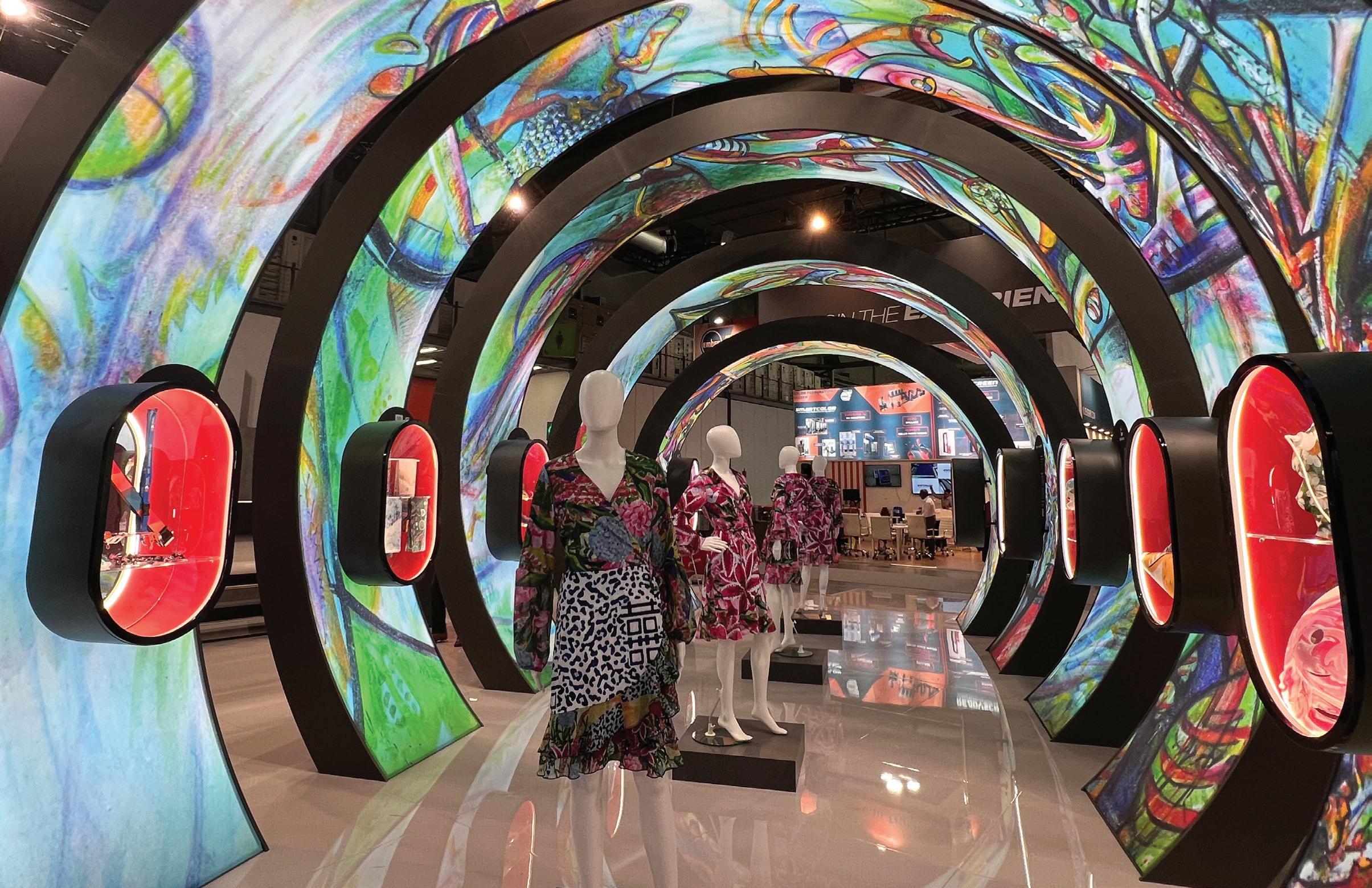
18 minute read
Innovation Super Stars Digital Color & Textile Recycling
By Caryn Smith

The best and brightest ideas from leading companies and new players in textile manufacturing and production were plentiful at ITMA Milan, which delivered on expectations. It is difficult to share all aspects that would do all justice. Rest assured, themes like reshoring, automation, production, traceability, circularity, and more, will be shared in future issues. Yet, two areas exhibited exponential innovation – playing a role in the emerging textile circular economy. They are digital textile printing and textile recycling. To understand the innovations, you must first review the issues they seek to solve.
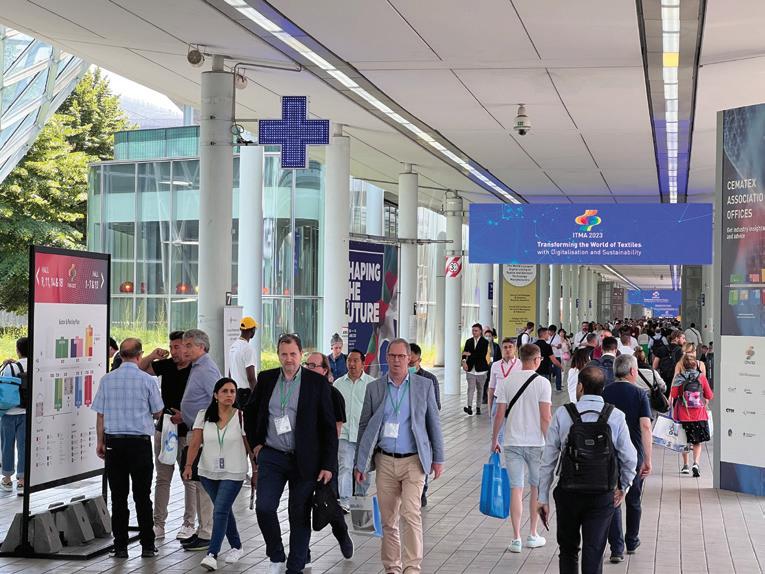
Impacts and Solutions
The textile industry’s exorbitant use of resources and generated waste are ever-present issues. As a reminder, according to the Geneva Environment Network (www. genevaenvironmentnetwork.org) in just fast fashion textiles alone, the statistics are grave. A search for sustainable fashion on their website is worth a look. Here are just a few facts that rising innovation can correct if adapted:
• The equivalent of one garbage truck full of clothes is burned or dumped in a landfill every second (UNEP, 2018)
• Approximately 60% of all materials used by the fashion industry are made from plastic (UNEP, 2019)
‘Transforming the World of Textiles’ was the theme of Mimaki’s ITMA 2023 booth, focused on sustainability, showcasing waterless digital textile print solutions through collaboration with fashion and textile designers. Insets: (L) Balkan Textile Machinery (pictured) and Trützschler partner to provide a complete line-up of technologically leading machinery which has been specifically developed for rotor and ring yarns from recycled materials; (C) ITMA attracted over 111,000 from 143 countries; (R) On display, Kyocera and Orange Fiber show off their collaboration to print on sustainable fabrics made utilizing citrus juice by-products with inkjet textile printer, FOREARTH.
