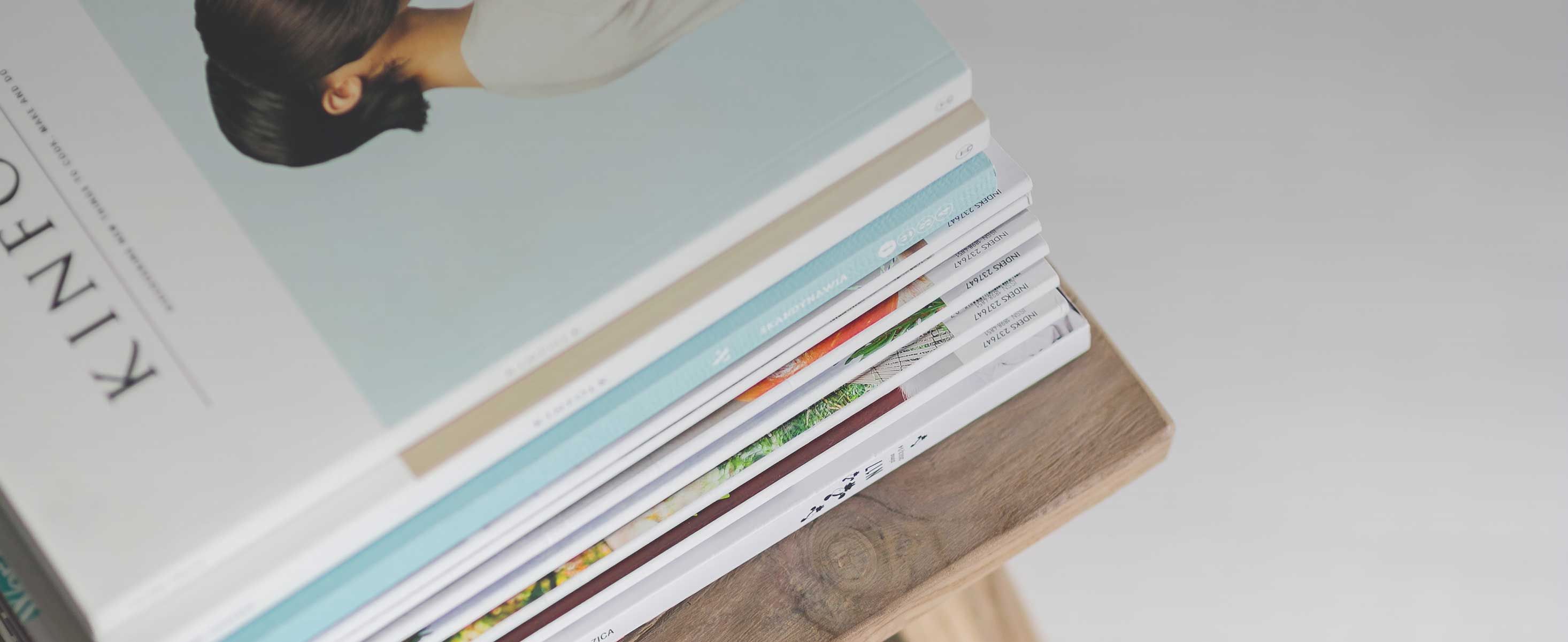
8 minute read
Thrust Reversers
Items to Monitor During Engine Start
Whether your particular engine-start sequence is handled automatically or manually, there are some important items to monitor during the starting process itself.
Once you select “engine start” and monitor engine speed as rotation begins via the starter, check for some oil pressure indication prior to initiating fuel flow. (The exact oil psi varies by manufacturer.) If no oil pressure, or low oil pressure is indicated during initial engine cranking, the start sequence must be aborted.
Also, monitor for EGT rise within a reasonable amount of time after initiating fuel flow, typically 20 seconds. If ignition or “light-off” does not occur within this timeframe, something is amiss and fuel flow to the engine should be discontinued.
