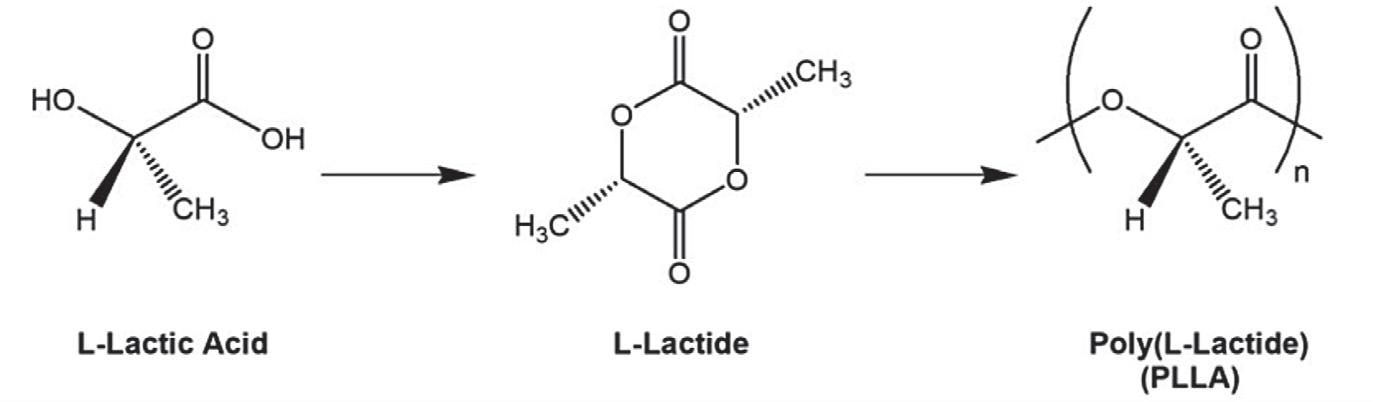
11 minute read
PLANT-BASED Materials
Sustainable and High Performing Innovation for Modern Filtration
By Chad Kamann and Koen Bastiaens
The global experience of the COVID-19 pandemic brought to light the acute need for safe, effective personal protective equipment (PPE) and filtration media to prevent the spread of disease. The additional need for more sustainable materials with a lower environmental impact drove many producers to consider replacing fossil-based plastics with plant-based materials given their versatility in various melt spinning processes from staple fiber to spunbond and increasingly in melt blown nonwovens.
The immediate need for PPE like surgical masks dissipated as the pandemic eased, but the need for broader sustainable filter media has only increased. As companies look to achieve their carbon reduction targets through the use of low carbon and biobased materials, development work with plant-based materials, like Ingeo™ PLA, has increased. Additionally, melt blown equipment has become more prevalent in the industry and is suitable for converting plant-based polymers, like PLA, into filtration media that achieves high-performance targets.
Circular Sustainability
The circular economy model is based on a vision for more sustainable production and consumption that prioritizes eliminating waste, circulating materials at their highest value, and decoupling materials from fossil-based feedstocks. Unlike the linear model of take-make-dispose, a circular model looks beyond consumer use of a product into multiple aspects of impact including where and how raw materials are sourced, the impact on human and environmental health, and after-use pathways such as reuse, recycling, and composting. According to Plastics Europe, in 2023, over 362 million metric tons of plastics were produced from oil and gas alone1 That volume is growing by over 25 million metric tons per year and contributing to a very linear waste model; once out of the ground, these fossil feedstocks can no longer be reproduced. Moving to a circular economy, where raw material feedstocks can be produced again and again, is a much more sustainable solution. Recycling contributes, but the capacity to recycle that much plastic is not available and has undeniable technical limitations. t Figure 3. Diagram of core and sheath in a biocomponent fiber.
Comparatively, the global production capacity of plant-based plastics (or bioplastics) is still nascent at less than 2.2 million metric tons but is expected to increase 7.4 million metric tons by 20282, which will help support companies striving to adopt new biobased materials and reach sustainability goals. Not all bioplastics are biodegradable, but they do make up 62% of the market’s capacity. Biodegradable polymers, like PLA, have a unique role to play in the circular economy not only for alternative ways to mitigate waste, but also in addressing the growing need for materials sources from renewable feedstocks and concerns around persistent microplastics3.
