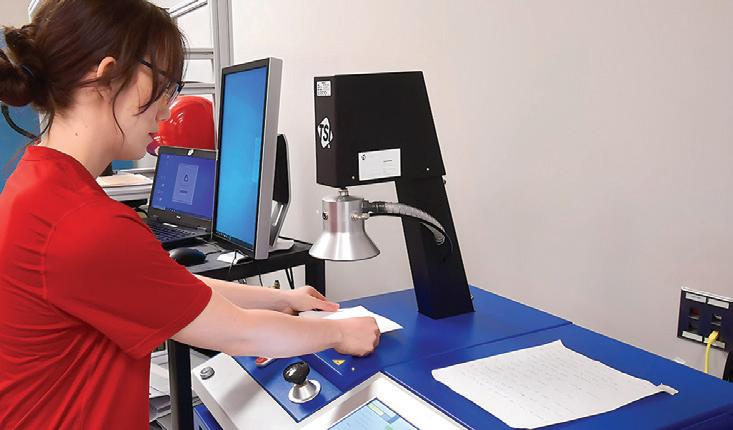
5 minute read
NOTES TECH
University at Buffalo: Researchers Develop Heat-Resistant Nanoporous Membrane
Industry has long relied upon energy-intensive processes, such as distillation and crystallization, to separate molecules that ultimately serve as ingredients in medicine, chemicals and other products.
In recent decades, there has been a push to supplant these processes with membranes, which are potentially a lower-cost and eco-friendly alternative. Unfortunately, most membranes are made from polymers that degrade during use, making them impractical.
To solve this problem, a University at Buffalo-led research team has created a new, sturdier membrane that can withstand harsh environments – high temperatures, high pressure and complex chemical solvents – associated with industrial separation processes.
Made from an inorganic material called carbon-doped metal oxide, it is described in a study published Sept. 7, 2023, in Science
“The processes of separating molecules – whether for water desalination, the production of medicine or fertilizers – use an incredible amount of energy,” said corresponding author Miao Yu, SUNY Empire Innovation Professor in the Department of Chemical and Biological Engineering, School of Engineering and Applied Sciences.
“What we have developed is a technique to easily fabricate defectfree, strong membranes that have rigid nanopores that can be precisely controlled to allow different-sized molecules to pass through,” added Yu, a core faculty member in the UB RENEW Institute.
To create the membrane, the research team took inspiration from two common, but unrelated, manufacturing techniques. The first is molecular layer deposition, which involves layering thin films of materials and is most often associated with semiconductor production. The second technique is interfacial polymerization, which is a method of combining chemicals that is commonly used to create fuel cells, chemical sensors and other electronics.
ISO-Accredited Filtration Testing Lab
NWI’s Filtration Testing Lab includes ISO 17025-accredited test methods, as well as a full suite of filtration testing equipment.
p The images above detail how the membrane forms. The three vertical images on the left show the bonds between titanium tetrachloride (metallic reactant) and ethylene glycol (organic reactant). The center image shows how the two materials combine. The images to the right side show the membrane without pores (dense OHF) and the membrane after carbon has been removed to create pores (porous CDTO). Illustration courtesy of UB
“These methods are not new,” says Sengupta, “however the manner in which we apply them is, and that is the key to creating our new nanoporous membranes.”
In experiments, researchers merged two low-cost reactants – liquid ethylene glycol and gaseous titanium tetrachloride – on an aluminumbased support. Within minutes, the reaction created a thin film.
To create the nanopores, they applied heat to the film. The heat burns off carbon, creating tiny, microscopic holes for molecules to pass through. The size of the nanopores can be anywhere from 0.6 to 1.2 nanometers in diameter – as determined by the calcination gas environment, as well as the amount and duration of heat.

The method allows researchers to avoid a nagging problem – small holes merging into larger ones, thus making them more porous than intended – by creating polymer-based membranes. www.buffalo.edu
The Nonwovens Institute (NWI) announced its newly expanded Filtration Testing Lab, featuring services for facemasks and respirators, along with filter media for automotive, HEPA and HVAC applications. Importantly, NWI’s Filtration Testing Lab is A2LA Accredited for ISO 17025*, enabling it to meet NIOSH requirements for testing materials used in respirators, and it is outfitted with equipment to perform ASTM F2299 testing for the measurement of Particle Filtration Efficiency (PFE) at 0.1 microns.
