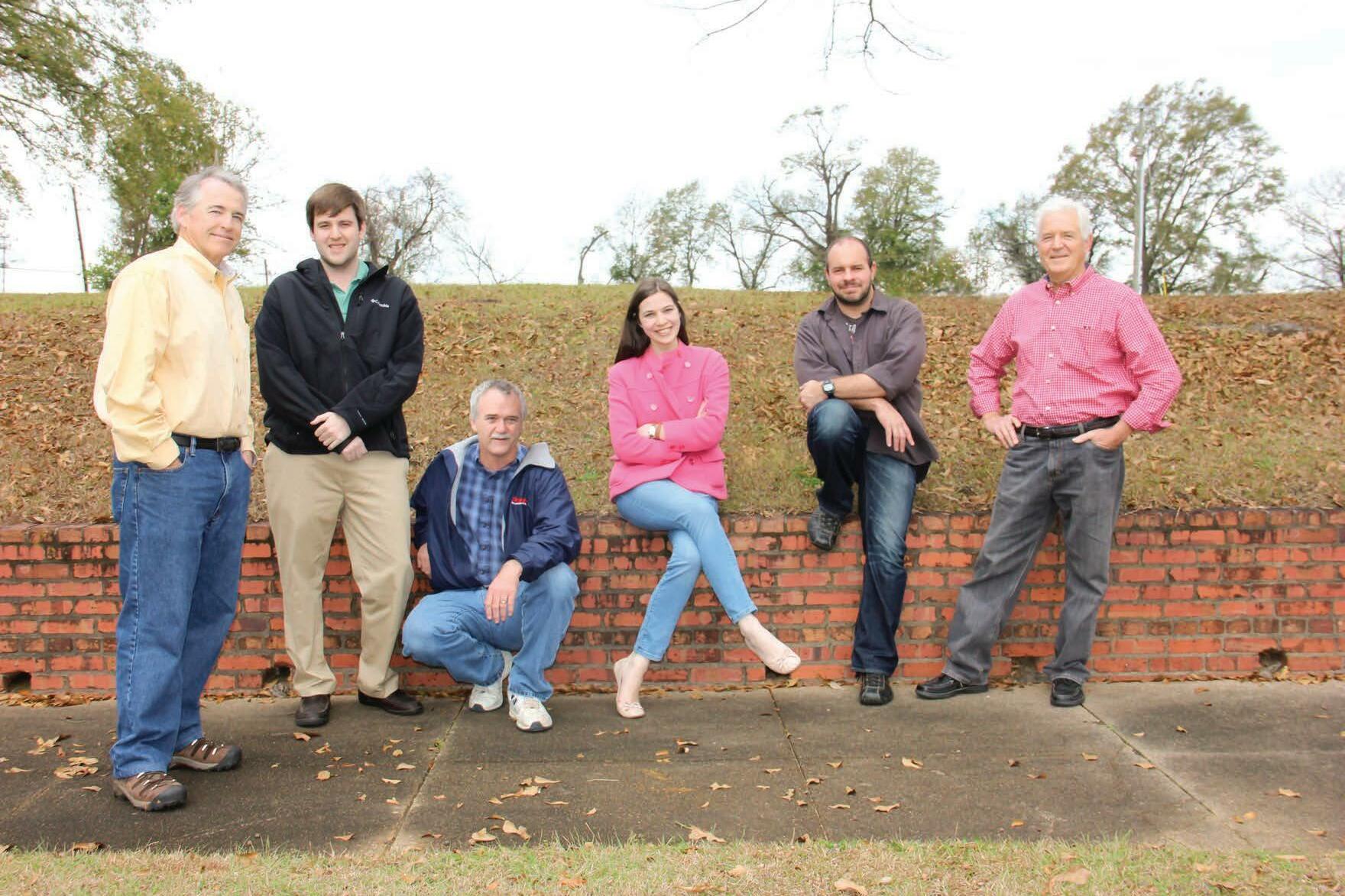
38 minute read
Southern Stumpin’
By David Abbott • Managing Editor • Ph. 334-834-1170 • Fax: 334-834-4525 • E-mail: david@hattonbrown.com
Fighting Windmills
Have you ever heard the expression “tilting at windmills”? It originates in the 1605 Spanish novel Don Quixote by author Miguel de Cervantes. Widely regarded as the first modern novel and often cited as foundational to Western literature, Don Quixote influenced later works like Alexandre Dumas’ The Three Musketeers and Mark Twain’s Adventures of Huckleberry Finn. One of the most widely translated works of fiction in the world, it has remained a popular classic for over 400 years.
The titular protagonist is delusional; a lower class gentleman, he imagines himself to be a knight of great nobility. He’s a wannabe hero, a visionary idealist lost in his own fantasy of the world. He goes on a series of adventurous, often humorous quests.
In one of the novel’s more famous scenes, Don Quixote mistakes a bunch of windmills for giants. Since he fancies himself a chivalrous knight with the duty to vanquish these monsters, he decides to attack them. His faithful sidekick/squire, simple peasant farmer Sancho Panza, who served as the voice of reason, tries to convince his master of the truth, but Quixote won’t listen. So the would-be knight charges at the windmills, only to get himself pummeled by the spinning sails.
The “battle” is of course both needless and fu tile, accomplishing nothing. The windmills were just there, inanimate and indifferent to Quixote’s misperception of them. They weren’t a threat to him, and he couldn’t really do anything much to them, either.
“Tilting,” by the way, means jousting, the way medieval knights liked to fight. So the expression “tilting at windmills” basically means to fight against an imaginary enemy; to waste time, energy and resources on a pointless quest.
These days, windmills, like everything else in our ever-more-divided cultural landscape, have been politicized on both the left and the right. Like electric cars, windmills have become symbolic of “Green New Deal” energy/environmental policies, part of the liberal/progressive agenda aimed at re ducing greenhouse emissions, replacing fossil fuels with clean, renewable energy and reversing climate change. Some folks think this is a good idea, even a vital one; others think it’s a fool’s errand, or worse, a scam. Depending on where you live and what you do for a living, your view of all this might blow one direction or the other.
Changing Winds
Lately, it seems to me that members of the logging community with whom I have interacted don’t seem quite as negative or hostile towards the concept of climate change as seemed to be the case maybe 10 or 15 years ago. If not entirely positive, the attitude seems at least neutral.
Now don’t get me wrong. I don’t mean to imply anyone is applying for membership in a tree-hugger society. But there seems to be an acknowledgment that there might be some truth to climate change, and moreover, a recognition of the fact that a lot of people believe climate change is a fact.
Myself, I have neither the qualifications nor the inclination to debate the science or the politics of it, on one side or the other. Believe in it or not, though, arguing over it might be a counterproductive waste of time. Trying to change people’s minds might be a fight against windmills (both figuratively and literally).
Seems like we’ve had a tendency to cast the logging community and environmental activists as natural enemies, on opposite sides of the issue. And when we think about halted timber sales, spotted owls, deserted mill towns and wildfires in westerns states, it’s easy to see why. It seems so obvious as to need no explanation: loggers cut trees; environmentalists don’t want trees cut.
But maybe it doesn’t have to be that way, and maybe it isn’t that simple or clear-cut. Maybe the social/political dimension of the climate change debate might actually represent a positive opportunity for the industry.
At the ALC Annual Meeting last fall, Scott Dane discussed the importance of selling what people are buying. It might be the first rule of business, really: give the people what they want. If you want to sell cars, make cars people want to drive. If you want to sell music, make music people want to listen to. And if you want to sell a narrative, tell a story people want to hear. As Scott put it, we know what the current administration in DC is buying—what drives their agenda.
We can and must work with whatever side is in power if we want to accomplish things, and we have to be able to meet them where they are, not where we wish them to be. It’s important we tell our side of the story, which, conveniently, also happens to be the truth: that loggers are, and should be recognized as, part of the solution, not the problem, when it comes to clean energy and a healthy planet.
Many of the loggers I talk to throughout the country tell me how highly they prioritize working to improve the public perception of logging, to rehabilitate the industry’s image. It’s not a deceitful spin or PR campaign to cover up anything nefarious. It’s just about better educating a poorly in formed public about a vital, necessary sector that has been widely misrepresented and misunderstood.
Common Ground
Last summer my family and I went to see the iconic country band Alabama perform at the Wharf Amphitheater in Orange Beach, Alabama. This was the sixth time I have seen them in concert in the last 30 years—you could say I’m a fan. They opened the show with their hit song from 1990: Pass It On Down. The song is basically a conservationist anthem: “Let’s leave some blue up above us, let’s leave some green on the ground. It’s only ours to borrow, let’s save some for tomorrow, keep it and pass it on down.” It reminds me of my dad lamenting modern pollution compared to the clean water and forests he enjoyed growing up in rural Arkansas in the 1950s.
Well, my dad and Alabama aren’t exactly flaming liberals; and there’s no reason why protecting (or responsibly managing) natural resources for future generations should be politicized or controversial. Environmentalists want less pollution, clean air and clean water, right? Well, those are our values, too. Who would be against clean air and water and less pollution? We all want these things. That’s some common ground; we can build on it.
Sure, there are some in that movement who go too far; but my guess is most of them just don’t know what they don’t know. They mean well; maybe they see themselves as idealistic heroes, as knights attacking giants. We just need to help them see that we are not the enemy; in fact, in many ways, our goals align.
Environmentalists want to stop deforestation. You know who’s really against deforestation? People who make their living from the forest! Families who plan to stay in logging generationally want to see trees replanted to be harvested in sustainable and responsible ways, because their livelihood today and the future livelihood of their children and grandchildren depends on it. It’s their legacy and they want to pass it on down.
Loggers, for the most part, don’t get into logging for how great the money is. They do it because they love being in the woods. They’re not out to destroy the thing they love. It’s a misperception that needs to be corrected with education, communication and good PR.
If the political goal is to mitigate the effects of man-made climate change, then a timber industry helping to sustainably manage healthy forests that can constantly regenerate and absorb carbon in the atmosphere must be an essential part of that plan. The new, younger generations believe in climate change; denying it is a losing strategy. Ridiculing that belief will get you nowhere. Rather than being antagonistic to those with differing political views, a wiser strategy might be to embrace, adapt and adjust. Put another way: if you can’t beat ‘em, join ‘em—but on your own terms, by showing how you can contribute to helping them get what they want. Form alliances instead of making enemies so you can have a voice in policymaking; be a part of the conversation and get a seat at the table so you can bring your point of view to the discussion.
Either that, or we could just keep fighting windmills. SLT
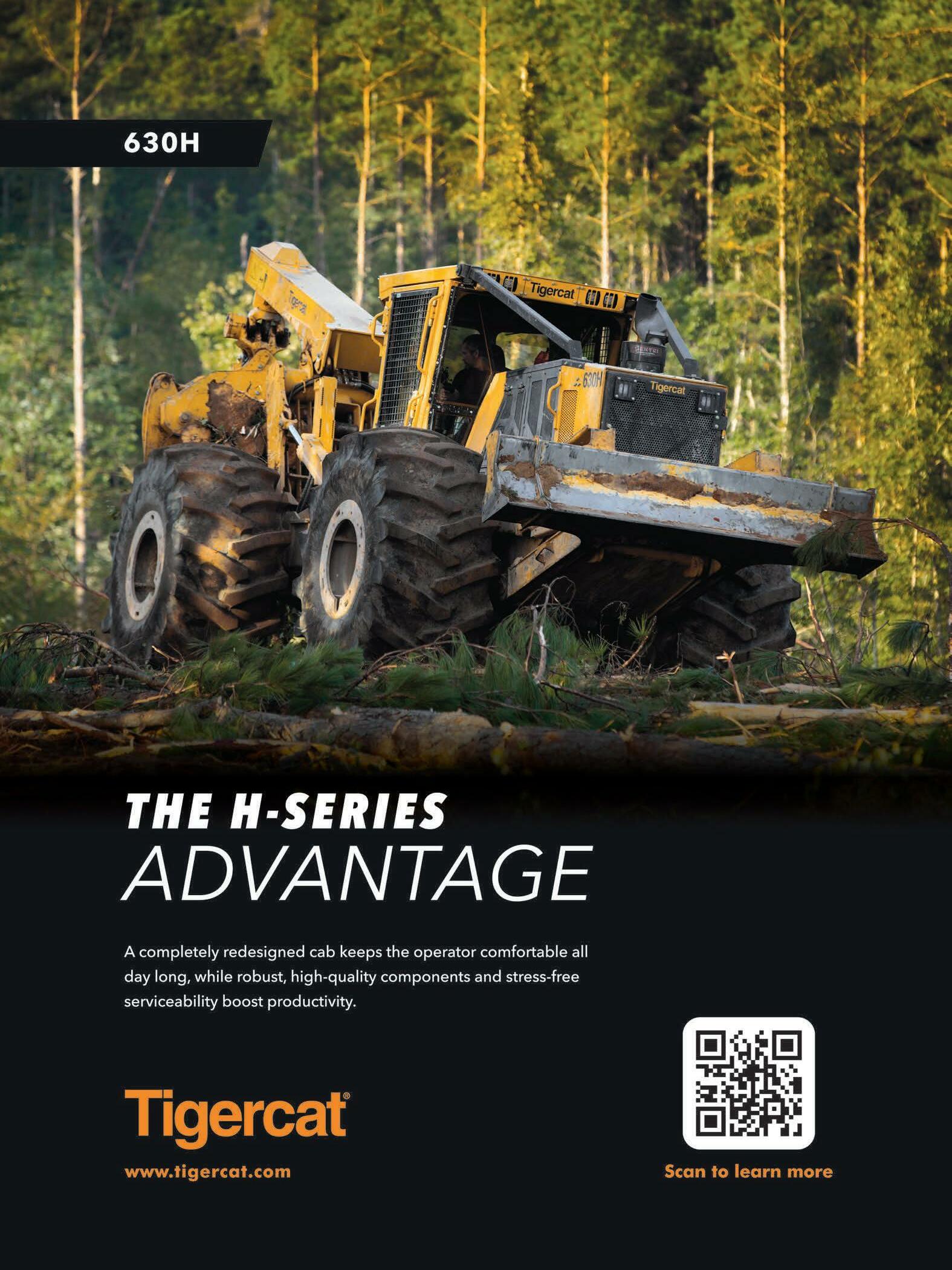
Change Of Pace
■ Former mechanic finds ways to alleviate logging pressures while commodities markets soar.