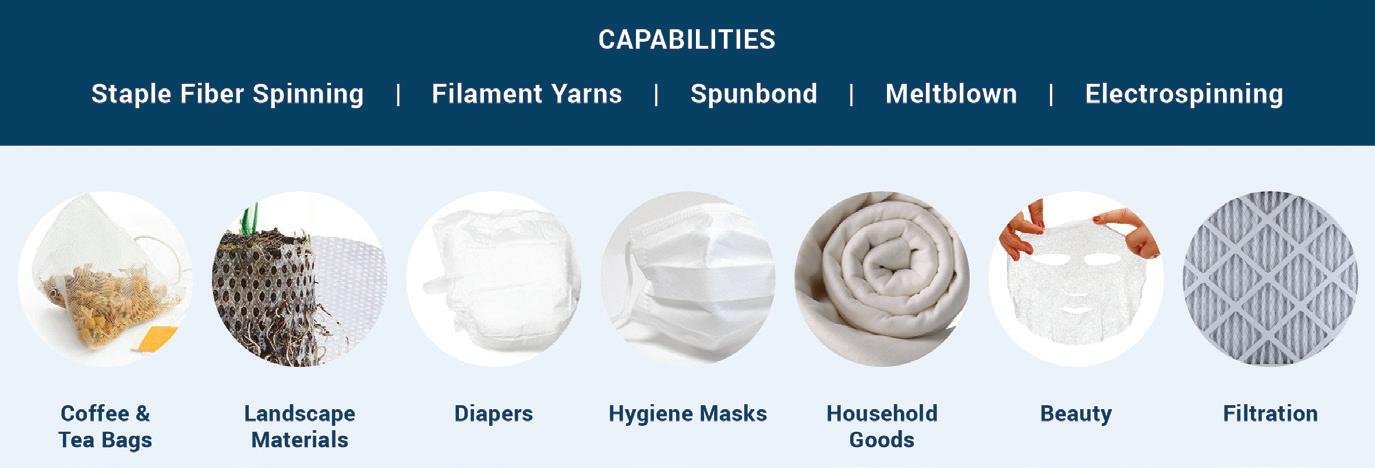
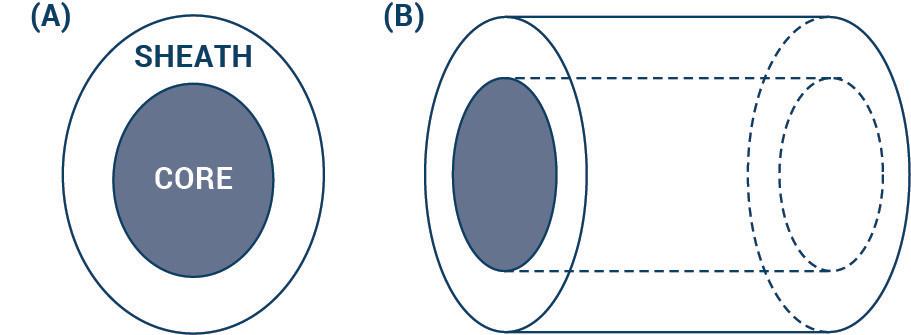
Figure 5. Spunbond strength comparison of 20 gsm Ingeo 6500D vs. 20 gsm generic PLA.

PLA Is a Plant-Based Material
Today, PLA is manufactured beginning with the fermentation of plant sugars derived from feedstocks like sugar cane or corn starch. Fermentation produces the monomer, lactic acid, which is a common food ingredient, and a chemical designated as Generally Recognized as Safe by the FDA. By definition, PLA made via condensation of lactic acid is called poly(lactic acid) and PLA made via ring-opening polymerization (ROP) of lactide is called poly(lactide) (Figure 1). NatureWorks has been producing a portfolio of PLA products via the ROP process under the Ingeot brand name since 2002, which allowed for production economics that can compete with incumbent fossil-based materials.
Over the last 20 years, R&D investment by NatureWorks has focused on optimizing Ingeo PLA grades for all fiber conversion processes targeting a broad range of downstream applications that need to meet unique performance criteria alongside sustainability criteria (Figure 2).
New Developments
Spunbond strength, softness, and processing improvements via nonwoven configuration and materials: Spunbond nonwoven construction plays a significant role in processability and strength of the web. Using a bicomponent fiber structure, amorphous PLA grades can be combined with crystalline PLA grades to achieve increased strength. Typically, the fiber sheath is made from amorphous PLA grades and comprises 30% of the fiber. Highly crystalline PLA grades are used for the fiber core and make up the remaining 70% of the fiber (Figure 3).
