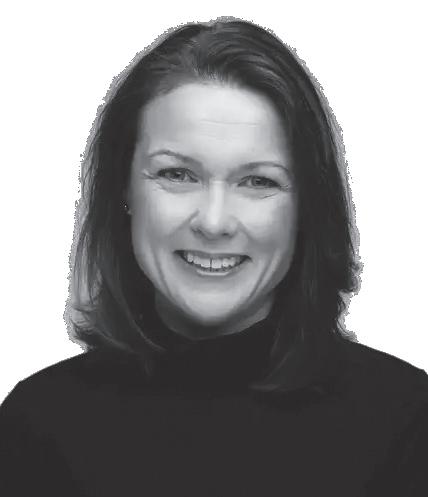
17 minute read
PPE PPE
By Marie O'Mahony, Smart & Advanced Textiles Correspondent, IFJ
olly Morris is a rare individual, holding dual professional accreditation across both surgical and medical textile industries. Morris is a hand and wrist surgeon specializing in the management of paediatric and congenital hand differences whose resume includes working at the Pulvertaft Hand Centre (UK) and membership of the Green Surgery Oversight Committee. In the report “Green Surgery – reducing the environmental impact of surgery care” commissioned by the UK Health Alliance on Climate Change in collaboration with the Royal College of Surgeons she urges: “ We must also work with our procurement teams, industry partners throughout the medical supply chain, and supporting services (including facilities and estates, instrument and linen reprocessing, and waste facilities), to optimize emissions associated with use of surgical products.”
Her presentation at the Emerging Technologies Conference, held during AT EXPO 2024, focused on the environmental impact of surgical procedures looking at PPE and other medical textiles in particular. For a largely textile audience this was a unique perspective and opened to question many of the medical decisions around use, reuse and even repair that many, including this interviewer, had thought sacrosanct.
IN THIS ISSUE: HOLLY MORRIS
Consultant Hand and Wrist Surgeon Fellow of Textile Institute (Medical Textiles)
International Fiber Journal: Holly, thank you for taking this time to answer some questions for IFJ. I would like to begin with a point from your presentation that highlighted the impact of the health care sector on global pollution you cited 20-30% thought to originate in hospital operating rooms. How did it get to be this bad?
HM : In the 1990s, it became very sexy to have disposable garments, gowns and drapes because there was a belief that they were better for infection prevention and it was also cheaper because you didn’t have to launder. But nobody really considered the environmental footprint. Studies are now estimating that operating suites in North America and the UK during a typical operation produce a carbon footprint of 146-232 kg CO2e, that is comparable to emissions associated with driving 400-650 miles in an average petrol car. In the American private healthcare sector it was often seen as an advantage to have a new thing for every patient, while in the public/UK National Health Service (NHS) this was less so because of budget constraints.
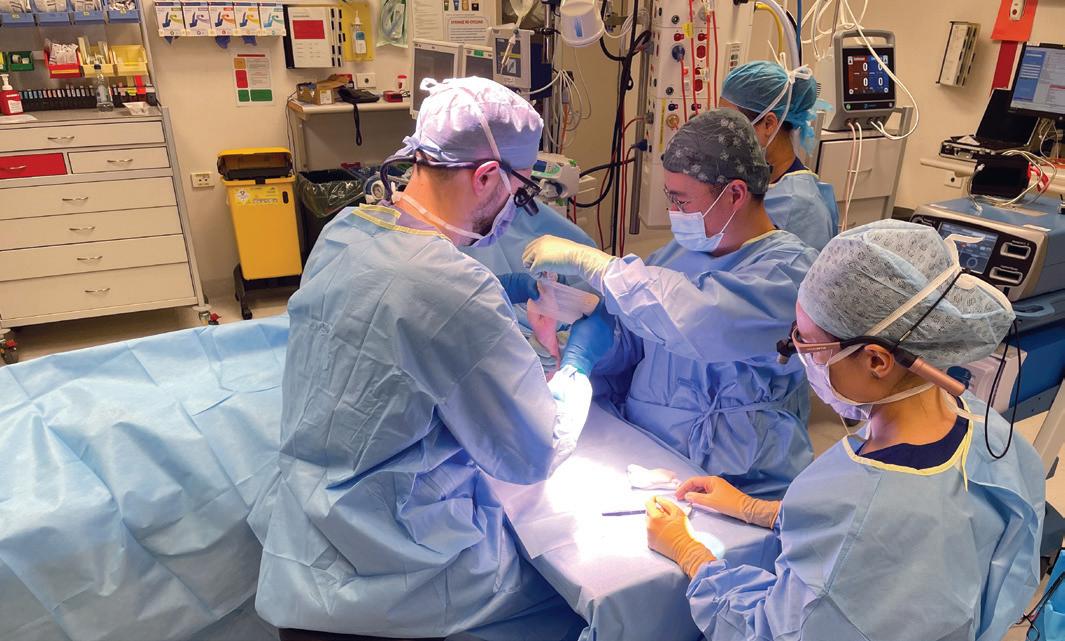
IFJ: Are medical textiles a particular problem?
HM : Medical textiles have become the fastest growing sector of the technical textile industry, worth around $13 billion in 2020, growing to $33 billion in 2023, with the global orthopaedic market valued at $45 billion back in 2019. Global emissions from the health systems stands at 4.4%, higher than a sector such as aviation which comes in less at 2.5%. Taking the example of the British NHS carbon footprint, we see around 65% coming from medicines, equipment and the supply chain with the next highest figure, 15% coming from energy, water and waste. Medical textiles account for 14-31% of healthcare waste. This includes a really broad range of materials, mostly manufactured from synthetic fibres and includes implantables, personal and protective equipment (PPE), incontinence products, smart textiles and even components of devices for environmental control, for example air filters etc.
