4 minute read
Business Insights: Viega
Next Article
Safer. Faster. Cleaner.
Save 60-90 percent on labor and stay on schedule with MegaPressG ® fast, flameless connections
Historically, best practices when it comes to joining pipe above two inches has been to weld everything. But with the new MegaPressG® from Viega®, contractors have a new, safer option to help them save time on jobsites.
“Welding certainly has its place and its strengths,” says William Dutcher, product manager for Viega. “Contractors should rethink how they can join carbon steel pipe for gas up to four inches these days.”
MegaPressG — available in ½- to 4-inch sizes — is going to allow your labor force to make an impact, no matter the skill lever of the workers on the job site. Viega has done the engineering behind these fittings to ensure confidence in their performance.
“The biggest advantage, aside from time savings, is just the predictability,” Dutcher says. “These fittings have been engineered with such strict tolerances that users understand what they can expect.”
Contractors can reduce the amount of call backs on a job site and can eliminate failures because of Viega’s Smart Connect® technology, which helps identify unpressed connections. Smart Connect ensures the user all of the connections have been made when they pressure test, thus eliminating a lot of the variability you get with welding.
HVACR Business spoke with Dutcher about advantages of MegaPressG versus traditional pipe-joining methods.
How does MegaPressG save job time?
The standard procedure for installing a MegaPressG fitting is easy. First, you ream and deburr the pipe, then mark your insertion depth to make sure that the fitting is seated all the way in for full grip. Then, it’s as easy as pulling the trigger on a power drill. It’s a seven second press.
For the larger sizes, we do require the use of a booster, so that takes only a couple of extra seconds, because it’s a two-cycle press.
When you compare it against traditional weld methods —preparing for the welds, you’re putting down tack welds, filling it, taking the slag off and then painting or finishing — it’s an 80 percent time-savings.
WILLIAM DUTCHER
Product Manager Viega 800-976-9819 viega.us
FOLLOW UP:
Looking to save time and money on jobsites? Learn about how Viega’s MegaPressG is the safer, faster, cleaner way to connect gas pipe. Visit viega.us/megapressG.
BUSINESS INSIGHTS: CONNECTIONS is brought to you by Viega
How safe is it to use MegaPressG?
Viega typically engineers a five-time safety factor for all fittings. For example, when we state our operating parameters are 200 PSI, these fittings have been tested to well beyond that. So just from a fitting perspective, the safety factor is quite large.
When you go into the reliability of our connections, you don’t have the variability between skilled labor … your apprentice can make the same quality connection that your journeyman pipe fitter has made over the years. Whereas welding, the new guy on the job can’t necessarily create the same quality weld that an experienced journeyman pipe fitter can.
And since there is no welding, there’s no exposure to harmful gases, chemicals or cutting oils.
Is that why this is considered a cleaner installation?
Yes, it’s a much cleaner procedure because, aside from the bags that the fittings would come in, there’s really not the jobsite debris that you would have with other systems.
There are no messy cutting oils versus a thread system. You’re not going through cutting dyes and shaving metal everywhere. As far as the comparison to weld, you don’t have to bring all these welding rods onsite either. From my experience, I’ve seen welders weld down to a certain distance on the welding rod and then simply chuck it into the metal bucket as sort of a scrap pile.
MegaPressG doesn’t have the consumables these other methods do, which naturally leads to a cleaner job site. It allows crews to get off of the job site faster and on to the next job.
Do technicians require less equipment?
Yes. In fact, one guy can carry both tool boxes in their hands, whereas a welder needs the following equipment onsite: tanks, welding equipment, safety equipment, any sort of welding blankets to cover nearby walls or things you need to protect and so on. It can be a multiple-trip job if you’re trying to do something on the 10th floor with no elevator or with a primitive kind of construction elevator.
