HIGHWAY ENGINEERING AUSTRALIA
APRIL/MAY 2024
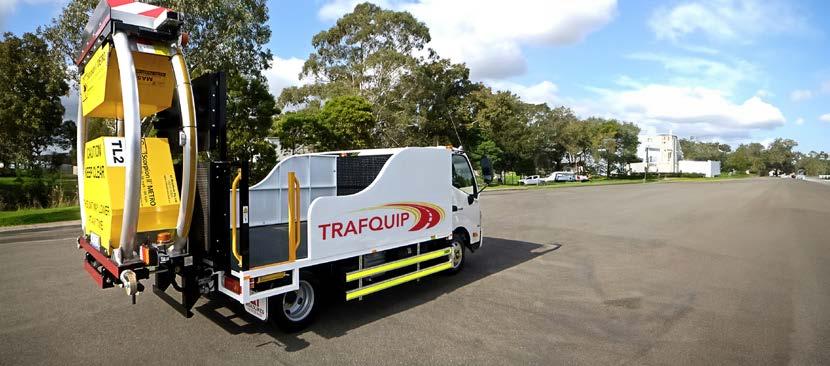
V55.3

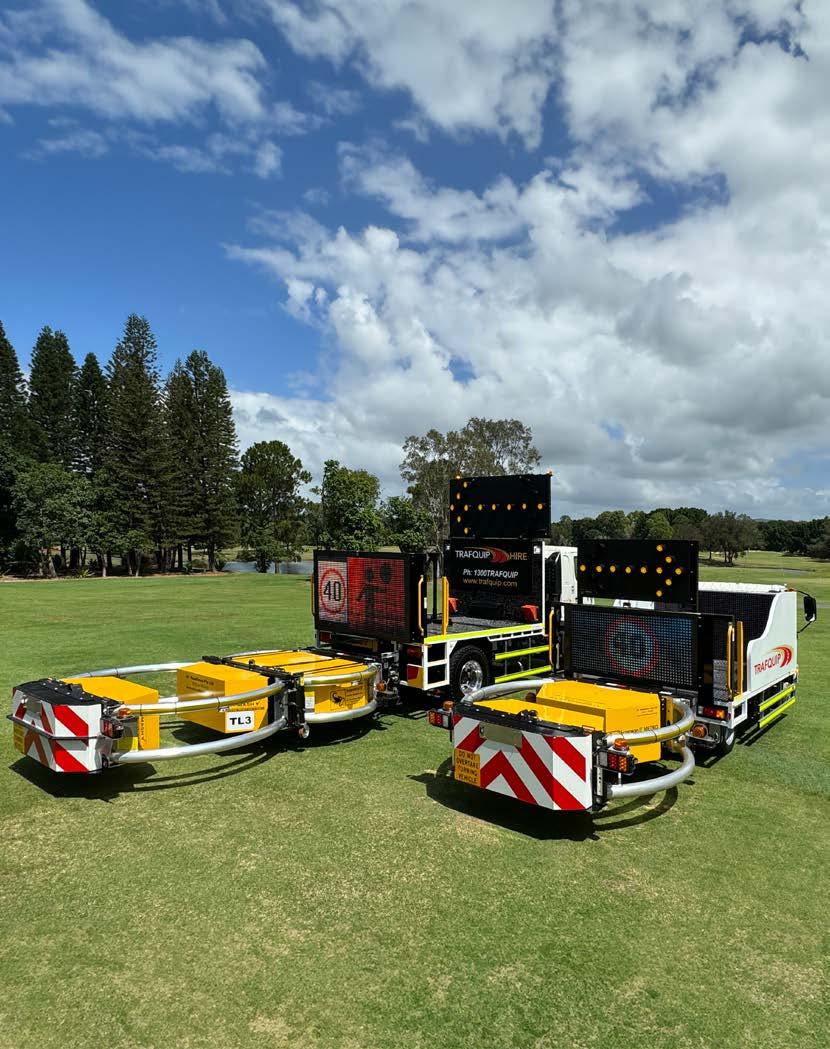
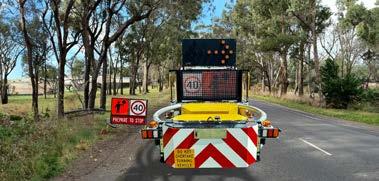

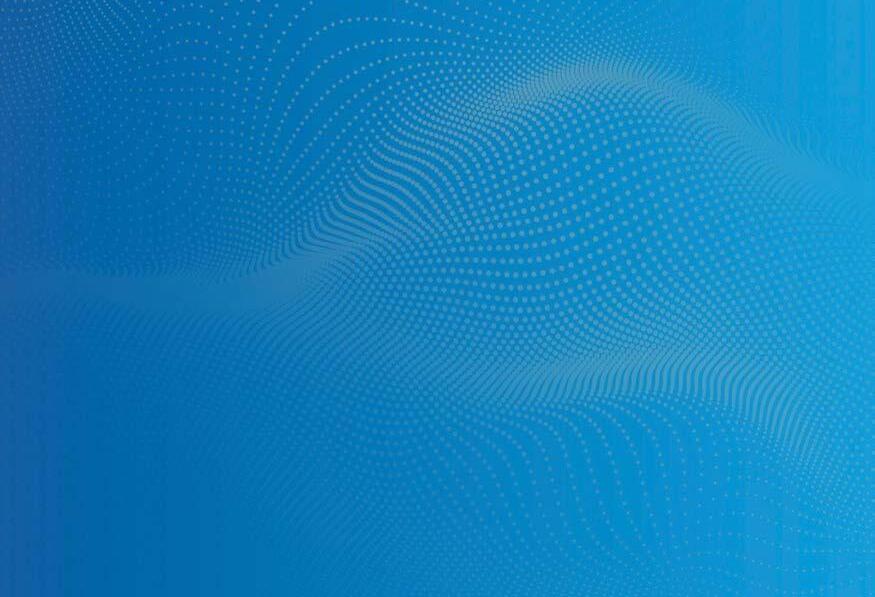
APRIL/MAY 2024
V55.3
Our integrated vehicle technology suite features advanced telemetry, video, and infotainment systems. It is supported by an automotivegrade cloud platform and cloud connectors that enable predictive analytics, detailed reporting, and effective fault code case management. Connecting manufacturers, dealers, fleets, and drivers seamlessly.
Discover why the world’s leading OEMs and fleets rely on our Australian-designed, turnkey solutions.
directedtechnologies.com.au
Investing in transport infrastructure to meet the needs of our expanding cities
Dear Readers,
While few would question the complexities associated with urban planning and development, it is also clear that in some areas - particularly ‘urban sprawl areas’ - something appears to have ‘gone badly awry’.
More specifically, it appears that regardless of the much-touted focus on ‘building communities’, the provision of appropriate supporting transport infrastructure, or for that matter, ensuring the suitability and/or capacity of existing infrastructure in the vicinity of many new developments is still, for many, a secondary consideration.
That’s not to say that the majority of commercial and residential developers don’t focus on providing infrastructure within the new developments - quite the contrary.
Indeed, for most developers, highlighting the array of facilities and services within the new residential estate or commercial area is often the number one selling point.
Unfortunately, in the majority of instances, it appears that the focus on quality infrastructure extends only as far as the boundaries of the development precinct.
More often than not, there appears to be little or no concern on behalf of those involved about the impact that a sudden – and often substantial - increase in population (working and/or residential) and, in particular, the impact that the associated increases in vehicular traffic or increased demand for
public transport, will have on the surrounding areas.
These issues are further compounded by the fact that in recent years, many new developments are now being marketed as ‘multifunction’ or ‘mixed-use’ precincts, where there is a particular focus on the establishment of home offices and/or micro businesses as well as residential dwellings. While this approach does have its benefits in terms of reducing long-distance commuting for many residents, it does increase vehicular activity and demand on infrastructure within the development area, often by attracting additional ‘inbound’ traffic.
These issues are further compounded by the fact that in the outlying and, in many instances, semi-rural areas that are often chosen as the location for these new developments, the existing infrastructure - particularly in terms of roads and drainage - is often well past its ‘use-by date’ and is already being expected to cope with demands that far exceed the original design specification.
With that in mind, I believe that unless we urgently address the problems associated with the lack of appropriate infrastructure and facilities in the areas around these new estates and developments, we are seriously running the risk of undoing much of the excellent work that has been done in recent years to improve the quality of life in our cities -particularly in terms of our road network.
It’s simply not good enough to place a set of traffic lights at one entry to a new estate and
consider it effective ‘traffic management’.
Sadly, there are a number of major new estates that haven’t even provided traffic lights! And even if there are traffic lights, they do nothing to overcome the problems of traffic congestion that result from the introduction of hundreds (if not thousands) of additional vehicles onto an already ‘overstretched’ road network - a road network which in many instances was never designed or intended to carry such high levels of traffic.
I believe that the only way to overcome these issues is to take an holistic approach to infrastructure development - one that considers the wider ‘footprint’ of these new developments and takes into account the ‘true’ impact on the surrounding areas.
Needless to say, this process must then also deliver appropriate funding for the development and delivery of suitable infrastructure in the areas surrounding new estates. And this new and/or upgraded infrastructure needs to be delivered and fullyoperational prior to the completion of the new estate - lest we run the risk of developing very expensive suburbs with second-rate facilities and access.
Anthony T Schmidt Managing Editor
Three winning entrants were announced for this year’s Intertraffic Awards at the event’s opening ceremony in Amsterdam. Chairman of the awards jury Pieter Litjens, took to the stage in the packed main theatre, to reveal the three winners chosen from the shortlist of 15 nominees.
A theme that marked out two of the winners was noise reduction. Italian company See won the Green Globe Award for its highly innovative Whisper NB-Eco-40-A3 acoustic panels, while UK-based Intelligent Instruments won for its Sound Vue noise-enforcement camera system in the User Experience category.
Meanwhile, the coveted Inspiration Award, was won by another British company Valerann, which particularly impressed the jury with its advanced real-time data analytics platform Lanternn by Valerann.
Litjens, who is director of CROW, the knowledge institute for infrastructure, public space and mobility – and the other members of the jury: Margriet Van Schijndel, programme director for Responsible Mobility, TU/e; Jorrit Weerman, founder and CEO of the Parking Network, Adam Hill, editor of ITS International and Tom Stone, editor, TTi and Intertraffic World – spent an entire day hearing presentations from the 15 nominated companies before eventually coming to a joint decision on the winners, after some heated debate.
