
8 minute read
No limits to quality BMB
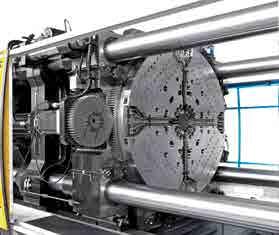
Rotating platen mould, part of the KW 1500/2x1300-2x2200 RT 4-injection press
NO LIMITS TO QUALITY
With a strong focus on quality and innovation, BMB has been growing and evolving right from the start. Today the company offers a range of hydraulic, electric and hybrid injection moulding machines and solutions for plastic materials. Indeed, it sets no boundaries to the market sectors it serves, as Barbara Rossi discovers from sales director Adriano Zucchelli.
BMB was established in 1997. Right from the start it has been known as a hi-tech company with a strong level of ‘human know-how’, able to innovate, evolve and remain ahead of the times. Its founder, Egidio Bugatti, and his son Marco have a very clear vision of how BMB should operate. Its aim is to offer customised machines and solutions to meet any plastic injection moulding need.
“We could say that in its 45 years of activity BMB has always been growing, both in terms of production quality and profit,” explained Mr Zucchelli. “To achieve this level of success obviously requires a high level of technology and innovation, but being able to rely on a strong and united team with common values is equally important.”
The pursuit of quality has been the primary concern for the company throughout its 40 years in the business. Because of this, today BMB is a forward-looking company that is highly competitive on the global marketplace and equipped with significant strategy resources.
Investing in expansion
BMB SpA is based in the Brescia industrial district (northern Italy), where it has three production units, alongside its functional and modern offices. These, together with its network of sales and post-sales service branches located in all its major commercial hubs, form an efficient customer-focused network. One of these branches is UK-based BMB Plastic Machinery Limited, which since 2013 has been led by MD and commercial director Nigel Baker. He is flanked by a skilled team, including a technical service assistant whose task is to supply UK-based customers with a fast service. The BMB site in the UK is new and comprises a sales and a service/ spare parts office.
BMB SpA has recently made another important investment. It will soon be opening a new site in the Toronto area (Ontario, Canada) which will operate both at commercial and technical level, thanks to a team of highly-trained staff.
“While we mainly supply our products to the packaging sector, we do not set any boundaries to the range of industries that we
KW 1800/7000+5500 RT bi-injection moulding machine Anthropomorphic robot for collecting moulded components. Part of the KW 1800/7000+5500 TR bi-injection press.
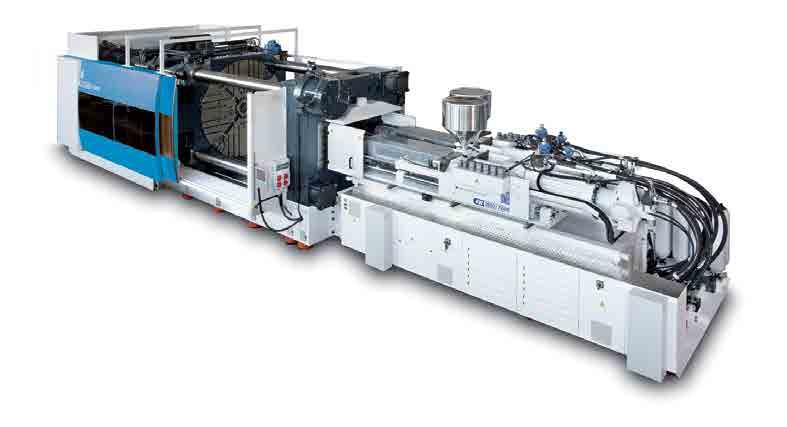

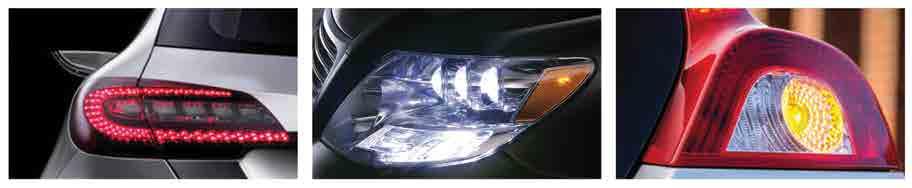
Cars light clusters moulded using the following special multi-injection presses: KW 1800/7000+5500 RT e KW 1500/2x1300-2x2200 RT
serve, as we can mould any plastic material product. Lately we have seen an increase in demand from the automotive sector and the synergies we have developed with our clients have allowed us to create machines which are totally unique in terms of power, sturdiness and precision. We also serve the medical segment.”
