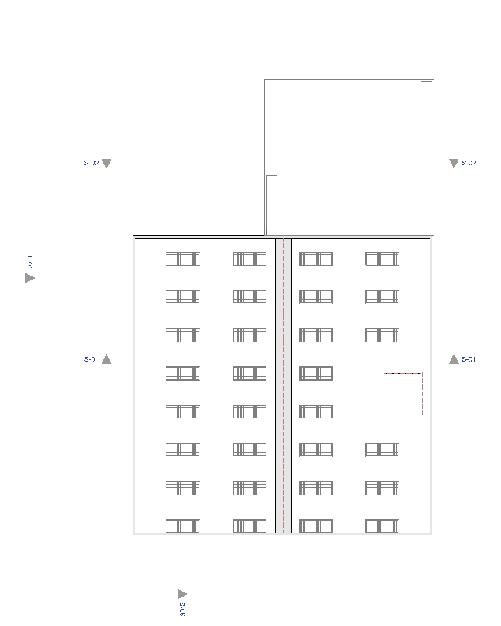
13 minute read
THE ALPHABETTI CREATIVE CO-OPERATIVE CENTRE, NEWCASTLE UPON TYNE
50m 75m Lower ground floor @ 1:100 ab iur, quae officto quiatur arum quos eturenimi, culparum non perempe est, cum secuptam, es dolent liquis dolo qui doluptat hilia sequia ex et ut velitas doluptus dolut eostorentia intorendae vid et omnimil igniaest qui quidentem qui quid quidestem dolo corehentinti sum voluptatibus apis ra cor arion rehent peribus cimpelluptat quiassiti rem quod utam et que eati bea plibus restrum alit eium que voluptur accullu ptatem acea sum quata commodit, tectae. Ut porum nisque di venis derorerum am ra simendictem que qui omnis doluptae latis soluptata sequias sit as dolessi cum sin et moluptae et omnihil in pre labo. Ebitatur as et aut alit omnis adigento quuntem reprepudam, voluptio conem andae mo modit aliquod
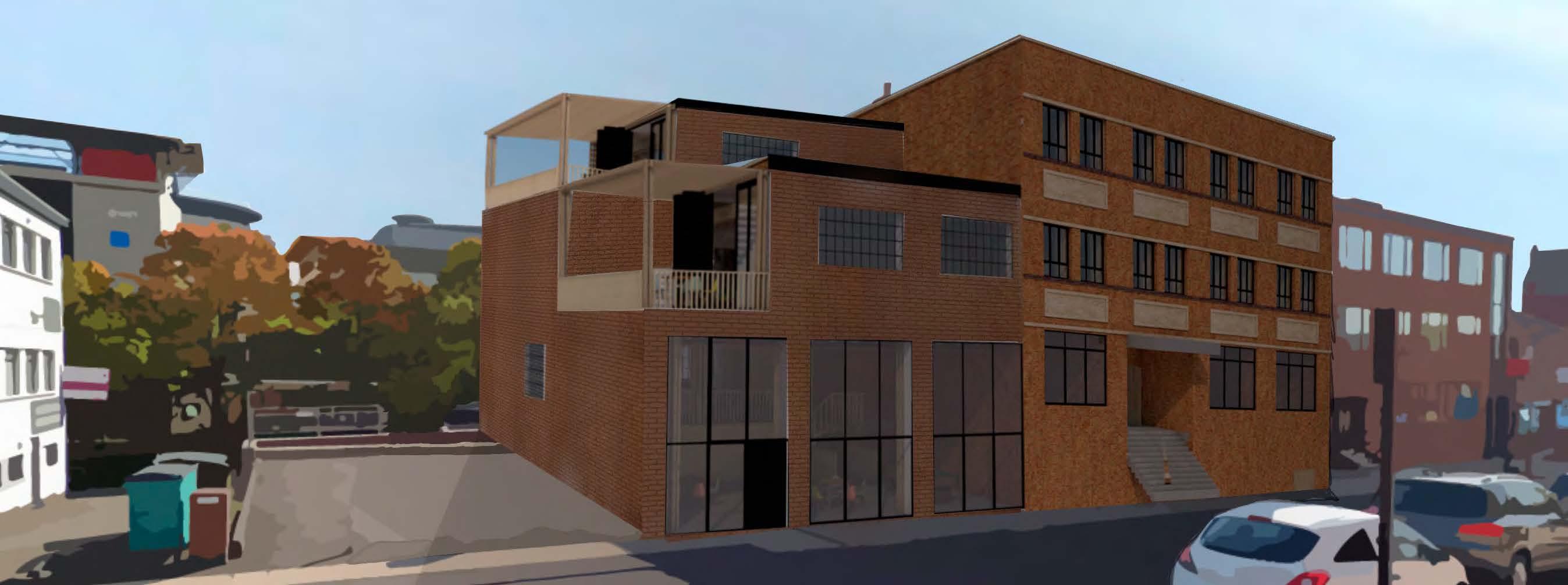
Advertisement
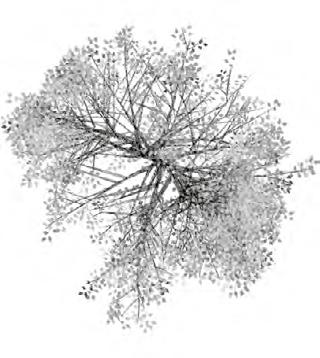
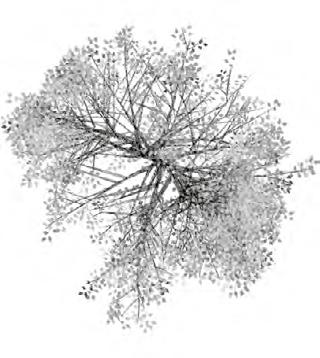
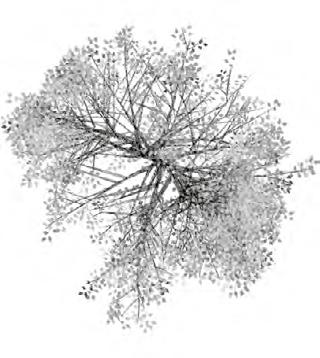
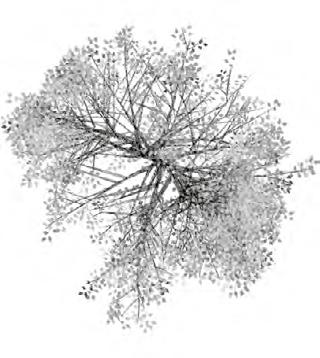
BA Hons, Year 3, Project 1
Newcastle’s City Image:
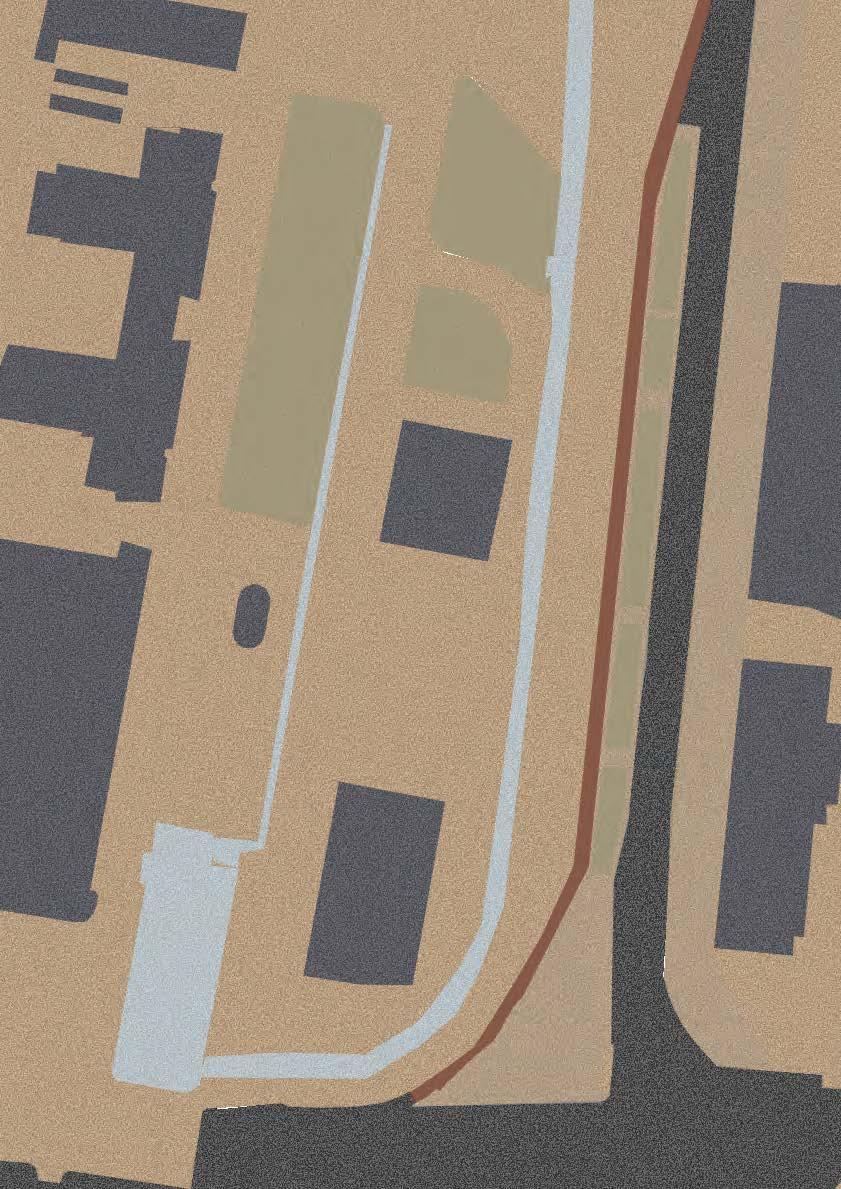
Strengths:
•There is a huge section of space that could become a new section of public realm
•There are multiple options for where to extend
