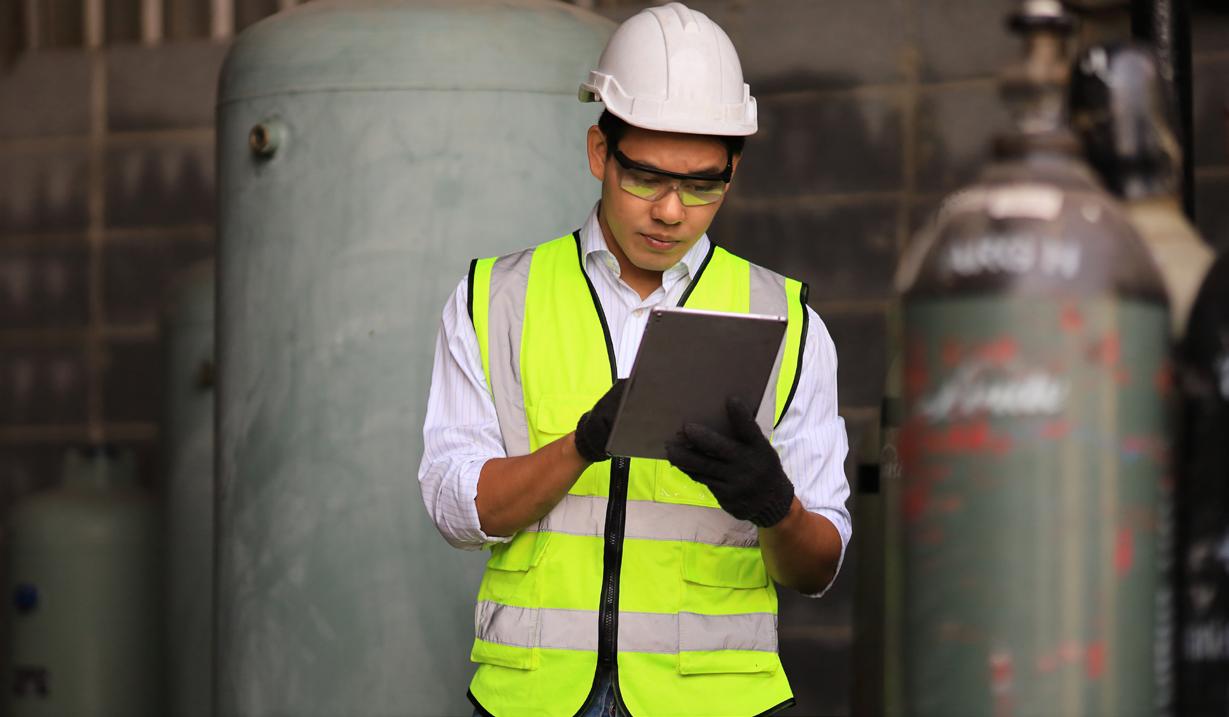
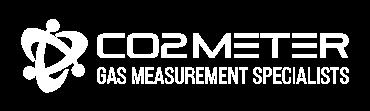
Outstanding Service and Solutions. Both in Sales and in Technical Support. We have purchased many solutions from CO2Meter and had a great experience from the sales process to the delivery. Very friendly staff, very quick responses – my last request was technical, addressed from their sales contact just before I left for work (I expected an answer by the next morning), but a solution from the technical support was in my mailbox before my bus stopped at home.
Matt Conradie Häme University of Applied SciencesSome of our partners include:
To understand how important gas detection is in an industrial application, one should know the history, background and evolution behind it. The history of gases in industrial applications parallels the broader history of gas detection technology, with a focus on challenges and requirements associated with confined spaces.
The earliest recognition of industrial gas hazards stems from the 19th century when industries like mining, manufacturing, and construction expanded. It was these industries where workers in confined spaces like tanks, silos, and underground passages recognized the poor ventilation and limited access when dealing with the accumulation of toxic or combustible gases in the field.
It was not until the mid-20th century when gas sensing technologies were adapted for use in confined space and industrial processes.
The majority of the confined space gas detectors at this time utilized electrochemical and solid-state sensors due to their reliability, sensitivity, and easy integration. As the awareness of confined spaces grew, standards began to establish guidelines and regulations for confined space entry. These regulations often included specific requirements for gas detection equipment, such as the types of gases being monitored, detection thresholds, calibration procedures, and alarm system functionality.
The biggest change in industrial gas detection did not occur until the late 20th century, when gas detectors saw improvements in sensor sensitivity, size, and digitization. Confined space gas detectors in industrial settings also started to become more compact, lightweight, user-friendly, and even started to offer wireless capabilities. These wireless and IoT features enabled real-time monitoring of industrial gas concentrations from remote locations, enhancing safety and operational efficiencies.
Beyond the technological advancements, there has been an increased emphasis on training and education regarding industrial gas safety and gas detection best practices. Workers and staff began to gain training and certification to confirm their understanding of how to use gas detection equipment, interpret alarm signals, and take proactive actions in case of a gas exposure incident or leak.
Overall, the history of industrial gas detectors continues to advance with further developments of selectivity, connectivity, and means of integration. Modern industrial gas detectors are often now part of a larger control safety system with integrations to third party shut down systems and remote monitoring capabilities.
Today, the history of industrial gas detection devices only reflects a constant drive towards advancement in the field and enhanced possibilities for ensuring safety across a broader range of industrial environments. It’s through these technological advancements and adherence to regulatory standards that workers can gain further peace of mind and minimize the potential for personal injury to occur.
As new applications and uses for gases developed, so too did the expansion of the type of gas detection equipment. One of the earliest devices used for detecting hazardous gases was the flame safety lamp, invented by Sir Humphry Davy in the early 19th century.
Miners commonly used these lamps in coal mines to detect the presence of flammable gases such as Methane (CH4). The lamp would operate by the flame changing in size or color when in the presence of hazardous gas, serving as a visual warning to workers in the field.
In the mid-19th century, chemical detectors also began to emerge in the industrial safety industry. These devices relied on chemical reactions to indicate the presence of the gas.
For example, a krebs detector, invented by German chemist August von Krebs in the 1860s, used a mixture of potassium hydroxide and alcohol to detect carbon monoxide concentrations. During this time, canaries, while not a technological device, were also used in coal mines as the birds were more sensitive to toxic gases than humans. If the canary showed signs of distress or died, it would signal the presence of hazardous gases, prompting miners to evacuate.
As time went on, the need for gas detection expanded into other industrial settings like wastewater plants, oil & gas, and refrigeration control applications. The first gas monitor in these industrial settings was a device with a valve to analytically show how much methane was present in the atmosphere. This was done with the help of a catalytic diffusion sensor, burning gas inside the sensor, and not letting the gas escape back into the original environment. While useful only for a short time, the downfall of this technology was having to manually press a button to see just how much methane was present.
It’s fascinating to look back at the different stages of early combustible and industrial gas detection. It laid the groundwork for the development of the advanced gas safety technologies that we rely on in industrial applications today.
Some modern gas detection technologies are inspired by natural phenomena. For example, the design of certain sensors mimics the olfactory receptors (sense of smell) found in animals, allowing for highly sensitive and selective detection of specific gases.
- National Center for Biotechnology
While they may seem primitive compared to today’s modern instruments, much of the early gas technology has still played a role in reducing the risk of gas-related accidents across various environments.
Today, you can find over a hundred different types of gas detection solutions and systems used in industrial applications for safety, analysis, and control.
It’s the Internet of Things (IoT) and Nanotechnology that will continue to shape the future in gas detection. These developments will only further the ability to alert appropriate personnel, shut down gas valves, trigger third party ventilation, and detect gas leaks.
Overall, it’s these developments that make gas detection systems safer, smarter, and more connected than ever before. In this next chapter we gain a better understanding of how these detectors work and understand the gases themselves and their role within industry processes.
While certain gases have more dangerous properties than others, all compressed gases are potentially hazardous.
As such, they require specific training on federal and state regulations covering the safe storage, use, and transportation - before you can even touch a cylinder or tank. Therefore, anyone handling compressed, hazardous or toxic gases should be familiar with the gas properties and potential hazards before working in their presence.
The best definition of compressed gas comes from the Compressed Gas Association (CGA) which defines compressed gas as, “a gas or mixture of gases in a container that has an absolute pressure of more than 40 pounds per square inch (psi) at 70°F (21°C). Most compressed gases will not exceed 2,000 - 2,640 psig (138182 bar), though some go up to 6,000 psig (414 bar).
