REFINO DOS AÇOS
Fundamentos e aplicações
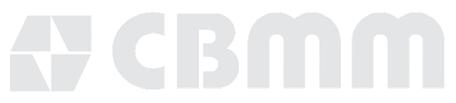
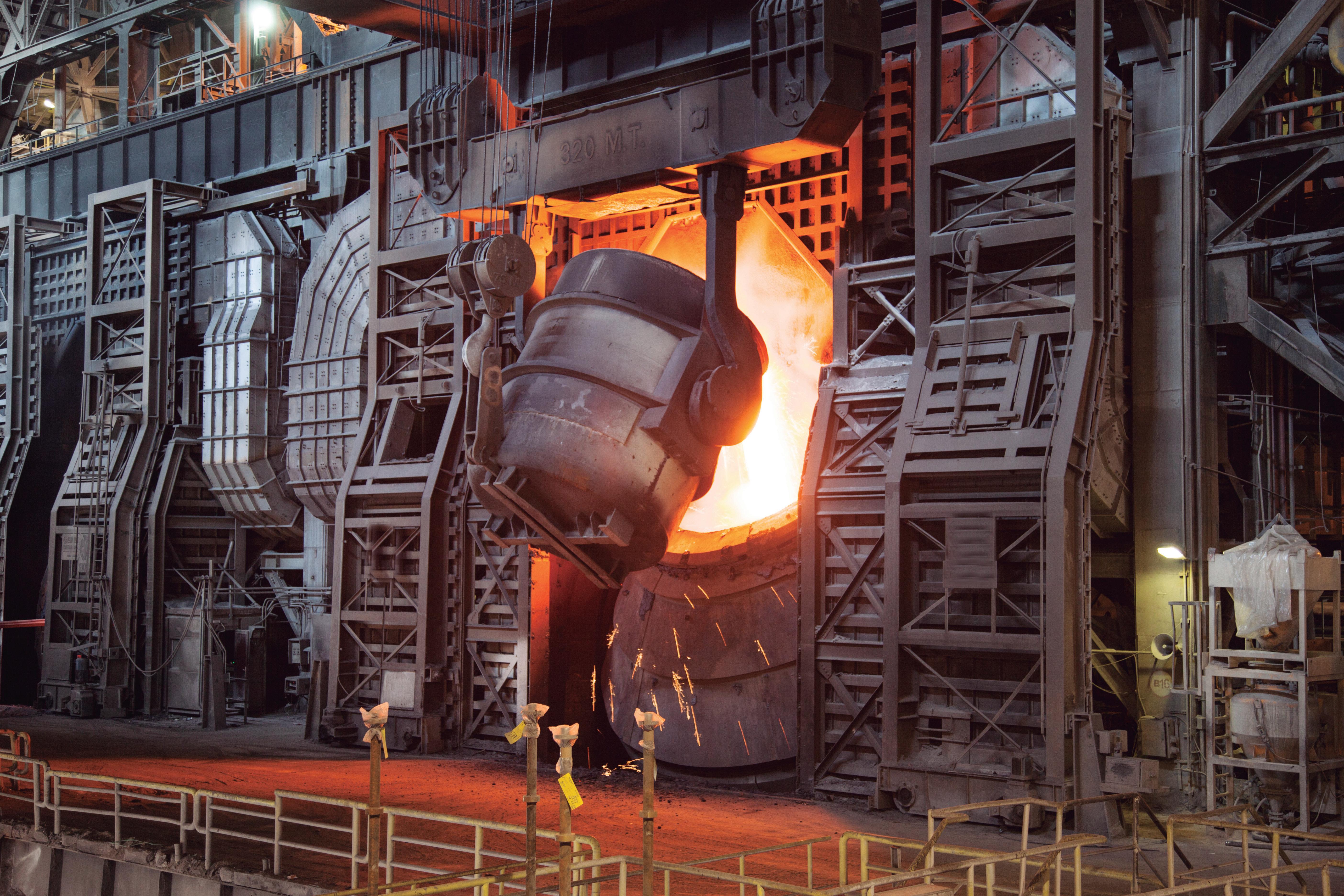
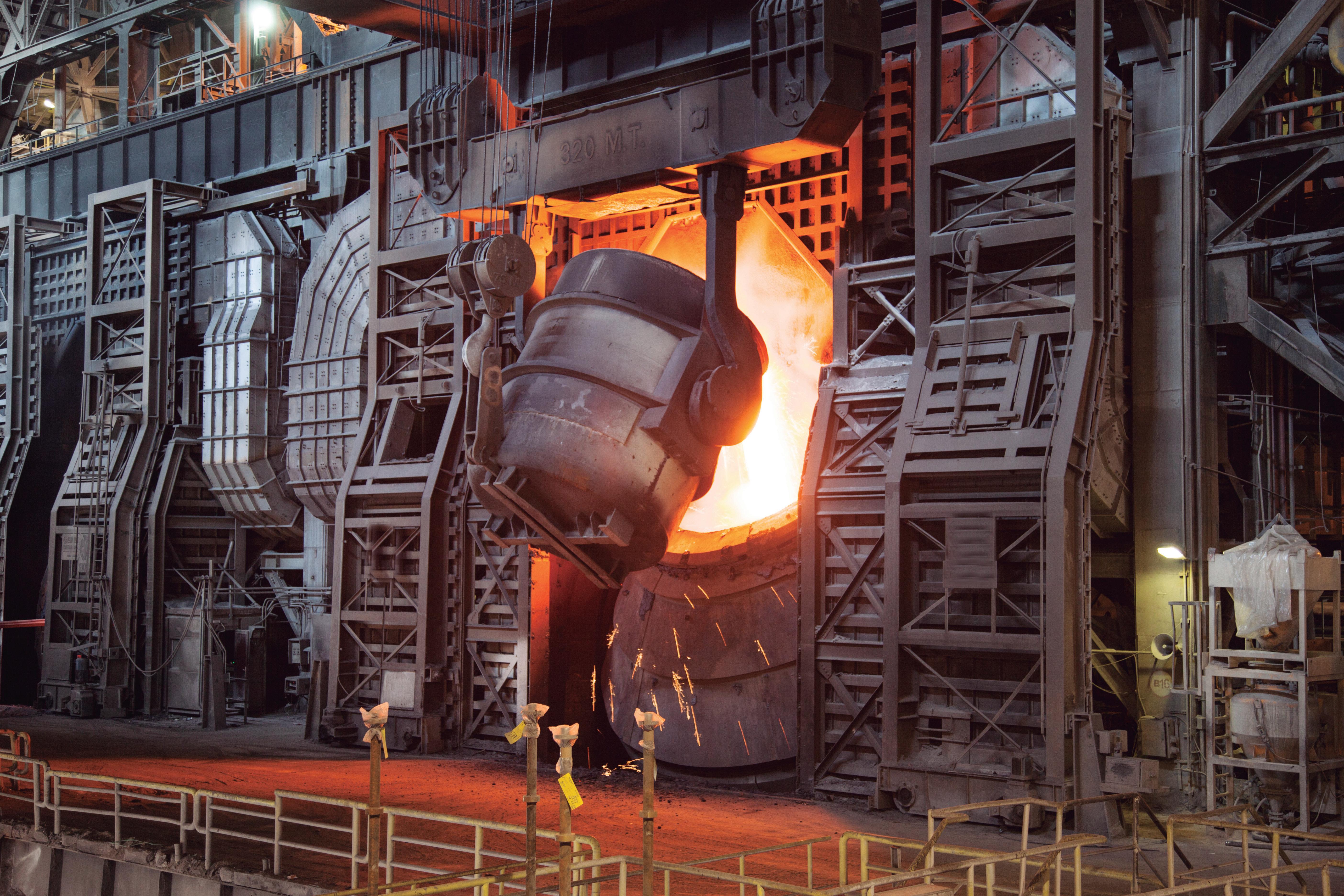
Refino dos Aços Fundamentos e Aplicações
© 2023 André Luiz V. da Costa e Silva
Editora Edgard Blücher Ltda.
Editor Edgard Blücher
Publisher Eduardo Blücher
Produção editorial Jonatas Eliakim
Preparação de texto Samira Panini
Diagramação Romério Damascena
Capa Laércio Flenic Imagem de capa iStock
Rua Pedroso Alvarenga, 1245, 4º andar
04531-934 – São Paulo – SP – Brasil
Tel.: 55 11 3078-5366
contato@blucher.com.br www.blucher.com.br
Segundo Novo Acordo Ortográfico, conforme 5. ed. do Vocabulário Ortográfico da Língua Portuguesa , Academia Brasileira de Letras, março de 2009.
É proibida a reprodução total ou parcial por quaisquer meios sem autorização escrita da editora.
Todos os direitos reservados pela Editora Edgard Blücher Ltda.
FiCHA CATALOGRÁFiCA
Costa e Silva, André Luiz V. Refino dos aços / André Luiz V. da Costa e Silva. - São Paulo : Blucher, 2023. 460 p. : il.
Bibliografia
ISBN 978-65-5506-106-2
1. Aço 2. Ligas (Metalurgia) I. Título
22-1241
CDD 669.142
Índice para catálogo sistemático:
1. Aço 2. Siderurgia 3. Aciaria 4. Termodinâmica
The invention all admired, and each how he To be the inventor missed; so easy it seemed, Once found, which yet unfound most would have thought Impossible!
John Milton (1608–1674). Complete Poems. The Harvard Classics 1909–14. Book VI
I had an immense advantage over many others dealing with the problem under consideration, inasmuch as I had no fixed ideas derived from long-established practice to control and bias my mind, and did not suffer from the too-general belief that whatever is, is right.
Sir Henry Bessemer (1813-1898). An autobiography With a concluding chapter. London, Offices of “Engineering,” 1905
O refino dos aços e seus objetivos
1 INTRODUÇÃO
Produtos de ferro são usados pela humanidade desde, pelo menos, 1200 a.C. Embora o ferro seja um dos cinco elementos mais abundantes na crosta terrestre, em peso, as ocorrências de ferro metálico na natureza são raras, normalmente associadas a meteoritos, já que a forma estável do ferro exposto ao ar são os óxidos de ferro. Assim, para obter produtos de ferro, a humanidade desenvolveu processos para extraí-lo dos minérios de ferro mais comuns, aqueles à base de óxido de ferro. O fato de que os combustíveis mais facilmente encontrados na natureza são ricos em carbono e o carbono, em condições adequadas, pode reduzir1 o óxido de ferro a ferro metálico foi decisivo no desenvolvimento de produtos e artefatos à base de ferro.
A presença de carbono durante as principais etapas do processamento usado para obter produtos de ferro também deve ter sido responsável pela observação de que adicionar carbono ao ferro produz importantes efeitos sobre suas propriedades, dando origem às principais ligas de ferro: aços e ferros fundidos.
