
7 minute read
Morska Agencja Gdynia / Poland – eight decades of operations
Morska Agencja Gdynia, operating in the transport and logistics sector on the Polish market, was established in 1951 and is now doing better than ever, writes Marek Kowalski Eubaltica, Consultancy & advisory company for MAG.
The company has more than 70 years of experience, flexibility, ability to adapt to changing market conditions, and most of all committed staff without whom MAG’s market success would be impossible.
Over time, despite providing agency services MAG extended range of activity to include chartering ships, port shipments of bulk goods and many others as well as employment agency for marines of ships under foreign flags.
Milestones In The History Of Mag 28th December 1950
A newly established state-owned enterprise called Morska Agencja in Gdynia resulted from the reorganization of a number of state-owned and private companies in Poland.
1st January1951
The Morska Agencja in Gdynia begins its operation.
MAG takes over the entire service of ships of domestic shipowners — Polish Ocean Lines and Polish Maritime Shipping, as well as units remaining in the chartered Polish-Chinese Ship Association — Chipolbrok.
The following years bring further changes like implementations of the first successful privatizations of a state-owned company in Poland. Morska Agencja in Gdynia becomes an employee-owned company and changes its name to Morska Agencja Gdynia (MAG).
The establishment of an office in London, dealing with the acquisition and recruitment of Polish crews on ships of foreign shipowners, is very important in the history of MAG.
Morska Agencja Gdynia, besides traditional ship agency services, freight and brokerage services, constantly expands the range of its activities by further transport and logistics, customs, warehousing and rail and road forwarding services.
In 2005, the Management Board decided to purchase land in the Port of Darlowo, where the MAG Port Terminal is being built.
In the following years, MAG constantly grows new branches. The new offices are located all over Poland and in Romania in Constanca. MAG gains leadership on the
Polish forwarding market, retaining its former character — an ideal composition of experience with a modern outlook on the ever evolving market.
In 2020 MAG celebrates its 70th anniversary and enters eight decade of operations.
Being over 70 years old, MAG is now an experienced and mature dynamically operating employee-owned company, which has retained its dominant position in the agency market, servicing the largest number of ships in all Polish seaports.
Due to the wide range of bulk cargo handled by ships entering/departing from Polish seaports, MAG provides agency services 24 hours a day, seven days a week, all year round. MAG’s share in the transport of bulk goods is constantly growing in many sectors, such as fertilizers, grain, iron ore, scrap, coke and coal, biomass, aggregates, fertilizers, logs, wood chips, chemical products, wheat, other raw materials. MAG handled more than 1,300 ships in 2022, from coasters to Capesize ships limited to 15 metres (maximum draught in the largest Polish seaports), in which dry bulk cargo accounted for approximately 35% of the agency’s ships served.
The volume and structure of bulk commodities increased, especially in the areas of imported coal and coke and grain in export.
A team of specialists in each field forms a well-coordinated crew, whose work translates into Morska Agencja Gdynia being a leader among companies in the maritime services industry in Poland.
MAG with many awards to its name, as well as the recognition of its contractors, has developed the idea of MAG Centrum, uniting companies that provide broadly understood ships agency, port, logistics, transport and offshore services.
MAG’s activities also include representation of foreign shipping lines, shipowners and insurance clubs (P&I) in Poland and MAG has a number of certificates confirming the highest quality of our services, ISO, AEO quality certified and is a member of BIMCO (The Baltic and International Maritime Council) and also The Polish Shipbrokers’ Association.
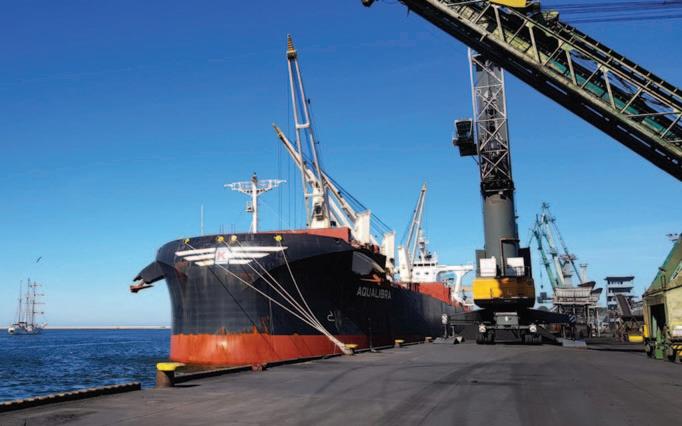
Inchcape’s new Marine Supply Chain Solutions taking the pain out of port turnarounds
The need for efficient procurement of essential supplies to expedite port calls has become an increasing pressure point for vessel operators amid port congestion triggered by the resurgence of world trade in the wake of the Covid-19 pandemic, according to Inchcape Shipping Services.