By Patrick Dunning
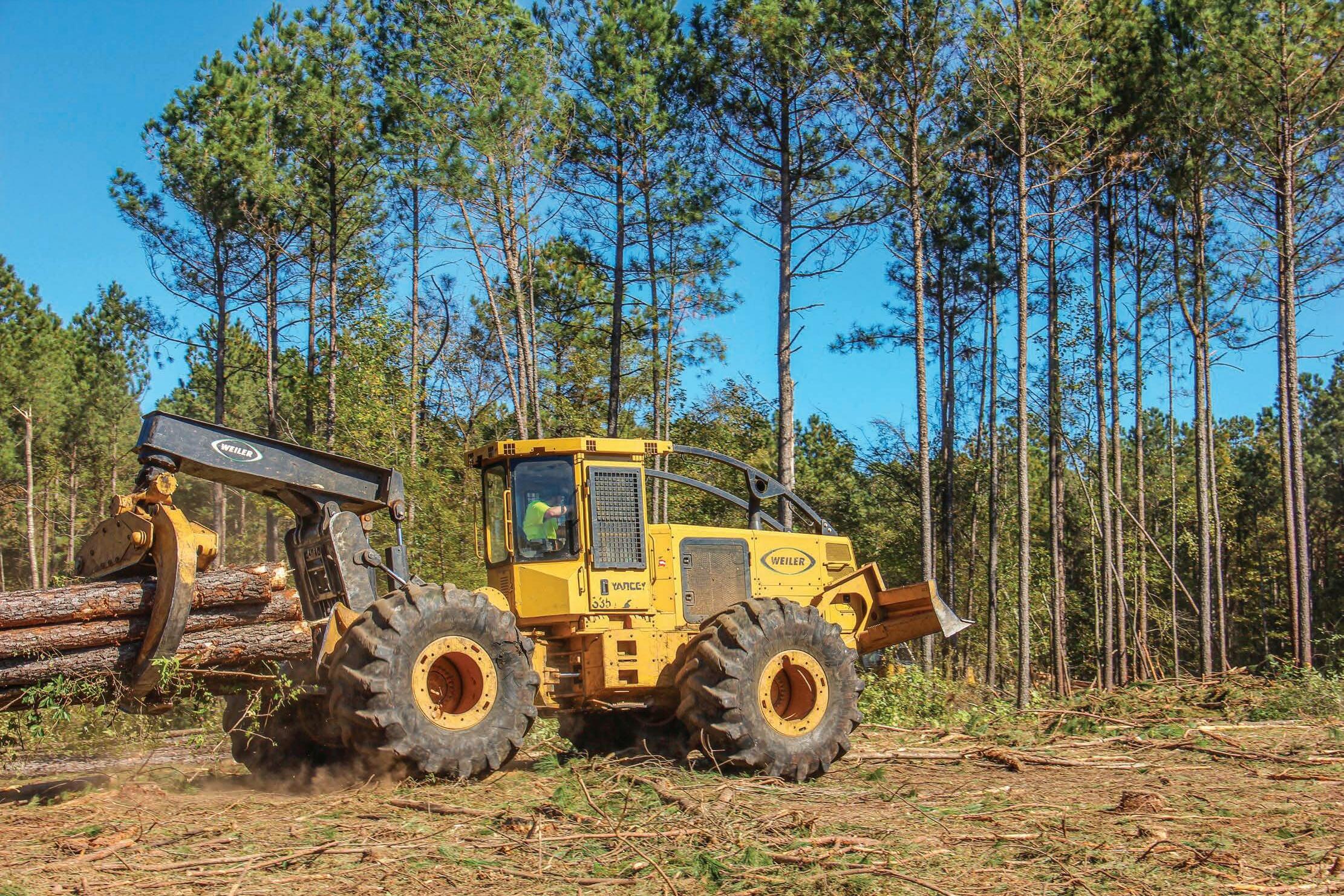
GRAY, Ga.
Brad Comer, 54, had been a full-time mechanic with a couple of trucks for more than 20 years before he hauled his first load of pulpwood. He’d been around logging his entire life, growing up in Hancock County; even his dad was a lifelong logger. Comer says this part of rural midwest Georgia has always relied on the timber industry, which has provided jobs for the families that live here.
Nearly a decade ago, Georgia’s forestry industry was moving forward following a setback from 2008’s downturn in the housing market. The state’s timberland coverage had remained stable and Comer, who was already considering a career change, figured it was a good time to start a logging business. He established Outlaw Timber Harvesting LLC in 2013.
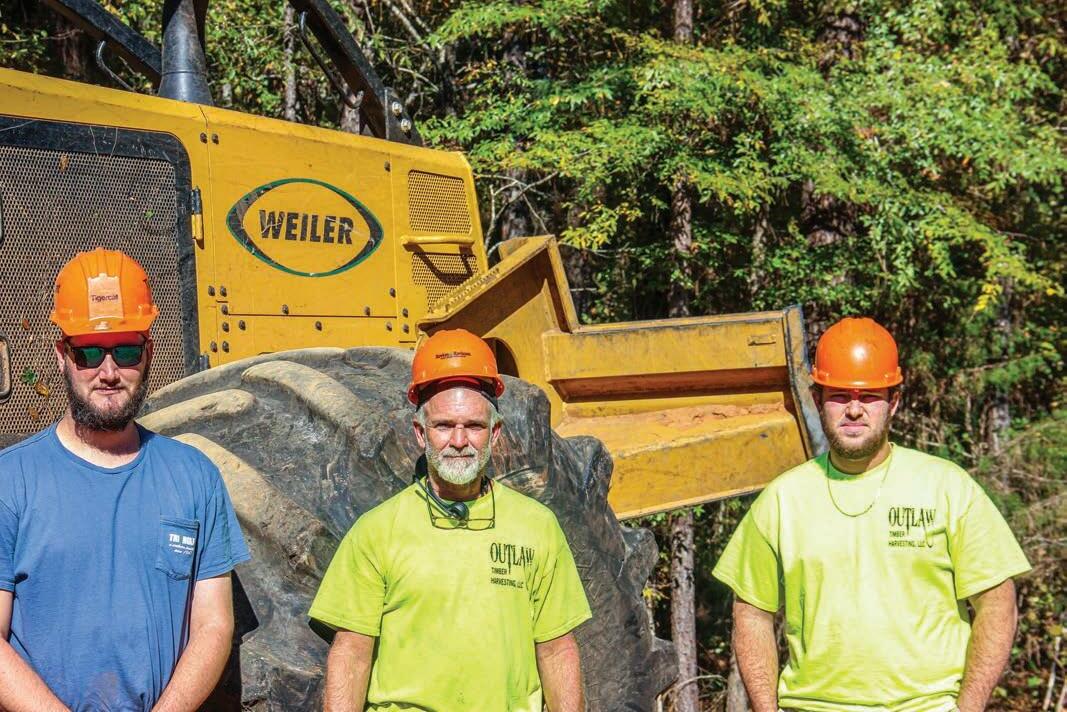
Brad Comer, center, says his young crew has been dependable.
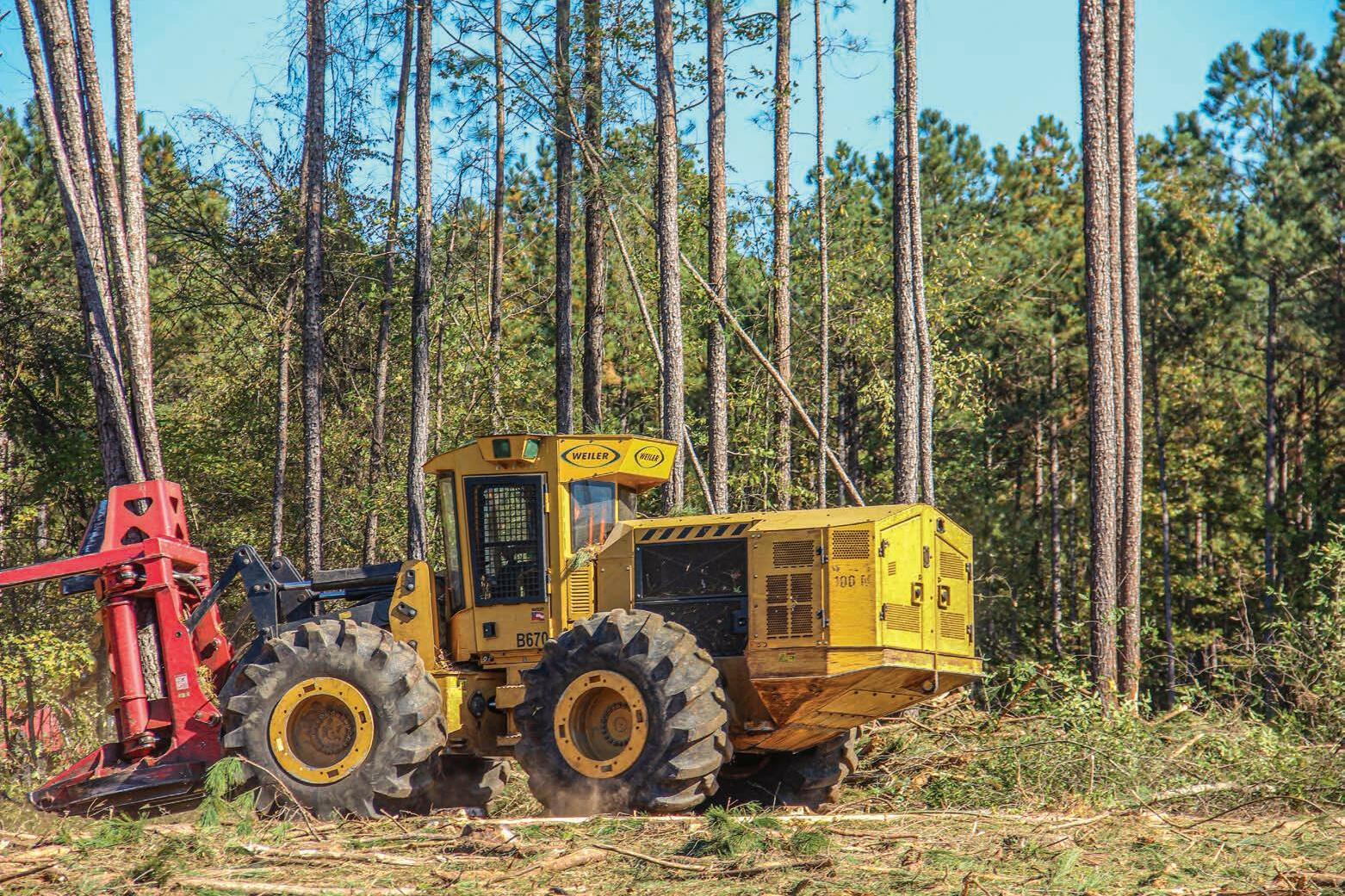
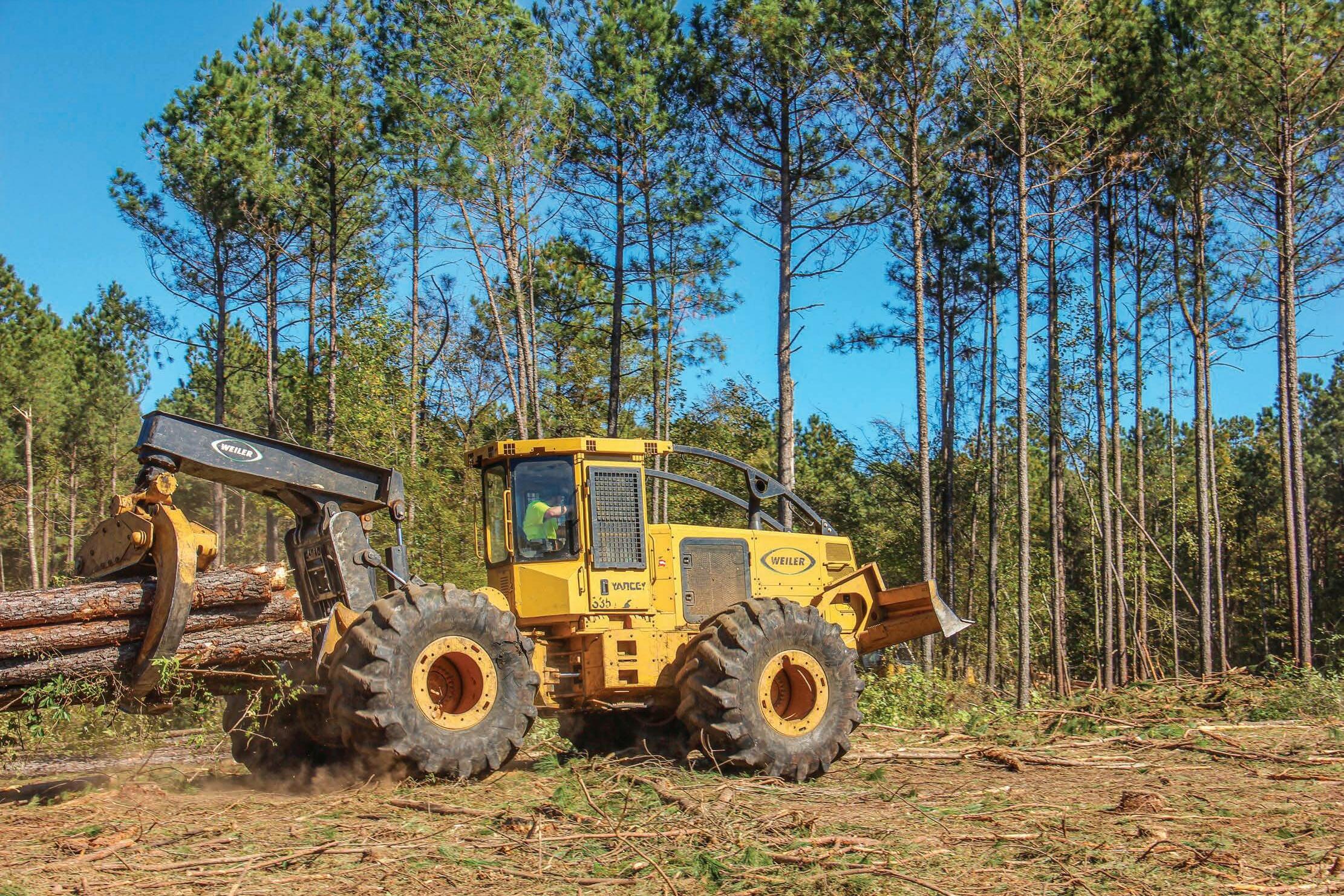
Comer switched to Weiler in 2019 because of their bumper-to-bumper four-year, 7500-hour warranty.
