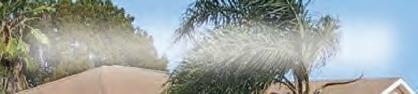
6 minute read
Benefits of Using Live-Bottom Trailers to Haul Asphalt
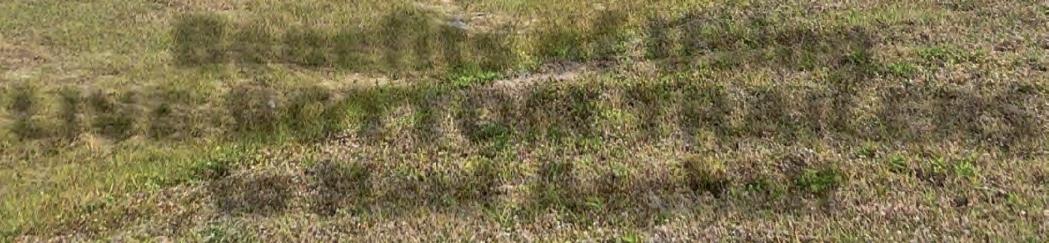
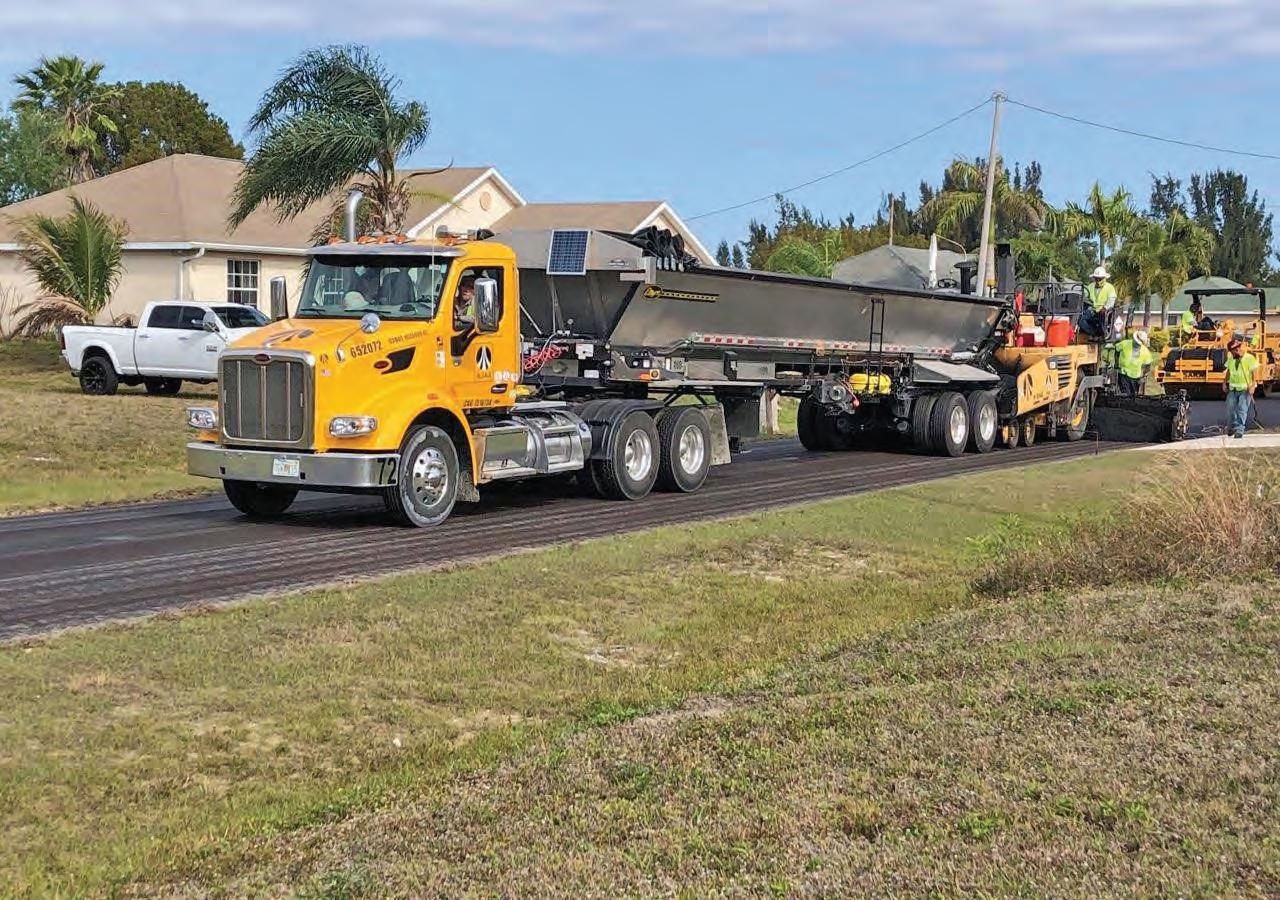
These trailers can increase safety, decrease unloading times and improve operations for paving contractors
LIVE-BOTTOM TRAILERS are not new to the asphalt hauling industry. In fact, these V-shaped units have been used to transport asphalt and other materials for years. But their popularity is increasing in many areas due to the benefits they can offer.
