32 minute read
News & Events
Next Article
Software launch delivers “completely new way” to design, produce and distribute furniture
imos AG has unveiled the latest version of its successful iX software technology, which is already in use at more than 4500 companies worldwide. imos AG develops and distributes software for furniture and interior design worldwide. iX 2021 is an integrated software solution that connects all essential work steps, from sales and design to production, into a continuous and efficient process.
Connectivity, new cloud services as well as optimisations in terms of handling, convenience and speed mean industrial companies, as well as more humble businesses, are, according to imos, able to expand their business models across company boundaries, to handle workflow from sales to production more securely, flexibly and efficiently, as well as modernising their service. imos says that with the extensive digital application possibilities of imos iX, furniture and interiors can be designed, produced and distributed in a “completely new way”.
Numerous videos, graphics and animations provide clear information on how the new version sets the digitisation of the furniture industry in its sights. Experience iX 2021 online at https://ix21.imos3d. com/en/ to review the innovations and brand-new features. www.imos3d.com
AAG launches new and upgraded website
Leading global manufacturer and distributor of industrial-class CNC machining solutions, AAG, has launched a new and radically upgraded website. Visitors to aagcnc.com will now have easier and faster access to comprehensive information about AAG’s AXYZ, WARDJet and CNCShop.com power brands, and the full range of tailored CNC routing/cutting and print finishing, waterjet cutting and essential spare parts, accessories and consumables available respectively via these brands. In addition to enabling companies to increase automation in the workplace and consequent business growth, competitiveness and profitability, aagcnc.com will open up a host of new opportunities. These will not only fuel further expansion within the industries in which these companies specialise, but also, and significantly, will open up new opportunities for engagement with other industries, due to AAG’s internal strategy of greater market diversification.
Innovative new features of the website include information on the specific industries in which CNC machines supplied by AAG have become a preferred choice, and a section entitled Featured Work, which highlights major projects undertaken by AAG customers, and in which AXYZ and WARDJet machines have been pivotal to their successful completion.
A history of AAG, from inception to the present day, which includes the origins and evolution of the AXYZ, WARDJet and CNCShop.com brands and details of AAG global locations, serve as a fitting conclusion to the new website. www.aagcnc.com
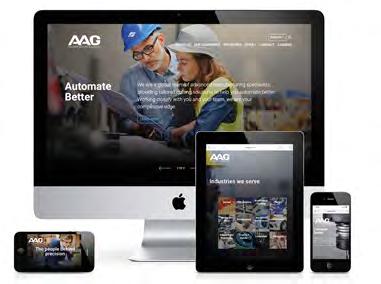
Blum appoint two new Product Support Advisors
Jodie Mack Jodie Mack joins Blum after a career including teaching sport at a school in Cambridge, followed by sales jobs in the catering industry. With time on her hands in lockdown, Jodie developed a hobby and passion for upcycling furniture, at one point having five pieces filling her garage! She really enjoyed the technical challenges involved.
With a move to Leighton Buzzard came the opportunity to move careers again, and in June 2021 Jodie joined Blum as a Product Support Advisor. “As a hands-on person, the technical role appealed to me. I had no experience in the kitchen industry, so the role also gave me the challenge of pushing myself and widening my skill set and knowledge in a completely new industry. The role offers a huge variety from day to day which is great. Blum is a wonderful company to work with – my team is so supportive, and Blum is providing me with the stepping stones to become the best I can.”
Nathan Sydney I’ve worked in various customer service roles over the last 13-14 years, from PC World to PortAKabin.
“I have always enjoyed practical work and believe I have a strong technical mind. The job opportunity at Blum allowed me to make use of my extensive customer service experience but also allowed me to utilise and develop my practical skills. The variety of tasks that the technical team gets involved in was a massive attraction for me since my last job was always the same day to day and I was losing interest.
“I am part of the technical team offering advice and technical services to our customer and partners. My focus going forward with be assembly devices so I will be working more with our machines, learning more about them and doing service and commissioning work. I am now part of the warehouse maintenance team and will be servicing our warehouse crane system.
I have really enjoyed my first three months at Blum, lots of variety, great training structure and made to feel very welcome. The office is a fantastic place to work, very comfortable and all the equipment we use is always to a very high standard.”
Jodie Mack Nathan Sydney
A big year for Daltons Wadkin
2021 has been an eventful year for Daltons Wadkin – celebrating its 120-year anniversary, recording record sales across all departments, welcoming new staff members to the expanding team, being nominated for the prestigious Made in the Midlands award, becoming an official SCM machinery partner, and opening an extended showroom and demonstration area.
Founded in 1901, Daltons Wadkin is the longest-established woodworking machinery supplier in the UK. Now under the watchful eye of fourth-generation family member Alex Dalton, the company has welcomed in its 120-year anniversary against a backdrop of soaring demand and a global pandemic.
“There is never a dull day’” comments MD, Alex. “We, like most of the industry, have been fortunate enough to be on the positive end of the pandemic. Demand for both new and pre-owned machinery has never been higher. Requests for operator training and service contracts have also been in huge demand. I often wonder what my late father and uncle would have made of it all ...”
To help keep pace with demand and ensure continuity of service for its customers, Daltons Wadkin has taken on new staff in all departments. “We have welcomed both newbies to the industry as well as seasoned professionals to our service, training and engineering departments,” continues Alex. “We have around 35 staff members now, and are looking to recruit further into Q4’”
The past year and a half has had its challenges, too. Like the majority of businesses, Daltons Wadkin was impacted by the arrival of Covid-19 and, in line with the Government guidelines, was forced to close its doors in March 2020.
The real success and achievements of this business lie in how it responded and adapted to the pandemic in order to remain current during a pivotal period in its history – a fact recognised by a nomination for the Insider Media Made in the Midlands award.
A key strength of Daltons Wadkin is its relationships with leading European manufacturing specialists, and 2021 saw the start of a new partnership between Daltons Wadkin and SCM.
“I have always admired the professionalism of the SCM brand,” enthuses Alex. “Their offering of high-quality, Italian-built machinery dovetails perfectly into our existing portfolio of solid wood- and panelprocessing equipment. It is early days, but already we have seen significant sales across the range, with new stock arriving almost daily’.”
An impressive range of SCM equipment joins Altendorf panel saws, Elcon wall saws, Kimla CNC equipment, Salvador crosscut saws and Stenner band resaws in Daltons Wadkin’s Nottingham showroom. To allow sufficient space for showcasing the huge range of machinery on display, the showroom and demonstration area has been expended by a further +50%.
“Demonstration is key for us. When viewed in person, the build quality, performance and advantages of the machinery we offer is immediately evident,” says Alex. “Our recent Wood & Panel Machinery Show was testament to this, and we continue to welcome anyone looking to take advantage of our specialist services.”
