
27 minute read
Excavator Attachments
Brandt Pin Grabber Coupler
A dedicated pin grabber coupler has been added to the Hard-To-The-Core John Deere-optimized attachment lineup.
•Features a rear wedge to keep the rear pin secured without relying on gravity •Internal safety lock is spring-engaged and hydraulically released to keep the rear wedge in place, securing the pin •Hydraulic interlock requires the coupler to be fully curled toward the cab in order to be disengaged to prevent accidental attachment drops •Hydraulic check valve maintains pressure in cylinders in the event of hydraulic hose breakage until proper function is restored •Works with all Deere excavator models from the 80-Series to 400-Series www.forconstructionpros.com/21427390
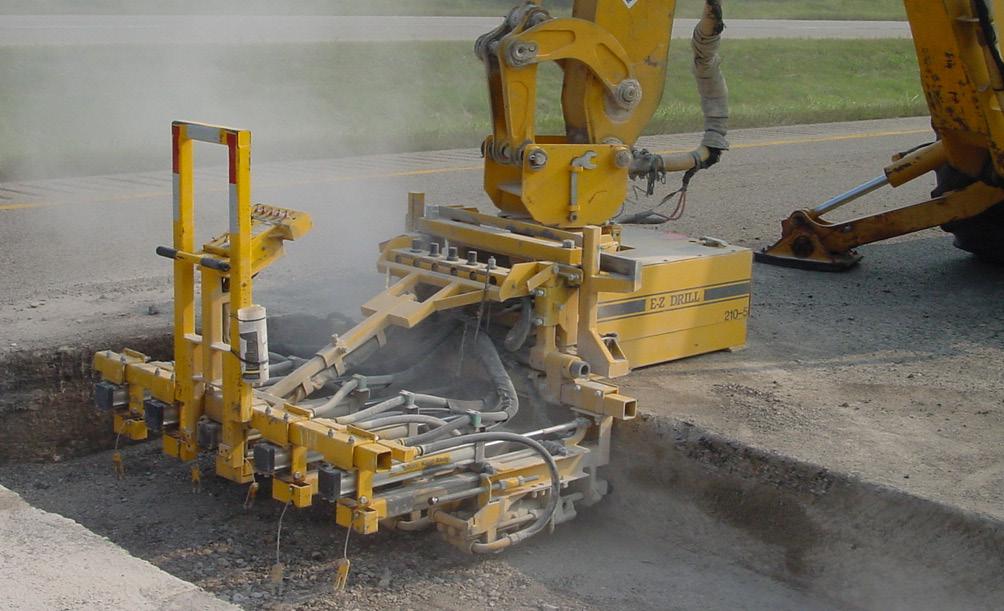
E-Z Drill 210 Series Concrete Drill Attachments
This equipment-mounted, pneumatic concrete drill attachment series includes the three-gang Model 210-3 EQ MT, four-gang Model 210-4 EQ MT and fivegang Model 210-5 EQ MT.
•Compatible with most models of backhoes and excavators •Capable of drilling 5/8- to 2 1/2-in.diameter holes at a depth of 18 in. •Each drill motor requires a minimum of 100 cfm for operation •Minimum of 300 cfm required to power the Model 210-3 EQ MT •User-friendly, easily accessible control panel mounted on drill www.forconstructionpros.com/10278334

Vacuworx Updated RC Series Vacuum Lifting Machines
The RC10, RC12, RC16 and RC20 can grip up to 120-ft. triple pipe joints and hold the shape of limber pipes and long joints of flexible plastic pipe.
•Single-cylinder diesel engine powers the rotary vane pumps on each attachment •Include an electronic ignition, remote operating control and a vacuum reservoir beam that doubles as a spreader bar •Control and alarm systems activate audio and visual warnings and prevent further lifts if the vacuum falls below a safe working level •Vacuum storage reservoir allows materials to be held for 15 minutes or more under no power www.forconstructionpros.com/10417599
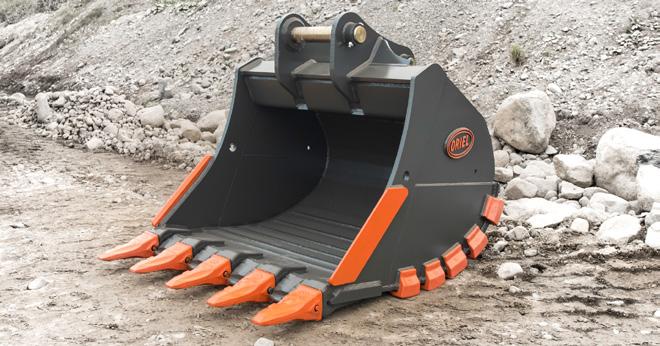
Oriel Attachments Heavy-duty Excavator Buckets
These buckets are built for heavy-duty applications with a main body built using AR 450 wear-resistant steel in all critical areas.
•Designed to maximize capacity and reduce drag, extending bucket life •Folded top section gives greater structural strength and allows a greater opening for ease of loading and unloading material •Available in a range of widths and capacities for excavators from 4,500 to 112,000 lbs. •Manufactured to the relevant safety standards with high-strength steels for optimal quality and performance www.forconstructionpros.com/21244748
Rockwater CB Hydraulic Breakers
CB Breakers are available for excavators, backhoes and skid steers ranging from .8 to 55 tons.
•Compact, lightweight range for compact excavators and skid steers includes a unique valve system and plumbing design that provide power and efficiency while requiring less oil flow •Medium range for backhoes and excavators offers power and versatility for working with a wide range of operating pressures and oil flows •Heavy-duty range for excavators beyond 20 tons are fully box framed with damping materials to reduce noise and recoils to the carrier, and come pre-installed with an auto grease system www.forconstructionpros.com/21070427


Allied Rammer Small Range Breakers
The 555, 777 and 999 Rammer small range breakers are designed without tierods and incorporate the Constant Blow
Energy (CBE) plus operating system. •For carriers between 7,500 to 27,600 lbs. •Integrated one-piece tool bushing design requires fewer parts and is easily field replaceable •Box-type housing with high-tech dampening material reduces noise and vibration and fully protects the power cell •Dual accumulator (High Pressure and Low Pressure) design provides maximum power with less pulsation in hydraulic lines www.forconstructionpros.com/12138533

Montabert V7000 Breaker
The V7000 fits in the 20,000-ft.-lb. impact energy class and is suited for carriers ranging from 70 to 120 tons.
•Variable energy technology automatically adapts breaker energy according to the rock/material hardness •Automatic pressure regulator ensures optimal performance regardless of oil temperature or hydraulic conditions •Energy recovery valve captures recoil and converts it back into additional energy •Suspension system reduces vibration and wear •Includes blank fire protection, an automatic lubrication system and optional air pressurization kit for underwater applications www.forconstructionpros.com/21131861

