
10 minute read
REWOFUEL
Sustainable biofuels set for take-off
Wood contains materials which could represent a valuable resource for the gasoline and aviation fuel markets. Researchers and companies involved in the REWOFUEL project are developing sustainable methods of producing gasoline and aviation fuel from residual wood, while also making use of other co-products, as Dr Tino Lassmann explains.
The aviation sector uses large
quantities of fuel, but with environmental and sustainability concerns growing, the search is on for alternatives to conventional fossil fuels. Based at the green chemicals company Sekab, Dr Tino Lassmann is part of the REWOFUEL project, an initiative working to transform residual wood into biofuels. “The process is divided into several steps before you eventually produce the aviation fuel,” he says. While the REWOFUEL project covers the entire value chain, including all the steps involved in the conversion process, Dr Lassmann’s main area of expertise is in converting the biomass into intermediate products. “At Sekab we have the skills and knowledge to open the structure of the biomass, and make the cellulose and hemicellulose accessible for conversion into sugars. These sugars are then further converted, in two separate steps, into aviation fuel,” he explains. “Our expertise lies in using biomass residues, and making the sugars that are in the biomass available, so they can then be further used for different applications.”
Pre-treating wood
This involves pre-treating soft wood in order to access certain materials within it, in particular lignin, cellulose and hemicellulose.
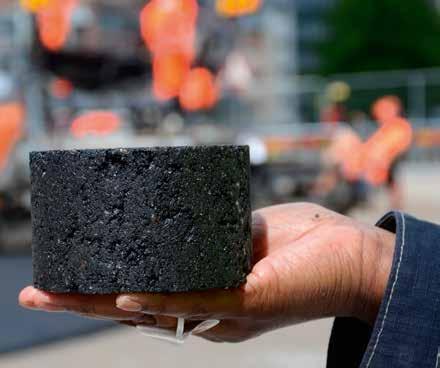
Roads made of trees - sustainable asphalt paving the way.
Lignin itself has a highly polymeric structure and a high energy content, so historically it has often been burnt, yet in recent years researchers have explored other possible applications. “It can be used in composite materials for example. In REWOFUEL we have tested lignin with a view to using it as a replacement for bitumen in asphalt. The company responsible for this was PEAB Asphalt, a Swedish road builder,” outlines Dr Lassmann. However, the main target in terms of making sugars available is cellulose, which is tightly bound in together with the lignin and the hemicellulose in woody materials such as sawdust, making it difficult to extract. “We’re using a pre-treatment process called the steam explosion process. The aim is to hydrolyse the hemi-cellulose in woody material, which then makes the cellulose accessible for the next step, the so-called enzymatic hydrolysis,” continues Dr Lassmann.
The steam explosion process takes place in a high-pressure reactor, with different catalysts available to solubilize the hemicellulose in the sawdust. Due to the pressure drop at the outlet of the reactor the structure is opened – the ‘explosion’ – and its surface area increases, which then makes it easier for the enzymes to go in and do their job. “The enzymes are then responsible for the conversion of cellulose - which is a long-chain sugar - into short-chain sugars, by cutting them at the right position,” explains Dr Lassmann. The steam explosion process is one of Sekab’s core technologies, with technology experts able to modify how it is run so as to maximise the amount of cellulose that is subsequently made available for enzymatic hydrolysis, while Dr Lassmann says there are also other factors to consider. “It’s also important to minimise the amount of acids or inhibitors that are produced during the pre-treatment process, as they can limit the effectiveness of the enzymatic hydrolysis,” he outlines.
