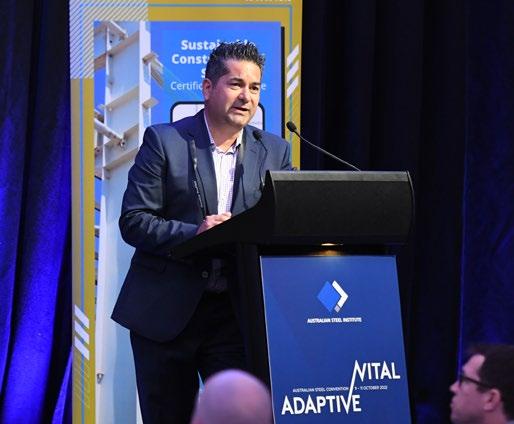
10 minute read
Case Studies
CASE STUDIES
The second session of day one featured four case studies that illuminated the innovation and adaptability that is alive and well throughout Australia's steel industry.
Advertisement
Lachlan's Line Bridge (subsequently renamed the Christopher Cassaniti Bridge)
Pablo Santos (Director, S&L Steel) provided a riveting overview of the $40 million Lachlan’s Line pedestrian and cycleway bridge. Believed to be the first of its type in the world, the eye-catching, bright blue double helix bridge twists and turns over Sydney’s M2 Motorway. At 178m in length, the bridge is a variable diameter helical steel truss bridge, curved on plan. The bridge weighs 335 tonnes, and has a maximum unsupported span of 70m. Of all the 3,600 steel plates used to fabricate the 335 tonne structure, no two are alike – every piece of steel has a different curvature, shape and thickness, and the helix varies 2.3m in its diameter in relation to the structural demand. This made for a complex process for the 14km of welding required for the bridge, undertaken by ASI member S&L Steel.
Murra Warra Wind Farm
Simon Preston (Group General Manager, Precision Oxycut, Allthread Industries and First Forge) presented on Australian manufacturing's place in the renewable energy market. According to Simon, the opportunities for steel in the national renewables market are huge. Simon also described the work that Allthread Industries has undertaken on the Murra Warra Windfarm. Constructed on a 4,250 hectare site some 25km north of Horsham in Victoria, Murra Warra is the first largescale wind farm to be built in the Wimmera. It is home to 99 turbines, capable of generating 435MW. Allthread Industries delivered a wind tower anchor cage solution for the 38 turbines installed during phase two of the project, including a unique, environmentally friendly alternative to the traditional grout pocket forming ingots.
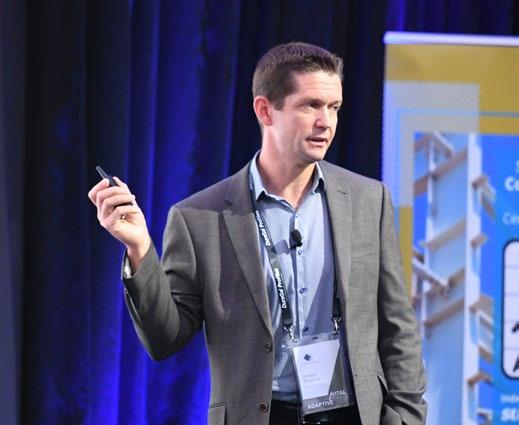
Morwell Government Hub
The Morwell GovHub is a $30 million, three-storey regional employment hub supporting economic growth, creating jobs and driving the industries of the future. Peter Blythe (Managing Director, Dynamic Steel Frame) described how Dynamic Steel Frame and Industry Cladding & Roofing came together to engineer, manufacture and install a facade framework design that features 18 light gauge steel modules that were craned into position and hooked onto the building. Each module was 8m wide and 14.5m high, and comprised over 3 tonnes of BlueScope's TRUECORE® steel, to form what could be the world's largest light gauge steel facade. The light gauge steel frames were prefabricated using an automated roll forming machine. This ensured the design was recreated perfectly to the millimetre. It also sped up the construction process; if the facade had been fabricated on-site, it would have required approximately $1 million worth of scaffolding.