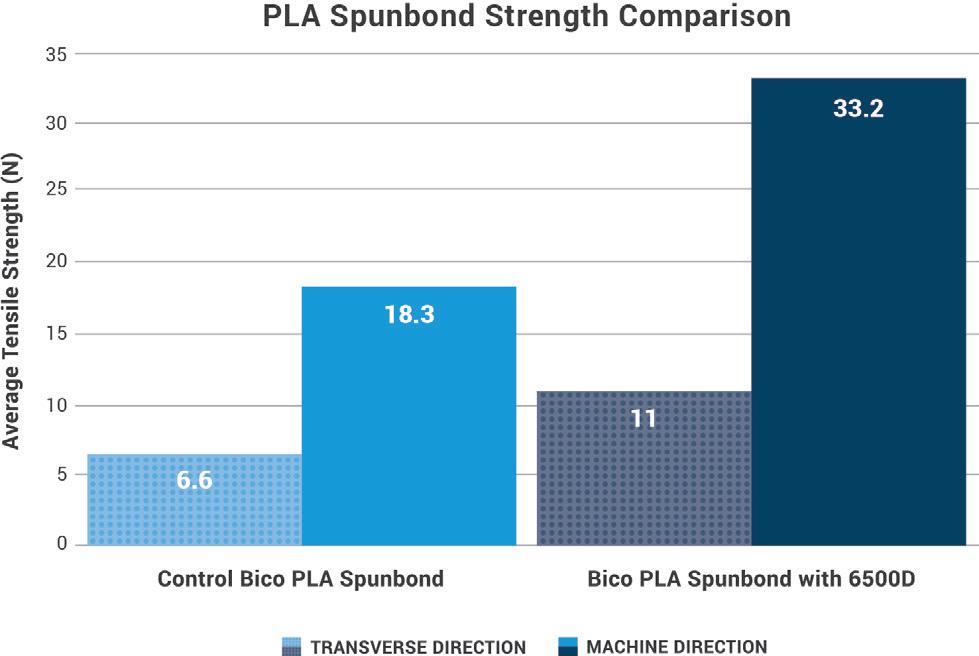
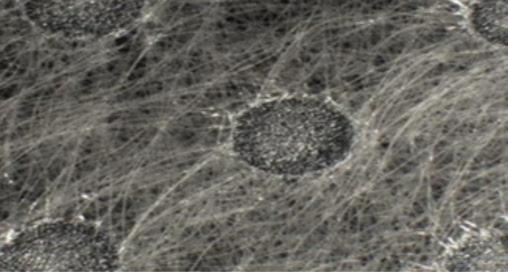
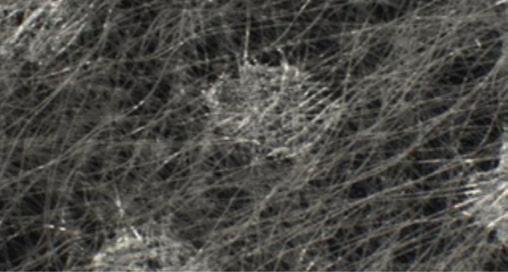
The amorphous sheath promotes improved bonding through the calendar roll resulting in improved web strength, while the more crystalline core results in a more thermally stable fiber and nonwoven web. Current spunbond nonwoven capabilities using Ingeo PLA grades can achieve basis weights from 12 grams/meter squared (gsm) to 200 gsm. In addition, since not all spunbond producers have bicomponent capabilities, new development work is currently underway to provide a monocomponent solution that will match the processability and performance of the bicomponent spunbond nonwoven.
In 2023, NatureWorks introduced Ingeo 6500D, which was the first grade to combine PLA with PHA in a formulation designed specifically for nonwovens. Testing with Ingeo 6500D demonstrated not only a step change in spunbond web strength but also a significant improvement in spunbond web softness. As seen in Figure 4, the spunbond fabric softness produced using Ingeo 6500D improved by approximately 40% when compared to a bicomponent generic PLA spunbond control sample. The softness was measured using a ¼” slot width on a HandleO-Meter and testing was conducted on a 15 gsm spunbond sample based on the ASTM D2923 test method. The spunbond web strength increased almost two times more than the incumbent control sample when testing was completed on a 20 gsm spunbond sample (Figure 5).
The strength and softness this new material also offers processing efficiencies over incumbent bicomponent PLA formulations and is more similar to polypropylene spunbond conversion based on multiple trials using state of the art spunbond equipment.
Another option for improving spunbond web strength was found when Ingeo PLA was combined with biobased PBSa as part of a biocomponent fiber. Adding 5 wt.% PBSa to the Ingeo PLA sheath component of the bicomponent structure improved the machine direction strength of the web by 113% and the cross-direction strength by 185%. Microscopic images of bond sites post-calender roll of a 20 gsm control sample showed more complete bond site generated by the calender roll when 5wt% PBSa is added to the sheath (Figure 6) when compared to no PBSa in the sheath (Figure 7). q Figure 9. The Nonwovens Institute developed new microfibrillation technology for spunbond nowovens using a bicomponent fiber of Ingeo PLA and PP to improve performance characteristics for filtration media.
