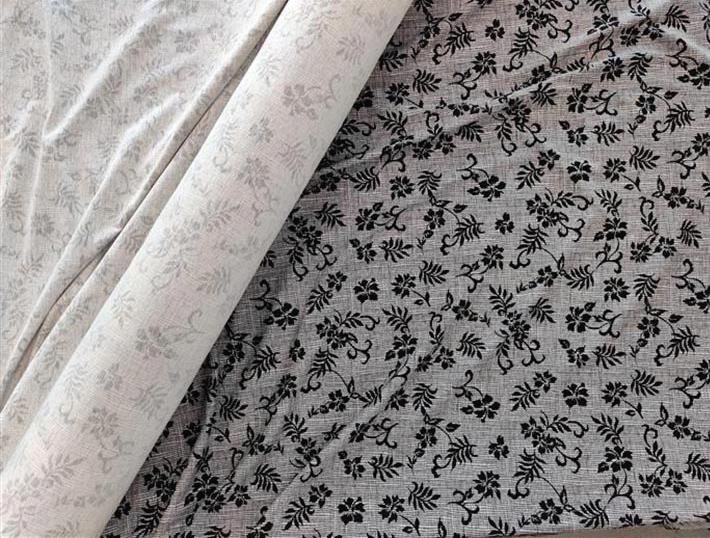
3 minute read
Archroma Introduces Breakthrough in Bio-Based Textile Printing
Archroma, a global supplier of specialty chemicals towards sustainable solutions, recently introduced the NTR Printing System to make bio-based pigment printing commercially possible for the first time. Based on renewable raw materials and designed for safer chemistry, it helps apparel and textile brands reduce their environmental footprint while producing brilliant black shades on garments that deliver both comfort and durability.
Bio-based pigment printing is an emerging technology that is attracting major interest from brands that want to use pigments derived from natural sources, such as plants, in the production of environmentally conscious textiles. Until now, however, bio-based pigments have not delivered color fastness that is comparable to synthetic pigments, and color quality and production performance have not been sufficient to support commercial-scale production.
Archroma’s NTR Printing System is the first to utilize renewable feedstock across pigment dispersion, binder and fixing agent. Crucially, it ensures good wet-rubbing and dry-rubbing fastness, with outstanding softness on all kinds of fabrics. Furthermore, it is suitable for most popular application technologies, including printing, coating and continuous pigment dyeing, with outstanding runnability for production efficiency.
The result of more than two years of research and development, the innovative new NTR Printing System required Archroma to create customized binding and fixing agents to ensure fastness for the pigment black dispersion comparable to current petroleum-based printing systems. All three printing elements are partially based on renewable feedstock to reduce reliance on non-renewable petrochemicals. Archroma also developed the new system to avoid toxic input streams and impurities, including formaldehyde. Two successful bulk trials were conducted with Textprint S. A. and Jeanologia. www.archroma.com
Teijin Frontier Launches OCTAIRTM High-Performance Insulation Fiber
Teijin Frontier Co., Ltd., announced it has launched OCTAIR ™, a new premium brand of insulation fiber for bedding and apparel. This innovative product utilizes a short-cut polyester fiber featuring a unique, hollow, 8-fin cross section with radiating protrusions. OCTAIR ™ meets growing demand for alternatives to natural feathers, which is experiencing declining production volumes and rising costs.
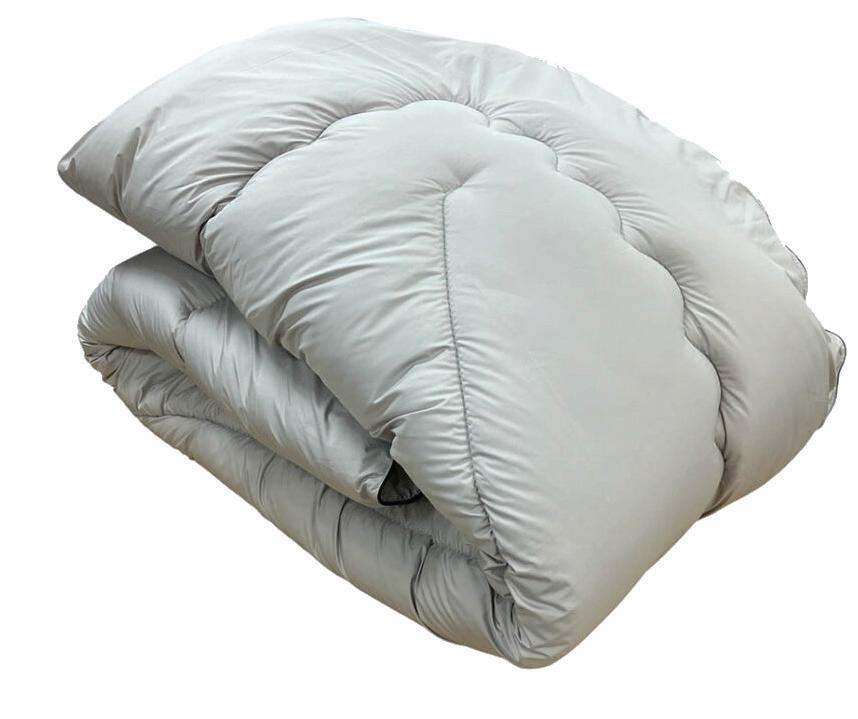
The company plans to expand its use across a wide range of materials. One of them is SOLOTEX™ OCTAIR™, an insulation material that incorporates polytrimethylene terephthalate (PTT) fibers along with OCTAIR™ fibers. In SOLOTEX™ OCTAIR™ insulation, the OCTAIR™ fibers’ hollow structure with an 8-fin cross section creates air pockets that provide excellent warmth, loft and lightweight properties. As a result, SOLOTEX ™ OCTAIR™ delivers insulation performance equivalent to the same weight of down (based on tests using 30cm square mini quilts).