Durante muitos séculos, a produção de ferro e suas ligas prosseguiu de forma artesanal, envolvendo diversos tipos de processos de redução, vários associados a trabalho mecânico, e algum controle das condições de aquecimento e resfriamento. No século XVIII, a percepção de que adições significativas de carbono reduziam sensivelmente o ponto de fusão das ligas de ferro e viabilizavam a produção em escala industrial, de metal rico em ferro, líquido, foi fundamental para o início da produção em grande escala de ligas ferrosas. Partindo de cerca de 40000 t2 anuais em 1856 [1] chegou-se à situação presente, no início do século XXI, em que cerca de 1800 Mt (em 2018-19 [2]) de aço são produzidas anualmente. (Para comparação, a capacidade de produção mundial de cimento é de 2800 Mt anual [3]).
1 Redução: converter do estado oxidado ao estado neutro (Fe+3 + 3 e– = Fe); o oposto de oxidação. Observar ao longo do texto, para não confundir reduzir, contrário de oxidar com reduzir, diminuir. Os dois sentidos são empregados.
2 Ao longo deste livro, as unidades e prefixos do sistema internacional são empregados, exceto quando indicado de outra forma.
É evidente que a produção dessa quantidade de aço por ano, a preços médios próximos a 0,5-2 USD/kg, envolve uma indústria que precisa ser extremamente eficiente e competitiva. Além disso, as demandas de desempenho e qualidade colocadas atualmente sobre os aços, fazem com que estes sejam materiais extremamente complexos, e que, rotineiramente, na sua produção, seja necessário garantir o controle preciso de pelo menos cinco elementos químicos presentes em sua composição. Em aços de sofisticação mediana, controla-se a presença de diversos elementos em partes por milhão3 e manipula-se a estrutura com uma precisão nunca antes experimentada [4, 5].
Esse cenário fez com que a engenharia do processamento do aço tenha evoluído de forma significativa nas últimas décadas. Em particular, as operações de refino dos aços, essenciais para que determinadas propriedades e características do produto possam ser atingidas com o processamento posterior, sofreu uma transição dramática do empirismo dos anos 1930-40 para um enfoque de elevada tecnologia e controle já no final do século XX. Neste livro, busca-se apresentar os principais aspectos tecnológicos e científicos que permitiram o desenvolvimento desse conjunto de operações que se passam em aciarias e são denominadas, de forma geral, de “refino do aço”. Alguns aspectos básicos dos processos de solidificação também são abordados, em vista da integração destes com os processos de refino em praticamente todas as aciarias do mundo.
É importante observar que o aço é um dos mais importantes materiais de engenharia há cerca de um século [6]. Por diversas ocasiões, nesse período, foram previstas mudanças radicais: a grande evolução dos polímeros nas décadas de 1960-70, por exemplo, levou à previsão de que a participação do aço, como material de construção no automóvel, por exemplo, seria dramaticamente reduzida. O aparecimento de diversos materiais opcionais para a embalagem de alimentos, também gerou a expectativa, não concretizada, de que as “latas” de aço para alimentos seriam eliminadas. Essas previsões frustradas se devem, em grande parte, à pujança da indústria do aço que, sistematicamente, desenvolve novos produtos com características cada vez mais adequadas aos empregos contemplados, por preços competitivos. Assim, o estudo dos processos de produção do aço, em particular dos processos de refino de aços, deve ser feito tendo em mente que todos os processos são desenvolvidos, aprimorados ou eliminados, em função do usuário do produto. Demandas objetivas sobre os produtos conduzem a alterações dos processos: tais alterações decorrem, fundamentalmente, da necessidade de produzir algum aço até então não produzido4 ou de
3 ppm, 1g/t ou 0,0001% em massa.
4 Ou atingir alguma característica ou propriedade de um aço até então não atingida.
produzir um aço já produzido, de forma mais econômica. Caso contrário, o estudo dos processos de produção do aço pode parecer ter um fim em si mesmo ao invés de ser movido pela necessidade de manter o aço como um material competitivo num cenário mutante de novos materiais e novas demandas.
2 O REFINO E AS CARACTERÍSTICAS DOS PRODUTOS DE AÇO
As características dos produtos de aço são definidas pela combinação de composição química e estrutura. A composição química dos produtos siderúrgicos é definida, praticamente, na aciaria, nos processos de refino5 Importantes aspectos da estrutura tais como segregação e limpeza interna (inclusões não-metálicas) são também definidos nesses processos. A aciaria tradicionalmente inclui a área de lingotamento, onde a solidificação ocorre. Nas etapas de conformação mecânica (como forjamento e laminação), as características estruturais produzidas na solidificação são modificadas, dando origem a outras importantes características dos produtos, tais como a anisotropia de propriedades mecânicas. Assim, os processos na aciaria e os tratamentos termomecânicos têm importância crítica para a definição das características dos produtos de aço.
Nesta introdução discute-se as variáveis críticas para a qualidade dos produtos finais de aço, destacando-se aquelas em que os processos de refino têm influência direta.
3 PRINCIPAIS FATORES QUE DEFINEM A QUALIDADE DOS PRODUTOS DE AÇO
A composição química e a estrutura combinadas definem as características dos produtos de aço. Estas duas famílias de fatores podem ser afetadas por diferentes processos industriais, como indicado na Tabela 1.1.
Para um produtor de aço, a “solução” da equação da Tabela 1.1 é realizada a partir da definição das propriedades desejadas. A solução é limitada, primeiramente, pelas características especificadas pelo cliente (que não podem, portanto, ser alteradas pelo produtor). Posteriormente, considerando as limitações técnicas de seus processos e as limitações de custo, o produtor define a combinação mais adequada de composição química e estrutura (em função das suas instalações de processamento) para atender as propriedades desejadas, respeitando os limites especificados pelo cliente e o custo adequado.
5 Tratamentos termoquímicos posteriores podem alterar a composição química na região muito próxima à superfície do produto.
Fundamentos de termodinâmica para o refino
1 INTRODUÇÃO
Quando observamos um sistema na natureza, com frequência nos perguntamos se este sistema, se não sofrer influências externas, permanecerá no mesmo estado ou sofrerá alterações com o passar do tempo. Em muitos casos, nossa experiência prática do dia a dia é suficiente para prever se mudanças ocorrerão ou não. Assim, por exemplo, se duas partes do sistema têm temperaturas diferentes, esperamos que, com o passar do tempo, o calor seja transportado da parte quente para a parte fria, até que a temperatura do sistema se equalize (Figura 2.1).
Da mesma forma, em um sistema mecânico sujeito a um campo potencial como o campo gravitacional (Figura 2.1), esperamos que o estado mais estável para o qual o sistema tenderá, será aquele de menor energia potencial.
Outro exemplo em que nosso senso comum (baseado na experiência prática) é suficiente é quando existem porções do sistema com diferentes pressões. Nesse caso, esperamos que a pressão se equalize, por exemplo, pelo fluxo de massa da região de pressão mais alta para a mais baixa.
À medida que os sistemas se tornam menos simples, o emprego do senso comum ou da intuição começa a ter sucesso limitado. Assim, enquanto sabemos que café e leite se misturam em qualquer proporção (e que o processo inverso não ocorre naturalmente), óleo e água nem sempre se misturam. Por fim, quando adicionamos alumínio ao ferro líquido contendo oxigênio dissolvido, nossa intuição pouco nos ajuda na previsão do que ocorrerá no sistema (ou do que não ocorrerá).
É claro que um comentário aplicável a todos esses exemplos é que se, por um lado somos capazes de dizer, com certeza, que determinado estado será mais estável do que outro (no sentido de que transformação pode ocorrer numa direção, mas não na direção inversa), não podemos garantir que a transformação efetivamente ocorrerá. Assim, mesmo que a posição 2 seja mais estável que a posição 1 na Figura 2.1(b), é possível que o corpo permaneça na posição 1 por um tempo indefinido se não for perturbado. Entretanto, temos certeza de que não há perturbação que torne a passagem de 2 para 1 “esperada”.
Um dos motivos pelo qual a previsão do que ocorre (ou não pode ocorrer) nos casos da Figura 2.1, é que nos três casos, temos diferenças de potencial bem caracterizadas (T, h e P, respectivamente) que indicam o sentido da transformação viável. Nas demais transformações mencionadas, não é tão claro que critério podemos aplicar para prever o que ocorrerá.
A termodinâmica é uma ciência cujo objetivo é prever o sentido das transformações viáveis e quantificar as variações que ocorrem nestas transformações.
Em sistemas que envolvem apenas energia sob a forma de calor ou trabalho mecânico, os potenciais pressão e temperatura são adequados para prever transformações.
Quando outras transformações são possíveis, principalmente aquelas que envolvem reações químicas e outros processos que têm efeito sobre a composição química do sistema, outra função potencial tem que ser definida. Essa função, como será visto, é o potencial químico.
Os conceitos discutidos nos próximos capítulos tentam resumir o essencial para a compreensão da termodinâmica em sua aplicação ao refino dos aços. Evitou-se o aprofundamento desnecessário, respeitando-se, porém, a consistência técnica. Para todos os temas aqui discutidos, o leitor encontra discussões mais aprofundadas em vários excelentes textos, bastante didáticos, como [1-3].
2 A ESTRUTURA DA TERMODINÂMICA
A termodinâmica é capaz de realizar previsões sobre o comportamento de sistemas utilizando medidas experimentais macroscópicas. Para tal, é estruturada em:
– Leis
– Definições
– Relações entre variáveis
– Critérios de equilíbrio
Da mesma forma que nas demais ciências, as leis são baseadas em observações experimentais, e não existem exceções à sua aplicação. Isto é, se aplicam a qualquer sistema, em qualquer processo, a qualquer momento.
Para simplificar o tratamento dos problemas termodinâmicos, uma série de grandezas e funções são definidas. É importante observar que, em todos os casos, existem um objetivo simplificador na introdução de uma nova definição!
As diversas grandezas e funções da termodinâmica estão intimamente relacionadas. Existe um conjunto de relações entre essas grandezas, que tem, frequentemente, importância prática. Todas as relações podem ser deduzidas matematicamente com base nas leis e nas definições.
Por fim, grande parte do estudo da termodinâmica se destina a permitir a definição das condições que reinam em um sistema quando ele está em equilíbrio. Assim, conhecido o estado de um determinado sistema, será possível dizer, com base na termodinâmica:
a) se esse sistema está em equilíbrio (isto é, não sofrerá alteração ao longo do tempo se não for submetido a ações externas) ou não;
b) no caso do não equilíbrio, definir em que direção o sistema deveria se modificar para atingir o equilíbrio;
c) a variação das características do sistema quando passa de um estado de equilíbrio para outro.
2.1 O Enfoque da termodinâmica e o de outras ciências
Enquanto outras ciências (como a metalurgia física, por exemplo) buscam a compreensão do porquê do comportamento observado em sistemas, a termodinâmica não se ocupa da compreensão do mecanismo segundo o qual os fenômenos por ela estudados ocorrem.
Assim, o estudo da termodinâmica de uma reação química não conduz à compreensão de como os elementos se ligam para formar um composto, ou das propriedades deste composto. Ao adotar, deliberadamente, um enfoque macroscópico para suas variáveis, e renunciar à compreensão dos mecanismos operantes, a estrutura montada pela termodinâmica se torna extremamente poderosa do ponto de vista prático por associar variáveis mensuráveis univocamente com o comportamento dos sistemas. Dessa forma, mesmo desconhecendo o mecanismo responsável
Cálculos de equilíbrio termodinâmico –fundamentos e exemplos
1. INTRODUÇÃO
Definidas as condições de equilíbrio, no capítulo anterior, ou conhecido o critério de equilíbrio (G mínimo para um sistema a P e T constante), é necessário encontrar métodos para realizar os cálculos das condições de equilíbrio de uma forma prática.
