
17 minute read
Biomass grain drying offers cost savings
One farming business in the Scottish Borders has redesigned its approach to grain drying around a 1MW biomass boiler. Ash Burbidge and Toby Whatley report.
Biomass grain drying offers cost savings
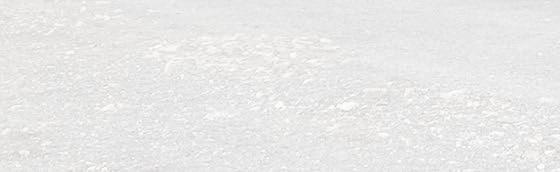
Growing a significant area of combinable crops in the Scottish Borders will always involve some catchy weather and less than ideal cutting conditions.
To address this, Mountfair Farming uses a mixture of drying systems across multiple sites to achieve the 14,000-tonne capacity it needs.
Aidan and Jorin Grimsdale know the challenges only too well, but it has taken a while to get to the point where they are now comfortably able to handle all that the elements can throw at them.
Aidan says: “For years we have focused on having enough drilling, spraying and combining capacity because without those vital tools you have got nothing ultimately.
“Being a relatively young business, we had to make do with what we had in other areas, particularly with our drying and storage facilities.”
The solution to the storage and drying challenge got underway in 2015 with the construction of a new 30 metre x 72m building, which was extended further in 2021 to 30m x 102m.
In addition to two 700t drying floors, there is also a 2019 48t Opico 4810 Magna batch dryer, which has recently been re-sited to its permanent position.
Combination
The storage site is one of four grain stores with Opico dryers operated by the business.
The site utilises a 1MW biomass boiler as its main heat source to dry a combination of crops. The business harvests around 14,000t of crops including oilseed rape, wheat and oats per year.
The dry weather this harvest has meant the business has only dried 3,000t, which has resulted in a huge cost saving.
Aidan says: “It has been one of the driest years anyone can ever remember. We do not normally manage to cut wheat under 15% moisture.
“This year we were cutting day after day at 12-13% all day long.”
The Opico 4810 unit is a conventional diesel-fired model operated in combination with a heat exchanger fuelled with Continues over the page.
The main store at Mountfair Farming dries 10,000 tonnes of cereals and oilseeds annually.
The 1MW boiler is fully automated.
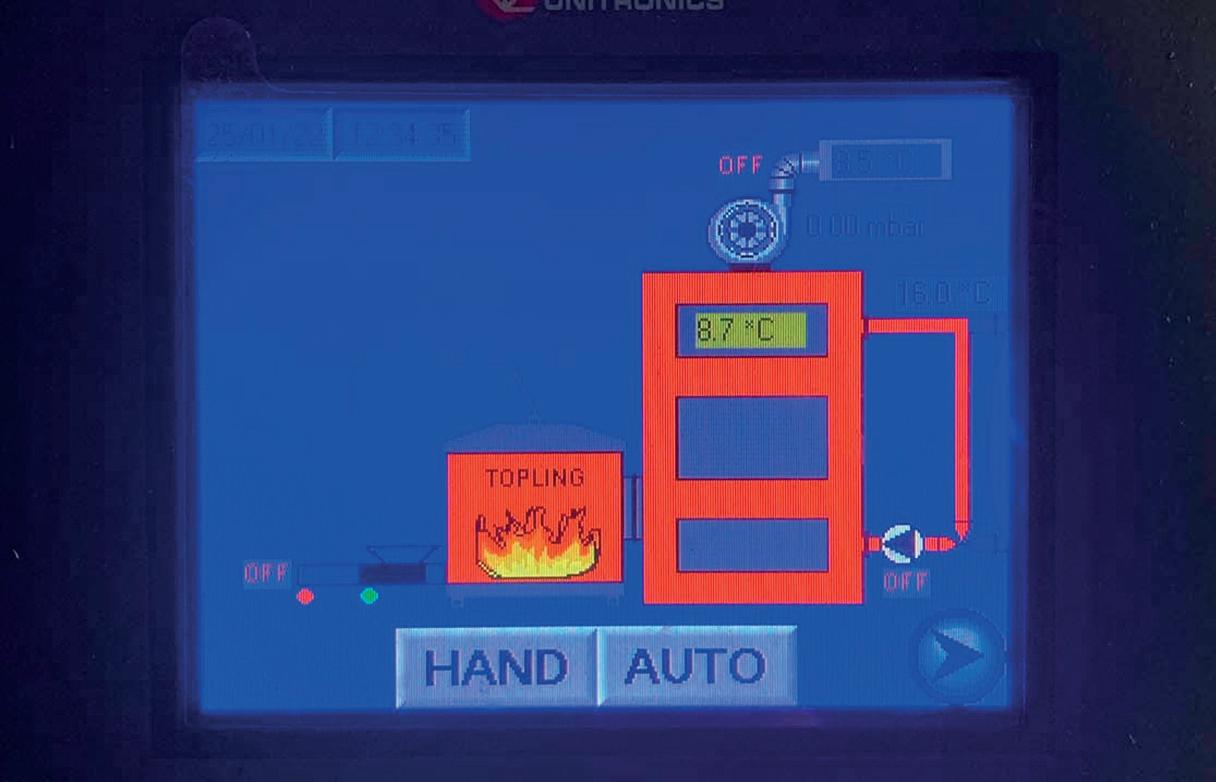
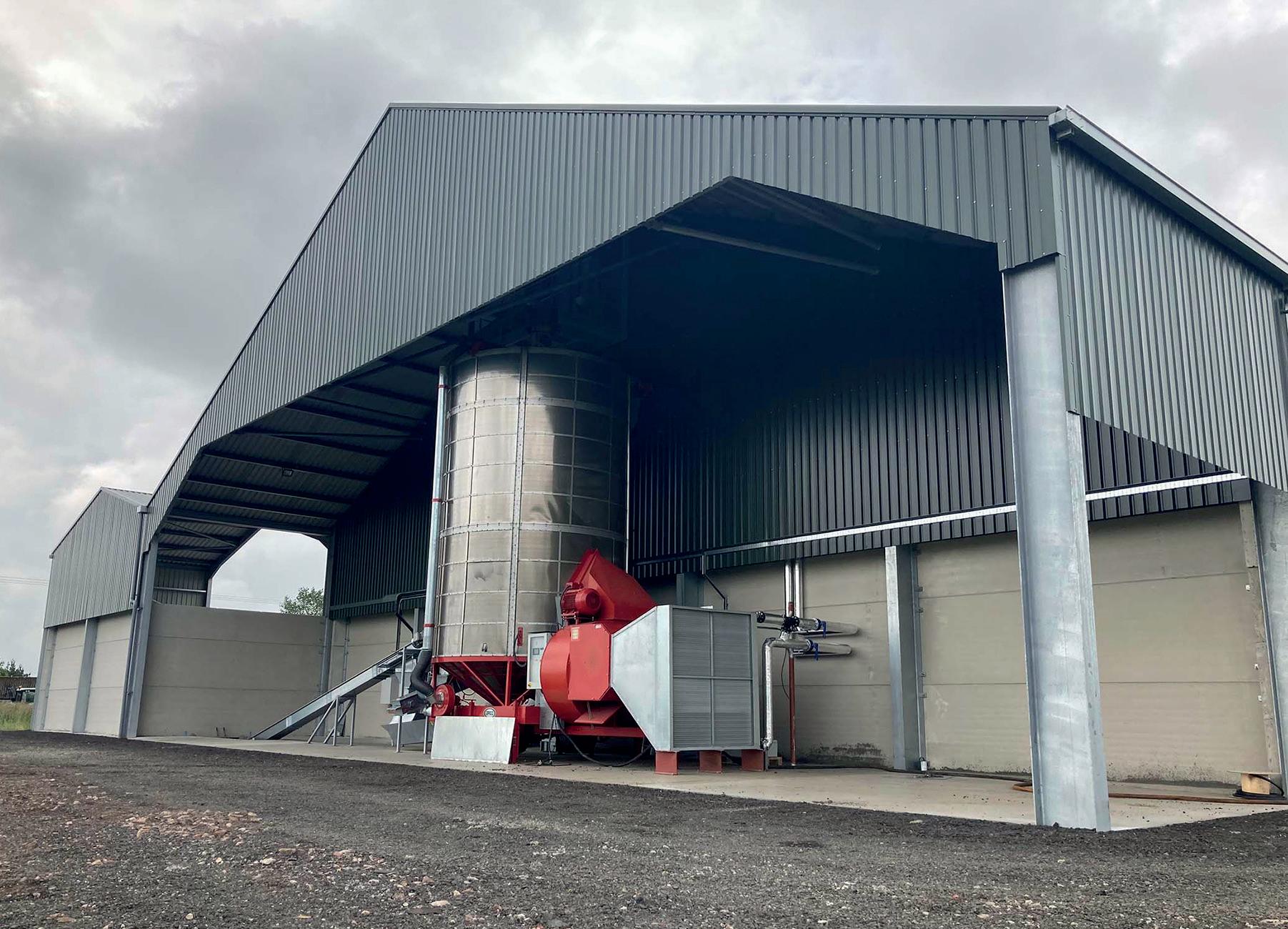
hot water from the main biomass plant.
