues forming a small family scene. Its dimensions, with a total height of six meters, make it a striking appearance on the promenade of Nieuwpoort (Belgium). Despite the size of Goshka Macuga’s artwork, the statues are extremely light in weight and can be placed without a heavy foundation.
The XXL 3D printing device at Poly Products was installed in 2019 and has played a key role in the realization of this project. The basis of the work of art were clay models of approximately 40 cm high. The challenge was to magnify it ten times without making the objects heavy. A digital process with high-resolution scans, CAD post-processing and the XXL 3D printer offered the solution. Every detail from the models was copied and was eventually incorporated into this huge work of art. The 3D printing process did not immediately lead to the final solution. The printer works with plastics, but part of the idea was to create a concrete look and not a ‘plastic look’. That is why the basic structure was printed with recycled rPETG with glass filling.
It is the second time that Poly Products has supplied a work of art for the Beaufort open air exhibition in Belgium. In 2018, Poly Products delivered the so-called ‘De Drie Wijsneuzen Van De Panne’: three pillars in the middle of the beach, 15 meters high and with large heads.
According to Poly Products, by using recycled materials with a very long lifespan and low environmental impact in production, the project is a good
example of a new way of production, using waste as a valuable raw material for new use for applications that have a positive impact on the environment. The materials of this artwork can be recycled after their use.
Beaufort>
About 3D printing at Poly Products>
Video Photo: Poly Products/Gijs Proost Fotografie
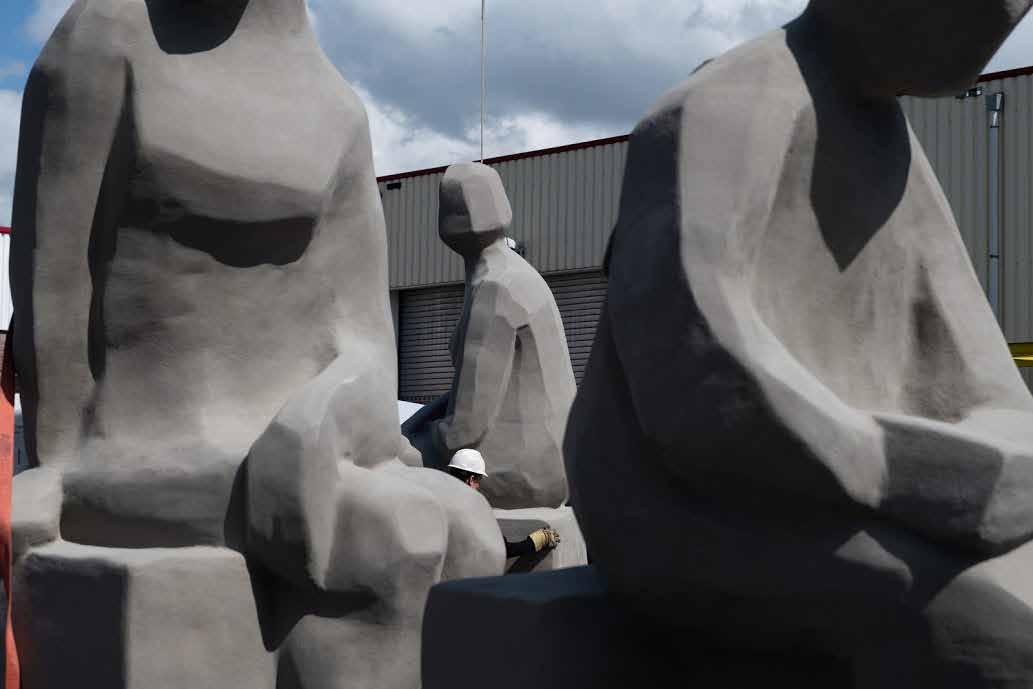
EcoTerra: Cement free surface
After seven years of intensive research and development, the German company METTEN Stein+Design has launched a new technology that makes it possible to produce concrete bricks, in which the cement in the top layer of the bricks has been replaced by cementless binders. According to METTEN, the new technology also makes the stone more resistant to external influences. The production of cement requires a vast amount of energy and a lot of CO2 is released. The use of a concrete block with EcoTerra technology reduces the CO2 load by 15 percent per m2. The use of recycled raw materials and climate-neutral production make the carbon footprint even better. In addition, the bricks have also been made ‘greener’ in terms of applicability by ensuring that they are available in permeable and water-passable variants with an air-purifying BlueAir top layer, if desired. Using a titanium dioxide catalyst, harmful nitrogen oxides (NOx) from the air are converted into small amounts of water-soluble nitrate under the influence of daylight. This substance, which is harmless to people and the environment, mineralizes on the surface of the concrete block and is discharged to the sewer during the next rain shower. In addition to the nomination for the ‘German Design Award 2021’, the EcoTerra technology was awarded with the ‘Red Dot Innovative Product 2020’. The EcoTerra technology has been patented.