A statement from the jury reads: “All the nominees to this edition of the Intertraffic Awards
were of an incredibly high standard, which gave the jury an extremely difficult task to pick just one winner in each of the three categories.”
“Whisper acoustic panels certainly weren’t the only product focusing on reducing noise from road transport. However, they were, the jury felt, worthy of the Green Globe Award due to not only their innovative low-CO2 production method but also that they completely do away with the need for any surrounding casing to protect them so that they can be easily attached to any existing wall, and last for at least 50 years. The sheer usability – instantly reducing the materials required for building noise barriers – and also their recyclability meant See Whisper can make a real, immediate difference to carbon footprints.”
“Sound barriers help reduce background noise from traffic, however, sometimes certain individual vehicles can be so loud that they break the law. Until recently enforcing such laws was challenging. But now, Intelligent Instruments has created Sound Vue. Using a combination of video, AI and ANPR, Sound Vue can detect and fine vehicles that break legal noise levels. The jury felt this represents a new trend in enforcement but the key reason that Sound Vue was deemed worthy of the User Experience Award was due to its elegant user interface and the ease with which the enforcement process can be automated.”
“The Inspiration Award went to Valerann for creating Lanternn by Valerann, a traffic management platform that seamlessly integrates
Since the launch of its Amsterdam event in 1972, the Intertraffic name has become synonymous with the leading global industry platforms for smart mobility, infrastructure, traffic management, road safety, and parking.
Intertraffic events are staged in the Netherlands, China and Mexico, offering comprehensive overviews of the very latest products, services and total solutions offered by suppliers, while also showcasing innovative industry-wide trends and developments.
Intertraffic is intended for policymakers, specialists and operational personnel from government authorities, engineering consultancies, and the industry at large.
More information is available at: www.intertraffic.com
all the very latest data sources and delivers them in such a dynamic and uniquely actionable way that the jury felt it to be one of the most versatile and usable innovations ever seen. It takes familiar concepts in traffic optimisation and delivers them in such a highly accurate way, that it enables a new level of real-time reactions, that the jury believes it will inspire urban mobility management for years to come.”
At the end of the opening ceremony, the Intertraffic Amsterdam show floor was officially declared open and the event’s knowledge sessions commenced, with ceremony attendees dispersing amid an atmosphere of excitement.
The New South Wales state Government is supporting the target of net zero infrastructure delivery with a new policy, measurement guidance and roadmap. The State Infrastructure Strategy recommended that NSW Government work towards net zero in the infrastructure sector, including through reducing embodied emissions in construction.
In support of the broader net zero target, the NSW Government is launching the Decarbonising Infrastructure Delivery Policy, which sets expectations for Government agencies on managing embodied carbon in public infrastructure projects. The policy, co-designed with NSW Government agencies and industry, will ensure upfront carbon emissions generated during the production of materials and the construction of infrastructure, is a key consideration across all project stages and carbon information is collected consistently for government projects.
A key aim of the policy is to uplift NSW Government agencies’ carbon management capabilities and to ultimately work towards targets for carbon reduction in infrastructure delivery.
To supplement the policy, Infrastructure NSW has developed guidance on measuring embodied carbon for all infrastructure types.
Speaking about the new policy, Infrastructure NSW Chief Executive Tom Gellibrand said the reducing embodied emissions requires a collaborative approach with all members of the industry supply chain and is necessary to ensure infrastructure built today is positioned for a net zero future.
“This new policy and measurement guidance will ensure NSW is among the world-leading jurisdictions to have a consistent approach to embodied carbon measurement across all asset types.”
“Infrastructure NSW will continue to engage closely and transparently with industry in implementing the policy to ensure everyone is on the same page and reaching for the same goal,” he said.
“The ultimate outcome of this work is to have carbon considered at
every stage of project decision-making as part of standard practice in infrastructure delivery, to drive our mutual goal of achieving net zero emissions by 2050,” Mr Gellibrand added.
Providing a policy and guidance on measurement of embodied emissions will give industry and Government the mandate and confidence to act to reduce emissions across the project lifecycle. The policy will apply to all NSW Government infrastructure delivery agencies, and to capital infrastructure projects over $50 million in the building sector and over $100 million for other infrastructure.
Transport for NSW Secretary Josh Murray, commented: “As the largest infrastructure delivery agency in NSW, Transport for NSW is delighted to be partnering with Infrastructure NSW to pave the way to net zero emissions for our state.”
“This new measurement guidance and TfNSW’s pioneering sustainable procurement approach is now being developed at a national level.”
“Working in collaboration with industry, we will use the purchasing power of our $72.3 billion capital pipeline to accelerate decarbonisation in the infrastructure sector,” Mr Murray said.
There will be a 12-month transition period before the policy becomes operational in 2025, during which time the NSW Government will continue to work with industry and Government agencies to effectively implement the policy.
The Decarbonising Infrastructure Delivery Policy and measurement guidance are part of Infrastructure NSW’s and Transport for NSW’s Decarbonising Infrastructure Delivery Roadmap which lays out the NSW Government’s plan and activities to reduce emissions across all project stages over the next three years.
To find out more, visit: https://www.infrastructure.nsw.gov.au/expertadvice/decarbonising-infrastructure-delivery
DYNAMIC INFRASTRUCTURE leverages all available asset condition data, reports and images - regardless of the format or age - to build a detailed chronological ‘health record’ for each bridge asset - providing you with immediate access to all your asset data and empowering you with actionable insights that lead to cost savings and improved maintenance e ciency.
With DYNAMIC INFRASTRUCTURE there is no need to change your current bridge inspection methods or service provider. The system utilises all existing data and reports, regardless of the format or age -including paper-based engineering drawings and plans, photos, paper-based inspection and condition reports, together with digitised data and images - to build a detailed ‘health record’ for each bridge asset.
Using DYNAMIC INFRASTRUCTURE’S AI-enabled technology to identify faults and damage e ectively transforms the entire process from a subjective one that relies on an individual to find and identify all faults on a structure and then make a judgement call on severity, to an objective one where over 99% of faults are identified, categorised, logged and then rated for severity against a global database of over 30,000 bridges and counting.
DYNAMIC INFRASTRUCTURE enables you to identify defects before they escalate into major failures, helping you to better manage risk and prevent unexpected expenses. It can even help you maximize warranty coverage through automated repair tracking - providing you with full visibility from the field to the o ce.
You’ve been asked to find ALL of the historic inspection, repair and maintenance data for just one of your bridge assets…. How long would it take?
A couple of hours? A couple of days? Longer?
With DYNAMIC INFRASTRUCTURE you can access ALL of your bridge asset data – including plans and historic inspection data (manual reports) as well as details of faults, damage, repairs and maintenance –within a matter of seconds.
All of the data, for each of your bridge assets, right at your fingertips… in one comprehensive, chronological digital ‘health record’ …and the MASSIVE TIME SAVING is only one of the benefits!
DISCOVER MORE
Specialist heavy-lifting and transport equipment
manufacturer Mammoet has supported ESTA in establishing new stability guidelines for Self-Propelled Modular Trailers (SPMTs) when transporting large and heavy loads. ESTA is the leading European association for the abnormal road transport and mobile crane rental industry.
Leading the project at Mammoet is Ludo Mous, Director of Operations for Europe. With over 30 years of industry experience, Mous has seen the market change and is passionate about enhancing SPMT training and safety.
Mous said: “In the past, there were rules of thumb which, for the time, were practical and acceptable to use. However, these days, with transport becoming more complex and reaching greater limits, the calculations for stability must be correct. By creating awareness of these guidelines, we hope to prevent operations being performed with dangerous and critical transports.”
Mammoet was part of ESTA’s first SPMT working group, established in 2016, which created its original Best Practice Guide for SPMT operation. A second, larger workgroup was later formed to review the existing guide and expand on it.
In October 2023, ESTA published new trailer stability guidelines, which will be referenced in the first upcoming revision of the DNV ST-N001 Maritime Operations Standard, published by assurance and risk management experts DNV.
“The core principle of the guidelines is a calculated approach,” explains Mous. “Past guidance was based on a measured stability method. This new method is calculating stability taking into account dynamic factors like braking, acceleration, wind, road camber, and so on.”
To establish the guidelines, testing was carried out by Mammoet on SPMTs at its quayside yard in Schiedam, the Netherlands. It covered aspects such as acceleration, breaking, tilting and emergency stops.
Currently, the group is reviewing a learning outcome that will be used to establish the minimum training requirements for an SPMT operator, further enhancing user knowledge and safety.
Australia and Singapore, which is home to the world’s busiest transhipment hub, have partnered on a $20 million initiative to help reduce emissions in the maritime sector.
The Australia-Singapore Initiative on Low Emissions Technologies (ASLET) for maritime and port operations will be jointly delivered by CSIRO, Australia’s national science agency, and the Maritime and Port Authority of Singapore (MPA). ASLET intends to support the outcomes of the Singapore and Australia Green and Digital Shipping Corridor (GDSC), which will help decarbonise and digitise shipping routes between Singapore and Australia.
The Governments of Australia and Singapore signed a memorandum of understanding to formally collaborate on establishing the GDSC, which was welcomed at the 9th Annual Leaders’ Meeting in March 2024.
ASLET is expected to unlock new fuel solutions and accelerate the deployment and uptake of zero or near-zero greenhouse gas (GHG) emission technologies at scale, and will explore cooperation opportunities between Australia and Singapore in green shipping and port infrastructure initiatives.
The initiative presents a significant opportunity for both countries, given Singapore’s position as the world’s largest bunkering and busiest transhipment hub port and Australia’s potential to be a leading producer and exporter of low-emissions fuels.
MPA Chief Executive, Mr Teo Eng Dih said, “ASLET has the potential to translate research outcomes from the scientific community from both countries and to use these technologies to help scale up the production and deployment of low-emissions fuels and technologies at scale.”
“Given Australia’s natural advantage for renewable energy production and Singapore’s hub status, MPA looks forward to making this partnership deliver value to the Singapore-
Australia GDSC and the wider international shipping and port communities,” said Mr Teo.
CSIRO Chief Executive Dr Doug Hilton said the collaboration addresses the key industry challenges faced when adopting low-emission fuels.
“In order to reach net-zero greenhouse gas emissions from international shipping close to 2050, we need to find reliable, trusted scientific solutions for the industry,” Dr Hilton said.
“We need to focus on transitioning to lowemissions fuels such as ammonia and hydrogen by developing accessible technology and infrastructure at ports that support a range of vessels.
“Collaborating with MPA and also industry partners from both countries, we aim to accelerate the decarbonisation of the supply chain and help revolutionise the industry.”
