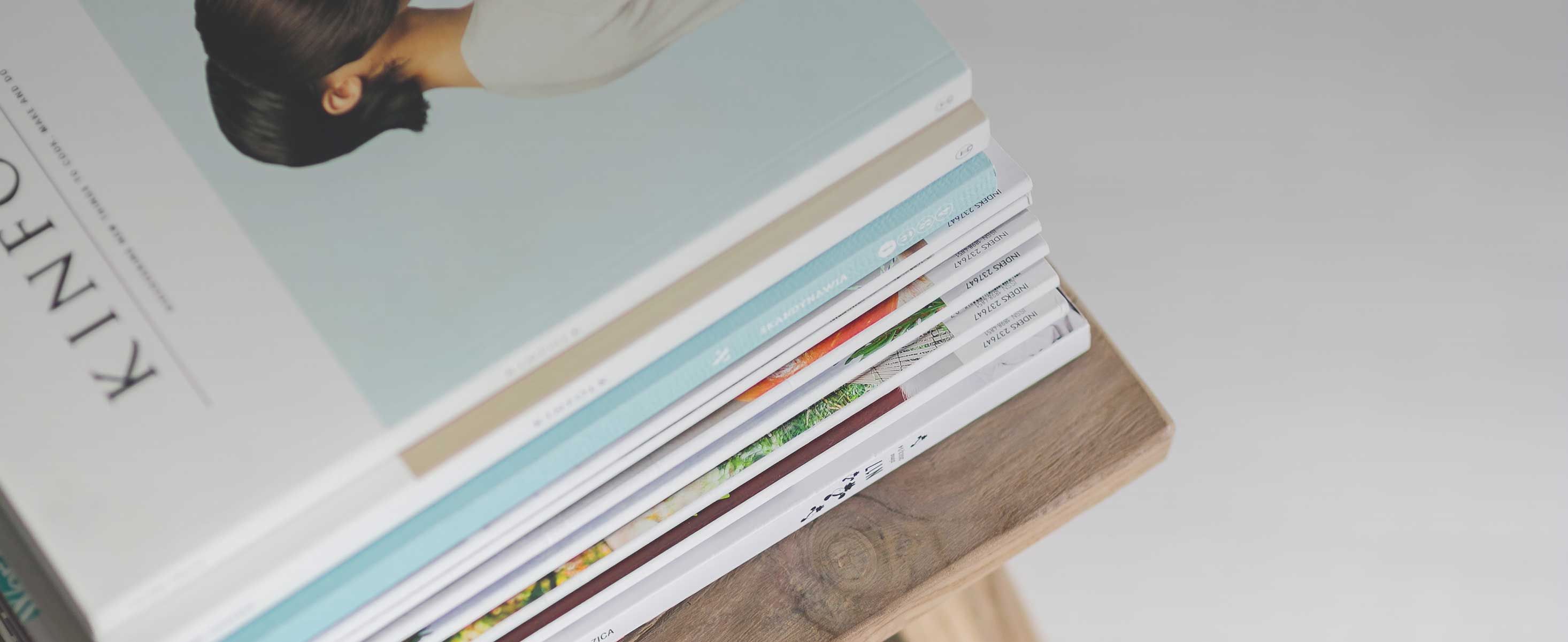
14 minute read
Hard-wired Switch Inputs
12.0 Hard-wired Switch Inputs
The ECM has 18 switch inputs available for feature interaction.There are 15 Switch To Input Sensor Common inputs and three Switch To Battery Positive inputs.
12.1 Switch to Sensor Common Electrical Specifications
Applied voltage to switches by the control will normally not exceed 11.5 Volts DC.Contact plating should not corrode or oxidize.Gold plated or silver alloy contacts are recommended.Normal current draw through the switches by the control will not exceed 6.5 mA. Contact chatter and momentary opening or closing should not exceed 100 milliseconds in duration.The switches should not open or close due to vibration or shock normally found in the application. ECM internal pull-ups force the respective input to 11.5 Volts DC when a switch contact is opened or the harness isopen circuited.Closure of an OEM installed switch must short circuit the input to a dedicated Sensor Common connection of the ECM (J1/P1 terminal-5, terminal-3 or terminal-18). Voltage thresholds measured at ECM: Voltage-In-Low < 0.9 Volts DC – With any switch contacts closed, ground potential differences, switch voltage drops, and wiring harness voltage drops must be such that a switch closure results in less than 0.9 Volts DC between the respective control inputs and Sensor Common terminal. Voltage-In-High > 4.0 Volts DC – With the switch contacts open, ground potential differences, switch voltage drops, and wiring harness voltage drops must be such that a switch opening results in greater than 4.0 Volts DC between the control input and Sensor Common terminal.
