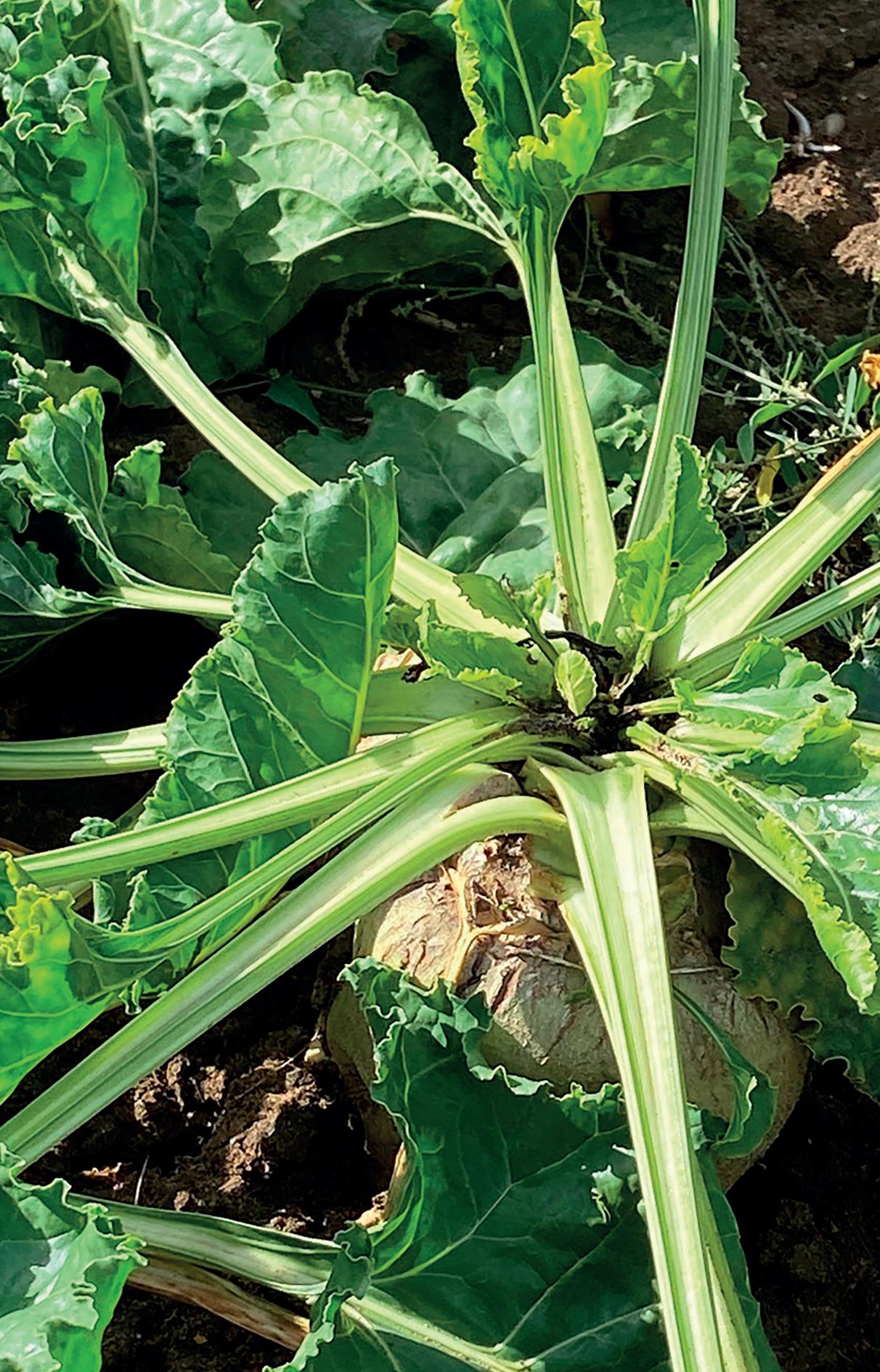
15 minute read
Beet moth pest threat to sugar beet crops
Growers attending a BeetField event in Norfolk were updated on the damage being caused by a hitherto rare pest of sugar beet in the UK. Teresa Rush reports.
Beet moth pest threat to sugar beet crops
Insect pests are agile opportunists and this summer’s hot, dry conditions appear to have opened the door to a new threat to sugar beet.
Growers in the Bury St
Edmunds beet factory area in
Suffolk and Cambridgeshire have been reporting black heart symptoms in their crops and the same damage was clearly visible in early September in the crop at a British Beet Research
Organisation (BBRO) BeetField event at Fersfield near Diss, on the Norfolk/Suffolk border.