A typical live-bottom trailer has a conveyor belt on the bottom of the tub that pushes the material out of the back of the trailer at a controlled pace. Unlike the conventional dump trailer, the tub does not have to be raised to deposit the materials. "Live-bottom trailers are different than a dump trailer in that they unload through a conveyor system in the bottom of the trailer," Larry McGee, president of Pegasus Trailers, says. "Not raising the bed to unload material has many advantages for both trailer drivers and paving contractors, including increased productivity, a better quality mat and the biggest advantage is safety."
Productivity Enhancer
When it comes to profitability of asphalt paving jobs, every minute saved matters. Live-bottom trailers can help the paving train be more productive by allowing crews to lay more material faster, get the job done quicker and move on to another project. "Conventional end and side dump trailers require that the load bin/box be hydraulically hoisted upwards or sideways at an angle so the material can slide out. The unloading speed is somewhat unpredictable and is typically uncontrollable," notes Richard Minotti, district sales manager, Trail King. "Live-bottom trailers remain horizontal during the unloading process. The flow of material is always predictable and controllable."
This allows for steady loading, which results in more efficient removal of material from the truck.

Live-bottom trailers remain horizontal during the unloading process. The flow of material is always predictable and controllable.
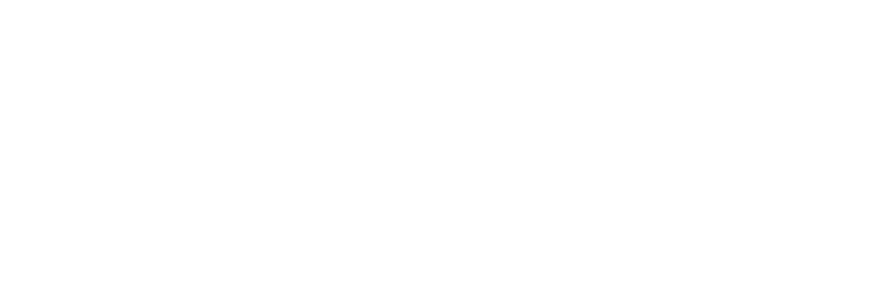
"That's a big advantage, being able to unload faster," adds Brian Horner, Etnyre Trailers. "Let's say you have a paving crew and you have 15 dump trucks that are running to that paver. You could get by with probably 12 belt trailers instead of 15 trucks and get the same capacity in a day."
For this reason, many drivers of livebottom trailers get better hourly rates than typical dump drivers.
Having predictable control over the materials also means that the paving contractor can better plan for putting material down and potentially have less stoppages to wait for a dump trailer to raise and unload. "With a live-bottom, you can turn the conveyor on at the same speed that the paver is feeding and you can unload your load without a stop," McGee points out. "That makes the whole paving train cover more ground in a day because you're not waiting for a body to go up and down."
The other benefit is being able to maneuver the trailer in tighter areas since there is no dump to get in the way. "You never have to body up and down to go under bridges or wires," McGee comments. "As soon as the [trailer] backs into the paver, it can go under anything without stopping. If you're working in town, that makes a big difference. Your productivity is so much higher with a live-bottom."
