12 minute read
Prepare for a Safe Refrigerant Transition
Next Article
For the past 10 years, the HVACR industry in the United States has advocated for a global structure to phase down the use of high-global warming potential refrigerants, chief among them hydrofluorocarbons (HFCs).
That effort culminated in 2016 with the Kigali Amendment to the Montreal Protocol.
The phase down initiative was undertaken in part to bring order to what was a country-by-country, region-by-region approach to a refrigerant transition that had the potential to cause disruption in the global HVACR marketplace, raising manufacturing and distribution costs, causing confusion among consumers and stymying the ability of manufacturers, distributors and contractors to properly plan for the future.
More than 90 nations having ratified the Amendment and it is now in effect around the world. The fact that the United States has not ratified the agreement, however, has created a policy vacuum that is being filled state-by-state, creating a domestic version of the very situation industry had tried to avoid with the global agreement.
In the absence of a federal framework, a handful of states are pursuing their own HFC regulations, following SNAP Rules 20 and 21, the EPA refrigerant regulations that were vacated by the DC Circuit Court of Appeals in Mexichem Fluor v. EPA on the grounds that EPA did not have Congressional authority to regulate non-ozone depleting refrigerants.
This state-by-state patchwork of regulations with various implementation timelines is creating challenges for equipment manufacturers that supply products not to individual states, but to a national market.
And given that many of the most promising new low-GWP refrigerants, compared to their HFC predecessors, have different flammability characteristics and require updated building codes, this transition must be managed in an orderly manner to prevent serious consequences for the manufacture-distribution-installation-consumer chain.
CALIFORNIA’S PROPOSED REGULATIONS
The California Air Resources Board (CARB) is charged with developing regulations to reduce HFC emissions 40 percent by 2030 compared to a 2013 baseline (SB 1383). Thus, California is writing HFC phasedown rules that go beyond those laid out in SNAP Rules 20 and 21 and at a pace even ahead of the Kigali phasedown schedule.
In terms of the residential and light commercial AC market, CARB is currently proposing the following: • A ban on AC systems using refrigerant with GWP greater than 750 GWP by
January 1, 2023. • A ban on servicing existing equipment with refrigerant with a GWP greater than 1,500 by January 1, 2022. o Potential exemptions for reclaimed refrigerants and R-410A remain an option.
Bearing in mind that these are, at present, just proposals, for most stationary cooling applications, this may require the use of A2L (lower flammability) or A3 refrigerants (higher flammability). BY STEPHEN YUREK AND JOHN GALYEN This state-by-state patchwork of regulations with various implementation timelines is creating challenges for equipment manufacturers that supply products not to individual states, but to a national market.
FLAMMABLE REFRIGERANTS
Flammable refrigerants are new to the U.S. air conditioning market — but not to the world. As categorized by ASHRAE, A2Ls are the class of low-GWP refrigerants expected to replace HFCs in many applications and while new to the U.S. market, A2Ls have been used safely in other parts of the world for years.
Today, more than 8 million mini-split systems around the world are using the A2L refrigerant R-32 and 80 percent of new cars sold in the U.S. use A2Ls in their air conditioners.
A3 refrigerants, such as R-290 (propane), on the other hand, are highly flammable and restrictions on their use are already included in U.S. and global safety standards. Some of the restrictions include: no more than 150g per refrigerant loop, no nearby sources of ignition and no use near points of egress.
Some manufacturers of refrigerant equipment and small-charge room air conditioners have redesigned their products to safely use flammables by reducing refrigerant charge sizes and the potential for leaks. One manufacturer reports that 6,000 commercial propane ice machines are operating with no problems.
A2Ls and A3s are new to the United
States and these replacement refrigerants have different flammability characteristics requiring updates in safety, training and building codes.
CODE UNCERTAINTIES RISK SAFE TRANSITION
The Uniform Mechanical Code (UMC), which is the building code predominately relied upon in California, did not adopt the necessary safety standards (ASHRAE 15 and UL-60335-2-40 standards, which would have enabled the safe use of A2Ls). So, to meet its phase down targets, the state will need to adopt these standards directly into state building codes rather than through the adoption of the model code.
