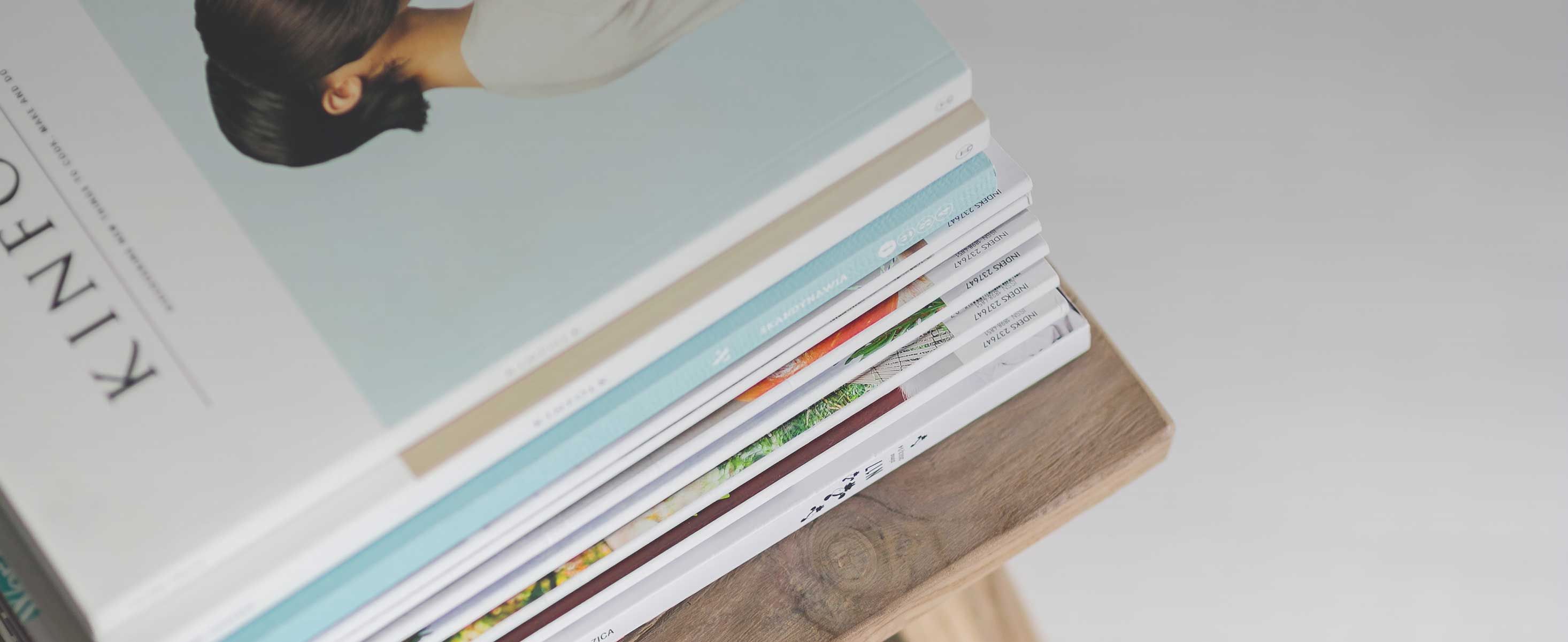
9 minute read
Takeoff, Climb, Landing, and Engine-Out Performance
Performance
10 CHAPTER
If you’ve been buzzing around the flatlands ’til now in piston airplanes, you’ve probably reduced the whole issue of performance to just a couple of items: cruise speed and fuel planning. While everyone studies takeoff and landing performance, a close look is rarely required for low-elevation piston operations. Those of us who routinely fly in mountainous areas, or who operate at gross weight in piston twins, must more frequently consider takeoff, climb, engine-out, and landing performances.
In turbine-powered aircraft, these performance issues must be addressed more diligently than ever. Despite much greater installed power, most turbine aircraft tend to operate, in many respects, much closer to their limits than typical light piston aircraft. Runway length requirements, especially for jets, are much greater than for piston aircraft. Therefore, turbine aircraft tend to require a larger percentage of the average runway for operations. This calls for more careful planning, especially for the possibilities of engine failures, go-arounds, and aborted takeoffs.
Also, turbine aircraft are designed to operate routinely at high weights since their best economic performance is generally tied to full passenger or freight loads. Even with all that extra power, many turbine aircraft don’t actually perform all that much better engine-out, at gross weight and high-density altitude, than many light piston twins.