Okada TSWB Series Primary Crusher
The TSWB concrete crushers include eight models weighing from 1,940 to 26,460 lbs. and suited for carriers from 13 to 330 tons.
•Crushing force at tip ranges from 40 tons for the 620V to 242 tons for the 2400V •Seamless casting components and a custom tooth design enable faster material fractioning •Feature a large jaw opening, 360° hydraulic rotation, standard speed valve for shorter cycle times, built-in pressure relief valve and flat-mount design •High-pressure twin cylinders with cylinder rod covers (except TSWB 2200V) www.forconstructionpros.com/21131869
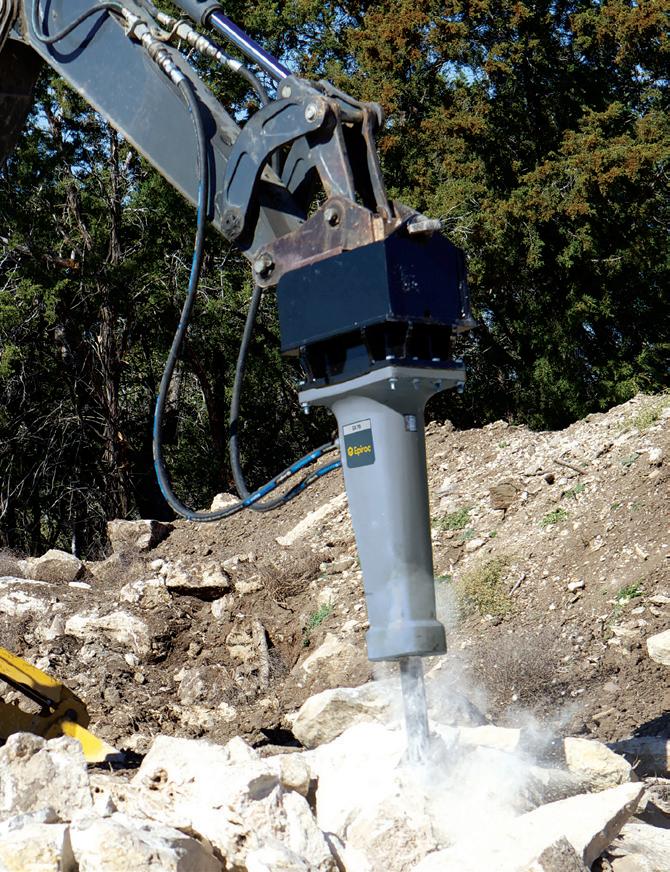
Epiroc ES Hydraulic Breakers
The ES hydraulic breaker attachments include the ES 60, ES 70 and ES 80 models for carriers ranging from 2,800 to 26,500 lbs.
•Slim, compact design provides easy handling, good visibility and high maneuverability •Solid block of special casted material eliminates need for a separate guiding system, tie-rods or stud bolts •Removable piston liner increases serviceability •Integrated control valve optimizes efficiency while the Energy Recovery system increases operating efficiency and lowers vibrations www.forconstructionpros.com/21201287
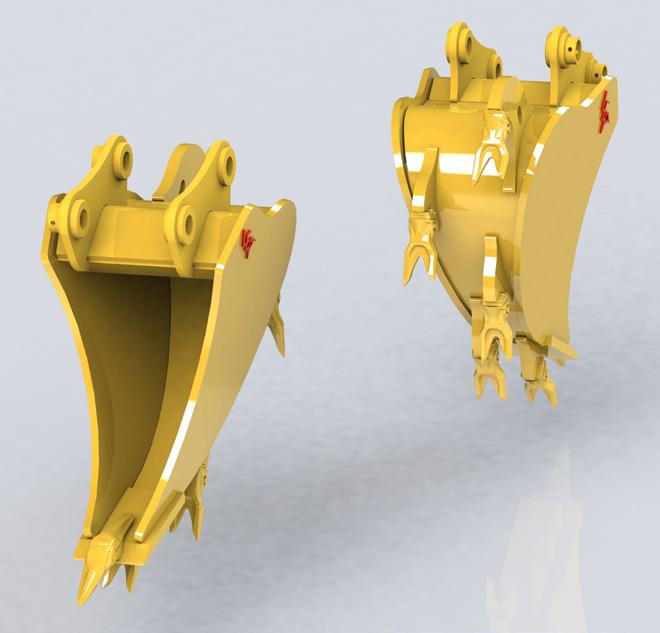
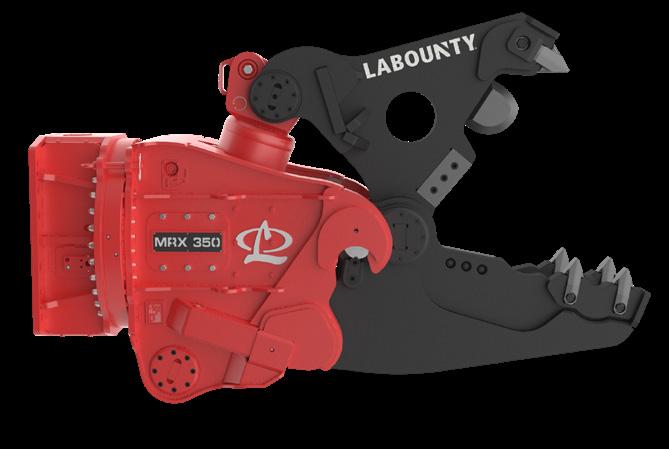
Leading Edge Multi-DigNRip V-Raptor Bucket
The Multi-DigNRip V-Raptor Bucket features a ripper/bucket combination for excavators and backhoes.
•Can be used to rip rock, coral or frozen ground, pry out and carry stumps and cradle boulders •Rip a clean narrow V trench for utilities •Scoop and load material •Manufactured with high-strength Swedish Hardox 400 alloy steel •Available for any backhoe, mini-excavator or excavator weighing over 6,000 lbs. www.forconstructionpros.com/21106160
Stanley LaBounty Multi-Jaw and Mobile Rotation Pulverizer
The LaBounty Multi-Jaw Demolition Tool (MRX) has 360˚ rotation and can be used for primary and secondary demolition and off-site concrete processing, while the Mobile Rotation Pulverizer (MRP) has a dedicated concrete pulverizer jaw.
•Short center of gravity •Interchangeable jaw with options for a concrete pulverizer, concrete cracker or shear •Open lower jaw improves penetration and rapidly downsizes material •Dual rotation motors with optimal holding power and durability •Replaceable wear areas www.forconstructionpros.com/21111022
Loftness Battle Ax Excavator Mulching Attachment
The Battle Ax for 4.5- to 20-ton excavators has a rotor with unique depth gauges to maximize the productivity of both knives and carbide cutting teeth.
•Two-stage cutting chamber capable of processing material more thoroughly by cutting material twice •Powerful direct drive with a variable displacement piston motor capable of turning the rotor between 1,600 and 2,500 rpm •Staggered spiral tooth pattern with singlebolt tooth mounting for easily reversing or replacing cutting teeth on the jobsite •Adjustable skid shoes for cutting up to 1.5 in. below grade www.forconstructionpros.com/20862622
Minnich A3/A6 Dowel Pin Drills
The A3/A6 pneumatically powered, machine-mounted drills can be mounted to an excavator, backhoe or skid-steer loader to form a self-contained and highly mobile drilling solution for full-depth repair.
•Feature up to six drills •Carrier used to transport the drill, eliminating operator fatigue and improving safety •Available side-shift functionality enables operators to drill a second set of holes without having to reposition the carrier •Optional dust collection system available www.forconstructionpros.com/20861565
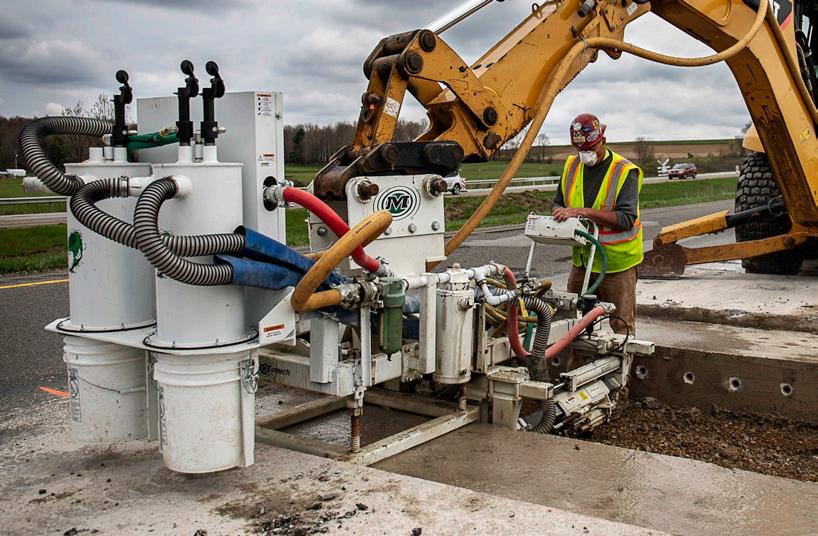
#1 Contractor’s Choice for Mechanized Cutting Solutions!
TRENCHING, DEMOLITION, ROCK EXCAVATION, SOIL MIXING and more
ROCK AND CONCRETE GRINDERS ROCK TRENCHING ATTACHMENTS
www.antraquip.net info@antraquip.net For Additional Information Call 301-665-1165
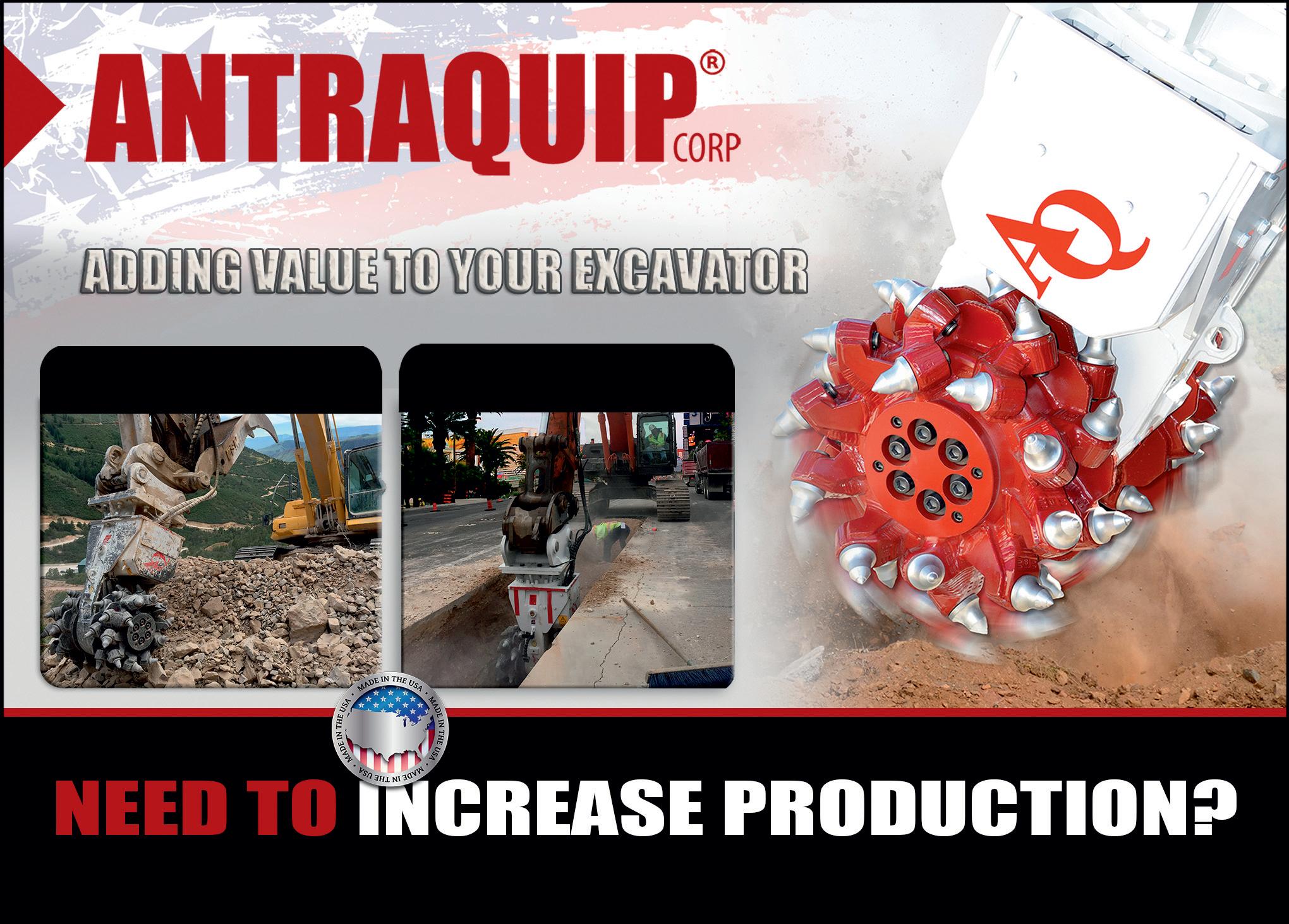
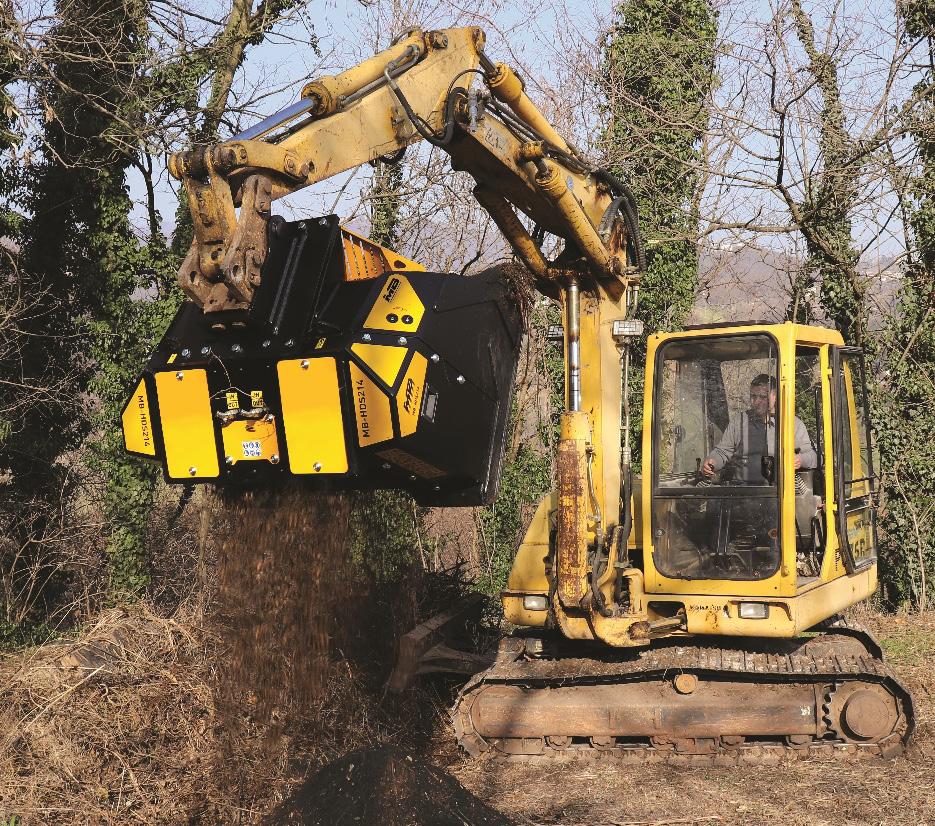
MB Crushers MB-HDS Series Shafts Screeners
The MB-HDS Series Shafts Screeners offer four shaft kits (RC Compost, RM Mixer, RE8/RE16 fine crusher and RQ20/RQ50 medium crusher kits) that enable them to adapt to a range of environments and material types.
•Can crush excavation and demolition materials, asphalt, coal, organic materials, wood, bark and light plastics, plus enable products to be immediately re-purposed •Can be installed on excavators, loaders and other carriers from 5 to 35 tonnes •Automated shock-absorbing hydraulic system reduces material discharge •Rotating shafts can be changed on site and include a centralized greasing system www.forconstructionpros.com/21063572
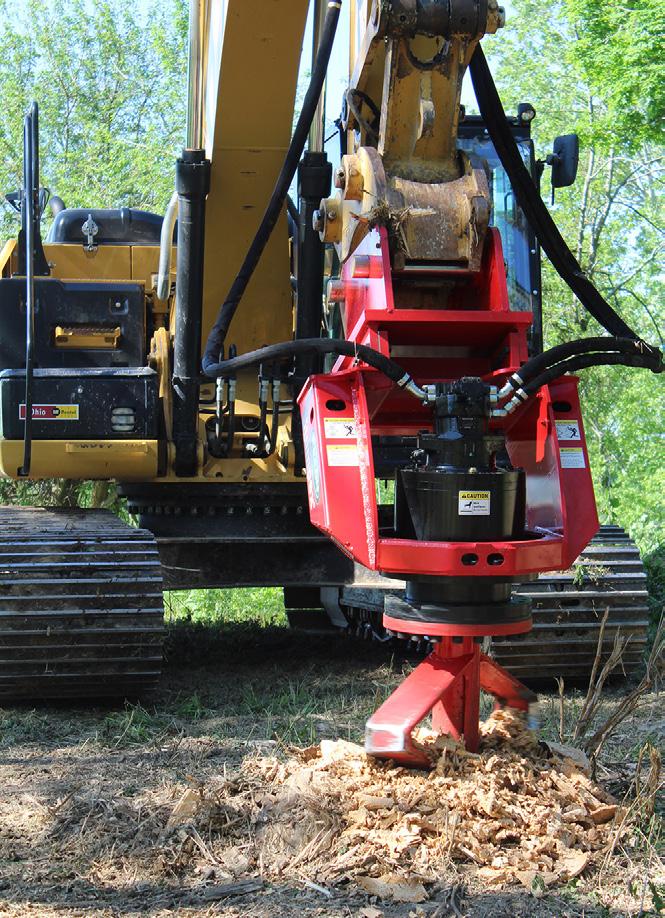
Fecon Stumpex EXC Stump Grinder
The Stumpex EXC low-speed, hightorque auger-type stump grinder attachment is suited for excavators from 12 to 20 tons.
•Can cut any species of stump from 10 to 28 in. in diameter in a single pass, with larger diameter stumps eradicated with multiple plunges •Cutting depth to 20 in. •Operates at 7 to 17 rpm •Threaded replaceable cone and staggered AR500 cutting blades grind out stump and root material with minimal discharge •Low-maintenance design www.forconstructionpros.com/21139763
Bobcat Large Excavator Thumbs
Large excavator attachments include the HT Thumbs (main pin) and Pro-Link Thumbs paired specifically with the E145 and E165 large excavators.
•HT thumbs use a hydraulic cylinder to provide up to 137° of rotation, are compatible with 36- and 42-in. buckets and are suited for demolition and land clearing applications •Progressive link units have up to 180° of rotation, follow bucket throughout the work cycle for improved material pickup and placement close to machine and are compatible with 36- and 42-in. buckets www.forconstructionpros.com/21204864