Prior to start, be sure you are familiar with the normal engine indications before, during and after the engine start sequence. Abnormal fuel flow, temperature, engine RPM or oil pressure indications could require an immediate abort of the engine start.
Turbine Engine Characteristics in Flight
Turbine engines are not particularly sensitive to power changes in the air (especially as compared with turbocharged reciprocating engines) and therefore are extremely easy to manage in flight. While maximum EGT or ITT has to be monitored under certain conditions, you can readily and abruptly change thrust or power in turbine aircraft (say, from cruise to idle) with no adverse effects. Additionally, since the fuel control unit is directly controlled via the power or thrust levers, no “leaning” or “mixture” control of any kind is required.
Power management of turbine engines in flight does vary from that of piston aircraft in several important ways. First, turbine engines take time to spool up when power is applied. If left at low power, engine compressor speed is slow. The term spool up refers to the time it takes, after power application, for thrust to increase from idle to the selected values. Most of a turbine engine’s thrust is developed in the top 10 percent or so of the engine RPM (N1) range.
Let’s say that a jet is coasting along at flight idle (60 percent to 65 percent N1) when the pilot calls for max thrust. It can take quite a while for the engines to spool up to the 90 percent N1 range, where most thrust is generated. While adding full throttle in a piston aircraft may result in maximum power within a few seconds, turboprops take a bit longer, and maximum thrust in jet aircraft may not result until five to ten seconds after power application.
For these reasons, being low and unspooled in turbine aircraft on approach to landing is absolutely unacceptable, due to the time it takes for the engines to spool up for go-around. (On at least one old foreign military turbojet, spool up time from idle to full power takes twelve seconds. Modern jet engines are required to spool up in five seconds or less.)
Because response to thrust changes can be so slow in pure jet aircraft, power management in these vehicles requires plenty of planning. For example, on final approach in jets all of those high-lift, high-drag devices (flaps and leading edge devices) are extended to slow the aircraft enough so that relatively high thrust must be carried all the way to landing. This aids in go-around situations because, since thrust is already high, spool up time is minimized. Cleaning up the airplane turns out to be faster than waiting for spool up, especially on older turbojet aircraft.
Another challenge arises in jets (less so in turboprops) because turbine engines offer relatively little drag when thrust is reduced to flight idle. While the drag of propeller discs will quickly slow a prop aircraft with engines at idle, pure jets tend to just coast. (Glide ratios can exceed 20:1 in modern jetliners.)
That means thrust management to meet descent restrictions in jets can also be challenging, due to the low-drag characteristics of such aircraft. For example, it’s difficult in many jets to maintain the 250knot speed limit below 10,000 feet and to descend at the same time more than 1,500 or so fpm. This means that jet pilots must plan ahead on descents and in some cases negotiate with ATC. (“We can hold our airspeed to 280 knots or make our 13,000 altitude crossing restriction, but not both.”)
Thrust Reversers
For purposes of both safety and airport size, it’s important to stop landing aircraft in the shortest distances possible. Therefore, many turbine-powered aircraft are equipped with thrust reversers to enhance deceleration upon landing. Typically, a
little less than 50 percent of an engine’s rated takeoff thrust is available in reverse thrust.
Thrust reversers don’t impact minimum landing distance as much as you might think. A given aircraft might land and stop in 4,000 feet with reversers versus 4,500 feet without. In any case, manufacturers are not allowed to incorporate the effects of thrust reversers when calculating aircraft runway length performance. (One reason is that the aircraft must be able to stop within the specified distance in the event of a failed engine, when little or no reverse thrust may be available.)
So why install thrust reversers? They offer a number of valuable benefits. First, it turns out that calculated minimum landing distance for a given aircraft is based on maximum braking. No one ever lands that way, except under extreme conditions. Therefore, the effects of reversers for shortening routine landings are significant.
