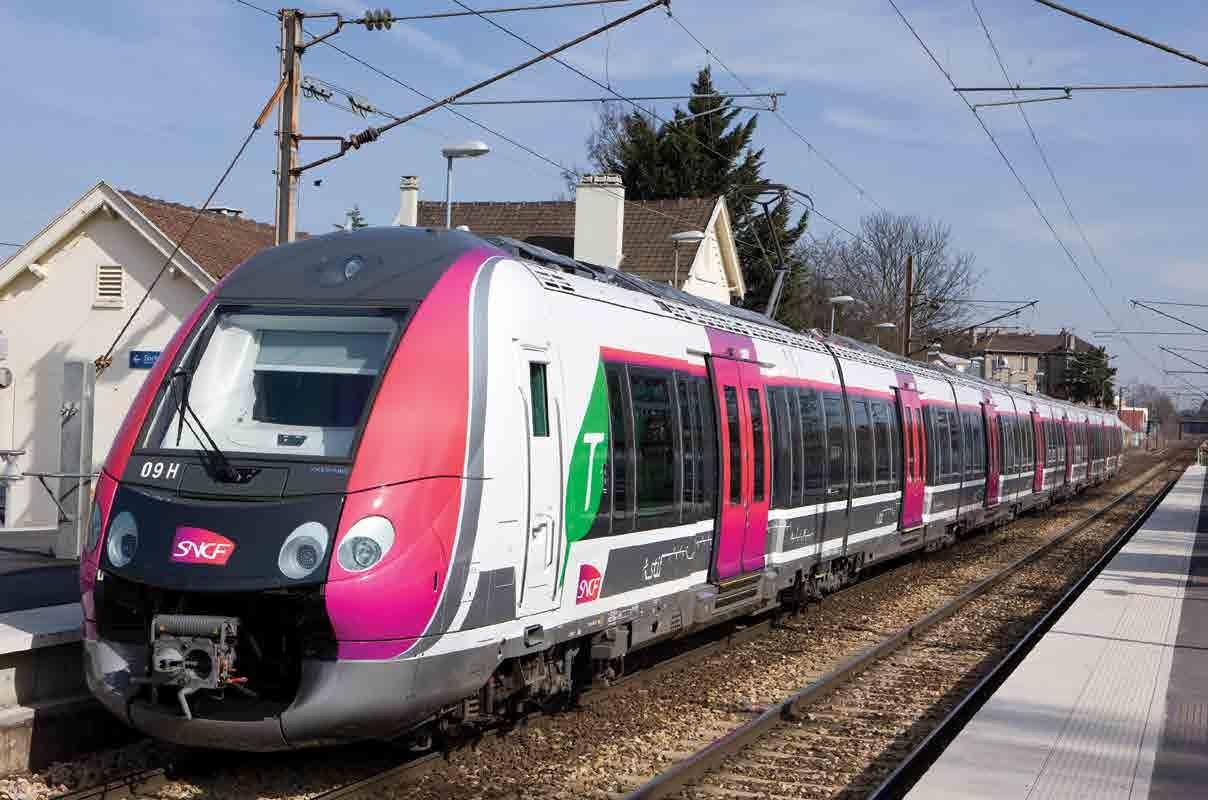
5 minute read
Future mobility solutions
Bombardier Transportation is the No. 1 solution provider in the railway industry. The company has won a large percentage of the biggest orders in the world in the past few years and is the leading provider of innovative products and solutions for the mobility challenges of today and tomorrow. Edina Beale reports.
Bombardier has an optimistic outlook for the future. Over the next few years the company expects to see continued growth in the rail market as the fundamental drivers for the rail industry, such as the global trend towards urbanisation and a rising need for mobility, remain positive. Numerous turnkey projects in emerging markets, in addition to large fleet replacement projects in mature markets – such as eastern Europe – are encouraging indicators for the future development of the industry.
With its double deck TWINDEXX Vario and the double deck wide-body OMNEO trains, both of which are suitable for urban and regional traffic, Bombardier has the right products to meet the increasing challenges of urban congestion.
One solution to meet these challenges is the BOMBARDIER INNOVIA Monorail 300. It bridges the gap between low capacity light rail systems and high capacity heavy metro systems. The INNOVIA Metro 300 system has been optimised to reduce costs, infrastructure requirements and environmental impact. With its compact vehicles, it uses dedicated, slender guideways that integrate seamlessly into cities and urban areas.
