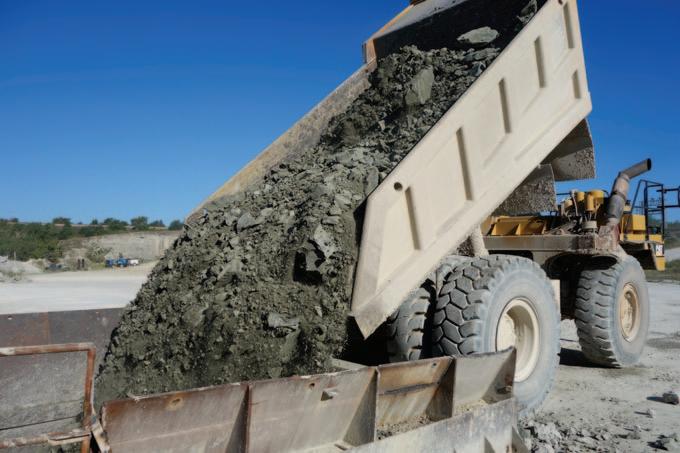
4 minute read
THE POWER OF GREAT BULK HANDLING
Reduced handling costs, shorter turnaround times, reliability and flexibility: Nemag grabs give dry bulk terminals throughout the world that competitive edge they need in today’s demanding market.

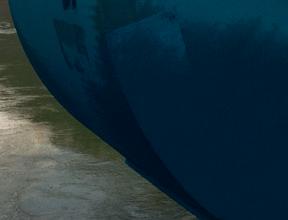
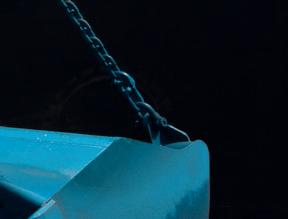
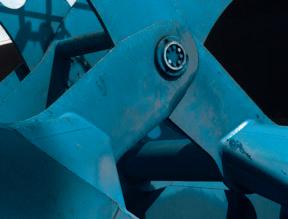
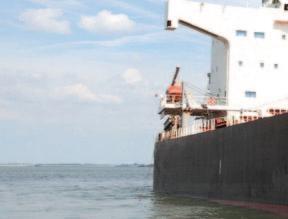
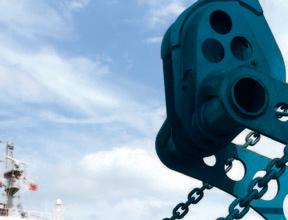
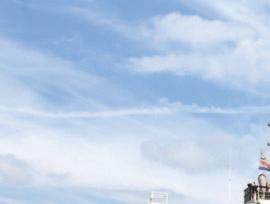
Driven to achieve the best performance, we closely listen to our clients’ needs. For almost a hundred years, Nemag’s innovative grabs make it possible to realize the highest productivity at the lowest costs.
Explore our comprehensive range of high-quality grabs and discover the power of great bulk handling. From coal and iron ore to wheat, scrap metals, minerals and clinker: Nemag has the optimal solution for every dry bulk flow!
Contact us find out how we can take your bulk handling to the next level.

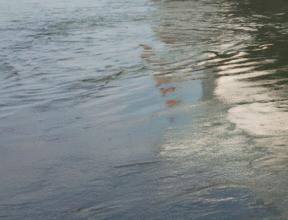
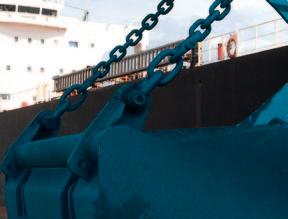
GAMBAROTTA GSCHWENDT’s coal handling expertise and experience
Davide Gambarotta, CEO of GAMBAROTTA GSCHWENDT, explains, “Our mission is to offer customers our experience, knowledge and innovation to render the exceptional products that we design and produce available all over the world, thus creating value for all those who participate in the company and share its objectives.”
The Company
GAMBAROTTA GSCHWENDT SRL is a family-owned company which was founded in 1919 by Umberto Gambarotta Senior in Trento after World War I. At that time, its main business was general mechanical work such as truck fixing, modifications transforming trucks from fixed to tipping,
(especially in Germany, ever since 1958), GAMBAROTTA GSCHWENDT acquired a wide-ranging presence, by getting important foreign orders that led to the opening of commercial offices, first in the Americas, in Asia and then in Africa and Australia.
The new establishment of the Gambarotta Group, led by the current CEO, Davide Gambarotta, took place between 2019 and 2020 and is made up of five leading companies in the sector and about 130 people specialized in 44 different fields.
The companies involved are: GAMBAROTTA repairs to mining equipment, forge jobs, etc. Steel parts were recovered from World War I remnants, since the region had been deeply affected by the conflict.