•There is already a really strong cultural presence with the theatre and museum opposite
•The site is in the west of the city – a historically neglected part of the city
Weaknesses:
•St. James’ Boulevard is a huge urban edge cutting the site off from the city centre
•The boulevard creates lots of noise pollution and air pollution
•Too much hardscaping and not effective planting for biodiversity
•The existing fabric of the building will have to be upgraded in terms of thermal performance
•The party wall of the building will have to be considered very carefully to eliminate thermal bridging
Opportunities:
•The boulevard could be closed down over time and this could create yet more public realm
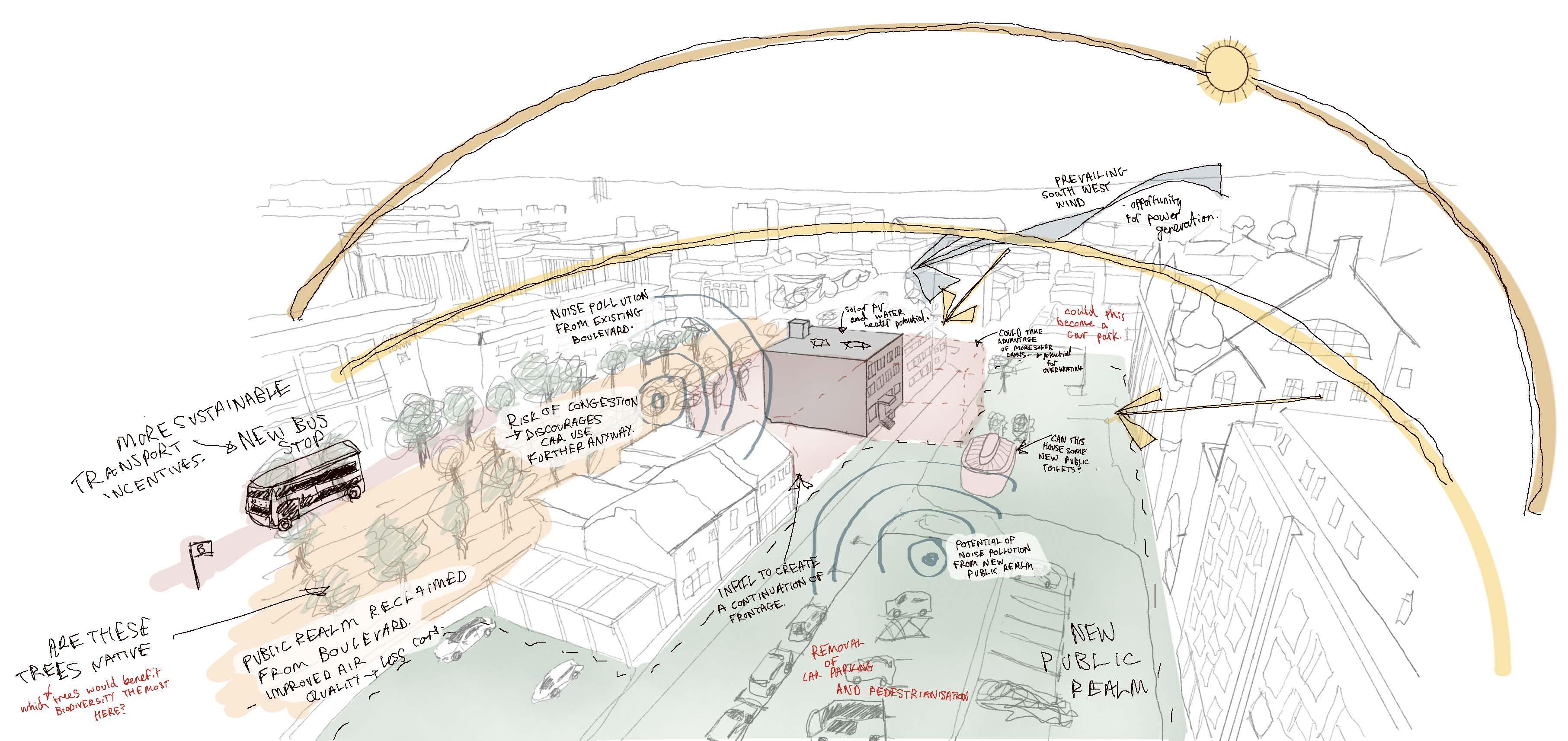
•Availability of sun and wind on site could be used to generate electricity and heat water
•If I extend to the north there is an opportunity to create a new sense of frontage for Blandford Square
•There is an opportunity to connect with the Newcastle Helix site and maybe be a small business hub
Threats:
•If the boulevard is closed down, there is a risk of city-wide congestion
•If the extension is to the west here is a risk of overheating in summer
•There is potential that the are could become gentrified – therefore the community will be the decision makers
