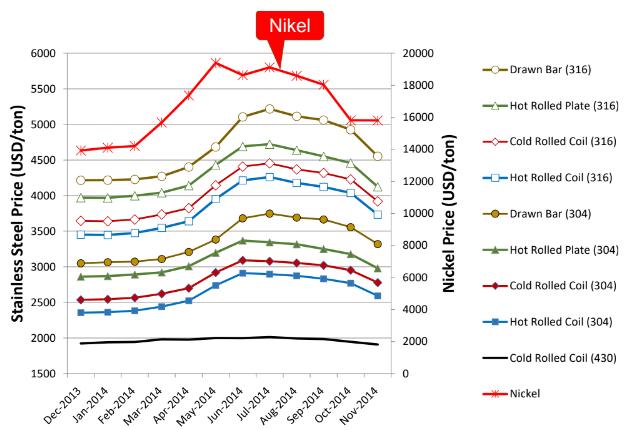
33 minute read
● Proses AL
Prosesinidilakukanpadatekananatmosferdantemperaturyanglebih rendah (95-1000C). Pada dasarnya hampir sama dengan proses di HPAL namun Fe dan Al tidak mengendap selama leaching. Teknologi ini juga mengalami beberapa perkembangan seperti penggunaan leaching agent yang dapat diregenerasi. Salah satunya, diterapkan pada Proses Jaguar. Reagen pelindi berupa asam klorida dapat diperoleh kembali melalui proses pyrohydrolisis. Tidak hanya reagen pelindi, presipitate agent seperti magnesia juga diperoleh kembali[1] .
Gambar 4. Diagram Alir Proses Jaguar [4]
Advertisement
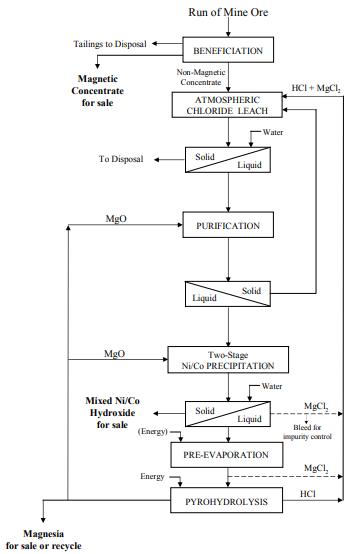
Secara umum, proses atmospheric agitation leaching (AL) memiliki beberapa kelebihan dan kekurangan sebagai berikut.
Tabel 3. Kelebihan dan Kekurangan Proses AL [1]
Kelebihan Kekurangan
CAPEX lebih rendah daripada HPAL
Recovery Ni dan Co lebih rendah
Teknologi dan peralatan lebih konvensional
Kurang selektif terhadap besi, konsumsi asam lebih besar
Konsumsi energi lebih rendah dari HPAL
Kinetika reaksi berjalan lebih lambat
Kendali proses lebih mudah
Peluang dan Tantangan
Belum teruji secara komersial
Cadangan bijih nikel dunia didominasi oleh nikel laterite dengan kontribusi 70% dari total cadangan, sedangkan 30% sisanya berupa nikel sulfida. Begitupun di Indonesia, tipe bijih nickel yang banyak tersedia adalah dalam bentuk nikel laterit, baik untuk jenis limonit maupun saprolit. Di sisi lain, tekanan dari industri mobil listrik yang berkaitan dengan kebutuhan sumber nikel terus berlanjut. Hal ini dikarenakan lebih dari 70% dari total harga kendaraan listrik merupakan hasil kontribusi dari baterai tersebut. Lalu, jika ditelaah lebih lanjut 30% dari biaya baterai berasal darimaterialkatoda. Untuk baterai NMC 811misalnya, 80% material katoda adalah nikel sehingga kebutuhan akan rantai pasok nikel sangat vital peranannya untuk perkembangan industri mobil listrik kedepannya.
Isu berikutnya terkait industri baja tahan karat yang diprediksi masih tetap mendominasi konsumsi nikel kedepannya. Umumnya, nikel yangdigunakanuntukpaduanpadabajatahankaratadalahnikelkelas 2 yang merupakan produk akhir proses pirometalurgi.
Gambar 5. Pengaruh Harga Nikel Terhadap Harga Baja Tahan Karat
Dinamika harga baja tahan karat sangat dipengaruhi oleh fluktuasi harga nikel, khususnya untuk baja-baja yang mengandung nikel pada unsur paduannya. Kenaikan harga nikel akan menyebabkan naiknya harga baja tahan karat. Begitupun sebaliknya, penurunan harga nikel juga akan menurunkan harga baja tahan karat. Pada CRC 430 tidak banyak terjadi perubahan karena tidak melibatkan nikel dalam unsur paduannya. Data dari GSKM 2021 menunjukkan bahwa bahan baku untuk pembuatan baja tahan karat sebagian besar masih diimpor dari luar negeri. Contohnya yang dilakukan oleh PT Jindal Stainless Indonesia, PT IMR ARC Steel, dan perusahaan-perusahaan lain.
Industri berikutnya yang sangat bergantung pada ketersediaan nikel adalah paduan-paduan yang berbasis nikel yang digunakan untuk aplikasi temperature tinggi yang biasa disebut sebagai superalloy. Ketergantungan ini dikarenakan paduan berbasis nikel memiliki kekuatan, ketahan fatigue, dan ketahanan korosi yang cukup tinggi untuk operasi temperature tinggi. Selain itu, kemampuan luar biasa yang jarang dimiliki oleh material lain adalah ketahanan creep pada temperature tinggi. Umumnya suatu material akan mengalami creep ketika suhu operasi telah mencapai 30-40% dari melting point-nya. Contohnya aluminium yang memiliki titik leleh 660°C dan titanium yang memiliki titik leleh 1668°C akan mengalami creep ketika suhu operasi masing-masing telah mencapai 150 and 350°C. Namun, hal yang berbeda terjadi pada paduan berbasis nikel. Pada temperature operasi 850°C, paduan berbasis nikel masih cukup kuat untuk menahan terjadinya creep dan stress rupture.
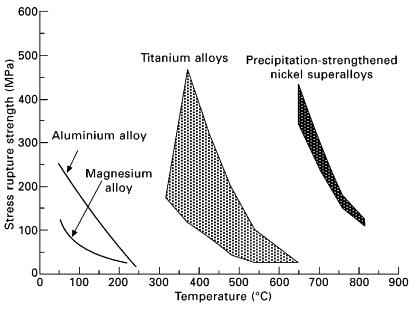
Gambar 6. Hubungan Temperature Terhadap Stress Rupture Strength
Contoh penggunaan paduan berbasis nikel yaitu sebagai komponene pesawat terbang, gas turbine engines, reaktor nuklir, turbin pembangkit listrik, peralatan petrokimia, dan mesin roket. Dimana kebutuhan akan nikel pada industri superalloy diprediksi akan terus meningkat mencapai 481.000 ton pada 2023.
Tentu hal tersebut menjadi peluang sekaligus tantangan khususnya bagi indonesia sebagai negara yang memiliki cadangan nikel terbesar di dunia. Untuk menjawab tantangan tersebut, diperlukan langkah yang tepat agar sumber daya dan cadangan yang tersedia dapat dimanfaatkan sebagaimana mestinya. Salah satu langkah Indonesia dalam menjawab tantangan tersebut adalah melalui pembagunan smelter-smelter untuk mengolah nikel menjadi produk-produk nikel kelas 1, seperti nikel sulfat, kobalt sulfat, MSP, MHP ataupun nikel kelas 2, seperti FeNI, NPI, dan Ni-matte.
DiIndonesia,industrihilirpengolahannikeltelahbanyakberkembang khususnya pada sektor peleburan dan pemurnian nikel. Saat ini, beberapa teknologi yang telah diterapkan di Indonesia antara lain:
1. Blast Furnace → mengasilkan NPI
2. RKEF → mengasilkan NPI, FeNi, dan Ni-matte
3. HPAL → mengasilkan Ni sulfat, Co sulfat, MSP, dan MHP Adapun rincian beberapa pabrik peleburan dan pemurnian nikel yang telah, sedang, dan akan dibangun adalah sebagai berikut.
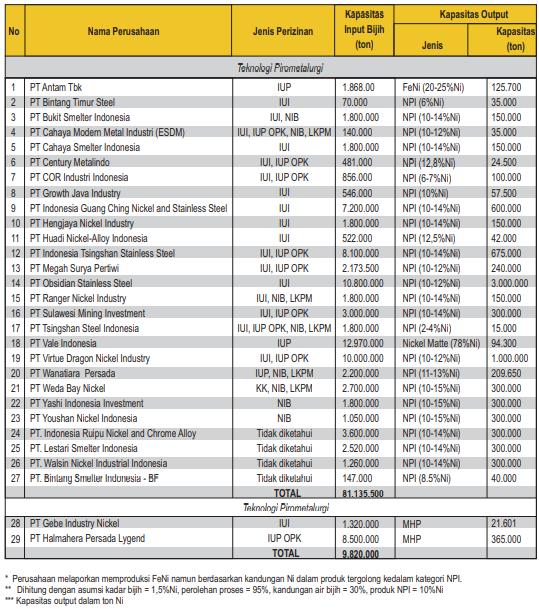
Gambar 7. Daftar Perusahaan Peleburan dan Pemurnian Nikel
Teknologi Pirometalurgi dan Hidrometalurgi yang Telah Beroperasi

Tahun 2021
Gambar 8. Daftar Perusahaan Peleburan dan Pemurnian Nikel
TeknologiPirometalurgiyang SedangdanAkan DibangunTahun 2021
Gambar 10. Daftar Perusahaan Peleburan dan Pemurnian Nikel Teknologi Hidrometalurgi yang Akan Dibangun Tahun 2021
Aspek penting yang perlu diperhatikan dalam pengembangan industri nikel adalah terkait keberlanjutan dan aspek lingkungan. Perilaku konservasi sumber daya dan cadangan perlu ditekankan sedemikian sehingga diperoleh ketahanan industri secara optimal. Selain itu, dampak lingkungan yang berkaitan dengan efek gas rumah kaca juga perlu dipertimbangkan. Sebagai perbandingan, emisi yang dihasilkan oleh pengolahan nikel kelas 1 melalui proses HPAL memberikan emisi CO2 yang lebih rendah dibandingkan dengan pengolahan nikel kelas 2 melaluijalurpirometalurgi.Akantetapi,jikadilihatdariaspeklimbah, proses hidrometalurgi khususnya HPAL menghasilkan limbah sisa hasil pengolahan mencapai 128 ton per ton Ni yang diproduksi atau sekitar 3 kali lipatnya dari SHP (sisa hasil pengolahan) proses pirometalurgi.
Gambar 11. Emisi CO2 Hasil Proses Peleburan dan Pemurnian pada
Berbagai Jenis Bijih Untuk Tiap-Tiap Teknologi
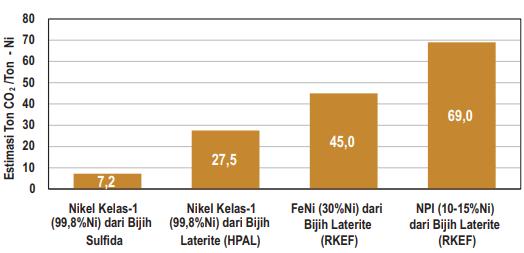
Gambar 12. Estimasi Jumlah SHP Hasil Peleburan dan Pemurnian Nikel
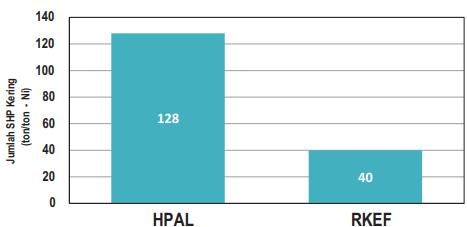
Untuk mengatasi hal tersbut, beberapa poin penting yang perlu dilakukan demi pengembangan industri nikel di indonesia adalah sebagai berikut.
1. Ketahanan sumber daya dan cadangan bijih nikel-kobalt harus diperhatikan untuk keberlanjutan industri.
2. Faktor lingkungan akan menjadi salah satu aspek penting yang mempengaruhi pengembangan industri nikel-kobalt.
3. Pengembangan teknologi yang lebih ramah lingkungan dan upaya pemanfaatan SHP perlu ditingkatkan untuk mengurangi dampak negatif terhadap lingkungan.
