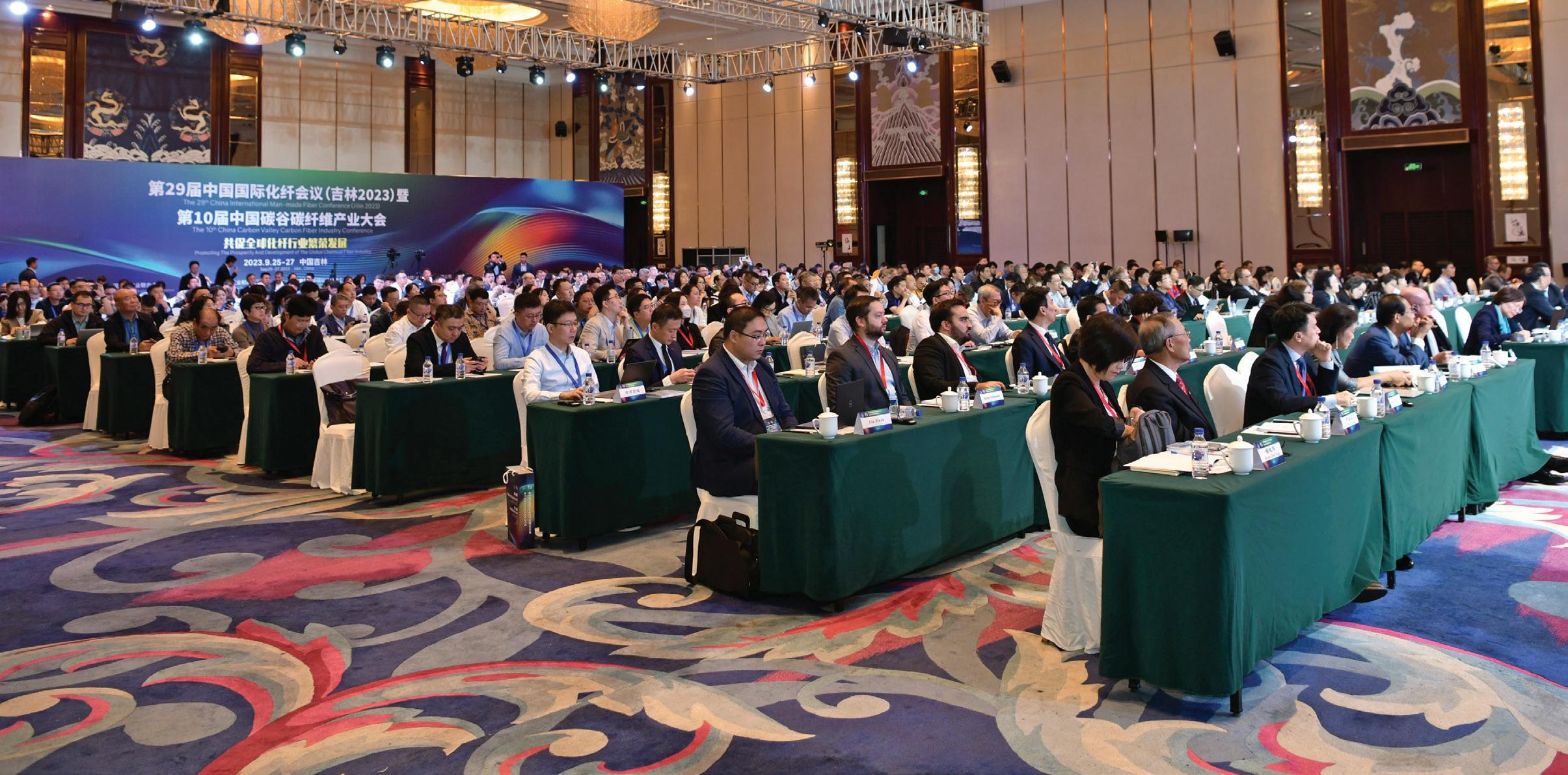
14 minute read
China’s Fast-Growing Carbon Fiber Demand
Expanding Sustainability Includes Exploring Fiber Advancements in China for the Growth of Their Green Economy
By Jason Chen
At the 29th China International Manmade Fiber Conference (CIMFC), September 26-27 in Jilin City, Jilin Province, China, experts and executives spoke about challenges and opportunities, advanced materials, manufacturing technologies, and sustainability relevant to the manmade fiber industry.
