27 minute read
Joinery, windows & door production
Next Article
Weinig UK has completed the third instalment of its in-house event series, Connect, with its CNCs For Solid Wood open house. The three-day event, which took place at the company’s showroom in Abingdon last month, offered visitors an exclusive opportunity to see Weinig’s five-axis Pro-Master 7125 CNC in action, and explore the possibilities it had to offer those in door, window and stair production.
“For many of our visitors, Weinig UK’s Connect series has been the first opportunity they’ve had since the pandemic began to see new technology demonstrated to them on a one-to-one basis,” says Mark Smith, regional sales manager for Weinig UK.
“With each Connect event focused on a specific manufacturing process, Weinig’s machinery specialists have been able to tailor machinery demonstrations to meet
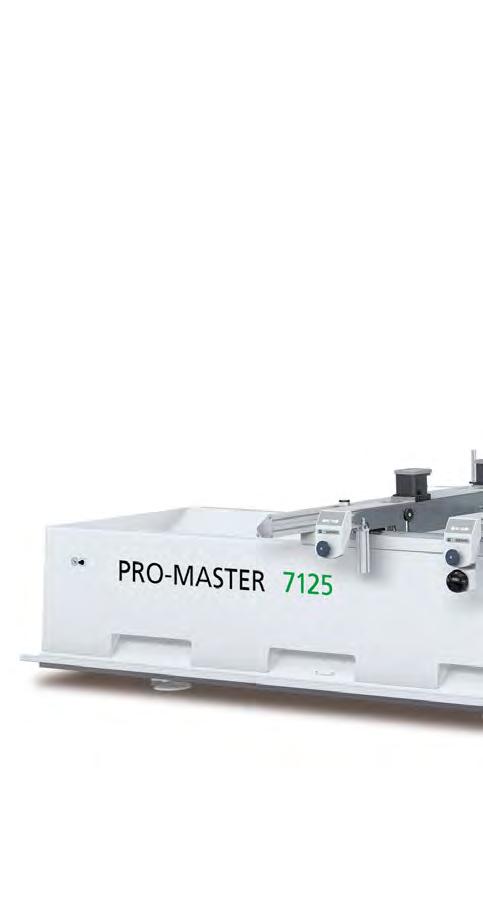
Joinery, window & door production
Weinig UK’s Connect Series continues
the needs of their visitors, and showcase the latest software and processing options available – helping new and existing customers stay connected with market trends and developments.
“This event has been about demystifying the world of CNCs, and proving you don’t need to be a CAD technician to use the software effectively,” admits Mark. “Investing in a Pro-Master 7125 is the next step for many traditional machinery users who are looking to deliver efficiencies in their workshop. It’s ultimately a step change in how they will manufacture in the future – saving on time, skill and labour – and it’s been fantastic to see visitors embrace this change and the benefits that come with it.”
Mark adds: “As well as running the machines throughout the event, we also demonstrated our software, to reassure visitors just how easy the machine is to programme and use. We wanted to highlight the simplicity of a Pro-Master 7125, and break down the costs associated with the purchase into clear, manageable chunks.
“We believe this approach added real value to our attendees. The Connect series continues to be a great opportunity for our customers – large and small – to explore Weinig’s machinery portfolio, and we’re looking forward to welcoming people to our next in-house event, Smart Workshops For The Smaller Manufacturer, on the 1st3rd February 2022.” www.weinig.co.uk
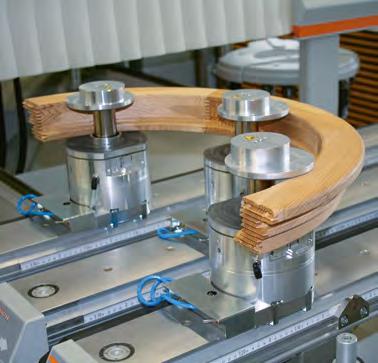
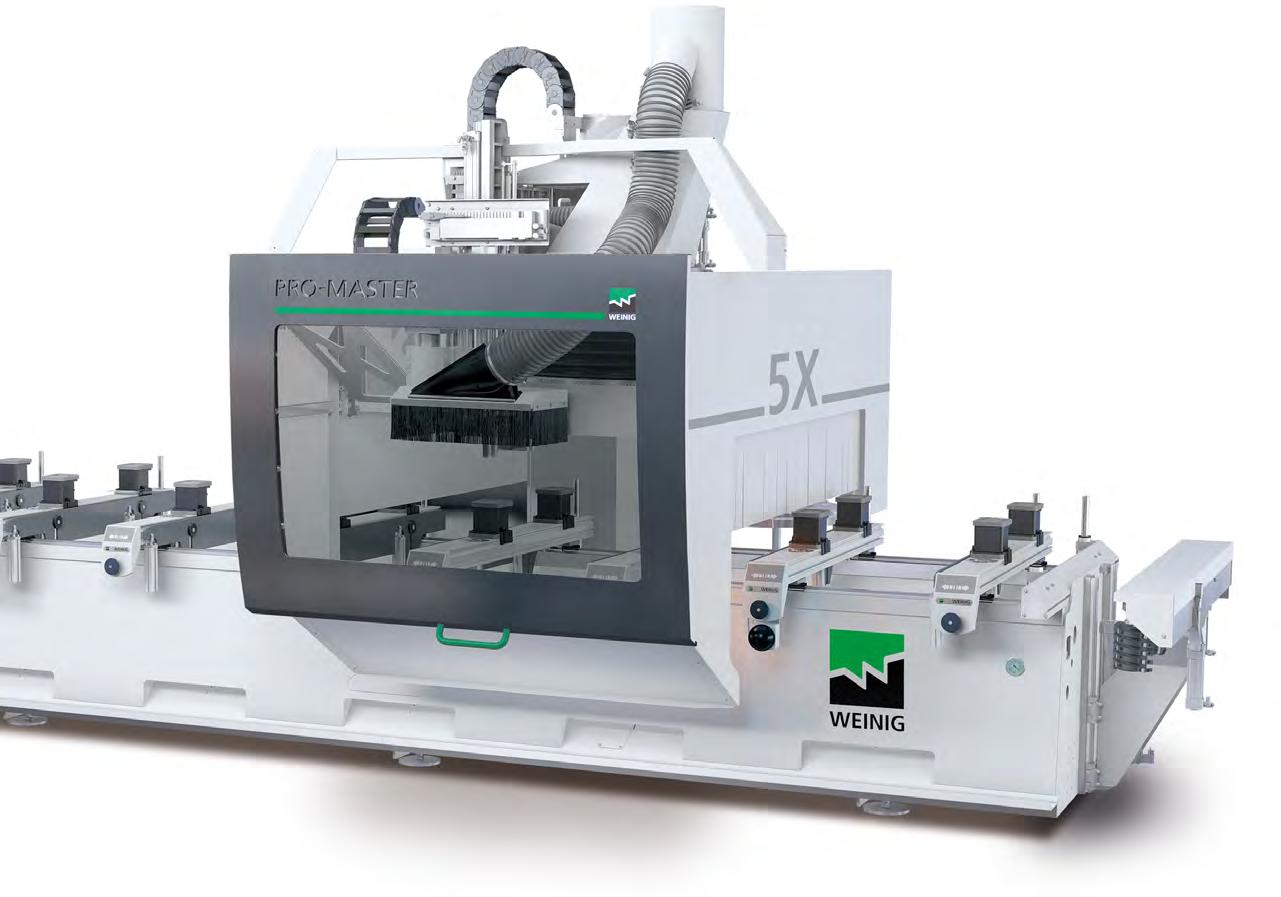
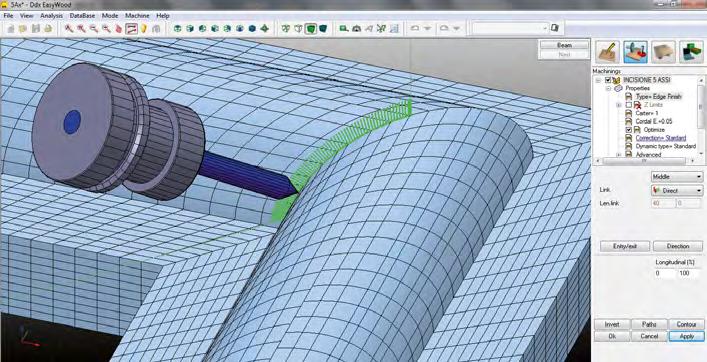
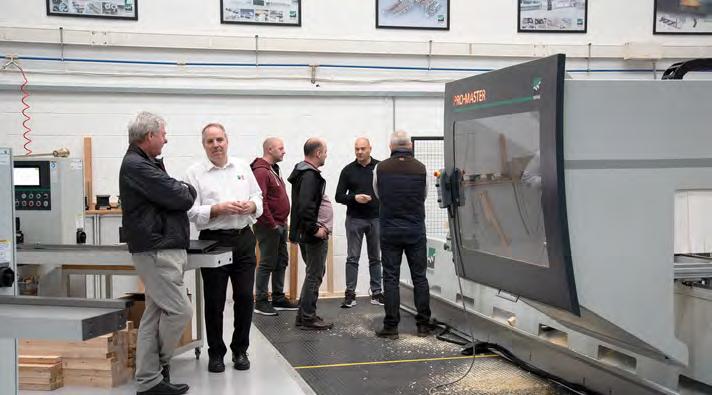
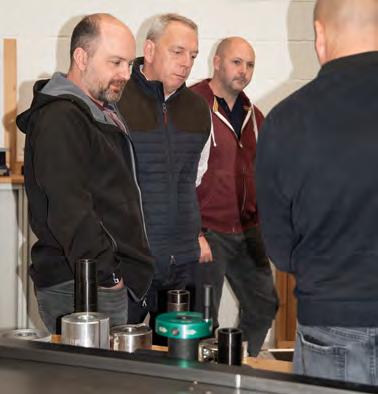
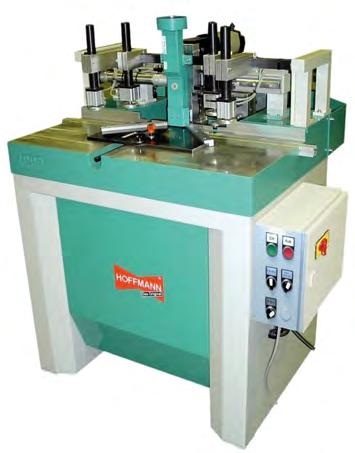
AJB Group specialises in the design and manufacture of high-quality internal joinery, external doorsets, windows, composite doors and mouldings, established in 1999 and providing an excellent service for residential, commercial renovations and new-build developments of all sizes.
