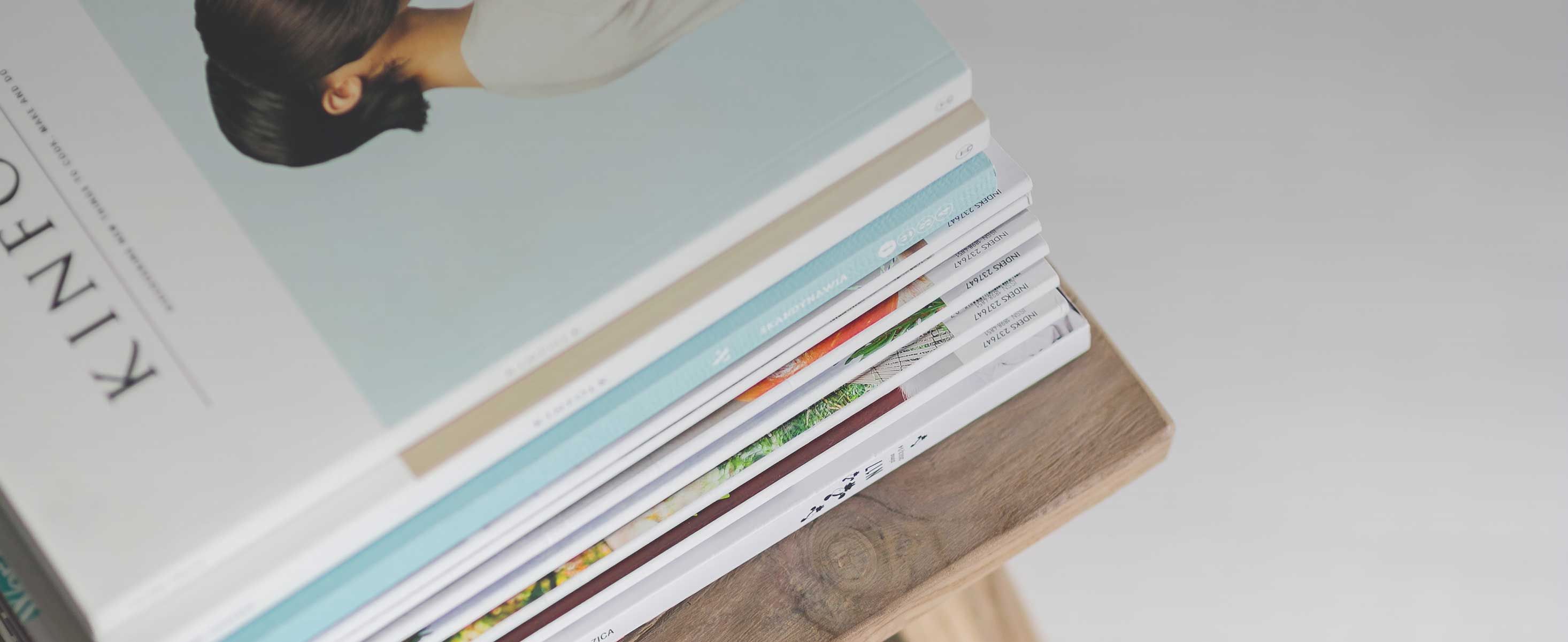
9 minute read
Propeller Supplement for Transitioning Military Jet Pilots
There are several types of propeller synchronizing systems, but they fall into two basic categories: the propeller synchronizer, which matches propeller RPM between multiple engines, and the propeller synchrophaser, which in addition to matching propeller RPM also matches propeller blade positions between engines for maximum noise reduction.
The “brains” of a propeller synchronizer or synchrophaser system is the control unit. The control unit compares electronic signals generated from two different magnetic “pick-ups,” one mounted on a stationary location, such as the propeller gear box assembly, and one mounted on the rotating propeller hub backplate.
To control prop RPM, the prop synch control unit signals magnetic synchronization coils mounted on the propeller governor flyweights, thereby magnetically controlling them for precise positioning. In this way, whenever RPM or phase corrections are required, the governor is guided to adjust propeller RPM in a normal manner, by increasing prop blade angle to reduce RPM or decreasing prop blade angle to increase RPM.
In-flight operation of prop synch systems is simply a matter of manually synchronizing the propellers within a predetermined RPM range and selecting prop synchro “ON.” The control unit will then match prop RPMs between engines, greatly reducing propeller noise levels.
Some prop synch systems require the pilot to manually synchronize the propellers to within a few RPMs of each other and then manually select propeller blade phase to the quietest blade position. Other units automatically adjust blade phase position to a predetermined setting that is identified as the quietest during flight testing (see Figure 3.23).
