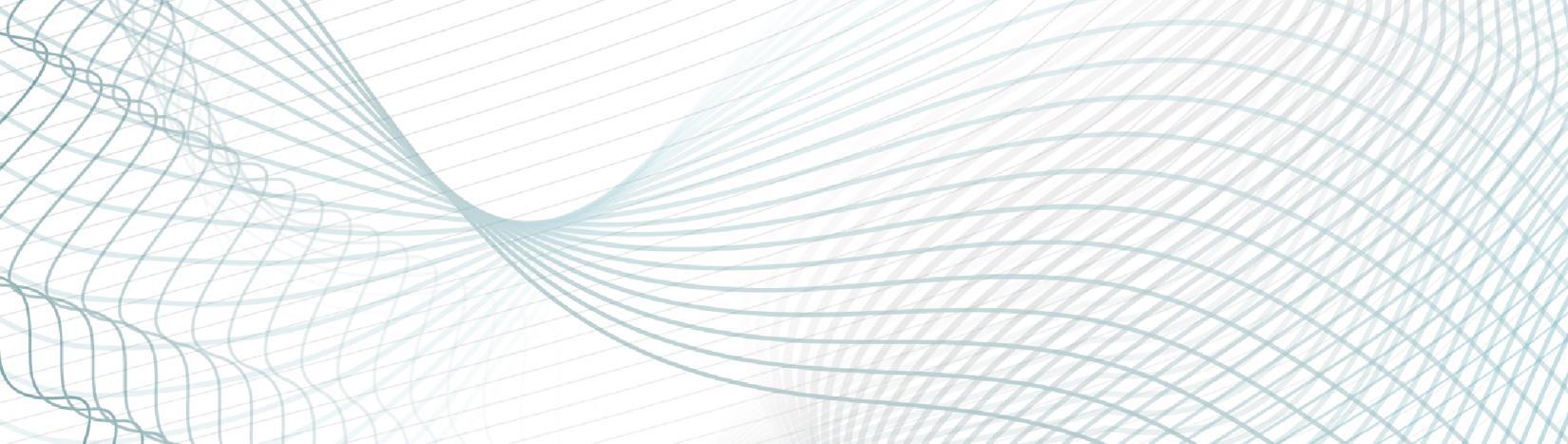
8 minute read
DOKUMEN KAJIAN
Nickel Processing And Its Issues
Klasifikasi Bijih Nikel
Advertisement
Bijih nikel diklasifikasikan menjadi 2 jenis, yaitu nikel laterite dan nikel sulfida. Nikel laterite memiliki mineral utama berupa nickeliferous limonite [(Fe,Ni)O(OH)] dan garnierite [(Mg,Ni)3Si4O10(OH)2·nH2O]. Nikel jenis ini terbagi atas 2 kategori, yaitu limonit dengan kadar Ni < 1.6% dan Fe sekitar 15% serta saprolit dengan kadar Ni > 1.6% dan Fe sekitar 35%. Sementara itu, pada nikel sulfida kadar Ni-nya sekitar 1 - 2% yang berasosiasi dengan logamlogam lain seperti Cu, Co, Fe, S, Au, Ag, As, Se, dan Te.
Perbedaan tipe-tipe bijih berimplikasi pada perbedaan cara pengolahannya. Untuk nikel sulfida umumnya diekstraksi melalui jalur pirometalurgi yang melibatkan concentrating, smleting, dan refining dengan produk akhir berupa Ni, Co, dan PGM. Di sisi lain, nikel laterite dapat diolah baik secara pirometalurgi maupun hidrometalurgi, bergantung pada kadar Ni yang terkandung di dalamnya. Untuk limonit proses ekstraksinya dilakukan melalui jalur hidrometalurgi dengan produk akhir berupa nikel kelas 1 yang banyak digunakan sebagai bahan baku utama katoda baterai Li-ion untuk kendaraan listrik, sedangkan untuk saprolit proses ekstraksinya melalui jalur pirometalurgi yang menghasilkan produk akhir berupa nikel kelas 2 seperti FeNi, NPI, dan Ni-matte yang banyak diaplikasikan sebagai paduan logam pembuatan baja tahan karat.
