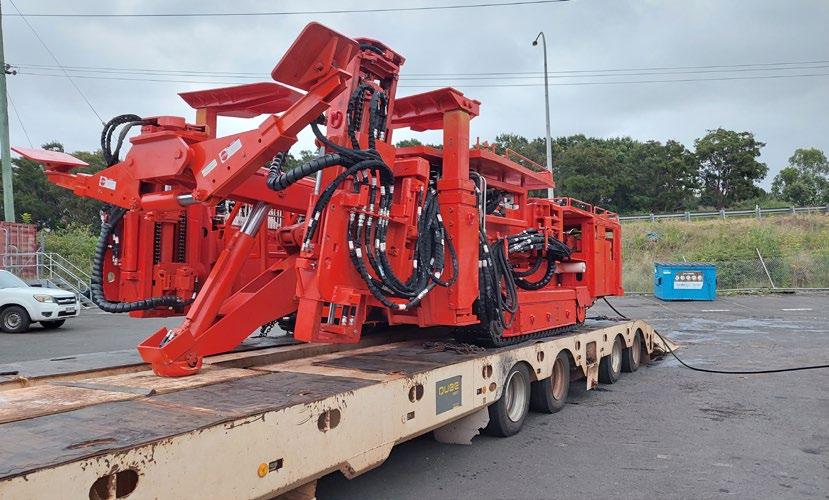
4 minute read
The Rebirth of a Roof Bolter
from Momentum Edition 3
by inenco2
The client wanted a new roof and wall bolter. The problem was the delivery lead-time quoted by the manufacturer was well outside the envelope of what the mine’s production schedule deemed feasible. The solution was to get CRAM Mining and Undercarriage to essentially rebirth a machine the client had withdrawn from service.
The Fletcher CHDDR17 is a track-mounted roof and rib or wall bolter used in underground coal mines. Its function is to drill holes in the roof and walls and then install chemically-anchored bolts to stabilise the rock strata. It’s a big machine: it weighs in at 26+ tonnes, is 8 metres long x 3 metres wide and just over 1 metre high and has an operational height range from 1.2 metres up to 5.2 metres.
Advertisement
This is the machine sent to CRAM for a complete overhaul and rebuild.
However the job would prove to be considerably more than a strip down and rebuild. The machine had been languishing in a machinery ‘graveyard’ for almost ten years. No maintenance had been carried out and many of the parts were not serviceable. It would be a back to square one; a nut-and-bolt rebuild.
The first step was to strip the bolter to its bare bones, sandblast all metal parts to remove any rust and the like and then test all the structural components for cracking and any weld defects – a step that initiated three weeks of weld repairs and re-welds. When repaired, theses parts were painted and stored ready for re-assembly. All pins and bores were evaluated for serviceability then, depending on their condition, either cleaned and reused or removed and replaced.
The hydraulic circuit – vital to the operation of the machine – was completely removed.
All the actuators were stripped down, inspected and overhauled – which in this case included re-chroming and grinding of the rods, bringing them back to original specifications. After necessary repairs were made, new seals were fitted to the cylinders then new hoses fitted. The hydraulic pumps were replaced and the valves stripped down and either repaired or replaced as considered necessary.
All the components were individually tested and then reassembled ready for installation.
Two of the sixteen cylinder assemblies on the machine were purchased and fitted to replace the original units lost over the years of dormancy. On two bespoke cylinders from Fletcher, some technical troubleshooting was necessary, requiring the rams to be replaced new. Ultimately they too were ready for installation as the machine went back together.
The electrical circuit was subject to the same process. All components were stripped out and replaced with modern equipment, including the addition of a PLCcontrolled tramming system.
The undercarriage assembly was reduced to its component parts. The tracks frames were stripped, the track guides were replaced on the track frames and new track plates were purchased. Then, following a thorough inspection, the gear train within the track frames was replaced old for new.
With the exception of two specialised services – electrics and re-chroming – all the work was completed in-house which ensured consistency of workmanship and quality control.
Logistically the job was not without its challenges – keeping track of 1000+ individual parts occasionally resembling a giant jigsaw puzzle on the workshop floor was achieved through a proven tracking and storage system – but in a little more than 26 weeks the machine had been completely stripped, inspected, repaired, overhauled and rebuilt to original specifications and returned to site for re-commissioning.
CRAM Mining then turned its attention to the compliance upgrade of two machines recently acquired by the same client.
Although not as detailed as the rebuild, bringing the two machines up to Australian compliance requirements and standards was just as technically demanding. Both the hydraulic system and electrical system required upgrading.
Under Australian compliance conditions, hydraulic hoses are required to be compliant with the relevant Mining Design Guidelines, which meant removing and replacing all the hydraulic hoses on both machines. Additionally, the hydraulic oil had to be replaced which meant flushing the system and replacing it with an approved fluid.
While these upgrades to the hydraulic system were under way, the electrical system too was replaced in order to meet the relevant Mining Design Guidelines. Projects of this nature are a core function of CRAM Mining & Undercarriage and the company brings extensive knowledge and resources to such jobs. The ability to complete almost all tasks in-house gives the company and its clients significant cost and efficiency advantages.
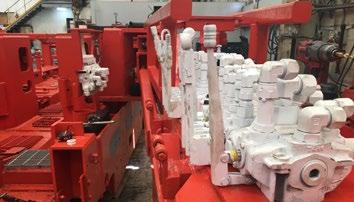
Valve blocks were remanufactured in house
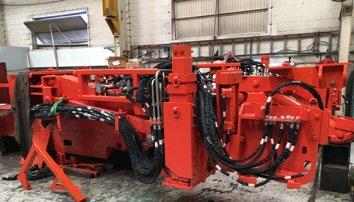
New MDG-compliant hosing
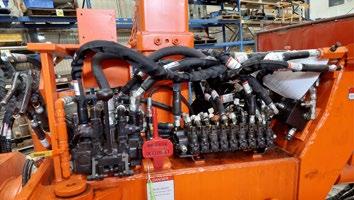
Some design changes were necessary to accommodate locally-sourced equipment