At this year´s InnoTrans, Bombardier yet again set new efficiency standards for products and services. On display at the event was the energy efficient TRAXX F140 AC locomotive with the Last Mile feature, the innovative FLEXX Eco bogie and the ground-breaking FLEXX Tronic WAKO system. New structure
Bombardier Transportation is part of the Canadian multinational Bombardier and currently employs about 38,000 people worldwide. The group’s revenues totalled $8.8 billion for the year ending 31 December 2013, compared to $7.8 billion for the previous fiscal year. Mátranovák in Hungary is a vital site for Bombardier’s European operations. Bombardier Transportation Hungary Kft manufactures bogie frames and primary parts that are then delivered to Bombardier’s bogie final assembly sites in Crespin, France and Siegen, Germany. The Mátranovák factory is the largest bogie making plant within the Bombardier Group, in which more than 560 staff are employed to manufacture 1200 bogie frames every year.
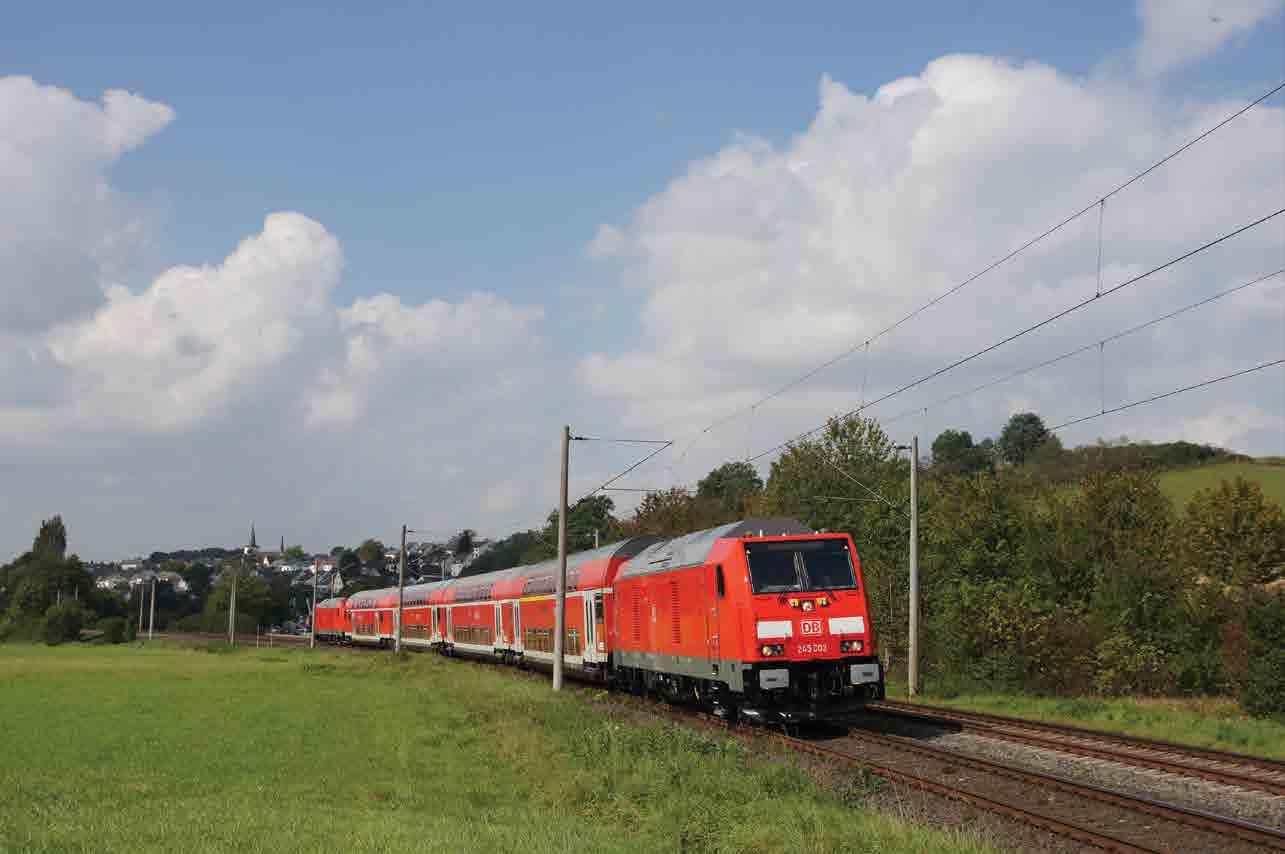
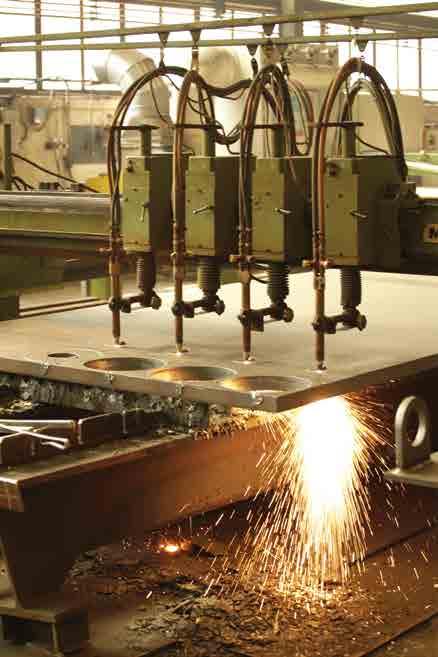
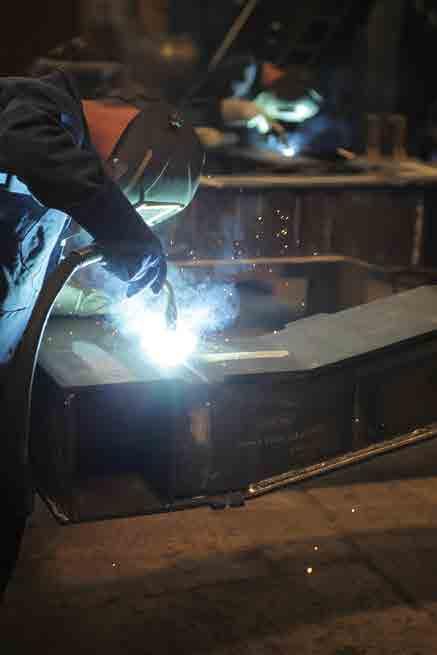
