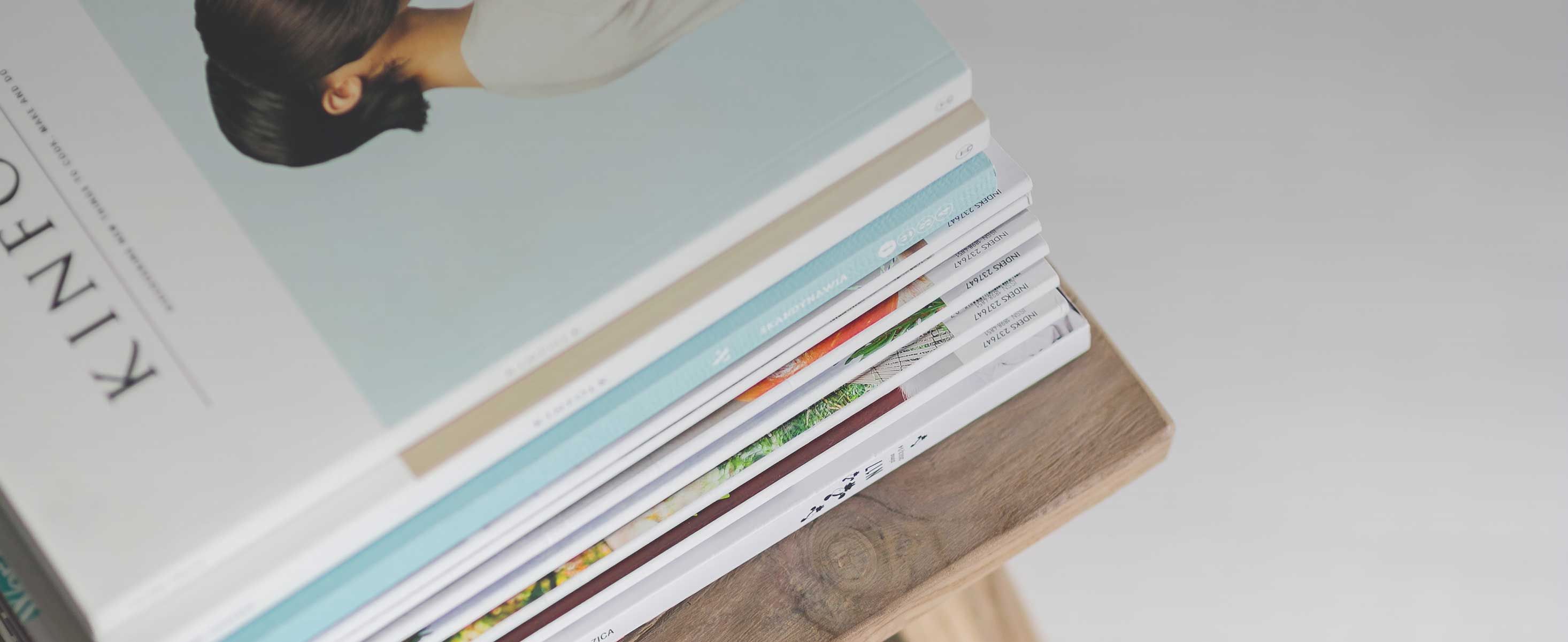
13 minute read
Landing Gear Systems
had problems with ice formation on upper wing surfaces, even at above-freezing temperatures, due to the presence of cold fuel in the wet wings. (“Wet wings” refers to integral wing fuel tanks. See “Fuel Systems” in Chapter 5.) Fuel lines were rerouted in that design to address the problem, and electrically heated thermal panels were developed for ground heating of its upper wing surfaces.
Rain Protection
In addition to icing liabilities, turbine engines are also vulnerable to flameout (engine failure due to smothered combustion) if large amounts of water are ingested in flight. In precipitation this problem is addressed by selecting “igniters on” and in some cases operating at higher power settings.
Many turbine aircraft also have windshield rain protection systems, for purposes of preserving visibility on takeoff and landing. Along with heavyduty windshield wipers, many larger jets use rain repellent chemicals, which may be released onto the windshield from the cockpit. Rain repellent chemicals reduce adherence of water to the windshield by changing its viscosity and slipperiness. The result is reduced formation of water droplets on the windshield and, therefore, enhanced visibility. Neither wipers nor rain repellent fluid should ever be used on a dry windshield!