Logistics and the procurement of spare parts, provisions, consumables, bunker fuel and other supplies play a vital role in keeping trade flowing and ships on track to ensure that contractual voyage commitments in relation to time and cost are met.
But Inchcape’s Head of Global Marine Supply Chain, Robbie Mclellan, says: “Shipowners and managers are facing logistical challenges with rising costs of procurement and delivery, supply bottlenecks, a lack of capacity to handle increased workload, and a lack of visibility and transparency that have affected port turnaround times.”
He also points out that many smaller shipping companies do not have the manpower and resources to carry out internal procurement in a fast and costefficient manner and would benefit from leveraging Inchcape’s global supply chain.
Buying Power For Lower Prices
Consequently, Inchcape has seen increasing requests from clients to meet their logistics and procurement needs, in addition to provision of port agency services, and has therefore launched a dedicated Marine Supply Chain Solutions (MSCS) service with a newly opened warehouse in the shipping hub of Singapore to serve the global market.
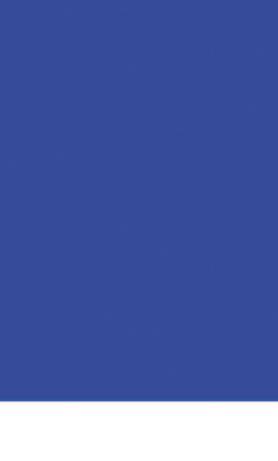
“This brings to the market a strong value proposition as we are able to leverage the scale and expertise of Inchcape’s global network to carry out procurement based on our existing strong relationships with approved local vendors at hundreds of ports in 60 countries,” Mclellan says.
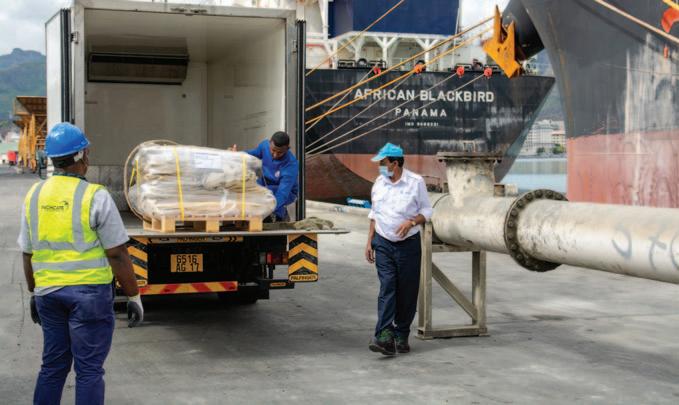
The MSCS team manages the entire supply chain process from procurement of items to last-mile onboard delivery as part of a bespoke solution for shipowners and managers, as well as wind farms, shipyards and other businesses.
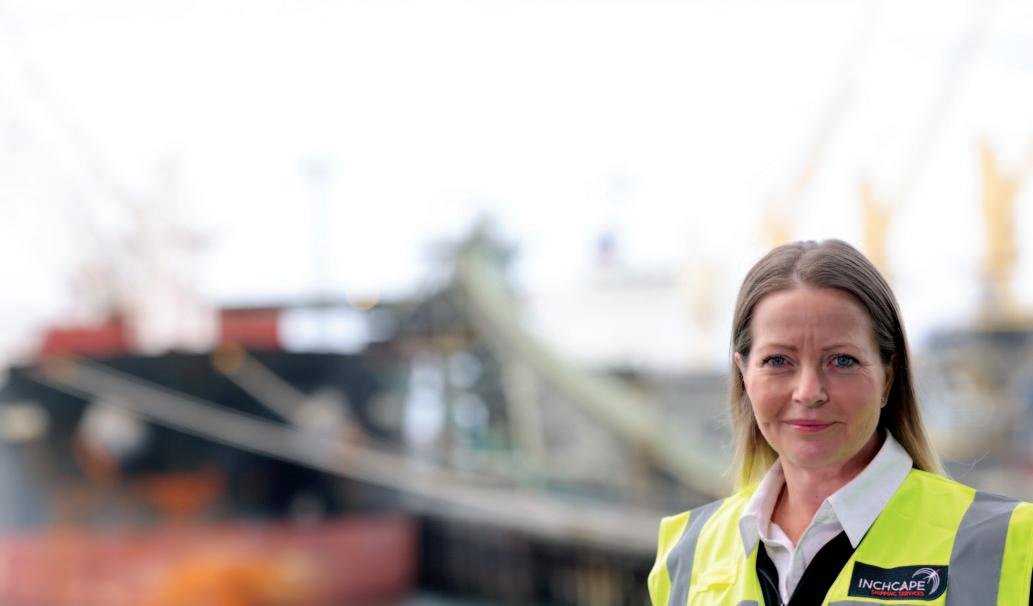
Mclellan explains that Inchcape’s global reach and extensive customer base give it “huge buying power” with its vast vendor network to gain access to better prices in multiple locations around the world.