•If the new landscaping is not carefully considered the impact of the new tree species etc could cause consequences later down the line
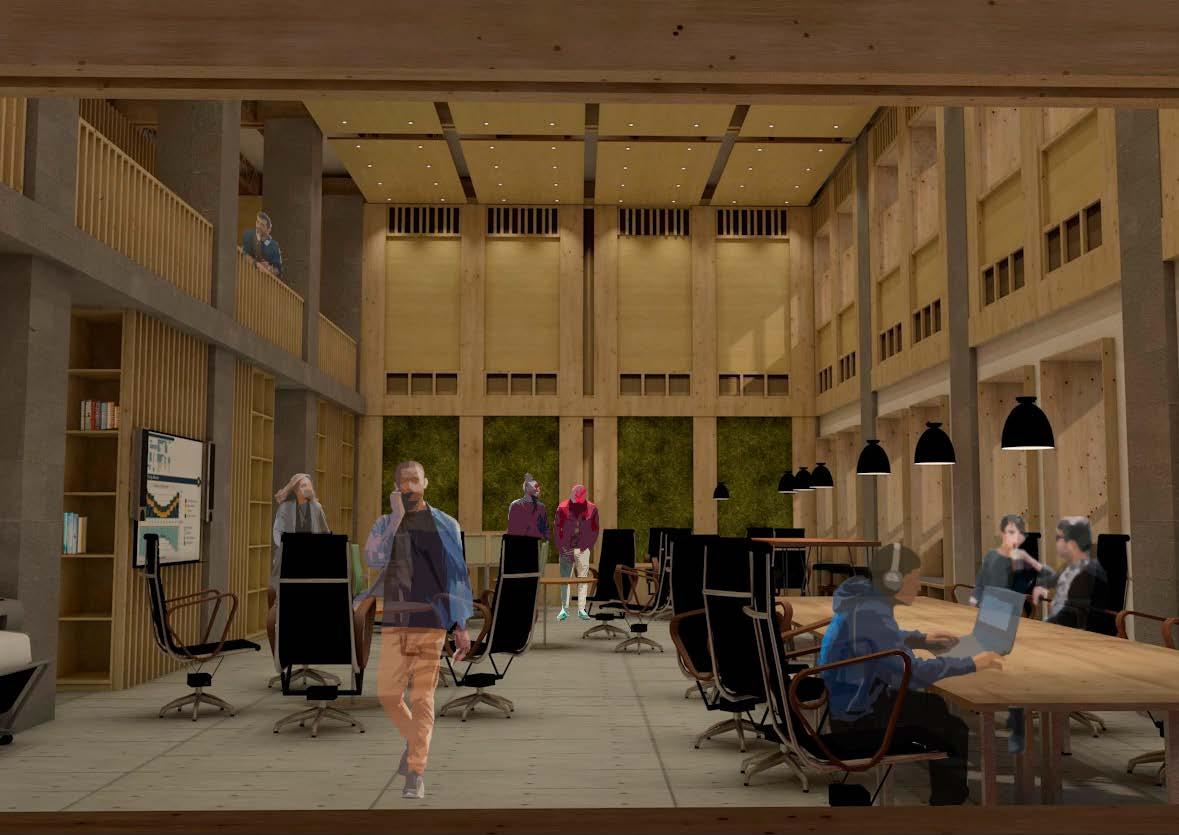
Web joists used to suspend panels finished with stil acoustic veneer in a nano-perforated, quartercut Douglas Fir finish. These panel act as acoustic baffles with in-built, direct downlighting and led backlighting strips
Concrete frame of existing building exposed and floor plate cut through to create double height space – edge of slab reinforced with a new steel angle inside. Concrete left untreated Repetition of 2x4 timber elements used to create railings and slats with 150mm centres
BASIS High table By e15 and Ergo Impact LeanRite Elite - Ergonomic Standing Chairs to enable a range of different ergonomic settings
Depth of columns used to create an alcove occupied with bespoke shelving and a place for printing and plotting.
Fixed in place computer workstations have ethernet connections as well as other data ports such as SD Card slots etc – essential for the creatives working here who maybe don’t have ready access to their own computer
Windows are openable for purge ventilation in a morning - required to extract the Carbon Dioxide generated from the internal green wall’s overnight respiration Biotecture UK interior green wall provides air purification and a connection to nature from within the building.