A related factor is the large range of weights at which a typical turbine aircraft operates. As you know, the operating airspeeds of an aircraft vary, based upon weight. Therefore, when flying at gross weight in a light aircraft, you may decide to rotate at a higher airspeed and on final to “cross the fence” a little faster than normal. Due to the range of operating weights for larger turbine aircraft, along with density altitude and other considerations, the spreads of proper rotation, emergency, and landing speeds are much larger. “A little faster” simply is not accurate enough for safe operation of turbine aircraft.
Sure, cruise performance must be addressed on every flight, due to fuel planning requirements, but among the major performance planning issues for turbine aircraft are takeoff, climb, landing, and engine-out situations.
If you’ve been flying light piston aircraft until now, you’re used to learning a specific set of airspeeds for each plane. There was a standard takeoff rotation speed, best angle (VX) and best rate of climb (VY) speeds, and recommended airspeeds for approach and for crossing the threshold on landing. These same parameters apply to turbine pilots, but they’re described differently. Since turbine aircraft operate under broad variations of weight, configuration, and environment, a wide range of operating speeds must be calculated for takeoff, landing, and emergency or abnormal operations (such as engine-out and noflap landings). Since pilots can’t possibly memorize every speed variation for every possible situation, an entire airspeed terminology has been developed that is unique to turbine aircraft.
There’s more than convenience involved in the use of turbine “V-speeds.” Sharp multiengine piston pilots know the safety benefits of engine-out planning prior to takeoff. In the event of an aborted takeoff, will there be adequate runway for stopping? Can the trees be cleared in the event of an engine failure after rotation?
The FAA has carefully defined calculation of turbine V-speeds in order to ensure that engine-out aircraft performance meets minimum safety standards
under such circumstances. “V1,” “VR,” and “V2” are among the airspeed terms familiar to every turbine pilot. Let’s first examine these terms in the context of required safety-related performance planning. Then we’ll consider practical usages of these terms in dayto-day flying.
Takeoff and Climb Performance
All takeoff and initial climb performances in turbine aircraft is planned with one situation in mind: safe continued operation after an engine failure. Certain standard decision points are established for takeoff, with specific performance capabilities required at each. These decision points are described in the form of airspeeds attained by the accelerating airplane and are known as “V1,” “VR,” and “V2.” As safety speeds, these takeoff V-speeds allow the aircraft to achieve optimum or required performance for each particular segment of takeoff in the event of engine failure. Each is computed before every takeoff and varies with the aircraft’s weight at the beginning of takeoff roll. (By the way, you ex-military types will miss the takeoff acceleration check; few civilian airports have runway distance markers.)
V1 : Takeoff Decision Speed
Let’s start with V1, takeoff decision speed. Simply put, it is “go or no-go” speed. If an abnormality occurs before V1 is reached, takeoff is to be immediately aborted. If an engine failure or other abnormality occurs after V1 is attained, takeoff is continued, and the problem is treated in flight. Most airline and corporate flight departments have historically based V1 speeds upon “balanced field length” for their particular aircraft. If an engine failure occurs exactly at V1, the distance required to abort the takeoff and stop is the same as the distance required to continue the takeoff. In familiar multiengine terms, this means that accelerate-go distance equals acceleratestop distance.
However, many airlines with large transport-type aircraft, and some corporate operators, now adjust V1 to a lower speed than the balanced field length V1. Lowering V1 has the effect of lowering the speed where an abort might be initiated; pilots have been doing this in response to numerous accidents that have resulted from high-speed aborts. With most multiengine turbine aircraft, it turns out to be safer to continue takeoff after engine failure than to abort and to try to safely stop the aircraft on the remaining runway. This is especially true for more massive transport category aircraft.
After all, balanced field length V1 is determined during flight testing with a brand new plane, new brakes, a dry runway surface, and a well-rested super test pilot type in the left seat who’s prepared for any emergency. With this in mind, it seems more than reasonable to reduce the V1 speed slightly to compensate for the average pilot flying a used airplane in bad weather after seven flying legs.
For the same reasons, many captains now carefully define “abnormality” on the before takeoff briefing reference the V1 “go/no-go” decision. “We’ll abort for minor malfunctions or yellow caution lights up to 80 knots and for red warning lights or the fire bell up to V1. Takeoff will be continued for any problem occurring after V1, and we’ll handle it in flight.” Operators may require further adjustments to V1 under special conditions, such as takeoff on wet or slippery runways (Figure 10.1).
You may have heard the expression, V1 cut. This term refers to the act, during pilot training or testing, of simulating an engine failure precisely at V1 on the takeoff roll. It’s easy to see both the training benefits and safety hazards of experiencing engine failure at such a critical moment. V1 cuts are among those exercises best experienced in the simulator.