Auger Torque Variable Mulchers
This line of variable mulcher attachments enables excavators and skid-steer loaders to tackle overgrown ditches, low-level vegetation or whole tree removal.
•Working widths of 40 or 60 in. •Provide capability of changing the whole tooth drum instead of individual teeth •Hinged cover helps to contain debris and allows easy access to the tooth drum •Robust motor and gearbox conceal gears and bearings to prevent dust/dirt ingress •Low-profile design for enhanced visibility www.forconstructionpros.com/21070419


Alpine Rockwheel Rock and Concrete Grinders
The Rockwheel rock and concrete grinders incorporate hydraulic rotary cutting technology that delivers the power and precision to make efficient, low-vibration, low-noise excavations for any application.
•Models available from 12 to 295 hp for carriers from 1 to 75+ tons •Cutting force from 949 to 32,360 lbs. with cutting widths from 11.8 to 49 in. •Chain drive, gear drive, direct drive and axial drive versions www.forconstructionpros.com/12026954
The Slab Crab is used to remove concrete slabs and bridge decks and can accommodate slabs ranging from 4 to 19 in. thick.
•Available for excavators from 5,000 to 150,000 lbs., as well as models sized to fit backhoe-loaders •Serrated teeth line the upper jaws to prevent slabs from sliding •Smooth lower jaw allows operator to release the slab in the desired location •Available as a direct pin-on or to attach with the WedgeBolt Coupler System •Custom models can be fabricated to accept larger slab thicknesses www.forconstructionpros.com/21110190
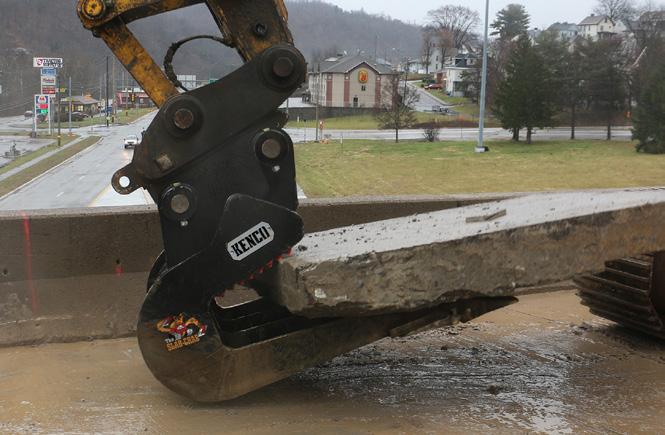
Caldwell Multi-Grapple Lifting System
The multi-grapple lifting system is suited to use in any environment where handling of irregular-shaped or inconsistent loads is required.
•Come in 3,000- to 12,000-lb. standard capacities with custom models available •Three arms provide a stable lift of irregularly shaped heavy debris •Centermounted actuator locks open grappler arms with automatic latching •Can work with a crane hook but is more commonly used with equipment such as excavators and backhoes www.forconstructionpros.com/21067900
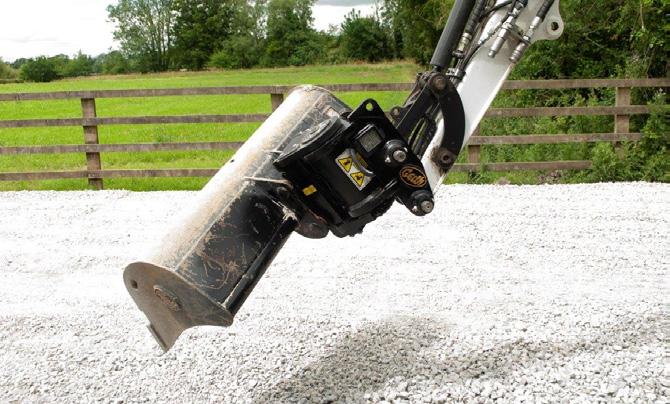
Geith Tilting (GT) Quick Coupler
The GT quick coupler is available for 2- to 27-ton excavators, and allows operators to tilt any bucket or attachment up to 180°.
•Variable pin center design allows operators to easily pick up and swap a range of OEM attachments •Can reverse buckets to allow the operator to excavate against walls and under pipes •Durable, compact design minimizes the tip radius extension •Allows for more control of attachments with minimal drift so operator can easily achieve different angles and positions www.forconstructionpros.com/21174227