AJB’s talented and youthful workforce is a breath of fresh air, bringing life into their product range – and they believe this is “where timber meets perfection”. They continue to move forward with modern methods of manufacturing, combined with advanced technology, which creates the hub to their success.
In the woodworking industry the mitred corner has always been recognised as a sign of high value and quality, especially in door production.
The joints, when finished using the Hoffmann Key, offer strength, durability and stability, while the process of production offers simplicity and speed. AJB found all of these attributes in both the Hoffmann MS40 SF double mitre saw and the Hoffmann PP2-H-DB pneumatic dovetail routing and dowel boring machine – resulting in “the perfect combination” in the fabrication of its door frames.
The Hoffmann MS40 SF double mitre saw is designed to simultaneously cut one left- and one right-hand mitre with each machining cycle. Accurate, repeatable mitre cuts are achieved in a variety of materials, including hard and softwoods, wood-related materials (MDF, plywood, particleboard), plastics, and non-ferrous metals such as aluminium.
The heavy-duty design of the saw heads and precision machined components, as well as the use of industrial-quality, carbidetipped saw blades, assures “perfect” cuts with no burrs or tear out, making it “the ideal double mitre saw for small and large shops when accurate and efficient mitre cutting is required”.
The Hoffmann PP2-H-DB pneumatic dovetail routing and dowel-boring machine is a freestanding version specifically designed for mitred corner production. The machine cycle begins by pressing the foot pedal. The workpiece is clamped pneumatically, and the units router the dovetail slots and drill the dowel holes. The workpiece is then released. The joint is completed using dowels and Hoffmann Keys W1/2/3/4.
Extensive development has been AJB’s footprint to becoming a manufacturer of the highest quality in modern and traditional joinery. It has designed a product range that not only satisfies the performance and technical criteria of today’s industry, but exceeds all expectations.
“We focus our attention on engineering timber and timber-like products to the highest possible degree, and then take it one step further. We take a raw material and engineer out all of its natural defects to provide our client with the very best in carpentry and joinery. With intelligent inhouse designs, accurate estimating and a state-of-the-art production facility, we can deliver success without any hesitation,” says Amarjit Binji, MD of AJB Group. 01524 841500 www.hoffmann-uk.com
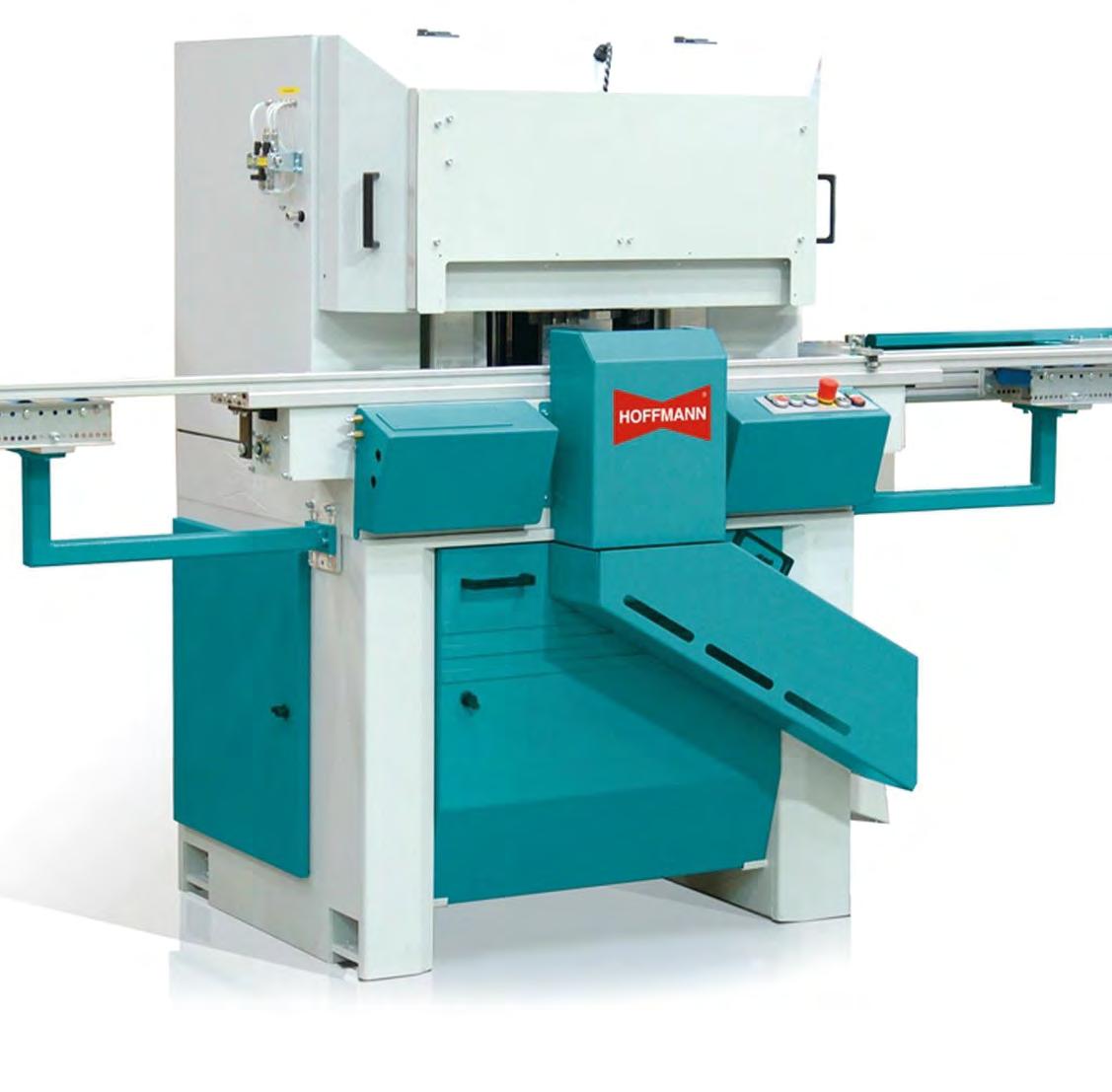
MS40-SF
Hoffmann’s optimum solution for quality joinery firm
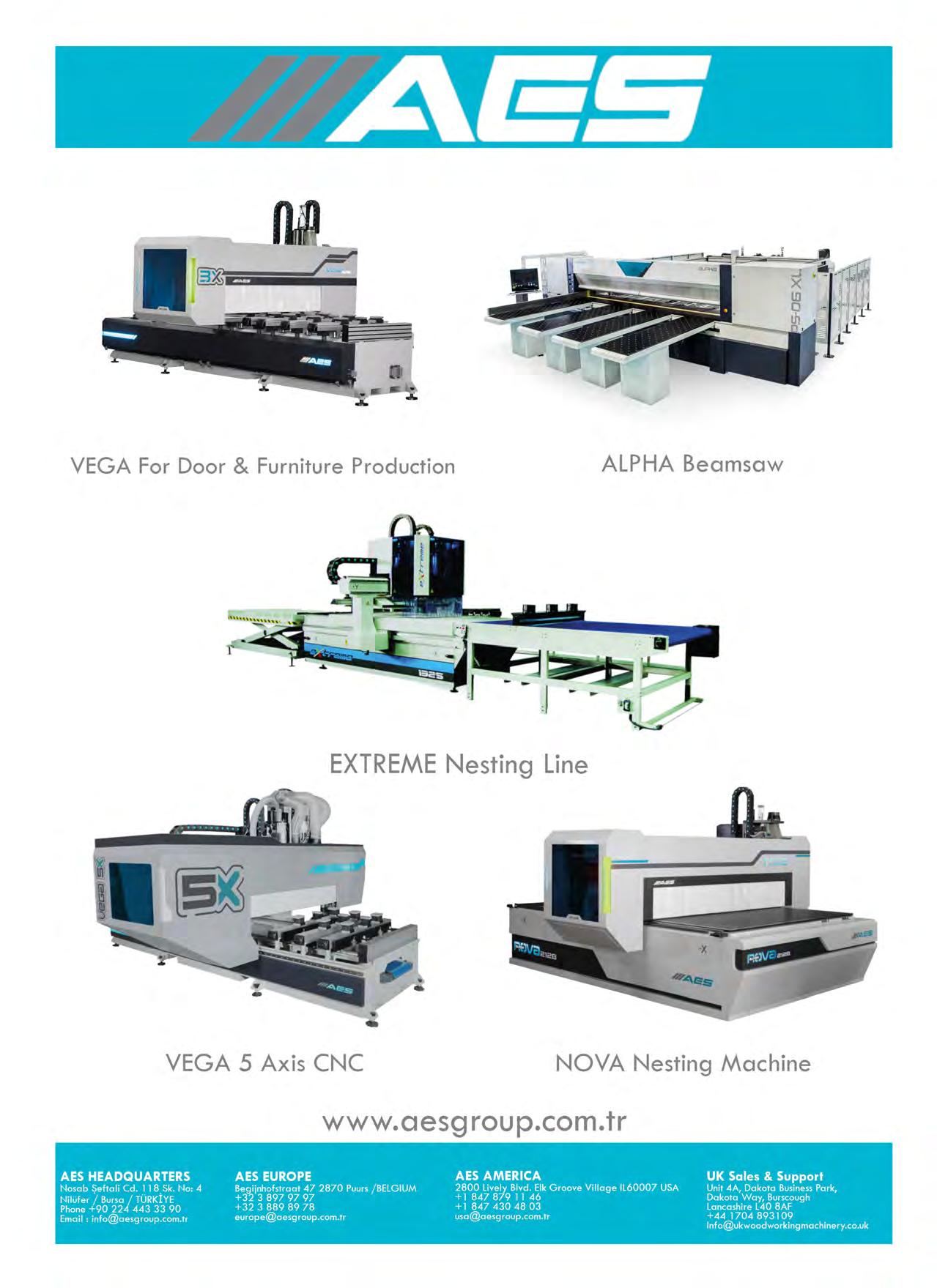
Special is our standard

This year STEMAS celebrates its 40th anniversary as Italy’s leading specialist machinery manufacturer, primarily within the woodworking and panel processing industries.