For more information on the range of equipment and services offered by Daltons Wadkin, call 0115 986 5201 or email info@daltonswadkin. com. www.daltonswadkin.com
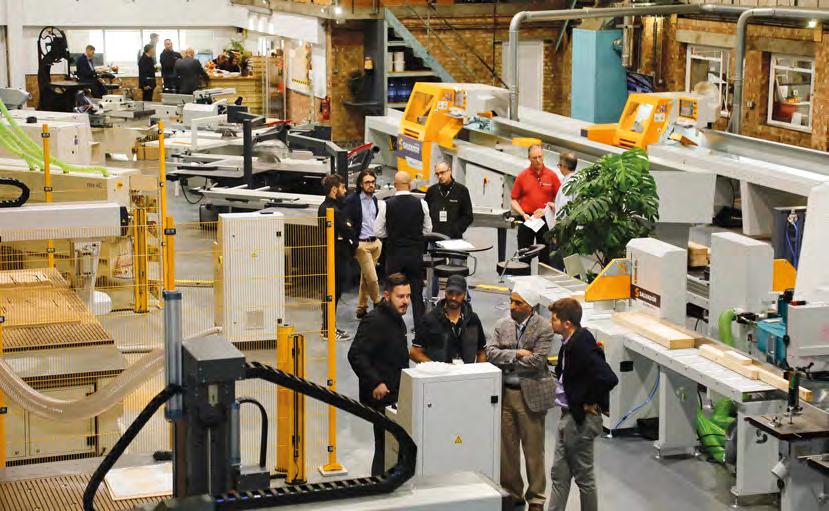
‘I have always admired the professionalism of the SCM brand … it is early days, but already we have seen significant sales across the range, with new stock arriving almost daily’
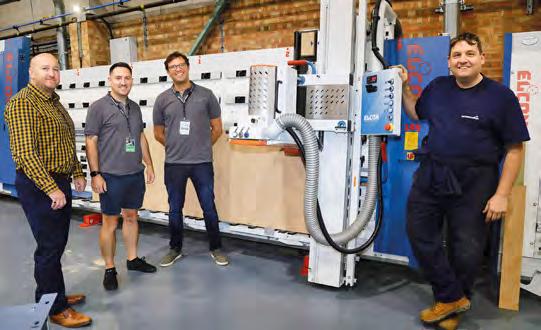
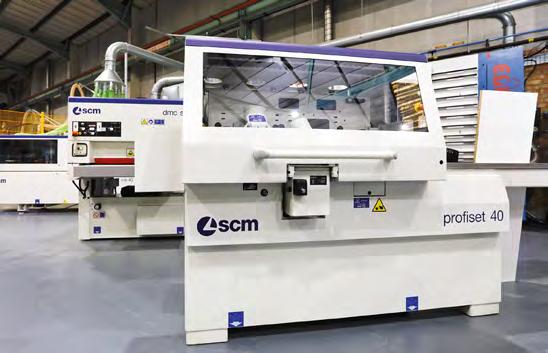
BFM service offers Covid-compliance support
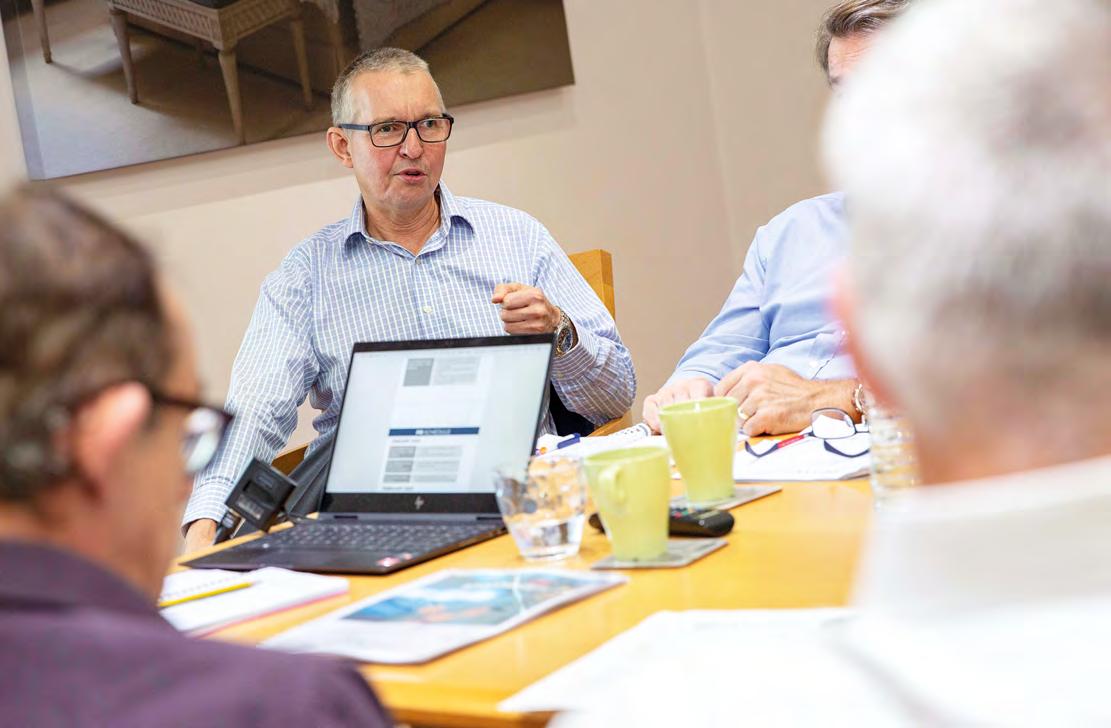
Navigating the health and safety environment can be a challenge enough, but Covid has added new pressures for the furniture manufacturing sector.
Support in this vital area is at hand to ensure compliance, through the British Furniture Manufacturers’ (BFM) Environmental, Health and Safety (EHS) service.
Developed to help furniture manufacturers keep their workers safe and their business compliant to avoid prosecutions, the service is one of the trade body’s most valued member benefits.
Headed-up by Alistair Bromhead, it has proved of significant value as the industry addresses the changing work environment in the pandemic.
BFM MD Nick Garratt says: “The Health and Safety Executive (HSE) is calling for businesses in Great Britain to make sure they’re Covidsecure.
“Inspectors are out and about, putting employers on the spot and checking that they are complying with health and safety law.
“The HSE is publicising that it is still continuing its Covid-19 spot checks in workplaces, especially with increasing numbers of office workers returning to the workplace. As of September 2021, some 316,000 checks have been completed.
“Being Covid-secure means being adaptable to the current guidance and putting measures in place to control the risk of coronavirus to protect workers and others.
“By law, employers have a duty to protect workers and others from harm, and this includes taking reasonable steps to control the risk and protect people from coronavirus.
“It’s important that workers are aware of the measures that will be put in place to help them work safely.
“Our EHS service is here to help ensure compliance. That includes 24/7 access to BFM’s online guidance, handbooks and downloadable templates,
“Members can also access BFM’s free telephone helpline, as well as individual on-site support at heavily discounted rates and a monthly EHS bulletin.”
An attractive feature of BFM membership is the provision of a subsidised first visit in the year for EHS issues – at a rate of £125 + VAT + travel expenses.
Any additional visits are then charged at the normal daily member rate of £450 + VAT + travel expenses, which represents a sizeable discount over the typical market rate.