Whether in fighters, bombers, or tanker/transport aircraft, most recent military pilots have spent their careers piloting pure jet aircraft. Therefore, if that’s your background basic propeller theory is probably not familiar to you. Like it or not, there is still a possibility that your first civilian flying job will be in a turboprop aircraft.
Familiarity with basic propeller characteristics is important, especially in engine-out operations, because these characteristics affect both handling and performance of the aircraft. For this reason, we review some basic propeller theory for those who
primary propeller governor primary propeller governor
prop synch control unit
Propeller synchronizer/synchrophaser systems reduce pilot workload, noise and “prop beat” by matching propeller speed and/or position. Prop synchronizers compare rpm of each propeller, then automatically adjust one primary propeller governor to match the other. Propeller synchrophasers additionally compare and adjust relative propeller positions to further minimize noise.
FIGURE 3.23 | Propeller synch on multiengine aircraft.
need it. Pilots should be familiar with these concepts, along with principles of turboprop propeller systems (already discussed; see the preceding), before entering ground school for a turboprop aircraft.
The good news is that propeller systems, although somewhat complex mechanically, are relatively easy to use. To prepare for turboprop training, pilots with only jet experience would benefit by taking even an hour of instruction in any aircraft having a constantspeed propeller. (It need not be a turboprop; piston prop systems are operated in a similar manner.)
Propeller Terminology
Propeller Pitch
Propeller pitch refers to the blade angle of a propeller relative to its plane of rotation. High, steep, or coarse pitch refers to a large blade angle. Low, flat, or fine pitch refers to a small blade angle. Flatter pitch is used for takeoff and climb, where acceleration and climb performance are improved by higher RPM and faster acceleration of air passing through the propeller. Steeper pitch is more efficient for cruise flight, where a larger blade angle results in a bigger “propeller bite” and, therefore, power transfer to a larger volume of air at a lower RPM. Reverse pitch refers to negative blade angles, meaning those that direct thrust forward to slow the plane in reverse range (see Figure 3.24).
The constant-speed propellers found on turboprops are variable in pitch to provide the performance and efficiency benefits of both high- and low-pitch propellers. Propeller RPM is set by the pilots and then kept at constant RPM by a propeller governor. The governor varies blade angle, which in turn impacts rotational drag of the propeller to keep RPM constant. When RPM increases above the value for which a governor is set, the governor turns the propeller blades to a higher angle, thereby increasing load on the engine and reducing RPM. Conversely, when propeller RPM decreases below the value for which the governor is set, the governor decreases propeller blade angle, thereby decreasing propeller load on the engine and increasing RPM.
Windmilling prop refers to a propeller that is at flight pitch settings but is developing no power. In this configuration, the spinning propeller disk creates tremendous drag, often enough to prevent
Low, fine, or flat pitch refers to a small blade angle (high rpm, used for takeoff and climb). High, coarse, or steep pitch refers to a large blade angle (low rpm, used for cruise flight). Feathered prop refers to a blade angle near 90° to minimize propeller drag on an inoperative engine. Reverse pitch refers to negative blade angles (normal prop rotation delivers reverse thrust).
Propeller pitch refers to the angle between a propeller blade and its plane of rotation.
FIGURE 3.24 | Propeller pitch.
the airplane from sustaining altitude on the remaining engine(s). On some aircraft, it is also difficult or impossible to maintain directional control with a windmilling propeller. Propeller feathering addresses this problem by setting propeller blade angle on the failed engine close to 90°, thereby minimizing prop drag. A feathered prop is critical to sustained flight of most propeller-driven aircraft after an engine quits.
Asymmetric Propeller Thrust
An important characteristic to understand, regarding propeller-driven aircraft of all types, is that the thrust produced by any one powerplant propeller is not symmetrical. While a jet engine produces power directly along its axis, aircraft propellers generate forces in both lateral and rotational directions that affect handling. These forces can cause both roll and yaw tendencies. While most pronounced in singleengine aircraft, these effects also arise in twins, especially during takeoff, climb, and engine-out situations. (You fighter jockeys are going to learn to use the rudder in propeller-driven aircraft.)
P-Factor
P-factor (or asymmetric propeller thrust) is most noticeable at high angles of attack and high power settings. During flight at high angles of attack, the propeller’s plane of rotation is not perpendicular to the relative wind. This causes the descending blade
ascending blade has a small angle of attack descending blade has a large angle of attack
RELATIVE WIND
near blade far blade
Asymmetric thrust causes plane to yaw left.