Antraquip Rockwheel Attachments
Carbide rockwheels and diamond saw attachments are available for excavators of all sizes and various applications.
•Carbide rockwheels offer a cutting solution for soft to medium hard rock and concrete cutting applications with a minimum width of roughly 2 in. •Diamond saw rock wheels (AQD Series) cut the hardest rock including granite, basalt, etc., as well as reinforced concrete www.forconstructionpros.com/21045623
Steelwrist TCX Tilt Coupler and S30 Quick Coupler
The fully casted TCX S30-180 and S30-180 are suited for miniexcavators up to 2 tons and can be delivered with manual or hydraulic locking.
•Front Pin Safety Hook •Free from welding and have large pin contact surfaces and optimized material thickness for a robust design •Lightweight TCX S30-180 is easy to install and available direct mounted with the S30 coupler (manual and hydraulic) www.forconstructionpros.com/21197523
Don’t Let Brakes Slow Productivity
Maintain air brake systems to keep your trucks rolling.
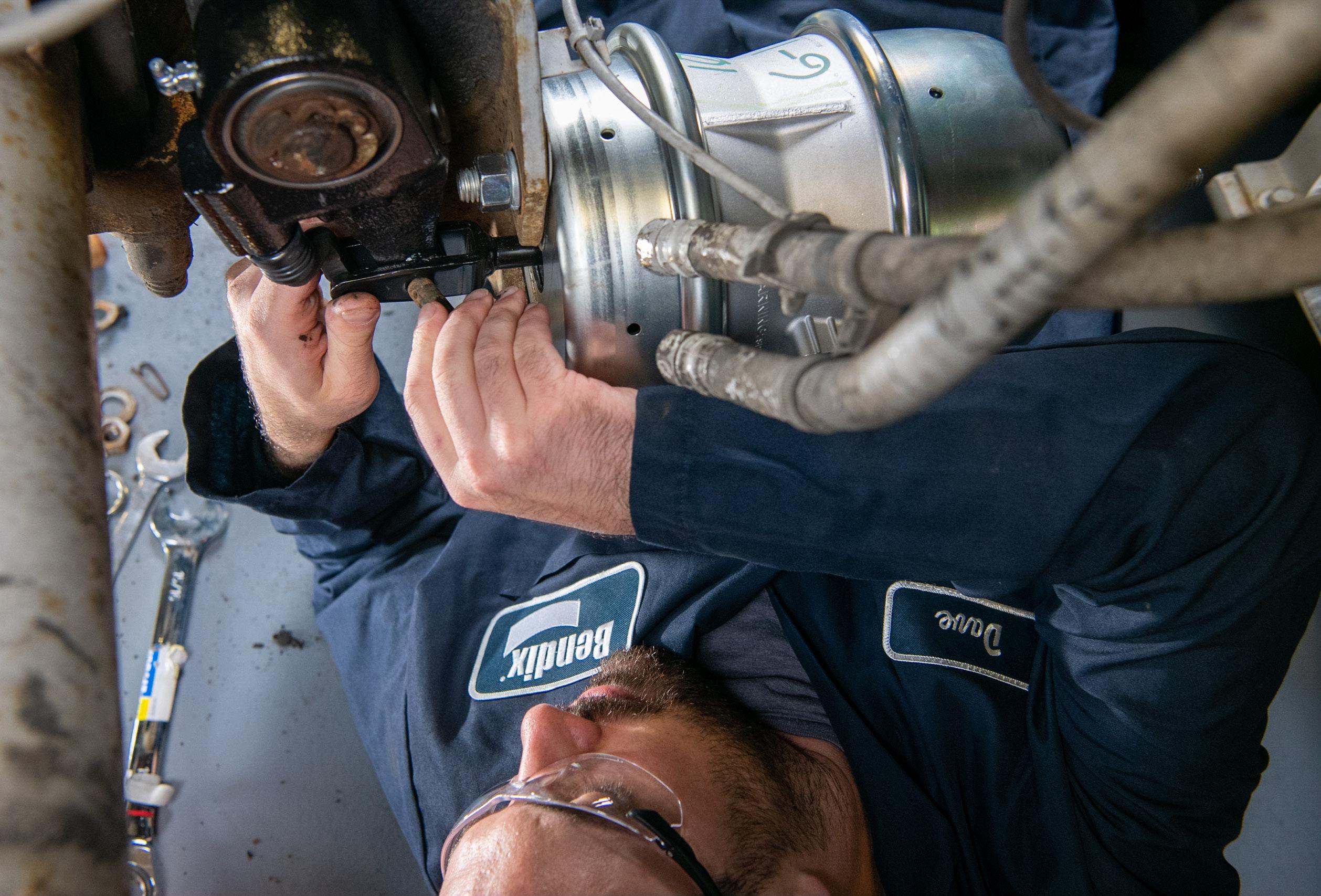
On an air brake system, the slack adjuster is used to adjust the brakes. It takes up the slack in the stroke as the friction surfaces wear away. Modern trucks are equipped with automatic slack adjusters that adjust themselves during full brake applications and should only require manual adjustments during installation.
All photos courtesy of Bendix
Air brakes have a long history of reliable performance in the medium- and heavy-duty truck markets, yet these systems cannot be ignored without costly consequences. A good inspection process and preventive maintenance (PM) plan can keep your trucks from being sidelined.
Improper air brake maintenance accounts for a large percentage of trucks being tagged out of service during Department of Transportation (DOT) inspections. The Commercial Vehicle Safety Alliance (CVSA) performs the annual Roadcheck inspection as part of an initiative to drive awareness to keep roadways safe. According to CVSA, one-fifth of the more than 50,000 commercial vehicle inspections during the 2020 International Roadcheck event resulted in a vehicle being taken out of service because of safety violations. Close to 40% of these vehicles were tagged out of service due to the brake system and/or brake adjustment.
“Many of the critical issues flagged during these inspections are maintenance-related, and many are issues that could have easily been prevented with regular, thorough maintenance procedures,” says Fred Andersky, Bendix Director - demos, sales and service training. Pre-trip inspections are a good starting point, and should include looking for visible brake system problems such as loose hoses or damaged brake components, such as air chambers or pushrods.
Recently, air disc brake systems have been gaining popularity due to performance gains and the ease of maintenance. But though reliable, these systems shouldn’t be ignored.
“Regardless of whether you have a drum or air disc brake system, regular maintenance is required to ensure safe operation and longer service life,” says Mark Holley, director of marketing and customer solutions, wheel end, Bendix. “Although service intervals may be longer with many air disc brake applications, they do require regular inspection and maintenance. With air disc brakes, some technicians inspect at the PM, but most of the time technicians fail to conduct a good visual and caliper movement inspection.”
PERFORM ROUTINE INSPECTIONS
Since brakes directly affect uptime and safety, it is critical to inspect as often as possible.
“Do a quick inspection when the vehicle is in the shop, even if it is not for a brake issue,” says Kevin Pfost, technical service, Bendix. A quick visual check can prevent future problems. “Make sure all brake chambers have the rubber plug properly installed in the caging bolt hole to keep contaminants out of the chamber.”
Brake systems must operate in often hostile environments. For instance, exposure to winter chemicals can wreak havoc on brake systems. “Chemicals are not good, even without winter weather,” says Pfost. “Chemicals contribute to rust on parts like drums/rotors. Water with salt and chemicals can be ingested into seals and bushings.” You can combat this with the proper application of grease. “Greasing the cam brake can help force water and contaminants out. Slack adjusters should be regularly greased. Lubricate the clevis pin so the brake can operate and adjust properly.”
While still in the shop, Bendix recommends the following during air brake inspections: ˜ conduct a 90- to 100-psi brake application and listen for leaks ˜ measure chamber stroke at each wheel end to ensure proper brake adjustment ˜ examine friction material for good condition and minimum thickness ˜ measure/inspect each rotor and drum for wear and heat cracking and/or leopard spotting
It is difficult to predict exactly when brake components need to be inspected and/or replaced. The vehicle’s duty cycle will impact the frequency of maintenance. “Obviously, the more cycle time you have, the more often you should inspect and lubricate the components,” says Holley.
The environment is also a big issue for brakes. Compared to highway applications, brakes on vocational trucks are often exposed to mud, sand and water. These elements create additional wear factors.
ENSURE PROPER ADJUSTMENT
Brakes being out of adjustment is a common DOT citation. On an air brake system, the slack adjuster is used to adjust the brakes. It takes up the slack in the stroke as the friction surfaces wear away. Modern trucks are equipped with automatic slack adjusters that adjust themselves during full brake applications and should only require manual adjustments during installation.
“Always follow the manufacturer’s guidelines for slack adjuster operation and troubleshooting,” says Pfost. “When backing off a Bendix slack adjuster, it could take up to 70 lbs.-ft. to back off. Leave the wrench on the adjuster nut or mark the nut and slack adjuster body and cycle the brake a couple of times to see if the wrench turns in the clockwise direction. This will tell the tech if the slack is adjusting properly. If there is no resistance when backing off the slack, the slack adjuster is bad and should be replaced.”
After initial setup, a properly installed automatic slack adjuster that is lubricated and operating correctly should never need to be manually adjusted. If it is out of adjustment, you need to identify the underlying cause.
You also need to ensure the brake stroke length falls within the recommended range so the brakes are functioning correctly and you are not cited with a DOT violation. To measure the stroke length, check the distance from the chamber mounting face to the pin with the brakes released. Then check this same distance after a full brake application. The difference between the two is the chamber stroke, and the maximum allowable

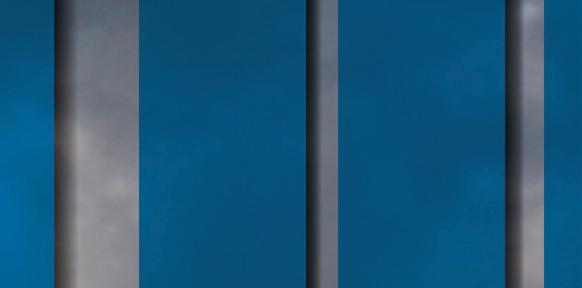
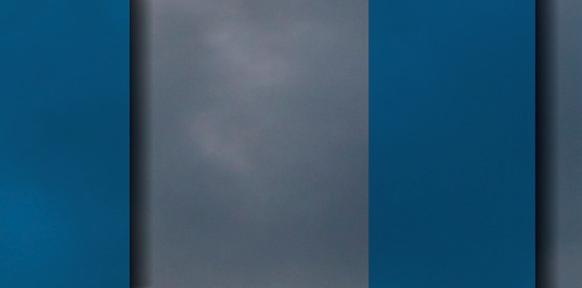

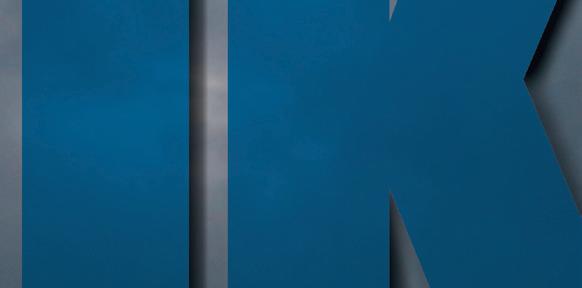
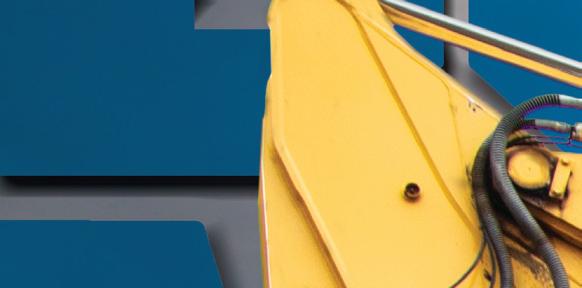
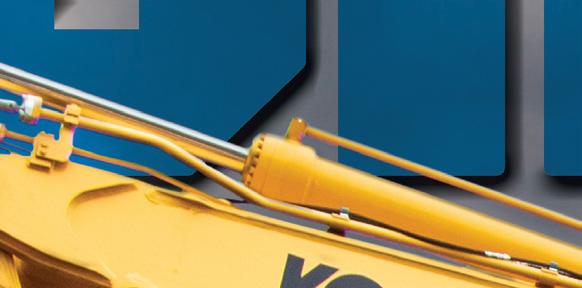
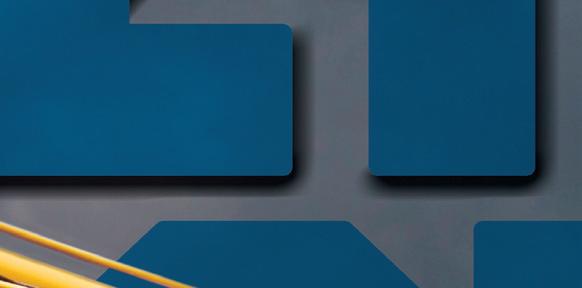
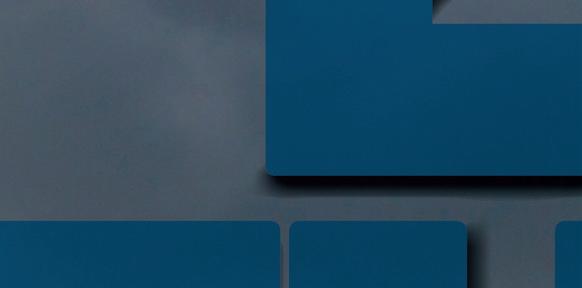