Services available include: review of EHS issues; noise surveys; audiometry (hearing tests); spirometry (asthma surveillance for those exposed to wood dust or coatings); dust exposure monitoring LEV testing (local exhaust ventilation); and help with risk assessments, training or improvement notice compliance. www.bfm.org.uk
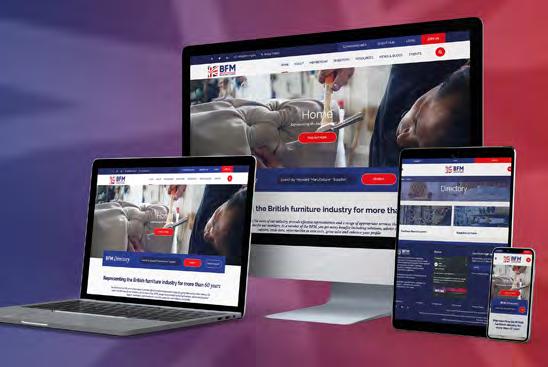
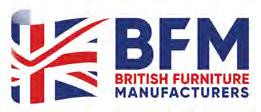
CAD+T welcomes a new generation

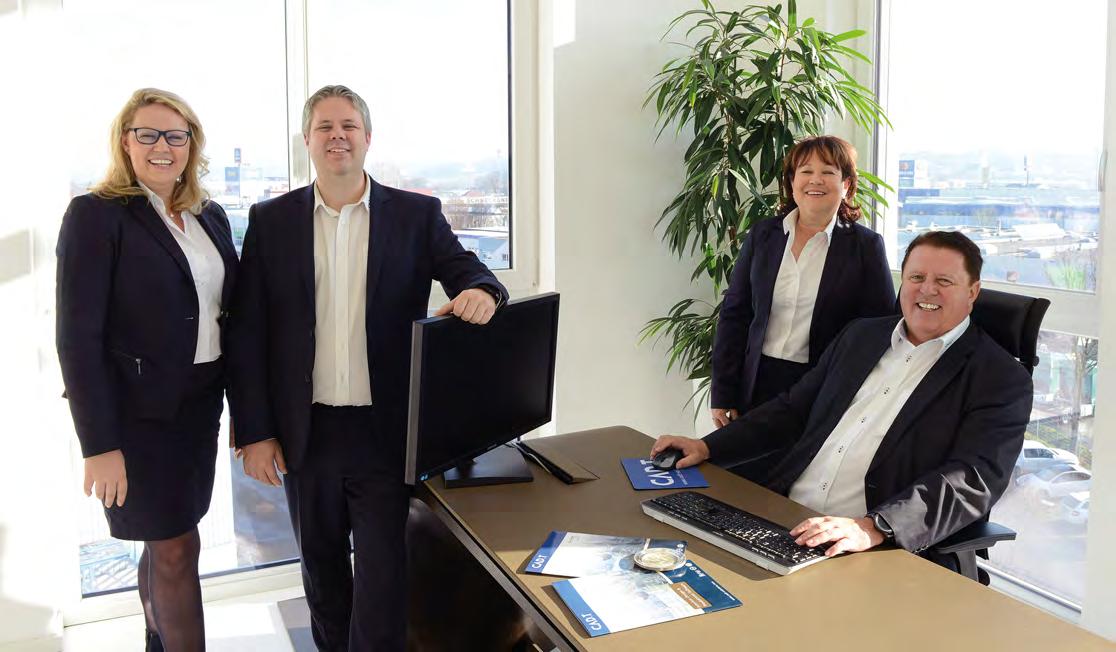
Martina and Thomas (left) with Rosemarie and Anton Schwarz
After more than 30 years, the founder and CEO of the international CAD/CAM and ERP software company, CAD+T Consulting, Anton Schwarz, is stepping down as CEO. The move, which will take effect from this autumn, will see the current CTO, Thomas Schwarz, and international sales director, Martina Schwarz, reprise the role and continue to carry the business forward.
Anton founded CAD+T in 1990, and in the same year launched the company’s first AutoCAD-based design software. Success followed, and a year later the company opened its first subsidiary in Germany, growing its bespoke software and consultancy offering to the furniture design and manufacturing industry. Within 10 years, the company had over 1000 clients worldwide, and as his workforce grew, Anton welcomed his son, Thomas, and later his daughter, Martina, into the business.
Today, the company has subsidiaries across the world, including in the UK, UAE, East Asia and Australia, and employs over 80 members of staff. It is renowned for supplying complete software solutions to the furniture industry, and offers over 60 software applications based on AutoCAD and Autodesk Inventor for batch-size-one production and serial production.
Martina says: “My father had a vision – to become a leading bespoke software provider for the furniture design market. He has achieved this and so much more. Now, with the industry entering a new generation of developments, and cloud-based solutions leading, it seems like a fitting time for him to pass the baton onto the next generation of the Schwarz family.
“My brother and I share my father’s vision. We want to continue to create innovative software solutions to the global furniture design and manufacturing industry, with the family ethos still very much at the heart of our business.
“After all, companies consist of people. The quality of our technology, product offering and service depends on the people behind it. We want to offer our customers continuous added value, and that all stems from the enthusiasm and dedication of our staff. We intend to continue on this path and work with our customers to embrace technology and the power of digitalisation, and reap the benefits it has to offer.” www.cadt-solutions.com
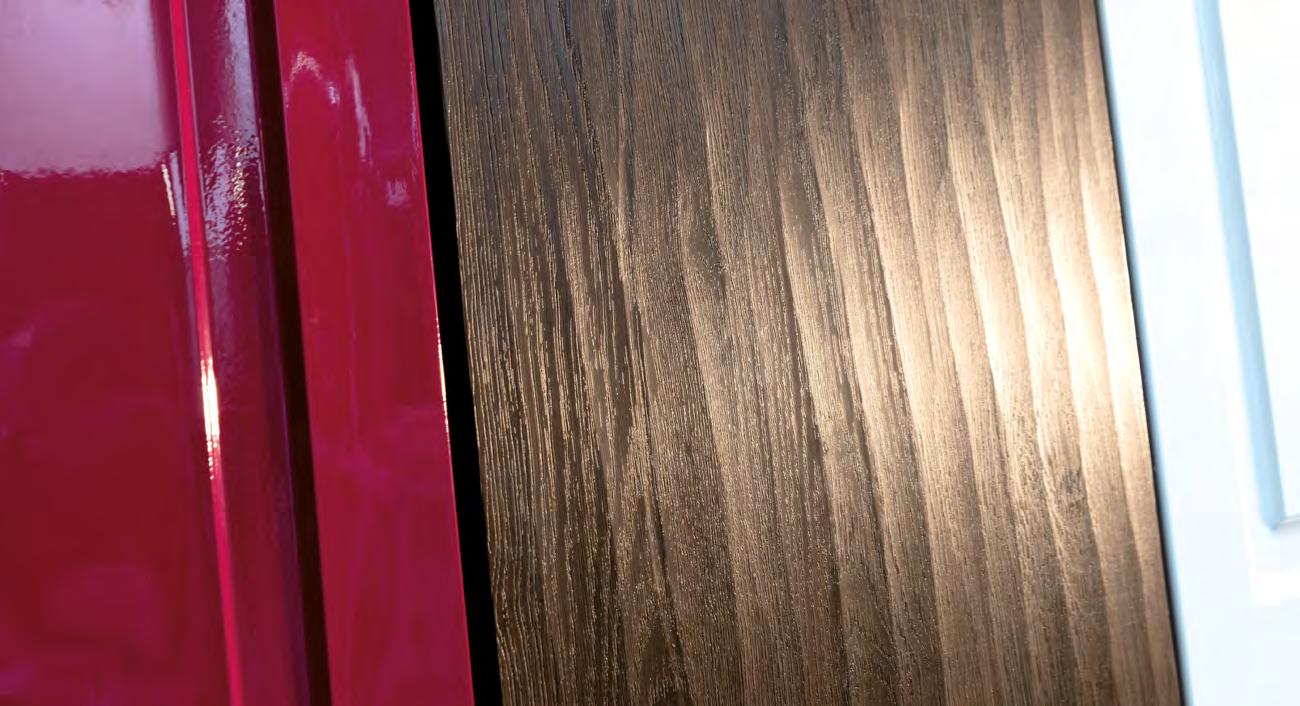
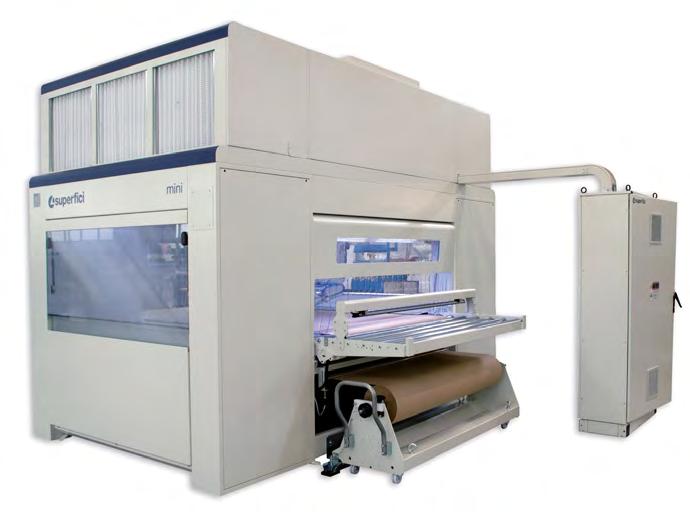
Furniture Clinic rolls out 100% recycled plastic for its product packaging in sustainability drive
Leading UK leather, wood and fabric restoration product manufacturer, Furniture Clinic, has reduced its use of virgin plastic by 80% as part of its eco-drive to minimise its plastic packaging footprint.