The first ASLET Steering Committee meeting, led by representatives from MPA, CSIRO and Singapore’s Agency for Science, Technology and Research (A*STAR), was be convened on 19 April at the Singapore Maritime Week 2024. The Steering Committee, established as part of a joint collaboration agreement, aims to provide strategic direction and evaluate and approve projects on low-emission technology projects for maritime and port operations.
The Steering Committee intends to issue a grant call to develop a pipeline of projects consistent with its focus areas and accelerate joint efforts between both countries in maritime decarbonisation. As part of ASLET, both Singapore and Australia will commit up to $10 million each in their respective currencies to deliver projects under the initiative. It is expected that the program will also attract industry co-funding.
The initiative will facilitate the research, demonstration, and commercialisation of zero and near-zero greenhouse gas emission technologies, fuels and energy sources for use in maritime shipping and port operations.
In his first public speech as Chief Executive Officer of Inland Rail, Nick Miller has told the Australasian Railway Association Rail Freight Conference in Sydney that Inland Rail is on track to deliver strong progress in 2024, as it seeks to complete the Beveridge to Parkes sections by 2027, in line with the recommendations of the independent review into Inland Rail.
Having recently completed successful possession works on the Beveridge to Albury project in Victoria and the Stockinbingal to Parkes section in New South Wales, Miller told conference delegates that Inland Rail was making strong progress towards to completing the Beveridge to Parkes sections by 2027.
Miller said Inland Rail environmental approvals in New South Wales were also progressing well, with the New South Wales government in the final stages of the approvals process for the Albury to Illabo and Illabo to Stockinbingal sections in southern New South Wales with the Australian Government having approved the Narromine to Narrabri section in February. In Queensland, Miller told the conference
that Inland Rail was hopeful of finalising the Environmental Impact Statement for the Border to Gowrie (B2G) section with the Queensland Co-Ordinator General in the coming months.
With construction moving ahead in New South Wales and Victoria, Miller said Inland Rail was already delivering substantial direct benefits to rural and regional communities during construction, noting that over $420 million has been spent with over 530 local businesses on the alignment, with some $42 million spent with nearly thirty First Nations businesses.
already been completed in New South Wales, work is well underway on a third, and we should receive two more major environmental approvals in the coming months,” he said.
“Inland Rail is one of the biggest infrastructure projects ever undertaken by the Australian Government, it is a critical part of the transport supply chain and the economic development of Australia and is needed to keep pace with the freight demands of our growing population,” Nick Miller said.
“Like all major projects Inland Rail has had its share of setbacks and challenges, and I dare say there are more to come in the years ahead.”
“However, let’s make one thing clear, Inland Rail is not a ‘stalled project’, we are making strong progress on the ground, two sections have
“More importantly, we are also delivering significant benefits for regional communities, last month we saw the first GrainCorp train travel on the upgraded Narrabri to North Star line, picking up canola at Croppa Creek and taking it all the way down to the Port of Newcastle for global export,” Mr Miller added.
“This is what Inland Rail is all about, opening up new opportunities for our critical primary producers in rural and regional Australia, allowing them to take get their products to domestic and international markets quickly and costeffectively,” he concluded.
Daimler Truck has selected global logistics leader
DB Schenker to operate its new 20,000 square metre warehouse in Melbourne, encompassing more than 44,000 SKUs for truck and bus parts.
The new warehouse, located about 23km from the Melbourne CBD and 20km from Tullamarine Airport, has been designed to strengthen Daimler Truck’s ability to supply stock and parts across Australia and New Zealand, and stocks everything from small washers to full truck cabs.
“This warehouse is the first Daimler Truck operation in the world to stock parts for three different truck brands all under the one roof,” says Craig Davison, CEO, DB Schenker Australia and New Zealand Cluster.
“Daimler Truck Australia Pacific offers a vast range of class-leading vehicles covering every segment of the Australian road freight industry with its Mercedes-Benz, Freightliner, and Fuso trucks, as well as Fuso buses.
“We were delighted to build on our long-term and productive relationship with Daimler Truck with the contract to operate this new warehouse,” he adds.
The warehouse has more than 70,000 individual locations, including a 4,000m2 mezzanine level, and customised racking to store large truck cabs. A super awning of approximately 3,400m2 was constructed so that parts could be loaded and unloaded in full protection from the weather. The warehouse itself has a high clearance section, with additional pallet storage above 10m in height.
The building has a five-star Green Star rating, and includes EV charging stations that staff can use, a focus on recycling, and LED lighting with motion control throughout the facility. The focus on sustainability aligns with DB Schenker’s global commitment towards a more sustainable future.
In addition to operating the warehouse, DB Schenker also handles the leasing of the premises in Melbourne’s West.
“We worked with Daimler Truck to find a solution that suited their needs now, and into the future. The site typically has more than 50 onsite employees on any given day, with more during peak demand periods,” said Davison.
“There’s flexibility built into the warehouse operations because we know needs can change. The combination of this state-of-theart warehouse with DB Schenker’s operational experience will help maximise customer uptime by ensuring that truck and bus parts are where they need to be, when they need to be there,” he added.
“Daimler Truck is a world-class brand, and DB Schenker has been able to leverage our considerable global experience and resources to set up warehouse operations that maximise efficiency, and help Daimler Truck deliver on its customer service goals.”
Daimler Truck Australia Pacific President and CEO, Daniel Whitehead, says the introduction of the new warehouse represents a big step forward for the company.
“This new dedicated truck and bus parts warehouse is at the centre of our commitment to our customers across Australia. I would like to thank DB Schenker for working with us to introduce this sustainable state-of-the-art facility that will allow us to better serve our customers and meet their specific needs.”
The Volvo Group recently announced that it will build a new heavy-duty truck manufacturing plant in Mexico to supplement the Group’s U.S. production. The plant will provide additional capacity to support the growth plans of both Volvo Trucks and Mack Trucks in the U.S. and Canadian markets, and support Mack truck sales in Mexico and Latin America. The plant is expected to be operational in 2026.
The Mack LVO plant in Pennsylvania and the Volvo NRV plant in Virginia will continue to be the company’s main North American heavy truck production sites. The Group has invested more than $73 million over the last five years in LVO expansion and upgrades, and is currently investing an additional $80 million to prepare for future production.
The NRV plant is completing a six-year, US$400 million expansion/upgrade to prepare for production of the new Volvo VNL model.
The massive new plant will be approximately 158,000 square metres in size, and will focus on the production of heavy-duty conventional vehicles for the Volvo and Mack brands. It will be a complete conventional vehicle assembly facility including cab body-in-white production and paint.
Adding production in Mexico will deliver logistical efficiencies for supporting sales to the southwestern/western regions of the U.S., and to Mexico and Latin America. It also provides a mature supply and production ecosystem that will complement the U.S. system and increase the resilience and flexibility of the Group’s North American industrial footprint.
French industrial group MND, a major cable transport player, recently unveiled ORIZON™, its new range of cable transport solutions (gondolas and chairlifts) intended to provide reliable, high-performance, sustainable mobility solutions for mountain environments, as well as transport operators in urban and tourist environments.
With its innovative range of detachable, single-cable gondola lifts and chairlifts, MND group is consolidating its position as a global player and aims to win new market share in a fast-growing sector. The ORIZON™ range equipment caters to the most demanding configurations: steep gradients, long distances, large vehicles, and high flow rates. They are available in a wide range of configurations, from 6-seater chairlifts with or without bubble to 10, 16 and 20-seat gondolas, and capacities of up to 8,000 people per hour and per direction at speeds of up to 7 metres per second.
MND has invested 20 million euros in the development and industrialisation of its ORIZON™ range, as well as 10 million euros in the construction of a new production and assembly facility at Sainte-Hélène-du-Lac (Savoie-France). In addition, a first unit will be built on-site to allow customers can discover and test the products in a live operating situation.
Over the last few years, MND has mobilised a dedicated technical and industrial team of more than 60 people to design and produce this new generation of cable transport, with a mission to create a range with the following features: high-performance, reliable single-cable detachable technology using tried-and-tested components, large-capacity, easy access, innovating design cabins, high throughput with a low carbon footprint, greater wear resistance to optimise maintenance costs, and a patented Direct Drive motor directly connected to the pulley.
Special attention has been paid to optimising the installation's energy consumption, particularly in terms of recovering and using the energy produced by the gravity transport system, the automatic eco-drive system that adapts to flows in real-time, the recovery of heat for use in buildings, and integration of solutions to produce renewable solar energy.
MND worked with Stellantis Design Studio to design the new ORIZON™ ecosystem, which seamlessly integrates into natural, tourist and urban spaces, to enhance the transport experience, and promote a sustainable and efficient mobility solution. Because each project is unique, a vast catalogue of options has been designed to meet operators' technical and aesthetic requirements: interior/exterior colours and decoration, choice of materials, interior/exterior lighting, eco-driving system, automatic operation, integrated recovery, onboard information system, video surveillance, etc.
4" TRASH PUMP ... DIRTY WATER SPECIALIST ü Self priming to 7.6m ü Fast, easy set up ü Flows to 1,600 lpm ü 10HP Yanmar diesel ü Mine Boss model shown
Mobile Media Blasting - Soda & Garnet
• Specialising in Concrete preparation for Carbon Fibre application
• Abrasive & Non-Abrasive Blasting
• Paint, rust & contaminant removal from many substrates
• Line marking removal
• Graffiti removal & protection
• Removal of sealers & coatings
• Creation of non-slip surfaces
• Compact machinery for easy access
• Low media usage which means less environmental issues with reduced containments and dust
• Suitable for confined space blasting
Trafquip expands its fleet of Scorpion TMAs with new Scorpion® II TL3 and Scorpion® METRO TL2 units
Building on its existing fleet of more than 40 Scorpion® Truck Mounted Attenuators (TMAs), leading Australian traffic equipment hire specialists Trafquip has recently taken delivery of two new Scorpion® TMAs, including its first Scorpion® METRO MASH TL2-rated unit. Trafquip has also entered into a major Impact Protection Vehicle (IPV) building program, which will see the company secure 1-2 new TMA’s per month over the next 12 months.
Speaking about the new Scorpion TL2 unit, Trafquip Managing Director, Jeff Trim, said that it represented a major step forward for the industry, especially in terms of recognising the importance of providing protection for workers from vehicular impacts in work zones along suburban streets and in areas with posted speed limits of 70 km/h or less.
“Accidents happen above 70 km/h and below 70 km/h, so it’s critical to provide protection for all stakeholders in all locations,” Jeff said.