Positioned about 60m from the main boiler, an additional insulated pipe circuit has been installed to bring the hot water to the dryer-mounted radiator.
The hot water is pumped through a large radiator mounted on the air intake for the dryer, lifting the air up to 55degC from ambient before being blown in. The diesel burner then lifts the air temperature the remaining 45degC to the 100degC target operating temperature.
The process of pre-heating the intake air has allowed for a more than 50% reduction in the diesel requirement to run the unit.
“Most of the time it runs on the low flame, except on colder nights when the high flame is switched on too,” says Aidan.
“Initially we had some challenges in setting up the diesel burner, as the set up required some unusual nozzle jets. Originally even the low flame was burning far too hot, however, once that was sorted and set up correctly it works well.”
Included in the assembly is an automated valve which diverts the water flow once the dryer burner cuts off during the cooling cycle. The addition of the radiator has increased the cooling cycle by 25-30 minutes as this must be cooled down before cooler air can be pushed through the grain.
“The cooling cycle is longer, but this is fairly consistent, so we factor this in when running the plant and the time it takes to run a batch through the dryer,” Aidan adds.
In terms of operating costs, using the biomass boiler to pre-heat the air has made a significant difference to the cost per tonne to process the crop, although costs have increased as a result of the higher diesel price.
Diesel prices
“So, instead of being £2.50/t we are back up to £5.00/t, almost like when we were just running straight fuel; this is because diesel prices have doubled,” says Aidan.
However, other adjustments have been made to improve the economics of using the Opico dryer, he adds.
“We have also managed to reduce our electricity consumption. Because we do not currently have a meaty enough three-phase supply to run the
AIDAN GRIMSDALE
Aidan Grimsdale dryer we have been reliant on a generator.
“It requires an inverter which has enabled us to tweak the drier fan. Rather than running at the standard 50 Hertz, we have reduced it to 40Hz.
“The downside of that is we have to run the dryer slightly slower – it is 10-15% down – but it means we have halved the generator fuel consumption. That reduction in capacity is a penalty that is well worth paying – the whole set-up is now so much more energy efficient,
“Electricity price increases have not as yet affected us because we’re still in contract until the end of this month [September] so we are still running at 18p/kWh,” says Aidan.
The biomass source previously was windfall softwood which is bought round and chipped on-site as required by a specialist contractor.
This year they have managed to source most of the softwood on farm due to Storm Arwen that came in last November.
“Lots of the wood that has been used this year has been our own wood that we chopped up and got the chipper in for. There was an abundance of wood on the Scottish Borders as we got really hammered by the storm.
“We use roughly 300t of dry chip a year, but that does vary a bit depending on our intake source,” says Aidan.
“Usual moisture content for the chip is 20%. We have had it as low as 18% and as high as 23%. Obviously, the wetter the chip,
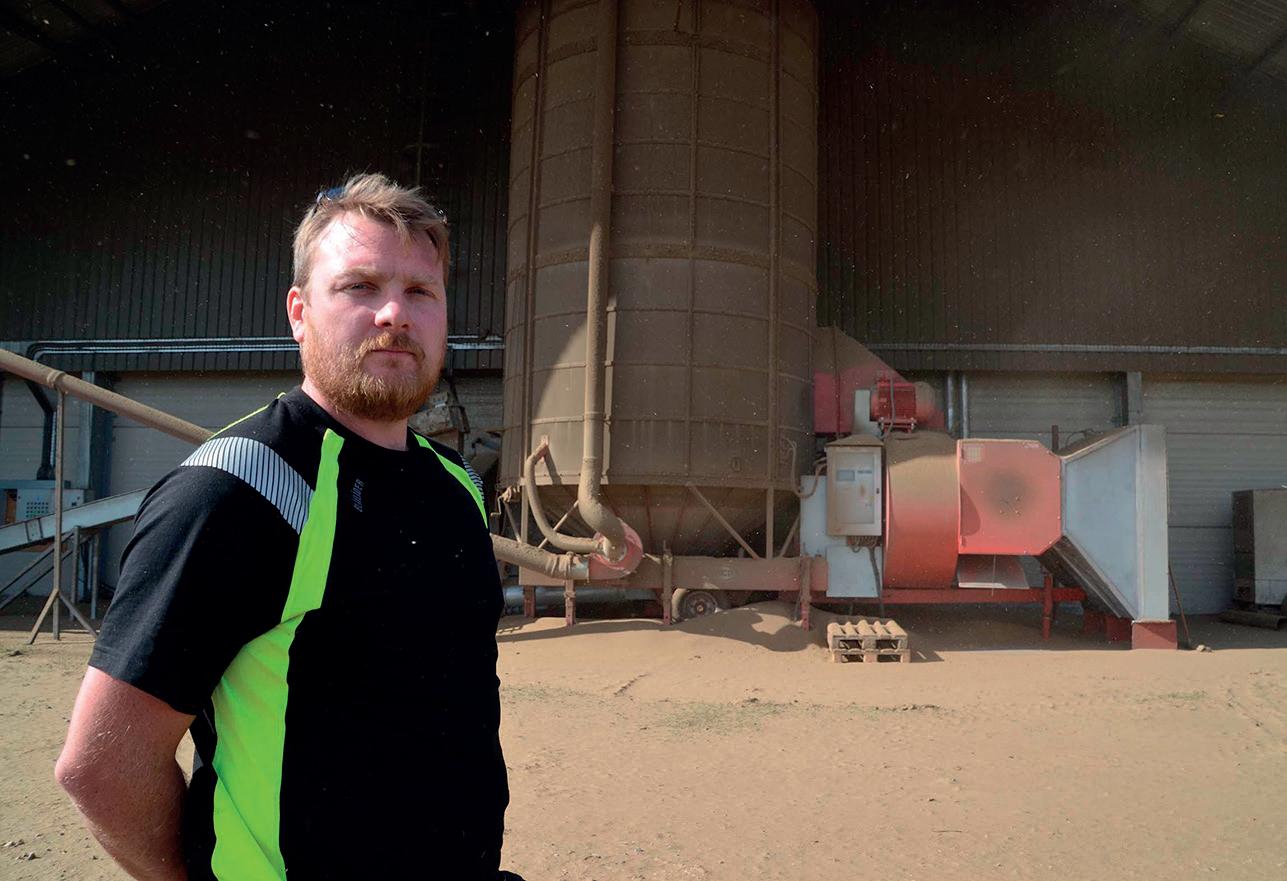
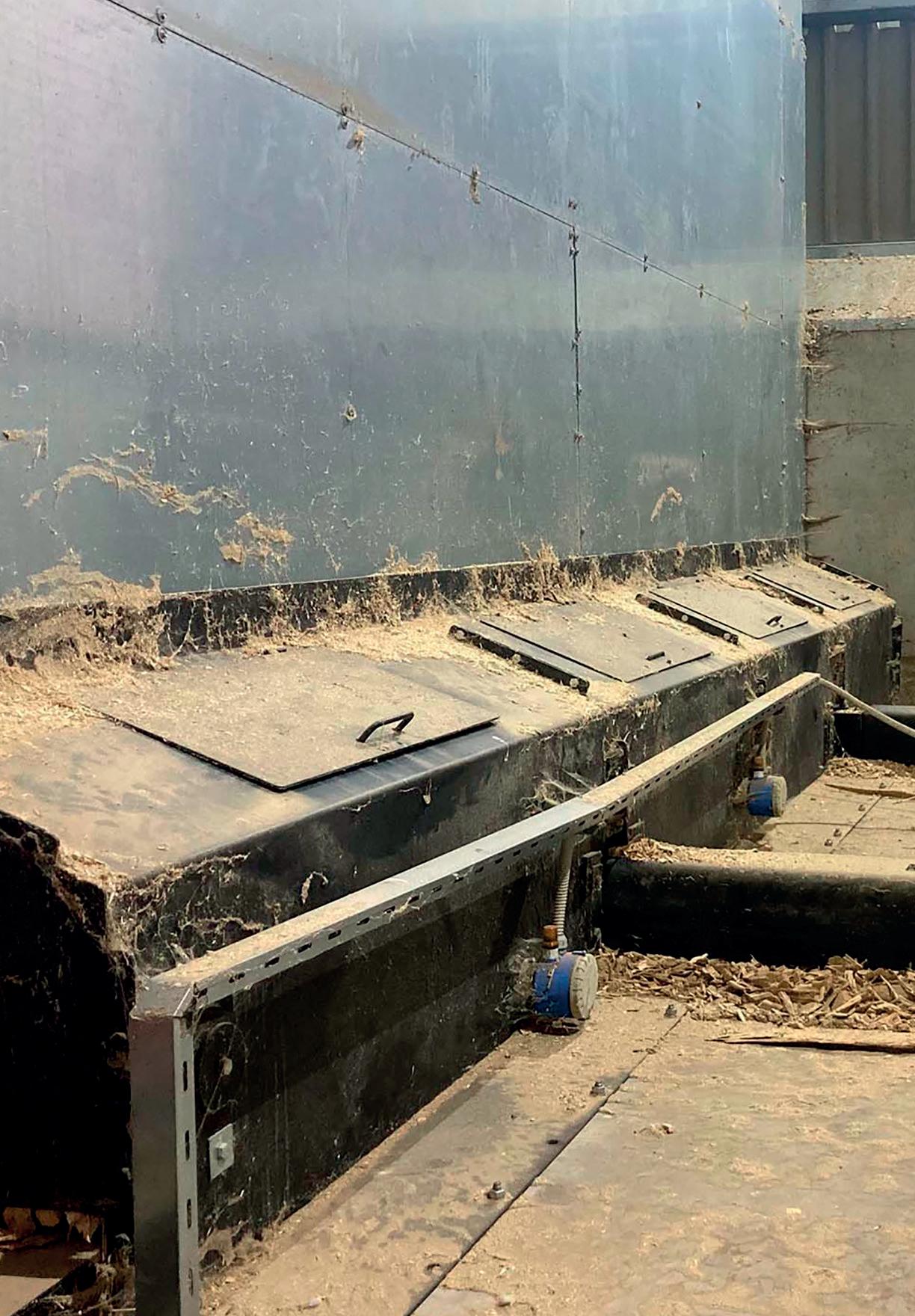
A hydraulically-operated walking floor pulls material towards the intake auger.