In addition to NWI’s Filtration Testing Lab, NWI offers a fully equipped Analytical and Physical Testing Lab with more than 60 tests available for nonwoven materials. NWI also offers lab- and pilot-scale capabilities for Fiber Spinning, Meltblown, Spunbond and Hydroentangling, Staple/Carded Nonwovens, among others. www.thenonwovensinstitute.com
Customized Dispensing Systems and Reactive Resins
RAMPF Group, Inc. presented its dispensing systems and reactive resins for sealing, casting, and bonding filters and filter elements for fast and efficient production processes at FiltXPO 2023 this fall.
There are several materials used in filter manufacturing – from two-component polyurethane gaskets for frames, one- and two-component epoxies to solid or foamed polyurethanes for potting panels and end caps. Each material requires a dispensing system that best fits its chemical and mechanical properties.
RAMPF is a leading supplier of high-performance machines for mixing and dispensing single-, dual-, and multi-component reactive resins. The company has developed more than 3,300 system solutions worldwide – from simple manual systems through to fully automated production plants.
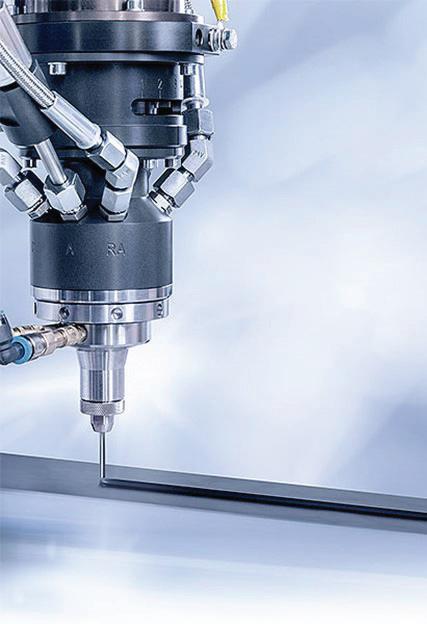
The company offers a wide range of metering pumps and dispensing heads as well as automated work cells that include robotic dispensing and parthandling, conveyors systems, curing equipment, hot-melt stiffening, laser marking, and testing. Service and spare parts are provided from the RAMPF head office in Wixom, MI.
The company also offers contract manufacturing for customers who have immediate requirements, prototype needs, or smaller part volumes. Part builds are supported from either Wixom or the RAMPF site in Suwanee, GA. www.rampf-group.com
CLEANR Debuts Powerful New Washing Machine Filters
CLEANR, a new greentech venture based in the U.S., recently unveiled its powerful new internal and external-retrofit microplastic filters for washing machines at the world’s largest appliance industry conference, IFA Berlin. Washing machine wastewater is the single largest source of microplastic pollution globally, accounting for 35% of emissions.
CLEANR’s nature-inspired technology has consistently outperformed the market in manufacturer-testing and is the first solution proven to meet upcoming French regulatory requirements, including microplastics capture efficiency and usability. CLEANR’s filters capture more than 90% of microplastics down to 50-microns in size and are highly user-friendly, where microplastics removal is easy, dry and takes less than 30 seconds per week and maintenance takes less than two minutes per month.
For washing machine manufacturers, the solution is cost-effective and integrates into virtually any washing machine model due to its simplicity and small size: the technology requires no additional pumps and can be separated into two parts to accommodate washing machine models with tight interior space limitations.