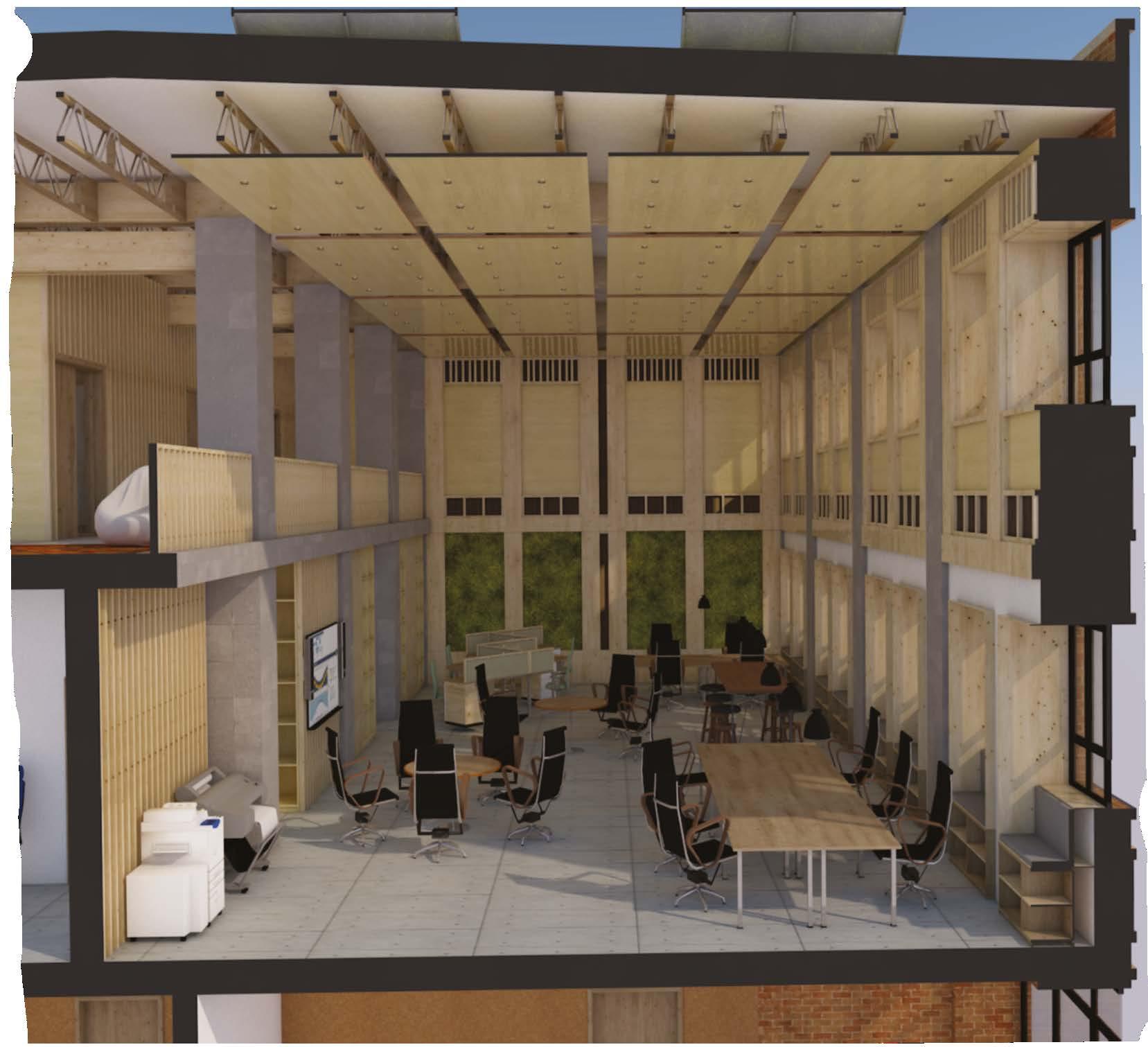
Lime plaster finish – this is naturally white but not too stark that it is overpowering and it complements the muted and natural tones of the other wall finishes
Deep wall build -up allows for bespoke window seats and shelving
BASIS Workstation table By e15 Charles and Ray Eames Aluminium chair ea119 finished in chrome and black leather.
240 Volt, USB A and USB C ports built in to desks with all wires routed under tables in trays, down into the floor through service “channels” or “trays” in the raised access floors
Kingspan RMG600 raised access floor with 150mm pedestals allows for some ventilation ducts as well as all plumbing electrical and telecommunications cables to be routed through service channels in the floor.
Existing building:
1. Solar PV Panels as a part of the BioSolar blue roof from Bauder
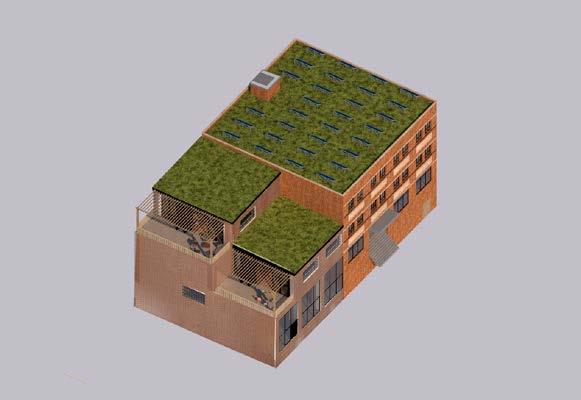
2. Bauder BioSolar StormSub BLUE roof
3. New supporting roof structure composed of Baubuche beams and web joists
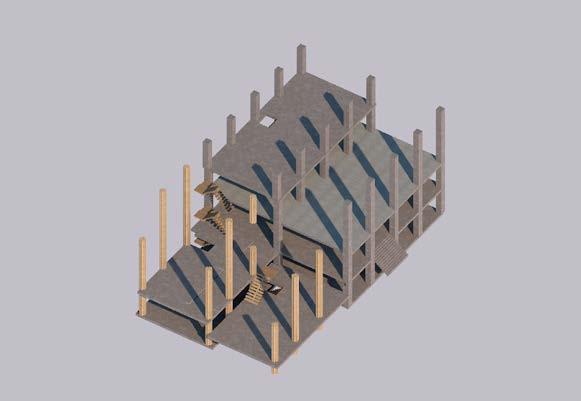
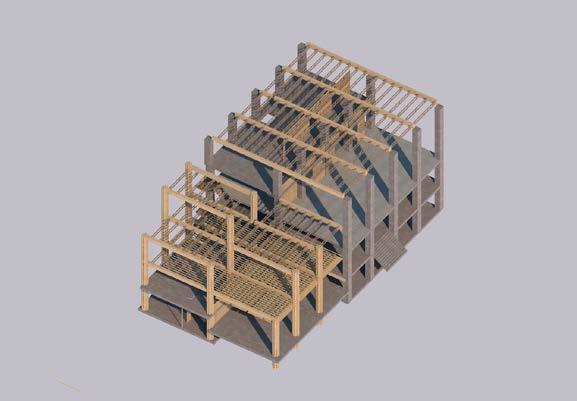
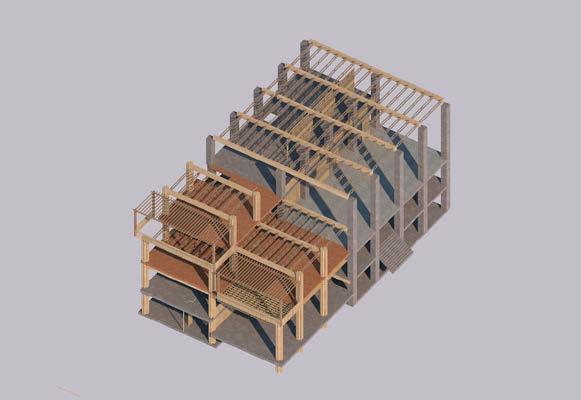
4. Acoustic baffles with integrated lighting
5. Existing reinforced concrete frame
6. Acoustic surface treatment