The radiator heated with water from the biomass plant pre-heats the intake air to 55degC.
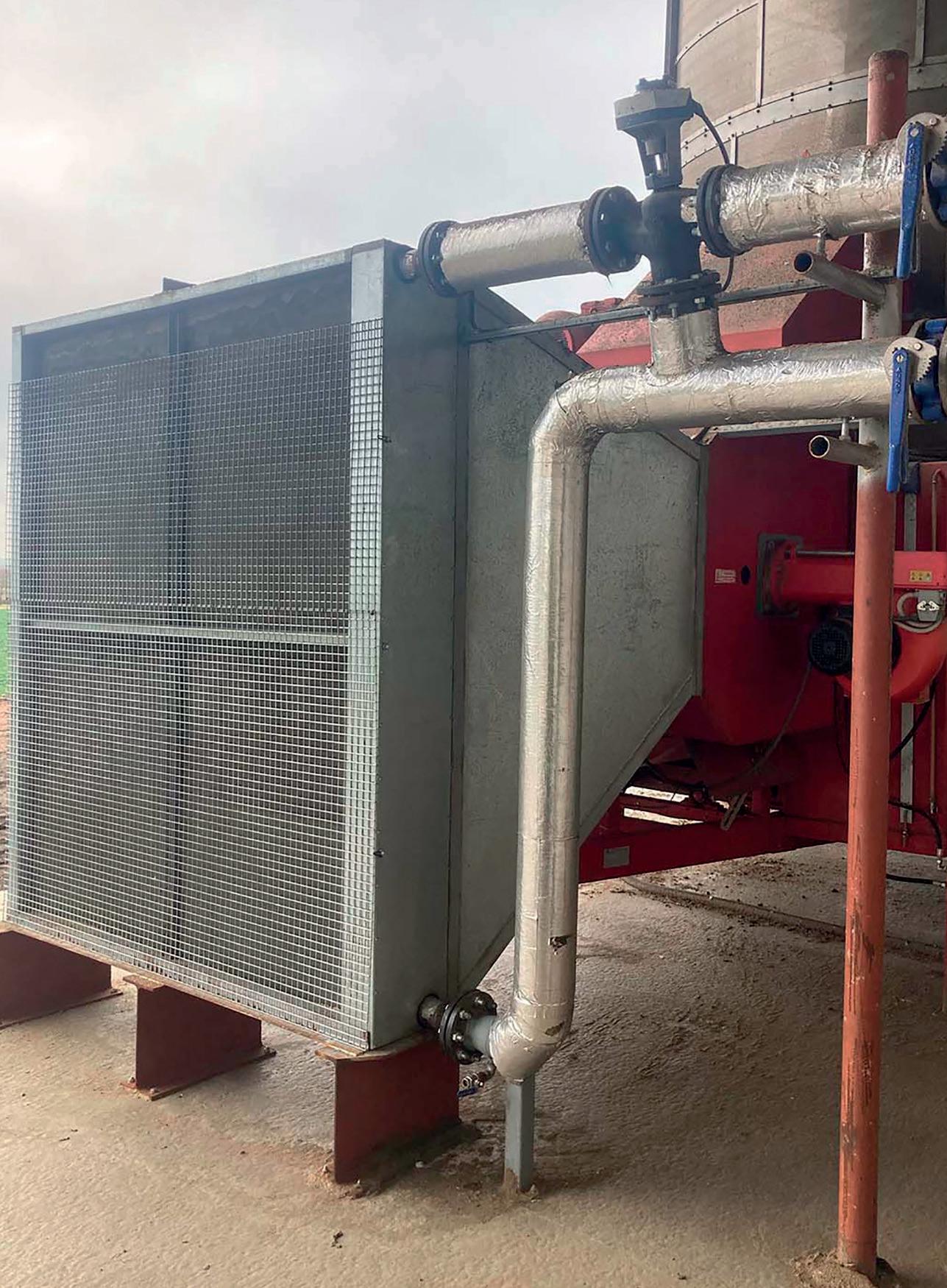
AIDAN GRIMSDALE
the more we use.
The price of woodchip has not moved much, adds Aidan.
The biomass plant supplied by Topling is automated and controlled through a central touch-screen.
A hydraulic walking floor pushes the chips into the boiler intake auger, which regulates the fuel input based on the demand from the system.
The boiler is aligned to a Renewable Heat Incentive scheme, so the capacity and its use to dry grain and a small amount of firewood on the drying floors are matched to optimise this system.
The dryer, elevators and store handling are all automated through a central control, linking the demands of the dryer and the output of the dried crop.
A recent installation of a large wet pit has allowed more utilisation of this system, reducing the labour requirement to operate the plant.
Aidan says: “For the first two seasons we had the 48t set-up outside with a 25t bin feeding it, but it meant having someone on hand all the time to keep it running at full capacity.
“Last winter, the store was completed, the dryer fully integrated, conveyors installed, and a 300t wet grain bunker installed with a proper trench intake conveyor to keep it constantly fed.
Revolutionised
“With it wired into the dryer’s touch-screen computer, it now loads and unloads itself under its own steam.
“It has totally revolutionised the job so that it will process 150t without anyone going near it. I can now load up the bunker at 11pm and leave it running all night.
“Dropping 17% moisture grain down to 14.5%, will take about three hours per batch, doing three batches before it needs any attention.”
In the two seasons that the Grimsdales ran the 48t drier in its temporary position, with the 25t intake bin, it required someone on-site all the time it was running, loading the hopper and managing the dryer’s discharge.
That often meant it might sit idle through the early hours of the morning until someone arrived to start loading it.
With the addition of the 300t intake bunker and some changes to the store discharge system, Aidan estimates that the requirement for human input has been reduced by an average of six hours every day.
Maintaining sprayer stability and output on steeply undulating land can be challenging. farming and contracting business which has found a solution.
