
6 minute read
Premier Steel Technologies: The Custom Rollforming Experts
Premier Steel Technologies is a specialist custom rollforming company based in Wetherill Park in Sydney. Established in 1980, Premier Steel has earned an enviable record for the manufacture of a wide variety of custom, high quality rollformed products.
Premier Steel Technologies—originally known as Premier Rollform—was founded by Hilton Dupen and lifelong friend, Tom Morsillo, in 1980.
Advertisement
According to Colin Dupen (Technical Manager, Premier Steel Technologies), "My father, Hilton, had in-depth knowledge of rollforming, having been involved in quite a large rollforming company. His business partner, Tom, was a builder. Initially, the company was based in a small factory at North Parramatta in western Sydney. Hilton and Tom took a 50-50 share in the company, and kicked it off with one product. That product was an angle brace, used for timber framing for houses." company ownership back with key personnel here in Australia,” said Col.
"As the company evolved, it eventually started manufacturing other products and quickly outgrew the space in North Parramatta. So, Premier Steel moved to Smithfield into a larger facility. The company soon took over the factory next door and got involved in the business of one of the neighbouring companies—a steel house framing company," said Col.
In 1995, when Tom stepped away from Premier Rollform, Singapore-based company, Techsteel Corporation bought his share of the business. It was then that the company name was changed to Premier Steel Technologies.
In 1998, Premier Steel outgrew its premises again and moved to its current location in Wetherill Park, a 2,500m2 factory. With a workforce of 16 people and a fleet of 15 rollforming machines, Premier Steel concentrates on custom rollform manufacturing.
"When Hilton retired in 2001, Techsteel Corporation took control, making us wholly owned by a Singaporean company. Techsteel then shared some
CUSTOM ROLLFORM MANUFACTURING
Premier Steel is well known in the rollforming industry and has earned a reputation as an original and innovative manufacturer. The business has expanded rapidly since it was first established, manufacturing challenging profiles in various metals. "We are constantly working with newly designed products. Customers will call and say, 'I want to make this component, can it be rollformed?'. We’ll assess the product and assist with product development. We’ll work with the customer, do all the tooling design and roll the product for them. We deliver a quality, cost effective product, so that the customer doesn't need to worry about the manufacturing process," said Col.
Since 1980, Premier Steel has boasted an extensive client and product list. With products for all types of businesses and hundreds of thousands of metres
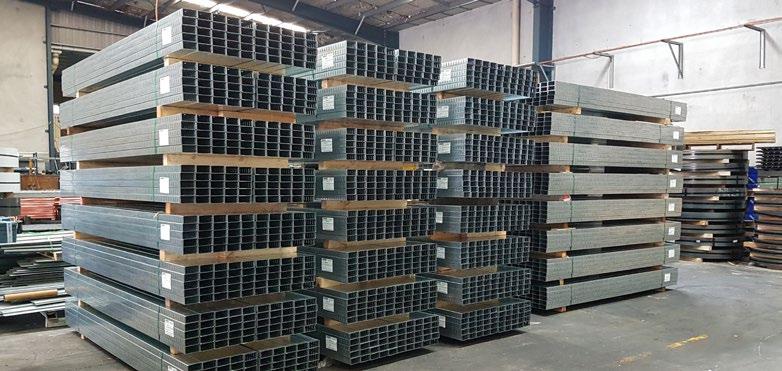
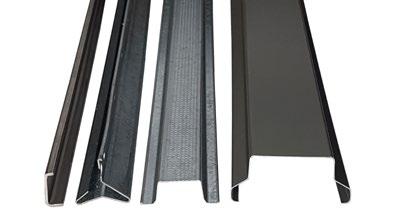
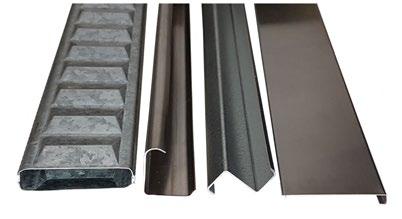
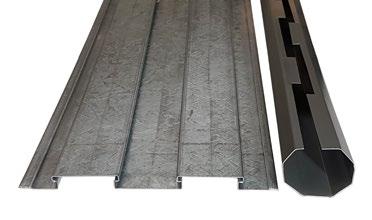
of products successfully designed and manufactured, the list includes products made from mild steel, ZINCALUME® steel, galvanised steel, COLORBOND® steel, hi-tensile steel, stainless steel and aluminium, in metal thicknesses ranging from 0.3mm to 4mm.