Had the symptoms been seen earlier in the season, in May or
June, downy mildew or boron deficiency would have been suspected, BBRO head of science Prof Mark Stevens told growers attending the event.
“But if you get your penknife and start digging around in these heart leaves, you’ll probably start to find larvae probably starting to show in Cambridgeshire back in May. And it’s been very much favoured by the weather pattern that we’ve had. It likes it warm, and it likes it dry. And unfortunately, with the dry conditions being so prolonged, these larvae have probably been able to go through two if not three generations.”
Check crops
He advised growers to go back to their farms and check their beet crops.
“You’ll probably find four, five, six larvae per crown and what they’re doing is feeding on the inner heart leaves and potentially are grazing out the heart all together.”
Control is difficult, but heavy rain events, thunderstorms and even irrigation will often destroy the larvae, which are normally regarded as a transient problem and not really an issue.
More than 90% of the BeetField site was affected and there is also damage in BBRO trials. Crop damage is wide-
PROF MARK STEVENS
which are anywhere from a couple of millimetres to a centimetre long and vary from light green to dark green, red, purple and even black. And, unfortunately, it’s the larvae of the beet moth.
“Beet moth is something we’ve been keeping an eye on. We did see it in 2019 at about this time of the year. But I think from what we now know it was
Also in this section
20 Clamp considerations for successful storage 24 Yields up in an historic harvest 28 Growing for gold with new spring bean 31 N prices set to remain high 35 Funding helping shape future crop production 38 CropTec seminars to analyse costs and climate change 40 Improving wheat resilience through genetics
Take time to assess varieties on-farm
JWhile the summer’s drought put many sugar beet crops under considerable stress it has provided an opportunity to measure drought resistance in sugar beet varieties, said BBRO head of knowledge exchange Dr Simon Bowen, who encouraged growers to assess the performance of different varieties on their farms.
“Take the opportunity to see how each of the varieties is performing and recovering because there are differences,” he said.
Canopy recovery is one aspect, but final root weight
Black heart symptoms indicating beet moth larvae damage in a sugar beet crop near Diss, Norfolk, on September 8.
spread along the A14 trunk road corridor through Suffolk and into Cambridgeshire.
Chemical control options are
varieties on-farm
and sugars will also need to be measured, he added.
“But there are some quite big differences. We’ve been walking the Recommended List trials and scoring them.”
Next season
Looking ahead to next season, he urged growers to think about the key traits in the varieties they have ordered.
“Because using those in a tactical way can give you an advantage, whether you’ve got BCN tolerant varieties or more specialised ones such as AYPR or early drilling.
“Often in a drought year we see a lot more BCN patches in fields. You will have an opportunity to soil sample if you want to make sure of that, but make a note where you’ve seen it and make sure you deploy those BCN varieties in the right fields next season.”
There is concern BCN levels are increasing, but with no data to back this up a survey is planned within the next couple of years, said Dr Bowen.
Early autumn is also a good time of year to look at differences in levels of foliage disease across varieties.
“It is really quite important to use that information when it comes to where you may put your varieties next year, particularly in the context of fields which you’re going to earmark for later lifting.”
limited, and label approvals tend to be specific, targeting silver Y moth for example, although cypermethrin has an approval for general caterpillar control in sugar beet. There is also a physical challenge with getting an insecticide spray to where it is needed.
“The problem with this is that they [the larvae] are embedded within the heart. You cannot get the product to them and you really need that contact activity to try and control them,” said Prof Stevens.
Spray volume
A spray volume requirement of 600-1,000 litres per hectare is also adding to the challenge.
At the BBRO Morley site near Norwich, damage levels had increased from less than 1% of the crop affected in early August to 10-20% by early September.
“They are damaging the heart but they are not completely killing it out and that’s really important. I hope they will come back but if you lose the apical dominance what you are going to get is a late multi-crowning effect and smaller leaves and that will potentially have an impact on how these crops grow and accumulate sugar as we go through the rest of the autumn.”
Questioned on the lifecycle of the pest, Prof Stevens said it overwintered on chenopodiaceae species as well as on beet or in the soil surrounding beet.