Combining PLA with other biobased polymers like PHA and PBSa helps maintain high biobased content in nonwovens while improving performance attributes. However, PLA can also improve the performance of polypropylene (PP) fibers and increase the speed of converting into spunbond nonwovens when the two materials are combined in a bicomponent fiber structure. Trials completed at the Nonwovens Institute (NWI) at North Carolina State University demonstrated an 86% increase in the PP throughput when Ingeo PLA was added across multiple bicomponent configurations. The results in Figure 8 show an increase in processing from 200kg/hr when using a 100% PP fiber to 345kg/hr when using a 30% PP sheath and 70% Ingeo PLA core fiber. A similar result was also seen for a 70% PP sheath and 30% Ingeo PLA core.
Figure 8. An 86% increase in throughput of PP fibers was demonstrated when combined with an Ingeo PLA core in a bicomponent structure (30 gsm spunbond).
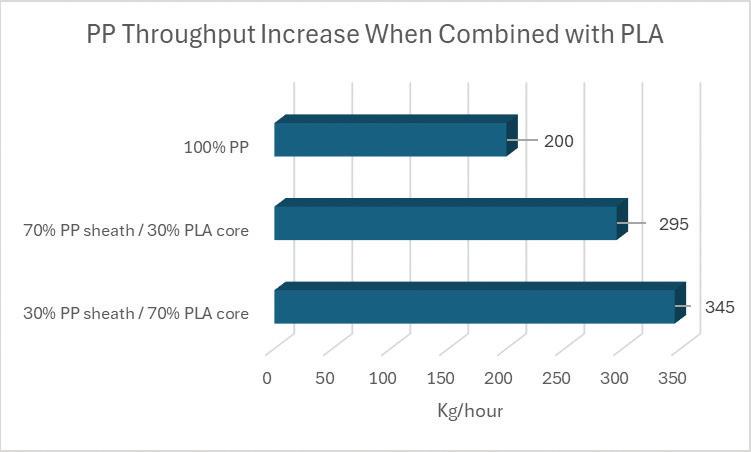
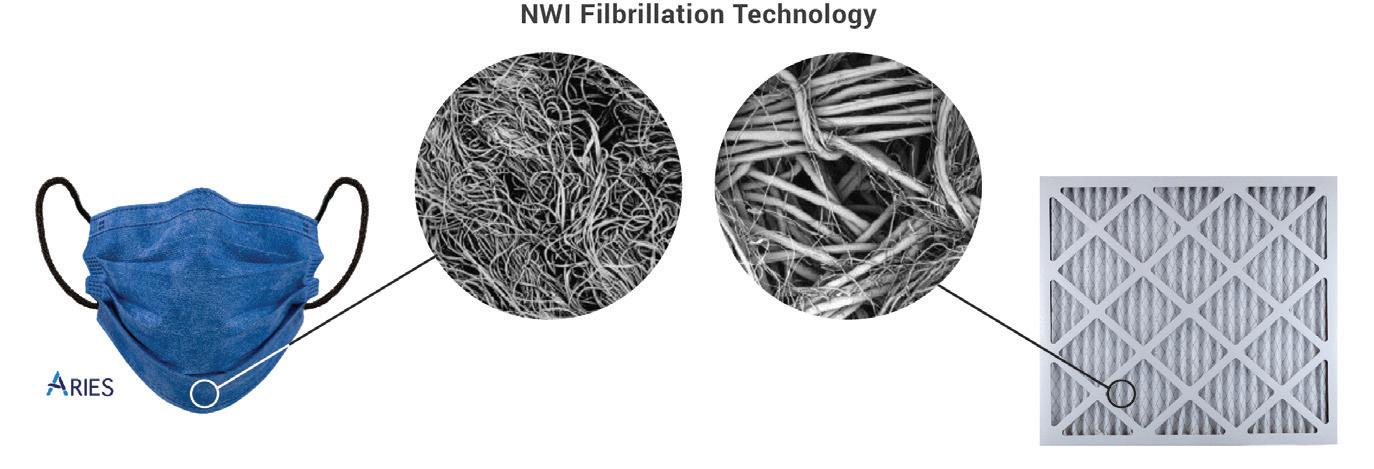
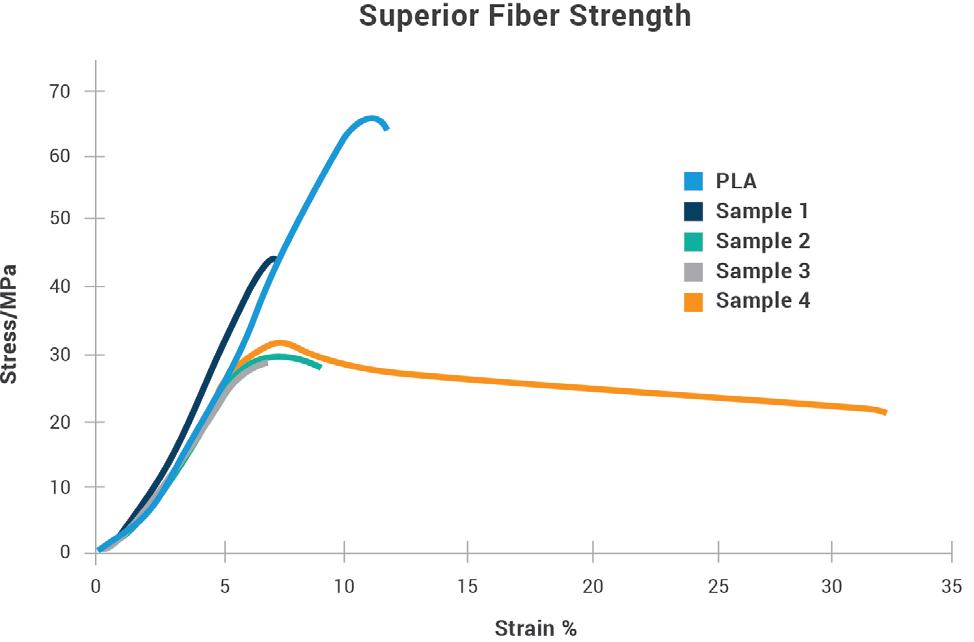
The increase in throughput can be implemented due to the broad melt spinning window offered by PLA, which allows PLA to be processed at the higher cabin pressures (8500-10,000 pascals) required to produce thermally stable fibers and spunbond web. Higher throughputs (1.0-1.5 gram/minute/hole) allow PLA to process more consistently at the higher cabin pressures and produce the small fiber sizes used for hygiene and filtration applications. In contrast, the PP melt fractures at the higher shear rates typical of the higher throughputs and/or filament velocities used with PLA. The broad melt spinning window of PLA allows these performance benefits to be realized and could be an easy way to start incorporating plantbased materials like Ingeo PLA into a product portfolio to meet sustainability goals and achieve improved processing economics.
