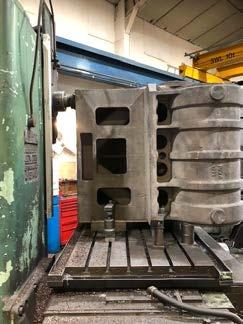
6 minute read
A Night Owl Emerges from the Dark Part 4 Paul Perton
Paul Perton, Marketer, Writer and Photographer
Activities and production of parts for 4709 continue to make significant progress in several key work areas.
Advertisement
Having finally achieved the casting of two 4709 cylinder blocks using polystyrene patterns, the castings have been stress relieved and delivered to a specialised engineering contractor in the Midlands for machining.
Even in this modern high-tech world of locomotive restoration and construction, the casting of new cylinders is one of the less common activities. That may well change, as locos saved from Barry - most now in their eighties - are showing signs of longterm wear and tear, especially cylinders which not only suffer from wear, but also other degradation processes like rust and chemical attrition.
The decision to cast new cylinders will largely be centred around the cost of wooden patterns and their cores. Pattern making is a highly skilled enterprise and given the complexities involved, high costs are a given.
On 4709, we re-designed the cylinder block to accommodate the modern requirements of mainline running and conformance to the NR loading gauge. We also investigated ways by which the use of a wooden cylinder pattern could become economic and significantly reduce the risk of a casting failure - thereby lowering the unit cost.
One line of enquiry was to review the pattern making process, to optimise the latest technologies. Another was to investigate the Swindon approach, whereby a standard cylinder pattern could be developed which had interchangeable sections to cover the maximum number of GWR classes.
New technology won the day, with the CAD-based design for the revised cylinder being used to cut two identical patterns in blocks of polystyrene. On completion, 4709’s cylinders will be bolted together to make a siamesed pair.
The positive benefits for other GWR locos needing new cylinders is now clear; much of the basic design work is complete, the technique of cutting the patterns in polystyrene is better understood with every new project and likewise, the casting process itself, more predictable and with outstanding results.
After heat treatment, our cylinder blocks have each been sent to a specialised machine shop. Here, they have been set up on a horizontal boring machine for a thorough dimensional check to ensure that sufficient metal exists where it is needed - in the past, unaware machinists have taken too much metal from one end to find insufficient remaining at the other.
Proven to be dimensionally correct and correctly set up, each cylinder then had one of its ends
(Above and Below) Machining the cylinder blocks

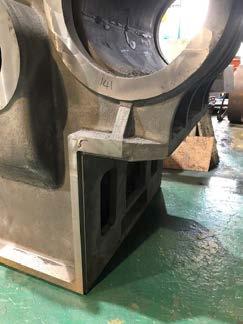
(Above) the machined cylinder block) (Below) some of the wooden patterns
machined flat, to establish a measurement datum. The castings were then stood vertically on this datum end and the bolting faces machined at right angles to the ends. The bolting faces were then used as a datum and work commenced on opening up the bores. 4709’s cylinders are currently just at this stage.
The next work package for 4709 is a set of new rear cylinder end covers. These are handed as the pressure relief valve boss changes sides and the angle of the gland box changes.
These are complex patterns and have been made in wood, which means that they can be used again and again for other classes and locos, as needed. The front covers are symmetrical and a very straight forward job by comparison. The covers are being cast as this article goes to press. The finished items being sent to the same machine shop as the cylinders, once completed.
The patterns for the compensating suspension arms are also complete and they too will be cast in the near future. These will require significantly less machining and will be ready to fit to the engine once the front end project is finished.
In other 4709 news, the July issue of the Model Engineer Magazine carries a very detailed article showing all that had to be achieved at the foundry to cast our cylinders.
This miniature world is full of excellent engineers who build locomotives, just in scales less than full size. We hope to work closely with the Model Engineer magazine and encourage readers and engineers of all ages to help us build 4709. There are tasks to suit everyone. Perhaps this will lead to young people electing to take up a career in engineering.
Machining the Cylinder Blocks
The machining of the two new cylinder blocks for 4709 is now well advanced at Roach Engineering at Brierley Hill in the West Midlands. As they are to be siamesed as a pair before installation in 4709’s chassis, the work is likewise being progressed
Great Western Star is available on subscription through the website - www.greatwesternstar.com
It is available on Facebook, on Instagram and Twitter.
Take Great Western Star with you wherever you go!
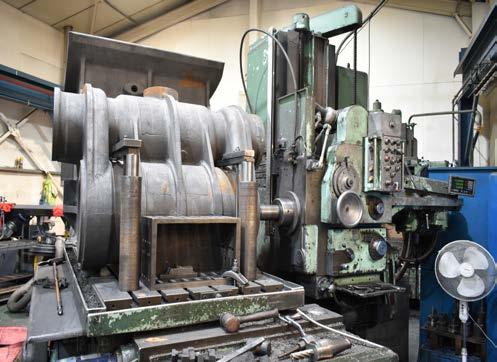
Machining the cylinder blocks at Roach Engineering Ltd
with both castings being machined sequentially in stages, in preparation for their joining.
This arrangement will ensure that machining operations are undertaken for each casting one after the other. With identical alignment for the first cylinder being used for machining the second, the team at Roach can ensure excellent dimensional repeatability, while saving significant time (and resources) by avoiding multiple set ups.
New castings for the front and rear cylinder covers are also in train and will shortly join the newly cast valve covers already at Roach. The work is progressing to programme with completion expected in early Autumn. The finished covers will then join 4709’s cylinders, ready for assembly.
Mounting the Cylinder Assembly into the Frames
The next step will be to mount the new cylinder assembly into the extension frames. This work will be carried out by and under the supervision of the Dinmore Manor Fund’s Mike Solloway at the Tyseley workshops. Mike lives in the Midlands and recently successfully fitted new cylinders to former GWR 2-8-0, 3850. His expertise with almost exactly the same process for 4709, will be invaluable.
The progress will see the front-end assembly offered up each of the extension frames and its
102
mating cylinder in order to ensure precise alignment of all the bolting holes.
Once achieved, the cylinders are then bolted together upside down; the mating faces having been treated with sealant prior to the join. The extension frames are then final fitted to their respective cylinders and all of the newly machined bolts finally fitted.
Only at this stage can the dimensions for the racking plate be measured, as it has to be installed to be a very ‘snug’ fit between the extension frames.
When done, this allows the racking plate/ extension frame angle to be accurately machined, requiring very precise measurement to achieve the required standard of fit. Once all the numerous and newly machined bolts are finally in place, the twoton leading centre stay can then be machined from site dimensions and it too finally fitted in place.
To complete the front-end assembly, the buffer beam will re-fitted. At this stage, the whole unit will be ready to be (re-)fitted into the 4709’s frames.
The 4709 project is broken down into a series of work packages and we are now planning many months ahead with respect to the manufacture of various key components and how they can be funded. If you have a contribution to make, the 4709 Web site (https://www.4709.org.uk/) has a donation link on every page.