“I’m not sure how cold it would need to get to take it out. We’re also learning as well as trying to work out what’s going on. There is some work in eastern Europe looking at neonic sprays that may have efficacy, but the problem is you need something that’s going to be systemic to get into the plant or something, as with the pyrethroids, with a high water
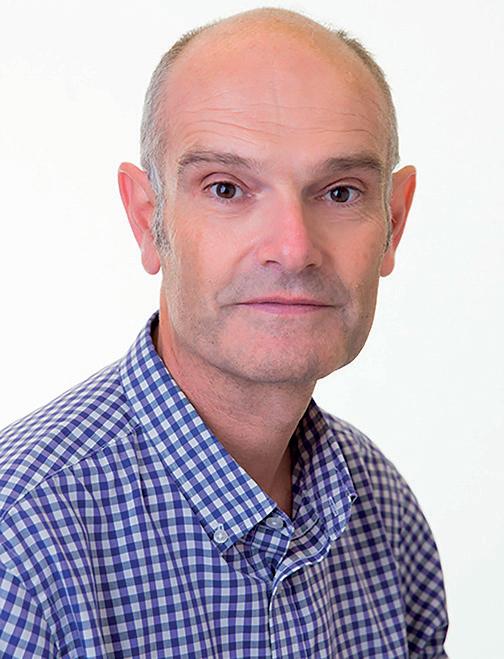
PROF MARK STEVENS
volume to try and get at it because once it’s protected, it’s a bit more like leaf miner – as soon as it goes into the leaf you are struggling to deal with it.”
Beet moth is a Mediterranean pest that with climate change and climate volatility has started to head further north, he added.
“It’s probably something we’re going to have to either live with or potentially think about alternative strategies [for control].
“But if you haven’t walked your beet recently, it may well be worth just having a look.
“It [beet moth] may just be transitory on the back of this summer, but it has now got a foothold, more so than I would like,” said Prof Stevens.
DR SIMON BOWEN
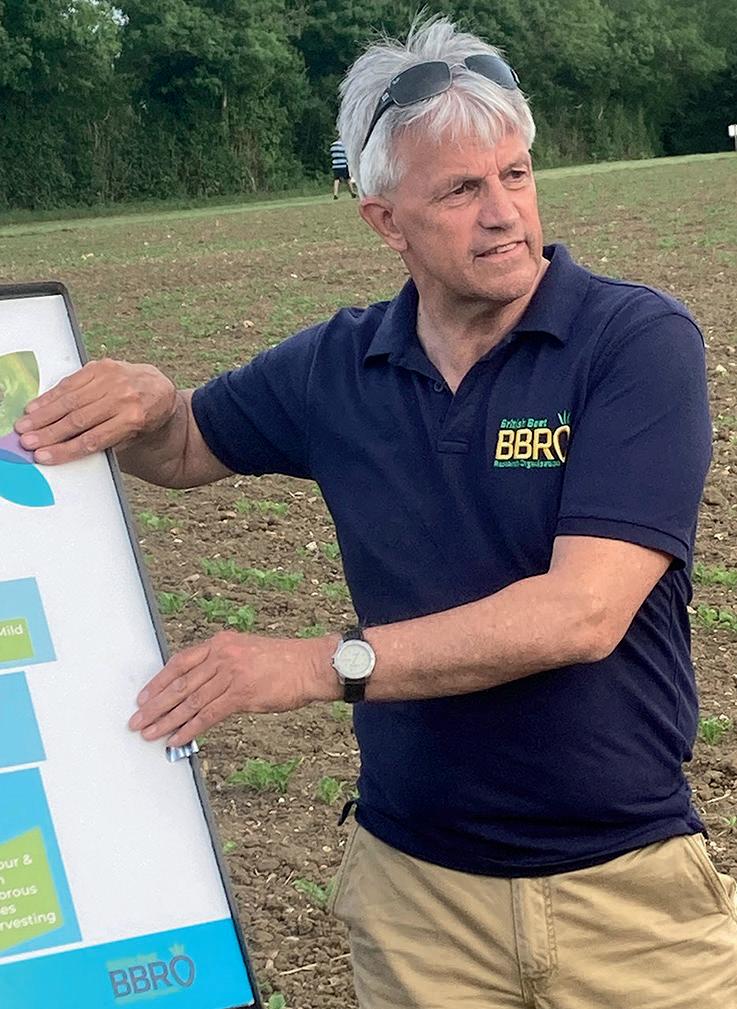
Consider the relationship between harvester output and compacting capacity when filling a clamp.

With maize silage volumes down after a hot, dry summer, getting clamping right will be even more important this season. Teresa Rush finds out more.

Clamp considerations for successful storage
Do we know as much as we ought to about storing silage for use in anaerobic digesters (AD)? Can we learn from experience overseas and improve silage quality and gas yields in UK AD plants?
These are questions occupying the mind of Will Wilson of silage storage expert Ark Agriculture, after more than a decade of building silage clamps across the UK.
“We have a phenomenal amount of value going into AD plants,” he says, reflecting that this year’s silage crop is possibly the most valuable silage growers will have made.