Developments in Sustainable Filters
The Nonwovens Institute (NWI) and NatureWorks have been jointly developing fiber and fabric configurations and applications for PLA through a 15-year partnership. During the COVID-19 pandemic, NWI was able to leverage some previously developed microfibrillation technology and spundbond nonwovens made from a bicomponent Ingeo PLA and PP fiber to make a facemask filter medium with an ultra-low pressure drop.
The fibrillation process uses novel jet strips that form a “quilted” structure to control the pressure drop. The degree of fibrillation can be controlled; partial fibrillation will result in a mix of fibers (~1-2 μm) and coarse fibers (~15-25 μm), while full fibrillation results in a structure with fibers in the range of 1-2 μm (Figure 9).
Performance Benefits for PPE
• High filtration efficiency yet more breathable
• Renewable and reusable
• General use facemask meets ASTM F3502
• Performance benefits for HVAC filtration
• High filtration efficiency with low pressure drop
• Renewable
• Improved pleatability
• Increased spunbond throughput
• Lint free
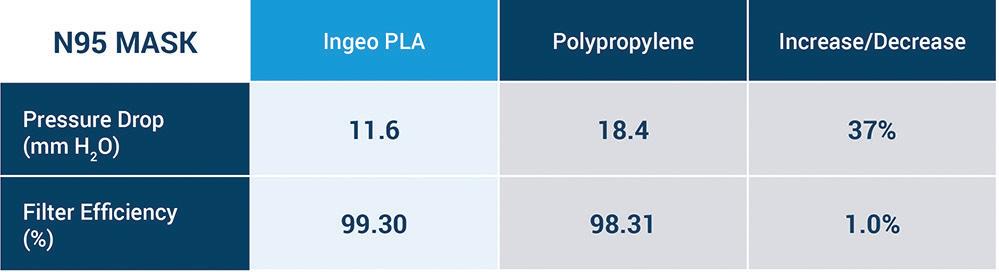
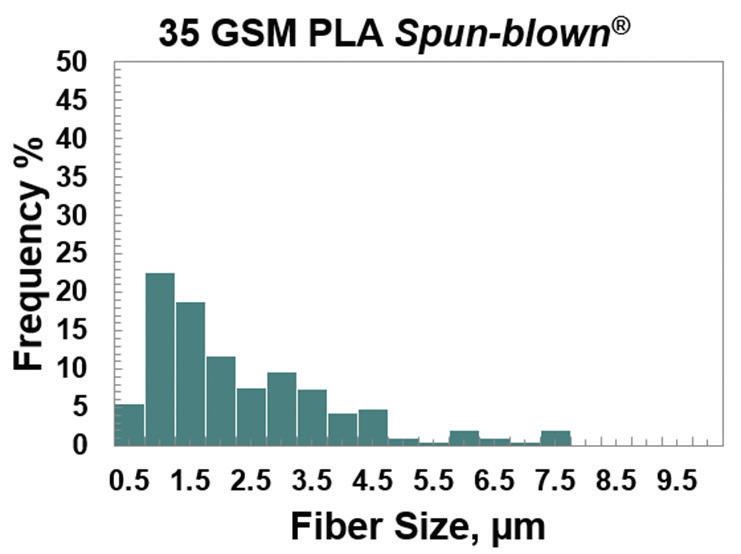
The process results in triboelectric charge and this new nonwoven structure does not require electrostatic corona charging meaning the substrate can be reused and re-sterilized. It is also strong enough to be cut and sewn, or automatically converted into masks and respirators.
