AUGUST / SEPTEMBER 2022SAWMILLING • LOGGING • BIOMASS USNR now offers wood yards, log handling, and merchandising systems SAWLINESSkiddersShredders&GrindersForestryMachines
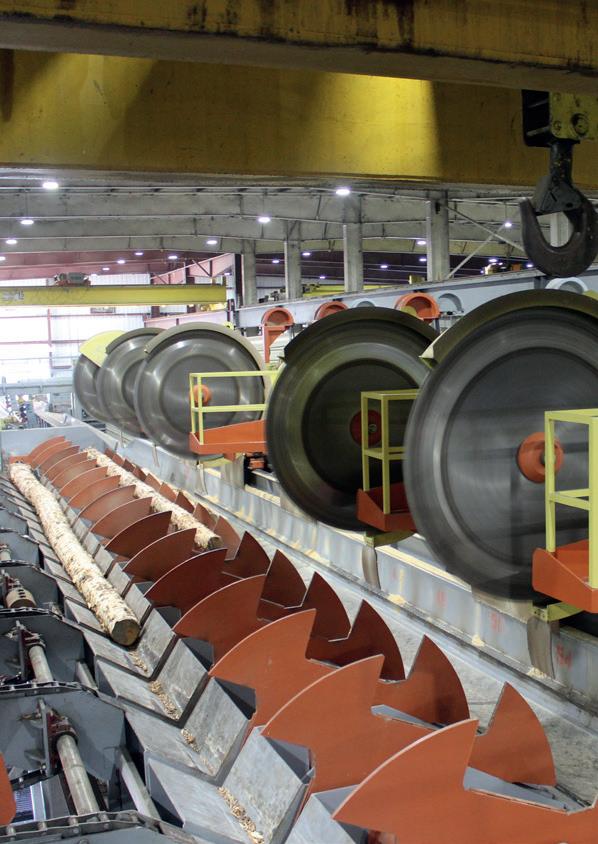
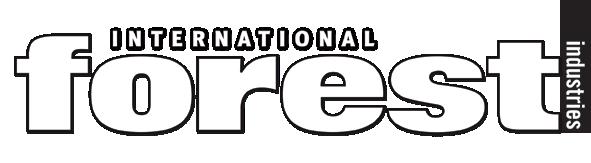
Astec offers the right tools for any job. With a full line of Peterson horizontal grinders, in both diesel and electric configurations, you can tackle any application efficiently and effectively. Our industryleading equipment offers improved fracturing, accurate product sizing and increased throughput. to see our full horizontal grinder line
Scan
BUILT TO CONNECT
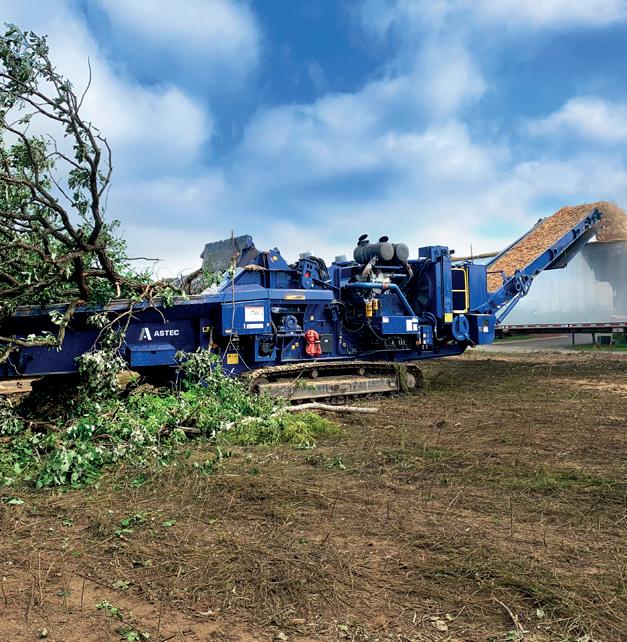
International Forest Industries | AUGUST / SEPTEMBER 2022 1 47 GRAPPLE CARRIAGES Making full use of a motorised grapple carriage 30 SKIDDERS John Deere’s powerful 768L-II Bogie Skidder 44 FORESTRY MACHINES Purpose-built for forestry applications; these machines raise the bar and maximize productivity when it comes to tackling the most difficult jobs 44 34 SHREDDERS & GRINDERS LOGGING • BIOMASS CONTENTS AUGUST / SEPTEMBER 2022 REGULAR FEATURES 6 Logging News 48 Advertising Index LUMBER PROCESSING CONTENTS COVER - USNR USNR is proud to supply nearly all the equipment at West Fraser in Lufkin, Texas although the merchandiser system was provided by LogPro. USNR recently acquired Timber Automation and its LogPro product line, creating the industry’s most comprehensive supplier of equipment and technology. The addition of log yard equipment represents a major market expansion for USNR, and the Baxley products, including optimization, edgers, and lumber processing equipment, as well as VAB’s lumber grading equipment, fully complement USNR’s product offering, providing more options for high-quality machinery. The combination solidifies USNR’s leadership position in providing equipment and technology to the global wood processing industry. AUGUST / SEPTEMBER 2022 SAWMILLING • LOGGING • BIOMASS USNR now offers woodyards, log handling, andmerchandising systems &ShreddersSAWLINESSkiddersGrindersForestryMachines 47 30 www.usnr.com

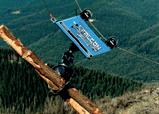
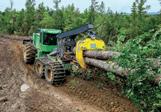
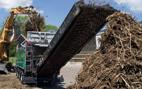
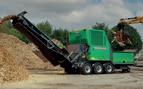
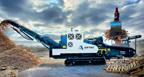
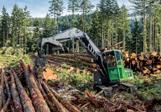
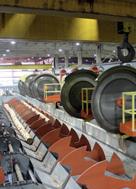
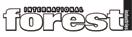
2 International Forest Industries | AUGUST / SEPTEMBER 2022 LUMBER PROCESSING 24 LATVIJAS FINIERIS Automatic Patching Line – for intelligent and sustainable manufacturing 25 MICROTEC Logeye 900 Stereo: a revolution in carriage scanning 2425 28 MERCER TIMBER Mercer Timber Products utilizes laser scanning and 3D facility design 22 BID GROUP Quickly Detect Sawing Anomalies with BID’s New Trimmer SmartTool using Artificial Intelligence 29 USNR The addition of Timber Automation’s LogPro line of log yard equipment represents a major market expansion for USNR 28 22 SAWLINES 29 26 LIMAB BoardProfiler 3D - for Edgers & Trimmers 26 #teamfranzen2022 www.franzen-machines.com We have the Solution.
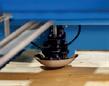
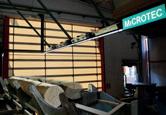

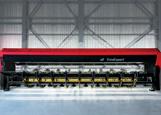
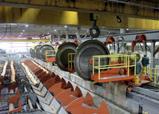
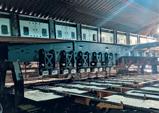
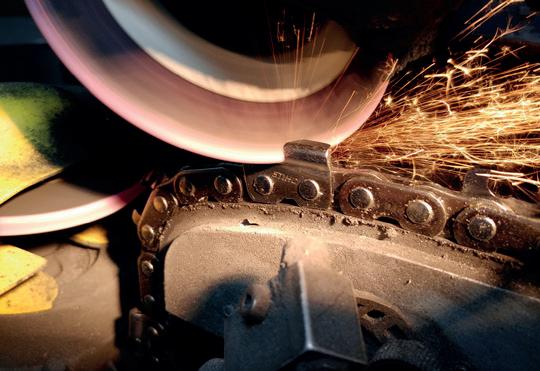
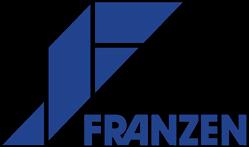
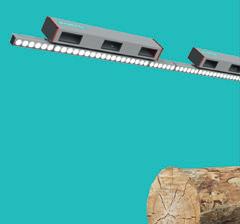
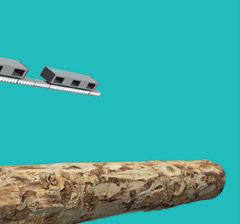


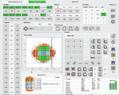
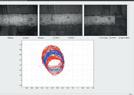
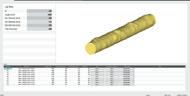
4 International Forest Industries | AUGUST / SEPTEMBER 2022 SUBSCRIPTIONS Tel: +44 (0)1442 877 583 UKAnnualemma@internationalforestindustries.comSubscriptionandEurope£160, €230 Rest of the world US$270 EDITORIAL T: +44 (0)1442 877 583 F: +44 (0)1442 870 B2www.internationalforestindustries.com617ClaridgeCourt,LowerKingsRoaderkhamsted,Herts.HP42AF,UK Editor Chris chris@internationalforestindustries.comCann Editorial Board Dr Patrick Moore – Chairman and Chief Professor Piotr Paschalis-Jakubowicz –Warsaw Agricultural University (Poland) Mr Kim ForestDirectorCarstensenGeneralStewardship Council Eduardo Morales South American Forestry Consultant ADVERTISING AND PROMOTIONS International Forest Industries Ltd Advertising Manager Phil +phil@internationalforestindustries.comPlayle44(0)1442877777 Associate Editor Robin robin@internationalforestindustries.comPeach Advertising Production Enquiries Emma publishedInternationalBerkhamsted,2byInternationalemma@internationalforestindustries.comSmithForestIndustriesispublishedInternationalForestIndustriesLtd,ClaridgeCourt,LowerKingsRoadHerts.HP42AF,UKForestIndustries(ISSN1755-6732)is bi-monthly by International Forest Industries Ltd GBR and is distributed in the USA by Asendia USA, 17B South Middlesex Avenue, Monroe NJ 08831 and additional mailing offices. Periodicals postage paid at New Brunswick NJ. POSTMASTER: send address changes to International Forest Industries, 17B South Middlesex Avenue, Monroe NJ 08831 © International Forest Industries Ltd 2007 – 2019 IFI uses, as preference, SI units throughout. All dollars are US unless otherwise stated. ISSUE 88 August / September 2022 EDITOR’S COMMENT
The timber price, meanwhile, continues to contradict this macro trend and slide south. The World Bank’s Timber Price Index was at 88.3 in March; had dropped to 83.5 when we last published; and had dipped below 80 at time of Thoughwriting.thejury is still out on whether we are heading for a global recession, I find it hard to see another outcome. Federal bankers are walking a tightrope in balancing interest rate rises that are their only weapon in the war on inflation, with the need to maintain at least a creeping level of growth –growth that will be undermined by the same rate rises. It will take a coordinated effort from policy makers around the globe, with a mistake from just one major economy having the potential to trigger recession for itself and its trading partners.
The recessionary window some 13 years ago forced a dramatic change in structure for contractors and industry suppliers. We saw those in the timber stands look for greater efficiencies and versatility in operations to add multiple revenue streams, adding diversification and some protection against demand fluctuation in specific markets. It was much the same in the sawmills.
Suppliers (and some sawyers) merged –either through distress or strategically – to achieve scale and bring down costs, while shifting R&D efforts toward those new demand areas from contractors.
Leading into that period, wood industries had enjoyed unbridled growth for several decades – arguably the ‘Gilded Age’ in the late 19th Century was the last time the world saw a period of such sustained prosperity.
ChrisEnjoy Cann of the beginning
The last time I used these column inches, I painfully opined the current squeeze on contractors, as the price of timber shrank away and the cost of, well, everything – including equipment and inputs such as fuel – rose at a pace not seen in a Thegeneration.searchfor better news for this column has come up well short. My natural disposition is to look for the positives in situations and so the search for a positive spin was extensive. In that context, the dearth of useable developments that could be seen in a summer glow, is even more disappointing. But facts are facts. If we take the US as our proxy, inflation has been charging north since late last year, surging from 5.4% at the end of the September quarter to 9.1% in the most recently published figures available at the time of writing (June) – that’s up from 8.6% in May, representing the highest levels since November 1981.
The relatively brief period of partly constrained growth since 2008-2009 leading into present day has hardly allowed wood industries to relax their discipline, and so the sector we have today is lean and mean – it is in great shape to endure a global Still,recession.wepredict any manufacturer offering clear cost saving and efficiency gains will be well received in markets over the next 18 months, as margins and survival take priority of revenues and growth.
End
While it may be hard to find outright positives in this situation, there is perhaps a silver lining to be seen on an otherwise dark cloud. And it is born of the pain from that 2008-2009 recession.
Wood industries would, like most others, contract during a global recession. Inflation would necessarily flatten off for at least some daily industry consumables in such an environment, but it will remain the most difficult period since the global financial crisis in 2008-2009.



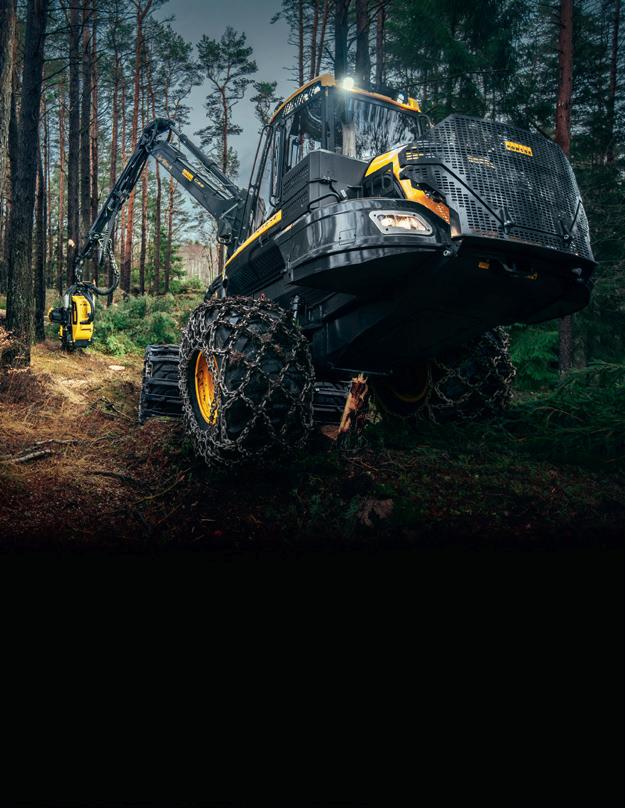
• Recently making its debut on the 900 MH-Series Tracked Harvester machines and now available on the 803MH, 853MH, and 858MH models, Intelligent Boom Control (IBC) technology is a boom tip guidance technology that improves consistent boom motion and speed throughout the harvesting envelope.
• This technology also offers increased machine and attachment life by actively dampening all functions, protecting boom structure during operation.
John Deere introduces the latest updates to its Knuckleboom Loader lineup, including visibility enhancements. Aiming to increase operator safety and accuracy, the 2022 models of 437E and 337E Knuckleboom Loaders feature a newly designed front window by removing the external mesh
• Tree damage is greatly reduced, What is Intelligent Boom Control?
John Deere has updated its Knuckleboom Loader lineup with enhancements that improve visibility, precision and overall operator experience
John Deere introduces Intelligent Boom Control on 800 MH-Series Tracked Harvesters
Following the introduction of Intelligent Boom Control technology on to the John Deere 900 MH-Series Tracked Harvesters earlier this year, John Deere has introduced Intelligent Boom Control on to its 800 MH-Series Tracked Harvesters. Now available on the 803MH, 853MH, and 858MH models, Intelligent Boom Control (IBC) technology is a boom tip guidance technology that improves consistent boom motion and speed throughout the harvesting envelope. of each independent boom cylinder function.
• The faster cycle times and more precise control require less finesse and hand-eye coordination for the operator.
• The automation logic commands boom and jib cylinders.specialsimultaneouslyfunctionsbymonitoringsensorsintheboom
• IBC also provides precise positioning of cut stems for use in TimberMatic Maps.
Intelligent Boom Control Benefits
Availability • 800 MH-Series Tracked Harvesters with Intelligent Boom Control technology are available for order now. For more information about Intelligent Boom Control, please visit dealer.harvesters/www.deere.com/en/tracked-orcontactyourlocal
& enhances Knuckleboom Loader visibility with cab upgrades
• Operators can control the boom tip and attachment position directly with one joystick instead especially during thinning applications.
Jarvis de Groot, product marketing manager, Forestry Swing Machines and Knuckleboom Loaders guard and replacing it with a clear, polycarbonate window for uninterrupted view. “We are always looking for ways to increase operator comfort on the job while keeping a focus on machine safety and design,” said Jarvis de Groot, product marketing manager, Forestry Swing Machines and Knuckleboom Loaders at John Deere. “By removing the external window guard and redesigning the front window on the 437E and 337E Knuckleboom Loader models, we are significantly improving visibility for the operator, making for a safer and more comfortable work environment.”The2022model-year upgrades also feature a new hood profile in the left-rear corner of the machine, which opens up the view behind the machine. The new design partners with the window updates to make for a safer, easier-tooperate machine. By offering enhanced visibility, these models enable the operator to be more precise, maximizing uptime. In addition to visibility enhancements, the latest models will offer optional satellite-ready radio, improving the operator experience in the cab. A new optional hydraulic vacuum pump can also be added to 2022 modelyear machines, minimizing oil loss and spillage during times of hydraulic maintenance and repair.
• This technology also helps the operator maintain constant boom speed during parallel motion at any boom reach.
6 International Forest Industries | AUGUST / SEPTEMBER 2022
• IBC technology promotes a reduced learning curve for new operators by providing intuitive operator assistance.
• IBC technology automatically adjusts swing speed and boom tip trajectory depending on working height, terrain, and work cycle requirements.
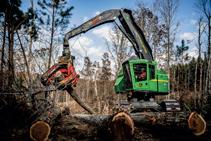
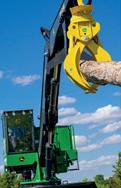