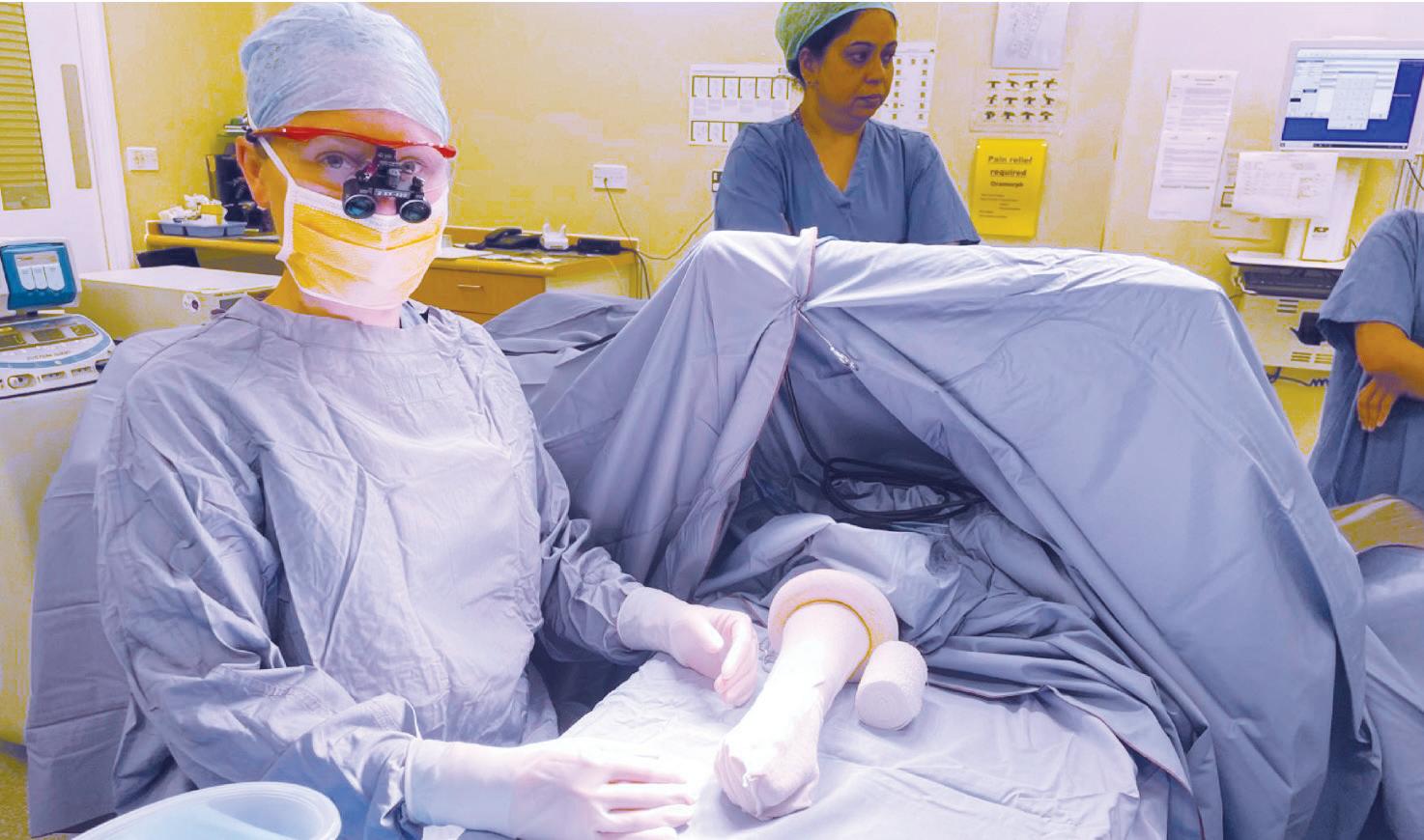
IFJ : Medical and hospital staff as well as patients need to be safe, do you see a way that this can be done with less impact on the environment?
IFJ : Do you think that there is sufficient guidance available on repair and recycling?
HM: Much of the current guidance is pretty archaic and really needs to be revisited both on repair and recycling. Studies have shown that patching a hole in a surgical gown or drape does not increase the risk of contamination and patient infection. Disassembly is another consideration both for repair and the recovery of useful portions that might be reused in the healthcare system or elsewhere. Design plays an impor- tant role in the carbon footprint of an item as it impacts on construction, number of pieces in the garment or unit, type of seaming and material selection. It’s worth remembering that the full cost of an item needs to be considered when deciding whether an item should be repaired, this include energy, chemical and water use. I see so many items that just need a small repair in order to be reused but we need to have systems in place to make it happen.
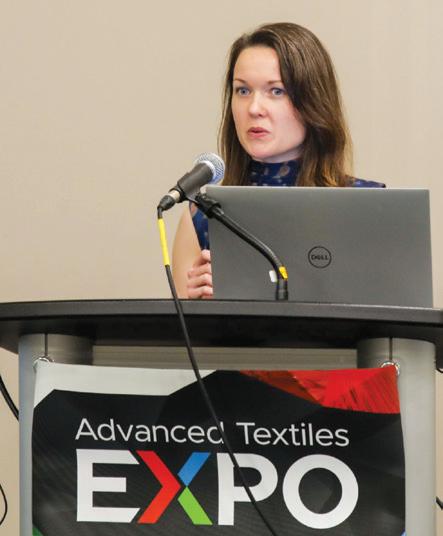
HM: The pandemic created unprecedented demand for medical textiles, particularly PPE. But it also highlighted the sheer quantity of material and waste being generated, much of it after a single use. This is now being looked at in terms of financial and environmental cost, with many countries now looking to encourage greater use of reusable drapes and gowns over disposable ones. One of the issues that needs to be addressed is the supply chain, and laundry in particular. Another is recycling and there is a hesitation in accepting surgical linens for recycling because of the fear that it will be heavily contaminated. A system of laundering and sorting linens after their final use would be one way of mitigating this risk. Putting the right systems in place would help to reassure stakeholders immeasurably.