“While the larger Scorpion II unit provides MASH TL3 certified impact protection for speeds up 100 km/h, it’s not always practical, or for that matter, even possible, to have a large TL3-rated Impact Protection Vehicle at every worksite – especially those located along narrow suburban streets or low-speed roads.”
“Now, thanks to the new Scorpion® METRO units, we’re able to provide our customers with a fully tested, certified and approved MASH TL2-rated Impact Protection Vehicle that has been specifically designed for use along streets and roads with posted speed limits of 70 km/h or less,” he added.
“The traffic management industry is developing at an extremely rapid rate. Even looking back over the past 10 years, it’s easy to see how far things have come. The industry is maturing, and compliance is improving – not only across major projects but also along smaller suburban and regional worksites,” Jeff said.
“With that in mind, we believe that the Scorpion TL2 TMA can play a major role in boosting safety for workers along low-speed suburban and rural roadwork zones, and as such, we’re expecting to see a significant increase in demand for these units from councils and contractors alike,” Jeff said.
Established in Brisbane in 2007, Trafquip started out as a specialist traffic management design and planning company, providing services for councils and contractors across Queensland.
Building on this knowledge and experience, the company expanded into ‘dry hire’ (e.g. equipment only / no operator) of traffic management fleet and equipment. From Truck Mounted Attenuators (TMAs) – also known as Impact Protection Vehicles (IPVs) – Cone Trucks, Super Utes, Traffic Control Utes, Civil Vehicles and Management Vehicles, through to Lighting towers, Portable Traffic Lights, Variable Message Sign (VMS) Trailers, Portabooms, and eSAS (Electronic Speed Awareness Signs), Trafquip has built an enviable reputation for the supply of high quality, well maintained and reliable equipment.
“I always say, we don’t do compressors, generators and that sort of equipment. We only do traffic management equipment, because that’s what we know and understand,” Jeff Trim explained.
“We believe that our understanding of the industry and the traffic management business is our major advantage. So, rather than trying to be a ‘Jack of all trades and master of none’, we focus on ensuring that we provide safe, well-maintained traffic management equipment solutions for our clients.”
Not surprisingly, the decision to focus purely on traffic management fleet and equipment, combined with the team’s extensive first-hand industry experience, saw a significant growth in demand for its services. Indeed, from its relatively humble beginnings, Trafquip now provides traffic management vehicles and equipment to clients in Queensland, New South Wales, Victoria, Northern Territory and South Australia.
The company’s main depot in Loganholme, south of Brisbane, incorporates a large mechanical workshop and dedicated manufacturing/ fabrication facility, with a separate auto-electrical service yard located on an adjacent property. Trafquip also operates a depot and maintenance facility in the Adelaide suburb of Elizabeth South.
Trafquip’s fleet of equipment now encompasses more than 650 units, including more than 40 Scorpion TMA-equipped Impact Protection Vehicles.
“Everything about us is about protecting stakeholders,” Jeff Trim said.
“First and foremost, we’re a safety business, and we try and reflect that in everything we do. Whether that’s introducing new equipment like the TL2 TMA to our fleet, or sponsoring the TMAA Young and Rising Stars traffic management award, our aim is to promote best practice traffic management, encourage industry professionalism, and maximise safety for all stakeholders.”
“That’s also why we choose Scorpion TMAs for our Impact Protection Vehicles. They’re well designed and built, they’re fully MASH tested and certified, and they’re well supported across Australia by A1 Roadlines.”
“Most importantly, they deliver proven life-saving protection for workers,” he said.
“That said, our customers have a lot of say in what we do in terms of equipment choices, and they also prefer the Scorpions. Scorpion TMAs have an excellent reputation for quality and reliability in the field, and when it comes to equipment, particularly hire equipment, that’s critical. Our customers need to know that when the equipment arrives on site, they’ll be able to deploy it quickly, without any issues.”
“Most importantly, when it comes to Impact Protection Vehicles, our customers need to be
Mounted on a Hino 300 Series 616 Hybrid 4x2 HYBRID cab chassis, Trafquip’s new Scorpion® METRO is not only the first MASH TL2-certified TMA to be deployed in Queensland, it is also one of the first Impact Protection Vehicles to be built around a Hybrid-powered vehicle.
The truck’s hybrid driveline, which is powered by Hino’s N04C four-cylinder engine and a 201V AC Synchronous electric motor, delivers a combined 150hp and 470Nm of torque from a very low 1000RPM. It is also the first Japanese-manufactured light-duty truck in Australia to meet Euro 6 exhaust emissions standards.
The unit also includes Hino SmartSafe, a comprehensive safety package found in all 300 Series 4x2 trucks. The SmartSafe package incorporates a range of safety features, including a Pre-Collision System (PCS) with autonomous braking, Pedestrian Detection, Lane Departure Warning System (LDWS), Vehicle Stability Control (VSC) and Reversing Camera with audio.
Supplied by Scorpion’s exclusive Australian distributor A1 Roadlines, the new Scorpion METRO TMA provides MASH TL2 Plus-rated protection from an impacting vehicle weighing up to 2,270kg, travelling at 80km/h and with an impact angle of 25° degrees.
Importantly, as with the larger TL3 unit, the Scorpion METRO TMA has been fully tested and certified to current MASH (Manual for Assessing Safety Hardware) Standards.
In fact, the Scorpion METRO is not only the first TL2 TMA to be fully tested and approved to the latest MASH Standards, it is also currently the only TL2 Truck Mounted Attenuator to be successfully TESTED, PASSED & ELIGIBLE to the current MASH Standards.
The Scorpion METRO TL2 TMA has also been assessed and Recommended for Use throughout Australia by ASBAP (Austroads Safety Barrier Assessment Panel).
The new Scorpion METRO TL2 delivers the ideal combination of compact size, convenient operation, and reduced operating costs. In addition to the obvious fuel cost savings and reduction in carbon footprint, the fact that it’s mounted on the Hino 300 Series Hybrid cab chassis means that it can be driven with a standard car licence, making it much more versatile out in the field.
BELOW: The Scorpion® II METRO TL2 TMA has been fully tested and certified to current MASH Standards, and been assessed and Recommended for Use throughout Australia by ASBAP (Austroads Safety Barrier Assessment Panel).
Scorpion METRO TL2 and Scorpion II TL3 TMAs both incorporate Scorpion’s unique modular design. This not only plays a critical role in absorbing energy during an impact, it also helps to significantly reduce the cost of repairsparticularly after moderate impacts and/or in the event of accidental damage - with only the damaged components requiring replacement.
With most non-modular units, even minor damage caused by a driver inadvertently reversing into an object or colliding with a stationary object while positioning the vehicle can have extremely costly consequences. In fact, with some units, even minor impacts can result in having to replace the majority of the TMA unit.
Needless to say, with very low speed and minor impacts accounting for around 80% of the total impacts into TMAs, the cost and inconvenience of having to replace an entire unit or the majority of a unit any time minor damage occurs can be considerable. Thanks to their unique modular design, both the Scorpion TL2 and TL3 TMA models are extremely quick and easy to repair. And with the greater majority of repairs coming in at only a fraction of the cost of a replacement unit, they both deliver outstanding ‘whole of life’ value.
While ‘Infinity Testing’ (where the host vehicle is anchored in place during the test, thereby ensuring maximum impact energy is absorbed by the TMA) is clearly the most demanding testing regimen for TMAs - and a critical factor in certifying both Scorpion TMA models with no upper weight limit for host vehicles - it’s important to note that both Scorpion models also performed extremely well in standard ‘RollAhead’ type MASH testing.
In addition to undergoing three ‘Infinity’ MASH tests, during a fourth MASH crash test (MASH 2016 Test 2-53), the Scorpion METRO TL2 TMA
was fitted to a stationary unrestrained host vehicle in second gear and with the park brake engaged. It was then impacted at an angle of 9.9 degrees by 2014 Dodge RAM 1500 with a curb mass of 2295kg travelling at 81.6km/h.
Impressively, even during this extreme impact, the host vehicle measured a roll-ahead distance of only 12.4 metres.
In the same ‘unrestrained’ crash test, the Scorpion II TL3 TMA was impacted at 103.8km/h an angle of 10.3 degrees by a vehicle weighing 2266kg. In that test, the host vehicle measured a roll-ahead distance of only 5.1 metres.
Protecting road work crews from errant vehicles is just as important on suburban streets as it is on major highways and arterial roads.
Ideal for use on suburban streets and roads with posted speed limits of up to 70 km/h, Scorpion II® METRO TMA delivers the ideal combination of life-saving MASH TL2-certified impact protection in a compact, easy-to-manoeuvre size.
ASSESSED, APPROVED & RECOMMENDED FOR ACCEPTANCE throughout Australia by ASBAP (Austroads Safety Barrier Assessment Panel), the Scorpion II® METRO TMA is not only THE FIRST TL2 TMA to be fully tested and approved to the latest MASH Standards, it is currently THE ONLY TL2 Truck Mounted Attenuator to be successfully TESTED, PASSED & ELIGIBLE to the current MASH Standards.
Winners to be selected and announced at the Year in Infrastructure and Going Digital Awards event in Vancouver
Bentley Systems Incorporated, the infrastructure engineering software company, recently announced its call for nominations for the 2024 Going Digital Awards in Infrastructure
The awards, which are judged by independent juries of industry experts, recognise infrastructure projects for going digital advancements in infrastructure. The deadline for nominations is April 29, 2024.
Users of Bentley software are invited to enter their projects in the Going Digital Awards in Infrastructure program, no matter which phase the project is in – preconstruction/conceptual, design, construction, or operations. The three finalists chosen for each awards category win a trip to Vancouver to attend The Year in Infrastructure and Going Digital Awards event as guests of Bentley Systems.
As part of the conference, the finalists will present their projects before the judges, industry thought leaders, and members of the media.
The 2024 Going Digital Awards in Infrastructure categories include:
• Bridges and Tunnels
• Construction
• Enterprise Engineering
• Facilities, Campuses, and Cities
• Process and Power Generation
• Rail and Transit
• Roads and Highways
• Structural Engineering
• Subsurface Modelling and Analysis
• Surveying and Monitoring
• Transmission and Distribution
• Water and Wastewater
These projects recognise innovative advancements and measurable impacts in infrastructure delivery and performance using Bentley software, including Bentley Infrastructure Cloud and Bentley’s iTwin Platform for infrastructure digital twins. Projects may also be recognised for advancements
that empower sustainable development goals in terms of climate action, energy transition and efficiency, circularity of land and water resources, and healthy communities.
In addition to the juried awards, Bentley’s founders will honour select projects representing organisations or individuals whose undertakings contribute notably to infrastructure advancement and/or environmental and social development goals.