Not only is it less equipment — and easier to use — it’s a huge time savings just in the fact that you can walk these tools up the stairs versus some of the traditional methods, such as getting a threading machine or welding machines into position. u
Pros use Viega ProPress ®
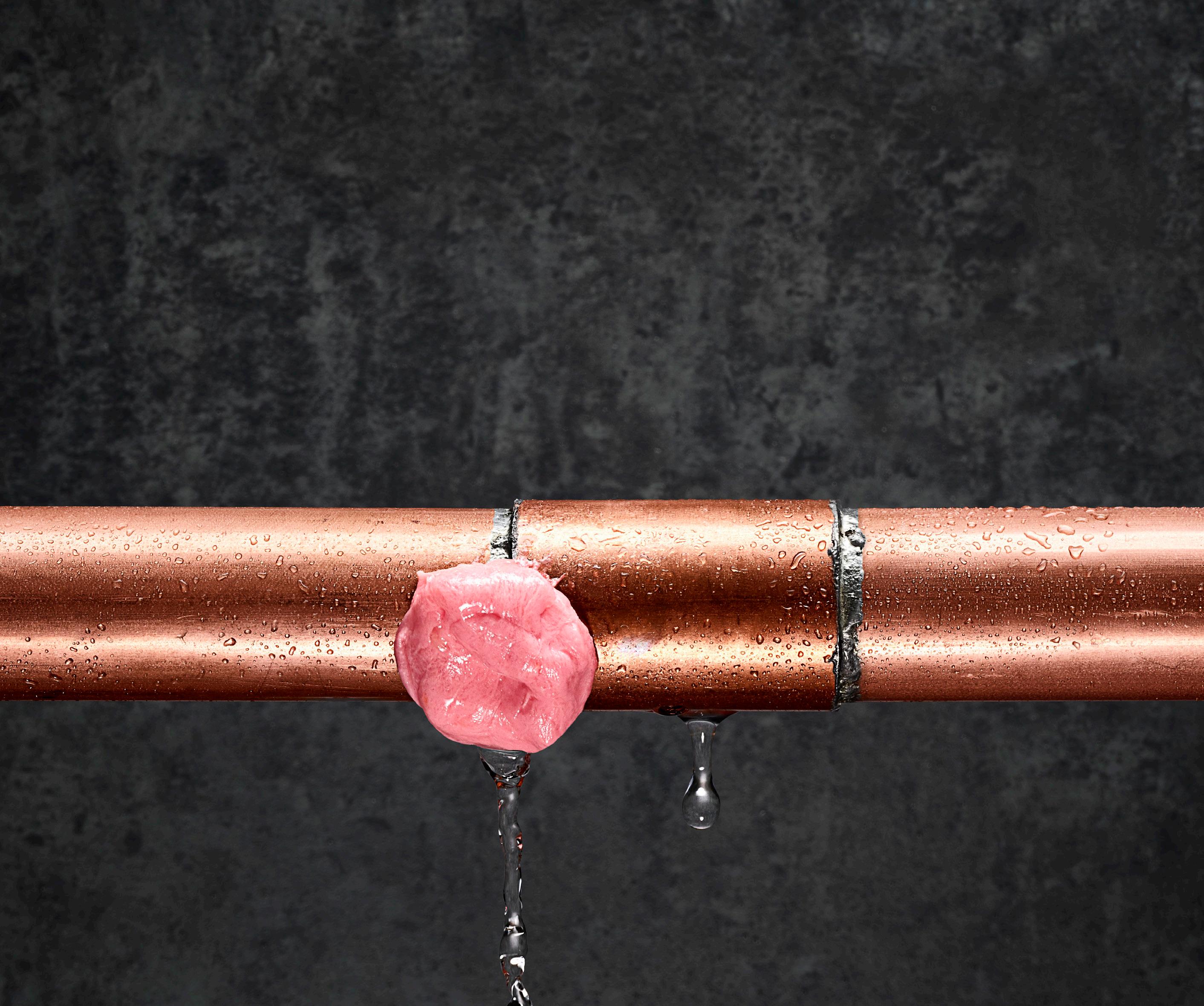
viega.us/pro
The most durable, dependable, innovative pipe connector on the market.
If you take your reputation seriously, you don’t trust your pipe fitting to any old technology. Unlike soldering, only the Viega ProPress system connects in seven seconds or less. And with Smart Connect ® technology, you can easily identify unpressed connections.
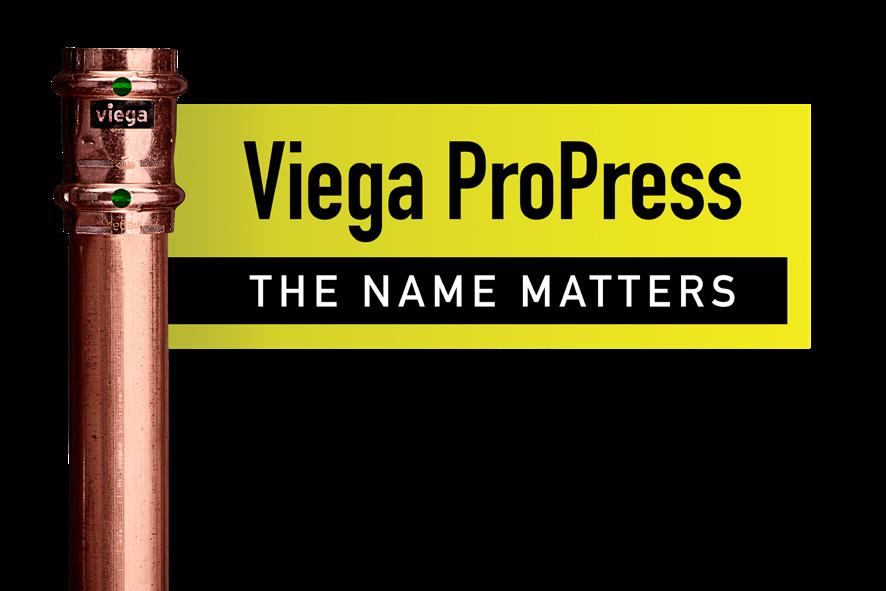