By modifying the operational conditions of the reactor, in particular the temperature, pressure and residence time, Dr Lassmann and his colleagues are able to influence the
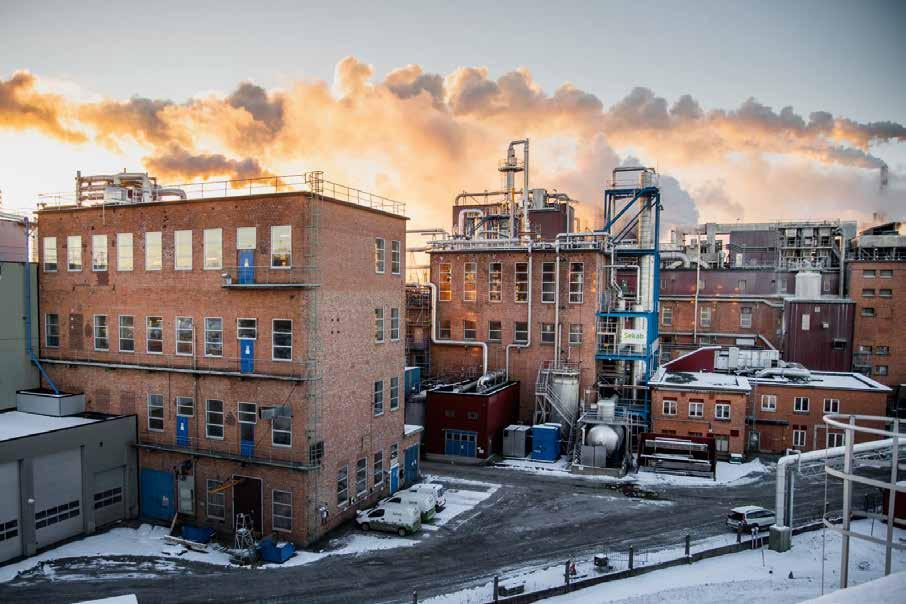
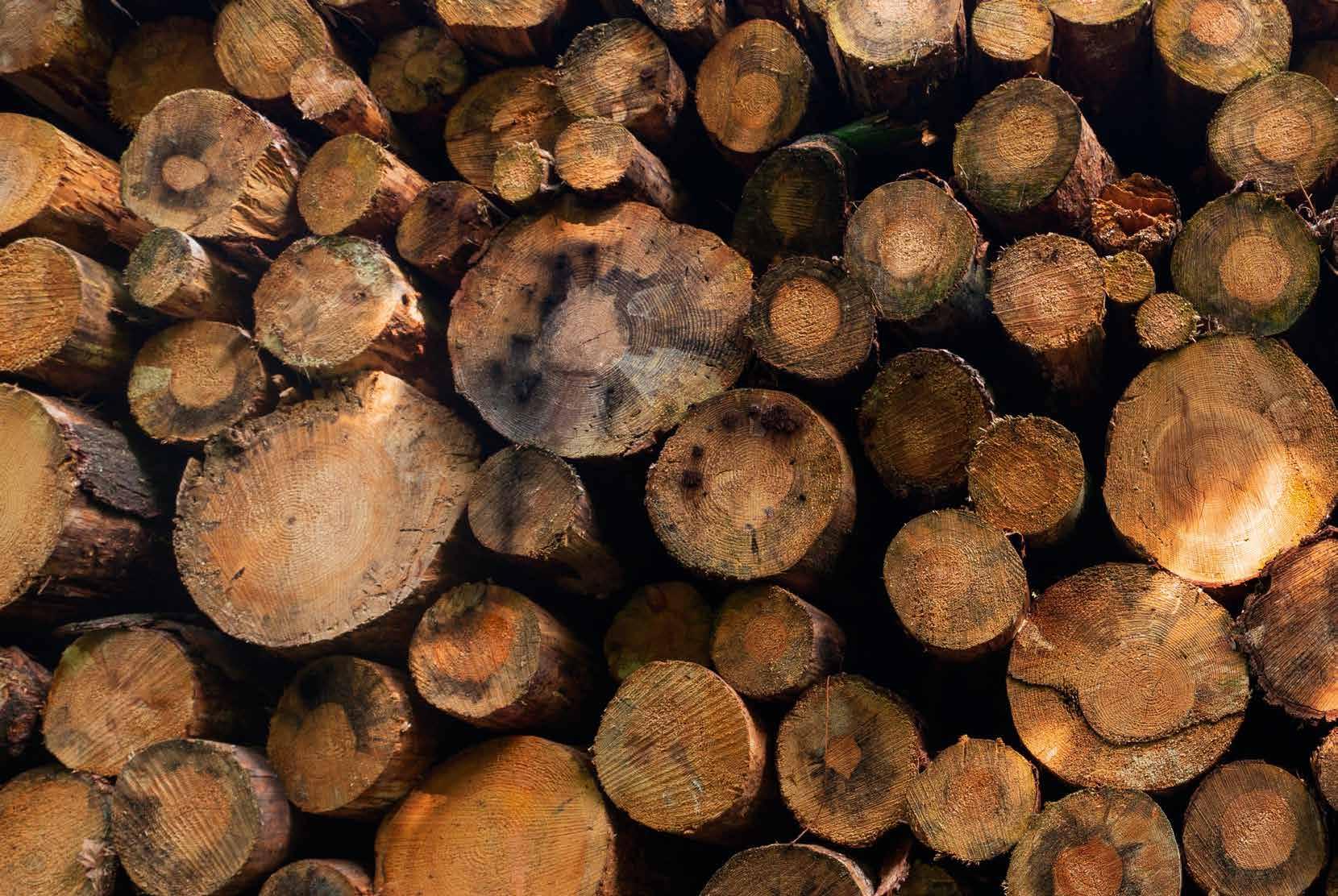
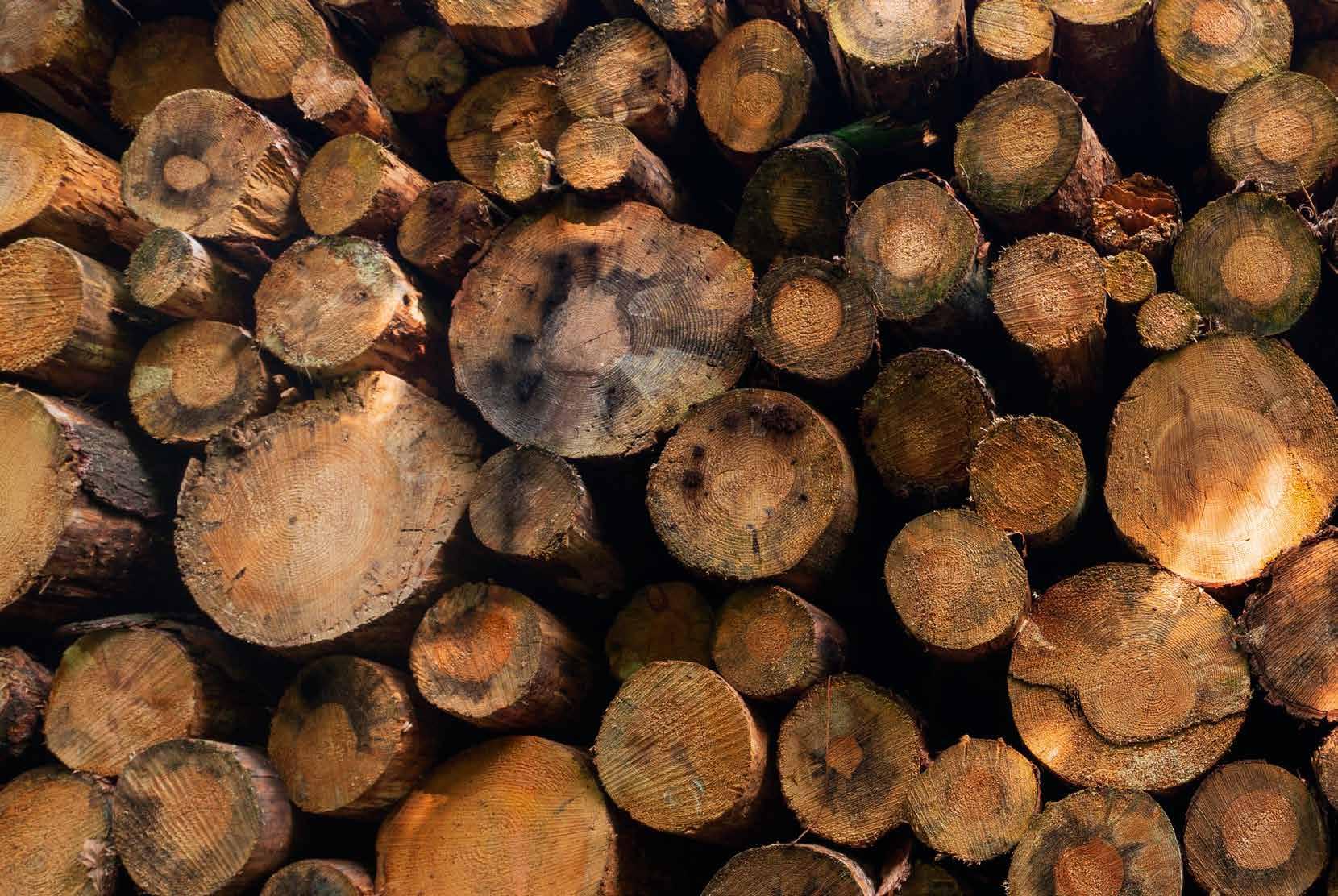
Biorefinery Demonstration Plant (BDP), Örnsköldsvik, Sweden
result of the steam explosion process and so steer it towards certain applications. In the case of biofuel production, once the right amount of sugars are available, there are then several further steps in the conversion process. “A partner in the project called Global Bioenergies has developed a process where they can ferment the sugars to bioisobutene (Bio-IBN). The Bio-IBN is then further converted into fuel components ETBE, Iso-octene and Iso-dodecene, utilizing proprietary technology developed by Neste,” says Dr Lassmann. Other partners in the project are involved in producing the jet fuel, while Dr Lassmann says experts at SkyNRG are also looking to assess its performance. “The people at SkyNRG are currently working with the certification process, utilizing fuel samples that have been produced during the project. These certification processes can take a long time,” he says.