Geographically speaking, the key markets for BMB are currently the UK and Latin America (especially Brazil and Mexico) but also continental Europe as a whole. The opening of the Toronto branch will be the first step to entering the North American market.
Developing production profile
The company’s product range covers electric, hydraulic and hybrid solutions for plastic injection moulding. Its flagship models for the fully hydraulic machines are the KW series (ranging from 160 to 3500 tonnes) and the KWPi series (ranging from 160 to 850 tonnes). The latter is ideal for packaging products.
“In terms of hydraulic machines, we also offer the KX series for high tonnages (from 1400 to 3500 tonnes) but nowadays the market demands hybrid and completely electric solutions, for which we can offer the following series: eKW hybrid, eKW Pi Full Electric and eMC Full Electric. The eKW Hybrid series offers machines specifically for packaging and technical products, featuring a clamping strength ranging from 200 to 2200 tonnes. The eKW Pi Full Electric machines are specifically designed for packaging products and have a clamping strength varying from 100 to 1150 tonnes, while the eMC Full Electrics are mainly used for technical products and offer a clamping strength range from 70 to 200 tonnes.”
Over the past two years the company has been developing and manufacturing special multi-injection machines, mainly for the automotive sector. “We have been ready to respond to demands with regard to multicolour and multi-material processing. Almost every industry today employs this technology, for many different purposes. The final aims are extremely diverse, but may be summarised as follows: aesthetic and functional (or sometimes a combination of the two).
“Our multi-injection presses feature two or more injection units which can be set with different configurations. According to the product to be moulded the injection units can be employed to carry out multicolour processing (using the same polymer with
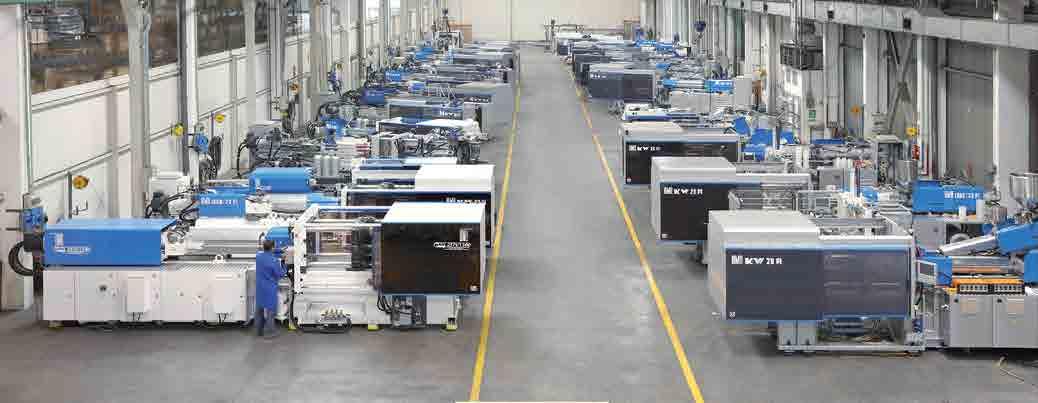

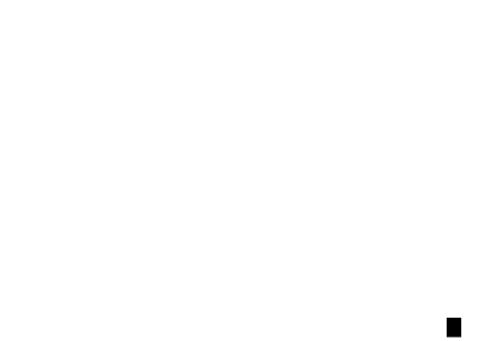

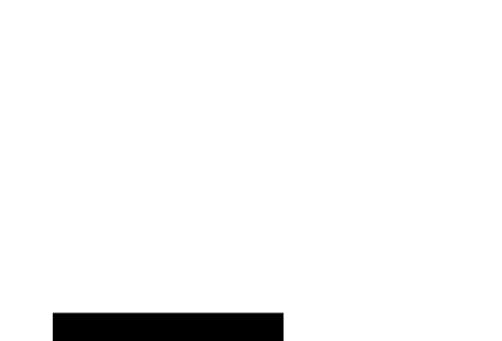
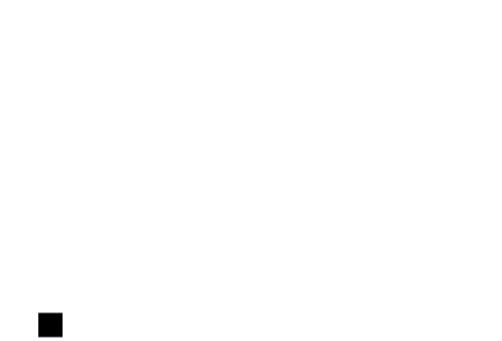