Time is of the essence here, for the following reasons: AC original equipment manufacturers (OEMs) require certainty that the building codes are in their final form at least three years before a regulatory implementation date. They need to know exactly what will be required in the building code and be able to use those requirements to engineer new equipment, test its efficacy and safety and certify that equipment with third-party testing labs under the AHRI Certification Program.
This is an expensive and time-consuming process that must be completed before equipment can be commercialized. In addition, supply chains must be filled with parts used in equipment and equipment must be stocked in warehouses to be prepared for the transition. If by the end of 2020 the industry has certainty that the codes will allow the use of A2Ls, OEMs could still meet CARB’s proposed January 1, 2023 implementation date.
WHAT THIS MEANS TO YOU
This uncertainty is putting the safe refrigerant transition in serious jeopardy. Equipment using alternative refrigerants must be thoroughly tested and all those who handle it must be properly trained.
If the building codes are not updated very soon to incorporate ASHRAE 15 and UL-60335-2-40 as they are currently written and CARB enforces a January 1, 2023 implementation date, OEMs and the rest of the supply chain will have difficulty complying.
Suppliers may not have sufficient parts available, technicians may not be fully
The industry, through its trade associations, have been actively engaged in this issue since the Kigali Amendment was agreed to in October 2016.
trained — especially if the codes deviate from the standards as written — and the opportunity to further field-test equipment may be lost.
If equipment manufacturers are not able to design, test and manufacture products that comply with CARB’s mandate because of delinquent adoption of updated building codes, they may not have equipment that is legal to sell in California on January 1, 2023.
Under these circumstances, the OEMs and their suppliers simply could not meet the schedule, which means that California businesses and residents would be unable to purchase new, legal AC equipment.
Thus, consumers’ only option should their AC units fail would be repair. Should repairs be too expensive or impossible, they simply would not have air conditioning.
WHAT INDUSTRY LEADERS ARE DOING
The industry, through its trade
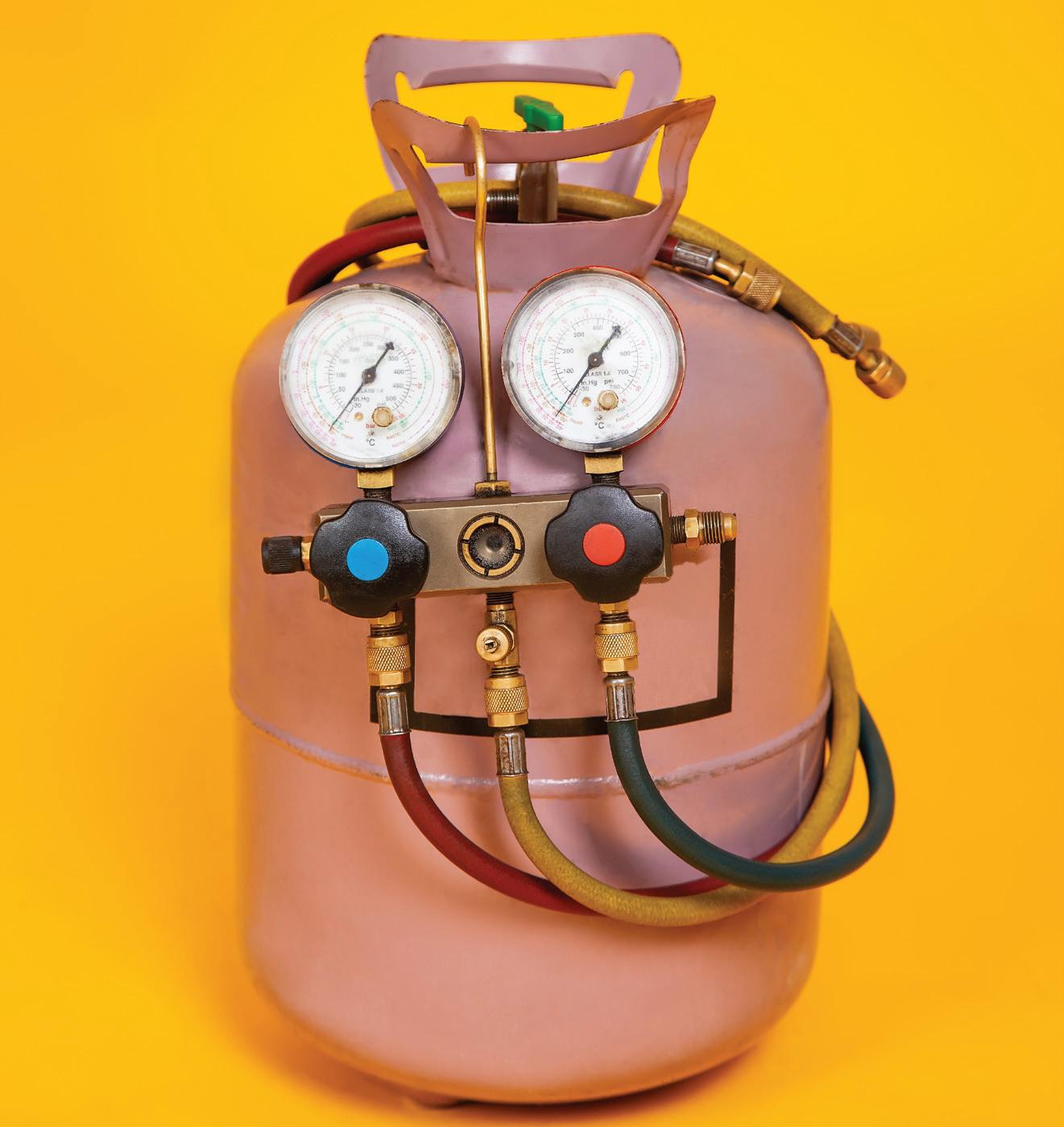
