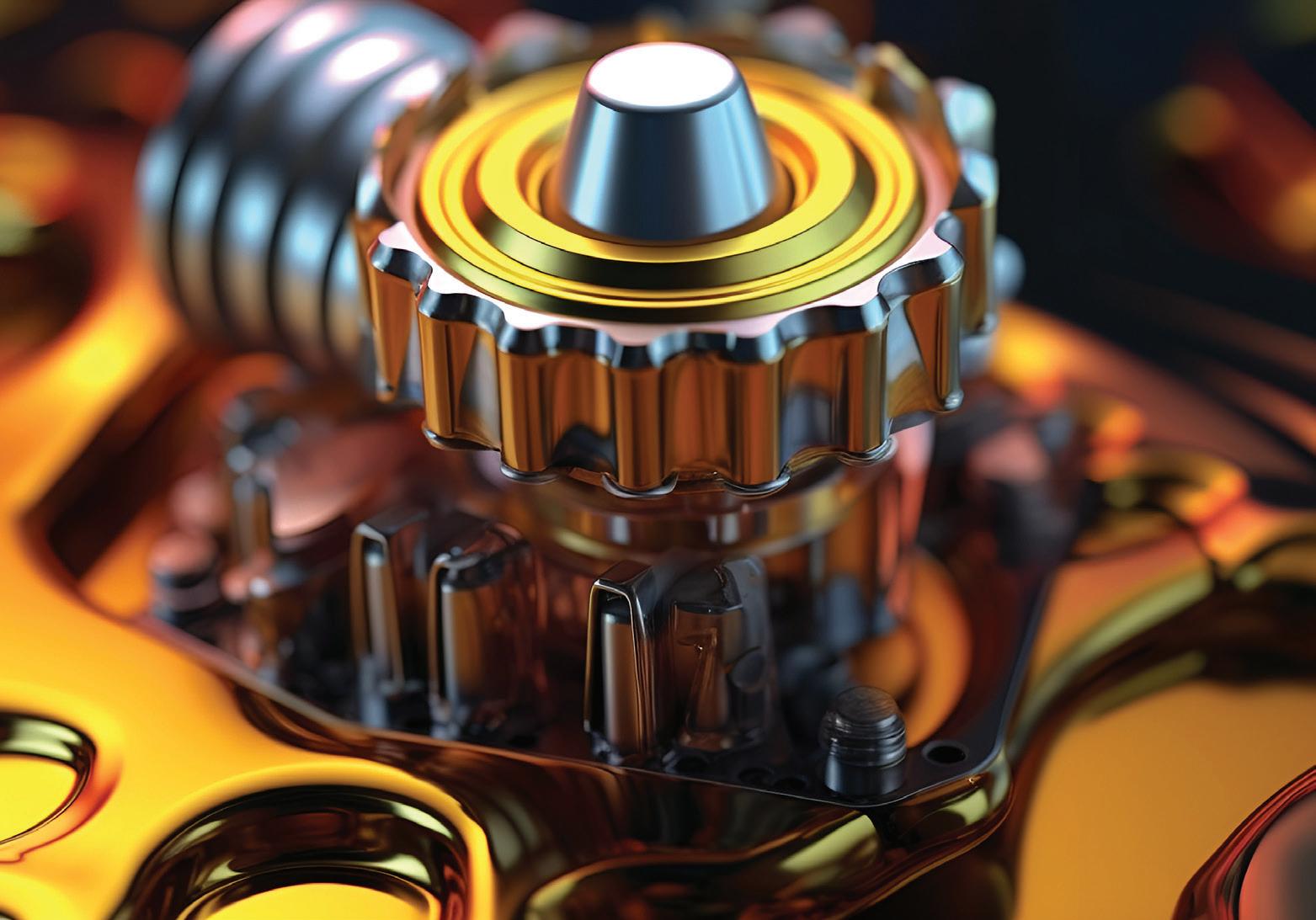
3 minute read
The future of bearing related maintenance
BY DOUG MARTIN
Recently, I visited a large mine site in Northern Canada on a day that layoffs were announced, and one of the maintenance personnel I was to meet, was one of the casualties. Driving on the site with my hosts, a discussion began about how they will have to depend more on suppliers for technical assistance. This comment clearly defines what may be the future of maintenance.
However, this story is not new, it has been hanging over the traditional maintenance structure in Canada (or at least traditional heavy/primary industry) for the decades. That story is exemplified by the anecdotal evidence of new pulp mills built in South America in the late ‘80s early ‘90s. In these facilities, the maintenance department was a contractor.
T he pulp company was an entity that “made pulp” and any support “departments” were contractors.
What does this mean for large facilities like the mine site? For several years, instead of changing a single bearing on a belt conveyor pulley, the whole pulley is removed. In turn, companies who changed out whole motors when there is a bearing problem had their own motor shops, but now they use an outside motor shop.
Today, we are seeing larger assets being changed out and rebuilt off-site by a contracted shop. Even the traditional bearing distributors have developed their own service centres, in which they rebuild these assemblies. It is the way they can continue to sell the bearings, seals, and other components, they once sold as individual parts, to the large users. maintained, and replacing any wires that may have been damaged.