Because of the associated dangers when it comes to hazardous gas in the workplace, the global harmonized systems (GHS) have created a worldwide classification criterion that determines the nature and relative hazard severity of a chemical substance or mixture.
When we discuss hazardous gases, we are speaking about gases that are sufficiently toxic or reactive to meet one of the definitions provided below. These gases include acutely toxic, corrosive, flammable, dangerously reactive, and oxidizing gases.
We highlight the GHS classification categories and the most common industrial gases found in applications and processes to enable workers to easily identify the type of gas they’re working with and it's associated hazards.
Asphyxiant Gases: asphyxiant gases are either minimally or entirely non-toxic but can dilute the oxygen in the surrounding air when released. This can lead to fatality by asphyxiation if inhaled for a long enough period. In large enough concentrations, toxic gases can also cause asphyxiation and can include interactions with the respiratory system where oxygen volume is reduced in the air.
Cryogenic Gases: cryogenic gases can be non-flammable, flammable, or oxidizing, due to their extremely cold temperature. At sub-freezing temperatures, system components can also become brittle and crack, leading to damage and dangerous conditions. Cryogenic gases also have a boiling point of -130 °F (-90 °C) at atmospheric pressure.
Corrosive Gases: Corrosive gases are those that corrode material or organic tissue on contact or in the presence of water. They are highly reactive and can also be toxic, flammable and/or act as an oxidizing agent. Most are hazardous in low concentrations over an extended period, so it’s essential that the equipment used for handling corrosive gases be constructed of proper materials, including stainless steel, aluminum, carbon steel, copper, brass, bronze, or titanium.
Flammable Gases: a flammable gas is a gas that burns in the presence of an oxidant when provided with a source of ignition. The risk of fire increases in relation to the amount of gas present. If the concentration of the flammable gas is below the lower explosion limit (LEL), there is no reaction for lack of fuel. If it is above the upper explosion limit (UEL), there is no reaction for lack of oxidant.
Inert Gases: inert gases do not react with other materials at ordinary temperature or pressure. They are also colorless, odorless, tasteless, non-toxic and non-flammable. While it might sound like an inert gas is harmless, they can become life threatening in high concentrations in a confined space and in large quantities.
Oxidizing Gases: oxidizers (or oxidants) are gases that support combustion and can displace oxygen from the air, except for O2 itself. While oxidants don’t burn on their own, it is essential to eliminate all possible sources of ignition, as oxygen and oxidants can react rapidly and violently.
Pyrophoric Gases: Pyrophoric gases are commonly used in the semiconductor industry. They are extremely dangerous to handle as they do not require a source of ignition to explode or erupt in flames.
Toxic Gases: toxic poisonous gases produce varying, potentially lethal health effects and can be high-pressure, reactive, flammable and oxidizing. To ensure safety, it’s important to adhere to OSHA’s permissible exposure levels when working with toxic gases.
You should thoroughly test and inspect the containment system and purge all lines with an inert gas prior to use.
When we look at how gas is used in industry, it’s important to know each gases unique properties to better assess the potential risks associated with their use or presence in a given environment.
Gaining education about gas properties is also fundamental to promoting safety awareness and fostering a culture of safety in the workplace. By providing training on gases and their properties, employers can empower employees to recognize risks and take appropriate precautions to protect themselves and others. Below, we highlight the most used hazardous gases found in industrial settings and review their unique properties and function in the workplace.
Ammonia is a compound with several unique properties that make it valuable across many different industries. This gas is most recognized for its pungent odor, water solubility, high vapor pressure, and reactivity across a wide range of chemical reactions. Its toxicity and potential environmental impact require safe handling and management to ensure safe and responsible use. This gas is most used in refrigeration systems, fertilizer production, poultry farms, pharma, and as a cleaning agent in commercial settings.
The welding process with the highest temperature (and is the most common) is oxyacetylene welding. Using a mixture of fuel gases and oxygen, this method reaches extreme temperatures up to nearly 6,332° F.
Carbon dioxide is a compound with several unique properties used in various industrial, environmental, and biological processes. CO2 is most known for its chemical stability, acid-base properties, heavier than air weight, and its ability to extinguish flames. CO2 is found in applications such as beverage dispensing, food processing (as a refrigerant and preservative), fire suppression systems, indoor agriculture, welding, and as feedstock in chemical synthesis.
Carbon Monoxide is most notable due to its toxicity. CO can bind to hemoglobin in red blood cells with much higher affinity than oxygen, forming carboxyhemoglobin. Despite being non-flammable, CO is also highly combustible in the presence of oxygen. When it comes to in-application, CO can act as a reducing atmosphere to prevent oxidation of metal surfaces during annealing, sintering, or brazing operations. This helps maintain the desired properties and surface finish of metal components. CO is also a silent hazard, highly toxic and can be explosive in high concentrations.
Methane is the primary component of natural gas, which is used extensively as a fuel for heating, power generation, and industrial processes. It is highly flammable in air, with a wide flammable range of concentrations (5% to 15% by volume). It is burned in furnaces, boilers, turbines, and other combustion systems to produce heat or electricity. Because it is odorless, methane producers add a chemical odor to help detect leaks. The unique properties of methane contribute to its importance as a valuable energy resource and environmental factor, while also presenting challenges related to safety, emissions, and climate change.
Modern industrial refrigerant gases used today include R-290 (Propane), R-152a (Difluoroethane), R-744 (CO2), and R-717 (Ammonia) which have replaced older hydrochlorofluorocarbons (HCFCs) and R404A (Freon) Refrigerant gases also have low boiling points which allows them to absorb heat from their surroundings and evaporate into a gas when passing through evaporator coils in a refrigeration system. Refrigerant gases are also flammable and safety should be ensured in handling, storage, and use. These gases are used commonly in power generation, marine industry, food and beverage, petrochemical oil & gas, dataprocessing, and district cooling.
Oxygen possesses several unique properties that make it essential for various biological, industrial, and environmental processes. Oxygen is a highly reactive element that supports combustion and facilitates the burning of fuels. It is also essential for industrial processes, including combustion, welding, cutting, and oxidation reactions.
Hydrogen is the most abundant element in the universe, constituting about 75% of its elemental mass. However, on Earth, it is relatively rare in its pure form because it is so light that it tends to escape the planet’s gravity and dissipate into space.
Hydrogen is the lightest element in the periodic table and is used in various industrial processes, including hydrogenation reactions, ammonia production, petrochemical refining, and as a fuel in fuel cells and hydrogen-powered vehicles. However, it is also flammable and can pose hazards in confined spaces at high concentrations. It is also the most abundant gas in the universe and is a clean-burning gas with the potential for energy production. Ongoing research and technological developments aim to harness hydrogen’s potential as a sustainable and environmentally friendly energy carrier for a carbon-neutral future.
Nitrogen is chemically inert under normal conditions, meaning it does not react with other substances. This property alone makes nitrogen suitable for use as an inert atmosphere in applications where oxygen-sensitive materials or processes need protection from oxidation or combustion. This gas is widely used for inserting, purging, and blanketing applications to prevent oxidation, moisture contamination, and combustion in processes such as chemical manufacturing, food packaging, and semiconductor fabrication.
Understanding workplace hazards is crucial for ensuring the health, safety, and well-being of employees and customers in any gas-related workplace. Here are just a few reasons why employees and supervisors should recognize workplace hazards in the field.
Identifying workplace hazards allows organizations to implement appropriate safety measures and controls to prevent accidents and injuries. This includes addressing hazards such as confined spaces, falling objects, machinery hazards, electrical hazards, gas overexposure and ergonomic risks, which can cause injuries ranging from minor cuts and bruises to severe negative health effects or fatalities.
Workplace hazards can pose risks to employee health, leading to short-term and long-term health issues, illnesses, and occupational diseases. Identifying and mitigating hazards such as exposure to hazardous gases, biological agents, and airborne contaminants can help prevent adverse health effects and protect employees from occupational hazards.
Many countries have regulations and standards in place to protect workers’ health and safety in the workplace. Identifying and addressing workplace hazards is essential for ensuring compliance with legal requirements and regulatory standards established by government agencies such as the Occupational Safety and Health Administration (OSHA) in the United States or the Health and Safety Executive (HSE) in the United Kingdom. Failure to comply with regulations can result in legal penalties, fines, lawsuits, and reputational damage for organizations.
