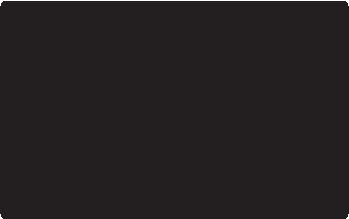
13 minute read
Routine Performance Planning
VREF : Landing Reference Speed
As discussed earlier, the large range of turbine aircraft operating weights results in a corresponding spread of landing speeds. Therefore, there’s no single final approach speed used in large turbine aircraft. Rather, the term VREF is used as landing reference speed. Lest all these new terms sound too mystifying, let’s consider where VREF comes from. Remember your old rule of thumb for calculating final approach speed? VREF for many turbine aircraft is similarly calculated at 1.3 VS0 (1.3 × stall speed in landing configuration). VREF accordingly increases with aircraft weight. A Boeing 727, for example, may weigh anywhere from around 110,000 pounds to 180,000 pounds on final approach. Based upon landing weight, its final approach speed varies from around 112 knots to 147 knots. As with the takeoff V-speeds, pilots must compute VREF for every landing.
V2 and engine-inoperative best rate of climb are also recomputed for every landing to allow for engine failure in case of a go-around. Approach climb gradient (climb performance during singleengine go-around) must also be considered for such situations; it’s usually the most restrictive landing performance issue. To determine approach climb gradient, it is necessary to consider the outside air temperature (OAT), airport density altitude, aircraft configuration, and aircraft weight.
When determining landing performance, the FAA again requires that minimum standards be met for operations onto any particular runway. Airport density, altitude, wind components, runway surface conditions, and slope must be considered, along with aircraft configuration and weight, when determining required field length and maximum landing weight. The FAA requires most categories of aircraft to be able to land safely within 60 percent of the landing distance available at the primary destination airport. (Seventy percent is allowed for filed alternate airports.)
Braking Performance
One additional factor to consider on both takeoff and landing performance calculations is the aircraft’s braking system. This is very important because all deceleration and stopping performance is predicated on use of wheel braking only. (Thrust reverser performance does not enter into the calculations, even though the effects may be great. Consider reversers as adding to the margin of safety.) Braking charts are provided for crew reference on larger turbine aircraft.
Routine Performance Planning
We’ve now covered most of the performance issues unique to turbine aircraft operations. The performance charts and graphs themselves, which you’ll see in ground school, are similar to those you’ve used in the past for piston or military aircraft. But all of those performance calculations can be a lot of work!
When aircraft are delivered to corporate or airline flight departments, they come with manufacturers’ performance charts. These charts tend to be very complex and too time-consuming for flight crews to use routinely. Therefore, most flight departments develop quick reference performance charts for their flight crews. Quick reference charts are particularly valuable for regularly scheduled operations, which often may include “ten-minute quick turns” and nine or more flying legs per day.
TOLD Cards
Two types of quick reference charts are particularly common among operators. Most flight departments construct simple quick reference Takeoff and Landing Data cards (TOLD cards), allowing flight crews to quickly determine aircraft V1, VR, V2, and engine-inoperative best rate of climb for takeoff, as well as VREF, V2, and engine-inoperative best rate of climb for landing (Figure 10.3). Using TOLD cards, these airspeeds may be quickly calculated for a given aircraft based upon gross weight, flap position, and sometimes other conditions. On new technology aircraft, computers are often used to calculate these airspeeds, along with power settings and other flight parameters.
Airport Analysis Tables
To deal with airport-specific performance computations in a safe and timely manner, all air carriers and many corporate flight departments enlist the aid of specialized companies or computer programs to prepare performance data for every likely situation. This
information is provided to flight crews in the form of an FAA-approved Airport Analysis, a customized book of tables covering every authorized runway at every airport to which an operator flies. The Airport Analysis is a quick source of required aircraft performance under current conditions on any given day. It may include various options that the company deems necessary, such as intersection departures, rolling takeoff restrictions, company-preferred IFR departure procedures, or maximum operating weights for particular runways.
As you may imagine, it’s often impractical for a flight department to include an analysis for every runway and every intersection at every airport where the company might operate. So be careful when considering intersection departures! Depending on specific FAA approval, most commercial aircraft may operate only from runways and intersections published in their own companies’ Airport Analysis material, and then only under listed conditions.
Every company instructs its pilots on the use of its particular Airport Analysis charts during ground school. When used properly, this information keeps pilots safe and in compliance with FAA regulations without the labor of hand calculations. It is required to be onboard an operator’s airplane every time it is flown.
It is possible, under unusual circumstances, to get approval from company dispatch for situations certified by the manufacturer but not covered in the company Airport Analysis. However, the company must then furnish the flight crew with all required performance material.
An interesting story related to this occurred in Phoenix, Arizona, during June 1990, when outside air temperature reached 122°F (50°C). Boeing aircraft were grounded because their published performance charts included OATs up to but not including 50°C. McDonnell Douglas aircraft, on the other hand, were flying that day. They carry certified performance data up to and including 50°C!