THE IMPLEMENTATION OF CIRCULAR ECONOMY ON THE FIELD OF METALLURGY
Definisi Umum Circular Economy
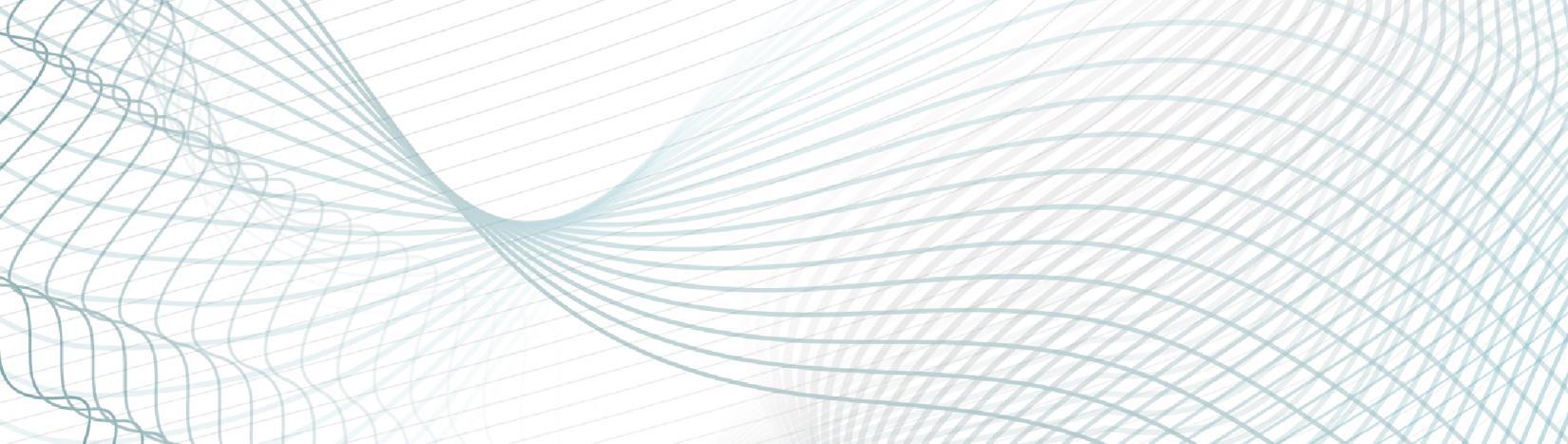
Circular economy merupakan ekonomi dengan pendekatan sistemik untuk menanggulangi berbagai masalah terutama limbah dengan cara mengolah kembali limbah hasil dari produk. Akan tetapi, circular economy jauh lebih luas dari daur ulang. Pada circular economy produk semenjak awal sudah didesain agar tidak hanya sedikit limbah namun dapat dengan mudah diolah kembali juga.
Prinsip Circular Economy:
● Eliminate waste and pollution
● Circular product and material
● Regenerate nature
Eliminate waste and pollution, pada circular economy limbah dan polusi di desain untuk sesedikit mungkin bahkan tak ada baik dalam pembuatan maupun pemakaian benda.
Circular product and material, pada circular economy benda didesain untuk kuat, tahan lama, serta material yang digunakan dapat digunakan kembali
Regenerate nature, pada circular economy penggunaan bahan bakar tidak terbarukan dihindari.
Circular Economy di Indonesia
Circular economy di indonesia masih menggunakan model linear, namun model linear ini merupakan model yang tidak berkelanjutan untuk jangka panjang karena pendekatan sistem linear menggunakna pendekatan “ ambil - pakai - buang”
Di Indonesia, terdapat beberapa faktor pendorong circular economy dari eksternal maupun internal, faktor eksternal berupa kebijakan yangkonsistenuntukmendukungimplementasicirculareconomy, tax regulation yang baik, sampai spesifikasi konsumen. Sedangkan faktor pendorong internalnya berupa corporate responsibility, shareholder pressure, competitiveness, sampai budaya dan perilaku yang baik.
Selain itu, juga terdapat hambatan dalam implementasi ekonomi sirkular dari eksternal dan internal. Hambatan eksternalnya berupa kebijakan pemerintah yang tidak mendukung, kurangnya permintaan konsumen, terbatasnya rantai pasokan, sampai terbatasnya teknologi dan infrastruktur. Sedangkan dari sisi internal yaitu adanya model bisnis yang sangat komersil sampai budaya dan sikap yang tidak mendukung.
Peran Metalurgi dalam Circular Economy
a. Product Design
Pada kehidupan sehari-hari, apapun barang disekitar kita tentunya didesain oleh industri agar siap digunakan. Pada saat ini, Ellen Macarthur Foundation sedang melakukan kampanye dan pengadaan perjanjian dengan negara-negara dan perusahaan-perusahaan besar di dunia mengenai circular economy, termasuk industri metalurgi. Dalam circular economy ini, tentunya product design terlibat dalam menunjang circular economy ini berhasil. Product design dalam industri metalurgi sangat dibutuhkan, apalagi industri metalurgi yang rata-rata belum bisa menghasilkan produk yang sustainable atau memenuhi konteks circular economy.
Dalam kasus aluminium, ⅓ dari Aluminium saat ini yang ada di dunia diproduksi dengan proses daur ulang dan akan meningkat 50% pada tahun 2050. Tujuan ini tentu dapat terpenuhi apabila product design pada aluminium memenuhi circular economy. Maka dari itu ada beberapa inovasi product design yang dapat menciptakan aluminium yang sustainable.
Contoh pada kaleng minuman aluminium yang bahannya secara umum menggunakan 2 seri aluminium alloy yaitu AL 5182 dan AL 3004. AL 5182 digunakan sebagai tutup kaleng dan AL 3004 sebagai body kaleng. Seri AL 5182 merupakan alloy yang tahan korosi. Komposisi dari seri alloy AL 5182 sebagai berikut, https://www.azom.com/article.aspx?ArticleID=8652
Seri ini biasanya digunakan kemasan produk, kaleng makanan atau minuman, dan panel body kendaraan. Sedangkan untuk komposisi dari seri alloy AL 3004 sebagai berikut, https://www.azom.com/article.aspx?ArticleID=6619
Serialloyinibiasanyadigunakanuntukpekerjaanlembaranlogamdan produksi tangki penyimpanan.
Campuran kedua alloy ini dalam proses pembuatan kaleng minuman atau makanan mempersulit proses daur ulang dari kaleng ini. Maka dari itu agar dapat memenuhi prinsip 6R (Recover, Reuse, Recycle, Redesign, Reduce, dan Recycle), body dan tutup kaleng menggunakan satu seri alloy saja yaitu AL 3004. Walaupun seri alloy AL 3004 memiliki tensile strength yang lebih rendah (215 MPa) dibandingkan AL 5182 yang memiliki tensile strength sebesar 275 MPa, tutup kaleng dapat diubah bentuknya menjadi cekung agar lebih baik ketahanan dan distribusi beban pada kalengnya. Berikut bentuk desain kaleng minuman unialloy.
Meskipun perubahan bentuk pada kaleng dengan 1 seri alloy bisa membuat distribusi tegangan lebih baik, performa struktural dari kaleng ini tetap perlu dinilai. Pada kaleng dengan campuran 2 seri alloy biasa, performa strukturalnya harus bisa menahan tekanan gas internal sebesar 90 psi atau setara dengan 620528,1561 Pa dan beban atas sebesar 113,8981 kg. Maka dari itu, diperlukan analisis distribusi tegangan menggunakan ANSYS. Hasilnya didapatkan bahwa dengan model proposal maupun model final, didapatkan tegangan maksimum sebesar 336 MPa.
Denganinovasi ini, prosesdaur ulang akansangatdipermudah. Proses separasi dan ekstraksi pada dua furnace yang berbeda bisa dihilangkan, konsumsi energi dikurangi, dan emisi karbon juga berkurang.Apabilahaltersebutterjadi,dapatberdampakbagiindustri secara ekonomi, lingkungan, dan sosial.
b. Production
Suatu produk tidak akan ada barangnya jika tanpa melalui proses produksi terlebih dahulu. Secara umum produksi dari aluminium dibagi menjadi 2 yaitu produksi dari primary aluminum dan produksi dari secondary aluminum. Dari proses produksi primary aluminum dibagi menjadi 5 sub proses yaitu penambangan bauxite, pemurnian alumina, produksi anoda, pelelehan aluminum, dan pengecoran ingot. Sedangkan proses produksi untuk secondary aluminum terdiri dari: koleksi dari reusable aluminum, transportasi, pra perawatan, peleburan ulang, pengecoran.

Sebagaimana kita tahu dalam proses produksi akan terjadi pereaksian reaksi kimia sehingga akan menghasilkan gas-gas yang akan berbahaya bagi lingkungan atau kita bisa sebut greenhouse (GHG). Dengan perbedaan proses produksi antara primary aluminum dan secondary aluminum pasti akan menghasilkan jumlah GHG yang berbeda pula.
Grafik perbandingan GHG emission untuk primary Al dan secondary Al
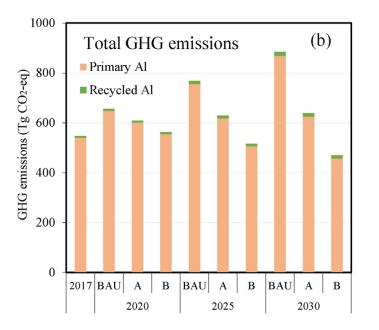
Untuk sumbu x tersebut menjelaskan tentang 3 skenario yaitu BAU, skenario A, dan skenario B. Skenario BAU adalah skenario ketika China tidak mengendorkan ekspor dari aluminium sehingga tuntutan untuk memproduksi Al akan semakin banyak sehingga GHG emission akan semakin tinggi. Sedangkan untuk skenario China mulai mengendorkan ekspornya dibanding dengan BAU skenario sedangkan skenario B China mengendorkan ekspornya sehingga kurang dari ekspor BAU, dan skenario A. Bisa dilihat juga dari grafik GHG emission yang dikeluarkan oleh recycled Al sangat sedikit dibanding dengan GHG emission yang dikeluarkan oleh primary Al. Oleh karena itu cara terbaik untuk mengurangi emisi dari produksi aluminum adalah produksi aluminum melalui daur ulang aluminum.
Alasan mengapa pembuatan aluminium dari primary aluminium memproduksi lebih banyak GHG emission karena pembuatan aluminium dari primary aluminium membutuhkan energi yang lebih besar. Jika kita ingin membuat aluminium dari primary aluminium maka kita harus menambang bijih bauksit terlebih dahulu, setelah itu dilakukanprosespemurniandanpemrosesanlebih lanjut.Energi yang dibutuhkan tersebut diambil dari proses pembakaran batu bara, minyak, ataupun dari gas alam. Sedangkan jika kita membuat aluminium dari recycled aluminium maka kita bisa menghilangkan proses penambangan bauksit dan juga proses pemurnian aluminium dari pemanfaatan daur ulang aluminium membutuhkan lebih sedikit energi karena kita tidak harus melelehkan lagi aluminium dari keadaan mentahnya
Dismantling
Sebuah produk sebaik apapun tentunya akan mencapai massa akhir dari penggunaanya. Oleh karena itu perlu dilakukan dismantling dari sebuah produk untuk memisahkan sisa dari produk yang dapat diolah dan yang tidak dapat diolah kembali.
Proses ini sendiri kurang lebih mirip dengan pengolahan bahan galian pada hasil tambang. Awalnya sisa sampah melalui proses kominusi dan/atau aglomerasi sehingga zat-zat yang dapat menggangu proses pelelehan dapat terpisahkan. Kemudian, sampah melalui classification dan sorting proses ini untuk memisahkan senyawa metalikdannonmetalik.Prosesinimenggunakanperbedaansifatfisik seperti densitas, magnetik,dll.