Organizations that prioritize workplace health and safety demonstrate their commitment to employee welfare, corporate responsibility, and ethical business practices. A positive safety culture and reputation for providing a safe work environment can enhance the organization’s brand image, attract top talent, and strengthen relationships with customers, suppliers, investors, and other stakeholders.
Overall, recognizing and addressing workplace hazards is essential for safeguarding employee health and safety, ensuring regulatory compliance, minimizing financial losses, and promoting a positive organizational culture. By investing in effective workplace hazard identification, risk assessment, and control measures, facilities can create safer, healthier, and more productive workplace environments for their teams.
Additionally, by fostering a culture of continuous improvement, organizations can proactively address hazards, prevent incidents, and enhance safety performance over time.
Without proper gas detection monitoring in place, it is very difficult to detect a potential gas leak or hazard within the workplace. Even more so, it is dangerous because with some gases, personnel won’t be able to detect a leak by sight, taste, or smell.
You would never be able to tell if there are high concentrations of gas in your facility unless you start noticing the initial negative health symptoms. Gas overexposure and hazards in industrial facilities can stem from a variety of different sources.
These could include gas-powered equipment, tanks, cylinders, and process vessels. Below we highlight the specific areas where gas poses the most danger and those in which supervisors and staff should continually be aware of to mitigate hazards in the field.
Areas where hazardous chemicals are stored, such as warehouses, storage rooms, or chemical laboratories, may pose gas hazards due to the potential release of toxic, flammable, or reactive gases from stored chemicals.
Example: Pool rooms where CO2 is being used to balance the pH in the pool.
These facililtes utilize gases such as CO2, CO, and N2 in order to preserve food and other perishable goods during long-term storage inside modified atmospheric packaging (MAP)
Example: In the food production line where these gases are being used.
Confined spaces, such as tanks, vessels, silos, tunnels, sewers, and underground vaults, pose significant gas hazards due to limited ventilation, restricted access, and potential accumulation of hazardous gases, such as oxygen deficiency, flammable gases, or toxic vapors.
Example: Cleaning processes inside vessels in brewing and winemaking.
Work areas where welding, cutting, brazing, or soldering operations are performed may present gas hazards due to the production of welding fumes, gases, and vapors, including ozone, nitrogen oxides, carbon monoxide, and metal fumes, which can pose respiratory, asphyxiation, or fire hazards.
Example: Gases like CO2 and Ar in confined welding areas.
Inadequate ventilation and exhaust systems can lead to a buildup of combustion byproducts (including carbon monoxide) within a facility. This is especially concerning in areas where there is limited airflow.
Improperly installed gas lines and connections are a significant source of a gas leak. These leaks can occur anywhere along the gas supply lines, connections, piping, tubing, hoses, or storage container plumbing.
Example: Walk in draft beer coolers in a restaurant or brewpub.
Areas containing boilers, furnaces, heating systems, or combustion equipment may have gas hazards associated with the combustion process, such as the release of carbon monoxide, nitrogen oxides, sulfur dioxide, or other combustion byproducts, which can pose respiratory, asphyxiation, or fire hazards.
Example: Offgasing from boilers that contains CO2 and CO.
Laboratories, research facilities, and educational institutions may have gas hazards associated in a given environment. These hazards may appear from handling and storage of chemicals, compressed gases, cryogenic liquids, or flammable substances. These all could pose toxicity, flammability, or explosion hazards.
Example: Measuring CO2 and O2 inside incubators.
Work areas where hazardous waste is generated, handled, stored, or disposed of may have gas hazards associated with the release of volatile organic compounds (VOCs), toxic gases, or landfill gases (e.g., methane, hydrogen sulfide) from contaminated soil, groundwater, or waste materials.
Example: Measuring offgasing from sites that contain H2S, CO2, and CH4.
Construction sites, demolition sites, and excavation areas may have gas hazards associated with underground utilities, sewage systems, or decomposing organic matter, which can release flammable, toxic, or asphyxiating gases into the air.
Example: Measuring the CO2 that is used in concrete production.
Tanks, vessels, or containers used for storing or processing gases, liquids, or solids may pose gas hazards due to the potential release of hazardous gases, vapors, or fumes from leaks, spills, overflows, or pressure buildup.
These are just a few examples of common workplace locations that may be defined as gas hazards. It’s essential for employers to conduct thorough hazard assessments, implement appropriate control measures, provide employee training, and establish emergency response procedures to mitigate gas hazards and protect worker health and safety
Since the Occupational Safety and Health Administration (OSHA) was created in 1970, workplace fatalities have decreased by more than 60% and occupational injury and illness rates have declined by 67%. That’s a testament to the importance of prioritizing gas safety in the workplace.
Because of the number of hazards and injuries that have occurred due to gas-related incidents and leaks, industry codes and standards have been created. Depending upon your country, these industry codes and gas safety requirements are specific to industrial gases to ensure their safe handling, storage, transportation, and use. The primary purpose of these standards is to protect human life and health.
Gas leaks, improper installations, or mishandling of gas equipment can all lead to serious workplace hazards if not taken seriously. Further, industry guidelines and standards are in place to create a sense of following to mitigate risks and create a safer environment for all.
It’s important to recognize that non-compliance with many of these regulations can lead to legal penalties, fines, enforcement actions, and liability for damages in the event of an accident involving hazardous gases. Compliance with these standards helps build trust, credibility, and confidence amongst stakeholders, including employees, customers, suppliers, regulators, investors, and the general public.
In this section, we highlight just some examples of the most followed industry standards and regulations you should be aware of.
Gas tanks and cylinders are indispensable in the industrial gas community, serving not just as containers, but also a critical component in ensuring customer's operations are successful. When you think about the versatility and adaptability of gas in its widespread use, it serves as a vital tool across a broad spectrum of industrial, medical, welding, and scientific environments. Beyond just the use of storage, gas cylinders and tanks are engineered to ensure the safe delivery of gas at a specific pressure and flow rate, a crucial aspect in processes ranging from medical oxygen delivery to industrial welding methods.
However, working in the industrial gas sector can be hazardous due to the nature of using gas and the operations involved. Toxic gases, flammable vapors, and oxygen-deficient atmospheres are all common hazards that can lead to accidents, injuries, or even fatalities. Gas leaks, improper ventilation, and combustion processes can all contribute to the presence of these hazardous gases.
Specific gases such as oxygen, nitrogen, ammonia, hydrogen, and others, if mishandled can lead to catastrophic accidents with severe consequences. Ensuring their safe handling helps maintain product quality and consistency, as well as avoid disruption or defects in overall applications.
Overall, prioritizing gas safety is essential in industrial applications to protect human lives, the environment, and the reputation of businesses operating in the industrial gas community.
In this section, we will discuss the importance of gas safety in the workplace and the proper measures and guidelines that should be taken to protect workers and partners in the field.
Just this past year, the spotlight has been on America stating that 2023 was the deadliest year for catastrophic gas-related explosions in nearly 20 years.
These alarming statistics, as unfortunate as they are, provide much needed insight and awareness for those in the field specifically on the importance of gas detection safety. If you are unsure about the necessity of a gas detection safety system for your business, in the next few pages, we provide further analysis on the benefits of industrial gas safety systems and highlight the core advantages where gas detectors play a pivotal role in saving lives.
First and foremost, gas detection systems protect workers from exposure to toxic gases every day. When it comes to industrial processes, they typically involve the generation of chemicals that release harmful substances into the air. Inhalation of toxic gases without proper monitoring solutions can lead to immediate health effects, such as respiratory irritation, dizziness, nausea, asphyxiation, and even fatality.
By continuously monitoring the air for toxic gas concentrations, gas detection systems can alert workers and supervisors when levels exceed safe thresholds. This early warning indicator can further empower workers to evacuate the area, put on the appropriate personal protective equipment (PPE) and take the overall necessary precautions to avoid overexposure.
Additionally, gas detection safety systems can also help prevent explosions and fire hazards. For instance, flammable gases, when present in sufficient concentrations and combined with an ignition source, can lead to serious or even catastrophic accidents. Explosions and fire not only pose immediate dangers to workers but can significantly disrupt operations and cause extensive property damage which can put those in and around the location at greater risk as well. Gas detectors that can identify combustible gases allow for early detection of leaks, enabling quick interventions to prevent the buildup of explosive environments and atmospheres. By triggering alarms and shutdown mechanisms, these gas safety systems can also mitigate the risk of both ignition and consequent gas-related incidents.