With immediate effect, the County Durham based business will switch plastic bottles across its own patented range of 100 specialist products to 100% recycled plastic (rPET), saving an estimated 30,000kg of virgin plastic from landfill each year. Furthermore, the introduction of cardboard packaging and paper packing, instead of plastic, will solidify its sustainability drive. Furniture Clinic, which operates from its 50,000 sq ft factory in Consett, County Durham with offices in New York and Hong Kong, employs 60 staff in the UK and shifts over 1,000,000 products annually to customers and distribution partners in over 40 countries worldwide. Accoladed as one of the top ten fastest growing companies in the North East of England in the prestigious Fastest 501, Furniture Clinic is also recognised as one of America’s fastest growing companies (Inc. 5000).
With a mission to extend the lifespan of any leather, fabric or wood item – from luxury home and garden furniture, to car interiors and equestrian equipment – conscious consumption is at the heart of the business model. An early pioneer of sustainability with founding roots dating back to 2004, Furniture Clinic secured an ISO 9001 accreditation2 in 2020, recognising its progress in reducing waste and increasing efficiency. The company is now focussed on developing its Environmental Management plan to become ISO 4001 certified within the next year. As part of its on-going sustainability drive to become cleaner, greener and more energy efficient, Furniture Clinic, has implemented several additional new systems to maximise its energy efficiency and further reduce its ecological footprint. Culturally, all employees are encouraged to help reduce carbon emissions; post pandemic, all office staff are able to work from home on a hybrid basis, cutting out unnecessary travel for meetings in favour of Zoom – there are also dedicated car pool spaces in the car park to encourage ridesharing. Charging points will soon be installed to promote electric vehicle usage and company car renewals will all soon be electric.
Beyond product packaging which has been overhauled to ensure it’s 100% recyclable, Furniture Clinic constantly review and assess a product’s lifespan and impact on the environment, reworking the formula if necessary to ensure it is ecofriendly. Passionate about reducing waste, the company recycles wherever possible and operates a near paperless environment. Furniture Clinic’s Managing Director, Ben Staerck, said: “As a restoration business, sustainability is deeply embedded in our DNA and we constantly strive to deliver the highest quality yet eco-friendly solutions for our customers and partners. Today’s news is an important milestone in our circularity quest and we’re proud to be doing what’s right to help preserve our planet for generations to come.”
From humble beginnings when founder Keith Staerck ran a small furniture upcycling business and produced and sold wood restoration products at trade exhibitions, Furniture Clinic grew exponentially when son, Ben, boarded to develop its digital presence in 2004. Today, Furniture Clinic has firmly cemented its reputation as the leading manufacturer of leather, wood and fabric cleaning and restoration products and services in the UK. All products are created inhouse using the most advanced and innovative techniques with input from expert leather restorers, upholsterers and French polishers who work alongside Furniture Clinic’s in-house and development experts to create the highest quality and most extensive range. The product range not only comprises cleaning and care products but also a full range of dyes, paints, fillers and glues. From DIY users and hobbyist renovators to professionals, the range is accessible and easy to use. Loyal B2B customers include Harrods, Rolls Royce, John Lewis, DFS, Four Seasons Hotels and the Royal Air Force. www.furnitureclinic.co.uk
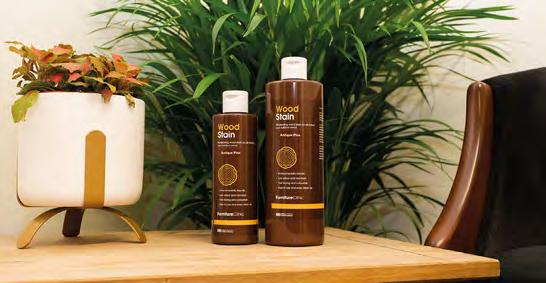
Furniture retailer walks coast to coast and raises £11k for Step 2 It
Furniture retail professional David Tracey has raised £11,000 for industry charity The Furniture Makers’ Company by trekking one of the UK’s longest hiking trails, the Coast to Coast, for the Step 2 It campaign.
The Coast to Coast walk is a 192-mile trailway that crosses the breadth of northern England, starting in St Bees, Cumbria and finishing at Robin Hoods Bay, North Yorkshire. Devised by fell walker Alfred Wainwright, the walk passes through three contrasting national parks: the Lake District National Park, the Yorkshire Dales National Park, and the North York Moors National Park.
David started the challenge on Tuesday 7th September, and he completed it in 16 days, finishing on Wednesday 22nd September. At the end of the trek, David had racked up 204 miles in distance with 25,300ft of elevation, which translated to 487,000 steps a 14 pound weight loss.
After setting off from St Bees, David spent five days walking through the Lake District, the most challenging part of the journey. The next leg of the challenge saw him cross over the Pennines at Nine Standards Rigg followed by traversing some boggy moorland. David was able to enjoy gentler landscape through the Yorkshire Dales National Park and Upper Swaledale, before stopping at Raven Seat Farm at the halfway point.
The Vale of Mowbray preceded the Cleveland Hills and the last three days took him across the North York Moors and onto his final destination at Robin Hoods Bay.
Completing the hike has been a long-held ambition of David’s and he decided to take on the challenge in 2021 as part of The Furniture Makers’ Company’s Step 2 It campaign, which has been inspiring individuals and companies in the sector to get active and raise funds for the charity.
David, who has worked in the furnishing industry for 40-plus years in senior and director level roles in companies including Dreams, Harveys, Hygena, MFI, Moores Furniture Group and Wesley Barrell, raised a total of £11,114 (including Gift Aid).
Commenting on the fundraiser, David said: “I’m so grateful to everyone who has sponsored me and donated to The Furniture Makers’ Company, a charity close to my heart. The support really did inspire me to get the job done, through some very challenging days – thank you all.” There is still time to sponsor David via his Virgin Money Giving campaign page: https:// uk.virginmoneygiving.com/DavidTracey
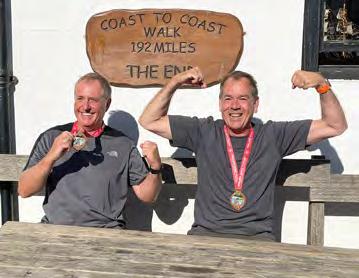
David, right, completing his impressive walk
Unilin Group claim a world first – the recycling of MDF and HDF boards
Innovative recycling technology developed in Belgium provides missing link for circularity
Timber is a renewable product and stores CO2 as long as it is not incinerated. So the longer timber can be used and reused, the more our climate benefits. For the production of its MDF and HDF boards, Unilin Group, a global reference in interior design and the building industry, is deliberately opting for the use of recovered and recycled wood.