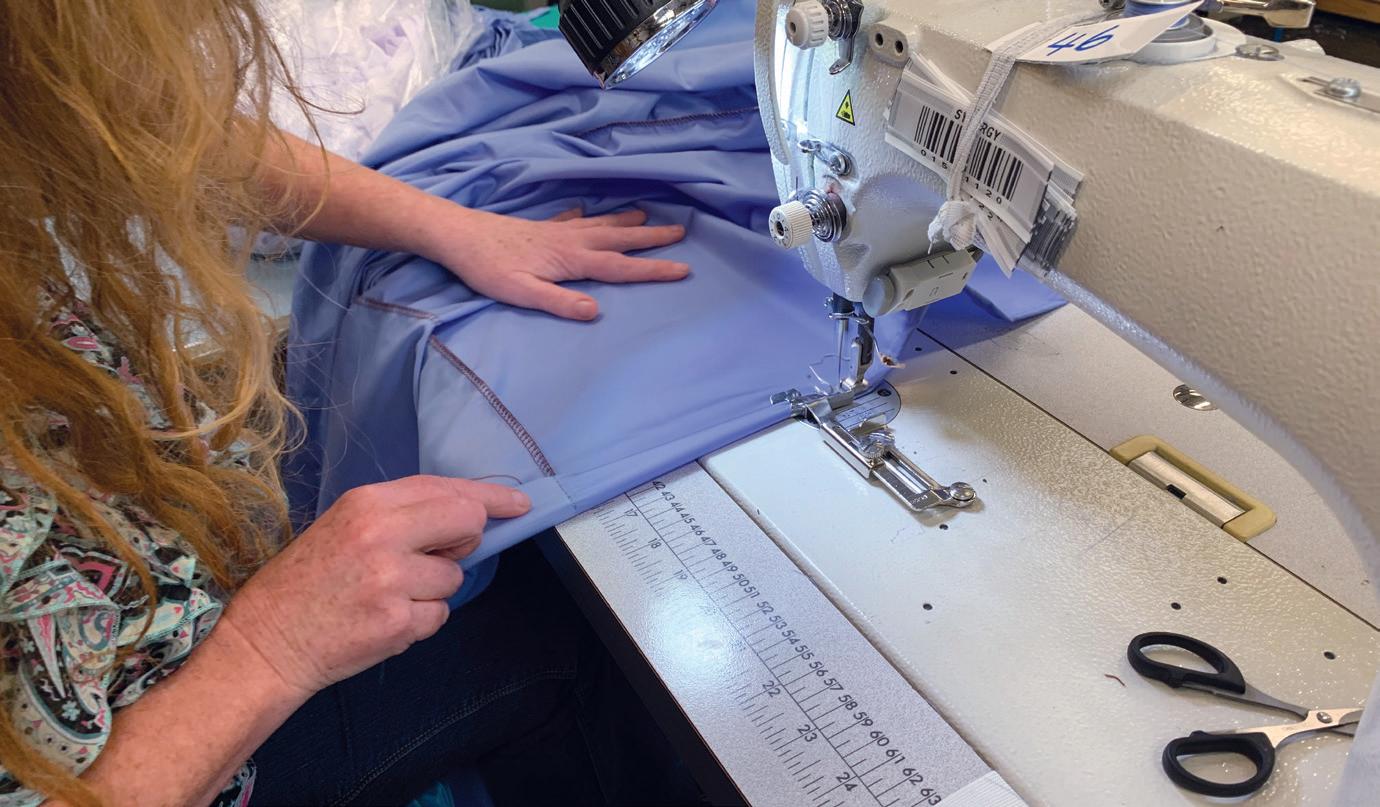
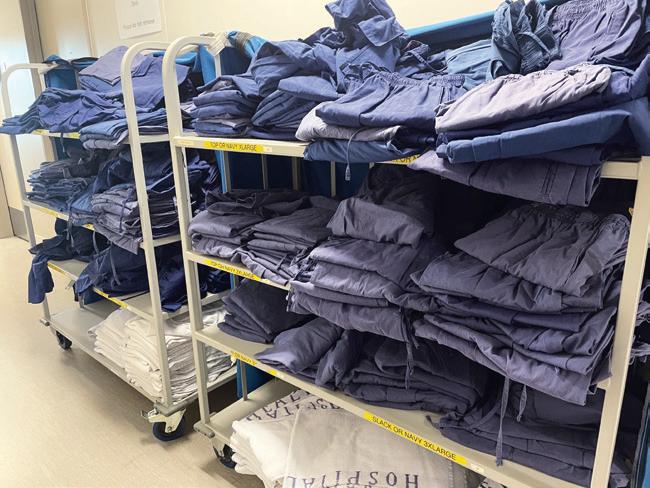
IFJ : Do you see stringent medical standards as a major obstacle?
HM : There is a lot that can be done simply looking at behavior changes during surgery. Clinicians can evaluate how they drape their patients and assess whether they can reduce what they are using. It isn’t just drapes but also the equipment we use. Only opening the items that we use reduces waste and the need for reprocessing or disposal. At a hospital level, a change to reusable textiles such as theatre hats, sterile gowns, patient drapes and trolley covers would also improve the carbon footprint.
IFJ : You have said that 70% of emissions are primarily derived from the health care supply chain. Can you unpack that a little and indicate where there might be easy gains to be made here?
HM: The manufacture of items, the transport of these and the processing of effluents (air/waste water) all generate emissions. This area is harder to directly control as the supply chain is large. I see laundry as an area where easy gains might be made on this. Clear guidance on optimising machine loading would certainly yield benefit. This should look to ensure the correct weight and ratio of textiles, factoring in the level of dirt and careful mixing so that heavily soiled linens are not being put together with lightly used ones. The use of environmentally preferable detergents and filters to capture microfibers would also bring benefits. Looking beyond the amount of energy to focus on renewable energy sources would also be good. Time and tempera- ture alternatives for thermal disinfection can also be examined more closely. Currently there is work underway to revise and update the laundering guidance used within healthcare in the UK.
IFJ: In an academic paper earlier this year you claimed that there are lessons to be learned from the fashion-clothing retail supply chains, can you elaborate on this?
HM : My clinical practise is based in the Derby. Derbyshire was home to the great British fashion designer Vivienne Westwood who was well known for being a climate change activist – perhaps there is something in the water! It’s all too easy to dismiss the fashion sector as irrelevant but I see a lot that we might learn from the complex supply chains and relationships that the fashion industry has in place, particularly with the interest in reducing fast fashion and the disposal or recycling of the end product. To begin with, we must be aware that the stories of labor abuses and sweatshops are not confined to fast fashion. A report by the British Medical Association identified that there is statesponsored Uyghur and North Korean forced labor found in the manufacture of PPE in China and forced labor of gloves in Malaysia and Thailand. One of the most important lessons I see is the need for oversight and accountability. Nothing operates on trust and you see retailers not just checking inventory, but checking all aspects from design to production visit- ing factories and warehouse facilities to see for themselves. This kind of connectedness generates better understanding on both sides that goes beyond the specification, and helps identify where and how improvements can be made.
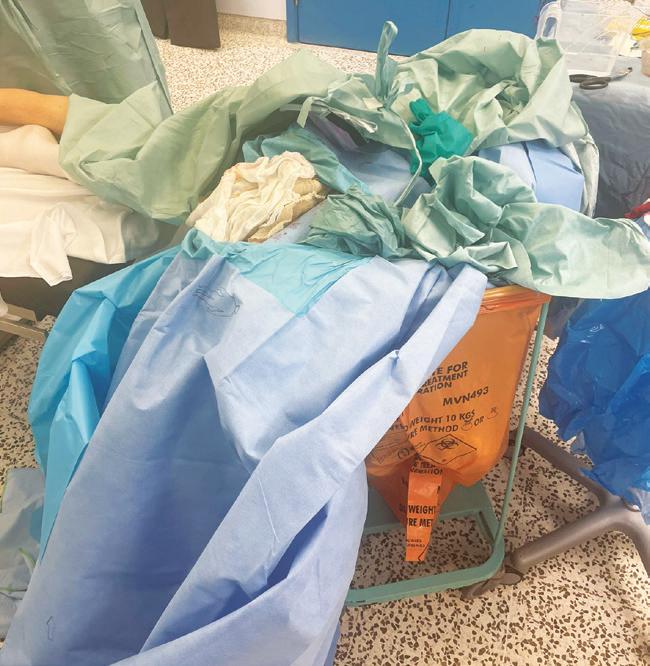
IFJ: Are you seeing any new fiber or fabric developments that look promising?