When it comes to gas distribution, no one is using, storing, and handling gases more than this industry. Unless companies are manufacturing their own gases on site they rely on prompt delivery of gases that they need for their operation.
Gas distributors store a wide range of inert gases for use by manufacturers. Industry regulations mandate that gas distributors follow certain guidelines for the storage and disposal of these substances to reduce the risk of fires, explosion, gas leaks, and other incidents.
When everything is working correctly, gas flows as its needed from the supply tank to a storage dewar ready for delivery. But what happens if the supply line develops a leak, or a storage tank is not properly sealed? You’re hit with a pivotal moment where everything can go wrong. However, if a gas detection safety system is in place, appropriate action can be taken well in advance to protect employees, partners, and prevent severe accidents.
Awareness and education: Gas detection safety systems increase awareness among employees about the potential hazards in their workplace. Training programs on gas detection procedures and response protocols empower workers to understand the risks and take appropriate actions.
Trust and confidence: When employees see that their employer invests in advanced gas safety systems, they gain confidence in the company’s commitment to safety. This trust fosters a sense of security and reinforces a positive safety culture.
Compliance with regulations: Many jurisdictions have regulations and standards in place that require gas distributors to implement safety measures to protect public safety, their customers, and the environment. Using gas safety systems ensures compliance with these regulations and avoids potential legal liabilities.
Improving & protecting revenue: Many gas distributors find added value for their customers in providing gas safety systems as an added offering. In addition, these systems will identify gas hazards which can reduce potential damage, costs, and safety problems prior to them happening due to early detection.
Prompt response: Gas detection safety systems enable rapid responses to emergencies. This demonstrates to employees that their safety is a top priority, encouraging them to report concerns and actively participate in safety initiatives.
Open communication: Implementing gas detection safety systems encourages open communication about safety concerns. Employees feel more comfortable discussing potential hazards, suggesting improvements, and participating in safety-related discussions.
Before OSHA existed most American workers did not have access to the basic legal right to a safe workplace. Employers often adopted a take-it or leave-it attitude to workplace safety.
- OSHA Online Training Center
Overall, when it comes to implementing gas safety systems, they act as an indispensable means for any workplace exposed to the risk of gas-related accidents. They offer versatility, cost-effectiveness, and most importantly, lifesaving capabilities.
When gas distributors prioritize the safety and well-being of their workers and customers, they can secure a safer work environment and have the proper safeguards in place to mitigate potential injuries on the job. The most prudent and safest approach is to prevent problems entirely. This is where gas detection safety systems play a critical role.
Detection Coverage: Determine the optimal placement of gas detectors to ensure adequate coverage of the area and early detection of gas leaks. Consider factors such as airflow patterns, potential gas sources, and the layout of the facility.
Calibration and Maintenance: Establish a regular calibration and maintenance schedule for gas detection equipment to ensure accuracy and reliability. Follow manufacturer guidelines for calibration intervals and procedures. Conduct routine inspections to identify and address any issues promptly.
Alarm Systems: Implement effective alarm systems to alert personnel in the event of a gas alarm. Consider audible alarms, visual indicators (such as flashing lights or LED displays), and remote notification systems.
Integration with Control Systems: Integrate gas detection systems with other safety and control systems, such as ventilation systems, emergency shutdown systems, or building automation systems to facilitate coordinated response to gas incidents and enhance overall safety.
Training and Education: Provide thorough training to personnel on the use of gas detection equipment, recognition of alarm signals, and proper response procedures in the event of a gas leak or abnormal gas levels. Ensure that personnel understand the importance of gas safety and are familiar with emergency protocols.
Documentation and Record-Keeping: Maintain accurate records of gas detection activities, including calibration records, maintenance logs, alarm events, and response actions. Documentation is essential for compliance purposes, performance evaluation, and legal protection in the case of a gasrelated incident. GASLAB gas detection systems will record this data for you.
Regulatory Compliance: Stay informed about relevant regulations, standards, and guidelines governing gas detection and monitoring in your industry or jurisdiction. Ensure that your gas detection systems meet or exceed regulatory requirements to avoid legal liabilities and ensure a safe working environment.
By considering these key factors and implementing robust gas detection systems, organizations can effectively mitigate the risks associated with gas hazards and enhance the safety of their personnel and facilities.
It’s important to know how to select the right gas detection solution.
For anyone working in or around hazardous gases, it is vital that they be properly protected by a gas detection safety system. These devices typically can be either fixed or portable, or both, depending upon overall use case and application. Both are critical components in any gas safety system solution. In this chapter we will highlight the most common, fixed gas detection systems.
Choosing the correct type of fixed gas safety solution is simple. Here are a few questions to get the process started:
1. What is your application?
2. What gases are present or being created?
3. What is your overall use case?
4. What does your jurisdiction require?
Once you are aware of the answers to these questions above, selecting the right gas safety system will be very straightforward.
When it comes to gas detection safety systems, they must be reliable. In the event of a gas leak or overexposure, gas safety systems must be quick to alert and effectively protect personnel, facilities, and the planet from dangerous situations where combustible, suffocating, or toxic gases are emitted. With the help of modern technology, it is possible to react quickly and before a situation becomes potentially lethal.
Fixed gas safety systems are generally installed across a wide range of facilities. These devices operate by detecting hazards and providing an early indication of higher-thannormal gas concentration levels. They are typically mounted in one location and used as a permanent fixture when constant gas detection safety monitoring is required. Fixed gas safety systems are also configured using relays and specified alarm set points to meet the NFPA, NBIC, and IFC requirements or OSHA/NIOSH standards.
These settings also ensure that the safety systems respond accurately and quickly to potential atmospheric hazards. In addition, these relays provide several core functionalities that can be critical to saving lives, including but not limited to:
• Triggering an exhaust fan
• Opening ventilation
• Alerting personnel
• Triggering shut-off valves to shut off the gas supply
• Wiring to a fire control panel to instantly notify emergency services of a hazard
Additional fixed gas safety system advantages include:
• 24/7 continuous monitoring, allowing for unmanned monitoring and action
• Audible/Visual indicators and alarms
• Wireless and IoT capabilities to monitor/measure values remotely
• Integration into BMS/BA (BACnet, Modbus)
• Can be hard-wired into buildings electrical power circuit
Most incidents and injuries involving gas cylinders occur during handling or transportation. To prevent injury from occurring on the job OSHA provides additional solutions and documentation on confined spaces, fire safety, PPE, and more. Click here to learn more >>
• Internal function monitoring with integrated hardware watchdog
• Hardware and software according to SIL compliant development process
• Easy maintenance and calibration procedures
• Modular technology (plug-in and exchangeable)
• 3 relays with SPDT contacts, potential-free max. 250 V AC, 5 A
• 2 transistor outputs, 24 VDC, 0.1 A (plus switching)
• Serial RS-485 interface with protocol for DGC-06 or Modbus protocol
• 2 digital inputs
• LCD display (option)
• Warning buzzer and status LED for alarm, fault, and operation option
• Operating voltage input 100–240 VAC (option) or 24VDC
Conformity to:
o EN 50271
o EN 50270 Type I
o IEC/EN 61508-1–3
o EN 45544
o EN 14624
o EN 60335
o EMC Directives 2014/30/EU
o Low Voltage Directive 2014/35/EU
o CE, UKCA
o EN 61010-1:2010
o EN 50271, EN 50270 Type I, IEC/EN 61508-1–3,
o EN 45544-1, -3, EN 14624, EN 60335, EN 378
o Option: ANSI/UL 61010-1, CAN/CSA-C22.2 No. 61010-1
Multi-Sensor Controller Gas Capabilities and Measurement Ranges:
o Ammonia (NH3) (0-5000ppm)
o Carbon Dioxide (CO2) (0-20,000ppm)
o Carbon Monoxide (CO) (0-500ppm)
o Hydrogen (H2) (0-1,000ppm)
o Methane (CH4) (0-100%) LEL
o Oxygen (O2) (0-25%)
o and additional gas options!