Until now it was technically impossible to recycle the 100 million m3 of MDF and HDF boards manufactured worldwide each year. Unilin Group, with its headquarters in Flanders, has now developed a unique and innovative technology to reclaim the wood fibre from these boards in an economically viable manner and reuse them for the production of high-quality fibreboards on an industrial scale. Over time, this innovation will enable Unilin Group to keep 380,000 tons of CO2 per year stored in the wood fibre that is given a second life through this new technology. Missing link in a sustainable concept MDF (Medium Density Fibreboard) and HDF (High Density Fibreboard) fibreboards are commonly used in the furniture industry, in interior design and for the production of laminate floors. Unilin Panels, the division within Unilin Group that produces panel material, deliberately chooses to use recovered wood for its production. This is wood waste or wood that is no longer usable and is therefore saved from incineration. This means that Unilin Group is not cutting trees for production purposes in the first place, but is able to extend the life of waste material with a new application. Now Unilin Group takes things to the next level.
Véronique Hoflack, president of Unilin Panels, who herself was at the origin of the new recycling technology, explains: “Because of the use of adhesives as a binding agent for the wood fibres, no industrially viable method existed to recycle
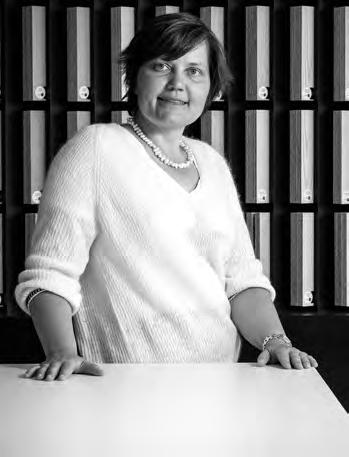
Véronique Hoflack, president of Unilin Panels
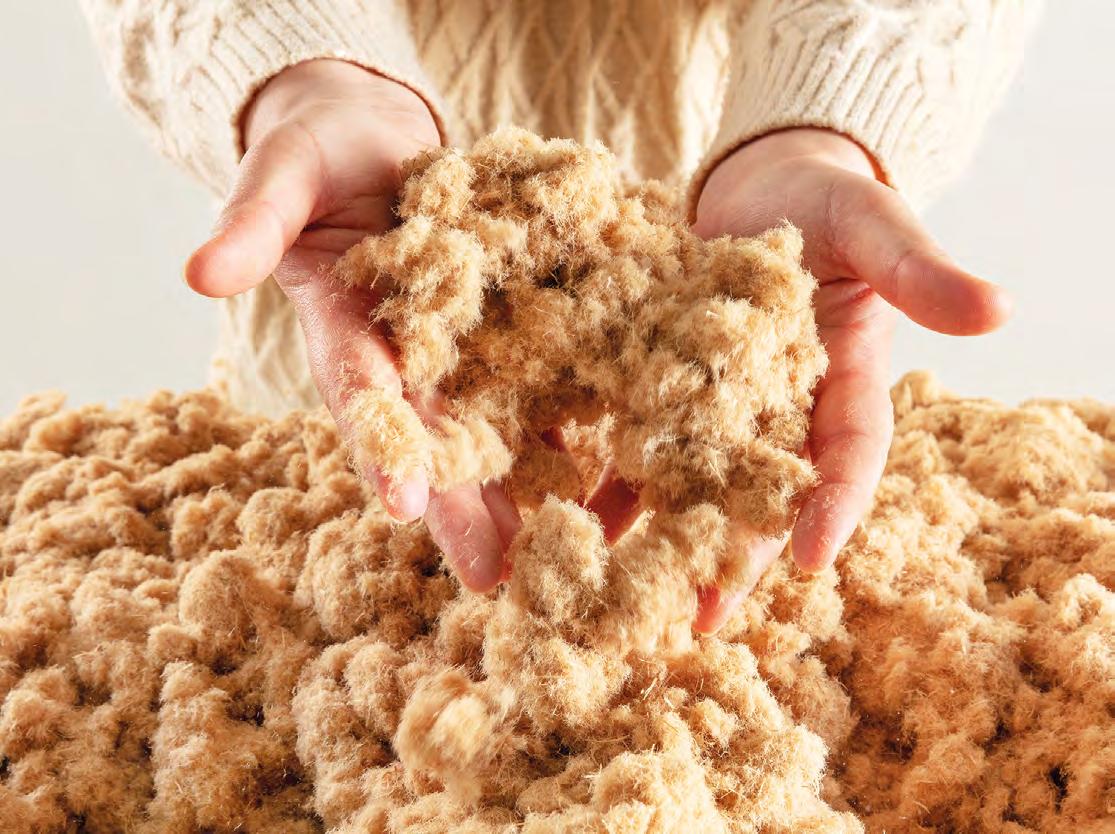
Bernard Thiers, CEO Unilin Group
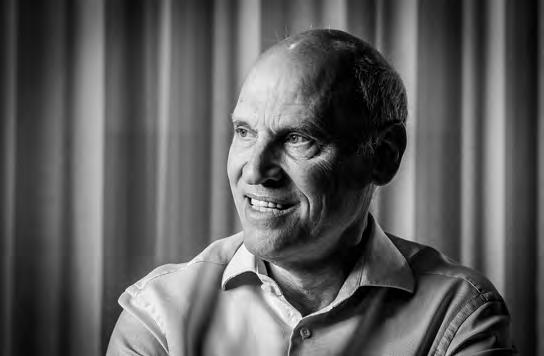
Unilin’s Bazeilles, France factory
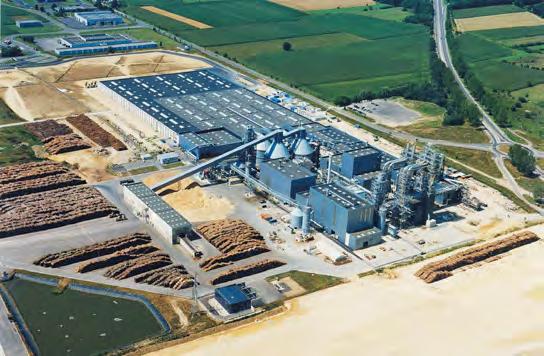
the fibres from fibreboard waste at the end of their product life. That means that the lion’s share is incinerated after use (on average 14 to 20 years). We have now succeeded in developing a new and innovative process to recycle these wood fibres and reuse them for the production of new panel material. For example our decorative Evola panels or Quick-Step laminate floors. This new technology doubles the life of the wood fibres! This longer life will give new trees the chance to grow and, in turn, store CO2. A major step forward towards circularity.”
Circularity in our DNA The development of this groundbreaking new technology fits seamlessly with the sustainability strategy of Unilin Group, which underscores the company’s commitment to contribute to the realisation of the Paris Agreement to limit global warming to 1.5°C. Unilin Group considers its commitment to innovation a precondition to realising these ambitious goals.
In the next two years the group will invest a further €160 million in Belgium, amongst others in research and development.
Bernard Thiers, CEO Unilin Group: “Circularity has been embedded in Unilin Group’s DNA from day one. In 1960 we started out as a manufacturer of flax chipboards and we developed a solution for the waste from the local flax industry. Even then we saw the challenges involving the reuse of materials as an opportunity and this is still the case today. With our new technology we can now close the
circle completely for our MDF and HDF boards (the basis of the QuickStep laminate). This development is fully in line with our sustainable raw materials strategy of using 100% recovered or recycled wood and prolonging the product life of wood as much as possible.”