7. SIP Cassettes with integrated bespoke window seating
8. Existing Alphabetti façade with upgraded Velfac V200e windows
Building extension:
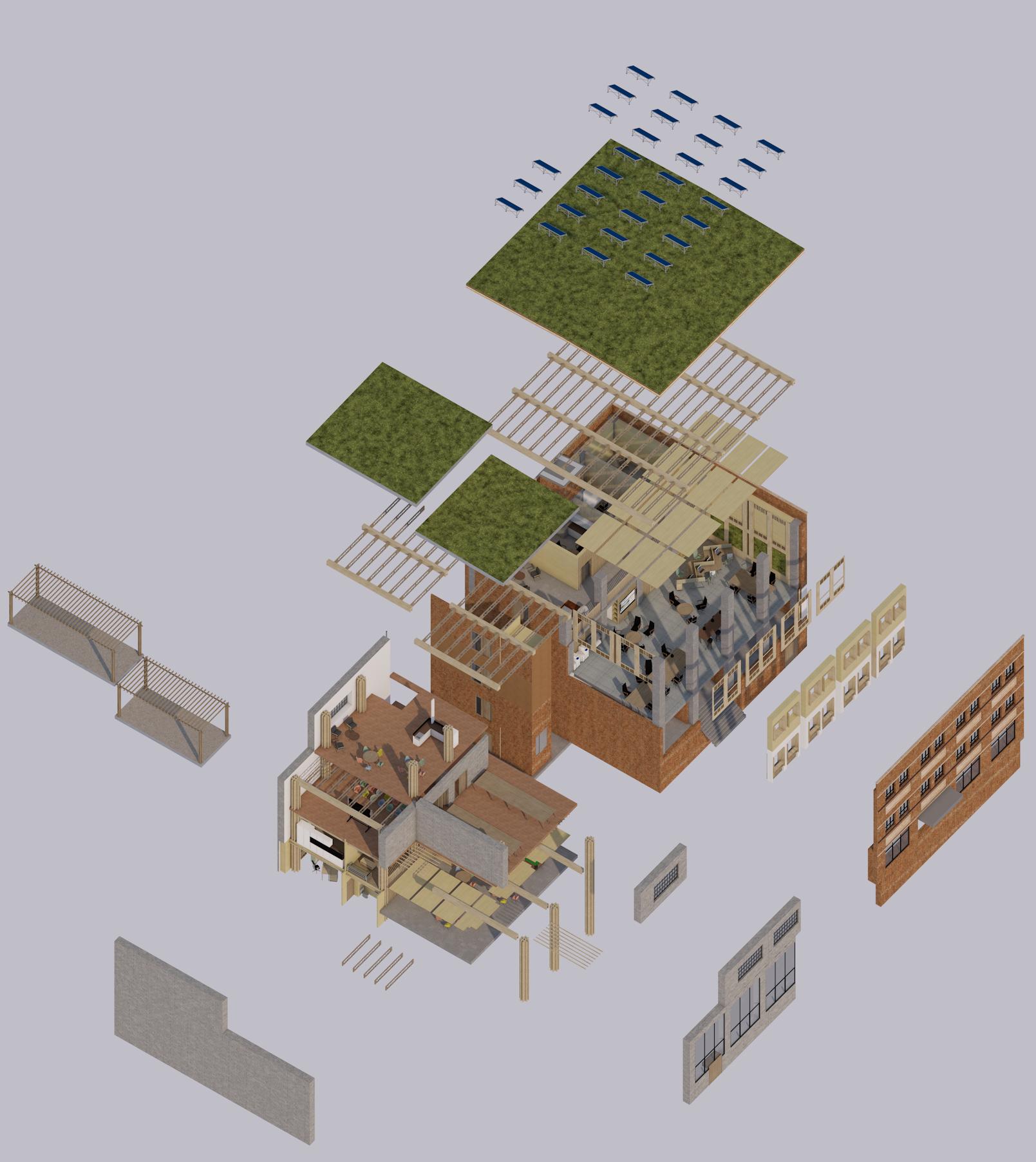
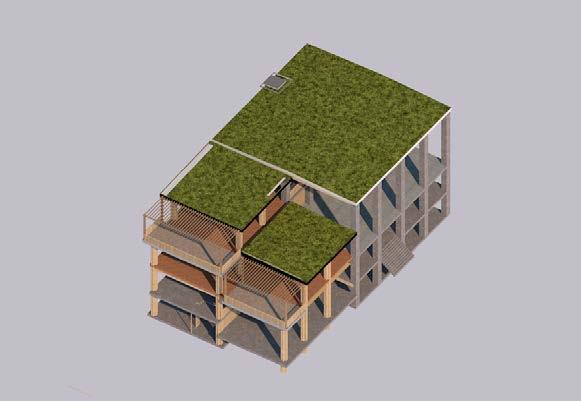
9. Technal tental 50 feature cap curtain wall
10. SIP Cassette façade
11. Timber battens for floor
12. Primary Baubuche profiled columns
13. Web joists
14. (see 10)
15. Bauder StormSub Blue roof finished with stone pavers
16. Timber pergola
17. Roof structure composed of Baubuche beams and web joists
18. Bauder StormSub Blue roof finished with native wildflower blanket
Ground Floor/ External Wall Detail:
1. Compacted Earth
2. Continuous flight augured pile – reinforced concrete using 40% Seratech cement
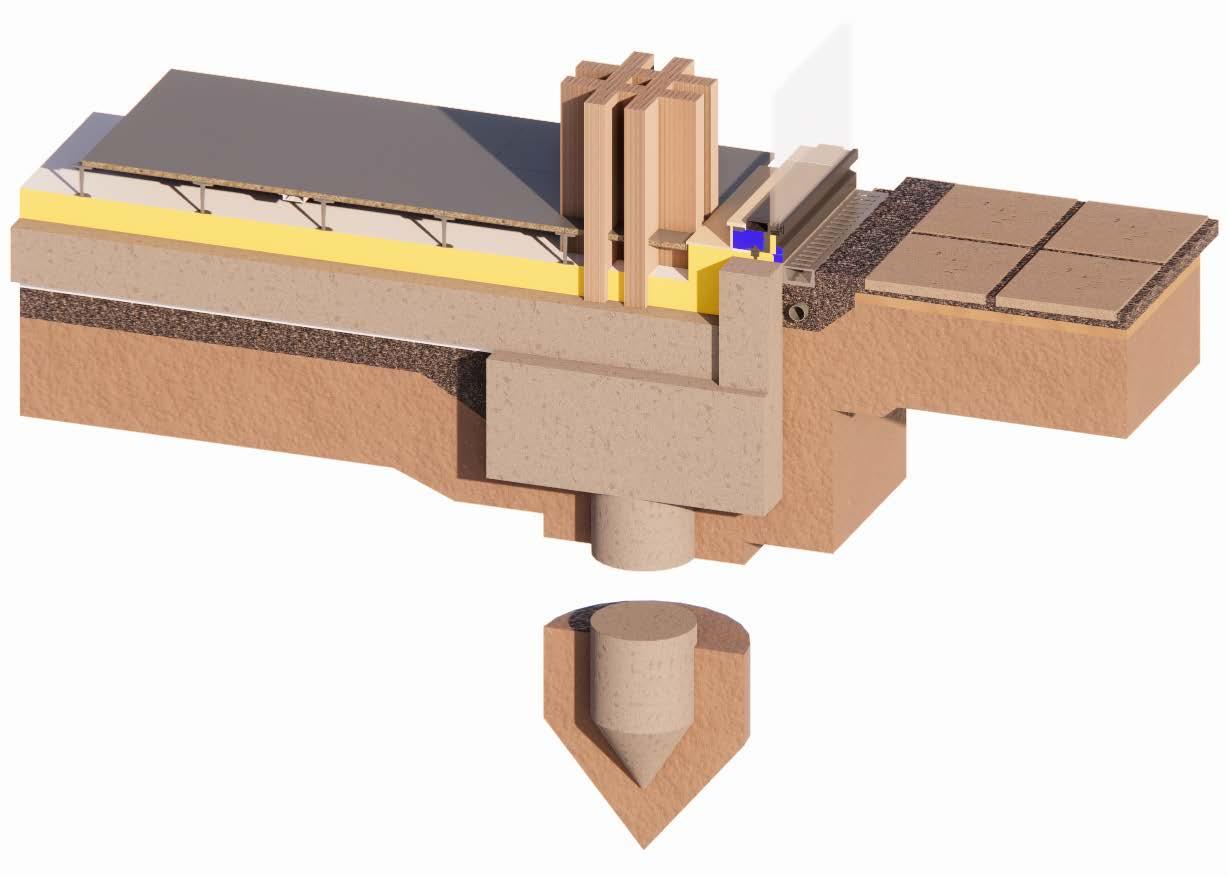
3. Dörken Italia – Delta DPC Tagliamuro
4. Reinforced concrete pile cap using 40% Seratech cement
5. 150mm recycled concrete aggregate hardcore (from existing floor plate that was removed)
6. 75mm sand
7. 275mm reinforced concrete slab using 40% Seratech cement
8. 150mm Knauf V SmartWall S C1 rigid rock mineral wool insulation
9. Pro Clima Intello Plus Intelligent vapour check and airtight membrane with Pro Clima TESCON No.1 Airtightness tape at the seams and over any holes from screws etc
