6 minute read
Pivoting Examples
How member companies of the German-Australian Chamber successfully adapted their business operations during the COVID-19 pandemic
2M Language Services' COVID-19 Response
Social distancing rules forced the cancellation of all onsite events world-wide. This also meant the cancellation of simultaneous conference, bilateral business, court and most healthcare interpreting.
2M Language Services was quick to respond with remote solutions such as 2M’s innovative RSI (Remote Simultaneous Interpreting) platform for virtual conferences and 2M Lingo for VRI (Video Remote Interpreting) for courts and hospitals. Language access to crucial information has been restored in healthcare including telehealth as well as in corporate sectors and international trade and collaboration.
The VRI platform 2M Lingo allows a nurse, judge or mining engineer to select the language and call a certified interpreter with specific subject matter expertise from their phone, tablet or computer who will then appear via 3 way video link to interpret between the 2 speakers. The 2M RSI platform allows up to 3000 users to log on via video or audio link, choose their language channels and listen to the source or the simultaneous interpreting of their preferred language.
Take BHP’s CEO Mike Henry, for example. He now conducts his Town Hall Meetings via the RSI platform and a typical scenario includes 3 BHP speakers located in remote locations, one 2M interpreter in Buenos Aires, another 2M interpreter in Brisbane and 2000+ BHP attendees spread across Australia, US and Latin America. Through remote simultaneous interpreting, the
2M Team enables seamless multilingual support week after week for BHP virtual Townhall Meetings.
2M had been investing heavily into video remote interpreting technologies and system connectors for the past years which is now paying off. Furthermore, COVID-19 forced shutdown has seen a sharp increase in eCommerce, online courses and other digital services. The demand to localise content to reach out to international markets has skyrocketed. 