More at METTEN>
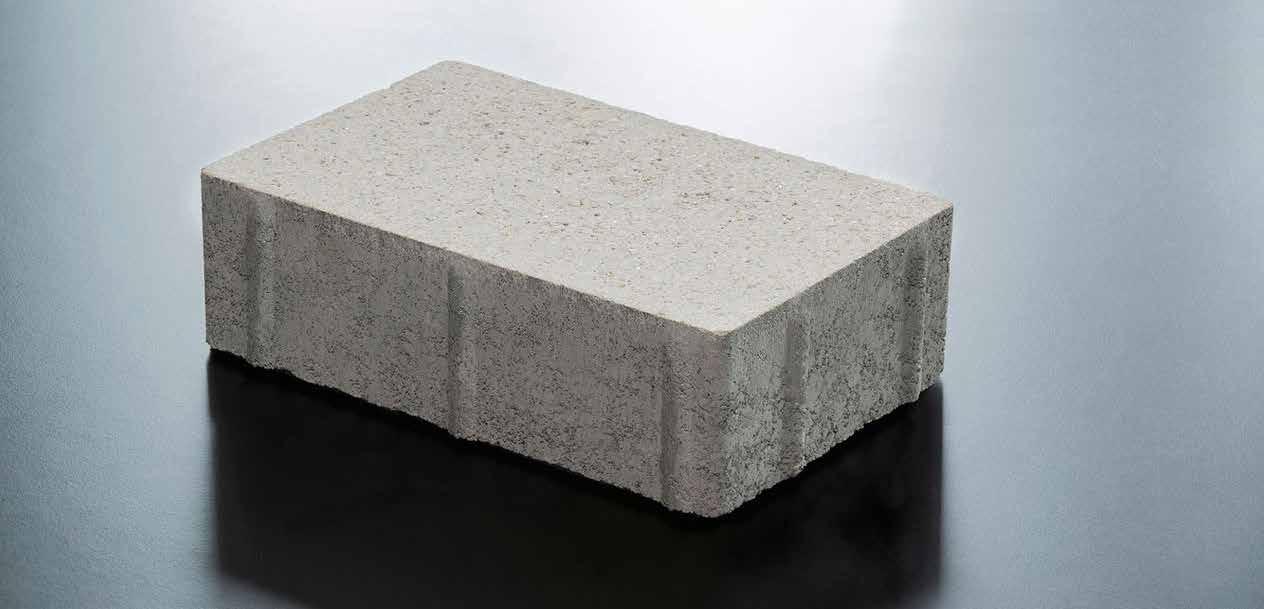
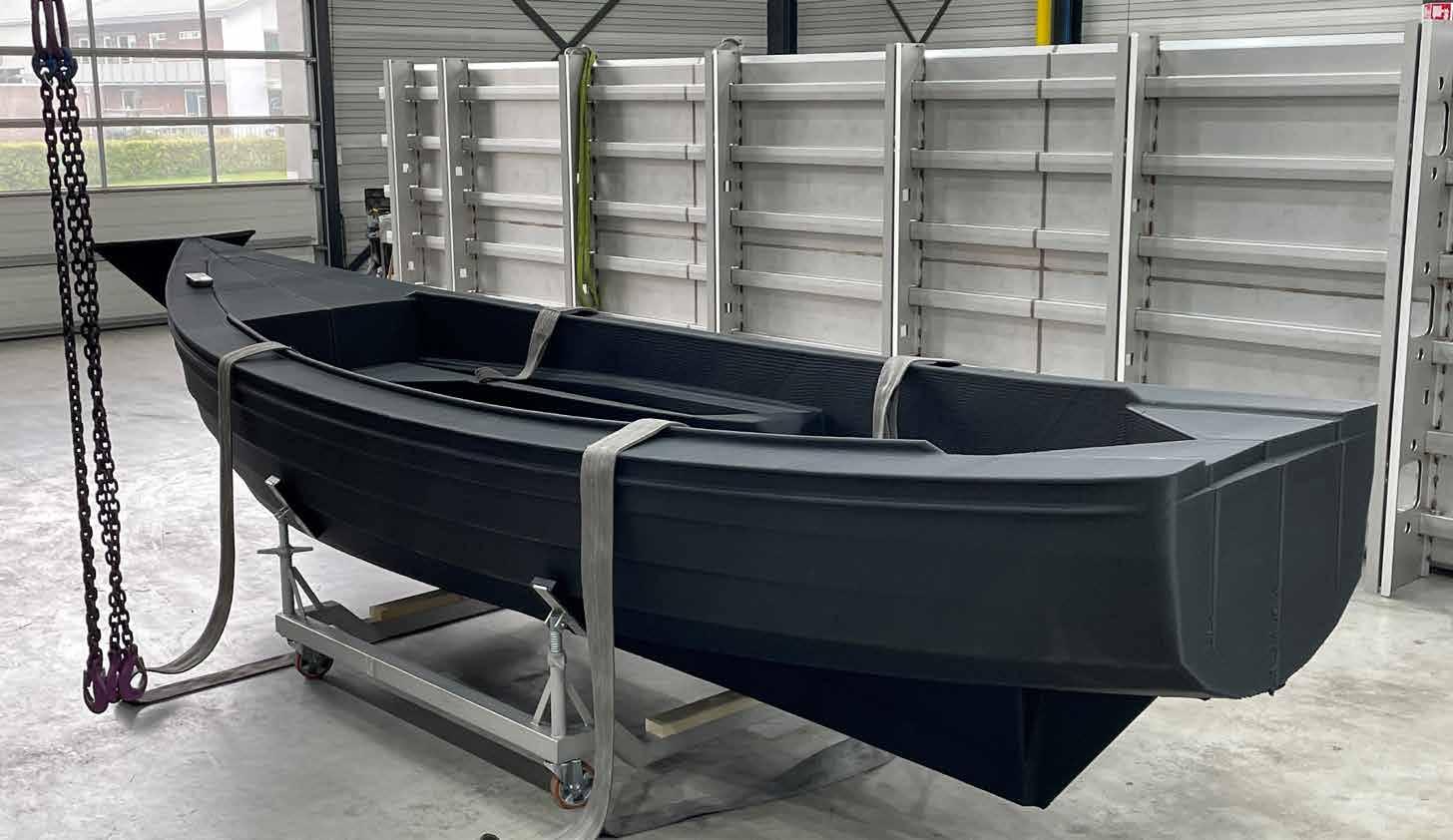
Sustainable sloops from recycled material
Sloepmakerij B.V., a new company in Woudsend, has started an initiative called ‘duurzamesloepen.nl’. It is an electric sloop with a 3D printed hull made of waste plastic, which will be completed in a 100 % sustainable way. The choice of material ultimately determines the degree of durability. But what is ‘ durability ‘? In order to be able to answer that question, the sustainability of the sloops is now being mapped in cooperation with TU Delft. Sustainable sloops is an initiative of two Frisian entrepreneurs Marieke de Boer and Jörgen de Jong.