HM: The new developments that I am most excited by are those that can be used to reduce the environmental impact of existing medical textiles. We need to be looking at whether other methods of laundry are viable, such as polymer bead laundering which are more effective. This method uses only around a third of the water that a conventional commercial laundry machine uses. The energy use drops by an estimated 88% because no hot water is used and 15% more water is removed so that there is less drying needed and an energy saving to be made there also. Microfiber pollution filters are essential. Currently available options can capture more than 99% of microfibers with their filtration technology. When you think that around 500,000 tons of microfiber flows into our oceans each year that offers quite a difference.
IFJ : Any final thoughts on how to move things forward?
HM: During COVID everything went up in price and that has a legacy. The problem is that procurement are focused on the upfront cost only, not the disposal cost. If they had to take account of the full lifetime cost then strategies like repair, reuse, laundry etcetera, more sustainable medical textiles would come out cheaper. If you were to add a carbon tax to that then the argument becomes even more compelling.
Dr. Marie O’Mahony is an industry consultant, author and academic, the author of several books on advanced and smart textiles published by Thames and Hudson. She can be contacted at marie.consultant@ gmail.com or https://www.linkedin.com/in/ dr-marie-o-mahony-94776836.
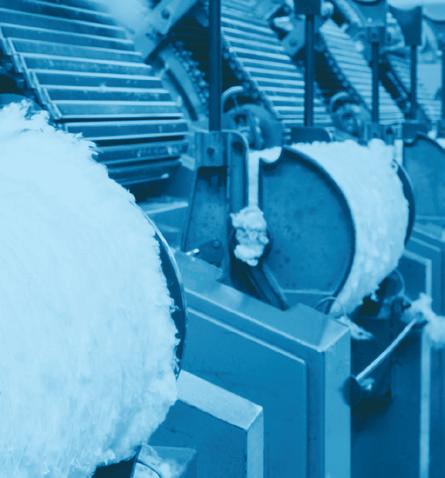
Your Complete Resource to Industry Companies Offering
NEW! THE BUYER’S GUIDE JUST GOT BETTER
Do You Want to Increase Your Company Exposure to Fiber & Filtration Professionals?
YOU GET 3X EXPOSURE IN PRINT GUIDE, DIGITAL GUIDE + SOCIAL MEDIA!
Take advantage of this incredible way to be found among the best of the industry!
w For $495, Standard Company Listings receive:
• Up to 5 categories for a searchable listing + logo for 1 year in online guide
• Print listing + logo with categories listed in IFJ publication
• NEW: Buyer’s Guide link accessible from INDA.ORG website, increasing SEO
• NEW: Promotion of Buyer’s Guide on IFJ Social Media & in the Monthly E-Newsletter
• NEW: Digital Flipbook with clickable links on Home Page of IFJ websites w For $995, Premiere Vendor Category Listings receive all the Standard Company Listings (listed left), with the additional value of:
• Up to 12 categories for a searchable listing + logo for 1 year in online guide
• NEW: New “Premiere Vendors” Buyer’s Guide landing webpage* – only for this category –with clickable company logo
• NEW: Two “Buyer’s Guide e-Promotions” with the logos of all “Premiere Vendors” (clickable) sent to IFJ promo lists
Choose from specialties in over 70 categories! IFJ Buyer’s Guide for International Fiber Journal is printed in the November/December issue (Vol. 6).
The listing runs for an entire year on www.fiberjournal.com/buyers-guide.
TInnovation Continues in 2024 with Quick Pace
By Adrian Wilson, International Correspondent, IFJ
hroughout 2024 there has been an acceleration in approaches to the regeneration of synthetic fibers at industrial scale – and especially PET polyester.
Fantastic work has also continued in developing natural fibers and biopolymers as the raw materials for new circular supply chains, but the growth of such alternatives to PET and other synthetics will only go some way to meeting overall future demand.
The total consumption of all fibers by the global textiles industry is forecasted to climb from 120 million tons in 2023 to 140 million tons by 2030, and at present polyesters, largely PET, account for an estimated 81 million tons of all production.
CiCLO Additive
Alongside schemes for taking both waste PET fabrics and plastics back to polymers and monomers as new raw materials, some true alternatives have also arisen, such as the CiCLO additive of Intrinsic Advanced Materials/Parkdale Mills.
CiCLO is an additive that is applied at the fiber extrusion stage of production to enable the accelerated biodegradation of synthetic fibers. It creates countless biodegradable spots in the matrix of the polymer that enables microbes that naturally exist in certain environments to break down the materials just like they do with natural fibers. All that remains are natural biogases and biomass. The mechanism is only activated under conditions that allow for biodegradation and they will not prematurely deteriorate while in storage or use, just like biodegradable fabrics made from natural fibers like cotton and wool.
Long-term studies have proven that CiCLO PET and also nylon fabrics biodegrade at greatly accelerated rates compared to such fibers without them.
Parkdale Mills has rapidly established a network of over 50 certified fiber and yarn manufacturers to ensure quality assurance and traceability in the supply of CiCLO products and such has been the interest in CiCLO, that Intrinsic cofounder Andrea Ferris has predicted that non-biodegradable PET will be extinct within a decade.
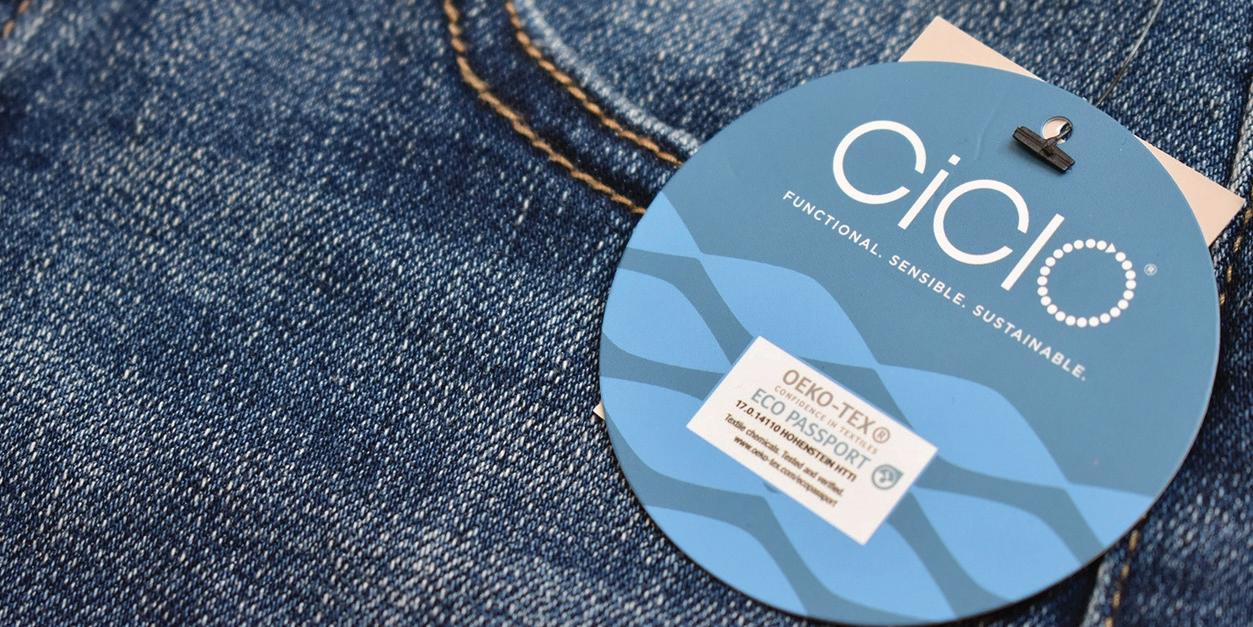
Synthetic Alternatives
OceanSafe, based in Berne, Switzerland, has also been making progress in 2024 with its naNea polymer, as a next generation replacement for PET polyester.