Author Lorenzo Esposito, Technical Sales Manager, STEMAS
Over these ensuing years STEMAS has developed to become the predominant market leader in the manufacture of special execution machinery; however, in terms of CNC Routing Technology and in particular door processing, they are widely recognised as the undisputed industry frontrunner in terms of highspeed house door processing machinery.
In the last two decades, Stemas has reputedly become the leading supplier of specialist high-speed through feed routing and ironmongery inserting systems for the door industry around the world; with many large fully automatic door line system installations in Poland, the one of the biggest house door manufacturers in Europe, as well as the UK, Israel, China, South Korea, USA.
The PERFECT-DOOR Systems, represents the first serious choice for either a small/medium producer, facing a growing demand on their production capacity, or indeed a medium to large door manufacturing enterprises in need of achieving unmatched productivity of up to 3 doors per minute and to gain a competitive edge over their market rivals.
In the UK there has been a proliferation of door manufacturers coming to the market in the last five or so years, especially the Fire Door market, each one following the exact same ‘Calf Path’ manufacturing routine as all the others, namely buying one standard 4 or 5 axis, ‘run of the mill’ CNC router after the other.
“Of course, one must start somewhere, and the traditional CNC Router is the correct starting point, no doubt about it” comments Angelo Glenn Onorio CEO of Stemas “but there comes a point in time where the ‘stand-alone CNC Routers’ start become very inefficient”
“For example,” continues Angelo “The production inefficiencies really starts to come to light once a company gets to three CNC routers, then a fourth and possibly a fifth or more even, at this point door processing with traditional 4 or 5 axis traditional routers, is really uneconomical and the manufacturer truly risks losing market and more importantly margin and profit”
Three doors per minute “When a door manufacturer approaches ‘Critical Mass’ with his existing production capacity he must re-evaluate his door manufacturing methods and efficiencies.” Adds Lorenzo Esposito, Technical Sales Manager “It is fair to assume that a traditional 4 axis CNC, which I understand is the most common style in the UK door industry, generally takes around 10 to 15 minutes to complete a basic door process*, hinges, door locks, keyholes etc, and in many cases we have observed much longer processing times, especially when the door is being loaded on and off manually, if a company has five CNC’s this equates five possibly six men producing say 20 to 30 doors per hour”
“With the fully automatic Perfect Door System, in one hour” continues Lorenzo “One can produce around 170 – 180 doors with only one man, only in partial attendance; carrying out a similar basic door processing operation, if one calculates the extra manufacturing capacity the fully automatic perfect door system creates and the sevenfold reduction in manpower the savings are phenomenal, they run in hundreds of thousands of pounds”
The ‘PERFECT DOOR’ System, is designed as a unique modular concept, wherein the line can be built up in customised stages to suit the purchaser’s individual needs, for example, a fully automatic ‘First Stage’ system can produce one complete door in just over 45 seconds*
The ‘PERFECT DOOR’ system has certain features that traditional door routers simply do not have, nor can they be supplied, for example, in essence it does not require a full-time operator as it is a fully automatic/ autonomous line, it will ‘check measure’ the door before machining starts, it will ‘talk’ in real time to the production planning dept and production managers.
The modular construct of the PERFECT DOOR system allows the customer to build up in stages the level of speed, sophistication and flexibility in a stepby-step approach so as to minimise the initial investment costs and also to maximise productivity at the same time enjoy significant reductions in day-to-day operating costs and then as demand builds up, the ability to add further modules to the line.
Stemas have recently taken two orders for their fully automatic lines, one in the UK and one in the Republic of Ireland, one will be delivered by the end of 2021 and the second within the first six months of 2022 as well as these two recent firm orders there has been a major groundswell of interest from several major UK door manufacturers with projects reaching “Critical Mass” and orders are expected to be placed for two, possibly three full lines before the end of the year.
Tailor made solutions Although the PERFECT DOOR systems are of very well proven technology, developed over many years each system is designed to the customers exacting requirements to suit their specific manufacturing needs as opposed to the more traditional ‘off the shelf’ CNC Router offerings where, more often than not, the customer always
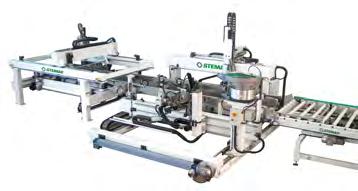
has to make a compromise, he can never truly have what suits his exact needs. In essence with STEMAS, the attitude towards producing special execution CNC routing solutions is a normal day to day activity, the process of customising the machine line configuration prior to manufacturing is a key element to the success of the PERFECT DOOR systems, it is 100% co-operation with the client, their input is highly valued.
Different types of door hardware really do require dedicated working units, so as to achieve the high through feed speed whilst maintaining dimensional accuracy and quality of machining. Stemas PERFECT-DOOR can work with almost every kind of hinge on the market as well as the standard or tailored lock systems, with the advent of ‘SECURE by DESIGN’ more specialist hardware is required and again STEMAS provide the systems to accommodate such.
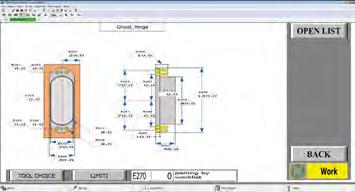
Unlike many providers of door processing machinery STEMAS have their own ‘Software House’ with some of the top software engineers in Italy, STEMAS are justifiably proud of their unique systems; The internal software department makes sure that the user interface displays on the touch screen are a parametric graphic which grants an easy programming of any change in the machining of the hardware locations, in essence extremely user friendly and again bespoke to the client’s needs, no short-cuts are made in this regard
State of the Art As stated earlier the PERFECT DOOR system is a modular concept and can be built up in stages as the client’s work and orders increase, ranging from semiautomatic to fully autonomous self-running systems only requiring basic supervision and not needing an operator in permanent attendance.
There are two basic ‘units’ one can consider as a start point, the ‘Stage One’ and the ‘Full Line’ even these two basic systems can be enhanced greatly either straightaway and/or step-by step.
The stage-one PERFECT-DOOR comes as a single working station, able to perform a basic door process every 45 seconds* ; Basically, the milling of three/four hinges with pilot holes on one side, plus the milling of the lock and strike-plate with pilot holes, keyhole and handle seats on the other side.
It is the natural evolution of the traditional CNC centre, combining the flexibility of the various working processes with the possibility to work on two sides and the top router simultaneously, to boost the overall productivity.