WORK, EVEN WHEN IT RAINS. With incredible stability in soft or sloped terrain, the new John Deere 768L-II Bogie Skidder efficiently retrieves timber in hard-to-reach places. The bogie axles on this six-wheel skidder combine excellent traction and flotation with reduced ground pressure helping you move big loads long distances no matter the conditions. Add one to your fleet and get ready to OUTRUN. JohnDeere.com/OneInTheWoods OUTRUN™
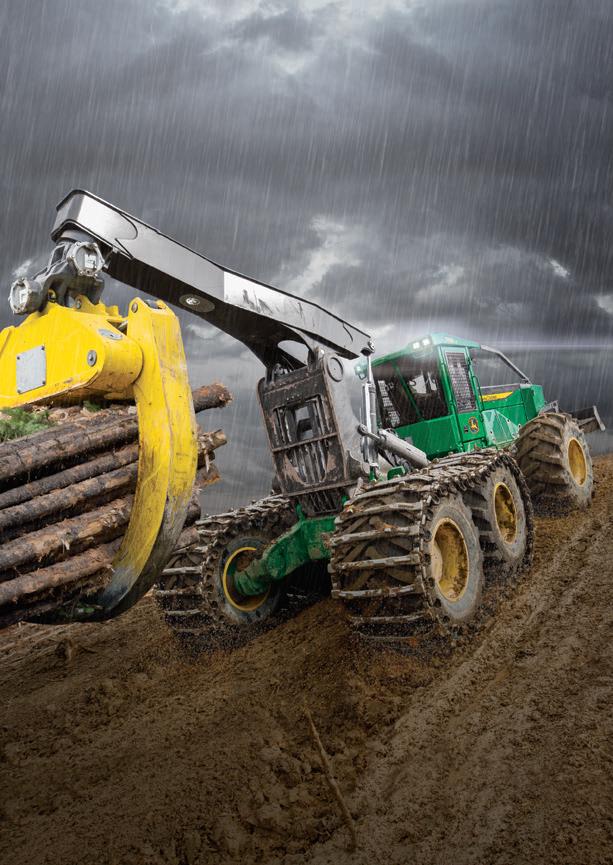
Crambo_MS_IFI_190x80v04.indd 1 02.08.2022 10:10:00
The D61EM-23M0 performs automatic traveling, stopping, and planting on the preset courses upholds sustainable forestry, which not only engages in harvesting and forwarding, but also includes silviculture and forest management. Komatsu also works to mechanize dangerous work, facilitate wide use of forest machines that contribute to safety, and promote smart forestry that analyzes drone and satellitebased data for the management of forests, including the number and height of trees. Tree planting is expected to expand worldwide for lumber production and environmental concerns, such as the promotion of carbon neutrality. At the same time, the need for mechanization is growing, especially because tree planting is labor-intensive work, with an increase in planting in remote areas, and a decrease in the workforce. With extensive knowhow of silviculture over the years, Bracke develops, manufactures, and sells processes.attachmentsapplication-specificforuseinsilviculture
Since 2014, Bracke and Komatsu have engaged in joint development by sharing respective technologies and experience accumulated over the years, respectively in forest and construction machines. In FY2021, Komatsu launched the D61EM-23M0, the world’s first bulldozer-based automatic crawler planter, in Brazil. Even after the acquisition, Komatsu will continue to incorporate Bracke’s technologies and expertise in the field of planting in order to accelerate its pace of mechanization of all processes other than harvesting and forwarding, which have already been mechanized. Komatsu will work to generate synergy for smart forestry and provide higher valueadded products in order to enhance the safety and productivity of customers’ jobsite operations and make carbon-neutral contributions.
komptech.com
CRAMBO E-MOBILE
Komatsu has acquired Swedish attachments manufacturer Bracke Forest to expand its sustainable forestry business. As defined by the US Forest Service, silviculture is the art and science of controlling the establishment, growth, composition, health, and quality of forests and woodlands to meet the diverse needs and values of landowners and society such as wildlife habitat, timber, water resources, restoration and recreation on a sustainable basis.
Processing of woody biomass into renewable fuel. - no exhaust emissions, - high efficiency, - full flexibility.
Komatsu’s forestry business
8 International Forest Industries | AUGUST / SEPTEMBER 2022 LOGGING & BIOMASS NEWS
Komatsu buys Bracke
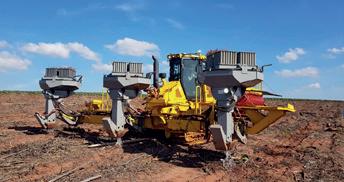

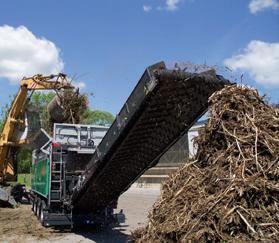
New Komatsu Comfort Ride
See more at komatsuforest.com/newcomfortride
The next generation of comfort Great news for all forwarder operators – the new generation of Komatsu Comfort Ride has been improved with comfort-enhancing features like adjustable sideways firmness and automatic side levelling at standstill and at low speed. The elevated unloading mode now also works at low speed, which gives you a good overview at the log piles. As you see, you’re truly in for a comfortable ride.
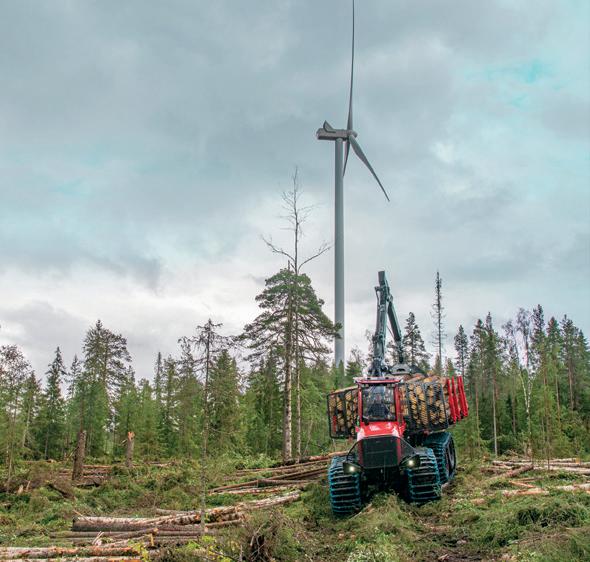
10 International Forest Industries | AUGUST / SEPTEMBER 2022
pewag completes the acquisition of forestry specialist Wallingford’s and BABAC
Combination of pewag group and Wallingford’s/BABAC results in a leading position in forestry traction and supplies as well as snow chain traction devices in North America Graz, Austria / Pueblo, Colorado / Oakland, Maine / New Hampton, New Hampshire – pewag group, a global leading company in traction chain devices and industrial chain solutions (founded 1479), recently announced that is has completed the acquisition of Wallingford’s Inc. and BABAC Inc, a leading U.S.based provider of forestry traction devices, forestry supplies and snowWallingford’schains. and BABAC have been consolidated as part of pewag’s Traction and Forestry segment as of December 17th, 2021.The acquisition of Wallingford’s and BABAC is a strong fit with pewag’s North American forestry business and in particular its forestry traction devices business. It is part of the strategy of pewag to be a leader in this segment globally. Moreover, the highquality forestry traction devices, developed and manufactured by pewag in Austria and Czech Republic will be integrated in the portfolio of Wallingford’s. pewag has hundreds of years of experience in the manufacturing of chains and their components. Since the first documented reference of its forging plant in Brueckl, Austria 1479, pewag group became one of the leading chain manufacturers worldwide. Today its success is based on well-engineered state-of-theart quality products. pewag’s business areas are mainly snow chains, forestry traction, hoist and conveyor chains, do-it-yourself products, engineering, lifting and lashing chains and accessories and tire protection chains. Modern impressive chain production facilities in Europe and in Pueblo, Colorado allow for this variety of high-quality products.
“The combination of pewag’s strong portfolio in forestry with traction devices and the wide distribution network of Wallingford’s in the forestry industry will result in a leadership position in this sector in NorthAmerica. Moreover, the skidder and ring skidder traction devices developed and manufactured by BABAC will complete pewag’s global forestry product range.”
Rob Bekkers CEO pewag Traction and Forestry Founded in 1975, Wallingford’s Inc. is an international wholesaler of tire chain, logging and industrial supplies and the largest of its kind. Products are predominantly sold to distributors in North America. The range includes in particular traction systems (tracks/skidder chains/ tire chains), cutting systems, logging supplies and industrial supplies.Thesales and marketing office is located in Oakland/Maine, with a distribution, assembly and administrative facility in New Hampton, New Hampshire, and Canadian distribution centers in Edmonton, Alberta and in Montreal, Quebec. In the position as President of Wallingford’s Inc., Chip Wallingford will be in charge for the future development and is taking over this position from John J. Wallingford. (Thank you, John, for your efforts and commitment over the past years!) “We are very excited to be Rob Bekkers, CEO, pewag Traction and Forestry now part of the global pewag group, which will add value and quality to our product portfolio, improve our position in the NorthAmerican forestry market and will definitely give a further push to our professional customer service. We have always valued the high-quality European products and we are very pleased to have pewag products in our portfolio. Furthermore, the global leadership of pewag’s snow chain traction devices will be strengthened with Wallingford’s offerings.”
Chip PresidentWallingfordofWallingford’s Inc Currently both group of companies will investigate and implement a strategy to optimize its presence on the North American markets with the aim to offer a better, broader product portfolio and further improved services to their clients.
Timbeter opened its first LATAM office in Pernambuco, Brazil. Company has been working with some of the largest companies in Latin-America since 2017 such as CMPC (Chile), Suzano (Brazil), Klingele (Brazil), Faber-Castell (Brazil) and many others. Last year, during the Climate COP26 in Glasgow , the Governor of the State of Pernambuco, Paulo Câmara, Anna-Greta Tsahkna, CEO of Timbeter and José Bertotti, Secretary of Environment of the State of Pernambuco, signed an agreement to start a cooperation project focusing on strengthening legal and sustainable practices for the forest industry in Brazil. The main goal of the cooperation project between Timbeter and the Government of the State of Pernambuco was to use Timbeter’s innovative technology for measuring timber as an efficient supervising tool for the environmental inspection teams. “For us it was a logical step to expand our activities in the Latin-American market and be near to our customers. We see a lot of potential for growth as Continued on p48
Timbeter opens office in Brazil


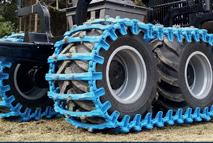

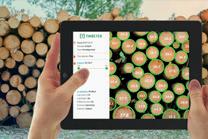

Horizontal Grinders • Whole Tree Drum & Disc Chippers • Flails • Forestry Mulchers • Mulching Attachments MORBARK WOOD HOG HORIZONTAL GRINDERS MORBARK DRUM CHIPPERS MORBARK CHIPARVESTOR®DENIS CIMAF YouATTACHMENTMULCHINGbegineachday before dawn with a drive and determination to do more than the day before. When you move at this pace, you know to do more you need equipment that is made for more. That’s why our forestry, biomass, and recycling equipment is built from the ground up to meet your needs, delivering: More Power and Production Consistent, Quality End Product Lower Operating Costs Ease of Maintenance Greater Longevity and Resale Value Find your local Morbark, Denis Cimaf, and Rayco Dealer at www.morbark.com/b/international-dealer-network

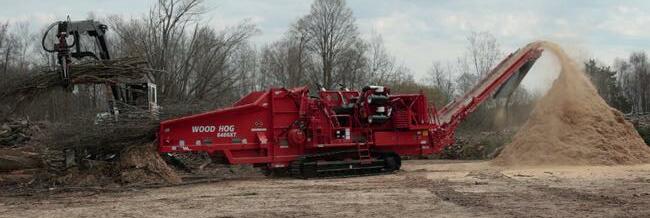
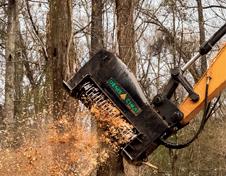

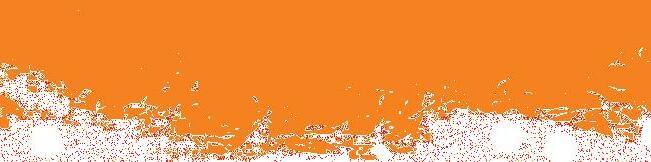

Reclaim and recover wood fiber effectively
12 International Forest Industries | AUGUST / SEPTEMBER 2022
Arkadiusz Banach, Global Product Manager, Forestry Cranes, Hiab Davide Director,Pernice,Global Product Management, Forestry, Hiab Henri Janhonen, Vice President, Sales & Product Management, Demountables, Forestry and Recycling Cranes, Hiab The new cranes have been tested in demanding conditions ranging from cold, snowy winters and heavy rainfall in Finland and Sweden to hot summers and varying weather conditions in Germany. Overwhelmingly, the new cranes have had a reliable performance in even the toughest environments.“Thereisnothing more expensive, and potentially a safety risk, than equipment failure, but our customers can count on LOGLIFT to deliver efficient reliable equipment and services. We are also proud to introduce a higher level of safety standards in our new forestry cranes,” says Arkadiusz Banach, Global Product Manager, Forestry Cranes, Hiab. The next generation of forestry cranes has optional in-built connectivity so they can access Hiab’s HiConnect™ to further enhance performance, safety and avoid unnecessary downtime with real-time insights into equipment utilisation, operation, and condition.Operators will benefit from more feedback about the forestry cranes’ conditions, customisable output and safety features such as overload protection indication and stabiliser activation. It is made possible by the operating system SPACE X4 customised for forestry cranes. It is based on Hiab’s SPACE system used for loader cranes so the next generation LOGLIFT cranes will be easy to configure using the same tools that are currently being used.ProCare™ service agreements are also available to LOGLIFT to secure original performance with regular preventative maintenance checks and scheduled inspections. “LOGLIFT is ready to lead the way into the future with state-of-the-art, next generation forestry cranes. The sum of all the advancement is a crane that delivers more profitable and safer operations with full access to Hiab’s HiConnect service for further gains,” says Henri Janhonen, Vice President, Sales & Product Management, Demountables, Forestry and Recycling Cranes, Hiab.
Hiab launches next generation Loglift forestry cranes
Hiab, part of Cargotec, launches the next generation of LOGLIFT forestry cranes with greater and safer performance, and improved uptime. The first crane available to order is the Z boom crane LOGLIFT 18Z with a max outreach of 10.4 metres and a max lifting capacity of 18 tonne metre (tm). “Our next generation of LOGLIFT forestry cranes are created for the new generation of operators. Easy to operate and service, and designed for comfortable and safe operation, the next generation forestry cranes are also the first with digital solutions that can further increase productivity and uptime,” says Davide Pernice, Director, Global Product Management, Forestry, Hiab. The new geometry of the boom creates a powerful crane with an increased outreach. To reduce the chance of unexpected downtime, hoses are placed inside the boom system of the 18 tm crane with fully protected oil distribution and cables. Larger hydraulic pipes improve flow to avoid fatigue during warm severalanaccess.ergonomicsimprovedOperatorstemperatures.benefitfromanhighseatwithbetterandsturdierladderOnceseatedtheyhaveimprovedfieldofvisionandnewsafetyfeatureslike an illuminated emergency stop button and better illumination. A new modular design for speedier installation of the new cranes, which can be installed with accessories.
West Salem presents the market with versatility in the field of size reductionMilland maintenance managers demand severe-duty machines with low maintenance requirements and minimal downtime. West Salem (WSM) wood and bark hogs, screens, shredders, hammermills, no-knife re-sizers, and panel shredders are rugged and reliable with maintenance friendly features and mill-grade construction.Thisgearprovides dependable, long-term operation in the most demanding applications. Maintenance friendly features and mill-grade construction means this gear provides dependable, long-term operation. WSM grinders, shredders, and screens can help convert bark and mill residuals to mulch, sawdust and shavings into animal bedding or pellet feedstock, chips overs and hogged wood into marketable fiber, and scrap/reject panels or trim into re-useable product. “Count on WSM’s hogs, grinders, shredders, hammermills, re-sizers, screens, and panel shredders to help reclaim and recover wood fiber,” the company states.“High volume production with minimal horsepower requirements, makes for energy efficient, low cost, 24/7 operation.”



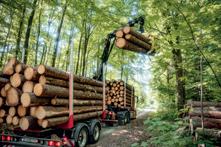


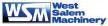
From waste to money. Use JENZ Shredders. www.jenz.de
NEW FAE RCU-75: the compact and powerful remote controlled tracked carrier FAE is expanding the RCU series with the new RCU-75 model, a compact, professional and powerful, remote controlled tracked carrier. The RCU-75 is designed to work on hard-to-access areas and steeply sloping terrain that requires dedicated equipment to ensure operator safety and operating efficiency. It’s excellent for working in hilly wooded areas, near railroad tracks, power lines, gas and oil pipelines, gardens, roadsides, highways, canals, rivers andThelakes.new FAE tracked carrier is powered by the Kohler Common Rail electronic fuel injection engine — a compact, powerful and fuel-efficient 74-hp propulsion system that complies with the most stringent emission standards. The heavy-duty undercarriage features a hydraulic extendable & retractable independent track a large 3.5” display for superior management of all vehicle and attachment functions and with customizable function keys. A 2.4 GHz transmission frequency ensures reliable communication. The layout of the controls, the wellbalanced shoulder straps support, make the FAE RCU remote control ergonomic and easy to use. The RCU-75 can be paired with the BL2/RCU mulcher, designed to mulch vegetation up to 6” in diameter. This mulcher features a fixed tooth rotor and Bite Limiter technology that provides higher productivity with even less horsepower due to low power absorption.TheRCU range will be available in 2023. gauge system and an automatic tensioning system. Thanks to high profile rubber tracks – 86 mm pitch and 13 in width - oscillating rollers and triple-flange style idlers, it can operate in the strongest conditions. High-tech solutions give the RCU unbeatable traction, enabling it to work on steep slopes up to 55°. Moreover, the steel track undercarriage version provides great traction even on the most difficult terrains. A dual hydrostatic transmission provides better traction and optimal management of the attachment. Electronically controlled piston pumps combined with a dedicated electronic control unit provide an integrated technological system. The result is high performance and reliability that lasts, plus a simple and intuitive operation. The RCU-75 is guided by an ergonomic remote control with
LOGGING & BIOMASS NEWS
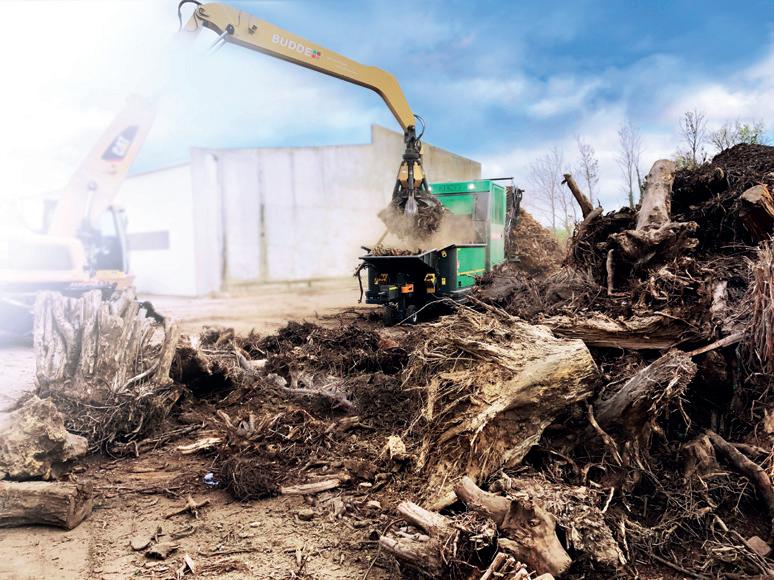