To meet the EN requirements, the DGC-06 fulfills monitoring (CO) in garages, tunnels, and cart tracks according to the current EN 50545-1. Additionally, the Ammonia (NH3) refrigerant plants can be monitored according to the requirements EN 378, VBG 20 and the guidelines “safety requirements for ammonia refrigeration systems”.
Additional Features Include:
• For 128 gas sensors, 96 digital and/or 32 analog (4–20 mA) sensors
• Suitable for 86+ different toxic, combustible, and refrigerant gas types
• Easy-to-Read, Navigate LED Display Menu
• Flexible configuration due to programmable parameters and setpoints
• 4 adjustable alarm thresholds per sensor
• 5 menu languages, free adjustable
• Several alarm relays configurable per alarm
• Access to menu operation via 4 code levels
• Project protection
• Alarm release by falling/increasing gas levels, select for each threshold
• Connector for PCE06 Software at the controller module
• Fault relay with normally open contact
• Maximum 16 analog outputs, 4–20 mA, with select signal outputs
• EN 50545-1 compliant
• SIL2 Level compliant
DGC-06 Controller Gas Capabilities and Measurement Ranges:
o Ammonia (NH3) (0-5000ppm)
o Carbon Dioxide (CO2) (0-20,000ppm) or (0-10% vol)
o Carbon Monoxide (CO) (0-500ppm)
o Nitrogen Monoxide (0-100ppm)
o Nitrogen Dioxide (0-100ppm)
o Methane (CH4) (0-100% LEL)
o Formaldehyde (0-10ppm)
o Hydrogen Chloride (0-20ppm)
o Hydrogen (H2) (0-1,000ppm)
o Ethylene (0-200ppm)
o Ozone (0-10ppm)
o Chlorine (0-20ppm)
o Sulphur Dioxide (0-20ppm)
o Hydrogen Sulphide (0-1500ppm)
o Oxygen (O2) (0-25%)
o Ethylene Oxide (0-10ppm)
o and others
• (3) Configurable Safety Alarms (Audible and Visual)
• NDIR or Zirconia Sensor with extended lifespan
• Rugged powder coated aluminum or stainless steel enclosure options
• Quick-release connectors to last in harsh environments
• Push button configuration (No control panel needed)
• 4-20mA output for communication with building maintenance systems
• (3) Dry contact relays triggered by each alarm level (NO or NC)
• Back-up battery connection available
• Easy calibration function
• Barometric pressure compensation
• Temperature compensation
• Alarm latching function
• Internal heating element for improved air flow
• Strobe siren accessories available for added visual indicators
At CO2Meter, we support our partners and customers every step of the way. From helping you choose the right gas safety solution thats right for your needs, to providing you with the right gas safety resources and training for your team, we ensure that you are looked after.
For more information, please reach out to a CO2Meter specialist and we can assist you to ensure you have the right gas detection solution for your facility, application, or industry requirements.
IoT-enabled gas detection systems can not only monitor gas levels in realtime but also utilize advanced analytics to predict potential gas leaks before they occur. These systems can detect subtle changes in gas concentrations or equipment behavior that may indicate a risk of a future leak.
When it comes to selecting the proper industrial gas safety system for your application, regular maintenance is critical to ensure continued reliability. Similar to getting an oil change on a motor vehicle, gas detection safety systems over time can become less accurate due to environmental factors, exposure to gases, or general wear and tear. Further, proper maintenance helps calibrate and adjust the detectors to maintain their accuracy and longevity for years to come.
At CO2Meter, we continue to be recognized as a leader in gas detection safety solutions. We ensure the detection devices are set to valid standards and encourage that systems are continually tested and recalibrated for maintenance on an annual basis. To this end, we provide thorough instructions for on-site calibration or offer factory calibration.
During calibration, our gas sensors are recalibrated based on their natural deviation after the specified interval. During this process, the zero point is set first, and the sensor is gassed in its natural ambient air or with zero gas and calibrated to its specific value. The calibration is then performed with the gas to be measured. During the process all audible/visual and safety functions are then tested.
Overall, maintenance and proper handling of any industrial gas safety system is essential for ensuring their reliability, accuracy, compliance, and effectiveness in the field. Further, as industrial gas safety systems are often the first line of defense against leaks or hazards; regular maintenance and calibration ensures that the system is sensitive enough to detect leaks early, allowing for timely intervention and prevention of potential disasters.
Real-time data in gas detection safety systems refers to the continuous monitoring and analysis of gas concentrations in an industrial environment. When it comes to gas detection safety systems, IoT and wireless capabilities can provide benefits for viewing, analyzing, and alerting individuals immediately via PC, smartphone, or tablet.
CO2Meter offers cloud control for its industrial gas safety systems to help our customers predict potential failures or malfunctions.
Here are a few benefits to using the cloud features with a gas safety system:
Immediate Response: Real-time data allows for immediate detection of gas leaks or abnormal gas concentrations.
Early Warning: real-time data can provide early warnings of potential issues and allow employees to take preventative action.
Trend Analysis: Data can be analyzed over time to identify patterns or trends in gas concentrations levels.
Continued Improvement: Organiztions can identify areas for improvement in their safety protocols or operating procedures.
Gas detection safety systems play a critical role in ensuring the safety of staff and customers wherever soft drinks, beer, or wine are dispensed. In addition, these businesses use gas-powered appliances such as stoves, ovens, or grills that can emit carbon monoxide, which is highly toxic. This helps protect both employees and customers from the harmful effects of CO poisoning.
In addition, whether restaurant, brewing, beverage bottling, or in warehouses or production halls using CO2 extinguishing systems – wherever CO2 cylinders, lines, or tanks are required, a gas detection safety system should be utilized. The MSC2 is an ideal solution to secure access in confined spaces where CO2 leaks may occur and indicate an increased gas concentration in real-time. A combination of CO and CO2 monitoring is the safest way to operate overall equipment without dangers.
Restaurant or beverage industries may also use natural gas or propane for cooking, heating, or powering equipment such as water heaters or fryers. Gas detection safety systems are an essential element for monitoring these gases to detect leaks promptly. Natural gas and propane are highly flammable, so early detection of leaks is crucial for preventing fires or explosions.
When we look at beverage dispensing systems, refrigeration equipment is also commonly used to keep beverages cold. These systems often contain refrigerants that, if leaked, can pose health risks, or contribute to environmental damage. Gas detection safety systems can be used to monitor refrigerant levels to detect leaks early, preventing potential harm to employees and patrons and minimizing environmental impact.
Gas detection safety systems act as a critical safeguard to protect automotive technicians and other workers from the health hazards associated with carbon monoxide exposure. Further, because gasoline and diesel fuel vapors can present fire and explosion, these systems are used to monitor the concentrations of fuel vapors in the air and provide early warning of potential leaks or spills. This helps prevent accidents and ensures the safety of workers and equipment in the vicinity.
Gas detection safety systems are also integrated with exhaust systems in automotive maintenance facilities to ensure that vehicle exhaust gases are effectively captured and removed from the workspace. The continued monitoring of exhaust gas concentrations helps to ensure that extraction systems are operating properly, and that workers and staff are not exposed to harmful emissions.
In the event of a gas leak or emergency, gas detection safety systems in automotive applications alert workers to the presence of gas and trigger audible/visual alarms to notify personnel to evacuate the area and implement proper emergency response procedures like shutting down equipment or activating ventilation systems.
Most car parks above a certain size require a gas detection safety system (regulations vary from region to region) to meet the specifics and compliance with EN 50545-1. This regulation notes that a system must trigger an alarm and reliably protect people and equipment in confined space areas. These gas detection safety systems can be precisely adapted as well to the respective regulation due to flexible setting options and the ability to switch thresholds depending on the state and requirement
Overall, these fixed gas detection safety systems are reliable in meeting the safetyrelated requirements in EN50545-1 if the permissible CO limit value of 30ppm is exceeded. Should a potential hazard occur, the gas detection system regulates the air quality and decides when the ventilation must be started. In the event of a risk of poisoning or fire caused by leaking LPG gas, the rescue control center can also be informed at the same time.
Refrigeration systems provide many potential hazards when it comes to high concentrations of refrigerant gases such ammonia, hydrochlorofluorocarbons (HCFCs), and hydrofluorocarbons (HFCs). These systems, also above a certain size must be equipped with a gas detection safety system depending upon the type of refrigerant and the specific application environment – the requirements of EN 378 and EN 14624 apply.