Sebagai contoh pada alumunium pada proses ini akan dilakukan kominusi terlebih dahulu agar dapat dipisahkan antara alumunium dan zat pengotor lainnya. Kemudian, digunakan magnetic seperation agar material yang bersifat feromagnetik dapat dipisahkan hal ini disebabkan Fe sangat berpengaruh pada sifat alloy dari alumunium sehingga jumlahnya perlu diperhatikan dengan seksama. Kemudian dapat digunakan metode eddy current seperation untuk memisahkan antara logam dan non logam atau bahkan antara logam. Prinsip dari metode ini yakni menggunakan perbedaan sifat konduktivitas listrik dari bahan. Dengan cara membuat medan magnet yang berubah terhadap waktu kemudian medan magnet ini akan menghasilkan gaya gerak listrik . Sedangkan, di sisi lain di dalam bahan akibat adanya gaya gerak listrik maka dihasilkan medan magnet induksi yang besarnya tergantung konduktifitas bahan serta dengan arah berlawan medan magnet awal. Oleh karena itu terjadi gaya tolak menolak dan dapat digunakan untuk memisahkan antara bahan dengan konduktivitas berbeda. Akan tetapi, untuk proses dengan volume rendah maka pemisahan secara manual dilakukan mengingat biaya yang diperlukan untuk membeli teknologi terkini bisa jadi tidak ekonomis. c. Recycling
Recycle adalah proses mengubah bahan limbah menjadi bahan dan benda baru. Kemampuan recycle suatu bahan tergantung pada kemampuannya untuk memperoleh kembali sifat-sifat yang dimilikinya dalam keadaan semula. Pemurnian dilakukan untuk memastikan produk akhir berkualitas tinggi dan bebas dari kontaminan material lain. Salah satu metode yang paling umum digunakan untuk pemurnian adalah elektrolisis. contoh limbah elektronik pada umumnya mengandung 0,1 % emas seperti pada motherboard komputer, teknik pemisahan logam ini ada beberapa cara salah satunya elektrolisis namun tetap memperhatikan kelebihan dan kekurangan baik dari segi ekonomis maupun ekologi sehingga diperlukan berbagai kombinasi untuk menghasilkan metode yang efektif dan ramah lingkungan
Sebagai contoh aluminum scrap mengandung cukup banyak hidrokarbon yang dapat meningkatkan emisi, remelting loss dan pembentukan sampah berlanjut. namun scrap juga mengandung kadar organik yag tinggi sebagai sumber energi yang bisa menghemat bahan bakar. kategori utama yang mengandung hal tersebut ialah pernis, tinta print, plastik, kertas ataupun logam. scrap yang mengandung sisa zat non logam seperti air, minyak, kayu, kaca, dan beberapa jenis scrap lainnya. Ada berbagai jenis pelapisan pada aluminium dan masing masing punya perilaku berbeda selama proses pyrolisis dan emisi yang dikeluarkan selama proses ini terkait dengan senyawa yang terkandung dalam coating. apabila kandungan plastik tinggi selama pyrolisis maka resiko emisi beracun lebih tinggi juga. Ketika bahan yang tercoating dipanaskan langsung dalam furnace, gas buang dilepaskan karena penguraian plastik, selain itu partikel dari gas karbon terbentuk yang bereaksi dengan logam dan alumina dan membentuk karbida, yang cenderung terakumulasi dalam slag atau sampah. Untuk mendeskripsikan material input dengan jelas, prosesnya dibagi menjadi 2 yaitu pemisahan atau dekomposisi termal dari hidrokarbon yang ada di lapisan dan pembakaran produk dekomposisi, langkah pertama tergantung pada jenis pelapis dan bahan dasar. Selama pembakaran, kokas yang dihasilkan selama pyrolysis dan tetap berada di permukaan akan bereaksi dengan oksigenmembentukCOdanCO2.Selamapyrolisis,tekanandikurangi, yang berarti bahwa bahan dilelehkan tanpa kehilangan oksidasi yang berarti, gas yang dihasilkan oleh perlakuan termal mengandung tar, minyak debu dan polutan.
Diagram butterfly circular economy dalam metalurgi
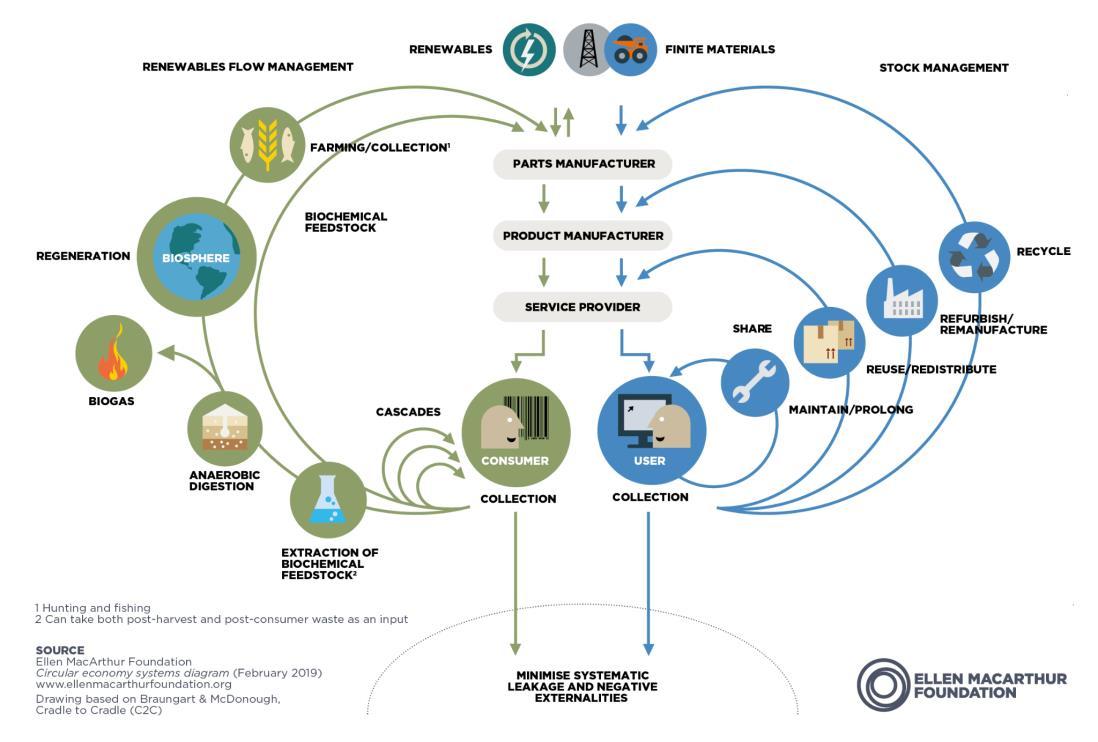
Hilirisasi Batubara “BATUBARA JADI DME”
Indonesia dengan estimasi sumber dan cadangan batubara sebesar 105,2 miliar ton dan 21,1 miliar ton berturut-turut menjadikan
Indonesia memiliki potensi besar dalam pemenuhan kebutuhan batubara global. Meskipun demikian, batubara di Indonesia lebih dari separuhnya merupakan batubara peringkat rendah yang berharga murah, memiliki nilai kalor rendah, dan efisiensi pembakaran yang kecil. Oleh karena itu, untuk meningkatkan nilai tambah dari komoditas ini diperlukan adanya hilirisasi batubara. Pemerintah melalui UU Minerba No. 3 Tahun 2020 menyebutkan bahwa batubara dapat dikembangkan atas enam metode berikut: Peningkatan mutu batubara (coal upgrading), Pembuatan briket batubara (coal briquetting), Pembuatan kokas (cokes making), Pencairan batubara (coal liquefaction), Gasifikasi batubara (coal gasification) termasuk underground coal gasification, dan Coal slurry/coal water mixture.
Salah satu dari enam metode tersebut, coal liquefaction, telah dikembangkan secara komersial dalam beberapa rute. Pyrolysis, direct coal liquefaction (DCL), dan indirect coal liquefaction (ICL). ICL menghasilkan berbagai produk yang sangat berguna, salah satunya adalah dimethyl eter (DME) yang akan menjadi fokus pembahasan saat ini.
Dimethyl-eter (DME) dengan rumus kimia CH3OCH3 saat ini menjadi semakin terkenal usai Presiden Joko Widodo meresmikan pembangunan pabriknya di Tanjung Enim, Sumatera Selatan. Nilai impor dari liquified petroleum gas (LPG) yang begitu besar hingga mencapai Rp. 80 triliun ditambah lagi subsidi mencapai Rp. 60 - 70 triliun menjadi perhatian khusus dan pertimbangan bagi pemerintah sehingga dapat memulai pembangunan industri ini. Secara rinci, proyek ini diperkirakan akan memproduksi 1,4 juta ton DME per tahun dan mengurangi angka impor LPG hingga 1 juta ton per tahun. Lebih lanjut, proyek ini akan menghemat cadangan devisa negara hingga Rp. 9,14 triliun/tahun pada harga rata-rata LPG 637,3 USD/MT (menggunakan basis rata-rata HIP LPG 2021). Langkah pemerintah ini juga berkaitan dengan pemenuhan hilirisasi batubara yang telah dicanangkan beberapa tahun sebelumnya.
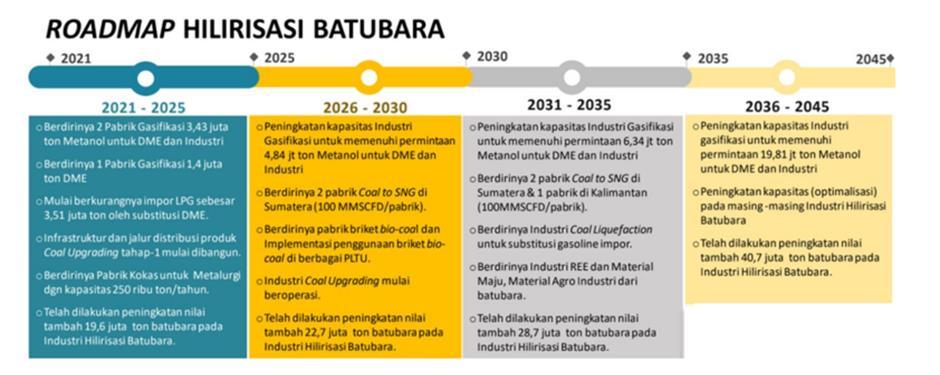
Pemanfaatan DME sebagai bahan bakar memiliki beberapa keunggulan. DME, memiliki sifat-sifat yang sempurna untuk compression ignition combustion, kadar NOx yang lebih rendah, nearzero smoke, nyala api lebih stabil, dan tidak mengandung sulfur serta partikulat. Beberapa penelitian juga menunjukkan bahwa DME memiliki angka setana yang tinggi, lebih dari 55, sehingga berpotensi menjadi pengganti bahan bakar diesel, terlebih efisiensi pembakaran dari DME lebih tinggi daripada solar.
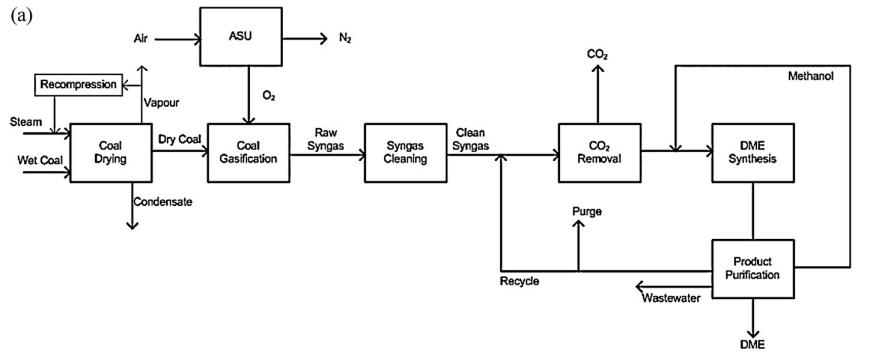
DME dapat disintesis dari syngas yang berasal dari derivat reforming gas alam dan atau berasal dari gasifikasi batubara ataupun biomassa. Proses produksinya pun dapat dilakukan baik menggunakan one-step process ataupun two-step process. One-step process melibatkan tiga reaksi yang berlangsung secara simultan: reaksi pembentukan metanol (1), dehidrasi metanol (2), dan water gas shift reaction (3). Reaksi total ditunjukkan oleh persamaan reaksi (4)
Dari persamaan reaksi kimia tersebut terlihat bahwa produk reaksi setiap tahap merupakan reaktan bagi tahapan reaksi berikutnya sehingga sinergi dari ketiga reaksi ini dalam one-step process mampu menghasilkan nilai konversi lebih tinggi daripada two-steps reaction. Proses ini telah diteliti salah satunya oleh (Seo et.al., 2008) dengan katalis yang digunakan adalah Cu/ZnO/Al2O3 untuk sintesis metanol dan γ-Al2O3 untuk dehidrasi metanol.