A sustainable sloop is a 3D-printed sloop made of recycled material. The first ship is made of polypropylene (PP), which comes from household waste. The sloop is also equipped with an electric inboard motor and the outfitting is completely sustainable. The floors are made of bamboo, cork or flexiteek (ship decking); tube caps from PET bottles;
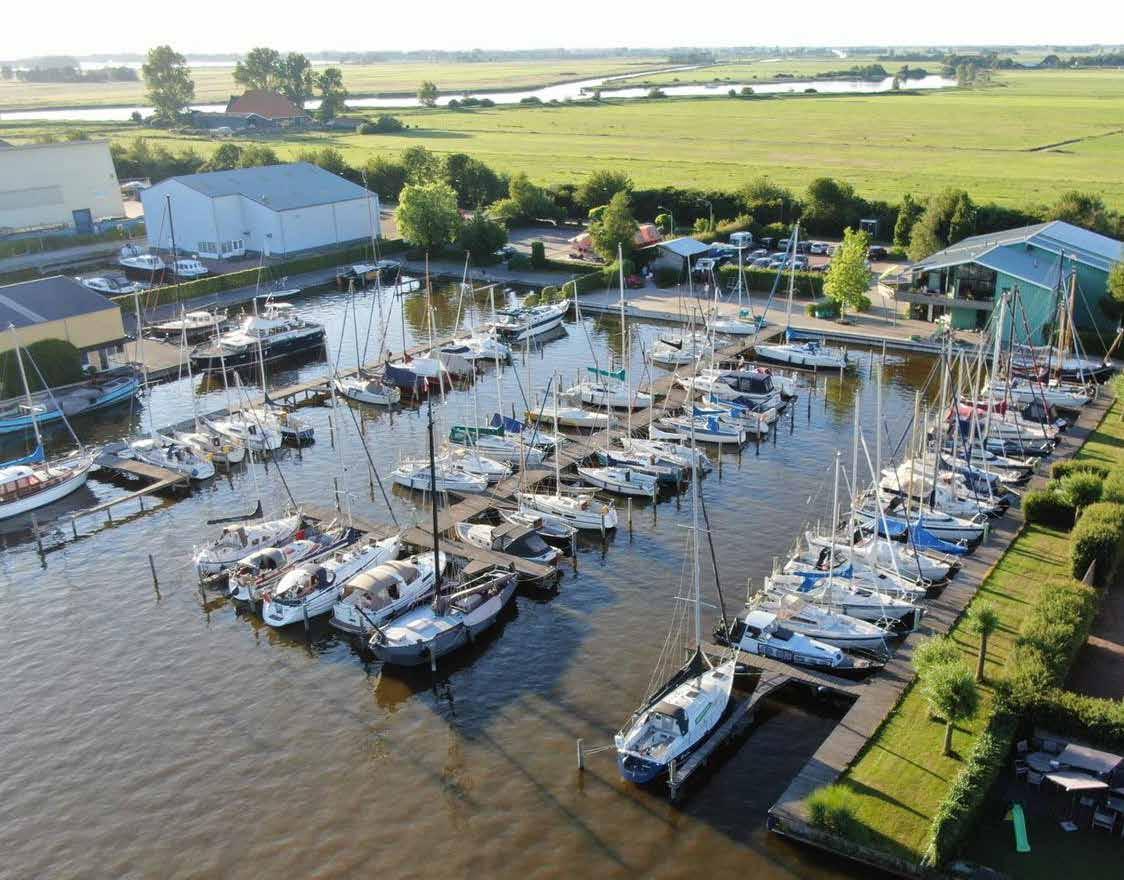
cushion sets of used sails or denim and a durable filling. Even the flag is made from PET bottles. According to the company, customers can put together their own sustainable sloop as desired. Various studies are currently underway for all sustainable options, which should, among other things, clarify which materials are eligible and how sustainable they actually are. With this, the company wants to make a demonstrable distinction between a ‘good sales story’ and real sustainability.