associations — Air-Conditioning, Heating & Refrigeration Institute (AHRI), Heating Air-Conditioning & Refrigeration Distributors International (HARDI), Plumbing-Heating-Cooling Contractors Association (PHCC) and Air Conditioning Contractors of America (ACCA) — have been actively engaged in this issue since the Kigali Amendment was agreed to in October 2016.
AHRI established a Safe Refrigerant Transition Task Force — which includes participation from virtually all industry stakeholders — whose job it is to manage the process so that the transition benefits all and is not unduly burdensome on any entity.
Thus, staff and members of all the mentioned associations have been working diligently with California on code issues, while simultaneously working with the national building code developers, the national, state and local fire service organizations and entities in other states to accomplish this goal.
In addition, AHRI staff and members have taken the lead in securing passage of legislation that would put in place a national phase down structure designed to bring some measure of certainty to the process. Such legislation has been introduced in the House (H.R. 5544) and in the Senate (S. 2754) on a bipartisan basis and there is reason for hope that a national plan can pass this year.
While all that has been going on, AHRI also established, with the U.N. Environment Program, a “Refrigerant Driving License” program to train technicians around the world in the safe handling of flammable refrigerants.
Following pilot programs in several countries, the RDL initiative is poised to launch around the world and many of its aspects will be applicable to a U.S.- based training program being developed by ACCA, AHRI, HARDI, NATE and PHCC, as well as other industry training organizations and by individual manufacturers for their specific products.
CONCLUSION
Understanding the state, federal and global regulations impacting the HVACR industry is incredibly challenging, especially considering the pace of change. Ironically, though, this multi-layered fabric of regulations is providing some clarity to an industry that was thrown into a bit of chaos when the federal courts struck down SNAP Rules 20 and 21, which the industry had believed would be the mechanism of the U.S. phase down.
After an incredible amount of work on the part of all involved, the industry is beginning to understand this timeline and is making the proper preparations. If all those preparations — code changes, legislation, technician training — result in a predictable and manageable path forward, this transition can be as orderly as previous transitions have been.