Co-product valorization
This work on biofuels is a central part of the project, yet there is another dimension to REWOFUEL, with several of the partners also looking to make use of certain outgoing coproducts. This includes lignin, which can be used as a replacement for bitumen in asphalt. “ When you produce asphalt you work to a kind of recipe and you have a certain amount of ‘filler’. Depending on what type of asphalt you produce, there are certain standards that need to be fulfilled. These standards define the recipe for the amounts of binder and filler in the asphalt,” explains Dr Lassmann. Over the course of the project, experts at PEAB Asphalt have explored the impact of introducing lignin later on in the asphalt production process. “The lignin turns more into a sort of filler. The lignin that we produced in our demo facility has been put into bitumen for industrial stock, and a method has been developed for how it can then be blended in and used. This was used by PEAB for testing at laboratory scale as well as in field tests,” continues Dr Lassmann. “So far the field tests have shown positive results, with road samples suggesting the material is well-suited to this application. Now we have to see the long-term effects, such as how the different test roads deal with sustained traffic, which can take a few years.”
A further aspect of the project’s work involves using residual biomass to provide microbial protein for animal feed, part of the goal of improving resource efficiency. With every step involved in the fuel production process, the capital expenditure required increases, which Dr Lassmann says heightens the need to valorise the co-products generated along the way. “One of the goals of this project has been to valorise all the outgoing products as much as possible,” he outlines. This will improve the efficiency of resource use and in the process reduce greenhouse gas emissions, helping address environmental concerns. “In the project we are trying to figure out different kinds of processes to make the best use possible of the raw materials available,” says Dr Lassmann. “The ambition in the project was to produce high-performance drop-in biofuels from abundant resources, and to achieve a high level of co-product valorization.”