10. Steel footplate with self-tapping concrete anchor bolts
11. Kingspan RMG600 raised access floor with 150mm pedestals – unfinished and sealed with Solid StepCote Clear DIY
Abrasive Anti-Slip Floor Coating SSC02 grit size
12. Power and data cable tray
13. Plywood window reveal
14. 600mm reinforced concrete perimeter ring-beam
15. Technal Tental50 feature cap Curtain wall system
16. Pollimier Baubuche profiled columns
17. Steel drainage channel
18. Gravel and French drain
19. 50mm coarse sand
20. Geotextile water permeable membrane
21. 600x600mm Northumberland Buff stone paving slabs
Wall To Roof Junction:
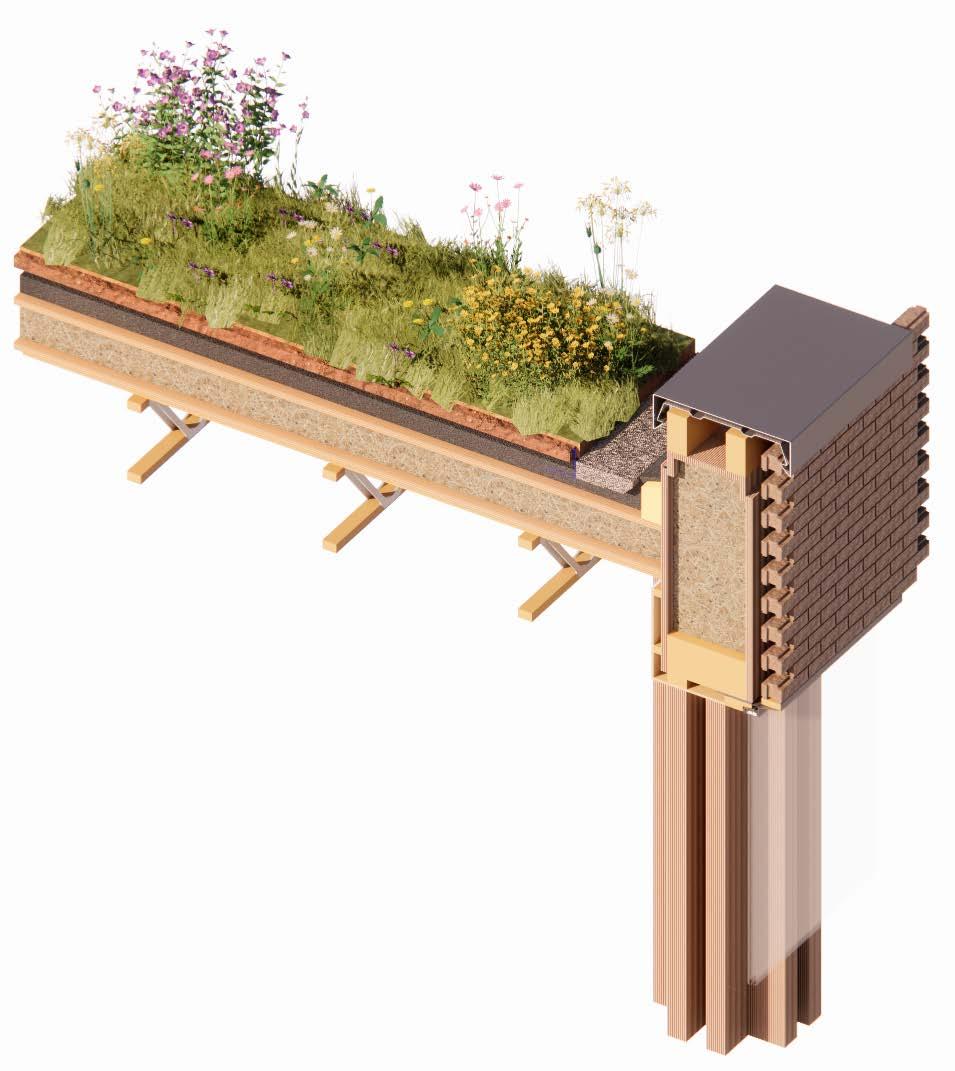
1. Pollemeier Baubuche Profile column 675x675mm
2. Pollemeier Baubuche Beam with shadow gap and led strip fixture
3. Web joist (420mm depth)
4. 38x75mm Timber battens (300mm Centres)
5. Velfac V200e energy windows
6. Plywood reveal
7. Insulation around window reveal
8. Pro Clima Intello Plus Intelligent vapour check and airtight membrane with Pro Clima TESCON No.1 Airtightness tape at the seams and over any holes from screws etc
9. Metsawood Kerto Ripa System SIP Cassette made up of KERTO LVL Q panels and S studs
10. 4 200X100MM Timber sections acting as a lintel and SIP Cassette termination
11. 400mm Hemp fleece insulation
12.