“You may have drilled this year’s silage at last year’s prices, but you will be valuing it at this year’s prices,” he says.
Which makes any losses – and loss levels of up to 20% through fermentation and aerobic spoilage are not uncommon – even more costly.
Mr Wilson would like to see clamp design move up the priority list when AD plants are being designed and constructed. Clamp design is not complicated, but it is very easy to get wrong, he says.
Drainage
“You will look at diagrams and it will be a square box drawn with a ruler and it has no detail about the drainage or capacity.
“All it will say is there is a four to five metre-high back wall and it has three bays. So, it will be length times width times height equals capacity, but what we know from experience is a lot more detail needs to be thought about at the early stage to get the design right.”
A scenario Mr Wilson often encounters is a lack of capacity.
“Clamps went into planning that were maybe 4.5m high, they were too wide, too short and we would end up with a scenario where a clamp to store 10,000 tonnes had to store 20,000t. Initially there may have been plans to build several extra clamps but they never happened.”
What then happens is that clamp walls are overloaded, leading to collapse, which increases the risk of a pollution incident.
Choice of clamp base is another area where there is room for improvement, says Mr Wilson.
“We see a lot of plants that were built with concrete; it was a cheaper solution at the time. But we are now seeing after 10-15 years that concrete has not worn as well as asphalt, especially on the expansion joints. And you are left with fewer options
WILL WILSON
to repair a concrete base than you have with an asphalt base.”
These issues should be considered on day one of the planning process, along with contingency plans and how Environment Agency requirements will be met.
“A contingency plan might be AgBags, a long-term plan might be to have a budget for future extensions to the clamp or satellite clamps, neither of which are quite as good as having capacity on site.”
Probably the most logical way of understanding how strong a clamp’s walls will be is to think about axle load, says Mr Wilson.
This indicates the maximum weight of compacting machinery that can be used on the clamp and how high up the panel can compaction safely occur. Modern clamp machinery can weigh more than 20t and compacting machinery will have two axles, which means maximum axle weight would be 10t.
“So that is something you might want to ask anyone who is building your clamp. Can you express your design in terms of axle loads?
But for those with existing clamps, the first and obvious thing to do is look after it, says Mr Wilson.
“People forget about silage clamps and their day-to-day maintenance.
“Clamp drains, walls, joints are all important. You can get big problems with silage clamps that you have not maintained; it is going to cost you a lot of money to sort them out in the long term.”
He recommends plant operators pay attention to joints where a concrete base meets an asphalt base.
“Those areas are really important to pay attention to because what happens is the joints expand and leachate goes underneath and can travel under the base and undermine the walls.”
Filling the clamp is all about reducing the amount of air in the silage and creating a high level of anaerobiosis – the anaerobic condition which stops silage breaking down and ensures that the energy that growers have spent so much money trying to bring into the clamp is retained, says Mr Wilson, who has several tips for creating the optimum clamp conditions.
“If you are moving material from a field to the AD plant and it is travelling a long distance, you want it to be coming in a regular pattern. You do not really want to have the first 10 trailers of the day arrive all at once. I know several AD plants where contractors set their people off staggered times.

Logistics
“The logistical exercise of moving hundreds of thousands of tonnes of silage is a military operation when we start talking about bigger plants.
“So one of the golden rules is basically a third of the weight of the grass and a fifth of the weight of the maize that comes into your silage camp per hour should be on the clamp’s compacting machinery.
“So, 100t of maize per hour arriving in the clamp equals 20t minimum weight of compacting machinery on the clamp.
“But 100t of maize arriving into a clamp is nothing. There will be plants that do 100t in 20 minutes. In which case you need to upscale your compacting machinery or slow your harvesting down, but it is almost impossible to slow down a contractor.”
Silage layers should be no thicker than 20cm and compacting machinery should move slowly across the clamp.
“The faster you go, the less compaction you achieve.”
An emerging trend within the last couple of years has been to either leave clamps uncovered or cover them with a layer of digestate, to reduce labour costs and the amount of plastic waste.
“I can see all the reasons why operators do not want to be involved with uncovering and re-covering clamps but the more we look into this the more we understand that the losses are phenomenal,” says Mr Wilson, who cites recent research conducted at a plant in Northamptonshire comparing a digestatecovered clamp to one covered with proper sheeting.
Losses were found to be about 40-50% where digestate was being used to cover the clamp.
“Which is a phenomenal amount of money,” says Mr Wilson.
“And there are other implications of not covering or covering with digestate; the loadings on the walls increase massively because your clamp is absorbing a huge amount of rainfall rather than letting it wash off.