Search for stability leads to Infinity
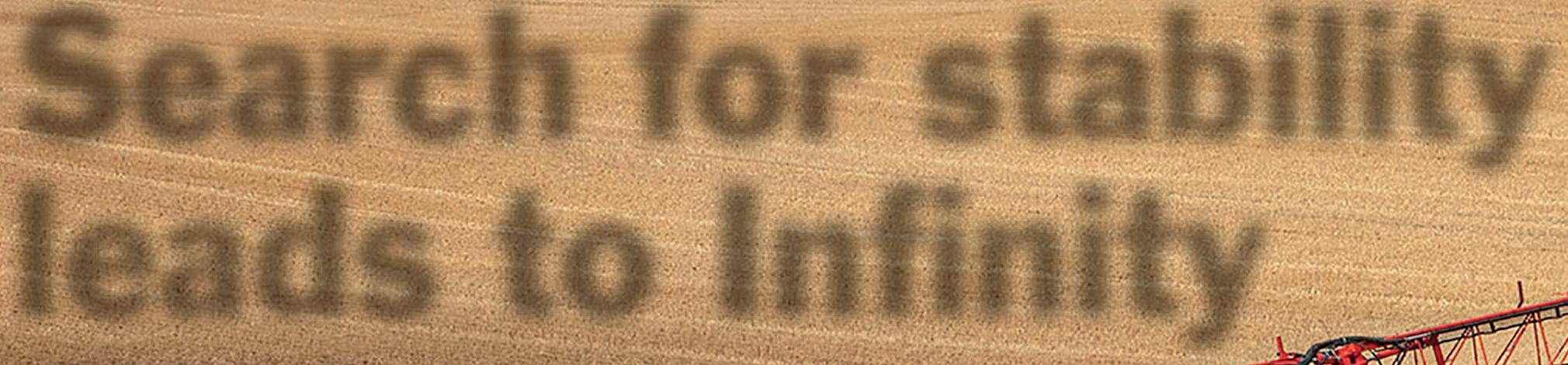
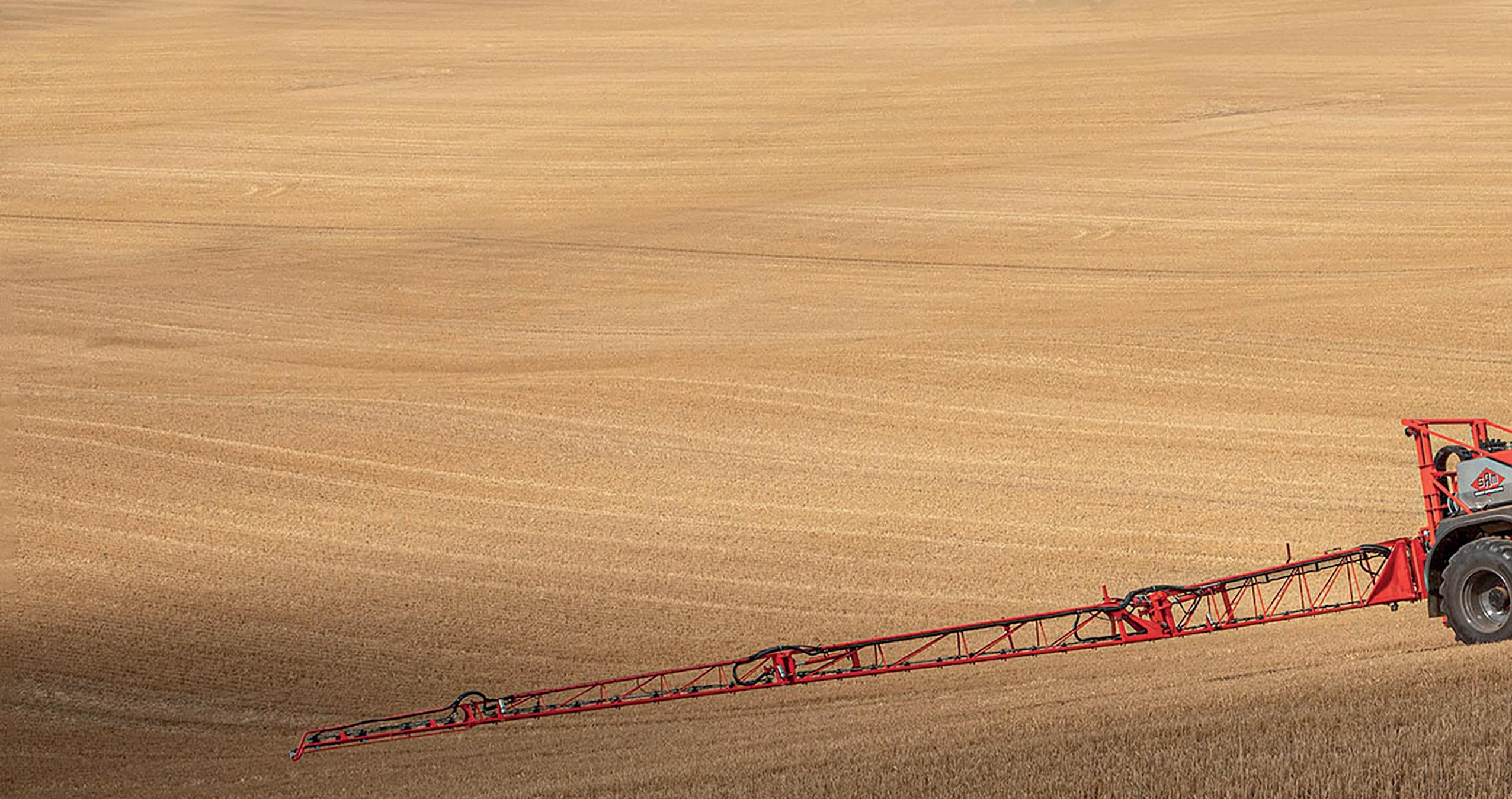

For Ed Smith and his brother Oli, farming on the Lincolnshire Wolds is not without its challenges. One of which is the steeply rolling countryside that can see machine power and stability tested to its limits.
“We have some really steep gradients, which does push machinery to its limits,” says Ed.
“It also puts a lot of emphasis on logistics when it comes to spraying. And that includes tackling the steeper parts with less liquid in the tank to continue to operate safely.”
The brothers run a 2,000-hectare business that comprises its own land, plus rented and contract farming customers, spread over a 10-mile radius from their base near Horncastle, Lincolnshire.
While spray tank capacity is essential for output, the family have been in search of better traction and stability, to maintain forward speed on slopes and lift productivity.
Oli says: “A recent change in how we farm has seen the new
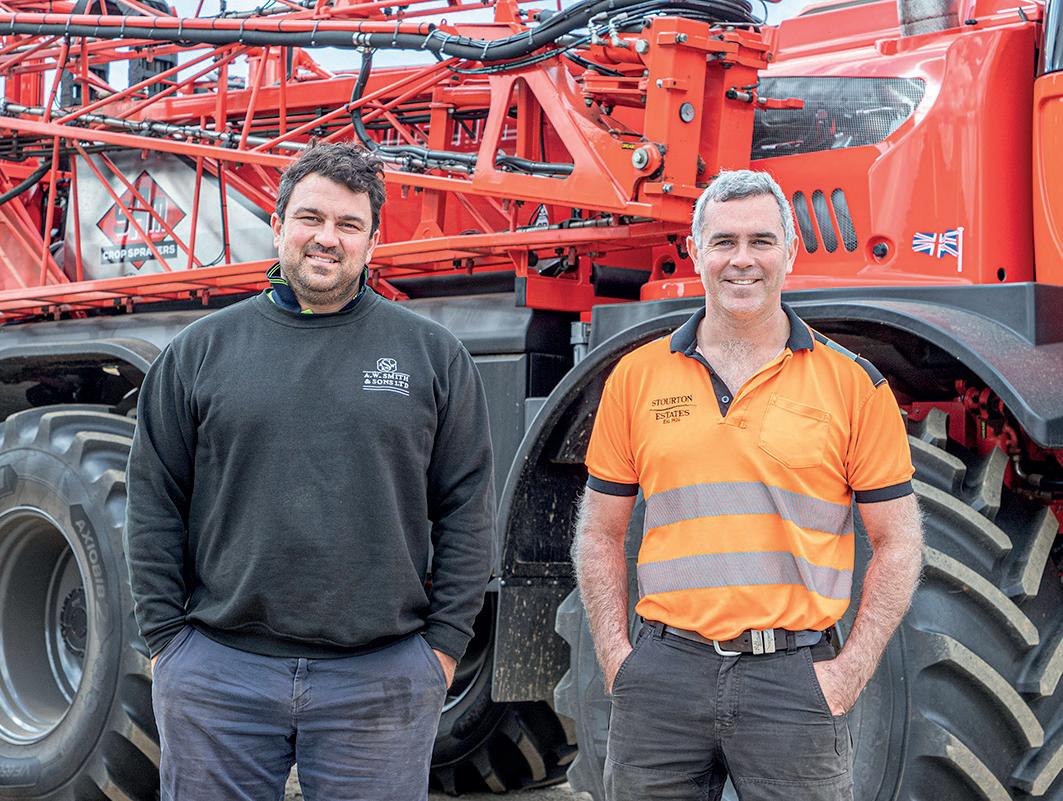
Ed (left) and Oli Smith are pleased with the decision to upgrade to Sands’ Infinity sprayer.
Sands Infinity sprayer brought in to replace a 24-metre Househam AR3500 and a 36m Sands Horizon with 6,000-litre tank. And the Infinity is proving to be a considerable step up from the Horizon.”
Wheelbase
Launched at Cereals earlier this year, the Infinity sees an all-new chassis underpin this latest self-propelled sprayer range from British maker Sands Agricultural Machinery. Only the cab is shared with the Horizon, with the rest of the sprayer new from the ground up.
While the Infinity chassis is identical in length to the Horizon, its wheelbase is around 200mm longer than the Horizon for better weight distribution.
This change also supports the use of larger wheels and tyres without compromising on manoeuvrability.
Tyres
Sands says the Infinity has a 7.6m turning circle – identical to its short wheelbase 3,000-litre Horizon. The brothers’ machine is shod on Michelin AxioBib VF650/65 R34 tyres and has access to a set of 380/95 R38 row crops.