While still itself a synthetic, naNea is inherently biodegradable in water, soil and landfill. In ocean water, 93% of it will biodegrade in just 99 days and it is currently the first and only synthetic material to date to have received the stringent Cradle-to-Cradle Gold certification.
OceanSafe’s polymer is already being turned into fibers and yarns by an extensive list of partners. The resulting fabrics have all the favorable processing and performance properties of PET, yet are circular, biodegradable, compostable and toxin-free. They are also high performing, durable and highly scalable, and as volumes go up, the price for naNea will only come down.
The polymer is a drop-in solution for PET manufacturers and fibers and yarns being made from it can be fully woven or knitted and dyed and finished conventionally.
Compostable Celys
Intimiti Australia has meanwhile been attracting attention with Celys, a certified compostable polyester fiber which is 95.4% compostable in 179 days under industrial composting conditions, as a result of a third chemical monomer introduced into its molecular structure during the polymerization process.
The company has inserted easily hydrolysable and easy-to-break-down ester linkages into the polymer backbone of Celys fiber, to facilitate hydrolyzation and greatly accelerate the biodegradation rate. After biodegradation, all that remains is carbon dioxide, water and biomass.
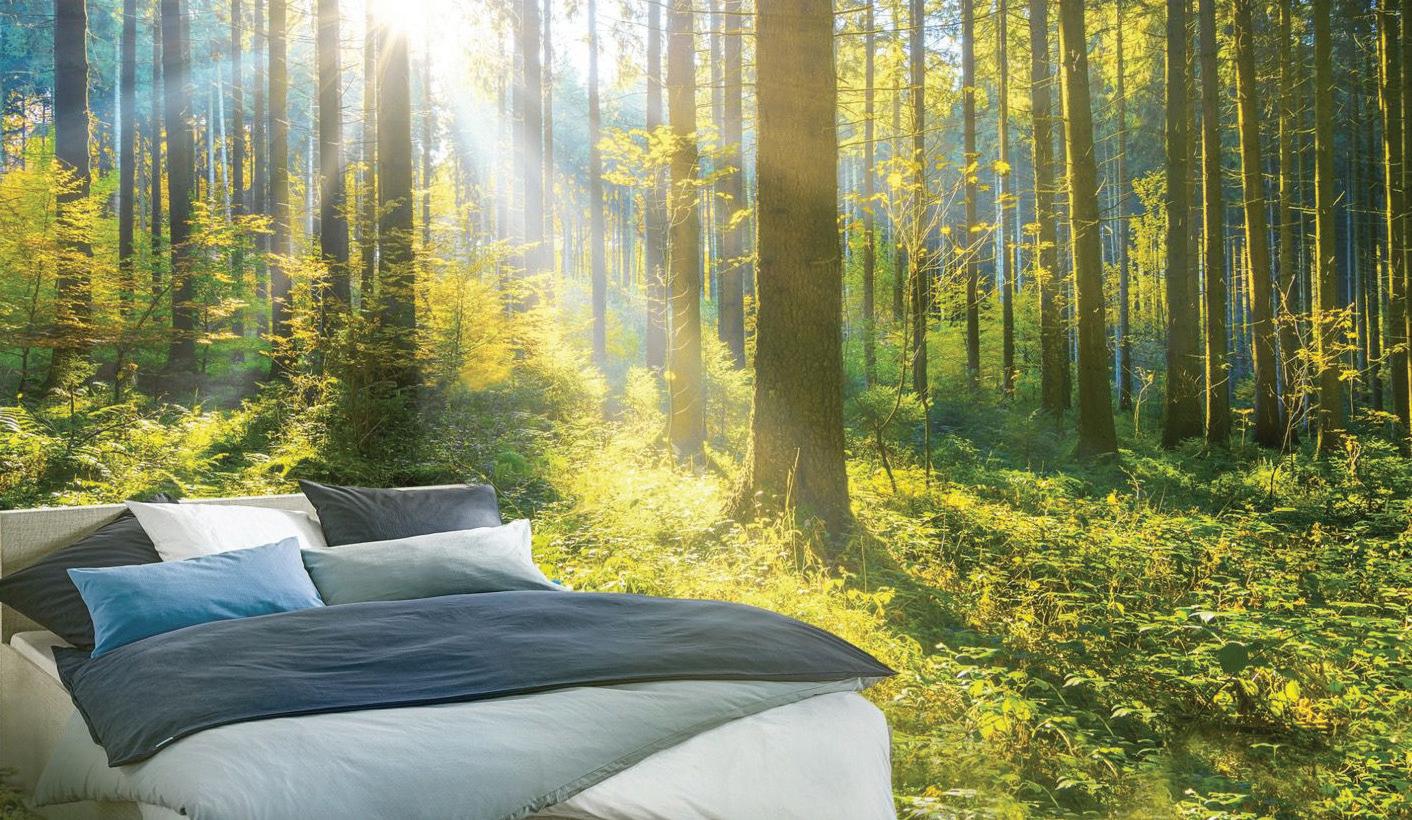
OceanSafe’s naNea is inherently biodegradable in water, soil and landfill.
Reformation is the latest brand integrating Ambercycle’s cycora regenerated polyester into select pieces of its new 1920s-inspired collection. Reformation
Fabric properties achievable with Celys include a soft cotton-like touch, low pill ing, hydrophilicity, low-temperature dye ing, natural wicking and breathability, and quick drying.
Ambercycle
It is in the area of the chemical recycling of synthetic fibers, however, and primar ily PET, that the biggest impact will be made in the years to 2030.
In August, for example, Shinkong Synthetic Fibers, a global polyester manu facturer headquartered in Taipei, Taiwan, announced a strategic $10 million invest ment in Ambercycle’s first commercial plant for producing its cycora polyester made from PET waste.