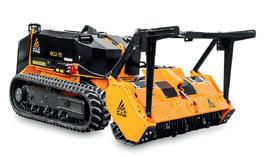
Klabin introduces to its forest harvesting a pioneering forestry machine developed in partnership with Ponsse
A forestry machine capable of bringing developmenttechnologicaltothefield, bringing more safety to operation and reducing CO2 emissions into the atmosphere. This is harbunk’s goal, developed from studies by Klabin, the largest producer and exporter of paper packaging and packaging paper in Brazil, in partnership with Ponsse, based on the Harvester Bear machine, from the Finnish manufacturer of forest harvesting equipment. With technology to fulfill all stages of wood harvesting of the whole tree system (Full Tree), the novelty of the market also increases productivity and lowers the costs of this operation, especially in small areas. Until then, Klabin carried out forest harvesting in small areas, only by ctl (cut-to-length) system, a format that guarantees operational efficiency in larger areas and requires the use of two machines (Harvester and Forwarder), each responsible for a phase of operation. This process increases the investment of companies and small rural producers, and consequently increases CO2 emissions.Byhaving a differentiated design, Harbunk optimizes the process, since this single machine can perform the extraction and processing of wood, considerably reducing the costs of the operation, while offering a more efficient and sustainable harvest. One of the main gains is the reduction of lost time with the transport of machines. As it is just a machine, it stays longer in each forest than the cut-to-length or full tree set, reducing the travel time between the harvesting areas and consequently increasing the machine’s availability for operation. Harbunk’s benefit, however, goes beyond the harvesting process. The equipment, which took two years between the conception of the idea and the final product, reduces the risk of forest accidents, because it can harvest in virtually all types of areas, including those with wavy topography, strengthening the safety of the operation. In addition, Harbunk’s technology follows the state of the art in the forestry sector, which has safe and comfortable technology machines. “The Harbunk machine demonstrates once again Klabin’s pioneering pioneering of promoting innovation in all its areas of expertise as an important driver for business evolution. The development of the machine is an initiative focused on operational excellence in forest harvesting that provides environmental and social improvements for its employees and community, reinforcing the Company’s recognition as a citizen and innovative company”, says José Totti, Klabin’s Forest Director. In constant search for innovation, Harbunk is the result of dedication and synergy between the forest business areas, international partners and is part of the portfolio of the Forest Projects and Development area. “In the area of Projects and Forest Development we implement methodologies to manage a strategic and agile portfolio, ensuring the execution of our innovations. We seek to support Klabin’s strategic growth by ensuring the implementation of innovation projects in harvesting, forestry and forestry logistics. Our commitment is to bring projects 2030 Agenda, which promote sustainable development, while increasing operational efficiency,” adds“WeTotti.are always at the side of our customers to develop solutions to the real problems of forest harvesting. We took a Klabin team to learn about innovative initiatives in Europe and developed together a machine model that would suit their needs, further optimizing the operation, especially in smaller forest areas,” said Rodrigo Marangoni, Ponsse’s sales and marketing manager.
José Totti, Forest Director, Klabin
Besuchen Sie uns! SeppiMulcher Contact Italy,www.seppi.comsales@seppi.comus!38017Mezzocorona (TN) ■ FORESTRY MULCHERS ■ S TUMP GRINDERS ■ S TONE CRUSHERS for excavatorspto-tractors,orprime movers
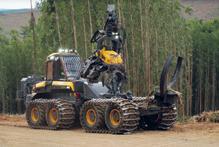


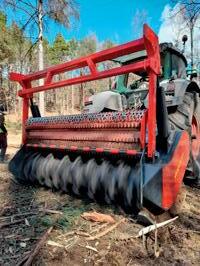
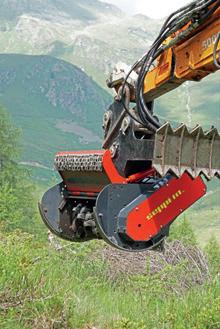
Simple servicing With a new valve that simplifies serviceability, the HTH618C Series-III features improved hose routing, enhanced valve cover assembly and easier access to make quick work of servicing. Likewise, hose protection helps keep the head running and increases durability. Easier access to the rear of the valve near the head module as well as inlet hoses also helps increase uptime while a larger oiler filler improves ease of filling bar and chain oil. Benefitting from direct customer input, the HTH618C Series-III has improved access and serviceability to help lower daily operating costs.
Waratah Forestry Equipment debuted the HTH618C Series-III – a new generation of its HTH618C harvester head built for increased productivity, reliability, uptime and more. With a variety of new features paired with a compact and durable design, this agile thinning head is well-suited for mixed diameters.
Waratah Forestry Equipment’s new HTH618C Series-III provides increased productivity, simple servicing
The Waratah HTH618C Series-III is currently available to customers in Europe, the United States, Canada, Australia, New Zealand, Asia Pacific, Brazil and Latin America.
“The HTH618C Series-III is highlighted by a new valve that delivers more responsiveness and operating efficiency. This Series-III model delivers what our customers expect and need from Waratah,” said Brent Fisher, product marketing manager for Waratah. “Additionally, with new twin diameter measuring and improved hose routing, servicing and guarding, we’re looking forward to delivering another head that is truly Built To Work®.”
International Forest Industries | AUGUST / SEPTEMBER 2022 15
The HTH618C Series-III features twin lower delimb arms and a high-performance valve to ensure superior delimbing with agile and responsive log control – tackling a wide range of harvesting jobs. The maximum delimb opening of 660 mm (26 in.) can handle larger stems. Improved cutting performance and tilt control also contribute to increased productivity.Low-powered base carriers will have improved processing output and productivity with improved feeding performance and feed motor options.
Increased productivity
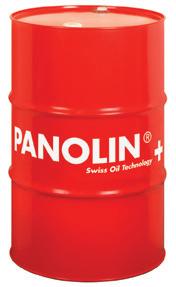
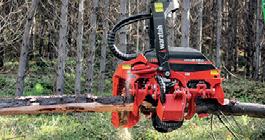

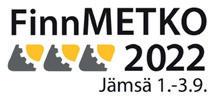
Western Forest Products invest $29m in B.C. Operations Western Forest Products Inc. (TSX: WEF) (“Western” or the “Company”) has announced capital investments totaling approximately $29 million towards its B.C. operations. The investments are part of the Company’s ongoing commitment to support valueadded manufacturing on the B.C. Coast and grow its value-added wood products business, all while continuing to improve Western’s long-term competitiveness. These capital investments represent an increase of $13 million over and above the $16 million of capital investments discussed in the Company’s first quarter 2022 Management’s Discussion and Analysis. Specifically, the investments include: • $12.3 million in a new continuous kiln at the Saltair sawmill in Ladysmith, B.C., allowing for increased capacity for continuous drying of lumber, while reducing energy consumption. The sawmill is the largest singleline sawmill on the coast of B.C. have undergone a previous multi-phase strategic capital investment of over $45 million since 2015 to modernize the facility.
Aaron Stone, Mayor of the Town of Ladysmith
Katrine Conroy, Minister of Forests
“Western has deep roots in the community and plays an active role by providing significant employment and contributions. This investment further affirms the company’s commitment to Nanaimo, and we look forward to our ongoing partnership for many more years to come.”
Kim Smythe, Greater Nanaimo Chamber of Commerce President and CEO
“We are pleased with this investment in the future of the mill and our community. Western’s manufacturing facility is a strong economic driver, supporting numerous workers and their families while also generating business and benefits for vendors and contractors.”
16 International Forest Industries | AUGUST / SEPTEMBER 2022
• $8.3 million in other capital investments in the Company’s B.C. operations, including new kiln control systems at the Saltair sawmill and our ValueAdded Division in Chemainus, B.C. to increase supply of kiln dried finished products for customers.Eachofthese investments will serve to generate additional value from Western’s wood products. Work on these investment projects is underway and is expected to be completed by 2023. Western is one of the largest private employers on Vancouver Island with six sawmills and two remanufacturing plants, providing 3,500 jobs that support nearly 20 healthy and vibrant communities across the province. These operational upgrades are an extension of the Company’s significant investment in valueadded manufacturing on the Ravi Kahlon, Minister of Jobs, Economic Recovery and Innovation “Investing to upgrade Western’s operations is great news for forestry workers, communities and the industry as a whole. These capital investments support our government’s vision to increase innovative, made-in-BC manufacturing and get more value out of every tree harvested.”
“We are proud to add to our ongoing investments in our manufacturing facilities on Vancouver Island with substantial upgrades that maximize the value of the wood products we process locally. With the use of wood in multistorey construction growing as a low carbon solution, we have invested in considerable research to determine how we can participate in this growth opportunity. Adding equipment that allows us to manufacture product lines used in glulam and mass timber building represents an exciting step forward for our company and employees, as we pursue growth while supporting the needs of our communities and planet. We are also looking forward to increasing our drying capacity by approximately 72 million board feet, which is an important part of the process in making higher value wood products.”
Joel Fournier, Vice President of Canadian Manufacturing, Western Forest Products About Western Forest Products Inc. Western is an integrated forest products company building a margin-focused log and lumber business to compete successfully in global softwood markets. With operations and employees located primarily on the coast of British Columbia and Washington State, Western is a premier supplier of high-value, specialty forest products to worldwide markets. Western has a lumber capacity in excess of 1.0 billion board feet from seven sawmills and four remanufacturing facilities. The Company sources timber from its private lands, long-term licenses, First Nations arrangements, and market purchases. following the previous multi-phase strategic capital investment of over $42 million undertaken to modernize the sawmill since 2013. The facility has three existing kilns on site for drying lumber.
• $7.9 million at the Duke Point facility in Nanaimo, B.C., to optimize the centralized planer facility with new equipment, including a machine stress rated (“MSR”) lumber grading machine. The MSR machine provides strict lumber grade quality control with known values for strength and stiffness for lumber utilized in engineered products, including roof trusses, glulam and mass timber. The sawmill and planer B.C. Coast. Since 2013, Western has invested over $450 million throughout its entire operating platform. Quotes “Congratulations to Western Forest Products on these substantive value-added investments on Vancouver Island. These projects will strengthen our province’s position as a world leader in mass timber and developing value-added wood products. When we work together towards achieving clean growth, we are supporting our StrongerBC Economic Plan, helping to fill the jobs of tomorrow while building an economy that works for everyone.”
Duke Point facility in Nanaimo, B.C
Leonard Krog, Mayor of Nanaimo
“We welcome Western’s ongoing investments to manufacture wood products from sustainably managed forests. This type of investment helps sustain jobs and build a more prosperous future for the many in and around our community who depend on forestry.”

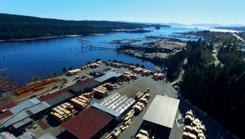
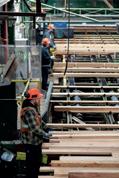
BRAIN WAVES. RIPPLE EFFECTS. MAXIMIZE YOUR PRODUCT VALUE WITH THE INTELLIGENCEARTIFICIALBEST PROCESSINGFORMODELSWOOD BID ARTIFICIAL INTELLIGENCE BENEFITS • Increases your softwood/hardwood board production value and recovery • Fastest ROI in the industry for sawmills with small or large volume production • Eliminates bottlenecks at wood grading • Maintains constant production quality to meet customer expectations KEY FEATURES • Unmatchable accuracy of defect detection • Unsurpassed identification of wood species • Up to 100 times faster than generic AI algorithms • AI models specifically adapted by experts for your production and wood fiber We offer AI solutions for debarking, sawing, trimming, edging, grading—and there’s more to come. Call now to find out how you can maximize your production value. 450-435-2121 | www.bidgroup.ca Watch our new video about AI
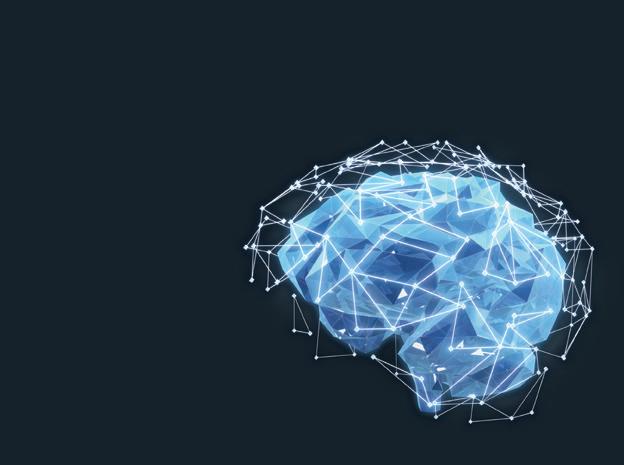
The sustainment of the plant’s operational life cycle excellence will be supported by BID’s Reliability program which will provide comprehensive service, parts, consumables, and upgrades. The project will incorporate new leading-edge solutions from its strategic partner Rockwell. “We would like to thank Canfor for their ongoing trust in our people and technologies. We are humbled that they have chosen to partner with us again for their next significant capital investment and ongoing operational excellence,” said Alistair Cook, President and CEO of BID Group. Work on site will begin late in 2023 and startup of the sawmill is scheduled for the third quarter of 2024 Stephen Mackie, Executive Vice President, North American Operations, Canfor
JS-50X6BNEW CARRIAGES EDGERSSHORT-INFEED& SIMPLY BETTER SAWMILL SCANNING
18 International Forest Industries | AUGUST / SEPTEMBER 2022
VANCOUVER, WASHINGTON, USA
BID Group has announced it will be partnering with Canfor Corporation (Canfor) to deliver a new state-of-the-art sawmill complex in southern Alabama. Through its industry-leading wood processing technologies and integrated solutions offering, BID will manage, design, build, equip, install, and provide full start-up services for the project. “We are thrilled to partner with the BID team again to continue our investment in world-class manufacturing operations applying state-of-the-art technologies that enhance our sustainability objectives. This project will employ the best complement of modern technologies to meet our growing customer demand for the highest quality products, enhance our sustainability goals, and transform our workplace to offer employees a modern facility that will operate for generations to come. Working with an industry leader like BID provides the confidence that this major project will be done right and delivered on time,” said Stephen Mackie, Executive Vice President, North American Operations, Canfor. The new operation will incorporate the full spectrum of BID’s best-in-class wood processing technologies including equipment, software, automation systems, Artificial Intelligenceenabled optimization, and the plant-wide Industry 4.0 solution,
BID to Deliver a New State-of-the-Art Turnkey Facility for Canfor
JoeScan to debut new scan heads
The sawmill scanning experts at JoeScan will soon bring the proven simplicity of their JS-50 scan head to more parts of the sawmill. “Mills love how our latest JS-50 WX model performs on their edgers and trimmers,” says JoeScan president Joey Nelson. “It’s a robust, reliable platform that is very easy to use. So we’ve been working hard to develop nextgen scanners for more machine centers.” JoeScan will debut several new scanners at the TP&EE trade show in Portland, Oregon on September 28, 29, and 30. Stop by their booth or visit joescan.com to learn more.
OPER8™. BID’s Integrated Solutions Team will provide the design, engineering, planning, fabrication, and installation services for this Turnkey project.





International Forest Industries | AUGUST / SEPTEMBER 2022 19 LUMBER PROCESSING NEWS
|
refreshed logo further promotes consistency for new and existing customers. The legal business name will remain Delta Computer Systems, Inc. for the foreseeable future, although CEO Nylund states that, “the plan is to eventually change the company’s name to Delta Motion, Inc.” The new logo will be prominently used in Delta’s marketing moving forward.
Delta Computer Systems celebrates its 40th anniversary and announces a refreshed logo
Delta Computer Systems, Inc. of Battle Ground, Washington celebrates 40 years in business this summer. Delta, a leading manufacturer of high-performance motion controllers was incorporated in June 1982. Since then, Delta has grown into the goto choice for industrial hydraulics and other demanding applications in the manufacturing, wood products, automotive, testing, entertainment, aerospace, and many other industries. Delta’s powerful RMC family of motion controllers and RMCTools software offer users decades of lasting value; and with a policy of zero-obsolescence, there are thousands of modern and legacy versions of Delta’s motion controllers in use around the globe, all of which are fully supported by Delta’s team of engineers and Steve Nylund, Delta CEO technicians.SteveNylund, Delta’s CEO, co-owner, and one of the founders, says, “At this time, I want to extend a big THANK YOU to those who have been instrumental in Delta’s success: Current and former Delta employees, consultants, contractors, vendors, addressDeltaindustrialofMotionanniversaryinaonDelta’sAsfocusandwitheasyhigh-performancefocusimportantly—customers.and—mostOurhasalwaysbeentoprovideproductsthataretoapplywhilebackingthemexceptionalcustomersupport,Iamgratifiedtoseethatthatcontinuestobesuccessful.wemoveintothenextchapteroffuture,weremainfocusedthatmission.”Deltachosetointroducerefreshedcompanylogoconjunctionwiththe40thcelebration.DeltarepresentsareinforcementDelta’songoingfocusonthemotioncontrolmarket.haslongusedthewebsitedeltamotion.com,sothe
“We have been using the screw solutions from SPRINGER since 2018. We are thankful to have chosen SPRINGER equipment because maintenance is more manageable. With that, we can focus on our business, namely veneer production.”
Shawn Eby, Coastland Wood Industries Ltd Log merchandiser – Coastland Springer USA Inc | office@springer-usa com www.springer-usa.com 550 Brookshire Rd, Ste A | Greer, SC 29651 T +1 (864) 908.3822
|
|
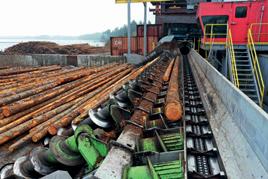