In 2013, Dr Lutz Bertling was appointed the new president and COO of Bombardier Transportation. This appointment was followed by the launch of a new organisational set-up, OneBT, to further empower project management, reduce organisational layers and overhead costs, speed up decision making, implement leaner processes and foster upfront product development and standardisation. “Bombardier’s new organisational structure is an initiative aimed at securing our long-term competitiveness and improving our cost structure. Commitment to customer support and flawless execution remains Bombardier’s focus,” confirms Mr Kurt Lievens, managing director of Bombardier Transportation Hungary Kft. Major contracts
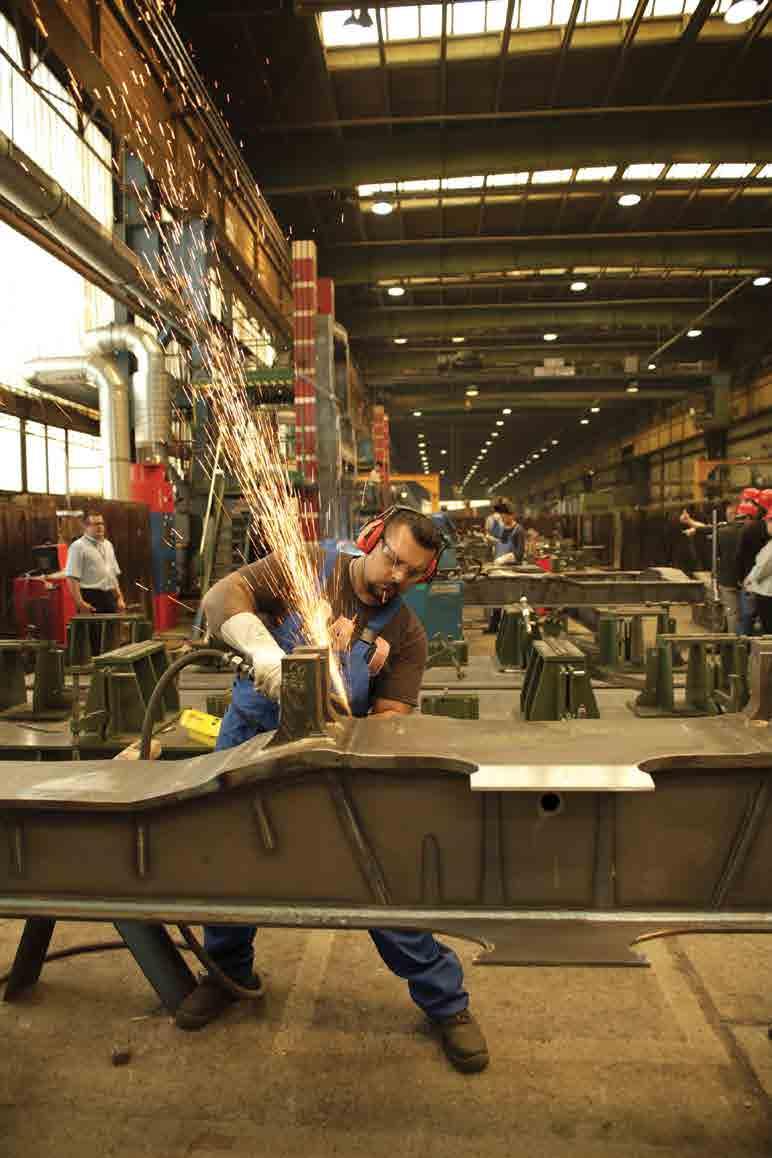
In 2013 Bombardier Transportation signed significant contracts across all its product segments and geographic regions and the company is well positioned for future growth. The group recently concluded agreements to deliver 130 BOMBARDIER TRAXX electric locomotives and 18 electric double-deck multiple units (EMUs) to Deutsche Bahn, for a total value of $1 billion. The Stockholm Public Transport Authority of Sweden granted a contract for 384 BOMBARDIER MOVIA metro cars valued at $771 million, while S-Bahn Hamburg GMbH signed an agreement for 60 single and dual-voltage commuter trains valued at $427 million. Bombardier Transportation has also entered the growing tram market in China through its technology-licensing