“I was 43 when I decided I wanted to be a logger,” he recalls. “I’m sitting around drinking some beers with a friend of mine who had just bought a truck and said he wanted to haul wood with it. At the time I had never hauled wood before and told him, ‘I’m going to buy a trailer tomorrow and we’re going to be a couple of outlaws doing it’ and it stuck.”
Comer jokes that his attempt to change occupations only resulted in him having two careers at once, only now he doesn’t get paid for working on equipment. “I got tired of being a mechanic. Now I’m a logger and a mechanic,” he laughs. “Went from getting paid to do it to doing it for free now.”
Outsourcing Help
Since Outlaw Timber’s inception Comer has contracted for Piedmont Forestry, headquartered in Macon and servicing the middle-Georgia region. In the past Comer purchased
Outlaw Timber plans to reduce its weekly production and become more efficient with trucking.
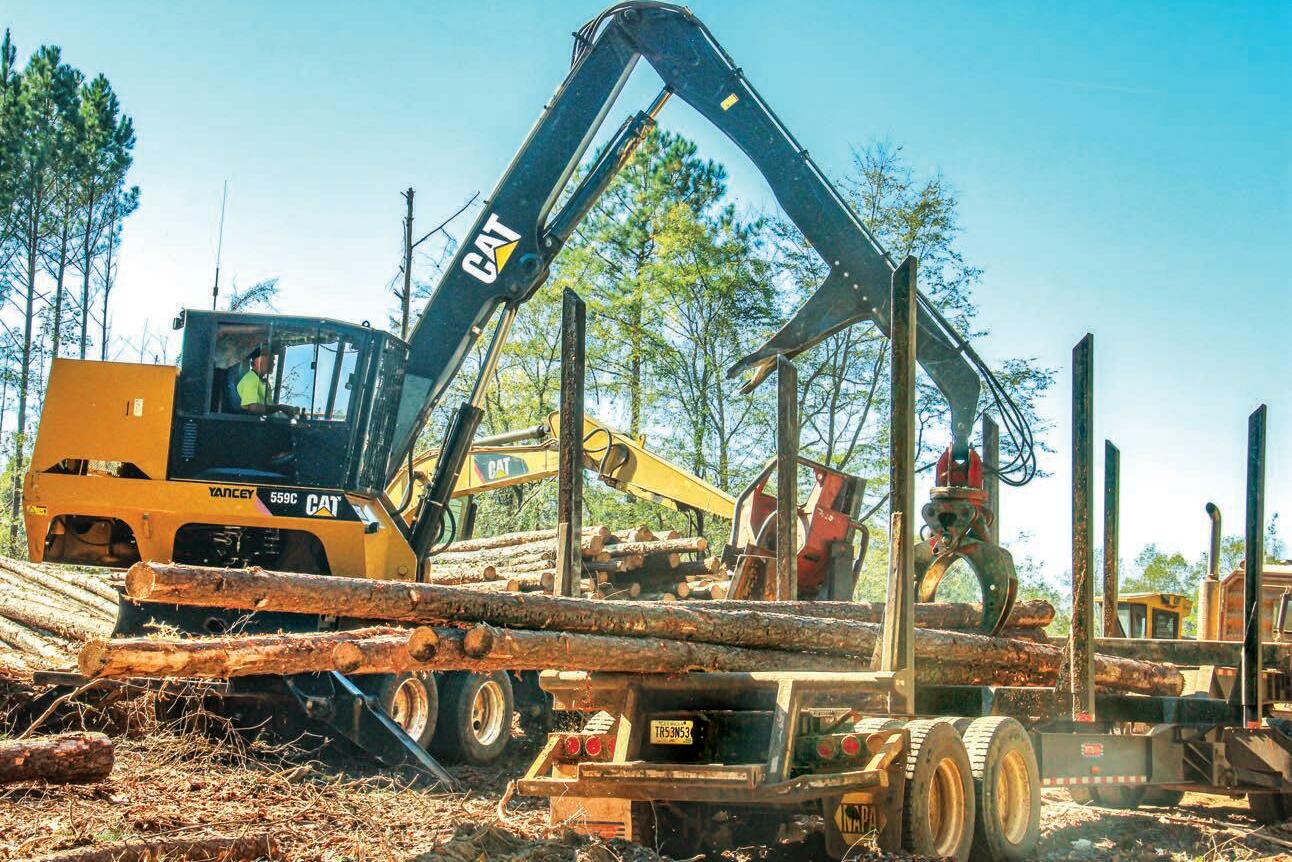
his own stumpage and coordinated with mills himself, but now believes contracting is the simpler solution and allows him to focus efforts more on in-woods operations.
“I prefer contracting because often times it’s harder to sell your wood,” Comer asserts. “I don’t have time to do what I have to do now. I’d love to haul 40 loads a week that’s worth 70 but the mills around here prefer you go through a forester. The middle man needs his money, especially some of these pulpwood mills.”
Trucking is another area Comer is contracting out to a third-party to remain focused on meeting production goals. As of last month, J.B. Hunt’s newest endeavor to mitigate cut-and-haul headaches by offering dedicated fleets has made its way to Outlaw Timber’s loading deck.
Comer currently owns six trucks, has four full-time truck drivers and pays near $20,000 annually per truck for insurance premiums. With the price-per-ton rates failing to compensate for rising operating costs, Comer says eliciting J.B. Hunt’s services through Piedmont Forestry is a sure-fire way to reduce insurance and liability costs on his rigs. Still, how effective J.B. Hunt’s efforts will turn out to be remains to be seen, the logger admits.
“J.B. Hunt says this is something they want to get into,” he says. “They’ve already deployed trucks in Alabama and Florida. They’re putting a big price tag on it but know we are at a vulnerable point as loggers. I know three or four loggers around here personally that said if J.B. Hunt didn’t pull through, they would have had to get out of the industry. Insurance companies have put contractors out of business. Why would a man want to have his own truck and liability and make the same he could driving mine and parking it on the weekends?”
Jeremy Morris, General Manager, J.B. Hunt Timber Services, says their dedicated solution provides loggers with a contracted hauling capacity they can rely on every day. He believes a stable trucking force will give loggers a competitive advantage.
“A logger’s main competency is cut, skid and load logs,” Morris says. “J.B. Hunt’s core competency is trucking. When those two marry, you’ve got a great thing. Now you
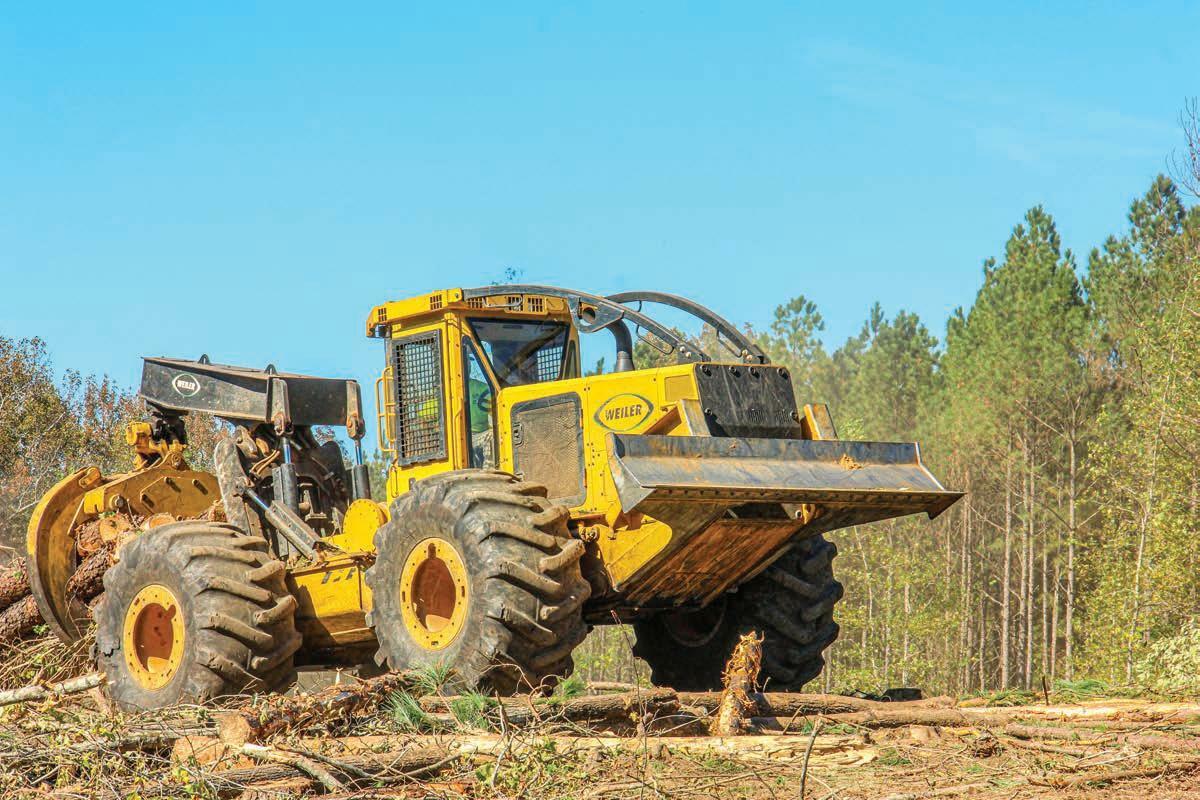
Nearly 70% of the company’s volume is dedicated to Interfor in Eatonton, Thomaston and Perry.
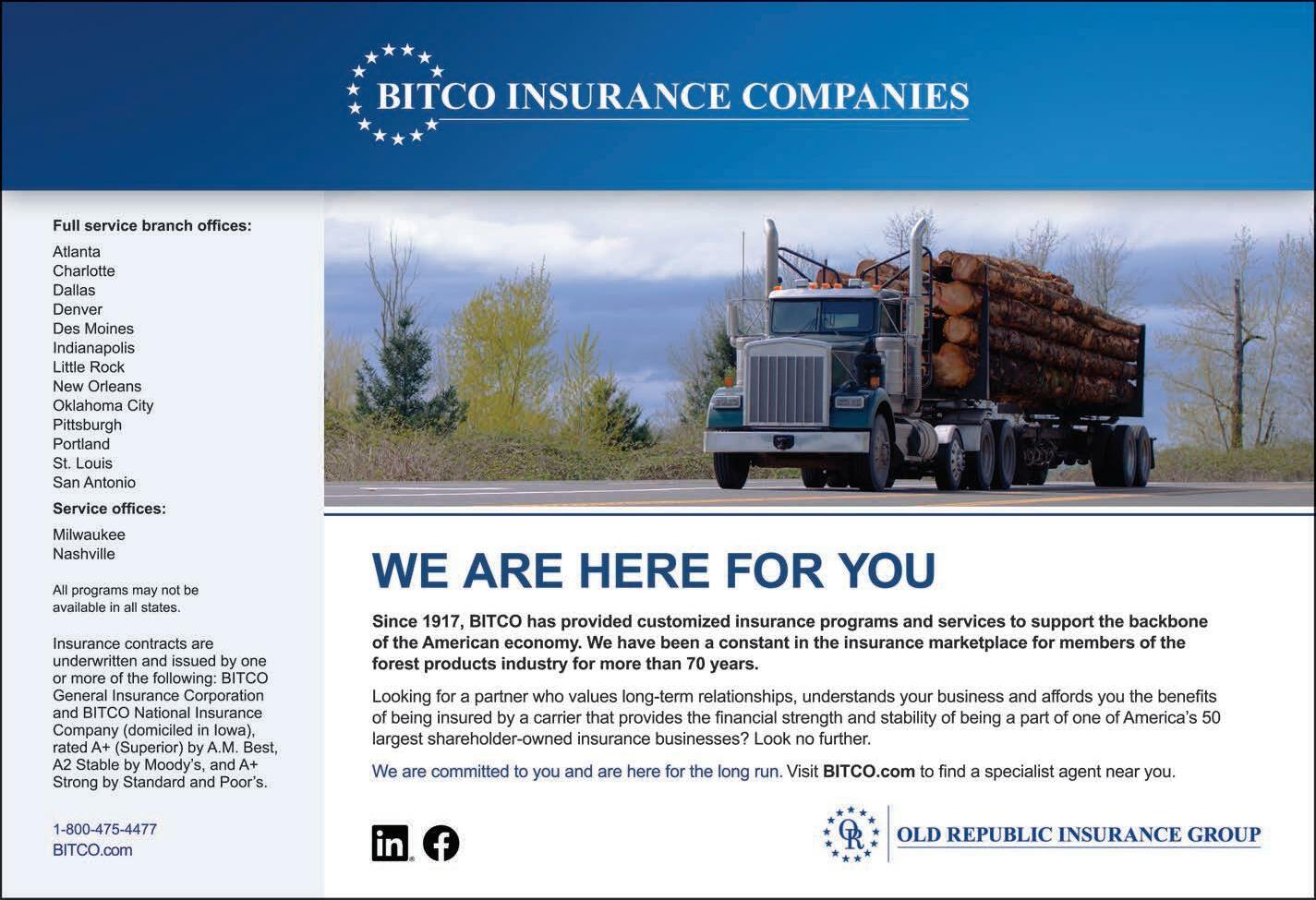

have two companies focused on their core values, which in the end is to give the logger the results he needs and that’s more wood across the scales. We put someone on site with that customer and in essence became an extension of Piedmont. I’ve got guys imbedded at that Piedmont office that operate our fleet, working with the logger and logistics professionals every day to maximize efficiency.”