Adapun two-step process atau cara konvensional memproduksi DME dengan dua tahapan terpisah: pembentukan metanol dilanjutkan dengan dehidrasi metanol. Untuk persamaan reaksinya sama dengan reaksi one-step process, hanya saja tanpa adanya reaksi water-gas shift (RWGS).
(5)
(6)
Setiap rute proses memiliki kelebihan dan kekurangan masingmasing. Untuk one-step process memiliki batasan termodinamika yang lebih rendah dan proses bisa berlangsung lebih ekonomis. Namun demikian, keperluan adanya reaktor eksoterm yang besar diperlukan karena besarnya panas yang dihasilkan serta adanya keperluan katalis membuat cara ini masih harus dievaluasi kembali sehingga diperoleh katalis yang lebih ekonomis. Untuk two-step process proses lebih bersifat tradisional dan sederhana. Namun demikian, hambatan termodinamika cukup besar serta nilai konversi metanol yang lebih rendah apabila dibandingkan dengan one-step process.
Referensi:
Kementerian ESDM RI - Media Center - Arsip Berita - Resmikan Proyek Hilirisasi Batubara jadi DME, Presiden RI: Tekan Impor dan Serap Lapangan Kerja https://www.cnbcindonesia.com/market/20211210125539-17298258/begini-siasat-ptba-ubah-batu-bara-jadi-dme https://media.neliti.com/media/publications/98941-ID-dimethylether-dme-dari-batubara-sebagai.pdf
Seo, Y., Jo, S.-H., Ryu, H.-J., Yi, C.-K., & Jin, G. T. (2008). One-Step DME Synthesis from Coal-Derived, CO-Rich Syngas in a Slurry Reactor. JOURNAL of CHEMICAL ENGINEERING of JAPAN, 41(7), 585–589. https://doi.org/10.1252/jcej.07we091 https://doi.org/10.5614/j.eng.technol.sci.2016.48.3.6
Sasongko,D.,Luthan,A.F.H.,&Wulandari,W.(2016).ModifiedTwoStep Dimethyl Ether (DME) Synthesis Simulation from Indonesian Brown Coal. Journal of Engineering and Technological Sciences, 48(3), 320–333.
PT GNI
Smelter nikel GNI diresmikan pada 27 Desember 2021. Smelter ini sendiri menerapkan proses Rotary Kiln Electric Furnace (RKEF) dan dengan produksi 1,9 Juta Nickel Pig Iron per tahun. PT GNI sendiri sudah berdiri sejak tahun 2019.
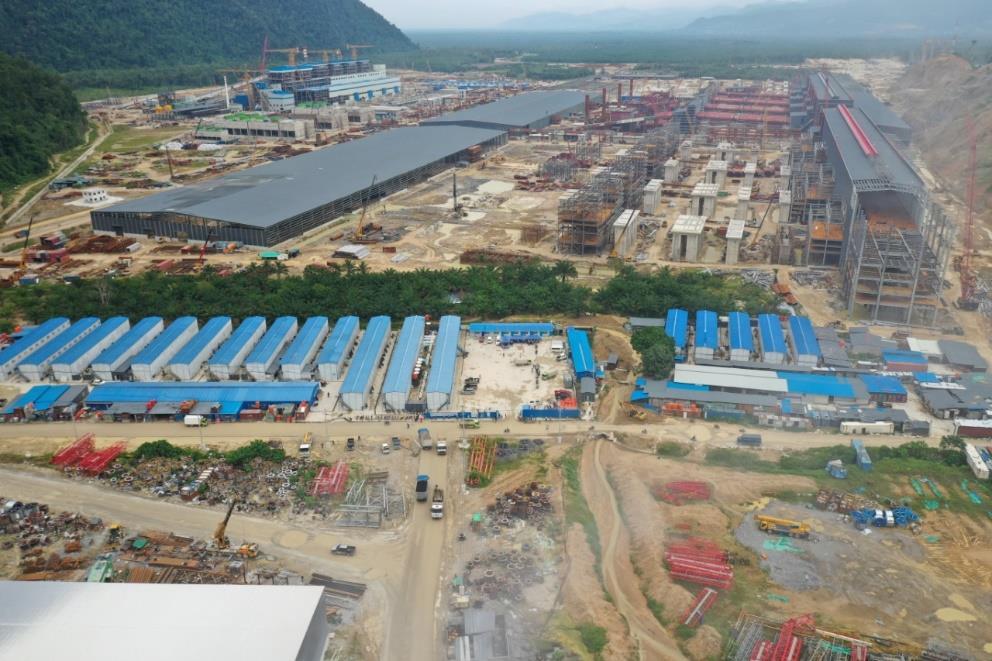
Smelter nikel GNI yang terletak di morowali terbakar pada Kamis 22 Desember 2022 pukul 04:15 WITA. Bedasarkan saksi mata api berasal dari salah satu tungku dan dengan cepat menjalar. Akibat kejadian ini 2 pekerja dinyatakan tewas. Kejadian ini sendiri saat ini masih diselidiki penyebabnya.
Pt Iwip
• Sejarah Singkat PT IWIP
PT IWIP merupakan kawasan Industri terpadu untuk pengolahan logam berat yang berlokasi di Desa Lelilef, Kecamatan Weda, Kabupaten Halmahera tengah, Provinsi Maluku Utara. Perusahaan tersebut berdiri pada tanggal 30 Agustus 2018.
• Kebakaran di PT IWIP Halmahera Sumatera Utara
Kebakaran smelter milik perusahaan pertambangan terjadi pada hari Jumat (6/1/2023) pada pukul 13.00 WIT. Dalam insiden tersebut sedikitnya 7 orang karyawan yang menjadi korban dan 2 diantaranya merupakan warga negara Asing (WNA). Menurut kapolres Halteng, AKBP Moh Zulfikar Iskandar kebakaran terjadi karena kerusakan pada penampungan batubara smelter L sehingga ledakan timbul dari salah satu pipa di smelter tersebut. Penyelidikan mengenai kebakaran tersebut masih terus berlanjut
• Informasi tambahan
Kebakaran di PT IWIP yang terjadi baru-baru ini bukan merupakan kasus yang pertama kali. Pada 15/6/2021 PT IWIP juga pernah mengalami kebakaran. Kebakaran tersebut disebabkan karena percikan api dari sebuah tungku dalam smelter sehingga api cepat membakar bangunan. Kebakaran tersebut menyebabkan 12 pekerja mengalami luka serius.
Investasi Baja Untuk Electric Vehicle
Besi dan baja merupakan logam dasar yang paling utama digunakan, dengan global market value senilai USD 225 miliar per tahun. Pada tahun tahun 2016 total konsumsi baja mentah (crude steel) sebesar 14 juta ton, sedangkan total produksi dalam negeri baru mencapai 8 juta ton. sehingga untuk mencukupi kebutuhan dalam negeri, indonesia harusmengimpor6 jutatonproduk baja. Untuk memenuhikebutuhan besi dan baja yang dan menekan angka impor besi baja telah dibuat rencana pengembangan industri besi baja Nasional .
“Roadmap Pengembangan Industri Baja Nasional”
2015 – 2019
Kapasitas produksi: 12 Juta Ton
Pengembangan Iron Ore Pellet, Sponge Iron, Pig Iron, Nickel Pig Iron, Ferro Alloy, dan baja untuk keperluan khusus
2020 – 2024
Kapasitas produksi: 17 Juta Ton
Peningkatan kapasitas produksi: Slab, Billet, Bloom, HRC, CRC HRP , PengembanganFerro Alloy, Stainless Steel, dan baja untuk keperluan khusus (kesehatan, pertahanan dan otomotif)
2025 – 2035
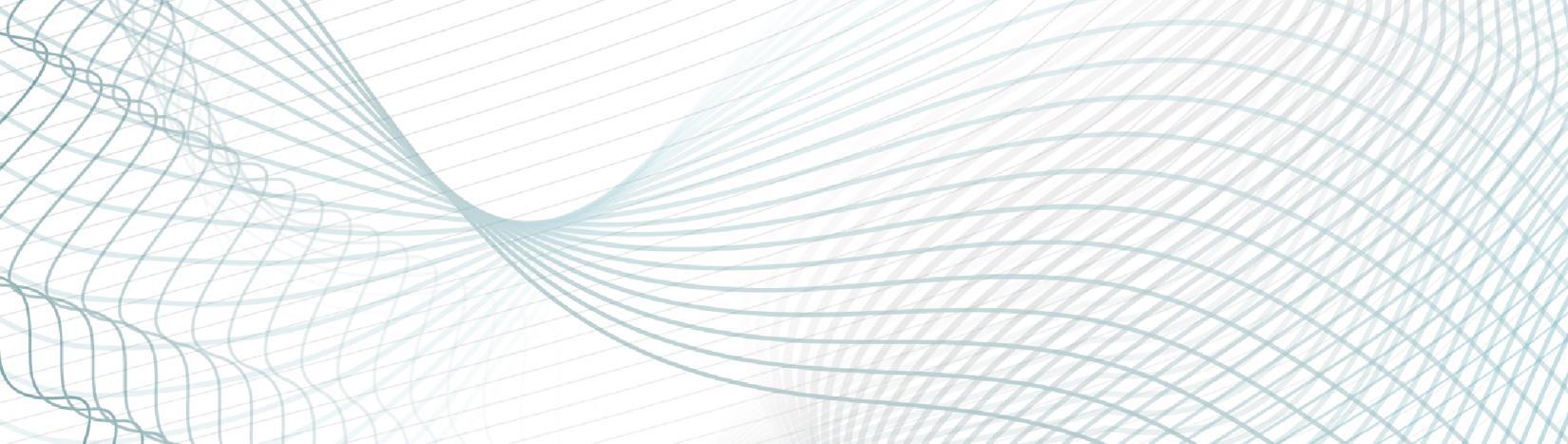
Kapasitas produksi: 25 Juta Ton
PengembanganSeamless Pipe, Ferro Alloy, Stainless Steel, dan baja untuk keperluan khusus (kesehatan, pertahanan dan otomotif)
Seperti yang tertulis dalam Roadmap Pengembangan Industri Baja
Nasional untuk tahun 2020-2024 terlihat bahwa indonesia sedang mengembangkan produksi baja dan paduannya untuk memenuhi kebutuhan industri otomotif yang permintaanya terus meningkat khususnya dalam perkembangan industri EV.
Kementerian Badan Usaha Milik Negara (BUMN) menilai tambahan investasi PT Krakatau Steel Tbk dan Pohang Iron and Steel Company (POSCO) senilai US$ 3,5 miliar atau Rp 52,2 triliun bakal memperkokoh ekosistem industri baja dan otomotif di dalam negeri. Seluruh investasi tersebut akan disuntikkan untuk usaha patungan
Krakatau Steel dan POSCO, yakni PT Krakatau Posco mulai mulai 2023. Krakatau Posco akan menggunakan dana untuk menambah kapasitas produksi baja, khususnya baja untuk kendaraan listrik atau EV.
Tambahan Investasi ini juga diharapkan dapat menekan angka impor bahan baku besi dan baja nasional , hal ini sudah tertulis dan disepakati melalui penandatanganan MoU kerja sama strategis antara Krakatau Steel dan Posco di bidang industri baja, yang disaksikan oleh Presiden.
Dengan adanya Tambahan investasi ini juga akan memperbaiki arus keuangan Krakatau Steel. Saat ini, Krakatau Steel berhasil menempuh restrukturisasi utang dan mulai mencetakkan laba setelah konsisten merugi delapan tahun berturut-turut dan pada akhirnya dapat menghasilkan untung sebesar 800 milliar ditahun lalu.
Salah satu alasan dari POSCO dalam menambah investasi adalah cadangansumberdayaalamyangbesardalampengembanganindustri EV. Strategi tersebut sejalan dengan rencana Krakatau Steel untuk meningkatkan kapasitas produksi baja canai dingin (CRC) sebanyak 1,2 juta ton per tahun menjadi 2 juta ton per tahun. Hal tersebut dilakukan dengan pembangunan Cold Rolling Mill 2 pada awal 2024 dan ditargetkan beroperasi pada akhir 2024.