“Environmentally, you are putting a lot more stress on your leachate collection because you are not collecting rainwater, you are collecting slurry that comes off the digestate that then fills your drains.”
Other points to consider include the oxygen transmission rate of silage films, which should be low as possible, and use of sidewall sheets.
“Sidewall sheets are still a no-brainer. I know people do not want to use them, but they do such a good job of protecting the walls and creating tight seals around the edges.
“Hopefully, we can develop new products that remove the labour intensity of these solutions. But at the moment, the best thing to do is try and engineer out the labour requirements,” he says.
Safety
Looking to the future, he suggests clamp safety is one of the biggest challenges facing AD plant operators.
“We have not really addressed the problem that silage camps are probably the most dangerous structures on an AD plant. You send operators to work at height on unstable surfaces to uncover and re-cover silage clamps and they have to do that in all weathers. We have to
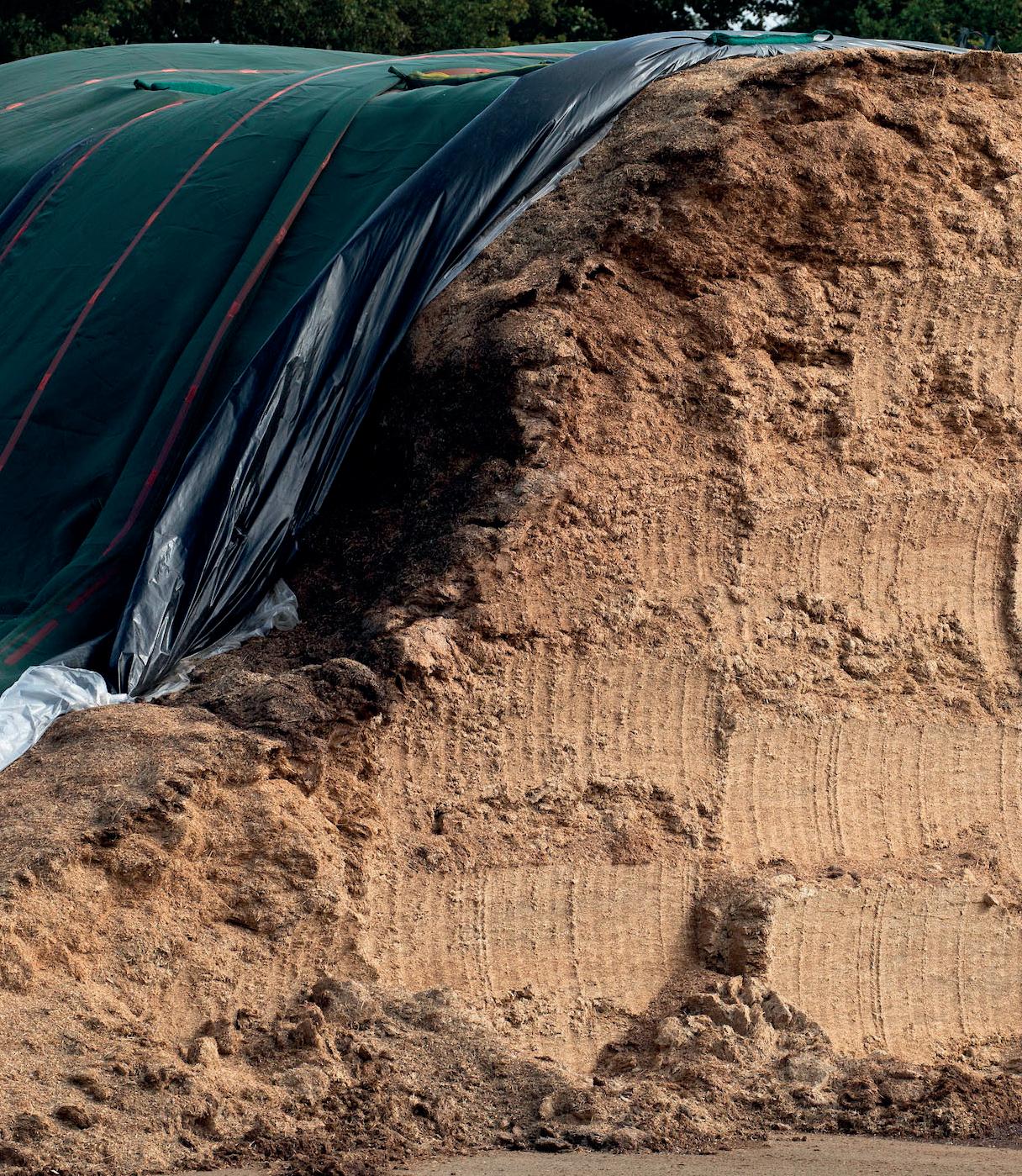
Reducing feedstock storage costs is a key challenge for AD plants.