Automatic Ice Protection Systems
Newer aircraft designs incorporate fully automatic systems for ice protection. These systems use ice detectors to identify icing conditions and when appropriate, automatically alert engine bleed-air management controllers to activate wing and enginecowl anti-ice systems. These systems will continue to operate automatically until the ice detectors no longer detect any icing. Amazingly, most systems will also recognize engine-out situations or other relevant system failures, and configure all valves appropriately to ensure sufficient heat for anti-icing. Traditional manual deice and anti-icing systems require a good deal of pilot attention for proper operation, so these new automated systems greatly reduce cockpit workload.
Landing Gear Systems
While there are a few fixed gear models around (such as the DHC-6 Twin Otter and the singleengine Cessna Caravan), retractable landing gear is found on most turbine aircraft. Some older airplanes used electrically powered, gear-driven landing gear retraction systems. These proved to be heavy and electrically demanding, with high maintenance requirements due to the large forces required to extend and retract landing gear. Hydraulic power has proven to be ideal for this purpose and is found on virtually all of today’s retractable landing gear systems.
Light turbine aircraft, such as the smaller King Airs, often use the same types of electrically powered hydraulic power packs found in general aviation piston aircraft. On these systems, an electric motor drives a dedicated hydraulic pump, based on pilot selection of the gear handle. Hydraulic lines transmit the generated hydraulic pressure to power landing gear operation.
Most large aircraft have generalized, multipurpose hydraulic systems, of which one major duty is powering landing gear operation. Gear doors on these systems are usually also hydraulically powered through the use of piston-type hydraulic actuators. Door operation may be separately controlled or may be made part of the gear retraction cycle through the use of hydraulic sequencing valves in the landing gear hydraulic circuit. On some aircraft, gear doors are linked mechanically to landing gear operation, using some combination of pushrods, cables, or pins.
All aircraft having retractable gear are required to have pilot warning systems in order to reduce the likelihood of unintentional gear-up landings. In most cases, gear warning horns are designed to sound when the landing gear is retracted, and some combination of flap position, low power setting, and perhaps airspeed suggests imminent landing. You’ll be required to memorize the gear warning conditions for aircraft you fly.
Other safety features are built into landing gear systems to confirm proper position and operation of the gear. Sensors known as landing gear position switches are located at every landing gear strut to confirm gear position as up and locked or down and locked, as appropriate. These are usually
mechanically actuated electric switches, all tied to a central warning system that monitors and compares gear positions. Cockpit warnings are triggered if any gear position doesn’t match that selected by the pilots.
Landing Gear Squat Switch
One particularly noteworthy type of landing gear position switch is known as a landing gear squat switch (sometimes called a “weight-on-wheels switch” or “landing gear safety switch”). These electric switches are mechanically actuated by the weight of the airplane compressing the gear struts, thereby positively indicating whether or not the plane is on the ground.
Why does the squat switch rate its own section? These switches are very important. First of all, landing gear safety systems use squat switch position to prevent inadvertent gear retraction on the ground. If the gear struts are compressed, the system will not allow gear retraction, regardless of gear selector handle position in the cockpit.
This alone would be a valuable safety feature, but the lowly squat switch sends its simple message, “The airplane is…” or “The airplane is not on the ground,” to all sorts of interesting places.
As with the gear selector, many aircraft systems have built-in safeguards to prevent accidental activation at times when it could be dangerous. These automatic safeguards prevent selected systems from working unless certain conditions are met. We’ve noted that if the squat switch says the plane is on the ground the landing gear will not retract. This information is also valuable for safe operation of many other systems.
Ground spoilers, for example, should never be activated in the air; their effects in flight could be fatal. One condition for their deployment, on many aircraft, is an on-the-ground message from the squat switch. The engine thrust reversers of some aircraft are tied to the squat switch for the same reason; reverser actuation aloft would be (and has been) disastrous for certain aircraft.
On many airplanes, the cabin pressurization dump valve is activated by the squat switch when the airplane touches down, thereby depressurizing the plane upon landing. Pressurization begins again after takeoff, based on switch position. In other vehicles, the switch signals the system to change pressurization criteria to meet differing flight or ground parameters.