A metodologia geral de cálculo por meio da minimização da energia livre do sistema pode ser descrita pelos seguintes passos, resumidos na Figura 3.1.
Definidos os elementos químicos existentes no sistema e as quantidades de cada um, é necessário identificar as fases que podem ser formadas. Se existir uma expressão para a energia livre de Gibbs de cada fase em função de P, T e da composição química, é possível formular uma expressão geral para a energia livre total do sistema como
O problema geral consiste em determinar o mínimo dessa expressão sujeito às limitações de que a composição química de cada fase tem de somar 100% e que os elementos presentes no sistema devem se distribuir entre as fases, respeitando a conservação da massa. É evidente que, quando o mínimo for identificado, normalmente diversas fases não estarão presentes, isto é, terão n fase = 0 1
Critério de equilíbrio
A P e T constantes, GGsistematotal ' = do sistema será mínimo.
Quais elementos existem no sistema?
Quais fases podem existir?
G de cada fase pode ser calculado:
Gα = f(P,T,%E1,%E2,...,%En–1)
Gβ = g(P,T,%E1,%E2,...,%En–1) .
Gφ = h(P,T,%E1,%E2,...,%En–1)
Minimizar GTOTAL sujeito às limitações descritas:
2. EQUILÍBRIO EM SISTEMAS REATIVOS
Há diversas maneiras equivalentes de tratar o equilíbrio em sistemas reativos. A maneira classicamente adotada em siderurgia é estabelecer como critério de equilíbrio a P e T constante o mínimo da função energia livre de Gibbs, G. Esta será a formulação adotada aqui. É importante notar que essa formulação é equivalente às demais formulações adotadas por outros autores, como DeHoff [1], Lupis [2] entre outros.
Uma reação química qualquer pode ser expressa como:
aA + bB +....... = lL + mM.......
É possível (e conveniente) tabelar a variação da energia livre de Gibbs associada a essa reação. A maneira mais simples de fazê-lo é assumindo que todos os reagentes e produtos se encontram no seu estado de referência (estado “padrão”).
A vantagem dessa metodologia é reduzir o número de tabelas necessárias, facilitar a comparação de resultados obtidos por diferentes pesquisadores e, idealmente, facilitar ao usuário a compreensão do estado a que os dados se referem.
É importante notar que, como G é função de estado, a reação não precisa efetivamente ocorrer com os elementos em seu estado de referência, nem à pressão de 1 atm e temperatura de 298,15 K (frequentemente adotados como variáveis de estado que definem o estado de referência) para que se possa conhecer a variação de G associada à reação. Em verdade, a maior parte das medidas experimentais que resultam nos dados tabelados não foi obtida por meio de reações nessas condições!
2.1 Tabulações de variações de energia livre de formação
O método descrito na Figura 3.1 depende do conhecimento de expressões para a energia livre de Gibbs de cada fase em função da temperatura e composição (e, frequentemente, da pressão). Esse método é usualmente empregado em termodinâmica computacional na qual não há dificuldades maiores para tratar os cálculos envolvendo polinômios com diversos coeficientes, como visto no Capítulo 2. Entretanto, quando se deseja realizar cálculos “manuais” ou empregando planilhas de cálculo, pode ser mais conveniente empregar apenas o conhecimento da diferença de energia livre de Gibbs entre as fases de interesse (ou variação de energia livre de Gibbs na transformação entre “reagentes” e “produtos”, de forma geral).
Se, em um processo, a diferença entre produtos e reagentes for negativa, isto indica que a formação dos produtos reduz a energia livre do sistema e é, portanto, um processo espontâneo.
2.1.1 Estados de referência e tabulações de ∆G
O sobrescrito “0” indica que as substâncias ou espécies estão em seu estado de referência. Assim como no caso dos cálculos de entalpia (Capítulo 2), a escolha do estado padrão ou estado de referência é de grande importância para o correto emprego dos dados termodinâmicos e simplificação das operações matemáticas a realizar.
De forma geral, para os elementos e substâncias, é comum usar o elemento ou substância pura à temperatura de interesse como estado de referência ou estado padrão. A pressão do estado de referência é normalmente considerada 1 atm (≅ 1E5 Pa) mesmo que isto nem sempre seja indicado explicitamente.
Assim, o estado de referência em tabulações muitas vezes difere do SER por não fixar a temperatura de 298,15 K. É importante observar ainda que, se o estado SER não é usado como referência, é essencial indicar temperatura, pressão e qual a fase (ou estado físico) do elemento ou substância é considerado como estado de referência.
Físico-química de soluções simples
1 INTRODUÇÃO
Soluções são misturas de constituintes (que podem ser elementos ou substâncias). As soluções foram apresentadas no Capítulo 3 por meio de leis empíricas que descrevem seu comportamento. Entretanto, diversos modelos físico-químicos podem ser aplicados com sucesso para melhor compreender o comportamento das soluções e, até, para ajudar a realizar predições “educadas” quando dados experimentais não estão disponíveis.
2 MODELOS DE SOLUÇÕES
Nem sempre é possível medir as propriedades termodinâmicas para todas as composições e temperaturas de interesse de um sistema. Uma das alternativas para tentar resolver esse problema é a formulação de modelos de soluções, que possam ser ajustados aos dados medidos e permitam realizar previsões razoáveis do comportamento do sistema fora das regiões em que existem medidas, tanto interpolando como extrapolando.
Além disso, modelos podem ser muito úteis para a compreensão do comportamento das soluções, do ponto de vista físico-químico.
O enfoque usualmente empregado para a previsão das propriedades termodinâmicas das soluções consiste em modelar a variação da propriedade associada ao processo de mistura. De forma geral, os modelos mais comuns são focados em obter descrições da energia livre de Gibbs das fases, soluções ou misturas.
2.1 Como descrever matematicamente a energia livre de diferentes fases?
Para uma descrição consistente de um sistema, em primeiro lugar é necessário obter-se um método para descrever a energia livre dos elementos puros em diferentes fases para, a seguir, propor modelos para a variação das energias livres associadas aos processos de misturas. Normalmente, nos algoritmos de cálculo manual, empregamos como “zero” ou referência para o cálculo a energia livre de Gibbs de determinada fase à temperatura e pressão do processo.
100
Isto é, para o processo de mistura de A e B na fase φ, formando uma solução A-B:
XA XB AB ABφφ+=
Calculamos a variação de energia livre no processo de mistura:
∆= −+() GG XG XG mA BA AB B φφ e tomamos GGAB φφ == 0 para T e P do processo de mistura. Naturalmente, isso só precisa ser feito quando se deseja fazer um cálculo manualmente. Caso contrário, adotamos descrições mais ou menos completas para as propriedades de A e B na fase φ:
Gf PT eG gP T AB φφ = () = (),,
2.1.1 Elementos puros
A maioria dos cálculos de equilíbrio de interesse em metalurgia envolvem pressão e temperatura constante, razão pela qual a minimização da energia livre de Gibbs é utilizada como critério de equilíbrio. Existem relações bem definidas entre cP, H, S e G de uma substância, como visto nos capítulos anteriores. Dependendo da faixa de temperatura a que se aplicam podem aparentemente contradizer as teorias da física, uma vez que é esperado, para baixas temperaturas, que cP→0 e que descrições do tipo cP = gT + aT3 sejam adequadas [1]. Uma relação empregada com frequência é aquela proposta por Kubaschewski [2] que resulta, como visto no Capítulo 3, no conjunto de equações:
tável Φ Φ a 298 15 298 15 , ,, K H i K () é denominada GHSERi (o sobrescrito T indica que G é função da temperatura).
GHSER =G -H 298,15K i T, i i ()
Expressões para GHSERi em função da temperatura para os elementos puros em diversas fases são dadas no banco de dados do SGTE [3].
A energia livre do elemento i em uma estrutura (fase) Π Π () , G T i pode ser descrita da mesma forma, e também é dada por Dinsdale [3]. A diferença entre Ge G TT ii ΠΦ é frequentemente denominada lattice stability do elemento i na fase Π
Isto é:
GH KG GGHSER T T T ii ii i ΠΦ ΠΦ () =− + 298,15 =
= Lattice Stability da fase Π do elemento i + GHSERi Os modelos mais simples (principalmente os modelos pioneiros de L. Kaufman e colaboradores [4,5]) consideram para fins de modelamento do diagrama de fase que GHSERi não influencia nos resultados e trabalham, portanto, apenas com as “lattice stabilites”. Nesse caso, uma das fases do elemento (normalmente aquela que é estável à temperatura ambiente) é escolhida como estado de referência e tem sua energia livre fixada em zero a qualquer temperatura. A principal dificuldade associada a esse enfoque é a impossibilidade do emprego dos dados para cálculos de variação de entalpia, por exemplo, balanços térmicos.
3 MODELOS PARA SOLUÇÕES SÓLIDAS E LÍQUIDAS
Conhecidas as propriedades dos elementos puros nas diversas fases possíveis (por exemplo, para o elemento Fe: CCC, CFC, HCP, Líquido, Gás) é necessário considerar o efeito de elementos em solução nestas fases, sobre suas propriedades termodinâmicas.
A vantagem evidente da descrição sob a forma de polinômio é a facilidade de manipulação algébrica. Os termos propostos por Kubaschewski, refletem, além disso, vasta experiência no ajuste empírico de polinômios à função cP nas faixas de temperatura usualmente de interesse metalúrgico. (Note que a proporção que se ultrapassa θDebye mais deveria cv se aproximar de um valor “constante”: e cP?).
2.1.2 Estado de referência para elementos puros
Enquanto é possível obter valores absolutos de cp e S (conforme a terceira Lei da termodinâmica), o mesmo não acontece para H e G. Assim, é necessário definir um estado de referência para a entalpia e para a energia livre. O estado de referência mais comum adotado para a entalpia é o estado SER, discutido anteriormente. Esse “zero” fixa, em conjunto com a terceira lei da Termodinâmica, o “zero” para a energia livre de um elemento puro i, G i T,Φ , que é referida à entalpia de sua forma es -
De forma geral, para uma solução substitucional qualquer, pode-se expressar a energia livre da solução como:
Na equação, o termo “excesso” retrata, em geral, o desvio em relação à idealidade de uma solução real.
3.1 Solução Ideal
Quando avaliamos no Capítulo 2 as propriedades parciais molares de uma solução, verificamos que, para a uma propriedade qualquer da solução, (em particular a entalpia) ela obedece às seguintes equações:
Alguns sistemas binários de importância para o refino dos aços (e algumas combinações)
1 INTRODUÇÃO
Alguns sistemas binários são particularmente importantes para a compreensão dos processos de refino dos aços. Neste capítulo, alguns desses sistemas binários e sua extensão parcial a ternários relevantes são revistos. São também analisadas algumas das interações mais importantes entre alguns desses sistemas.