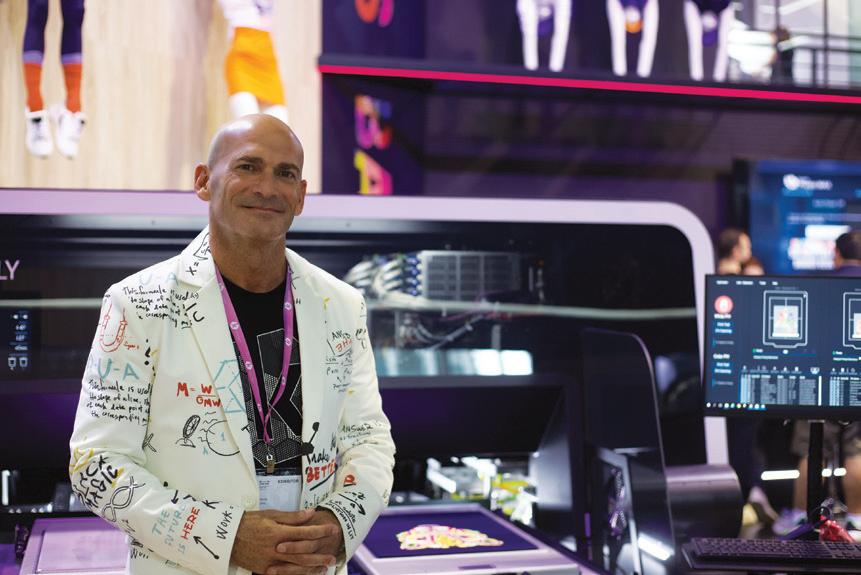
• 500,000 tons of microfibers are released into the ocean each year from washing clothes — the equivalent of 50 billion plastic bottles (Ellen MacArthur Foundation, 2017)
• The fashion industry is responsible for 8-10% of humanity’s carbon emissions – more than all international flights and maritime shipping combined (UNEP, 2018). If the fashion sector continues on its current trajectory, that share of the carbon budget could jump to 26% by 2050 (Ellen MacArthur Foundation, 2017)
• Some 93 billion cubic meters of water – enough to meet the needs of five million people – is used by the fashion industry annually, contributing significantly to water scarcity in some regions (UNCTAD, 2020)
• Around 20% of industrial wastewater pollution worldwide originates from the fashion industry (WRI, 2017)
In the panel on Development of a Sustainable Digital Future, Kevin McCoy, Vice President, MADE, New Balance Athletics Inc., says, “You must look at the value. Doing the right thing is hard and can be expensive. Know that up front you’ll get attention as a challenger to the status quo. Regardless of technology, it starts with design. Design for manufacturing.”
These thoughts were echoed by others. During a press event discussion centered on Kornit Digital’s advancements (we will get to those shortly), Muriel Laurent, Director of Digital Marketing, at SOL’S believes that on demand and digital production are key to the future of textiles. “Print on demand is the most sustainable option for the future.” Jaymes Clements of Mad Engine says, “Retail brick and mortar have limited space. There is no need to premanufacture, when the product can only exists because someone has purchased it,” believing that this is a reliable business model for ensuring stability, efficiency, and growth in dynamic circumstances.
“Offering increased level of creativity, taking digital mainstream, brands need to change the way they think about production,” emphasizes Ronen Samuel, Chief Executive Officer at Kornit Digital. “With the ability to print on any kind of fabric, save resources, automated utilization systems, it is an evolution the industry has never seen before.”
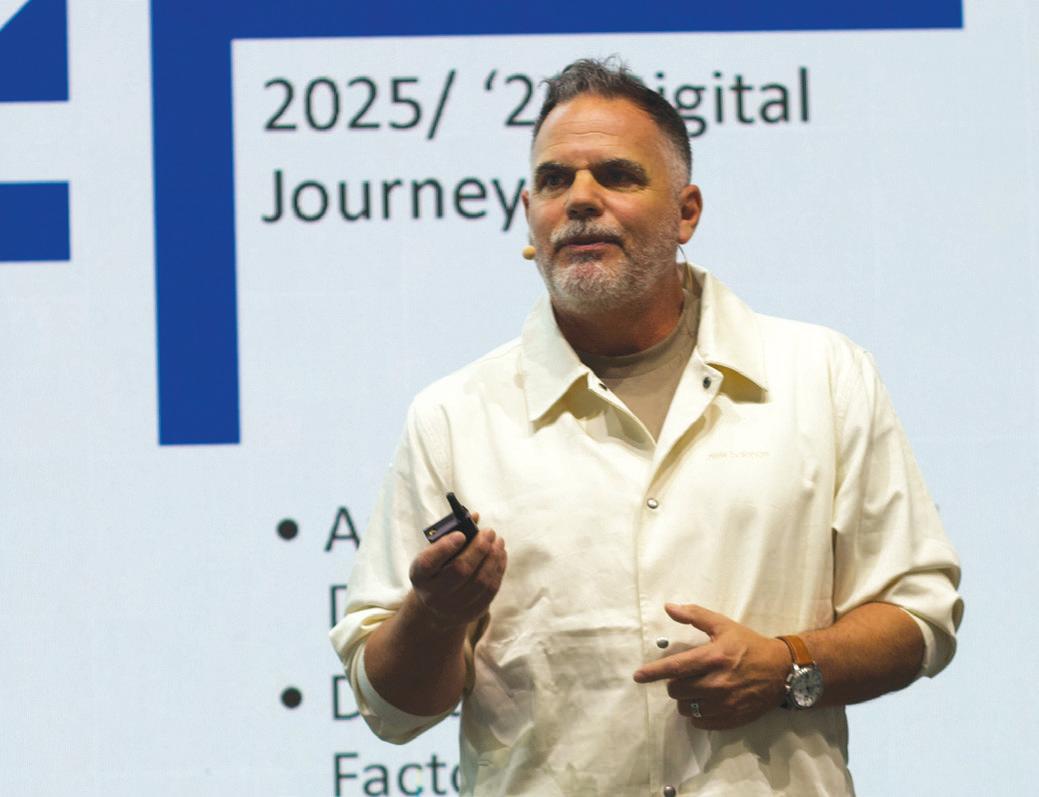
Alon Moshe, Twine Solutions CEO, comments on the company’s newest technology, the TwineX4 digital yarn and thread dyeing system. “We believe this system represents the future of textile production and will be a huge change for our customers. We are confident that it will help textile manufacturers increase efficiency, reduce costs, and produce more sustainably.” The convenience of on-demand, in-house thread and yarn digital dyeing for small to medium-sized batches eliminates supply delays, supports the implementation of lower waste-to-landfill goals, reduces CO2 emissions in transportation, and has significant water and energy savings.
Switching topics to end-of-life textiles processing, the concept of recycling is catching on, but … Ever. So. Slowly. A McKinsey Sustainability report notes that less than 1% of textiles produced for clothing are recycled into new clothing, representing a missed revenue opportunity of more than $100 billion a year. With the popularity of synthetic blends, that task is complex, time consuming and expensive. Yet, big brands like Levis, Adidas, and Zara have made recent news on their commitments to textile recycling.
New waste legislation in the U.S. could fast track recycling. A CNBC* news article recently reported, “In New York State, The Fashion Sustainability and Social Accountability Act, also known as the Fashion Act, would hold companies accountable for their recycling practices. It is currently backed by fashion brands like Eileen Fisher, Stella McCartney, Everlane, and Patagonia, as well as other advocacy organizations pushing to pass the bill.”
With those points made, let’s get back to solutions. ITMA Milan showcased many, and here are the ones that stood out with a splash of color.
* https://www.cnbc.com/2023/06/11/a-recycled-idea-at-levis-adidas-to-stopclothing-from-going-to-waste.html
Digital Color Solutions On The Rise
Kornit Digital
Kornit Digital LTD elevated their standard for sustainable, on-demand digital fashion and textile production technologies with its “Kornit ecosystem.” The company sees agility, versatility and green production as the future of fashion, sportswear and home décor as producers seek to minimize industry waste, without sacrificing quality or profitability. The tech allows for designers and retailers to focus on productivity, creativity, and on-demand flexibility.
At the center of this ecosystem is Kornit Apollo, offering high-throughput, on-demand garment decoration. It is a versatile automated solution for digital, single-step, short- to medium-run decoration of garments at high volumes, ideal for nearshore and onshore production models. Kornit customers can now achieve optimal total cost of ownership and the highest output per operator at up to 400 garments per hour for any type of job. Enabling digital production to go mainstream, Apollo allows customers to become more agile, drive revenue opportunities, shift to localized production, and ease complex workflow processes.