More than 30 speakers and approximate 400 fiber professionals attended the conferences for two days of programming. Speakers and attendees were primarily from mainland China, with representatives from the Europe, Japan, South Korea, Thailand, Taiwan, and Thailand also in attendance.
The conference was organized by the China National Textile & Apparel Council (CNTAC), the Jilin Municipal Government, the China Chemical Fibers Association (CCFA), the China Textile International Exchange Center (CTIEC), and Jilin Chemical Fiber Group (JCFG), the world’s second largest carbon fiber producer, which is headquartered in Jilin City. A combined conference, the 10th China Carbon Valley Carbon Fiber Industry Conference (CCVCFIC), was also held simultaneously with the CIMFC, making carbon fiber a main focus of the events.
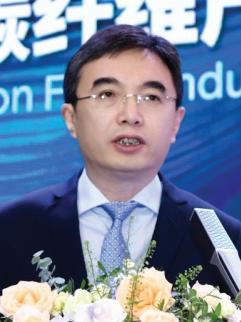
Mr. Duan Xiaoping, vice president of CNTAC, spoke about the challenges and opportunities for the Chinese manmade fiber industry.
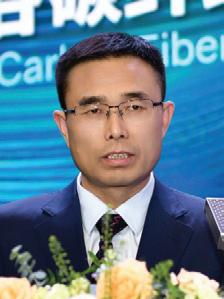
Ambition for Carbon Fibers
Jilin Province is where China started its dream for carbon fibers. In 1962, the Changchun Institute of Applied Chemistry (CIAC), a Chinese Academy of Sciences (CAS) branch located in Changchun City, the capital of Jilin Province, began the research and development for carbon fibers. But commercialization hadn’t been achieved until in the 2000s when JCFG and several other Chinese companies launched their carbon fiber lines.
JCFG, founded in 1959 as one of China’s oldest manmade fiber producers, started to manufacture carbon fibers in 2007. Today it has capacity of 49,000 metric tons per year, ranking No. 2 in the world, only after Toray. In addition, it has annual capacity of 160,000 metric tons of carbon fiber precursor, and 20,000 metric tons of carbon fiber composites.
JCFG has an even bigger plan. Currently, it is building several new plants, aiming to expand its capacity to exceed 400,000 metric tons per year in the near future. The goal includes 100,000 metric tons of carbon fibers, 330,000 metric tons of carbon fiber precursors, and 65,000 metric tons of carbon fiber composites.
Mr. Song Dewu, president of JCFG, spoke in the conferences.
JCFG’s ambitious expansion is based on China’s fast-growing carbon fiber demand. In 2022, China’s apparent consumption for carbon fibers reached 70,300 metric tons, up 21.98% from 57,600 metric tons in the previous year. Homegrown producers only met part of the demand, with 29,300 metric tons of carbon fibers and their related products imported in 2022. The fast growth and the gap between supply and demand attract Chinese companies to invest a lot more to expand their capacity rapidly.

Carbon Reduction Boosts
Carbon Fibers
The booming demand for carbon fibers is mostly boosted by China’s efforts for a green economy. In September 2020, China proposed its “double carbon goal” of reaching peak carbon emissions by 2030 and achieving carbon neutrality by 2060. For this goal, China will largely increase its renewable energy output to replace conventional energy, and wind energy is one such solution. Wind power generation emits zero greenhouse gases, and carbon fibers are the main materials for making turbine blades of wind power plants.
Compared to its main competitor fiberglass, carbon fiber helps reduce the blade weight by approximate 30% due to its light weight and high strength properties. The weight reduction would allow the production of longer blades, which have higher energy efficiency than their shorter counterparts. As a result, carbon fiber has been gradually replacing fiberglass, becoming a primary material for making wind power blades.
China installed over 37.63 million kilowatts of wind power capacity in 2022, increasing its total wind power capacity to 365 million kilowatts. The installation of wind power in 2022 consumed 23.5% of China’s carbon fibers, or 16,520 metric tons, according to ATA Carbon Fiber Tech Guangzhou Co Ltd (ATA), a Chinese consultancy. At the same time, China has a goal for wind power of exceeding 581 million kilowatts by 2025, which means the country will install at least another 216 million kilowatts of wind power capacity in the following three years, creating a demand for another 95,000 metric tons of carbon fibers from 2023 to 2025.