A significant degree of progress has been made over the course of the project in this respect, with the partners working to improve yield and productivity at every stage, demonstrating the efficiency of the process and the performance of the products. The first step with the biofuels would be to use them as a drop-in fuel, that can replace at least a certain proportion
REWOFUEL gasoline and aviation fuel production process from residual wood.
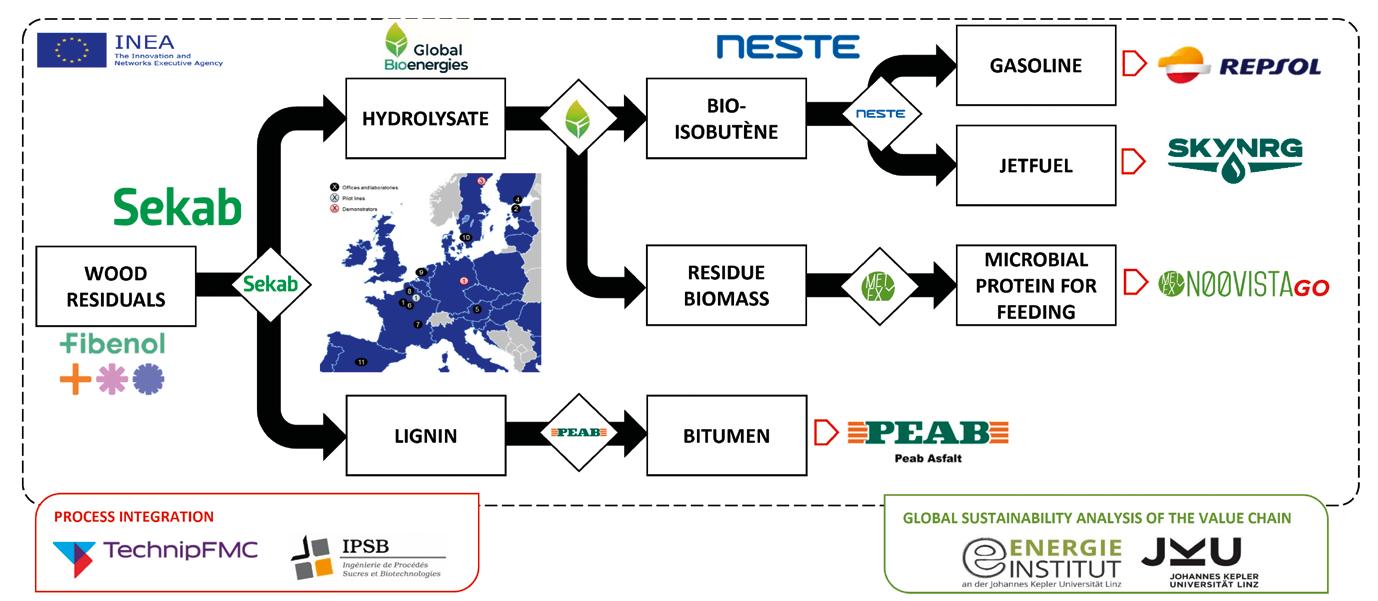

of the fossil-based fuels, and Dr Lassmann says the ratio could be increased further in future. “A certain maximum amount of biofuels can blended into aviation fuel, with the regulations varying across different countries,” he outlines. On the co-products, a lot of effort has gone into ensuring that the feed formulation is suitable for animal feed, while Dr Lassmann says the experts at PEAB asphalt are also working to increase the amount of lignin that can be blended into the asphalt. “The more you can reduce the amount of bitumen you have in your asphalt, the better. It is important to find the maximum amount of bitumen that can be replaced with lignin while still maintaining the necessary quality of the asphalt,” he stresses.