Every project nominated for an award receives recognition across the global infrastructure community. Through the 2024 Going Digital Awards in Infrastructure program, participants:
• Get their infrastructure projects profiled in Bentley’s Infrastructure Yearbook, which is distributed in print and digital formats to media, government, and industry influencers around the world.
• Enhance their competitive edge by demonstrating to existing and potential clients the value that the participants add to projects through their digital innovations.
• Receive coverage from global media and support from the Bentley team in marketing and promoting their respective projects to the media.
For additional information about the 2024 Going Digital Awards in Infrastructure program, or to nominate a project, please visit: https://www.bentley.com/yii/welcome
22 August 2024 Brisbane Speaker
With its innovative design and patented ‘post/fuse’ system, DOLRE ‘Regular’ barrier delivers MASH TL4-rated protection while limiting the maximum transverse force transmitted to the bridge deck to less than 44 kN/post (22 kN/metre), which equates to only 14% of the ultimate outward transverse design load as per AS5100.2-2017.
What’s more, at around 120 kg/m installed, DOLRE bridge tra c barriers are significantly lighter than many AS5100 ‘Regular’ / MASH TL4-rated barrier alternatives.
DOLRE transitions have been designed and tested to provide full longitudinal load transfer between the bridge tra c barrier and connecting roadside barriers.
The DOLRE ‘Regular’ barrier, together with the DOLRE transitions and Thrie-Beam barriers create an engineered continuum of MASH TL4 protection – delivering maximum safety for road users onto and across the bridge structure.
DOLRE’s clean, uncluttered lines and aesthetically pleasing design make it an ideal match for a wide variety of bridge designs and locations. The design allows for rapid installation, as well as rapid repair and reinstatement of the barrier following an impact. DOLRE is also easy to dismantle and remove in times of flood, thereby helping to significantly reduce the risk of damage to valuable bridge assets caused by flood-borne debris.
DOLRE is also available with an extensive range of standard or custom fascia designs and integrated lighting options.
Available in a range of AS5100-2017 performance levels, including DOLRE Low (MASH TL2 | EN1317 N2), DOLRE Regular (MASH TL4 | EN1317 H2) and DOLRE Medium (MASH TL5+ | EN1317 H4b), there is a DOLRE barrier to suit virtually any bridge, culvert or road embankment application.
All DOLRE systems feature three rails - two rails for the initial vehicle impact and one rail to resist rollover – and one post design per system type, suitable for both sides of the bridge.
Ideal for bridge refurbishment and safety upgrade projects, DOLRE’s ground-breaking ‘low stress’ design restricts the outward transverse force transmitted to the bridge deck during a vehicular impact to a fraction of the bridge deck's capacity, thereby minimising the risk of damage to the bridge deck and structure during a vehicular impact.
DOLRE bridge tra c barriers can play a significant role in extending the serviceable life of many existing bridges - delivering AS5100 and AS3845 compliant protection without the need for expensive deck strengthening works or additional reinforcement.
DISCOVER MORE
In the current construction market, we are seeing an overdue focus on ensuring that compliant products are procured and installed in our building stock.
This comes at a time when global markets are providing a wide range of options for supply. As a consequence, methods for demonstrating compliance and giving the end user confidence in the manufacturing process of products are being requested by more builders as they look to mitigate risk.
The reinforcing and structural steel markets are not immune to these pressures. With products being supplied from multiple sources, there are often questions regarding compliance with material Standards, the origins of products and/ or traceability through the supply chain.
As the steel supply chain comes under increasing pressure to demonstrate compliance, important questions are raised, including:
• what are the risks of receiving non-compliant material?
• how can we reduce these risks? and
• how do we help to ensure that end-users are getting products that are fit for purpose and meet the relevant Australian and New Zealand Standards?
All products used in building and construction need to comply with the relevant quality and safety standards. For buildings, they fall under the Australian National Construction Code (NCC) or the New Zealand Building Code (depending on jurisdiction), while for infrastructure projects, nominated Standards for compliance are specified. Legislation already exists in a number of states, but increasingly, it is being mandated that all parties along the supply chain of building products need to ensure compliance. In addition, we are also now seeing increasing requests along the materials supply chain for independent compliance monitoring and certification by a trusted third party.
For reinforcing and structural steels, ACRS has a 20-year history of ensuring that both the manufacturers of steels, together with the downstream processors of reinforcing steels, are meeting the requirements of the relevant Australian/New Zealand Standards. This includes mechanical and geometric testing, along with product traceability from source to site.
The ACRS certification process involves an annual on-site assessment of all certificate holders, conducted by experts in steel making. These assessments are further enhanced through witness and independent testing, along with ongoing surveillance of material quality as outlined in the Standards. The ACRS Product certification scheme is independent of manufacturers and holds JAS-ANZ accreditation.
Australian and New Zealand Standards stipulate that all materials, including those being processed downstream, need to be traceable back to the source. They recognise that changes are made to the material and geometric properties of steel during the manufacturing processes.
As a consequence, the Standards require additional testing to be carried out after downstream processes have been completed. For reinforcing steel, downstream processors include mesh manufacturers and facilities that cut and bend reinforcement to the scheduled lengths and shapes.
For mesh materials there are requirements for geometry, material properties and weld capacities of the joints. For reinforcing bar, the process of straightening and bending may change the mechanical and geometric properties of the product.
Unfortunately, in some cases, a product that was a compliant material from the steel manufacturer is delivered to the end user in a non-compliant state as a result of the downstream processing.
The ACRS scheme monitors all the requirements of the Standards, including testing requirements and traceability, thus providing users of ACRS-certified steels with assurance that the received product is compliant, mitigating risk to the builder.
To ensure that the ACRS-certified product is installed, it is essential that ACRS-certified product is specified up-front, and throughout the procurement process. Importantly, all steel should be checked for compliance when it arrives on site.
In accordance with the relevant Standards, all ACRS-certified products have markings and tags for traceability. Under the ACRS scheme, all tags need to meet the requirements of the relevant Standards and must also include the ACRS Logo and/or certificate number.
The scope and validity of suppliers’ certificates should also be verified in this process.
ACRS certificates all now carry a QR code to circumvent fraudulent certificates. The QR codes may be scanned using the free ACRS Cloud app which is available for download from https://steelcertification.com/cloud
If the QR Code is valid, the app will display the scope of accreditation and other details regarding the certificate in question.
By ensuring that ACRS-certified steel is specified and supplied, the builder/ installer is ensuring the steel products meet the requirements of the relevant Australian and New Zealand Standards, thus minimising the risk of:
1. having to replace product with unknown origins
2. delivering a structure that is not fit for purpose
3. serious reputational damage.
Specifying and ensuring ACRS-certified products are supplied is as simple as looking for suppliers and processors with the ACRS brand. It is important to remember that any break in the traceability chain may call into question your product's compliance.
Recognising the industry's move to digital systems and to ensure confidence in the ACRS scheme is maintained, ACRS has launched ACRS Cloud - a digital verifiable conformance scheme. By combining certification and digital product traceability, ACRS will be a trust anchor, providing confidence and traceability to the market.
ACRS Cloud is the first digital certification system of its kind for steel in the Australian and New Zealand construction industries. ACRS Cloud gives steel buyers and users instant assurance over product certificates at the touch of a buttonin a secure environment - to provide confidence in products’ conformance to AS/NZS Standards. Users throughout the supply chain can gain product peace of mind by checking the nature and authenticity of ACRS steel certificates in the new ACRS Cloud app, which is available free on Apple and Android.
The ACRS Cloud system will see batchspecific tags with QR codes put onto steel at steel producers, fabricators, and processors. At each point, these QR codes (and/or those on ACRS certificates) can be scanned on-site to instantly identify the source of a product and its certification details against a ‘single source of truth’, including batch number; bar and tag markings; and verification of product conformance to provide full traceability through the supply chain.
Just like via the ACRS online database, you will be able to search for certificate holders by mill name or country and report any concerns, all in the app.
For certainty over the steel you use, make sure you are specifying ACRS-certified steel, and checking conformance easily in the new ACRS Cloud app. Find out more at: https://steelcertification.com/cloud
The ACRS Cloud app further protects the market from product compliance issues: not just in poor product identification or deliberate misrepresentation, but by making it easier for users to check steel’s provenance at every stage. It also supports best practices for those seeking sustainable steel.
How well do you know your
Are you getting the steel you specified?
Does ALL of the steel you’re receiving comply with the right Standards?
With ACRS Certified steels, you can be confident that you are getting the AS/NZS compliant steel you ordered.
By providing an effective, independent, continuous review of both the manufacturer and the fabricator/processor, the ACRS 2-stage product certification scheme, together with the ACRS traceability certification scheme, significantly reduce the risk of non-conforming steels being delivered to your project.
Talk to us TODAY about how ACRS Certification gives you confidence in your steel supply.
ACRS - Independent, Expert Third Party Certification and Verification of Reinforcing, Prestressing and Structural Steels for Compliance with Australian and New Zealand Standards
Australia’s leading designer and manufacturer of high pressure water blaster equipment is launching their FREE Safety Training Course, “Aussie Blaster Safe Operator”.
Australian Pump Industries has long been concerned with safety for operators of high pressure cleaners. The Aussie Pump range of pressure cleaners, sold not only in Australia now but globally, has set new standards in the safe design of high pressure cleaning devices up to 500 bar (7,300 psi).
As the product range expanded and received domestic and export attention, the company realised that safety in the use of the equipment is an essential part of the package.
When Australian Safety Standards were introduced to protect operators in the workplace
from potential serious injuries, training courses for Class B equipment operators became compulsory.
“Although Class B operators are mandated to undertake formal training and certification, we know there are hundreds, if not thousands, of operators using Class A machines without training of any kind,” said Aussie’s Chief Engineer, John Hales.
Aussie Pumps produced their own training program for Class A operators, “Aussie Blaster Safe Operator ”. The course promotes safety awareness, explains high pressure water technology, covers simple machine maintenance, and aims to prevent misuse of the equipment and operator injuries. The course is aimed at operators of high pressure water blasters of all types and brands.
“It’s our contribution to the industry,” said Hales. “We provide this free training program to all Class A users, regardless of the brand they are operating.”
“We are always open to listening to feedback from end users, and through this, we realised there were some extraordinary risks being taken by untrained operators,” said Hales.
“Our aim is to prevent injuries by training operators to identify hazards and in understanding how the equipment works.”
It takes less than half an hour, and when completed, participants will obtain an Aussie Pumps Certificate of Completion.