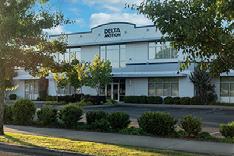

Boise Cascade announced on July 25 that it has completed the previously announced acquisition of Coastal Plywood Company and its manufacturing operations in Havana, Fla., and Chapman, Ala. “We’re very pleased to welcome these new associates to the Boise Cascade team,” said Nate Jorgensen, CEO. “We look forward to serving our customers with this expanded capacity.”
The transaction is expected to close in Q3 2022 and is subject to customary closing conditions.
BID Group has announced it has entered into an agreement to acquire Smith Sawmill Service. The transaction brings together two customer-focused organizations and further expands BID’s industryleading operational life cycle product and service offerings to include the essential recurring saw and tooling capabilities required to support modern wood processing operations.SmithSawmill Service is one of the largest suppliers and service providers of saws, cutting tools, filing room equipment, and critical consumable products to the wood processing industry. Smith serves the North American market with both proprietary cutting technologies and industryleading brands. With locations in Texas, Louisiana and North Carolina, Smith is a recognized service leader, equipped to meet the growing customer demand for personalized saw and knife repair and reconditioning solutions. “We are excited to partner with the Smith team. The combination of our organizations’ capabilities is a natural fit given our shared emphasis on excellence in total customer experience,” said Steven Hofer, BID’s Executive Vice President, Strategy and Business Development. “The comprehensive new line of products and services will offer our customers added value through the best complement of modern tooling technologies and services to meet their growing demand for the highest quality, innovative outcomes. Incorporating the Smith product and services into our BID Turnkey and wood process system offerings further compliments the investments BID
Steven Hofer, BID’s Executive Vice President, Strategy and Business Development. has made in the development of its own cutting tools solution, Blade.” “I am incredibly pleased with the opportunity to unite with an industry leader like BID.” Said Paul Smith, President and CEO of Smith Sawmill Service. “I would like to thank our team for their dedication and hard work to build a thriving business. We are confident this partnership will provide our employees, suppliers, and loyal customers with greater opportunities and benefits.”
Boise Cascade completes $512 million acquisition of Coastal Plywood
BID to acquire Smith Sawmill Service
Coastal Plywood Company’s Havana, Fla., plywood facility
In June, the Boise Cascade Co. reached an agreement to acquire Coastal Plywood Company, including its two manufacturing locations, from Coastal Forest Resources Company for $512 Nate Jorgensen, CEO Boise Cascade million.Coastal is a provider of plywood, lumber, and treated wood products throughout the eastern U.S. The purchase agreement includes its locations in Havana, Florida, and Chapman, Alabama, which employ approximately 750 people.“This acquisition incrementally expands our veneer capacity in support of our customers,” said Nate Jorgensen, CEO, of Boise Cascade. “Near term, it provides us the ability to optimize our existing engineered wood products (EWP) asset base. Longer term, we are excited to fully integrate this strategic venture and we intend to invest $50 million into our Southeast operations over three years to further our EWP production capacity.”
Paul Smith, President & CEO of Smith Sawmill Service
LUMBER PROCESSING NEWS
20 International Forest Industries | AUGUST / SEPTEMBER 2022




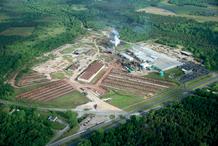




The new facility will replace the existing operation in the City of Mobile. Following the construction and startup of the new facility, an orderly wind down of the Mobile operation will be undertaken. All current employees will have the opportunity to remain with the Company. About Canfor Corporation Canfor is a leading integrated forest products company based in Vancouver, British Columbia (“BC”) with interests in BC, Alberta, North and South Carolina, Alabama, Georgia, Mississippi, Arkansas and Louisiana, as well as in Sweden with 70% interest in Vida Group. Canfor produces primarily softwood lumber and also owns a 54.8% interest in Canfor Pulp Products Inc., which is one of the largest global producers of market Northern Bleached Softwood Kraft Pulp and a leading producer of high performance kraft paper
Don PresidentKayne,& CEO, Canfor Canfor Corporation (TSX:CFP) has announced it will invest approximately $210 million USD to build a new, state-ofthe-art sawmill complex in southern Alabama. Using leading technology, the new sawmill will have an annual production capacity of 250 million board feet on a twoshift basis and will provide a new, modern work environment for the approximately 130 people who will be employed directly, in addition to supporting significant indirect jobs. In alignment with their sustainability goals and decarbonization targets, the facility design includes investment in a biomass-fueled lumber drying system. Startup of the facility is anticipated in the third quarter of 2024“Building on Canfor’s proud operating history in Alabama, we are excited to invest in a new world-class facility that will ensure our long-term ability to operate competitively. In addition, the facility’s versatility and flexibility will enhance our ability to more closely align our production of high-quality products with market demand,” said Don Kayne, President and CEO, Canfor. “We greatly value our employees and are committed to providing family-supporting jobs and generating economic activity in the region. We are pleased to be transforming the workplace for our employees by providing a new, modern facility that will continue to operate for generations,” said Tony Sheffield, President, Canfor Southern Pine. “The expansion of Canfor is a strategic investment in the community, sawmill industry and economy of South Alabama. As one of the most heavily forested states in the nation, Alabama has ample opportunity to attract significant new capital investment in the forest industry, and it’s apparent we’re doing just that,” said Governor Kay Ivey. “Mobile – and all of Alabama – has been proud to be the host of Canfor’s U.S. headquarters, and we look forward to seeing their continued, nation-wide success after this highly-anticipated and much-needed facility growth.”
International Forest Industries | AUGUST / SEPTEMBER 2022 21 LUMBER PROCESSING NEWS TURNS YOUR LOGS RIGHT • Improves your recovery • Increases your throughput • Fits on most existing log turners LET US HELP YOU TO ROTATE YOUR LOGS PROPERLY! 450-434-8389 | info@autolog.com | autolog.com
Canfor to invest in new facility in Alabama
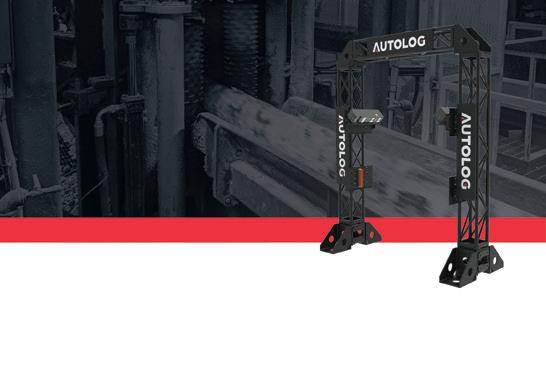
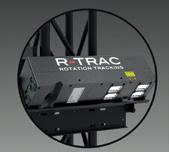


BID’s Comact TrimExpert, the most common AI optimizer for Hardwood that, until recently, was impossible: automatically identifying the exact cutting tool that has processed the face of the board (patent pending). Looking for cutting accuracy issues can be tedious, especially with the lack of experienced personnel. With this SmartTool, you will easily identify which tool has cut a specific board. All
• thickness/width taper
BID’s Advanced AI Over the past few years, BID has developed the most advanced AI engine in the industry. Put to the test in over 200 vision systems, it has proven itself and demonstrated exceptional and reliable performance. Benefiting from the technological advances of BID’s AI platform and the development of specific diagnostic algorithms, this SmartTool can accomplish a task dimensional statistics can be tallied by cutting tool source. Therefore, production and quality control staff now have an overview of every machine’s cutting accuracy over time, will receive real-time alarms on specific issues, and will be empowered to monitor trends to avoid upcoming issues. Pinpointing and correcting the source of a dimensional issue becomes effortless. Powerful dashboards and alerts Activated on the trimmer line, this integrated software benefits from the optimizer’s high 3D precision measuring devices. The software computes and monitors many crucial statistics including, but not limited to:
Quickly Detect Sawing Anomalies with BID’s New Trimmer SmartTool using Artificial Intelligence Producing bad lumber that will end up in low grades or in trim loss is very costly. Identifying a defective or ill-fitting cutting tool can take time... So why not have
these actions accuratelyandautomatically,performedreliably,inrealtimewithBIDGroup’snewTrimmerSmartTool,asolutionthatwillquicklyanddetectsawinganomalies,allowingyoutomaintainproductqualityandimproveproductionvolume.
22 International Forest Industries | AUGUST / SEPTEMBER 2022 SAWLINES
• piece-to-piece sawing deviation
• bevel • left-right wane distribution
• sawing deviation inside a piece
• the percentage of pieces on target dimensions
With the new Trimmer SmartTool, there is no need to perform regular manual quality checks to find costly issues. By leveraging BID’s advanced Artificial Intelligence (AI) vision, the Trimmer SmartTool can find the origin of each board, assess its quality, and identify cutting tools that may be defective or incorrectly set, allowing you to fix the quality issues of your sawline on the spot. This new product is part of the state-of-the-art SmartTool Quality Control Suite which has been designed to add operational intelligence to your production lines.
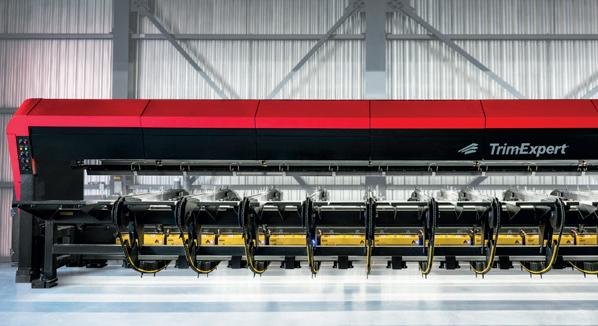

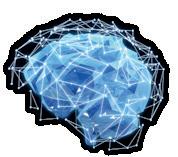
International Forest Industries | AUGUST / SEPTEMBER 2022 23 SAWLINES
Alarm and correction to proceed with were identified automatically by system. All data is presented using configurable and easy to read dashboards and reports. 28-30, 2022 OREGON
PORTLAND,
All data is presented using configurable and easy-to-read dashboards and reports. The configurable dashboards will display trends on the sawing’s dimensional accuracy before problems arise. Moreover, emails and custom alarms can be set to ensure no problem goes unnoticed, whether you’re in the mill or miles away. Requirements The Trimmer SmartTool solution requires vision on your trimmer, so you either need a Comact TrimExpertTM, or a Comact trimmer optimizer that has the capability to be retrofitted in order to add a vision section to it. Unlike external third-party systems, all the tools are already included in Comact optimizers’ software and hardware. The Trimmer SmartTool can be activated in any up-to-date version of the software. All the KPI’s are accessible within the software and benefit from the renowned Comact Deep Learning AI engine. Reduce your targeted dimensions Ultimately, the Trimmer SmartTool will help you reduce the sawing dimensions. In many cases, sawmillers keep too much “meat around the bone” to compensate for sawing inconsistencies. By having more control using the Trimmer SmartTool, and especially if combined with BID’s Primary Breakdown Closed-Loop SmartTool, it is then possible to improve and maintain production volume and quality at the sawmill. To sum it up, the Trimmer SmartTool offers you peace of mind knowing that your production is always being monitored and that the lumber produced is right on target. It can even detect hard-tonotice, infrequent issues. Recurrent quality control checks are no longer necessary, taking the pressure off your team. All this integrated seamlessly into Comact’s potent optimizing software and backed with BID’s renowned 24/7 service. Curious to know how the SmartTool Suite could help you sustain high product quality at all times? Contact BID now or visit www. bidgroup.ca
September

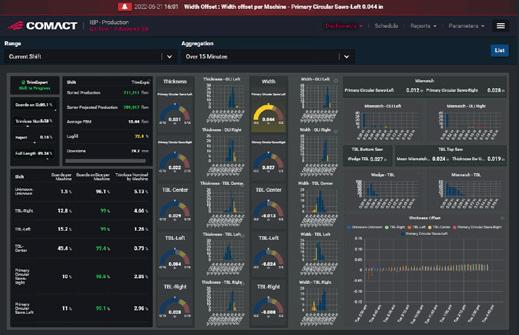
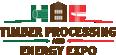
2. remote plus: Holtec employee and customer connect in a virtual room via VR smart glasses. The HOLTEC service technician can see the interface of the glasses of the maintenance expert on site and give him exact instructions for maintenance or repair of the system by means of live image processing and voice control.
• High precision and increased production speed
3. ticket system: a central ticket system makes it possible for customer enquiries to be clearly mapped,forwarded quickly and in a targeted manner, and processed transparently. It guarantees the structured, fast coordination of all service requests.
Automatic Patching Line –for intelligent and sustainable manufacturing Efficiency is among the top priorities of Latvijas Finieris Group.
Automatization allows speeding up of the production process, therefore increasing work efficiency and saving resources. Birch wood has outstanding technical properties given by nature already. For creating excellent quality birch plywood products, each veneer has to go through a multi-step process where its quality and suitability for designed product has to be evaluated.Patching is one of the most effective ways of repairing various defects in birch veneers, such as holes and knots. Veneer repairing increases capacity of supplying high quality panels without open defects on face veneers and inner layers. In addition, it allows optimisation of raw material consumption. Patches are made of birch tree as well, while intelligent
• Increasing capacity of supplying high quality panels without open defects on face veneers and inner layers laser technologies precisely spot defects and fix them without overor under-patching.Varioussizesand shapes of butterfly type patching heads enhance the quality of the end product by precisely fixing defects and scanning veneers with laser technologies, and avoiding human errors.•Patching heads in multiple sizes and shapes
The HOLTEC mobile service tool will be unique in the industry and will be available from summer.
The advantages: Elimination of travel time, rapid problem resolution and support, shorter downtime and Increased plant effectiveness.
24 International Forest Industries | AUGUST / SEPTEMBER 2022 SAWLINES
• Strong patch that holds in place
• Optimised raw material consumption • Enhanced energy efficiency in manufacturing Holtec develops its own app Holtec is developing its own app and will in future bundle all services under the tool: HOLTEC mobile services. They have created a service platform in the last few months that combines various digital services and represents another big step in terms of digitalisation. This is made possible by three important service modules: 1.e-Parts: Spare parts and documentation online via smartphone or desktop. Simple and mobile parts identification. Any part can be scanned and displayed directly in the app via QR code. Shopping cart function with automatic request, relieves service staff.
• Quality control using intelligent laser technologies
Automatic patching lines are used in production of Riga Wood birch activitieshumandecreasingplywood,manualworkforceinputindailyproductionandreplacingitwithintelligenttechnologies.
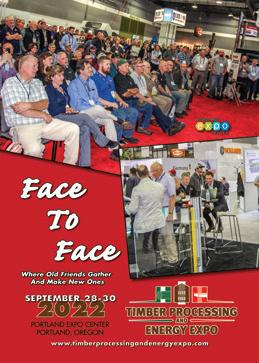
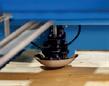
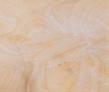
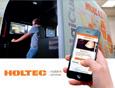
Logeye 900 Stereo: a revolution in carriage scanning
MiCROTEC has upgraded an existing and
International Forest Industries | AUGUST / SEPTEMBER 2022 25 SAWLINES September 28-30, 2022 PORTLAND, OREGON
productivityaccuracyhigh-performingsystemtorefineandboostinthemill
MiCROTEC has released the latest revolution in Carriage Scanning – the Logeye 900 Stereo. The Logeye 900’s stereoscopic imaging system provides a full 360° scan of a log as it’s rolling into the carriage, headrig, or end dogger.Since the scanning takes place as it’s transferred into position, the log is already fully optimized and ready for sawing the instant it is dogged. This leads to higher throughput speeds and vastly improved recovery, as the entire surface of the log is imaged without shadows or occlusions. The scanner is also able to detect the current rotation of the log at any point in the process, allowing full rotation optimization and turn correction, a feature that was only previously possible on lineal log scanning lines. The Logeye 900 Stereo is an efficient and modular solution. Each module can measure up to 1,500 mm and be combined for even greater scan length. The Logeye 900 can scan logs up to 1,400 mm in diameter. Once the scanner is installed, operabilitytheof the band saw significantlyisMiCROTEC’ssimplified.trusted Maxicut sawing optimization is fully integrated in the scanning system, providing unparalleled pattern optimization. The Maxicut sawing optimization provides a new standard of breakdown optimization.Thissoftware considers the geometry, quality, and resale value of final products as well was the customer-specific product quality requirements – all while evaluating the optimum cutting pattern of logs. Maxicut simulates and calculates the best possible yield and lumber recovery that can be obtained by combining different finalWhenproducts.theLogeye 900 Stereo is paired with MiCROTEC’s unique Optiline system, the optimized pattern is overlaid on the live video of the log as it’s being sawn, to assist the sawyer in breakdown decisions and provide complete transparency to the optimized solution.“TheLogeye 900 Stereo is a true revolution for the wood products industry – a unique, interesting, and efficient system,” MiCROTEC stated. The scanner continues to become more and more relevant on the European market. The Logeye 900 Stereo is also gaining fast traction in the North American market as MiCROTEC has sold units to Conifex and Canfor in BC, and Cascade Hardwoods in Chehalis, Washington. The Logeye 900 alone gives us about 5% more cutting performance Pfeifle Holz sawmill, Germany
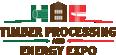
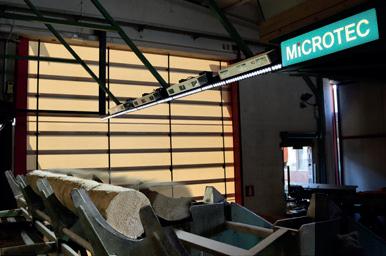
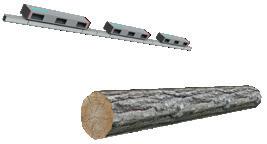
Block Controls functions include • Ripsaw, up to 8 sawblades
Theversions.greatthing about their system is that the software is almost identical for all versions, which has proved interesting for several customers as they have invested in both edger and trimmer in their lines. All versions are also available for transverse and longitudinal processes.
BoardProfiler 3D-LE. Lineal scanning system for edger and ripsaw optimization Edger system Case study 2. “Edger” From a sawmill in Sweden their customer uses our BoardProfiler 3D both in edger and trimmer.
• Harptests shows better than 98% or similar to human test results.Inboth case studies the BoardProfiler 3D is used. Just different versions but with almost the same screenview and position for input data. Easy to learn and handle for
Block Control system builds on their Edger which has been a success since the first system was sold about
• Positioning for chipper
LIMAB advantages:
3D - for Edgers & Trimmers
• Sensors transmit data for block positioning for chipper and rip-saw
operators!SAWLINES
• With LIMABs solution, the customer did not have to change mechanics.
BoardProfiler is the system for the wood industry that was developed more than 30 years ago, and it has to date been sold to more than 250 customers. The latest version of the system BoardProfiler 3D, is available in four
LIMAB advantages:
• Old frame was dismantled and LIMAB standard frame was installed together with system.
BoardProfiler
10 years ago. The system is easy to install, takes up little space in the process, is easy to integrate with sawmill automation systems and has a simple and easy-tounderstand software. The sensors used in Block Control and Edgers are normally their own 2D sensor, ProfiCura 600, 700 or 800. Each sensor with a high resolution of 640 measuring points across the line. The number in the series indicates the length they have on the laser line that measures the block or board. In that way, they can optimize the measurement and use the sensor that provides the best measurement performance and consequently the highest yield.
• Quick and easy installation gave an effective edging with top yield results. Result of case studies:
• LIMAB BoardProfiler 3D-L Block Control was the best and most flexible solution for the mill. LIMAB Edger is more or less the same system as the Block Control system. It has the same functions and includes skewing and trimming if necessary.
• Because of the accuracy of the system, customers can use smaller blocks to optimize bigger boards than before. Yield saving!
• Customer can decide how much/ little of the wane that should be left on each board.
• System will transmit data to superior system (sawline/ trimmer) to optimize correct and increase yield.
• Dimensional control of block.
Case study 1. ”Block line” From a sawmill in France where they had a line for thinner blocks, lack of space was a crucial point when deciding on systems.
• Block control (optimization for chipper or ripsaw)
26 International Forest Industries | AUGUST / SEPTEMBER 2022
• Flexible solutions where they can place sensors more or less wherever they want in the line.
• Edgers • Trimmers • Classifier (Sorter, Dimensional control)BoardProfiler
• Old and obsolete parts to continue run to present edger.
• Dimensional positioning of block
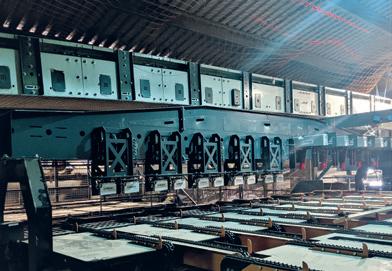
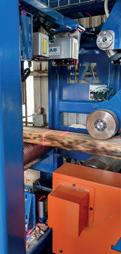