When it comes to gas detection these systems often include the ability to continuously monitor the refrigerant levels in each system. If a leak is detected, the system can trigger alarms or alert others to notify operators of the potential danger. In these specific environments, the MSC2 stand-alone-controller can be used or for larger facilities that depend on multiple sensing capabilities, the DGC-06 can be utilized.
Gas safety systems are a great add for refrigeration applications as well due to the safety regulations and standards that must be adhered to, and these monitors ensure that the refrigeration systems operate within those legal and safety guidelines.
Often in refrigeration systems it is also necessary to distinguish between a natural vs. a synthetic refrigerant. Synthetic refrigerants can affect health and must be monitored for leaks in the circuits. With any natural refrigerant, such as propane, carbon dioxide, or ammonia there is always a danger of explosion in the case of a leak and the danger of gas poisoning. In these specific environments, the MSC2 stand-alone-controller can be used. For larger facilities that depend on multiple sensing capabilities, the DGC-06 can be utilized.
A common application that requires gas detection safety systems is refrigeration and cold storage. These environments typically require a means of monitoring to ensure the safe storage of perishable products while minimizing risks to personnel and property. Detecting potential leaks early can prevent the buildup of potentially harmful concentrations of refrigerants in the air.
In addition to the modern technology of cold storage environments, ripening chambers are a common area where various gas concentrations are involved in the overall process. Fresh fruits and produce are alive and continue to breathe after harvested, however, what this does is lead to oxygen consumption and generation of CO2 and water vapor. To keep the produce fresh, you must slow down this process while maintaining the overall quality of the product. To speed up or slow down the ripening process, different gases like CO2 and oxygen concentrations are used which are monitored with the help of a gas detection safety system.
When a refrigerant leak is detected, gas safety systems activate alarm systems to alert personnel to the presence of a hazard. If detected, audible alarms, visual indicators, and remote notifications can all be triggered to ensure that appropriate action can be taken. Gas safety systems in cold storage facilities can often include emergency shutdown mechanisms that can halt the operation of refrigeration equipment in case of a critical fault or hazard. This helps to prevent further escalation of the situation and protects both personnel and stored goods.
When it comes to pharmaceutical, laboratory, or medical applications various gases are used. The most common are nitrogen, oxygen, and carbon dioxide.
Nitrogen is used for blanketing, purging, pressurizing, and mixing. It also is used to protect reagents and products from reacting with oxygen in the air since it is nonreactive. It can also be utilized as a packing gas and in sterile form-fill-seal vials to preserve pharmaceuticals from deteriorating.
In biopharmaceutical applications, oxygen can be employed to manufacture pharma chemicals in fermenters using cell cultures. Since the ambient oxygen concentrations are often insufficient for bioreactors, pure oxygen is used to enrich the internal environment, enhancing growth rates and cell productivity.
One final gas that can be found throughout pharma industries is carbon dioxide. Much like nitrogen, it is an inert gas. As a result, it is useful for blanketing and packing. It can also play a vital role in pharmaceutical production.
Gas detection safety systems also can help pharmaceutical and medical facilities comply with stringent regulatory standards, such as those set by the U.S. Food and Drug Administration (FDA) and Occupational Safety and Health Administration (OSHA).
Gas safety systems are crucial components of biogas plants, ensuring the safe production, storage, and utilization of biogas generated from organic waste materials. In his application, personal protection and plant safety are critical in addition to process optimization. By implementing gas detection safety systems they can protect personnel from combustible and toxic gases, as well as oxygen.
When it comes to monitoring gases in biogas applications, methane is a common gas used and represents a high hazard potential for operators. An explosive mixture exists when the concentration of methane in the air is between 5% and 15% by volume. By monitoring in pump rooms with gas detection you can protect personnel, minimize losses from leaks, and avoid potential explosive hazards.
Gas safety systems can also provide multi-sensing capabilities that monitor the concentration of additional gases outside of methane, such as carbon dioxide, hydrogen sulfide, and oxygen. Continuous monitoring can also help monitor changes in gas composition, and potential hazards in various areas of the biogas plant.
By incorporating alarm systems that trigger audible and visual alerts, these detectors will trigger when gas levels exceed safe thresholds or when abnormal conditions are detected. Alarms can then notify plant operators and personnel of potential hazards, prompting them to take appropriate action, such as evacuating the area or implementing emergency procedures.
Gas detection safety systems are integral to ensuring the safety of personnel and facilities in petrochemical plants, where the handling, processing, and storage of various flammable, toxic, and volatile gases pose significant risks. In the chemical and petrochemical industry, permanent monitoring of rooms and plants in which explosive or toxic atmospheres can form is required. Personal protection requires the monitoring of hazardous gases in accessible areas, on the one hand to prevent accidents, and on the other to comply with MAC values and guarantee the safety of employees.
Gas detection safety systems also serve to protect systems from financial losses. These systems can help further optimize the process of safety in the field. These safety systems are used to continuously monitor the ambient air for the presence of hazardous gases, including flammable gases (such as methane, propane, and hydrogen), toxic gases (such as hydrogen sulfide and carbon monoxide), and oxygen concentrations. Only precise monitoring can ensure early detection of gas leaks, spills, or releases that could pose safety hazards to personnel and equipment.
These gas detection safety systems are also equipped with alarm systems that activate audible and visual alarms when gas concentrations exceed predetermined threshold levels. Alarms alert personnel to potential dangers, prompting them to evacuate the area, initiate emergency response procedures, or take corrective actions to mitigate risks. These systems are strategically installed throughout petrochemical facilities to provide comprehensive coverage of critical areas, including production units, storage tanks, pipelines, loading docks, and confined spaces.
The use of hydrogen as an energy carrier of the future is ever evolving. In addition to its wide use in welding or as fuel for rockets, the focus is currently on the automotive sector. Hydrogen is also a very reactive gas, which means constant monitoring by a gas detection safety system is critical.
Despite Hydrogen’s potential to become a widespread clean-energy source, there are very real safety issues to contend with. Hydrogen’s unique chemical properties also make it an exciting fuel alternative. However, because Hydrogen has a propensity to leak, it’s undetectable by humans, is fast detonating, and more explosive than natural gas.
This makes gas detection safety systems – essential.
Gas detection safety systems are truly critical to ensure the safe handling, storage, and utilization of hydrogen gas in various industrial applications. These systems are installed in areas where hydrogen is stored, handled, or used to continuously monitor for potential leaks.
These systems also utilize hydrogen-specific sensors or detectors capable of accurately detecting low levels of hydrogen gas in the ambient air. Early detection of leaks also allows for prompt intervention to mitigate safety risks and prevent the accumulation of explosive concentrations of hydrogen.
Personnel in waste management applications are exposed to hazards from both toxic and flammable gases. When gas leaks occur, rapid alerting and reliable monitoring is essential in this field. Gases are used both to treat waste and are a byproduct of the waste treatment process.
For example, landfills use gas collection systems to capture methane for energy production. Methane is a natural byproduct of decomposing waste. The collected gas is typically routed to a flare station and combusted. Waste management workers are continually exposed to hazardous gas generated during waste processing, treatment, and disposal activities.
Gas detection safety systems at landfills are used to monitor the composition and concentration of landfill gases, such as methane (CH4) and carbon dioxide (CO2), which are produced as organic waste decomposes. Continuous monitoring helps identify potential gas migration, assess landfill gas extraction system performance, and ensure compliance with regulatory requirements for landfill gas emissions.
In anaerobic digestion facilities and biogas plants, gas detection systems are used to monitor biogas production processes, where organic waste is converted into biogas through microbial fermentation. Gas sensors monitor methane (CH4), carbon dioxide (CO2), hydrogen sulfide (H2S) and other gases. This helps to optimize process efficiency, ensure gas quality, and prevent safety hazards associated with toxic or flammable gases.
Aquaculture refers to the farming of aquatic organisms under controlled conditions. It involves the cultivation of fish, crustaceans, aquatic plants, algae, and other aquatic organisms in freshwater or marine environments. Aquaculture encompasses a wide range of activities from raising fish in ponds or tanks to cultivating seaweed in oceanic farms.
The main advantage of fish farming in an aquaculture system (RAS or a specially designed tank) is that the production is independent of location and has minimal impact on the environment and water consumption, as it is a closed system. Moreover, they can be built near consumer markets where there is not enough water or suitable climate conditions for selected fish species. Water treatment and sterilization both play an essential role in aquaculture. This places high demand on the facilities as well as new health and safety criteria for the personnel working there.