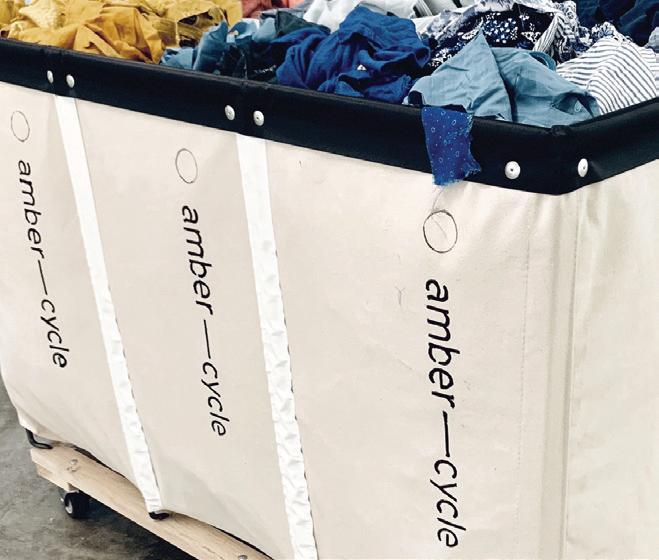
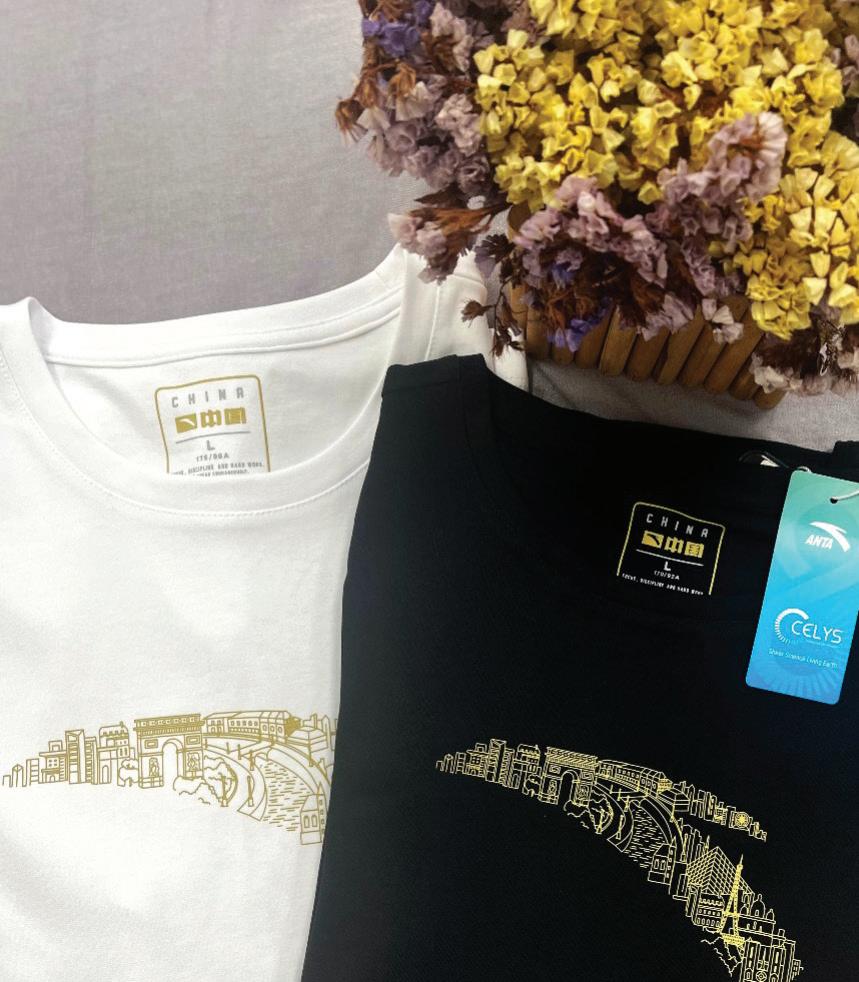
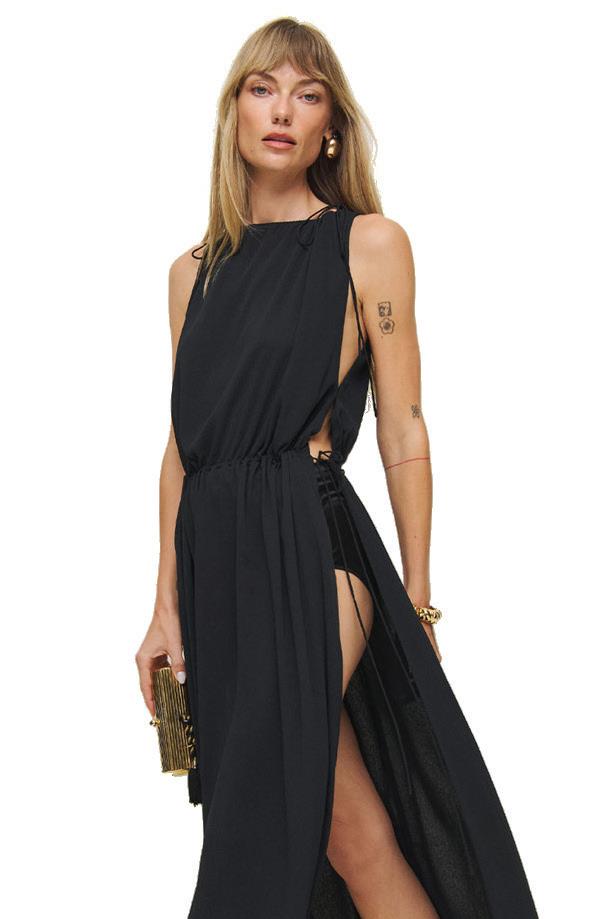
The investment builds on three years of collaboration on Ambercycle’s molecular regeneration technology, with Shinkong providing extensive experience in the premium polyester market.
Ambercycle expects to commence operations at its new industrial facility, with an as-yet unspecified location or capacity,
In June 2024, Hyosung became the first manufacturer in South Korea to introduce Ambercycle’s cycora into supply chains and in the same month, MAS Holdings, a global apparel manufacturing and tech conglomerate headquartered in Sri Lanka, negotiated a three-year off-take agree-
Inditex, the Spanish owner of the leading Zara brand, has signed a three-year agreement to buy a significant portion of the annual production of Ambercycle’s cycora with a value of more than €70 million.
Eastman Methanolysis
Four major methods for reverse engineering PET waste back into its monomer building blocks – methanolysis, glycolysis, hydrolysis and enzymatic recovery – are also rapidly being industrialized. Methanolysis is based on the treatment of polyester polymers with methanol at relatively high temperatures of between 180-280°C and pressures of 20-40 atm, which leads to the formation of the constituent monomers dimethyl terephthalate (DMT) and ethylene glycol.