2M’s smart integrated workflows automate the content flow between the client CMS and 2M’s data-secure translation management platform helping many organisations with their business continuity and ongoing export sales of their products and services. Virtual meetings and events are here to stay post COVID-19. There are many advantages including extensive savings in travel expenses and increased domestic and international reach.
The need for content and software localization equally will continue as increased eCommerce and digital services accelerated by COVID-19 will remain. Yet again we see that technology is the most single economic driver of the future. And what has made the company resilient is not only the ability to pivot and adapt in times of crisis but to be at the forefront of technology. Technology with human in the loop futureproofs the business model beyond COVID-19. Provided by 2M Language Services Tea C. Dietterich, CEO, 2M Language Services
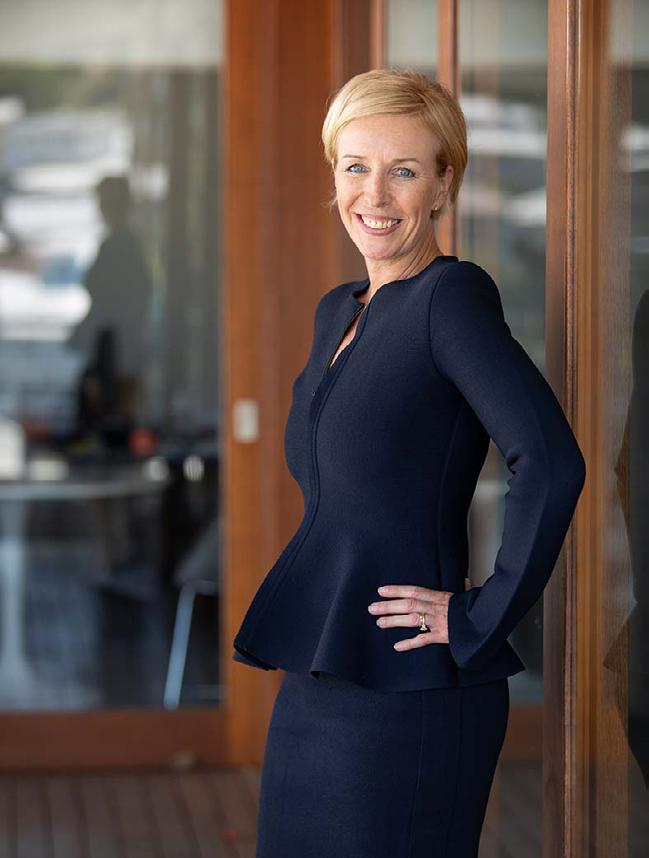
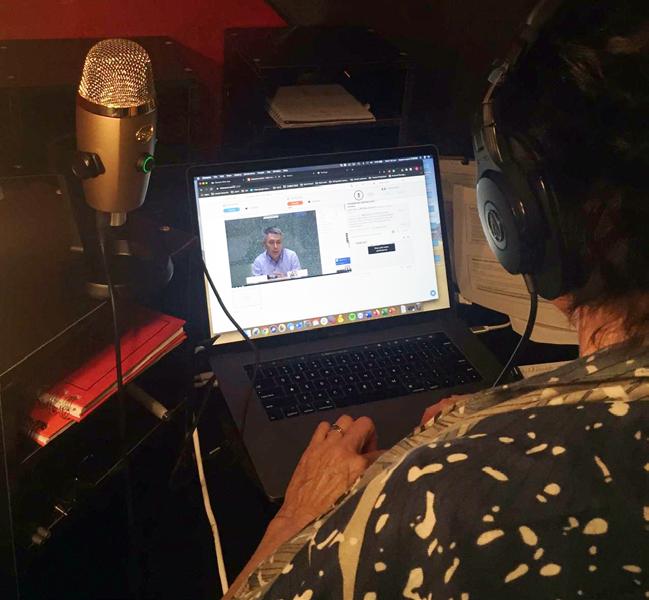
More information: Thomas Lespes Muñoz www.2m.com.au
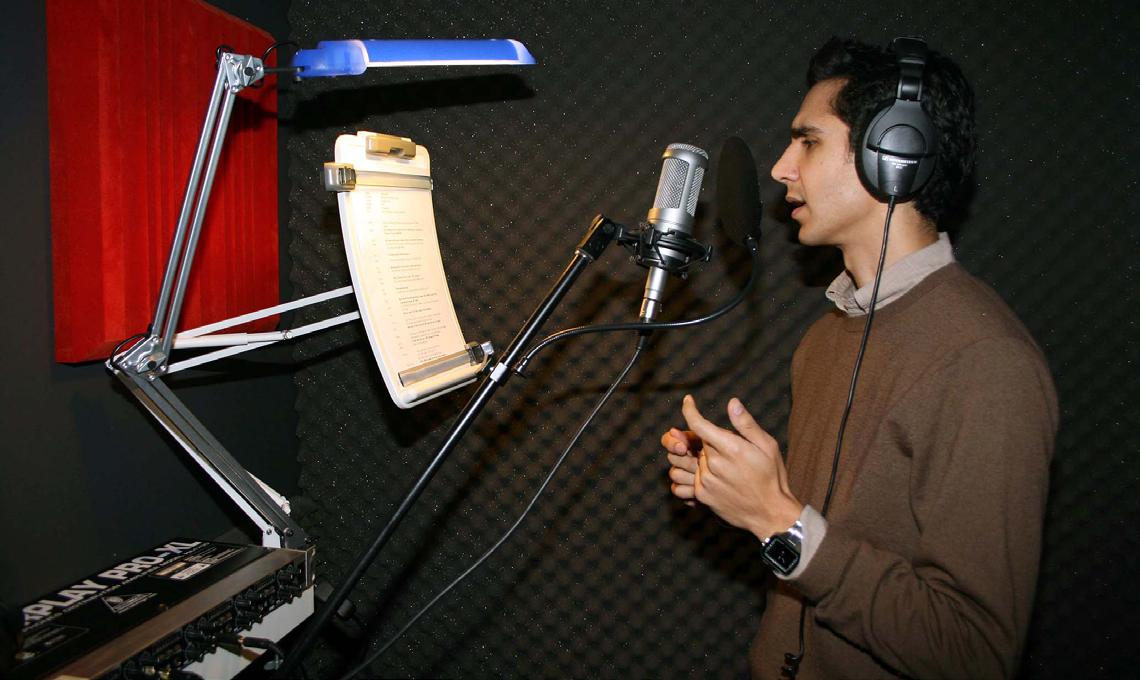
Speed3’s COVID-19 Response
In response to COVID-19, our business focus shifted from sales into manufacturing to looking at how our technology could assist in fighting the pandemic. We knew that copper had antimicrobial properties and that is a material we already specialised in printing, however, we didn't yet know what effect, if any, it had on SARSCoV-2, the virus that causes COVID-19. So our first action was to seek testing to see what effect our ACTIVAT3D copper material had on the virus. The challenge early on was finding a lab who had access to the virus and had the time and resources to test our copper. We ended up working with the Australian NATA accredited clinical trial speciality laboratory, 360Biolabs, who tested the effect of ACTIVAT3D copper on live SARS-CoV-2. The results were positive and showed that 96% of the virus is killed in two hours and 99.2% of the virus is killed in 5 hours.
