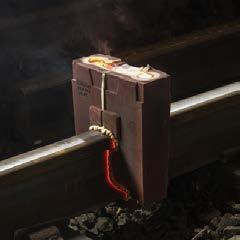
5 minute read
Pandrol Advanced Welding
Tyne and Wear Metro, Newcastle, United Kingdom
The Tyne and Wear Metro in north east England is a light rail network that covers over 48 miles and serves a total of 60 stations. Owned and operated by Nexus, it serves as the rapid transit system linking South Tyneside and Sunderland with Gateshead, Newcastle, North Tyneside and Newcastle Airport.
Advertisement
As part of renewing rail in a tunnel on the metro system, Nexus needed 140 aluminothermic welds to be completed in a tight timescale. Possession times were short, with access to the track from 1am to 4am, Sunday to Thursday.
Railway contractor GPX Engineering was appointed to deliver the welding services, including inspection and certification. Teams of welders began work using the Pandrol PLA one-shot crucible welding process.
Pandrol Solution
With work already underway, Pandrol approached GPX and suggested that its new Advanced welding process would provide a particularly effective solution to help meet the time challenges of the Nexus project. Having looked at the process in detail and having carried out a risk assessment that showed a reduced level of risk, GPX and Nexus agreed that Pandrol Advanced should be used for the remainder of the project.
Pandrol Advanced brings together innovations at every step of the welding process to save time and improve safety, ergonomics and weld quality. A small team of welders working on the Nexus project were trained over two days by Pandrol and then supervised on site while they cast their first welds using the new process.
Aluminothermic welding traditionally involves luting – sealing moulds to rail ends with paste or sand to avoid metal leaks. With Pandrol Advanced, the luting process is replaced by AutoSeal, the world’s first self-sealing mould. AutoSeal comes with a built-in insulation joint that expands during pre-heating to create a tight seal when fitted onto the rail. This brings five key benefits: • It saves time – at least five minutes per weld, as sealing the mould is automatic and there is no need for the luting procedure. • It makes sealing more reliable – especially in cold weather and tight spaces. • It reduces the defect rate – by facilitating moisture evacuation during the preheat. • It is environmentally friendly – reducing plastic waste and saving the energy needed to transport traditional luting material. • It promotes the welder’s health and wellbeing – with less time spent kneeling and reduced stress.
The self-sealing mould proved extremely popular with welders working on the Nexus project. ‘It’s quick, simple and saves time kneeling down on the track,’ explained Shane Jennings, one of the welding team. ‘The weld is clean and lines are defined, with no blemishes. Collar formation is spot-on every time.’
Rather than the large CJ2 crucible, the Pandrol Advanced process uses the smaller, CJ1 one-shot
The Autoseal Mould Startwel electronic ignition system

Using the Pandrol Connect Welding App
crucible, which is suitable for all standard gap and HWR welds (98.5% of all Pandrol welds cast in the UK in 2019). Pre-installed with a Startwel electronic ignition system, the CJ1 design makes it safer and easier to ignite the portion within the crucible. By using the CJ1 crucible as part of the Pandrol Advanced process, Nexus saved on waste, cost and transportation (the CJ2 is 2kg heavier and its traditional igniter is classed as explosives).
Further savings and efficiencies were achieved by: • the introduction of an improved cooling procedure that saves 10 minutes per weld • the use of a semi-automatic weld shearer to remove the excess weld, which has ergonomic lifting points for ease of use • changes to the internal mould design to create a fracture point so that the welder can simply hit off the vent riser with a hammer after 20 minutes, instead of having to use an angle grinder.
The whole Pandrol Advanced process is managed through the Pandrol Connect welding app on the welder’s mobile phone. Rather than recording data by hand, the welder inputs data into the app before, during and after welding. This is then reviewed by welding controllers and monitored from the office.
Results
The transition to the Pandrol Advanced process went smoothly on the Nexus project and the client, GPX Engineering and welders were all delighted with both the process and its outcomes.
The welds were completed during the allotted night shifts, on time and with no defects. An estimated 20 minutes was saved per weld – a considerable time-saving across the whole project. Using the Pandrol Connect app improved traceability and cut down on paperwork.
GPX Engineering and the welding team were extremely positive about the new process. ‘It’s much quicker and more efficient than traditional methods and the failure rate was zero,’ says Paul Marshall, Technical Lead at GPX. ‘Our welders loved it – in particular, taking out the luting procedure makes the welding process so much easier and less stressful. And there are clear safety benefits every step of the way. We will definitely use Pandrol Advanced again.’
Furthermore, Nexus were extremely pleased with the quality of service GPX had delivered: The customer service from GPX has been to a high standard – everybody I’ve been in contact with has been attentive and helpful.
Network Rail using innovative fibre-optic technology to boost railway safety and performance
Network Rail has awarded a contract to a consortium led by Thales Ground Transportation Systems Ltd to develop and trial Fibre Optic Acoustic Sensing (FOAS) technology that will support improvements in safety and performance on the railway.
FOAS technology will be enriched with data fusion to enhance the ‘listening’ capabilities of optical fibres, of which there are already around 20,000km running alongside Britain’s railways. The implementation of this technology – effectively creating a virtual microphone every few metres – has the potential to enhance remote condition monitoring of assets and provide valuable data to improve train performance and reduce disruption for passengers.
The awarding of the contract follows a Design Contest launched in November 2020, led by Network Rail in collaboration with Dutch rail infrastructure operator ProRail, which challenged over 40 suppliers of different sizes to come up with proposals for a funded 12-month outcome-focused trial of FOAS, IoT sensors and smart CCTV cameras, amalgamated through intelligent data fusion and processing. Companies were required to address four areas of operational challenges on the railway: • Train movement and position reporting • Rail and wheel defects • Level crossing safety management • Detecting trespass and people on the trackside
The trial work with Thales’ successful bid – featuring a consortium comprising SMEs to deliver different parts of the technology – will be conducted at Network Rail’s RIDC Melton test track, and on the mainline railway from Melton Mowbray to Leicester, commencing in Autumn 2021.