To demonstrate that the sustainable sloops from Woudsend are really sustainable, the company approached Delft University of Technology. Five students are currently working together with Prof. Jilt Sietsma, professor of Materials Science at the TUD, on a life cycle assessment, which looks at the environmental impact of the sustainable sloop in comparison with traditional sloops. The aim is to develop a model that can demonstrate the durability of the sloops. For example, it should become possible to make a sloop that is already 70 percent sustainable, even more sustainable through different material choices; by choosing a bamboo or cork floor for instance. In this way, the vessel can be supplied sustainably in gradations. TU Delft calculates which component contributes what percentage to sustainability. The new sloop is now extensively tested according to the CE mark. This is necessary, because the material from which the hull is made did not exist initially, and strength calculations have to be made. The inspections are important, because they determine whether you are allowed to sail on the Wadden Sea or the IJsselmeer, for example. The company has now purchased a marina, also in Woudsend, where the production facilities will be located in 2022.

The team of TU Delft and Duurzame Sloepen
Duurzame sloepen>
A week of immersion in the world of 3D manufacturing!
December 6 to 10 2021, International multi-event – Benelux region
The International multi-event - 3D Delta Week - will be organized from 6 - 10 December 2021. The 3D Delta Week will create value for users and providers along the 3D Manufacturing Value Chain. It will be the 3D manufacturing meeting point for expert and layman, inside or outside the Benelux region.
The 3D Delta week is already gathering a dozen of renown events and will continue growing as the place-to-be, with activities aimed at specific sectors, at R&D and industry, at users and suppliers. The scheduling of events will allow participants to easily move from one activity to another. The Benelux area (the Delta) is a top region in terms of 3D production, with a myriad of academic and applied research centres, a particularly high number of 3D-printers and numerous promising start-ups and established enterprises. On the user side, the region boasts a multitude of application areas - all in all, an extremely versatile and high-quality ecosystem. Now, the appropriate podium has been created to bring this leading 3D production region to the fore.
The 3D Delta Week is an initiative initially set up by Brainport Eindhoven, Flam3D, Jakajima and Mikrocentrum.
www.3ddeltaweek.com
MAKE IT MATTER
MAKE IT MATTER is compiled in collaboration with MaterialDistrict (MaterialDistrict.com). In this section new, and/or interesting developments and innovative materials are highlighted.

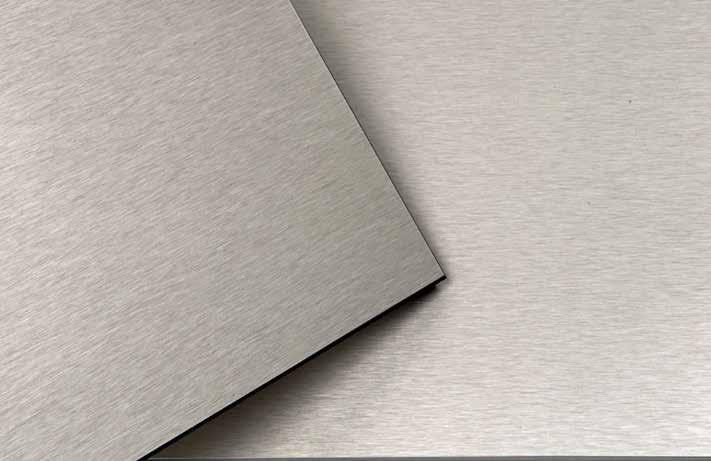

3D printed wood
US-based start-up Forust developed a method to 3D print sawdust into objects which look and feel as if they were cut from wood. The material can be sanded and refinished like real wood without the loss of realism. The strength of the material is also comparable to real wood. The technology allows the imitation of nearly any wood grain. It also allows for new design opportunities in wood. Since the parts are formed layer by layer without the need for supports, parts can be created that are complex or even impossible to make with traditional woodworking methods.