These trailers are also suited for wind-up work or smaller jobs, as you can meter out just a little bit of mix at a time and move the trailer to another location to unload more mix. "A lot of guys will have to use a skid loader to fill in some corners or something on smaller jobs," Horner notes. "With a live-bottom, you can meter out just a little bit below a skid loader bucket, close the doors, let him do his thing and come back. You're not dumping a big pile somewhere and making a mess that you have to clean up. So, it makes it very good for that wind-up work."
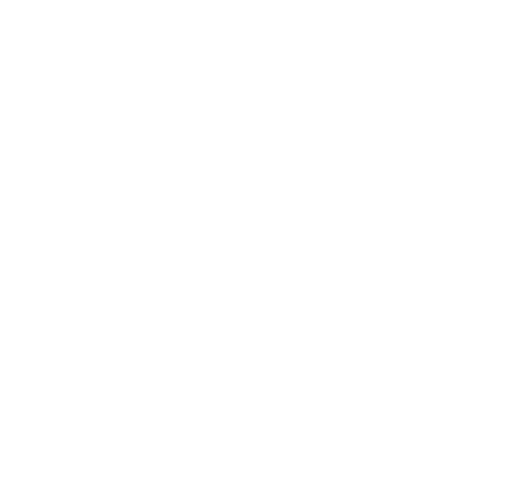
Maintenance Matters
Live-bottom trailers do require a bit of additional maintenance than traditional dump beds, but not nearly enough to deter use.
“You need to make sure you’re checking that the flashing is where it needs to be and always make sure your belt and your chains are tensioned correctly,” says Brian Horner, Etnyre Trailers. “Make sure you keep them tight.”
Loading unreliable mixes or damaging materials could damage the conveyor so be aware of that, as well.