In 1958 Umberto Gambarotta Jr. (father of the current CEO, Davide Gambarotta) joined the family business and actively contributed to the real first corporate turning point: the truck repair business was replaced by the industrial activity of designing and supplying systems for cement plants, mines and magnesium.
GAMBAROTTA GSCHWENDT transformed itself from a mechanical repair shop, with exclusively local clientèle, to an entity dedicated to the design and supply of conveyor systems for process plants.
From the 80s to the 90s there was great international expansion of the company: from a European industrial reality
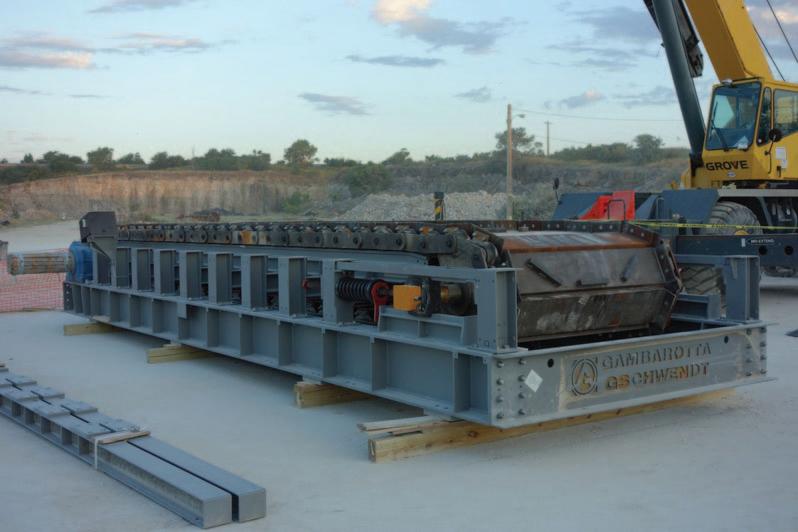
GSCHWENDT SRL; GAMBAROTTA AUSTRALIA; v MDG HANDLING SOLUTIONS SRL; v MDG AMERICA INC.; and v OSSITAGLIO SRL. v
Today, GAMBAROTTA GSCHWENDT’s main products include bucket elevators, screw conveyors, drag chain conveyors, pan conveyors, apron feeders, loading bellows, rotary valves, slide gates and top-quality spare parts for above mentioned equipment.
This article focuses on GAMBAROTTA GSCHWENDT coal handling systems.
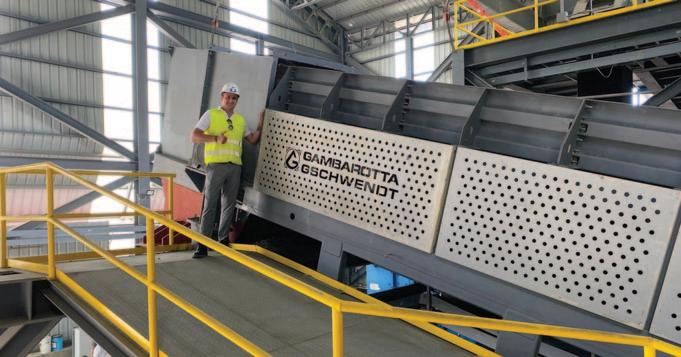
Apron Feeders
The most suitable machine to convey coal is the apron feeder (type EP). It is used to extract bulk materials (such as clinker, limestone, gypsum, coal, minerals, etc.) in lumps of up to 500mm from hoppers or silos.
These machines are generally linearshaped and have a horizontal layout, although they might be used with a slightly inclination (up to about 20°).
The apron feeders comprise a sturdy electro-welded structure that supports the metal deck carrying the material. This deck is formed by a series of base pans — sometimes equipped with reinforced supports on the lower section — joined together by the drive chains. The rigidity of the pans is designed to withstand the static load that is thus distributed on the side tracks through the support and guide rollers.
In the intermediate section, the pans have one or more guide shoes that adhere to the corresponding intermediate tracks, when large dynamic impacts occur (especially when the material falls onto the metal deck). The pans have two small side walls that help to contain the material. A suitable lip placed between two successive plates prevents downward spillage of finegrained material. Two link chains with pins and fixed bushings, which are bolted under the pans, connect the various pans so as to form a continuous metal deck that is jointed thanks to the chain pins. Every second pan is equipped with a pair of rollers with guiding edge and rollingelement bearings: these roll on appropriate tracks and support the metal deck with its load of material. A rigid crossbar placed above the metal deck — in the area where the material exits the hopper or silo — helps to limit the height of the material being extracted. This component, together with the conveying speed (almost always adjustable), allows to achieve the right flow rate.
The drive station in the discharge zone includes a drive unit that imparts movement to the deck, while the return station on the opposite end includes the chain tensioning station.
Recommended speed: <0.20m/sec v with the possibility of adjustment to 1:6 reduction ratio or more; rarely, a curve on the vertical plane v may be required (recommended radius >5m).
A complete range of strong apron feeders is available for the heavy duty extraction of material from hoppers under wagon tippler or truck unloader.
The main features of GAMBAROTTA GSCHWENDT’s apron feeders include: MATERIAL LOAD impact rails: absorb the force of v material loading and protect the roller bearings; the plates flex under the loading v shock, discharging the force on the frame through the impact rails, thus protecting the roller bearing; and once the material is loaded, the plates v are stiff enough to flex back and proceed supported by the rollers without contact with the impact rails.

PLATES thick steel sections forces the material v to follow the plates even during the hardest extractions under a full hopper; and the anti-spillage lip is in special v armoured steel and ensures continuous contact between two adjacent plates, minimizing material spillage.
WHEELS AND CHAINS: drive wheels are made in high alloy v steels with replaceable toothed segments; the parts in contact with the chain are v induction-hardened to extend their operating life; the chains with pins and fixed bushes v are in high alloy steel, inductionhardened on the wear surfaces; and pins and bushes are tempered to v ensure a very long wear life.