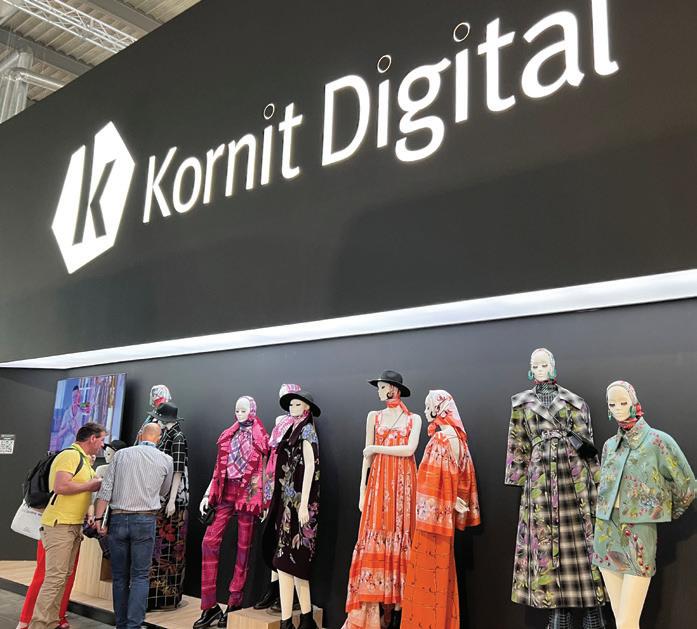
The main drivers offer quality digital on-demand printing to the mainstream for any fabric, while saving resources in production. The company’s bold impact statement reveals that by 2026, Kornit technology will enable production of approximately 2.5 billion apparel items in a responsible manner, saving 4.3 trillion litres of water, 17.2 billion kilograms of greenhouse gas emissions, and reduction overproduction in the fashion industry by 1.1 billion apparel items.
“Kornit Digital solutions directly answers surging industry demand for the highestquality, sustainable, on-demand manufacturing at scale,” says Ronen Samuel, Chief Executive Officer. “Delivering real industry change and bringing the market to the next level, the world’s biggest brands can now thrive in a market where anything is possible, and consumers can expect the world. Ultimately,” he says, “this enables brands or retailers endless design options, carrying no inventory until an order is placed.”
Kornit
The new Kornit Atlas MAX POLY makes short runs profitable with high-throughput and automated single-step processes, geared towards professional and recreational sportswear, teamwear, and licensed gear. This machine is the most efficient specialty system for polyester decoration, covering blends, tri-blends, and other synthetic fabric combinations. Colorful and vibrant prints using innovative neon inks are the star of this machine to produce retail-grade quality, durable goods.
The company has enhanced the Kornit Presto MAX capabilities, with industryfirst capabilities of brilliant white printing on colored fabrics. Kornit also unveiled NeoPigment™ Vivido ink set, which achieves darker, deeper blacks and colors to establish new fashion standards with a pigment-based process. Kornit’s patented solution is a streamlined and completely dry process for the most sustainable fabric decoration.
Epson
Versatility and sustainability were on display at Epson Como Printing Technologies, where the Monna Lisa line of textile printers were producing beautiful designs on textiles.
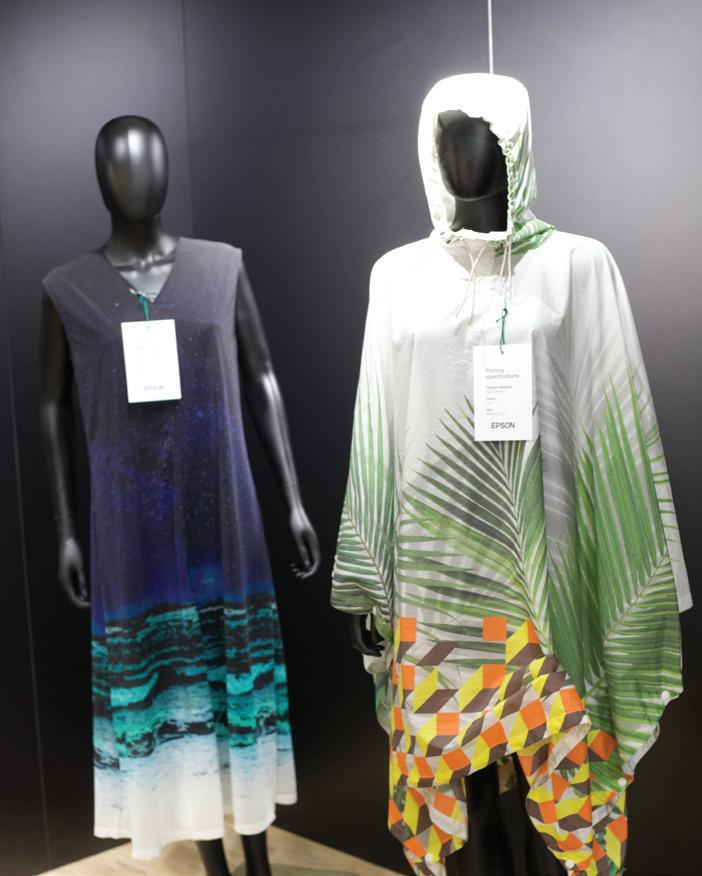
The company unveiled the new Monna Lisa ML-16000/HY, that can uniquely digitally create any type of special effect on fabric. The hybrid printer has been developed to reproduce the most sophisticated effects for modern printed fabrics with gold, silver, and glossy tints. “Our big news is the ML-16000/HY’s ability to expand beyond flat colors into metallics and special effects. It is really going to being something new and special to textile producers,” says Paolo Crespi, Commercial Director of Epson Como Printing Technologies (ECPT).
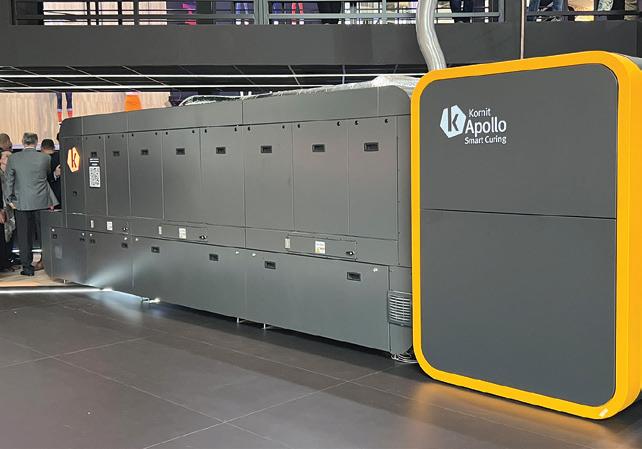
The combination of the ML-16000/HY’s 8 color inkset, 16 PrecisionCore printheads and 64 nozzles, enables the digital printing of special effects, previously exclusive to conventional screen or cylinder printing. The company’s Genesta waterbased inks (Acid, Reactive, Disperse and Pigment) guarantee color accuracy and resistance in fabric prints, while exclusive pastes developed and produced by ECPT create the special effects.
In sheer size alone, the ML-24000 delivers unprecedented flexibility and widest color range in the series. The highly flexible solution is the first to be equipped with 24 Epson PrecisionCore printheads and 12 colors.