If all parties involved do their jobs correctly, consumers should notice no difference in accessibility, comfort, safety or affordability. This should be the goal of all of us as we move forward. u
Stephen Yurek is president and CEO of the AirConditioning, Heating & Refrigeration Institute (AHRI). John Galyen is chairman of AHRI and president of Danfoss North America. For additional information, visit ahrinet.org.
5 Ways to Generate Cash Now
EDITOR’S NOTE: Due to the unprecedented situation we find ourselves in with COVID-19, Ruth King is suspending the Rules of Wealth series and writing about actions that can help you survive these times and prepare for the future. Once this pandemic is over, she will resume the Rules of Wealth. T he old saying was “Cash is King.” Now, in this era of quarantines and stay-at-home orders, cash is even more important. Cash is now emperor!
Here are five ways you can generate and watch your cash now.
REVISIT TICKLER FILES
Thankfully, HVACR is deemed an essential business and will become more essential as it gets hotter. You can work. Just do it safely!
There should be a list of work that customers said at the end of last year, “I think I will wait until next summer before I make those repairs.”
That is your tickler file. Contact those people by phone, text or email (many are responding more to texts than in the past) and find out whether they want the work done now.
Many people are home and want to get their systems prepared for summer now. There are others who are requesting that you move your maintenance to later this summer. Until you contact them, you don’t know into which category they fall.
In addition, customers have declined repairs. A quick phone call to let them know you care is important.
You can gently remind your customer that the last time your technician was at their home, he mentioned additional work on the HVACR system. Your technician is available to perform that work safely and without contact if they want to go ahead with it.
Many people are home and want to get their systems prepared for summer now.
PROPOSAL FILES AND QUOTES
Unfortunately, many salespeople give a customer a proposal/quote and either never follow up or only follow up once. Many times, the customer has not bought from anyone. They’re waiting to hear back from a salesperson.
One of my clients laid off his salesperson and started going through his files. He made many telephone calls and within a day uncovered $80,000 of work the customer said yes to … Many people told him “we never heard back from anyone.” Follow up — even if the proposal/quote is old.