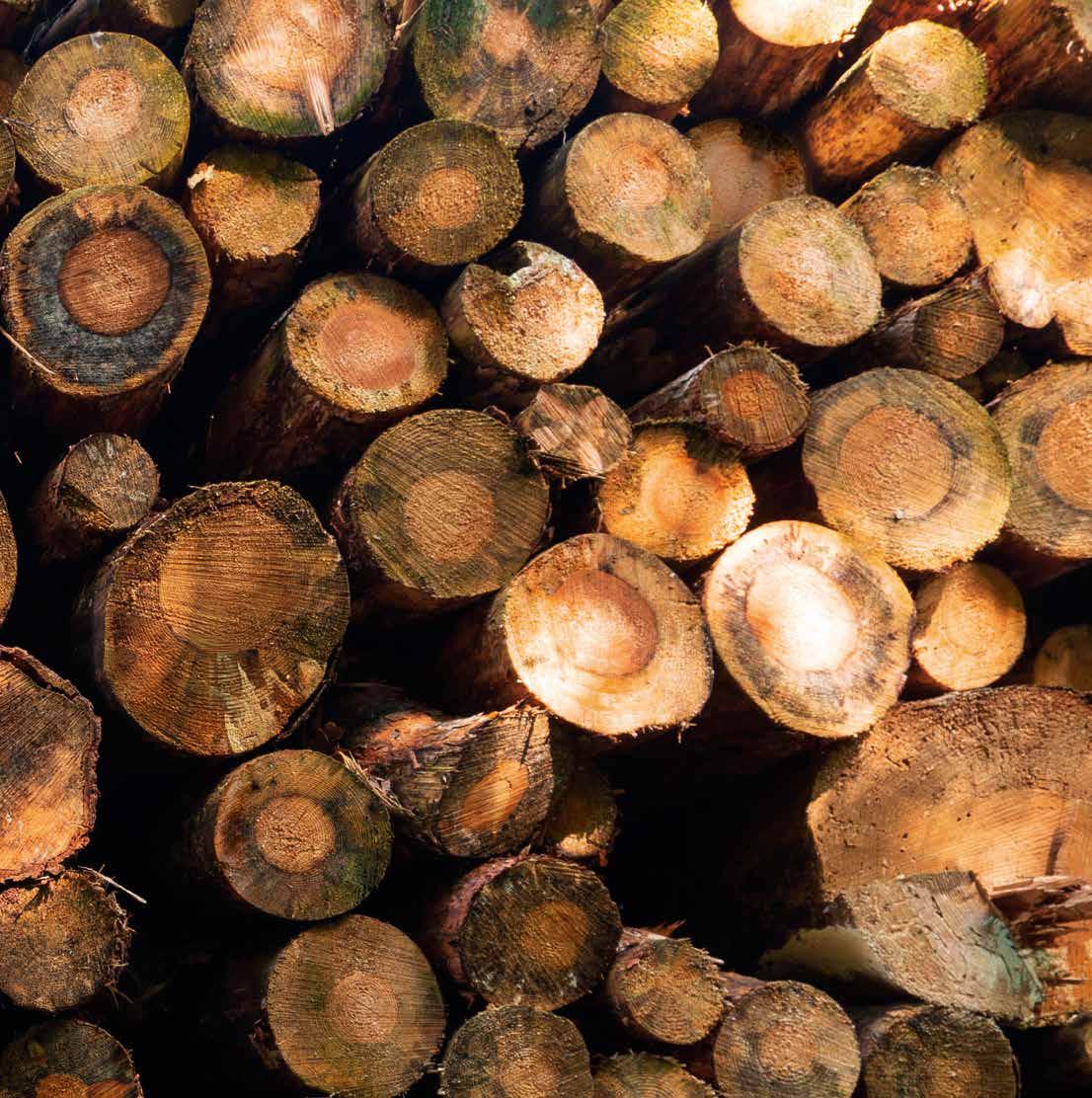
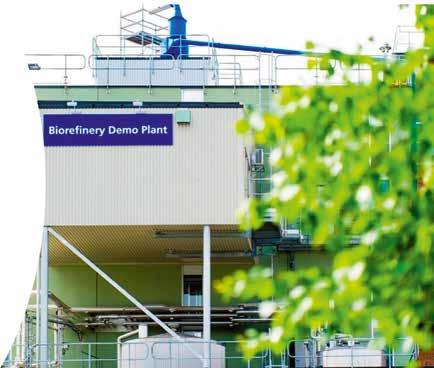
Biorefinery Demonstration Plant (BDP)
At Sekab we have the skills and knowledge to open up or convert biomass into sugars. These sugars are then
Environmental concerns
This research is being conducted against a backdrop of growing concern over the environment, with the industrial sector under pressure to reduce emissions of greenhouse gases. The REWOFUEL project could have a significant impact in this respect, potentially replacing around half of the overall aviation fuel market, while also demonstrating that alternative sources to fossil fuels can be developed. “It’s about utilising the resources you have locally to find substitutes for fossil-based materials or fuels,” says Dr Lassmann. Sweden has access to large amounts of biomass, and Dr Lassmann hopes the project will help identify ways in which this resource can be used effectively in supporting the sustainable industries of the future. “There are companies from different parts of Europe working together in REWOFUEL, using their expertise in different fields to find new pathways of developing biofuels,” he says.