2 O SISTEMA Fe-O (E O SISTEMA Ni-O)
2.1 Equilíbrio Fe-O
O diagrama de equilíbrio de fases para o sistema Fe-O a 1 atmosfera de pressão total é apresentado na Figura 5.1.
É importante observar que o oxigênio tem uma solubilidade bastante alta no ferro líquido (cerca de 0,23% a 1600 oC) e praticamente nenhuma solubilidade nas fases sólidas do ferro (Figura 5.2). Três óxidos são formados, com diferentes estequiometrias: “FeO”, Fe2O3 e Fe3O4 (um espinélio FeO.Fe2O3). Isso está associado ao fato de o ferro ter duas valências (ou níveis de oxidação) usuais, Fe+2 e Fe+3. Embora o sólido formado pelo Fe+2 e pelo oxigênio (a wustita) seja comumente chamado de “FeO”, ele é deficiente em Fe, existido lacunas na sub-rede do ferro em sua estrutura cristalina. Tem a mesma estrutura da halita (NaCl).
O óxido líquido em equilíbrio com o ferro líquido a alta temperatura tem fórmula aproximada “FeO”. O extenso campo “óxido líquido” , a estas temperaturas, é possível em virtude da existência dos dois níveis de oxidação do ferro, +2 a +3 (ver Figuras 5.6 e 5.7, nesta mesma seção).
Figura 5.1 Diagrama de equilíbrio de fases do sistema Fe-O a 1 atm. A pressão de oxigênio (atividade ou potencial químico do oxigênio) evidentemente, NÃO é constante nem igual a 1 atm ao longo do diagrama. Adaptado de [1, 2].
Dois fatos importantes são observados da Figura 5.2: como a solubilidade do oxigênio no ferro sólido é muito baixa, é possível ocorrer formação de óxidos de ferro durante a solidificação, em função da elevada solubilidade do oxigênio no ferro líquido. A wustita funde a temperaturas relativamente baixas e, no sistema binário Fe-O rico em ferro, causa o aparecimento de líquido a 1370 oC (Figura 5.1).
Para correlacionar os diagramas das Figuras 5.1 e 5.2 com o potencial químico ou a atividade do oxigênio, é preciso conhecer o comportamento das soluções diluídas de oxigênio no ferro, que segue, aproximadamente, a lei de Sieverts.
Figura 5.2 Região rica em ferro do diagrama de equilíbrio de fases Fe-O a 1 atm de pressão. A solubilidade do oxigênio nas fases sólidas do ferro é muito baixa. Adaptado
[3].
A Figura 5.3 mostra os resultados da quantidade de oxigênio dissolvido em ferro e em níquel a diferentes temperaturas, em função do potencial de oxigênio expresso como pressão de oxigênio.
Escórias – estrutura, propriedades e reações envolvendo escórias
1 INTRODUÇÃO
Escórias são formadas nos processos metalúrgicos com dois objetivos principais:
a) Reter os óxidos ou outros compostos indesejáveis presentes nos minérios sujeitos ao refino, e
b) Reter compostos formados a partir das impurezas que se deseja remover dos metais sendo refinados.
Além disso, as escórias de aciaria têm duas funções adicionais extremamente importantes:
c) Agir como isolante térmico no topo do reator (forno, conversor, panela, distribuidor);
d) Moderar ou evitar o contato do ar com o metal líquido, limitando a entrada de oxigênio, nitrogênio e hidrogênio (via umidade do ar).
Assim, as características das escórias são extremamente importantes nos processos metalúrgicos.
A escória, em um processo metalúrgico não é um subproduto que ocorre de forma pouco controlada. Para garantir a eficiência da remoção das impurezas e a separação dos compostos indesejáveis assim como a própria separação da escória do metal, é necessário que propriedades como viscosidade, ponto de fusão, densidade e tensão superficial sejam cuidadosamente controladas. Assim, adições de fundentes e formadores de escória são utilizadas em, essencialmente, todos os processos metalúrgicos.
Historicamente, as escórias metalúrgicas eram ricas em sílica, pois silício e oxigênio são os dois elementos mais abundantes na crosta terrestre e os minerais mais abundantes são silicatos e a própria sílica [1, 2]. À medida que os conhecimentos necessários para se atingir os objetivos metalúrgicos dos diversos processos foram sendo acumulados (empírica ou cientificamente) as escórias passaram a ser ajustadas de modo a ter uma composição química otimizada para seu objetivo, por meio da adição deliberada de compostos.
Há um ditado clássico em metalurgia que diz: “Cuide da escória e o metal cuidará de si mesmo” [3], que reflete a importância dada pelos operadores de processos de refino à composição e comportamento da escória.
Por outro lado, a seleção dos refratários empregados nas operações de refino está, normalmente, condicionada à escória que será utilizada, uma vez que a siderurgia é, possivelmente, um dos poucos processos químicos em que o reator é consumido durante o processo - este consumo é largamente definido, também, pela combinação escória-refratário selecionada.
A Tabela 6.1 apresenta algumas composições típicas de escórias de processos siderúrgicos:
Enquanto a descrição do comportamento dos solutos nos metais líquidos é relativamente simples, como discutido nos capítulos anteriores, a descrição do comportamento dos diferentes solutos em escórias industriais tem sido um desafio contínuo. Isso se deve ao fato de que essas escórias raramente são soluções diluídas, e a complexidade da estrutura desses líquidos.
A compreensão da estrutura das escórias líquidas pode auxiliar na formulação de modelos de solução que eventualmente venham a descrever adequadamente o comportamento das escórias líquidas, sob o ponto de vista termodinâmico.
2 ESTRUTURAS DAS ESCÓRIAS
A estrutura das escórias líquidas depende do comportamento dos elementos presentes. A eletronegatividade, a maior ou menor tendência à ionização dos elementos, tem um papel importante na definição desse comportamento.
A divisão simples entre ligação covalente e iônica é uma simplificação útil, embora nem sempre exatamente correta [4-6], e é adotada nesta discussão.
As escórias líquidas são normalmente condutoras elétricas, enquanto vários dos seus constituintes não conduzem eletricidade no estado sólido. Assim, é razoável supor que as escórias líquidas contenham íons positivos (cátions), como Ca+2, Mg+2 e Fe+2 e íons negativos (ânions) como O−2, PO4−3 e SiO4-4 no líquido, com alguma mobilidade.
Acredita-se que, à semelhança das estruturas das fases sólidas da SiO2, o silício se coordene com quatro O−2, formando SiO4−4 com estrutura de tetraedros, como mostra a Figura 6.1.
(círculos pretos: átomos de silício; círculos brancos, átomos de oxigênio). Adaptado de [7].
da sílica
É evidente que, para que essa estrutura seja compatível com a estequiometria, é necessário que os vértices dos tetraedros sejam compartilhados, como indica a Figura 6.2.
No estado sólido, os tetraedros podem se organizar de diferentes formas [8], como mostra a Figura 6.3, dando origem ao polimorfismo da sílica.
Fundamentos da cinética dos processos de refino
1 INTRODUÇÃO
Durante um longo período da história recente da metalurgia, os processos de refino dos aços evoluíram à frente do conhecimento técnico sobre os fenômenos neles envolvidos. O desenvolvimento do conversor Bessemer, por volta de 1856 [1], capaz de produzir uma corrida de aço em cerca de 30 minutos de sopro, por exemplo, foi fundamentalmente empírico. Os fornos Siemens-Martin, desenvolvidos pela aplicação do conceito de regeneradores térmicos por William Siemens [2]1 foram uma evolução da “pudlagem” do ferro, que os metalúrgicos da época podiam compreender, do ponto de vista empírico. O refino consumia cerca de 12 horas. Naturalmente, o controle dos processos, especialmente nos conversores era tão limitado quando a compreensão dos fenômenos que neles ocorriam. Enquanto Bessemer aparentemente tinha dificuldades em controlar o fim de sopro, Goran Goransson,2 na Suécia, controlava o fim do sopro por meio da ductilidade das gotas de metal ejetadas do conversor [2]. Quando o oxigênio produzido industrialmente se tornou disponível e se buscou o desenvolvimento de conversores empregando este gás, o desenvolvimento foi ainda empírico e os motivos pelos quais as reações de refino se passavam de forma tão rápida, mesmo com o sopro por cima, ainda foi mal compreendido.
Enquanto os conhecimentos da aplicação da termodinâmica ao refino dos aços se consolidaram nas décadas de 1940 e 1950,3 na década de 1960 começou a ficar aparente que, para atender principalmente as demandas de aumento de produtividade e de melhor controle das características do aço produzido era preciso uma compreensão mais exata dos processos que se passavam no interior dos reatores de aciaria. Em especial, era necessário entender como se passavam as reações químicas envolvidas, o que limitava a taxa4 global com que ocorriam e, mais importante, como seria possível controlar e acelerar estas taxas. Os trabalhos com meto-
1 William Siemens era irmão de Werner von Siemens. Ambos foram inventores e empreendedores. Werner von Siemens fundou a empresa que leva seu nome.
2 Goran Goransson foi o fundador da empresa Sandvik.
dologia bem definida de estudos cinéticos possivelmente se iniciaram com Darken [3]5 nos EUA e Schenk na Alemanha e amadureceu nos esforços e trabalhos hoje clássicos de grupos como os de Julian Szekely e de J. Keith Brimacombe (aluno de F. D. Richardson), para citar alguns, e com o desenvolvimento, fundamentado em modelos matemáticos e físicos do processo AOD na década de 1970.
2 FUNDAMENTOS DA CINÉTICA EM REFINO DOS AÇOS
Durante o refino dos aços diversas alterações (de composição química, temperatura etc.) são desejadas. Essas alterações são “movidas” pela busca do equilíbrio termodinâmico. Entretanto, não se passam instantaneamente. Algumas dessas alterações estão associadas a reações químicas, outras não. Para que se possa compreender o que define a taxa com a qual essas alterações ocorrem, não basta compreender o estado de equilíbrio que o sistema busca atingir: é necessário compreender e estudar como essas alterações ocorrem. Como, em muitos casos, as alterações não envolvem reações químicas e, em outros, apesar de envolverem reações químicas envolvem outras etapas importantes, é conveniente denominar o objeto de nosso estudo cinético como um “processo” que pode ou não englobar uma reação química. Embora correndo o risco associado ao emprego da palavra também para descrever um processo empregado para o refino (Forno Elétrico etc.), evita-se a confusão com a cinética de uma “reação”. Assim, a menção à cinética de uma reação, se refere, neste texto, à cinética apenas dos processos químicos envolvidos na transformação de reagentes em produtos.
Excetuando-se os processos de homogeneização de uma determinada fase, e os processos que envolvem apenas transmissão de calor e fusão, os processos que ocorrem no refino dos aços envolvem reações que se passam, normalmente, em interfaces entre fases.6 Os processos de homogeneização de uma fase podem ser tratados por modelos fluido dinâmicos ou por correlações, por exemplo, como discutido no Capítulo 8.