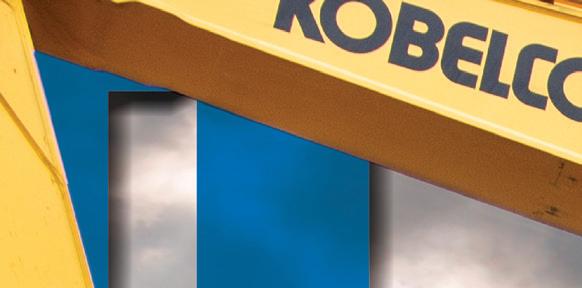
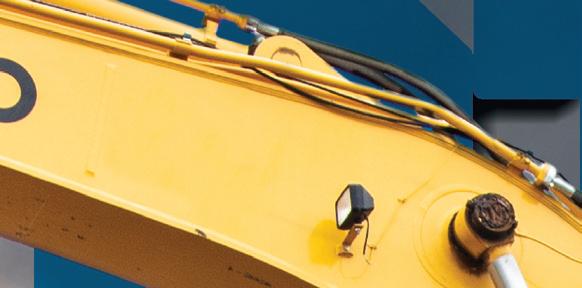
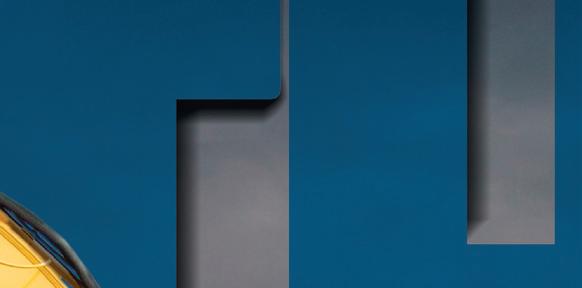

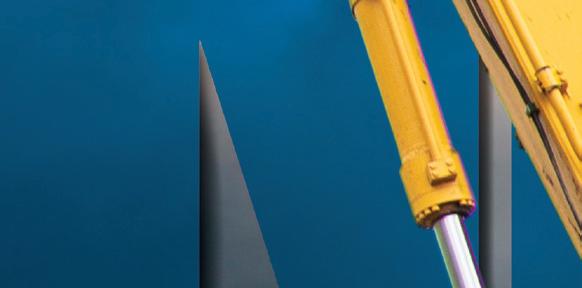
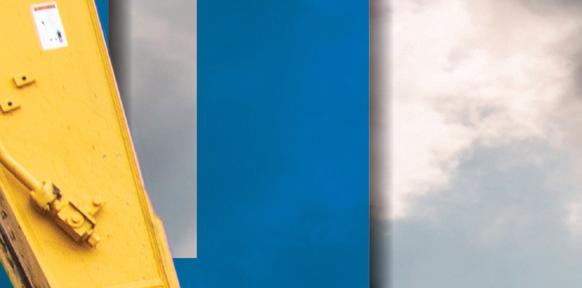
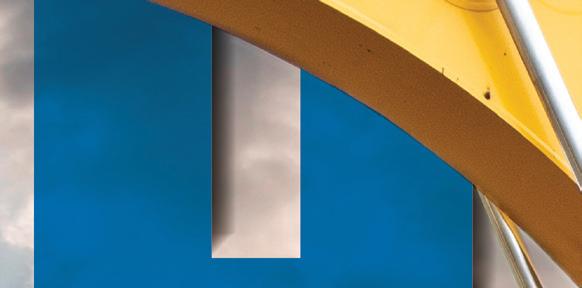
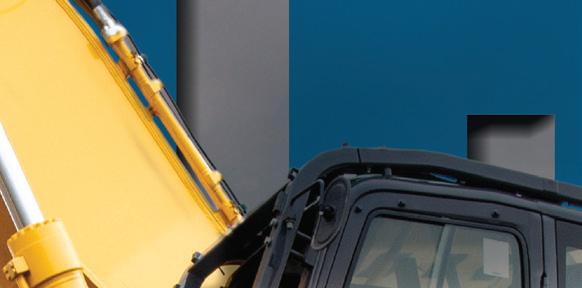
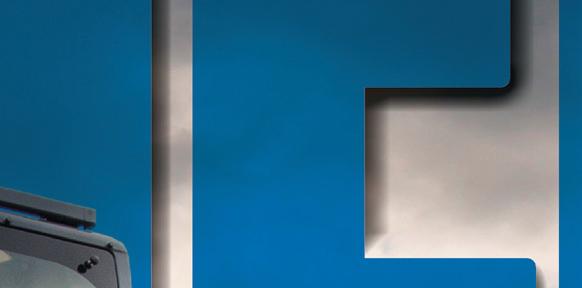

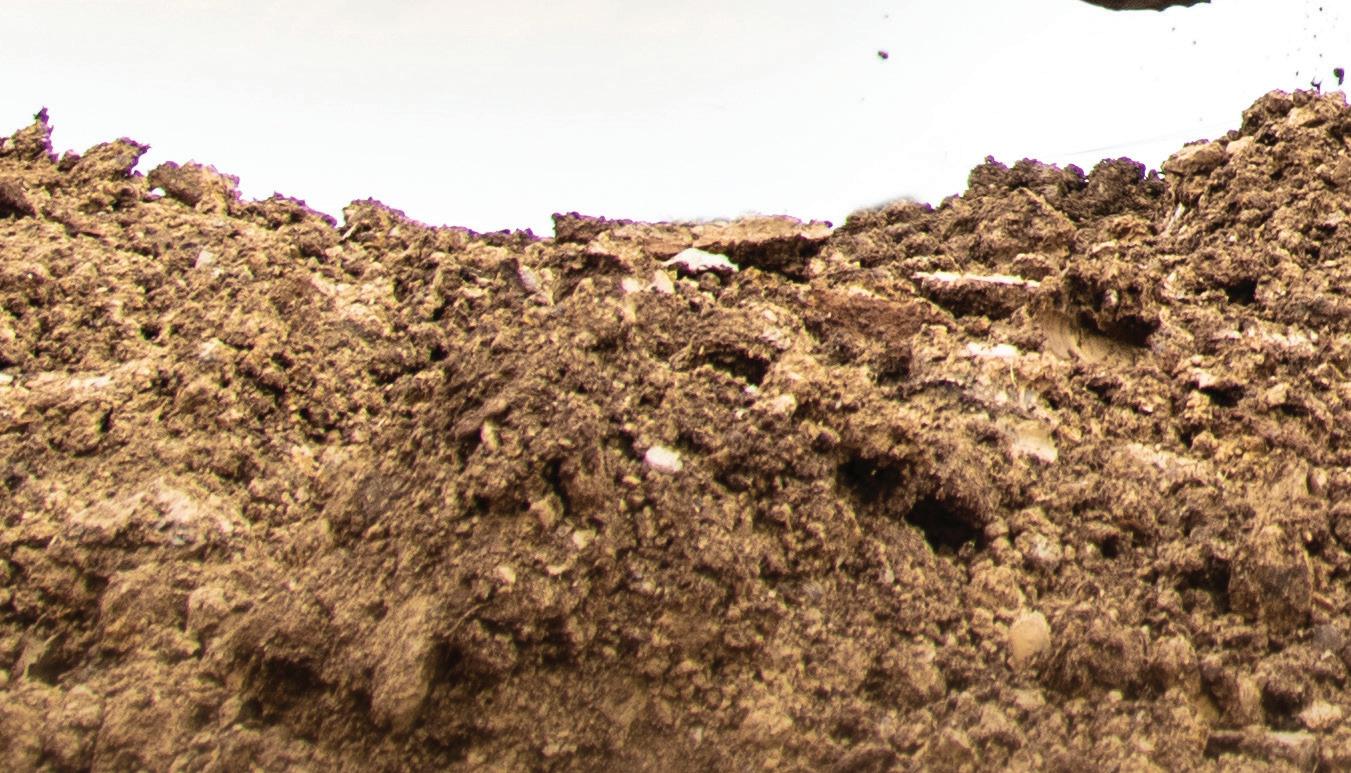
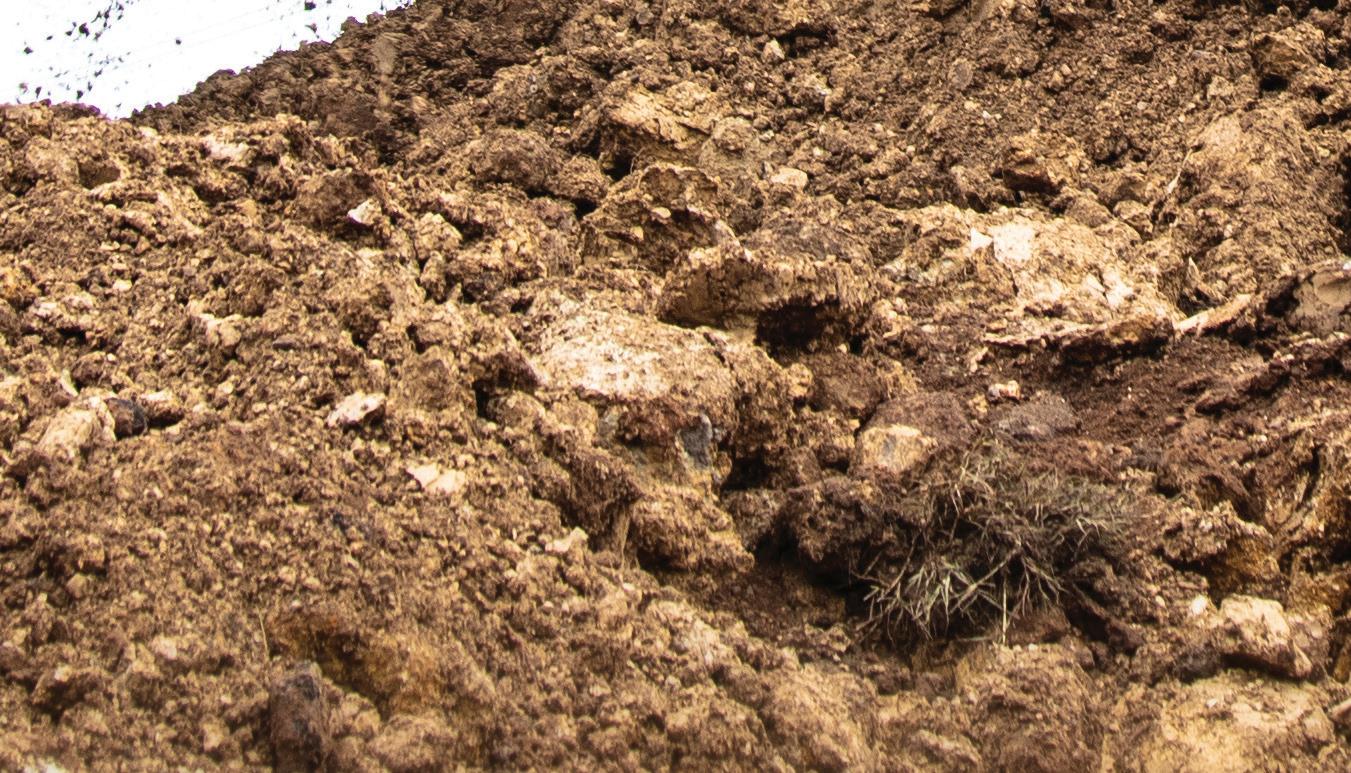