These lines come with a Portal Vacuum Bridge for the automatic feeding and stacking of the doors; lifting the doors from the stack which is normally placed on pallets and/or roller tracking; the stacking is the same operation except in reverse, the line is effectively autonomous, and requires no real manual intervention, as long as the in/outfeed of material is taken care of, most PERFECT DOOR systems run from motorised roller tracking on the infeed and outfeed and there is no real no for the line to stop unless it runs out of doors to process.
These systems also have certain automatic ‘dimensional quality’ check via the numerical control which can dialogue (Bar/Q codes) with the internal servers to extract the working data after the automatic reading of a barcode or RFID, as well as simply import a .csv working list.
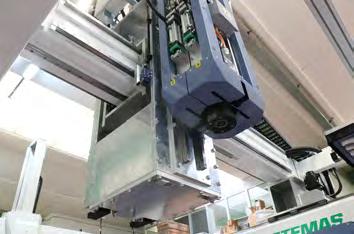
Besides the most common operation for interior doors, the top router with tool magazine up to 24 positions, is able to execute special operations such as the milling of the automatic door closer, ventilation holes or the bottom guillotine seats.
The through feed system also works in conjunction with integral vacuum cups, which raise and secure the door above the feeding belts, the whole surface is free for a 6-side processing, including the squaring and the opening for glass or panels as required by the client. PERFECT-DOOR-HP, is in essence a second routing/work station added to the stage one module ,the two working stations divide the longest operations between them and ensure a productivity up to a completed door each 20 seconds.
This advanced solution, is suitable to process wooden and/or metal doors, it is now reputed to be the ‘go to’ choice of the biggest door producers in the world.
It can come as a turn-key solution or also be the result of a future upgrade of the single station, helping the customers in a two-step process of growing production.
The layout of the line can be also designed with an additional working station able to insert the hardware. Either rotative or vertical magazines for hinges or locks feed 3-cnc-axis units able to insert the elements and screws with brushless motors.
It is also very common for these full lines to have ‘barrel turners’ between the two working stations to further increase operational flexibility
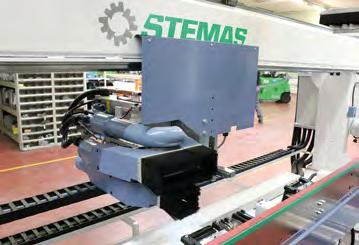
Component insertion In recent years there has been a growing demand within the door process industry for the automatic insertion of hardware, including the UK, this is where STEMAS really does lead the market in cost effective systems, hinge insertion with screw fixing, lock insertion with screw fixing
The layout of the line can be also designed with an additional working station able to insert the hardware utilising either rotative or vertical magazines for hinges or locks feed three CNC axis units able to insert the elements and screw with brushless motors.
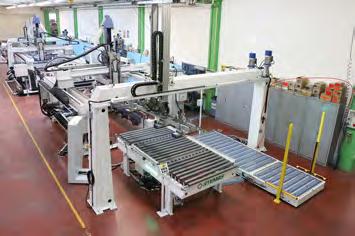
A fundamental feature of Stemas commercial strategy is the long-term relationship with its customer. Whoever owns a Stemas machine is a repetitive purchaser; many door factories can be a display of up to 30 Stemas machines, being proof of the high reliability of the installations and the after-sale service.
For further information please visit our websites or email for more details. www.stemas.it stemas@stemas.it
TK Joinery (Blandford) Ltd a leading joinery manufacturer in Dorset with exacting standards which has re-cently taken delivery of a Soukup UK Series CNC Window Centre Model Crafter and Soukup Hydraulic Frame & Sash Cramp Model FP32.21 to increase productivity and efficiency to meet increased demand for its quality timber windows and doors. Chris Owen, owner of TK Joinery researched the market for several years for a CNC window machinery supplier which could supply the correct CNC window machine complete with tooling and window software providing a total package from one supplier – rather than from suppliers which could only supply a CNC machine without tooling advice or any dedicated window software.
Until Chris contacted International Woodworking Machinery (IWM), the exclusive supplier of the award-winning, specialist, dedicated, window and door machinery manufacturer Soukup Machinery.
In recent years, Soukup Machinery has gained an impressive reputation in the UK joinery industry for man-ufacturing unique CNC window machinery – dedicated to the UK window and doors joinery market com-plete with Soukup-designed window tooling to BS 6375-1:2015 and PAS 24:2016 certification plus its im-pressive Soukup Wincreator window software.
The impressive Soukup package provides users with a comprehensive three-inone package for UK window styles of casements and doors, sliding sash windows with pulley and weights and balance springs includ-ing creating the horns, trenching the cill and head, producing the boxes, cills and beading.
Chris Owen and his works manager, Dylan, naturally wanted to view a machine in action, and as such ar-rangements were made to visit one of the 25 Soukup CNC Crafter installations in the London area alone – all within the M25.
One such Soukup Crafter customer is Todi & Boys Ltd in Chessington which installed in 2017 a Soukup Crafter, Coukup Hydraulic cramp FP32:21, Soukup CNC milling and drilling Versa, Soukup automatic crosscut crossline 500 plus a Soukup five-head planer/moulder.
Following their visit, Chris and Dylan were suitably impressed with the Crafter and its capability to manu-facture at least 10/15 complete sliding sash including boxes, cills, horns, trenching the cills, heads, bead-ing per day – plus at least 15-20 casements and doors and other joinery components all achieved with just one operator. In view of this outstanding performance, Chris was minded to confirm his order for a Soukup UK series Crafter CNC Window Centre and a Soukup Hydraulic Frame and Sash Cramp.
The machinery was delivered, installed and commissioned, immediately after the Easter holidays and ev-erthing went seamlessly – complete with training provided to Chris and Dylan with the full knowledge on how to produce knock-down finished window components saving more than 40% of production time over normal tradition joinery production methods.
Following the installation, works manager Dylan commented: “The Soukup is brilliant, it makes makes fantastic windows, but the only thing wrong is it doesn’t make the coffee!” 01636 918280 www.iwmachines.co.uk
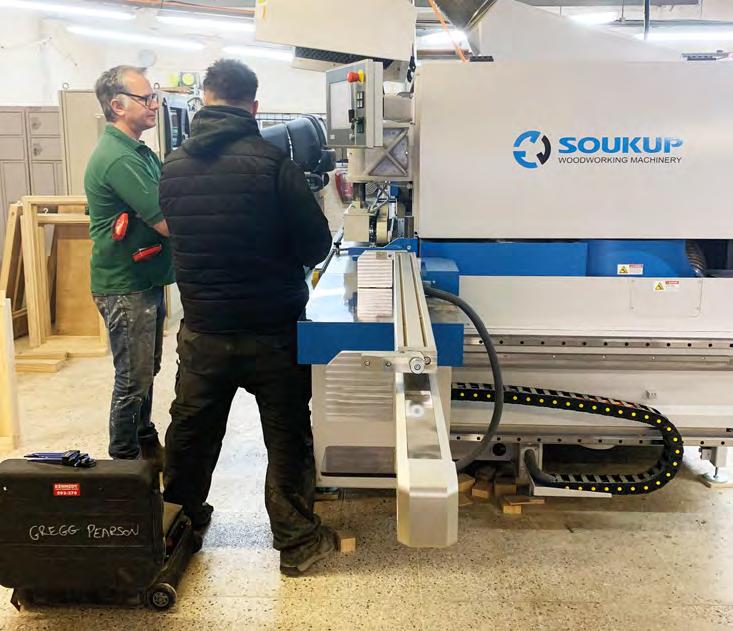
Dorset joinery firm impressed with outstanding window and door CNC machine performance
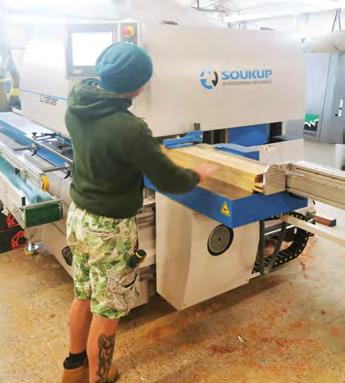
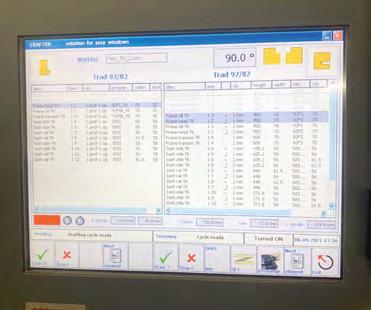
Chris Owen of TK Joinery during commissioning and training
Kündig is widely recognised as being one of the most experienced and highestquality manufacturers of wide-belt and edge sanding machinery. Kündig has two manufacturing plants, one in Switzerland (which is also its headquarters, and where the research and development and special projects are developed), and the other in Gotha, Germany, where the production of the standard wide-belt and edge sanding machinery takes place.
In today’s market, where manufacturers are facing all sorts of different challenges in generating the right surface finish, Kündig boasts the experience to respond and to offer a solution to what is seen by many as near impossible.
Where first impressions count, manufacturers strive to achieve ‘that something special’ when it comes to surface finishing, and this is exactly why some of the world’s leading manufacturers of grand pianos have researched the market and commissioned Kündig to produce sanding machines to generate a perfectly flat surface and give intermediary sanding, building up to a high-gloss finish where any imperfection would stand out and not be accepted.