Spray tank choices for the Infinity have capacities of 5,000 and 6,000 litres, leaving the Horizon range to cater for those seeking a spray tank of 4,000
Also in this section
52 Dammann sprayer hits the spot 54 Joystick steering ideal for centre-feed harvester 58 Raft of Lexion updates 60 700 Series loaded with next gen upgrades 62 Affordable access to variable rate drilling
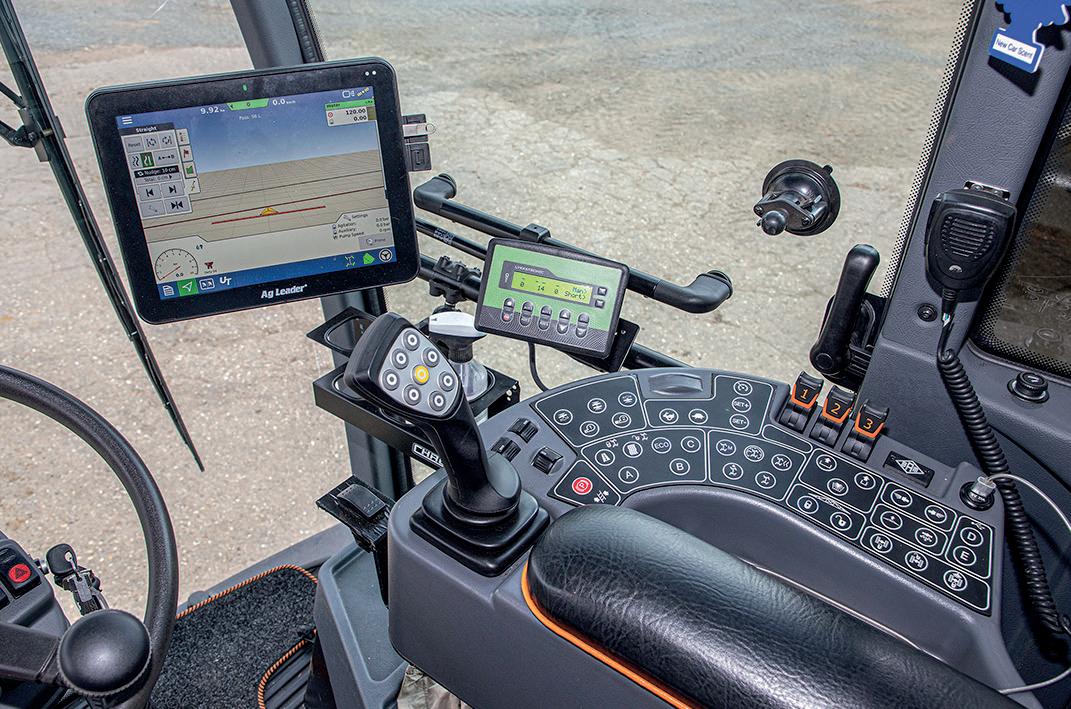
Geoff Ashcroft reports on one Lincolnshire

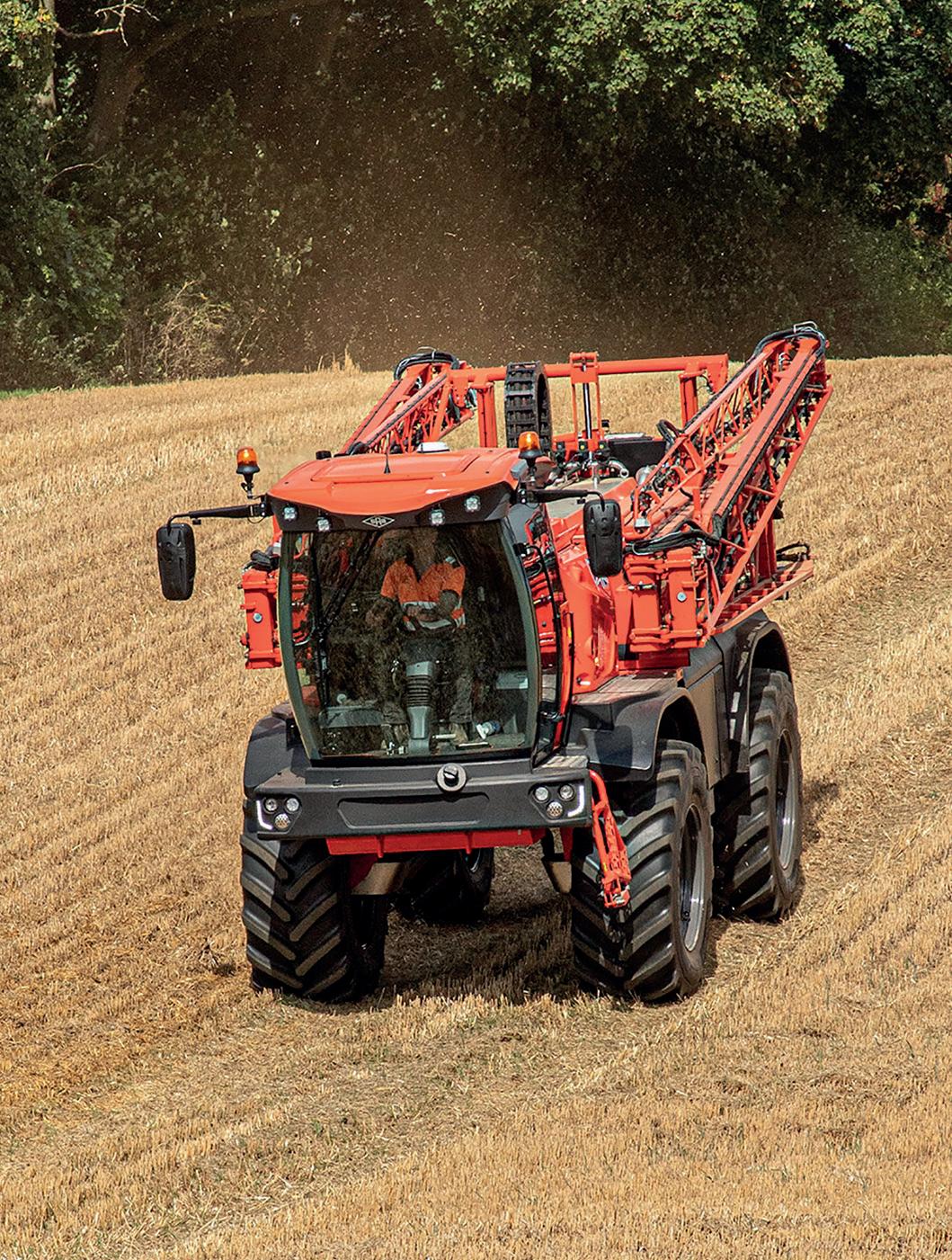
The 36m boom uses six sensors for contour following and auto height control.

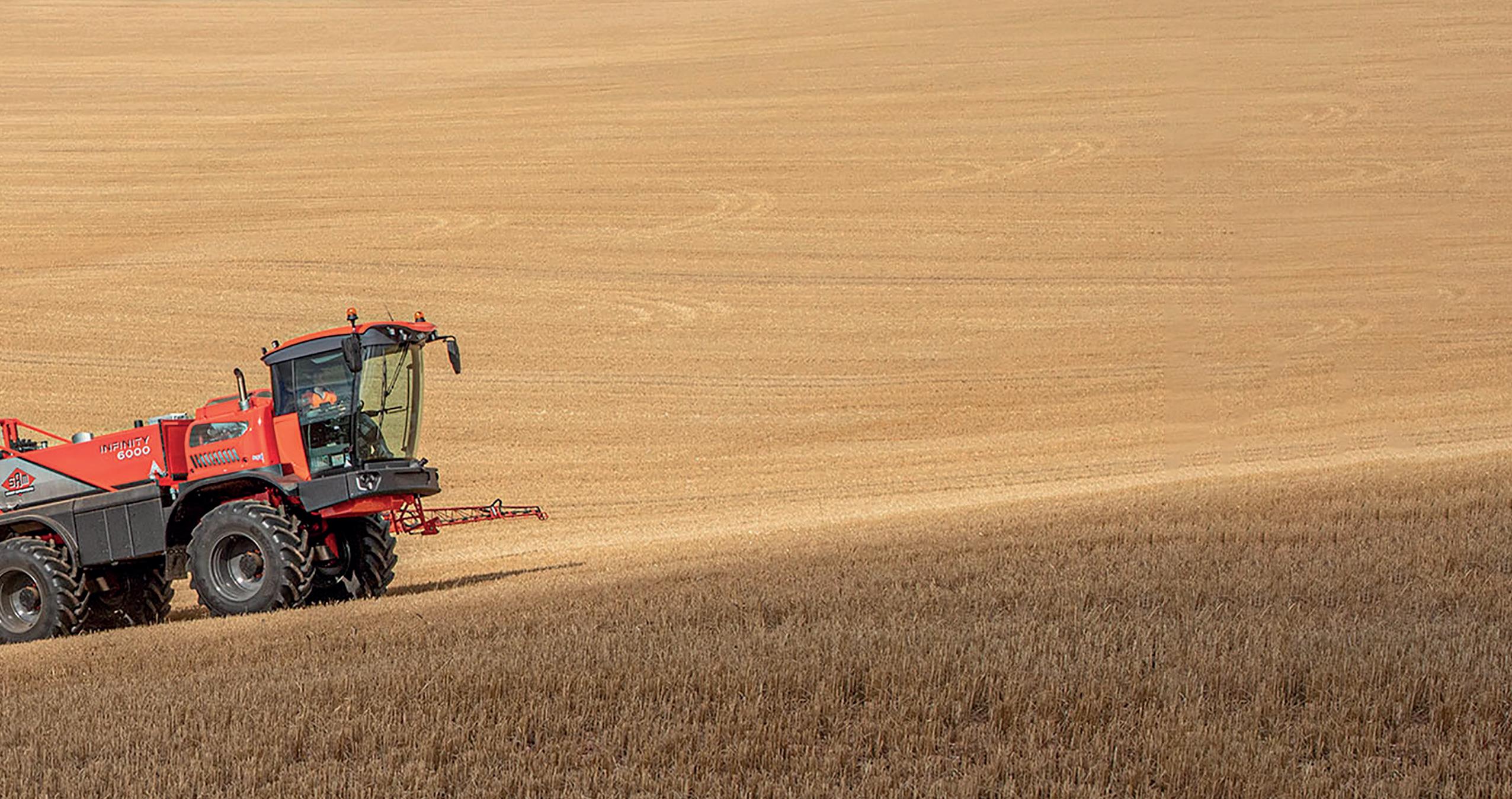
litres or less. Tank construction is now stainless steel, which has led to a larger sump and shorter pipework for improved liquid management.