The APUs of some aircraft are not certified for operation in the air. The squat switch turns them off upon takeoff if shutoff is missed in the cockpit. Bleed-powered wing anti-ice systems, on the other hand, generally cannot be used on the ground. Guess what closes the wing leading edge anti-ice valves at touchdown if the pilots forget?
In ground school, you’ll have to learn all of the squat switch tie-ins for the aircraft you fly. This is important for many reasons, not the least of which is understanding what else doesn’t work if the squat switch fails in one position or the other. You’ll want to check all visible landing gear switches during preflight inspection, but pay extra close attention to the landing gear squat switch(es) tied in to all those safety systems.
Brakes
On light airplanes brakes are conceptually very simple. A pilot presses the toe pedals, moving pistons in the brake master cylinders. The pistons push hydraulic fluid through hydraulic lines to slave cylinders out at the wheels. Pistons in the slave cylinders convert hydraulic pressure back to mechanical movement, which squeezes brake caliper pads against brake disks (“rotors”) mounted on the wheels, slowing the airplane. These systems are found on light turbine, as well as light piston aircraft.
Even something as conceptually simple as brakes becomes complex, however, when the object is to stop several hundred thousand pounds of airplane. Brake mass and contact area have to be very large in order to stop a jet airliner in a reasonable distance. For the “heavies,” this requires multidisk rotor-andstator brakes mounted on many wheels. Power assist is required to multiply the strength of the pilots in doing the job.
In addition, the energy of the airplane’s rolling mass is converted to heat (and lots of it) as the vehicle is brought to a halt. All that heat causes some interesting problems that must be addressed by large aircraft braking systems and operating procedures. First of all, as the brakes heat up during rollout, brake effectiveness decreases. This phenomenon is known as brake fade.
With this in mind, brake systems on large aircraft are designed to deliver at least one maximum effort stop from landing speed or V1 without overheating. (This assumes that thrust reversers are not used.) If a second use of the brakes is required any time soon afterward, overheating is a distinct possibility, resulting in reduced brake performance. In fact, it is entirely possible to overheat the brakes to the point of blowing out the tires or even causing a fire. (Many aircraft have fire extinguisher systems installed in their wheel wells to suppress fires resulting from hot brakes and other causes.)
What does this mean to the pilots? On an aborted takeoff, for example, the nonflying pilot notes airspeed when braking is initiated. Once the airplane has slowed, he or she refers to a brake cooling chart to determine when braking may be safely used again. The answer could very well mean a takeoff delay, but you wouldn’t want less than optimum braking available in the event of another aborted takeoff. In some cases, it may not even be allowable to taxi the airplane off the runway until some period of cooling has taken place.
Larger aircraft are required to have wheel thermal plugs installed on any wheel associated with a brake system. Thermal plugs, also known as fuse plugs, are hollow bolts installed in the wheel rim to protect against tire explosion during a brake overheat. The bolt or thermal plug is filled with a material that melts at a preset temperature and is then ejected from the bolt by tire pressure, allowing the tire to controllably deflate and thereby prevent a potentially catastrophic tire explosion.
Brake Antiskid and Anti-Ice Systems
Obviously, it’s no fun to slide around on a wet or icy runway in a fast airplane. To prevent this from happening, brake antiskid systems are installed on many turbine-powered aircraft. Brake antiskid systems use computer-controlled hydraulics to maximize braking effectiveness under such conditions. Use of antiskid by the pilots is straightforward: apply steady maximum braking at the pedals. The system works by monitoring rotational speed of each wheel and comparing it with the expected value based on a dry runway. If actual wheel speed is less than 85 percent or so of normal, braking is momentarily released to let the wheel speed up. By pulsing the brakes in this manner, antiskid systems maintain the best wheel speed for optimum braking.
A few aircraft models are also available with brake anti-ice systems, which use bleed air heat to prevent the brakes from icing up. This kind of problem can occur when runway slush sticks to cold landing gear and brake surfaces. It’s also a problem when the aircraft takes off from a wet or slushy runway, then climbs to below-freezing temperatures at altitude. By landing time, everything can be pretty well frozen if brake heat is not available.