• The Logeye 900 Stereo represents a revolution. The stereoscopic measuring system enables a 360° scan of the log, while it is rolling on the band saw carriage. This full-contour measurement of the log on the bandsaw carriage, while it is still unique in the world, is a modular and a very efficient solution. The product has received excellent customer feedback. For example, Pfeifle Holz recently reported an increase in performance of at least 5% with the Logeye 900 Stereo alone, a fast return on investment and a significant simplification of the operation of the bandsaw.(see page xxxxxxx)
• MiCROTEC is the only manufacturer to offer a calibratable round timber measurement system for Germany
On June 29th and 30th, 2022, the German Sawmill and Wood Industry
International Forest Industries | AUGUST / SEPTEMBER 2022 27 Optimise productionyourplan... Optimiseoperationsyourwww.halcosoftware.com Whatever your mill... Maximize profit by resolving trade-offs between recovery, production rate, and value HALCO Software Systems Vancouver, Canada• Tel: 1 604 731 9311 HALCO AD:Layout 3 3/8/10 17:22 Page 1 OVER 25 SYSTEMS SOLD
MiCROTEC’s Innovations at the German Wood Congress 2022: • Sets the standards!technologicalIn2021was the first manufacturer to receive the examination certificate for the legally compliant invoicing of logs according to the new measuring law
• The Logeye-DE-700 - the calibratable version of the variant of the Logeye 301 for Germany - is enjoying great popularity. Since February 2021, 20 reference plants have already been commissioned and conformity assessed.
MiCROTEC’s Innovations at the German Wood Congress 2022 in Berlin
• In addition to the proven “fixed angle” method, this type of measuring device enables the diameter measurement of logs with the “variable angle” method (rotating jaw)
• The new Goldeneye and Woodeye scanners complete the product range for cross-cutting applications in sawmills as well as in the finishing sector. The Woodeye line decisively expands the product portfolio in the field of hardwood scanning and optimization.
Wood is a raw material with thousands of years of tradition and a varied history. In the fight against climate change, its qualities are more important today than ever before. For 125 years now, the representative body of the sawmill and timber industry has been campaigning for its sustainable use. On the occasion of the anniversary, the German Wood Congress 2022, shed light on the position of wood in society, politics, science and business. MiCROTEC couldn’t miss it.
the(DeSH)AssociationorganizedGermanWoodCongress.
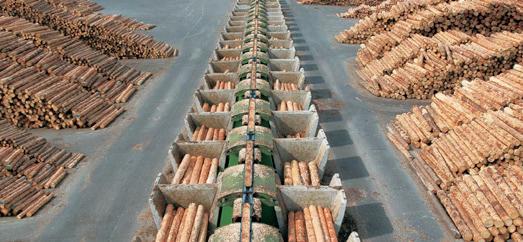
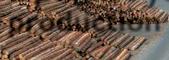
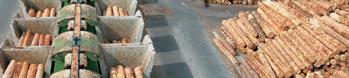

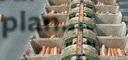

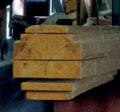
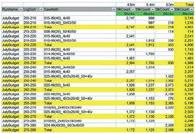

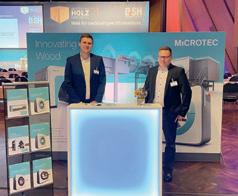
• Disclaimer – Mercer Timber Mercer International Inc. published this content on 03 August 2022 and is solely responsible for the information contained therein. Distributed by Public, unedited and unaltered, on 03 August 2022 13:48:06 UTC.
International Wood Fair 2022 International trade for forestry management and technology, sawmill technology and timber construction Dates: 8/31/2022 - 9/3/2022 Venue: Klagenfurt Exhibition Centre, Klagenfurt, Austria
28 International Forest Industries | AUGUST / SEPTEMBER 2022 SAWLINES
Laser scanning of the Log Yard, using 3D facility design, forms the basis for the smooth renovation of existingbuildings.sawmill As part of the Mercer Timber Products two-week summer revision in 2021, the existing roundwood measuring system on Log Yard 1 was revitalized. The installation of a completely new log measuring system, including new measuring chain conveyors, was accomplished in the shortest possible time thanks to a laserscanning method. Once the decision to replace the 20-year-old measuring devices was made, it quickly became clear that strong preliminary planning was required in order to see a successful project through. It was during this planning that we learned we had extremely limited space in the existing building for the measuring system. Because of this, we could foresee numerous collisions between the new devices we were working to implement and the existing steel structures, concrete foundations, pipes, and cable lines. In order to find a solution to this problem, MTP commissioned Holtec. As part of our ongoing partnership with the company, Holtec previously delivered new measuring block hoists for both production lines of Log Yard 1. Because of this, their expertise was brought in once more to carry out a 3D laser scan to document the existing system of the Friesau sawmill. Over the course of just one weekend, the entire plant and A rendering of the new measuring and conveyor system, designed using 3D imaging building stock of Log Yard 1 could be measured and recorded digitally using this non-contact measuring method. By placing the measuring unit at more than 100 positions throughout the plant, a threedimensional ‘point cloud’ was generated, with each measuring point represented. With the help of a high-performance computer, all points were then joined together to form an entire 3D model. Using this model, the lengths, angles, and other dimensions of the scanned object can be precisely determined – in fact, these 3D scanners can achieve accuracy of up to one millimetre.Thenext step was to create a detailed construction plan with CAD programs on the basis of the virtual log yard model. Here, the new conveyor systems were fit into the three-dimensional digital model. The collision test with the existing components enabled precise dividing lines to be defined on the steel structure and foundations, as well as enabling the necessary cable routing to be planned.Thanks to the preliminary planning of this project, and determining the spacing issue of a new measuring system beforehand, our team made it possible to stick to the tight schedule for dismantling the old, as well as assembling the new, measuring block hoists. This formed the basis for the company Jörg Elektronik to install the new JORO-3D roundwood measuring system. Here, too, the enormous advantage of laser scanning was demonstrated, as the positioning and assembly of the necessary measuring frame and the darkening tunnel are subject to the highest accuracy requirements. With not one but two positive experiences as part of the same two-week revision, this planning approach brought MTP forward in such a way that we are excited to use laser technology for future revision and construction projects.
Mercer Timber Products utilizes laser scanning and 3D facility design

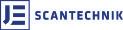
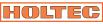
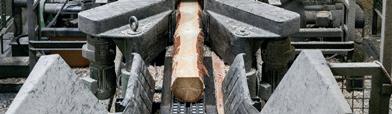

International Forest Industries | AUGUST / SEPTEMBER 2022 29 USNR acquires Timber Automation USNR, a division of Wood industryhasInternational,TechnologiestodayannouncedthatitacquiredTimberAutomation,anleaderinwoodprocessingequipmentandtechnology.ThecombinationsolidifiesUSNR’sleadershippositioninprovidingequipmentandtechnologytotheglobalwoodprocessingindustry,addingmorethan250employeesandover200,000squarefeetofmanufacturingspace John TimberPresident,Steck,Automation Dale USNRPresident,Brown, The transaction will help Timber Automation gain wider market distribution for its state-of-the-art sawmill and woodyard equipment, while USNR will benefit from the addition of Timber Automation’s highly-skilled team members and production capacity.“The addition of Timber Automation’s LogPro line of log yard equipment represents a major market expansion for USNR, and their werebettergivevalues.withby“USNR’sPresidentfromrightproductsandoptimizationVABareBrown,high-qualitycustomersproductequipment—complementedgers,products—includingBaxleyoptimization,andlumberprocessingouroffering,providingourwithmoreoptionsofmachinery,”saidDalePresidentofUSNR.“Wealsoexcitedtobuilduponthedivision’shighlyinnovativeandgradingsolutionstheopportunitytobringthosetonewmarkets.”“WeknewthatUSNRwastheownerforTimberAutomationtheoutset,”saidJohnSteck,ofTimberAutomation.reputationfordoingrightthecustomeralignsperfectlyourcompanycultureandThispartnershipwillhelpuswidervisibilityandprovidesolutionsforcustomers.”Termsoftheprivatetransactionnotdisclosed. The addition of Timber Automation’s LogPro line of log yard equipment represents a major market expansion for USNR SAWLINES




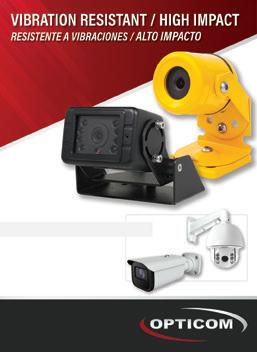
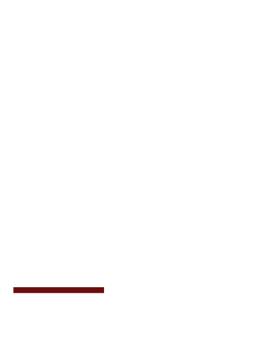
Skidder
30 International Forest Industries | AUGUST / SEPTEMBER 2022
Profitability and productivity are critical in the woods, and as loggers take to new areas for jobs, they need dependable machines that are built with these niche applications in mind Matthew Flood, Product Marketing Manager, John Deere John Deere’s purpose-builtpowerful768L-IIBogie
John Deere recently introduced the new six-wheel 768L-II Bogie Skidder, a true woodland warrior designed to conquer wet conditions and steep slope terrain. Incorporating the proven, durable features found on the John Deere L-II Skidder lineup, the new 768L-II maximizes productivity, performance, and comfort when carrying hefty loads over long distances in challenging conditions.“Profitability and productivity are critical in the woods, and as loggers take to new areas for jobs, they need dependable machines that are built with these niche applications in mind,” said Matthew Flood, product marketing manager, John Deere. “With our new 768L-II Bogie Skidder, we’re delivering a purpose-built machine that navigates tough terrain, such as swamps or steep slopes. Providing distinct features, the John Deere bogie skidder helps loggers maximize their potential, regardless of the conditions.” The 281-horsepower 768LII features heavy-duty bogie axles, which incorporate large components to maximize durability and stability for long axle and tire life. The heavy-duty axles are purpose-built for tough applications, effortlessly pulling heavy loads and maneuvering tough terrain. The smooth, stable operation results in reduced machine vibration, ultimately minimizing operator fatigue.
&ONGRAPPLE22.3MAXIMUM-SQ.-FT.THE768L-II948L-II
Another key feature is the excellent tractive ability and floatation. When combined with the bogie axles, ground pressure is reduced, allowing the 768L-II to work in wet terrain not accessible with a four-wheel skidder. As a result, the harvesting window is extended, adding more working days to the calendar.
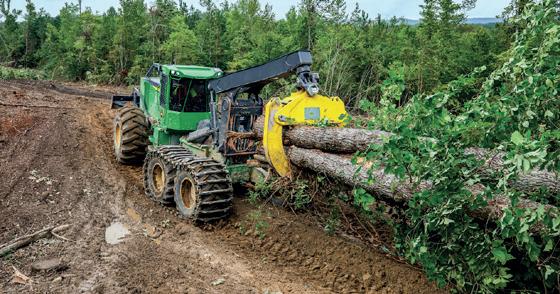
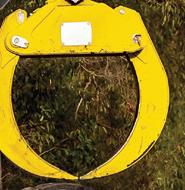
SKIDDERS
The new arch design provides the operator with an expansive rearward view of the grapple and work area, providing excellent visibility. Improving maneuverability, the long wheelbase and boom-arch envelope boost reach and lift capability for the boom and grapple, increasing dexterity in the woods. The tight turning radius enhances agility at the landing. “The John Deere bogie skidder is hands down twice as good as a regular four-tire skidder. It’s just all-around better in my book for productivity and ground disturbance,” said Jason Dawson of Triple J Logging. “With the 768L-II, you can carry twice as much of a load, especially in wet conditions and on the steep terrain, without tearing the ground up.” The 768L-II retains the other customer-favorite features
DowntimeProductivityPower FOR AUTOMATIC RADIATOR CLEANING | www.cleanfix.org
systems result in improved uptime and increase guarding and protection of key components. An
768L-II BOGIE SKIDDER Gross Power: 210 kW (281 hp) Gross Torque: 1,276 Nm (941 ft. – lb.) Max Grapple Capacity: 2.07 m2 (22.3 sq. ft.) Operating Weight: 23,697 kg (52,245 lb.) the L-II product lineup. Streamlined hydraulic increased grapple squeeze force twospeed productivity, while articulation steering sensors improve the operatorHighlyexperience.regardedby customers, all L-Series II models feature a spacious cab, including ample storage space, configurable controls, and an effective HVAC system. controljoystickofaccessible,electrohydraulicArmrest-mountedcontrolsofferhand-fingeroperationallmachinefunctions,andsteeringprovidessmoothofsteer,direction,and ground speed. The industryexclusive Continuously Variable Transmission (CVT) marries the efficiency of a direct-drive transmission with the smoothness of a hydrostatic drive. As a result, CVT provides more power to the ground by sensing the load, increasing torque and tractive effort as needed to maintain the desired speed.
The John Deere bogie skidder is hands down twice as good as a regular four-tire skidder. It’s just all-around better in my book for productivity and ground disturbance Jason Dawson of Triple J Logging
winch further increase
and
REVERSIBLECoolingFANS
and redesigned electrical and
introduced on
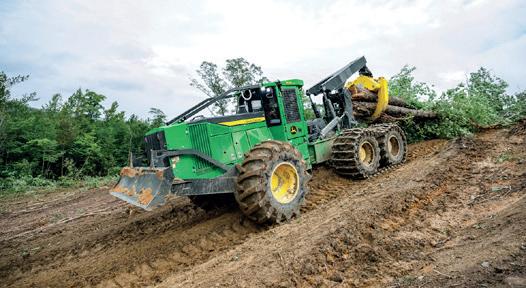













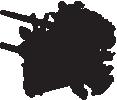
switchablemachinesinterestedcontractorsforestrywereprimarilyinpowerfulwithall-wheeldrive,differentiallocksand a logging crane. Today the focus is also increasingly on other factors: Drive comfort and ergonomics are becoming more important. Also, efficiency and waste as well as sustainability and environmental compatibility of the machines are playing an even greater role. Welte has developed the new 6-cylinder machines in the proven tradition of modular construction for forestry contractors with very diverse requirements. In order to meet the particular range of tasks in the best way, all variants of the new generation contain the reliable, compact and proven Welte machine technology. On combi machines the quick-change system also offers the forestry contractors the option to change between clambunk and loading basket, with no problems and in a time-efficient manner. The two-part combi basket patented by Welte is particularly suitable where different product ranges as well as energy wood have to be logged – changing from short to long can be performed during the trip in no time at all, without rebuild time.
Up to now,
The HSM name is synonymous these days not just with outstanding quality and innovation but also with first class service and spare parts service. Competent technical advice and maximum parts availability ensure that their customers remain competitive. This is also backed by their dealers and partners worldwide. During the design stage of the machinery, particular attention is given to accessibility and service friendliness. HSM 805 The HSM 805 was designed systematically as a cable machine for terrain with extremely steep gradients and for wet ground. The heavy duty frame construction, the height-adjustable rear blade with high cable infeed and good visibility to the skid plate make it the perfect skidder. The low weight with optimal load distribution in conjunction with the powerful hydrostatic drive unit ensure very good gradability. With a wheelbase of 2.95m and a width of 2.4m (with 23.1x26 tyres), the 805 S is compact and agile.* High productivity at low operating costs make the HSM 805 S the perfect skidder.
32 International Forest Industries | AUGUST / SEPTEMBER 2022
*To ensure forwarding without damage to the harvested product, the machine can be optionally equipped with radio remote
W230 4-wheel forwarder (skidder) The W230 signals a new era for 6-cylinder skidders. Equipped with a Tier 5 engine, the new, ergonomically optimized panorama cab featuring an unobstructed rear panel gives operators a perfect view of the work area. The W230 redefines the skidder and can be used as a pulley, crane and clam bunk skidder.
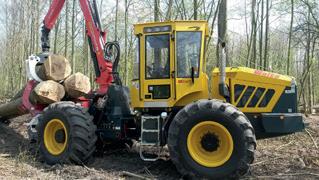


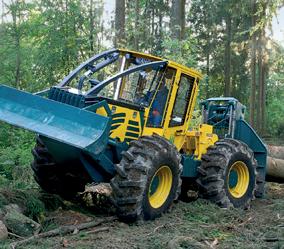
Benefiting from modern technology in accordance with market requirements, the TAF 2012 PowerShift 6C from IRUM is the newest machine designed in their Research and Development Center. It is characterized by performance, efficiency and comfort intended for emerging markets, unregulated from the point of view of emissions. The high-performance PERKINS engine, the modern power steering TAF 2012 Powershift 6C system or the PowerShift gearbox are just some of the high-quality components integrated by IRUM in the new TAF 2012 PS 6C machine: all the systems of the 2012 predecessor have been redesigned for more efficiency and comfort , resulting in a truly user-focused machine. What does this mean for you? The numerous technical and ergonomic improvements brought to the machine reduce the physical and mental stress on the operator, Being perhaps the most important component of the machine, the engine of a TAF must adapt to extreme working conditions, using lower quality fuel, be reliable, easy to maintain and economical at the same time. Precisely for these reasons, THEY opted for the experience and skill of the PERKINS company, a world leader in the field of diesel engines for agricultural and industrial applications. The 1106D-70TA model used in the TAF 2012 PowerShift 6C develops 153hp and is part of the manufacturer’s more permissive range from an emissions point of view. The engine is mated to a 4-speed PowerShift automatic gearbox. Also, the machine has axles with multi-disc brakes in oil bath and lockable differential, 2×14 ton hydraulic winch, air conditioning, as well as mobileComfortshield.and exceptional features are also strong points of the machine. From the adjustable driver’s seat with air cushion and seat and backrest heating, to the video camera for monitoring the load, the TAF 2012 PS 6C makes for easu operation. The exceptional sound insulation ensures a wellprotected workplace in any season. The machine’s cabin, in addition to increased robustness and ROPS, FOPS and OPS certification, can be folded 45° to the right to facilitate service and maintenance work in hard-to-reach places, and the location of the controls has been redesigned for more ergonomics and comfort in use . Even the steering column is adjustable. The new TAF 2012 PowerShift 6C from IRUM is a Romanian forestry machine with Western performance, standing out for cutting-edge technology, efficiency and comfort.
• Hydraulic folding hopper for more hopper volume
Shredders & Grinders
Crambo E-Mobile
The Crambo is one of the best machines for shredding all types of wood and green cuttings. The e-mobile series adds semi-mobile electric-powered versions to the line-up, featuring maintenance-free electric motors instead of diesel engines. The concept combines the compact design and flexibility of a mobile machine with the energy efficiency of a stationary machine. Two slow-running drums with shredding tools minimize fine particle and noise/dust emissions, and resist contraries. The particle size is configurable by simply exchanging screen baskets. A modern operating console and convenient access to all maintenance points make everyday work very easy.
Slow running dual-shaft shredder for wood and green waste
International Forest Industries | AUGUST / SEPTEMBER 2022 33
• Extremely large shredding compartment with two 2.8 metres long shredding drums
• Counter-rotating drums with tools in a spiral arrangement for active material movement
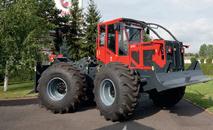

