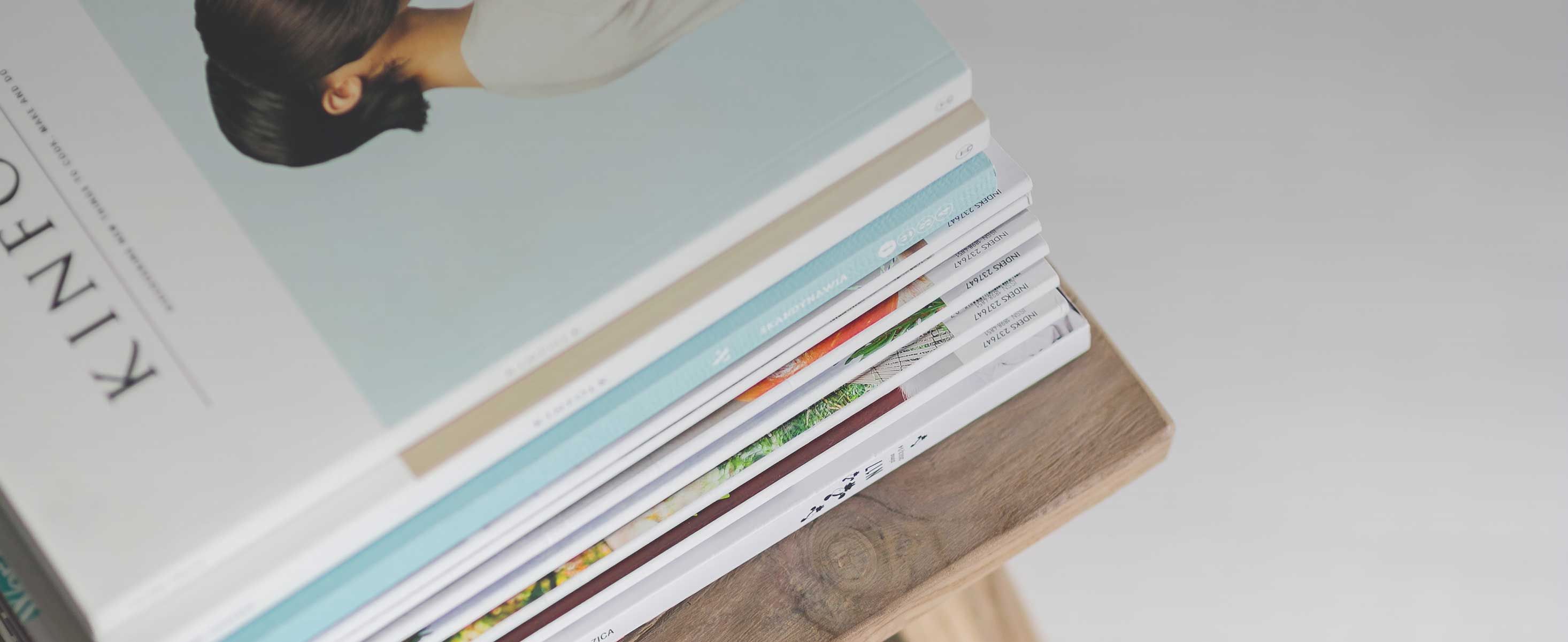
7 minute read
Pneumatic Power Systems
cockpit controls and flight control surfaces. In case of complete hydraulic system failure, the RAT then supplies necessary hydraulic pressure to actuate the flight controls. In order to produce the required hydraulic pressure to do this, the aircraft must be flown at a high enough airspeed to generate sufficient air pressure to turn the air turbine. (For example, the Boeing 767 requires a minimum airspeed of 130 KIAS be maintained when using the RAT.) RATs are typically installed in the underside of the aircraft fuselage, where they can be easily extended by gravity alone. RATs may be extended manually or automatically depending on the installation (Figure 4.23).