Pengolahan Nikel Melalui Jalur Pirometalurgi
Seperti yang telah dijelaskan sebelumnya, bijih nikel terbagi menjadi 2, yaitu nikel sulfida dan nikel oksida atau sering disebut dengan nikel laterit. Nikel laterit tersebut diklasifikasikan lagi berdasarkan komposisinya menjadi dua, yaitu saprolit dan limonit. Umumnya, nikel saprolit diolah menggunakan jalur pirometalurgi dan nikel limonit diolah menggunakan jalur hidrometalurgi. Salah satu alasan yang mendasari bijih saprolit diolah dengan menggunakan jalur pirometalurgi adalah komposisi Magnesium Oksida (������) dalam bijih tersebut cukup besar sekitar tiga puluh persen. Dengan adanya kandungan magnesium oksida yang cukup tinggi dalam bijih saprolit, jalur hidrometalurgi sangat tidak dianjurkan karena dapat mengonsumsi kadar asam sulfat yang sangat tinggi. Maka dari itu, jalur pirometalurgi lebih disarankan untuk menjadi proses pengolahan bijih nikel saprolit.
Dalam proses pirometalurgi, bijih saprolit dapat diolah dengan beberapa proses yang digunakan di dunia saat ini, yaitu Rotary KilnElectric Furnace (RKEF) sebanyak 93 persen, Blast Furnace (BF) sebanyak enam persen, dan satunya lagi yang jarang diketahui teknologi dari Jerman (Krupp Renn) sebanyak satu persen. Salah satu penyebab proses blast furnace tidak diminati adalah terak yang dihasilkan dalam proses tersebut sangat besar sehingga memerlukan energi yang lebih besar lagi untuk memproses terak yang dihasilkan dari pengolahan bijih saprolit.
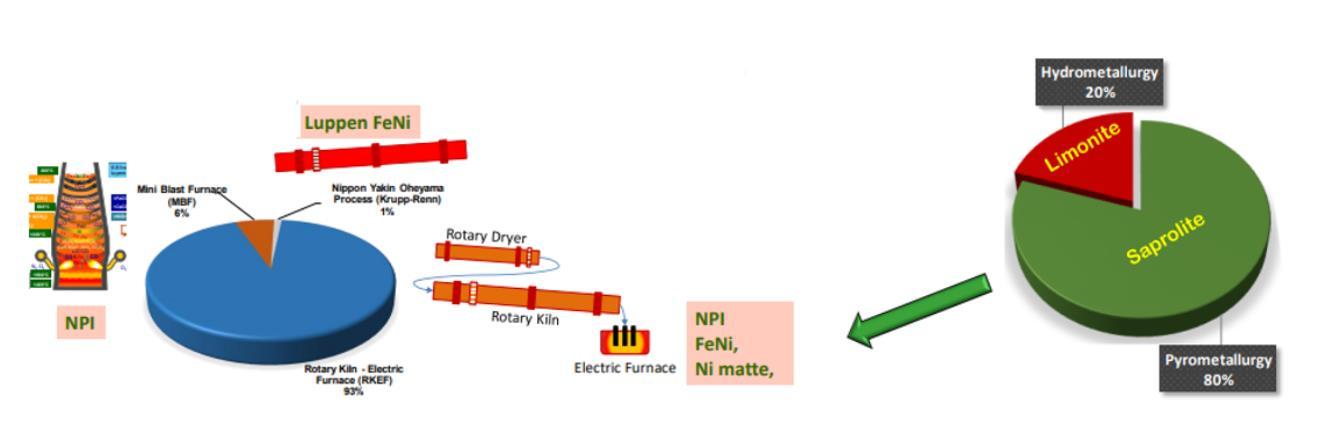
Gambar 2. Perbandingan Data Biaya Operasi BF dengan RKEF[2]
Dari grafik di atas, biaya operasi dari teknologi blast furnace cenderung memerlukan biaya yang lebih besar dibandingkan dengan teknologi Rotary Kiln-Electric Furnace (RKEF). Teknologi blast furnace digunakan pertama kali untuk menghasilkan Nickel Pig Iron (NPI) pada tahun 2006 dengan bijih limonit. Umumnya, teknologi tersebut digunakan untuk mengolah besi baja dengan efisiensi yang tinggi tetapi teknologi tersebut tidak disarankan untuk pengolahan bijih nikel karena memerlukan biaya operasi yang sangat tinggi. Beberapa reaksi yang dapat terjadi pada blast furnace dapat digambarkan dalam gambar di bawah ini.