“These trailers also do not typically lend themselves to excavation and extraction of product. Sticky clay could cause problematic unloading, and a rough unpredictable product mix could damage the conveyor belt (i.e. tree stumps, concrete with rebar, etc.),” Trail King’s Richard Minotti says.
Better Results
Because the load of hot mix is continually moving through a live-bottom trailer via a conveyor belt, and not being unloaded in lumps, aggregate and heat segregation are dramatically reduced, which improves mat quality. "The whole load moves back and then dumps out the bottom. It's never tumbling in there, so there's less segregation of your asphalt," Horner
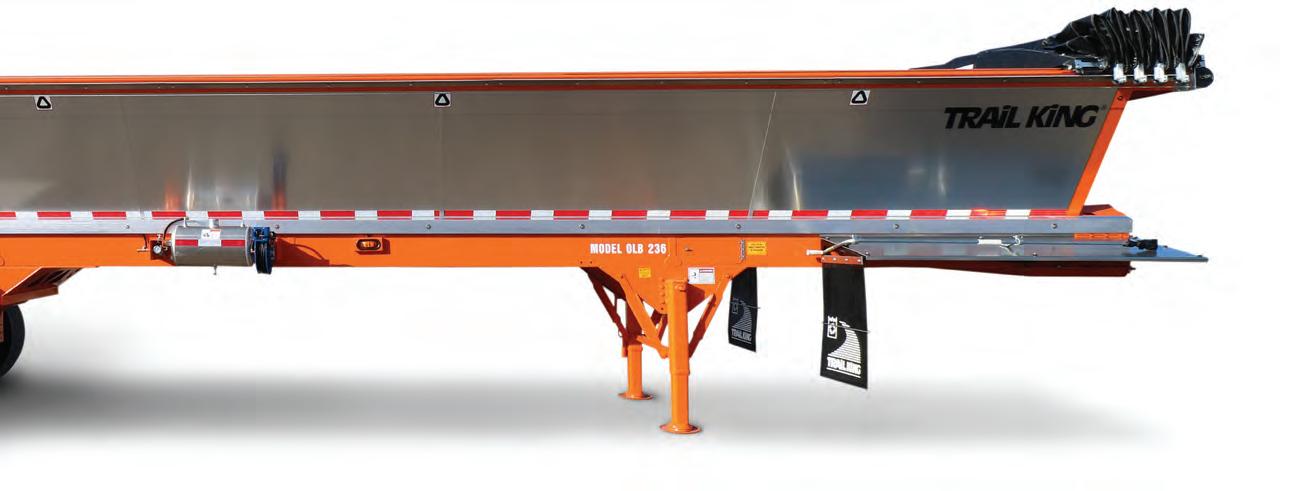
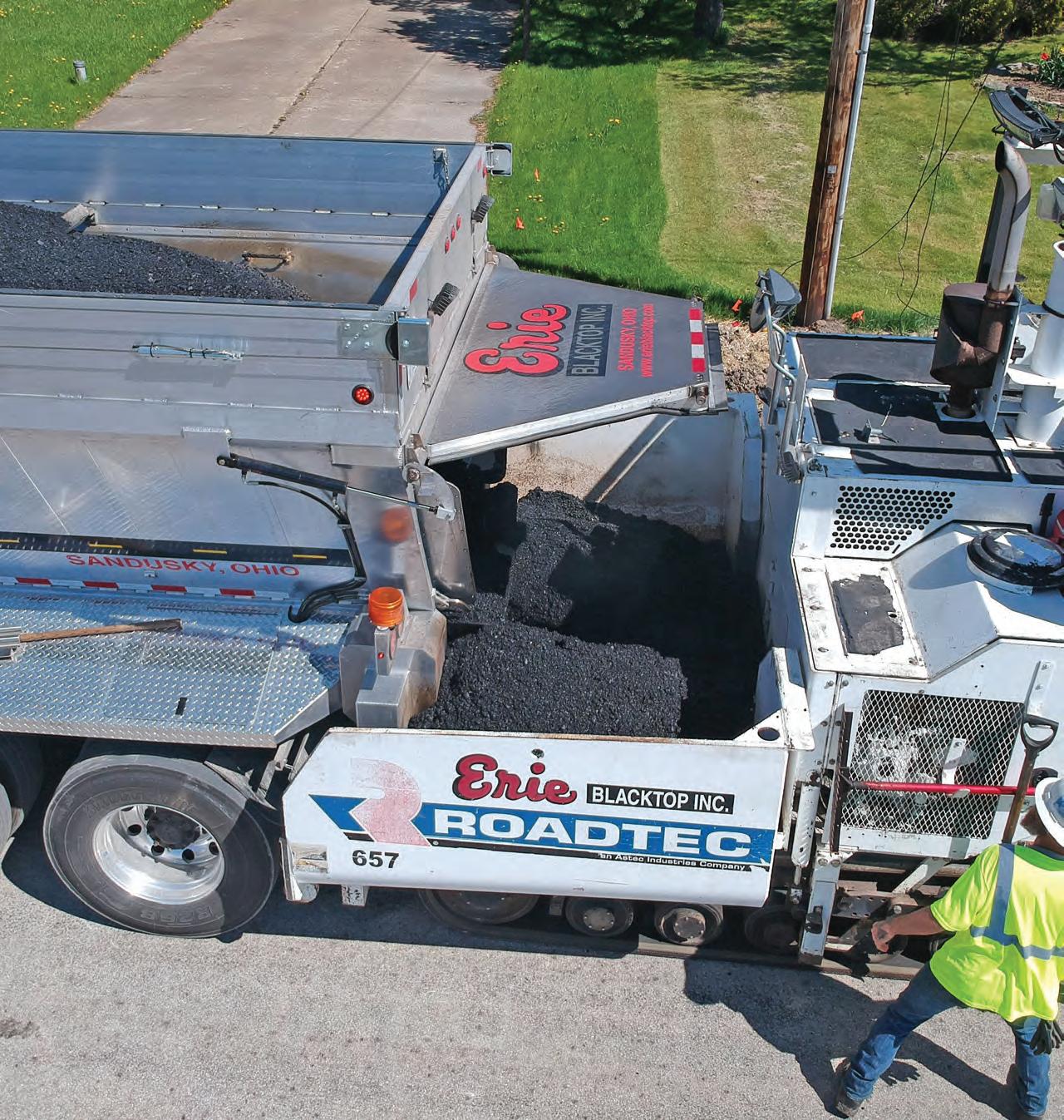
says. "Really, that whole load, in a half a revolution of that belt, empties the trailer. The belt is not just sitting in there spinning. It's moving slow and just moves that whole big mass out to the back of the trailer and dumps it into your paver."