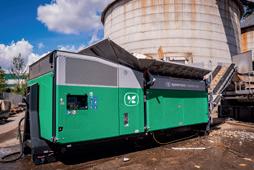

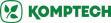
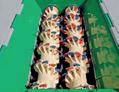
The argument goes that any forms of green product, particularly green and renewable energies, will be favoured as governments use increased stakes in enterprise to force the environment to the front of the business agenda. This is likely to be a boon for forestry in general, but particularly for biomass production. And while high-level chippers may be the primary recipient of this new favour, all size-reduction technologies could potentially have an angle into new business. Here, we present some of the leading products in this technology space that could turn forest waste into money for entrepreneurs. Astec Industries is an industry leader producing a full line of Peterson grinders, disc and drum chippers, flail debarkers, and blower trucks. A history of innovation and reliable manufacturing has established a reputation for equipment of the highest quality. Astec equipment is manufactured in Eugene, Oregon, where each machine is engineered and built to exact standards. Peterson was one of the first
8 Multiple Engine Options Depending on emission both Tier II, Tier IV, and 4 3
Shredders
& Grinders
3 Feed Chain Conveyor A robust feed chain conveyor efficiently feeds the rotor. A hydraulic drive motor synchronizes with the feed roll for near continuous feeding and massive throughput.
5 Impact Cushion System Absorbs energy shocks component life and helps severe impact.
1 Safety Guards Peterson horizontal grinders are built with safety in mind, including the projectile guard.
4 Adaptive Feed System Monitors the grinding load and varies the speed of the feed system to keep the engine working at its optimal power curve. It accelerates the feed when the engine load is light, slows when the load is high, and reverses feed when the load is excessive.
6 Rotor Placement Optimum rotor placement reduces the potential of rotors are available.
5 Impact Cushion System Absorbs energy shocks and spikes to extend grinding system component life and helps prevent catastrophic damage from severe impact.
2 Sloped Feed Walls Allow better visibility while loading and smoother feeding for more production in a wide variety of materials.
1 Safety Guards Peterson horizontal grinders are built with safety in mind, including the projectile guard.
4 Adaptive Feed System Monitors the grinding load and varies the speed of the feed system to keep the engine working at its optimal power curve. It accelerates the feed when the engine load is light, slows when the load is high, and reverses feed when the load is excessive.
2 1 to develop portable horizontal grinders as wood waste recycling machines. This industry-changing innovation made sustainable forestry practices more attainable. Using horizontal grinders to process bark waste from in-field chipping into a value-added
revenuelookingSize-reductiontechnologyismoreandmoreprofitableasasecondarystreamorprimarybusiness
3 Feed Chain Conveyor A robust feed chain conveyor efficiently feeds the rotor. A hydraulic drive motor synchronizes with the feed roll for near continuous feeding and massive throughput.
34 International Forest Industries | AUGUST / SEPTEMBER 2022
7 Mobility Options Astec horizontal grinders or stationary electric versions. an optional tow dolly for be towed with a dump truck.
2 Sloped Feed Walls Allow better visibility while loading and smoother feeding for more production in a wide variety of materials.
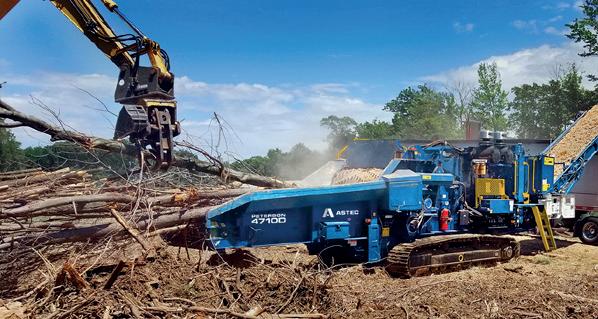

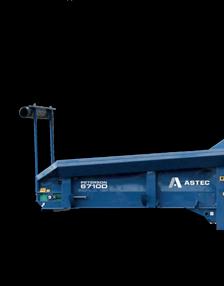
10 Continuous Discharge Conveyor One continuous discharge conveyor reduces materiel loss, increases uptime, and lowers maintenance.
7 Mobility Options Astec horizontal grinders are available in wheeled, tracked, or stationary electric versions. Larger tracked grinders have an optional tow dolly for easy transport, while the 1700D can be towed with a dump truck.
The Astec Industries Peterson 4710D Horizontal Grinder is a track mounted horizontal grinder designed for highvolume producers with very demanding specificationsend-product
14 Optional Magnetic Headroll Peterson grinders feature a magnetic headroll that allows for effective metal separation and high capacity production.
15 Optional Tracked Stacking Conveyor Add an optional Peterson stacking conveyor to pile material even higher.
12 IQAN Operating System Fine-tune adjustments for maximum productivity.
12 10 13 14 15
System and spikes to extend grinding system helps prevent catastrophic damage from placement ensures positive feeding and thrown material. Pinned or drum Options grinders are available in wheeled, tracked, versions. Larger tracked grinders have for easy transport, while the 1700D can truck.
12 IQAN Operating System Fine-tune adjustments for maximum productivity. “Not only are they built to withstand the harsh conditions of forestry operations, but they also offer the lowest operating cost per tonne,” the company said. Astec’s three-stage grinding process starts with its patented upturn rotor, drawing material into the grinding chamber. The anvil is positioned for optimum sizing and the large grate area offers high-production. The upturn process provides better material fracturing, and Astec’s four-grate sizing system makes it easy to produce the size material customer demands.Thisgrate system offers unparalleled customization to tool the machine to fit output needs.
13 Optional Cross Belt Magnet Powerful cross-belt magnets pull tramp metal off of the conveyor, producing cleaner, profitable material. Earn additional income from scrap metal!
Grates are removed through an easy-access door on the side wall. Combined with Astec’s heavy-duty bits, and robust anvil, their horizontal grinders have an
15 Optional Tracked Stacking Conveyor Add an optional Peterson stacking conveyor to pile material even higher. exceptional wear life and accurate product sizing.
All Astec grinders feature an adaptive feed system. This system monitors the grinding load and varies the speed of the feed system to keep the engine working at the top of its power curve. A patented Impact Release System allows contaminants to be ejected from the grinding chamber to reduce the risk of catastrophic damage from ungrindable objects like rocks and metal, a system unique to Astec.
11 Guard Rails With safety in mind, guardrails are high-visibility yellow, reducing potential slip & fall hazards when servicing the machine.
13 Optional Cross Belt Magnet
Powerful cross-belt magnets pull tramp metal off of the conveyor, producing cleaner, profitable material. Earn additional income from scrap metal!
10 Continuous Discharge Conveyor One continuous discharge conveyor reduces materiel loss, increases uptime, and lowers maintenance.
5 6 7 14 12 11 13 15 10 9 8 product means leaving less waste and site clean-up. Grinding slash into hog-fuel or nutrient-rich forest bedding can lessen logging impacts to an operation site. Reducing materials before it leaves the job site can increase payload and reduce truck traffic, fuel usage, and road erosion. Astec’s continued commitment to sustainability and innovation has developed specialized delivery and processing equipment that turns low-grade organic materials into high value products. The company’s strong foundation of innovations, one built upon the next, culminate into a premium product.
11 Guard Rails With safety in mind, guardrails are high-visibility yellow, reducing potential slip & fall hazards when servicing the machine.
International Forest Industries | AUGUST / SEPTEMBER 2022 35
14 Optional Magnetic Headroll Peterson grinders feature a magnetic headroll that allows for effective metal separation and high capacity production.
8 Multiple Engine Options Available Depending on emission standards for your region, Astec offers both Tier II, Tier IV, and EU Stage V engine configurations. 9 Telematics connectivitygives New D-Model grinders feature Remote Monitoring Analytics, including a wireless display for operators and offsite analytics.
Options Available standards for your region, Astec offers EU Stage V engine configurations.
9 Telematics gives connectivity New D-Model grinders feature Remote Monitoring Analytics, including a wireless display for operators and offsite analytics.
6 Rotor Placement Optimum rotor placement ensures positive feeding and reduces the potential of thrown material. Pinned or drum rotors are available.
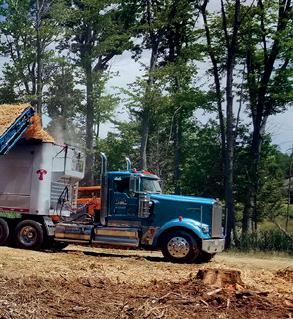
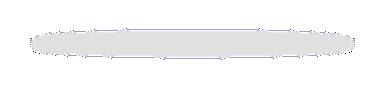
DURABILITY & PERFORMANCE
1700 Series Horizontal Grinders Astec’s most significant addition to the horizontal grinder lineup brings big power in a small package. This compact grinder has a 44 ft 1 in (1,344 cm) operating length but packs an impressive 455 hp (339 kW) Caterpillar C9.3B Tier IV engine and a large feed opening of 54 ft x 27 in (137 x 69 cm). The 1700D Horizontal Grinder is available with wheels, while the 1710D Horizontal Grinder is a tracked model. The 1700D has a pintle hitch and can be transported between job sites with a dump truck. 1 Up Cutting Rotor Opposing rotational forces create an aggressive shearing action. The upturn rotor draws material into the grinding chamber and minimizes bit wear. Provides the first stage in material size reduction. Available with pinned or drum rotors.
2750D Horizontal Grinder Astec’s 2750D Electric Horizontal Grinder is powered by a single 600 HP (450 kW) electric motor. An on-site electric machine may be the answer for grinding mill residuals to increasing profits since electric power costs are typically much lower than diesel fuel costs.
2 Anvil Positioned for optimum sizing and production, the anvil provides the second stage in the sizing process.
4700D Horizontal Grinder
36 International Forest Industries | AUGUST / SEPTEMBER 2022
Peterson+ is a telematics system that is now available on all new Astec grinders. It gives the owner and operator a live view of their equipment performance, and GPS location details. Loading operators can see common machine analytics right from their cab. Peterson+ includes a host of other features, including maintenance log, directions to the machine site, and historical machineOptionaldata.features increase the grinders flexibility between jobs. Work lights, cold weather kits, magnetic cross belt conveyor. The company’s liquid injection system is a high-flow water option that’s great for mulch coloring and dust control, and an optional transportation dolly is available on many Astec grinder models. With an eye on innovation, Astec has added several models to the lineup.
3 Grate Area The last step in the 3-stage sizing process, the large grate area results in high-production of a wide variety of materials and end products.
The most recent model release, the 4700D Horizontal Grinder, is designed for high-volume producers with very demanding end-product specifications. The 4700D is powered by a Tier IV Caterpillar C18 engine rated at 755 HP (563 kW).
The machine uses an upturning rotor in combination with a down-force compression roll to grind the feed material in a three-stage process, resulting in more accurate and consistent finished products.
3-STAGE GRINDING PROCESS
With a feed opening of 60¾ in x 32 in (154 cm x 81 cm) combined with Astec’s high lift feed roll for an optional opening up to 44 in (112 cm) high, the 2750D can reduce a diverse range of raw materials. While Astec brought the industry-changing horizontal grinder to the marketplace to process wood waste from in-field chipping operations, sustained growth and a focus on customeroriented products continues to keep the manufacturer at the forefront of the market. Heavy duty and mobile, the 1710D Horizontal Grinder can readily reduce a wide range of materials
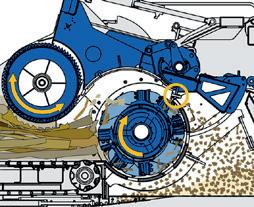
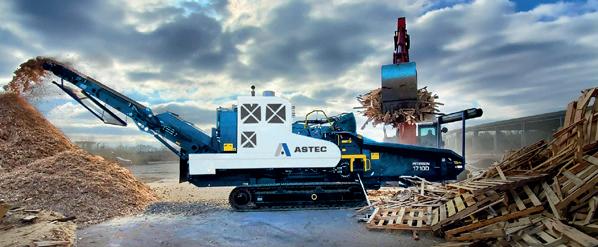
During the preliminary design there are many factors that should be considered. Such factors include species of wood, moisture content, diameter and length of incoming wood waste, metal contamination and most importantly the required end product size. For high volume high capacity wood handling operations that typically receive a large variety of contaminated materials such as railroad ties, pallets, construction, demolition and hurricane waste, Rawlings recommends wood waste systems to incorporate a combination of equipment. This could include both horizontal and vertical feed Horizontalgrinders.grinders or slow speed grinders are often utilized as the primary grinder while the vertical grinders are used to produce a smaller more consistent particle size. Using metal protection, product screening and separation allows the customer to protect their investment while producing a high-quality consistent endIfproduct.thewood handling system is designed to receive a steady stream of bark or sawmill waste a vertical feed hog is the preferred option. Typically in this scenario most of the incoming material is preprocessed further upstream and it already sized to be processed through this type of grinder.
Rawlings Vertical Grinders
Each unit is equipped with the Rawlings Super Hi-Inertia Solid Steel Rotor. With the increased inertia of the solid steel rotor our machine runs at lower RPM’S than many competitors, resulting in overall savings of electricity and maintenance costs. The Rawlings wood hog is recognized in the industry as a ‘Green monster hog’ and provides the crushing and shearing power needed to handle really tough jobs like green waste, cypress, redwood, cedar, black spruce, poplar and a wide range of other stringy and fibrous material. The machines are also tolerant of contaminants, rocks and metal without catastrophic maintenance costs if metal enters the grinding chamber.“Forover 40 years, we’ve assisted our customers in utilizing renewable resources while reducing and recycling a wide variety of wood waste into valuable wood fiber products,” Rawlings stated. “We offer a complete line up of seven different sizes of both vertical and horizontal hogs to fit any application.”
Equipment manufacturer Rawlings describes itself as a “proven leader” in size reduction technology that specializes in helping business owners with the design of custom wood-waste recovery systems for specific processing needs and budgets. Rawlings states it can handle every aspect of configuring, building, installing, and supporting a complete materials processing system. Its electric stationary systems come in all shapes and sizes – indoor/outdoor; from simple stand-alone vertical hogs for saw and paper mills, to complete multi-dimensional systems.“Adda wide variety of available options, and you’ve got the flexibility to customize the perfect wood waste recovery system,” the company stated. Each system can be designed with work platform decks, choice of belt, chain or vibrating in-feed and out-feed conveyors, metal or magnet protection, product screening and separation all customizable for specific operations.Markets for wood waste start with feedstock for engineered woods, landscape mulch, soil conditioner, animal bedding, compost additive, sewage sludge, and boiler fuel. All these end uses have similar processing requirements in that the wood waste has to be separated from other wastes, cleaned by removing contaminants and fasteners, and, in some cases, processed through grinding or chipping. The final use of the wood waste often determines how clean and consistent the feedstock must be (California Integrated Waste Management 2001). “During our 40 years designing wood waste grinding systems we have found that most of our clients are looking to get the smallest end particle size on a single pass, onestage pass through the grinder,” Rawlings said. “We often suggest that this is not always the most economical option in the long run. “Running the grinder and related equipment at full surge capacity results in higher consumption of spare parts and maintenance costs. And depending if you’re using electricity or diesel fuel these costs add up over time.”
International Forest Industries | AUGUST / SEPTEMBER 2022 37
WASTEWOODHOGS.COM 1-866-ROCWEAR (762-9327) SERVICEPARTSSALES COMPLETE LINE-UP OF THE MOST PRODUCTIVE AND COST EFFICIENT WOOD GRINDERS VERTICAL & HORIZONTAL MODELS AVAILABLE Visit us at the 2022 ProcessingTimberExpoBooth237

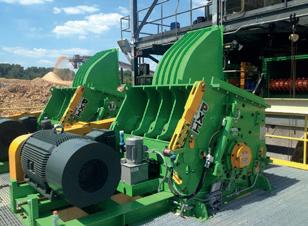
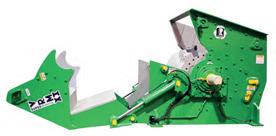
resultalsotoshredderintroducedsuccessfullyitsnewgenerationthemarketinrecentyears.Nowthelargestbiomassprocessortodate,theBA965,hasbeenrevised.TheistheBA1016-anewdimensionintheJENZshredderrange.
The development work for the BA 1016 is largely based on the experience of our BA 916/926 newcomers, which have been very well received on the market to date,” explains Dominik Meden, JENZ product manager and specialist in the field of shredder technology. “This starts with the optimal intake geometry, “ followed by the pronounced userfriendliness and ending with the new hydraulic system ‘JENZ Smart Hydraulic’. In addition, there is the screening technology for shredding applications, which is newly developed for the BA 926, which is also not to be missed in the BA 1016. The result is a technically mature and enormously powerful machine that nevertheless stands out clearly from its ‘little brother’ BA 926.” Powerful engine for extreme throughputs Equipped with a Caterpillar C18, the BA 1016 has an output of 812 hp. The CAT engine, installed in the largest configuration, makes
Higher, faster, farther: A specially developed discharge conveyor ensures fast and uniform material flow.
38 International Forest Industries | AUGUST / SEPTEMBER 2022
Superlative shredder technology
New introduction of the largest JENZ biomass processor BA 1016With the BA 916 and BA 926 series, JENZ