Hydraulic System Characteristics
One interesting characteristic of hydraulic systems is that most of the work is done with relatively little movement. Continuous-operation systems are kept constantly pressurized by hydraulic pumps, but fluid movement occurs only when something hydraulic is operating. Even then, fluid flow is minimal when small actuators and cylinders are being powered. In these cases, the work is done more by pressure than by flow. Compare a hydraulic system to a flexible rod being pushed through a tube—small movement at the driving end of the system is transferred hydraulically to push a faraway button, to move a valve, or to deflect a control surface.
Since hydraulic pressure is kept bottled up between the pump and devices it powers, hydraulic return lines generally carry little pressure or flow back to the reservoir. Exceptions occur when rotary hydraulic motors are powered to operate high-load devices such as landing gear and flaps. Then, both hydraulic flow and pressure are significant.
Pneumatic Power Systems
Pneumatics provide yet another method for transmitting engine power to various aircraft systems. In this case, the medium for power transmission is compressed air. Since air, being a gas, is compressible, pneumatic power is far less efficient than hydraulic power for heavy-duty jobs. On the other hand, pneumatic systems are much lighter than hydraulic systems, need little maintenance, and require no special fluids.
On piston airplanes, pneumatic power comes from pressure or vacuum pumps driven mechanically off the engines. These systems are basically pretty simple. Rotary pneumatic pumps correspond to the pump in our reference water power system. The ready source of atmospheric air eliminates the need for any type of reservoir, and control is relatively simple through a series of valves. Pneumatic systems in piston aircraft typically operate gyro instruments, pressurization, and deicing boots.
Turbine-powered aircraft use pneumatic systems for the same types of applications, plus many more. The reason is that turbine engines are essentially giant pneumatic pumps. As you remember, the engine’s gas generator compresses huge amounts of air to support combustion. It’s a relatively simple matter to draw this “bleed” air from the engines and use it to power all sorts of things (see Figure 4.24).
High-pressure bleed air is drawn from the compressor section of a gas turbine engine. Some systems draw bleed air from two or more “stations” on each engine, yielding different pressure and temperature outputs. (These differing bleeds are sometimes identified as “high-pressure bleed air” and “low-pressure bleed air.” In this book, the terms “high-pressure bleed air” and “bleed air” are used interchangeably to refer to all such variations.)
High-Pressure Bleed Air
High-pressure bleed air has many applications straight out of the engine, including engine and wing thermal anti-ice. It is also used, via some combination of air cycle machines (ACMs, or Packs) and heat exchangers, for cabin pressurization, heating, and cooling. (See “Pressurization” and “Environmental Systems” in Chapter 5.)
On large turbine aircraft, high-pressure bleed air also powers the engine starters. Large engines such as the CFM 56 are started pneumatically, as an alternative to the heavy electrical loads and motors required for electrical starting of turbine engines.
Typically for engine starting, the aircraft APU is started electrically to provide bleed pneumatic power, or else a ground pneumatic power source is used. When the captain calls for starting, a start valve is opened, sending compressed air to spin up a small turbine in the pneumatic starter. This, in turn, spins up the engine core compressor. Fuel is
introduced, and when N2 (high-pressure compressor RPM) reaches a predetermined value, the start valve is closed, and the starter turbine is disengaged from the engine’s compressor.
Low-Pressure Air
Some high-pressure bleed air is metered through a pressure regulator to much lower pressures, normally around 18 psi. This low-pressure air (sometimes called instrument air) corresponds, in pressure and in applications, to the piston airplane pneumatic (vacuum) systems you may be familiar with. As such, low-pressure air in turbine aircraft drives air gyros and pneumatic deicing systems, if installed. Lowpressure air may also be used for mechanical control functions such as valve actuation (pneumatic and/or hydraulic), control of pressurization outflow valves, and inflation of door seals to sustain pressurization (Figure 4.25).