Lime-stabilised earth, dry-stacking brick
13. Steel reinforcement bar
14. Weatherproof membrane
15. Wall tie
16. Mesh to prevent bees and wasps nesting in the cavity
17. Timber lintel
18. 2 200X100MM Timber firrings
19. Aluminium parapet cap
20. BauderBLUE adjustable flow restrictor
21. Bauder waterproofing system
22. Bauder FMS600 protection layer
23. Bauder Re 40
24. Bauder RE substrate
25. Bauder filter fleece
26. Bauder biodiverse substrate
27. Vegetation with WB native wildflower blanket
28. Gravel Drainage channel
29. 200mm Hemp fleece insulation
This scheme would be comprised of 2 major packages of works – a public realm improvement, phased over 24 months and a building development as an extension to the existing Alphabetti theatre. This pre-construction plan is for the latter half of the works and focuses specifically on the extension build rather than the paving etc that would already be complete by this stage.
KEY:
1 - Changing rooms and showers
2 - PPE Storage
3 - Toilet Block
4 - Canteen/ Mess
5 - HSE Office
6 - Meeting room
7 - Plant
8 - Secure lock up
TCR - Tower Crane - 35 boom
TH - Turning head
CP - Car park
W - Water mains connection
P - Power mains connection
A - Carpentry workstation
B - SIP storage/ prepartion area
C - Stick system curtain wall station
Proposed build area
Temporary units
Ancillary
On-site Health and safety principles:
• Every worker on site must be provided with the adequate PPE before commencing work, this will be provided in the PPE store on site and the workers will have a changing facility on site.
• Before setting foot on site, each worker must have the relevant training and be signed off by an examiner – for a example a relevant CSCS Card for the activity they will be undertaking etc (Construction Builder Support [CBS], 2021)
• The removal of the existing windows and the floor plate as well as the extension build means that there will be a number of workers working at height i.e. 2m or more. These workers will be equipped with the appropriate fall protection – i.e. harnesses, fall nets, tool retention lanyards etc.
• Repetitive strain injuries can have a big effect on a workforce, yet they are some of the easiest injuries to avoid. Therefore, the handling of heavy components on site will be carefully monitored – no person should be lifting more than 10kg worth of weight at once. This applies to loads over 10kg too, for example a 30kg weight would require 3 workers.
• Construction is generally a dangerous industry and there are inherent risks attached to that fact. Therefore, there will be some hazards that can’t be fully eliminated. However, the risk can be mitigated and should be carefully considered to minimise the potential for harm as much as possible.
Risks that cant be fully eliminated will be mitigated by providing sufficient safety measures to reduce the likelihood of accidents. For example: provision of break spaces to prevent fatigue, implementing the relevant health and safety signs, and having a HSE on site that will ensure operations are running safely and in line with the health and safety principles outlined above.
PPE Provision:
The provision of the correct PPE is of paramount imporatnce for protecting workers. All of the following standards (below) are derived from SHE PPE: Complete guide to Personal Protective Equipment unless stated otherwise (SHP, 2022)
• Hard hats - The relevant standards are BS EN 397 and BS EN 14052
• Steel toe caps - The relevant standard for safety footwear is BS EN ISO 20345.
• Hi-vis clothing – The relevant standard for hi vis clothing is BS EN 471 + A1.
• Ear defenders - The relevant standard for the ear protectors is BS EN 352 Part 1.
• Safety goggles - The relevant standards are BS 7028 (Guide to Selection of Eye Protection for Industrial and Other Uses) and BS EN 166 (Specification for Eye Protectors).
• Gloves - BS EN 388 covers the specification
Fall Nets:
Due to the fact tha tthe proposal removes a part of a floor plate top open up a space in the existing building, there would have to be a sufficient net installed to prevent not only falling workers being injured, but materials and tools wouldn’t fall on others below.
Site compound: of gloves against mechanical hazards.
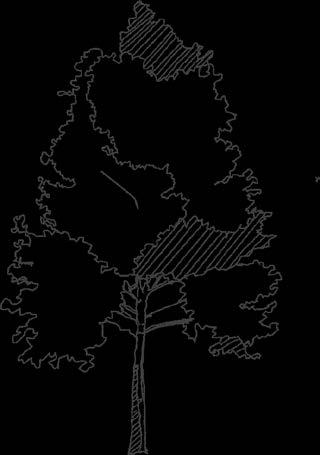
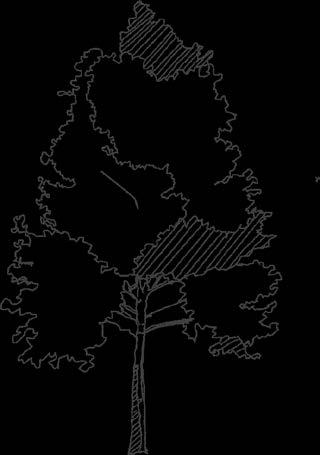
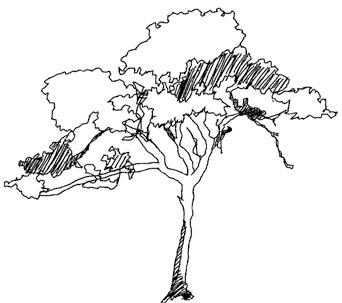
The Portakabins comprising the site compound have been arranged in a stacked configuration in order to reduce the overall footprint without comprising the facilities.