More information
JWill Wilson was speaking at an Anaerobic Digestion and Bioresources Association (ADBA) clamp management and compliance training event.
For more information on ADBA, visit adbioresources.org
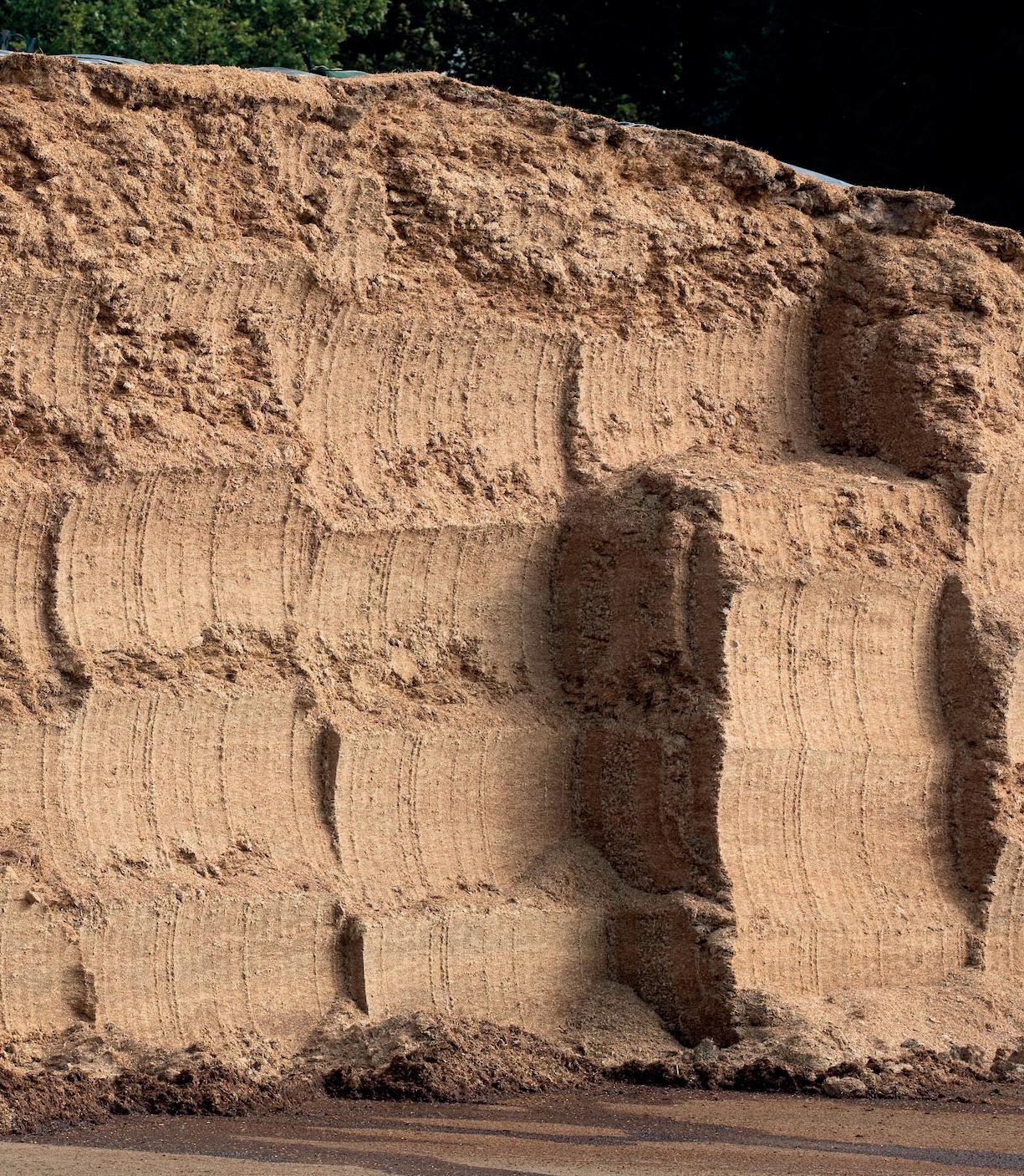
work out how we can help making uncovering silage clamps safer.”
Storage costs make up a large proportion of the costs associated with silage and there is room for improvement, says Mr Wilson.
“It is all relative to the cost of the value of the silage but how do we reduce the cost? How do we make silage covering simpler? How do we automate more of it?
