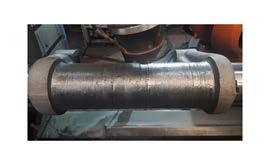
11 minute read
Comes Home to SVR
the conventional way but, in this case, the polystyrene melts, then burns as it is replaced with the molten metal. Clearly, care must be taken in the casting process to allow the gases from the burning plastic to escape, or the finished casting could be defective, with pockets of trapped gas leading to any number of flaws. To prevent such occurrences, a consumable volume is added to the pattern to allow these gases to be released. The polystyrene pattern will be lost because of the cast but being an almost virtual pattern, any number of identical patterns can be fabricated using this technology, all at a very low cost.
In the case of 4709, the cylinder blocks for 4709 have taken a little longer to reach the casting stage because the original GWR cylinder block design has had to be modified in three areas: • Reduced saddle height to accommodate the current Network Rail loading gauge for mainline running • Reduced width over the cylinders to increase route availability • Slightly reduced cylinder bore to ensure sufficient strength despite the reduced width
Advertisement
The castings were now due to be poured late in August. Meanwhile, thanks to Bob Meanley, who produced the redesign and Elliot Powick who provided the 3D CAD drawings.
The Boiler
The Barry Ten will continue to give until little is left but some rust flakes and the memories of their past, but there is still one thing none of our donors can give us and that’s a boiler. 4700 did carry a No 1 boiler for two years but, once the specially designed No 7 boiler became available in 1921, it was swapped. We could follow the same path with 4709 and use the boiler from 2861. Potentially, this would be a cheaper solution, by as much as £500,000 however, during 2019 we decided to build a new no.7 boiler, as the risks and costs associated with using the older and marginally less powerful boiler from 2861 were felt to be unrealistic. So, we remain committed to 100% authenticity – a new No.7 boiler, fabricated in the UK.
The Rockshafts and Rockshaft Brackets
Parts removed from the donor engines for use on 4709 also include the rockshafts and rockshaft brackets. These transfer the movement of valve gear located between the engine frames to the piston valves on the outside of the frames.
In service, the rockshaft sits in a bronze bearing within the rockshaft bracket. Unfortunately, the valuable bronze bearings were removed from the donor engines in the early days at Woodham Brothers scrapyard, leaving the exposed surfaces of the shaft and bracket to corrode for decades in the marine air of Barry docks.
Grit blasting the damaged surfaces of the rockshafts and rockshaft brackets revealed the metal loss was severe. Remaking these parts
Laser Surfacing the Rockshafts Laser Surfacing the Rockshaft Brackets
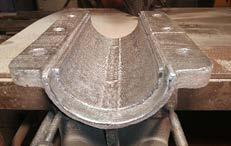
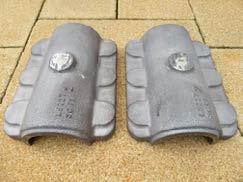
The rockshaft caps
would be extremely costly because new foundry patterns or forging dies would be needed. If the original parts were to be salvaged, more metal needed to be added. The problem was how can new metal, which is at least as strong and ductile as the original material be permanently bonded to the damaged parts? One solution could be to weld on to the surfaces of the components using a conventional electric arc welding process, but the weld metal is unlikely to have properties as good as a forged rockshaft. In addition, the high level of heat input from a conventional welding process would cause thermal stresses, which could easily distort the part or result in premature failure of the component in service.
An alternative but much less common, heat source for welding is a high-power laser, which offers intense but very localised heating. The relatively small heat input minimises distortion and produces a stronger and more ductile weld metal. The metal to be applied, which is specially formulated to give optimum weld metal properties, is fed into the laser beam as a powder. The laser head, together with the metal powder feed, is on a robot arm driven by a computer, which is programmed with the complete welding sequence. The accuracy of the process is such that features in the original part, like threaded holes, can be left completely undamaged. Potentially, this is a ground–breaking process for steam locomotive component repair. At the time of writing, the laser welding of rockshaft brackets and rockshafts has been completed successfully. Machining of the rockshaft brackets is currently underway with the rockshafts to follow
Pony Truck
This is a significant sub assembly for 4709 and is therefore the main part of the engine currently being restored in Exeter. The re-use of donor parts has many advantages, but it is essential that thorough condition inspections are undertaken to ensure that ageing components are fit for re-use on the mainline. (To be Continued)
Wolverhampton’s new railway station is set to open fully to the public in the spring, as work on the exterior of the building nears completion
Contractors Galliford Try have installed the steelwork, clad the building and lifted in the floor and roof slabs to make it watertight. It is part of the second phase of works to the station, which will see more retail units, a customer waiting room and help point introduced.