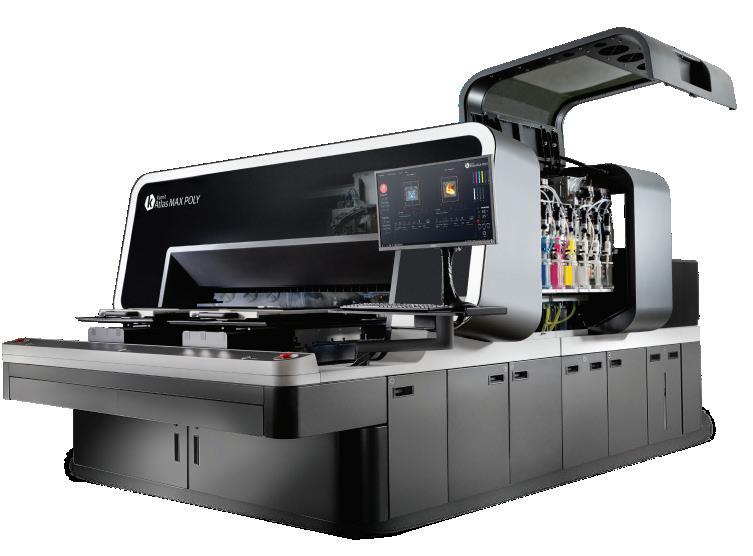
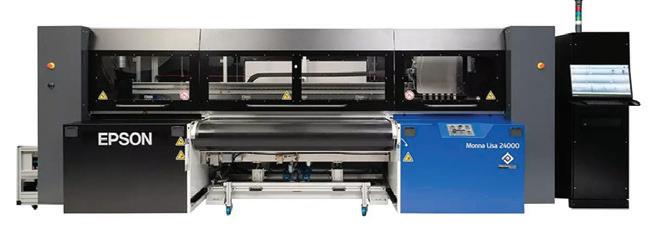
“All the line, from the mini-Monna Lisa to the new ML-24000 delivers the same quality, same process. They fit into any market experience,” says Crespi. “Studios can promote their own designs or collections, create prototypes, and more, with the flexibility of the Monna Lisa line which provide significant savings of time, energy and water.”
Furthermore, the integration of sustainability into the core business, with the ability to print on sustainable fabric –such as coconut or banana fibers – along with industry standard natural, artificial, and synthetic fabrics, contributes to the fashion’s transition towards a lower environmental impact.
“Special effect fashion market segment is on the rise,” notes Crespi as trends. “Home textiles collections will change style more frequently, not every five years. Big brands need to offer the stylists more possibilities to be creative. With production moved back to China, solutions like the Monna Lisa can provide a reshoring opportunity, marketed as sustainable in materials and as a viable business model. Lastly, it takes just one person to run our automated machines, or even several at a time, which offers better working conditions and helps with workforce management.”
Ntx
NTX® Cooltrans® colorization is cool, for sure. The ink chemistry and technology is both a novel and waterless textile coloration solution. The breakthrough is the result of merging innovations in chemistry and machinery to deliver precise and accurate colorization of nearly any fabric material without heat, up to 90% reduction in water use, 40% reduction in dye use, while retaining uncompromising color fastness, hand feel, and functional performance. Three different systems, each with varying capabilities, make up the NTX® Cooltrans® family.
“We offer the best of digital sublimation, an extremely precise dosage process, offering color brilliance on all fabrics, polys, cottons, blends,” says Jeffrey F. Hsu, Chief Innovation and Marketing Officer. “Our machines offer double-sided printing, utilize shorter lead times, and produce amazing handfeel.” Also, he notes that NTX® Cooltrans® eliminates the tension and strain put on the materials and is therefore perfectly suitable to use with finer, lighter, and more delicate materials.

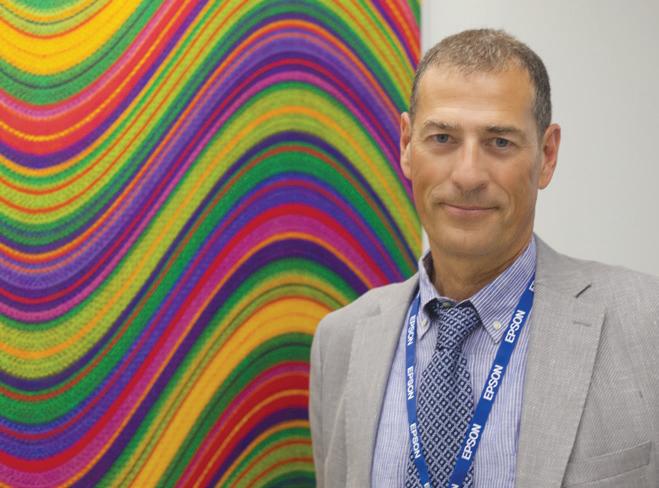
The newest offering, Eco-Denim, was the star of NTX show. To see the samples, you think you are looking at traditionally dyed denim material, but upon closer inspection, the printing tells a different story. Using panel or engineered printing technology, garments can be produced (i.e., printed) to replicate garment effects like simulated denim wear, distress, and an aged look with a precision that’s genuinely impressive. Moreover, it provides a quality answer to the fashion’s sustainability challenges with denim.
This new line of denim coloration not only looks and feels just like traditional denim, but it also brings with it substantial environmental benefits. By using panel printing, NTX® can create the classic worn and distressed effects on denim without resorting to water and energy-intensive methods to create them, thereby saving resources with shorter production cycles.
The time savings in production allows for time to apply a “final touch wash” to the denim. This process gives the jeans a truly authentic washed feel while still maintaining the impressive environmental benefits of NTX manufacturing process.
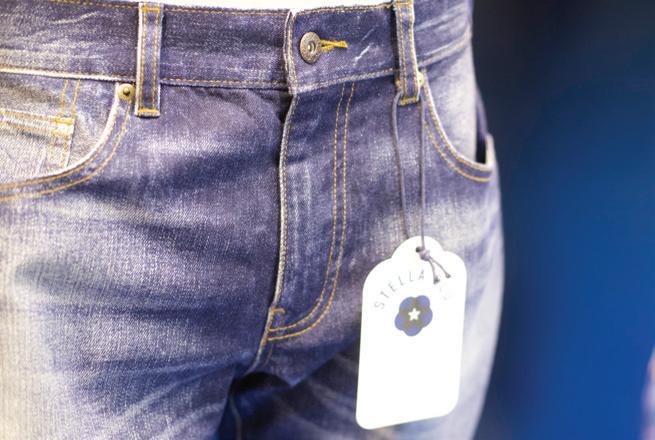
NTX is attracting brands such as Addias and Stella Blu to collaborate. “The really exciting thing is the cost-competitive aspect of implementing NTX® Cooltrans® into the value chain for our brand partners,” says Kalvin Chong, Chairman and Co-founder of NTX®. “The savings associated with lower energy requirements and water usage allow us to bring this game-changing innovation to ecology conscious consumers around the globe without impacting the manufacturing-costs of the final products.”
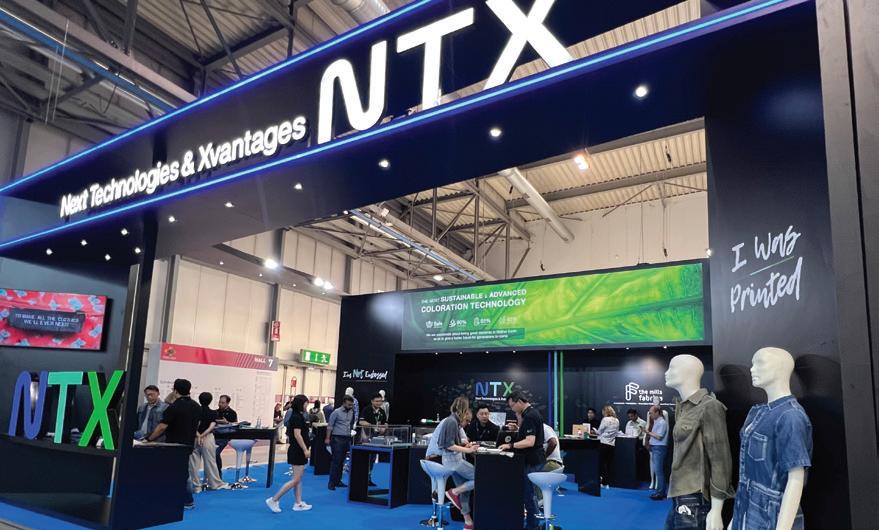
Digital Color Solutions On The Rise

Alchemie Technology
Alchemie Technology is on a water conservation mission with its own waterless smart dyeing machine, Endeavor.™ The company spent 10 years developing a digital print head for their machine, utilizing advanced digital manufacturing technology to deliver a breakthrough in the cost structure, supply chain capability and sustainability of fabric coloration.