In the past Comer averaged 120 loads per week, sometimes more depending on available trucks. Now with 35 trucks at his discretion with one phone call, Comer’s plan is to efficiently reduce the number of loads he hauls to 75 per week. Within his current big-rig inventory of three Macks (’06, ’08, ’10), two Freightliners (’96, ’07) and a ’98 Peterbilt, Comer plans to reduce his fleet to four in the near future.
“I don’t want to haul over 75 loads a week,” he says. “I’d rather just not worry about trucking. I don’t want to get back to 100 loads per week. I was on a roll there for a minute but I’m getting older. Operations
When Southern Loggin’ Times visited Outlaw Timber in November last year, Comer’s three-man crew was clear-cutting a 200-acre private block of 20-year-old planted pine in Hancock County.
When Comer started in 2013 the first piece he bought was a Caterpillar loader. He ran a Tigercat skidder and cutter for a stint. He switched to Weiler in 2019 because of their four year, 7,500-hour warranty. “That’s bumper to bumper,” he asserts. “I met Pat Weiler before and he’s a really good man. What that warranty covers is a no-brainer.”
Comer’s cut-skid-load operation utilizes a ’20 Weiler B670 fellerbuncher and ’19 S350 skidder with 35x5 tires. At the loading deck he runs a ’16 model 559C Cat and ’20 538 Cat Forest Machine featuring a ’17 model HTH622B Waratah processing head. Comer doesn’t strip wood with either of his loaders, only loading trucks, so combined both loaders have just 6,000 hours.
Roughly 70% of Outlaw’s volume is dedicated to Interfor in Thomaston, Eatonton and Perry. The remainder is hauled to Georgia-
Pacific in Warrenton and Madison.
“I’ve had that processing head almost five years now. Some people thought I was crazy to buy it but it’s fast and Interfor guaranteed me quota if I bought it. We do all cut-to-length for Interfor and there’s no waste left.”
The 32 in. saw bar can cut up to a 30 in. tree and features a twin retainer knife and strengthened upper delimb castings to improve delimbing durability.
Outlaw Timber just finished constructing a new 40x60 shop at the company’s headquarters in
Gray. Comer maintains both Cat loaders and Cat skidder and all warranty maintenance on his Weiler cutter and skidder is done by
Yancey Brothers, Macon.
“In this area, Yancey has the best service-oriented people,”
Comer believes.
Comer buys his oil and fuel in bulk, 1,000 gallons at a time, from
Chambers Oil Co. Inc. in Mil ledgeville. He changes oil every 250 hours in woods equipment with Cam2 semi-synthetic 15W40, and every 20,000 miles in trucks. Today’s synthetic blends expand the service window and newer engines produce significantly less particulate matter. It’s one way Comer reduces costs.
“I changed oil every 10,000 miles for 20 years but with today’s oil it’s not necessary,” he affirms.
“Mack truck oil changes are every 45,000 miles or so now. Yesterday’s oil, yes, but (with) synthetic oil blends today, you don’t need to change oil and filters often.”
Outlaw Timber’s liability and workers’ comp insurance have been through Hawkins & Rawlinson since day one. The company also utilizes Safety On Site, Inc., which provides quarterly safety meetings. SLT
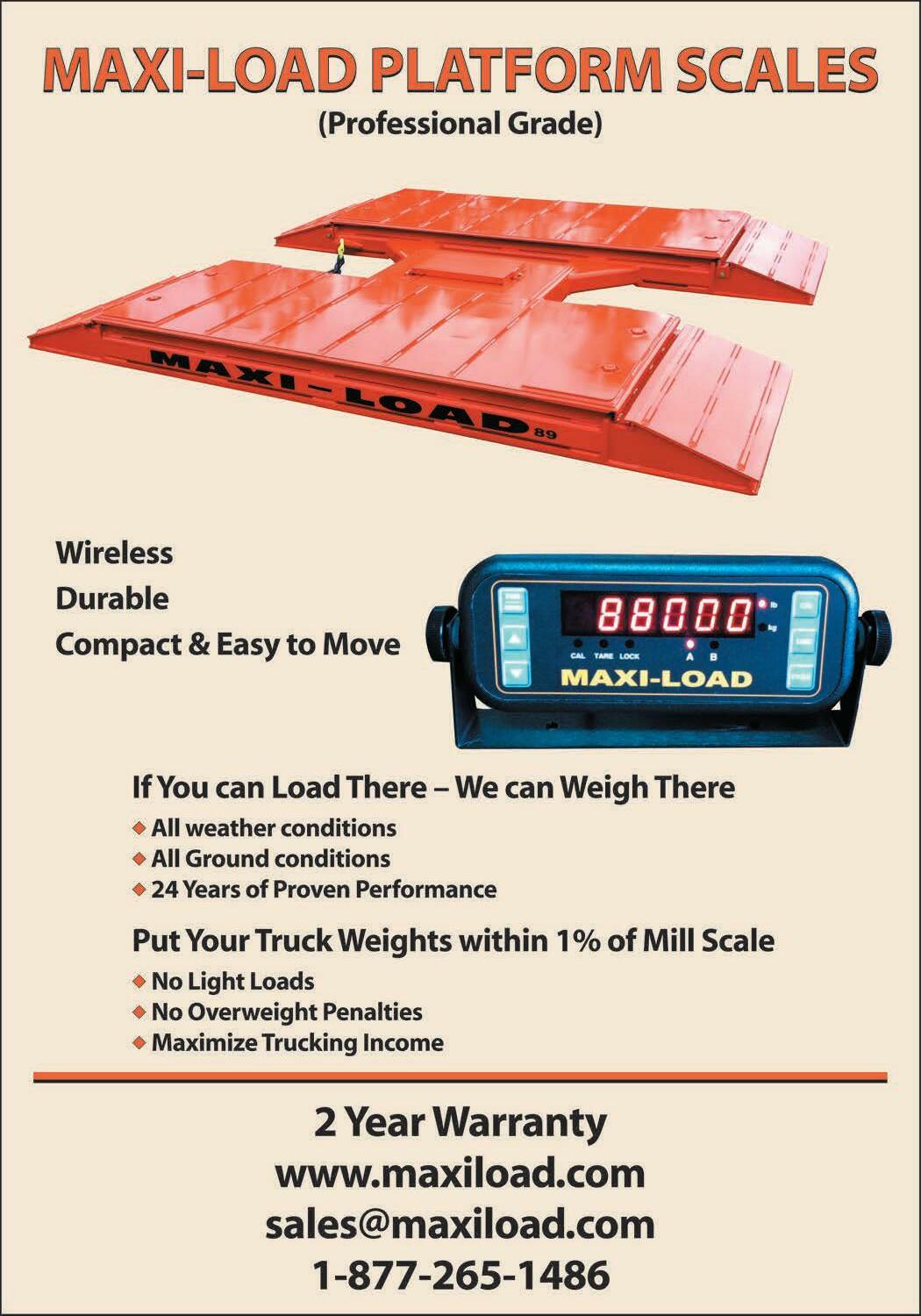

Always Something
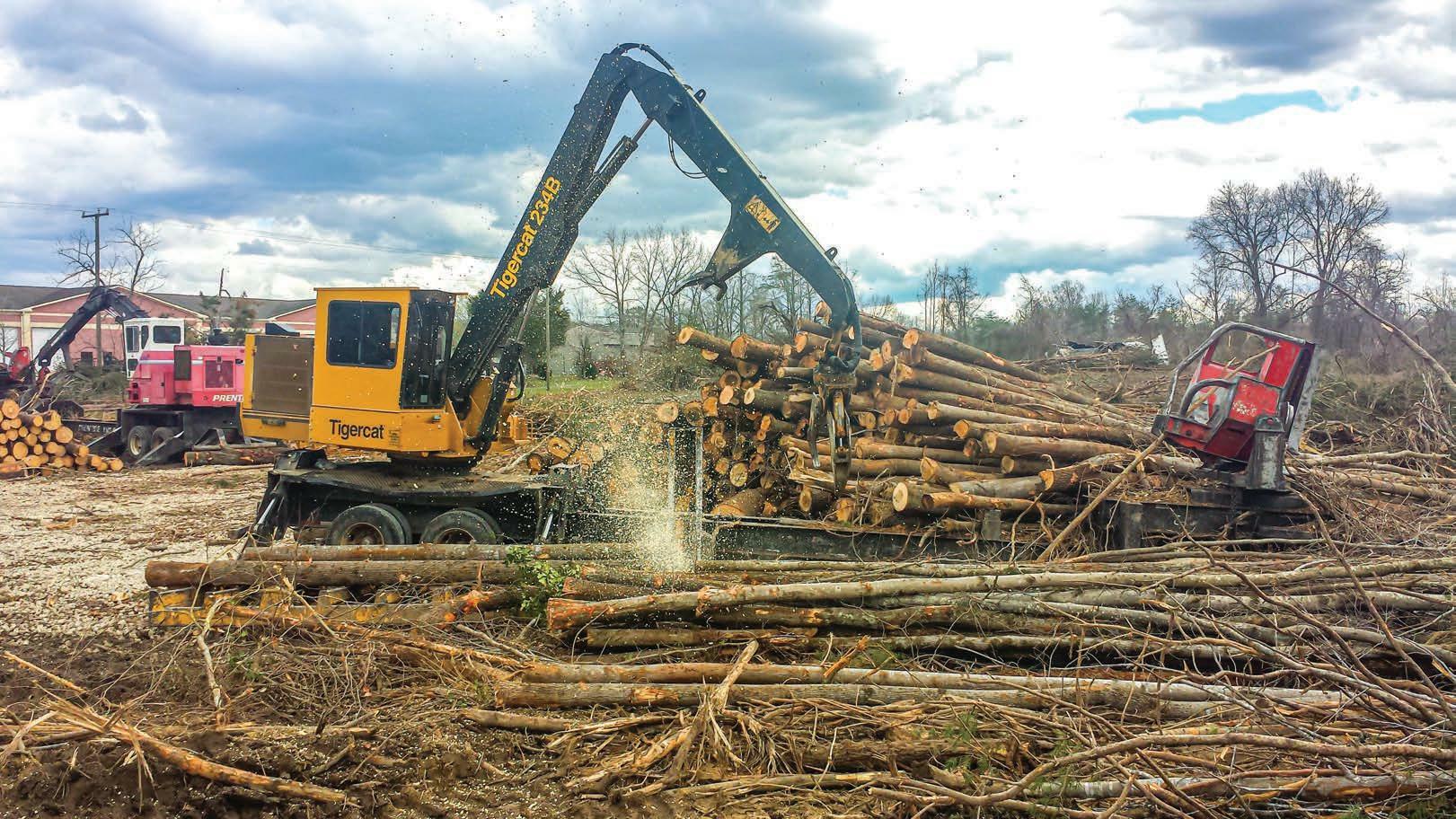
■ Contract trucker Phillip Brooks expanded his PSP Hauling into PSP Logging four years ago.
By Tim Cox
SPOTSYLVANIA, Va.
Phillip Brooks II is com mitt ed to his log ging busi ness. He is some what of a newcomer to the logging contracting business, but he’s no stranger to logging. Actually, he started out as a trucking con tractor, hauling logs, with one truck in 2013. He launched his logging business in 2018.
The name of the trucking business is PSP Hauling, and the name of the logging entity is PSP Logging. Those letters come from the first letter of his first name, and the first letter of the first names of his parents, Phillip Brooks, Sr. and his wife, Sonya. “I couldn’t have done it without my parents’ help,” the younger Brooks says. “It’s always been a team effort.”
His father retired after working for the federal government for more than 30 years. Described by his son as a jack of all trades, the elder Brooks, 69, helps the company maintain its equipment. “He keeps things run ning,” his son says.
His mother runs the office in their home and takes care of the ad min is tra tive side of the business.
The company has a wood yard equipped with a watering system to prevent logs from drying out, as well as a shop and office at his parents’ property in Spotsylvania. Brooks has four employees work ing in the woods and also a fulltime me chanic back at the shop who works on both the logging equip ment and trucks. One of his employees is a nephew, Montana Moody, who operates a skidder.