Car Weight Reduction
China’s double carbon goal also relies on emission reduction from other industries such as automobile and aerospace through using advanced materials such as carbon fiber reinforced polymers (CFRPs). For automobiles, CFRPs are often used to make the bodies, chassis, and suspension system components, reducing 20% to 50% weight compared to their metal counterparts. When an automobile reduces
10% weight, it typically reduces 6% to 8% energy consumption. As transportation accounts for around 10% of China’s total greenhouse gas emissions, the use of CFRPs will help China reduce a substantial amount of greenhouse gas emissions.
Mr. Ye Fuheng, senior engineer and researcher of China FAW Group Co Ltd (FAW), one of China’s oldest and largest automakers, spoke about carbon fibers’ use for FAW automobiles in the 29th CIMFC. He said that FAW had been developing carbon fiber-based components since 2012, and the company’s flagship model, Hongqi, has used carbon fibers for making engine hook, wrap frame, and other structural components. According to ATA, Chinese automakers took 2.56% of the country’s carbon fiber consumption in 2021, or a total of 1,475 metric tons. Automobiles’ carbon fiber consumption is expected to have a double-digit annual growth rate in the following decade.
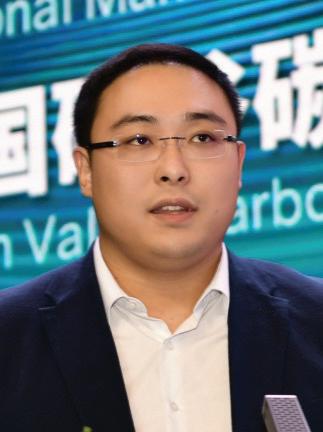
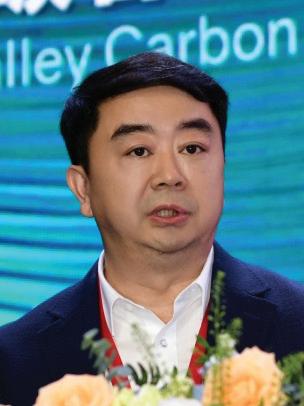
Low Manufacturing Cost, Recycling and Bio-Based Route
Although having all the advantages and benefits, carbon fibers are expensive to manufacture, impacting their adoption. Currently, the prices of carbon fibers mostly range from $13 to $35 per kilograms, depending on grades, manufacturers, and specific deals. As a result, experts are looking for new solutions to lower the manufacturing costs for market expansion.
Mr. Ziwen Liu, research assistant at Institut für Textiltechnik of RWTH Aachen University (ITA), introduced a method to shorten the stabilization time by 20% by using potassium permanganate (KMnO4), or nitrogen (N2), under atmospheric pressure as pretreatment media. Today, about 96% of the world’s carbon fibers are produced by spinning polyacrylonitrile (PAN) co-polymer to form PAN fibers, and then thermally converting the PAN fibers to carbon fibers. The thermal conversion process includes multiple steps such as stabilization and carbonization. Stabilization usually accounts for 15%-18% of the total cost of making carbon fibers. Mr. Liu said that the method not only reduces the stabilization time, but also lowers the stabilization temperature. The reduced time and lower temperature would result in energy reduction and cost saving.
Recycling is another solution for lowering carbon fiber cost, and also makes carbon fiber’s lifecycle more environmentally friendly. However, most of the recycling methods currently available in the market would produce short fibers and cause fiber damage, thus decreasing the quality and values of recycled carbon fibers.
Mr. Deniz Yesilyurt, research assistant at ITA, introduced a new method to reduce the fiber damage by optimizing surface treatment and sizing. He said in the conferences that this method would make multiple recycling for continuous carbon fibers a possible solution.
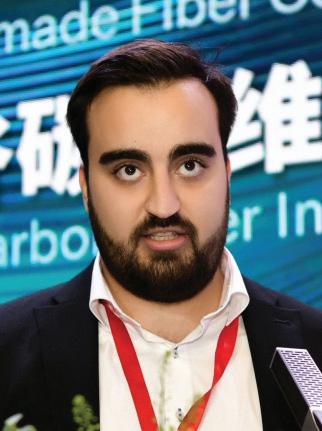
On the other hand, although carbon fibers help reduce weight and emissions, their production still emits a substantial amount of greenhouse gases as they mostly made from fossil-based PAN. Mr. Stefan Schonauer, another research assistant at ITA, said in the conferences that making acrylonitrile (ACN), the raw material of PAN, from bio-based glycerin is a promising solution. He said the glycerin used for making ACN is a waste in biodiesel production, which is significantly cheaper than crude oil. As a result, the glycerin route is both greener and more economic than the fossil routes.