4 É comum em português usar-se “velocidade” ao invés de taxa. Entretanto, é conveniente reservar “velocidade” para a taxa de movimento apenas. As variações de outras grandezas (como quantidade ou concentração) em função do tempo, de forma geral são chamadas de “taxas”. Em inglês “rate” é usado. “speed ” nunca é empregado, nem tampouco “velocity ”.
5 A apresentação de um modelo simples para a evolução do CO no forno Siemens-Martin no livro de 1953 se tornou uma das fontes mais comuns do valor da espessura da camada limite em um banho de aço, embora Darken, na ocasião, tenha deixado claro que apenas estimara (let us postulate tentatively) esse valor!
6 De forma estrita, os processos de fusão também ocorrem em interfaces, no caso entre a fase sólida e a fase líquida.
3 ETAPAS DE UM PROCESSO HETEROGÊNEO
Em função desse aspecto topológico, esses processos são chamados de processos heterogêneos.7 Conceitualmente, todo o processo que envolve uma reação em uma interface, envolverá diferentes etapas, em série, para que seja completado:
a) O transporte do reagente nas fases envolvidas, até a interface;
b) Eventuais fenômenos interfaciais como adsorção ou dessorção;
c) A reação propriamente;
d) O transporte dos produtos a partir da interface nas fases envolvidas.
Quando duas fases fora de equilíbrio estão em contato, em uma interface, existe uma força motriz para que o equilíbrio seja atingido. Se assumirmos que a temperatura e a pressão (dois potenciais termodinâmicos) das duas fases são iguais, a força motriz para que o equilíbrio seja atingido será a diferença entre os potenciais químicos das espécies ou elementos envolvidos. Analisando-se de forma macroscópica, essa força motriz é usada para produzir as transformações listadas acima, isto é, causar o transporte dos reagentes e dos produtos e fazer com que a reação química ocorra. Se uma das fases ainda não existe (por exemplo, quando ocorre a nucleação de uma bolha ou de uma inclusão não-metálica no metal líquido), parte da força motriz é necessária, também, para causar a nucleação da fase em questão.
3.1 Um processo simples – remoção de nitrogênio do aço líquido
Para compreender como as diversas etapas de um processo heterogêneo são importantes no resultado global do processo, é conveniente apresentá-las em um exemplo de um processo simples como a remoção do nitrogênio dissolvido no aço pela exposição ao vácuo. Posteriormente, os aspectos importantes dessas etapas serão estudados em mais detalhe.
A diferença de potencial químico µµ N metal N gás s é a força motriz para que o aço seja desgaseificado, isto é, para que o nitrogênio passe do aço para o gás. Essa diferença de potencial será empregada nas diferentes etapas que acontecem no processo, de modo que o processo ocorra e, eventualmente, a condição de equilíbrio, , se estabeleça.
7 Em contraposição a processos homogêneos, que se passam em qualquer ponto de uma fase.
Cinética – interações entre fases
1 INTRODUÇÃO
No Capítulo 7 observou-se a importância do coeficiente de transporte de massa na cinética de um processo heterogêneo. Dois casos específicos de interações entre fases foram discutidos: o escoamento de um fluido, em regime estacionário, em contato com um sólido (item 2.3.1) e o escoamento do metal na superfície de um forno a indução (item 2.3.3.3). Em processos siderúrgicos, as interações entre fases são, normalmente, bem mais complexas. Os processos de refino do aço que tiveram longa vida, industrialmente, ou que ainda hoje são empregados, normalmente dependem de formas bem-sucedidas de interação entre fases, combinadas com condições termodinâmicas adequadas aos objetivos do processo. Neste capítulo, os tratamentos das interações entre fases nas configurações mais comuns no refino dos aços são apresentados e discutidos. Esse enfoque é interessante já que diversas configurações se repetem em diferentes processos e, pode-se esperar, serão empregadas em novos processos que virão a ser desenvolvidos. A ênfase é na discussão e apresentação de formulações de emprego relativamente fácil na aciaria e que conduzam à compreensão dos fatores mais relevantes nestes processos. O modelamento computacional fluido-dinâmico (CFD) não é discutido em detalhe. Ao leitor interessado, recomenda-se textos dedicados a essa técnica (por exemplo [1]).
2 SISTEMAS LÍQUIDO-GÁS
Interações entre gás e líquido estão presentes em praticamente todos os processos de refino. Uma vez que esses processos ocorrem à pressão constante, o contato gás-metal ou gás-escória é sempre presente na superfície dos banhos. Um exemplo simples foi discutido no Capítulo 7 (evaporação no forno de indução). Nos casos relacionados à desgaseificação e absorção de gás foram considerados apenas o efeito global, independente do efeito das condições de injeção de gás.
Por outro lado, uma das interações importantes entre gás e líquido em processos de refino é a transferência de quantidade de movimento (momentum ou momento linear) do gás para o metal. Injeção de gás e sopro de gás são frequentemente responsáveis por agitação e homogeneização de banhos de metal e da escória. Em diversos casos, o gás é usado com esse propósito,
principalmente (por exemplo, uso de gás inerte). Em outros, o gás, além de transferir quantidade de movimento, também reage com o metal (sopro de oxigênio, por exemplo).
O conhecimento da forma, dimensões e velocidade individual das bolhas é interessante e importante para a quantificação da área interfacial e do transporte de massa.
Um efeito importante em sistemas líquido-gás é a possibilidade de formação de misturas físicas: espumas e emulsões. Esses fenômenos são tratados mais adiante, no Item 3.2.
2.1 Injeção submersa
O efeito da transferência da quantidade de movimento pode ser estimado por relações globais que não consideram as bolhas individualmente, o que é mais simples, matematicamente.
No aço, o processo de formação das bolhas é complexo e nem sempre intuitivo. Uma parte significativa do conhecimento sobre as interações entre gás e metal líquido foi obtido estudando-se sistemas estáveis à baixa temperatura usando água, soluções aquosas, óleos e mercúrio, por exemplo. A densidade do aço líquido é cerca de 7 vezes maior que a da água. Logo, a variação de pressão ao longo da profundidade do banho é muito grande. A tensão superficial aço-gás é significantemente mais alta do que entre água e gás. O efeito dessas características nos fenômenos de formação de bolhas será discutido mais adiante, mas a transferência das informações entre diferentes sistemas deve ser feita cuidadosamente, respeitando-se os princípios de similaridade [2].
2.1.1 Agitação – modelos macroscópicos de injeção localizada
Quando gás é injetado por baixo do metal, o diâmetro da região bifásica metal-gás (pluma) aumenta, à medida que a distância do ponto de injeção, no fundo do vaso, aumenta. As pesquisas originais levaram a visualização da pluma como mostra a Figura 8.1.
Essa configuração foi determinada por meio de vários estudos experimentais como os apresentados na Figura 8.2.
Ao injetar um gás em um líquido de baixa densidade, o gás transfere energia cinética e potencial para o líquido. Esse modelo prevaleceu para a injeção de gás no aço, durante alguns anos [3]. Já no final da década de 1970, o efeito da energia cinética na injeção em metais era questionado, em vista da elevadíssima diferença de densidade entre as duas fases. A principal implicação desse questionamento é a baixíssima penetração de jatos injetados lateralmente em banhos metálicos [5]. A injeção lateral tem pouca penetração e, dependendo do arranjo do vaso e da posição do sopro, pode contribuir para o desgaste refratário acima da região de injeção. A energia potencial do gás é associada à posição vertical onde é injetado e a sua expansão, associada à diferença de temperatura entre as fases e a variação de pressão com a profundidade do banho. Cerca de 1,4 m de profundidade de aço correspondem a 1 atm de pressão (equivalente a uma profundidade de 10,13 m de água)!
Refino primário – conversão
1 PROCESSOS DE REFINO DOS AÇOS
Neste capítulo é apresentada a evolução histórica dos processos de refino de aço. O conhecimento dessa evolução permite compreender melhor os processos atuais. A seguir, são apresentados os principais processos de refino, fazendo uso dos conceitos cinéticos e termodinâmicos discutidos nos capítulos anteriores. Os processos de conversão são discutidos neste capítulo e o forno elétrico a arco, no capítulo seguinte.
2 HISTÓRICO
Embora o alto-forno seja um processo muito antigo, o seu aperfeiçoamento por Abraham Darby em 1709 [1] viabilizando a produção de grandes quantidades de gusa líquido é um ponto crítico na história do aço como material de construção.
Muitos produtos interessantes podiam ser produzidos diretamente do gusa. Entretanto, a tenacidade e ductilidade do aço já eram consideradas importantes na época, pois havia processos de produção de aço em pequenas escalas, sem fusão completa. Os processos de fabricação do aço líquido, entretanto, demoraram mais a ser desenvolvidos. A produção de metal líquido é praticamente essencial para viabilizar a produção em grande escala de metal.
A Figura 9.1 apresenta as alterações necessárias na temperatura e no teor de carbono para se obter aço líquido em condições de ser lingotado. No início do século XIX, já era evidente que o gusa precisava ser oxidado para remover o excesso de carbono principalmente, e que o equipamento usado deveria ser tal que permitisse um significativo aumento de temperatura. Para a oxidação, dois tipos de oxidantes baratos e facilmente disponível foram considerados: o ar atmosférico, com cerca de 20% de oxigênio – e o remanescente, essencialmente nitrogênio e minério de ferro, com cerca de 30% de oxigênio (Fe2O3) e o restante de uma “impureza” inofensiva, o próprio ferro.
Quanto aos aspectos térmicos, duas rotas foram desenvolvidas na época. A rota da conversão1 do gusa, em que nenhum aporte de energia externo é realizado e apenas o calor decorrente da oxidação do carbono, silício, fósforo, parte do ferro e manganês é utilizado para aquecer o banho e a rota em que fornos (onde há aporte de energia) são empregados. O importante efeito da “energia térmica” foi visto nos balanços térmicos apresentados no Capítulo 2.
Mesmo com uso de energia externa, atingir a temperatura de cerca de 1600 oC não é fácil: Somente as ideias de Carl Wilhelm Siemens, com os fornos regenerativos (em que o calor do gás queimado é usado para aquecer o gás de entrada por meio de regeneradores) aliadas à criatividade de Pierre-Emile Martin, que em 1865 desenvolveu os conceitos de Siemens para a criação do forno de soleira aberta (open hearth) chamados de Siemens-Martin [1] viabilizaram esse processo como será discutido adiante.