"We’re involved in a range of industries and products, including fencing, electrical support systems, steel framing, general angles, packaging companies, building products, and road-side posts," said Col. "We don’t make any generic products, like purlins or corrugated iron. There are a lot of companies that make these sorts of products. Our specialty is specific, custom products made according to a client’s request. We very often develop new products."
Premier Steel becomes the manufacturing partner for their customers, taking on the production schedule, quality control and on-time delivery of products.
"Our team consists of a number of people who have been involved in the industry for a very long time. They have exceptional, in-depth knowledge of the rollforming process. This means that we can assist our customers in developing products with them. We sit down with our customers, and say this will be difficult to rollform, but if you do this and that, it will cut your production time and costs down. This custom product development is a key aspect of the level of service we give our customers," said Col.
Premier Steel manufactures just one of its own products: TRUEDEK® Steel Decking. This is a permanent concrete formwork system, purpose-designed to bring a broad and clear range of practical advantages over typical metal decking systems. The system is lightweight, modular, easy to handle and made to specification. With truss heights of 90mm, 110mm, 140mm and 160mm, the most noticeable difference is that TRUEDEK® concrete formwork systems can span over 7m, and typically requires no propping.
CUSTOM MACHINERY
"Premier Steel used to build a lot of custom machinery. At one stage, this service accounted for approximately half the business," said Col.
From 1992, Premier Steel developed a relationship manufacturing several products for BHP. As a result, Premier Steel was commissioned by BHP's Export Division in Port Kembla to rollforming machines. We'll hunt down used rollformers, overhaul them, install our customer’s tooling on them, and make the customer’s products on the refurbished machine," said Col.
THE FUTURE
Colin is positive about the future, not only for Premier Steel, but for the entire Australian steel industry.
"We’ve noticed a trend recently where a number of our old customers are coming back to us. Five to 10 years ago, these customers offshored their manufacturing to China because it was cheaper. But that's just not the case anymore. One customer told me recently that less than 12 months ago, he was bringing in products from China at a cost of about $5,000 a container load. Now, that same container load is $13,000. So it's just not viable. Adding to this are issues around freight delays and delivery dates being constantly pushed back."
"Customers are bringing their manufacturing back to Australia. Industry needs to embrace this opportunity, rather than relying on international supply chains."
"We’re always looking at new projects and new products. Every week, we have a new inquiry from a new customer, and we expect this to continue to grow. We're excited about the future of the industry—not only for Premier Steel, but the entire Australian steel supply chain," said Col.

design and build two state-of-the-art production lines to make the internal and external protective rings for their coil packaging facility.
After several months of designing and building, both machines were successfully trialled and delivered to BHP's Wollongong premises and are still in operation today.
Premier Steel was also commissioned to build the entire production facility for a steel house frame company, Uniframes, which was one of the first companies in the building industry to utilise light gauge hi-tensile steel profiles. The facility included eight production lines, consisting of a top and bottom plate wall profile, stud machine, top and bottom chord truss profiles and an in-line high frequency welding machine to make the truss webbing. Each machine was fully integrated with CAD design and interface software and could be programmed to manufacture the exact lengths for each frame design, which were assembled on specialised truss and wall assembly tables, designed by Premier. The system won an Australian Design Award and was the first light gauge steel house frame design to achieve a cyclonic rating.
"In recent years, we've downscaled this service quite a bit. Today, we will build custom machinery for select clients, and we also do refurbishing of
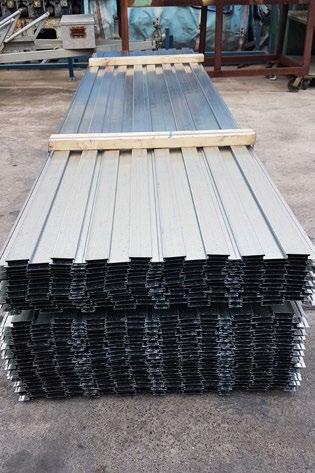