Further information on Aussie’s complete range of high pressure cleaners in both hot and cold versions is available from Australian Pump Industries. Call (02) 8865 3500 or visit the website: https://aussiepumps.com.au
THE QR CODE OR VISIT AUSSIEPUMPS.COM.AU TO VIEW THE “AUSSIE SAFE OPERATOR” COURSE ONLINE
Aussie invites all users of pressure cleaners, irrespective of brand, to complete the course online at https://aussiepumps.com.au
You could risk potential liability claims in the event of an accident or failure.
Ensure the ductile iron and steel covers & grates you purchase are compliant with AS3996-2019.
Request proof of compliance from a reputable and authorised authority.
Civilcast ductile iron, steel covers and grate range is Global-Mark Certified compliant for your peace of mind.
Be Compliance Sure. Be Civilcast Sure.
Over two days in Brisbane at this year’s Roads, Tolling and Technology Conference, ITS experts discussed the data and technology that can deliver massive safety and efficiency benefits for our road networks, but warned that educating and convincing road users is critical for these benefits to be realised. The conference, which attracts ITS leaders from industry and government, has expanded in recent years to cover not just toll roads, but all aspects of road operations and the interconnected technologies that drive them.
This year's conference began with a look at significant road and technology projects from across Australia and New Zealand, with host state Queensland, through the Department of Transport and Main Roads, outlining the systems, technologies and innovation driving their network management of the massive 33,000 kilometres of State roads.
Attendees were also given an insight into the complexity of the transformational North East Link Project in Victoria, described as the missing link in Melbourne’s freeway network. As well as outlining the intricate land use planning decisions preceding the project and the complex tunnelling component of the build, Major Road Projects Victoria CEO Duncan Elliott described the key to success to date and into the future as having a ‘social licence’. This includes the intensive engagement with 34 sporting clubs along the North East Link route to relocate and rebuild new and enhanced facilities, as well as the imperative to keep communities informed by providing real-time and accurate information on disruptions and alternative travel solutions.
ITS Australia CEO Susan Harris reiterated the critical theme of focusing on the end user, which emerged as a major talking point both in
and out of sessions over the two days.
“Our expert presenters were consistent in their desire to put customers at the centre of what they do, arguing the best solutions will be achieved by ensuring user engagement at all stages of project development,” said Ms Harris.
“Nowhere was this more evident than in the critical discussions on the topic of data and privacy, where panellists stressed the need to clearly explain the benefits of data sharing to consumers.”
“As an industry, we must work collaboratively to sell to the community the safety benefits that come from data sharing, while reassuring them about the safeguards in place to ensure the highest privacy standards are maintained.”
During the plenary panel session ‘Data Sharing vs Community Privacy Expectations’, a lineup of industry and government leaders looked to Europe as a template for the urgent work that needs to be undertaken in Australia to implement clear frameworks for data governance. Panellists agreed that collaborative governance was the critical next step to support the broad ITS ecosystem in managing data appropriately but stressed while government must set the scene for the work to be done, it was not the job of
government policymakers alone to design the framework.
“Industry operates on the signals it gets from government, this is a critical starting point for government and industry to get together and develop a plan for implementation that also includes appropriate data governance. Ultimately, in the case of government it needs to just do it!” said Adviser and Consultant Chris Koniditsiotis, who was on the panel.
A key feature of day two of the conference program was a panel discussion in which toll road operators, tolling tech providers, and government leaders delved into the key future technology challenges and opportunities in operating and managing motorway tolling systems.
According to the panel, Australia’s ITS industry has been a world leader in building cross-border partnerships across all sectors to deliver harmonised tolling solutions, but that collaboration must now continue into the C-ITS generation of tolling.
The panel also considered global technology innovations, with representatives from tolling technology leaders Kapsch and Q-Free sharing insights into solutions operating in other countries and how we could use that technology to significantly enhance Australia’s tolling ecosystem.
The conference also featured a wealth of fascinating contributions from industry leaders including Carla Hoorweg, CEO, ANCAP Safety; Matthew Bereni, CEO, Traffic Management Association of Australia; Rita Excell, Head of Transport – ANZ, Amazon Web Services; Pablo Ruiz, Head of Operations – Australia, SICE; Dr Geoff Allan Chief Executive Officer, Austroads and Associate Professor Doug Wilson, Director of Transportation Research Centre, University of Auckland.
In addition to the comprehensive two-day program, a small group of industry leaders convened for an ITS Australia hosted Thought Leadership Dinner on the Tuesday evening before the conference. The guest list, which comprised senior leaders from ITS Australia Platinum and Gold Member organisations was privileged to hear a keynote address from ANCAP CEO Carla Hoorweg, who provided an overview of ANCAP’s program of work and their aspirations to partner with the ITS industry into the future.
The ITS sector will continue many of the important conversations canvassed at Roads, Tolling and Technology at the annual ITS Australia Summit, taking place in Sydney from 13 to 15 August 2024. Under the theme, ‘Safe, Sustainable and Inclusive Transport for Vibrant Communities’, more than 1,000 attendees from Australia and abroad are expected in Sydney to tackle the critical issues and help shape Australia’s transport future.
Yunex Traffic, a global leader in intelligent traffic management solutions, has been selected by McConnell Dowell to install the traffic management and control systems for the New Bridgewater Bridge in Tasmania, Australia. The new bridge will connect local communities, create more open space and transform the way people travel between the north and south of the State.
The construction of the New Bridgewater Bridge started in October 2022 and will be completed in 2025.
Yunex Traffic Australia will provide the traffic management and control systems for the New Bridgewater Bridge, including design, procurement, supply, manufacture, testing, installation and commissioning. The systems and solutions provided by Yunex Traffic will enable comprehensive traffic management to improve safety for all commuters. For example: Potential critical conditions can be identified based on real-time data insights, supported with additional CCTV instalments.
Spanning the River Derwent, the future 1.2 km-long bridge is designed to improve connectivity with its four lanes of traffic accommodating 22,000 daily motorists. Complementing its functional design, two major interchanges contribute to the bridge's overall connectivity and efficiency.
Prioritizing safety, the bridge incorporates an 80 kmph speed limit, safety screens and barriers to ensure safe travel for all. Going beyond mere functionality, it
prioritizes inclusivity with a shared path for cyclists and pedestrians, creating a safe and accessible environment for multiple modes of mobility.
“We are proud to be a key contributor to Tasmania's landmark project, the New Bridgewater Bridge,” says Fred Kalt, Managing Director Yunex Traffic Australia.
“Our selection by McConnell Dowell underscores our commitment to delivering cutting-edge traffic management and control solutions.”
“As we embark on this journey, we recognize the immense impact this bridge will have on Tasmania's transportation landscape. By integrating our intelligent solutions, we aim to not only improve connectivity and traffic efficiency, but also prioritize safety for all commuters,” he said.
“We are excited to be part of this transformative infrastructure initiative that will ultimately shape the future of transportation in Tasmania,” he added.
Recently, Yunex Traffic Australia was also contracted to build and install the Operations Management and Control System (OMCS) for the Western Harbour Tunnel project in Sydney, Australia.
“We are excited to expand our presence in Australia to revolutionize mobility through intelligent, connected traffic management solutions. Our vision is to create a safer, greener and more efficient travel experience for all commuters, leaving a sustainable impact,” Mr Kalt concluded.
So too, the Engineer can use the vast capacity of Finite Element analysis to validate, optimize and adapt data to create the finest design solutions.
by Paul Uno, Director, ETIA
When I graduated from the University of Sydney in the mid-1970s, engineers used AS1250-1972 and AS1250-1975 for their structural steel design, AS1480-1974 for their reinforced concrete design, and AS14811978 for their Prestressed Concrete Design. These days we use AS36002021 for both reinforced and prestressed concrete design, AS4100-2021 for structural steel design and AS3990-2016 for mechanical engineering steelwork.
So, what has changed in these Standards (or Codes, as we called them in those days) over the past 50 years, and what were the reasons for these changes?
When I worked for Transfield as a structural engineer designing steel structures (e.g. transmission towers, foundations and water retaining structures) we used the AS1250-1974/1981 Structural Steel Code. The common steel grade used in those days for nearly all structural elements including UB, UC, and angles, was 250 grade yield stress (though less common higher grades were available).
The commercial (or black) bolts were mainly grade 4.6 (i.e. 400 MPa ultimate tensile capacity and 240 MPa yield capacity). You could get 8.8 grade bolts (i.e. 800 MPa ultimate tensile capacity and 640 MPa yield capacity) but these bolts were much more expensive than commercial bolts so most engineers and builders used 4.6 bolts.
The structural design principles set out in AS1250 were based on Working Stress (Serviceability), i.e. “everyday loads”, not factored loads.
This Code, therefore, was not only used by structural and civil engineers but also mechanical engineers (who focus primarily on serviceability in their designs), whereas structural engineers focus on both strength and serviceability.
Around the mid-1970s-80s, engineering academics and Standards committee members decided to follow overseas trends and move towards Ultimate Strength Design principles (USD). The other terms used were Limit State (LS) or Load and Resistance Factored Design (LRFD).
In America, one of the leading figures pushing LRFD was Theodore Galambos (Prof of Civil Engineering at Washington University) and many of his papers on the topic featured in the American Institute of Steel Concrete (AISC) journals and magazines.
I worked at the Australian Institute of Steel Concrete (AISC) - now called ASI (Australian Steel Institute) - in the late-1980s and was on the Standards Committee BD1 looking at changing AS1250 from working stress to a limit state format. Many of the committee members wanted to keep 1250 as the number in the title of the Standard. I pointed out that in days to come, no one would know whether the AS1250 Code used on a project was the Working Stress version or the Limit State version, so a new number should be chosen. I was over-ruled in my proposal, however, when I returned to the AISC office and spoke to my boss (Arthur Firkins) and explained the situation, he agreed with me and made it his focus to get the number changed. Suffice to say, he was successful and it then became AS4100.
However, the dilemma for mechanical engineers is that they only design in “working stress” due to the nature of mechanical structures (e.g. fatigue, vibration which are all working load related). With that in mind, they produced their own Australian Standard to replace AS1250 and it became AS3990-1993 ‘Mechanical Steelwork’ which covered boilers, pressure vessels, lifts, cranes, mining equipment, gas and liquid petroleum piping systems and bulk handling equipment.
The current Steel Standard, AS4100-2021, utilises Limit State Design principles, 300 MPa yield stress steel (up from 250 MPa) as the common grade, and 8.8 Grade bolts as the common bolt connection type (costs now being very competitive to the original 4.6 bolts). Higher grades of steel are also available (350, 400 etc).