Spotsylvania is a county on the west side of Fredericksburg, which is situated about halfway between Richmond and Washing ton, DC. Brooks nor mally buys standing timber and tries to stay within 4050 miles of the com pany’s base. “We try to stay as close as possi ble.” A typical job is about 75-100 acres in Spotsyl vania or the neigh boring counties of Orange to the west, Stafford to the north, or Caroline to the south.
PSP Logging has worked as far away as Chesapeake, about 150 miles away in the Hampton Roads region. Brooks has a cou ple of jobs coming up, one closer to Wash ington and one in Maryland.
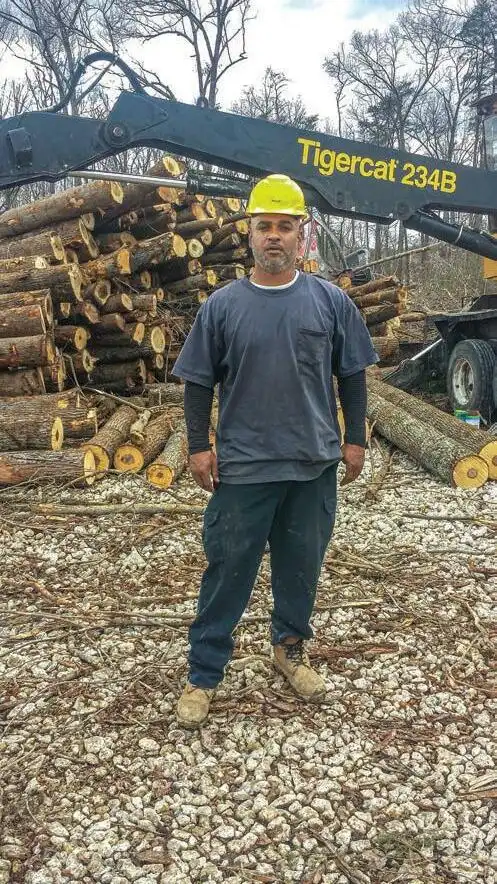
Phillip Brooks II
Coming Up
Brooks grew up on a farm. He started his logging career when he turned 18, working for Mid At lantic Tree Harvesters, a con trac tor in central Virginia. By the time he started PSP Logging, he al ready had about 15 years of ex perience working in the woods. When asked why he started PSP Logging, he puts it simply: “Make more money.”
PSP Logging performs clearcuts and select cuts. “We cut big hard wood,” Brooks says. “That’s what we’re known for.” He doesn’t com pete for pine. “There’s not enough money in it. We like doing hard wood.”
He gets jobs with hilly ter rain and soft bottomlands. “It’s al most impossible to get out,” Brooks says. “I don’t get the easy ones.” It’s timber other con trac tors don’t want.
When Southern Loggin’ Times visited Brooks, the company was working on a job of 37 acres in
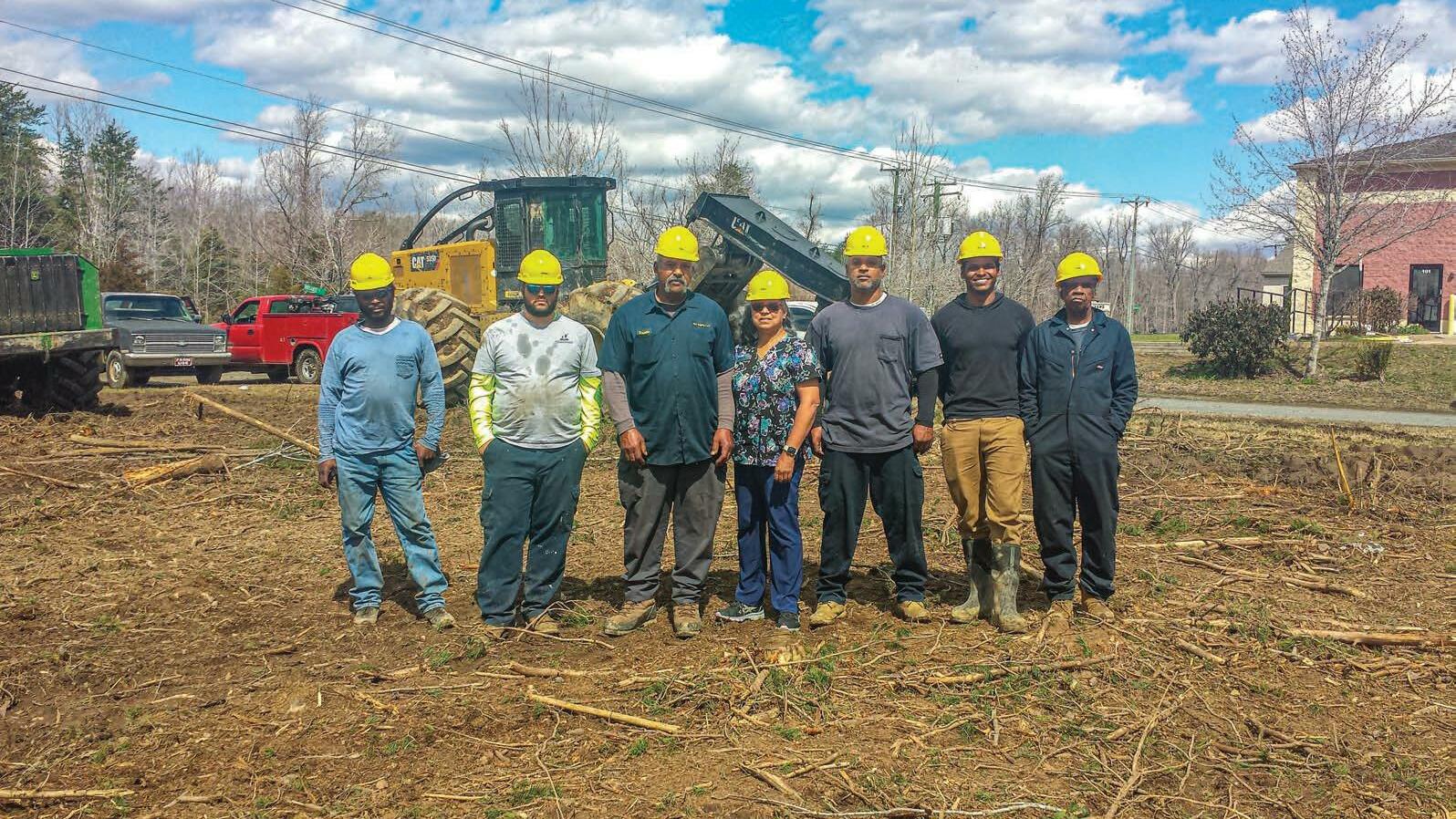

Staf ford adjacent to U.S. 1. The tract con tained white oak, poplar, and Vir ginia pine. The job was producing about 60% pulpwood and 40% sawtimber, he estimates.
Pulpwood, both hardwood and soft wood, normally goes to the West Rock paper mill in West Point, which is at the head of the York River and represents a haul of 75 miles from Fredericksburg. Sawlogs are sup plied to mills in Spotsylvania, Orange and Caroline, and also Culpepper, which is north. Brooks also supplies grade hardwood logs that are bound for export and buys additional logs for that market.
Equipment
The company is equipped with a mixed fleet of logging machines. It has a John Deere 643K fellerbuncher (and another spare machine); two grapple skidders (a 2018 Cat 535D and a John Deere 848H); and a pair of loaders (a 2020 Tigercat 234B and a 2014 Prentice). Brooks also has a Case bulldozer for building roads and landings and a Cat 559C loader with delimber and ground saw at his wood yard.
The crew—Robert Holmes, Ken dall Lanpher, Elisha Parker, and Moody—is cross-trained on the equipment and used inter change ably to operate machines. The only exception is Moody, who is still dedicated to operating the skidder full-time until he is trained on the other machines.
At the job in Stafford, the loaders were set up so that two trucks could be loaded at the same time. The loaders are matched with CSI DL 44 ground saws and CTR 426 pullthrough delimbers for processing the trees.
Brooks likes to try to have a trailer on the job at all times, ready to fill with a load of wood. “You can’t let up production,” he says, “even though it costs more to produce it.”
He likes to do 60 loads of wood per week, and that’s what the company normally averages.
PSP Hauling is equipped with West ern Star and Kenworth semitractors and Pitts, Evans, and Kauf man log trailers. For trucks and trailers, he is not wedded to any particular dealer, although he has purchased seven Kaufman trailers directly from the company’s factories in North Carolina and South Carolina.
Currently Brooks is only running one of his seven log trucks, relying on contract haulers to make up the difference. The reason: a shortage of drivers. “It’s terrible,” Brooks says. Walmart is paying drivers $40 per hour, according to Brooks, who notes that small businesses like his can’t compete for drivers at those wages.
“We really rely on the contract haulers,” says Brooks, who has help ed some of his former drivers buy their own rigs.
He started the business by pur chas ing used machines, but has made some new purchases since. Going for ward, he plans to continue to invest in new machines. “Less down time,” Brooks believes.
Much of the preventive mainte nance on the machines is done at jobs in the field, and the crew performs it. The company’s mechanic services the trucks and also works on trucks for other contractors.
“We’re a lean crew,” Brooks says. If something breaks down, they all pitch in to get it running again. “We’re all versatile.”
For dealer service Brooks relies on Tigercat dealer Forest Pro, the com pany from which he purchased the Tigercat loader. Forest Pro has three locations in Virginia: Albemarle County, to the west, Charlotte Coun ty, to the west and south, and King William County, to the south and east, which is the closest one to PSP Logging and the one with which Brooks does business. He also purchased his Cat skidder from Forest Pro, while the John Deere machine was purchased from James River Equipment, which has multiple locations in Virginia and the Carolinas.
Business
Besides scouting timber, bidding on timber, and working with a land owner to lay out the next job and set up the deck, Brooks is hands-on. “I do whatever needs to be done,” he says. He runs the loaders a lot but also operates the cutter sometimes.
Brooks has enjoyed a measure of success. He just bought the land where he did his first logging job in 2018. It will be the site of a future shop and office.
Safety on the job is important to Brooks. He holds a weekly meeting with his crew. He uses those ses sions to review the work of the prior week, the plans for the current week, and to address any safety matters. “I’m proud to say we’ve never had an accident,” he says. “We try to be safety conscious.”
He is well aware of the risks and danger of logging. “I’ve seen a lot of bad stuff happen on other logging jobs,” Brooks says. “I try to be proactive.” When he is on a job site he is constantly watching the crew and how they work to correct any safety-related issues. “I’m watching everyone all the time,” he says.
Brooks has been trained and certi fied under the Virginia Forestry Assn. SHARP Logger program. He is a member of that association and also the Virginia Loggers Assn. and attend ed the loggers trade group annual meeting in Roanoke last year.
Brooks calls the recent spike in fuel prices “ridiculous.” At the time he talked with SLT, he was paying $3.50 per gallon for off-road diesel – $5.05 delivered to his shop. Diesel fuel for trucks was at $4.98 per gallon but had been as high as $5.49. “That’s what hurts the most,” Brooks adds. “When that fuel goes up, everything goes up with it.” On the day when SLT visited his job, Brooks was waiting to hear how much of a surcharge one of his mills was going to pay to help offset the high fuel prices.
Asked what he likes to do when he has free time, Brooks says he enjoys traveling, whether he can get away for a few days or a week or more.
One gets the impression he doesn’t get away very often, though. Brooks works 70-plus hours a week, he estimates. “I work every day. There’s always something to do.”
He adds, “I like to log,” and des cribes himself as a workaholic.
SLT visited his job on a Friday. The PSP Logging crew knocks off for the week at lunch time each Friday—but not Brooks. After the crew left, he was planning to climb in the cutter and fell some more timber. Like he says: There’s al ways something to do. SLT
Moving forward, PSP Logging is investing in new machinery.