Jason Chen is an international correspondent for International Fiber Journal . He is a leading journalist covering the fiber industry in Asia and a senior analyst who has published more than 50 books and reports for polymers, composites, and other advanced materials and technologies. He can be reached at jasonchen200501@hotmail.com
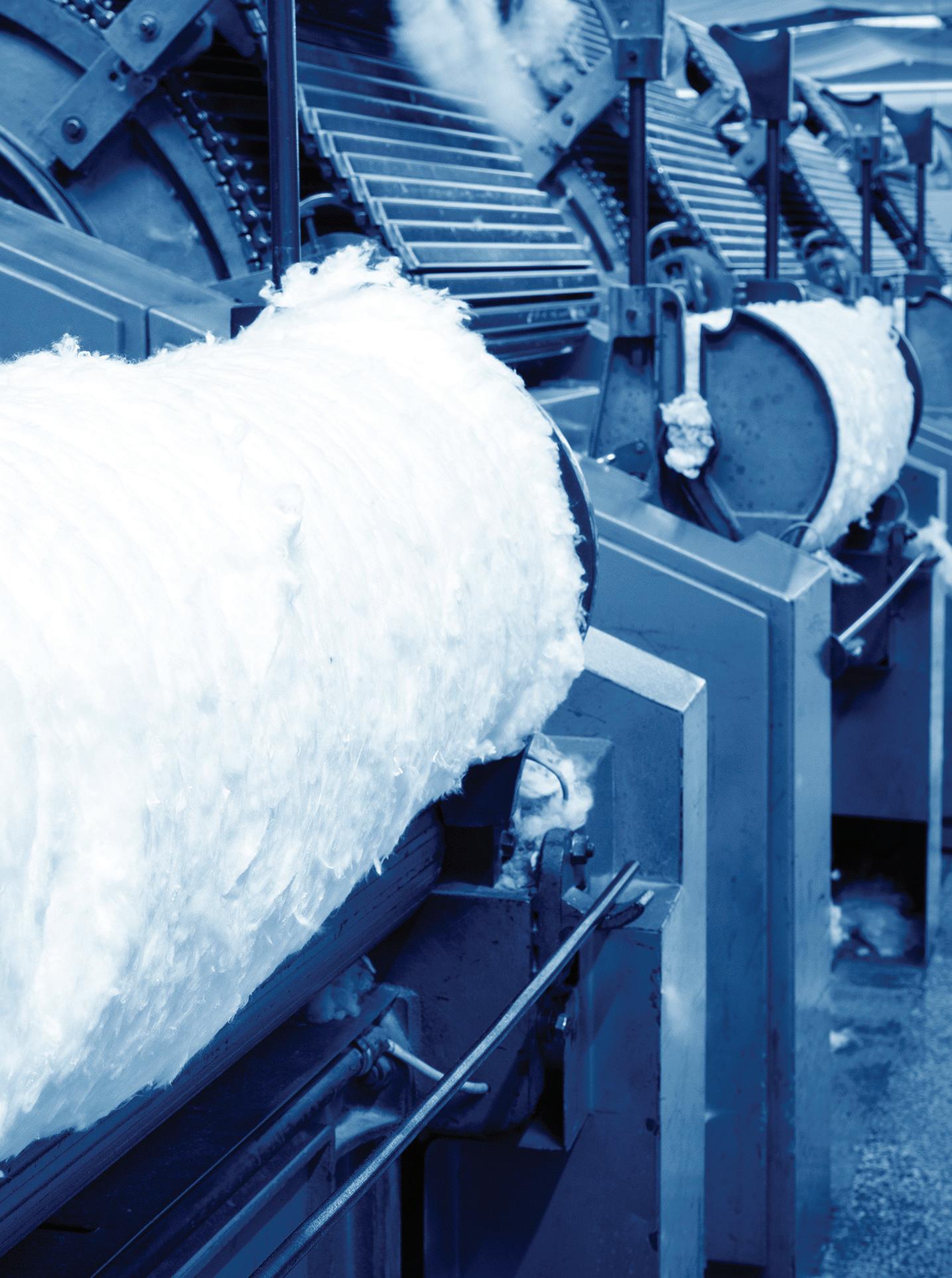
Chase Machine & Engineering Inc.