In the initial phase Unilin Group will use the technology for the recycling of internally used material at the production site of Bazeilles, where the group has a history of investing in cutting-edge technology for the production of MDF and HDF boards. In the next phase production capacity will be increased to also allow the recycling of externally harvested fibreboards and laminate floors. This technology, which has been patented in the meantime, is an absolute world first. The goal is to replace at least 25% of Unilin Group’s raw materials mix with recycled fibres by 2030. Over time, this will enable the Unilin Group to keep 380,000 tons of CO2 per year stored in the wood fibre that is given a second life through this new technology.
“With our new technology we can now close the circle completely for our MDF and HDF boards”
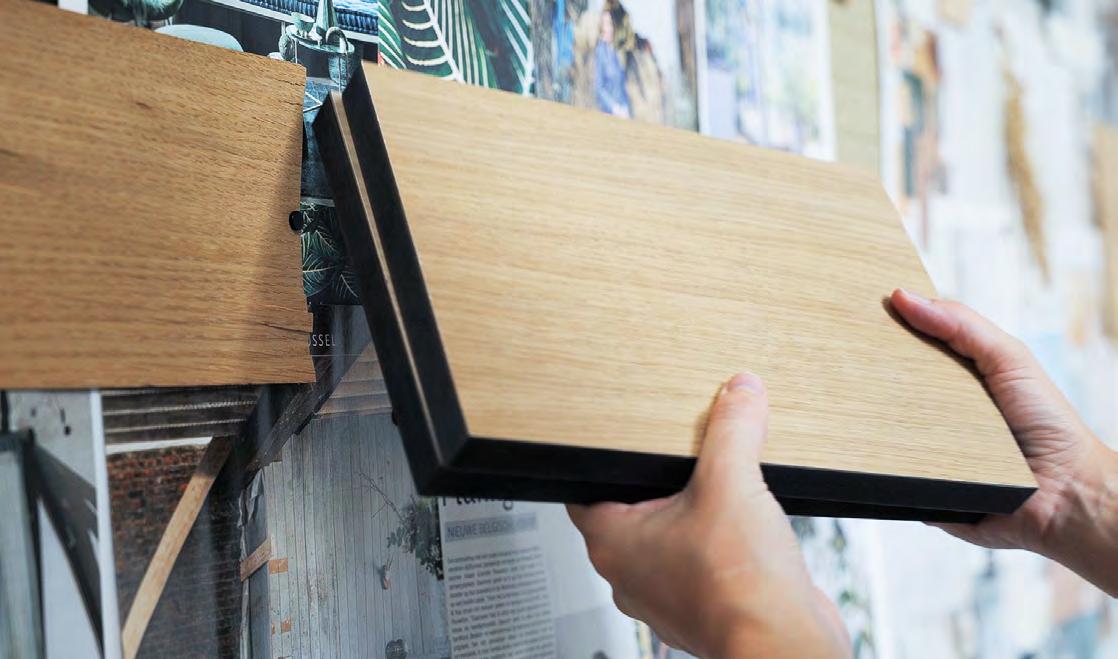
Mattress recycling now a reality with start-up of new Renuva plant
Orrion Chemicals Orgaform’s chemical recycling unit in Semoy, France where Dow’s Renuva Mattress Recycling Program will use chemical recycling to convert this recovered foam into new valuable polyurethane raw materials (polyols)
Renuva polyol, now ready for use in flexible foam applications, promises to deliver greater sustainability offerings for the bedding industry.
Dow Polyurethanes and Orrion Chemicals Orgaform, together with Eco-mobilier, H&S Anlagentechnik and The Vita Group, have inaugurated a pioneering mattress recycling plant as part of the Renuva programme.
Old mattresses made of polyurethane (PU) foam will now be recovered, dismantled and chemically recycled to create a new polyol, which is a key starting material to produce PU. This Renuva polyol is designed for various applications including mattresses.
This is a major step forward in the recovery and recycling of PU foam, and a significant advance for closing the loop for end-of-life mattresses. At full capacity the plant will process up to 200,000 mattresses per year, helping to tackle the growing mattress waste problem.
“We are immensely proud to have unveiled this plant. By doing so we are answering the question of what can be done with recycled PU foam. It is part of Dow’s strong commitment to delivering solutions that help close the loop and protect our environment,” comments Marie Buy, sustainability leader EMEAI, Dow Polyurethanes.
“As Renuva now shifts focus to the production phase and the first foam made with the new polyol, our Dow Polyurethanes sustainability journey continues. We are actively exploring future possibilities for recycled material and potential applications. It is really a new beginning.”
The Renuva mattress recycling plant is the result of strong collaboration between Dow and key players from across the mattress lifecycle.
“This really is a first for our company and for France. We have a longstanding commitment to creating more sustainable solutions, and have long recognised the need for industry to part of the solution,” comments Christian Siest, president, Orrion Chemicals Orgaform. “Our plant uses a chemical recycling process in which the PU foam is decomposed and converted into a novel single product. The great thing about this is versatility – we can process foam from any mattress, and the Renuva polyol recipe itself can be tailored for different applications.”
“Our ambition is to ensure the quality of the materials collected and delivery to Renuva so that we keep to the promise of a closed loop”, states Dominique Mignon, president of Eco-Mobilier.
As previously announced, flexible PU foam solutions provider The Vita Group will use the Renuva polyol to create its award-winning Orbis flexible foam, providing a more sustainable offering to the bedding market.
“Consumer attitudes have changed significantly, and people are becoming a lot more focused on making sustainable choices. We have already seen strong interest from customers across Europe for Orbis foam and interest in the Renuva technology, providing exciting opportunities for our product lines,” comments Mark Lewis, operations and projects director at The Vita Group.