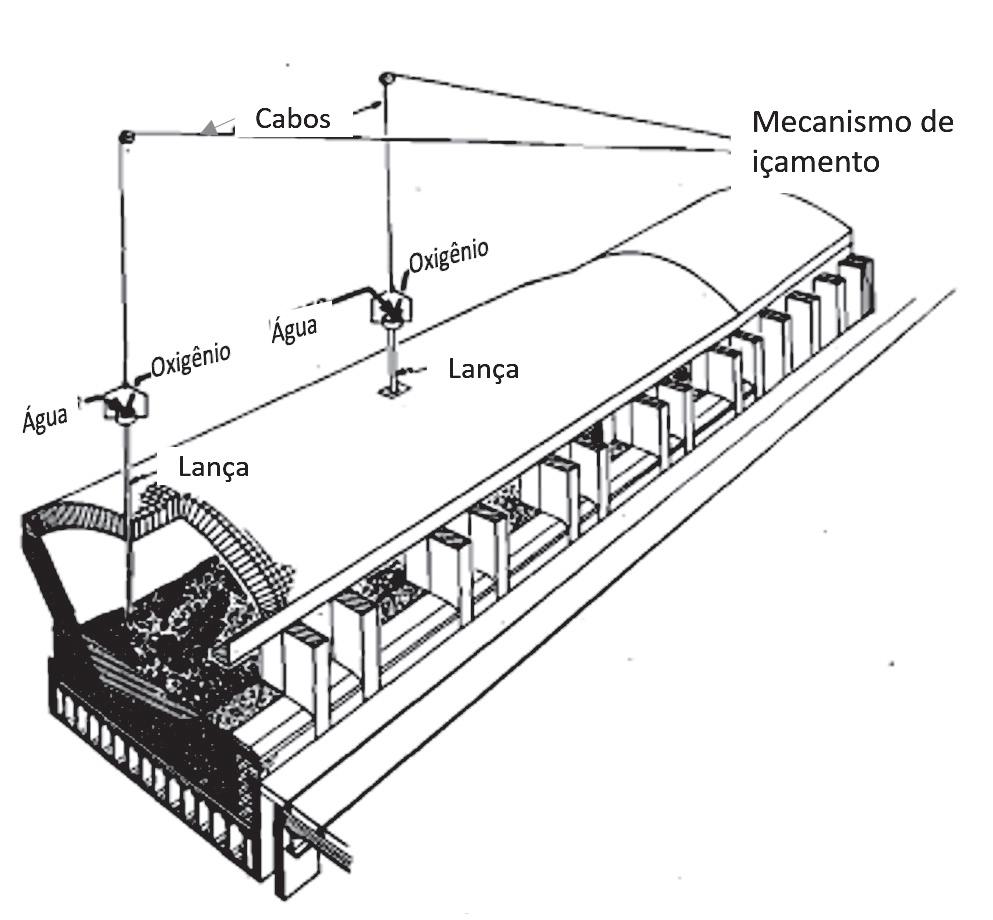
2.1 Processo Siemens-Martin BOHF (Basic Open-Hearth Furnace)
O processo Siemens-Martin dominou a produção mundial de aço aproximadamente até a década de 1960, em vista de sua flexibilidade quanto à qualidade do aço produzido, com possibilidade de algum controle do teor de residuais e capacidade de fusão de sucata.
1 É convencional chamar, em inglês, o equipamento no qual o gusa é convertido em aço SEM aporte de energia externa de converter. Em português, a nomenclatura adotada em Minas Gerais e Espírito Santo, é “convertedor”, enquanto no Rio de Janeiro se dá preferência a “conversor”, adotada neste texto.
Cabos Mecanismo de içamento
Oxigênio
A Figura 9.2 mostra esquematicamente um forno Siemens-Martin. A Figura 9.3 mostra a evolução da composição química do metal e da escória em uma corrida em que a oxidação do metal é feita somente pela adição de minério de ferro. Água Água
Oxigênio Lança Lança
(a)
Banho
Furo de vazamento
Banho
Portas
Regenerador
(b)
Queimador de óleo
Portas
Furo de vazamento
Soleira
(c)
Vista em corte
ar gás
ar gás Vista de topo
Regenerador
Refino primário – forno elétrico a arco
1 INTRODUÇÃO
Existem vários tipos de fornos que empregam a eletricidade como fonte de energia para a fusão e aquecimento de aço líquido. Entretanto, em termos de utilização, o forno a arco e o forno de indução são os mais comuns. Como o emprego de escória no forno de indução é difícil (em função da dificuldade para seu aquecimento), esses fornos encontram maior emprego em fundições e praticamente 100% da quantidade produzida em aciarias elétricas provêm de fornos a arco.
O forno elétrico a arco (FEA) foi inventado por Paul Héroult em 1889 [1]. Entretanto, o crescimento da utilização desse forno, na indústria siderúrgica, foi limitado, durante vários anos, pelo custo da produção de eletricidade. Já na década de 1930, o FEA tinha atingido um nível de desenvolvimento e participação na siderurgia “onde seria difícil ou quase impossível produzir determinadas especificações de aço sem seu emprego” [2]. Nas últimas décadas do século XX e início do século XXI o desenvolvimento em FEA tem sido impressionante. Uma das características notáveis do FEA, que permitiu esse avanço, é viabilizar o controle da temperatura de forma praticamente independente do controle do potencial de oxigênio. Como discutido anteriormente, isso não é possível nos conversores e era quase impossível nos fornos Siemens-Martin. O FEA é, portanto, o equipamento primário mais versátil de produção de aço. Nas últimas décadas, também vem se tornando um dos mais eficientes. Algumas das importantes vantagens do FEA são:
– Permite produzir praticamente qualquer tipo de aço, em função do controle do aquecimento virtualmente independente de reações químicas;
Tem alta eficiência energética;
– Versatilidade de carga: pode ser operado desde 100% de carga sólida até 100% de carga líquida;
– Permite operação intermitente e mudanças rápidas na prática de produção em escalas desde dezenas até centenas de toneladas. Permite operação com adição contínua de sucata ou ferro esponja.
Entretanto, nos últimos anos, o foco principal no desenvolvimento dos fornos elétricos a arco tem sido a obtenção rápida e eficiente de uma carga de aço líquido [3]. Mesmo com a flexibilidade metalúrgica do FEA, cada vez mais as etapas de refino do aço têm sido transferidas para fora do FEA. A motivação para isso tem sido a busca da combinação de processos mais econômicos e eficientes para a produção do aço. Por esse motivo, os aspectos de geração e transmissão de calor e físico-química no interior do FEA têm se tornado extremamente importantes. As limitações termodinâmicas e físicas associadas a esses fenômenos adquirem, portanto uma importância fundamental [3].
O número crescente de fornos a arco instalados, a tendência a instalações cada vez maiores (fornos de 200 a 250 t) e a participação crescente desses fornos na produção mundial de aço são claras evidências da importância crescente desse processo.
No Brasil os fornos elétricos a arco são predominantemente de corrente alternada. No mundo, pouco menos de 10% dos fornos elétricos a arco, em aciarias, é de corrente contínua (em cerca de 1100 FEA no mundo [4, 5]). Madias e colaboradores avaliaram a carga e o desempenho de cerca de 190 FEA, dos quais 15% eram de corrente contínua [6]. Essa participação é bastante inferior às estimativas em 2000 de que cerca de 50% da produção em FEA seria em corrente contínua [7]. Fornos de corrente contínua introduzem menos instabilidade e “ruído” na rede elétrica a que estão ligados. Esse é, possivelmente, o principal motivo de seu desenvolvimento na Europa e nos EUA.
Em geral, o principal componente do custo operacional de um FEA é a carga metálica (cerca de 70% dos custos operacionais [3]). Uma parcela muito significativa do restante dos custos operacionais é representada pela energia elétrica, eletrodos, e os eventuais combustíveis.
2 EQUIPAMENTO – VISÃO BÁSICA
Classicamente, os FEA são compostos por uma carcaça de forma próxima à cilíndrica, com um fundo aproximadamente semielíptico e uma abóbada, além de uma sofisticada instalação elétrica (para prover a energia aos arcos de forma controlada) e mecânica (capaz de bascular o forno, abrir a abóbada e manter os eletrodos corretamente posicionados). Essencialmente, dispunham de uma bica de vazamento, como mostra o esquema da Figura 10.2 (a). A tecnologia de vazamento excêntrico foi um importante avanço (Figura 10.2 (b)), eliminando a bica. A eliminação da bica com vazamento pelo fundo, permite melhor retenção de escória no forno, especialmente importante para a desoxidação e para a metalurgia secundária. Em um forno a arco de
corrente alternada e trifásico, três eletrodos de grafite são ligados às três fases do secundário de um transformador de tensão variável cuj a faixa de operação é normalmente de 100 a 1000 V, podendo chegar a 1600 V [3]. Estabelecem-se arcos elétricos entre os eletrodos, sucata ou metal líquido e a radiação do arco aquece e funde a carga.
Nos fornos de corrente contínua é empregado um eletrodo central de grafita e uma conexão elétrica no fundo do forno, como mostra a Figura 10.3. A corrente alternada é retificada por intermédio de tiristores que têm importante papel no controle do forno.
O consumo teórico de energia para aquecer e fundir 1 t de ferro desde 25 °C até 1600 °C é da ordem de 375 kWh. No começo da década de 1960, empregavam-se fornos com potência de 300 a 400 kVA/t. Ocorreu um grande desenvolvimento, visando a otimizar a capacidade de produção desses fornos, tendo-se atingido potências instaladas de 600 a 750 kVA/t e, posteriormente, até superiores a l000 kVA/t em fornos UHP (Ultra High Power – ultra-alta potência).
A Figura 10.1 apresenta um levantamento em cerca de 200 FEA, confirmando esta tendência.
Figura 10.1 Dados de cerca de 200 FEA, compilados por Madias e colaboradores [6]. A linha indica a potência instalada de 1000 MVA/t. Adaptado de [6].
Quanto maior a potência instalada, tanto mais rápida deve ocorrer a fusão da carga. Entretanto, a radiação causada pela alta energia disponível no arco acelera o desgaste dos refratários das paredes e da abóbada do forno e as elevadas correntes conduziam à necessidade de eletrodos de grandes diâmetros e considerável consumo desses, por oxidação. O adequado aproveitamento dos fornos UHP exigiu o desenvolvimento de painéis refrigerados a água em suas paredes e também abóbadas refrigeradas a água. Sobre esses painéis forma-se uma camada de escória sólida e o conjunto age como “refratário”.
Refino secundário
1 INTRODUÇÃO
Os processos secundários de refino foram desenvolvidos, inicialmente, visando obter condições termodinâmicas ou cinéticas que não eram possíveis de serem obtidas nos processos de refino primário. Assim, os problemas associados ao hidrogênio em grandes forjados levaram ao desenvolvimento da desgaseificação sob vácuo [1] e a busca de reações de refino mais rápidas levaram ao desenvolvimento do processo Perrin [2], no qual uma escória é adicionada ao aço durante o vazamento do refino primário. Paralelamente, processos de refino secundário por refusão foram também desenvolvidos para obter estruturas de solidificação mais favoráveis que no lingotamento convencional [3, 4]. Esses processos também oferecem condições termodinâmicas em que reações interessantes (eliminação de gases e inclusões, na refusão sob vácuo [5, 6], eliminação de inclusões e redução do teor de enxofre na refusão sob escória condutora [7, 8], por exemplo). A introdução dos processos de refino secundário trouxe, entretanto, além das melhorias metalúrgicas evidentemente esperadas de cada processo, mudanças profundas na estrutura da produção de aços, por dois motivos principais:
a) Em primeiro lugar, como complemento dos processos primários de conversão, viabilizou a produção de uma ampla gama de aços que não podiam ser produzidos em conversores. Aços com teores mais elevados de elementos de liga, aços com baixos teores de enxofre, aços de elevada limpeza interna etc.;
b) Em segundo lugar, permitindo uma otimização dos equipamentos da aciaria, reduzindo significativamente os tempos totais de processo e aumentando a produtividade. Essa alteração foi essencial para o desenvolvimento da moderna aciaria elétrica (a operação eficiente dos FEA UHP discutidos no capítulo anterior só é possível se o refino é concluído em um forno panela).