Other companies which have faced challenges have needed sanding accuracy to +/-0.02mm, and turned to Kündig to meet the tight tolerances for final product. These machines are typically used in the automotive industry, but have also been installed by manufacturers looking to calibrate brake discs for commercial aircraft, insulation materials, plastics, etc.
Of course, the more familiar application for Kündig is in the woodworking industry, where its fixed-bed design has proven to give long-term accuracy, being fixed to the machine frame and the sanding group that raises and lowers.
This system has proven to be especially beneficial for calibrating heavy components – typically fire doors, where the fixed bed cannot move despite the weight of the door or the amount of pressure generated during sanding. This fixed-bed system is, of course, also a huge benefit for veneer sanding, where veneer-cutting technology has increased, making the thickness of veneers less and less – hence making sanding accuracy more important than ever.
To cater for a wider part of the market, Kündig recently celebrated its 75th anniversary with the introduction of the new Kündig Master, which offers an out-of-the-box solution. The idea behind the machine is to produce a more cost-effective machine while keeping to all the traditional values associated with Kündig.
The machine is produced in the same factory as the Premium, Brilliant and Perfect models but is manufactured to a standard configuration to allow serial production, hence reducing the cost to produce. The Master has a generous 1350mm working width, and two sanding heads – first contact roller followed by finishing pad, which is available for solid wood or as a segmented pad for sanding veneers.
The Brilliant series of machines are aimed at those
Setting superior sanding standards since 1945
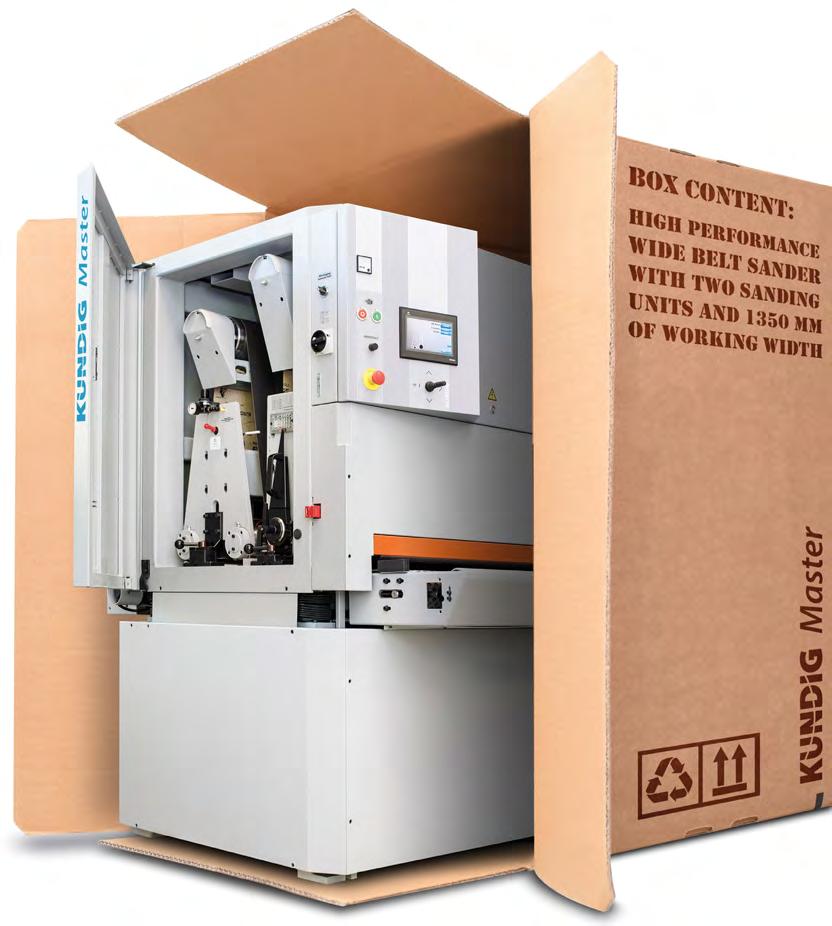
looking to achieve the highestpossible quality of surface finish. Simply placing the abrasive at a 10° angle eradicates the wavy scratch pattern inherently shown on traditional-style sanding machines. These machines are available in widths of 1100, 1350 and 1600mm as standard, and available as either single- or multi-head machines.
In recent times Kündig has seen a substantial increase in the demand for purpose-made machines throughout different industries. Typical of this is a recent delivery to a company which wanted a machine to calibrate five-piece doors ready to go straight to spraying, to then denib and also have the possibility of creating a rusticstyle surface with a ‘bandsaw’ finish.
The answer was a four-head sanding machine with a contact roller, oblique sanding pad, cross belt to sand the rails – alternatively, using a 16-grit belt to create the rustic surface – followed by a carousel brush unit to sand into the profiles and soften the edges.