The U.S.-based face mask manufacturer, Aries, received ASTM 3502 certification for their mask produced from this new spunbond nonwoven technology. This mask was also one of the first to be highlighted on the National Institute for Occupational Safety and Health (NIOSH)’s website. The filtration efficiency of a one-layer mask was measured at over 83%, and the pressure drop was 5 mm. In comparison, a face mask made with a standard PP meltblown nonwoven has a filtration efficiency of 99% and 13 mm of pressure drop. With additional layers, or a higher degree of fibrillation the Aries mask could reach 99.9% filtration efficiency.
Spunbond filter media made with PLA and PP also has uses beyond PPE for applications such as durable microfiber wipes or HVAC filters. These types of applications benefit from the inherent stiffness of PLA, where even in sub-micron fibers, a more three-dimensional structure can be produced resulting in significantly lower pressure drops and improved depth t Figure 11. Masks made of Ingeo PLA using a combination spunbond/ meltblown process have a lower pressure drop than N95 masks made from PP, and maintain filtration efficiency. made with the ultra-small fibers are stronger than conventional high tenacity materials even though the fiber size is more than 10 times smaller (Figure 10). filtration. PLA also improves the pleatability of the filter media when incorporated at 90% or more of the construction. A potentially self-pleating solution could eliminate the need for a scrim layer and lower costs.

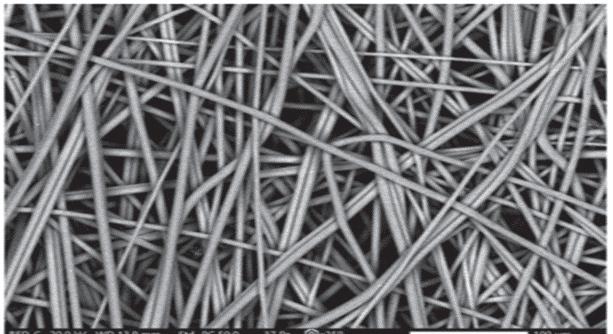
Hybrid Technology Bridging the Gap Between Spunbond and Meltblown
Equipment and system solution provider, Hills, Inc., has done extensive work in multicomponent fiber technology to improve fiber performance. Recent trial work has demonstrated that by drawing PLA at speeds up to 9,000 meters per minute, the resulting fibers are much smaller having achieved <0.5 denier. The high spinning speed induces high orientation of the polymer molecules, producing fibers of superior strength, and fabrics
Figure 15. Jabil filter media demonstrated comparable penetration performance with MERV rated filters at lower basis weights. Testing was completed at 18.3 L/min flow rate.
Currently, Hills Inc. is working with dissimilar biopolymers such as using amorphous and crystalline PLA and activating the fibers into spiral configurations to create lofty nonwoven materials. Tony De La Hoz, Director Product & Process Development at Hills Inc. noted, “Sustainability is opening the door to the development of high added-value materials, taking the driver seat for innovation. This is a revolution.”
The company 5K Fibers has developed a combination spunbond/meltblown process branded Spun-Blown®. Using this process, 5K Fibers has produced masks made with Ingeo PLA that have a low pressure drop of 11.6 mm, making them easier to breathe through, while maintaining a filtration efficiency that matches N95 masks made with polypropylene (Figure 11).
The increased filter efficiency and reduced pressure drop make the use of

Ingeo PLA and the Spun-Blown® technology ideal for surgical masks as well as HVAC filtration media. The superior filtration performance results in how the Spun-Blown® process creates nonwoven webs with wider fiber distributions providing a wider, yet controllable, fiber size (Figure 12).
Meltblown Developments
Using meltblown processing, the company, Jabil, developed a novel solution combining Ingeo 6252D with acrylic to produce smoother, continuous filaments in nonwovens (Figure 13, Figure 14). The patented technology produces nonwovens that are highly efficient at particle filtration while still maintaining low air resistance. The polymer blend allows for improved electrostatic filtration driven by its unique microstructure. In addition, the flow characteristics of Jabil’s blend allows for high throughput processing compared to traditional melt blown materials.