“For over 50 years, Vita has recycled or rebonded pre-consumer foam trim into material suitable for a range of products such as underlays for flooring. Our collaboration with Dow allows us to take our sustainability vision to the next level, and we are extremely proud and excited to play our part in driving this groundbreaking innovation forward.” www.dow.com
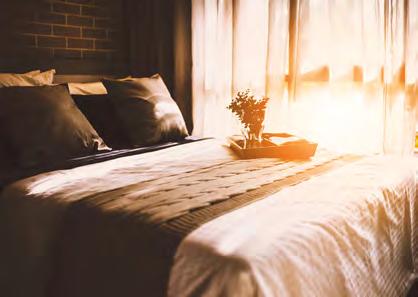
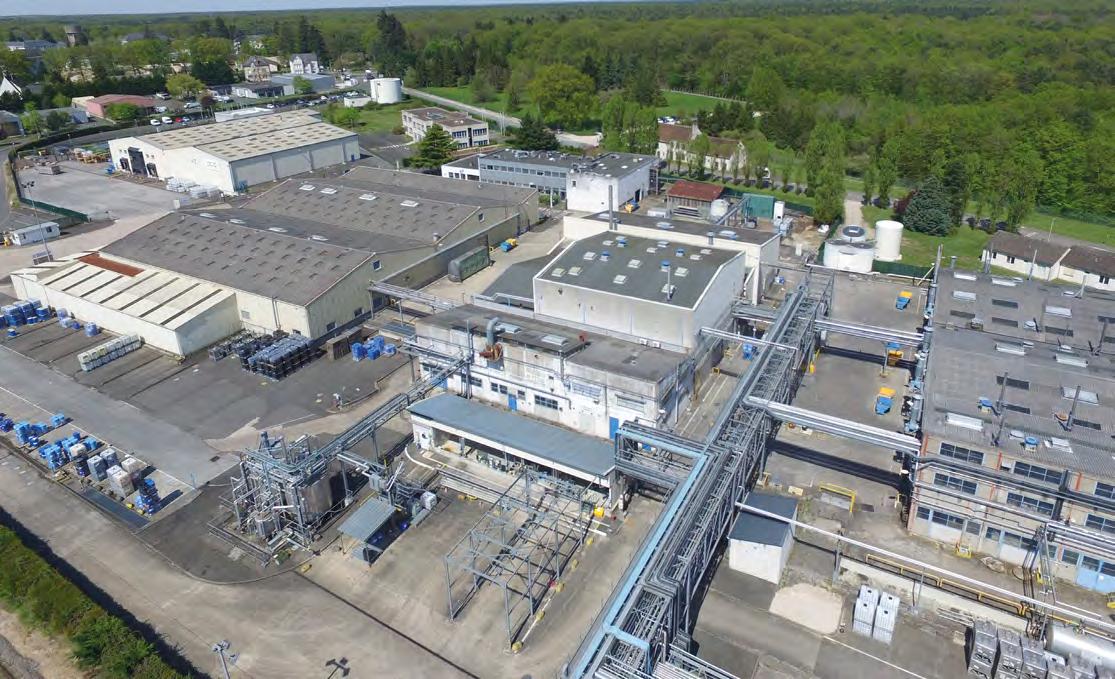
Xylexpo and bi-mu collaborate to provide stellar event
With a focus on digitisation and sustainability, the next edition of BI-MU and Xylexpo, the events organised by Ucimu-Sistemi Per Produrre, the association of Italian manufacturers of machine tools, robots and automation, and by Acimall, the association of woodworking machinery manufacturers, to be held from 12-5th October 2022 at the Fieramilano-Rho expo centre, near Milan.
The two events – 33.BI-MU and Xylexpo will cover eight halls in the West area of the show grounds. Halls 9, 11, 13 and 15 will be assigned BI-MU; halls 14, 18, 22 and 24 to Xylexpo. The organisers are positing that it is reasonable to expect that Xylexpo and 33.BI-MU will ‘return to normal’ after the necessary breaks we have all endured.
A premium event BI-MU and Xylexpo, two distinct but complementary events, are set to merge into a single entity where operators from all over the world will find technologies, equipment, services and ideas to produce in an increasingly sustainable and efficient way, according to the principles of Industry 4.0.
BI-MU and Xylexpo together will give life to the week of instrumental mechanics, attracting to all manufacturing industry operators who will be able to combine the visit to both exhibitions at Fieramilano-Rho with a single trip,
The stars of the events will be the most advanced technologies that, without neglecting all the related sectors, will show the evolution of production systems, their progressive integration, the constant involvement of different and complementary materials, including light alloys, composites, aluminium.
Four days that will attract technicians, entrepreneurs, opinion leaders and operators from all over the world to Milan, especially from those countries where the demand for Industry 4.0 solutions is higher, solutions that are automatic, flexible, effective, and at the same time, empower an effective management of energy and resources thanks to increasingly ‘friendly’ digital systems.
The organiser states that from this edition, the exhibition enters a new digital dimension that, through a dedicated platform, will further extend its geographical and time boundaries.
Registration update More than positive, the early reactions of the exhibiting companies involved, who have immediately seized the new opportunities that arise from the collaboration between the two events, which will be promoted through an even more effective communication campaign all over the world, starting in the coming weeks. Barbara Colombo Barbara Colombo, president of Ucimu-Sistemi Per Produrre commented: “In recent weeks, we have updated the 2021 forecasts for the industry. The data processed by Centro Studi & Cultura di Impresa of Ucimu-Sistemi Per Produrre tell us that we are cruising at twice the speed estimated only a few months ago. And the data for Q3 2021, just processed, indicate an increase by 52% compared to the same period of last year, thus confirming that the positive trend will continue throughout 2022. Government incentives are supporting domestic demand and will keep doing next year to the benefit of 33.BI-MU.”
Luigi De Vito “Technologies for the wood and furniture industry are experiencing an extremely positive season,” commented Luigi De Vito, president of Acimall. “If the figures relating to the first part of the year are confirmed in the coming months, it is reasonable to believe that in 2022 the world of Italian technologies for wood-furniture will record a double-digit growth in production, approaching the threshold of €3bn, two of which from export.
“Such trend will be reflected in Xylexpo that, once again, will be a great international showcase of innovation, the world reference in evennumbered years, a not-to-be-missed event not only because it takes place in a market – Italy – highly attractive both in terms of quantity and quality of demand, but because it has always been a key meeting point for industry operators from all over the world”.
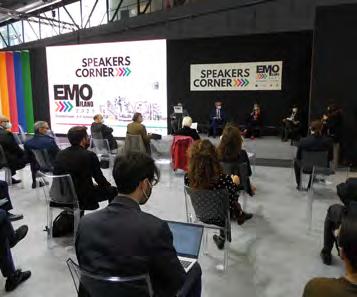
Alfredo Mariotti Alfredo Mariotti, general manager of UcimuSistemi Per Produrre, said: “The participation of industry operators in Emo Milano 2021, the world-leading industry exhibition currently hosted at Fieramilano-Rho, is further evidence of the excellent moment that the market is experiencing. This positive situation, together with the numerous innovations that will characterise 33.BI-MU, starting with ‘RobotHeart’, the new area dedicated to robotics, will certainly attract the interest of exhibitors, a hundred of whom have already confirmed their participation, booking a total area of approximately 12,000 sq m”.

Dario Corbetta Dario Corbetta, director of Acimall, added: “There are a hundred companies that have long confirmed their participation, 10,000 sq m of exhibition space assigned already in the aftermath of the cancellation of the 2020 edition, and by the end of the year we expect a massive increase in both exhibitors and exhibition area. We will achieve this result thanks to the levers on which a trade association can act, having no other objectives than the promotion of the sector it represents, including the ‘early bird’ rates for those who register by 31st December – or the decision to keep the participation costs unchanged.”
Side events Many events, seminars and collateral initiatives will be deployed by the two organisers, offering opportunities for in-depth analysis and discussion on the most current topics of industrial production.
Alongside the shared paths between 33.BI-MU and Xylexpo, there will be specific initiatives in the programs of each fair.
Xylexpo is renewing the appointment with Xia-Xylexpo Innovation Awards, that in 2022 will reward the commitment to sustainable business (and the development of digital solutions and structures. A specific award will go to the best technologies for the production of furniture with a special design content.