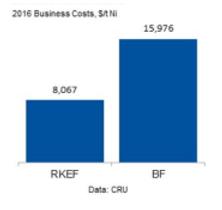
Bijih nikel yang akan diolah dengan menggunakan teknologi blast furnace terlebih dahulu dikeringkan dengan melakukan penyimpanan di dalam suatu gudang, lalu dicampurkan dengan kapur bakar yang bersifat higroskopis dan dilakukan sintering. Setelah itu, kokas yang diperoleh dari coking plant ditambahkan bersamaan dengan hasil sintering sebelumnya dan batu kapur yang berfungsi untuk pengaturan dari komposisi terak yang dihasilkan nantinya ke dalam tempat penampungan (bins) untuk disalurkan ke blast furnace. Hasil yang diperoleh dari proses tersebut adalah Nickel Pig Iron (NPI) yang memiliki kadar nikel sebesar delapan sampai lima belas persen dan terak yang cukup besar dibandingkan logamnya. Secara garis besar, proses pengolahan tersebut dapat digambarkan secara skematik pada gambar di bawah ini.
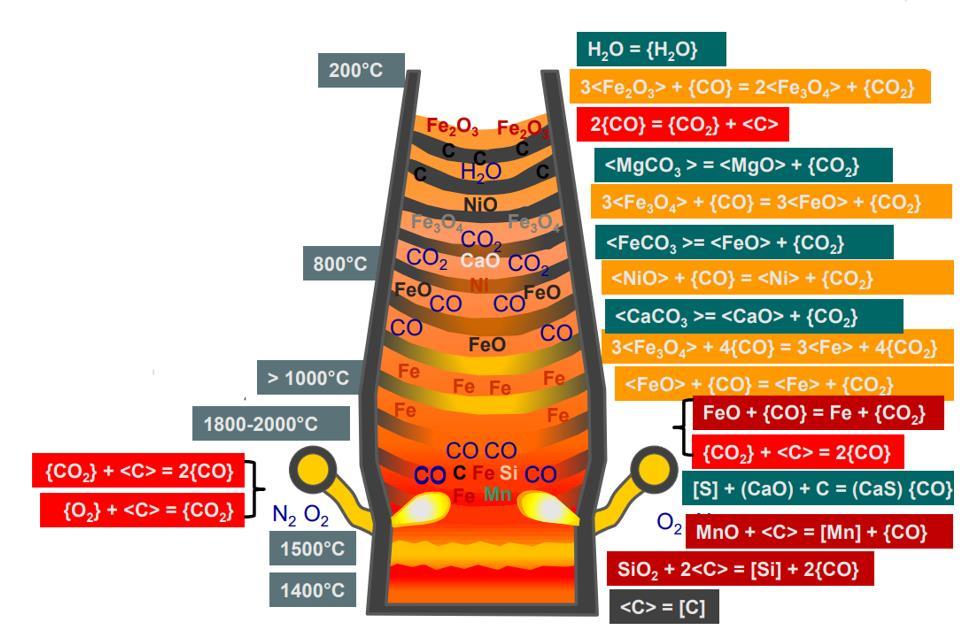
Jumlah terak yang dihasilkan dalam proses blast furnace bervariasi berdasarkan oksidator apa yang digunakan dalam proses tersebut. Pertama, proses pengolahan bijih besi dalam blast furnace tergolong efisien karena jumlah terak yang dihasilkan hanya sedikit dibandingkan logamnya. Kedua, proses pengolahan bijih nikel limonit dengan menggunakan blast furnace menghasilkan jumlah terak yang cukupbanyaktetapitidaksebanyakpadaprosespengolahanbijihnikel saprolit tetapi hal tersebut tidak dilakukan karena penggunaan pirometalurgi pada pengolahan bijih limonit tidak dapat mereduksi logam-logam yang berharga selain nikel pada bijih limonit, seperti kobalt dan skandium. Ketiga, proses pengolahan bijih saprolit menghasilkan jumlah terak yang sangat besar dibandingkan proses lainnya sehingga hal tersebut menyebabkan rendahnya tingkat recovery. Beberapa skematik jumlah terak yang dihasilkan dalam beberapa jenis oksidator pada blast furnace sebagai berikut.
