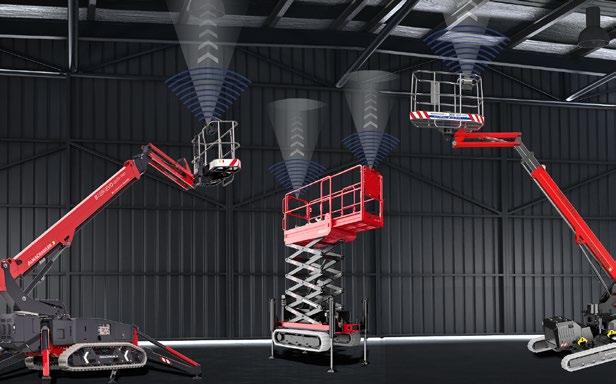
2 minute read
Almac anti-collision detection
Almac anti-collision detection puts safety first
Manufacturers are advancing EWP capabilities as quickly as new technologies emerge and evolve.
Buyers of elevated work platforms balance many considerations when deciding their next asset purchase, including efficiency and productivity, total cost of ownership (TCO), utilisation, hire rates, and resale value.
However, the most critical component is operator safety. SafeWork Australia recently reported that incidents involving EWPs have resulted in death and serious injury, with at least nine fatalities and 355 workers’ compensation claims between 2015 and 2019.1
Common hazards related to the use of EWPs include uneven or unstable ground, machine failure, falling objects, weather-related hazards, and traffic or pedestrians.
The range of motion available on some modern EWPs introduces the increased possibility of a crushing incident for operators. Almac sees the risks as highest when: • equipment is used near overhead structures such as roofs, beams, trees, pipework; • a platform moves unexpectedly near an overhead structure due to uneven or unstable ground; • ineffective use of controls, or a controls malfunction; • the operator becomes distracted while manoeuvring the EWP.
Before operating an EWP in, around, or near fixed structures, SafeWork Australia has identified that a person conducting a business or undertaking (PCBU) must eliminate crush risks by identifying hazards and assessing and controlling risks where practicable to do so.
Secondary guarding
SafeWork Australia has developed guidance for managing the risks of EWPs. This includes avoiding the use of EWPs not fitted with secondary guarding when there is a risk of crushing. Various secondary guarding devices may help prevent crush or trap injuries, depending on the type of EWP and type of work being done.
AlmaCrawler is fitted with intelligent integrated anti-collision sensors (compliant to Australian and New Zealand standards) to prevent the movement of their EWPs into unsafe areas. This feature is available on the JIBBI (see below/opposite etc re boxed copy), Athena, and Billennium range of EWPs.
Safety sensors
During operation, Almac’s anti-collision sensors create a large proximity-detection zone above the operator. These monitor for potential impact with any overhead obstructions that may result in injury or death and damage to the equipment or surrounding structures.
The main sensors are fitted to the top rail of the platform and are always active during operation. If a proximity breach is detected, the sensors trigger both an audio and visual alarm while simultaneously locking other machine’s functions except for the lowering ability. The operator must initially release the control and assess the surroundings to determine the detected proximity risk. Should the operator decide to continue with elevation, a three-second delay is activated before continuing.
While secondary guarding technology will undoubtedly minimise the risks involved in working at heights, accidents can unfortunately occur at any time.
Employers must ensure that operators are fully trained on safe use of the EWP. Operation manuals and manufacturer specifications should always be followed, ensuring that safety features are not ignored, modified, or removed at any time. Safety standards, signage, PPE, training, and checklists all form part of controlling risks in relation to the use of EWPs.
Emerging technologies such as AlmaCrawler’s collision detection capabilities, coupled with regular machine maintenance and other preventative measures against EWP hazards, will ensure more workers return home safely to their families at the end of the day.
Explore the AlmaCrawler product range at www.almac-pacific.com.au.
1 New Guide on Managing the Risks of Elevating Work Platforms, September 2021, SafeWork Australia