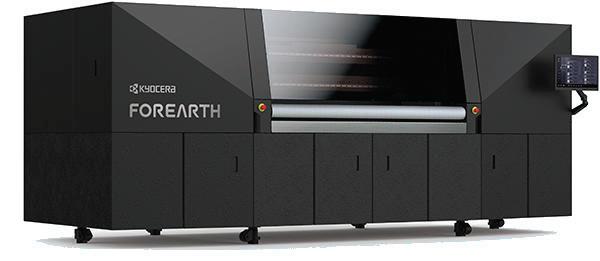
The high throughput roll-to-roll single-pass technology delivers dramatic manufacturing cost reductions, profitability benefits, reduces minimum run lengths and enables rapid changeovers between colors and fabrics. The process delivers excellent handfeel, which has been assessed by major brands and designers to be equivalent to traditionally processed fabrics.
Dr. Alan Hudd, CEO & Founder, shared that the targeted tech solution is one answer to solve the industry’s water pollution problem. It is the second largest contributor, at over 20%, to global water pollution. “Demand in 2030 will increase 40% for fresh water. We are on a journey to a no-green-premium,” he notes. “Further, there are 1.2 billion digitally defined drops per linear meter of fabric. This precision means no excess dye is used.”
The Endeavour™ reduces the carbon footprint of dyeing by over 85%. This is significant because textile dyeing and finishing is responsible for approximately 3% of global CO2 emissions (Quantis Report 2019). The company claims to have significant cost reduc-

Kyocera
tions of energy consumption greater than 50%, reduction of energy consumption by greater than 85%, with digital manufacturing agility to address the 25% materials waste in the supply chain.
Unlike other digital printing systems, the Endeavour™ process is designed to be compatible with all colorant chemistries used in traditional dyeing. The system is an open platform, and any approved commercial colorant chemistry can be used in the system. The system can also be used with reactive, acid dyes, Vat dyes and a range of specialty colorants to enable digital dyeing with a wide range of substrate types. The production line replaces between three and ten traditional jet dyeing machines and the footprint and labor requirements are significantly reduced versus the traditional dyehouse.

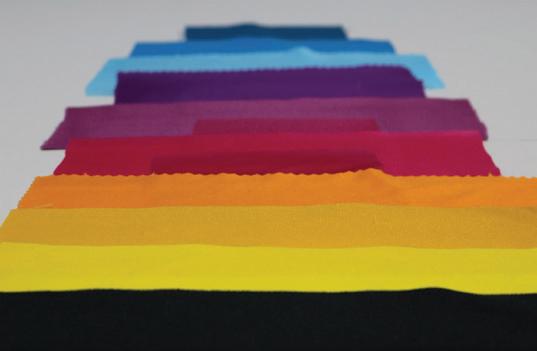
Works of art served as décor and samples of the brilliant reproduction of the Kyocera FOREARTH® digital textile printer. From largesize motifs, photos, random motif patterns to gradation, the print possibilities are endless, and especially suited for women’s fashion, sports and kids’ wear and home textiles. The system utilizes Kyocera Integrated Printing System (KIPS) to realize high-quality printing on a wide range of fabrics, including cotton, silk, polyester, nylon and blended fabrics. This offers FOREARTH® an edge for textile producers who what complex designs to print with a luxury handfeel.
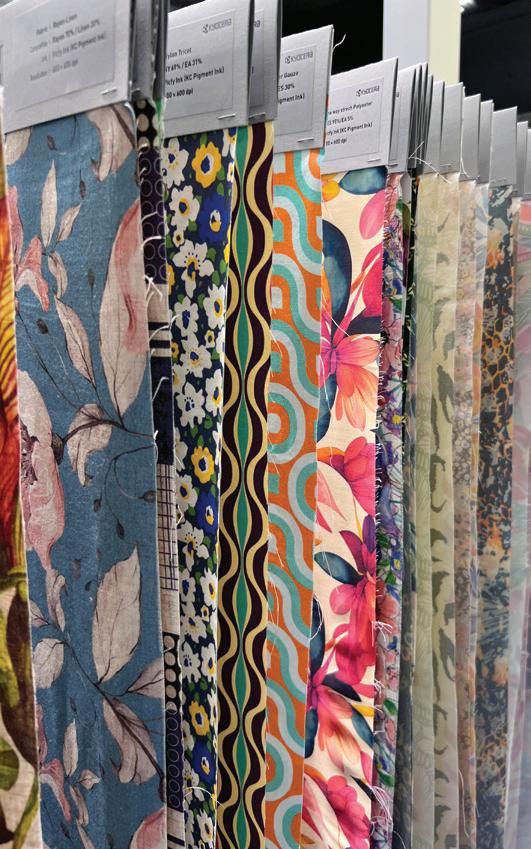
As a two-step process, printing and drying, no water used in production like other systems. The difference lies in the Allin-One Textile Printing System – KIPS, whereby FOREARTH® installs Kyocera’s inkjet print head which is top global share* for its digital textile printing, and by incorporating KIPS proprietary Picfy® pigment ink, pre-treatment liquid, and finishing agent, where the water free concept is realized.
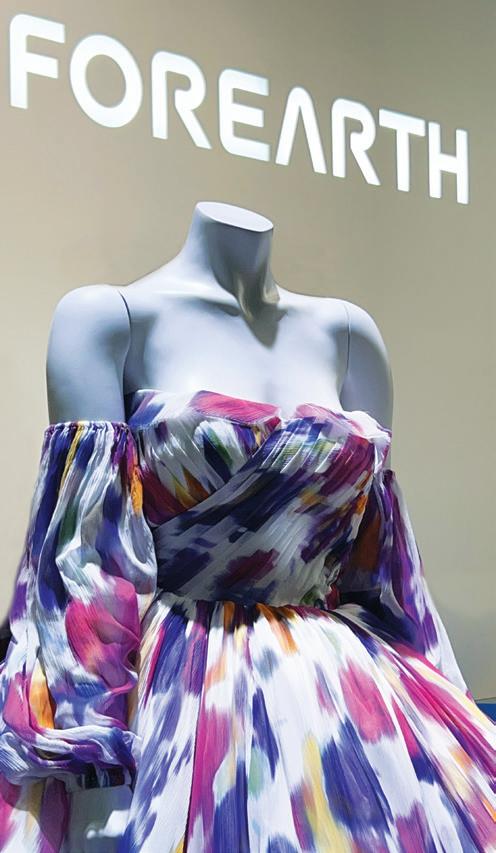
It has 18 printheads (Color – 16; Pretreatment Liquid – 1; Finishing Agent – 1), utilizing up to 8 colors (CMYK + 4 special colors) with a maximum print width of 1800MM and maximum cloth width of 1850 mm. Resolution is a sharp 600x600 DPI and print speed comes in at Standard: High-quality mode; 2 pass, 250 m2/h. The capacity and color is a show stopper.
*In terms of printing area, according to 2022WTiN.
Twine Solutions
Colorizing thread and yarn are also experiencing disruption. Twine Solutions brings innovation, the entrepreneurial spirit and decades of experience in the print and software industries to its new solution.