“It is a real challenge, especially when we have clamps that aren’t really designed well to begin with.”
And he highlights issues around the environmental impact of silage production for AD, not only in terms of pollution, but the environmental cost of losses too.
“If we’re throwing away 20% of our silage, we have already burned the diesel to do that. If we could reduce that waste by 5%, we could make a massive difference to the carbon footprint of our feedstock, which in the future may become really valuable,” Mr Wilson concludes.
Clamp design considerations
rWhat is the maximum fill height of the finished clamp across the face? rIs it only designed to be filled level with the tops of the panels or can it be filled higher? rWhat is the density of the silage the clamp is designed to hold (t/cu.m)?
Grass, maize and wholecrop have different densities, which can also be expressed as dry matter percentages. rHow close can the machinery used on the clamp be driven to the edge of the panel?
Some designs mean that compacting machinery cannot operate within four metres of the inside edge of the wall, which is a significant flaw in a clamp that requires even distribution of the weight of compacting machinery. rWhat is the maximum weight of the compacting machinery that can be used on the clamp and how high up the panel can compaction safely occur?
The best way to understand this is based on axle weight. Source: Ark Agriculture
TODAY’S SPREADING TECHNOLOGY FOR TOMORROW
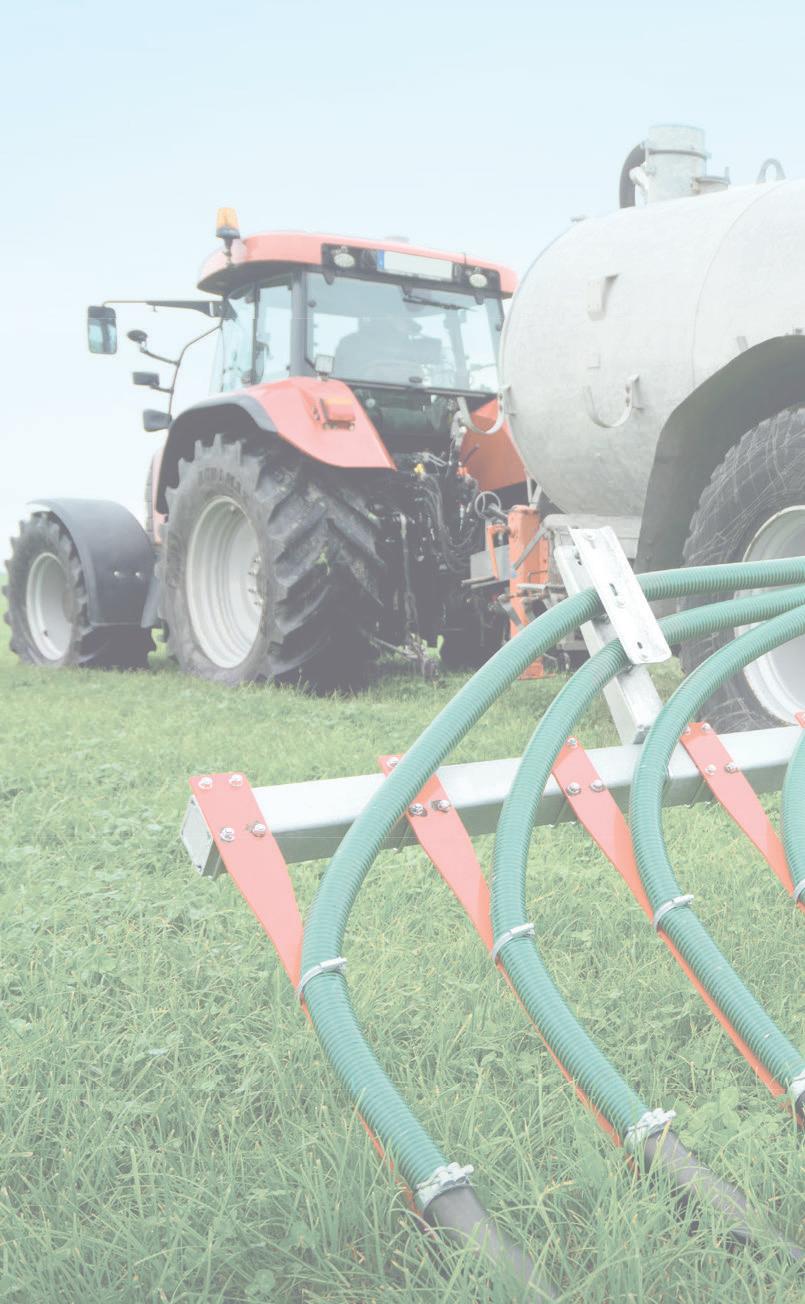
Universal, reliable and easy to maintain: UniSpread and ExaCut ECL. Invest in technological advances that take you further! For example, in the UniSpread universal technology, available as dribble bar linkage or trailing shoe system. Combined with Vogelsang ExaCut ECL precision distributor, you will have the highest distribution accuracy, even for small working widths. Vogelsang offers the right technology for every need: whether on large or small farms, on grassland, arable land or growing crops.