PSP team, from left: Robert Holmes, Kendall Lanpher, Phillip Brooks Sr., Sonya Brooks, Phillip Brooks II, Montana Moody, Elisha Parker
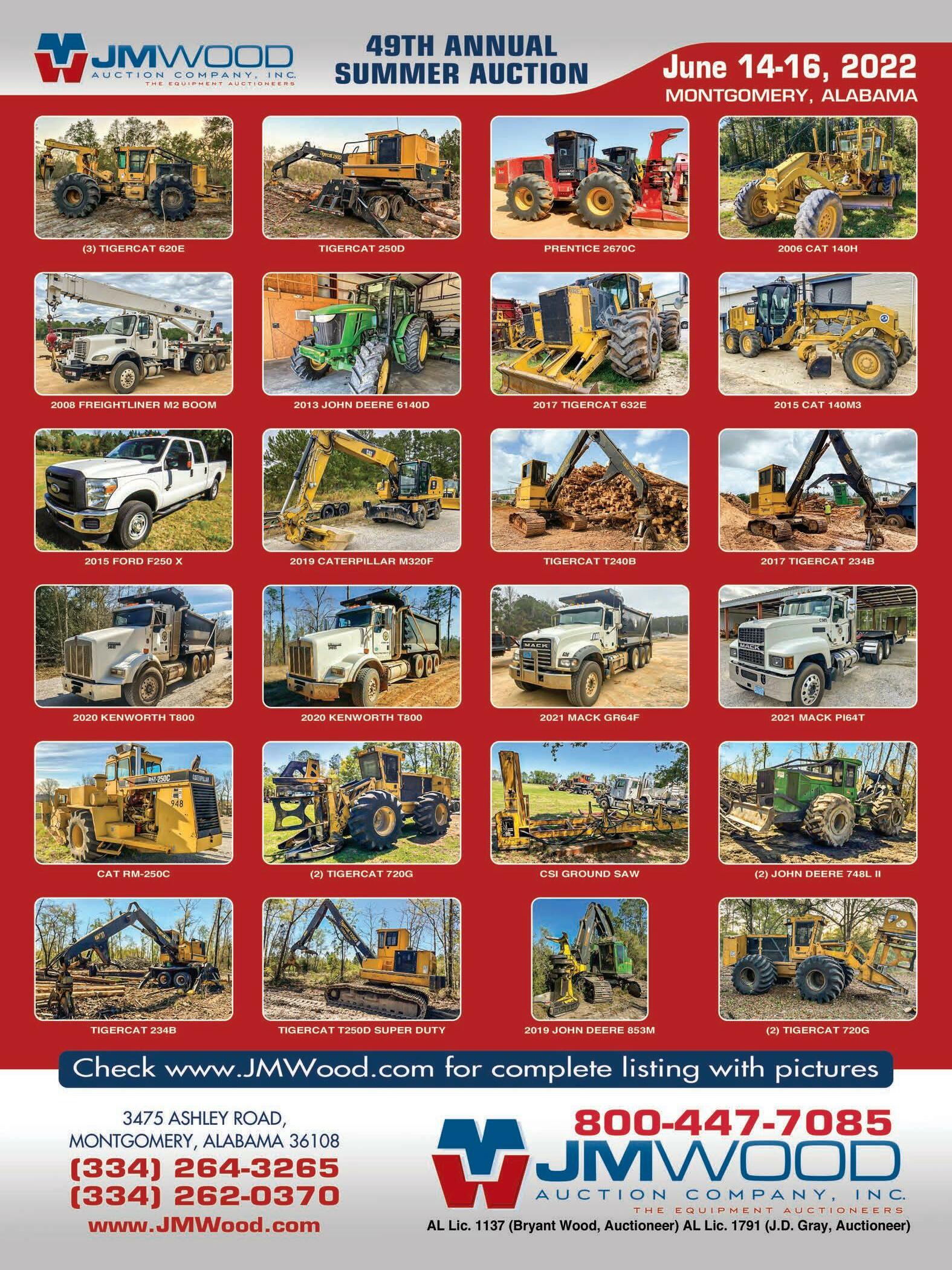
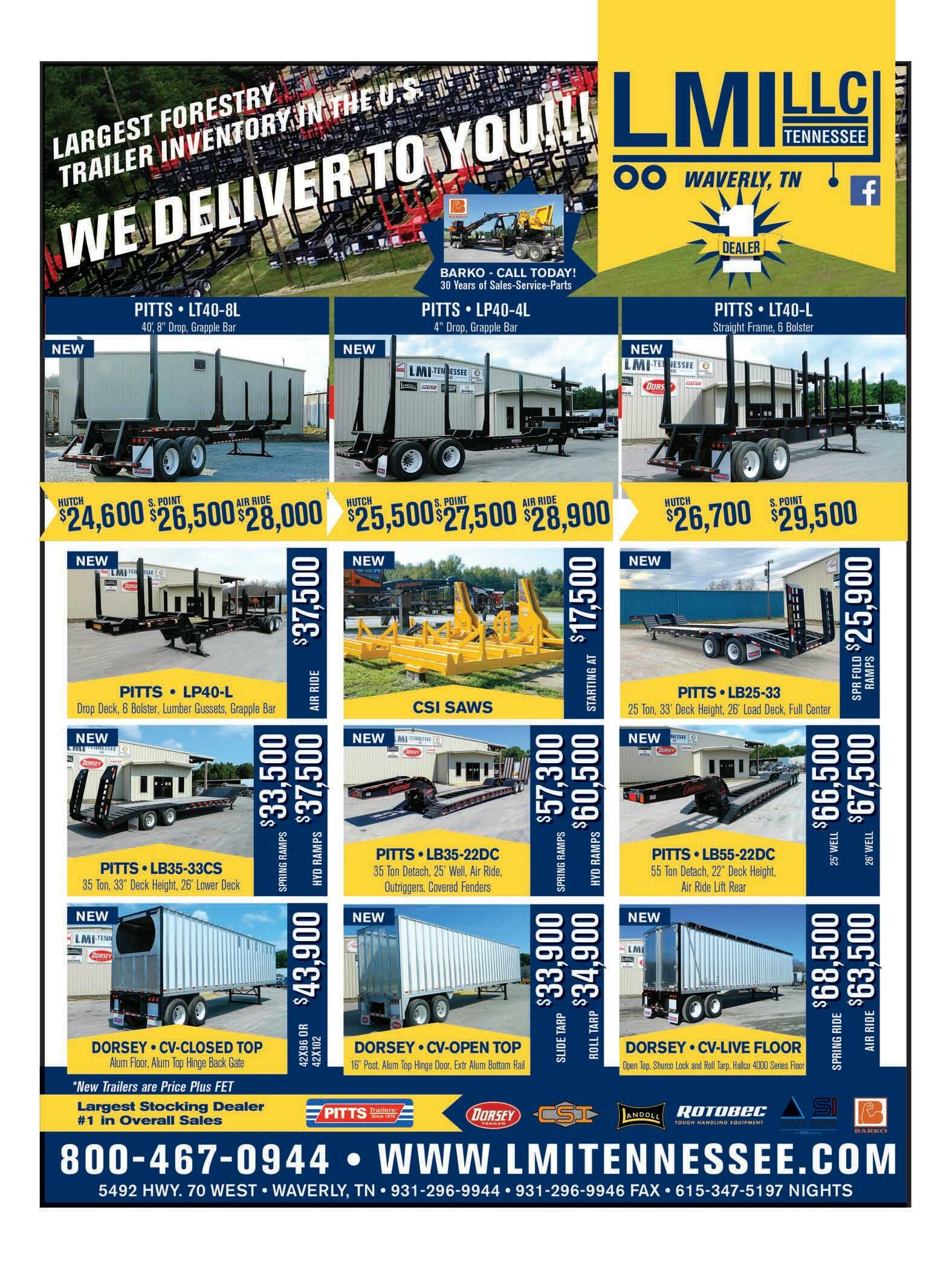
Bright Side
■ Randy Broadway was the Outstanding Louisiana Logger for 2021.
NOTE: This article previously ran in the September 2021 edition of Forests and People magazine, a publication of the Louisiana Forestry Assn., and the October 2021 issue of Louisiana Logger, the magazine of the Louisiana Logging Council.
By Jeff Zeringue, Media Specialist, Louisiana Forestry Assn.
PROVENCAL, La.
Spend a little time with Randy Broadway and you’ll quickly find out how much he likes to joke around. At a logging site, he likes to keep things light-hearted, but he also is serious about his business because he knows it’s not just about him. That joyful attitude, dedication to doing good work and the will to help others through a giving spirit has culminated in Broadway and his company, R&B Logging, being selected Outstanding Louisiana Logger for 2021.
The Provencal Master Logger has been in business for a quarter century, but before then he was working logging jobs for other logging companies. It’s a profession he’s loved for many years. “I just enjoy going out in the woods,” Broadway says. “You feel like you’re free.”
Bruce Colclasure, production manager for Walsh Timber Co., says he enjoys working with R&B Logging. It’s a family operation, typically fun to work with on any job. “They do an excellent job on big timber but they clear-cut, any type of job, really,” Colclasure says. “They’re a pretty diverse kind of operation.”
Tom Leone agrees. Leone hauls wood for the Broadways through a contract hauler. He went to work for R&B Logging when they had trucks 16 years ago. After trucking costs led to the use of contract trucks, Leone continues to haul for the Broadways through the contractor. He’s 83 and has no plans to quit now.

Family Affair
Randy works with two of his brothers: Terry, who operates the feller-buncher, and Gary, known as “Boo-Boo,” who is also co-owner of R&B Logging.
Like most loggers, Randy is in the woods when the sun rises, a sight he especially loves about his job. Another aspect of his job that makes it enjoyable is working with family, he says.
“It’s good to have brothers to work with you,” Broadway says. “Sometimes you have problems, but
we work them out.”
Terry Broadway says he has been in the woods since he was 10. He’s 63 now. For the past 11 years, he’s worked with his brother after working for other loggers in the area. He says he enjoys it.
“If something comes up, I can take care of it,” Terry says. “I know what I have to do every day.”
Sometimes taking care of things means taking care of himself. Terry says he has diabetes and had a difficult time fighting through the coronavirus. His brother allowed him to take the time he needed to get well. “I’d do anything for my brothers,” Terry says, “and I know they’d do anything for me.”
That doesn’t mean each won’t dish out ribbing and joking with each other. Randy Broadway says you have to be prepared for it. “They love picking on each other; not only them, but I pick on them, too, especially if they think they have something on you, they’ll pick with you about it,” Randy says. “That just makes the day go better.”
The three Broadways have had quite some time learning to work with each other, Randy says. They did it growing up with three other brothers. In addition to working together, each knows what’s happening with the others’ families.
“We talk about everything going on in your family,” he says.
Some things that are good for siblings to talk about, however, are also difficult. On the day Broadway was interviewed for this story, his father, Peter Broadway, Jr., known to everyone as “Junior,” was gravely ill. In the mornings preceding the elder Broadway’s death, Randy would talk with his brother Terry as they rode to work. At the logging site, “Boo-Boo” joined in the conversation and all three shared memories of their father or how he might have been that day. “Sometimes it’s hard to talk about your dad, like he had a rough night last night,” Randy says. That night, Junior Broadway passed from this world.
Family is also what keeps R&B Logging going. Randy’s wife, Becky, runs the office. “Our office is set up in our home, so I do the office work in our home,” Becky says. But she’s not alone. The couple’s daughter Shanna helps her mom with the necessary duties to keep a small business going. “You’d normally think a small business doesn’t take that much to operate, but you’d be surprised by what it does take, and everything you have to keep up to date,” she says. Shanna helps out with payroll or “whatever else Daddy needs me to do.”
Before working in the family business, she was a registered nurse. “(Working in the family business) helps me to be with my children,” Shanna says, adding that her sister Hannah also helps out.
Randy and Becky Broadway
Faithful
The Broadways are quick to admit that the logging industry has its ups and downs, just like most industries. But the family has risen to the challenge and is thankful for what logging has allowed them to accomplish. They fully understand that the business isn’t just about the Broadways.
“If you’re just looking out for yourself, you just as soon hang it up because logging is for everybody,” Randy says. “You look down the line, you’ve got seven or eight families you’re helping. They’re making a living, too. I
thank the Lord He can provide for them and help them out.”
Broadway’s generosity is one of the things Shanna admires about her father. Shanna also admires her father’s ability to look at things positively, like the time Becky needed a new liver. The family rallied around the matriarch and Shanna was to donate part of her liver to her mom. While going through tests to determine if she would be a suitable donor, the younger Broadway learned she was pregnant. That meant she could not help to save her mother’s life.
Randy’s faith (he is a deacon at the Provencal Free Methodist Church) and positive attitude carried his daughters through the difficult time.
“He’s always so optimistic; I love that about him,” Shanna says. “I can always call him and he’s an encourager, no matter what is going on, he knows we can get through this.”
That encouragement lifted Shanna’s spirits. Soon, the Broadways would learn that a donor had been found and she would have to get to Baylor University Medical Center in Dallas as soon as possible. The call came on a Sunday when the Broadways were in church.
“It was a touchy situation, but the Lord provided for us and I thank Him for that,” Randy says.
A quick trip to Dallas and several hours of surgery later, Becky’s system was able to accept the organ and did very well, but that wasn’t the only medical challenge the Broadways had to work through.
“During our stay out there, we discovered my sister (Hannah) needed a kidney transplant,” Shanna says.
Another Broadway, another organ transplant and both are doing well. Six years later, they find themselves well enough to work in the logging business, and Becky is well enough to spoil her grandchildren. “We really, really spoil them,” Becky, whose grandchildren call her Gammy, says with a broad smile.
Randy, who is called Pawpaw by his grandchildren, admits he spoils them, probably more than he has spoiled his daughter. But providing for his family isn’t the only thing he considers when it comes to sharing his blessings with others. Broadway also participates in community fundraisers and contributes to St. Jude Children’s Hospital each year.
“There’s a lot of needy people out there and I’m just thankful we can help,” he says.
As for the joking, that, too, will continue at work and home. Shanna says she has picked on her parents almost as much as they’ve picked on her. “Poor Mama, sometimes she just gets caught in the middle,” Shanna says.
That seems to be the way it’s always been, even as the young couple was starting out. Becky recalls how Randy pulled the old watch the coin flip on the water bottle trick. Becky ended up with a face full of water. "And I fell for it," Becky says as she and Randy erupt with laughter. "That's what's bad. Thank God we were married. If we had been dating it might have been a different outcome."