CRM 2 direncanakan memiliki kapasitas produksi maksimum sebanyak 1,1 juta ton per tahun. CRC/Cold Rolled Coil (Baja Canai dingin) merupakan besi yang biasa digunakan sebagai kerangka mobil, baja jenis ini merupakan baja dari proses lanjutan dari HRC. Slab baja hitam yang telah melalui proses pendinginan akan diproses kembali dalam tahap annealing. Proses annealing ini merupakan prosespemanasan baja pada temperatur austenit yang ditahan beberapa saat. Kemudian dilakukan proses pendinginan yang dilakukan secara perlahan-lahan sehingga sifat-sifat fisik yang berubah saat proses deformasi dingin baja hitam dapat dikembalikan, begitu juga dengan sifat-sifat mekaniknya. Selain itu, CRC juga akan memiliki peningkatan kekuatan hingga 20% dari proses pengerasan regangan.
Manufacturing process of cold rolling steel

Cold rolling process
Continuous annealing line (CAL)
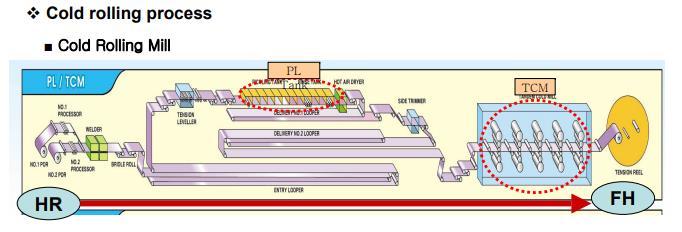
CRC merupakan bahan baku untuk mmebuat kerangka mobil , saat ini krakatau steel memiliki kapasitas produksi maksimum CRC sebanyak
800.000 ton , Krakatau steel memasok baja ke industri otomotif sejak
2019 melaluiPTKrakatauNipponSteelSynergy. Pada2019,penjualan baja KRAS ke sektor otomotif mencapai 350.000 ton.
Selain itu, Krakatau akan meningkatkan kapasitas produksi maksimum pabrik Hot Steel Mill 2 menjadi 3,9 juta ton. Saat ini, produksi maksimum Hot Steel Mill 2 baru mencapai 1,5 juta ton per tahun. Silmy menargetkan kapasitas produksi maksimum Hot Steel Mill 2 mencapai 4 juta ton. Dengan demikian, produksi baja canai panas atau HRC KRAS akan mencapai 6,5 juta ton.
HRC adalah lembaran baja yang digulung saat temperatur baja masih tinggi. Baja ini umumnya digunakan sebagai bahan baku konstruksi, seperti dinding, lantai, atap, maupun kerangka. "Bangunan Hot Steel Mill 2 sudah ada, jadi tinggal ditambah beberapa peralatan produksi dan kapasitas produksi maksimum Hot Steel Mill 2 bisa sampai 4 juta ton," kata Silmy.
Bentrok Maut di Smelter GNI, Time-bomb TKA
China?
Apa Kejadiannya?
Bentrokanantaratenagakerjaasing(TKA)asalChinadan tenagakerja
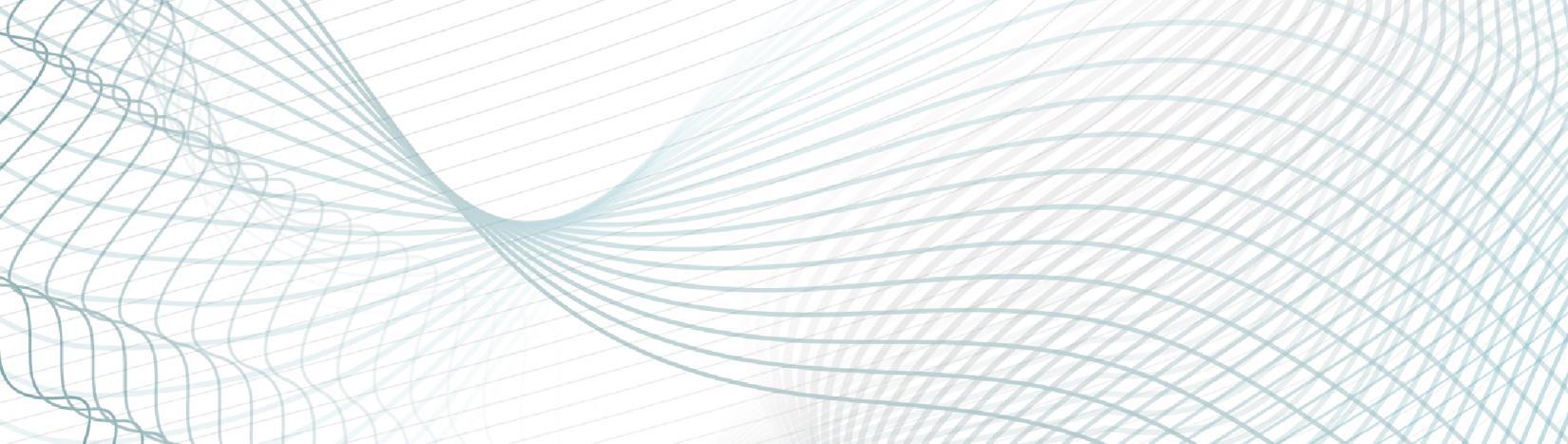
Indonesia (TKI) pecah di area pabrik smelter PT Gunbuster Nickel Industri (GNI), Morowali Utara, Sulawesi Tengah, Pada Sabtu 14
Januari 2023. Bentrok ini memakan dua orang korban, XE (30) TKA asal China dan MS (19) TKI asal Parepare.
Profil Singkat PT GNI
Dilansirdarilamanresmiperusahaan,PTGNImerupakanperusahaan pengolahan bijih nikel yang beroperasi diMorowaliUtara yang berdiri sejaktahun2019.PTGNImenggunakanteknologi RKEFdanmemiliki sebanyak 25 jalur produksi. PT GNI mampu menghasilkan 1,9 juta nickel pig iron (NPI) per tahun.
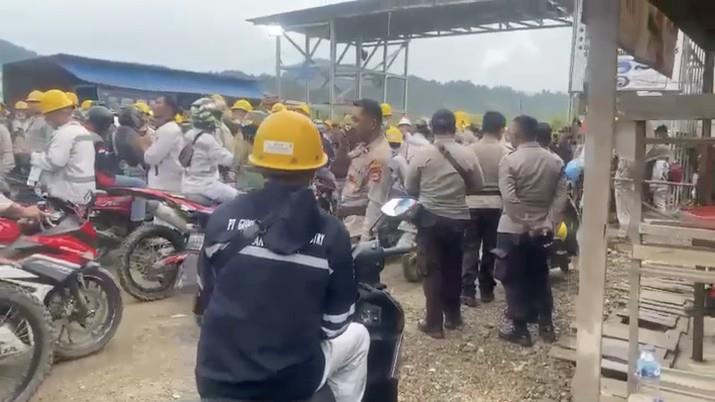
PT GNI memiliki visi menjadi nomor satu dalam industri smelter di Indonesia dan menambah nilai dari produk nikel. Sementara misinya adalah berjuang untuk pertumbuhan ekonomi dalam jangka panjang.
Di samping itu, PT GNI menyatakan membuka kesempatan bagi stakeholder dan komunitas di mana beroperasi untuk terus berkembang. Termasuk membangun hubungan yang baik dengan stakeholder dan warga lokal, serta berkomitmen mengembangkan kualitas dari komunitas dan menjaga lingkungan tempat PT GNI beroperasi.
Berlokasi di Bungintimbe Petasia, Morowali Utara, Sulawesi Tengah, jam operasional perusahaan ini mulai pukul 10.00 Wita hingga 22.00 Wita.
PT GNI mampu menghasilkan 10-12 persen Nickel Pig Iron (NPI) dengan kapasitas produksi pertahun 2,000,000 metrik ton. Hasil produksi disuplai langsung kepada konsumen yang kemudian diolah lagi menjadi produk yang dapat digunakan sehari-hari.
Apa penyebabnya?
Dilansir dari detik.com, Menteri Ketenagakerjaan Ida Fauziyah telah memaparkan akar masalah dari bentrokan pekerja di PT GNI. Akar masalah dari insiden ini adalah adanya tuntutan pengunjuk rasa yang belum direspons oleh pihak perusahaan, sehingga memicu terjadinya unjuk rasa yang berakhir anarkis.
"Akar masalah ada beberapa tuntutan, yang disampaikan kepada perusahaan yang belum direspons, sehingga memicu terjadinya unjuk rasa yang berakhir pada anarkis. Jadi, ini pada persoalan yang belum direspons dengan baik oleh pihak perusahaan," ungkap Ida
Kronologi?
DilansirdariBisnis.com,Kejadiannahasiniberawaldariadanyaunjuk rasa yang digelar oleh Serikat Pekerja Nasional (SPN) di PT GNI pada Sabtu (!4/1/2023) pukul 06.00 WITA. Unjuk rasa ini berlokasi di dua tempat yakni Pos 4 PT GNI dan Pos 5 PT GNI. Tidak tercapainya kesepakatan dalam pertemuan antara SPN PT GNI dan pihak perusahaan PT GNI pada Jumat 13/1/2023 menjadi pemicu dilakukannya aksi unjuk rasa ini. Dalam aksi ini, para pekerja menyampaikan 8 tuntutan yang belum sepenuhnya disetujui oleh PT GNI.
MasihdihariSabtu(14/1/2023)sekitarpukul19.40WITA,terjadiaksi anarkis di area jalan masuk Pos 4 PT GNI oleh karyawan dengan jumlah massa sekitar 500 orang. Aksi tersebut berujung pelemparan serta pengrusakan di area jalan masuk Pos 4 PT GNI. Aksi anarkis tersebut bermula dari pihak security yang menghalang jalan masuk Pos 4 sehingga memicu adanya perlawanan dan melakukan pelemparan terhadap pihak security serta merusak fasilitas kantor PT
SEI dan PT GNI. Kemudian pukul 20.15 WITA, massa berhasil menerobos pintu masuk Pos 4 PT GNI dan langsung menuju mes karyawan yang berada di belakang pos4 serta melakukan pembakaran sebuah mes dengan menggunakan sebuah bensin yang menyebabkan bangunan mes terbakar. Di waktu yang bersamaan, aparat keamanan
TNI/Polri berhasil memukul mundur massa. Lalu sekitar pukul 20.50
WITA, bentrokan kembali terjadi di area smelter 1 PT GNI. Penyebab terjadinya bentrok karena adanya karyawan divisi Dump Truck PT
GNI yang awalnya ingin bekerja tetapi kemudian berkumpul di parkiran Dump Truck untuk melakukan aksi mogok kerja. Saat kembali dilakukan pengawalan oleh unit Patroli Polres Morowali Utara, ada karyawan divisi dump truck PT GNI yang tidak mengikuti pengawalan dan melintas di area smelter 1 PT GNI. Bentrok tersebut mengakibatkan 3 orang karyawan divisi dump truck mengalami luka dibagian badan dan 3 unit kendaraan R2 dirusak. Aksi kejar mengejar dan saling lempar pun terjadi, dan menelan dua korban jiwa, masingmasingmerupakanTKAdanTKI.Keduakorbansudahdievakuasioleh pihak keamanan ke klinik PT SEI dan PT GNI. Aksi baru bisa dilerai sekitar pukul 21.10 WITA. Pada pukul 22.00 WITA, karyawan PT GNI yang diperkirakan berjumlah 500 orang menuju ke mess karyawan dan melakukan aksi pembakaran terhadap 5 unit kendaraan jenis loader dan 4 unit kendaraan R12 mobile crane. Adapun lokasi pembakaran berdampingan dengan mes pelangi yang dihuni oleh karyawan perempuan, sehingga pihak keamanan mengevakuasi karyawan perempuan. Tak berhenti di situ, sekitar pukul 23.50 WITA, para karyawan PT GNI bergeser menuju mess PLTU. Namun, dihadang oleh pihak keamanan TNI/Polri menggunakan mobil taktis. Sekitarpukul02.00WITA,massakemudianmembubarkandiri ke tempat masing-masing.