To enhance the SOLOTEX™ OCTAIR™ fibers, the PTT fibers’ unique helical molecular structure offers a soft texture, elasticity and good shape retention. Additionally, the tips of the fibers are soft, do not spread out easily and reduce tangling, making the blowing process for filling comforters and clothing smoother than with conventional polyester insulation. This new insulation also offers sustainability benefits through the incorporation of plant-based raw materials. www.teijin.com
Paradise
Textiles Unveils First Garment with Kintra Bio-Synthetic Fiber
Paradise Textiles, the material science hub of Alpine Group, has partnered with Kintra Fibers, a leader in bio-based fiber innovation, to create the first garment using Kintra’s groundbreaking proprietary bio-synthetic material. This lightweight jacket serves as a proof-of-concept, representing a crucial milestone in Kintra’s journey toward commercial viability as a sustainable alternative to traditional fossil-based polyester.
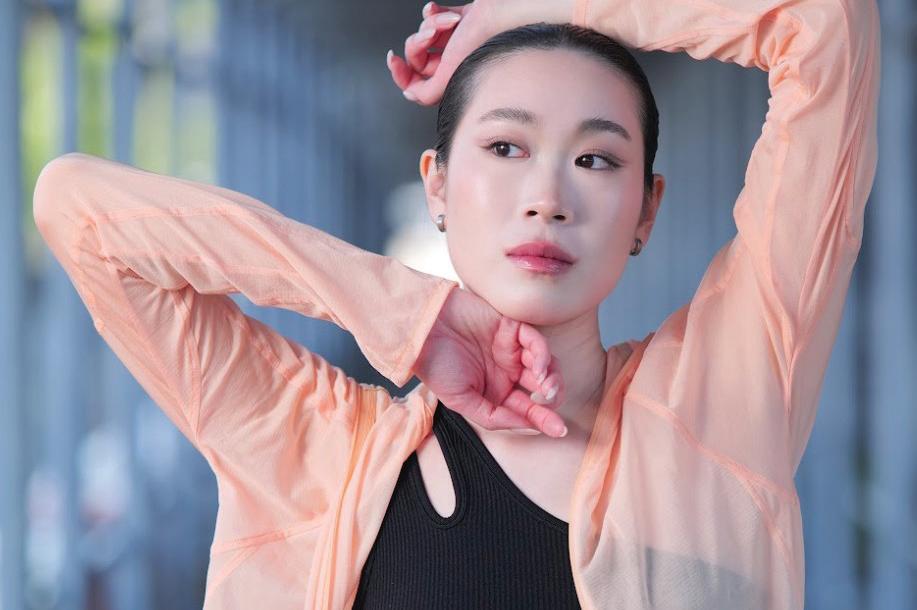
Kintra’s proprietary bio-synthetic material provides a sustainable alternative to polyester. Made on the same equipment as conventional polyester, Kintra’s resin is estimated to reduce emissions by 95%, water usage by 30%, and energy consumption by 20%. These advancements are achieved with the use of bio-based inputs, lower processing temperatures, and efficient production methods. Upon the completion of a full life cycle assessment, the company expects to see continued energy savings and reduced Scope 3 emissions in downstream processes, including yarn spinning, dyeing, and finishing.
In terms of performance, testing conducted by Paradise Textiles has shown that Kintra yarns are on par with polyester with regard to strength, yet are four times softer, and have twice the stretch, resulting in a unique fabric profile. Fabric testing demonstrated that Kintra knits and wovens are on par with, or surpass, the polyester benchmark in strength and durability tests including tensile strength, seam slippage, tear strength, and abrasion and pilling resistance.
The jacket above highlights Kintra’s compatibility with existing textile production machinery and dyeing processes, making it an ideal choice for brands seeking to transition to sustainable materials seamlessly. www.alpinecreations.com