Automatic Brake System
Automatic braking systems are installed in some aircraft to deliver a preselected rate of deceleration during landing rollout. Various levels of deceleration can be selected by the flight crew prior to landing (e.g., minimum, medium, maximum). Typically, automatic brakes are designed to apply brake pressure when thrust levers are retarded to idle position and the main landing gear antiskid system computer has sensed wheel spin-up. The automatic brake system will then bring the aircraft to a complete stop, unless the pilot either selects the system to off with the automatic brake switch or applies brake pressure manually, which disables the auto brake operation.
Automatic brake systems offer another important safety function on departure—immediate, maximum braking in the event of an aborted takeoff. For this purpose, the automatic brakes are generally selected prior to takeoff. The aborted takeoff mode is then armed by some combination of throttle position and main landing gear wheel speed on the takeoff roll (for example, wheel speed greater than 80 knots and throttles advanced past 50 percent of their travel). Once the system is armed and takeoff roll initiated, maximum braking will be applied if the throttles are retarded to idle. The amount of braking force corresponds to the pilot applying maximum manual braking (Figure 6.6).
Nosewheel Steering
If you’ve been flying light aircraft much, you’re used to the concept that ground steering is mechanically controlled by the rudder pedals. However, on more sophisticated aircraft, hydraulic nosewheel steering systems are normally used for a variety of reasons. First of all, the distances and forces involved make
it impractical to run mechanical linkages all the way from the rudder pedals down to the retractable nose gear on a jetliner. Then there’s the fact that steering sensitivity needs to be different for parking than for rolling down the runway at 120 knots.
Hydraulic steering systems suit these purposes well. Hydraulic power lines, as you remember, are easy to route, and systems can be designed to offer two or more steering sensitivities for different circumstances. The optional hydraulic nosewheel steering on the Beech 1900, for example, offers “taxi” and “parking” modes for ground maneuvering. Once that aircraft is lined up on the runway, nosewheel power steering is selected “off,” and differential braking is used to assist in steering the castering nosewheel before rudder effectiveness is achieved. Other vehicles provide power steering over a broad range for ground maneuvering (± almost 90° in the case of Boeings), with limited rudder pedal steering (±10°) through the takeoff roll.
Another point is worth noting to save you embarrassment on your first flight as copilot on an aircraft with hydraulic steering. Ground maneuvering, with most powered nosewheel steering systems, is done exclusively by the captain. Somewhere around his or her left knee is a steering wheel or tiller with which the deed is done. On your flying legs, the captain will taxi the plane to and onto the runway. Once the plane’s lined up and ready to go, the captain will inform you that “it’s your aircraft.” After landing, as the plane slows, the captain again takes control of the plane for the journey back to the gate. Ah, the privileges of command!
Abort Takeoff
Off
Maximum
Medium Minimum
Automatic Brake System
Antiskid System
OFF ON
Tailskid
In order to accommodate more passengers, many aircraft manufacturers offer model variants with stretched fuselages adding an additional 10–40 feet of length to the aircraft. Unfortunately, as the length of a given aircraft fuselage is increased, there’s a reduction in tail clearance during take-off and landing attitudes. In order to avoid structural damage caused by the rear end of an aircraft striking the runway, a tailskid is mounted on the bottom of the aft end of an aircraft’s fuselage. Of course, tailskids go way back in aircraft design, but the modern ones on larger aircraft can be surprisingly sophisticated. Modern tailskids are designed as shock absorbers to prevent costly damage to the aircraft during a tail strike. They typically extend and retract in conjunction with the landing gear, and some even deliver a flight-crew alerting message to the cockpit if the tailskid contacts the runway. All tailskid systems have visual cues designed to reveal strikes during a pre- or post-flight “walk-around”. Some operators paint the bottoms of their tail skids yellow in order to better help flight crews identify scrapes from contacting the runway. Other tailskids have an indicator pin that extends when the skid has been compressed by contact with the runway. This pop-up pin indicator may also be painted red or yellow to help flight crews identify an aircraft that has suffered a tail strike. Anytime you spot an extended pop-up pin or scraped paint on an aircraft tailskid, it’s important to give maintenance a call to rule out any hidden structural damage.
FIGURE 6.6 | Automatic brake.