From a commercial perspective, many customers wanted the work done now when no people were in the building. It caused the least amount of disruption of their otherwise normal business.
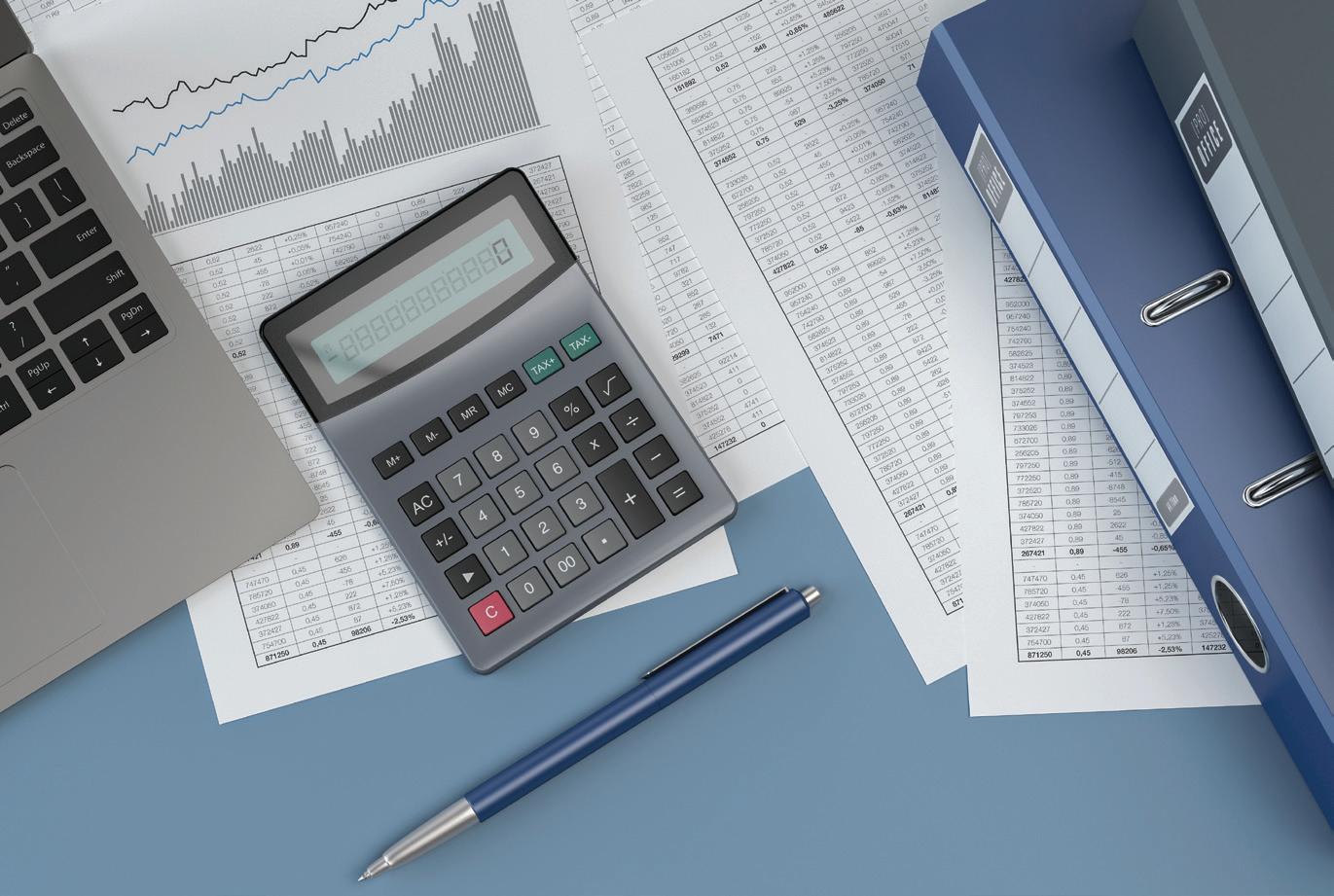
WATCH YOUR CASH
Log on to your bank account every day. Make sure there is nothing you don’t recognize. Look at deposits, checks and ACH withdrawals. Do they make sense? If not, start digging.
The bookkeeper for one of my clients noticed two deposits, each less than $1. He assumed the owner was setting up a new account and didn’t think to ask him about it. The next day the bank called and asked whether they had authorized a $50,000 withdrawal from their account! Obviously, they shut down the account immediately. If something doesn’t look right, question it immediately.
NEW RATIO
Use this new ratio to watch your cash on a weekly basis:
Accounts receivable + cash Accounts payable + credit cards
My old ratio, accounts receivable divided by accounts payable, is not as valid in these times. Now the amount of cash that you have and the amount of credit card payments owed, are just as important.
This ratio should be steady or increasing. If it is under one, you are in trouble because you will not be able to pay your bills. You need to generate profitable work and collect the payments for that work, to steadily increase this ratio. without profitable work.
INVENTORY IS A BET
This is especially true, especially in these times. You are using your precious cash to purchase items that you may not sell quickly.
Watch your inventory purchases. If at all possible, use the parts in your shop and on your trucks to complete service calls and jobs. Purchase additional materials only when you need them for a job or a service call. These purchases are not inventory. They go directly into cost of goods sold.
Your inventory days should be less than 30 days (Inventory days are 365 divided by inventory turns. Inventory turns are Annualized cost of goods sold divided by inventory).
Your shelves should be bare at the end of this pandemic!
Cash is no longer king — it is emperor. Watch it closely. u
Ruth King has more than 25 years of experience in the HVACR industry and has worked with contractors, distributors and manufacturers to help grow their companies and become more profitable. Contact Ruth at ruthking@hvacchannel.tv or call 770-729-0258.