324 Washington Street
West Warwick, RI 02893
Tel: 1-401-821-8879 • Fax: 1-401-823-5543
Email: guygil@chasemachine.com
Website: www.chasemachine.com
Contact Person: Guy Gil
Founded in 1954, Chase Machine and Engineering designs and builds custom converting machinery for Film, Foil and WovenNonwoven Fabrics. We utilize 3-D modeling to design equipment such as Unwinds/Rewinds, Slitters and Laminators, Festooners, Blockers, and Spoolers/Traverse Winders, while integrating technologies such as Ultrasonics, Glue Dispensing, Impulse and RF welding as well as Thermal bonding. When you have a web converting project, contact CHASE!
EQUIPMENT & MACHINERY: Automation
Equipment I Cutting & Joining Equipment I Equipment to Manufacture Limited Single Use Products I Extrusion Equipment I Filtration Equipment I Pilot Lines I Ultrasonic Converting Systems
Davis-Standard
1 Extrusion Drive
Pawcatuck, CT 06379
Tel: 1-860-650-4886
Email: ndenerley@davis-standard.com
Website: www.davis-standard.com
Contact Person: Nichole Denerley
Davis-Standard is a global leader in the design, development and distribution of extrusion and converting technology. Our systems support manufacturing applications and customers in a wide variety of industries, including automotive, building & construction, consumer products, medical, and packaging. Davis-Standard is committed to engineering systems for you that are cost-effective, environmentally friendly, and offer a high return on investment.
END USES: Absorbent Hygiene Agriculture l Building Construction – General l Building
Construction – Insulation l Building
Construction – Roofing l Disposables l Electronics l Home & Office Furnishings –Floor Covering l Home & Office Furnishings
– Furniture l Home & Office Furnishings
– Miscellaneous l Medical or Surgical l Packaging l Pilot Lines l Plastic Machinery l Protective Disposable Apparel l Protective Durable Apparel l PPE l TransportationAirplane l Transportation – Automotive l Transportation – Marine l Web Forming Machinery, Complete Processing Lines l Wipes – Baby l Wipes – Industrial or Institutional l Wipes – Personal Care l Wipes – Specialty
Dilo Systems GmbH
P.O. Box 1551
69405 Eberbach, Germany
Tel: + 49 6271 940-0
Email: info@dilo.de
Website: www.dilo.de
DiloGroup supplies complete production lines for all nonwoven fabric technologies which employ staple fibre. A range of equipment is engineered for fibre opening/blending, recycling of textiles, web formation by carding or airlay, subsequent crosslapping and needle punching as determined by fabric characteristics and application. Potential fabric uses can either be disposable or durable ranging from geotextiles, automotive, filtration, synthetic leather and papermakers’ felts to cosmetic, medical and hygiene.
EQUIPMENT & MACHINERY: Filtration
Equipment l Web Bonding Machinery l Web Forming Machinery, Complete Processing Lines l Web & High-Loft Forming Machinery Components
EDWARD C. GREGOR & ASSOCIATES, LLC
10432 Bethpage Drive
Indian Land, SC 29707-5868
Tel: 1-803-431-7427
Email: ecg@egregor.com
Website: www.egregor.com
Contact Person: Edward C. Gregor
Edward C. Gregor is a specialty technical consultant, who works with clients to bring new disruptive material technologies to market in fiber, technical textiles and nonwoven fabric markets and M & A activities.
SERVICE PROVIDERS: Consulting
EMTEC Electronic GmbH
Gorkistr. 31
D-04347 Leipzig, Germany
Tel: + 49 341 245 7090
Fax: + 49 341 245 7099
Email: info@emtec-electronic.de
Website: www.emtec-electronic.com
Emtec Electronic, located in Leipzig, Germany, develops and manufactures very specialized test devices for the pulp and paper, nonwoven and textile industries. Globally positioned in more than 80 countries, their TSA Tactile Sensation Analyzer in combination with the cloud-based Virtual Haptic Library is the game changer in objectivity, digitization and sustainability and can be used for process & product optimization, R&D, quality control and troubleshooting.
EQUIPMENT & MACHINERY:
Lab/Testing Equipment
Fibre
Extrusion Technology Limited
Units F & G, Treefield Industrial Estate, Gelderd Road, Leeds, LS27 7JU, England
Tel: + 44 (0)113 253 7676
Fax: + 44 (0)113 253 6006
Email: sales@fetuk.com
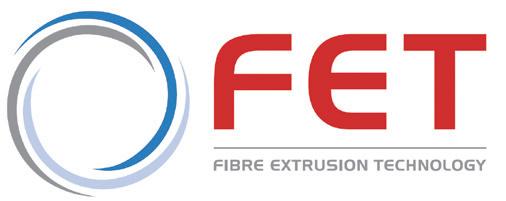
Website: www.fetuk.com
Contact Person: Richard Slack
Fibre Extrusion Technology (FET) designs, develops and manufactures small scale extrusion equipment for technical textile material applications. Typical applications include melt and wet spinning of biomedical materials, sustainable polymers, functional materials and for a wide range of composites. The FET product range covers melt spinning systems for multifilament, monofilaments, non-woven structures and also wet spinning systems for filaments and fibres.