For now, the Broadways will continue to log, to pick on each other and to be an important part of the Provencal community. SLT
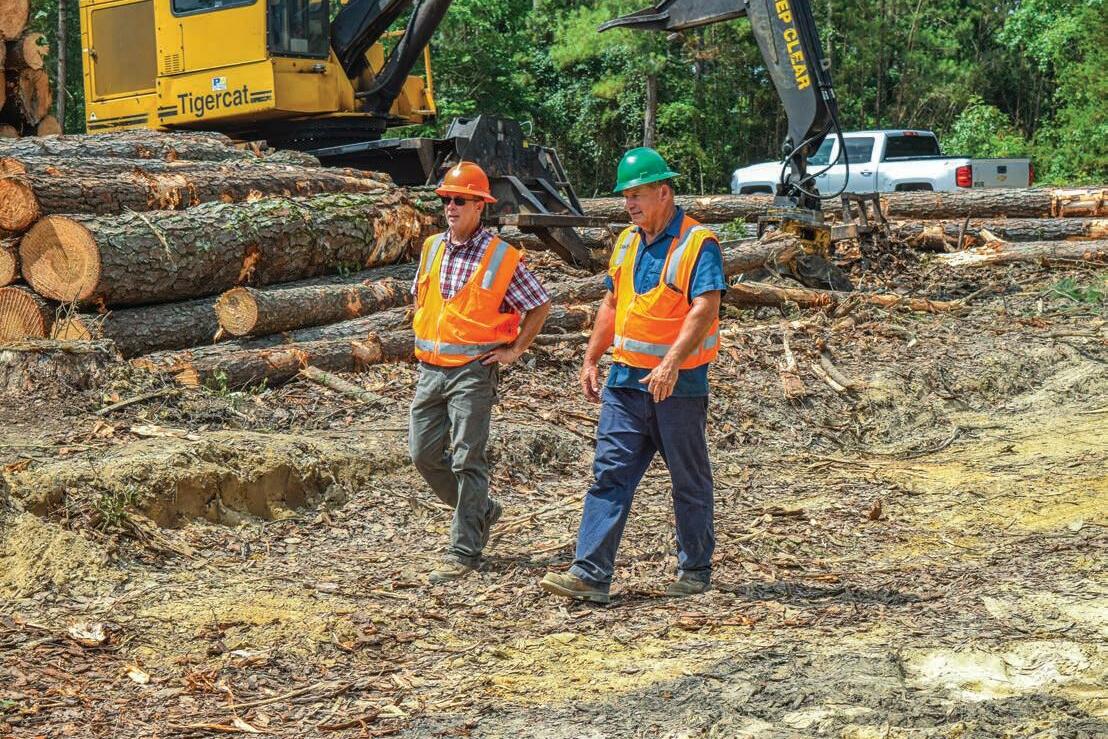
Randy, right, with his brother, Terry, left Randy Broadway, right, with Bruce Colclasure, Walsh Timber forester, at left
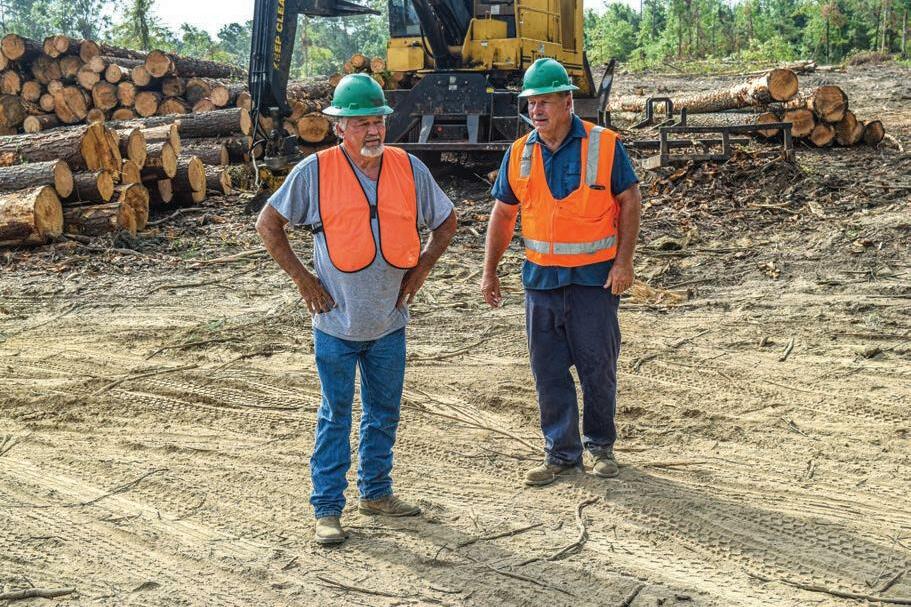
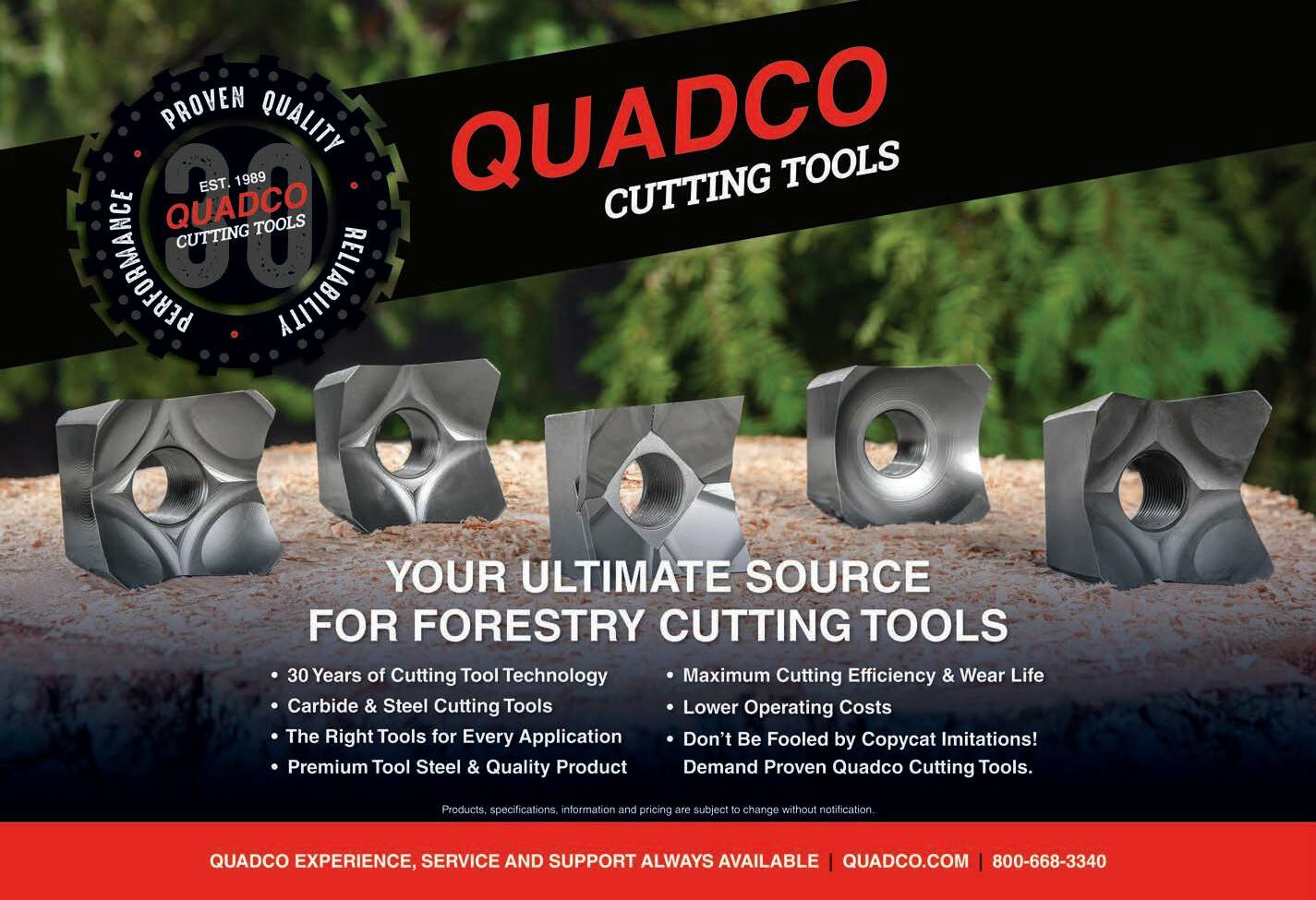
Tomorrow’s Timber
■ Adam Mizell looks to the future, with a focus on reforestation.
By Steve Werblow
EDITOR’S NOTE: This article was written exclusively for Southern Loggin’ Times by Yokohama Off-Highway Tires America, Inc.
CALLAHAN, Fla.
Every day, Adam Mizell and his crew at Mizell Development, Inc., plant the seeds for tomorrow’s timber harvest. After earning a forestry degree from Lake City Community College and building a business specializing in logging roads, Mizell found himself doing more and more site prep contracts. He discovered that he was drawn to the reforestation side of the timber industry. After a little over 10 years in the reforestation business, the Florida Forestry Assn. named Mizell the Silviculture Contractor of the Year for 2016.
“I’m a farmer at heart,” says Mizell, who represents the fifth generation of a poultry producing family. “I have no doubt if I lived somewhere else, I’d be growing corn or soybeans.”
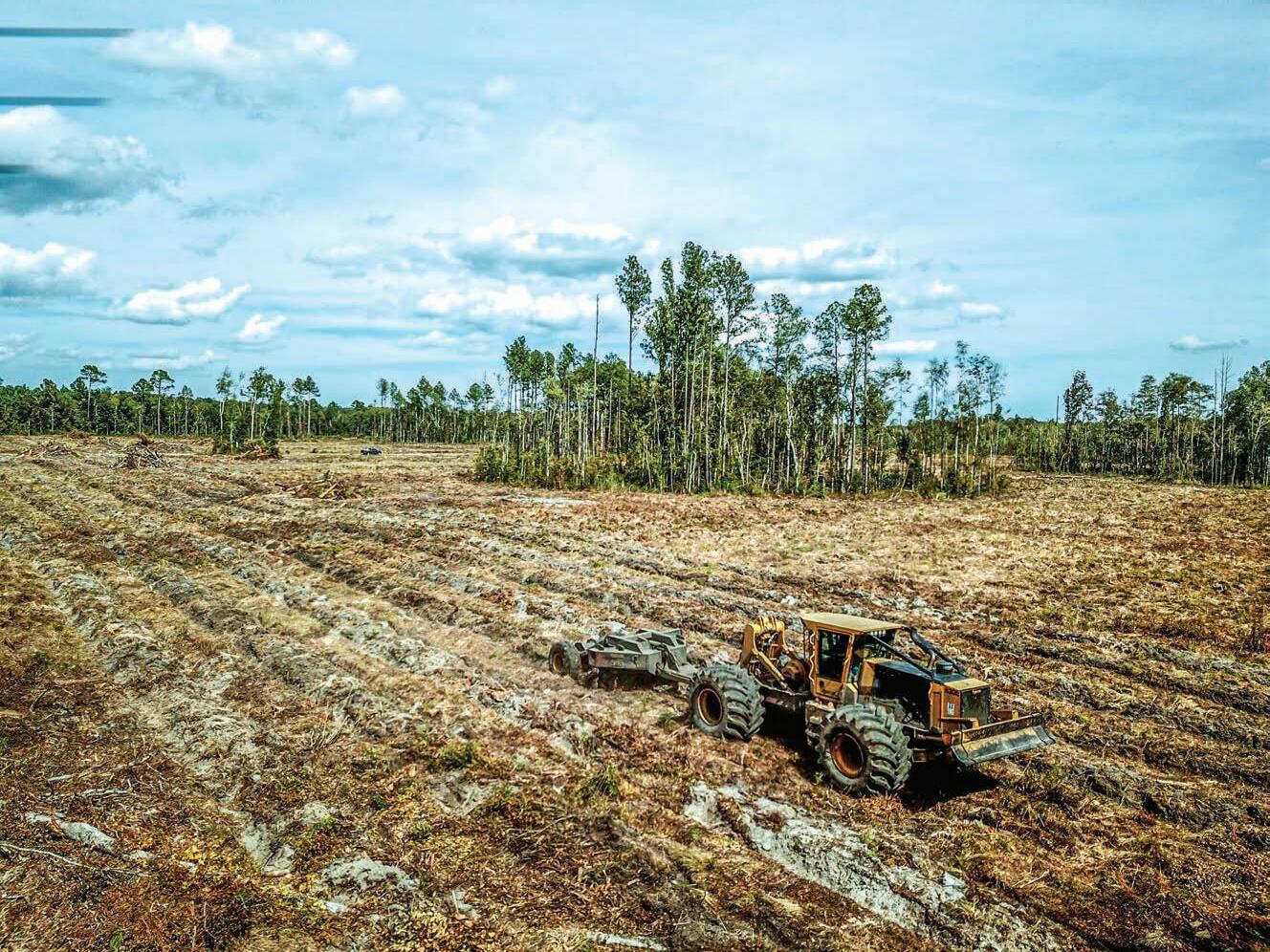
In The Field
On a fall day on a cut-over softwood site outside of Callahan, Fla., one of Mizell’s Tigercat 630E skidders was pulling a 20,000-lb. Marden Industries drum chopper, pre paring the ground for a stand of slash pine. Mizell’s skills in site preparation will put that land on the fast track to its next timber harvest, helping make Southeastern logging even more sustainable than ever. In 15 to 20 years, the trees on this parcel will be ready for the pulp mill; in about 30 years, the landowner will have a rich stand of saw logs.
Site prep and replanting can account for as much as 20% of a timber harvest budget, so reforesting a site is a major investment for landowners—but it pays off. A University of Georgia study documented the benefits of replanting versus natural regeneration: slash and lob lolly pine replanted into prepared land had twice the growth rate— 5.85 tons per acre per year vs. 3.0— and greater economic returns than naturally regenerated stands of the same species.
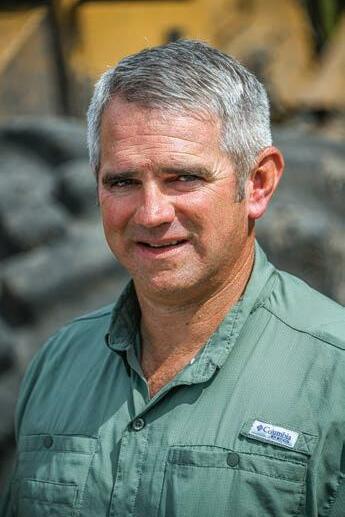
Forming beds for the next generation of pine forest is farming on a huge scale, Mizell says.