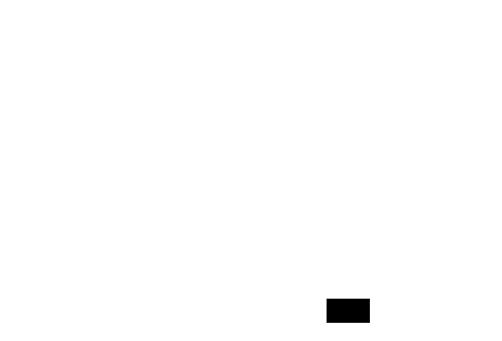
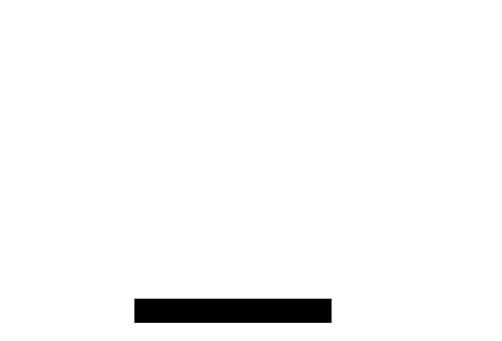
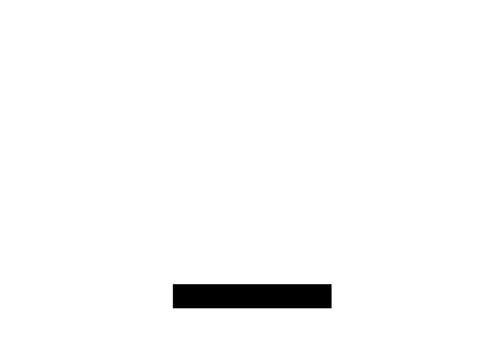
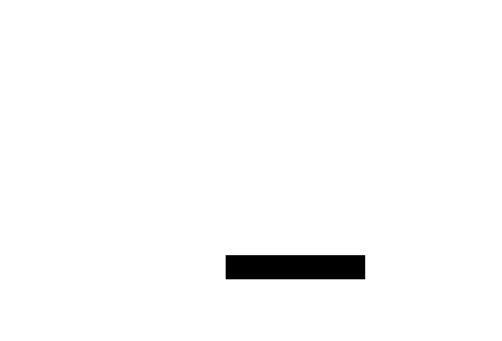
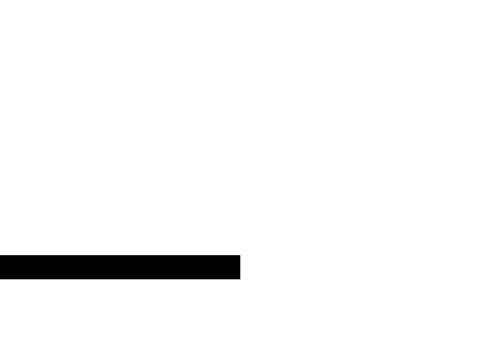
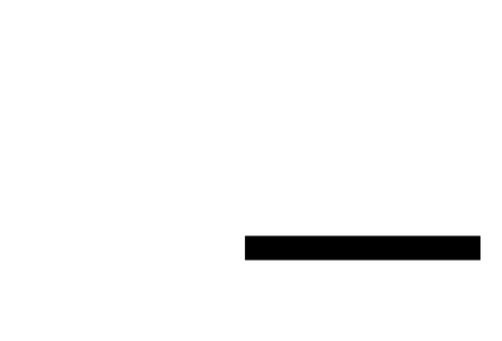
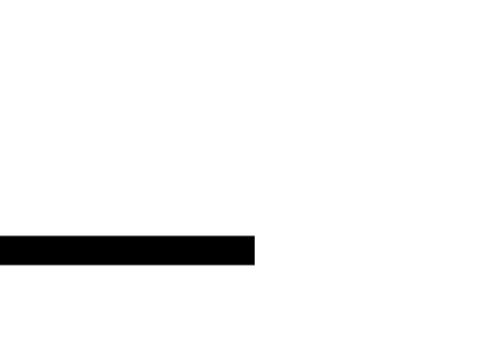
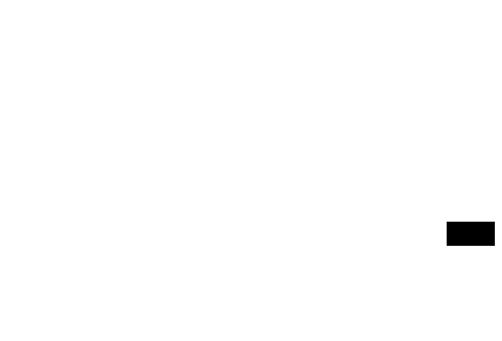
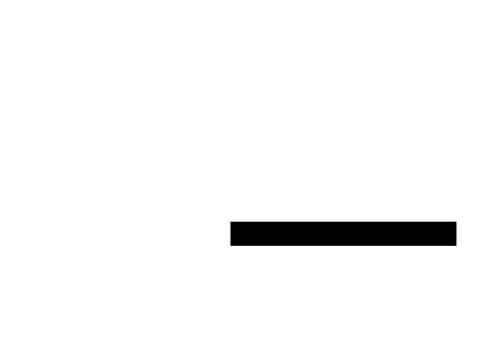
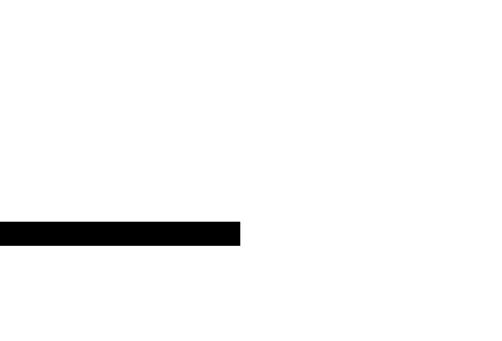

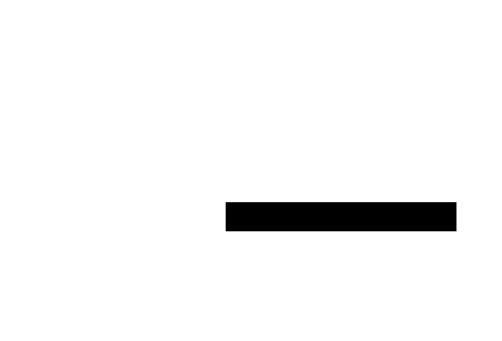
KW 250/2VP 700 bi-injection moulding machine
Lids in two or more colours or components moulded using the eKW25Pi/1300+330 Full Electric press
different colours) or its multi-material version, employing two or more different polymers. Currently our presses can be equipped with up to four injection units, especially when they have to mould complex products such as light clusters for cars. On the other hand, the clamping unit is customised according to the application, varying in terms of clamping strength, weights and passage between columns. Usually a multi-injection press clamping unit can feature many solutions: rotating platen, stack-mould and Index system.”