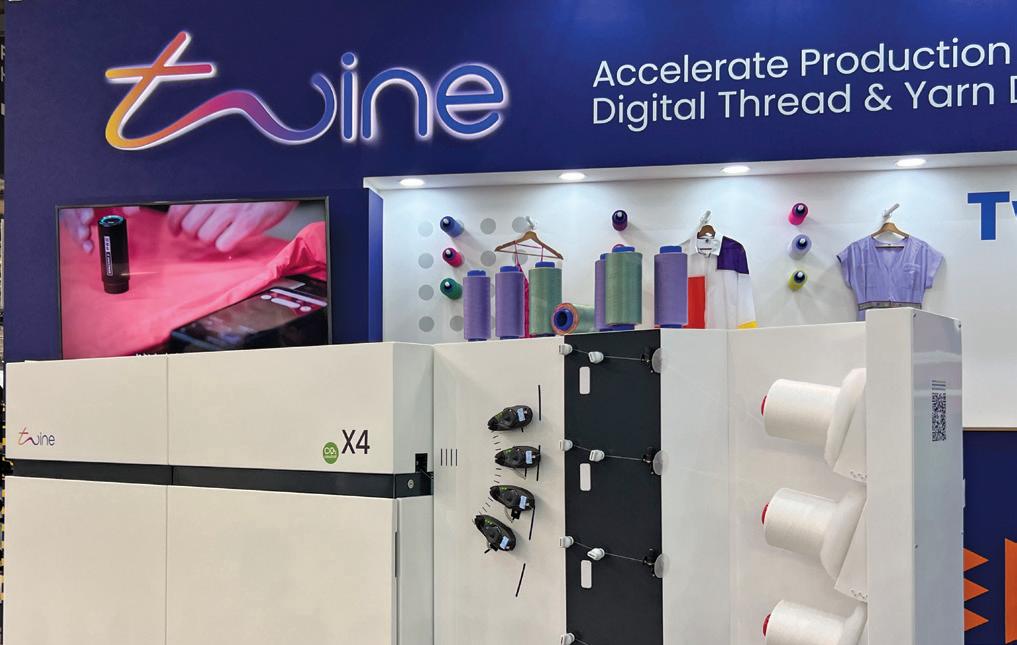
TwineX4 is a next-generation waterless, digital dyeing system for thread and yarn dyeing production, where textile manufacturers can optimize production processes, with accuracy, speed, efficiency and, yes, sustainability.
The system offers convenient on-demand, in-house capabilities for small to medium-sized batches, eliminating supply delays. This provides the quality product designers and textile producers want, with the flexibility to accelerate order fulfillment, and increase capacity to match the fast-paced demands of the fashion industry.
Sharon Ezra, Twine’s Product and Application Expert, and a fashion designer in highend Italian brands, says, “I know firsthand how big of an issue is color choice when it comes to samples and production processes. Brands always seek to differentiate themselves and want to know what colors you have in stock. Many times, you must compromise when the color you want is not available. With on-demand, you can print as many colors as you want.”
Highly energy-efficient, this system’s consumption is approximately 2.7 times more efficient per kg compared to the traditional dyeing processes. In-house dyeing allows designers to produce
RECYCLING SHIFT: SUSTAINABLE APPROACH AT END OF LIFE
Erema Group
PureLoop, member of Erema Group, shared their latest development in plastics recycling – the ISEC evo FibrePro:IV, specially designed for processing PET continuous fibers and fabrics. PureLoop specializes in combined shredder-extruder technology for the highly efficient recycling of clean production waste.
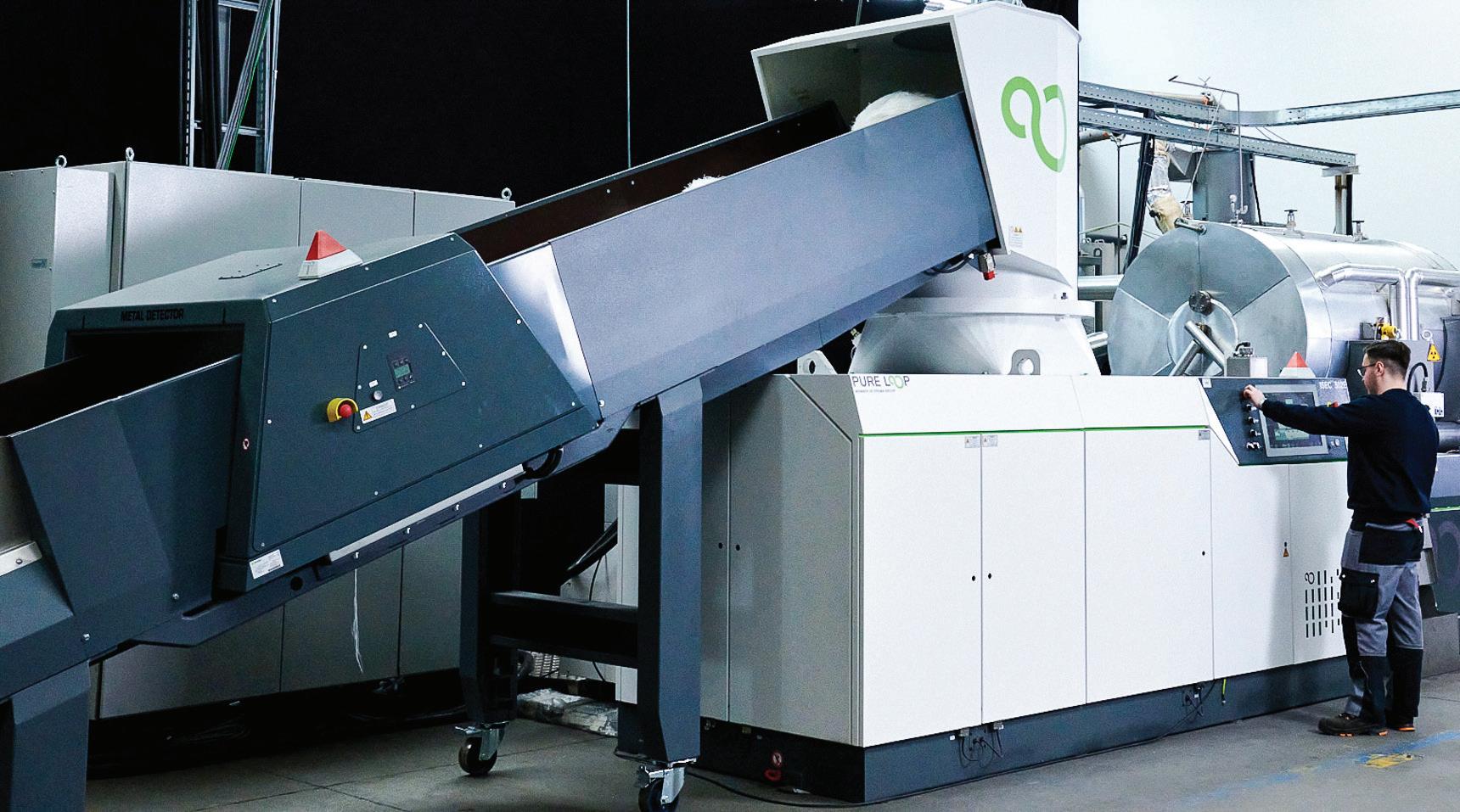
“Our ISEC evo machine is a material all-rounder for inhouse recycling that is particularly adept at processing fibers and textiles and has already been used for this application many times over. PE, PP, PA and PET in the form of fiber bales, ropes, filaments, textiles and nonwovens can be recycled using this shredderextruder combination,” says Manfred Dobersberger, Managing Director, listing some of the system’s special capabilities.
PureLoop displayed an innovative pilot project in fiber-tofiber recycling of polyester, a sample t-shirt which was made from 30% PT fiber recycled regranulated content from the ISEC evo FibrePro:IV. The project was in cooperation with RadiciGroup, a renowned Italian-based international fiber manufacturer. “Re- exact lengths of thread and yarn, reducing wasted materials by up to eight times the amount resulting from external supplier MOQs, and supporting lower waste-to-landfill goals. It also helps to minimize electricity and carbon emissions by reducing the need for excess inventory storage and streamlining the supply chain. cycling has enormous potential in the fiber and textiles sector. One thing I am sure of is that recycling will become a standard feature within the industry in the future. This project, initiated by the Radici Group, sees us taking an important step towards more sustainable production of fibers and textiles,” says Merlijn van Essen, Sales Manager, and responsible for this cooperation. (Continues on page 24.)