This is complemented by a side-mounted filling station that is protected by a top-hinged side panel. The revised fill station contributes to shorter pipework between pump and tank, and with a hydraulically raised and lowered 40-litre induction hopper, the operator can choose to set the bowl at any comfortable working height between X

Traction and stability are greatly improved over the farm’s Horizon model. PICTURES: GEOFF ASHCROFT
HELP US FIND THE NEXT FARM SPRAYER OPERATOR OF THE YEAR
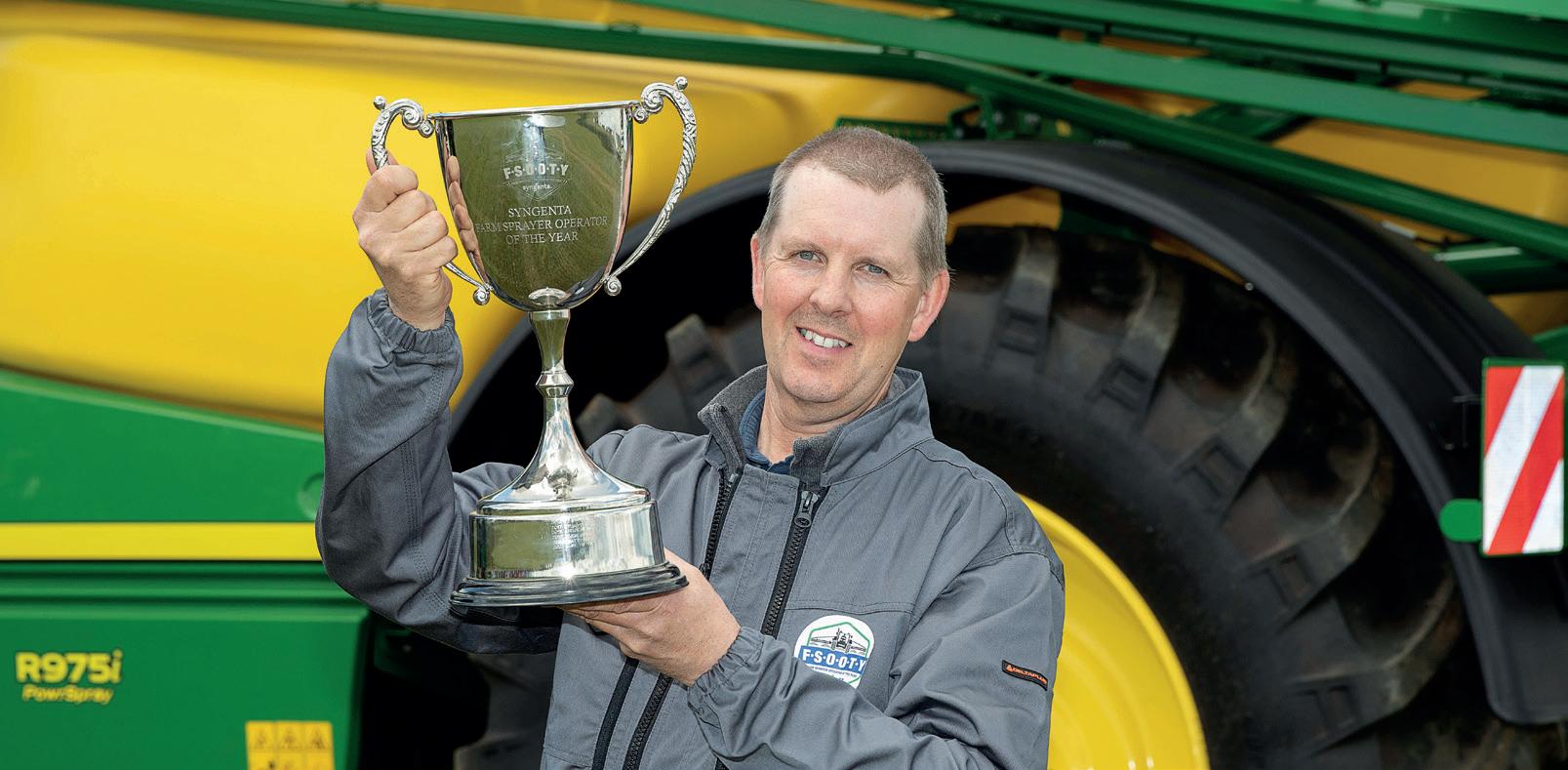
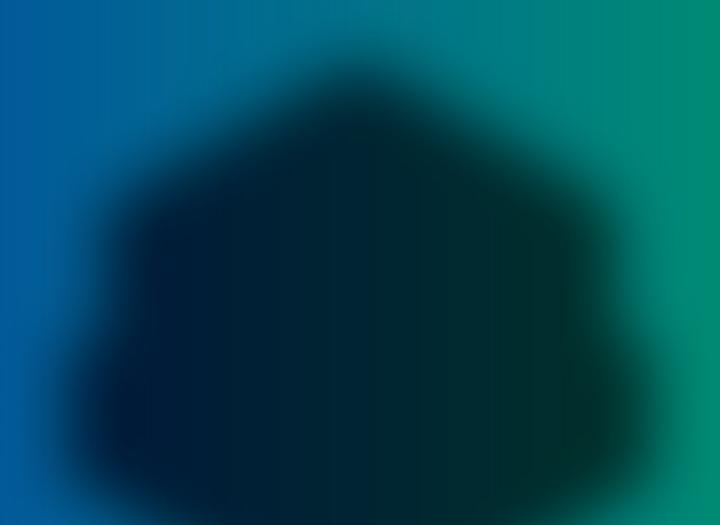

POINTS FOR ENTERING
NOMINATE NOW AT
WWW.SYNGENTA.CO.UK/FSOOTY
Syngenta UK Ltd. Registered in England No. 849037. Tel: 01223 883400 Web: www.syngenta.co.uk. Terms and conditions apply
its fully raised or lowered positions.
Sands’ fabricated steel tank has been designed to sit deeper in the chassis, lowering the new sprayer’s centre of gravity below that of the Horizon model.
Fully independent selflevelling hydraulic suspension is claimed to improve ride and stability, with power supplied by an EU Stage 5 compliant Deutz six-cylinder engine developing 242hp.
The switch to Bosch electronics and a Bosch Rexroth hydraulic system is said to have created better integration and control of all components and has seen the introduction of Eco engine management for road and field use.
But perhaps more importantly, the Infinity comes with a traction control system that works only when wheel slip is detected.
Oli says: “As a Horizon customer, we knew the Infinity was coming. And everything we saw during its development answered most of the shortcomings of our Horizon – the new chassis and powertrain really has a lot to offer for our business. And on top of that, this is a machine that is British-made and local.
“We did consider other well-known European makes on the market and we did think about going up to a bigger capacity spray tank too.
“But larger tanks tend to mean a taller and heavier sprayer. With stability being important for us, we chose to stay with a 6,000-litre tank size.”
With more than 325 hours now on its clock, the brothers’ Infinity has been pushed hard on spray and fertiliser applications since its arrival on-farm earlier this year.

Workload
It is a workload that sees more than 20,000ha covered each season, helped by strategic water points around the area farmed to help reduce downtime. However, a 16,000-litre bowser is planned for next season.
“The less running around we do means more acres sprayed each day,” says Oli. “And with liquid fertiliser to apply too, it’s important that we make the most of productivity and field support.
“We have three-inch hoses and 1,000-litres of pump capacity, so fill times are quite short. It’s good to know Sands has considered the needs of operators by including suction pipe storage built into both sides of the sprayer, so we’re never without pipework at any of our fill points. Filter access is practical too and is reached from the rear of the sprayer.”
The Infinity’s weight distribution is noticeable from the seat and it translates into better stability on and off-road, also bringing a big improvement in traction.
Ed says: “This is by far the best bit of kit we’ve ever had on our hills. It climbs considerably faster than the Horizon and it grips through those steeper areas where the Horizon would struggle to move forward without spinning its wheels. It’s also rock steady.”
He also has praise for the revised boom and its auto height control.
“The 36m boom comprises three 12m sections with six sensors, for positive and negative contour following. We’re both really impressed with its stability and its ability to hug the ground much better than our previous model.”
LED work lights and boom lights are a big improvement, making long days in the cab an enjoyable experience.