Because farmed fish are sensitive to pathogens and toxic substances, disinfection of facilities is provided by ozone oxidation or ozonation. Ozone is a severe health hazard and therefore dangerous to any employees working in ozone production premises. Gas safety systems offer perfect protection in case of ozone gas leaks or overexposure. Gas safety systems also often include oxygen sensors to monitor oxygen levels in aquaculture tanks or ponds.
Maintaining proper oxygen levels is critical for the health and survival of aquatic organisms. If oxygen levels drop below acceptable thresholds, the system can trigger alarms or activate aeration equipment to increase oxygenation.
If you are looking for more insights, here’s a glimpse of a few customer case studies from industry leaders in the space on their experience with our industrial gas detection safety systems and just how they integrate these systems within their facilities.
Our goal is to provide these real-world examples of gas safety and give the raw details to just how these systems have helped others in the field in safeguarding personnel, reducing gas-related risks, or ensuring compliance with safety code regulations.
We hope you enjoy, learn, and take something away from each customer case study.
Using energy once, profiting twice - that is the principle of combined heat and power (CHP). Whereas electricity and usable heat were usually generated separately so far, cogeneration combines these processes - with the result that less fuel is required overall. This energy company’s application offers enormous potential for climate protection and conservation of resources. The increased use contributes to reducing CO2 emissions and lowering the demand for primary energy.
An energy company, which has been engaged in the generation, distribution, and supply of electricity for more than a century and, for the last decades, in the distribution and supply of thermal energy and natural gas. The entire thermal power plant consists of various production units. Their highly efficient combined heat and power unit, which is powered by natural gas, generates electricity of 235MW and a thermal output of 50MWt.
Natural gas is an ideal fuel for CHP plants and at the same time a naturally occurring gas consisting largely of methane. In the gas-processing industry, gas detection systems can reduce fire and explosion risks immensely, as they provide very early warning of dangerous situations. The permanent monitoring and storage of the measured values serves the primary explosion protection and thus the safety of human life and equipment. The PolyXeta®2 PX2 gas detector for the ATEX zone was used for detecting methane leakage. The microprocessor-based gas sensor with output signal as well as alarm and fault relays (all SIL2 certified) monitor the ambient air for combustible gases and vapors using an infrared sensor element or a catalytic sensor element (pellistor). Analog signal values (4–20 mA), such as measured values and alarm activation, are sent to the DCS (Distributed Control System). The digital signal of the detector is sent to the ventilat cabinet to activate additional fans and to shut down the air chambers. The 4–20 mA / RS-485 Modbus output signal makes the gas sensor suitable for connection to the PolyGard®2 gas controller series from MSR-Elect as well as to other controllers or automation devices.
As an option, the PolyXeta®2 sensor is also available with LCD and relay output. In the event of an alarm or error, this company stands by the PX-2 and its backlight changes from green to red to provide instant visual indication should a potential hazard ever occur.
In addition, the DGC-06 was used to measure, warn, and control the overall device system for toxic, combustible gases and vapors as well as refrigerants. It is designed according to EN 50545 and can monitor and evaluate up to 128 gas sensors. Each sensor has 4 freely adjustable alarm thresholds. Freely adjustable parameters and setpoints enable flexible use in gas measurement technology. Various interfaces and protocols are also available for connection to a higher-level management system.
Overall, with the help of a robust gas detection safety system, the vehicle halls continue to have safeguards in place to protect emergency responders and other personnel from the potentially deadly effects of carbon monoxide exposure. These systems also have built-in diagnostics to detect any faults or malfunctions and quickly act to reduce the concentration of CO to mitigate risks from personnel. By continuously monitoring for the presence of carbon monoxide and providing early warnings of potential hazards, these systems help to prevent accidents, minimize exposure risks, and ensure a safe working environment.
A centrally located, practice-oriented, and innovative research university holds one of the most prestigious laboratory areas that needed proper gas detection safety systems for CO2, CH4, and O2 monitoring. For the protection of people working and learning for example in the areas of natural science, such as biomedicine, chemistry, forensics, marine, physics or even biotechnology, a gas warning system was installed to ensure the monitoring of combustible and toxic gases as well as of oxygen deficiency.
Because of the variety of gases used across the beverage industry, individual gas safety systems are put in place to detect toxic or combustible gas concentrations. In this case study, the MSC2 is used for monitoring of up to 3 gases and warning of toxic vapors within a wide range of gas measurement.
The gas safety system served integral to this beverage dispensing system application, particularly because pressurized gases were being used both CO2 and N2 for carbonation and dispensing. The gas safety system needed to ensure safe storage and handling of the gas and mitigate where the gas leaks were most likely to occur. If elevated gas levels were to be present or a gas leak happened, alarms would be triggered to alert personnel to the potential dangers.
These gas safety systems also incorporated features that aided the beverage dispensing company to detect and prevent gas leaks in the beverage dispensing equipment. This included leak detection that could automatically shut off gas flow in the event of a leak.
Further, the MSC2 played a critical role in ensuring the safe operation of beverage dispensing equipment by detecting and preventing gas leaks, monitoring gas pressure levels, and facilitating prompt emergency response in case of incidents. These systems helped to protect both employees and customers while maintaining the integrity and efficiency of beverage dispensing operations.
A gas safety checklist is commonly used to assess worker’s safety throughout a variety of industrial processes and applications. Using a checklist in the workplace further helps ensure compliance with regulatory standards including wearing specified personal protective equipment (PPE), installing proper gas detection monitoring devices, and passing routine workplace inspections.
The list provided will help you with the necessary steps and checklist items on protecting your facility, manufacturing plant or business when it comes to gas safety requirements in the field.
Are all employees gas safety trained/certified?
Are all instructions clear and understood by operators?
Are all employees familiar with standard gas equipment?
Are all employees aware of the hazardous substances used in the field?
Are all employees familiar with how to operate gas detection equipment?
Are all employees aware of all safety and emergency protocols?
Are all employees aware of the main workplace hazard points and what to do if an incident occurs?
Are all cylinders, tanks, couplings, and hoses, kept secure?
Have all gas pipelines and tanks been installed according to code?
Does your team have the education and guided resources to act should a potential gas leak or hazard occur with gas detection safety equipment?
Are all employees familiar with the equipment’s functions and features?
Is the proper safety signage in place in the proper locations for reference?
Are all employees familiar with troubleshooting and manual documentation?
Are all employees educated on the SOPs should an incident occur?
Does your team know how to calibrate the equipment or follow manufacturer instructions for calibration?
Are all employees familiar with how to operate the gas detection equipment?
Are all employees aware of environmental hazards or confined spaces?
Are all employees storing gas detection equipment properly?
Does your team have the right knowledge for on-going best practices during typical operation?
Are tanks/cylinders legibly marked to identify the gases contained?
Do all employees wear the proper PPE continually?
Are gas cylinders/tanks stored in a manner to prevent hazard?
If compressed gas is used for cleaning, is the pressure < 10 psi?
If welding gases are stored, are they separated by a 5’ barrier or 20’?
Are oxygen cylinders handled with clean hands or gloves?
If LP gas is stored, is it with accordance with safe practices?
Are fuel-gas cylinders placed with valve end up?
Are cylinders not attached when lifting a machine?
Does your team have the right knowledge for post-operation, maintenance, and clean-up?
Are all combustible materials swept away?
Is all equipment turned off and properly stored?
Are gas cylinder valves fully closed and put away?
Are all incidents reported to a supervisor?
Are waste items disposed properly in designated and appropriate waste containers?
At CO2Meter, we continue to use our expertise in the market to continually deliver educational resources and training to our customers. When it comes to individuals in industrial applications there are in fact several types of training available, including:
Personal Protective Equipment (PPE) Training
Hazardous Materials (Hazmat) Training
Fire Safety Training
Electrical Safety Training
Gas Detection Safety Training
Technique and Process Training
Download our Gas Safety Posters!
*While these six training principles are a base line in best practices for any facility, your own requirements may vary depending on the type of process being performed and the specific work environment. Staff should always follow standard safety procedures and guidelines provided by their employer and consult with their supervisor or safety officer if they have any questions or concerns.