BMB’s technical office is working towards innovation on three different levels: mechanics, electronics and software. The main aim is to meet any moulding need, even of the most complex nature. In fact, owing to its skilled, innovative and passionate technical staff, BMB is able to take on any customer’s project, transforming it into a success and thus into a new opportunity for growth. This is possible thanks to the synergy between BMB and its clients and the employment of 3D modelling systems and FEM structural analysis to best optimise machine design. With regard to electronics and software, BMB can avail itself of a close and continuous partnership with HEIDENHAIN and MOOG, two very well-established multinationals engaged in innovation on a regular basis. Thanks to this, BMB can always be at the cutting edge. n
60th Anniversary 1955-2015
Ferramenta Bresciana has over 60 years of experience in the manufacturing and distribution of tools, screws and bolts. The presence of the Italian fi rm’s large storehouse (more than 1000 square metres) ensures the availability of a wide range of products, including high resistance screws and special tools. In the last few years Ferramenta Bresciana has specialised in maufacturing of customisable hot stamped screws and bolts, giving the customer the possibility to choose each product’s shape and size. Ferramenta Bresciana can also design new products according to the customer’s needs.
FERRAMENTA BRESCIANA 25126 Brescia, Via Milano 68/B-70, ITALY T: +39 0303 2411124 | F: +39 030 2416176 | E: ferramentabresciana@libero.it
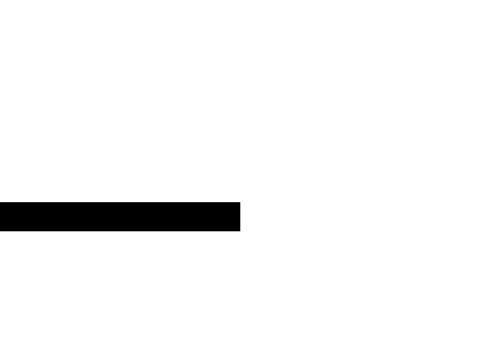

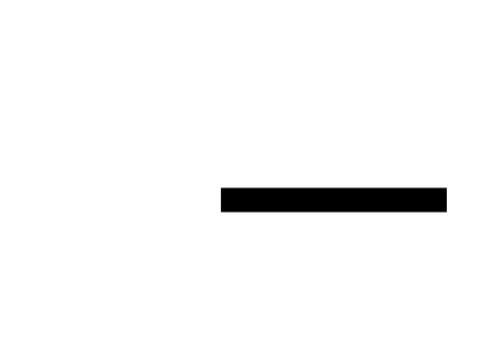

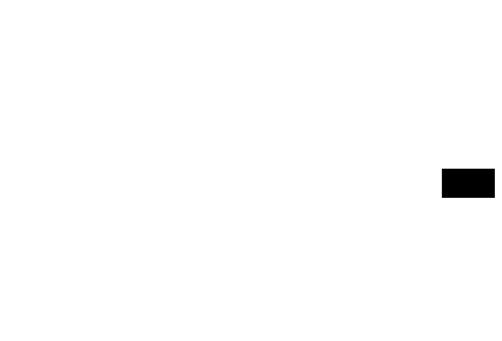




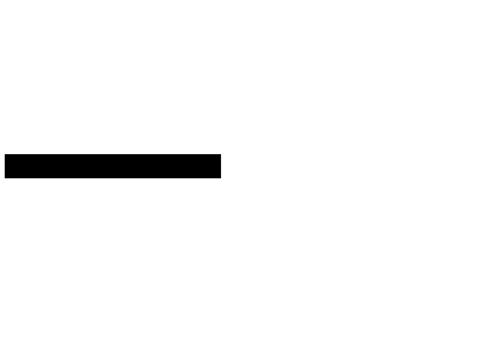
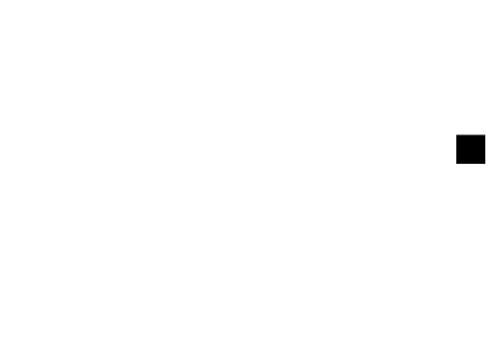
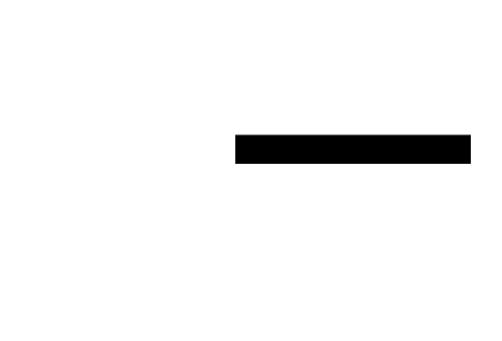

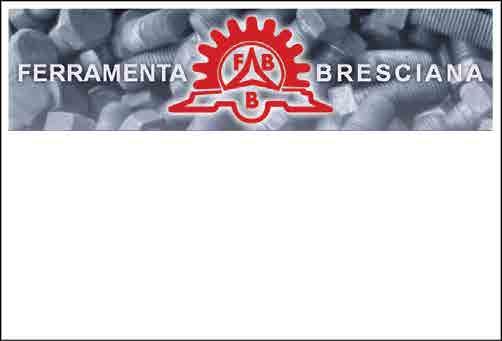
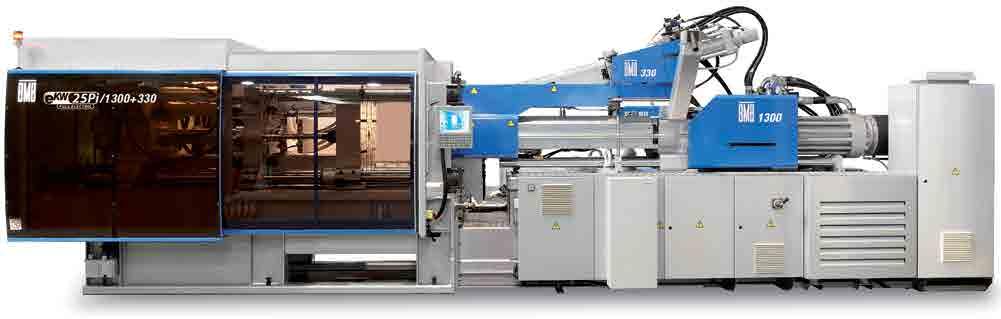

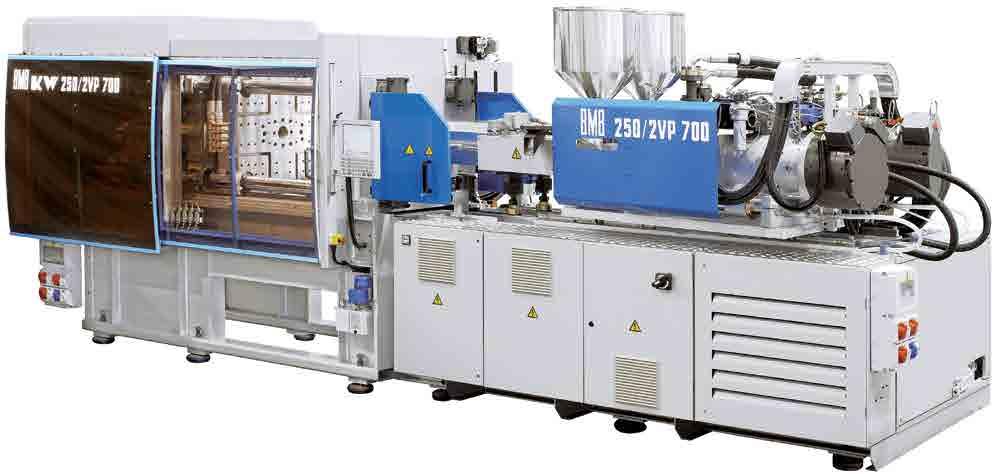