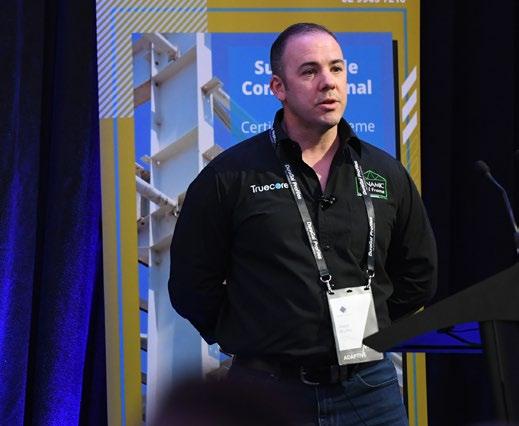
Kalbarri Skywalks
Kalbarri National Park is an iconic location, famous for its 80km gorge, coastal cliffs that plunge more than 100m to the ocean, striking wildflowers and many recreational activities. It is located 160km north of the nearest major centre of Geraldton and 500km north of Perth. The two cantilevered Skywalks provide exhilarating views, taking visitors beyond the edge of the gorge, and 100m above the Murchison River. Andrew Jens (Structural Engineer, TerpKos Engineering) described the process of designing the two 100m high Skywalks, which project 25m and 17m beyond the cliff face and complement the existing natural beauty of the surrounding area. Completed in April 2020, the Skywalks are quickly becoming a major attraction for Kalbarri, and have already prompted a boost to Western Australia regional tourism.
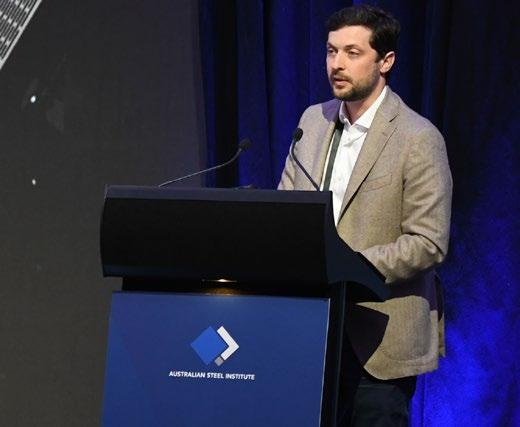
Pablo Santos (Director, S&L Steel)
Simon Preston (Group General Manager, Precision Oxycut, Allthread Industries and First Forge)
Peter Blythe (Managing Director, Dynamic Steel Frame)
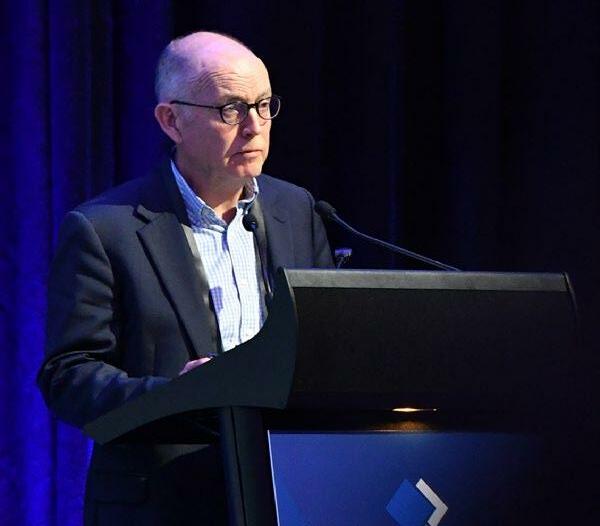
Shane Murphy (Executive General Manager Manufacturing, InfraBuild)
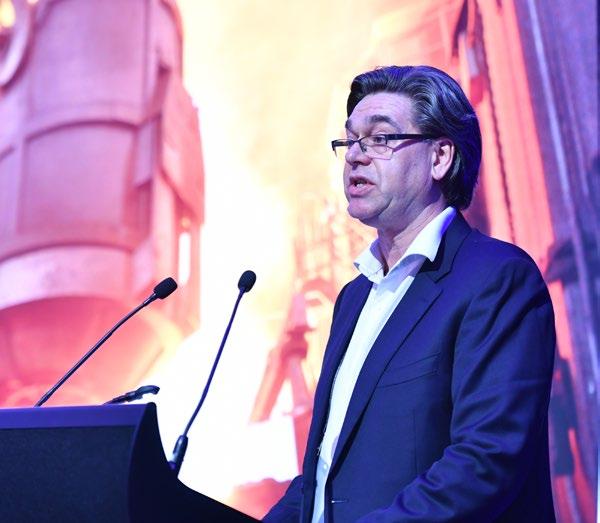
SUSTAINABLE STEEL. SUSTAINABLE FUTURES.
InfraBuild's Executive General Manager Manufacturing, Shane Murphy, delivered a keynote address. Shane acknowledged the growing global conversation around the decarbonisation of the steel industry and pointed to our ‘building futures through sustainable steel’ mission as proof of our commitment to the cause. He outlined work being done by InfraBuild to map its decarbonisation journey and the initiatives we are exploring to meet our Carbon Neutral 2030 (CN30) ambition.