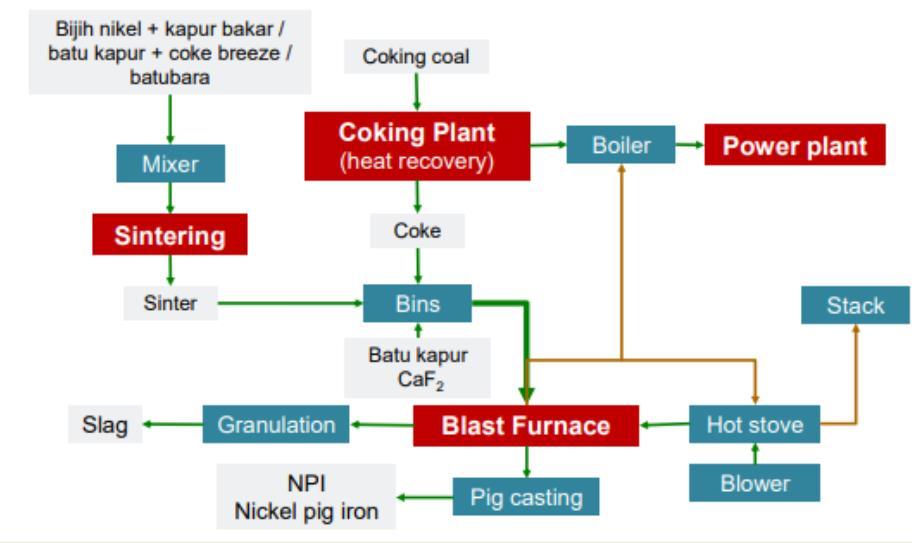
Gambar 5. Skematik Jumlah Terak pada Blast Furnace Berdasarkan Jenis Oksidator[1]
Selain teknologi blast furnace, salah satu teknologi yang mayoritas digunakan dalam proses pengolahan bijih nikel di dunia adalah teknologi Rotary Kiln-Electric Furnace (RKEF). Beberapa keuntungan RKEF adalah tingkat recovery yang tinggi (92-97%), tidak membutuhkan banyak kokas, dan adanya cooper cooler yang dapat memperpanjang umur pakai refraktori, serta biaya operasi yang lebih rendah. Berikut beberapa perbandingan antara RKEF dan BF.
Gambar 6. Perbandingan RKEF dan BF[1]
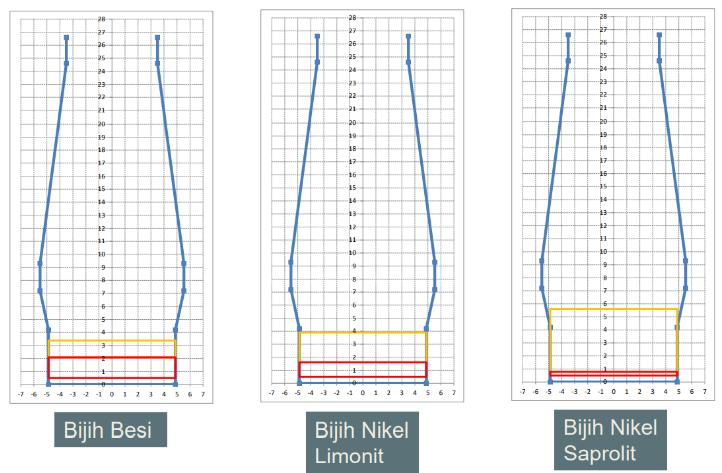
Secara garis besar, teknologi RKEF terdiri dari tiga bagian, yaitu rotary dryer, rotary kiln, dan electric arc furnace. Dalam rotary dryer, reaksi yang terjadi adalah reaksi penguapan air secara endotermik.