The cost is of course an important consideration, and ultimately the process has to be economically feasible. Some steps may prove to be too expensive, while Dr Lassmann says others may be modified and tweaked in certain ways. “Where do we have to increase the productivity to make the overall process economically feasible?” he outlines. The aim is to make the best possible use of the available material, reflecting wider sustainability concerns, which is the subject of detailed analysis in the project. “In the project researchers at the Energieinstitut an der Johannes Kepler Universität in Linz have performed a global sustainability analysis of the whole value chain, while the process integration was performed by Technip FMC and IPSB from France,” continues Dr Lassmann.
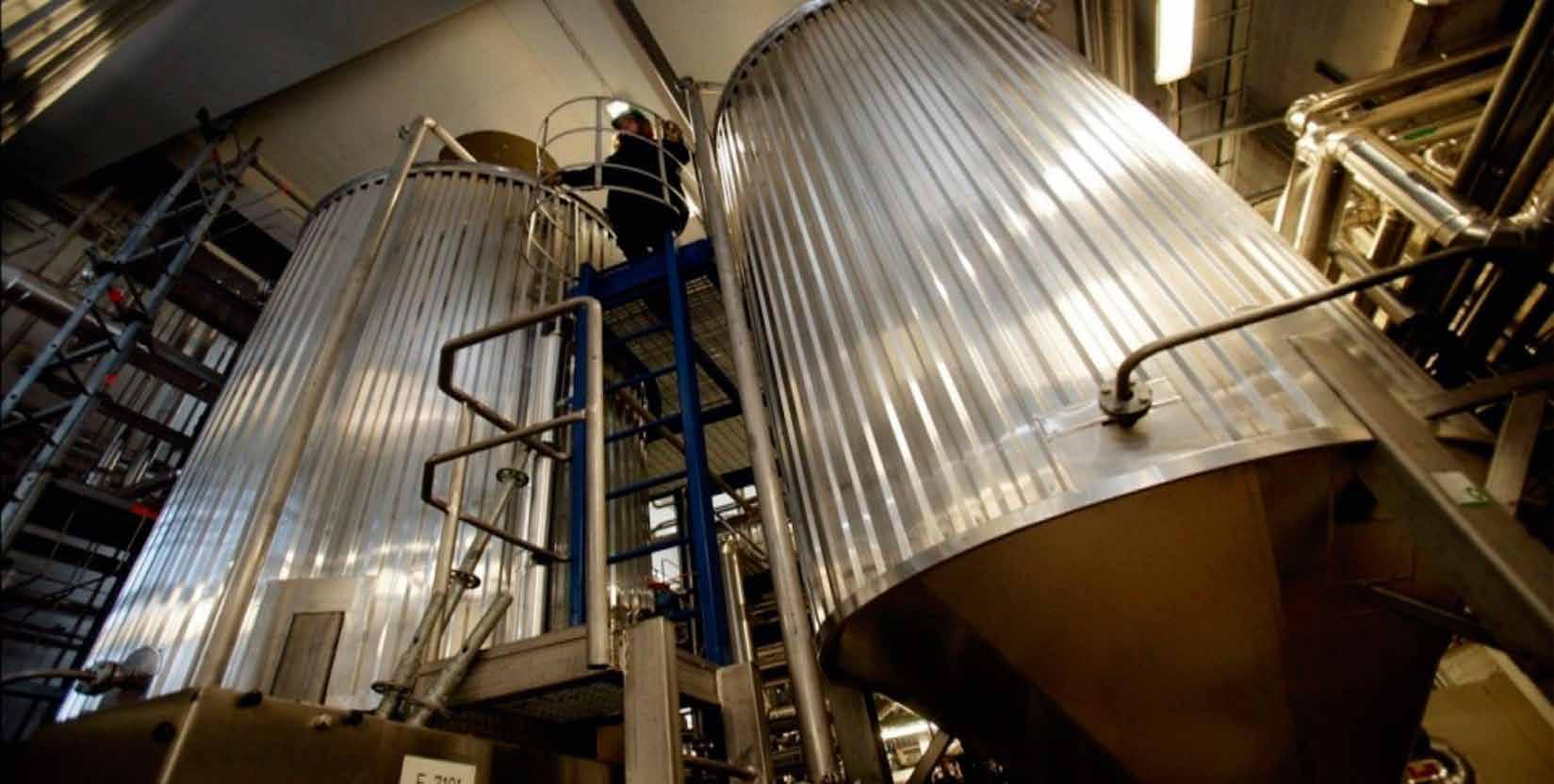
REsidual soft WOod conversion to high characteristics drop-in bioFUELs Project Objectives
During the course of the REWOFUEL project, the consortium was able to demonstrate the production of residual wood hydrolysate and establish a quality standard for RWH to feed an isobutene fermentation unit. Furthermore, the production of bio-IBN based biofuels from this RWH standard material at a representative scale was performed, whilst the valorization of lignin and other coproducts was demonstrated. A concept for a first of its kind commercial plant was developed, achieving the defined economic, social and environmental performances levels to a certain extend.
Project Funding
This project has received funding from the European Union’s Horizon 2020 research and innovation program under the grant agreement No 792104.
Project Partners
Project partners can be seen represented in the process diagram on the opposite page.
Contact Details
Tino Lassmann Senior Process Engineer & Project Manager Sekab E-Technology AB Hörneborgsvägen 12 SE-89250 Domsjö SWEDEN T: +46(0)660 794 84 E: Tino.Lassmann@sekab.com W: http://rewofuel.eu/
Tino Lassmann
Dr. Tino Lassmann holds a position as Project Manager & Senior Process Engineer at Sekab, specializing in process design & development from pilot scale to industrial scale of bioconversion processes. Postgraduate education from the Vienna University of Technology includes PhD in chemical engineering, with a specialization in thermal process engineering. Originating from Austria, he has been working for Sekab since 2018, managing national and international funded projects and collaborations, as well as customer projects. He has 10 years of experience in simulation, balancing, analysis, model development, process integration and optimization of industrial processes - within scientific research as well as in the chemical and pharmaceutical industry.
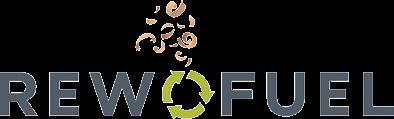