Stopping the paver to wait for mix inevitably creates a small bump in the mat. This can usually be avoided with live-bottom trailers. "With live-bottoms, you don't get the surge in the paver when the trailer backs into the paver, which bumps the screed," McGee says. "You can trickle mix into the paver at the same rate that the paver is trickling it back to get in front of the screed. That helps with mat quality, too." "Another benefit that is inherent to live-bottom trailers is that they have better thermal retention properties than conventional end dumps," Minotti says. "They keep hot mix product (asphalt) hotter longer."
Safer Unloading
One of the largest reasons the industry is seeing a shift to live-bottom trailers is due to the increased safety these trucks bring to a jobsite. Because they
Live-bottom trailers are well-suited for residential areas or where overhead obstructions are an issue as the dump does not need to raise up to empty the material. This improves safety and productivity. don't lift to empty the material, not only are they ideal for tight situations like under bridges and in residential neighborhoods, it also means there is no risk of the truck rolling over when the dump is raised. "Conventional dump trailers are very unstable during the unloading process and are extremely susceptible to rolling over," says Minotti. "Live-bottom trailers are ultra-stable as their center of gravity is never shifted during the unloading process. They are by far the best, safest choice for worksites."
As the number of trucks on site increases, so do the chances of an accident occurring. Many insurance companies are realizing the risk of dump trailers and either refusing to ensure them or charging higher rates. "I've had some customers tell me that their insurance companies didn't want to cover their dump trucks anymore because of roll overs that they had, so they ended up purchasing some live-bottom trailers," McGee states. "We have also seen some dump trucks go into wires and had electricity jump from wires to the box and [electrify] the truck. They could have had a really bad accident and luckily no one died, but I know other companies have had fatalities from electrocution from the dump trucks being up in the wires. So, live-bottoms are a lot safer. No rollovers and no wires."
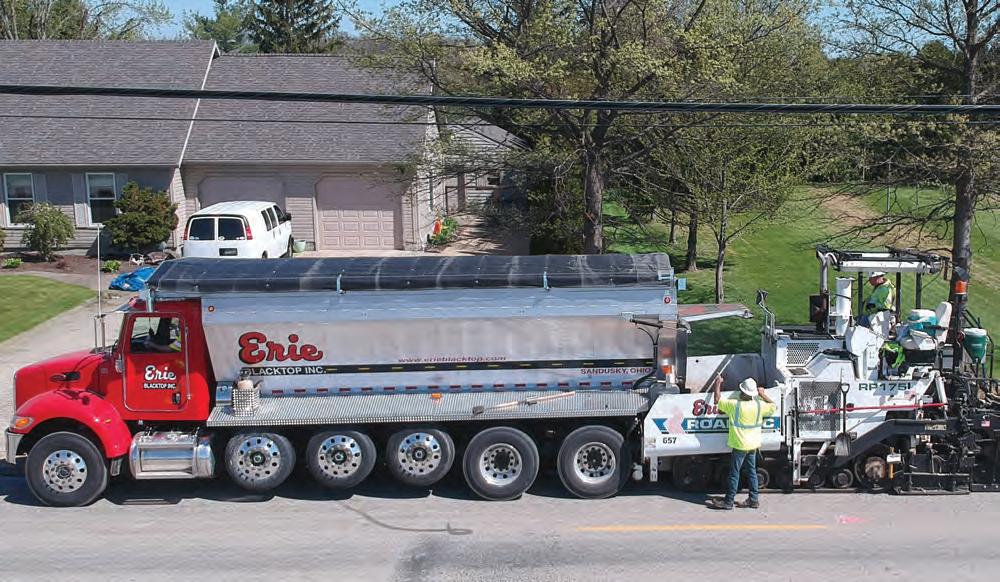