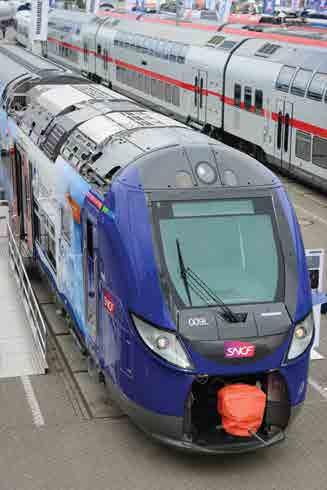
agreement with CSR Nanjing Puzhen Rolling Stock Co. Ltd. (CSR Puzhen). So far, CSR Puzhen has won orders for 18 low-floor trams and 15 catenary-free low-floor trams using BOMBARDIER FLEXITY 2 technology.
Furthermore, as part of a consortium Bombardier Transportation recently entered into a contract valued at approximately $4.1 billion with the State of Queensland, Australia, for a New Generation Rolling stock Project. The group’s share of the contract, involving the supply of 75 EMUs, the construction of a purpose-built maintenance centre and 30 years of maintenance services, is valued at $2.7 billion.
Bombardier Transportation has been recommended as the winning bidder for the Crossrail rolling stock and depot contract in the United Kingdom.
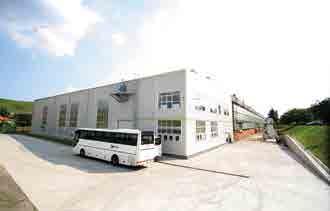
New Bogie Technical Centre
Bombardier continuously invests in new technologies. One of the biggest investments in 2014 was in its new Bogie Technical Centre (BTC). “This Bogie Technology Centre confirms the leading position of Bombardier in terms of bogie technology and will ensure that we continue to pave the way in terms of new developments and technology. The BTC also gives us the possibility to do much more upfront testing,” adds Mr Lievens.