Energi tersebut berasal dari pembakaran batubara halus yang berfungsi untuk menurunkan kadar air permukaan dari sekitar 35 persen menjadi 20 sampai 23 persen sehingga dapat mempermudah proses handling ke tahap berikutnya. Terdapat lifter pada bagian rotarydryer yangberfungsiuntukmemaksimalkanprosespenguapan yang terjadi pada bijih yang masih basah. Dalam rotary kiln, terdapat tiga reaksi yang terjadi, yaitu reaksi evaporasi air permukaan sebelumnya dari proses rotary dryer (biru), reaksi pelepasan air kristal (coklat), dan reduksi nikel laterit dan besi oksida (merah). Secara umum reaksi pada rotary kiln sebagai berikut,
Proses yang terjadi pada rotary kiln adalah berlawanan arah berkebalikan dengan rotary kiln yang searah yang disebabkan oleh produk kalsin yang dihasilkan dalam rotary kiln harus dalam keadaan suhu yang tinggi untuk mengurangi energi yang dibutuhkan pada tanur listrik karena bijih yang sudah agak lembab perlu dipanaskan lagi dalam tanur listrik sehingga prosesnya tidak efisien.
Terakhir, bijih yang sudah diolah menggunakan rotary dryer dan rotary kiln selanjutnya diolah dalam tanur listrik. Terdapat tiga reaksi yangterjadipadatanurlistrik,yaitureduksitidaklangsungdengangas CO, reduksi langsung dengan karbon, dan reaksi pembentukan feronikel pada suhu 1450℃. Berdasarkan jenis arc-nya, tanur listrik dibedakan menjadi tiga, yaitu open arc smelting, shielded arc smelting, dan immersed smelting. Open Arc Smelting menggunakan prinsip arc yang berada pada udara dan tidak tertutupi oleh kalsin, prinsip tersebut menghasilkan daya yang sangat besar sesuai dengan rumus ��
Hambatan udara memiliki nilai R yang lebih besar dibandingkan dengan hambatan yang eksis pada terak. Maka dari itu, jenis tersebut memiliki daya yang lebih besar tetapi panas yang dihasilkan akan keluar dari refraktori sehingga efisiensi panas menjadi sangat buruk. Selanjutnya, jenis shielded arc smelting adalah jenis arc yang sangat mudah dijumpai dalam industri metalurgi karena daya yang dihasilkan besar dan efisiensi panas yang baik yang disebabkan oleh kalsin berperan sebagai penutup panas pada proses tersebut sehingga panas dapat terisolasi dengan baik. Terakhir, jenis immersed smelting adalah jenis arc yang menyentuh terak sehingga arc tidak ada udara dalamkasus tersebut.Makadariitu,sesuaidengan rumussebelumnya daya yang dihasilkan jenis tersebut paling kecil diantara jenis-jenis sebelumnya karena faktor R yang kecil pada terak dan jenis tersebut hanya cocok untuk digunakan dalam skala yang kecil.
Selain ditinjau dari segi arc-nya, terak dalam tanur listrik juga harus diatursedemikianrupasehinggaterakyangdihasilkandapatleleh dan mempermudah proses tapping. Penentuan titik leleh dari terak dalam tanur listrik dimodelkan dengan baik dalam diagram terner berikut,
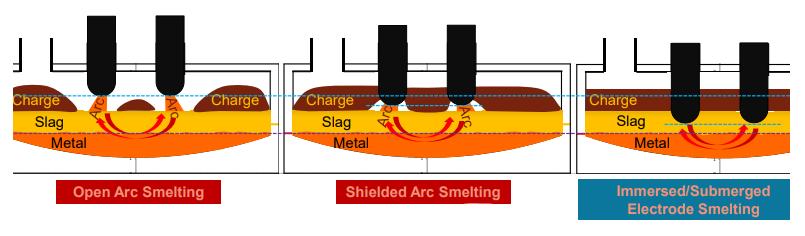
Dari gambar di atas, dapat diinterpretasikan bahwa titik leleh terak harus berada dalam garis biru yang tertera pada gambar. Jika nilai komposisi ������2 ������ atau (S/M) 1 maka diperlukan penambahan ������ dengan komposisi yang tinggi agar terak pada proses tersebut dapat leleh. Sedangkan perbandingan (S/M) 2,33 diperlukan penambahan ������ sedikit untuk mengubah fasa terak menjadi likuid. Perbandingan S/M yang ideal adalah 1,8 sehingga dalam kondisi ������ manapun terak tersebut pasti leleh.