Aircraft Weight: 25,000 pounds
TAKEOFF Flaps 10° 5° 0°
V1 = VR
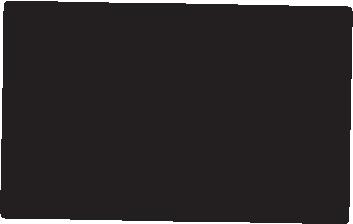
V2
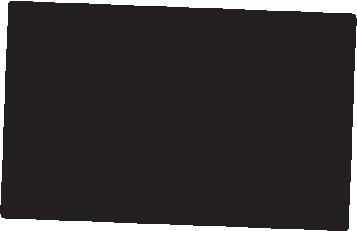
VYSE
LANDING 82 89 –
88 98 105
– – 107
Flaps 30° 10° 0°
VREF 86 92 111
Takeoff and landing data cards provide quick pilot reference for takeoff and landing V-speeds. There are two general types of TOLD cards. The type shown is a part of a series of cards, each offering specific speeds for a given aircraft weight. Correction factors may be provided to compensate for such factors as field elevation and outside air temperature. The other type of TOLD card (not shown) simply provides blanks to be filled out using “longhand” methods. The TOLD card, in that case, just serves as a convenient place to display calculated speeds.
FIGURE 10.3 | Takeoff and landing data card (TOLD card).
Temperature-Derived Reduced Thrust Takeoff
In efforts to reduce engine wear and engine noise associated with maximum thrust takeoffs, many airlines and corporate flight departments use temperature-derived reduced thrust takeoff procedures when feasible. For turbine-powered aircraft, the required runway length is calculated prior to every takeoff. In most situations, aircraft weight and ambient atmospheric conditions are such that an aircraft can safely take off in a much shorter distance than the actual amount of runway available. For reduced-thrust takeoffs, the flight crew or the company’s performance engineering staff calculate a lower-than-maximum thrust setting that although requiring more runway, will still safely maintain FAA-required minimum takeoff and climb performance on departure. The maximum allowable amount of thrust reduction regardless of attainable climb performance is set by the FAA or other national governing authority and is a fixed percentage of the full-rated engine takeoff rating.
Depending on the aircraft or engine manufacturer, reduced-thrust takeoff procedures may have a variety of names such as assumed temperature thrust, flex-temp thrust, factored takeoff thrust, or simply reduced thrust. Reduced-thrust settings are computed using the performance data of an “assumed” temperature that’s higher than the actual ambient temperature for purposes of calculating corresponding V-speeds, takeoff thrust settings, and
climb-out flight-path performance. It’s important to note that use of reduced thrust takeoff is “optional,” and full-rated engine thrust is always available at any point in the takeoff run and subsequent climbout should the need arise. Most flight departments require flight crews to use reduced-thrust takeoffs because of the considerable maintenance cost savings and increased engine reliability this procedure offers.
In practice, most flight departments offer the flight crew a choice of multiple reduced-power takeoff settings. The choices may vary by runway, required climb performance, flap settings, or flight department preferences. Generally, for every takeoff, pilots will choose from up to a half dozen or so different reduced-thrust setting options. (For example, some Boeing aircraft offer reduced-thrust alternatives in terms of AT30, AT40, AT50, etc., referring to ambient-temperature 30°C, ambient-temperature 40°C, and so on.)
Depending on the weight and data numbers, weather, and other variables, the flight crew often waits to set the reduced power setting until just a few minutes before the actual takeoff (Figure 10.4).
As you might imagine, there are a few limitations placed on the use of reduced thrust takeoffs. For instance, reduced thrust procedures are not permitted when the runway is contaminated with snow, ice, slush or standing water. Additionally, certain aircraft systems must be in operation for use of reduced thrust. These items differ by aircraft type but generally include safety systems like anti-skid brakes, abort-takeoff brake mode, key power-setting instruments, and some or all thrust reversers. Weather conditions are another factor the flight crew must consider when determining the power setting to be used. Frontal thunderstorm activity, strong winds, the threat of wind shear, and wake turbulence avoidance are all potential reasons for the flight crew to choose maximum takeoff power over reduced thrust procedures.
maximum takeoff thrust
“AT30” thrust setting
“AT40” thrust setting
“AT50” thrust setting
Thrust
full rated thrust (engine pressure limit)
minimum thrust required full rated thrust (engine temperature limit)
Outside Air Temperature
30C 40C 50C
ambient temperature
assumed temperature
FIGURE 10.4 | Temperature-derived reduced takeoff thrust.
Derated Thrust
Derated thrust is closely related to, and often confused with, the temperature-derived reduced-thrust takeoff procedure we’ve just discussed. However, derated thrust is a fixed value of thrust reduction without entering temperature into the performance equation as with a reduced-thrust takeoff. Many aircraft offer derated-thrust settings that may be selected by the flight crew at any time during takeoff or in flight. These settings vary in name and units depending on aircraft type. For example, an engine control panel or engine performance page might offer “Thrust 1” or “Thrust 2” settings representing thrust reductions of 10% or 20%, respectively, of full-rated thrust. (The actual percent reduction varies by aircraft type.) Other aircraft offer “Derate 1” or “Derate 2” settings in which the pilots select the actual derated thrust value rather than a percentage (e.g., Full rated thrust = 26,000 lbs of thrust; Derate 1 = 24,000 lbs of thrust; Derate 2 = 22,000 lbs of thrust). Note that while derated-thrust settings may be available in a variety of flight profiles, the previously discussed temperature reduced-thrust takeoff settings are typically only available during the takeoff segment of the departure (Figure 10.5).