In other metals-related Standards, even the Aluminium Code AS1664-1979 changed from its working stress format to a limit state format in 1997 (AS1664-1997).
The Reinforced Concrete Code AS1480-1974/1982 and Prestressed Concrete Code AS1481-1978 were merged into one Standard called AS3600 in 1988. This merger of the two Codes occurred due to pressure from the prestressed industry who thought few engineers embraced PSC/PT because it appeared too different to reinforced concrete.
However, it must be stated that the AS1480 and AS1481 Standards were already in Ultimate Strength format, and so preceded the Steel Code in changing to the new format by about 10 years.
The other Australian Standard relating to reinforced concrete that has changed substantially from its inception in 1986 to the present day was AS2870 Residential Slabs and Footings Standard. Its current version is AS2870-2011, however, during the period from 1986 to the current version, there were four major revisions: 1988, 1990, 1996 then finally 2011. This Standard is different to AS3600 in many ways, in that it focuses primarily on Serviceability (i.e. crack control) with structural strength being the secondary issue to check.
ETIA will be conducting a face-to-face 2-day workshop on Structural Steel Design to AS4100 in Brisbane, QLD from 29-30 April 2024. Similarly, ETIA will then be conducting a 2-day face-to-face workshop on Residential Slabs and Footings (Design and Construction to AS2870) in Brisbane, QLD from 2-3 May 2024.
Both workshops will be held at the Voco Hotel, 85-87 North Quay (Cnr. Ann Street), Brisbane, QLD. For registrations and information on these or any other ETIA workshops, please visit the ETIA website: www.etia.net.au
Tired of traffic jams? Asia-Pacific’s rivers and waterways can soon turn into green highways with the first hydrofoiling electric ferry, the Candela P-12.
Rapid economic growth has seen a tremendous rise in road transport of goods and people across most of the APAC region. The downsides are congested roads, pollution, and frustrated commuters, who in many cities are regularly stuck for hours in traffic jams.
Ferries are expensive to run and often speedrestricted in urban waters due to the large, damaging wakes that they create.
Another concern in recent years is that their diesel engines spew out harmful emissions, contributing disproportionately to pollution and bad air quality.
The Swedish tech company Candela aims to change this with the world's fastest electric ship, Candela P-12, whose revolutionary technology will soon be demonstrated at the Singapore Yacht Festival, in conjunction with the opening of Candela’s new APAC office.
“Across Asia and the Pacific, from archipelagos to cities, we see a huge market and demand for new sustainable transport solutions that can reduce congestion and emissions,” says Björn Antonsson, Candela’s newly appointed Regional CEO for Asia-Pacific.
“Our technology offers quicker journeys, lower costs for operators, and zero emissions.”
Thanks to computer-controlled wings beneath the hull, the Candela P-12 Shuttle flies above the water surface at high speeds, which considerably reduces friction. It differs from all other fast ships – electric or diesel - by using a staggering 80% less energy than traditional ferries. Thanks to this, it’s the first fast electric ferry with long range – up to 100 km on one
charge, at a speed of 25 knots.
When flying, it generates no waves or noise, and its outstanding energy efficiency drastically reduces operational costs compared to traditional ferries. Designed for multi-modal transport, the P-12 fits 30 seated passengers along with storage for bikes and luggage.
The first unit was launched last fall in Stockholm, and a pioneering P-12 line will be operational in the city’s local transport system later in 2024. In Asia-Pacific, a P-12 line will be inaugurated in New Zealand in 2025, where Meridian will operate the ferry on the country’s pristine Lake Manapouri.
A unique feature of the P-12 is that it generates minimal wakes even at high speeds, which is the reason it has been exempted from speed restrictions on its maiden route in Stockholm. This reduces commuting times in Stockholm from 55 minutes by car to 25 minutes on the P-12.
“Shifting commuters from private vehicles and winning them back to the public transport system is a big challenge. It’s only possible by offering them better comfort, quicker commuter times, and more convenience,” says Björn Antonsson, who thinks that the Stockholm example can be replicated in cities across APAC.
“From electric cars to maglevs, many countries in the region have a history of leapfrogging conventional technology.”
“The waterways are humankind’s oldest transport infrastructure; the cities are built around water, and with our technology, we can unlock its full potential for sustainable transport,” Mr Antonsson added.
In Asia-Pacific, Candela will also market and sell their revolutionary leisure boat, the
Candela C-8, which utilizes the same hydrofoil technology and software as the P-12. The C-8 is the best-selling electric boat in Europe, offering a combination of long-range, high speed, and a superior, quiet experience on the water.
Catering to a growing crowd of customers for premium recreational boats, utilizing cuttingedge technology.
“We’re seeing very strong recreational boat markets in places like Australia, New Zealand and the rest of the region is developing fast,” says Björn Antonsson.
As the world’s first electric hydrofoil ferry – and the fastest electric ship, with the longest range – the Candela P-12 features:
• 30-passenger capacity
• Top speed of 30 knots and service speed of 25 knots
• Up to 100 km range at high speed
• Uses 80% less energy at high speed than conventional vessels
• No wake
• Up to 60 % lower OPEX than diesel vessels
• Designed for open & inland water use
• DC charging in one hour
• Over-The-Air updates of software & remote servicing
In addition, the fact that the vessel uses an active Flight control system that automatically adjusts the hydrofoils to counteract waves, the Candela P-12 offers the added benefits of a significant reduction in sea sickness, with superior comfort for crew and passengers, The Hydrofoils can be retracted into the hull to dock at low tide or shallow water, and the vessel is easily trailerable by truck for fast and easy transport and shipping.
Located some 265km south of Perth, the rural town of Kojonup has plugged into the WA EV Network, becoming the 31st location to join the network.
The electric vehicle fast charger on Benn Parade near the Kojonup
Swimming Pool features a 150-kilowatt fast charger and a 22 kW backup charger.
Its opening means the network’s South West loop – which includes fast chargers now live in Bunbury, Margaret River, Manjimup, Walpole, Albany and Jerramungup – is now complete.
Another fast charger site is expected to open in Brookton in June.
Speaking about the latest EV charging installation, Western Australian Energy and Climate Action Minister, Reece Whitby said it was great to see range anxiety become a thing of the past in the State’s South West.
“By encouraging sustainable transport through the WA EV Network, the Cook Government has put our State on the road to achieving net zero emissions by 2050.”
The comments we echoed by WA Agricultural Region MLC Shelley Payne, who said: “I’m proud the Cook Government is investing in one of the longest electric vehicle charging networks in the world.”
“The WA EV Network is providing the backbone of EV charging infrastructure which is critical for driving confidence in people living in the regions to invest in EVs,” she said.
“This charging station is perfectly situated between Perth and Albany, making it easier for EV drivers to explore our amazing south coast.”
“I hope visitors using the chargers will pop over the road to Kojonup’s Kodja Place museum and discover the rich history of Kojonup,” Ms Payne added.
There have been more than 15,000 charging sessions along the WA EV Network since the first site opened in Geraldton a year ago, with the network due to be completed later this year. It will be the longest EV network in Australia, spanning more than 7,000 kilometres from Kununurra in the north, to Esperance in the south and Eucla to the east.
For more details, visit: https://synergy.net.au/evnetwork
Did you know you can access the latest issue of Highway Engineering Australia via Informit?
The Informit Engineering Collection is an ever expanding resource covering aspects of highway engineering - planning and development, design, construction, maintenance and management. The database offers an extensive variety of resources including journals, trade publications, reports and conference proceedings.
The Collection guarantees quality through partnerships with peak professional bodies including Engineers Australia and the Institution of Professional Engineers New Zealand, as well as Content Providers including EPC Media Group.
The Informit Engineering Collection delivers hard to find content designed to complete and complement your highway engineering requirements.
Other key titles published by EPC Media include:
Construction Engineering Australia Waste + Water Management Australia
Request a quote or free trial via www.informit.org/trial-and-quote
Research for your global future
Vianode, an advanced battery materials company providing sustainable anode graphite solutions, confirms world-leading climate impact potential in Life Cycle Assessment (LCA) of planned industrial scale production.
The LCA verifies a climate change impact of 1.9 kilo CO2 equivalents per kilo graphite produced in Vianode’s process. Feedstock material production and processing are considered the main emission contributors. This represents a potential CO2 emission reduction of more than 90% compared to conventional fossil-based production according to Benchmark Mineral Intelligence, the latest LCA results, and internal company analysis data.
“Vianode’s ambition is to change the way batteries and battery materials are produced. In addition to leading sustainability metrics, our solutions offer high-performance properties that enable faster charging, longer service life and better recyclability of electric vehicles (EVs). We will provide a unique combination of the highest material quality along with the world's lowest emissions for anode graphite solutions. Moreover, we are aiming to enable resilient local value chains by establishing industrial scale production in North America and Europe,” says Burkhard Straube, CEO of Vianode.
“Vianode’s synthetic anode graphite production offers a very low CO2 footprint and the potential to contribute to significant emission reductions within the battery and EV value chain without compromising on product quality,” says Lydia Bridges, senior sustainability consultant and graphite specialist at Minviro, a recognised environmental consultancy specialising in LCA’s for the industrial and battery materials industry.
Sustainable production of anode graphite solutions is key for the green transition of mobility. Graphite makes up around 70 kilos per battery pack in an EV and represents up to 40% of battery cell emissions based on the average present-day production.
“Production of high-quality sustainable anode graphite solutions will be a major step towards more sustainable batteries and EVs. Once in full industrial scale production, our contribution to CO2 footprint reductions will be equivalent to more than the emissions of the city of Copenhagen every year,” says Andreas Forfang, VP Sustainability and ESG in Vianode.
The LCA is a cradle-to-gate scope 1, 2 and 3 production study of the prospective production of battery-grade synthetic anode graphite at Vianode’s planned large-scale production site. This means that the impact is assessed from the point of resource extraction to the factory gate, where the product is packed and loaded onto trucks. Seven internationally accepted impact categories were interpreted in detail: climate change, water scarcity footprint, land use, acidification potential, particulate matter, fossil resource use and mineral and metal resource use. The study has been certified according to the ISO-14040 and ISO-14044 standards.
Vianode has produced anode graphite solutions at its industrial pilot in Kristiansand, Norway since 2021. Vianode’s Technology Center opened in the same city in 2022 and the next milestone is the opening of the first full-scale production plant at Herøya, Norway, in the second half of 2024. Vianode’s ambition is to produce high-performance anode graphite solutions for 3 million EVs annually by 2030 across Europe and North America.