Rudder is used to counteract yaw caused by P-factor and other prop characteristics.
At high aircraft angle of attack, such as during climbout, ascending and descending propeller blades have different angles of attack. The resulting asymmetric thrust must be counteracted with rudder.
FIGURE 3.25 | Propeller P-factor. (Figure and comments depict clockwise-rotating propeller installation, as viewed from behind.
of the propeller to have a greater angle of attack than the ascending blade and a higher relative velocity.
These combined effects give the descending blade significantly more thrust than the ascending blade, thereby offsetting the propeller’s center of thrust to the descending blade’s side of the propeller hub and causing a yawing moment on the aircraft, which pilots must counter through application of rudder during takeoff and climb (see Figure 3.25).
In cruise flight the propeller’s plane of rotation is nearly perpendicular to the relative wind and therefore thrust is almost symmetrical. On many aircraft, the engines and tail surfaces are installed asymmetrically in order to compensate for any offset propeller thrust in cruise, with the interesting result that rudder in the opposite direction is often required during descent to counter the effects of the asymmetrical configuration.
Torque Effect
We again refer to Newton’s third law: for every action there is an equal and opposite reaction. In the case of a propeller, this is called torque reaction, or torque effect. Simply put, torque effect refers to the tendency for an aircraft to rotate in a direction opposite the rotation of the propeller. (Helicopter pilots are particularly familiar with this effect.) Torque reaction is greatest at high propeller RPM and high power settings and is most noticeable upon rapid power changes.
Propeller Slipstream Effects
Accelerated propeller slipstream: Unlike the relatively clean airflow over surfaces of a pure jet, a propeller can affect the amount and velocity of air flowing over an aircraft’s wings and control surfaces. The propeller creates a large area of accelerated airflow over parts of the wing, creating more lift. Accelerated airflow can also increase rudder and elevator effectiveness. Since rapid power adjustments change accelerated airflow, they impact lift and control effectiveness. Therefore, it’s important on many propeller-driven aircraft to make smooth power adjustments at slow speeds and low altitudes, such as on short final.
Spiraling propeller slipstream: A rotating propeller imparts its rotation to the airflow it generates. If the propeller is rotating clockwise, for example, it creates rearward airflow rotating in the same
Accelerated propeller slipstream over wings and tail surfaces causes asymmetrical lift and control effectiveness.
Spiraling propeller slipstream results in asymmetrical rudder effectiveness.
FIGURE 3.26 | Propeller slipstream effects.
direction. In most aircraft this causes asymmetrical airflow to strike the vertical stabilizer and rudder, pushing the tail to one side (see Figure 3.26).
Critical Engine
Because of all these asymmetrical propeller properties, failure of one engine, on a given aircraft, may be more detrimental than loss of another. An airplane’s critical engine is the one whose failure would most adversely affect the performance and handling qualities of a given multiengine aircraft. In determining which engine is critical, the manufacturer considers all of the propeller effects previously discussed. (P-factor is generally considered to be the most influential propeller effect.) Engine-out performance and procedures for that aircraft are then developed based on the worst case failure of the critical engine (Figure 3.27).
Tractor versus Pusher Propellers
Tractor propellers are mounted on the airplane in such a way that their thrust pulls the aircraft forward. Tractor propellers are mounted in front of the engine nacelle with the propeller shaft facing forward. This type of propeller installation is most common because its location in front of the engine nacelle allows it to operate in relatively undisturbed air; therefore, it arguably has highest efficiency.
Pusher propellers are mounted behind the engine nacelle with the propeller shaft facing rearward so that their thrust pushes the aircraft forward instead of pulling it. Although historically pusher propellers have rarely been installed on landplanes, lately there has been renewed interest in using them on canard aircraft designs and for purposes of reducing cabin noise. Both Beechcraft and Piaggio have produced multiengine turboprops with rearmounted engines and pusher propellers, and several other pusher designs are on the drawing board.
thrust line farthest from aircraft’s axis
thrust lines equidistant from aircraft’s axis
On twin-engined aircraft with clockwise-rotating propellers (as viewed from behind) the left engine is the critical engine. Since the right engine’s thrust line is farthest from the aircraft’s longitudinal axis, failure of the left engine creates the strongest yawing tendency. On aircraft equipped with counter-rotating propellers, performance is affected equally by failure of either engine. Therefore such aircraft have no “critical engine.”
Due to P-factor and other propeller effects, failure of one engine often results in greater aircraft yawing tendency than failure of the other. The engine whose failure most adversely affects flight performance on a given aircraft is known as the “critical engine.”
FIGURE 3.27 | Critical engine on propeller-driven aircraft.