Focus on user-friendliness Similar to the BA 916 and 926 series, the new BA 1016 also focuses on user-friendliness. This includes smartphone-like control via the proven JENZ easy2 machine control system, the Operator Info System with LED status lights and new easy2CONNECT radio remote control, or intelligent assistance systems such as the GFA (Grinder Feed Assistant) infeed control.
Dominik Meden (left) JENZ Product Manager discharge height of 5.10 m. Due to the increased width and the selected profile, the material layer thickness is lower and the magnets can clean the material optimally. The result: very clean end material,” says the product manager. An additional plus point of the new conveyor belt: a reduced machine length. This is ensured by a different folding technique that enables machine transport without a special permit or special vehicle. “We are proud that we have succeeded in combining 812 hp performance with a compact transport length of 10.55 m. This makes the BA 1016 a mobile but very powerful shredder with technology that is kept simple. This enables worldwide operations, even in remote regions,” says Meden.The product manager sees a wide range of applications: “Due to the energy transition, heating material from waste wood and roots is increasingly in demand, so that powerful machines are becoming more and more important. Likewise, the compost market is demanding ever more powerful shredders due to rising fertilizer prices. This is exactly where the BA 1016 comes in with its efficiency and enormous throughput.”
International Forest Industries | AUGUST / SEPTEMBER 2022 39 TECHNICAL DATA: BA 1016 Performance / Throughput up to (in lcm/h) Greenwaste 430 Bark 440 Waste wood 310 Roots 190 IntakeIntake width x Intake height (mm) 1.620 x 960 Free loading length (mm) 4.500 Main Standard-Dieseldrive engine CAT C18 (kW / HP) 597/ 812 Shredding unit Rotor diameter (mm) 1.120 Number of fails 34 the BA 1016 extremely powerful in terms of throughput. “ We consider the fact that it continues to do just fine without AdBlue and yet also meets the Stage V requirements, as particular advantages of the C18. The distinctive torque curve allows us to operate at wear- and fuelsaving speeds while still increasing throughput. Maximum efficiency and throughputs of over 400 m3 were the goal here,” says Dominik Meden.
Ergonomic maintenance has also been taken into account. “The two-part screen basket system in particular makes screen basket changing fast and ergonomic, as it can be done by just one person,” emphasizes Dominik Meden. The operator’s everyday work is made easier by the newly implemented “JENZ Smart Hydraulic” hydraulic system. “In the area of the intake, we have significantly improved control behavior as a result. In short: we can selectively keep the auxiliary engine lugging and thus can use the complete performance spectrum of the engine and bring it selectively to its capacity limit. This results in more throughput, paired with lower fuel consumption. Additional advantage: the machine and the auxiliary engine are protected by the quieter, constant operation.” New conveyor belt for optimized material flow and easy transport Due to its inlet width of 1,620 mm and its inlet height of 960 mm, the BA1016 can process large quantities of material. To ensure that the enormous material flow is low in fuel and wear, the JENZ engineers rely on an extra-large screening surface and a specially developed discharge belt. “In total, the conveyor belt has become longer and wider and scores with an increased delivery speed. As a result, even difficult material can now be conveyed onto high transport vehicles with a maximum Newcomer BA 1016: The machine has a powerful CAT C18 engine with 812 hp, a large rotor diameter and a large inlet opening – an entirely new dimension in the JENZ shredder program.
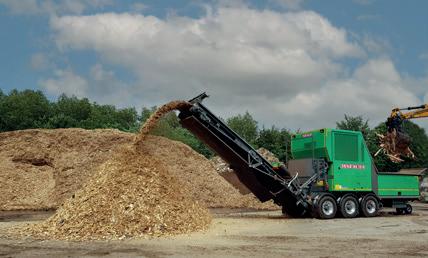
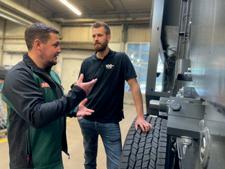
FEATURES AND BENEFITS
6400X WOOD HOG HORIZONTAL GRINDER Ideal for processing wood waste, land clearing and storm debris into saleable products, the 6400XT Wood Hog weighs in at less than 96,500 lb (43,772 kg) and measures 11’5.5” (3.49 m) wide with the standard Caterpillar 325L undercarriage with 600mm double grousers, allowing the unit to be transported to nearly all domestic and international markets. The infeed bed is 24 inches (60.96 cm) longer than previous Morbark grinders in the 1,000-plus horsepower range and has sloped sides. This configuration improves operator sight lines for more efficient loading of material.
•screens.TheMorbark Integrated Control Systems (MICS) automatically adjusts feed rates and monitors pressures and feed wheel position to maximize production and engine •efficiency.Standard on the 6400X is a removable infeed chain return floor, which allows excess material to fall away to minimize the wear on the floor, bed chain and inserts, particularly useful in land-clearing or other applications with dirty •material.Thehydraulic hinged and locking door allows quick and easy access for changing grates.
3400X WOOD HOG HORIZONTAL GRINDER
Morbark offers a full line of Wood Hog Horizontal Grinders and specialist Tub Grinders in a range of sizes, on tracks or tires, diesel or electric powered. Add a wide variety of available options, and you’ve got the flexibility to customize the perfect grinder for your particular needs. The Wood Hog is the best industrial-grade grinder you can get for processing brush, yard waste, clearing debris, storm debris, C&D waste, other mixed woody feedstocks, and asphalt shingles into saleable products.
Listening closely to customer feedback while developing the design for the 3400XT Wood Hog, Morbark provides the features customers want and the versatility they need, while staying true to our proven technology. One of the most important features of the 3400XT is that it can be made as narrow as 8’6” (2.59 m), making it within the legal transport width in any country, no matter what engine is used.With 800 horsepower (596 kW), this model is ideal for a broad range of applications in a wide variety of markets worldwide. Like all of Morbark Wood Hog models, the 3400XT also is available with electric power. The size of the 3400XT allows the model to be configured for 6400x Wood Hog Horizontal Grinder 3400x Wood Hog Horizontal Grinder
All Wood Hogs come standard with the Morbark Integrated Control System (MICS) to maximize production and engine efficiency; a laser-cut, factory-balanced rotor for unsurpassed durability; and an aggressive feed wheel with an internal poclain drive that has no chains or sprockets for more torque and reduced maintenance.
• A proven external adjustable break-awy torque limiter provides drive line protection against catastrophic damage from contaminants.
40 International Forest Industries | AUGUST / SEPTEMBER 2022
• The area between the hood and the engine has been reconfigured to 31.5” (80 cm) of working space, for better access to components for general maintenance or to change
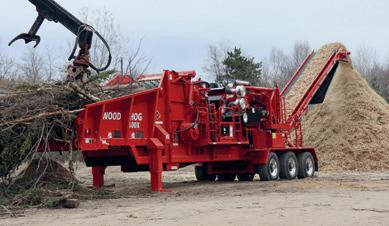
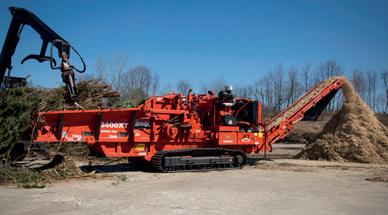
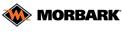
3000X WOOD HOG HORIZONTAL GRINDER
2400X WOOD HOG HORIZONTAL GRINDER
• Laser-cut, factory-balanced mill with forged hammers provides optimum grinding power.
International Forest Industries | AUGUST / SEPTEMBER 2022 41 multiple applications and global markets without additional design considerations.
The largest tub grinder on the market, the Morbark 1600 Tub Grinder is able to power through and reduce materials from large land clearing or organic/wood waste programs. With an 11’2” (3.4 m) tub diameter, 15’ (4.57 m) tub opening and a capacity of 20 cubic yards (15.3 cubic meters) and 1,200 horsepower (895 kW), this machine can power through tons of raw materials from large land-clearing projects and organic/ wood waste processing. The Morbark Integrated Control System (MICS) monitors key systems while
Morbark introduced the first industrial tub grinders for use in wood waste recycling and land clearing operations in 1990, and has led the industry ever since. We offer the most complete line of tub grinders available, in a range of sizes and in several configurations – with or without cab and loader, on tracks or tires, diesel or electric powered. Add to these choices a wide variety of available options, and you’ve got the flexibility to customize the perfect Morbark Tub Grinder for your particular needs. Morbark Tub Grinders are designed for the most challenging recycling applications. They excel at processing yard waste, pallets and other mixed woody feedstocks into saleable products.
3000x Wood Hog Horizontal Grinder
1600 TUB GRINDER
Ideal for niche markets like municipal recycling, pallet recycling, lot clearing, nurseries and tree care debris, the Morbark 3000XT Wood Hog Horizontal Grinder is perfect for processing yard waste, brush and other mixed woody feedstock into saleable product. The size of the 3000XT allows the model to be configured for multiple applications and global markets without additional design considerations.
The compact and configurable Morbark 2400X Wood Hog Horizontal Grinder is perfect for processing yard waste, brush and other mixed woody feedstock into saleable product.
2400x Wood Hog Horizontal Grinder 1600 Tub Grinder maximizing performance, and the remote control allows you to quickly adjust feed systems for top production rates and fuel efficiency. FEATURES AND BENEFITS • Tub is equipped with hydraulic augers that allow the operator to quickly remove product from beneath the mill. During material surges, pressure sensors automatically slow tub rotation to prevent plugging.
• The full breakaway torque limiter system protects the engine and clutch against shock and overload without stalling the engine.
TUB GRINDERS
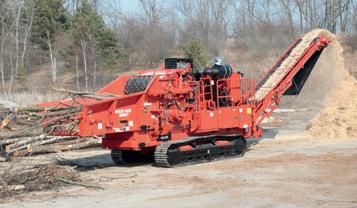

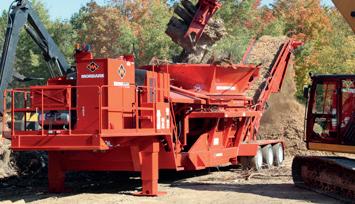
Double-shaft shredder
Shreddersapplications&Grinders•Highmaterial quality
• durable Tools Available as: diesel mobile and electrical stationary
•
IMPAKTOR
•
•
The mobile double-shaft shredder has gained international recognition since its launch and is now a primary choice for companies within the demolition and processing industry. The extremely flexible and robust shredder features a unique combination of track system and hook lift version, a revolutionary shaft quick-change system, an innovative SCU control and a shaft design that expands the machine’s range of applications many times over.In addition to numerous applications for construction and demolition waste, the mobile shredder is also suitable for processing railway sleepers, rootstocks, old and trunk wood, tyres, household and commercial waste and many other with high throughput performance Low maintenance Low noise emissions Advantages: high performance low energy consumption low noise emission • minimal dust formation
Double-shaft 950
Double-shaft shredder
•
42 International Forest Industries | AUGUST / SEPTEMBER 2022 XR mobil-e Single-shaft shredder for efficient coarse, medium and fine shredding of different material flows • Mobile shredding concept • Sturdy design with high resistance to foreign objects Primary shredder VB 450 series HAMMEL Recyclingtechnik GmbH Applications: Wood: wood waste, demolition wood, small root stems, green waste, pallets Waste • domestic waste, industrial waste, paper • Scrap: electronic scrap • Functional hydraulicallyprinciple:operated slow speed recycling machine with two-shaft-system
IMPAKTOR 250 evo
TITAN 950 In nature, the element TITAN stands for strength, reliability and durability. These characteristics have been and continue to be the key specifications for the development of the double-shaft shredders within the ARJES heavy-duty class. In order to be able to guarantee a wide range of applications with the best results, the mobile shredders are equipped with a track system as standard and are available in two different versions.TITAN shredders feature a revolutionary shaft quick-change system, an innovative SCU control and a shaft design that even meets the most difficult requirements. Numerous applications can be found in the construction and demolition industry, for shredding mixed scrap metal*, car bodies, tyres, in the processing of household and commercial waste, as well as in composting and wood processing plants.
Double-shaft shredder 250 evo
expenditures •
shredder TITAN
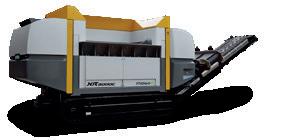


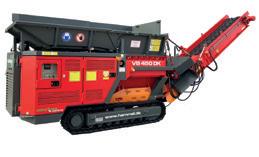
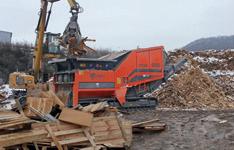
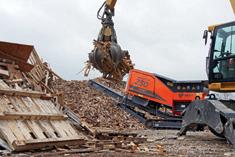
Comfortable working in long continuous operations
KESLA cranes can be used with chippers of any make
Kesla Vision XL is a slightly more spacious cabin, providing extra comfort in long continuous crane work for larger operators as well. Comfort and ergonomics can be further improved with an optional air seat and armrests. The temperature can be adjusted as desired by equipping the cabin with heating and air conditioning.Electriccontrol, which is the preferred choice for chipper feeding, can be had with either mini joysticks or vertical levers. The combination of a control valve with generous flow capacity and an electric control system adjusted to personal preferences guarantees excellent efficiency and ergonomics.Goodvisibility is ensured by the large window area and the positioning of the cabin on either the right or left side of the pillar, as required. Strong polycarbonate windows secure cabin safety. The cabin can be equipped with the Cyclone air cleaner and F9-level fresh air “Kesla’sfiltering.extensive experience with chippers is evident in the design of the cranes,” says Pirhonen.
Kesla timber cranes fit for bioenergy subsistenceshowdevelopmentsPoliticalupneedforforestryandfacilitatingtechnologies
The need for self-sufficiency in energy production has become more prominent since the start of the war in Ukraine. Wood is an excellent, renewable and carbon-neutral energy source, and residual wood can be chipped for energy. This has seen demand for chippers increase in 2022.Besides traditional timber handling, Kesla cranes can be used for the efficient feeding of chippers of any make. Cranes used for feeding chippers must be durable Chipper feeding includes long continuous operating periods compared to the traditional transport of wood, where the crane is only needed when picking up timber from the site and later at a terminal, for example. It increases the requirements for the durability of cranes in bioenergy use. Kesla cranes are designed with durability in mind.“Our cranes are mainly made of high-strength steel. Production design has studied the properties of high-strength steel carefully, and the work methods have been selected based on the properties of the material,” says Ari Pirhonen, Business Director of Truck and stationary“Welding,cranes.ofcourse, is an important work phase, and we have ISO 3834-2 certification as proof of the excellent quality of the welds.” Surprisingly, the streamlined design of the cranes, especially at the joints, also improves their fatigue durability. All models in the Kesla range have passed a fatigue test before entering the market. The fatigue test exposes the crane to extreme Production design has studied the properties of high-strength steel carefully, and the work methods have been selected based on the properties of the material Ari Pirhonen, Kesla stress, revealing any weakness in the Astructure.longreach is a feature many wish to have for their bioenergy crane. Kesla cranes offer a maximum reach of up to 12.5 m, with stabilizers ensuring stability. Stabilizers with a width of 3.8 m are typically preferred on forest roads, whereas extra-wide (4.5 m) options can be used for maximum stability at terminals with more space.Easy serviceability is naturally important both in traditional and bioenergy use to ensure long service life for the crane. Automatic centralized greasing, which carries out the lubrication of the crane, is particularly popular.
KESLA Vision XL cabin offers comfortable working conditions also when working long hours.
KESLA crane models suitable for bioenergy use, for example for feeding chippers and shredders: 2112T, 2115T, 2117T, 2012T and 1200. The crane range includes Vision XL cabin, proC control system (with either Parker or Olsbergs valve), stabilizer legs beam (width L=4500) and compressor air conditioning.
International Forest Industries | AUGUST / SEPTEMBER 2022 43
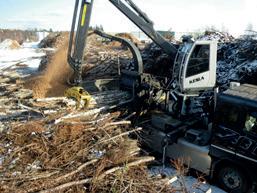

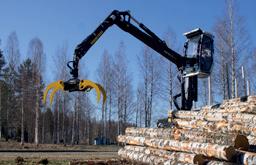
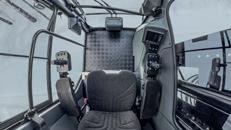
John Deere 959ML John Deere 3756G
44 International Forest Industries | AUGUST / SEPTEMBER 2022 Loaded Deereandboostenhancementswithtoperformancecomfort,theJohnG-Seriesforestryswingmachinesandshovelloggersprovidethedurabilityandreliabilityit’scustomersexpect
Purpose-built for forestry applications; these machines raise the bar and maximize productivity when it comes to tackling the most difficult jobs. Both the G-Series Swing Machines and the Shovel Loggers are equipped with JDLink telematic compatibility. This technology lets contractors track equipment, see which machines are working, and know if they’re being utilized properly and at maximum productivity and efficiency. The remote diagnostics and programming enable a dealer to quickly identify the issues at hand, minimizing the time and cost it would take to send a technician to the logging site for an initial diagnosticAdditionally,visit. TimberMatic Maps and TimberManager software – available on both lines of equipment – are designed to enhance machine connectivity and communication. The TimberMatic Maps solution includes mapping software for use in the field, which utilizes a mobile network to share real-time production information between operators, as well as back to the office. Data is collected by the sensors on the equipment, while the production location is gathered through GPS technology. Information is then transmitted to the cloud, where managers can access TimberManager from their PC, tablet, or phone, allowing loggers to follow the progress of the work site <subhead>remotely.G-Series Forestry SwingDevelopedMachinesthrough years of invaluable customer input and thousands of hours of testing, the G-Series forestry swing machines are purpose-built with loggers’ needs in Composedmind.of eight models, including the 2154G, 2156G, 2654G, 2656G, 3154G, 3156G, 3754G, and 3756G, the G-Series line sets the standard for power and efficiency in the woods. Available in either a log loader or forestry excavator configuration, these machines ensure performance and reliability in forestry expectations,Redefiningapplications.swingmachinethesemachines are equipped with several features,
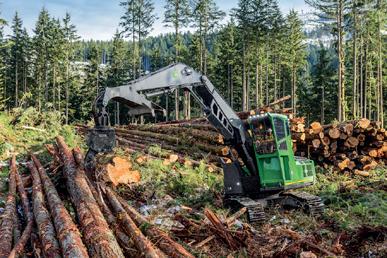
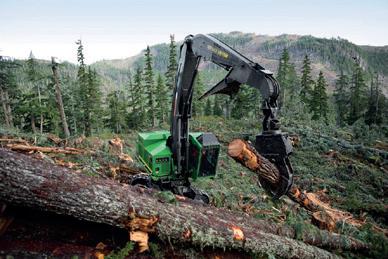
International Forest Industries | AUGUST / SEPTEMBER 2022 45 Purpose-Built Forestry Machines structures, and components that hold up in the unique and tough working conditions faced in the woods.The operator cab surpasses all safety requirements, while also providing creature comforts in intense conditions. Spacious and comfortable, the side-entry cab on the forestry excavator models is 25% larger than the previous model. The rear-entry cab on the log loader models features isolation mounting, and floormounted windows, for superb visibility to the working area. Increasing stability, the 2656G and 2156G Log Loaders and 2154G and 2654G Forestry Excavators include a longer track option. Reducing downtime and maintenance life, the 2154G, 2156G, 3154G, and 3156G are suited with larger lower rollers. Additionally, the 2154G, 2654G, 3156G, and 3756G models are available with hydraulic plumbing for processing heads. Boasting removableswingschecks.andservicing,maintenance,convenienttheground-levelfilters,fluid-filllocations,greasepointshelpeasedailyThehingedACcondenseroutalongwiththeengine-compartment screen, simplifying cleanout of debris.Areduction in electrical components increases uptime, while the efficient hydraulic management systems increase airflow and lower operating temperatures. Service bays featuring drop-down work platforms and LED service lights improve long-term durability while also increasing uptime. Shovel Loggers A direct result of the continued growth of the steep slope and soft ground logging conditions, the John Deere 959ML and 953ML Shovel Loggers are designed to boost productivity even in the most challenging of applications. “We are committed to providing loggers with proven equipment solutions that meet their unique needs, regardless of the job site,” said Jim O’Halloran, John Deere Product Marketing Manager. “The 953ML purpose-built shovel logger can effortlessly tackle swampy terrain while the 959ML leverages the best-in-class leveling control system designed specifically for steep slope operations.”Theoperator cab on the 959ML machine was engineered with the challenges of the steep slope environment in mind. The roomy design includes a large, upward viewing skylight and downward viewing window for increased visibility and accessTierwithspongyandmaximizesandwithandAnotherduringoverboom,grappleswamp-loggeroperatorssteephighspecificallytheheelinmonitoringgeometryprovidesFurthermore,awareness.themachineoutstandingboomandoptionalslopesystem.Availabletwoconfigurations,theliveshovelloggerboomanddirectionalfellerboomsaredesignedtoensureperformanceinchallengingslopeapplications.Thepowerful953MLprovideswitha36ftliveheelboomwith60incapacity.Withtheliveheelthereisimprovedcontrolthepositioningofthelogtimber-handlingoperations.keyfeatureisthelongwideundercarriage,combinedexcellentgroundclearanceproventractiveeffort,whichthemaneuverabilityflotationinsoft,swampy,andconditions.TheML-Seriesisequippedapowerful,efficientEPAFinalengine,andoffersconvenienttoservicecomponents
The 953ML purposebuilt shovel logger can effortlessly tackle swampy terrain while the 959ML leverages the best-in-class leveling control system designed specifically for steep slope operations Jim O’Halloran, John Deere Product Marketing Manager. which helps complete maintenance checks in a timely manner. Additionally, the series also comes with a variety of optional features such as a tether-ready hitch field kit, a slope monitoring system, and a four-point seat harness. John Deere 2656G
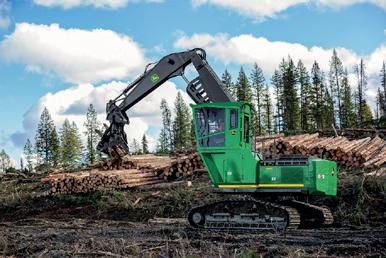