The 2024 Kia EV9 has achieved a remarkable dual victory at the 2024 World Car Awards.
Revealed during a live announcement at the World Car Awards ceremony at the New York Auto Show, the EV9 secured prestigious titles for both World Car of the Year and World Electric Vehicle.
Selected by a jury of 100 distinguished automotive journalists representing 29 countries, the World Car Awards recognized the Kia EV9’s innovative design, spacious seven-seat interior, and competitive price point. Based on the E-GMP platform, the EV9 is the first Kia to feature fourthgeneration battery technology for improved performance.
Established in 2003, the World Car Awards are renowned globally as a premier standard for automotive excellence and leadership, celebrating remarkable accomplishments within a rapidly changing automotive industry.
Prior to the 2024 event, Kia had already claimed three wins at the World Car Awards – the Telluride as World Car of the Year and the Soul EV as World Urban Car in 2020, along with the Kia EV6 GT taking World Performance Car of the Year in 2023.
“We are hugely honoured that the 2024 EV9 has been named the World Car of the Year and World Electric Vehicle,” said Ho Sung Song, President and CEO at Kia.
“This triumph is a testament to our unwavering commitment to pushing the boundaries of technology and design excellence.”
“The Kia EV9’s continued success will drive us to keep delivering exceptional vehicles that redefine the driving experience for customers around the world,” Ho Sung Song said.
Two wins in the World Car Awards add to an impressive haul of accolades for the EV9, including the 2024 North American Utility Vehicle of the Year.
“EV9 is a clear representation of Kia’s vision, and further evidence of our dedication to quality,” said Seungkyu (Sean) Yoon, President and CEO of Kia North America and Kia America.
“This award cements Kia’s standing as the frontrunner in sustainable mobility solutions that go beyond conventional automobiles.”
“We share this honour with our global teams who contributed their utmost efforts to drive EV9’s success,” Mr Yoon added.
For more information, please visit www.kia.com
Softree Technical Systems, a civil engineering software developer, has deployed a new global release of its RoadEng® Version 11 Software. This new version includes AIbased technologies to quickly find low-cost, constructable road and corridor locations, ideally suited to greenfield road projects.
Research and development for Path Explorer has been ongoing for years, guided by collaboration and dialogue with clients.
“We continually engage with our customers to better understand their challenges, this helps us focus our R&D effort on features that matter to them, ultimately giving them better, faster and easier solutions,” said Matt Dickie, Applications Specialist & Training Manager Softree Technical Systems.
“We are committed to empowering our customers with tools that not only streamline road design processes but also drive substantial cost savings.”
For greenfield road projects, Path Explorer Ai enables users to explore multiple route options from Point A to Point B within minutes, offering optimised alignment solutions while considering various constraints such as grade limits, side slopes, and environmental factors. This innovation not only accelerates decisionmaking but also optimizes costs.
This is especially pertinent in wind farm development, where swift planning and analysis of proposed roads and road networks are frequently required.
"Path Explorer Ai enables users to explore multiple route options from Point A to Point B within minutes, offering optimised alignment solutions while considering various constraints such as grade limits, side slopes, and environmental factors."
The placement of roads is often influenced by project factors like turbine locations. The ability to account for those factors and quickly determine lower-cost, feasible road locations accelerates project initiation, reducing upfront capital expenses and expediting the overall project timeline.
“Path Explorer integrates into our established earthwork optimization workflow within RoadEng, where the potential for savings is substantial,” explains Erin Wasney, Business Development Manager at Softree.
“Minor adjustments to the vertical alignment, aimed at minimizing cuts and fills, yield rapid and significant results.”
“Just recently, one of our Australian clients shared an impressive success story from one of their windfarm projects—a staggering $1.9 million in savings. That's a remarkable 19% reduction in subgrade costs,” Erin Wansey added.
Version 11 introduces additional features aimed at reducing environmental impact and increasing user efficiency, including:
• Hydrology Toolkit
• Improvements in Lidar Processing and Corridor Design
• Automated Horizontal and Vertical Curve Generation
• Drafting and Output Improvements
For more information about Path Explorer and RoadEng Version 11, please visit: https://www.softree.com/version-11
Softree Technical Systems is a leading provider of innovative engineering software solutions, specializing in rural road design and optimization.
With over 30 years of expertise, Softree Technical Systems is dedicated to revolutionising the engineering landscape by delivering intuitive and efficient software tools tailored to the needs of modern infrastructure projects and our environment.
For more information, please visit: www.softree.com
Queensland asphalt company MR-Roads recently announced the launch of a new community program that will reduce the rate of carpark incidences and improve community road safety.
As part of the new Community Carpark Safety Program, the young Brisbane start-up will donate asphalt mix and crew hire to repair damaged school, hospital, charity and small business carparks across South East Queensland. The initiative will see as much as 4 tonnes of unused asphalt redeployed each week - the equivalent of roughly 75 potholes a month, valued at $16,000.
MR-Roads co-founder and co-CEO James Rolph said the program was a no-brainer for a nimble asphalt company with close local ties to the community.
“We’re seeing so many more deteriorating carparks than ever before, due to the past few years of heavy rainfall, and we know this can be quite costly to fix particularly for schools and community clubs,” Mr Rolph said.
“Pothole and carpark repairs can cost in the thousands of dollars which means they often get de-prioritised and left for up to months at a time, which has huge consequences for the people who use them.”
The program invites local organisations within a 100km radius of North Lakes, Brisbane to apply for one-off, pro-bono repairs to their damaged carpark.
North Brisbane health club Fitness Cartel at Kippa Ring was the first to receive support under the program, with MR-Roads donating $3,600 of repairs to mend a 8m2 diameter pothole at the centre of their member carpark.
A Fitness Cartel Health Clubs spokesperson said members and staff had been avoiding the main section of their carpark for months, hindering access to the gym entrance.
“We were so thrilled to have MR-Roads reach out and offer to fix our carpark. Without them we’d probably still have people driving around to avoid hitting it. Now, the entire area is just a smooth, seamless experience and is a lot safer for everyone,” they said.
“As a small business, getting the money to fix potholes doesn’t typically rank high on our priority list, so having access to this kind of support is just phenomenal.”
MR-Roads co-founder and co-CEO Daniel Mikus said increasing rainfall and severity of weather conditions in Queensland will continue to impact
roads and carparks, and more support was needed to reduce the pressure.
“Potholes and road failures don’t just cause issues for motorists and pedestrians, it impacts the community’s perception of a business. It also puts the business at risk of litigation if damage caused is significant enough,” Mr Mikus said.
“Cracks will form as part of the natural life cycle of a road, but when water gets into these cracks, it will start to deteriorate the sublayers of the asphalt, and basically it will soften the soil until it caves in.
“We’ve had a few years of heavy rain and so it’s natural we’re seeing an increase in potholes and road damage. What’s not helpful is that costs of construction have increased at the same time, and so it puts a lot of our small local businesses in a tough position - pay money they don’t have to fix the damage, or put the community at risk.
“Keeping our local areas safe for everyone should be a priority and so we’re really excited today to bring this program to life and give back.”
Applications for the Community Carpark Safety Program are now open and businesses can apply for support at: https://mr-roads.com.au/ community
PROJECT: CENTRAL STATION METRO
LOCATION: SYDNEY, NSW
MASTER PRECASTER: WAEGER CONSTRUCTIONS
STAINING: ECOTONE
In the constantly evolving fabric of urban landscapes, the significance of visually appealing infrastructure goes beyond mere visual attractiveness. Beyond the superficial charm of well-designed structures lies a profound connection between meaning, beauty and sustainability, weaving a narrative of communal pride and environmental stewardship.
Communities that take pride in their surroundings are more likely to engage in sustainable practices. Aesthetically pleasing infrastructure that embodies meaning, becomes a symbol of a community's commitment to preserving its heritage and nurturing its future.
Two ventilation and service buildings located at each end of the new platform 14 of Sydney's Central Station feature a stunning artwork that establishes a visual link between the historical and contemporary elements.
Designed by renowned Bundjalung artist Dr Bronwyn Bancroft, the artwork has been created by incorporating stained bricks into 216 precast panels. A modern interpretation of “Connection to Country”, titled 'Time Travellers’, the artwork features imagery resembling a serpent, symbolising one of the numerous creation stories passed down by First Nation's people for over 60,000 years.
The project is part of the $955 million transformation of the 117-year-old station, executed by Laing O'Rourke for Sydney Metro. It stands as one of the most extensive upgrades undertaken on Australia's busiest railway station in decades.
Waeger Constructions, a National Precast Master Precaster, manufactured the panels,
with the vibrant staining process handled by ECOTONE, a National Precast Industry Supplier member. The outcome has achieved a remarkably resilient and innovative finish… a visual effect that is reminiscent of glazed bricks in various colours.
Sarah Bachmann, CEO of National Precast, highlights that staining provides a contemporary yet durable alternative to painting, showcasing its versatility.
“The project at Central Station's new buildings exemplifies the application of staining, where inlaid bricks were stained. There are many other projects where the precast itself has been stained, which emphasises the broad use of this innovative technique in infrastructure development,” says Bachmann.
Ms Bachmann notes that staining, traditionally utilised for colour correction in brickwork and, more recently, in cast insitu concrete, has become a common practice in precast as well. It allows for stunning colour statements ranging from translucent and opaque to metallic finishes. The durability of staining makes it a valuable application, particularly when applied in the factory, maximising the advantages of off-site manufacturing for both infrastructure and building projects.
The use of staining on precast, much like in brickwork, serves the purpose of colour correction by penetrating the surface. When harnessed to its maximum capability, staining has the ability to produce vibrant, naturallooking colours that harmonise seamlessly with the concrete, delivering an authentic appearance surpassing that of paint.
retains its vibrancy for an extended period. As well, stains offer artistic flexibility, allowing for customised applications that create diverse effects, from translucent hues revealing the concrete's texture to more opaque tones for a solid colour.
Stained concrete offers increased resistance to fading from UV exposure due to weather conditions, making it a practical choice for both indoor and outdoor applications. Its low maintenance requirements and environmentally friendly formulations contribute to its appeal, making stained precast concrete a versatile and sustainable option for architectural and design projects.
“Staining precast provides a variety of benefits that enhance both aesthetic appeal and durability. In this instance, the final outcome delivers a wonderfully pleasing aesthetic that also tells a story. At the same time, it has incorporated the off-site manufacturing efficiencies and durability that are inherent in precast concrete construction,” Bachmann concludes.
Whatever your line marking or tra c management requirements, A1 Roadlines has the equipment and expertise to meet your needs.