“Decarbonisation cannot happen overnight, but it must happen. And we firmly believe we can achieve our ambition of carbon neutrality by 2030,” Shane said. “Built environments account for 25% of global emissions. And now, more than ever, the market is looking to manufacturers to enhance the sustainability credentials of their projects by supplying lower embodied carbon materials.”
Shane said pursuing these goals will require a shift in the way InfraBuild operates, how they source, use, consume and think about energy and feedstocks, and how they engage with stakeholders. But InfraBuild is well-positioned to make this transition, owing to their Electric Arc Furnace (EAF)-based steelmaking processes and the ability to eliminate 76% of some of emissions by switching to renewable electricity.
Shane also spoke about the growing role of data to meet the market’s expectations on traceability and how this provides customers with confidence and certainty. “In our industry, traceability used to stop at the mill gate when the product left, but through some great work from our InfraBuild Fulfilment team, customers will soon have visibility right up until the product is delivered,” Shane said.
Shane said it was incumbent on the steel industry to shape its role in Australia’s future and why sovereignty of supply is critical to success. He also called on the industry to work together to help the country achieve its environmental, social, and economic sustainability objectives. “Throughout the industry’s proud history, we have provided countless people with an opportunity to pursue the vocation they love. Whether it be in steelmaking, transport, finance, whatever their career may be, the industry offers myriad opportunities for domestic and international workers. In the context of the pandemic we’ve just been through and the risk it posed to people’s livelihoods, the ability to continue working was something our workers appreciated greatly,” Shane said.
WORKING TOGETHER FOR GROWTH
John Nowlan (Chief Executive, Australian Steel Products, BlueScope) was a keynote presenter on day one of the Convention. According to John, BlueScope is focusing its efforts on maximising its domestic steel manufacturing.
"We have the plate mill running seven days per week, and the metal coating lines up to seven day a week. We've increased the capacity of our paint lines in Queensland and New South Wales. We've also worked on our rail, transport and logistics capacity."
BlueScope is investing in its future metal coated capacity by building an additional metal coating line. John explained that this project is expected to be approved at the end of this year, and receive planning approval from the New South Wales Government. "We currently have six metal coating lines in Australia. By adding a seventh, we will add an extra 240,000 tonnes of capacity per year. The new line will be adjacent to Western Sydney paint line, which will increase galvanizing capacity. We've invested in a second coil plate line to produce TRU-SPEC® steel."
BlueScope is also set to upgrade its Plate Mill, having received a Modern Manufacturing Initiative (MMI) grant from the Federal Government. The grant, which is $55.4 million, will catalyse a further $161.6 million of investment by BlueScope and its partners Keppel Prince, Bisalloy and the University of Wollongong, and will create approximately 200 new jobs in steel manufacturing, plus up to 1000 jobs in associated industries.
BlueScope's No. 5 Blast Furnace at Port Kembla is expected to reach the end of its life sometime between 2026 and 2030. As such, the relining of the No. 6 Blast Furnace is being planned—this will be critical in ensuring the future of steelmaking in the Illawarra region.
John Nowlan (Chief Executive, Australian Steel Products, BlueScope)
"All this investment benefits local industry. For every $1 million invested, we create five full time jobs, $2.8 million is contributed to the economy and $1.1 million is added to the Australian GDP," said John.
"Steel is critical to the world’s future, underpinning the transition to renewable energy. There is at least two million tonnes of additional steel required to meet the 2030 renewables targets. And another 10 million tonnes to meet the 2050 targets. This capacity has to be built."
MISSION IMPOSSIBLE: ACT COVID-19 SURGE HOSPITAL
Andrew Fowler (Managing Director, Austruss) presented a highly engaging case study on the ACT's COVID-19 Surge Hospital. In the grip of the global COVID-19 pandemic, pre-fabrication specialists Austruss and construction company Manteena and delivered a 17,000m2 51-bed medical facility in just 36 days. Working day and night shifts, the team had upwards of 130 contractors on-site and completed 22,000 man hours. The facility was built using pre-fabricated wall frames and roof trusses made from TRUECORE® steel, manufactured off-site by Austruss. The brief required that the design be flexible, allow hospital live loads, withstand high wind loads, be reusable, and be able to be packed in a shipping container and shipped overseas at end of use. Plus, it had to be designed to Australian Standards and on-site within just eight days.
According to Fowler, "We took each section of the building and broke it into certain elements. The only way we thought we could achieve the compressed delivery timeframe was to use a simple kit of parts that were interchangeable. So we designed trusses on either side of the building and they were all standardised. The walls were all standardised. We came up with a telescopic wall frame system to give flexibility to the whole assembly process. The key was as many repeatable elements as possible to simplify the delivery process."