The Bogie Technical Centre is a long-term project. The first step will combine a Test and Validation Centre with a Business Unit hub welcoming international engineering and associated functions to come together and work on the innovations and products of the future in a modern, innovative and

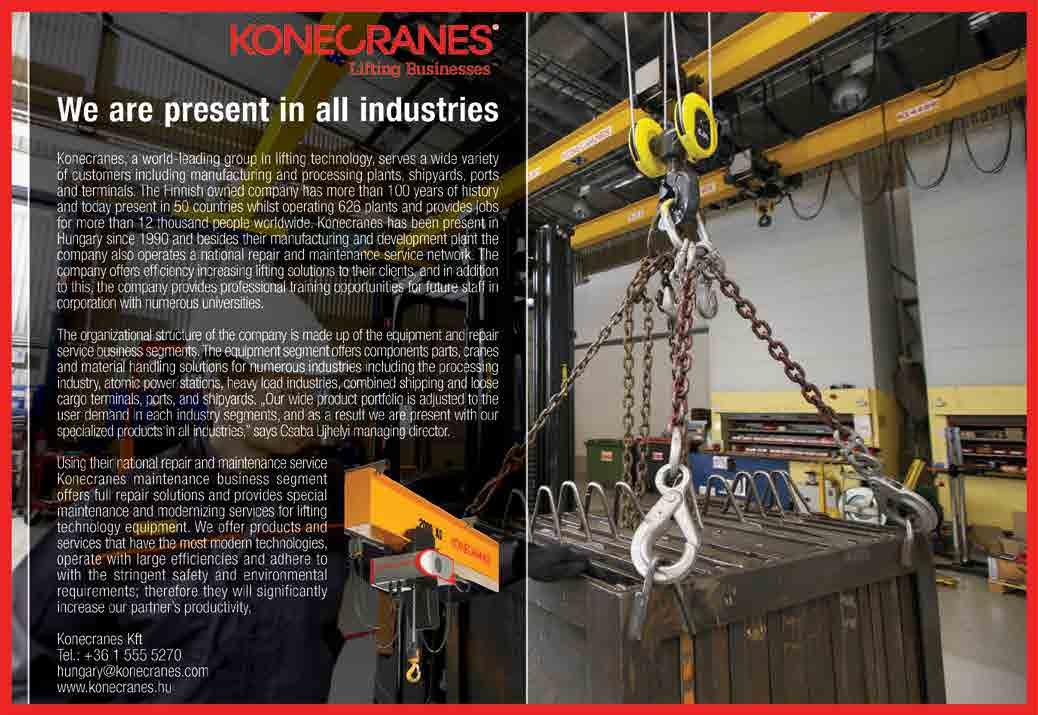
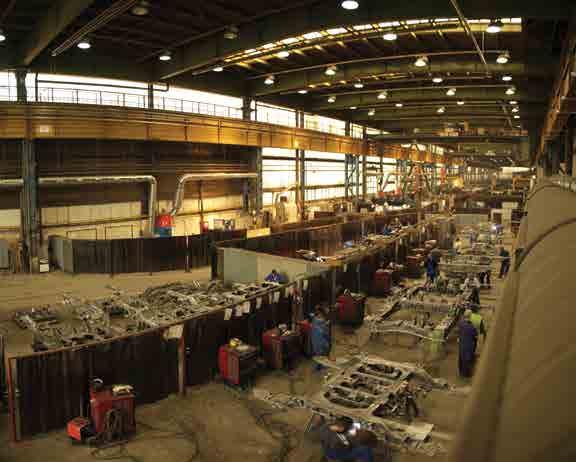
open landscape office. It will invite people from different sites and functions, customers and suppliers to cooperate and communicate. The Bogie Technical Centre will also be the link to the outside world, a place known by customers, suppliers, certification bodies and the academic world. It should attract new employees and new ideas. “Bombardier is No.1 in bogies and aims to remain in this position. The BTC will create a substantial competitive advantage and bring the necessary tools to the engineering experts to develop even more reliable and safer FLEXX bogies meeting the requirements of the future.” n
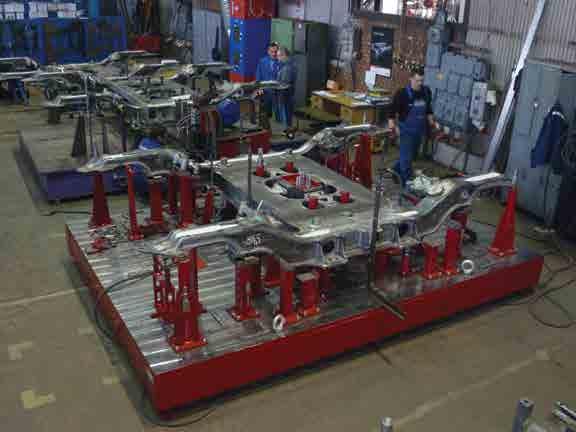
AKG Alföldi Kohászati és Gépipari Zrt Manufacturing of steel castings in various material composition, carbon steel, low-alloyed, alloyed, heat resistant and stainless steel, in the weight range between 15-2500kg.
Machining shop with NC and CNC machining centers and audited welding shop with welding subassembly.
As the supplier of the leading railway manufacturers in Europe we have all the necessary certifications.
Certificates: ISO9001, IRIS Rev2, 15085-2 CL1, 3834-2, AD2000 Merktblatt W0. Customer Audits: DB HPQ, SNCF, MÁF Gépészet, PED 9723/EC 0525 Modul H
Po. Box.: 5901, Orosháza, PF85, Hungary Tel.: +36-68-510-420 Fax: +36-68-510-450 Email: akg@akgrt.hu Web: www.akgrt.hu