Despite the disruption throughout the past year, Kündig have seen sales growth, both in the UK and in other markets. 0845 833 0565 www.kündig.co.uk
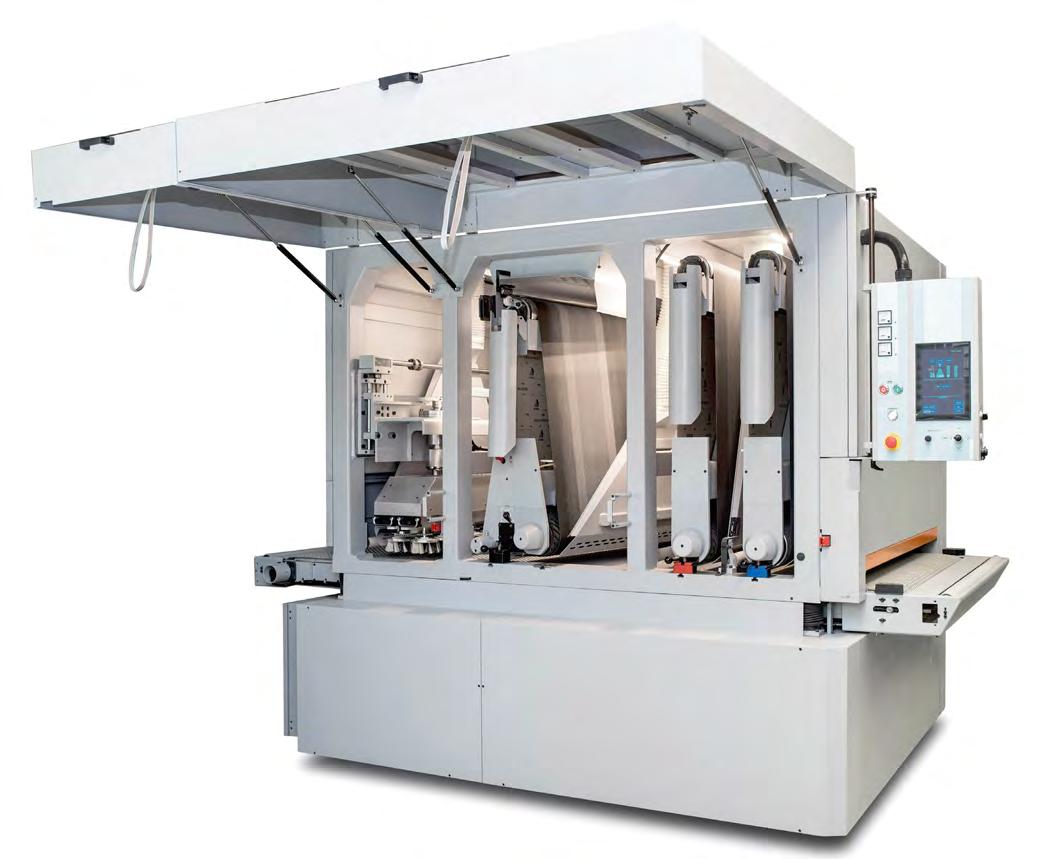
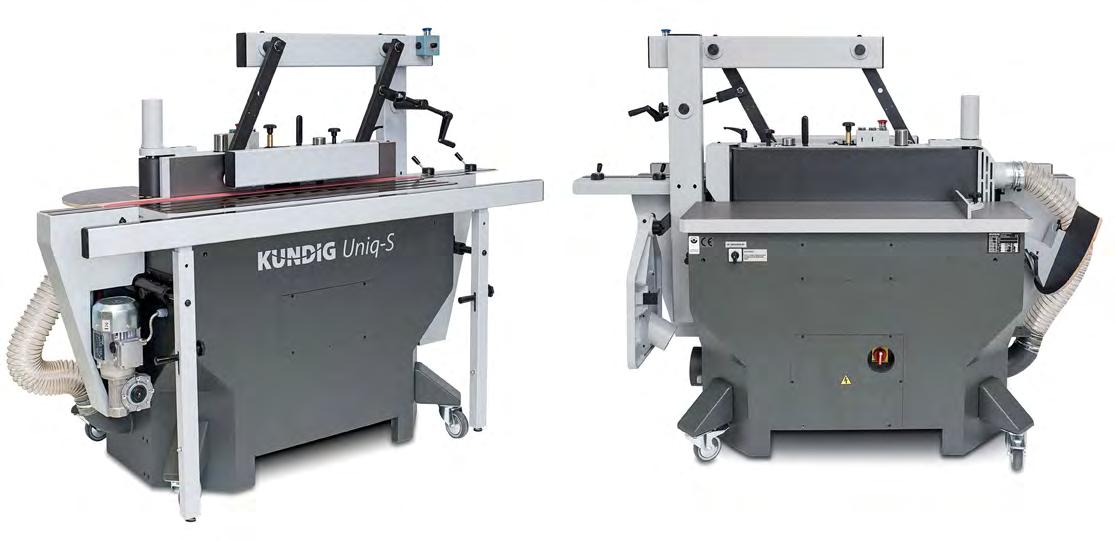
2022 promises to open new doors for Moralt AG
Despite a number of challenges and disruptions, 2021 has proved to be a very good year for the specialist German producer of certified technical door solutions, Moralt AG. Clearly, throughout 2020 the pandemic affected a lot of businesses with lockdowns in several of its key markets, staff on furlough at both its customers and suppliers and major door projects cancelled or placed on hold, all adding to a subdued and frustrating trading period. “Our particular need to further test and develop products was also badly hit,” explains Steven Dennard, who looks after Moralt’s International Sales. “Test institutes were unable to offer their services and lack of available finances to fund these developments meant we were all especially happy and eager to welcome 2021.” “A slower start to the year began to show signs of promise in the Spring and our twoweek acoustic test package at IFT in Arnsberg, northern Germany with the support of Mann McGowan showed some excellent product performances and assisted the mood greatly. Our FireSound Xtreme FD120 door now performs acoustically to Rw dB44 as a single leaf door, and as pair, dB43, making this our strongest acoustic product, which at only 58mm thick, is excellent. Further confirmed positive acoustic performances within the internal “Laminesse” door range with concealed hinges and concealed door closers means that our acoustic door offer has become a lot stronger for contract specifiers. “A fire door test package FD60 to BS 476 Pt. 22 at DMT in Lathen, Germany in early September in part to compliment the March acoustic testing covering concealed closers and hinges, was our next larger testing programme. Moralt FireSound was the principle focus of these tests and we included an RFID access solution from Assa Abloy in the test doors as well so that specifiers could consider a high acoustic, fire rated door products with electronic card readers for use in hospitality,
‘Despite the ongoing challenges presented by the pandemic, 2021 has been an extremely successful year for us with strong sales from the UK, European and Middle East markets’
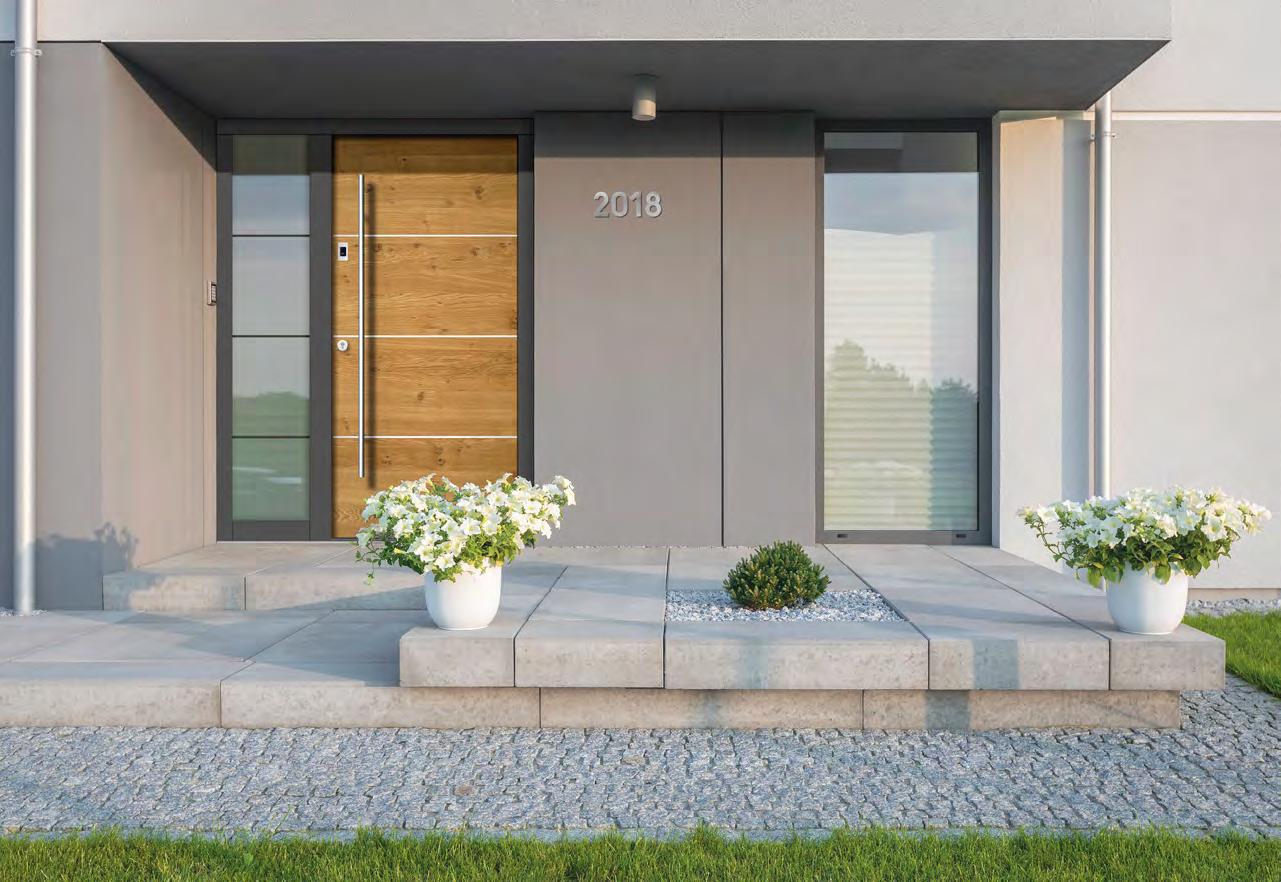
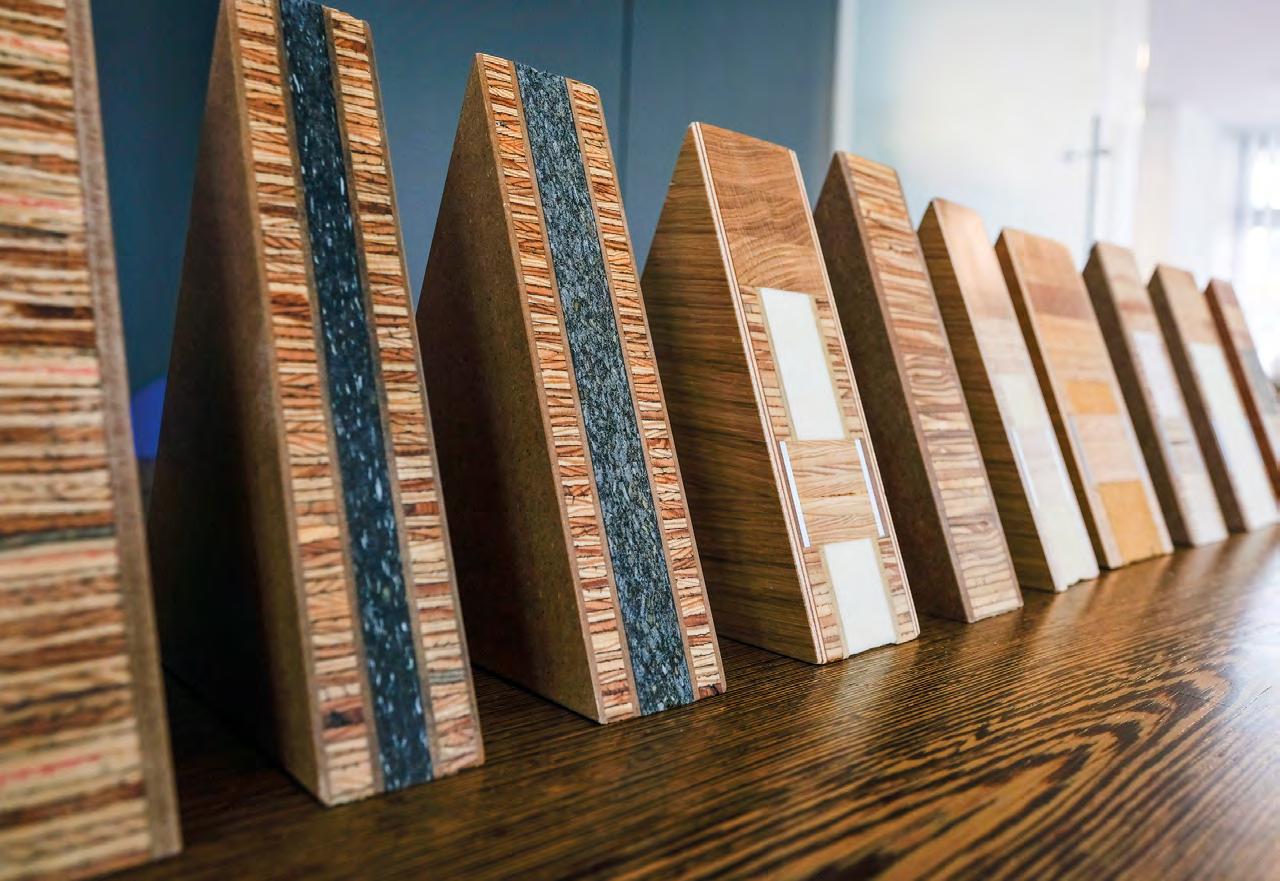
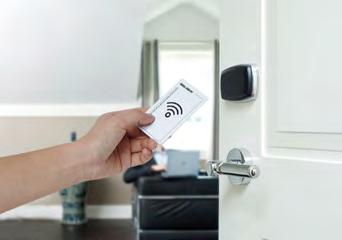
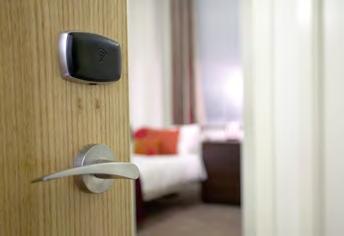
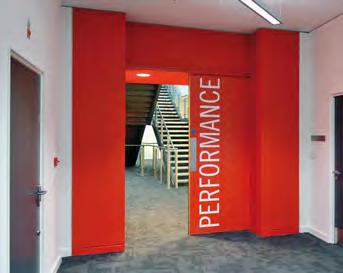
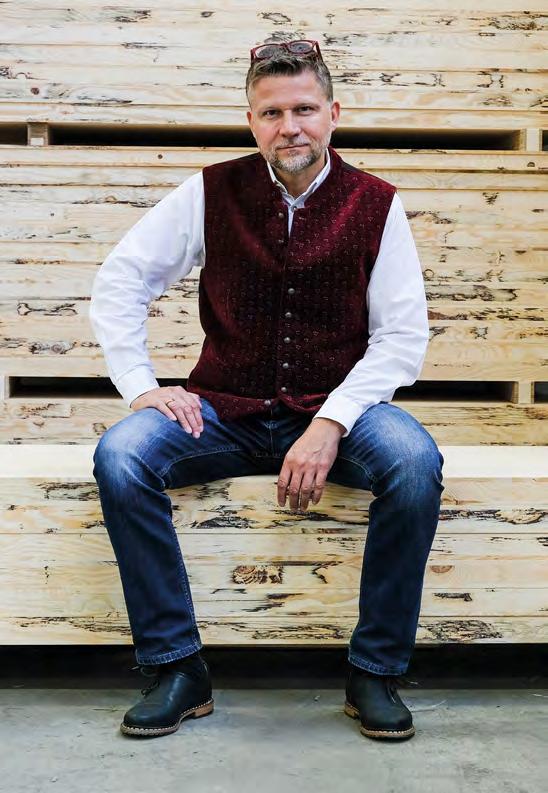
Moralt’s range of internal and external door blank solutions is one of the most technically sophisticated on the market