De uma maneira geral, os processos de refino secundário são todos os processos de refino em que a principal fonte de metal é o aço líquido proveniente de um processo
primário. Exceção importante são os processos de refusão, nos quais a fonte de metal é aço sólido proveniente de um processo de refino que pode englobar uma combinação de processos primário e secundários.
A discussão a seguir não é realizada na ordem histórica do aparecimento dos processos. Alguns processos que se tornaram menos relevantes tampouco são discutidos. A divisão escolhida foi agrupar os processos com características metalúrgicas similares, embora essa tarefa não seja simples pela variedade de processos e características na indústria, em 2022. Assim, serão discutidos:
a) Forno panela e similares;
b) Processos de desgaseificação (uso do vácuo);
c) Processos para o refino de aços inoxidáveis e similares.
2 OPERAÇÕES SIMPLES – ADIÇÃO DE LIGAS E HOMOGENEIZAÇÃO
A produção de aços commodities envolve uma pres são significativa sobre o controle dos custos de produção. Assim, a primeira maneira de aprimorar a custo mínimo os produtos de conversores, consiste em homogeneizar o aço e os desoxidantes em uma estação “pós-conversor” na qual é possível realizar adições de ligas e desoxidantes de forma controlada, com agitação por gás inerte. Essas “estações de borbulhamento” frequentemente injetam gás inerte por meio de lanças revestidas de refratário, economizando o uso de “ plug poroso” nas panelas e permitem uma relativa melhoria da qualidade quando se considera os resultados comparados com a realização de todas as adições durante o vazamento no conversor. Além disso, permitem resfriamento controlado, se necessário, e algum tempo de espera quando é necessário ajustar o sequenciamento no lingotamento contínuo. Parte das inclusões não-metálicas provenientes da desoxidação é eliminada e a escória pode ser parcialmente desoxidada, para diminuir seu efeito como fonte de oxigênio, causadora de reoxidação. Essas estações são o processo de refino secundário mais barato presentemente em uso. Não são comuns em usinas com FEA, mas são amplamente empregadas em usinas com grandes conversores.
A Figura 11.1 apresenta os processos mais simples, desde uma estação de borbulhamento “simples”.
Possivelmente, o mais sofisticado desses processos é o chamado IRUT (Injection Refine – Up temperature, Figura 11.2) ou CAS-OB (CAS, Figura 11.1, com Oxygen Blow) [9] uma estação na qual pode ser executado, também, aquecimento aluminotérmico e algum tratamento com escória sob condições controladas.

Estação de borbulhamento convencional CAS SAB CAB
Escória do conversor + adições
Panela Ar
Ar Ar Ar
Escória do conversor + adições
Escória do conversor + adições
Tampa Escória sintética Fe-ligas Escória do conversor + adições
CAS: “Composition Adjustment by Sealed Argon Bubling” – Ajuste de composição química com borbulhamento de Argônio selado
SAB: “Sealed Argon Bubling” – Borbulhamento de Argônio selado
CAB: “Capped Argon Bubbling” – Borbulhamento de Argônio coberto
Figura 11.1
Processos simples de tratamento do aço em panela. No processo CAS e no processo SAB o “olho” de metal exposto pelo borbulhamento de argônio é mantido em região protegida com argônio para reduzir a reoxidação, melhorar o rendimento das ferroligas e permitir tratamentos com escória sintética. No processo CAB, toda a panela é coberta e o espaço livre é inertizado com argônio. Adaptado de [9].
Adições de ligas
Lança de oxigênio
Lança de gás inerte para agitação
Figura 11.2 Esquema simplificado de uma sofisticada estação de injeção e borbulhamento, o processo IRUT (ver texto). Adaptado de [10].
Nos processos em que uma área da superfície do banho é isolada, como o CAS-OB é comum usar o borbulhamento de argônio para abrir o “olho” suficientemente, obtendo uma região livre da escória para realizar adições de desoxidantes e ferroligas (ver item 3.1.3 para uma discussão sobre o rendimento de adições). Como é frequente que o aço se sobreponha à escória na borda do olho, medidas por fotografias confirmaram os resultados de modelamento fluidodinâmico e indicaram que a estimativa do tamanho do “olho” pelo operador é, em geral, menor do que a necessária para evitar reter escória quando o “sino” é abaixado [11].
Solidificação e lingotamento
1 INTRODUÇÃO
Os processos de produção e refino de aços são capazes de produzir grandes massas de aço líquido com elevadíssima homogeneidade térmica e química. Entretanto, é necessário transformar essas massas de aço líquido em produtos sólidos com as formas e dimensões desejadas.
Os dois conjuntos de processos mais importantes na transformação do aço líquido em formas e dimensões adequadas à obtenção de produtos siderúrgicos são os processos de fundição e os processos de lingotamento. Grande parte das características estruturais dos produtos de aço está associada às transformações que acontecem durante a solidificação. Essas características sofrem algumas alterações no caso de produtos submetidos ao trabalho a quente (laminação, forjamento etc.). Como discutido brevemente neste capítulo, e em detalhe em outras publicações (por exemplo, [1 - 5]), essas características são preservadas, em boa parte, no produto final.
Os principais fenômenos de solidificação que dão origem às características dos produtos siderúrgicos são a contração de volume associada à mudança de estado físico e a redistribuição dos solutos do aço, chamada de segregação.
O arranjo atômico no aço líquido é menos compacto do que no estado sólido (CCC ou CFC). Isto é regra para a maior parte dos materiais – exceções importantes são a água, silício e bismuto. Assim, uma significativa variação de volume (contração) acontece durante a solidificação dos aços. Essa variação de volume pode induzir ao aparecimento de defeitos como vazios (rechupes, poros etc.) e trincas, e pode contribuir para a ocorrência de movimentos de líquido durante a solidificação. Esses movimentos podem influenciar na redistribuição de solutos, originando segregação em escala macroscópica.
Em geral, a solubilidade dos diversos elementos nas fases sólidas que se formam a partir do líquido não é a mesma que na fase líquida. Essa diferença de solubilidade nas fases líquida e sólida causa a redistribuição dos solutos durante o processo de solidificação.
Como o processo de solidificação não é tão lento que permita se restaurar completamente o equilíbrio ao fim da solidificação, parte dessa redistribuição se mantém nos produtos sólidos, sob a forma de segregação. Por outro lado, no estado sólido, o único mecanismo viável para a homogeneização da composição química seria a difusão. Outra observação importante é que embora a temperatura liquidus dos diagramas de equilíbrio de fases seja observada na prática industrial, a temperatura solidus de equilíbrio, raramente corresponde ao final da solidificação industrial pois em geral, o líquido no final da solidificação contém mais soluto do que esperado em equilíbrio, por causa da segregação.
A baixa mobilidade dos elementos substitucionais no ferro, no estado sólido, e a escala de dimensões em que a segregação de solidificação normalmente acontece, praticamente inviabilizam a eliminação completa da segregação, por homogeneização, nos produtos siderúrgicos.
A maior parte da produção mundial de aços é processada por meio de lingotamento contínuo, em que o aço começa a solidificação em um molde de cobre refrigerado a água e, após a formação de uma “casca” sólida de espessura suficiente, é resfriado diretamente por aspersão de água sobre esta “casca”. Para aços especiais, produzidos em menores quantidades, para grandes forjados e para alguns aços que exigem condições de solidificação especiais, o lingotamento “estático” ou convencional é empregado. Nesse caso, o aço é vazado em moldes chamados lingoteiras. A solidificação dentro das lingoteiras origina fundidos chamados lingotes. Adicionalmente, peças podem ser produzidas em sua forma final por meio de processos de fundição, em que aço é vazado em moldes em diferentes processos, obtendo-se peças com peso desde gramas (peças para armas, máquinas de costura etc.) até toneladas (rotores de turbinas hidráulicas etc.), por aspersão térmica ou por processos de manufatura aditiva. Esses processos não são discutidos em detalhe neste capítulo.
O produto de lingotamento ideal (lingote ou semiacabado lingotado continuamente) seria homogêneo física e quimicamente, com estrutura fina, equiaxial e isento de segregação, porosidade, cavidades e inclusões não-metálicas. Entretanto, as leis que regem a solidificação impedem a obtenção desse material perfeitamente homogêneo. Além dos problemas de qualidade interna, durante o lingotamento podem ocorrer também problemas superficiais, como dobras, trincas etc.
As características do processo de solidificação são discutidas a seguir. A discussão é limitada, uma vez que há excelentes textos na área [6-10].
Posteriormente, as interações dessas características com os processos industriais de lingotamento são discutidas, enfatizando os efeitos sobre a estrutura dos produtos.
2 CONTRAÇÃO DE SOLIDIFICAÇÃO
Durante a solidificação do aço, ocorre contração de aproximadamente 4% em volume, devido à diferença de densidade entre o aço sólido e o líquido (Figura 12.1). A sequência de fases formadas na solidificação e o intervalo de temperatura em que essa se passa tem importância sobre como a contração (e as tensões associadas) se distribui durante a solidificação. Nos aços efervescentes, essa contração era compensada pela evolução dos gases durante a solidificação [1,11].
Figura 12.1 Densidade de ligas Fe-C em função da temperatura, durante a solidificação em equilíbrio. O Fe puro solidifica a uma temperatura fixa, para a fase CCC (d) que não é compacta. Ligas com baixo teor de carbono não atravessam a transformação peritética. A liga com 0,05% forma d+L, depois fica completamente ferrítica (d). O resfriamento leva a atravessar o campo d+g e, a cerca de 1400 °C a liga é completamente austenítica, mais densa que a ferrita. A liga de aproximadamente 0,17% C tem a composição do ponto peritético. Forma d+L até ocorrer a transformação peritética, d+L→g, com brusca contração. A liga com 0,6% C já inicia a solidificação formando austenita. Calculado com Thermo-Calc [12] banco de dados TCFE10
Para garantir a ausência de vazios internos ao lingote (rechupe, porosidade etc.) e, portanto, bom rendimento metálico nos aços acalmados, é necessário concentrar essa contração em uma determinada parte do lingote. Isso é feito pelo controle do avanço da solidificação nas direções horizontal e vertical, garantindo a ocorrência de “solidificação direcional”.
De 2015 a 2020 o mundo refinou uma média de 1760Mt/ano de aço em aciarias, com um consumo médio de produtos acabados de aço de 200 a 227 kg/ano per capita. Desde a invenção dos conversores, por Bessemer, em 1856 e do desenvolvimento do forno Siemens-Martin em 1864 o refino dos aços vem sofrendo uma notável evolução. Esses processos viabilizaram a produção em alta escala de aços para aplicações comerciais, e o final do século XIX viu a explosão de aplicações do aço em estruturas de pontes, arranhacéus, material bélico e embalagens. A “metalurgia física” floresceu no começo do século XIX e, com o melhor entendimento das relações entre propriedades, composição química e processamento, demandas ainda mais rigorosas foram impostas aos processos de refino. Para atender a essas demandas, o empirismo foi sendo eliminado das operações de refino, sendo substituído pelo entendimento da termodinâmica das reações envolvidas e pelo estudo e modelamento dos processos cinéticos que controlam a velocidade do refino.