“It’s all about the details. We
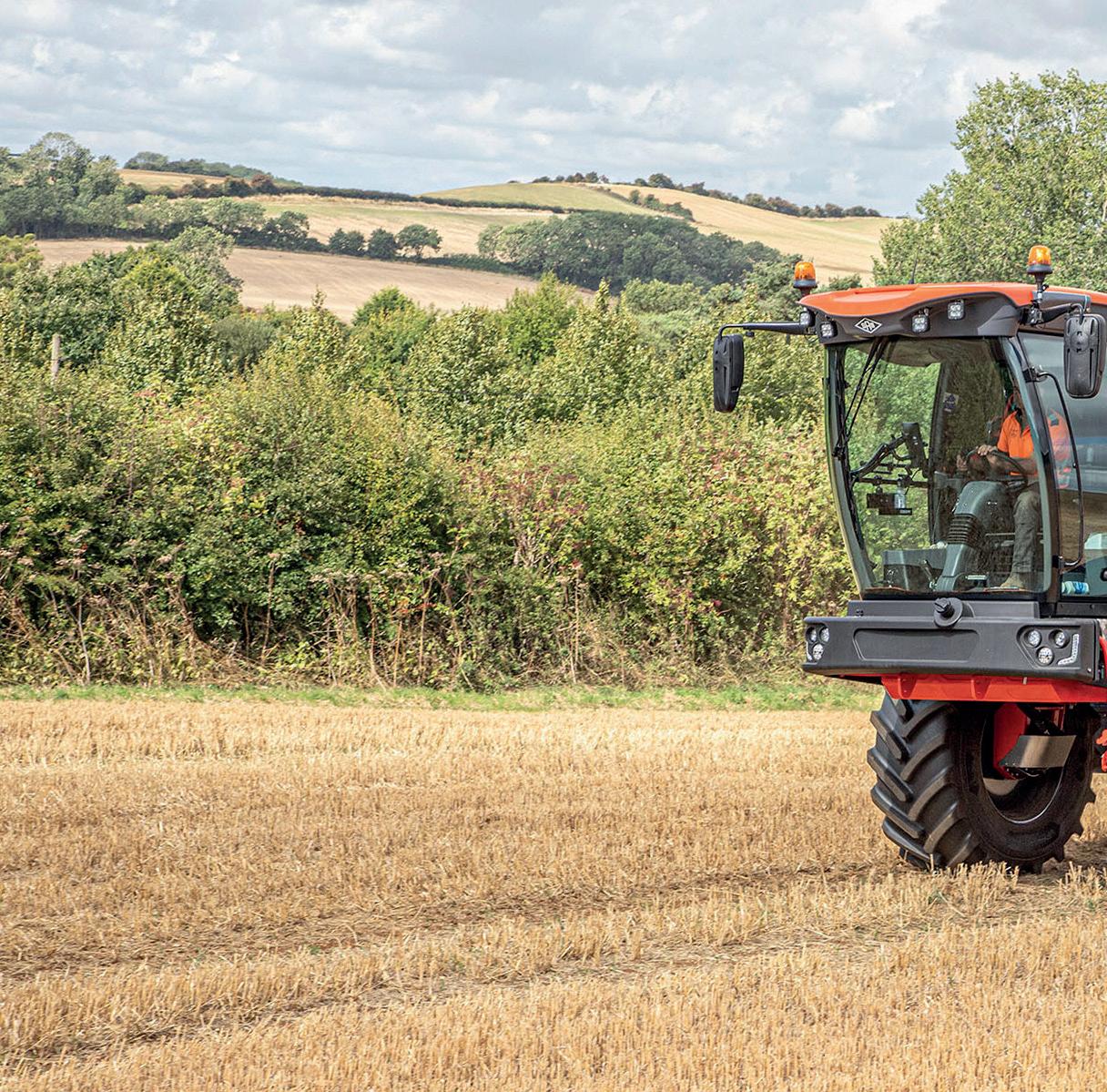
OLI SMITH
The Infinity is available with spray tank capacities of 5,000 and 6,000 litres.
The fully independent selflevelling hydraulic suspension improves ride and stability.
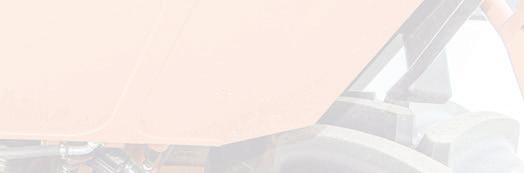
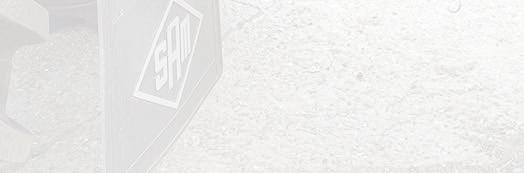

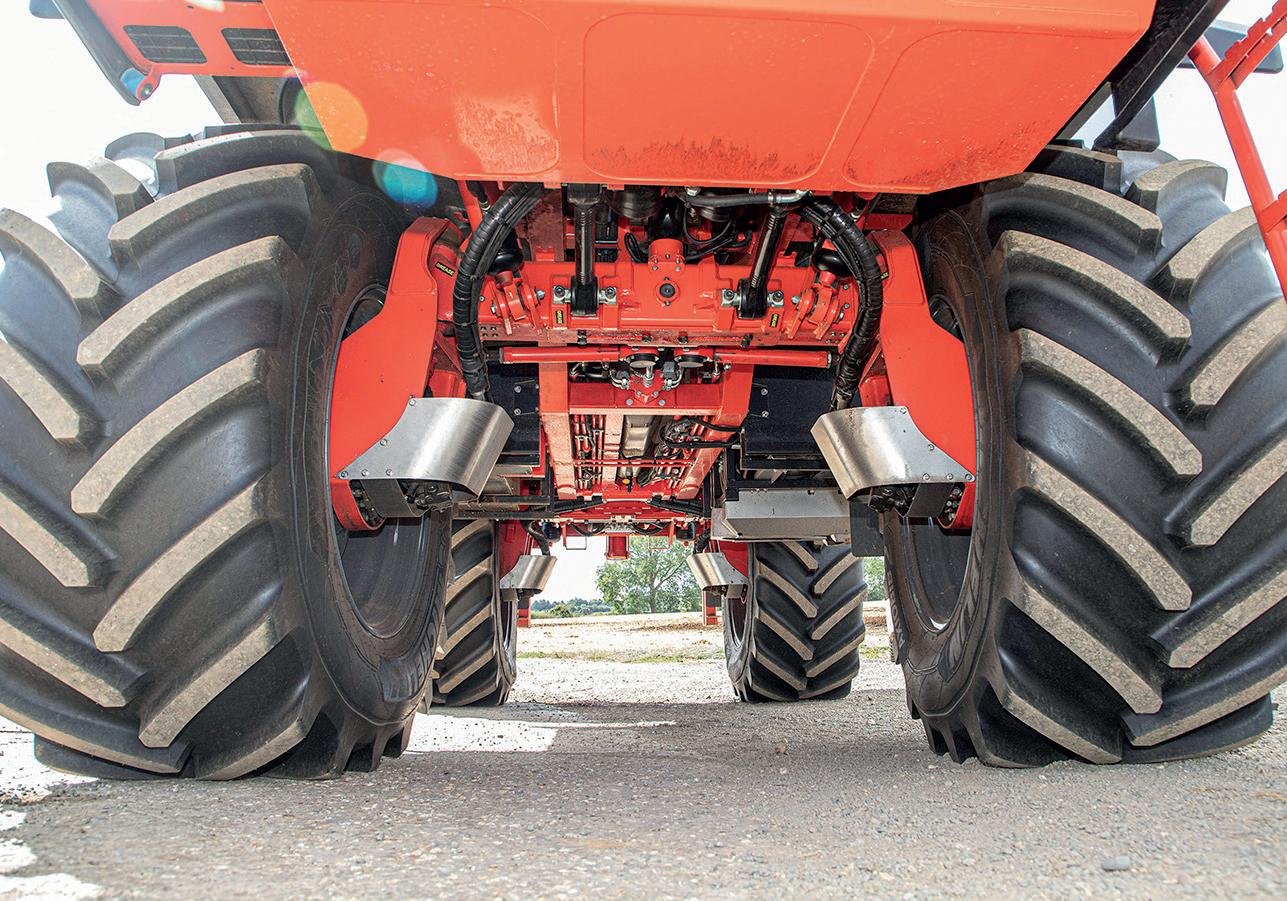
A side-mounted filling station is a departure from Sands’ traditional rear-fill location.