education, healthcare and administrative environments. The tested doors were all 2440 x 1000mm in size so that we might see a good size scope added to our already comprehensive acoustic and fire range of doors.” 2021 has seen the business continue to make significant investment, for example with the introduction of Hubspot, a CRM system which enables the company to manage product enquiries from around the globe more quickly and efficiently. “With this system in place, sales enquiries can be considered in line with our R&D work that is so critical in serving our customer’s requirements,” Steven added. Plus, in the Autumn, the company began work on a UL door test package for Spring 2022 which will appeal to existing markets in the Middle East as well as being the basis of its future commercial work in North America. “In September we exhibited
almost two years, the Big 5 in Dubai which saw heightened interest in our FireSound high acoustic and fire rated door cores, as well as our timber external door core range. It was great once more to be able to engage with people directly from around the globe and it proved to be a major success for us.” Managing director at Moralt AG, Klaus Feile echoes Steven’s optimism. “Despite the ongoing challenges presented by the pandemic, 2021 has been an extremely successful year for us with strong sales from the UK, European and Middle East markets. In addition, the introduction of FireSmoke and FireSound Xtreme (FD90 and FD120) as stock items at both UK distributors – James Latham and Falcon Panel Products – means that we now offer a full suite of FD30, 60, 90 and 120 fire ratings with our sustainable, certified timber door blanks but also a solid acoustic range too with dB40 and beyond acoustic performances in all fire categories. Klaus added, “Throughout this difficult period, we have used the time effectively, continuing to invest in the business with the latest technology to deliver innovative solutions across both our production facility and processing systems. This will ensure that we are in the best possible position for future growth which is expected to continue through 2022.” info@moralt-ag.de
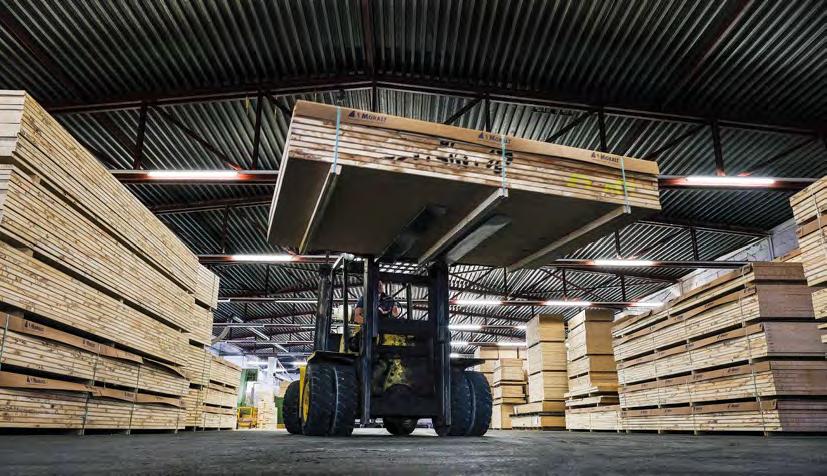
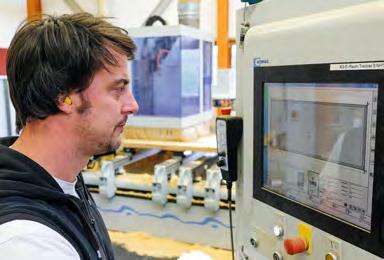
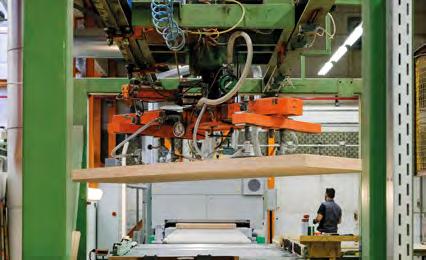
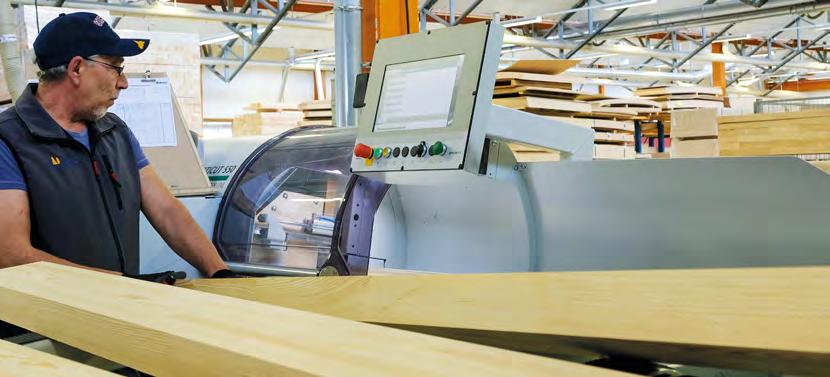
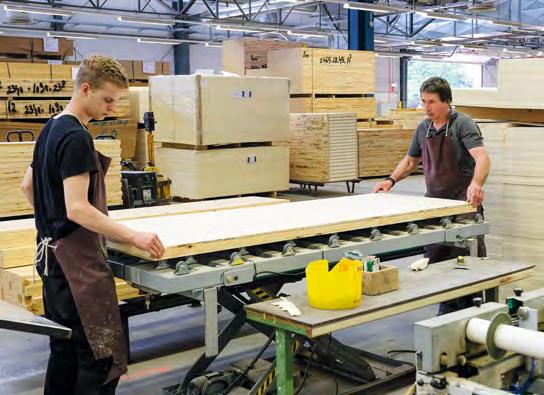
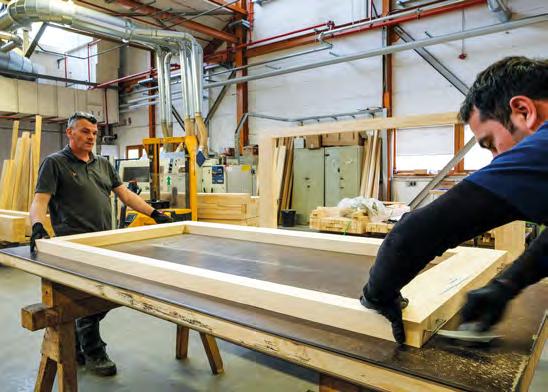
“A recent visit to one of England’s castles got me thinking about how doors and windows have evolved over the years,” says Neil Jones, marketing manager of Coastal Group, “a lot of which has come about from shifts in consumer demand, lifestyle, and perception of quality, further enforced through the ongoing pandemic.