EQUIPMENT & MACHINERY: Extrusion
Machinery Man-Made Fibers I Pilot Lines
Fi-Tech, Inc.
2400 Pari Way
Midlothian, VA 23112 USA
Tel: 1-804-794-9615 • Fax: 1-804-794-9514
Email: sales@fi-tech.com
Website: www.fi-tech.com
Contact: Jeffrey Bassett
Fi-Tech is the leading manufacturer’s agent and distributor serving the synthetic fiber, nonwoven fabric and technical textile industries in N. America. Our extensive offering of complete lines, machinery, technical components and spare parts gives manufacturers a single source access to the leading global suppliers. Fi-Tech is responsible for sales, marketing, customer service and other duties for these component and machinery suppliers: AstenJohnson, Autefa Solutions, Baldwin, Benninger, Brückner Textile Technology, Cason, Corino, Enka Tecnica, Erbatech, Futura, Galan Textile Machinery, Guarneri, Hansa Mixer, Hastem, Heberlein, Idrosistem, Mario Crosta, Mayer & Cie, Mozart Bladws, Neuenhauser Ontec, ProJet, Reifenhauser Reicofil, Sauer Fibrevision, Saureressig Surfaces, Schill & Seilacher, Shelton Vision, Spoolex, Tecnorama, TEMCO, Testa, T.EN Zimmer, and Tokuden.
EQUIPMENT & MACHINERY: Accessory
Equipment, Supplies l Chemicals l Extrusion Machinery l Finishing Equipment l Godet Rolls l Lab/Testing Equipment l Plastics Machinery l Separator Rolls l Web Bonding Machinery l Web Forming Machinery Complete
Processing Lines l Web & High-Loft Forming Machinery Components for Nippon Nozzle (Spinnerettes, Meltblown & Spunbond Dies, Spunlace Jet Strips & Filters, Spinnerette Inspection Equipment, Ultrasonic Cleaner and Pilot Meltblown line), Ramina Nonwoven Turnkey Production Lines, Sanyo Seiki Separator Rolls, Kluber Lubrication, Fourné Pilot Lines & Vacuum Pyrolysis Ovens, LUTZ® exactly Staple Cutter Blades and Chopping Blades, Reiners & Furst (Ring Spinning), Yamauchi Cots & Spinning Aprons, Strayfield Radio Frequency Dryers.”
EQUIPMENT & MACHINERY: Fiber Pilot and Plant Spinning Equipment I Fiber Preparation Machinery and Parts I Meltblown Lines I Nippon Nozzle Spinnerettes, Dies and Nonwoven Equipment I Spinnerette
Measuring Equipment I Ultrasonic Cleaning Equipment I Strayfield Radio Frequency
Dryers I Web Forming Machinery, Complete Processing Lines
HYDAC Process Technology GmbH
Am Wrangelflöz 1
D-66538 Neunkirchen, Germany
Tel: + 49 (0) 6897-509-1241
Fax: + 49 (0) 6897-509-1278
Email: thomas.schorn@hydac.com
Website: www.hydac.com
Contact Person: Mr. Schorn
HYDAC Process Technology GmbH as part of HYDAC group is your contact for fluid filtration in the production of polymers. Filter elements made out of Chemicron® are pleated as standard or tailor-made and have proven most effective in this field. Our filters are high performance quality products so we can ensure the function and the extension of the service life of components, systems and machines.