BigRep’s COVID-19 Response
In the wake of COVID-19’s spread, BigRep, the German-based global leader in largeformat additive manufacturing (AM) technology and solutions, acted quickly to help its customers and communities.
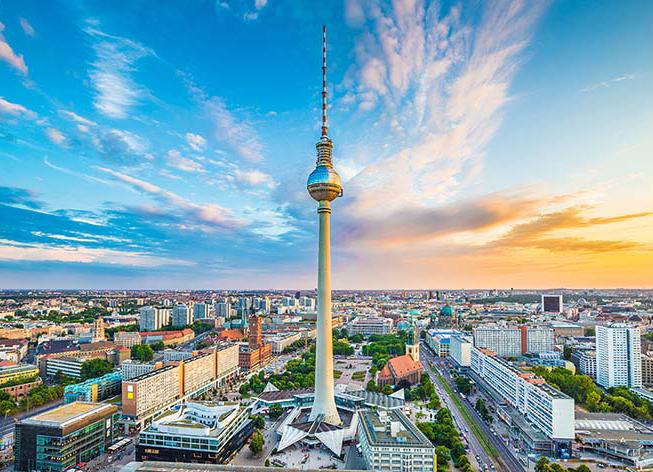
Being in a unique position to design and manufacture solutions for the health crisis facing our city, Berlin, we pivoted many of our staff from their normal business goals to instead create solutions for our local community and those of our partners. The first solution from this effort was protective face shields that we released as a free download on our website. We have produced many of these face shields ourselves on BigRep‘s large-format 3D printer AM systems and distributed them throughout the German capital, as have many of our partners. You can find and download the design to create yourself here: https://bigrep.com/posts/covid19-response/
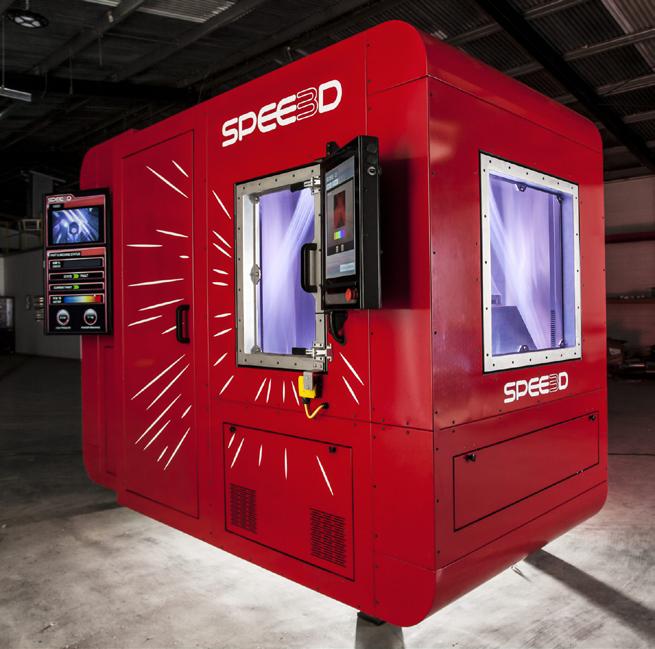
The next challenge was to modify the algorithms that control our 3D metal printer’s robotics to enable the coating of existing metal parts. While our printers are capable of printing entire parts in ACTIVAT3D copper, for the rapid and affordable deployment of copper products the ability to pivot to coating fixtures with
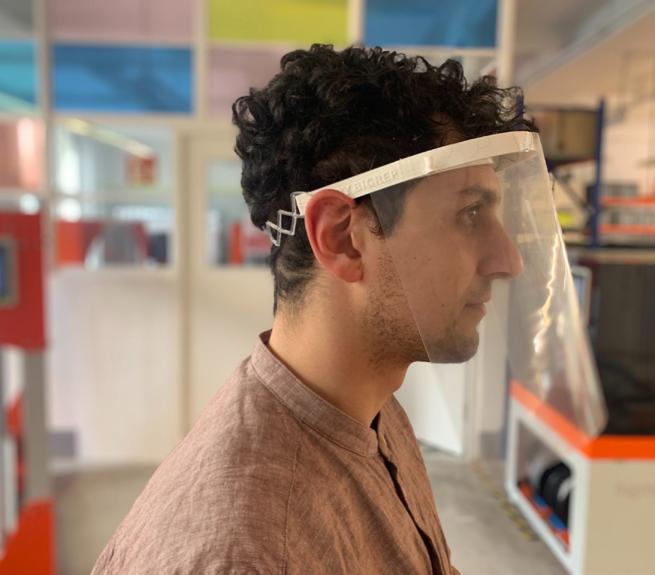
Since that first design we have also helped to produce 3D printed connectors for the German Red Cross (designed by a third party) to convert full-faced diving masks into improvised ventilators. We continue to work towards more solutions that might help stop the spread of COVID-19 here and abroad.
Our successful change management was only possible because we took quick action to protect the health and safety of our staff – adjusting operations by implementing effective health practices and social distancing in the workplace. Pre-emptively, we mandated any employee whose job does not require direct interaction with our products to work from home. Following the unique German “Kurzarbeit” approach (short-time work), and in collaboration with our employees, we successfully implemented a reduced working program antiviral copper made the process far more efficient.