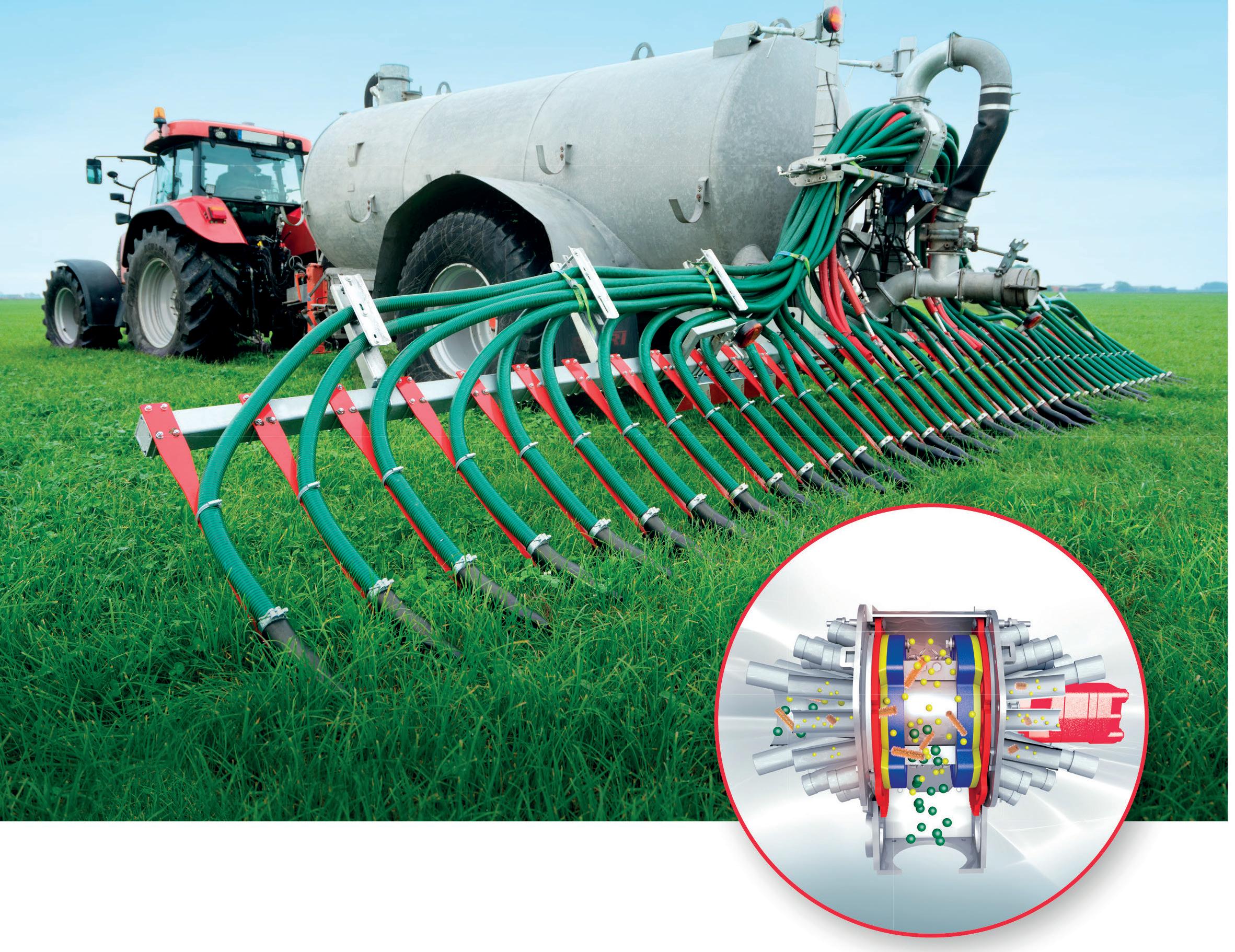
VOGELSANG - LEADING IN TECHNOLOGY vogelsang.info/uk/unispread
Grants available on Vogelsang application equipment
Please call Sion Williams on 07817 986561 or email Sion@vogelsang.co.uk