TwineX4 meets production requirements with its exceptional dyeing speed, averaging 21.6 kilometers per hour, wound on four cones, each capable of accommodating up to 1.5 kilograms in a single run. With its upgraded capacity, TwineX4 can dye up to two tons of thread/yarn per year.
RECYCLING SHIFT: SUSTAINABLE APPROACH AT END OF LIFE
PureLoop, and its ISEC evo FibrePro:IV, and RadiciGroup, an Italian-based international fiber manufacturer, collaborated on a pilot project in fiber-to-fiber recycling of polyester to manufacture a t-shirt made from 30% PT fiber recycled content, regranulated from the PureLoop system.
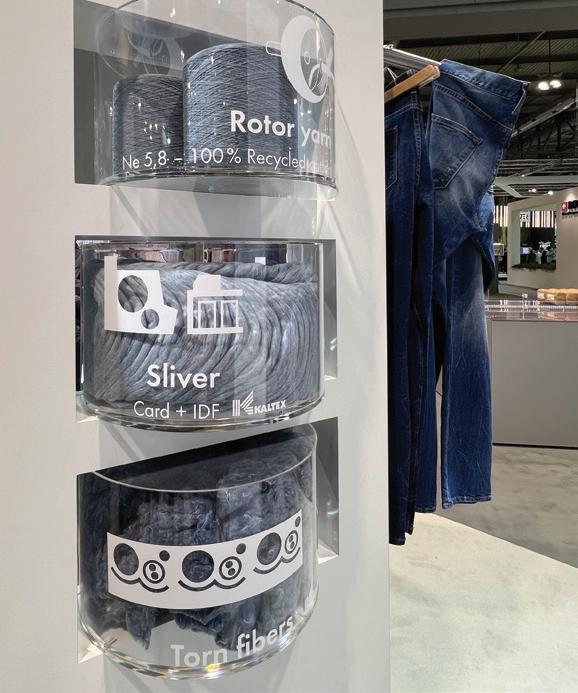
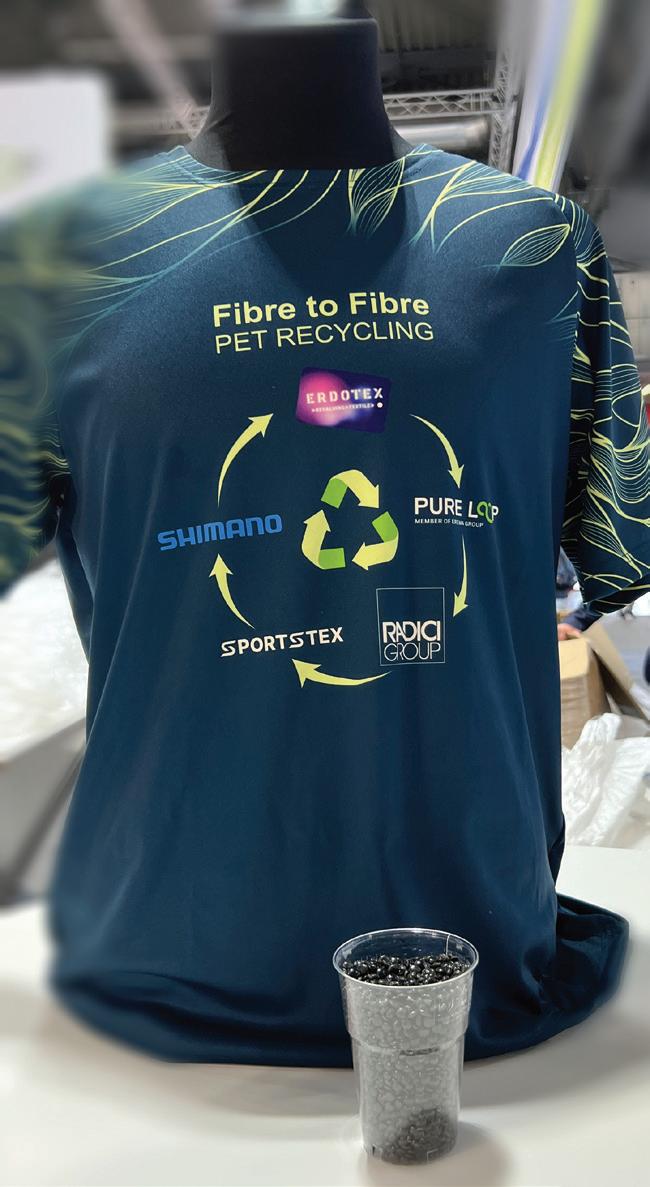
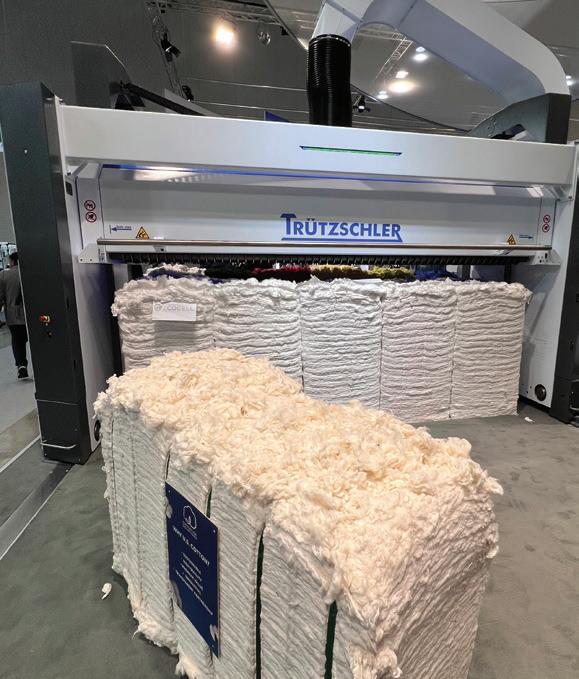
Trützschler
From waste to value is the mantra of TRUECYCLED recycling installations from Trützschler, makers of spinning technology solutions, as well as options for nonwovens, card clothing and man-made fibers.
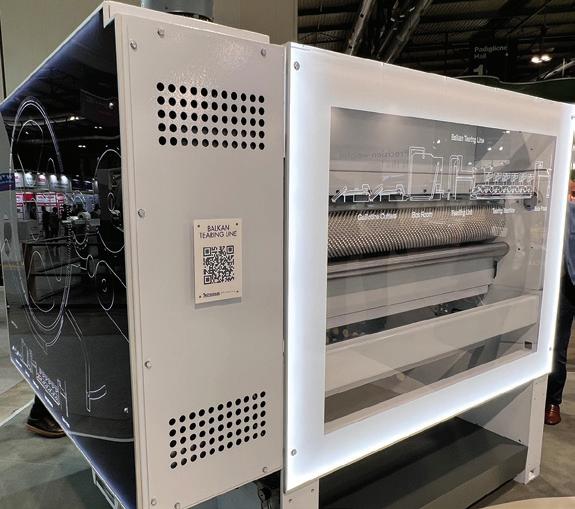
In a partnership with Balkan Textile Machinery, Inc. Co , Trützschler closes the loop and supports a circular economy by becoming the first full-liner in spinning preparation for recycling. Both Balkan and Trützschler are family-owned companies for whom sustainability in the textile chain is a major concern. Balkan’s machines help to cut, mix and tear textile waste into fiber tufts that are then pressed into bales of secondary fibers, which can be fed into the preparation process with Trützschler machines. Customers benefit from combined, perfectly finetuned, reliable and reproducible processes.
Once shredded, Trützschler blowroom lines for recycling feature flexible setting options and intelligent processes, facilitating perfect opening, cleaning and blending of synthetic and cotton secondary fibers. They also prevent unnecessary waste or new short fibers from being produced. The intelligent Card TC 19T for recycling converts shredded textile waste into quality fiber slivers for new yarns, the TRUECYCLED® brand.