Councillor Stephen Simkins, Wolverhampton’s economy chief, said: “The railway station is a beacon of the multi-billionpound regeneration that is taking place across our city. It is an extraordinary project, and I am delighted all the hard work is getting the recognition it deserves. This will help lever in more investment into the city and benefit future employment, helping to relight our city and encourage families to work, live and enjoy Wolverhampton with their children. A lot of hard work has been done by the council, Ion Developments and partners to make the transformational scheme a reality. The completed Interchange will connect train, tram and bus in one place and, alongside a thriving commercial district will ultimately provide a gateway to our city that we can all enjoy using - and be proud of.”
The new station is part of the city’s £150 million Interchange scheme which has been named the West Midlands Property Awards 2020 Regeneration Project of the Year. Magnificent
The project – which aims to improve bus, tram and train connectivity – scooped the Royal Town Planning Institute (RTPI) West Midlands Planning Excellence honour in November. Work has started on the station’s canopy cladding, ceramic tiling and mechanical and electrical installations and roof finishes, ahead of final phase work prior to opening.
Phase one of the new railway station opened to the public at the end of May and was handed over to West Midlands Railway (WMR), with the project split into two to ensure it didn’t impact on train services from Wolverhampton.
Once complete, the station will link up with both the Midland Metro extension along Pipers Row and the city centre’s bus station, meaning residents in Wolverhampton will be able to travel seamlessly across the West Midlands – and beyond when HS2 is up and running.
A computergenerated image of the completed railway station. Credit: Infinite 3D Ltd.
The Severn Valley Railway has welcomed back the overhauled boiler of its flagship locomotive 4930 Hagley Hall following 18 months of hard work. The return of the boiler was made possible by Northern Steam Engineering, who previously built a brand-new tender tank for Hagley Hall at their premises in Stockton. The boiler is now in its new temporary home at Bridgnorth, on a wagon that will allow volunteers access as the restoration continues.
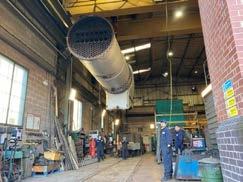
The 4930 boiler (Lesley Carr)
Work carried out on the boiler has been substantial, including new side sheets, throat plate and doorplate sections on the firebox, the insertion of a patch in the boiler barrel and a complete re-tube. Prior to the boiler’s return to the SVR, a steam test was carried out, where the safety valves lifted for the first time since the locomotive last dropped its fire in October 1986.
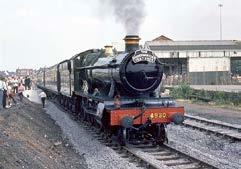
4930 Hagley Hall at kidderminster Town station on the 30th July 2014 celebrating the 30th anniversary of the opening of the station

The 4930 boiler arriving at Bridgnorth Works in December. (Bob Sweet of Friends of Locomotive 4930 Hagley Hall)
Danny Dymott, of Northern Steam Engineering, said: "This has been a major overhaul with the inner firebox being removed from the boiler and stripped to component
4930 “Hagley Hall” was built at the Great Western Railway’s Swindon Works under Lot 254, and entered traffic in May 1929, at a cost of £5,107. 4930 was new to Wolverhampton Stafford Road Depot, and during its career served at the following depots in succession; Wolverhampton Oxley, Chester, Bristol St Phillips Marsh, Wolverhampton Oxley, Wolverhampton Stafford Road, Oxley, Weymouth, Oxley, Chester, Oxley, Tyseley, Leamington, Tyseley, St Phillips Marsh, Weymouth, Bristol Bath Road, St Phillips Marsh, Westbury, Taunton, Exeter, Taunton, Exeter, Old Oak Common & Swindon.