Hoje, mesmo na elaboração de aços simples, pelo menos seis elementos químicos são regularmente controlados no aço, alguns inclusive no nível de partes por milhão (ppm, isso é 1g/t!).
Neste livro, o autor revê os conceitos de termodinâmica aplicados ao refino de aço com um variado conjunto de exemplos, incluindo o uso da termodinâmica computacional.
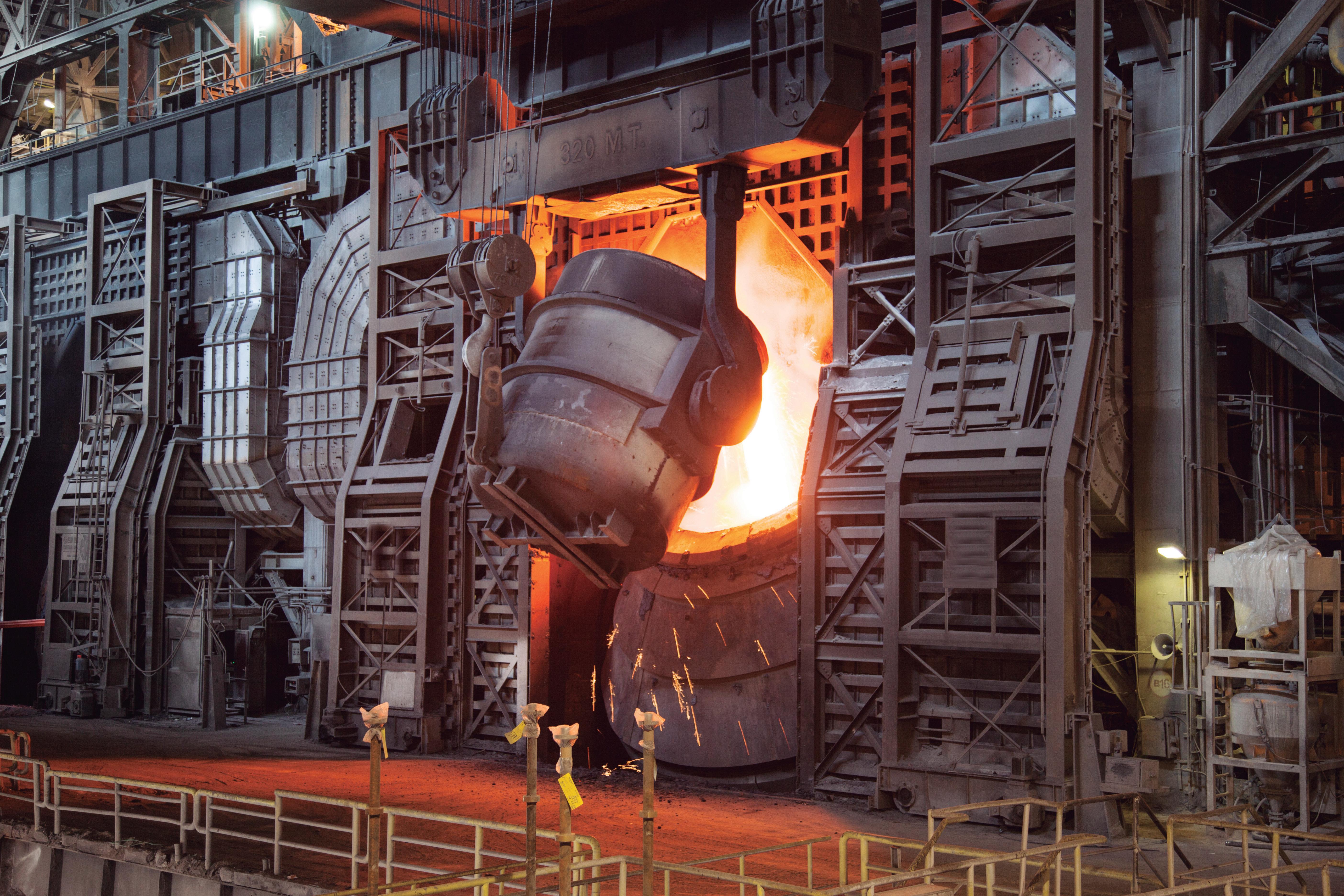
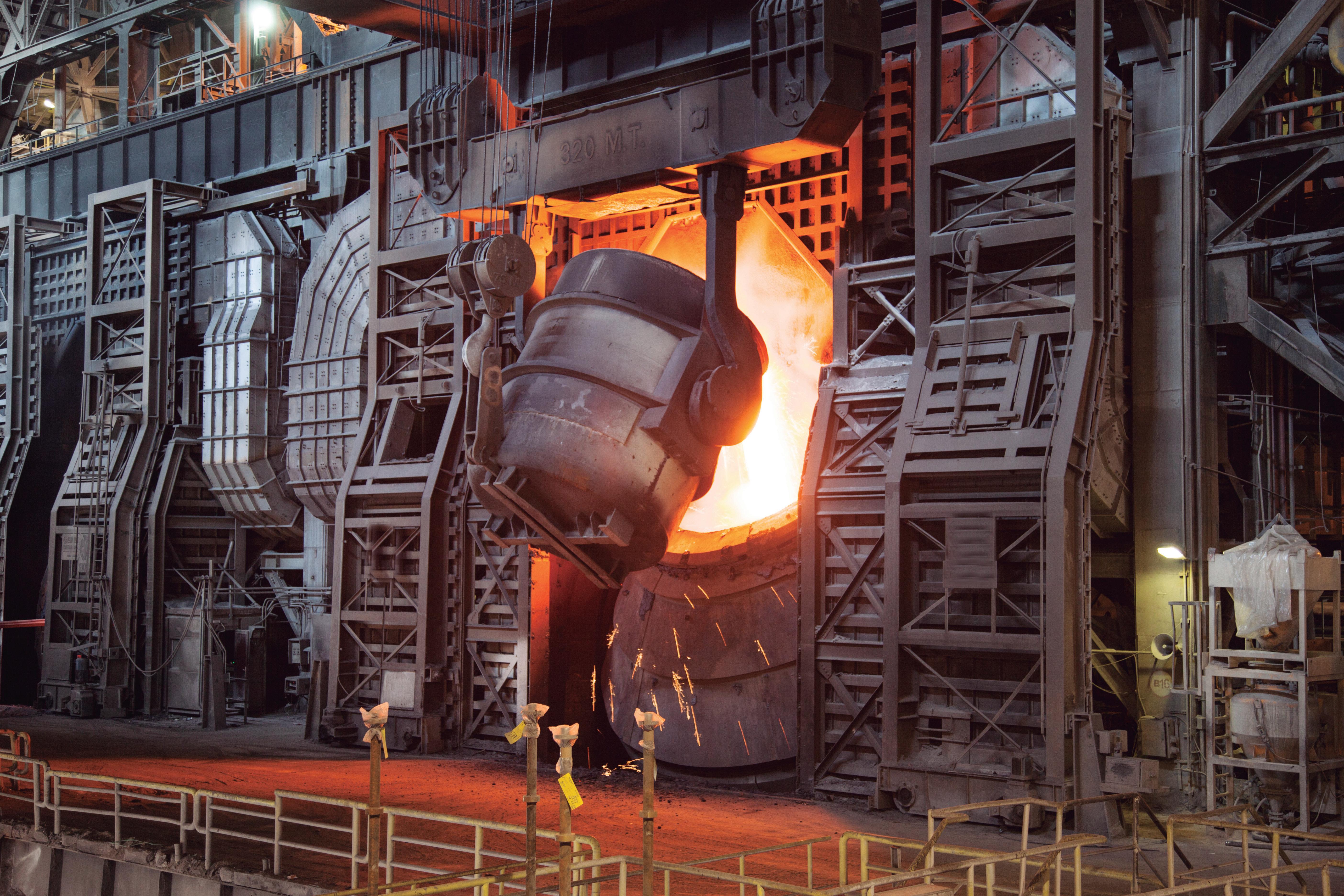
Da mesma forma, os fundamentos de cinética, com ênfase na cinética do transporte de massa, que tem papel central na taxa com a qual o refino se passa, são revistos e aplicados na análise dos processos. Assim, os processos de refino primário (Forno Elétrico a Arco e Conversor a Oxigênio, principalmente) e secundário (metalurgia de panela, desgaseificação, processos de produção de aços inoxidáveis, em especial) são apresentados e discutidos a luz dos fundamentos termodinâmicos e cinéticos, indicando as possíveis melhorias esperadas na produção de aço no futuro próximo. Embora os processos de aciaria atuais sejam capazes de produzir massas de aço liquidas com homogeneidade impressionante, desde 1870, pelo menos, a influência da solidificação sobre a homogeneidade e as características dos produtos de aço é conhecida. Por este motivo, os processos de lingotamento e os processos de refusão fazem parte da área de refino das usinas siderúrgicas e são aqui também discutidos.
O balanço entre fundamentos e aplicações e a discussão de suas relações segue, aproximadamente, o enfoque utilizado pelo autor no ensino do tema nas últimas décadas. Assim, espera-se que o texto seja útil tanto para aqueles que estudam o refino do aço como para os que já atuam na área, seja na produção ou na pesquisa e desenvolvimento.
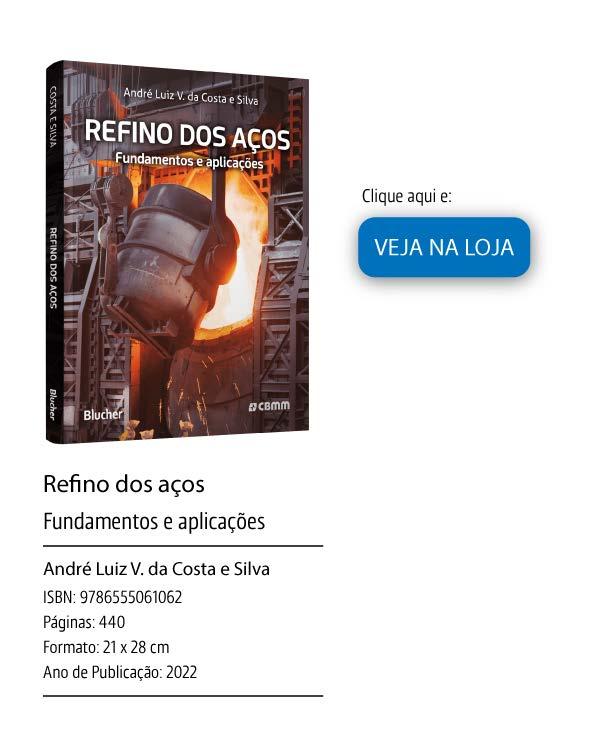