EQUIPMENT & MACHINERY: Filtration
Frankl & Thomas
111 Smith Hines Road Suite A Greenville, SC 29607
Toll Free: 1-800-832-7746
Tel: 1-864-288-5050 • Fax: 1-864-234-7544
Email: info@frankl-thomas.com
Website: www.frankl-thomas.com
Contact Person: Robina Hogan
Tel: 1-704-575-4333
Email: robina.hogan@frankl-thomas.com
Contact Person: Michael Alexander
Email: Mike.alexander@frankl-thomas.com
“Frankl & Thomas, in business since 1946, is the premier North American representative
Equipment l Filtration-Liquid Nonfood l Polymer Filtration Advancing Engineered Material Solutions
INDA, Association of the Nonwoven Fabrics Industry
1100 Crescent Green, Suite 115
Cary, NC 27518 USA
Tel: +1-919-459-3729
Email: jtessari@inda.org
Website: www.inda.org
Contact Person: Joe Tessari
INDA, the Association of the Nonwoven Fabrics Industry, serves hundreds of member companies in the nonwovens/engineered fabrics industry to achieve business growth. Since 1968, INDA helps members convene and connect, innovate and develop their businesses. INDA’s educational courses, business intelligence and market insights, test methods, consultancy and issue advocacy help members succeed by providing information they need to better plan and execute their business strategies.
INDA Media is the business-to-business publishing arm of INDA and publisher of International Fiber Journal and International Filtration News, which reach a vast network of professionals who employ fibers, filaments, and filtration systems to optimize their application environments.
SERVICE PROVIDERS: Government Agencies, Associations
Live Oak Capital, LLC
10432 Bethpage Drive Indian Land, SC 29707-5868
Tel: 1-803-431-7427
Email: ecg@egregor.com
Website: www.egregor.com
Contact Person: Edward C. Gregor
Specializing in mergers and acquisitions of technical textiles and the nonwoven fabrics industry having company sales of between $10 million and $1 billion. Focus is on family-owned businesses and smaller public companies.
SERVICE PROVIDERS: Acquisitions
MEZGER, INC.
170 Metro Drive
Spartanburg, SC 29303 USA
Tel: 1-864-542-8037
Fax: 1-864-542-8039
Email: info@mezgerinc.com
Website: www.mezgerinc.com
Contact Person: Mark Mezger
MEZGER INC. is a global distributor of equipment, testing instruments and accessories for the fiber and filament yarn extrusion processes. Such as online sensors, spinnerets, spin packs, screens, gaskets, ovens, inspection systems and much more.
EQUIPMENT & MACHINERY: Accessory Equipment, Supplies l Lab/Testing Equipment
Mid Atlantic Industrial Textiles Inc.
7854 Browning Road
Pennsauken, NJ 08109
Toll-Free 1-855-793-0325
Tel: 1-609-261-4886
Fax: 1-609-261-6345
South Carolina Warehouse
Tel: 1-864-436-1854
Email: reginal@yanpai.com
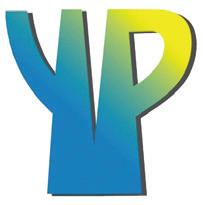
Air and liquid Filtration media now. Filter press cloth, dust collector fabrics, woven and nonwoven, non-woven membrane laminated, and chemical finishes all direct from Yanpai parent plant, in stock in the USA. No stress and no aggravation dealing with China. Deal directly with the world’s largest manufacturer through N. America Yanpai office. High quality, good service, low prices. We stock what you need!
RAW MATERIALS/MATERIALS/MATERIAL
SUPPLIERS: Coatings l Filtration-Air l
Filtration- Liquid Nonfood l Nonwoven Materials l Plastic-Formed Netting & Scrims l Woven Materials
SAHM – Georg Sahm GmbH & Co., KG
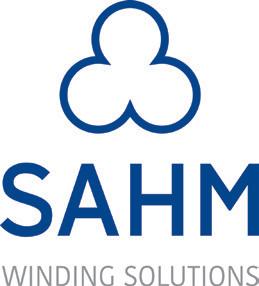
Sudetenlandstr.33
37269 Eschwege, Germany
Tel: + 49 5651 804-0
Fax: + 49 5651 13620
Email: info@sahmwinder.com
Website: www.sahmwinder.com
Contact Person: Oliver Eichenberg
SAHM is the worldwide technology leader for winders in the markets including high performance fibers, carbon fibers and slit film tapes for the converting industry. SAHM supports companies with winding solutions for a wide range of applications and materials and is always ready for new challenges. Sales and service will be supported by American Starlinger-Sahm, Inc. based in Fountain Inn, SC.
EQUIPMENT & MACHINERY: Winding Technology
SCHWING Technologies
300 Carnegie Center Drive #150 Princeton, NJ 08540 USA
Tel: 1-609-786-2404
Email: info@schwing.tech
Onyx Specialty Papers, Inc.