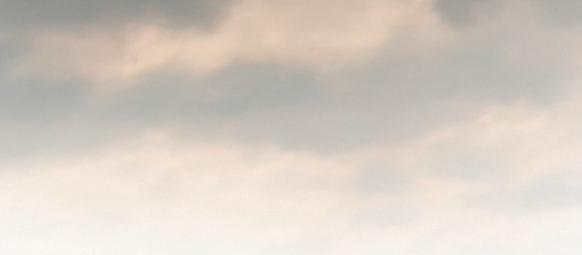

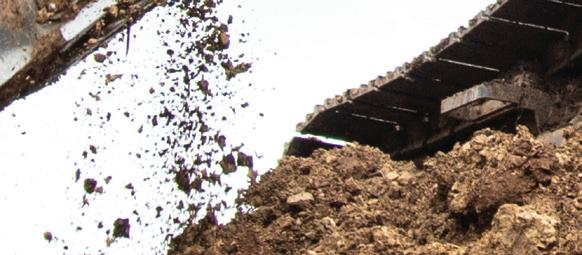

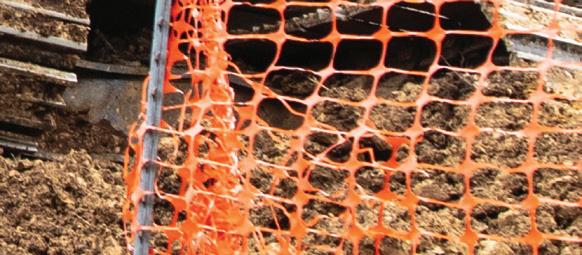

ENGINEERED TO DO ALMOST ANYTHING. ENGINEERED TO DO ALMOST ANYTHING.
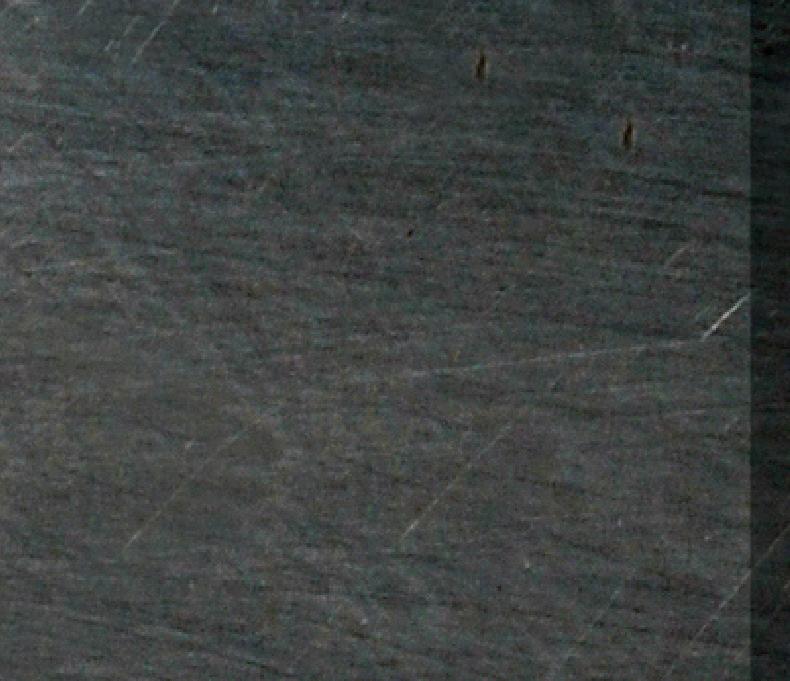



From our rigorous research & development to our precision manufacturing From our rigorous research & development to our precision manufacturing processes, KOBELCO machines are built to do more than any other excavator out processes, KOBELCO machines are built to do more than any other excavator out there. Dig, lift and travel simultaneously with our exclusive independent travel there. Dig, lift and travel simultaneously with our exclusive independent travel feature. Work without a time limit on power boost. And do it all faster, safer and feature. Work without a time limit on power boost. And do it all faster, safer and more effi ciently than ever before with other exclusive innovations you wonʼt fi nd more effi ciently than ever before with other exclusive innovations you wonʼt fi nd anywhere else. Step into a cab and see for yourself what sets them apart. anywhere else. Step into a cab and see for yourself what sets them apart.
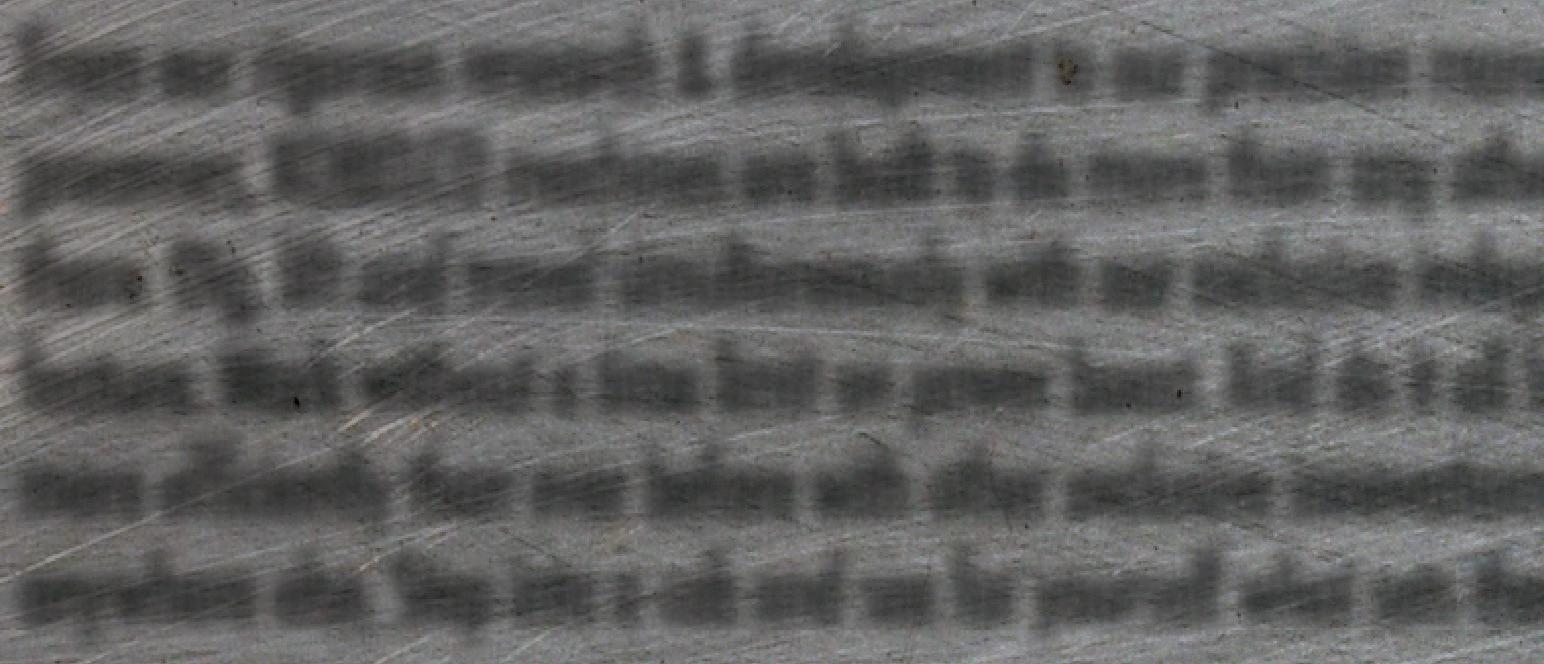