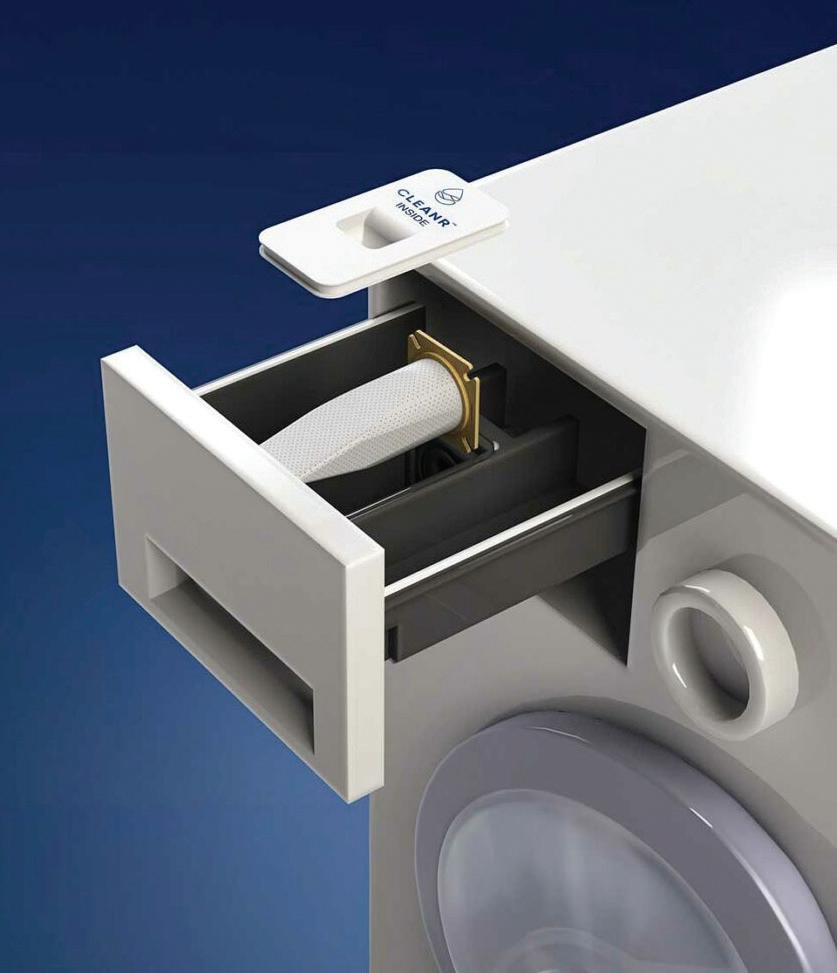
“CLEANR’s core technology, VORTX, is powered by a novel vortex filtration process that was inspired by nature and delivers 300% higher efficiency than traditional filters,” said Max Pennington, CLEANR’s CEO. “This enables our filters to handle three times as many wash-loads as others before filter-cleaning, operate with no electrical pumps, and trap the smallest microfibers.” www.cleanr.life www.camfil.com
Camfil announced the launch of the AirImage-COR, the latest innovation in corrosion control monitoring. Real-time corrosion monitoring and technology that enables users to act before having to react. Corrosion is a natural process that occurs when metals react with molecular contaminants in the air. Metal surfaces gradually deteriorate and compromise the integrity of electronic components.
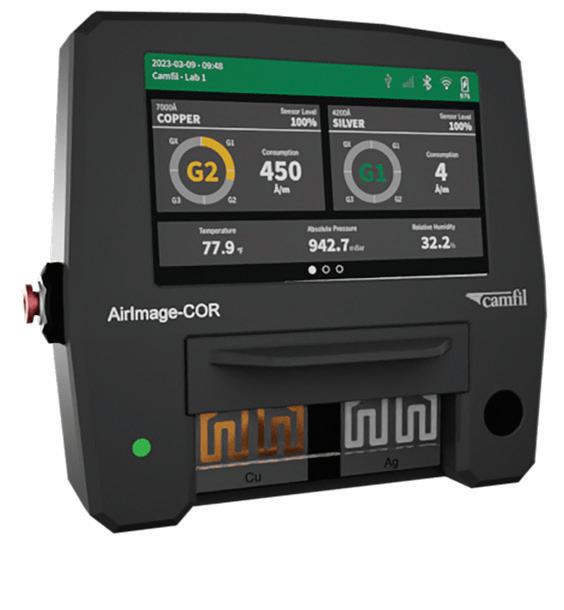
Electrical equipment is essential to the continuous operation of data centers, wastewater treatment facilities, petrochemical refineries, renewable energy plants, and now the emerging EV battery market. These industries all rely on automation processes to improve safety and reliability. Corrosion leads to unscheduled downtime, costly repairs, loss of revenue, and increased safety risks. The impact of corrosion extends beyond electronics.
Collections in museums and archives are extremely sensitive to corrosion due to the presence of acidic gases. Gas concentrations in such buildings may be low, but long-term exposure can lead to expensive restorations or even irreversible damage.