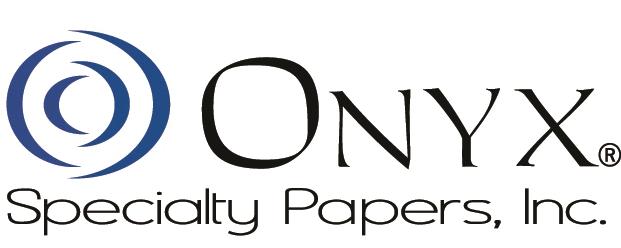
40 Willow Street
South Lee, MA 01260
Tel: 1-413-243-1231
Fax: 1-413-243-4602
Email: info@onyxpapers.com
Website: www.onyxpapers.com
Contact Person: Pamela Hayden
Onyx Specialty Papers, Inc. is committed to the design, development and manufacture of synthetic and fiber based filter media that meets complex and demanding performance challenges. Through an extensive knowledge of materials and processes, our team of accomplished scientists and engineers collaborate with customers to devise creative solutions that meet both performance and end use attributes.
RAW MATERIALS/MATERIALS/MATERIAL SUPPLIERS: Papers
Website: https://schwing.tech
Contact Person: Sales Dept.
SCHWING Technologies is a leading supplier of thermal cleaning equipment for the safe removal of polymer from spinnerets, filters, and extrusion tooling. SCHWING has over 50 years of experience cleaning spinnerets and tooling at its headquarters in Neukirchen-Vluyn, Germany – with North America office located in Princeton, New Jersey. Products include VacuClean, InnovaClean, CompactClean, and post-treatment solutions. Systems are energy efficient and environmentally friendly.
EQUIPMENT & MACHINERY: Accessory Equipment, Supplies
Sossna Gmbh
Fürst-Leopold-Allee 96
46284 Dorsten/Germany
Tel. + 49 (0) 2362 993710
Email: sossna@sossna.de
Website: www.sossna.de
Contact Person: Susanne Sossna
SOSSNA GMBH – SOSSNA Spinnerets(R) - is one of worldwide leading manufacturer of spinnerets for all kinds of high pressure, stainless steel spinnerets for melt spinning, dry spinning and the production of non-woven. Spinnerets and spin packs according samples or drawings can be supplied, and - in additionprofessional service for the development of new spinnerets or optimization of existing spinnerets and spin pack design is provided.
EQUIPMENT & MACHINERY: Polymer Equipment, Materials, Services l Spinnerets, Spin Packs
Tentoma Packaging Solutions
Smøl 1, DK-6310 Broager, Denmark
Tel: + 45 79 30 62 10
Email: info@tentoma.com
Website: www.tentoma.com
Tentoma manufactures RoRo StretchPack® packaging solutions, which are particularly suitable for 6-sided packaging of large rolls and products. RoRo StretchPack® provides 100% waterproof sealed packaging, and packaging and sealing are done in one automated operation. This reduces energy consumption and film consumption by 25-60% compared to conventional ways of packaging. Tentoma installs packaging systems for customers worldwide.
EQUIPMENT & MACHINERY: Packagin
Zund America, Inc.
8142 South 6th Street, Oak Creek, WI 53154
Tel: 1-414-433-0700
Email: infous@zund.com
Website: www.zund.com
Zünd digital cutters, manufactured in Switzerland, are industry-leading cutting solutions for (tech-)textile, composites, foam, and many other industrial applications. Unmatched in versatility and modularity, Zünd systems are completely customizable, with specialized tooling and application-specific workflow automation. This includes efficient nesting options for maximum yield, marking/labeling devices, projection-assisted sorting & kitting, automated/ robotic loading/off-loading, IoT-based production monitoring and analysis, and so much more.
EQUIPMENT & MACHINERY: Automation
Equipment l Cutting & Joining Equipment
By Len LaPorta Managing Director of Investment Banking, Wiley Bros.-Aintree Capital, LLC

Len LaPorta is a managing director of Investment Banking at Wiley Bros.-Aintree Capital, LLC – a 75-year-old firm, located in Nashville, TN, focused on investment brokerage and underwriting municipal bonds for utility districts in the state of Tennessee. Len brings to the Firm experience in crossborder M&A transactions between USA and Europe, advises business owners on sell-side and buy-side transactions, capital advisory, and valuations. Len is a graduate of the U.S. Naval Academy with MBA from Boston College and a veteran of the U.S. Navy. He is also a member of INDA’s non-woven Technical Advisory Board. llaporta@wileybros.com or (615) 782-4107.