Head Start
The reforestation process starts with a herbicide application soon after logging has ended. Mizell likes to let a clear-cut sit for about a year before site prep, giving some of the debris a chance to start breaking down, but he says he and his team are often chopping within a few months. Large stumps with a lot of heartwood can be sold to an explosives manufacturer, but the stumps are generally chopped to fertilize the next generation of trees.
“Chopping softens the soil so that the new roots can grow vigorously throughout the bed,” Mizell says. “You want a chopper with good, long blades so it will get down there and break up the lateral roots on the residual stumps and split the residual stumps as much as possible so it en courages the breakdown of all those things. The pine needles, the palmettos, the gallberries, all that gets broken down and folded into the bed and serves as nutrient and organic matter to help the new seedlings get ahead.”
Mizell follows chopping with a Fleco root rake, originally designed for wheel loaders and modified by Stokes Welding to fit Deere or Tigercat feller-bunchers. On the Callahan project last fall, a Tigercat 720G piled debris too big for the drum chopper to break up.
“Feller-bunchers make a fantastic raking tractor,” he explains. “We’ve used wheel loaders and dozers in the past, but the undercarriage cost is prohibitive. You have to guard them up with forestry packages, and sticks still get in there and break things. A feller buncher is made from the ground up to be protected from debris and logs and sticks stabbing up through the machine. They were engineered for this application, and you can get bigger tires on them.”
Mizell uses a variety of equipment, including both Tigercat and John Deere machines, and works with dealers Tidewater Equipment Co. in Brunswick, Ga., and Ring Power Corp. in Jacksonville, Fla.
Reforestation contractor Adam Mizell
Pulling Beds
The final step in land prep is pull ing beds, which Mizell forms with Savannah Global Solutions bedding plows pulled by Deere or Tigercat skidders in the 250-to-300-horsepower range. “They have the strength to pull through without having to gear down,” he notes.
About half of the sites Mizell prepares for planting are on beds 12 ft. apart on center. The rest range from 11 to 16 ft. on center, depending on soils and the foresters’ plans for stand density. Drier sites can be bedded in a single pass. On wetter ground, Mizell prefers to build the beds higher—about two feet from the bottom of the furrow to the top of the bed—with a second pass.
“It’s so flat here we get ponded water,” Mizell says. “None of it is very deep, but it will stagnate the tree’s growth if it’s just sitting in sour water.” Mizell’s work in the 150-mile radius around Callahan falls mostly in the heavy soils of the Okefenokee Swamp region.
In January or February, crews come through to plant seedlings. Mizell says 95% of the trees planted on the land he prepares are slash or loblolly pine, and the other 5% are longleaf pine. With a skilled crew and bareroot or containerized seedlings, Mizell says stand survival can be 98% or better.
Gearing Up
Mizell attributes successful site prep to simple factors. “Having goodquality equipment with good tires and a good man running it—that’s the key,” he says. “What makes a good contractor is someone who does what he says he’s going to and follows through with it, who has good equipment and good people on his team to make good on that.”
Mizell points out that horsepower is critically important, but so is making sure that all the horsepower reaches the ground.
“Tires are extremely important to my business,” he notes. “Our tires aren’t as susceptible to torque or puncture as a logging tractor be cause we’re not toting out the weight of the trees. All we have is the weight of the tractor and the tread of the tire—so if I don’t have good tires, I’m just spinning in place.
“Most particularly, when you’re pulling beds and your tire spins, the tractor sinks down some, then that makes the disk sink down some, and it becomes a tougher pull on your tractor,” Mizell explains. “So now the tractor’s dug itself into a hole it’s trying to climb out of, and that takes more fuel and horsepower—and if you don’t move on, you’re stuck.”
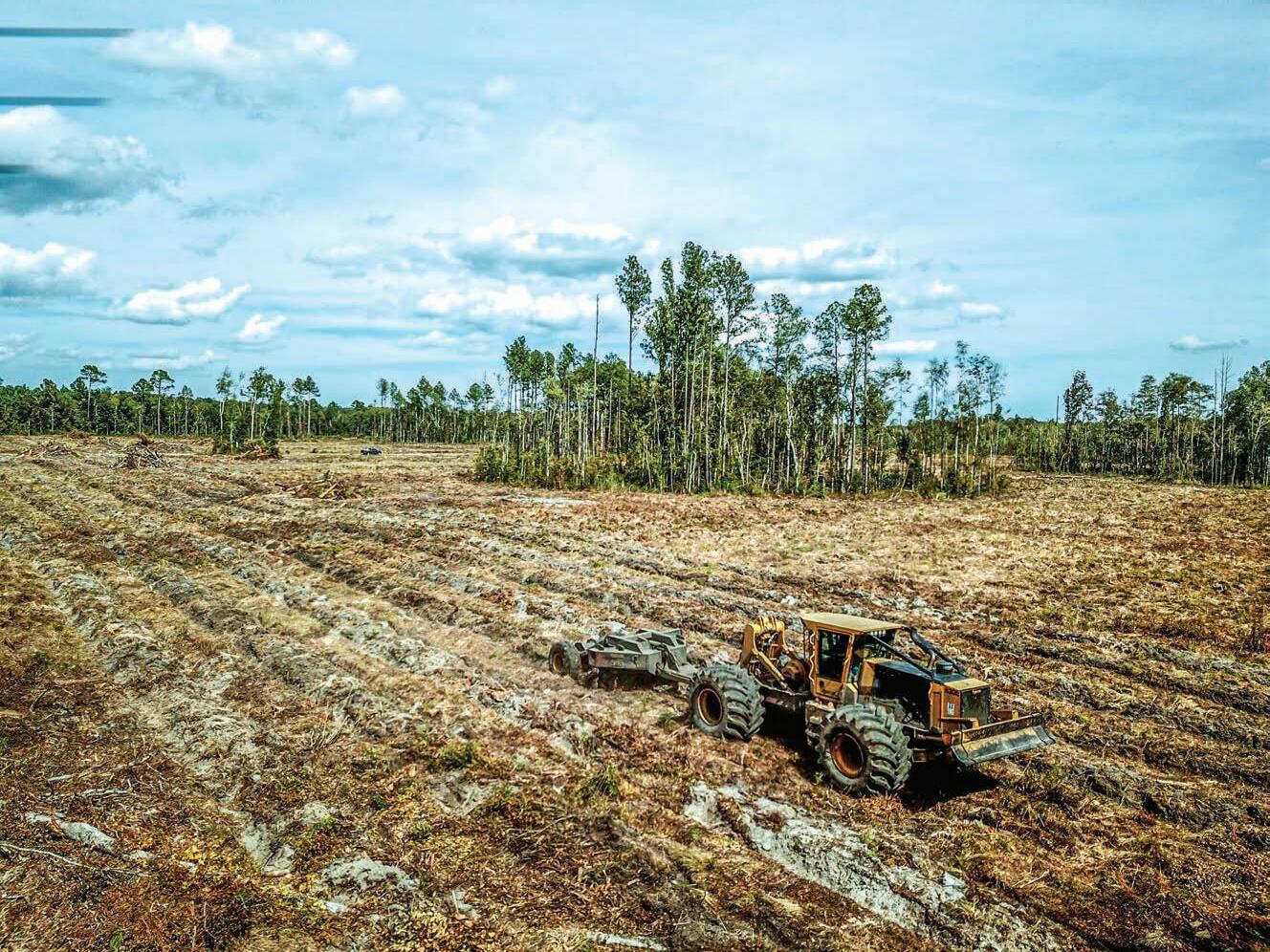
Bedding often takes two passes. Pulling a huge bedding plow takes horsepower and traction.

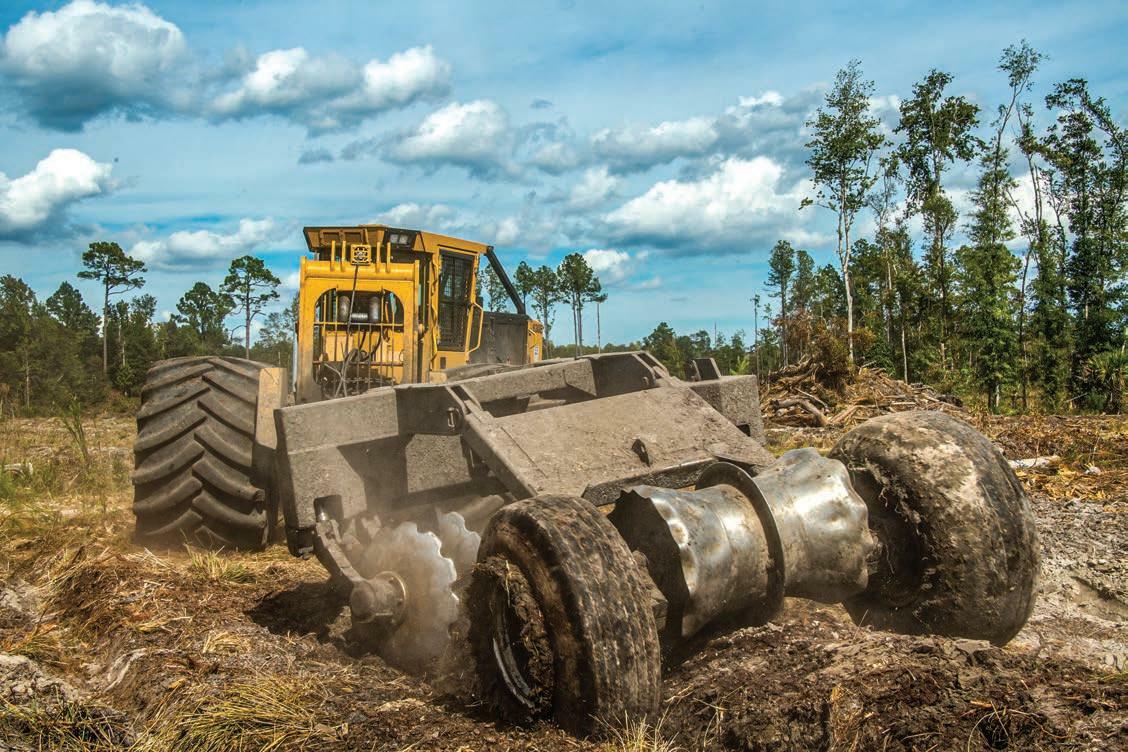
Deep Tread
Years of trial and error, and the evolution of logging tire design, led Mizell to Primex Log Stomper Xtreme tires. The 82/32” depth and wide construction of the tires’ curved lugs had instant appeal, and the durable compound reaffirmed his choice.
“They’ve got a thick, deep bar, which makes a lot of difference,” he says. “I try to stay on the new side—the first 50%—of a tire. I can have 3,000 hours on the Primex Xtreme and it will still have a bigger bar than other tires. In my business, if your tires start to get bald or worn down, they’re fine when you’re on dry ground, but we’ve got to work the whole field: the good, the bad, or whatever. You’ve got to have what it takes to get through those wet areas. We don’t want to leave those acres out, because they’ll grow a tree.”
Most of Mizell’s tires are standard 30.5 and 35.5 widths, but in some wet ter ground, he has experimented with 73x44.00-32 Log Stomper Xtremes. He says the extra wide tires have provided both better traction—helping his operators work swampy areas that would otherwise have to be bypassed—and better flotation, which minimizes soil compaction to maintain a healthier root zone for seedlings.
“A 300-horsepower skidder, whether it’s a John Deere or a Tigercat, is a heavy tractor,” he points out. “I needed more flotation and hoped to achieve a little more traction, and I think I got both things.”
Thin Margins
Mizell points out that, like every aspect of the logging business, reforestation is tougher than ever. “It’s all about efficiency nowadays,” he says. “You can be inefficient. But you just won’t be inefficient for very long.”
The name of the game is working more acres at thinner margins, and keeping crews active all the time.
“I look at labor as a fixed cost,” Mizell says. “If you’re going to have good people, you have to pay them consistently. If you send them home, you can’t blame them for looking for something else. You’ve got to keep them working. And if they’re out working, they have to be able to do the job. If they’re stuck, just sitting there spinning in place, they might have to get on the lowboy and leave and then come back later. We don’t get paid to move back and forth— that’s counterproductive.”
In the end, Mizell sees the results of his investments and his people in the tall stands of pines stretching through north Florida and south Georgia—tomorrow’s timber growing straight, tall and fast.
“I still have to be competitive,” he says, “but I always think first, ‘this is what we need to do the job right.’” SLT
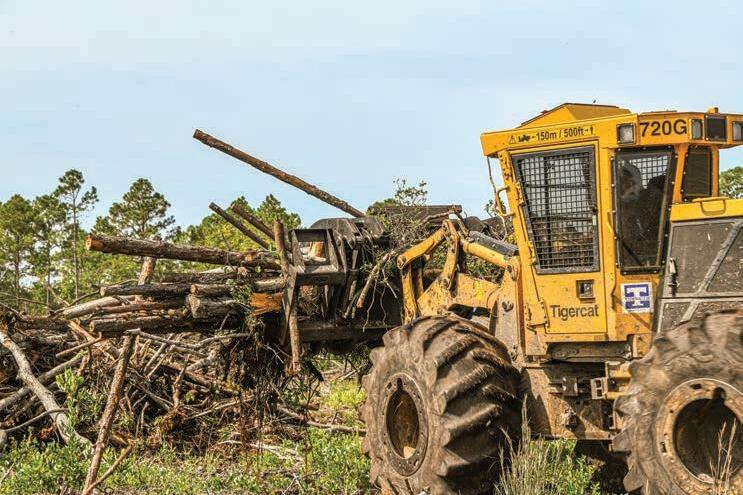