• Dust mask – there will be different standards of respiratory protection required for different tasks.
• Knee pads – knee pads and other body protection carry different standards and aren’t necessarily required – therefore workers may choose to not wear them however they would be provided on site.
• Safety harness – the different fall retention equipment will have different associated standards and will have to be thoroughly checked on a regular basis to ensure it is in working order.
Hammerhead tower crane (30m Boom):
The tower crane has a large enough boom to be able to reach ver the extension and existing building. It is also large enough to swing over the new public realm and site compound to move elements directly from HGVs or from the floor.
HGV Drop off Point:
Access for HGVs is essential for a smooth and seamless construction process. This has been positioned so that it is in the centre of the site as well as having a good connection to the road. The crane has a suffieciently long boom arm so that it can move components from the HGVs to a designated part of the site compound or lift them directly into the building.
Scaffolding:
Scaffolding is a key part of any construction project - this will allow for a temporary platorm for the removal of the existing windows as well as making the installation of the new windows and SIPs easier.
Temporary balustrade:
The partial removal of the existing floorplate would mean that there would need to be a temporary balustrade installed prior to the construction and installation of the new railing. This would be installedas soon as the floorplate has been removed along with the fall nets.
All information reffered to in the diagram to the right is taken from Approved Document B Volume 2 unless otherwise stated. (HM Government, 2022)
All exits are within the 18m maximum escape distance as outlined by table 2.1 (Office/shop and commercial - no more than 18m in one direction)
All exits are within the 18m maximum escape distance as outlined by table 2.1 (Office/shop and commercial - no more than 18m in one direction)
There has not been sufficent space left for a wheelchair refuge - the core would have to be redesigned.
The size and complexity of the floor plans of this building means that it will require an automatic fire detection system. This system will be primarily concerned with the protection of life as opposed to property. Despite the public nature of this building, a phased exit strategy would not be appropriate. The installation of an automated system would also eliminate the reliance on manual systems or staff operated systems. This would vary across the different types of spaces in the building so as to best prepare for the consequences of a fire in each specific space.
The stair case meets the width requirement for a building of 4 storeys with less than 270 people during a simultaneous evacuation (1000mm)
All information reffered to in the diagram to the right is taken from Approved Document B Volume 2 unless otherwise stated. (HM Government, 2022)
The size and complexity of the floor plans of this building means that it will require an automatic fire detection system. This system will be primarily concerned with the protection of life as opposed to property. Despite the public nature of this building, a phased exit strategy would not be appropriate. The installation of an automated system would also eliminate the reliance on manual systems or staff operated systems. This would vary across the different types of spaces in the building so as to best prepare for the consequences of a fire in each specific space.
The systems installed across the building would be: L3 – systems designed to warn of fire at an early enough stage to enable all occupants, other than possibly those in the room where the fire started, to escape safely before the escape routes become impassable because of fire, smoke or toxic gases. – in compliance with BS 58391.
• Most single story, contained spaces (e.g. offices and studio spaces) would be fitted with a point heat system
The fire detection method would vary across the building to suit the spaces:
• The larger atria would have to be fitted with a Aspirating Fire Detection system as the high ceiling heights would rule out the effectiveness of a point heat system
• The larger atria would have to be fitted with a Aspirating Fire Detection system as the high ceiling heights would rule out the effectiveness of a point heat system
• The plant room would be fitted with an infrared early fire detection system alongside a high-pressure mist system that would be capable of effectively suppressing a fire from the large pieces of machinery etc.
• The plant room would be fitted with an infrared early fire detection system alongside a high-pressure mist system that would be capable of effectively suppressing a fire from the large pieces of machinery etc.
The LVL frame structure will naturally char and build a layer around it that will protect it from fire. As this material is consistent and has a predictable char ratethe beams can be oversixed to give a suitable fire proof time of 120 minutes - this will be sufficient time to allow for evacuation and arrival of the firefighting team.
The LVL frame structure will naturally char and build a layer around it that will protect it from fire. As this material is consistent and has a predictable char ratethe beams can be oversixed to give a suitable fire proof time of 120 minutes - this will be sufficient time to allow for evacuation and arrival of the firefighting team.
+1500mm
+1500mm
4.2: BUILDING REGULATIONS: PART B
The stair case meets the width requirement for a building of 4 storeys with less than 270 people during a simultaneous evacuation (1000mm)
Exit Exit
The old, disused lift shaft has been converted into a dry riser. This carries pipework from the water tank to feed the sprinkler system throughout the building.
The old, disused lift shaft has been converted into a dry riser. This carries pipework from the water tank to feed the sprinkler system throughout the building.
There has not been sufficent space left for a wheelchair refuge - the core would have to be redesigned.
EXIT
The stair case meets the width requirement for a building of 4 storeys with less than 270 people during a simultaneous evacuation (1000mm)
EXIT EXIT
WT 45º
WT 45º
The doors to the fire safe core are outward opening, self closing (as outlined in diagram 2.4) and have a glass panel to see into a space on exit to see if it is safe.
The doors to the fire safe core are outward opening, self closing (as outlined in diagram 2.4) and have a glass panel to see into a space on exit to see if it is safe.
This door swings the wrong way to allow for a smooth and safe exit from the building.
This door swings the wrong way to allow for a smooth and safe exit from the building.
The doors to the fire safe core are outward opening, self closing (as outlined in diagram 2.4)
The new lift shaft also functions as a dry riser.
The ecape routes are not sufficiently protected and there would need to be a significant level of protection added to the large open spaces they pass through
The new lift shaft also functions as a dry riser.
The “dead end” zones do not comply with the 45 degree rule outlined in diagram 2.1
This door swings the wrong way to allow for a smooth and safe exit from the building.
MVHR system acts a smoke extractr system.
MVHR system acts a smoke extractr system.
MVHR system acts a smoke extractr system.
The “dead end” zones do not comply with the 45 degree rule outlined in diagram 2.1
The ecape routes are not sufficiently protected and there would need to be a significant level of protection added to the large open spaces they pass through
EXIT EXIT EXIT
DR DR 45º