Making the fastest progress here is Eastman, which in March announced its second molecular recycling plant for hard-to-recycle PET waste will be located in Longview, Texas.
The first plant, at its headquarters in Kingsport, Tennessee, also began initial production in March and is already generating revenue and is on target to earn around $75 million for the company in 2024.
The company’s methanolysis technology is said to break the waste down into the monomer building blocks for polyester that can be used again without compromising performance in a materialto-material high-yield loop.
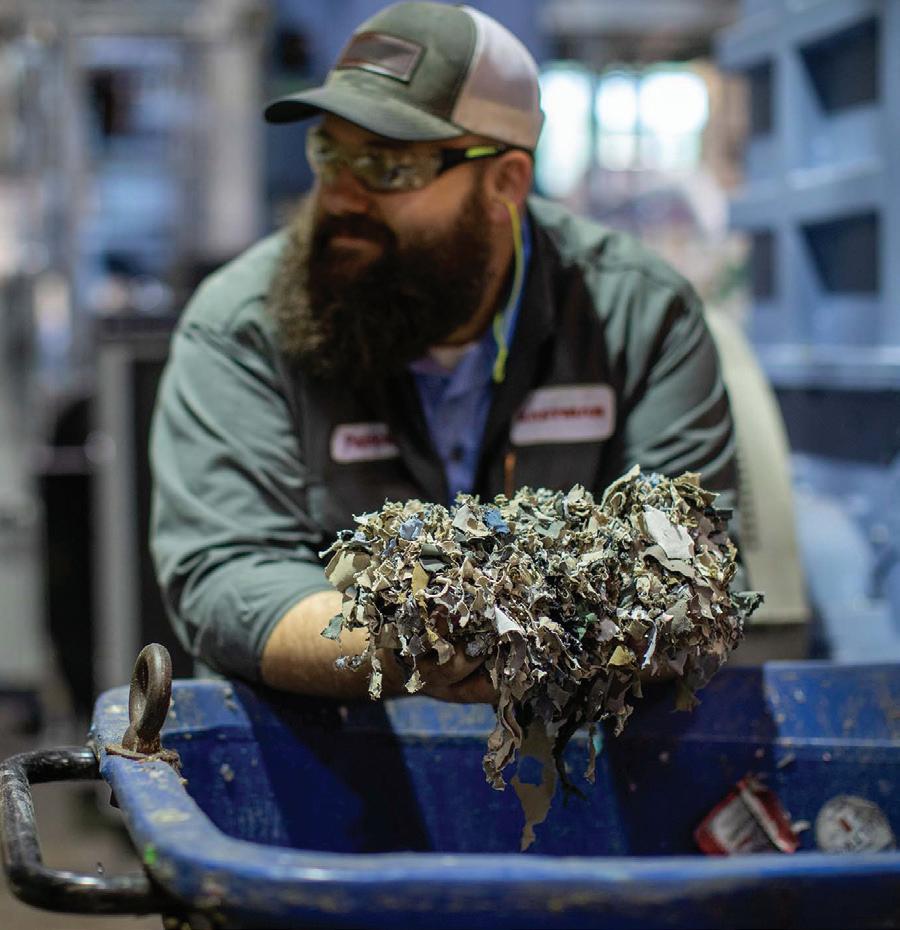
The Kingsport and Longview plants are aimed at meeting Eastman’s ambitious goals of recycling 125,000 tons of polyester by next year, and double that volume by 2030.
In January 2022, French President Emmanuel Macron and Eastman CEO Mark Costa jointly announced Eastman’s plan to invest up to $1 billion in a material-tomaterial molecular recycling facility in Normandy, France. The site will also recycle up to 110,000 tons of hard-to-recycle polyester waste by 2028.
Loop Industries
Loop Industries owns patented and proprietary methanolysis technology that depolymerizes PET plastic and polyester fiber waste, including plastic bottles and packaging, carpets and textiles of any color, transparency or condition and even ocean plastics that have been degraded by the sun and salt. The resulting monomers are filtered, purified and polymerized to create virgin-quality PET resins suitable for use in food-grade packaging and as polyester fibers.
In January 2024, UK-headquartered investment firm Reed Management announced financing of $66 million to enable Loop Industries to proceed with its plans to construct a recycling plant in Saint-Avold, France, with an annual capacity of 70,000 tons.
In May, Loop Industries further announced a joint venture with Ester Industries to establish a $165 million Infinite Loop plant to recycle dimethyl terephthalate (DMT) and mono-ethylene glycol (MEG) from PET waste in India.
Glycolysis
In the glycolysis process, high molecular weight polyester is treated with a glycol such as ethylene glycol to recover polyester monomers for new products.
Making big waves in this field is Syre, a new company based in Research Triangle Park, North Carolina, which launched in March 2024, and by May 2024 had secured a $100 million Series A funding package.
Supported by an offtake supply agreement with H&M, Syre plans to establish multiple plants producing circular polyester across the globe.
The funding round was led by founding investor TPG Rise Climate along with an additional investment from H&M and strategic partners Giant Ventures, IMAS Foundation, Norrsken VC and Volvo.
It will finance the construction of a blueprint plant in the USA which will be up and running later before the end of 2024, as well as preparations for the first two gigascale textile-totextile recycling plants. Syre has shortlisted Vietnam and Portugal or Spain as the locations for its first two plants.
The equity funding will further allow Syre to fully acquire the patented technology of North Carolina-based Premirr that is the centerpiece of the company’s textile-to-textile recycling solution.
Hydrolysis
Hydrolysis involves the use of water to break the ester bonds of polymers down into their constituent monomers. Hydrolysis monomer recovery processes have been developed for both PET and for polyamide.
Danville, Virginia-headquartered new fiber tech pioneer Circ is at technology readiness level (TRL) 7 and aiming to rapidly get to industrial scale with its process that can accommodate polycotton material in any blend ratio and any color, including post-consumer waste, as demonstrated through its partnership with Patagonia.
Its IP begins with a hydrothermal reaction initially developed for biofuels and now adapted for textiles.
In the process, the polyester is broken down through depolymerization by hydrolysis, when the fiber separation also occurs. When the polyester is broken down into monomers it dissolves into the liquid and results in two streams – the solid stream with just the cotton that’s left over and the liquid stream, which not only contains the polymers but also the dyes, finishing chemistries and coatings.
The cotton cellulose is further tuned so that it can be used in existing processes for manmade cellulosic fibers and from the liquid there is extraction and purification of the monomers, including the PTA (purified terephthalic acid).
“We’ve developed a purification method working with Professor Alan Myers of MIT which we’re very proud of because 99.9% purity here won’t necessarily work,” explains the company’s president and CEO Peter Majeranowski. “You have to make sure you screen out certain impurities that would prevent the PTA – which makes up roughly 70% by weight of polyester – from repolymerizing.”