KOBELCO-USA.COMKOBELCO-USA.COM
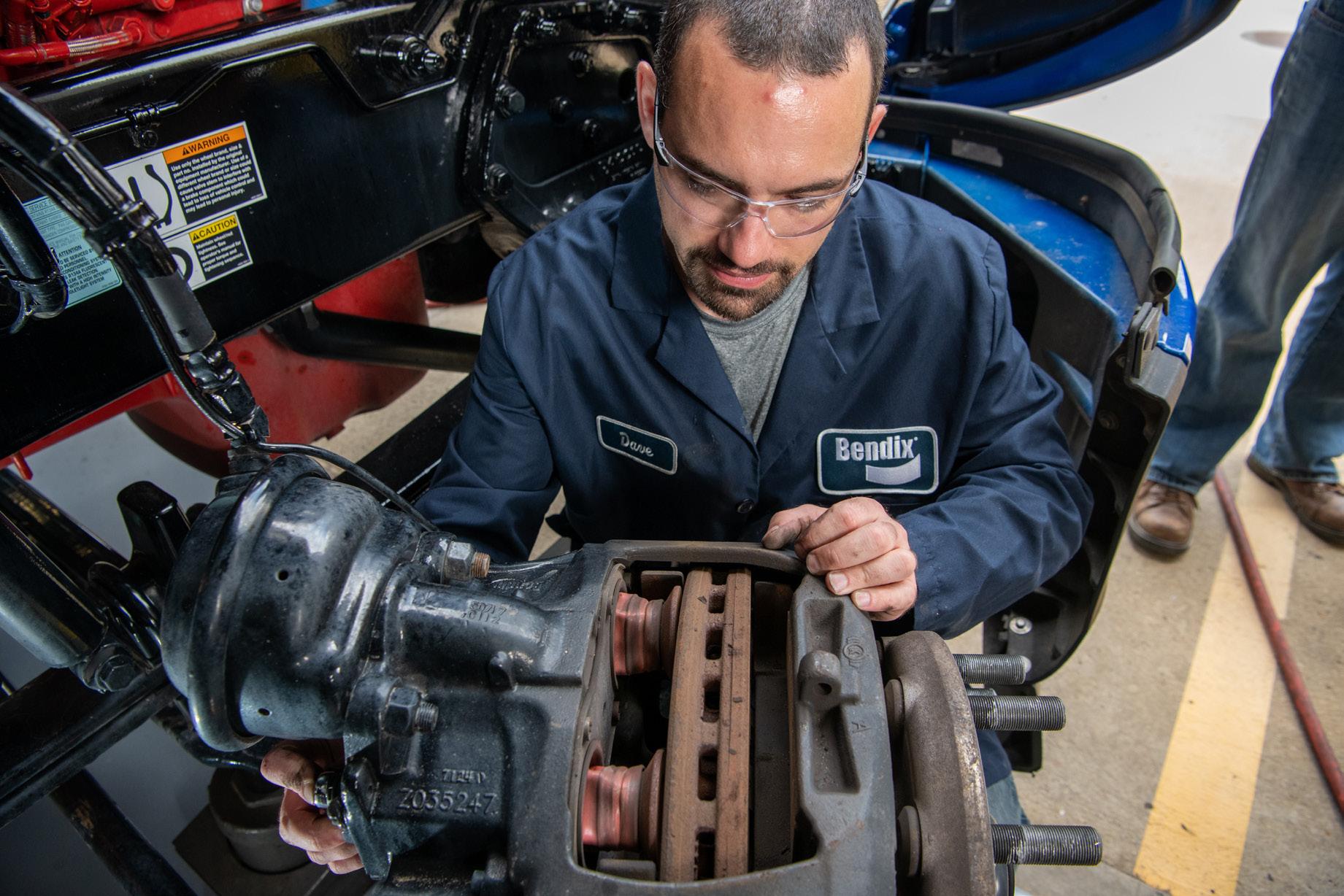
Air disc brake systems have been gaining popularity due to both performance gains and the ease of maintenance. Although service intervals may be longer with these systems in many applications, they do require regular inspection and maintenance.
Always follow the manufacturer’s guidelines for slack adjuster operation and troubleshooting. One of the leading causes of brake failure occurs when the cam brake stroke measurement is not taken with a tape measure.
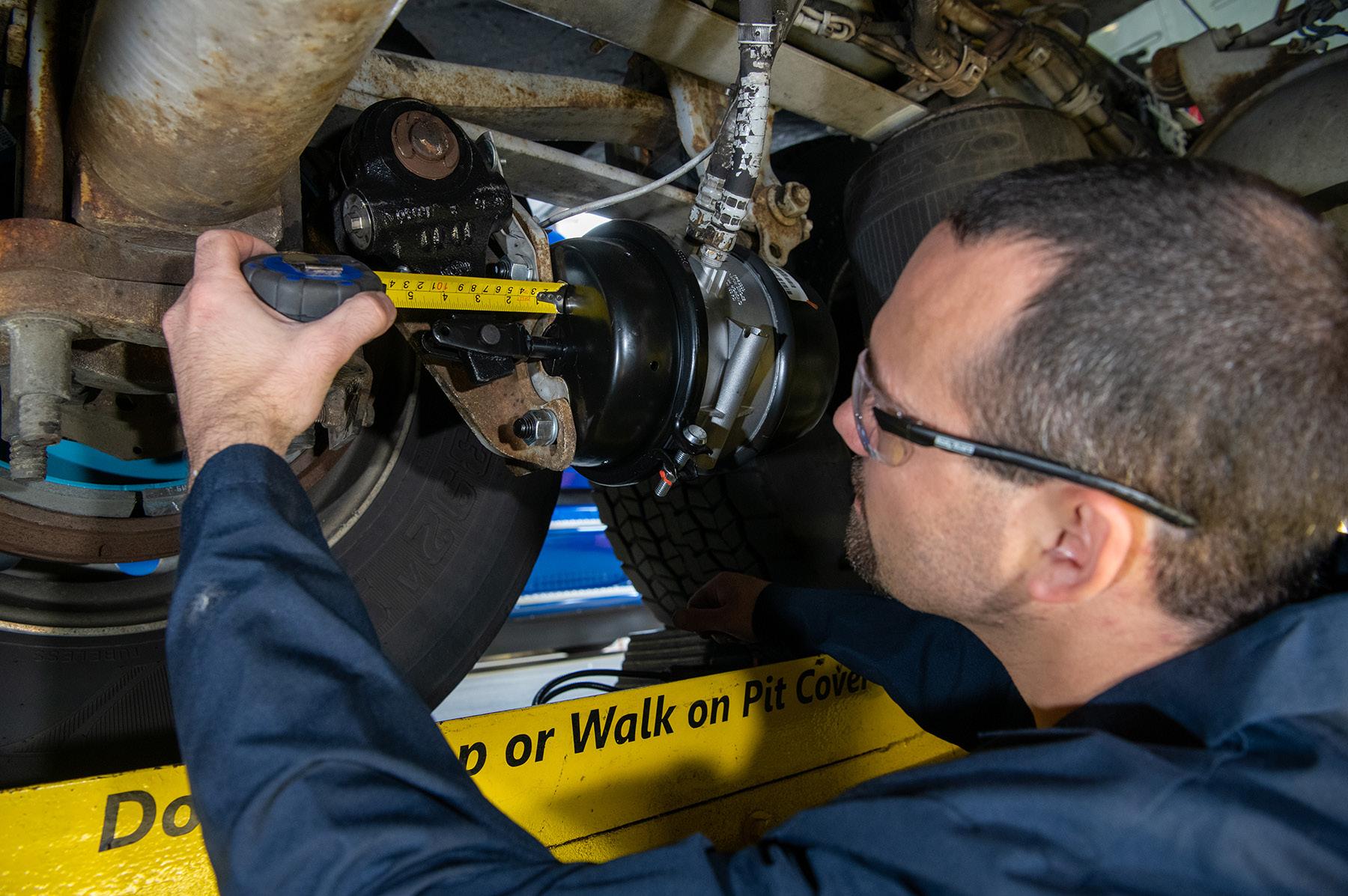
stroke is based on chamber size and type.
One of the leading causes of brake failure occurs when the cam brake stroke measurement is not taken with a tape measure. “Most of the time, technicians just readjust the slack adjuster at the PM instead of measuring,” says Holley.
If the automatic slack adjuster is working properly and the brake stroke length is out of adjustment, Bendix recommends checking: ˜ for proper operation of the brake camshaft and cam tube ˜ the cam head and rollers for abnormal wear ˜ the brake’s friction blocks for wear level and cracks ˜ camshaft bushings for wear ˜ radial and axial end play ˜ brake drums for maximum diameter and surface finish ˜ brake shoe return springs to ensure a proper return to the
“zero stroke” ˜ return spring on the air chamber or on the service side of double diaphragm spring brakes ˜ the clevis pins connecting the chamber to the automatic slack adjuster to ensure they turn freely
STOP AIR LEAKS
The two types of braking systems in use today are hydraulic and air. Air brake systems are used on heavy trucks because they can reliably stop an 80,000lb. load in a short distance. And unlike hydraulic brake systems where a leak causes a loss of braking performance, a leak in an air brake system causes the brakes to be applied. Air pressure is required to release the brakes.
To keep the truck moving, the air system must be properly maintained and air leaks must be kept in check. Loose fittings can often be the culprit. To check for air leaks, you can park the vehicle and monitor the pressure gauges. With the service brake applied, you should not lose more than 1 psi per minute.
While minor leaks may be difficult to find, you should listen carefully for leaks during the pre-trip walkaround.
“Just because you don’t immediately see or hear any leaks doesn’t mean they’re not present,” says Richard Nagel, Bendix’s director of marketing and customer solutions - Air Supply & Drivetrain. “If you notice that it’s taking significantly longer to charge the tanks — say, three or four minutes compared to one or two — then that’s a sign that your air brake system is losing air. The same thing applies if you notice the system is charging more often.”
For most trucks, as the brakes are used, the air compressor should kick in at approximately 100 psi and kick out at approximately 125 psi. If the pressure drops to 60 psi, a low air warning light and/or buzzer should be triggered. As the pressure drops lower, the spring brakes apply between 20 to 45 psi. MOISTURE IS THE ENEMY
Moisture and air brake systems don’t mix. Excess moisture can degrade brake actuation performance and cause corrosion, shortening the service life of air system components. In cold weather, the moisture can even cause the system to freeze up.
To combat moisture, all air brake systems should be equipped with a dryer cartridge that removes both water and oil from the system. This dryer cartridge needs to be maintained and the compressed air tanks should be periodically drained to minimize moisture in the system.
“Service the air dryer per manufacturer recommendations,” notes Nagel. “Drain air systems regularly.”
In fact, it is often advised to drain air tanks daily. If water is found in the system, take corrective action. Check to make sure the charging/drying system is operating correctly. Inspect for air leaks in the system and check the governor to ensure a signal is being sent to purge the air dryer. Also verify that the drying cartridge is functioning properly and that the desiccant cartridge isn’t saturated. If it is saturated, replace the cartridge.
Clean, dry air can go a long way toward ensuring brake system reliability.
DON’T SKIMP WHEN IT COMES TO REPLACEMENT PARTS
The OEM air brake systems are designed to meet mandated performance standards outlined in FMVSS 121. Aftermarket replacement materials, such as friction materials, can change the braking performance. In some cases, the system may no longer conform to the FMVSS 121 requirements.
To help mitigate any loss in performance, the Technology and Maintenance Council (TMC) recommends that the torque value of an aftermarket brake lining closely match that of the original equipment it is replacing.
Air brake systems are made up of many separate parts, all of which must be in good condition to provide reliable operation. Pre-trip inspections by drivers and periodic, more through inspections by technicians are key to keeping trucks safe and on the road. ET
TOP 7
Engine Service Tips and Tricks