“There are three main areas that have evolved in doors and windows: the ‘inside-out’ lifestyle, leading to increased demand for oversized glazing with larger, heavier sliding doors; home improvement programmes influencing homeowners to have an increased perception of the aesthetics of their doors and windows; and homeowners spending more time at home, meaning they’re looking for higher-quality products which look and perform better for longer.
“This had led to a need for door and window manufacturers and hardware manufacturers to evolve to meet this change in taste and demand, or get left behind. But not all companies have evolved with it.” “Don’t be the ‘Kodak’ of the door and window industry” As Loren Jenner, Coastal Group MD, says: “Whilst it’s difficult when you’re busy to take a step back and assess if your current hardware offering really does meet the current demand, it’s most definitely worth it.
“Nobody wants to become the ‘Kodak’ of the door and window industry – but there’s a danger of that happening once demand starts to settle and homeowners spend more time shopping around for their chosen supplier of their new doors and windows, unless you evolve with the times.
“And it’s through this that we’re seeing our BLU range of 316 marine-grade stainless steel hardware becoming increasingly popular,” says Loren.
“We’re constantly innovating and developing our hardware product offering based on customer feedback and requirements. Our BLU hardware range now includes product to suit contemporary and classic style tastes, and is available as a suited range in a variety of finishes. So, if a homeowner wants a classic-style front door, with hardware to suit that style of door, but then wants large sliding doors or a set of bifold doors on the back of the house, we have hardware to suit that also.
The evolution of door and window hardware
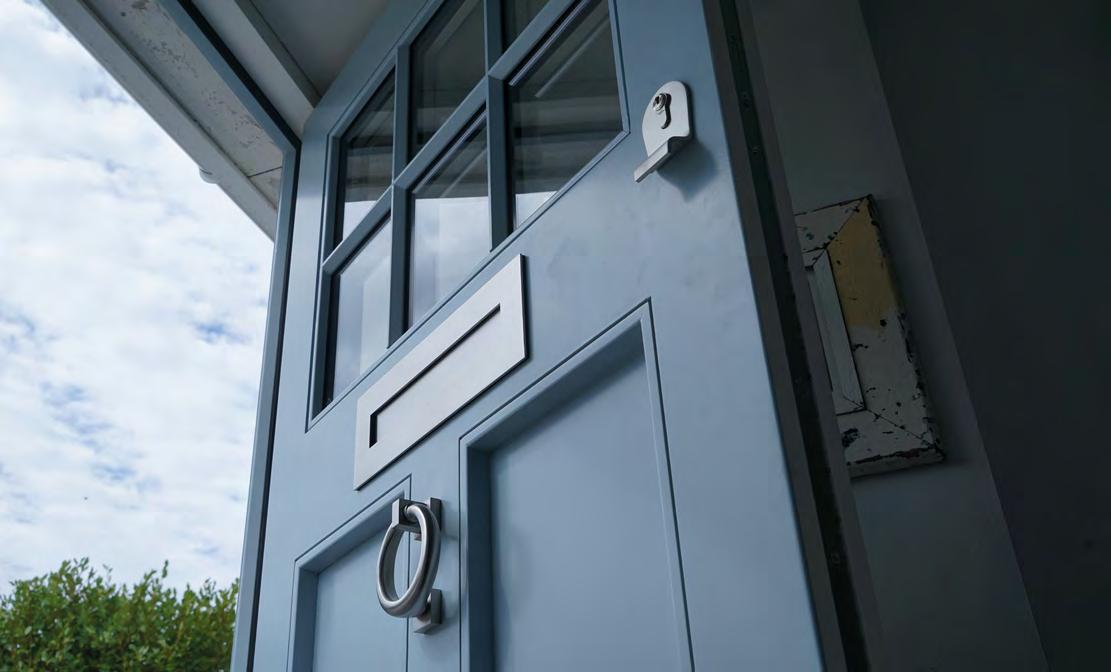
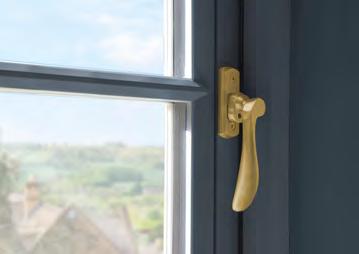
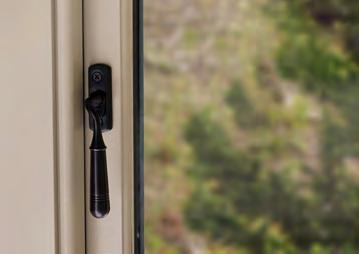
>> Ensuring the best possible performance for doors and windows “Throughout this ongoing development of the range we’ve continued to manufacture the BLU range using 316 marine-grade stainless steel, to give the best possible product performance.
“Compared to the overall cost of the door or window, the cost of the handle is a relatively low percentage,” Loren continues, “yet it is what gives the highest impression to the end-user client. The homeowner will often base his rating of how good the door or window is based on what they can see, touch and feel – the hardware.
Helping those that want to progress “We’re seeing the door and window companies that want to progress increasingly coming to us and standardise on offering our BLU door and window hardware for their front entrance doors, patio sliding doors, bifold doors and windows.”
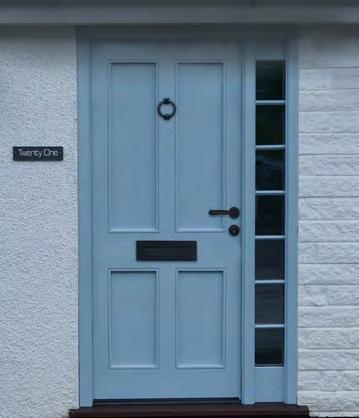

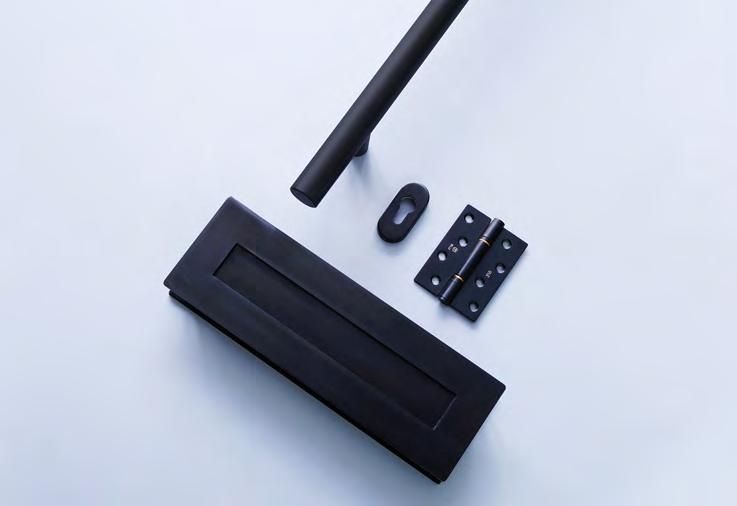
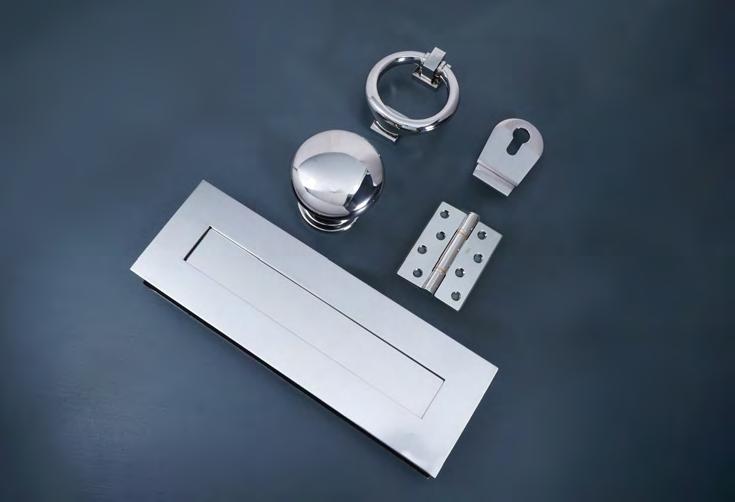
According to Lore, feedback from customers has been excellent, and is proving the benefits of using BLU hardware, as one composite door manufacturer testified:
“We were introduced to the BLU range of hardware after being let down by our supplier,” they said. “Coastal were able to step in and deliver a great service and great product. We were impressed from the start, as they not only got us out of a potential hole, but were happy to go the extra mile for us.
“From a product perspective, you are looking at high quality from the BLU range – the marine-grade stainless steel is second to none, both in terms of styling and performance.” 01726 871025 www.coastal-group.com