Dalam RKEF, terdapat teknologi copper cooling yang menggantikan peran batu kapur untuk memperpanjang umur refraktori. Prinsip kerja dari copper cooler adalah memproduksi slag freeze lining yang dapat menjadi penahan panas yang keluar dari refraktori sehingga dinding refraktori terlapisi oleh terak yang mengkristal dan dapat terlindungi dengan baik.
Maka dari itu, teknologi copper cooling tersebut dapat memperpanjang umur pakai dari refraktori. Jika copper cooler tidak ada, maka refraktori cenderung cepat terkonsumsi dibandingkan adanya teknologi copper cooler tersebut seperti skema pada gambar berikut,
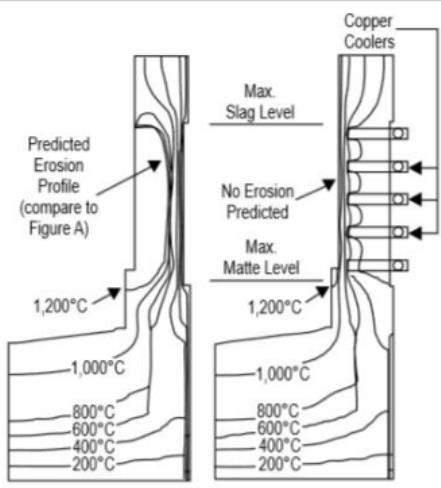
Selain dari dua teknologi yang telah dijelaskan sebelumnya, terdapat dua teknologi lanjutan, yaitu teknologi Krupp Renn yang berasal dari Jerman tetapi sekarang telah dibeli oleh Jepang dan teknologi RKMS Harbour Well yang eksis di Indonesia pada tahun 2010. Namun, keduanya masih kurang diminati karena perolehan nikel dan harga nikel dalam produknya yang rendah dibandingkan RKEF. Maka dari itu, Indonesia memerlukan sumber daya manusia yang dapat membangun lebihbanyak lagi RKEF sehinggaNegara Indonesiadapat menjadi negara penghasil logam nikel terbesar di dunia.
Pengolahan Nikel Melalui Jalur Hidrometalurgi
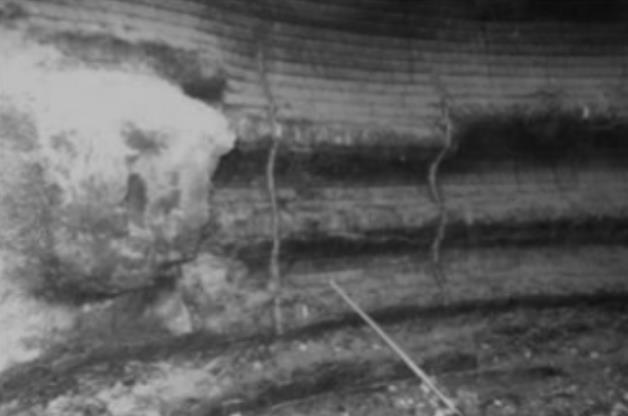
Bijih nikel limonit diekstraksi dengan menggunakan jalur hidrometalurgi. Jalur ini dipilih disebabkan oleh rendahnya kandungan nikel pada bijih limonit (0.8-1.5%) juga rendahnya kandungan magnesia (lebih sedikit mengkonsumsi asam)[1] .
Menariknya, dengan jalur ini, unsur lain seperti cobalt, bahkan hingga logam tanah jarang seperti scandium dapat direcovery secara selektif.