12.2 Sensor Common Connections
Three Sensor Common terminals are available to “ground”inputs connected to the ECM.All of the Switch To Sensor Common inputs must use one of the three terminals (J1/P1:3, 5, or 18).Switch inputs must not use chassis ground.Switches must not be Case grounded.
Terminal Description ECM Terminal Assignment AP Sensor/Switch Sensor Common J1/P1:5 Input Sensor Common #1 J1/P1:18 Input Sensor Common #2 J1/P1:3
12.3 Switch to Sensor Common Inputs
Switch function Default Optional Connection Connection(s) Cruise Control On/Off J1/P1:59 J1939 Cruise Control Set J1/P1:35 J1939 Cruise Control Resume J1/P1:44 J1939 Clutch Pedal Position Switch J1/P1:22 J1939 Service Brake Position Switch #1 J1/P1:45 J1939 Torque Limit Switch None J1/P1:7, 23 Ignore Brake/Clutch Switch None J1/P1:47 Two Speed Axle None J1/P1:6 Diagnostic Enable None J1/P1:46, J1939 PTO On/Off J1/P1:56 J1939 PTO Set J1/P1:58 J1939 PTO Resume J1/P1:60 J1939 PTO Engine RPM Set Speed Input A None J1/P1:46, J1939 PTO Engine RPM Set Speed Input B None J1/P1:7, 23 PTO Engine Shutdown None J1/P1:7, 23 Fast Idle J1/P1:40 None A/C High Pressure J1/P1:41 None A/C Fan Request (GMT560 Only) Sw to + Batt J1/P1:41 Shutdown Override J1/P1:40 None
Note: For switches with J1939 options, refer to the “J1939 Based Switched Messages”section for additional details.
The Service Brake Position Switch #1 is required for ALL applications.This is a normally closed switch and must be an open circuit when the service brake pedal is depressed.An Open circuit will deactivate or will not activate Cruise Control, Fast Idle (1 or 2), Extended Idle, or Cab Switches PTO.A change in state (depressing a released pedal, or releasing a depressed pedal) of the Service Brake, during Driver Alert, while the Idle Shutdown Timer is counting also overrides the Idle Shutdown Timer if the Customer Parameter Allow Idle Shutdown Override”is programmed toYes (default).Service Brake Position Switch #2 (switch to Battery Plus) may be required if needed to support the transmission style.
12.3.2 Clutch Pedal Position Switch Function
The clutch pedal position switch must be an open circuit when the clutch pedal is depressed.This switch is required on any application that uses a clutch and the Transmission Style must be programmed to Manual Option 1 or 2. AnOpen circuit will deactivate or will not activate Cruise Control, Fast Idle (1 or 2), Extended Idle, or Cab Switches PTO.Adjustment of the Clutch Pedal Position Switch is critical to proper system performance.A change in state (depressing a released pedal, or releasing a depressed pedal) of the Clutch, during Driver Alert, also overrides theIdle Shutdown Timer, if the ECM is programmed to allow Idle Shutdown Override.
The Clutch Pedal Position switch is required if the parameter Transmission Style is programmed to Manual Option 1, Manual Option 2 or Universal.If the transmission Style parameter is not programmed to one of these options, the clutch switch circuitry may be omitted.A jumper circuit from this input to Sensor Common is not required.
12.3.3 Diagnostic Enable
A Diagnostic Enable input is available to prompt the ECM for flashing Diagnostic Flash Codes via the hardwired Check Engine Lamp.The Diagnostic Enable parameter must be programmed to J1/P1:46 for this feature to function.A momentary normally open switch is required.The ECM will begin flashing and continue to flash out codes while this switch is closed.