Incidentally, you may hear the similar-sounding term, derated engine. Despite related concepts, derated engines are fundamentally different in purpose and execution than the derated-thrust operations we’ve just discussed. Aircraft operators sometimes find themselves in the situation of equipping an aircraft with different models of the same engine. These different models may appear identical to the naked eye, but may produce significantly different amounts of thrust for various phases of flight. If an engine to be installed produces more
thrust than another engine already installed in the airframe, then it must be permanently or semi-permanently derated at installation to equalize thrust between engines. Also, manufacturers often install derated engines in new aircraft to keep the aircraft within certification limits given available engine models, or to reduce engine wear and maintenance costs due to reduced engine loads. In any case, derating an engine would only be accomplished by a manufacturer or maintenance personnel on the ground, not by the flight crew as in derated-thrust flight operations.
maximum takeoff thrust
derate 1 thrust set
Thrust
full rated thrust (engine pressure limit)
derate 1
derate 2
minimum thrust required
Derate 2 is not available because for the current ambient temperature it is less than minimum thrust required. full rated thrust (engine temperature limit)
Outside Air Temperature
ambient temperature
FIGURE 10.5 | Derated thrust.
Cruise Performance: Fuel Planning
One of the great contributions of the turbine engine to aviation is its power-to-weight ratio. Tremendous power is available from relatively small turbine engines, resulting in excellent high-speed performance by most of today’s turbine aircraft. The bad news is that turbine engines consume lots of fuel in delivering such terrific power. Older turbojets are among the biggest fuel burners. Turboprops “sip” fuel, by comparison, but are significantly slower. The latest generation turbofan engines are providing big advances in fuel economy, but trip lengths have been extended at the same time.
One way or another, lots of fuel must be carried by turbine aircraft, and careful fuel planning is always required. This is especially true among jets, with their higher hourly fuel consumption and extended missions. Let’s examine some of the reasons why turbine fuel planning is so challenging.
First of all, turbine aircraft carry and burn a lot of fuel. To give you an idea of the numbers involved, an MD-11 carries a little over 256,800 pounds of fuel. Sounds like a lot until you consider the fuel burn of 16,000 pounds per hour (based on cruise fuel flow at FL 350 and aircraft weight of 460,000 pounds). Fuel planning for these aircraft must be very thorough in order to execute a flight within safe fuel limits.
Then there’s the fact that fuel efficiency varies tremendously by altitude; turbine engines burn much more fuel down low than at high altitudes. That same MD-11 burns more like 26,000 pounds per hour in cruise at 11,000 feet and achieves a much slower true airspeed. You can see that unanticipated assignment of a low cruising altitude can completely change fuel consumption for a flight.
Just for comparison, let’s also consider the performance of a popular business jet. At 33,000 feet, the “bizjet” cruises at a true airspeed of 415 knots. Fuel flow under those conditions is around 1,200 pounds per hour. Down at 15,000 feet, the same aircraft cruises at 370 knots, burning 1,800–2,000 pounds per hour of fuel. Consider the combined effects of a 60 percent increase in fuel flow, with a 10 percent decrease in true airspeed. Now you know why jet pilots don’t like to hear “early descent” requests from ATC!
Jets accomplish fuel efficiency partially through ground speed. They burn lots of fuel per hour but travel a great distance in that hour. Therefore, they are relatively efficient in range (distance per fuel load) but less so in endurance (flying time per fuel load). Anything that adds unexpectedly to the duration of a flight, such as holding for weather, can be costly or even potentially hazardous.
Since turbine aircraft operate at middle to high altitudes, winds can be very strong, dramatically
impacting ground speed. An extra hour in the air costs a lot of money in that MD-11. (Don’t forget to add all of those other hourly operating costs to the extra 16,000 pounds of fuel burned.)
Finally, long-range flights often require huge fuel reserves and careful “what if” planning throughout the mission. Where must the LA to Hong Kong flight land if Hong Kong socks in? The same question might be asked of a Chicago to Boston turboprop driver. Where to, if the entire Northeast fogs in? (Not an uncommon situation!)
The answer may seem as simple as carrying lots of fuel. Unfortunately, it’s not that easy. Since fuel consumption is so high in jets, lots of fuel capacity is required for longer missions. Therefore, there’s a huge weight difference between full and partial tanks. It is very expensive and costs payload to “tanker around” more fuel than is necessary for a given flight. First there are the lost revenues when cargo and passengers are left behind in lieu of fuel. Then there are the performance penalties of carrying excess weight (ironically including reduced fuel economy).
Balancing all of these issues is a tremendous concern for pilots and aircraft operators. Safety must be first, but pilots who routinely carry too much fuel cost the company money. True turbine pros develop the planning skills to operate with no more than prudent fuel reserves.