VR : Takeoff Rotation Speed
VR is takeoff rotation speed in turbine-powered aircraft. In the event of an engine failure, rotation at VR to a specified pitch attitude is designed so the aircraft will attain V2 by the end of the runway—at least 35 feet above the surface. VR may be set equal to or higher than V1.
V2 : Minimum Takeoff Safety Speed
V2, or minimum takeoff safety speed, allows the aircraft, in the event of an engine failure, to maintain an FAA-required climb gradient in the climbout flight path. From a practical standpoint, consider V2 as engine-out best rate of climb speed in takeoff configuration. V2, depending on terrain, is normally maintained up to a company-mandated altitude, usually 400 to 600 feet above ground level (AGL). Then airspeed is allowed to increase to engine-inoperative best rate of climb speed up to some specified
altitude, usually 1,500 feet above ground level. Once above that altitude, airspeed is increased to normal climb speeds, and appropriate After Takeoff or Climb Checklist(s) are accomplished.
Those who’ve flown twin-engined piston aircraft know engine-inoperative best rate of climb speed as VYSE (single-engine best rate of climb). For three- or four-engined airplanes and for some turbine twins other terms are used, such as “V3,” “V2 + 10 (knots)” or “best-rate-remaining engines,” depending on aircraft type. Because the terminology for this speed is not well standardized, we’ll stick with “engineinoperative best rate of climb speed.”
Engine-Out Climb
Engine-out climb gradient must also be considered for departure. In many cases, this is the most restrictive of all turbine-powered aircraft performance factors, especially at high-density altitudes and in mountainous terrain. Reduced takeoff weight is the way to provide for adequate engine-out climb performance. Pilots are sometimes faced with tough choices on departure: minimize fuel or restrict loading of passengers and cargo.
For routine (all engines working) climb performance after the initial takeoff segments, most manufacturers publish a “Time, Fuel, and Distance to Climb” chart or something similar. These charts estimate fuel burn, distance, and elapsed time required to climb to cruising altitude. Turbine aircraft climb charts provide more information than
rotation point 1st segment climb 2nd segment climb 3rd segment
400 ft. AGL
35 ft. AGL
“V1, VR, rotate”
“80 kt, all systems normal” “Positive rate, gear up” “V2” “Engine-inoperative best rate-of-climb speed, flaps up”
Typical takeoff profile
“Clean up” and accelerate
touchdown point
final approach speed VREF + 20 kt.
VREF + 10 kt.
VREF
Typical landing profile
V-speeds provide standard performance references for takeoff and landing safety in case of engine failure. Takeoff and landing profiles vary by operator, aircraft, and conditions.
FIGURE 10.1 | Takeoff and landing V-speeds.
those you may have used in the past. For example, flight crews may be offered several different climb speeds to choose from. Most flight departments instruct their pilots to use climb power settings slightly reduced from maximum continuous power.
Enroute Engine-Out Performance Planning
Enroute engine-out performance for turbine aircraft requires a little more planning than what you may be used to in piston aircraft. FAA certification requires multiengine aircraft to achieve certain engine-out performance during enroute flight. However, MEAs (minimum enroute altitudes) over mountainous areas are sometimes higher than the one-engine-inoperative service ceiling for a given aircraft. In order for operators to utilize their aircraft under these circumstances, the FAA allows use of a drift-down procedure for high-MEA route segments (Figure 10.2). Cruising altitude must be high enough that, in the event of engine failure, the airplane can pass safely out of the critical airway segment before “drifting down” to the MEA. (Those of you flying in the Midwest needn’t worry much about this one!)
Aircraft performance during cruise depends upon many of the same factors you dealt with flying piston aircraft. Engine power settings, aircraft weight, and weather conditions of wind and temperature all affect performance.
minimum altitude to meet drift-down requirements
Landing Performance
Landing performance calculations for turbine aircraft are similar to those used for piston aircraft. The greatest difference is that turbine aircraft generally operate closer to their performance limits. With their higher final approach speeds and much heavier weights, turbine aircraft require more runway. Therefore, landing performance planning requires plenty of attention in turbine aircraft.
drift-down path, in the event of engine failure
MEA MEA
terrain MEA
one-engine-inoperative service ceiling for this aircraft
Drift-down requirements apply when an aircraft flies a route segment where the MEA (minimum enroute altitude) is higher than its one-engine-inoperative service ceiling. The aircraft must fly high enough so that, in the event of engine failure, it will reach a lower route segment before "drifting down" to its one-engine-inoperative ceiling.
FIGURE 10.2 | Engine-out drift-down requirements.