3D coating door handles and push plates was the obvious first application for this technology considering multiple studies have attributed super spreading events to contaminated touch surfaces. The team developed a process that allows our printers to coat a standard stainless steel or brass door handle or push plate in just 5 minutes. There has been global interest in this technology and product coated in ACTIVAT3D copper. As our business is the design and delivery of 3D metal printers, our next step is to partner with large door handle manufacturers who can scale the production and distribution of these products.
By rapidly pivoting our business and following a lean manufacturing process we have been fortunate to retain all our staff through these challenging times.
Provided by SPEED3
to retain our staff amid the decrease in demand. Measures were similarly taken by companies across industries in Germany.
More recently, we have seen an increase in industrial manufacturers with disrupt-ed supply chains amid the social dis-tancing regulations. Our innovation consultancy, NOWLAB, are working with these new prospects to create additive manufacturing solutions that effectively replace their disrupted workflows. We have been in the fortunate position at BigRep to help both our local and industrial communities in their efforts to get through this crisis. Though we, like most businesses, had to reassess our goals, we believe that recent events have served to demonstrate the incredible possibilities of industrial 3D printing as a groundbreaking, cost-effective and highly flexible technology for industrial manufacturing. With it, we have been able to rapidly respond to unforeseen production challenges and quickly create solutions for unexpected problems. It shows how additive manufacturing can be leveraged for efficient, in-house supply chains with sustainable technology. We believe the future looks bright as industrial manufacturers are increasingly realizing that the future of production lies in localized processes with additive manufacturing solutions.
Provided by BigRep