Bleed Hazards and Protections
Since high-pressure bleed air is drawn directly from the engines, bleed usage on many turbine aircraft must be managed by phase of flight. For example, use of bleed air impacts the power produced by the engine supplying it, since air and pressure are being bled away from the engine prior to the combustion chamber. Therefore, in most turbine aircraft, highpressure bleed air use is restricted during takeoff and go-around situations. Low-pressure air remains operative on takeoff to power flight instruments, but other bleed-powered items may be turned off for departure, which are then reactivated as part of the after-takeoff checklist, if appropriate.
Sometimes weather conditions at takeoff do require use of high-draw bleed items, such as engine inlet anti-ice systems. For these situations, most turbine aircraft have correction factors in their takeoff power and performance charts, often restricting takeoff weights and/or speeds.
Use of bleed air for thermal wing anti-ice is virtually never permitted for takeoff. Not only do the bleeds sap lots of engine power, but on the ground, the 600°–800°F bleed temperatures can weaken the aluminum wing leading edges. (See “Ice and Rain Protection” in Chapter 6.)
Bleed pneumatic systems do have some other hazards associated with them. Due to the very high temperatures involved, fire can result from unattended bleed air leaks within the aircraft. Therefore, bleed systems are normally monitored in the
P2.5 air (175°C)
BLEED AIR
P3.0 air (390°C) “P” pressure stations are defined by the engine’s manufacturer and increase in order from front to back of the engine.
Bleed air is drawn from one or more points in a turbine engine’s compressor section. Pressure and temperature vary, based upon location from which the air is drawn.
cockpit. Temperature probes are often used to monitor passages carrying bleed air lines. Other systems run pressurized EVA (ethylvinylacetate) tubing along bleed lines. This material melts and signals a sensor when a leak occurs. In the event of a hightemperature leak, the associated bleed source must be shut off, followed by execution of the appropriate “abnormal” checklist. Some larger aircraft also have fire extinguishing capability for engine bleed lines in critical areas. (See also “Fire Protection Systems” in Chapter 6.)
Pneumatic engine starting systems offer some interesting hazards of their own. Pneumatic system pressure must be monitored throughout the start cycle (described earlier) because, if the start valve fails to close as the engine starts, bleed pressure from the now operating engine can blow back through the starter at high pressure. There have been several cases where a sticking start valve caused the pneumatic starter to be literally blown off the airplane, through the engine cowl, and quite some distance from the aircraft. Therefore, engine start must be aborted immediately if the start valve fails to close when it should.
Like other aircraft systems, pneumatic systems have multiple power sources and protective devices to minimize the effects of system failures. Redundancy is accomplished through use of bleed sources from all engines and sometimes from the auxiliary power unit (APU), when installed.
Check valves, like the ones in our reference water system, are used to restrict pneumatic flow in certain areas to one direction. Isolation valves (automatic or manual) allow separation of interconnected bleed systems in the event of leaks or other failures. Normally, if one bleed is shut off at its source, most systems can be operated on the remaining bleed air source(s), except under very high-draw situations. However, if a serious leak occurs somewhere in the pneumatic system, requiring use of an isolation
pneumatic starter pneumatic deicing boots
INSTRUMENT/ GYRO AIR
inflatable door seals
bleed air for engine inlet anti-ice
bleed air valve boot timer/ controller
high-pressure bleed air is drawn from engine compressor section
18 psi pressure regulator
highpressure regulator pressure regulator “steps down” high-pressure bleed air to low-pressure air
engine start valve
VACUUM TO CONTROL PRESSURIZATION OUTFLOW VALVES
isolation valve
LOW-PRESS. AIR FR. OTHER ENGINE
BLEED AIR FROM OTHER ENGINE
APU BLEED AIR
TO PNEUMATIC ENGINE STARTER
high-pressure bleed air low-pressure air (18 psi) cooled high-pressure air empty pneumatic line vacuum
GROUND SOURCE HIGH-PRESS. AIR
TO THERMAL WING ANTI-ICE thermal wing anti-ice valve 1st stage heat exchanger
PRESSURIZATION AIR, TO ENVIRONMENTAL “PACK”
FIGURE 4.25 | Pneumatic system components.