More at MaterialDistrict>
Fenix
Fenix NTA is a material produced by simultaneous application of heat and pressure, in order to obtain a homogeneous nonporous high density product. The core structure is composed of paper, impregnated with thermosetting resins. The outer surface is made of a real metal structure substrate treated with acrylic resins applied to the substrate as a multilayer coating. The result: an empowered metal surface: extremely matt, soft touch, anti-fingerprint and with a resistance to superficial micro scratches.
More at MaterialDistrict>
Reveneer
Pieces of veneer - left overs from industry - are pressed together to form a sturdy whole. By pressing the different layers of veneer together, combined with solid wooden parts, the material is shaped and gains its strength. Studio Jeroen Wand uses a simple vacuum technique which implies they don’t need to make difficult moulds, which also means they don’t need to use extra energy or materials. The manual process allows for freedom in arranging the different parts of veneer, where each object can have an individual, unique structure.
More at MaterialDistrict>
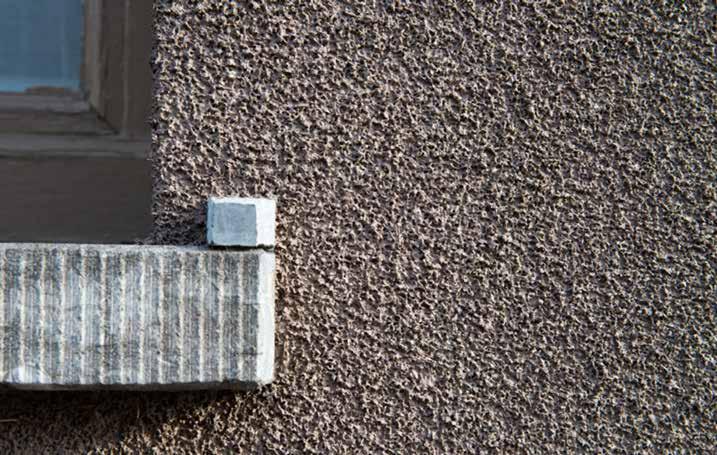



Cork spray
Decoproyec spray cork is an elastic and maintenance-free coating based on natural cork that protects buildings against wind and weather. The material is breathable, water-resistant and resistant to salty air, making it the ideal coating for buildings located by the sea. Decoproyec adheres particularly well to concrete, plaster and stone, but just as much to plastic, metal and wood.
More at MaterialDistrict>
Design solar panels
Studio Solarix works on innovative developments for the colouring of energy-generating facade panels, paying a lot of attention to the correct structure and materialization of the colours in combination with high energy yields. Due to a matt appearance in the high-quality ceramic colouring technique in Solarix Colours, they ensure that the colours of their facade panels combine well with other materials in the construction, such as stone, composite wood or aluminium due to the matt appearance.
More at MaterialDistrict>
Parabeam 3D Glass Fabrics
Parabeam 3D Glass Fabrics are a 100 % woven fibre glass material consisting of two deck layers bonded by vertical glass piles. During impregnation with a thermoset resin, the fabric is compressed but then immediately rebounds to its original height. The resulting laminate is strong, stiff, lightweight, and durable. Main applications: Sandwich structures in the marine, construction and transport industries, storage tanks in corrosive environments.
More at MaterialDistrict>
Doluflex
Doluflex is a corrugated aluminium sheeting machined by a cold forming system. The corrugated sheet is glued between two plain layers, resulting an extremely stiff lightweight sandwich panel which can be bent and shaped into components.