Hagley Hall was withdrawn from service in December 1963, having run 1,295,236 miles and was sold to Woodham's scrapyard in Barry, arriving there in April 1964. The large number of redundant wagons arriving for scrap ensured that most of the locomotives in the yard remained untouched by the cutter’s torch, and 4930 “Hagley Hall” numbered amongst these survivors. 4930 was purchased by the SVR Holdings Company in June 1972 and was moved “dead” by rail to Bewdley on 6th January 1973.
parts. It’s included a 75% new outer firebox, a new front tubeplate, produced by ourselves at Northern Steam Engineering using traditional methods, and fitting of all-new fire box stays produced at Bridgnorth by the Severn Valley Railway’s engineering team. The Covid-19 pandemic caused slight delays to the project but we are very pleased to announce that the boiler is now complete, bringing to an end a successful project that has been delivered on target and to budget. We look forward to seeing the progress at Bridgnorth with the locomotive’s overhaul, and its return to traffic as soon as possible.”
Martin White, the SVR’s head of engineering, added: “The return of Hagley Hall's boiler is the conclusion of 32 months of collaboration between the SVR and Northern Steam Engineering. An excellent working relationship has been developed between our two organisations, and although the work has been carried out at NSE premises, there are many components in the boiler which were produced by SVR personnel at Bridgnorth and shipped to NSE at Stockton. In the overall Hagley Hall project, delivery of the boiler is just one task that is now ticked off, albeit a fairly large and substantial one.”
Thirty-five years after Hagley Hall’s last steaming on the Seven Valley Railway, project leader David Fulcher-Insull is confident that the return of this key component brings the locomotive’s return to service a significant step closer. He said: “It’s always been a bit of a concern whether it would be ready. The delivery of the boiler now means we’ve got everything to move on to complete the project. We’re on target.”
Once the flagship locomotive of the Severn Valley Railway, Hagley Hall was built in 1929 by the Great Western Railway and clocked 1,295,236 miles in its 34 years of service. Withdrawn in 1963, it was rescued from Dai Woodham’s yard in Barry by the SVR Holdings Company in June 1972. Restored to running condition in 1978, Hagley Hall soon became one of the stars of the Severn Valley Railway, hauling the reopening train for Kidderminster Town Station in 1984.
Hagley Hall also represented the Railway further afield in mainline appearances, such as the 1985 GWR150 celebrations. In a memorable run, it stormed over the South Devon banks in a double headed run with 7819 Hinton Manor, having stepped in at the last minute to deputise for the failure of King class locomotive, King George V.
Withdrawn from SVR service in 1986, the locomotive was initially in storage, followed by a period as a museum exhibit until October 2013 when the long-awaited overhaul and restoration process began.
The 4930 has now been under Severn Valley ownership for longer than it ran on Great Western Metals and when Hagley Hall finally steams again it will be the culmination of the efforts of many, in particular the Friends of Locomotive 4930 Hagley Hall who have raised well in excess of £100,000 since their formation.
The return of Hagley Hall to steam service will be the crowning moment of decades of tireless fundraising and work by the group. Chairman Paul Hobson said: “The Friends of Locomotive 4930 Hagley Hall group are delighted that a significant milestone in the restoration of the locomotive has been achieved with the completion and return of the boiler to Bridgnorth, for which we extend our thanks to our friends at Northern Steam Engineering. The fundraising initiative, begun by the Friends group in 1999 and since admirably supported by our faithful donor Friends over many years, now has the finishing line in sight. Together, with the generous support of the SVR Charitable Trust and the £95,000 contribution from our grant-aid partner, the National Lottery Heritage Fund, we should see the reassembly and completion of the overhaul of 4930 by the engineering team at Bridgnorth Works over the next 12 months. We can all now look forward to being able to see, hear and smell our flagship locomotive Hagley Hall in steam for the first time in 35 years, which will be a moment to savour indeed.”