Made using Jabil’s PLA/acrylic blend, 75 PPE masks across three lots were tested for particle filtration efficiency (PFE) and resistance. On average, these masks filtered 99% of particles matching incumbent PPE products such as the 3M 8210 and Condor N95 masks. However, the resistance of the masks made by Jabil measured consistently lower than the 3M 82104 and significantly lower than the Condor N95 mask with relief valve.
In addition, Jabil’s filter media was produced at a lower basis weight with significantly less material and still had comparable penetration (Figure 15) and better resistance levels (Figure 16) when compared to other MERV rated filters.
While PLA is a relatively new polymer in the nonwovens industry, key collaborations between industry partners and with academia have resulted in new technologies that leverage the unique characteristics of Ingeo PLA to generate improved filtration capabilities that outperform incumbent polymers like polypropylene. Whether used on its own, in combinations with other polymers as blends, or in bicomponent fibers, PLA is demonstrating that beyond its sustainability characteristics it provides significant performance value in the nonwovens and filtration space.
Figure 16. Jabil filter media demonstrated lower resistance than other MERV rated filters. Testing was completed at 18.3 L/min flow rate.
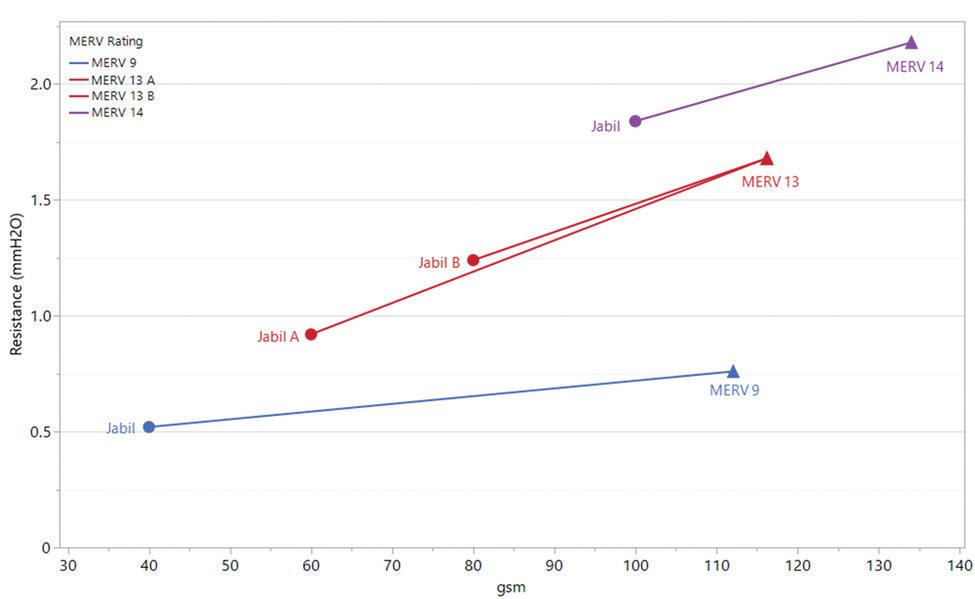
In both meltblown and spunbond nonwovens, exceptional filtration efficiency combined with newly attained low pressure drops is possible with both PLA fibers and blend with other biobased polymers. In addition, combining PLA with polyolefins in bicomponent fibers can increase throughput and structural formation that is especially interesting in filtration applications. However, the future of filtration media is invested not only in improving performance, but also ensuring sustainability is part of the research, design, and development process. Dedicating development to plant-based materials like Ingeo PLA, ensures that future filtration media will have a carbon footprint approximately 62% lower5 than when incumbent fossil-based polymers like PP are used.
New biopolymers are also important for reducing the impact materials have on both human and environmental health. For example, industry leading certifications like the Cradle to Cradle Material Health Certificate are certifying that materials like PLA are free of chemicals of concern6, and new studies are showing that biodegradable polymers like PLA are not persistent as microplastics in the environment7. Considering these impacts is critical in advancing the circular economy alongside the innovative technologies that will propel the filtration market into a more sustainable future.
Chad Kamann is the technical lead for fibers and nonwoven materials at NatureWork s . With over 20 years of experience as an Applications Development Engineer, Kamann partners with customers and the supply chain to develop product parameters, customize applications, and scale new innovations.
Koen Bastiaens is Strategic Market Manager for NatureWorks. Bastiaens leads the global strategy development and go-to-market planning for emerging technologies related to fibers and nonwoven applications. Sustainable filtration media is an emerging application which seeks to highlight the unique performance attributes of high-performing Ingeo™ biopolymers.
1 Plastics: The Facts 2023, Plastics Europe, https:// plasticseurope.org/knowledge-hub/plastics-thefast-facts-2023/.
2 Bioplastics Market Development Update, European Bioplastics, https://www.european-bioplastics.org/ bioplastics-market-development-update-2023-2/.