LeadingreductioncontrolledpowerfulaFAEmanufacturerhasunveiledsmalleryetstillremote-trackedcarrierforsizeefficiency
FAE is expanding the RCU series with the new RCU-75 model, a compact, professional and powerful, remote controlled tracked carrier. The RCU-75 is designed to work on hard-to-access areas and steeply sloping terrain that requires dedicated equipment to ensure operator safety and operating efficiency. It’s excellent for working in hilly wooded areas, near railroad tracks, power lines, gas and oil pipelines, gardens, roadsides, highways, canals, rivers andThelakes.new FAE tracked carrier is powered by the Kohler Common Rail electronic fuel injection engine – a compact, powerful and fuel-efficient 74 hp propulsion system that complies with the most stringent emission standards. The heavy-duty undercarriage features a hydraulic extendable & retractable independent track gauge system and an automatic tensioning system. Thanks to high profile rubber tracks – 86 mm pitch and 13 in width – oscillating rollers and triple-flange style idlers, it can operate in the strongest conditions. High-tech solutions give the RCU unbeatable traction, enabling it to work on steep slopes up to 55°. Moreover, the steel track undercarriage version provides great traction even on the most difficult terrains. A dual hydrostatic transmission provides better traction and optimal management of the FAE releases powerhouse RCU-75
attachment. Electronically controlled piston pumps combined with a dedicated electronic control unit provide an integrated technological system. The result is high performance and reliability that lasts, plus a simple and intuitive operation. The RCU-75 is guided by an ergonomic remote control with a large 3.5 in display for superior management of all vehicle and attachment functions and with customizable function keys. A 2.4 GHz transmission frequency ensures reliable communication. The layout of the controls, the wellbalanced shoulder straps support, make the FAE RCU remote control ergonomic and easy to use. The RCU-75 can be paired with the BL2/RCU mulcher, designed to mulch vegetation up to 6 in in diameter. This mulcher features a fixed tooth rotor and Bite Limiter technology that provides higher productivity with even less horsepower due to low power absorption.TheRCU range will be available in 2023.
46 International Forest Industries | AUGUST / SEPTEMBER 2022
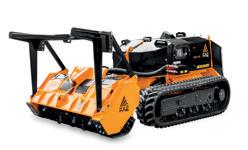
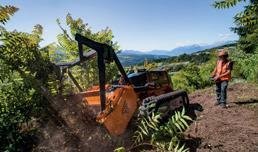
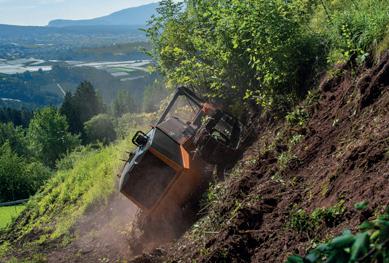

“The industry leaders who have recognised the potential of grapple carriages are seeing beneficial results in their operations, in addition to addressing the obvious safety concerns regarding the vulnerability of people working in dangerous situation,” says Dale Ewers, Owner of DC Equipment, which developed the highly successful Falcon Claw motorised grapple“Thesecarriage.include the solving of recruitment shortages for high-risk environments while increasing workflow and productivity on skid sites. We can’t pin the benefits to one or two points, more rather that crews are seeing an improvement across the wider harvesting process.“Tomake the best use of a motorised grapple carriage requires forward planning and that’s what we’ve aimed to cover in our new online guide. “Logging isn’t easy and there will always be challenges making a motorised grapple carriage work in certain settings, but there’s always a solution.“It’sknown in the industry that contractors have their own approach to how they’ll successfully harvest their blocks. They’ll know what has been working for them and the
challenges they have – we’re just being open and advising that in similar settings, we’ve had excellent results by utilising motorised grapple carriage combined with forward planning and accommodating the change in harvest“Howmethodology.weusedtolog 30 years ago and how we’re logging now has completely changed. How we log in the next 30 years will also be completely different, so being open to other harvesting strategies and improving current methods is a large component of increasing productivity.”Ewersaccepts that motorised grapples carriages are suited to shorter pulls and where there is good deflection, but he adds: “You’re not going to find the ideal setting every time, so you have to think more creatively. “For instance, with concave/ convex slopes you’re going to have a mixture of good and poor deflection, so when planning your setting it makes sense to identify a tree that can be used as a tail spar or maybe one that can be used as an intermediate spar to raise the height of the rope and keep the grapple carriage and wood off the ground. Or use a block to pull from a different direction to improve deflection.”Ewerssays the main reason he developed the Falcon range of motorised grapple carriages was for the safety of his employees – removing people from the dangerous task of hooking strops to trees on steep slopes is seen one of the most successful ways of preventing harm in the forest. But once they were introduced to his crews, they soon found there were numerous other advantages. For example, as yarder operators become experienced in using a motorised grapple carriage, cycle times will drop and logging operations become more productive.There’salso a misconception that motorised grapple carriages can only successfully be used with tower haulers and are not suited to swing yarders or yarder/ loaders, being too heavy and bulky, resulting in mechanical grapples being retained as the first option. However, new generation lightweight motorised grapple carriages that have been designed specifically for these types of yarders, are proving their worth in a variety of terrain, not just on steep slopes. These include environmentally sensitive areas in what would normally be a ground-based operation but where extracting trees or logs with skidders and forwarders will have a detrimental effect on the land or it’s just too difficult. Putting the tail hold on higher ground or using a tail spar to provide deflection keeps surface disturbance to a minimum.Andwith the latest high quality, durable cameras fitted to motorised grapple carriages providing the operator with a excellent view of felled trees on the ground, another bonus is that there’s no need for a spotter on the hill, as required with mechanical grapples.“Putsimply, if you are smart about the way you can make a motorised grapple carriage work in your crew, you’re going to be better off in a number of ways – operationally, financially, health and safety-wise and environmentally,” Ewers said.
The Falcon Claw is the logging industry’s most widely used Motorised, fully removed controlled, Grapple Carriage. This hydraulically operated grapple significantly reduces Health & Safety risks to crew members whilst increasing the efficiency of the log extraction process. With the 1750 model, which comes standard with the heavy-duty grapple, at an opening of 78” and has a payload of up to 17,500 lb, faster cycle times are a given.
Making full use of a motorised grapple carriage
International Forest Industries | AUGUST / SEPTEMBER 2022 47
Logging isn’t easy and there will always be challenges making a motorised grapple carriage work in certain settings, but there’s always a solution Dale Ewers, DC Equipment DC Equipment, a pioneer for the wide use of motorised grapple carriages more than a decade ago, produced an online guide to help foresters unlock their potential.
The difference in correctly using this technology can have a major impact on the bottom line Motorised grapple carriages seem to have been around for ages. When first introduced, they revolutionised the way many steep forests are harvested around the world. Yet, there is still some reluctance to use them in certain settings or at all.

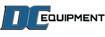


Japan CONTACT: Shigeru Kobayashi Japan Adver tising Communications, Inc. Star Bldg., 3-10-3 Kanda Jimbocho Chiyoda-ku, Tokyo 101-0051 Tel: 81-3-3261-4591 Fax: Email:81-3-3261-6126Shig-kobi@media-jac.co.jp
CONTACT: Bob Warren International Forest Industries Ltd Tel: +44 (0)1442 877 777 Fax: +44 (0)1442 870 617 Email: bob@internationalforestindustries.com Tel: +44 (0)1442 877 777 Fax: +44 (0)1442 870 617 Email: bob@internationalforestindustries.com
48 International Forest Industries | AUGUST / SEPTEMBER 2022 ADVERTISERS INDEX UK, Europe, South Africa, US East Coast CONTACT: Phil Playle International Forest Industries Ltd Tel: +44 (0)1442 877 777 Fax: +44 (0)1442 870 617 Email: phil@internationalforestindustries com
Western USA (AZ, C A, NV, UT) Australia, & New Zealand
USA Tel: +1 (630) 420 9752 Fax: +1 (630) 420 9763 Email: lapham@jpmediainc.com South America AEditecCONTACT:S.A.vdadelCóndor 844 Of. 205, Cuidad EmpresarialHuechuraba, Santiago, Chile Tel: +56 2 757 4200 Fax: +56 2 757 4201 Email: editec@editec.cl SALES OFFICES Autolog . . . . . . . . . . . . . . . . . . . . . . 21 www.autolog.com ASTEC IFC www.astecindustries.com Bid Group . . . . . . . . . . . . . . . . . . . . 17 www.bidgroup.ca CLEANFIX 31 www.cleanfix.org Franzen . . . . . . . . . . . . . . . . . . . . . . . 2 www.franzen-machines.com Halco Software Systems . . . . . . . . 27 www.halcosoftware.com Jenz 13 www.jenz.de John Deere . . . . . . . . . . . . . . . . . . . . . 7 www.JohnDeere.co.uk Joescan . . . . . . . . . . . . . . . . . . . . . . . 18 www.joescan.com Komatsu . . . . . . . . . . . . . . . . . . . . . . . 9 www.komatsuforest.com Komptech . . . . . . . . . . . . . . . . . . . . . . 8 www.komptech.com Microtec . . . . . . . . . . . . . . . . . . . . . . . . 3 www.microtec.eu Morbark . . . . . . . . . . . . . . . . . . . . . . . . 11 www.morbark.com Opticom . . . . . . . . . . . . . . . . . . . . . . . 29 www.opticomtech.com Panolin 15 www.panolinamerica.com Ponsse . . . . . . . . . . . . . . . . . . . . . . . . . 5 www.ponsse.com Rawlings . . . . . . . . . . . . . . . . . . . . . . . 37 www.wastewoodhogs.com Seppi m. . . . . . . . . . . . . . . . . . . . . . . . 14 www.seppi.com Southern Forest Products Association . . OBC www.SFPAEXPO.com Springer . . . . . . . . . . . . . . . . . . . . . . . 19 www.springer.eu Timber Processing and Energy Expo . 23/24/25 www.timberprocessingandenergyexpo.com USNR. . . . . . . . . . . . . . . . . . . . . . . . . F/C www.usnr.com
CONTACT: Kevin Lapham J.P.Media Inc 1163 E.Ogden Ave, Ste. 705-359 Naper ville I L 60563, Continued from p10 we have a very good experience working with Brazilian and Chilean companies that are open to adopt new innovative technologies in their operations. Thanks to Timbeter they are benefiting from higher efficiency, transparency and accurate digital data. Our goal is to contribute to sustainable forest management as much as possible. The need for green digital transformation in the public sector is also an important step for the Brazilian government towards innovation and development plans to reach the climate goals. Timbeter’s goal is the cooperation with different agencies in order to use the digital transformation for implementing sustainable forestry practice – efficient use of natural resources, better overview, monitoring and control against illegal logging activities. Furthermore, we see a lot of interest from the Brazilian side towards the e-Estonian experience in regard to digital transformation so hopefully we can help to intermediate cooperation, knowledge-sharing and capacity building between the two countries. Timbeter is also partnering with academic institutions in Brazil like Universidade de São Paulo, UFRRJ, Universidade Federal de Santa Catarina to contribute to the education of the future foresters. New office in Brazil enables closer cooperation with clients and partners in the region. About Timbeter Timbeter provides accurate AI measurement and data management solution for transforming forestry. Timbeter’s digital solution is changing the forestry sector by enabling sustainable forest management, increasing the safety of employees, maximizing the value of each log, helping to optimize logistics and guaranteeing fair trades. Also, it helps with monitoring and controlling the timber supply chain, supporting governments and law enforcement agencies to prevent illegal logging and keep a better overview on the volumes harvested.
US Mid-West, Central & Mountain
CONTACT: Bob Warren International Forest Industries Ltd Western USA (MT, ID, OR,WA) & Canada
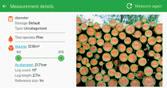
RK75
Tobias Johansson, CEO of Rottne Industri AB. moved at the driver’s command (out, in, up and down) and the system runs the extension automatically.Withthelaunch of the Rottne H8E, Rottne Industri is now taking another step forward in the development of flexible forest machines for efficient thinning work.We can proudly launch our first machine with a boom control developed here at Rottne. This, together with other improvements, strengthens our leading position in sustainable thinning for professional forestry, says Tobias Johansson, CEO of Rottne Industri AB.Demand for boom control for more of Rottne’s machine models is high and the company’s developers are constantly working on this. For the newly launched Rottne H8E, it will be available from April.
• Dynamic speed during crane slewing.
• Updated extension profiles and slide pads.
International Forest Industries | AUGUST / SEPTEMBER 2022 IBC
• Higher lifting height.
AB
• Rotator H101, also on the Log Max.
Rottne Industri AB launches the Rottne H8[E] – a new generation for stand-operating thinning Rottne Industri AB launches Rottne H8E – a significant upgrade of the predecessorpopularRottneH8D.
• New slewing house with many improvements, including roller bearing on crane slewing ring.
• Greater slewing angle.
• Improved hose and pipe routing, central lubrication, and crane geometry.
• Improved service accessibility.
• Improved control of the crane tip.
• Dynamic speed during crane lowering.
• Increased gross lifting torque (90kNm).
Mathias Systems,EngineerPaulsson,oftheControlRottneIndustri
The first machine from the upgraded series of the Rottne H8E has just left the production facilities at Rottne. More machines are in the production line now. On the outside, Rottne H8E looks almost like Rottne H8D, but on the inside there are a lot of improvements and a lot of new and advanced technology, says Mathias Paulsson, Engineer of the Control Systems at Rottne Industri AB. The crane, with all its mechanical upgrades, makes the big difference and it was when we developed it, we have seen the opportunity to upgrade the entire machine.RK50 has been around since the beginning of the 2000s. Now it will be replaced by RK75 with a lot of improvements and innovations. In short, all the benefits of the older crane have been retained and more advantages have been added. Everything from hardware to software has been reviewed in detail in order to produce a crane that will make both the work and the service easier. The new crane has a completely new turntable that makes it more efficient with better durability and reliability. Compared to its predecessor, the crane has been improved in all respects, which makes it stronger and with higher lifting power, says Mathias Paulsson.Among other things, it has a built-in position sensor in all cylinders that the control system recognizes. The boom control is
The versatile harvester has been updated on several points and will be equipped with the new and stronger crane, RK75, and have optional boom control.
• Increased torque (20kNm).
• End-position damping on lift and outer cylinders as well as crane slewing.
• Crane position direct to StanFord data.
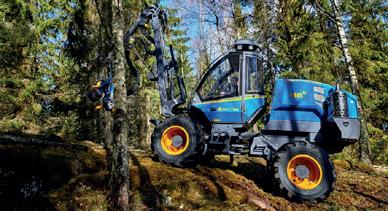


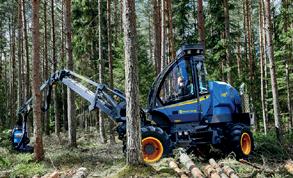
Reconnect with the entire wood products manufacturing SAVENOWcommunity.DATETHEVisitSFPAEXPO.comToday!August 23-25, 2023 • Music City Center • Nashville, Tennessee Bringing the sawmill industry together for more than 70 years, the Forest Products Machinery & Equipment Exposition is a major event featuring equipment and services for both hardwood and softwood sawmills.
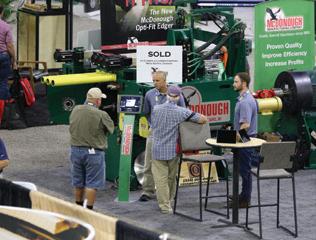
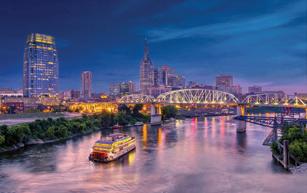
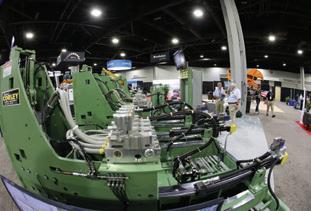

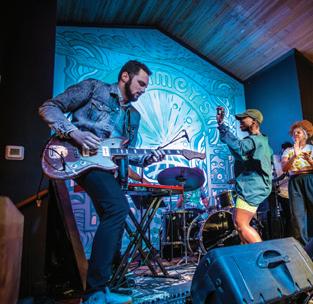