Pada ekstraksi nikel jalur hidrometalurgi, telah banyak teknologi proses yang telah dikembangkan. Beberapa di antaranya, proses Caron, PAL (Pressure Acid Leaching), HPAL (High Pressure Acid
Leaching), AL (Atmospheric Agitation Leaching), EPAL (Enhanced Pressure Acid Leaching), dan HL (Heap Leaching). Produk akhir dari jalur hidrometalurgi ini berupa nikel dan kobalt murni dalam bentuk cathode dan briquetting. Selain produk akhir, beberapa senyawa antara juga dapat diperoleh dari pengolahan ini meliputi Mixed Ni-Co sulphide precipitate (MSP), Mixed Ni-Co hydroxide precipitate (MHP), Nickel and Cobalt Sulfate yang digunakan untuk baterai mobil listrik (EV), dan Nickel and Cobalt Oxide. Di Indonesia, teknologi HPAL merupakan satu-satunya teknologi yang terbukti dapat diterapkan secara komersial. Hingga tahun 2021, terdapat dua perusahaan yang mengolah nikel dengan jalur hidrometalurgi dan menghasilkanoutputberupaMHP,yakniPTGebeIndustryNickeldan PT Halmahera Persada Lygend[2] .
Tabel 1. Daftar Perusahaan Pengolahan Nikel secara Hidrometalurgi di Indonesia Tahun 2021[2]
● Proses Caron a. Drying dan Grinding b. Reduction Roasting c. Leaching Hasil roasting didinginkan temperatur 150-2000C. Setelah itu, dilakukan pelindian dengan larutan amonia/amonium karbonat (nikel dan kobalt larut menjadi pregnant solution dan besi mengendap sebagai hidroksida). Reaksi pelindian tersebut dapat dinyatakan dalam persamaan reaksi berikut. d. Solvent Extraction e. Purification and Recovery
Proses ini merupakan gabungan antara jalur pirometalurgi dan hidrometalurgi. Teknologi yang teklah ada sejak 1944 ini sekarang digunakan secara komersial di Nicaro (Kuba), Punta-Gorda (USA), dan Yabulu (Australia)[3]. Adapun tahap dari proses ini sebagai berikut.
Campuran limonit dan saprolit dikeringkan menggunakan rotary kiln hingga kadar air 2-3%. Proses berikutnya bijih kering digrinding hingga ukuran sekitar 74 mikron.
Setelah digrinding, bijih diroasting pada temperatur sekitar 850 0C dimana proses ini menjadi penentu recovery nikel dari bijih laterit. Pada tahap ini hampir semua nikel dan 10% besi tereduksi menjadi logamnya. Reaksi kimia yang terjadi dinyatakan sebagai berikut.
Larutan kaya (pregnant solution) akan dipisahkan melalui serangkaian tahapan pencucian CCD. Setelah itu, pada larutan kaya akan dilakukan pemisahan cobalt dan nickel secara selektif dengan larutan amonium.
Larutan nikeldankobaltyangdiperolehkemudiandimurnikan lalu dipresipitasi sehingga diperoleh nikel ataupun kobalt dengan kemurnian tinggi.
Gambar 1. Proses Caron di Yabulu, Australia[1]
Proses Caron memiliki beberapa kelebihan dan kekurangan. Berikut ini rincian mengenai keduanya.
Tabel 2. Kelebihan dan Kekurangan Proses Caron
Kelebihan Kekurangan
Konsumsi leaching agent rendah Konsumsi energi tinggi, terutama untuk proses reduksi, roasting
Dapat mengolah campuran bijih saprolit dan limonit
NilairecoveryNidanCo lebih rendah dari HPAL
Codapatdirecoverymeskipunrendah (70%)
Limonite yang semakin banyak akan
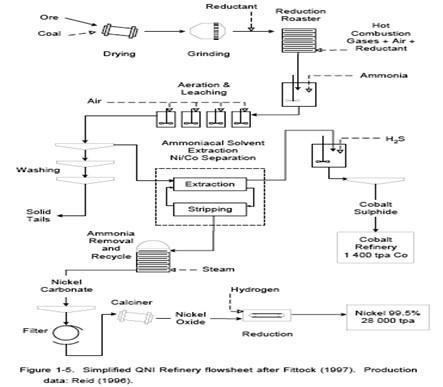
Menurunkan Recovery Kobalt
Material konstruksi tidak mahal karena proses korosi minimal (reagen berupa basa)
• Proses HPAL
HPAL merupakan teknologi pengolahan nikel secara hidrometalurgi dengan reagen berupa asam sulfat pekat pada suhu dan tekanan operasi yang tinggi. Proses ini dilangsungkan pada temperatur 240270°C dan tekanan 33-55 atm dalam sebuah reaktor Titanium-Clad Autoclave [1]. Pertama kali diterapkan secara komersial di Moa Bay Plant, Kuba sekitar 1959. Proses HPAL terus mengalami perkembangan dan perbaikan pada sistemnya. Saat ini, perkembangannya telah berada dalam apa yang disebut sebagai HPAL generasi ketiga[1] .