3 PeToPLA: A meta-study on the persistence and toxicity of PLA, and the formation of microplastics in various environments, HYDRA Marine Sciences, https://hollandbioplastics.nl/wp-content/ uploads/2024/06/2024.06.24_PeToPLA-Metastudy_ Technical-Summary_Public.pdf.
4 The 3M 8210 data was collected by the National Personal Protective Technology Laboratory and independently reported.
5 Ingeo PLA data from Life Cycle Inventory and Impact Assessment data for 2014 Ingeo™ Polylactide Production. Industrial Biotechnology, Vol 11, No. 3. Pgs 167-180.June 2015. Data on EU PP production from Plastics Europe, 2023.
6 https://c2ccertified.org/certified-products/ ingeo-biopolymer.
7 https://hollandbioplastics.nl/actueel/newmeta-study-highlights-that-hydrolysis-preventsthe-formation-of-persistent-pla-microplastics-inthe-environment/.
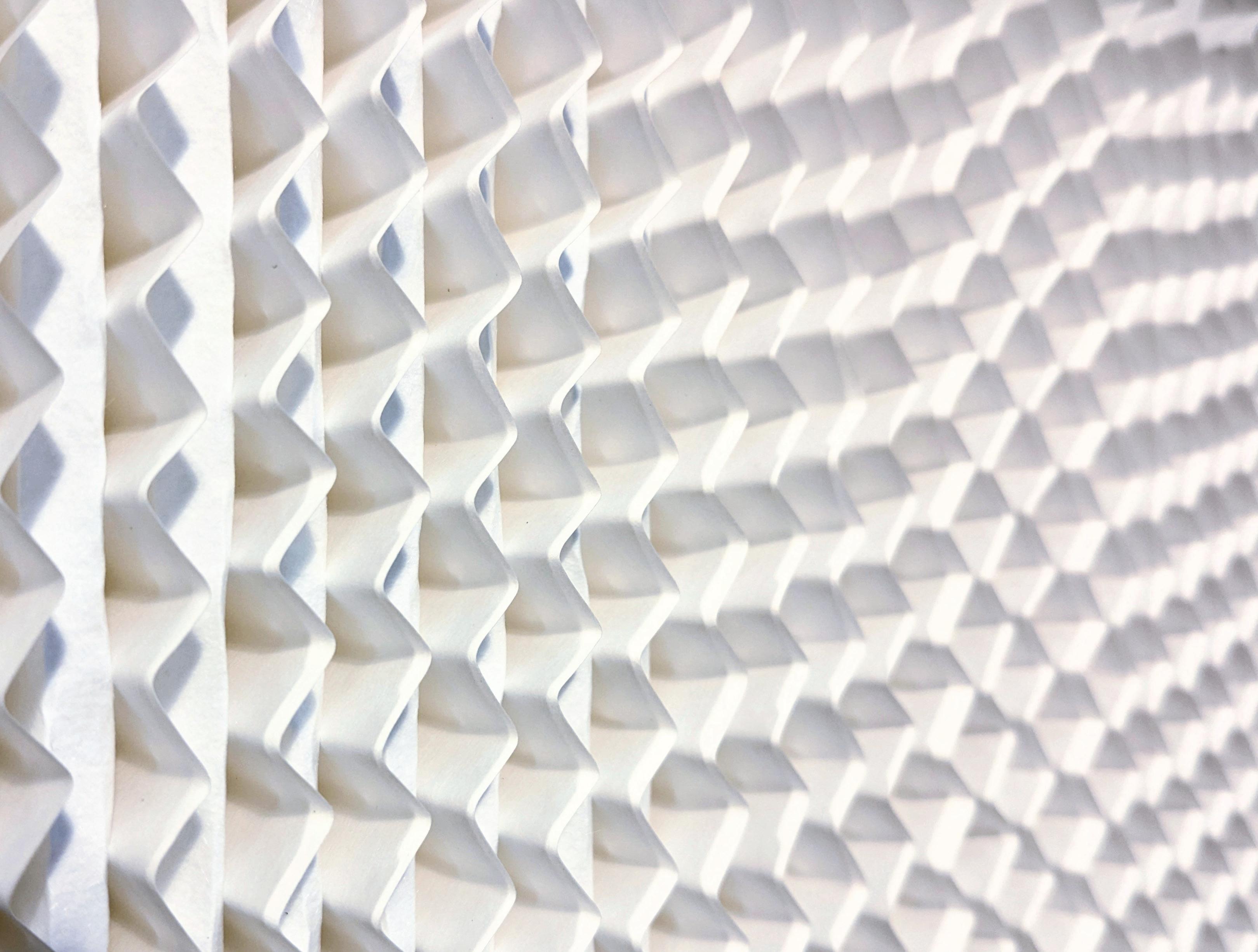