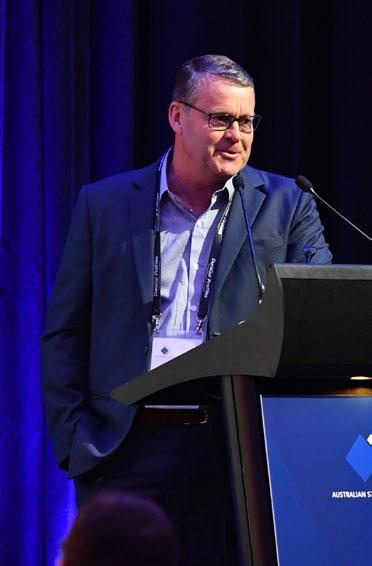
REGULATORY REFORMS: THE STATE OF PLAY
Bronwyn Weir (Director, Weir Legal Consulting) provided an overview of three key reports released over the last few years, along with the status of the recommendations in these reports: • Review of Security of Payment Laws: In 2017, the Government commissioned this national review to examine ways to improve consistency in security of payment legislation and enhance protections to ensure subcontractors get paid on time for work they have done.
According to Bronwyn, implementation of the recommendations in this report has been patchy. The key recommendation was that a single set of laws, applied uniformly across the country, be adopted by all states and territories. There has been absolutely no effort to implement this. • Building Confidence: In 2018, Bronwyn was commissioned by the
Building Ministers’ Forum (comprising 11 Federal, State and Territory
Ministers) to co-author the Building Confidence report with Professor
Peter Shergold. When this report was released, industry voiced their support for the implementation of the recommendations in a harmonised fashion. However, not a lot of action has been undertaken by Australian governments, particularly the Federal Government. • Senate Enquiry into Non-conforming Products: As Bronwyn described, conformity assessment schemes for building products in Australia lack rigor, and all are voluntary, leading to fraudulent practices. The NCC needs further strengthening in this area.
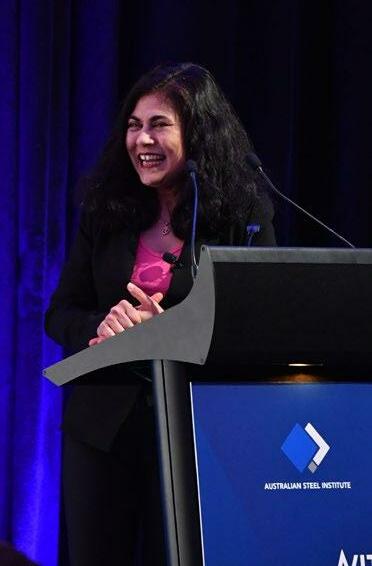
A SMART VISION FOR A SUSTAINABLE FUTURE
Veena Sahajwalla (Director, SMaRT at University of New South Wales) is renowned for her internationally commercialised EAF ‘green’ steelmaking process that is utilising millions of waste tyres otherwise destined for landfill as a partial replacement for coke. The conceptual and scientific breakthroughs that underpin ‘green steel’ have paved the way for an unparalleled portfolio of new ‘waste to value’ science, built over years of research at the SMaRT Centre, with valuable contributions from industry partners. This approach is enabling her to transform many of the world’s most challenging waste streams -like e-waste, automotive waste, batteries– into value-added materials that can be redirected back into manufacturing. According to Veena, "When we talk about waste resources, we have got to start questioning the fundamental elements and molecules that make up that material. We need to prove, in an engineering context, that the waste is, in fact, a functional raw material. We need collaboration between industry and research organisations. We need to look at new technological pathways and new innovative products together. Why wait for products to be shipped from overseas—taking months and months—when we have own materials and products available locally? What are our responsibilities as steel makers and consumers? As people, we consume a whole range of products, so why not take responsibility for reforming them into their next life?"
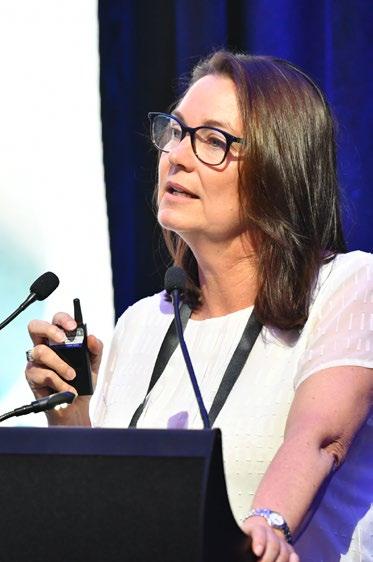
Andrew Fowler (Managing Director, Austruss)
Bronwyn Weir (Director, Weir Legal Consulting)