Selama proses HPAL bijih nikel limonit akan mengalami berbagai konversi sebagai berikut.
- Goethite terkonversi menjadi hematite
Alumunium dalam bentuk gibbsite terkonversi menjadi proses pemanasan sebelum pelindian
SetelahprosesHPAL,prosesCCDdilakukanuntukmerecoverylarutan kaya (pregnant solutioni) dari leach solution. Asam yang tidak bereaksi kemudian dinetralkan melalui proses neutralization dengan menggunakan CaO (lime). Larutan kaya (pregnant solution) yang diperoleh kemudian dimurnikan dan dipresipitasi dengan penambahan asam sulfida untuk membentuk MSP ataupun ditambahkan NaOH untuk membentuk MHP.
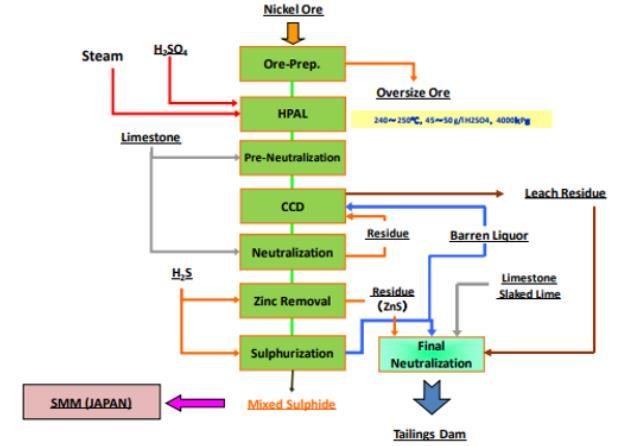
Gambar 3. PT. Halmahera Persada Lygend, Salah Satu Perusahaan Pengolahan Nikel dengan Teknologi HPAL di Indonesia
Sama seperti proses Caron, teknologi HPAL juga memiliki beberapa kelebihan dan kekurangan. Berikut ini rincian mengenai keduanya.
Tabel 3. Kelebihan dan Kekurangan Proses HPAL [1]
Kelebihan
Kekurangan
Recovery nikel dan kobalt tinggi CAPEX besar
KinetikareaksilebihcepatdariAL Material konstruksi mahal, biaya perawatan yang besar
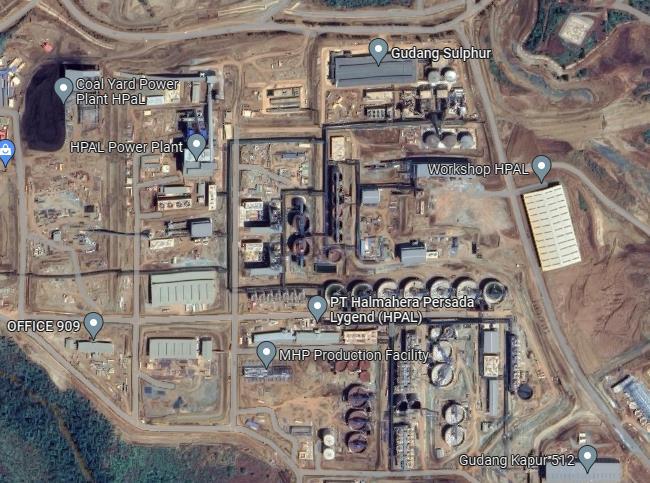
Selektif terhadap besi sehingga konsumsi asam rendah
Proses sudah proven meskipun terdapat beberapa masalah seperti scalling
Kendali proses lebih sulit
Masalah korosi dan scalling