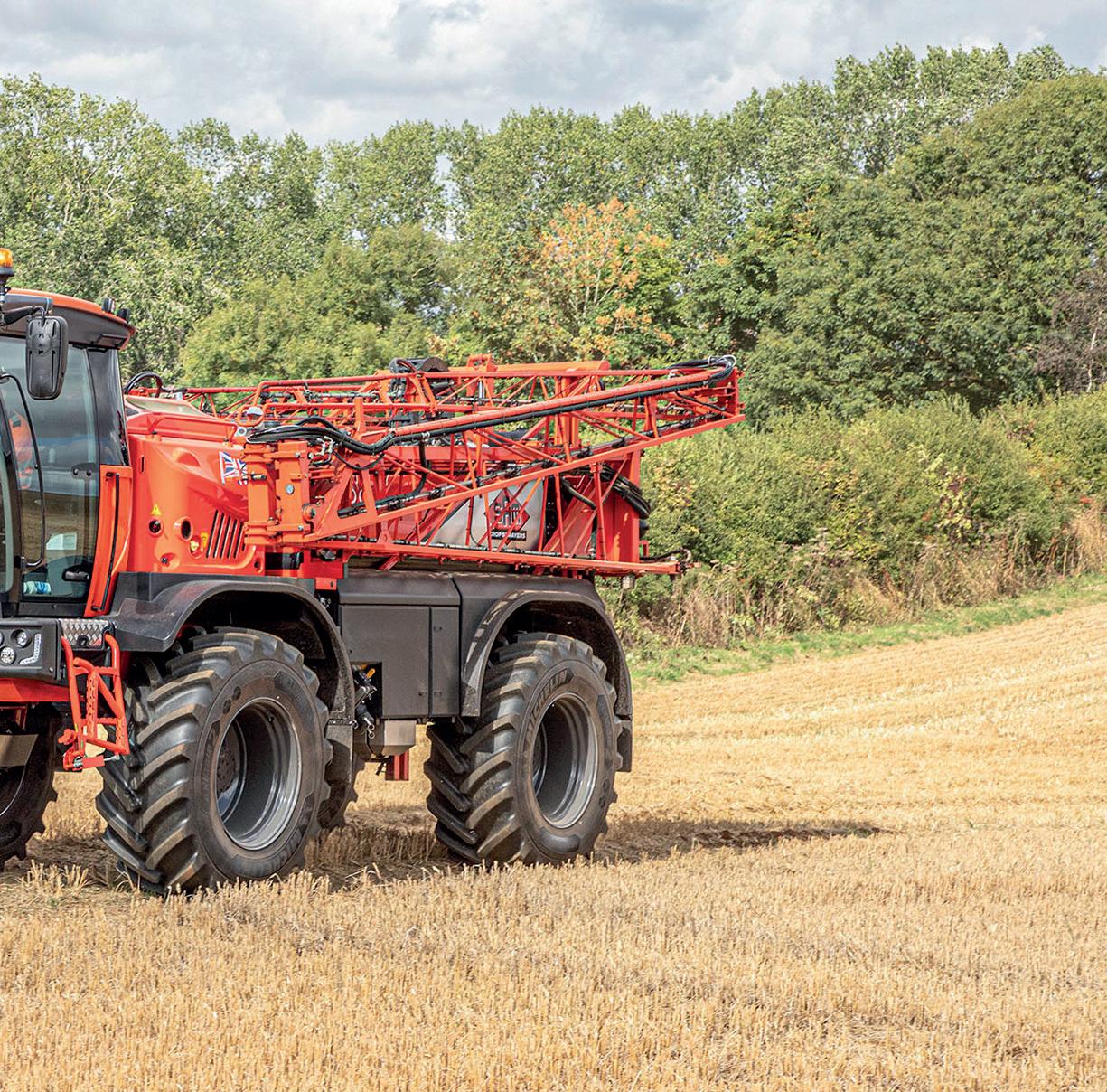
really like the overhead instrument panel. The diesel tank no longer spits back when a high-capacity refuelling pump is used, the AdBlue tank is neatly concealed in a right-hand locker and there’s plenty of storage all around the machine,” says Ed.
Overlaps
Field sizes extend from 2ha up to 46ha, with an average field size of around 10ha, and most are what the brothers describe as awkward shapes.
Oli says: “We opted for Ag Leader for GPS control and, with RTK across the farm, we have continued to minimise our overlaps with auto start-stop on 3m sections across the boom.
“Application is very accurate and although we considered individual nozzle control, we wanted to maintain an element of simplicity too, which is why we’ve stuck with Hypro Duo Reacts for auto nozzle switching, instead of choosing a quad nozzle system.”
Cropping is predominantly winter and spring-sown combinable crops, with sugar beet also in the mix. It sees the farming brothers use a 2m fixed track width, which incorporates 50cm sugar beet rows into a 36m tramline spacing.
“With this new sprayer, we’re confident of improved timings and better productivity across all our crops,” says Oli.
“Long before the sprayer arrived on-farm, we knew it would be the right investment for our farming business and, so far, it has lived up to expectations.”
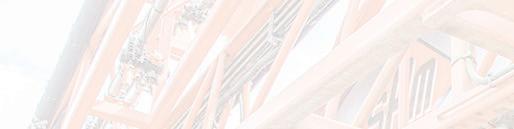
The Sands Infinity provides integral suction hose storage. Machinery and farm technology reporter
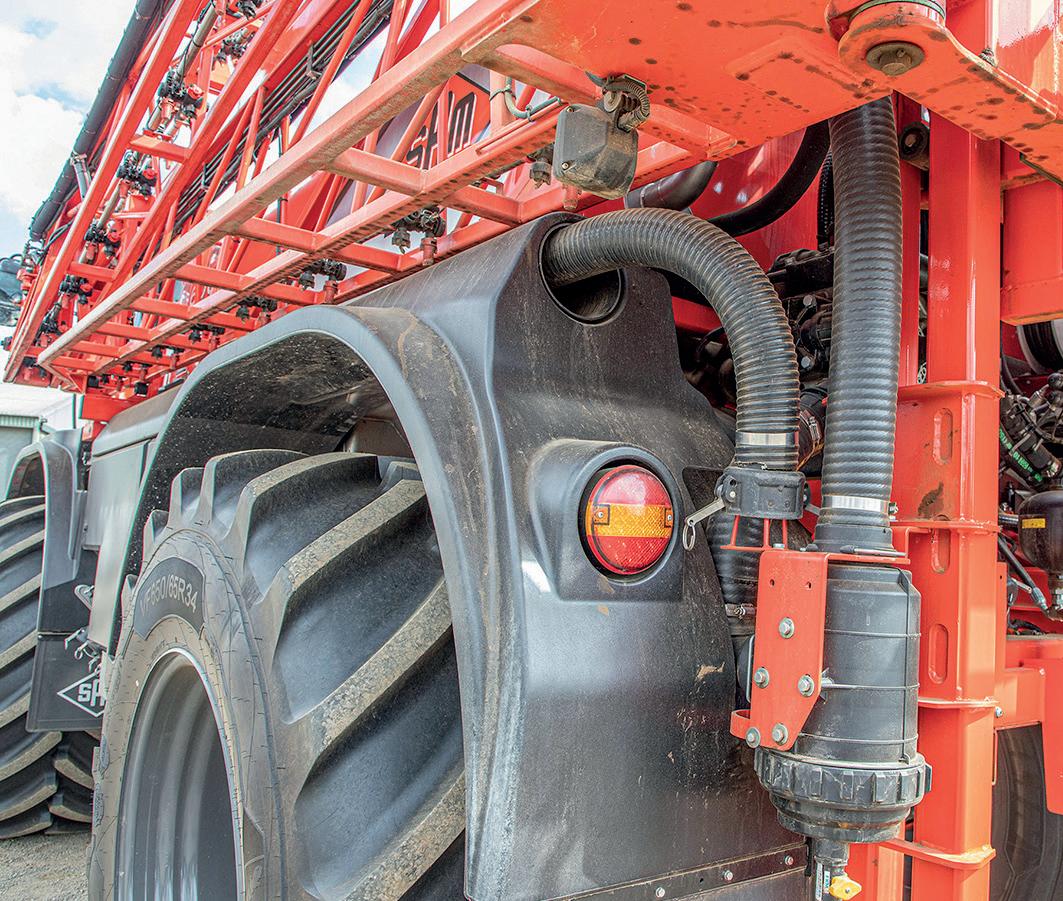
Farmers Guardian Location: Preston or home-based (flexible) Salary: Competitive
Have you got a passion for agricultural machinery and emerging technology in the farming sector? Do you want to provide great written, video and audio content for some of the leading brands in UK agricultural publishing and events? If so, then this is the job for you.
Farmers Guardian and parent company Agriconnect are on the hunt for a high calibre candidate to work for its machinery and farm technology team across prominent brands such as Farmers Guardian, Arable Farming and Dairy Farmer as well as involvement in thriving events such as LAMMA Show and the British Farming Awards.
With modern agricultural machinery and emerging technology changing the face of contemporary agriculture, the right person would work alongside the Head of Machinery and Farm Technology to produce the best coverage in the sector.
You would play a key role in generating both written and video content for this part of the portfolio, with travel opportunities across the UK and abroad. As part of the team you would have a keen focus on contributing content ideas for Arable Farming, Dairy Farmer and Farmers Guardian.
We offer an excellent package including 25 days holiday increasing to 27 after two years, an extra day off on your birthday, free life assurance, free parking, flexible working, contributory pension scheme and a 35-hour working week.
We believe that creating a culture of diversity will help to maximise everybody’s potential and achieve superior business results. We aim to harness differences to create a productive environment in which everybody feels valued, where their talents are being fully utilised and in which organisational goals are met.