Wiring Diagram 11 - Diagnostic Enable Circuit OEM provided and installed components required: 1) Normally open momentary switch. 2) Hardwired Check Engine Lamp Customer Parameter programming required: 1) Diagnostic Enable programmed to J1/P1:46
12.3.4 Two Speed Axle Switch
Two Speed Axle Switch may be programmed to None (Default) or J1/P1:6.When a two-speed axle is used Two Speed Axle Switch must be programmed to J1/P1:6 (Input #6).A normally open switch is required.When a twospeed axle is used, the change in gear ratios from the high-speed range to the low speed range alters the calibration of the vehicle speed signal.With this system, the ECM will automatically adjust the vehicle speed calibration when the switch is ON.This will ensure an ECM driven speedometer and ECM stored information correctly reflect the actual vehicle speed.The Low Speed Range Axle Ratio and High Speed Range Axle Ratio must be programmed as well.When the switch is closed between the ECM terminals 16 and 5, the ECM will use the following equation to calculate the actual vehicle speed: High Speed Range Axle Low Speed Range Axle Ratio Xcalculated vehicle speed = actual vehicle speed Note: GM trucks use a normally closed switch for this input. Where the calculated vehicle speed is the vehicle speed calculated using the programmed vehicle speed calibration (pulse per mile).This adjusted vehicle speed will be used to determine idle, PTO, and Fast Idle “Kickout” speeds as programmed.The vehicle speed broadcast over the data links and the ECM speedometer output vehicle speed will reflect the adjustment.If Two Speed Axle Switch is not programmed to J1/P1:6, the ECM does not use either axle ratio to determine the actual speed. OEM provided and installed components required: 1) Switch to close when low speed axle ratio is used (switch to OPEN if GM truck). Customer Parameter programming required: 1) Two Speed Axle Switch programmed to J1/P1:6 when a two-speed axle is used (default is NONE). 2) High Speed Range Axle Ratio and Low Speed Range Axle Ratio must be programmed or the feature is disabled.
DIAGNOSTICENABLE ECM
G844-PK H795-PK
46 5 P1J1 INPUT#7 APSENSOR/SWITCHSENSORCOMMON
Two-Speed Axle On/Off Switch ECM
G843-OR H795-PK
Switch Shown in High Speed Range
6 5 P1J1 INPUT#6 APSENSOR/SWITCHSENSORCOMMON
Wiring Diagram 12
12.3.5 PTO Switches
Several options are available to control engine rpm while in PTO.In order to operate in PTO Mode, a dedicated PTO ON/OFF switch is required.Three PTO modes are available.The Cruise Control Set/Resume switches can be used or dedicated PTO switch inputs can be programmed and installed to give a variety of controlled engine speeds. OEM provided and installed switches (required and/or optional): 1)PTO On/Off switch 2)Optional Switches 3)Transmission Neutral switch 4)Cruise Control Set/Resume 5)PTO Set/Resume 6)PTO Set Speed A 7)PTO Set Speed B 8)Torque Limit 9)Clutch Pedal Position Switch (for manual transmissions). 10)Service Brake Pedal Position 11)Ignore Brake/Clutch Customer Parameter programming required: 1)PTO Configuration must be programmed to Cab Switches, Remote Switches, or Remote Throttle. 2)Individual switch inputs as necessary.
12.3.6 Fast Idle Switch
A momentary Fast Idle switch can be used to elevate and maintain up to two programmed engine rpm settings. Pressing and releasing the switch once will cause the engine to ramp from Low idle to the programmed Fast Idle RPM #1 (1000 rpm default).Pressing and releasing the switch while at Fast Idle #1 will cause the engine to ramp tothe programmed Fast Idle #2 at the programmed “Idle/PTO Engine Speed Ramp Rate.”If Fast Idle #2 is not programmed, the engine will return to low idle.Fast Idle will be deactivated (kicked out) if the Service Brake or Clutch is depressed.The transmission Neutral switch, when in Gear, will also cause the Fast Idle to deactivate.
-
12V + FASTIDLEENABLE
FASTIDLEENABLEDLAMP P1J1 ECM
L902-GN H795-PK G880-PK 40 5 31
INPUT#18 APSENSOR/SWITCHSENSORCOMMON OUTPUT#9 G880-PK 21 OUTPUT#8
Optional Fast Idle Enabled Lamp Circuit
Wiring Diagram 13 - Fast Idle Enable Switch and Fast Idle Enable Lamp Circuits OEM provided and installed components required: 1) Fast Idle Enable Momentary Switch (N/O). 2) Fast Idle Enabled Lamp (optional) Customer Parameter programming required: 1) Fast Idle Lamp parameter programmed to J1/P1:31(default) or J1/P1:21.(optional) 2) Fast Idle RPM #1. 3) Fast Idle RPM #2 (optional).