(Continued from page 23.)
“This system offers fiber producers the ability to use recycled pellets in production, made from industrial waste,” says Gerold Breuer, Head of Marketing & Corporate Development, Managing Director. “The production from waste is in their hands, to use in the best possible way. They are in control with the ability to produce different through-put sizes.”
In August, the Erema Group launched another collaboration with Lindner Holding, in a 50:50 joint effort to create BLUEONE Solutions, a holding company focused on sharing expertise to execute research to create industry standards in plastics recycling. Lindner Washtech’s experience as a quality manufacturer of shredders and recycling facilities for the waste management industry for the 75 years will be combined with that of the extruder manufacturer Erema, active in plastics recycling for 40 years.
“‘A functioning recycling industry demands a focus on the entire process and value chain from waste collection and processing to recycling and the final plastic product,” says Manfred Hackl, CEO, Erema Group. “In detail, the recycling extruder, the upstream washing system and material handling can be optimally coordinated so that quality standards can be ideally met, and energy optimized – thanks to cross-process control and monitoring, supported by digital solutions. In the future, we will offer optimally coordinated all-in-one solutions that will enable our clients to buy a total package that is perfectly tailored to their needs.”
“We are now able to provide a complete line-up of technologically leading machinery which has been specifically developed for rotor and ring yarns from recycled materials,” says Markus Wurster, Director Sales and Marketing at Trützschler Group. “Customers benefit from less complexity when planning and executing a mill project. The combined processes from Trützschler and Balkan are perfectly fine-tuned, reliable and reproducible. And of course, customers have access to Trützschler’s premium service.” Osman Balkan, Owner of Balkan Textile Machinery, Inc. Co., adds: “I am very happy that we can join forces with such a strong international player like Trützschler. Together we can make a significant contribution to dealing with textile waste globally.”
Starlinger
Starlinger brings its recycling system to the industry with its recoSTAR line of equipment, which includes systems for non-wovens, woven bags, film and post-consumer waste. The technology offers a spectrum of innovative machinery solutions for the efficient recycling of a variety of plastics, such as PE and PP, PA, PS, PLA, PMMA, and many more. For PET bottle-to-bottle recycling applications, Starlinger offers the new recoSTAR PET art, an energy-efficient and user-friendly recycling system. It achieves 15% more output with less maintenance and space requirements than the previous model and saves around 21% in production costs.

Andritz
The display at ANDRITZ was all about recycling, in which the company has invested heavily. They have mechanical, chemical combined solutions, or anything a customer would want. ANDRITZ Recycling offers single equipment and complete conditioning systems comprising the following process steps: material feeding, shredding, conveying, separation, fine grinding, and storage of the finally conditioned material.
Textile fiber preparation lays the foundation for the subsequent textile recycling process steps, and ANDRITZ offers single equipment and complete fiber preparation systems, from material feed and shredding or tearing right up to the finally prepared textile material.
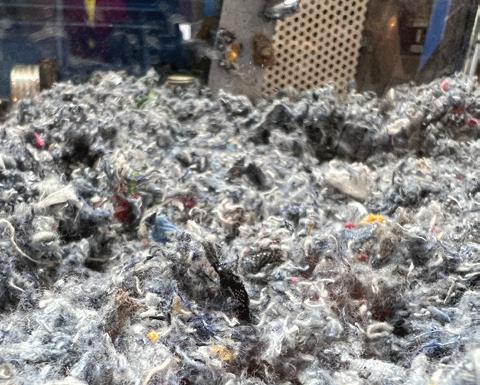
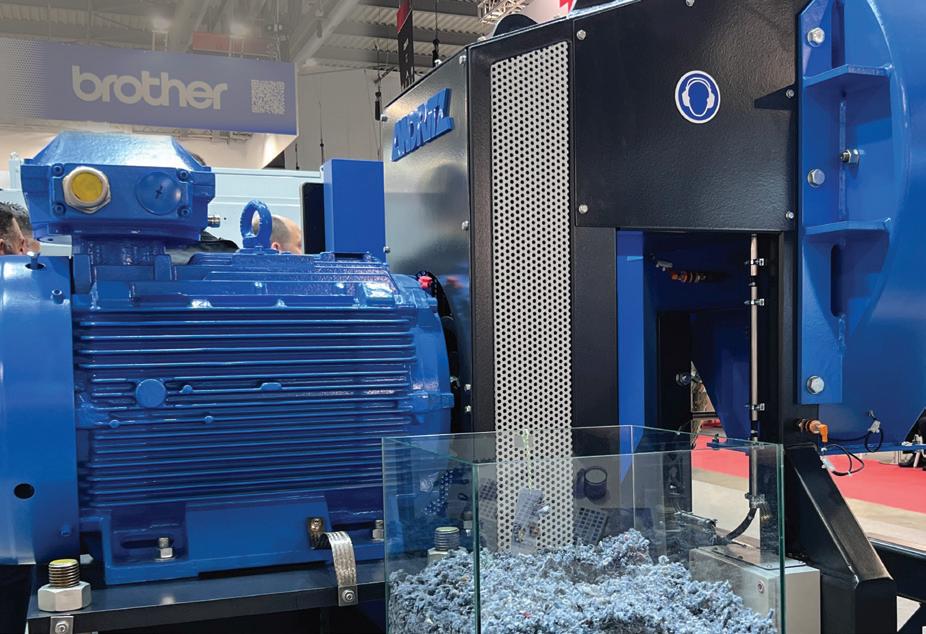

recoSTAR universal allows processing of fibres, filaments and nonwovens without precutting; only pre-portioning to fit conveyor belt dimensions is required. Starlinger
In other efforts, “As part of our ‘Circular Packaging’ concept, big bags made of polypropylene fabric are equipped with a material passport that allows to trace their life cycle from production to use to return and recycling,” explains Harald Neumüller, CSO. “This means that used big bags can be recycled without significant loss of quality and the regranulate used for producing new big bags – the packaging cycle is closed.”
Each recoSTAR line has specific characteristics, but the main features are common to all. Design is modular, so that based on the input material a line is configured from individual modules which are adaptable if necessary. As input materials and reapplication possibilities change, modules can be added and adaptations made in response to the market. Easy accessibility for maintenance, touch screen and visualization, one-button start-stop, inline quality control tools, and other features help reduce operating costs. So does the energy-efficient design – another mark of uncompromising commitment to sustainability.
Designed for recycling plastic scrap from industrial and postconsumer applications, recoSTAR dynamic are especially suited for processing hygroscopic, wet and/or pre-ground and foamed materials. recoSTAR universal allows processing of fibers, filaments and nonwovens in the ACTIVE shredder without pre-cutting; only preportioning to fit conveyor belt dimensions is required.
Recycling contributes significantly towards a positive perception of PET packaging: It increases ecological awareness and induces collection of post-consumer waste and obligatory reuse of recycled PET (rPET). Major brand-owners jump on the bandwagon and promote low carbon footprint and resource conservation.
“In the area of textile recycling, we are at the heart of the movement for state-of-the-art recycling solutions and collaborate with internationally renowned partners,” says Dr. Joachim Schönbeck, Chief Executive Officer. Earlier this year, the company delivered, installed, and commissioned a mechanical textile recycling line and an airlay line at Novafiber’s nonwovens production mill in Palín, Guatemala. The recycling line – the second tearing line they’ve supplied to Novafiber – processes post-industrial textile waste from Central America.
Overall, ANDRITZ has a diversity of solutions and cooperating partners covering the value chain from recovery of fiber to production of new yarn.
ANDRITZ offers a wide range of tearing machines to recycle textile waste into fibers from small to high volumes for respinning to new yarn, or to produce nonwoven roll goods and panels. Caryn Smith