“Typically, shipowners have limited negotiation power on their own to secure lower prices and do not have local boots on the ground with the necessary vendor relationships,” he says.
‘IF YOU WANT IT, WE CAN GET IT’
Furthermore, all of Inchcape’s vendors are verified on an annual basis for compliance with international QHSSE standards and anti-corruption regulations, while the company adheres to the CIPS Code of Ethical Procurement and promotes sustainable practices throughout its supply chain with regular performance reviews and reporting.
The global reach of MSCS has rapidly expanded beyond major ports like Singapore and Rotterdam to cover locations in more remote parts of the world where Inchcape already has a port agency presence.
“If you want it, we can get it where you need it,” Mclellan says, with MSCS arranging ‘door-to-deck’ delivery of items such as spare parts and provisions as well as bunker fuel and lube oil, in addition to providing handling solutions.
The scope of the service also extends to freight forwarding whereby Inchcape, acting as an intermediary, coordinates worldwide deliveries of diverse shipments by working together with its logistics partners to give favourable fixed freight rates for exporters.
Singapore Warehouse A Storage Hub
The Singapore storage facility covers an area of 10,000 square feet and is equipped with a 500-tonne capacity crane. The warehouse is able to handle inventories of up to 250 tonnes, while there is also a smaller transit warehouse at the port itself.
This is part of Inchcape’s global HUBS network of warehouses spanning North America, mainland Europe, the Middle East and Asia that is run together with partners and coordinated from the MSCS control tower in Mumbai, India.
The MSCS team recently handled its largest freight move to date with a 350tonne shipment from Japan to Singapore of a high-value and sizeable cargo that carried significant risk, demonstrating its credentials in heavy-lift freight forwarding, according to Logistics Manager Nathan Silvester, who is responsible for the Singapore facility.
Another weighty task for Inchcape was being entrusted by a leading global brand with procurement of IT equipment, mainly racking and servers, for shipment on as many as 170 vessels to far-flung destinations across the globe.
Freight Forwarding Tax Benefit
“Located at the heart of the East-West trade routes, Singapore is the busiest port in the world in terms of ship tonnage with an average of 140,000 vessels calling at the port annually and two every minute, of which Inchcape handles a large number. This makes it an important strategic location for freight forwarding,” Silvester says.
“The port offers customs flexibility on transshipments to other countries in the Asian region such as Thailand and Indonesia within a tax-free zone, which results in cheaper freight forwarding.
“Singapore is also an ideal location for supply of spares, provisions and bunkers, which was the rationale behind our decision to establish a range of in-house logistics solutions tailored to the needs of our stakeholders.”
Silvester says spare parts are typically sourced from China, Japan, South Korea and certain parts of Europe, where main engines are made, for distribution to the destination port as required by the client, a process that would usually entail communication at different levels with multiple parties and additional procurement costs for each link in the chain.
Streamlined Procurement Process
“We are able to streamline that process by providing a single point of contact for the vessel operators and having a single digital channel of communication through our global offices, which means we can control the cost factor,” he explains.
MSCS is able to ensure full visibility and transparency in the procurement process, also with a single point of remittance for payments that are invoiced separately to the port agency disbursement accounts, thereby avoiding multiple invoices from different parties. There are also detailed port costs, including first and last-mile delivery charges, as part of a transparent pricing model.
While MSCS is a separate service, Inchcape’s port agency clients can benefit from synergies on procurement given its local teams on the ground are constantly handling changes in voyage schedules and are therefore able to coordinate vessel supplies effectively, according to Mclellan.
“Cost-efficient port turnarounds are critically dependent on local expertise and voyage intelligence, together with effective communication and vendor collaboration, to avoid unnecessary costs and keep the wheels of supply chain logistics running smoothly,” he concludes.