12.3.7 Ignore Brake/Clutch Switch
The Ignore Brake/Clutch Switch is used to allow use of an engine set speed in mobile vehicle operations. WhentheIgnore Brake/Clutch parameter is programmed to J1/P1:47 and the switch is closed, PTO, Extended Idle and FastIdle features will ignore service brake and clutch switch inputs.If this switch is in the closed position when the ECMis powered up, this switch function is ignored until the switch is cycled Off and ON.
The transit industry calls for an engine shut down override switch to allow the operator to override a critical engine diagnostic induced engine shutdown.The purpose of the Shutdown Override Switch is to allow an operator to override the impending engine shutdown to allow the operator to move the vehicle to a more safe location.This feature is only available on C9 Mass Transit ratings. Shutdown Override Operation The Engine Monitoring System can be used to cause the engine to shut down when the engine has an active diagnostic code for Very Low Engine Oil Pressure, Very low Coolant Level or Very High Engine Coolant Temperature.When one of these Diagnostics is active, the Warning Lamp, or the dedicated lamps defined by theWarning Lamp option of “Option 1”, will start to flash.The flashing lamp indicates that the engine power is beingderated and engine shutdown will occur within a few seconds. If the Shutdown Override Switch has been closed before the Shutdown sequence has ended, a Shutdown Timer will start to countdown from 30 seconds.If the Shutdown Override Switch is opened and closed again before the engine has turned the fuel injectors Off, the timer will reset for another 30 seconds.Once the timer has counted down to zero and the fuel injectors have been disabled, the engine will shut down regardless of the position of theShutdown Override Switch. Initiating the Shutdown Override Timer will result in a Diagnostic Code being generated and logged into memory. ADiagnostic Snapshot will also be generated.The logged diagnostic code will require Caterpillar Factory Passwords to clear from the ECM’s memory.
ECM
40 3 Shutdown Override Switch Switch Common
P1/J1
Wiring Diagram 14
12.3.9 A/C High Pressure Switch
The A/C High Pressure switch is used in conjunction with the ECM controlled Cooling Fan.This is a normally closed switch and when opened, causes the ECM to engage the cooling fan.
12.3.10 Exhaust Brake Switch
The Exhaust Brake switch is used to allow the operator to enable or disable the engine’s exhaust retarder. OEM provided and installed components required: 1) Exhaust Brake Switch Customer Parameter programming required: 2) Exhaust Brake Switch programmed to J1/P1:16
12.4 Switch-to-Battery Electrical Specifications
Contact plating should not corrode or oxidize.Gold plated or silver alloy contacts are recommended.Normal current draw through the Input #12 and Input #13 by the control is 6.0 mA at 12 Volts DC.Normal current draw through the Ignition Key Switch by the control is 1.2 mA at 12 Volts DC. Contact chatter and momentary opening or closing should not exceed 100 milliseconds in duration.The switches should not open or close due to vibration or shock normally found in the application. Each of these ECM inputs is pulled to ground eliminating the need for external termination.Closure of an OEM installed switch must short circuit the input to the vehicle positive battery connection.
12.4.1 Voltage thresholds measured at ECM:
Switch Open < 0.9 Volts DC – With the switch contacts open, ground potential differences, switch voltage drops, and wiring harness voltage drops, the ECM must detect less than 0.9 Volts DC between the control input and the ECM negative battery connection. Switch Closed > 9.0 Volts DC – With the switch contacts closed, ground potential differences, switch voltage drops, and wiring harness voltage drops, the ECM must detect a switch closure resulting in greater than 9.0 Volts DC between the control input and the ECM negative battery connection.
12.4.2 Switch-to-Battery Circuit Protection
These circuits do not require dedicated circuit protection.
Switch function Default Optional Connection Connection(s) Ignition Key Switch J1/P1:70 None Transmission Neutral J1/P1:62 J1939 Service Brake #2 J1/P1:64 None A/C Fan Request (GMT560 Only) J1/P1:62 None
12.4.3 Ignition Key Switch to Positive Battery
The Ignition Key Switch input is J1/P1:70 and is not changeable.When the ECM detects the input is switched to vehicle battery (Ignition Key Switch ON), the ECM will be powered.The ECM will then control the injectors allowing the engine to start. OEM provided and installed components required: 1) Switch to close when the ignition is ON.