Fakta-Fakta Penting
• 8 Tuntutan Yang Disampaikan Pekerja PT GNI
1. Menuntut perusahaan wajib menerapkan prosedur K3 sesuai dengan peraturan perundang-undangan yang berlaku
2. Menuntut perusahaan wajib memberikan APD lengkap kepada pekerja sesuai standarisasi jenis pekerjaannya atau risiko kerja yang ada di lokasi kerja tersebut
3. Menuntut perusahaan segera membuat peraturan perusahaan
4. Setop pemotongan upah yang sifatnya tidak jelas
5. Setop PKWT untuk pekerjaan yang bersifat tetap
6. Menuntut perusahaan mempekerjakan kembali anggota SPN yang kontraknya diakhiri atau diputus sebagai akibat dari pelaksanaan mogok kerja sebelumnya
7. Menuntut perusahaan agar memasang sirkulasi udara di setiap gudang atau smelter agar tidak berdebu
8. Menuntut perusahaan agar memperjelas hak-hak yang telah diberikan kepada keluarga Almarhum Made dan Almarhumah Nirwana Selle sesuai dengan peraturan perundang-undangan yang berlaku
• PT GNI soal jumlah TKI dan TKA
Dilansir dari detikSulses, PT GNI telah buka suara terkait jumlah karyawan saat ini. Mereka membantah isu jumlah karyawannya hamper sama antara TKI dan TKA.
Informasi dari Assistant Manager PT GNI Yanita Rajagukguk, jumlah karyawan WNI ada 11.060 orang, dan jumlah WNA 1.312 orang
• Isu Pelanggaran K3 PT GNI menjadi salah satu tuntutan pekerja
Dilansir dari CNN Indonesia, dalam kurun waktu 6 bulan terakhir, tercatat tiga kali kecelakaan kerja berkaitan dengan K3 di PT GNI.
Serikat pekerja PT GNI mengajukan surat aduan PSP-SPN kepada Menaker Ida Fauziyah, dan melaporkan tiga kejadian ini:
Pertama, serikat pekerja mengadukan pelanggaran K3 PT GNI dalam insiden karyawan operator yang tertimbun longsor.
Kedua, karyawan crew smelter yang jatuh ke kolam slag.
Ketiga, ledakan tungku yang menewaskan dua orang pekerja operator hoist crane hingga hangus terbakar.
Pandangan Tim Kajian Keilmuan https://www.cnnindonesia.com/nasional/20230117091636-20901293/bentrok-maut-morowali-utara-dan-bom-waktu-tenagakerja-asing-di-ri https://www.pikiran-rakyat.com/nasional/pr-016120551/10-faktabentrok-maut-tki-tka-china-pt-gni-akar-konflik-versi-menakerhingga-kecemasan-bupati?page=2 https://www.cnnindonesia.com/nasional/20230117091636-20901293/bentrok-maut-morowali-utara-dan-bom-waktu-tenagakerja-asing-di-ri https://www.republika.co.id/berita/roirt4436/bentrok-pekerjalokal-dengan-tka-cina-di-perusahaan-nikel-di-morowali-inikronologinya https://www.bbc.com/indonesia/articles/c3g9z8wj72po
Isu TKA asal China merupakan salah satu isu yang telah lama hangat diperbincangkan. Kejadian ini bukanlah kontroversi terkait TKA China yang pertama. Pada tahun 2020, Pemerintah Indonesia memperbolehkan TKA asal China untuk memasuki wilayah Indonesia ditengah pandemi Covid-19. Hal ini sempat memicu protes dari berbagai pihak, terutama di masa tersebut banyak pekerja lokal yang kehilangan pekerjaannya.
Kejadian bentrok ini kami nilai merupakan akumulasi dari kekecewaan pekerja asli Indonesia terhadap haknya serta kelonggaran pemerintah terhadap TKA. Berbagai pihak menduga TKI menerima perlakuan tidak adil yang memicu aksi protes. Pasalnya, banyak ketimpangan yang dialami pekerja di Kawasan industry Morowali, seperti gap upah yang lebar, masalah K3, hingga hunian yang kurang layak. Dalam kasus PT GNI, tercipta suatu ketimpangan social ekonomi karena pekerja asing asal china banyak menempati posisi manajerial. Pemerintah juga kami anggap kurang transparan dan tegas terkait TKA China. Di satu sisi, hadirnya tenaga ahli TKA China nyatanya sangat membantu operasional pabrik karena kehandalannya dalam mengoperasikan teknologi yang umumnya berasal dari China. Di sisi lain, ditemukan juga banyak tenaga kasar yang dipekerjakan, dan tentunya ini memicu suatu tanda tanya. Dengan demikian, isu TKA China di Morowali ini kami pandang sebagai suatu bom waktu yang dapat meledak kapan saja.
Menyikapi kasus ini, harus dilakukan investigasi secara menyeluruh, terlebih melihat track record PT GNI yang cukup buruk terkait keamanan dan manajemen sumber daya manusia. Oleh karena itu, sudah semestinya PT GNI, dan juga seluruh perusahaan di Indonesia dengan seksama memperhatikan aspek K3 dalam operasinya.
Merupakan sebuah ironi karena isu ini muncul ditengah upaya pemerintah mengkampanyekan K3 Nasional. Pemerintah semestinya bisa lebih baik dalam menjamin hak-hak pekerja sesuai dengan konstitusi yang berlaku.
Bagaimana bisa dihindari?
Chinese and Indonesian Workers Clash at Indonesian Nickel Plant –The Diplomat
Kasus Morowali: TKI, TKA China, dan Bom Waktu - Halaman 2 (wartaekonomi.co.id)
Daun Jambu Biji Kini Bisa Mencegah Korosi
Korosi merupakan suatu momok yang tidak dapat dihindari tetapi dapat ditunda proses terjadinya. Umumnya, korosi ini hampir dapat terjadi pada semua jenis logam terkecuali logam dengan potensial reduksi yang sangat tinggi ataupun keberadaannya berada jauh di bawah dalam diagram Ellingham. Makadari itu, diperlukansuatu cara untuk menunda terjadinya korosi tersebut. Salah satu cara tersebut adalah penggunaan inhibitor korosi. Namun, inhibitor tersebut biasanya menggunakan bahan-bahan kimia yang berbahaya juga mahal. Lantas bagaimana solusinya??

Daun jambu biji hadir bagai sinar cahaya dalam goa yang gelap layaknya fans MU yang baru saja kemarin menelan kekalahan dengan skor 6-3. Inhibitor korosi dapat diperoleh dari ekstrak daun jambu biji yang mengandung zat tanin sehingga dapat menurunkan laju korosi terhadap logam. Oleh karena itu, kami akan membahas suatu penelitian yang dilakukan oleh Singgih dkk terkait kandungan zat tanin dalam ekstrak daun jambu biji yang dapat berperan sebagai inhibitor korosi dalam suatu logam baja.
Pada penelitian kali ini disiapkan labu ukur 1000 mL, 250 mL, gelas kimia, kaca arloji, neraca analitik, oven, pipet ukur 10 mL, buret 25 mL, vacuum rotary evaporator. Kemudian, disapkan bahan yang digunakan meliputi baja carbon steel, Natrium Klorida p.a, Alkohol, Akuadest, dan Asam Klorida 36%.
Ekstraksi Daun Jambu
Daun jambu dikeringkan dengan cara dianginanginkan tanpa terkena sinar matahari langsung. Dilanjutkan dengan menggunakan oven pada suhu 40°C. Daun jambu kering diblender kemudian ditimbang sebanyak 20 gram. Serbuk dilarutkan dengan alkohol 70% sebanyak 1000 ml kemudian dimaserasi selama 2 x 24 jam.
Setelah itu larutan disaring dan filtrate ditampung dalam wadah yang berbeda, residu dimaserasi kembali hingga didapatkan hasil filtrate yang terakhir dengan tannin yang negatif. Filtrat dievaporasi dengan vacuum rotary evaporator pada suhu 70°C, kecepatan 60 rpm untuk memperolehekstrakdaunjambu biji.Ekstrakkasar dilarutkandengan 250 ml alcohol 70% selanjutnya diuji kadarnya dan dibuat larutan inhibitor dengan konsentrasi 10.000 ppm
Identifikasi dan Analisa Kadar Tannin
• Filtrat hasil ekstraksi ditambahkan beberapa tetes larutan gelatin 10%. Jika terbentuk endapan berwarna putih berarti tanin positif.
• FiltrathasilekstraksiditambahkanbeberapatetesJikaberwarna hitam kehijauan berarti tanin positif Pipet 10 ml larutan ekstrak kedalam erlemeyer dan ditambahkan 20 ml H2SO4 0,2 N dan indikator indigo sulfonat, kemudian diencerkan dengan air sebanyak 15 ml.
• Larutan dititrasi dengan KMnO4 0,1 N hingga didapatkan titik akhir larutan berwarna kuning emas.
• Dihitung kadar tanin total. (1 ml KMnO4 ~ 4, 157 x 10-3 gram tanin.)
Persiapan Larutan Medium Korosif
Larutan medium korosif dibuat dengan cara melarutkan 37,5 gram NaCl dalam labu ukur 250 ml dan didapatkan larutan 15% NaCl.
Kemudian larutan tersebut diencerkan sejumlah volume tertentu hingga didapatkan konsentrasi sebesar 3% NaCl.
Preparasi Benda Uji
Sampel baja carbon steel dipotong dengan ukuran 10 x 20 mm. Benda uji dibersihkan dari kotoran (lemak dan debu) dan karat-karat dipermukaan logam dengan metode pickling sesuai ASTM G1-99. Baja dibersihkan dengan 500 ml asam klorida yang dilarutkan didalam akuadest hingga 1000ml. Semua spesimen yang masuk ke larutan pembersih kemudian dibersihkan dengan akuadest dan alkohol dan dikeringkan. Setelah itu ditimbang berat awal masing-masing spesimen sebelum diuji.
Larutan Media Korosif dan Inhibitor
Disiapkan labu takar 50 ml sebanyak 5 buah. Dipipet sebanyak 10 ml larutan NaCl 15% dan dimasukkan kedalam masing-masing labu takar 50ml. Ditambahkan larutan inhibitor 10.000 ppm sebanyak 0 ml; 2,5 ml; 5 ml; 7,5 ml; dan 10 ml ke dalam labu takar yang berisi larutan NaCl. Larutandiencerkandenganakuadesthinggatandaterasehingga campuran larutan masing-masing konsentrasi inhibitor yaitu 0 ppm, 500 ppm, 1000 ppm, 1500 ppm, 2000 ppm.
Pengujian Korosi
Sampel baja masing-masing dicelupkan ke dalam larutan campuran NaCl 3% dan larutan inhibitor. Variasi konsentrasi larutan inhibitor adalah 0, 500, 1000, 1500, dan2000 ppm. Waktuperendamanselama 1, 2, 4, dan 6 hari. Selanjutnya spesimen dibilas dengan aceton, akuades dan dengan alkohol kemudian dikeringkan dan ditimbang sebagai bobot akhir. Laju korosi dan efisiensi inhibisi korosi baja dihitung dengan menggunakan persamaan [3]:
Laju Korosi = Berat Awal - Berat AkhirLuas Plat Baja Waktu Perendaman
Efisiensi Inhibisi = Vko - Vki 100%Vki
Keterangan:
Vko = Laju korosi tanpa inhibitor
Vki = Laju korosi dengan inhibitor
Lalu, APA HASILNYA??
Tahap awal penelitian ini adalah identifikasi dan evaluasi kadar tanin pada daun jambu biji, tanin akan menjadi senyawa utama yang akan bereaksi dengan besi sehingga memberikan perlindungan besi dari oksidasi lebih lanjut.
Tabel 1. Analisis Hasil Kadar Tanin dalam Daun Jambu Biji
Kadar tanin dalam daun jambu biji adalah 13 mg/L sehingga daun jambu biji memiliki potensi untuk menjadi inhibitor korosi logam.
