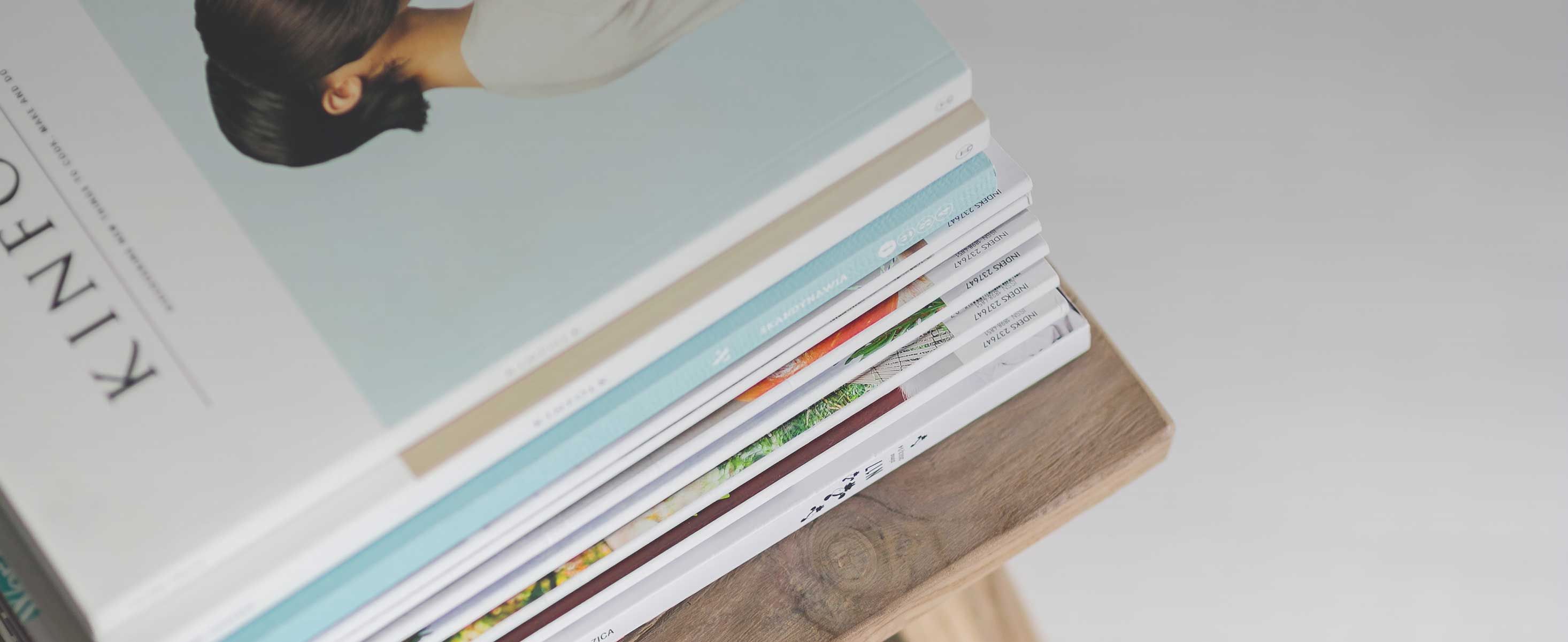
2 minute read
Balance Considerations
many large aircraft have fuel dump valves to jettison fuel overboard and thereby reduce weight below MLW for landing. Those aircraft without dump valves are faced with flying off the extra fuel before landing, or (like the 737) have special low descent rate landing procedures for heavy landings.
Aircraft Weight Categories
The FAA separates aircraft into weight categories, for purposes of wake-turbulence separation. Heavy aircraft are those certificated at 300,000 pounds or more maximum takeoff weight (MTOW). Large aircraft have maximum certificated take-off weights of more than 41,000 pounds, up to but not including 300,000 pounds. Small aircraft have certified MTOWs of 41,000 pounds or less and include all but the largest turboprop aircraft. As might be expected, ATC provides increased separation behind a heavy aircraft and those that follow it, based on these classifications. Note that aircraft are classified based on maximum certificated weight, whether or not they actually operate at that weight. What’s more, aircraft are sometimes reassigned by the FAA to heavier weight categories than their actual MTOW, due to unusual wake turbulence characteristics—the Boeing 757 being a notable example. Finally, at time of writing, ICAO had established a new Super weight category (to accommodate the giant Airbus A-380) that may eventually be adopted by the FAA. These FAA weight categories are constantly in flux, so be sure to check the FARs if you need current information for a particular aircraft.
A different FAA weight definition concerns pilot certification: type ratings are required to pilot all “large aircraft” having maximum certificated takeoff weights greater than 12,500 pounds. (This rule effectively applies only to large turboprop and piston aircraft, as type ratings are required to pilot all turbojet-powered aircraft, including “pure jets” of any size or weight.)
Balance Considerations
In order for an aircraft to fly safely and be controllable, its center of gravity (CG) must lie within a certified range. While this is important in light aircraft, it becomes even more critical in large aircraft due to the huge weights and loading ranges involved.
CG as Percentage of MAC
CG computations for light turbine aircraft are usually accomplished in the same general manner you’ve used before. Many large aircraft operators, however, identify CG location not in terms of inches from datum but as a percentage of mean aerodynamic chord (MAC). The only difference is in how the CG location is described. (Whether in inches or percentage of MAC, the actual CG position is the same.)
MAC is simply the chord of an imaginary rectangular wing that has the same aerodynamic characteristics as the actual airfoil of the airplane. This simple imaginary wing represents in performance what otherwise might be a very complex swept wing planform. MAC is used primarily as a reference for longitudinal stability characteristics (Figure 11.2).
Calculating CG position as a percentage of MAC (%MAC) is relatively straightforward. CG location is first calculated in the conventional manner. It may be described as inches from datum or in terms of “loading stations.” Loading stations are simply measuring units made up by the manufacturer. The calculations, in these cases, are the same as what you’re used to; just use the loading stations as arm values, instead of inches.
The length of MAC is calculated by subtracting LE MAC (leading edge MAC) from TE MAC (trailing
CG
%MAC
MAC
Imaginary rectangular wing used in calculating MAC has the same aerodynamic center of pressure as the real wing.
FIGURE 11.2 | Mean aerodynamic chord (MAC).