Service Brake Pedal Position Switch #2 is required if the Transmission Style is programmed to Manual Option 2, Universal, AT/MT/HT Option 2, AT/MT/HT Option 3, Automatic Option 2, or Automatic Option 3.Input #13 is used as the Service Brake Position Switch #2 input.The Service Brake Pedal Position Switch #1 (switch to ground) must also be used. This switch must be a short circuit to +Battery when the service brake pedal is depressed.The control will deactivate Cruise Control, Cab Switches PTO, Fast Idle, or Extended Idle when the Service Brake Pedal Position Switch #2 is ON.The Brake and Clutch Pedal Position Switches do not affect remote PTO.A change in state (depressing a released pedal, or releasing a depressed pedal) of the Service Brake, during Driver Alert, while the Idle Shutdown Timer is counting can also override the Idle Shutdown Timer, if the ECM is programmed to allow Idle Shutdown Override.
-
12V + SERVICEBRAKE#2PEDALPOSITION (PEDALRELEASEDPOSITION) L900-PU 64 P1J1 ECM
INPUT#13
Wiring Diagram 15
OEM provided and installed components required: 1) Switch to close when service brakes are applied. Customer Parameter programming required: 1) Customer Parameter Transmission Style programmed to Manual Option 2, AT/MT/HT Option 2,
AT/MT/HTOption3, Automatic Option 2, or Automatic Option 3.
12.4.5 Transmission Neutral Switch
The ECM can be configured to monitor the transmission’s Neutral Switch.This switch is used to indicate when anautomatic transmission is in neutral.The neutral condition allows features such as Cab Switches PTO, Fast Idle, and Extended Idle to be used.The switch is required if the Transmission Style Parameter is programmed to AT/MT/HT Option 3, AT/MT/HT Option 4, Automatic Option 3, or Automatic Option 4.
-
12V + TRANSMISSIONNEUTRALSWITCH (INGEARPOSITION) 409-OR 62 P1J1 ECM
INPUT#12
Wiring Diagram 16
OEM provided and installed components required: 1) Switch to close when the transmission is in neutral. Customer Parameter programming required: 1) Customer Parameter Transmission Style programmed to AT/MT/HT Option 3, AT/MT/HT Option 4,
AutomaticOption 3, or Automatic Option 4. 2) Transmission Neutral Switch parameter programmed to J1/P1:62.
12.4.5.1 Transmission Neutral Switch Status via J1939 Data Link
The ECM has the ability to receive Neutral Switch status information from a Transmission ECU capable of broadcasting the status via the J1939 data link.The J1939 option can be used to replace the hardwired switch input to the ECM.This option can only be used if the Transmission is capable of supporting the required J1939 message protocol, such as an Allison 2000 Series Transmission.The OEM is responsible for making this determination. The Transmission must support the J1939 PGN $F005 (ETC2 – Byte 1 – Selected Gear, Byte 4 – Current Gear or Byte 7 – Current Range) message to be compatible.If the message is not received, the ECM will assume the transmission to be In gear. OEM provided and installed components required: 1) Electronically Controlled Transmission capable or supporting required J1939 message protocol. Customer Parameter programming required: 1) Customer Parameter Transmission Style programmed to either AT/MT/HT Option 3, AT/MT/HT Option 4,
Automatic Option 3, or Automatic Option 4. 1) Transmission Neutral Switch parameter programmed to J1939 option.
The neutral switch is not normally used with manual transmissions.The ECM can also be configured to ignore the neutral switch if an automatic transmission is used.
Customer Parameter programming required: 1) Transmission Style parameter programmed to Manual Option 1 or 2, AT/MT/HT Option 1, AT/MT/HT Option 2,
Automatic Option 1, or Automatic Option 2. 2) Transmission Neutral Switch parameter programmed to J1/P1:62 (default) hardwired option or None. NOTE: Programming the Neutral Switch to “None”and the Transmission Style to “Automatic option 3”(or 4) or “AT/ MT/HT Option 3”(or 4) will cause the ECM to assume that the transmission is IN GEAR.