Also operating recycling plants with hydrolytic processes currently at pilot scale, but with scale-up ambitions, are DePoly (Sion, Switzerland), GR3N (Lugano, Switzerland) and RevolPet (Braunschweig, Germany).
On the polyamide side, Italy’s Aquafil, headquartered in Arco (Trento) Italy, has a well-established plant for recycling carpets and fishing nets into new polyamide monomers in Slovenia, with an annual capacity of 35,000 tons. Recycled products are marketed under Aquafil’s Econyl brand.
Enzymatic Recycling
Carbios has established a solvent-free enzymatic depolymerization process for recycling polyester and is currently constructing a €54 billion plant in Longlaville, in the Grand-Est region of France. This is expected to start delivering significant quantities of new recycled feedstocks in 2026.
Carbios is developing a licensing model for the technology which is already bearing fruit.
In July 2024, Carbios signed an agreement with Zhink Group to establish a new recycling plant in China. The two companies are planning a longterm partnership beginning with a first licensing contract to build a plant with a minimum annual processing capacity of 50,000 tons of prepared polyester waste. China is the world’s largest PET producer and also currently accounts for 78% of all PET transformed into r-PET, including PET bottles.
In August SASA of Turkey entered discussions with Carbios to license a polyester biorecycling facility with an annual capacity of 100,000 tons that it will build and operate at Adana site.
A new $1.5 billion SASA Polyester plant for PTA is poised to come on stream this year in Adana, with an annual capacity of 1,750,000 tons.
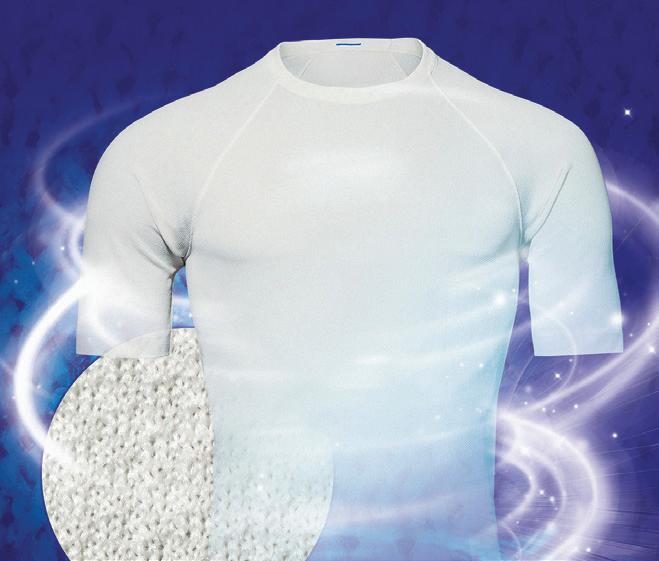
This will instantly position Turkey as a net exporter of polyester, rather than a net importer. SASA has pointed out that raw materials self-reliance is how both South Korea and China strengthened, stabilized and significantly grew their textile industries.
Milestone
In a significant textile industry breakthrough reported in October, Carbios and its fiber-to-fiber consortium brand partners On, Patagonia, Puma, PVH and Salomon, unveiled a plain, white polyester t-shirt that has been produced from 100% mixed and colored textile waste.
The t-shirt’s production began with all consortium members supplying rolls and production cutting scraps to Carbios in Clermont-Ferrand, France. The waste consisted of mixed blends of polyester with cotton and/or elastane, as well as various treatments such as durable water repellents and dyes, making them extremely complex to recycle using conventional methods.
The collected waste was deconstructed into its original PTA and MEG monomers at the Carbios pilot facility.
The resulting monomers were then repolymerized, spun into yarn and woven into new fabric by external partners, demonstrating their seamless integration into existing manufacturing processes.
The resulting t-shirt made from 100% textile waste meets the quality standards and sustainability objectives of the apparel brands of the consortium.
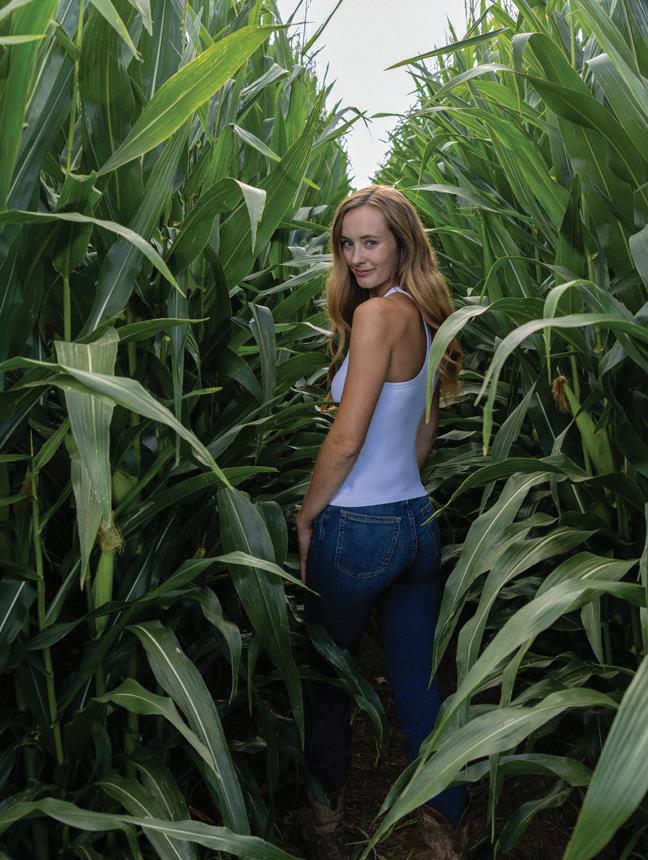
Lycra EcoMade
Finally, elastane, however valuable in providing stretch and comfort in garments, has been identified as a significant obstacle to many recycling operations, but in the first half of 2025, The Lycra Company will launch large-scale production of a new renewable elastane – Lycra EcoMade. Bio-derived Lycra EcoMade fiber is made with 70% renewable content and certified under the USDA Bio-Preferred program. Garments and fabrics made with it deliver equivalent performance to those made with original Lycra fiber, and no re-engineering of fabrics, processes or garment patterns is required.
“There’s no need to sacrifice performance for renewable content with bioderived Lycra EcoMade,” says Nicolas Banyols, chief commercial officer of The Lycra Company. “We are committed to transitioning to renewable resources as a key part of our sustainability strategy and it can help brands and retailers reduce their environmental impact too.”
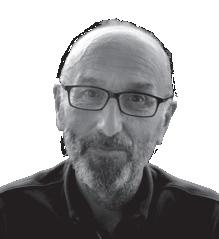
Adrian Wilson is an international correspondent for International Fiber Journal . He is a leading journalist covering fiber, filtration, nonwovens and technical textiles. He can be reached at adawilson@gmail.com.