Maintenance is an unavoidable part of the job, necessary to keep things moving, mitigate equipment failure and limit downtime. It can be a hassle — not unlike any routine task — but thanks to recent advancements in engines and engine design, it doesn’t have to be. Fortunately, manufacturers are developing features that reduce maintenance and associated downtime.
When it comes to engine maintenance, regular and preventive measures are essential. Here are the top seven tips and tricks to keep the engines in your fleet in premium condition to improve productivity on the jobsite.
1. FUEL FOR PRODUCTIVITY
An engine is only as good as the fuel you put in the tank. For years, fuel choices were limited to regular, unleaded and diesel. Nowadays, you can add ethanol fuel blends to that list. Lower-level ethanol, typically 10% or less, is safe to use in most gasoline engines. Ethanol-free gasoline with an octane rating of 87 or higher is generally a good fuel choice.
Choosing a fuel that is optimized for your engine is key to ensuring performance and avoiding engine issues, such as misfires and long-term damage.
2. CONSIDER PROPANE
While gasoline and diesel are the familiar industry fuels, in some instances, fueling with propane can offer advantages for your operation. Propane eliminates some elements of operator error in environments where that can be a significant problem. For example, if you’re working on a finished surface, fuel spillage can cause dead or brown spots. With propane, spillage is never an issue.
Using propane can also help avoid fuel storage issues. Propane-powered equipment can be stored for long periods of time since the fuel isn’t susceptible to going stale.
Using propane can impact your maintenance schedule by reducing the amount of time a crew spends refueling, as you can easily refuel on the job.
3. STORE SMART
Storing your equipment is unavoidable at times but doing so can quickly lead to stale fuel issues. Once fuel is added to a machine’s tank, it starts to lose volatility. To mitigate issues associated with stale fuel, such as diminished performance and vapor lock, fill your tank with
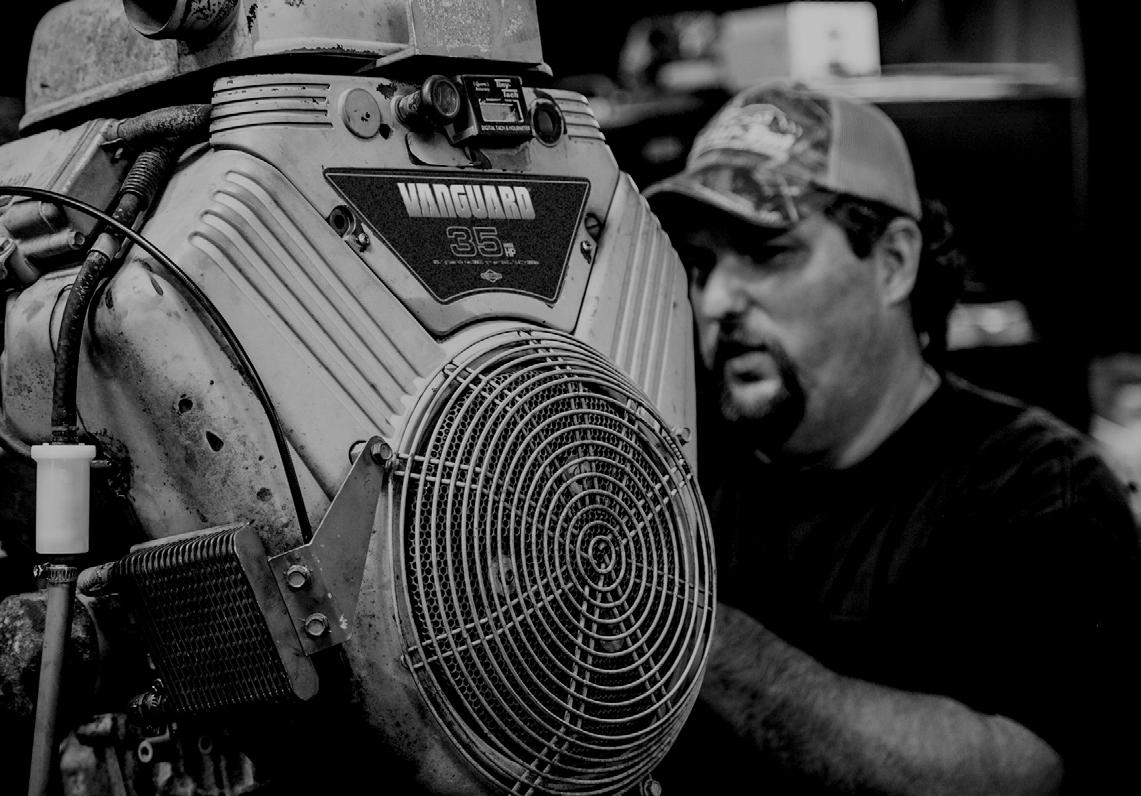
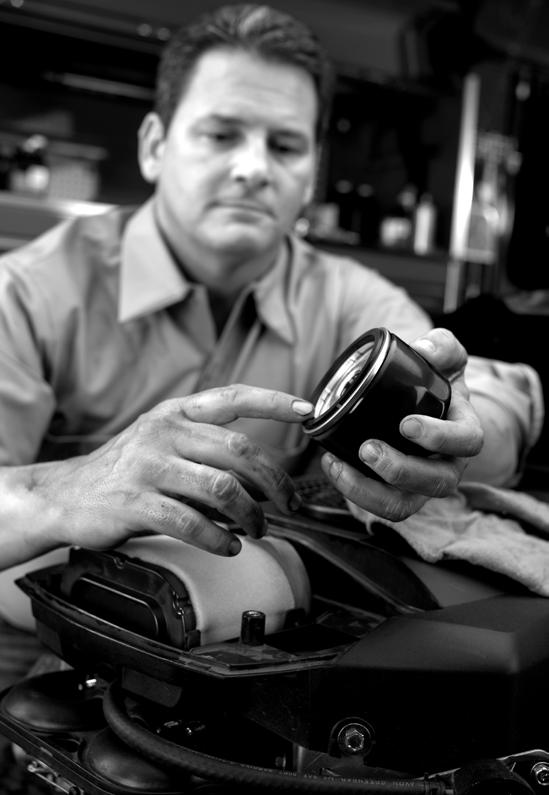
fresh fuel after removing equipment from storage.
If you know equipment will be stored for significant periods of time, use a fuel stabilizer to combat stale fuel. Often, fuel stabilizers help prevent gum and varnish buildup, and can combat corrosion — especially that associated with ethanol fuels — and chemical breakdowns.
4. SWAP OUT SPARK PLUGS
With time, spark plugs in gasolinepowered engines can be susceptible to carbon deposits and other types of performance-inhibiting damage. Worn spark plugs can lead to engine misfires, stalling and difficulty starting.
Regularly removing and inspecting your engine’s spark plugs, and replacing when necessary, can help you avoid these issues.
5. OPT FOR OIL CHANGES
Foregoing oil changes opens the door for significant engine damage. Relying on oil past its service life means relying on oil with decreased viscosity and a diminished ability to correctly clean, cool and lubricate your engine — all of which may lead to lower engine performance capabilities and lasting damage.
While the industry is starting to see advanced oil management systems and improved options that extend oil change intervals, it’s still important to know and understand the guidelines for your fleet’s engines. Changing oil too often can waste resources, while waiting too long can lead to engine damage.
Knowing your engine’s oil change intervals and adhering to them ensures your fleet can run like a well-oiled machine.
6. GIVE YOUR ENGINE FRESH AIR
Fresh air is one of the key performance components in small, air-cooled engines, which means regularly changing the air filter is critical. Generally, air filters should be changed every 100 to 250 hours, depending on application and filter type.
With advancing technologies, such as cyclonic air filtration, it’s important to choose OEM filters designed specifically for your engine to guarantee fit and performance. Often, these filters have a longer lifespan and will ensure better engine productivity.
7. ASSESS YOUR FLEET
At the beginning and end of each season, take stock of your fleet equipment and the engines you rely on to keep them running. Are the engines older, no longer performing efficiently or experiencing frequent issues? Can these performance issues be improved with proper maintenance practices or are they simply related to old age? If proper maintenance is no longer enough, it may be time to replace an engine.
Engine maintenance needs are being reduced and simplified as advanced technology continues to improve in the industry. However, performing proper maintenance will always be an integral component of ensuring your fleet is primed for productivity.
Until self-maintaining engines are developed (a person can dream), understanding your engine’s maintenance needs and sticking to a schedule is key to keeping your equipment fleet up and running. ET
Tom Billigen is customer education training manager at Briggs & Stratton.
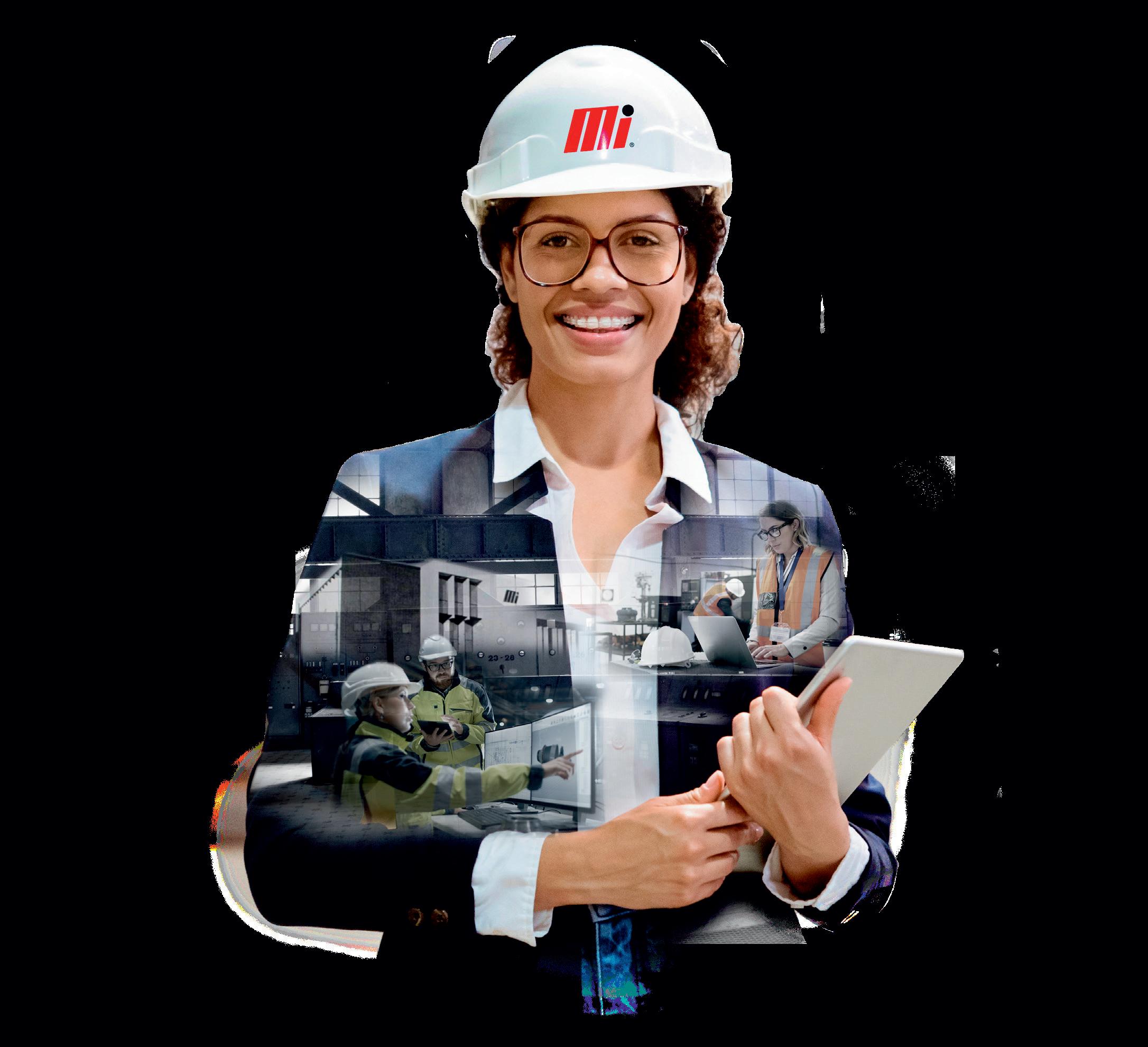