Xylexpo will also dedicate three exhibition days to as many topics of woodworking, through events and technological routes that will put specific segments of the production process under the spotlight. On Wednesday, 12th October, the topic will be panel processing, 13th Thursday will be dedicated to surface finishing, 14th Friday to processes from sawmill to semi-finished material production. www.xylexpo.com
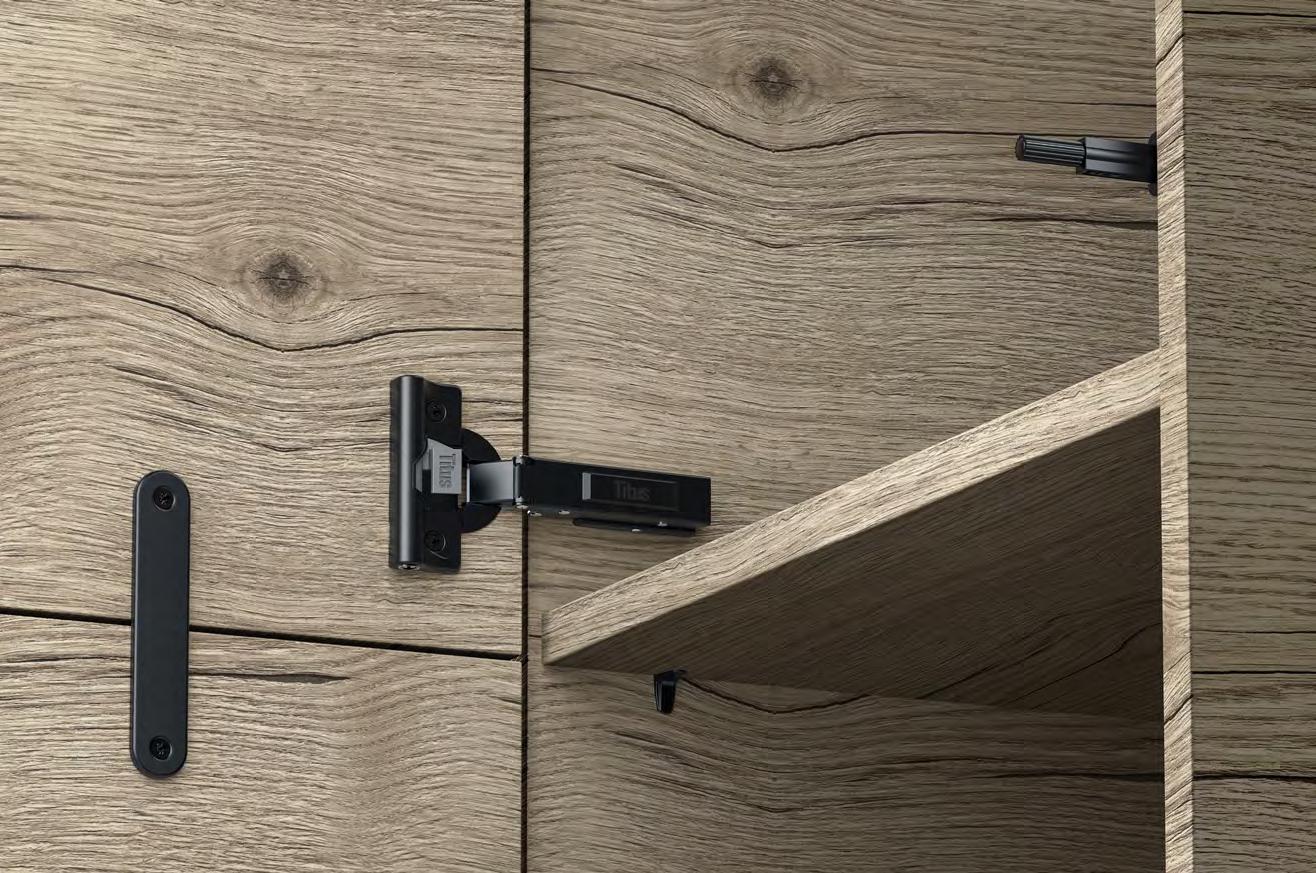
Surface Design Show unveils the best in new talent from across the world
Surface Design Show, the UK’s leading event for architects and designers to explore the best in surface material innovation, is getting ready to welcome over 120 exhibitors to its 2022 show, including over 35 confirmed New Talents.
In partnership with Canon UK and curated by Trendease International’s Jennifer Castoldi, the New Talent exhibitors will feature a wide range of start-up designers, all brought together to exhibit for the first time. Jennifer and her team travel to over 100 design events each year, seeking out the most innovative and dynamic designs. The class of ‘22 has been sourced from showrooms, trade fairs, exhibits and design shows in major design capitals, and new talents from the Netherlands, Singapore and Spain will be participating.
Surface Design Show and Canon UK are dedicated to supporting the New Talent showcased in this important and increasingly popular sector of the show. Derek Joys, product marketing manager at Canon UK, comments: “We are delighted to be partnering with the New Talent section of Surface Design Show, and to have the opportunity to work with such talented new global designers. From wallcoverings to textiles, digital printing plays a hugely important part in interior decor – we hope that through our involvement, we can pass on expert knowledge which will help these individuals to thrive in the future.”
The 2020 event featured talented new designers showing materials that included decorative panels, biomaterials, plastic waste tiles, flexible plaster and laser-cut biophilic surfaces. The 2022 show is set to be just as exciting, with participants offering a range of sophisticated and innovative designs – from textile designs featuring augmented reality to 3D tiles of eco resin and waste materials. Many of the participants this year also reflect a recurring theme of using natural materials and dyes.
“Once again Trendease International and I are delighted to bring together a diverse selection of new talent we have scouted from around the world. Over 35 fresh faces will present their creations at the next edition of Surface Design Show, ranging from 3D tiles and bioplastics, to wallpapers and textiles with circular design and wellbeing centre stage.” comments Jennifer Castoldi, CEO/chief creative director, Trendease International.
Among the New Talent designers for 2022 visitors will find surfaces using fruit waste, tiles using waste materials, a celebration of British wool, and lighting using wood veneer.
Designer Ellie Preece will bring her Kitchen Archives project to the show, an exploration of biomaterials with the goal being to create alternative packaging. Ellie’s biomaterials have been produced using various fruits, many of which can be sourced from fruit waste. The results are an edible packaging material, along with a material that can be used in place of plastics.
Emily Hatton’s work consists of a collection of 3D tiles that are made using a combination of techniques including laser cutting and hand construction, with elements of laser etch and digital print that incorporate subtle pattern into the designs. Some of the tiles have then been further developed by mouldmaking and casting with an eco-resin (Jesmonite) and waste materials. Each waste material is able to offer a unique surface texture to the resin. The 3D tiles can be applied to a range of applications including luxury wall panelling, unque wall art and adornments for furniture design.
Introduced for the first time to the New Talent section will be a lighting design by Chloe Hook. Developed using veneer, the design celebrates the beauty of nature and the importance of it in any environment. Chloe chooses to work with wood because of its primitive familiarity, warmth of colour and its sustainability credentials.
Textile designer Cara Tomi will introduce her project, The Psychology of Mandalas. The mandala is a spiritual symbol from the Buddhist faith – a sacred, circular, symmetrical pattern that can be understood in two different ways: externally as a visual representation of the universe; or internally as a guide for several practices that take place in many Asian traditions, including meditation.
The prints are made using the traditional Japanese technique of shibori (stich resist) combined with the contemporary application of structure and form through mandalas breathing new life into traditional designs.
Louisa Knapp of Knapp Textiles will showcase her textiles while championing British wool. After watching the documentary Kiss the Ground, the important role sheep can play when implemented in a regenerative farming system highlighted their ability to aid carbon sequestration into the earth’s soil, reversing the effects of climate change.
For Louisa this was unforgettably inspiring. Therefore, she aimed to investigate how wool could play a significant role in this regenerative period in the country’s economic and ecological reconfiguration.
Design enthusiasts are invited to discover this New Talent, along with enjoying some well-known, respected ones on 8-10th February 2022 at the Business Design Centre, London. www.surfacedesignshow.com

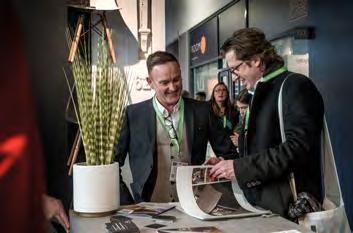