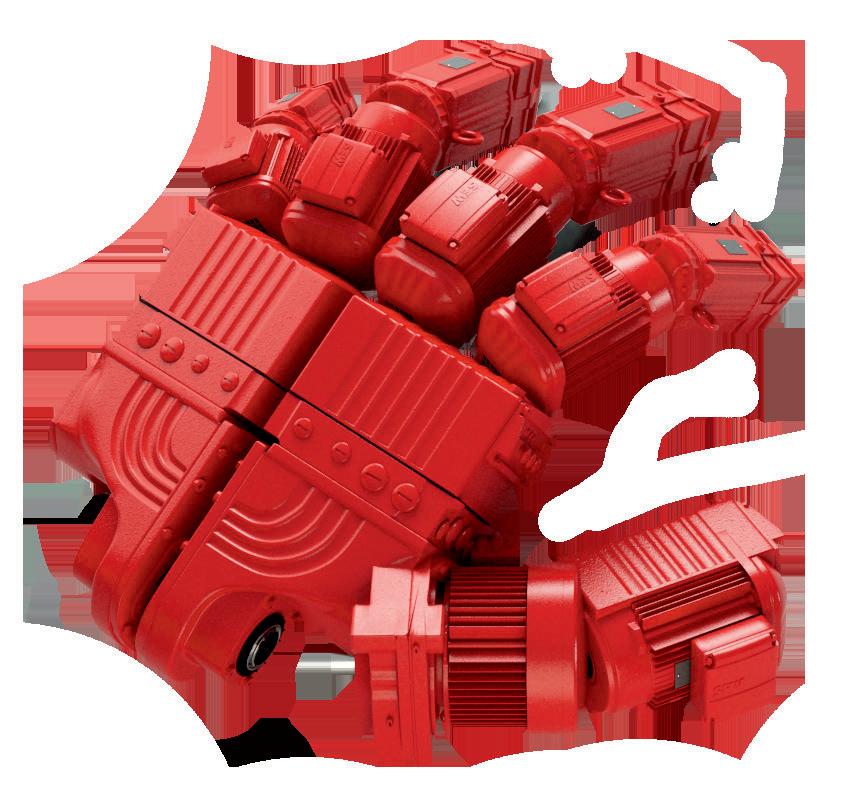
What is the benefit to this transformation?
It allows the mining company or pulp company to focus their attention on what they produce, and not trying to manage a maintenance department, or a rebuild department. It may also allow a higher level of quality control. They can write and enforce tighter quality controls over the rebuild than they were able to achieve within their own organization (especially in times when resources were strained). There are also some cases where recognized organizations or consultants will certify rebuild shops on behalf of users, in turn, giving a degree of confidence in quality of the job.
Last month, while at a pulp mill assisting with a critical fan installation. One portion of the job was to balance the rotating assembly prior to installation.This is a critical aspect of the job.The rotating assembly was sent out to a sub-contractor and returned within a day. I later asked why the fan was not balanced in house, knowing that they likely had the equipment to do so. The reply was they may have the equipment, but when their crew may only balance two or three assemblies a year, they lack the expertise to do the job quickly and with a degree of quality.
Another hurdle that condition monitoring/ vibration analysis systems face is the issue of security. Many of the latest technologies offered require an Internet connection to allow access to the software for the data analysis. The benefit of the online software is it removes the need for regular software release to be manually downloaded and installed (maintenance of system), and it allows collaboration within the organization. However, with recent data breaches and ransomware issues, IT departments have become very strict in who and what is allowed to be connected through the network.
There are other condition monitoring technology that may provide an alternate. There are online systems that can connect to the local cellular networks and allow communication/data transfer with the cloud, outside of the company’s internal network. The user can access the vibration data through a secure web site that does not endanger the security of the IT system.
In terms of less expensive systems, there is a move towards surveillance systems as opposed to diagnosis systems. What a surveillance system can do is monitor basic parameters like overall vibration and temperature, and then with its AI, learn how that machine r uns and warns the user there has been a change in the asset. This can lead to inspection and diagnosis of the problem with more complex tools (such as a route-based data collector). The benefit is shifting those in the vibration department from being data collectors to inspectors and troubleshooters of identified issues.
I have identified the change that we are in the process of, not made any bold predictions. That is production facilities becoming streamlined, focused on production of their product, and not large organizations with different departments dealing with all aspects of the operation. They will be supported by local vendors and shops that have become experts in their specialty and have the quality systems in place to provide a high level of service.
Condition monitoring/vibration analysis
With the lack of resources industrial facilities, the management group needs to find ways of putting hands on wrenches, not on data collectors, as is typical of the most common method of data collection for vibration analysis. However, even with online systems that do not require a technician to spend days on prescribed routes, there still is a level of maintenance required to maintain these systems.
A number of mills have online systems that are not being used simply due to a lack of system maintenance that includes, re-connecting data cables after the asset has been