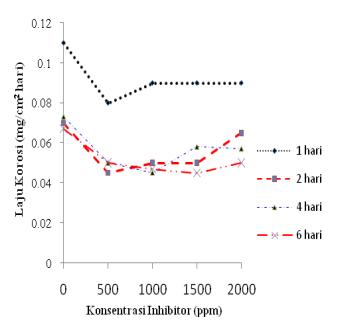
A. Pengaruh Konsentrasi Inhibitor Terhadap Laju Korosi
Gambar 1. Pengaruh konsentrasi inhibibitor terhadap laju korosi
Berdasarkangambar1,terjadipenurunanlajukorosiyangcukuptajam pada specimen baja yang direndam dalam media penambahan inhibitor dibandingkan dengan media tanpa inhibitor. Penurunan terjadi sampai sekitar 0.05 mg/cm2 hari. Hal ini mengindikasikan adanya perubahan perilaku korosi specimen karena penambahan inhibitor ekstrak daun jambu biji. Selanjutnya dengan penambahan inhibitor pada konsentrasi yang lebih besar akan terjadi penurunan kembali laju korosi yang disebabkan oleh adanya senyawa kompleks Fetannat yang terbentuk dari reaksi senyawa tannin dalam ekstrak daun jambu biji.
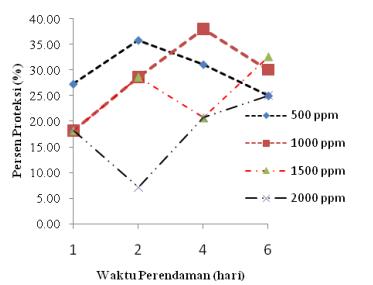
B. Efisiensi Inhibisi
Gambar
2. Pengaruh persen proteksi terhadap waktu perendaman
Efektifitas inhibitor ekstrak daun jambu biji pada rentang konsentrasi 500-2000 ppm cenderung meningkat dengan lamanya waktu perendaman. Hal ini terjadi karena semakin lama senyawa kompleks yang terbentuk antara senyawa tannin yang terdapat dalam daun jambu biji dengan ion Fe3+ semakin banyak sehingga lapisan pelindung yang terbentuk pada permukaan besi semakin meningkat. Nilai tertinngginyaberadapadakonsentrasi 1000ppm (optimum)dan akan turun seiring bertambahnya konsentrasi karena inhibitor mengalami kejenuhan.
Masa Depan Industri Sel Baterai

Mobil Listrik di Indonesia
Indonesia merupakan produsen nikel terbesar dunia pada tahun 2018 setelah menyalip Filipina. Ekspor nikel Indonesia pada tahun 2019 mencapai 17 miliar dolar AS atau 37,2 persen dari nilai ekspor dunia. Pada tahun yang sama, Indonesia berhasil memproduksi 29,6 persen dari total produksi bijih nikel dunia. Indonesia memiliki cadangan bijih nikel terbesar di duniadenganporsi 23,7%dari seluruh cadangan dunia, sehingga mampu memproduksi bijih nikel dalam jumlah besar secara berkelanjutan. Selain itu, Indonesia juga memiliki cadangan kobalt yang besar. Kobalt merupakan salah satu bahan utama yang diperlukan untuk membuat baterai. Cadangan nikel dan kobalt yang besar akan mempengaruhi produksi baterai dikarenakan komponen kobalt dan nikel mencakup ± 90 persen dari total komponen baterai.
Kekayaan alam Indonesia dan rendahnya upah tenaga kerja di Indonesia memungkinkan Indonesia untuk kemudian menjual mobil listrik dengan harga yang lebih kompetitif. Dengan demikian, mobil listrik dapat diakses oleh lebih banyak kalangan di Indonesia. Pasalnya, rata-rata tingkat kemampuan masyarakat membeli mobil hanya Rp 300 juta, sementara harga mobil listrik yang tersedia di pasaran saat ini masih berkisar Rp 500 - 1 miliar. Jika mobil listrik murah dan mudah terjangkau, maka tentu akan terjadi peningkatan pada penjualan mobil listrik di Indonesia. Jika mobil listrik murah dan mudah terjangkau, maka tentu akan terjadi peningkatan pada penjualan mobil listrik di Indonesia sehingga hal ini dapat mendongkrak ekonomi Indonesia. Selain itu, akselerasi pengembangan industri kendaraan listrik akan berdampak signifikan dalam mengurangi emisi, termasuk menekan impor dari BBM ke depan dan menciptakan lapangan pekerjaan.
Kementerian BUMN mengumumkan pembentukan perusahaan baterai yang bernama PT Industri Baterai Indonesia (IBI) yang bekerjasama dengan Konsorsium Hyundai dan LG Energy Solution. Holding IBI terdiri dari Mining Industri Indonesia (Mind ID), PT Indonesia Asahan Aluminium (Inalum), PT Aneka Tambang Tbk. (Antam), PTPertamina, danPerusahaan Listrik Negara(PLN). Tujuan dari kolaborasi ini, selain untuk manufaktur kendaraan konvensional, adalah untuk menjadikan Indonesia pusat pengembangan ekosistem kendaraan listrik berbasis baterai.
IBI menargetkan pembangunan Industri sel baterai yang terintegrasi dengan fasilitas tambang, smelting (peleburan), produksi prekursor, baterai, membangun penstabil penyimpanan energi, serta fasilitas daur ulang. Yang mana pengembangan ekosistem baterai untuk kendaraan listrik merupakan bagian dari target Net Zero Emission (NZE) pada 2060. BUMN - BUMN yang terlibat dalam holding IBI memiliki peran dan tanggung jawabnya masing-masing . Mind ID dan Antam akan berperan dalam penambangan dan pengolahan mineral mentah. Antam sendiri memiliki cadangan bijih nikel yang mencapai
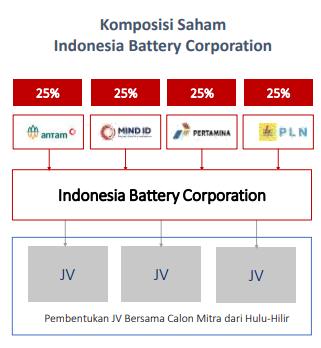
382 juta ton, terdiri dari 333 juta ton bijih nikel kadar tinggi (saprolit) dan49 jutaton bijih nikel kadar rendah (limonit). Saprolite digunakan untuk bahan baku stainless steel, sedangkan limonite akan menjadi bahan baku baterai EV. Sementara itu, PLN dan PT Pertamina akan bertanggung jawab atas pembuatan sel baterai dan kemasan baterai, serta pembangunan Stasiun Pengisian Kendaraan Listrik Umum (SPKLU) di Indonesia. Setelah dibangun, perusahaan ini diprediksi dapatmenyerapsekitar1,000tenagakerja.IBIdirencanakanmemiliki kapasitas produksi sebesar 140 gigawatt hour (GWh). Diperkirakan bahwa 50 GWh sel baterai yang diproduksi IBI akan diekspor ke luar negri.Kemudian,sisanyaakandigunakanindustribateraidiIndonesia untuk memproduksi mobil listrik.
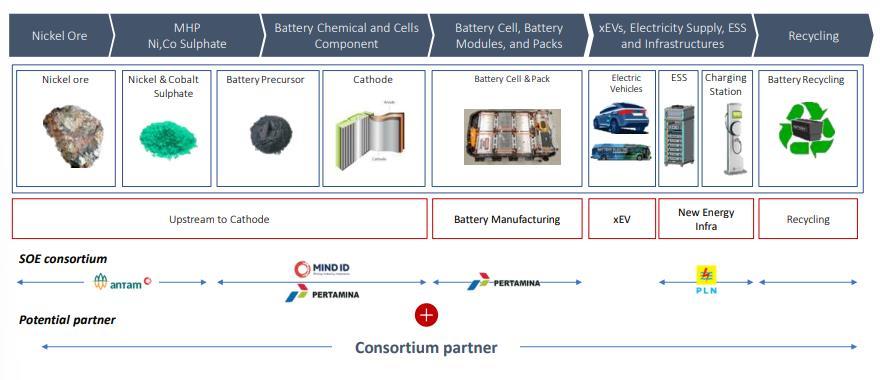
Paku Keling: Komponen Kecil yang Berakibat Fatal pada Royal Mail Ship Titanic?
Nama titanic tidak asing lagi, bahkan mungkin kapal karam ini paling terkenal dalam budaya populer kita saat ini. Titanic adalah kapal yang terdaftar di Inggris di garis white star yang dimiliki oleh sebuah perusahaanAS di manapemodal terkenalAmerikaJohn Pierpont “JP” Morgan adalah pemegang saham utamanya. Kapal ini dibangun di Belfast, Irlandia utara oleh Harland & Wolff untuk perjalanan transatlantik antara Southampton, Inggris dan New york city. Kapal ini merupakan kapal penumpang terbesar dan termewah pada masanya. Titanic diluncurkan pada 31 Mei 1911, dan berlayar dalam pelayaran perdananya dari Southampton pada 10 April 1912, dengan 2240 penumpang dan awak kapal.
Titanic memiliki panjang 882 kaki 9 inci sekitar 269 m dan mempunyai lebar 92 kaki 6 inci sekitar 28 m, memiliki Gross Register
Tonnage (GRT) 46.328 ton, dan ketinggian dari garis air ke dek kapal 60 kaki (18 m). Tiga baling-balingnya digerakkan oleh dua mesin uap bolak-balik empat silinder, ekspansi tiga kali lipat, dan satu turbin parsons bertekanan rendah. Uap disediakan oleh 25 boiler tipe scotch ujung ganda dan 4 ujung tunggal yang ditembakkan oleh 159 tungku pembakaran batu bara yang memungkinkan kecepatan tertinggi 23 knot (43 km/jam). Hanya tiga dari empat corong setinggi 63 kaki (19 m) yang berfungsi, yang keempat, ventilasi agar kapal terlihat lebih mengesankan, dek dalam kapal ini berjumlah 7 unit. Titanic dapat membawa sekitar 3320 penumpang yang terbagi ke beberapa kelas, first class berjumlah 735 orang, second class berjumlah 674 orang , third class 1026 orang dan awak kapal sejumlah 885 orang.
Gambar 1 & 2. Pembuatan Kapal Titanic
Pembangunan Titanic dimulai pada 31 Maret 1909, ketika desainer
Thomas Andrews meletakkan pelat baja kerangka kapal pertama di Galangan Kapal Harland & Wolff Belfast, Irlandia. Sejawat Titanic yakni The Olympic, telah dimulai sekitar tiga bulan sebelumnya, dan kedua kapal tersebut pada dasarnya dibangun secara bersamaan oleh lebih dari 15.000 pekerja. Proyek ini menelan biaya hidup 8 karyawan yang bekerja di lokasi konstruksi yang sangat besar dan seringkali berbahaya.
Ketika Titanic dirancang, tidak ada fasilitas untuk membangun atau menambatkan kapal sebesar itu. Harland & Wolff mulai membangun duaseluncuranbaruyangdiperlukan,menghancurkantigaseluncuran yang lebih kecil untuk memberi ruang. Mereka membangun dua gantries besar, dengan derek bergerak dan lift, yang disebut gantries
Arrol. Mereka juga membeli derek terapung seberat 200 ton untuk mengangkat boiler besar dan barang mekanis lainnya ke tempatnya di kapal. Dengan design seperti itu, apakah baja Titanic yang harus disalahkan atas peristiwa kelam itu? banyak faktor gabungan yang menyebabkan bencana besar Titanic di laut, termasuk kurangnya sekoci, cacat dalam desain kapal, dan kelalaian awak kapal.
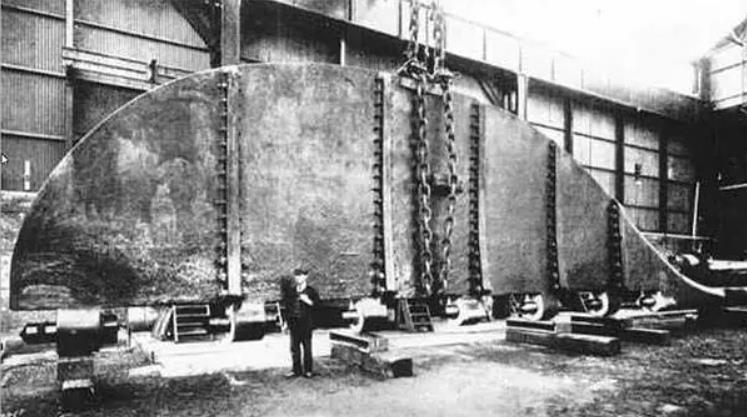
Menurut sebuah penelitian yang dilakukan pada tahun 1998 dan diterbitkan pada tahun 2008 oleh Dr. Phil Leighly, seorang profesor Teknik Metalurgi di University of Minnesota Rochester, baja yang digunakan untuk Titanic ternyata berperan dalam tenggelamnya Titanic. Dengan menggunakan sepotong baja yang ditemukan dari lambung kapal dan sekat yang lebih besar dari yang ditemukan sebelumnya, mereka dapat menentukan mengapa baja retak di lambung kapal.