Thrust reversers also tremendously reduce the energy absorbed by an aircraft’s brakes. Severe brake damage or even brake fires can result from a maximum energy rejected takeoff (RTO); thrust reversers reduce that likelihood by taking some of the load off the brakes. Brake and tire wear under routine use is also reduced through use of thrust reversers, thereby lengthening brake and tire life. Proper use of reversers also keeps brakes cool early in the touchdown roll, reducing brake fade and thereby improving brake performance on rollout.
Reversers also improve safety by increasing runway length margins and by imparting an extra measure of control on wet, snow-covered, or icy runways. Under normal runway conditions around 50 percent of an aircraft’s stopping power comes from thrust reversers. But under poor runway conditions, such as on wet or icy surfaces, thrust reversers may provide close to 80 percent of the aircraft’s stopping power.
Some operators also use thrust reversers to power back aircraft from terminal gates, although backing an aircraft under its own power is done only under strictly controlled and approved procedures.
The operating principle of a thrust reverser is simple: engine power is directed forward to slow the aircraft.
Thrust Reversers on Jets
On jets, engine thrust is mechanically directed forward to help bring the aircraft to a stop. Three types of thrust reversers are in common use on jet aircraft: clamshell, cascade-type, and petal door fan reversers. (Within these general types are numerous variations.) The equipment found on any given airplane varies by aircraft model and by installed engine type.
Clamshell reversers are simply metal doors that swing rapidly from the rear of the engine nacelle into the exhaust stream, vectoring thrust forward to slow the aircraft. Aircraft having engines with little or no bypass use this type of reverser, which is simple, effective, and relatively easy to install. Used on most corporate business jets and small to midsized airliners, clamshell reversers may be seen on Citations, Learjets, B717s, MD-80s, and EMB-145s, to name a few (Figure 3.18).
Cascade-type reversers are used on aircraft with high-bypass engines. This type of reverser utilizes metal doors to block bypass air, while a thrust reverser nacelle collar slides back to expose cascade vanes that vector thrust forward. While slightly less effective than clamshell reversers, cascade types do not protrude from the nacelles when activated; this reduces ground clearance problems on large underwing-mounted engines. Cascade-type reversers may be seen on 757s, 767s, and 737-300s and -500s (Figure 3.18).
Petal door reversers are also used on high-bypass engines. They operate in much the same manner as the cascade type, except that pivoting metal doors are used to vector the thrust forward out of the engine nacelle. Petal door reversers may be found on some older 747s.
On jets, thrust reverser cockpit controls are normally installed as secondary, piggyback levers on the thrust levers. These controls are designed to prevent selection of reverse until forward thrust has been reduced to idle. After touchdown, the thrust levers are first pulled aft to “idle”; then the reverse levers are pulled up and aft. Reverse thrust, from reverse idle up to maximum thrust with reversers deployed, is controlled exclusively by the reverse levers. (See Figure 3.15.) As the reverse levers move aft, engine thrust is increased in the reverse thrust configuration.
Once you get to ground school you’ll learn how your specific aircraft engines’ thrust reversers are actuated. How the thrust reverser is physically moved varies by engine manufacturer. Thrust reverser actuation may be pneumatically powered by bleed air drawn from the engine compressor, powered by the aircraft’s hydraulic system, or on newer aircraft, deployed by electric-motor actuators (much lighter). Be familiar with your particular thrust reverser system, as a failure in the relevant power-supplying system might affect the availability of thrust reversers on landing.
Reverse Thrust on Turboprops
On turboprops, reverse thrust is accomplished in a relatively simple manner. After touchdown, pilots select reverse thrust by lifting the power levers past a “gate” or detent aft of “idle.” (See Figure 3.16.) As the power levers are moved aft, propeller blade angle is gradually changed from positive (flight range) blade angles to negative (reverse range) blade angles. The effect is to first increase drag by “flattening” the propeller blades, then to direct engine thrust forward through negative propeller blade angles of attack. As the power levers move aft in the reverse range, propeller blades are moved to fixed mechanical stops
turbojet deploying clamshell reversers
turbofan deploying cascade reversers (shown diverting bypass air only)
FIGURE 3.18 | Two types of jet thrust reversers.