As we have mentioned, for anyone working near hazardous gas it can be very dangerous and it is important to follow specific safety requirements to minimize the risk of accidents or injuries. Some of the safety requirements that are necessary when working near hazardous gas include:
Hazard Assessments: Conducting a hazard assessment of the work area to identify potential hazards and assess the risks associated with working with hazardous gases.
Ventilation: Ensure that the work area is properly ventilated to prevent the buildup of hazardous gases. This can be achieved using ventilation systems, exhaust fans, and natural ventilation.
Personal Protective Equipment (PPE): Use appropriate PPE, including respiratory protection, eye protection, and protective clothing. The type of PPE required will depend on the specific hazardous gas being used.
Training: Ensure that workers are properly trained in the safe handling of hazardous gases and the use of PPE.
Emergency Response Plan: Develop an emergency response plan in case of a potential gas leak or other emergency. This plan should include evacuation procedures, communication protocols, and emergency contacts.
Warning Signs: Post warning signs in the work area to alert workers and visitors to the presence of hazardous gases.
Monitoring: Monitor the work area for hazardous gas levels using gas detection equipment. Regular testing should be conducted to ensure that gas levels remain within safe limits.
Since 2006, CO2Meter has provided customers with best-in-class gas detection solutions across multiple industries worldwide. Often identified as one of the leading sources in gas detection, our proven gas sensor technologies are continually recognized for their high-quality sensing capabilities. Not to be misconstrued by the name “CO2Meter”, our technologies encompass a wide range of gases from oxygen, carbon monoxide, ammonia, methane, nitrogen, argon, and many others that are used across applications globally.
Our reputation is in part due to our ability to continue to evolve, learn, and grow to better serve our customers, partners, and distributors. Customer and partner input has been both influential in adapting new technologies and continuing to lay a solid foundation in which we can develop long lasting business relationships and cement CO2Meter as a true leader.
Gas distribution, industrial, and welding applications have always been a strong focus when it comes to providing technologies and assisting those in the field. Whether it is providing solutions for Fortune 500 companies, global equipment manufacturers, gas suppliers or distributors – our gas detection devices continue to solve the urgent needs of our customers daily.
At CO2Meter, our mission is to provide best-in-class gas detection, monitoring, and analytic solutions, while ensuring the safety, education and long-term business of our partners and customers worldwide.
With many gas detection and safety solutions for CO2, O2, CO, NH3, CH4, and others; our ever-evolving brand ensures that we are the “go-to” source for gas detection technologies.
Through innovation, research, and strong development, our team will continue to provide solutions and enter new markets to meet the needs and requirements of our partners in the future.
To learn more about CO2Meter and our gas detection solutions, contact us or stay up to date and subscribe to our monthly newsletter.
These are the most frequently asked questions we’ve received from customers as they pertain to compressed gas, industrial safety requirements, and ensuring compliance in the industry.
What additional steps should industries be proactively taking to ensure safety for our staff?
Besides installing gas safety monitors, supervisors need to be continuously educating both new and existing workers on the hazards of gases, and ensure employees know what to do when gas safety monitors go off to mitigate the risk of overexposure, hypoxia, and fatality.
What are the potential side effects that may result from overexposure to gas?
Depending on the gas and concentration level, health effects and symptoms may range from headaches, fatigue, dizziness, asphyxiation, and even fatality.
The team at CO2Meter often asks our customers when we first sit down to discuss options for the following questions to better understand your use case which will then determine the best safety or analysis solution.
What is your application?
What volume of gas are you using and how frequently?
What gas(es) do you need to measure?
What does your typical day look like when using, producing, or storing gas?
Keep the gas detection safety system free of obstructions and contamination, and inspect it regularly. Report any damage immediately and ensure you are keeping up with annual calibration services.
The two most common exposure limits are established by OSHA in the form of permissible exposure limits or PEL and by the ACGIH in the form of Threshold Limit Values or TLV. For those working in the United States, your employer must keep exposures below the PEL.
The use of a gas detection/monitoring system, with appropriate action taken if dangerous levels of gases are detected, can help to prevent an explosion or can help to prevent worker injury or exposure to toxic gases.
Gas detectors can be used to detect combustible, flammable and toxic gases, and oxygen depletion. The most common gases that gas detection safety systems monitor are NH3, CH4, CO, H2S, and O2.
This depends on your intended application of where a gas analyzer is needed. Do you need a fixed system with the control panel on the outside of the room so that the sensors inside the room give you an accurate reading before you enter the room to ensure that the levels of gas are safe to enter? Do you need wireless capabilities to view concentrations across multiple facilities so that you can monitor the location in real-time? A CO2Meter expert would be happy to walk you through the right gas detection system for your application and needs.
What steps can you take to identify hazardous substances?
There are steps you can take to identify hazardous substances in your facility.
You should always read the labels on your equipment to review the warnings, safety precautions, and ventilation requirements.
You should obtain and review the material safety data sheets
You should review the safety signage (if applicable)
The ventilation or exhaust needed for your application depends upon factors such as: What factors need to be considered when determining the exhaust requirements?
• Workplace volume
• Workspace configuration
• Number of personnel
• Types of processes/materials used
• Allowable levels (TLV, PEL, etc.)
• Materials
• Natural airflow
Where can you find safety instructions regarding products that you use?
At CO2Meter, we are lucky to partner with some of the most reputable sensor manufacturers in the world. Most consumable products have a warning label that contains specific safety instructions regarding the product you have chosen. In addition, all CO2Meter gas detection safety devices come with an operational manual that highlights the proper safety and troubleshooting sections.
What factors need to be considered when using gas detection safety devices?
According to OSHA regulations, natural ventilation must be adhered to, and gas detection safety devices should be sufficient in meeting requirements provided that:
• The room or area contains at least 10,000 cubic feet for each employee
• The ceiling height is not less than 16 feet.
• Cross ventilation is not blocked by partitions or equipment.
• Industrial process is not done in a limiting confined space.
• The staff’s exposure must be controlled to below the PEL/TLV
What precautions must employers take if they have a confined space in the workplace?
Employers must have a written confined space entry program that includes specialized training for employees that enter confined spaces, and/or who serve as attendants to those entering and for those who supervise confined space entries.
Additionally, employers should use and properly train workers on standard operating procedures for gas detection safety monitoring equipment and devices to protect employees from potential gas exposure.
What is calibration and why does it matter?
For anyone using gas detection devices and to accurately detect gas levels you must calibrate the device. While most gas detection devices come pre-calibrated from the manufacturer – routine calibration is recommended annually in some cases and every six months in others, dependent upon the application and agressive environment. This calibration is critical to ensure accurate readings and maintain the device’s longevity.
When it comes to gas distribution, protecting the safety and well-being of employees is paramount. While gas is an essential ingredient in day-today operations, without proper safeguards potential gas leaks can cause severe harm to employees, customers, and overall facilities.
At CO2Meter, we continue to stay up to date on evolving trends in the industry and partner with key organizations and associations that set the standard when working with gases in the industry.
Gas distributors have a responsibility to ensure safety of their customers who handle or use the gases they distribute. Further, it’s important to understand the severity of overexposure to gases and be educated on how to protect your team and your customers in the field. Using gas is of course pertinent, yet the need to monitor the gas is even more critical when it comes to protecting people, property, and maintaining customer confidence.
Without any means of accurately monitoring hazardous, combustible, and toxic gases - there is no other indication for safety on the job.
Gas-related incidents can disrupt operations, lead to downtime, loss of revenue, and damage to an overall business’s reputation. Gas detection safety systems help ensure business continuity by minimizing the likelihood and severity of such incidents. We hope that with the proper knowledge and guidance from this eBook you will be able to better protect yourself and take the right precautions to protect your customers out in the field.
We hope that you found this eBook to be both informational and beneficial in taking the next steps for your business, understanding the importance of the gases themselves, their use cases across each application, and recognize the potential hazards that could arise without gas detection safety systems in place.
As we continue to ensure that we provide up-to-date educational resources and quality gas detection safety monitors, we would love if you could share your overall feedback on this “Benefits of Industrial Gas Safety Systems for Distributors” eBook to better assist our customers, partners, and suppliers needs now and in the future.
If you have any additional questions or concerns that were not answered here, please reach out to a CO2Meter expert. We would be more than happy to provide you with the right information you need to ensure gas safety in the workplace.
You can email us directly at Sales@CO2Meter.com, or call us at 877-678-4259