Kejadianinibermulapadatanggal10April1912 ketikaTitanicberhenti di Cherbourg untuk menjemput beberapa penumpang terakhirnya, kemudian kapal besar itu berangkat dengan kecepatan penuh menuju KotaNew York. Namun, tepatsebelum tengah malam tanggal14 April, RMS Titanic gagal mengalihkan jalurnya dari gunung es dan memecahkan setidaknya lima kompartemen lambungnya. Kompartemen ini terisi air dan menarik haluan kapal. Karena kompartemen Titanic tidak ditutup di bagian atas, air dari kompartemenyang pecah memenuhi setiapkompartemenberikutnya, menyebabkan haluan tenggelam dan buritan terangkat ke posisi hampir vertikal di atas air. Kemudian, Titanic pecah menjadi dua, dan sekitar pukul 02.20 tanggal 15 April, buritan dan haluan tenggelam ke dasar laut.Karenakekurangansekocidankurangnyaprosedur darurat yang memuaskan, lebih dari 1.500 orang tenggelam atau mati kedinginandiperairanAtlantikUtarayangsedingines.Sebagianbesar dari sekitar 700 orang yang selamat adalah wanita dan anak-anak. Sejumlah warga negara Amerika dan Inggris terkemuka tewas dalam tragedi itu, termasuk jurnalis Inggris terkenal William Thomas Stead dan pewaris kekayaan Straus, Astor, dan Guggenheim. Pada tanggal 1 September 1985, gerakan ekspedisi gabungan Prancis-AS menemukan lokasi bangkai kapal Titanic terletak kira-kira 2,5 mil di bawah Atlantik, kemudian di tahun-tahun berikutnya banyak penelitian yang dilakukan untuk memecahkan mengapa kapal tersebut bisa karam.
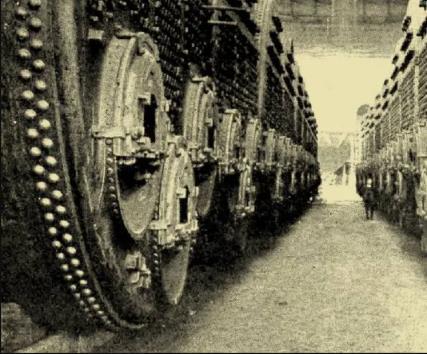
Pada tahun 1991, Institut Oseanografi Perancis membawa potongan pertama lambung kapal RMS Titanic dan disimpan di Museum Maritim Atlanik. Kemudian, pihak museum meminta peneliti yaitu DefenceResearchEstablishment-Atlantic (DREA)dan CanadaCentre for Mineral and Energy Technology (CANMET) untuk menguji sifat mekanik dari potongan baja tersebut. Selanjutnya, pada tahun 1996, Society of Naval Architects and Marine Engineers (SNAME) dan Discovery Channel membentuk tim untuk mencari tahu penyebab RMS Titanic tenggelam. Tim ini mengambil bagian lapisan lambung kapal yang disambung dengan paku untuk diteliti sifat fisik, kimia dan mikrostruktur dari bagian tersebut.
Proses investigasi ini didukung dengan beberapa metode eksperimen sebagai berikut:
1. Scanning electron microscopic (SEM) dan transmission electron microscopes (TEM) untuk mengetahui kondisi mikrostruktur dari lambung kapal.
2. Parallel electron energy loss spectroscopy (PEELS) dan energydispersive x ray analysis (EDS) untuk mengetahui konsentrasi pengotor pada batas butir.
3. Imaging secondary ion mass spectroscopy (I-SIMS) untuk mengetahui komposisi kimia dari partikel dan distribusi dari elemen pengotor dalam matriks.
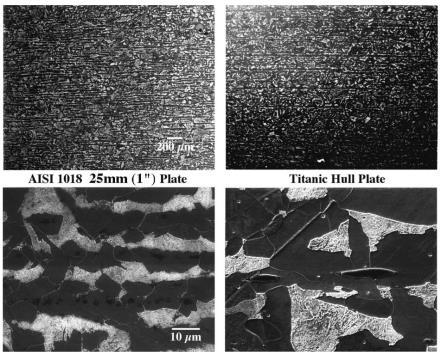
4. Uji tegangan dan uji coba charpy untuk mengetahui sifat mekanik dari bahan
Hasil dari SEM memperlihatkan permukaan lambung kapal yang penuh dengan butiran ferit dan kumpulan dari perlit. Perlit adalah kombinasi lapisan ferit dengan Fe3C. Terdapat kandungan MnS dan partikel oksida yang jelas serta perlit yang berukuran besar dan kasar mengartikan bahwa plat baja ini diproduksi menggunakan rolling mill berkecepatan rendah.
Gambar 3. Analisis Mikrostruktur Lambung kapal TItanic
Berdasarkan perbandingan tersebut, dapat dilihat bahwa ukuran butiran ferrit pada sampel kapal Titanic lebih besar dibandingkan dengan baja modern saat ini. Kondisi ini dapat menurunkan ketangguhandaribaja. Darihasilujitegangan(tensiletest)didapatkan bahwa tegangan geser sebesar 262 MPa pada material yang diambil tahun 1996, sedangkan pada material yang diambil tahun 1991 tegangan geser sebesar 280 MPa. Kemudian, untuk ultimate tensile strength sebesar 430 MPa pada material tahun 1996 dan 432 MPa pada material tahun 1991. Setelah itu, dilakukan Charpy impact test dan didapatkan bahwa suhu transisi (suhu pada saat sampel mengalami dampakenergisebesar 27J)sampellambungkapalTitanic di atas -2oC (suhu saat lambung kapal menabrak gunung es), yaitu 40oCuntukarahlongitudinaldan70oCuntukarahtransversal.Apabila dibandingkan dengan baja modern tipe A36, tingkat dampak energi atau ketangguhan baja A36 jauh lebih tinggi daripada baja lambung kapal Titanic.
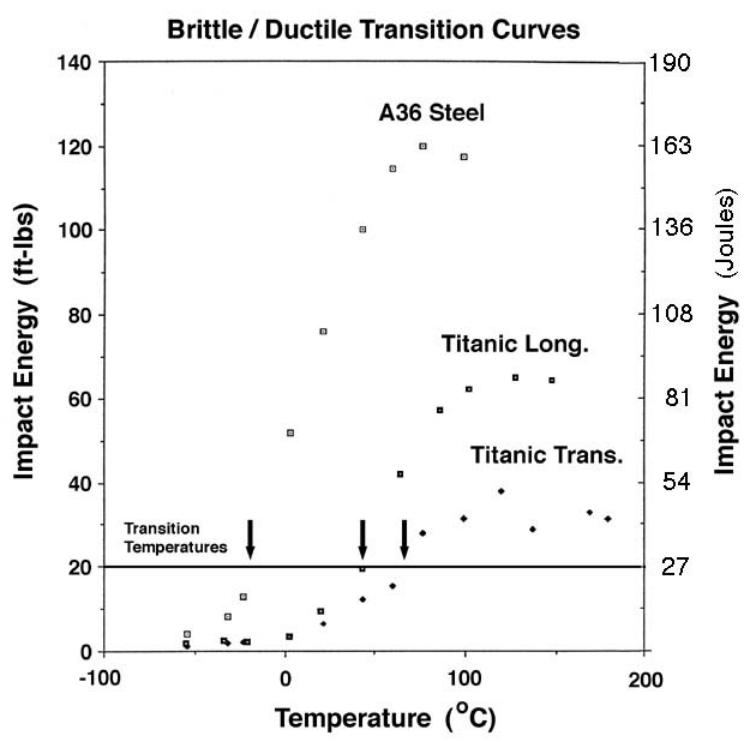
Gambar 4. Kurva Hasil Charpy Impact Test
Ketangguhan dari plat baja sampel lambung kapal Titanic terlalu rendah ketangguhannya ketika digunakan pada suhu air es. Hal ini disebabkan oleh kombinasi 2000 plat baja yang digunakan diambil dari industri baja yang berbeda-beda di Inggris. Selain itu, indikator untuk menguji ketangguhanpecahanseperti Charpy V-notch test baru dirancang 5 tahunsebelum pembangunankapal dimulai sehinggabaja untuk lambung kapal tidak dapat diuji secara maksimal.
Gambar 5. Mikrostruktur Hasil Charpy Impact Test
Sampel yang digunakan dalam Charpy impact test ini diuji lagi menggunakan SEM untuk dilihat susunan fraktur sampel baja tersebut. Hasil pengamatan didapatkan bahwa terdapat partikel MnS yang pecah. MnS yang pecah dapat berperan sebagai inisiator pecahnya keseluruhan lambung kapal. Namun, pecahan ini hanya terdapat 10% dari seluruh permukaan sampel. Dampak dari MnSpada ketangguhan lebih besar saat suhu tinggi daripada suhu rendah sehingga tidak terlalu memengaruhi ketangguhan lambung kapal Titanic saat menabrak gunung es.
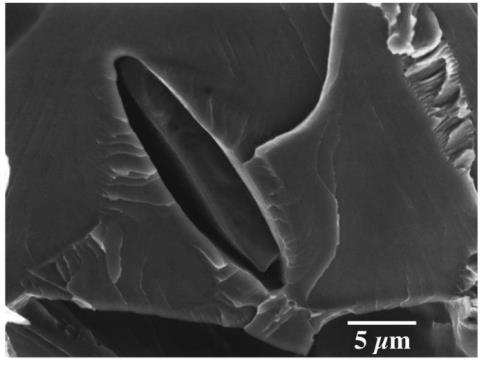
Berikutnya, sampel dianalisis komposisi kimia dengan SIMS dan PEELS pada TEM. Hasil dari pengamatan tersebut didapatkan bahwa sulfur pada baja hampir terikat seluruhnya dalam partikel MnS dan tidak terdistribusi ke dalam matriks ataupun pada batas butir. Komposisi sulfur yang tinggi dapat menurunkan ketangguhan dari baja, ditambah dengan komposisi mangan yang rendah dibandingkan dengan baja modern bisa berdampak pada ketangguhan dari matriks ferit. Hal ini disebabkan metallurgist di tahun pembangunan kapal RMS Titanic, 1909, menentukan komposisi dalam baja yang mereka produksi hanya berdasarkan pengalaman saja bukan berdasarkan perhitungan teoritis.
Lambung RMS Titanic disambung dengan 3 juta paku keling hidrolik yang terbuat dari besi tempaan dan besi silikat. Paku keling tersebut mengandung 9,3%±0,3% slag yang merupakan3 kali dari kandungan normal pada besi tempaan. Kondisi pada suhu rendah membuat slag silikat pecah dan membentuk retakan pada pusat besi. Ketika bagian pada paku keling terkena beban, beban akan ditransfer ke paku keling di sekitarnya hingga terjadi peningkatan tegangan pada setiap paku keling yang dapat memicu kegagalan sambungan pada dua plat baja tersebut. Kondisi ini juga terbukti pada kapal saudara dari kapal RMS Titanic, kapal RMS Olympic yang menabrak kapal HMS Hawke. Terdapat 50 paku keling yang hilang pada bagian plat yang terkena dampak dari tabrakan tersebut. Hal ini juga didukung oleh lubang pada plat baja untuk paku keling tersebut yang terdapat retakan kecil akibat proses pelubangan. Hal ini menyebabkan tegangan sisa bekas pelubangan mendorong retakan menjadi semakin besar. Apabila pada suhu rendah, retakan dapat terus berkembang hingga menimbulkan kegagalan plat baja.
Banyak faktor yang menjadi penyebab tenggelamnya kapal RMS
Titanic. Mulai dari rendahnya ketangguhan plat baja kapal RMS
Titanic pada suhu rendah hingga lubang pada paku keling yang retak.
Namun, kandidat yang paling mungkin menjadi penyebab utama secara metalurgi tenggelamnya kapal RMS Titanic adalah